Welcome, Guest |
You have to register before you can post on our site.
|
Online Users |
There are currently 263 online users. » 0 Member(s) | 262 Guest(s) Bing
|
Latest Threads |
Dominica visa free countr...
Forum: Off Topic
Last Post: axied12
06-24-2025, 12:37 PM
» Replies: 0
» Views: 108
|
Advanced microneedling
Forum: Off Topic
Last Post: axied12
05-28-2025, 01:25 PM
» Replies: 0
» Views: 262
|
Caviar and cheese
Forum: Off Topic
Last Post: axied12
05-28-2025, 12:38 PM
» Replies: 0
» Views: 235
|
Top-rated countertop comp...
Forum: Off Topic
Last Post: axied12
05-04-2025, 06:42 AM
» Replies: 0
» Views: 378
|
Ryanair letenky levně do ...
Forum: Off Topic
Last Post: axied12
02-11-2025, 01:37 PM
» Replies: 0
» Views: 759
|
Trusted essay writing ser...
Forum: Off Topic
Last Post: axied12
01-30-2025, 08:16 AM
» Replies: 0
» Views: 692
|
Bootverkopers - actieve j...
Forum: Off Topic
Last Post: axied12
12-07-2024, 11:07 AM
» Replies: 0
» Views: 823
|
Services for individuals ...
Forum: Off Topic
Last Post: axied12
12-02-2024, 03:31 PM
» Replies: 0
» Views: 793
|
Used excavators
Forum: Off Topic
Last Post: axied12
11-13-2024, 09:22 AM
» Replies: 0
» Views: 747
|
Buy Higo Rocket in Dubai
Forum: Off Topic
Last Post: axied12
10-25-2024, 01:09 PM
» Replies: 0
» Views: 856
|
|
|
Is a Bamboo Toothbrush Right for You? |
Posted by: eehis445ss - 08-30-2021, 05:05 AM - Forum: Welcomes and Introductions
- No Replies
|
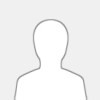 |
As more and more people reconsider plastic products, bamboo toothbrush isbecoming a popular alternative to the plastic kind. We produce more than 359 million metric tons of plastic every year, and a lot of it ends up in landfills. Plastic isn't designed to break down. Some plastic products like straws and toothbrushes are difficult to recycle. Bamboo toothbrushes aren't a new product, but before you make the switch, find out more about why bamboo may be an excellent alternative to reduce plastic waste at home.
What is a bamboo toothbrush?
Bamboo toothbrushes are manual toothbrushes, similar in design to what you would find on any store shelf. A bamboo toothbrush has a long handle and bristles to remove food debris and plaque from your teeth. The critical difference is that the long handle is made from more sustainable bamboo instead of plastic.
Bamboo toothbrushes are one of the oldest types of toothbrushes. The earliest toothbrushes were made in China using bamboo and other natural materials, like using boar's hair for the bristles. Today's bamboo toothbrushes use nylon for the bristles like most toothbrushes today. Some manufacturers still use boar's hair for the bristles or infuse the bristles with activated charcoal.
Are bamboo toothbrushes better for the environment?
Bamboo does have a smaller ecological footprint than plastic because bamboo plants grow quickly, regrowing what was taken for the production of the toothbrush. Bamboo is also biodegradable if used in its raw form, such as for toothbrush handles.
When the nylon bristles are removed, bamboo toothbrush handles can be composted, reused as garden plant markers, or other household uses! However, just like plastic toothbrush handles, they will take up space in a landfill if just thrown away.
Fully biodegradable toothbrushes do exist, with natural fibers for the bristles. Keep in mind that these natural bristles tend to be rougher than nylon bristles, possibly causing wear on your enamel and contribute to receding gums. Speak to your dental hygienist about biodegradable toothbrushes or environmentally-friendly toothbrushes, and they may have recommendations.
Are bamboo toothbrushes good for my teeth?
Bamboo toothbrushes can be just as good for your teeth as plastic toothbrushes. When choosing any kind of toothbrush, consider the size of the head, the shape of the handle, and the bristles. Toothbrushes that can easily fit into the narrow areas of your mouth with soft bristles and a comfortable handle are the best.
You should replace your toothbrush every three to four months or if there is visible damage to the bristles. Replacing your old toothbrush with a new one will help keep your teeth clean. Suppose you have more questions about switching to a bamboo toothbrush. In that case, your dental hygienist can make other recommendations that will keep your mouth healthy while considering plastic waste.
BAMBOO TOOTHBRUSH BENEFITS: WHY YOU SHOULD MAKE THE SWITCH
It was while I was growing up that ‘Reduce, Reuse, Recycle’ became popular. The movement toward being aware of, and protecting, our environment came of age and everyone was looking at ways to lessen our impact on the environment. These days we have evolved to a place where we’re looking for alternatives to materials that harm our environment. One of the best kids bamboo toothbrush benefits is that it is a renewable resource that is grown organically; one of the most environmentally friendly products available.
Bamboo Toothbrush Benefits
Bamboo toothbrush benefits encompass more than just the actual contribution to saving the environment. There is also the conscientiousness of knowing that actions you are taking will preserve plants and trees, rivers and streams, far into the future.
Six Reasons To Switch To A Bamboo Toothbrush
There are a number of reusable hotel bamboo toothbrush benefits to convince you to switch from what you’re using now to bamboo:
Biodegradable. Bamboo is biodegradable. Unlike plastic, which can take up to 1000 (!) years to decompose, bamboo can decompose in as little as 4 months (although it will likely take 3 to 4 years). Knowing that you are using a material that will biodegrade so quickly is the number one reason to switch to a bamboo toothbrush.
Renewable resource. Bamboo is one of the fastest growing plants in the world. It is an infinitely renewable resource ensuring that the supply not diminish and that we are not removing a vital plant in the eco-system from the world.
Antimicrobial properties. This one is definitely a little controversial. ‘Bamboo kun’ is a natural substance within bamboo that helps the plant grow and mature quickly before harvesting. It’s not understood, however, if these antimicrobial properties continue after harvesting or after being transformed into household objects or fabric. It remains, however, an interesting point.
Longevity. Lest you be concerned that a material that degrades so quickly might not be reliable; let me alleviate that. Bamboo toothbrushes last as long as, or longer, than plastic toothbrushes of the same type. Bamboo is strong, resilient, and reliable for far longer than the recommended 3 or 4 month replacement rate for toothbrushes. You may be more inclined to heed that recommendation knowing that bamboo is so biodegradable and good for the environment.
Affordability. Bamboo toothbrushes aren’t any more expensive than a good quality plastic toothbrush! You can pick one up for the same couple of bucks you were going to spend anyway.
Environmentally friendly. This deserves mentioning again. Not only is bamboo efficiently biodegradable, it’s also infinitely renewable, and is strong, resilient, and reliable – making it one of the most environmentally friendly materials out there.
Things to Like:
Recycled, biodegradable packaging
Activated charcoal embedded bristles
Smooth surface for a good mouthfeel
These environmentally friendly, biodegradable biodegradable family bamboo toothbrush is also cruelty free and vegan friendly. You can be sure that your impact on the world is limited when using these daily.
The best part about these toothbrushes is that they work as well as regular, plastic toothbrushes. The BPA free bristles clean effectively and are long lasting. They are charcoal infused; which is thought to help in preventing bacteria build up in the toothbrush between cleanings. The handle is strong and smooth for a good mouth feel.
Each individually wrapped toothbrush is embossed with a number; to help each member of your family know which toothbrush is theirs.
10 Amazing Benefits of Combing Your Hair with a Wooden Comb
Nature has bestowed us with many good things, and wood is one of them. Apart from being used in various ways to make our lives more comfortable, wood can also be carved into combs and used for grooming our tresses. From time immemorial, people have been using wooden combs to maintain the health and beauty of their mane. Here are some amazing benefits of using a wooden comb:
1. A Healthy Scalp
A healthy scalp supports healthy locks, and one of the natural ways of taking care of your scalp is by using a wooden comb. When you use a wooden comb to brush your hair, it presses against your scalp and triggers the acupuncture points and also gives a massage to your scalp. All this proves to be good for the overall blood circulation to your scalp and proves to be of great benefit for your hair.
2. Nourishes the Hair
If you are wondering how a sandalwood comb benefits your hair, well, whenever you use a wooden comb instead of a plastic comb, the natural oils present in your scalp get equally distributed across your tresses. Using a wooden comb not only reduces the chances of hair breakage and hair fall but it also helps to make your hair shinier, bouncer and healthier.
3. Promotes Hair Growth
If you wish to have healthy and long tresses, then do try using a wooden comb. This is because a wooden comb improves the blood flow to your scalp, which in return helps the hair follicles get optimum nutrients. It also helps in eliminating or removing impurities by regulating the production of sebum.
4. Prevents Greasiness
Most of us may be battling a greasy scalp, which results from the uneven distribution of natural oils secreted by sebaceous glands. However, when you use a wooden comb, the oil gets evenly distributed not only across your scalp but also across the length of your hair. This leaves your hair less greasy or oily in comparison to what may occur after using a plastic or PVC comb.
5. Prevents Breakage and Hair Loss
Using a wooden comb may prove better for your hair than a plastic comb. This is because a wooden comb slides smoothly through the hair, leading to less breakage and damage. Also, it has wider bristles, which move easily through the hair. That reduces friction and helps in detangling the hair in a better way.
6. Prevents Dandruff
Dandruff can be a very annoying scalp problem and a never-ending battle with the white scaly flakes. However, using wooden combs can help you prevent this issue because it is not only gentler and softer on your hair and scalp, but also prevents any harm to the scalp that may be caused due to friction, cuts or nicks.
7. Removes Foreign Particles and Dirt from Hair
Pear wood comb is very common for our hair to attract dirt or foreign particles. However, using a wooden comb can help in getting rid of these. This is because unlike metal or plastic combs that attract such substances because of the heavy charge in them, wooden combs may easily help in clearing any such substances from your hair and scalp.
8. Prevents Allergies
Plastic or metal combs may sometimes irritate or cause an allergic reaction on the skin. If you have a sensitive scalp, then using a wooden comb may be a wise thing to do. This is because these combs are made with natural components and some of these even come with a protective coating. Hence, they are less likely to irritate or cause any kind of allergic reaction on your scalp as compared to plastic combs.
9. Prevents Static Damage
Static is one of the worst things that can happen to your hair because it makes your hair more prone to damage and breakage. This condition becomes more pronounced when you use metal or plastic combs. However, wooden combs prevent your tresses from getting static and thus prove to be better for your hair.
10. Adds Bounce
If you are wondering what the various neem-wood comb benefits are, well, a neem comb or any wooden comb can give you bouncy tresses. When you use a wooden comb regularly, your scalp will be nourished with proper blood circulation and optimum blood circulation. Together, all this will lend a healthy bounce to your hair.
Kraft Boxes Types and Their Advantages
In today's world, there are a variety of different types of kraft paper box on the market, often used for different purposes such as shipping, gifts, and packaging. However, the Kraft boxes are the most popular paper boxes that apply to the diverse range of packaging.
The Kraft boxes change our world through their various packaging uses. They bring convenience to our lives when it comes to packing so many different products. Although there is a variety of custom carton packaging on the market today, many customers still prefer packaging boxes made of Kraft paper. First, Kraft boxes are environmentally friendly because they are made of high-quality pine materials. These Kraft boxes are completely recyclable. Second, Kraft boxes are strong enough to safely preserve and transport products inside them. Third, pine wood pulp plays a very important role in the manufacture of high-quality products. In addition, the use of Kraft materials is not harmful to the ecosystem.
Kraft paper is the material that makes these Kraft boxes, which is why they are named after it. Every industry has a variety of boxes made of Kraft paper, many of which you can't even imagine. Their wide range of uses provides us with a variety types Kraft boxes. Here let me share the top 10 Kraft boxes types and their advantages with you.
This kind of Kraft box is fold-able and flat shipped boxes. They are very commonly used Kraft box style, it has a Kraft paper sleeve and a sliding drawer, both are folded with a piece of Kraft paper. The sleeve can also be made of clear plastic, our store supply this kind Kraft boxes in a number of colors and sizes, you can click below image and shop now.
We can notice this type of Kraft boxes in almost all types of stores. From confectionery shops to cosmetics, decorations and even grocery stores, this Kraft box is available on their counter-tops. The advantage of using these Kraft boxes is to attract customers and enhance their impulsive purchases. Even in big brand stores, the reception desk has these Kraft boxes for advertising purposes. Because these boxes don't require much space to place. So they are very popular with sellers. These counter display Kraft boxes can be customized to any size and shaped advertising panel to suit packing various products in the market. They are a great way to brand your products.
We all know the jewelry box in rigid chipboard or plastic. Also, Kraft boxes are another packaging made for the jewelry business. Jewelry Kraft boxes are best suited affordable packaging for storing jewelry or selling handmade jewelry on the market to make a profit. Popular jewelry brands are using these boxes to differentiate their brands from other brands. A simple and natural Kraft box with white foam insert is a nice choice for protecting and organizing the jewelry like necklace, earrings to stand out their luster.
Together with cosmetics, these Kraft boxes are perfect suit. We are well aware that products that need to be used on the skin require quality packaging to protect their internal products. As a result, we often see Kraft cartons for lipstick, mascara, eye shadow and foundation in our daily lives.
|
|
|
Polypropylene as a Promising Plastic: A Review |
Posted by: eehis445ss - 08-30-2021, 05:04 AM - Forum: Welcomes and Introductions
- No Replies
|
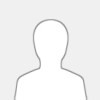 |
Darrell Griffin hates to fly, so it was with no small degree of trepidation that he faced a flight from Los Angeles to New York a couple of years ago. Desperate for a distraction, Griffin, a film producer at the time, turned to his business partner for help. "To take my mind off the flight, he put a film on my handheld PC," Griffin says. The movie was Hercules Unchained, starring Steve Reeves. The diversion worked, and by the time Griffin landed in New York, he had an idea for a new business.
When they returned to L.A., Griffin and his partner sat down to figure out how they could turn that distraction into a business. "Pocket PCs are synced up all the time," Griffin says. "We wanted to figure out how to create a retail product." They devised a technology to compress filmed content from CD-ROMs into a format PDAs could display. Then in November 2001, Griffin helped launch Pocket PC Films, in Sherman Oaks, Calif., to distribute video content for Pocket PC and Palm OS devices. Film fans can buy CD-ROM titles, load them on their computer and sync them into their handheld device. (The films will also run on desktop PCs, but the format remains handheld-size due to licensing issues.)
Griffin, now president of Pocket PC Films, has high hopes. "The market is growing faster than we thought," he says. "Dataquest estimates that 23 million PDAs will be shipped in 2003, but that was before Dell and ViewSonic announced plans to offer models."
Beware the 9 warning signs of bad IT architecture and see why these 10 old-school IT principles still rule.
Pocket PC Film now distributes 25,000 titles, priced from $9.99 to $49.99, that run the gamut from 1941’s King of the Zombies to Oliver Stone’s more recent Natural Born Killers. The company also provides self-help and business-oriented content, as well as classic TV packs with shows like Dragnet and the Sports Illustrated’s "Swimsuit 2002" special?the most popular title so far.
High Impact Polystyrene (HIPS), which made of HIPS rigid film, and Rigid Vinyl (sometimes referred to as PVC or RPVC) are often the main films considered for a variety of lower cost applications such as point-of-purchase signage, shelf danglers, membership and loyalty cards, and tags to name a few. On the surface, it is sometimes viewed that the two films are often interchangeable and either one can be used. However, there are some key differences in film characteristics that leads to one film being the better choice over the other depending on the application needs. The chart below compares key characteristics of the two films and will help you make the best choice in using either rigid vinyl or polystyrene film
Plastics are categorized into four main groups: thermoplastics, elastomers, thermosets and polymer compounds. Macromolecular structures distinguish the class of any plastic material as well as its physical properties. Elastomers and thermosets have soft and hard elasticity, respectively; and their resins cannot be melted for recycling purposes. However, thermoplastics are either amorphous or semi-crystalline. Amorphous resins are disordered statistical oriented macromolecules whereas semi-crystalline resins macromolecules are nearly ordered since they are embedded with crystalline phases. Typical amorphous resins are polycarbonate (PC), polystyrene (PS) and polyvinylchloride (PVC) where typical semi-crystalline resins includes polyamide (PA) and polypropylene (PP). Since PP is under the semi-crystalline class, our focus will be on this group.
The annual global demand for plastics reached 245 million tons and it is project to grow dramatically because of the increase in public demand. Figure 2 shows the total plastics demand by 2006. Around 90% of the total demand is accounted for five main commodity plastics: polypropylene (PP), polyethylene (PE), polyvinyl chloride (PVC), polystyrene (PS) and polyethylene terephthalate (PET). In 1954, Giulio Natta discovered PP, but commercial production began in 1957. PP is the most widely used thermoplastic since it is very cheap and flexible for molding. The second common plastic type is PE. There are different grades of PE linear low density (LLDPE), low density (LDPE), medium density (MDPE) and high density (HDPE). The density of PE grades ranges between 0.925-0.965 and obviously is higher than PP. However, the uniqueness of PVC film is associated with chlorine content (57 wt. %) in its structure. Annual worldwide PVC demand is approximately 35 million tons.
According to previous studies, plastics are the most recyclable materials and there were 4.4 million tons of plastics recycled in 2006.Polypropylene chemical resistance can be described as follows: excellent resistance to dilute and concentrated acids, alcohols and bases, good resistance to aldehydes, esters, aliphatic hydrocarbons, ketones and limited resistance to aromatic and halogenated hydrocarbons and oxidizing agents. Polypropylene has a crystalline structure with a high level of stiffness and a high melting point compared to other commercial thermoplastics. The Hardness resulted from the methyl groups in its molecular chain structure. Polypropylene is a lightweight polymer with a density of 0.90 g/cm3 that makes it suitable in many industrial applications. Still, polypropylene is not suitable to be used at temperatures below 0°C. Experiments proved that polypropylene has excellent and desirable physical, mechanical, and thermal properties when used in room temperature applications. It is relatively stiff and has a high melting point, low density and relatively good resistance to impacts.
Typical crystallinity of PP is between 40-60%. PP is a low-cost thermoplastic polymer with excellent properties like flame resistance, transparency, high heat distortion temperature, dimensional stability and recyclability making it ideal for a wide range of applications.Propylene is one of the most important industrial petrochemical building blocks used to produce various chemical derivatives. The dominant outlet for propylene is PP which accounts for nearly two-thirds of global propylene consumption as shown in Figure 3. There are three major sources of propylene: from steam cracking of naphtha, gasoline refining process and propane dehydrogenation technology. Polypropylene is the most important material among polyolefins due to three main reasons. First, great properties of PP such as low density, high melting temperature and chemical inertness with low cost making PP optimum for long-life applications. Second, polypropylene is a highly versatile material meaning that diversity in structural designs and mechanical properties are achievable. Third, different morphological structures of PP are possible by using fillers or reinforcing agents and blending PP with other polymers which yield to have superior characteristics. Special and reinforced polypropylene grades include elastomer-modified PP, elastomer modified filled PP, glass fiber-reinforced PP, filled PP, esthetic filled PP, flame-retardant PP and thermoplastic elastomers.
A study shows that branching process of linear Ziegler–Natta polypropylenes is possible by creating chains based on the molecular weight distribution. Introducing branching into a linear polypropylene will result in having a product with high molecular weight, high melt strength and better properties like high modulus and tensile strength, rigidity and excellent heat resistance. Branching parameters β, the average number of branch points per molecule, and λ, the number of branch points per 103 carbons, are calculated to identify the polymer structure and properties.
A post-reactor is used for the branching process. The branching efficiency is associated with chemical composition and temperature of the reaction. The relationship between branching parameters and molecular weight is important to design polymers with unique properties for different applications. PP rigid film is very suitable for reinforcing and filling. Thus, another study focuses on studying the effect of fibers reinforcement on the mechanical properties of fiber-reinforced polypropylene composites (FRPCs).
A composite material is a polymer matrix that is embedded with reinforcement fibers such as glass or carbon. FRPCs have better durability, moisture resistance and high strength properties; making them ideal in applications related to constructions, sports equipment and cars. Synthetic fibers yield to have better mechanical properties compared to natural ones. Glass fibers are widely used as a synthetic reinforcement with PP to produce very good mechanical properties composites. However, mechanical characteristics of composites are controlled by numerous fiber treatments and coupling agents. Fiber diameter is another significant factor in designing composites material. A certain value of fiber diameter thickness should not be exceeded; if so fibers will decrease composites strength.
Electrically conductive PP and PE composites are cost-effective, commercially proven and with outstanding electrical and mechanical properties. It is mandatory to understand the distribution, orientation, interaction and aspect ratio of conductive fillers with the polymer matrix to obtain the required conductivity. Better filler-matrix interactions are achievable at low viscosity, low surface tension and high crystallinity. Grafting technique initiates the interactions and the distribution of the fillers with PP and PE matrices.
|
|
|
Types of Hourglass |
Posted by: eehis445ss - 08-30-2021, 05:02 AM - Forum: Welcomes and Introductions
- No Replies
|
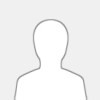 |
Before the invention of mechanical clocks, timepieces used the sun's motion or simple measurement devices to track time. The sundial may be the best known ancient keeper of time, and it is still manufactured as a popular garden accessory—but for its visual interest, not for practical time measurement. Stonehenge, the giant monument built of upright stones on the Salisbury Plain of Wiltshire, England, may have been used as a sundial and for other time and calendar purposes. Sundials have obvious disadvantages; they can't be used indoors, at night, or on cloudy days.
Other simple measurement devices were used to mark the duration of time. Four basic types could be used indoors and regardless of the weather or time of day. The candle clock is a candle with lines drawn around it to mark units of time, usually hours. By observing how much of the length of a candle burned in one hour, a candle made of the same material was marked with lines showing one-hour intervals. An eight-hour candle showed that four hours had passed when it had burned down beyond four marks. The clock candle had the disadvantages that any changes in the wick or wax would alter burning properties, and it was highly subject to drafts. The Chinese also used a kind of candle clock with threads used to mark the time intervals. As the candle burned, the threads with metal balls on their ends fell so those in the room could hear the passage of the hours as the balls pinged on the tray holding the candle.
The oil lamp clock that was used through the eighteenth century was a variation and improvement on the candle clock. The oil lamp clock had divisions marked on a metal mount that encircled the glass reservoir containing the oil. As the level of oil fell in the reservoir, the passage of time was read from the markings on the mount. Like the candle clock, the oil lamp clock also provided light, but it was less prone to inaccuracies in materials or those caused by drafty rooms.
Water clocks were also used to mark the passage of time by allowing water to drip from one container into another. The marks of the sun's motion were made on the first container, and, as water dripped out of it and into another basin, the drop in water level showed the passage of the hours. The second container was not always used to collect and recycle the water; some water clocks simply allowed the water to drip on the ground. When the eight-hour water clock was empty, eight hours had passed. The water clock is also known as the clepsydra.
History
Sand timer hourglass (also called sand glasses and sand clocks) may have been used by the ancient Greeks and Romans, but history can only document the fact that both cultures had the technology to make the glass. The first claims to sand glasses are credited to the Greeks in the third century B.C. History also suggests sand clocks were used in the Senate of ancient Rome to time speeches, and the hourglasses got smaller and smaller, possibly as an indication of the quality of the political speeches.
The hourglass first appeared in Europe in the eighth century, and may have been made by Luitprand, a monk at the cathedral in Chartres, France. By the early fourteenth century, the sand glass was used commonly in Italy. It appears to have been widely used throughout Western Europe from that time through 1500. The hourglass or sand clock follows exactly the same principle as the clepsydra. Two globes (also called phials or ampules) of glass are connected by a narrow throat so that sand (with relatively uniform grain size) flows from the upper globe to the lower. Hourglasses were made in different sizes based on pre-tested measurements of sand flow in different sizes of globes. A housing or frame that enclosed the globes could be fitted to the two globes to form a top and bottom for the metal sand timer and was used to invert the hourglass and start the flow of sand again. Some hourglasses or sets of hourglasses were set in a pivoted mount so they could be turned easily.
The earliest writings referring to sand glasses are from 1345 when Thomas de Stetsham, a clerk on a ship called La George in the service of King Edward III (1312-1377) of England, ordered 16 hourglasses. In 1380, following the death of King Charles V (1337-1380) of France, an inventory of his possessions included a "large sea clock … in a large wooden brass-bound case."
John Harrison and his brother James were introduced to clock repair by their father, Henry. At the time, clock making, or horology, was undergoing a developmental revolution. Mechanical clocks had existed since the fourteenth century, but had remained rather primitive in their operation until Christiaan Huygens invented the weight-and-pendulum clock in 1656. One limitation was that they were totally dependent upon the earth's gravity for their operation. This meant that they could not keep accurate time at sea, and could not be adapted for portability. Even moving them across a room would require adjustment.
The Harrison brothers set to work on developing a marine chronometer in 1728. The motivating factor was money. In 1714, the English Admiralty set up an award of £20,000 for anyone who could provide mariners with a reliable clock that, when used with celestial sightings, could keep them informed of their longitude at sea. Mariners had to rely heavily on dead reckoning to find their way, often leading to tragic results.
The Harrison strategy was to design an instrument that was not only internally accurate but also externally stable. The Harrisons made several models of marine chronometers. The fourth model proved to be the most successful. On a nine-week voyage from England to Jamaica in 1761, the device had only a five-second error.
The Board of Longitude, apparently miffed that a common artisan had achieved the coveted goal, reluctantly gave up only half of the prize. John, minus his brother, refused to accept only half of the reward and persisted until the other half was relinquished.
The Board subjected his invention to undue scrutiny and required him to design a fifth model. This time, Harrison outdid himself by designing a compact timepiece that resembled a modern day pocket watch. It was far more convenient than the previous models, which were heavy and bulky. The Board still refused to capitulate. Finally, only a personal appeal to King George III and the King's intervention could set things right, and Harrison received the full reward in 1773 at age seventy-nine. Harrison lived only three more years.
These two early associations of sand clocks with the sea show how navigation had become a time-dependent science. Compasses and charts, developed in the eleventh and twelfth centuries, helped navigators determine bearings and direction, but time measurement was essential to estimating distance traveled. The sand glass may have been invented —or perfected—for use at sea where equal units of time were measured to estimate distance; by contrast, on land, unequal time measurements were more important because activities depended on the length of day.
The great advances in maritime science occurred in the twelfth century with the development of the magnetic compass in Amalfi, Italy. Other Italian port cities like Genoa and Venice contributed to the astronomical advances in navigation, and, by coincidence, Venice was the world's greatest glass-blowing center. Furthermore, the fine marble dust from the quarries at Carrara was perfect for use as sand in navigational sand clocks. As well as measuring time as distance at sea, hourglasses were used by the navies of several nations to "keep the watch" or measure the time the crew worked. The ship's boy was in charge of turning the hourglass; to get off work early, he would "swallow the sand" or turn the glass before it was empty.
The most extraordinary hourglasses were made as gifts for royalty. Charlemagne (742-814) of France possessed a 12-hour hourglass. In the sixteenth century, Holbein (1497-1543) the artist made spectacular hourglasses for Henry VIII (1491-1547) of England. Other sand glasses contained multiple instruments. For example, a sand glass made in Italy in the seventeenth century contained four glasses. One had one-quarter hour of sand; the second, a half-hour of sand; the third, three-quarters of an hour of sand; and the fourth contained the full hour's measure of sand. Some glasses also had dials with pointers, so, with each turning of the glass, the number of turns could be shown with the pointer to mark the cumulative passage of time.
The upper and lower globes of each glass were blown separately with open apertures or throats. To join them so that sand could flow from the upper globe to the lower, the two halves of the glass were bound together with cord that was then coated with wax. The two-coned glass phial could not be blown as one piece until about 1800.
In about 1500, the first clocks began to appear with the invention of the coiled spring or mainspring. Some weight-powered clocks had been made before 1500, but their size limited their practicality. As the mainspring was improved, smaller, tabletop clocks were manufactured and the first watches were made. Mainspring-driven clocks made curiosities out of clepsydras and sand glasses, but, interestingly, the most beautiful hourglasses were made after 1500 as decorative pieces. There are many types of hourglasses, such as metal hourglass,wood hourglass and so on.
By the 1400s, many private homes had sand clocks for household and kitchen use. Sermonglasses were used in churches to track the length of the minister's sermon. Hourglasses were also routinely used in the lecture halls of Oxford University, craftsmen's shops (to regulate working hours), and in England's House of Commons where bells to signal voting and lengths of speeches were timed based on sand clocks. During the height of the sand glass, doctors, apothecaries, and other medical practitioners carried miniature or pocket sand glasses with durations of one-half or one minute to use when timing pulses; the practice of carrying these continued until the nineteenth century. Today, miniature versions containing three minutes worth of sand are sold as egg timers and as travel souvenirs. Larger sand clocks are still made today of ornamental materials and in interesting styles for use as decoration. All of these measuring devices (clock candles, water clocks, and sand clocks) have the disadvantage that they must be watched carefully.
How to use a massage ball
Like a foam roller, a massage ball can also be used to help release tension in our achy muscles after long hours spent in the office or after a workout. One of the differences being that it can get to those hard to reach areas such as the upper back, buttocks and feet. “Knots” or “trigger points” can be massive sources of pain in our bodies and using self-massage techniques can be very satisfying. Before diving in, there are a few important things to know which will help you achieve the best results.
Why a massage ball
Massage balls are affordable and small and therefore they can easily fit into a suitcase or handbag to use wherever you go. They also promote self-sufficiency so there is no need to rely on anyone else. Notwithstanding, it does not always give the same results as a traditional massage delivered by an experienced therapist
Find the right ball
There are many different types of massage balls ranging from very smooth and firm like a lacrosse ball to small and soft like a squash ball. Other balls include a tennis ball and the trusty spikey massage ball. To each his own but if you’re new to using a massage ball, perhaps start with a spikey ball or a tennis ball.
Where and when
Since they are so conveniently easy to use, you can use them almost anywhere for example against a wall, the back of a chair, on the floor or use your hands. Some office workers keep them at their desks as a reminder to use them during the day to help with releasing built-up muscle tension from poor posture or stress.
Start with only a few knots at a time, the most painful area being first. The idea is to trap the knot in the muscle with the ball and apply gently to medium pressure until the painful sensation has faded. Once you have the correct spot (and you will know when), hold it there and try to relax until only about 80% of the ache remains. When pressing too firmly, the sensation can be too painful for you to relax which defeats the purpose of using the massage ball in the first place, it could also potentially irritate the area. You are looking for a “good pain”.Roll the ball around to look for more tender spots or just enjoy gently going back and forth over the tight muscle. If you feel the muscle needs it, you can repeat it twice a day. After releasing the knot, follow it up with gentle stretches to the same muscle. It’s okay to lightly exercise the muscle afterward but avoid fatiguing it for 24 hours.
The gear shift knob in a manual transmission equipped car or light truck is the large knob, usually made of plastic, that attaches to the top of the gear shift lever. Over time the surface of the knob can wear and you might wish to replace it to spruce up the interior of your vehicle. Many aftermarket manufactures offer specialty gear shift knobs. Some of these are made out of exotic materials such as leather or billet aluminum. Some companies offer novelty gear shift knobs for owners who want to personalize the interiors of their vehicles.
|
|
|
Ball Valve - How They Work |
Posted by: eehis445ss - 08-30-2021, 05:00 AM - Forum: Welcomes and Introductions
- No Replies
|
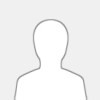 |
A ball valve is a shut off valve that controls the flow of a liquid or gas by means of a rotary ball having a bore. By rotating the ball a quarter turn (90 degrees) around its axis, the medium can flow through or is blocked. They are characterized by a long service life and provide a reliable sealing over the life span, even when the valve is not in use for a long time. As a result, they are more popular as a shut off valve then for example the gate valve. For a complete comparison, read our gate valve vs ball valve article. Moreover, they are more resistant against contaminated media than most other types of valves. In special versions, ball valves are also used as a control valve. This application is less common due to the relatively limited accuracy of controlling the flow rate in comparison with other types of control valves. However, the valve also offers some advantages here. For example, it still ensures a reliable sealing, even in the case of dirty media. Figure 1 shows a sectional view of a ball valve.
Standard (threaded)
Standard ball valves consist of the housing, seats, ball and lever for ball rotation. They include valves with two, three and four ports which can be female or male threaded or a combination of those. Threaded valves are most common and come in many varieties: with approvals for specific media or applications, mini ball valves, angled ball valves, ISO-top ball valves, with an integrated strainer or a bleed point and the list goes on. They have a wide range of options and a large operating range for pressure and temperature.
For more information on a threaded connection, read our ball valve connection types article.
Hydraulic
Hydraulic ball valves are specially designed for hydraulic and heating systems due to their high operating pressure rating and hydraulic and heating oil resistance. These valves are made of either steel or stainless steel. Besides these materials, the seats also make hydraulic valves suitable for high operating pressure. The seats of these valves are made of polyoxymethylene (POM), which is suitable for high pressure and low temperature applications. The maximum operating pressure of hydraulic ball valves goes above 500 bar while the maximum temperature goes up to 80°C.
Ball valves are used for both on/off and throttling service. Ball valves are similar to plug valves but use a ball-shaped seating element (Figure 4.56). They are quick-opening and require only a quarter-turn to open or close. They require manual or power operators in large sizes and at high operating pressures to overcome the operating torque. They are equipped with soft seats that conform readily to the surface of the ball and have a metal-to-meal secondary seal. If the valve is left partially open for an extended period under a high pressure drop across the ball, the soft seat may become damaged and may lock the ball in position. Ball valves are best suited for stopping and starting flow but may be used for moderate throttling. Compared with other valves with similar ratings, ball valves are relatively small and light.
Flanged
Flanged ball valves are characterized by their connection type. The ports are connected to a piping system via flanges that are usually designed in accordance with a certain standard. These valves provide a high flow rate since they typically have a full-bore design. When choosing a flanged ball valve, besides the pressure rating, you also have to check the flange compression class which indicates the highest pressure this connection type can withstand. These ball valves are designed with two, three or four ports, they can be approved for specific media, have an ISO-top and everything else a standard quarter turn valve could have. They are typically made out of stainless steel, steel, or cast iron.
Vented
Vented ball valves look almost the same as the standard 2-way ball valves when it comes to their design. The main difference is that the outlet port vents to the environment in closed position. This is achieved by a small hole that is drilled in the ball and in the valve body. When the valve closes, the holes line up with the outlet port and release the pressure. This is especially useful in compressed air systems where depressurization provides a safer working environment. Intuitively these valves look like 2-way ball valves while in fact they are 3/2-way due to the small borehole for venting.
Ball valves are not recommended for FO applications. Generally, it is possible to reduce the opening time of the fail open actuated valve by installing a quick exhaust valve on the control panel to release the instrument air from the pneumatic actuator in the fail mode quickly. However, a ball valve’s seat and disk are in contact during the opening and closing, which can jeopardize FO. In addition, moving the relatively large and heavy ball requires a higher stem torque, a larger actuator, and perhaps a longer opening time. The ball valve manufacturer was asked about the possibility of using a soft seat ball valve for this application. The manufacturer believed that FO of the soft seat ball valve in 2 s could cause damage to the soft seat because of the very quick contact with the ball. On the other hand, the manufacturer stated that a 2-s opening time can be achieved with a metal seat ball valve. But a metal seat has the disadvantage of possible leakage, unlike a soft seat, and it is a more costly solution than butterfly and axial control valves due to the valve and the large mounted actuator.
Unlike FO applications, a ball valve is a good choice as a blowdown valve with less opening time than an FO valve. Fig. 12.25 shows a blowdown ball valve to release the overpressured fluid from the equipment in an emergency mode. The blowdown ball valve is an 18″ Class 2500 in a 6MO body and a metallic Inconel 625 seat, which may need 18 s for opening. Blowdown or FO valves on flare lines usually see low operating temperatures because of the released gas pressure drop. Gas pressure drop reduces the operating temperature to ? 46°C or even lower, so the minimum design temperature is typically below ? 100°C. The low temperature application makes it impractical to use 22Cr duplex with a minimum design temperature of ? 46°C for the valve, so 6MO or Inconel 625 are the correct choices of materials. An extended bonnet is used for the valve to keep the packing away from the relatively cold service, similar to cryogenic valves.
Ball valve working principle
To understand the working principle of a ball valve, it is important to know the 5 main ball valve parts and 2 different operation types. The 5 main components can be seen in the ball valve diagram in Figure 2. The valve stem (1) is connected to the ball (4) and is either manually operated or automatically operated (electrically or pneumatically). The ball is supported and sealed by the ball valve seat (5) and their are o-rings (2) around the valve stem. All are inside the valve housing (3). The ball has a bore through it, as seen in the sectional view in Figure 1. When the valve stem is turned a quarter-turn the bore is either open to the flow allowing media to flow through or closed to prevent media flow. The valve's circuit function, housing assembly, ball design, and operation types all impact the ball valve's operation are are discussed below.Circuit function
The valve may have two, three or even four ports (2-way, 3-way or 4-way). The vast majority of ball valves are 2-way and manually operated with a lever. The lever is in line with pipe when the valve is opened. In closed position, the handle is perpendicular to the pipe. The ball valve flow direction is simply from the input to the output for a 2-way valve. Manually operated ball valves can be quickly closed and therefore there is a risk of water hammer with fast-flowing media. Some ball valves are fitted with a transmission. The 3-way valves have an L-shaped or T-shaped bore, which affect the circuit function (flow direction). This can be seen in Figure 3. As a result, various circuit functions can be achieved such as distributing or mixing flows.
Inspecting Pipes in Exterior Walls and Pipe Insulation
Locating water pipes in exterior walls should be avoided. If pipes are located in exterior walls, in addition to insulating the pipe, the homeowner should ensure that as much cavity insulation as possible is installed between the pipe and the outer surface of the wall. In cold climates, having pipes in unconditioned attics should be avoided. The image above is of uninsulated water supply pipes in an unconditioned basement.
Insulating water pipes can save energy by minimizing heat loss through the piping. Insulating pipes will reduce the risk of condensation forming on the pipes, which can lead to mold and moisture damage. Insulation pipe can protect the pipes from freezing and cracking in the winter, which can cause considerable damage in the walls of the home and result in significant home repair bills for the homeowner. Studies by the Department of Energy (DOE’s) Building America program have shown that distribution heat loss in uninsulated hot water pipes can range from 16% to 23%, depending on the climate. Adding 3/4-inch pipe insulation can cut overall water heating energy use by 4% to 5% annually.
The best practice is to avoid having water pipes located in exterior walls or through unheated attics. It is preferable to have plumbing fixtures aligned with interior walls. If pipes are located in exterior walls, the pipes should be insulated. To further protect the pipes from heat loss, the wall cavity containing the pipes should be air-sealed by caulking or foaming all seams between the back wall of the cavity and the framing, and by sealing any holes through the framing for the piping. In addition, cavity insulation should be installed behind the pipes, between the pipes and the exterior wall.
If the house has a hydronic (steam or hot water) heating system, heat loss can be reduced by as much as 90% by insulating the steam distribution and return pipes, which provides a quick payback on investment.
Insulated copper coil is one of the main aspects of many of Joseph Henry’s experiments in the field of Electricity and Magnetism is the large coils or helices of copper wire or ribbon he used. These coils were often quite large, usually containing over 1000ft of wire and sometimes weighing over 10lbs. As described by Henry in his papers, these coils were often insulated by wrapping the wires in cotton, dipping them in beeswax, and then painting.
Optimization and intelligent manufacturing are of particular interest and important to improve the severe situation of excessive mass and uneven stress distribution for three branch joint in treelike structures. In this work, the optimal shape of the three-branch joints under vertical load is studied by topology optimization method, and the complex topology optimization Y joint is manufactured using threedimensional (3D) printing technology because it is difficult to produce by conventional manufacturing processes. First, the original model is optimized by using the OptiStruct solver in HyperWorks version 14.0 (64-bit) software, and the element density cloud map and element isosurface map of the model are obtained. Then, the static behaviors of the topology optimization model are compared with those of the hollow spherical joint model which is commonly used in engineering and those of the bionic joint model based on empirical design. Finally, the 3D printing technology is used to produce the topology optimization joint model, the hollow spherical joint model, and the bionic joint model.
|
|
|
5 Reasons to Select Paving Stones Over Concrete |
Posted by: eehis445ss - 08-30-2021, 04:59 AM - Forum: Welcomes and Introductions
- No Replies
|
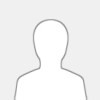 |
The walkway or drive that leads to your home should be both a personal statement and a reflection of your good taste. What’s more, the materials should stand up to the weather, look great for years at a time and not be a burden with costly, involved maintenance.
Concrete was the favored material for years because it met some of these criteria. But today paving stones are the clear choice. Here are five reasons why:
1. Stains and other imperfections can be easily hidden with pavers
If you splash a little oil on a concrete drive, the stain usually becomes an ugly, permanent blemish. Not so with pavers. These can be quickly flipped or replaced so you always have a surface that looks pristine.
2. Pavers come in a wide range of attractive colors and designs
Mixing and matching all the possible different combinations will give you a unique drive or patio every time. The different ways you can put paving stones together are limited only by your imagination.
3. A paver walkway is ready to go from the time it's installed
Unlike concrete, which can take three to five days before it’s ready for traffic, there’s no curing period with pavers — and no waiting.
4. It's easier to make adjustments with pavers
When a concrete base shifts, cracking can result in costly repairs that are visible even when they’ve been professionally done. It’s much easier to deal with a paver’s base that has moved. Just remove the stones over the affected area, level if needed, then replace the same pavers for a finish that looks as good as new.
5. Better drainage means a secure paver surface
Pavers are solid under your feet. Because of all the joints between paving stones, rain drains away much more easily than it does from flat concrete surfaces. This feature makes pavers much more slip-resistant.
Upgrading to pavers is the right choice for several reasons. This is a durable, worry-free material that will last for years.
Use Paving Stones to Transform Your Outdoor Space
If you find yourself gazing out into your backyard thinking of something you can do to spruce things up, have you considered using paving stones? Installing them is not difficult, and depending on the size of your project, it can be completed in as quickly as one weekend. The concept of using paving stones has been around as long as civilization --and for good reason. It is a simple, tried-and-true choice for builders who want attractive, durable results using simple tools and materials.
Few projects can be accomplished so quickly and last as long. Paving stones are versatile enough to suit jobs of any size or type. Regardless of your project: A simple walkway, a flower garden, a patio with barbeque, or even a driveway --paving stones are ideal. Below are some things to think about before starting your paving stone project:
Find inspiration
Do you already have an idea of what you want? If not, there are plenty of places to find inspiration. View landscaper’s websites and browse their galleries to see what is possible with paving stones. Of course there are always magazines as well. You may find new ideas that you weren’t aware of before you began your search.
Study your yard
Consider your needs and your space limitations. Can you fit your idea into the space you have? Take into consideration proximity to structure and trees. A small tree today may be a big problem in the future as the root system grows.
Types of stones
Are paving stones and stone pavers the same thing? Sort of. Paving stones (also referred to as pavers) are not necessarily made from naturally occurring stone. They are often cast from man-made materials like bricks. Some are cut from natural stone and therefore are called stone pavers. Besides a limitless number of colors, there are different types of pavers, such as brick, concrete, natural stone and even rubber. Most man-made pavers are also available in interlocking shapes.
Draw a picture
A piece of graph paper can be a great help. Draw out your plan, scaling each square as one foot (or other easily converted unit of measure). Color the bricks if you are planning to make a pattern with your stones. Using graph paper makes it easier to count how many stones of each color will be needed.
Unlike a deck, the maintenance for a stone patio is a snap. They are modular in nature, so it is also easy to move them around as your landscaping needs change. Also, have you ever stepped barefoot onto your deck after it’s been in the sun all day? Pavers are cooler on your feet. Finally, pavers won’t crack like concrete can. If planned and installed properly, you’ll be ready for the summer simply by sweeping your patio and bringing out your furniture!
How to design a fireplace with cultured stone
When searching for an easy and cost effective design solution for a fireplace, cultured stone or manufactured stone veneer should definitely be considered. There are a variety of patterns and colors to choose from, and a multitude of ways to enhance any interior space. Culture stones are a cost-effective way to add nature-inspired beauty to any indoor fireplace.
This ledgestone fireplace (left) was built in Parkland, FL. The fireplace was framed with drywall and had a wooden shelf with a large mirror in the center. The floor-to-ceiling fireplace with cultured stones is very interesting, visually.
The manufacturer’s recommendation is to install wire lath on top of the drywall with a scratch-coat of mortar; however, you should simplify this step and use backer boards instead. These provide the proper adhesion and save a considerable amount of labor. After the installation of the backer boards, apply bonding agent on the area getting stoned.
Cultured stones, also called manufactured stones, can be rustic or refined. If you wish to install cultured stones on your own I would advise that you lay out a selection of different stone sizes on the ground. This will make it easier to find the right size and achieve the best blend in color.
Always mix different sizes of stones. Also, alternate or stagger the joints create a pattern that is pleasing to your eyes. A good rule of thumb is to break up the vertical and horizontal joints as often as possible.
Even as Central Delhi begins the kerb stone makeover — paint them saffron and green — the decision, taken by the New Delhi Municipal Council, has come under severe criticism from several quarters, including the traffic police and an NDMC member herself.
Further, the use of regular paints, as opposed to the retro-reflective thermoplastic variety, is considered to violate road rules.
Kerb stones are placed on roads as markers of danger. They are usually painted in ‘black and white’ or ‘black and yellow’. The NDMC had touted the move as an “aesthetic initiative” which would “bring uniformity to the area”.
According to Indian Road Congress, the national body of technical highway engineers, “yellow, white and black are the standard colours used for markings”. The same is stated by the Unified Traffic and Transportation Infrastructure (Planning and Engineering) Centre and International Vienna Convention on Road Signs and Signals, of which India is a ratified member.
Granite Paving Stones Rise in Popularity
Granite paving stones are quickly becoming the “it” hardscape item of the year as more projects seek a product that’s cost effective, unique, and durable. Add those keys to a versatile product for both residential and commercial projects and it's no wonder they are becoming more popular.
Paving stones (commonly referred to as "pavers") are typically made from one of three materials: natural stone, brick, or cement. Each one of these provides a different look and feel to a specific project and have their own pros and cons.
4 Reasons Granite Paving Stones Are Trending
Compared to this time last year our sales of natural stone flagging and pavers are up more than 300%. The majority have been granite but a small percentage includes a schist and quartzite and it does not include bluestone. It’s exciting for us to see this growth and when we see a trend like this we look to focus on the “why”.
Sustainability: Natural stone products are natural and durable with minimal carbon footprint. The majority of our stone is from local quarries and our process involves breaking or cutting stone down to size so no chemicals are used in the product. Natural stone is considered to be a "green" building material.
Unique: We hear it on a regular basis, “I want something different”. No two pieces of natural stone are identical so when you lay down your granite pavers it’s going to be different than anything else out there. Even if your neighbor uses the same stone there will be variation.
Quality: We used the word durable in our first point and natural stone, especially from New England, continues to stand the test of time and elements. Granite paving stone is durable which is why you can work with “reclaimed” granite. It’s stone and it’s built to last.
Affordable & Available: Stone is heavy and for a long time was difficult to move or ship. Similar to the introduction of thin stone veneer, advancements in technology have made granite pavers more available, easier to transport, and help reduce the installation time, which saves money on the job.
It' s exciting to see the growing trend in natural and granite paving stones and we expect to see it continue to increase in demand for the years to come.
|
|
|
Desuperheater Application Best Practices |
Posted by: eehis445ss - 08-30-2021, 04:58 AM - Forum: Welcomes and Introductions
- No Replies
|
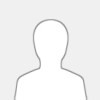 |
An ever-increasing need for steam at specific temperatures and pressures exists in many modern plants. Fortunately, significant improvements have been made to increase operational thermal efficiency and heat rates by the precise, coordinated control of the temperature, pressure and quality of this steam. But, much of the steam produced in power and process plants today is not at the required conditions for each application, so conditioning is required, often by a desuperheater system.
The sizing, selection, application, installation and maintenance of the proper desuperheating and steam-conditioning equipment, including control valves, is therefore critical to optimum performance. This article will discuss superheaters and associated control valves in detail, but first I will look at common applications and issues in affected industries.
Power Industry
Competing in the modern power market requires a heavy emphasis on the ability to utilize multiple operating strategies. Increased cyclical operation, daily start-stop and faster ramp rates are required to ensure full-load operation, particularly at daily peak hours, and to maximize profit and plant availability. Changes resulting from environmental regulations and economics also are combining to alter the face of power production.
At the same time, these changes are affecting the operation of existing power plants and the design of future plants. Advanced plant designs include requirements for increased operating temperatures and pressures along with stringent noise limitations in urban areas. Steam is used throughout power plants in many ways, from driving to turbines to feedwater heaters.
Hydrocarbon and Petrochemical Industries
Hydrocarbon and petrochemical industries rely on the efficient conversion of low cost feedstock to high profit products. Hydrocrackers, furnaces, distillation columns, reactors and other process units must be designed to meet a range of conditions to accommodate various modes of plant operation. Temperature is a critical factor that must be taken into consideration during the design of each process unit, and it must be controlled precisely to optimize each operation.
Temperature is controlled in many ways in these plants. The most common method is through the use of heat exchangers and process steam. Process steam must be conditioned to a point near saturation before it is transformed into a medium that is more efficient for heat transfer. The proper selection of equipment will ensure optimum plant availability, reliability and profitability.
Other process industries such as mining, pulp and paper, life sciences and food and beverage experience reliability issues caused by steam-conditioning challenges. These industries also use steam for motive force and heat transfer.
Desuperheater Basics
A schematic of a typical desuperheating system is shown in figure 1. A typical system consists of four main components:
Control valve.
Desuperheater.
Temperature transmitters.
Spray-water strainer.
When specifying a desuperheater, it is advisable to consult with the manufacturer because most desuperheater suppliers have multiple models from which to choose. Critical parameters (figure 2) include:
Spray-water temperature.
Spray-water pressure.
Initial steam superheat temperature.
Final steam superheat temperature.
Minimum steam velocity.
Maximum steam velocity.
Pipeline size.
Downstream straight-pipe length.
Steam-pipe liner.
Orientation.
While each components affects operation, a note on orientation is warranted. Orientation can affect the speed of vaporization. Horizontal installations are most common, but vertical flow-up installations perform slightly better because of the positive effect of gravity. Vertical flow-down pipes perform less efficiently because of the negative effect of gravity, which reduces residence time.
Details of the actual control of a desuperheater are beyond the scope of this article; however, suffice it to say that pressure, temperature and flow sensors feed data to a control system that adjusts the spray-water control valve to deal with changing conditions.
Control Valve Considerations
When a desuperheating system is purchased, often each component will be specified and purchased separately. In other words, the desuperheater will be purchased from one vendor, the control valve from another and so on. Unless the process plant has an extensive expertise in the design of superheating systems — not often the case — this approach is problematic due to the complexity of these systems.
The reasons are:
There is generally a turndown specification for the system that needs to be met. The control valve has a turndown ratio, the desuperheater has a turndown ratio and the combination of the two has a completely different turndown ratio. Therefore, sizing and selection are critical to ensuring system performance is met.
Different desuperheater designs will have different differential pressure (dP) requirements across the nozzles. The control valve differential pressure must be coordinated with the differential pressure across the desuperheater nozzles to ensure system performance is met.
If there is a high differential pressure across the control valve — when a high pressure source is used to spray water into a low pressure steam line, for instance — cavitation can occur in the valve. The proper anti-cavitation trim must be installed in the control valve to suppress cavitation. If not, it is possible to have a cavitating pressure drop across the desuperheater nozzle, with catastrophic damage resulting, and potentially sending eroded desuperheater components into downstream equipment.
A desuperheater nozzle has a specific flow coefficient (Cv). A control valve also has a range of flow coefficients based on its design. The flow coefficient for the valve and desuperheater must be matched so that overall system flow coefficient is optimized.
It presents results in the thermal energy recovery system (TERS) investigation, and the possibility of introducing them to production vehicles as subsystems. This prospective new technology should reduce dependence on fossil fuels. One of the TERS systems' research objectives is to create a sustainable, electrical power source, suitable for the energy to be stored and later used in the electrical vehicle driving mode (EV)1. It will also lower the impact on the environment by reducing fuel consumption through the application of automotive thermoelectric generators (ATEG) instead of classical alternators that convert mechanical energy to electrical.
Pressure reducer and desuperheater system (PRDS) is used for Steam Conditioning Services for reduction of pressure and temperature of steam. Suitably designed pressure reducing valve installed on superheated steam line, reduces steam pressure to desired operating pressure. The steam temperature is reduced close to saturation by injecting water into high velocity steam by controlled water flow through water control valve and often injected into the steam where steam velocity and turbulence are at their highest, which gives quick and efficient cooling. The purpose of this project is to optimize the Pressure reducing and desuperheating system to overcome the current losses such as valve leakage, gland leakage and header leakage.
|
|
|
Health Benefits of Peanuts |
Posted by: eehis445ss - 08-30-2021, 04:56 AM - Forum: Welcomes and Introductions
- No Replies
|
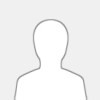 |
Surprisingly, peanuts are not actually in the nut family. They are classified as legumes along with foods like green peas, soybeans, and lentils. The peanut plant likely originated in South America in Brazil or Peru. Scientists have found 3,500-year-old pottery in the shape of peanuts, as well as decorated with peanuts, in South America.
Peanuts grow below ground as the fruit of the peanut plant. In the early 1800s, Americans started growing peanuts as a commercial crop. On average, Americans eat more than 6 pounds of peanuts per year. Today, 50% of the peanuts eaten in the United States are consumed in the form of peanut butter.
Health Benefits
Many people believe the peanut is not as nutritionally valuable as true nuts like almonds, walnuts, or cashews. But actually, raw peanuts have many of the same health benefits as the more expensive nuts and should not be overlooked as a nutritious food.
Heart Health
Much attention has been paid to walnuts and almonds as “heart-healthy” foods, given their high content of unsaturated fats. But research suggests that peanuts are every bit as good for heart health as more expensive nuts.
Peanuts help prevent heart disease by lowering cholesterol levels. They can also stop small blood clots from forming and reduce your risk of having a heart attack or stroke.
Weight Loss
Foods with a lot of protein can help you feel full with fewer calories. And among nuts, peanuts are second only to almonds when it comes to protein count. Studies have shown that people who include a moderate amount of peanuts in their diet will not gain weight from peanuts. In fact, peanuts could help them lose weight.
Longer Life Span
Eating roasted peanuts might help you live longer too. A large-scale study found that people who regularly ate any kind of nuts (including peanuts) were less likely to die of any cause than were people who rarely ate nuts.
Because the study was observational, it cannot prove that peanuts were exactly what caused the lower death rates, but they are definitely associated with them.
How to Save Seeds
1. Know what to grow
Start With Open-Pollinated Seeds
Open pollinated varieties, aka OPs, are like dog breeds; they will retain their distinct characteristics as long as they are mated with an individual of the same breed. This means, with a little care and planning, the seeds you produce will be true-to-type, keeping their distinct traits generation after generation as long as they do not cross-pollinate with other varieties of the same species.
Annual, Biennial, Perennial
Not all plants flower, set seed, and die in a single growing season. Those that do, like lettuce, tomatoes, and peppers, are called annuals. Biennials, such as carrots and onions, don’t flower until their second growing season, after they have gone through a cold period. Some long lived plants, like apple trees and asparagus, are perennial, surviving and flowering for many years.
Learn About Species
A species is a group of individuals that are able to reproduce together. In the garden, most crops are different species from one another, but not always. There are several species of squash and two distinct species of kale - meaning some varieties of these crops are not able to cross pollinate with each other. On the other hand, Cucumis melo, commonly categorized as a melon, also contains some varieties that are sold as cucumbers like ‘Armenian’ because fruits of the variety are unsweet and sometimes pickled.
2. Plan for seed saving
Start With Easy Crops
Some crops like peas, beans, lettuce, and tomatoes are great for beginning seed savers. These annual, self pollinating crops require little to no isolation, and only a few plants are needed to reliably produce seeds.
Grow Enough Plants
Some crops have a hard time producing seeds when too few plants are around. Others can reproduce with just a single plant. If the population size of a seed crop is too small, some genetic diversity may be lost and over many generations; in time this can result in a noticeable decrease in plant stature, overall vigor, germination, and yield.
Put A Little Space Between Varieties
In order to produce seeds that are true-to-type, a little garden intervention is needed to prevent unwanted cross pollination between different varieties of the same species. For some crops like lettuce and peas, all that is needed is a little extra space between varieties. For others, more advanced methods can be used, including larger isolation distances, pollination barriers, or hand pollination.
3. Collect Your Bounty
Know When Your Seeds Are Mature
For crops that produce wet fruits, the seeds are not always mature when the fruits are ready to eat. Eggplant, cucumber, and summer squash fruit are eaten when the fruits are immature and still edible, but before the seeds are actually mature. This means that seed savers need to leave a few fruits to fully mature in the garden when they want to save seeds. Dry fruited crops, like grains, lettuce, and beans, can be removed from the plant once seeds are dry and hard.
Know How To Harvest Seeds
Garden crops can be classified as either dry fruited or wet fruited. Collecting seeds from dry fruited crops, can be as simple as going out to the garden, handpicking a few mature seedpods, and bringing them into the house for further drying and cleaning. Fruits from wet fruited crops must be picked when their seeds are mature. The harvested fruits are either crushed or cut open, and the roasted seeds are extracted from the flesh and pulp before the seeds are dried.
Store Seeds
Raw seeds are happiest when they are stored in a cool, dark, and dry place. A dark closet in a cooler part of the house or a dry, cool basement are both good spaces to store seeds for a year or two. Once properly dried, seeds can also be sealed in airtight containers and stored in the refrigerator or freezer for several years. The seeds of some crops are naturally longer lived. Tomato seeds and beans can be left for many years in adequate storage conditions, while onion and carrot seeds are notoriously short lived. Don’t forget to label your seeds with the crop type, variety name, and any useful notes about your seed source, when you harvested the seeds, and how many plants you harvested from.
Snack foods
Snack foods are a very broad category with a wide range of processing steps. In general, snack foods have a more robust flavor profile and require a standard or reduced-flavor sage or rosemary antioxidant. If possible, the antioxidant should be added to the dough of the snack food. This could be predispersed in a water or oil phase or added directly to the blender. If adding without predispersion, an antioxidant should be chosen with a less concentrated form of antioxidant and used at a higher dosage rate (i.e., 0.2%). This will allow for even distribution throughout the dough and avoid “hot spots” that could occur when using a more concentrated product. If the snack food does not have a mixing step (i.e., potato chips), the antioxidant could be added to the frying oil or after preparation as a spray-on step. For snack foods, the easiest way to measure oxidation is use of GC to measure hexanal or another marker compound.
Is peanut butter good for you?
Peanut butter is a firm favorite among adults and children alike. Although tasty, many people wonder about the health benefits of peanut butter.
Peanuts and peanut butter contain nutrients that may boost a person’s heart health and improve blood sugar levels.
Depending on how people use peanut butter in their diet, it can help them lose weight, or put on pounds during weight training or bodybuilding.
However, peanut butter is high in calories and fat, so people should enjoy it in moderation.
In this article, we look at the benefits of eating peanut butter and explain the risks associated with consuming it.
Peanut butter provides a good amount of protein, along with essential vitamins and minerals, such as magnesium, potassium, and zinc.
Most notably, each 2-tablespoon (tbsp)Trusted Source serving of smooth peanut butter provides the following nutrients, minerals, and vitamins:
Protein. Peanut butter contains 7.02 grams (g) of protein per 2-tbsp serving. This counts toward the
recommended dietary allowances (RDA)Trusted Source
for women of 46 g and 56 g for men, which varies by age and activity level.
Magnesium. With 57 milligrams (mg) of magnesium, each serving helps towards the
RDATrusted Source
of 400–420 mg in men and 310–320 in women. Magnesium is essential for health, playing a role in over 300 chemical processes in the body.
Phosphorous. Each serving contains 107 mg of phosphorus, which is about 15.3 percent of the RDA of 700 mg for adults. Phosphorus helps the body to build healthy cells and bones and helps cells to produce energy.
Zinc. A serving of peanut butter provides 0.85 mg of zinc. This is 7.7 percent of the
recommendedTrusted Source
daily intake of 11 mg for men, and 10.6 percent of the RDA of 8 mg for women. Zinc is necessary for immunity, protein synthesis, and DNA formation.
Niacin. Peanut butter contains 4.21 mg of niacin per serving, which makes a useful contribution towards a person’s recommended intake of 14 to 16 mg. Niacin benefits digestion and nerve function and helps produce energy.
Vitamin B-6. With 0.17 g of vitamin B-6 per serving, peanut butter provides almost 14 percent of an adult’s
RDA of 1.3 mgTrusted Source
. Vitamin B-6 plays a role in over 100 enzyme reactions in the body and may be necessary for heart and immune system health.
However, there are also nutritional disadvantages if a person eats more than the recommended amount of peanut butter.
Peanut butter is high in calories, saturated fats, and sodium.
Each serving contains 3.05 g of saturated fats, which is 23.5 percent of the American Heart Association’s maximum recommended daily intake of saturated fat for those consuming 2,000 calories a day. People should aim for less than 13 g of saturated fat per day.
It also contains 152 mg of sodium, which is 10.1 percent of an adult’s ideal daily upper intake of sodium of 1,500 mg.
|
|
|
Environmentally Friendly Packaging & the Impact on Customer Satisfaction |
Posted by: eehis445ss - 08-30-2021, 04:55 AM - Forum: Welcomes and Introductions
- No Replies
|
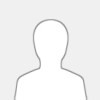 |
In recent years, almost every business has aimed to become as environmentally friendly as possible, whether that be by using environmentally friendly products or just simply turning equipment off when not in use. In the packaging industry, the growing trend of becoming more environmentally friendly has been taken off, and it would seem that even consumers are looking to embrace the trend. Businesses are now starting to choose environmentally friendly packaging over that of non eco-friendly packaging, and consumers are becoming more and more influenced by this choice.
There are a number of ways to make your business more environmentally friendly, with the choice in packaging being the common focus for all businesses. Choosing packaging made from recycled, renewable ingredients is a simple way to reduce negative environmental impact. For packaging to be considered eco-friendly, it must have a minimal impact on the environment during its life cycle (from the creation of the packaging to the recycling of the packaging). There are a number of advantages to using eco-friendly packaging:
Decreases your Carbon Footprint: The obvious benefit to eco-friendly packaging is reducing your carbon footprint. Being made from bio-degradable, recycled materials means there is less waste of natural resources.
Disposal: Another benefit of eco-friendly packaging is the ease of disposal, often costing a considerable amount to move and dispose of supplies. Eco-friendly packaging on the other hand is compostable, reusable, and recyclable, meaning that after its original use, the packaging can be buried (compostable), recycled (Broken down and made into more packaging) or re-used (you can either re-use it yourself or recycle it to be used again).
Brand Image: One of the biggest benefits of using eco-friendly packaging is how it reflects on your business. When consumers learn you’re using eco-friendly packaging, it reinforces the idea that your business is a responsible company, willing to look out for the environment. Better brand image leads to better sales and better profits, all because you looked out for the environment.
Cost Benefits: The best news for your business is that eco-friendly packaging is actually cost-effective. With companies reducing the materials used in their packaging, manufacturing the packaging ends up costing less. With fewer materials, packaging weighs less, saving on transportation costs when compared to before.
However, the main question is, do consumers really care about eco-packaging? Well, fortunately, it appears they do. According to an article from sustainablebrands.com, “more than three-quarters of consumers claim that eco-friendly packaging has an influence on the beverage brand they purchase." Consumers are even willing to purchase products that might cost a little more if the packaging is eco-friendly and are sometimes even willing to avoid a specific brand for their lack of eco-friendly packaging. All of this information has lead to a large majority of businesses taking the environment into account as a part of their business strategy, looking to focus on using eco-friendly materials -- with renewable materials becoming a key focus from businesses.
While the stats do look promising, it’s worth noting that “environmental factors were a bigger influence for more developing countries like Brazil, Turkey and India, than in already developed areas like the UK, USA or Japan.” Developing countries saw around 60% of all surveyed saying that they actively look out for environmental information when thinking about purchases, compared to only 25% from the more developed countries. In another article by campaignlive.co.uk, it is said that in an online survey of 1,000 people, conducted by Toluna, “Almost two-fifths of respondents said they would be more likely to buy a product if it had less packaging than a rival’s. More than one-third said they thought some products have too much packaging, and 32% said they like products to have a lot of packaging, only if they are fragile.” It is shown that consumers link the amount of packaging on a product with value, with over-packaged products causing consumers to believe they will have to pay more for it, as well as the obvious impacts on the environment compared to well packaged eco-friendly packaging.
What is PLA packaging?
Firstly, PLA stands for Polylactic Acid. It’s a new type of high molecular polymer material and is commonly known as corn plastic. PLA is made from renewable resources, is biodegradable and has characteristics similar to Polypropylene (PP), Polyethylene (PE) and Polystyrene (PS). There are many uses for PLA and the most recognised include the following:
Bottles
Biodegradable medical devices (screws, pins, rods, plates etc.)
3D printing
Packaging
How is PLA packaging made?
PLA is a polyester made with two possible monomers or building blocks: lactic acid, and lactide. Lactic acid is produced by fermentation under controlled conditions of a carbohydrate source, such as corn starch or sugarcane, making the process sustainable and renewable.
PLA can be produced by the direct condensation of lactic acid. However, this process usually results in a low-density form of PLA (not ideal). In order to produce high-density PLA, the lactic acid must be heated in the presence of an acid catalyst to form cyclic lactide. This is known as ring-opening polymerisation.
How can PLA packaging be disposed?
When it comes to renewable and biodegradable packaging, the PLA packaging play a key part in the sustainability of the given product.
For PLA, there are two main methods of disposing:
1. Compost degradation – Within the first 180 days of a PLA product’s life, it’s 100% biodegradable and can be composted to ensure sustainability. PLA will decompose into digestible polymer fragments in about 7 days at 60°C in a moist environment - a typical composting condition for a large composting operation.
2. Renewable energy recovery (incineration) – Because PLA doesn’t contain any chlorine atoms, so can be safely incinerated under controlled conditions without producing any dioxins (highly toxic chemicals). Although, as biodegradability is the primary motive for PLA and other bioplastics, incineration should be considered after compost degradation as the end-of-life option.
What is PCR Packaging?
PCR means Post-Consumer Recycled material or Post Consumer Resin, and generally refers to plastics such as PET, PP and HDPE which are widely recycled and then reprocessed into a resin that is used to make new packaging. In simple terms, it is packaging that is being given a second life.
Why use PCR in your packaging?
Principally, because it helps the environment. Virgin plastics are generally processed from fossil fuels so reprocessing them has massive benefits to the environment. But that’s not the only reason to use them:
The more people that use PCR resin, the greater the demand will be. This in turn drives more recycling of used plastic packaging, helping the commercial case to recycle and means that less plastic ends up in landfill, rivers or then becomes yet more plastic in the ocean. So by using PCR, you help the “snowball effect” of recycling.
Many countries around the world are bringing in legislation to force the use of PCR and being a step ahead will help you to be compliant with regulations.
Using PCR adds a responsible element to your brand and shows your marketplace that you care.
Many consumers will be prepared to pay more for products packaged in PCR packaging, making your product more valuable and potentially more profitable.
Sugarcane Packaging Vs Paper Packaging
If you’d like to learn more about our sugarcane packaging tableware range, or the differences between the two types of materials and how they’re used, please reach out to us today.
In our latest blog we explore the differences between sugarcane packaging and paper packaging products, so you can make an informed decision based on your business needs and values.
While products made from paper and the sugarcane by-product bagasse, look and feel similar, their main differences lie in the way the materials are grown and produced.
Not only is sugarcane food packaging a much better alternative than plastic, there’s also quite a big difference in volume of raw product required between paper vs sugarcane food packaging.
We’ll start our article by delving into sugarcane or bagasse containers, as that’s what our compostable tableware range is made from.
How do spray bottles pump fluid?
Spray bottles are an extremely useful type of machine and an excellent demonstration of basic plumbing principles. A spray-bottle head is made up of only a few parts. It has a trigger lever, which activates a small pump. This pump is attached to a plastic tube that draws cleaning fluid from the bottom of the reservoir. The pump forces this liquid down a narrow barrel and out a small hole at the gun's muzzle. The hole, or nozzle, serves to focus the flowing liquid so that it forms a concentrated stream.
The only complex element in this design is the fluid pump, and it's about as simple as they come. The main moving element is a piston, housed inside a cylinder. Inside the cylinder, there is a small spring. To operate the pump, you pull the trigger back, pushing the piston into the cylinder. The moving piston compresses the spring, so when you release the trigger, the piston is pushed back out of the cylinder. These two strokes of the piston, into the cylinder and out again, constitute the entire pump cycle.
The downstroke, the piston pushing in, shrinks the area of the cylinder, forcing fluid out of the pump. The upstroke, the spring pushing the piston back out, expands the cylinder area, sucking fluid into the pump. In a spray bottle, you need to suck cleaning fluid in from the reservoir below and force it out through the barrel above. In order to get all of the fluid moving through the barrel, the pump must only force the fluid up -- it cannot force the fluid back into the reservoir. In other words, the fluid must move through the pump in only one direction.
The device that makes this possible is called a one-way valve. A spray bottle has two one-way valves in the pumping system: one between the pump and the reservoir and one between the pump and the nozzle. Typically, the valve between the pump and the reservoir consists of a tiny rubber ball that rests neatly inside a small seal. The sides of the seal are angled so that the ball won't fall through. Depending on the design, either gravity or a small spring holds this ball against the seal so that the water passageway is blocked off when you are not pumping. When the piston moves out (when you release the trigger), the expanding area of the cylinder sucks on the fluid below, pulling the ball up out of the seal. Since the ball is lifted up, fluid is free to flow from the reservoir. But when you squeeze the trigger, the outward force of the moving fluid pushes the ball into the seal, blocking off the passageway to the reservoir. Consequently, the pressurized fluid is pushed only into the barrel.
In a spray mechanism, the one-way valve between the pump and the nozzle is a sort of cup, which fits over the end of the barrel. On the upstroke, the inward pressure from the pump pulls the cup against the barrel, so air can't flow in through the nozzle. On the downstroke, the fluid pushing out lifts the cup off the barrel slightly and flows on through the nozzle. Without this second one-way valve, the pump system wouldn't be able to draw fluid up from the reservoir because there would be no suction (no drop in air pressure). The upstroke wouldn't lower the air pressure in the pump; it would only draw in more air to maintain that pressure.
5 Benefits of Using Tubes Packaging for Cosmetic Containers
In the cosmetics industry, we can see a great increase in demand for different types of cosmetic products, such as hair removal, anti-aging, and sunscreen products. The interesting thing is that both men and women are the buyers of these products. These products are sold in attract containers that protect the integrity of the material inside. Let's read about some of the benefits of tubes as cosmetic containers.
For cosmetic containers, plastic tubes are becoming the ideal choice. The reason is that they are attractive and versatile. That's the reason they can satisfy the needs of this fast-growing industry. Given below are some reasons these products are a great choice. Read on.
Affordable
Today, consumers are quite conscious as far as spending money is concerned. They try their level best to save as much money as possible. If you want to reduce your packaging costs, you can try the squeeze tubes.
Fancy cosmetic containers, such as glass are quite expensive. Therefore, they add to the price of the product. On the other hand, plastic tubes use the best technology available. Therefore, they are the most affordable option you can try. The cost is low but the container quality is great.
Versatile
Unlike plastic or glass, plastic tubes offer more versatility. The thing is that they are designed to carry a lot of a substance, such as a sunscreen or shampoo. Apart from this, the openings are adjustable to accommodate the product viscosity. This allows you to store different types of substances, such as cosmetic foundations, astringent toners, and creams, just to name a few. So, versatility is another primary benefit of using these tube containers.
Eco-friendly
Heavy jars of plastic and glass containers are quite eco-friendly. As a matter of fact, small containers don't waste plastic as they are recyclable. Actually, the makers of these products make use of green processes in order to have a minimal effect on the environment. Therefore, if you are looking for an eco-friendly option, we suggest that you try out these containers.
Transportable
Unlike glass containers, plastic tubes are more portable. The reason is that they cover less space, easier to transport and are less fragile. They are much easier to ship as they are more stable. Plus, they can make sure that the quality of the product is always high. You can carry multiple tubes in your own pocket.
Easy to use
Unlike jars that need to be unscrewed before each use, tubes are much easier and convenient. All you need to do is pop the lid, press the tube and the substance will come out. Therefore, they are much easier to handle than glass containers, which makes them an ideal choice for most users.
Long story short, these are the benefits of tubes as cosmetic containers. If you are a manufacturer of a cosmetic product, we suggest that you consider using cosmetic tubes. They can help you bring the costs down and offer your products at a much lower price. Hope this helps.
|
|
|
The Ultimate Guide to Waterproof Dry Bags |
Posted by: eehis445ss - 08-30-2021, 04:54 AM - Forum: Welcomes and Introductions
- No Replies
|
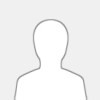 |
Dry bags are a must-have piece of gear for any outdoor adventurer. While they are simple, easy to use, you’ll find there are many different styles, sizes, materials, and features that go into them. I hope to guide you through the decision-making process with this ultimate guide to waterproof dry bags. Let’s get started!
If you’re just looking for our best dry bag recommendation, check out Gold Coast gear for all sizes and colors.
What’s a Waterproof Dry Bag?
As the name implies, their primary job is to keep any piece of outdoor gear dry. The bag is a flexible container, typically with a roll-top closure. Roll-top Dry Bags provide a Watertight enclosure by the way they are secured. Instead of a Zip-top or zipper type of closing mechanism, the bag is secured by rolling down or dog-earing the top at least three times, them clipping the buckles together.
We will go over other ways of securing a dry bag, but the most reliable ones are closed with a roll-top seal. The reason Mountaineers prefer this over a zipper and zip-top closing style is that a rolling top is virtually indestructible.
Two pieces of fabric being pressed together won’t wear out like a waterproof zipper. It will perform the same in a cold environment (unlike a zipper) and can easily be closed with gloves on.
Who Uses Dry Bags & What Are They For
Waterproof dry bags are one of the most common items for many outdoor activities. It’s easy to see why, over the years, many people have adopted them.
Backpackers: Wanting to separate valuable gear keeping it clean and dry. Have multiple smaller dry bags of different colors help keep them organized.
Water Sports: It’s ubiquitous to find a large waterproof dry bag on a Kayak or Canoe. Waterproof backpacks are used for paddleboarding or SUP for short. Large dry bags are also routinely used for rafting as well.
Camping: Dry bags are used to keep wet gear separate from dry clothes. Small dry bags can hold electronics, keeping them safe from water and dust.
Alternative Uses: Using them as a pillow, gathering water, a bear bag, and a boat anchor.
These are just some of the uses for people that need to protect their equipment.
Different Closing Dry Bag Styles
Closing roll-top dry bags is recommended, but let’s look at other ways of closing them. Let’s compare the zip-top and zipper closing bags to the roll-top.
Zip-Top or Ziploc Closing Dry Bag
This type of bag is excellent for smaller, lighter items that fit nicely in the small pockets of a backpack. I keep a few Ziploc bags whenever I go hiking to keep my toiletries clean. The problem with this closing mechanism is when you have larger, more substantial items.
With heavier gear rolling around in a Ziploc bag, the top can easily blow out. If you close a Ziploc bag with air in it, a small amount of pressure will pop the bag right open. A roll-top dry bag won’t do this. If enough force is applied to a roll-top style bag, the seams will blow out before the top will.
Cold weather will make the zip-top stiff and hard to close. While they will be fine in most temperatures the cold weather will affect the performance.
Freegrace sells a dry bag that has a zip-top combined with a roll-top. While this isn’t necessary or really adds any extra protection, they claim it’s for added security. They also note that in cold weather, the zip-top won’t perform well, and oil needs to be applied before closing the bag.
Waterproof Zipper Dry Bags
A true waterproof zipper will not leak, but the problem is many so-called “Waterproof Zippers” are merely water-resistant. This kind of zipper will let water leak in if they are exposed in the rain or dropped in water long enough. Bag manufacturers do this to save on costs because true waterproof zippers are expensive.
Another downside is that waterproof zippers are stiff, so they don’t slide easily like the normal zippers we’re used to using. This can be a real pain in cold weather as the zippers will be even stiffer. Lubricating the zipper can help with this stiffness.
As with zip-top bags, zippers can blow out when overstuffed. If this happens while you’re out on the trail, you could be stuck with a useless bag for days.
The last downside is that zipper bags are difficult to close with gloves on. In cold weather, the zipper will stiffen up, making it even hard to close with thick winter gloves.
How to Choose The Best Dry Bag
Before we look at different sizes of dry bags, we need to choose a material first. Dry bags generally come in two different categories, thick heavyweight or thin ultra-lightweight material.
Thick Dry Bags
Some dry bags are heavy, but they’re built to take a beating. Take a look at a dry bag made from 500D PCV Tarpaulin for durability. It’s tough, but at the downside of being very heavy and inflexible. These kinds of dry bags are usually recommended as “best value” because they last for years in harsh conditions.
Benefits Of Having A Waterproof Backpack
One of the most infuriating things about going camping, backpacking, or hiking during the rainy months of the year is reaching your destination and finding all your gear and equipment soaked through. And it doesn’t even have to be raining for you to experience this. Sometimes, crossing a river or a creek or walking under a waterfall is more than enough for this to happen. That is why many knowledgeable and experienced camper or backpacker knows how important it is to have a reliable waterproof backpacking or hiking backpack.
A waterproof backpacking backpack or camping backpack comes with many benefits that you wouldn’t get from a typical everyday backpack. However, some of the latest waterproof backpacks imbued with the best waterproofing technology can be quite expensive which is why some people are on the fence when it comes to purchasing one. If you are looking for a reason or two as to why you should invest in one, we have outlined the best ones below for you. But before we dive into our top reasons why you need a waterproof backpack, let’s go over a brief description of what it actually is and how it is different from another popular type of outdoor backpack, the water-resistant backpack.
The Best Waterproof Duffel Bags: Duffel Dry Bags for Travel & Outdoors
If you've ever been concerned about your belongings getting wet while traveling or spending time outdoors---a waterproof duffel bag is your secret weapon. These durable and fully waterproof bags are ideal for situations when you just need the ultimate protection.
A versatile travel backpack is great for everyday travel, but when you need to keep your gear safe from even the most extreme conditions, dry bag type duffels are a much better option.
When traveling, especially in foreign climates, you just don't know what conditions you'll find yourself in---and who knows what happens to your bag in transit. I've learned to be better prepared and safe, than sorry.
I've taken 10+ hour overnight bus journeys only to arrive at my destination finding that my luggage was moved from the secure and dry under bus storage to the top roof rack! Thankfully on this trip I decided chose decided to take my The North Face Base Camp Duffel, which keep all my belongings dry---even through a wet and rainy night.
Your average travel backpack and luggage are great for the casual traveler, but if you are one who seeks adventure and outdoors, they often just don't cut it.
Most travel bags will do a decent job keeping your gear dry when exposed to light rain, but a fully waterproof bag will ensure your stuff stays dry---no matter what.
Cooler Bag Technology
The original ice chest was made out of galvanized metal. Later versions were made from hard plastic. They were double-walled with a layer of dense Styrofoam in between which helped to keep the contents cool. Today's ice chests are still made this same basic way.
Styrofoam was a suitable insulator, but it had to be relatively thick to maintain internal temperatures for an extended period of time. And, of course, Styrofoam is easily dented and broken, so it had to be encapsulated in a hard shell to prevent breakage. As such, ice chests have to be rigid.
By contrast, cooler bags are not rigid. Instead, they are usually made from heavy but flexible fabrics, like polyester, on the outside. The inside is lined with heavy duty foil. In between the outer and inner layers are layers of materials like flexible foam, which are thin but dense and have the ability to maintain internal temperatures for several hours. This technology allows for a bag that is flexible and thin and, therefore, easy and convenient to transport. Also, unlike their rigid predecessors, cooler bag can be manufactured in a wider variety of sizes and shapes.
How to get abandoned, lost and discarded ‘ghost’ fishing gear out of the ocean
Fishing gear and plastic marine debris is a growing global issue. Abandoned, lost or discarded fishing gear — often called ghost gear — can contribute up to 76 per cent of all marine debris found during beach cleanups.
Estimates of the weight of abandoned fish gear vary widely by region and by type of gear used. One study retrieved 14 tonnes from the northwestern Hawaiian Islands. In one fishing region in Nova Scotia, an estimated 22 tonnes of fishing gear remains at sea. Overall, an estimated 640,000 tonnes of ghost gear is lost globally in the oceans every year.
This derelict fishing gear continues to catch fish, including commercially valuable and threatened species, and other marine fauna. For example, ghost gear, especially nets, are responsible for entangling seals and sea turtles. One abandoned fishing net in Puget Sound in the United States is expected to catch two invertebrates per day, one fish every three days and one seabird every five days.
It also costs fishers. Ghost gear reduces catch rates and cuts into profits, it is expensive to replace and it can be dangerous — getting tangled in propellers and snarling anchors.
What Makes a Good Fishing Cooler?
Fishing cooler bag generally spend a lot of time in the sun and around the water, so it’s important that these coolers are both rust resistant and UV protected. Other benefits of a true fishing cooler will be the added insulation as well as odor and stain resistant materials. A good fishing cooler will also need to come equipped with a good seal to protect ice retention. There are many great fishing coolers to choose from, but have you ever thought about an insulated fish bag? These insulated bags can be a great alternative depending on how you plan to use your fishing cooler.
What is a Fishing Bucket?
Fishing bucket is frequently used by professional fisherman for the simple fact that they have been proven that the original weight of a fish can be maintained by placing it in an insulated bag with ice. Good insulated fish bags are lightweight, weighing much less than even small coolers. UV resistant, they are designed to hold ice all day; keeping your newly caught fish fresh for hours. These insulated fish bags should be leak proof and should be constructed in a way which makes them easy to clean. So, which is the best choice for your next fishing trip? Let’s take a look at the pros and cons of both.
|
|
|
How to design PET preform mould |
Posted by: eehis445ss - 08-30-2021, 04:53 AM - Forum: Welcomes and Introductions
- No Replies
|
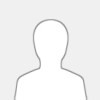 |
PET preform mould for plastics materials (PET) have been made in some manner for centuries. Some of these PET preform moulds were fine works of art, as, for example, the moulds used by craftsmen in glass. The coming of the modern plastics moulding materials brought about great advancement in this old art, and transformed it into a science. Mass production PET preform moulding machinery has been developed, and new PET preform mould steels and alloys have been introduced to withstand severe service. Accuracy is a requirement in modern manufacturing, and PET preform moulded plastics are produced by steadily mounting standards of precision, which have necessitated new machine tool applications and methods.
A PET preform mould may be defined as a form for shaping a plastic material ”PET” into a finished product-here is PET preform. PET preform moulds are made of plain carbon steel or of alloy steels, and are hardened to provide compressive strength and hard surfaces to take and maintain a high polish under severe wearing conditions. PET preform moulding materials require heat and usually pressure to achieve the plasticity necessary for them to flow into the shape of the mould cavity. Pressure is required to force the material into the cavity and to hold it to shape until it is set, and to give the casting or finished product the required strength. A PET preform mould must be polished to give the casting a good finish,and to allow it to be ejected easily.
A mould for the general run of PET parts is divided into two halves which meet at the parting line. These halves are mounted on backing plates which are drilled to allow passage of steam or cooling water, and which carry the guide pins which aligning the halves of the PET preform mould. The mould halves and backing plates assembled constitute the PET preform mould proper.
The fundamentals of mould design are discussed and applied to representative type PET preform moulds. The important compression PET preform mould types are classified for study; transfer and jet moulding are described; injection PET preform moulds are presented both as units and broken down into elements of design and construction. Methods of moulding screw threads are discussed; methods of PET preform mould sinking and applications of mould base standards are shown. mould building methods and equipment, moulded parts finishing, product design considerations and estimating methods are included as background information. A summary of practical points in PET preform mould design and construction, shrinkage charts and a nomenclature section provide a basic fund of data required by the serious learner.
Since many factors enter into the design of plastics PET preform moulds, and into the design of products to be pet bottle mould, it is well for product designers, tool designers, and tool makers to have a common understanding of plastics PET preform moulds and PET preform moulding in order to cooperate to the fullest extent in making possible PET preform moulded products of high standards of quality and economy.
Requirements for PET preform mould Designing
To design plastics preform bottle mould, a plastics engineer should have an intimate knowledge of a proper design procedure which is based upon a knowledge of the characteristics of materials; of the technique of PET preform mould building; of the economics of each production schedule; of the tooling cost both to purchaser and to the PET preform mould manufacturers; of PET preform moulding equipment operation; of the special mould steels and alloys; and of the moulding and finishing facilities of his own plant.
The design of plastics PET preform moulds includes, besides the design of the mould proper, the provision for mounting the mould in a press; the provision of means to eject the finished PET bottle mould casting; and a provision for temperature control. There are also finishing tools to be designed, such as drilling jigs, buffing attachments, holding fixtures, cooling fixtures, gages, and other devices for obtaining accurate and economical production.
Two General Types of Plastic moulding in General Use
There are two general types of moulding in general use compression and injection. A compression Mould is one which is open when the material is introduced, and which forms the material by heat and by the pressure of closing. An injection Mould is one which is closed before the material is introduced from an external heating, or plasticizing cylinder. Compression Moulds are usually operated in hydraulic presses; while injection Moulding presses have been developed for either mechanical or hydraulic operation.
The Mould designer does not always have complete information on the product his Mould must produce. Usually a sketch or drawing is supplied, and sometimes a model. The model is useful since a Moulding or finishing feature may appear in three dimensions which would escape notice on a drawing. A model, while desirable, is not absolutely necessary, and most Moulds are built without their use. As the die or the die casting designer, the Mould designer can very frequently find details which may be altered slightly to allow more convenient and economical Moulding. The Mould designer can render a real service by making such suggestions for approval before completing his design.
Single Stage Blow Molding Machine
While PET bottle development was proceeding in the US, a large manufacturer of injection molding machines in Japan, was leading a project to develop a machine to make biaxially oriented PP (polypropylene) containers. They recognized that the prototype machine could be used to produce the new PET bottles and, in December 1975, the One-stage ASB-150 injection stretch blow moulding machine for making the new biaxial oriented PET bottles was unveiled. All one-stage injection stretch blow moulding machines derived from this original Stretch Blow design are referred to as classic one-stage machines, as the concept has long since been extended into other PET developments. The classic one-stage machines design is extremely versatile in that the same basic machine design can be used to make a wide variety of bottles and jars in all shapes and sizes.
Two Stage Blow Molding Machine
In the early developments, performs were made by continuously extruding a PET tube. To make these prefroms, a perform manufacturing machine that took a continuously extruded PET tube, heated and closed one end, and then heated the other and formed a thread finish by blow moulding. This process had a faster output rate, at 12000 preforms per hour, than the early injection moulding routes of 8 and 16 cavity moulds. Being extruded, the performs could be multilayered with barrier materials. The system was overtaken by injection moulded performs as the cavitation increased to 32 and beyond. The quality of the injection moulded (IM) neck, adding for example vent slots, made the IM finish preferable. Moreover, IM technology is available from more than one company, giving customers greater technical and commercial choice. Two-stage technology machines with six blow moulds operating at around 4000 bottles per hour. Subsequent mould and cooling development increased the output to 6000 bottles per hour.
Two stage PET processing includes:
Making performs by Injection Molding
Blowing bottles by Stretch Blow Molding
Because it is more flexible than one step processing, it is widely accepted in Plastic packaging market. You may choose to make preforms only or blow bottles only if you want to do one of them specially.
Integrated Two Stage Blow Molding Machine
In Integrated Two Stage approach the performs were made by more conventional injection moulding routes (with the number of cavities optimized to match the required output) and then, while still hot, were carried to a separate blowing machine with the optimized number of blow moulds to suit the required output. This was the first ‘integrated ‘approach to PET bottle making. Equipment developers took the ‘single-stage’ approach. Here the equipment had the same number of injection cavities as PET blowing mould. This was a more compact approach and proved ideal for small batch output with excellent glossy surfaces.
Blow molding is a type of plastic forming process for creating hollow plastic products made from thermoplastic materials. The process involves heating and inflating a plastic tube known as a parison or preform. The parison is placed between two dies that contain the desired shape of the product. Air is then supplied to expand the tube causing the walls to become thinner and conform to the shape of the mold. Once the blowing process is complete, the product is then cooled, ejected, trimmed, and prepared for the secondary processes.Bottling and packaging are the main applications of blow molding which comprise about 49% of the global blow molding market share. This is followed by building and construction, consumer products, and transportation industries.
The global market share of blow molding was estimated at around $78 billion in 2019 and is expected to grow annually by 2.8% from 2020 to 2027. Typical raw materials used are polyethylene (PE), polyethylene terephthalate (PET), and polypropylene (PP).Plastic blow molding originated from the ancient process of glass blowing. Both glass and plastic in their molten state can be formed easily by introducing small amounts of air inside the molten material. The first injection molding process for glass, known as free-blowing, was created around the 1st century BC. Glass mold-blowing was later developed as an alternative process that came about around the 1st century AD.The first blow molding material used other than glass was natural rubber. The process was patented by Samuel Armstrong in the 1850s. The next major advancement came around the 1930s with the development of the first blow molding machine by Plax Corporation. The process uses cellulose acetate as the raw material. Come 1939, low-density polyethylene (LDPE) was introduced by Imperial Chemical Industries from England. LDPE is more suitable for blow molding which then paved the way for further process development. By the 1950s, the commercialization of blow molding was completed, and the industry grew exponentially.
This chapter discusses the general blow molding process. Blow molding is a fairly straightforward process that includes melting, homogenizing, extruding, molding (blowing), cooling, and ejection. Different manufacturing plants can employ additional processes such as additional cooling or heating cycles and additives and colorants compounding. These additional processes depend on the design and intended application of the final product.
Plastic Resin Feeding or Charging: The first step in the blow molding process is plastic feeding. This is done by conveying the plastic pellets into the extruder hopper. Vacuum pumps draw pellets from big bags or bulk containers and transfer them into the raw material silos or hoppers. A rotary feeder at the bottom of the silo controls the rate of feeding into the plastifier or extruder. Compressed air is then used to convey the stored pellets to the extruder hopper. In other systems, plastic pellets from big bags or bins can be vacuum conveyed directly to the extruder hopper without the need for a separate conveying air system.
Plasticizing or Melting: As the plastic resin enters and goes through the extrusion machine, it is melted by continuous kneading and heating. Electric heating elements or heating bands are wrapped around the extruder barrel to provide heat for melting the polymer. The extruder screw has different sections that serve a specific purpose. These are feeding, compressing, and metering. The extruder screw is designed to provide sufficient shearing and compression to homogenize and extrude the plastic.
Parison Extrusion or Preform Injection: This process is the preparation of the parison or preform to be inflated. This is done by extruding the plastic through free extrusion or injection into a preform mold. The different processes in producing the preform are discussed in detail.
Sealing or Clamping: Sealing or clamping involves a split die that captures the preform. The ends of the parison (extrusion blow molding) are sealed except for one hole, typically the container opening, where the compressed air will be injected.
Inflation or Blow Molding: This step is where the plastic takes its form. Compressed air is introduced inside the preform. This inflates the preform until it is molded according to the profile of the die.
Cooling and Ejecting: The next step is the cooling process. Typically, as the plastic touches the die, it cools at a predefined rate which stabilizes the dimensions of the product. After cooling, the mold opens and ejects the product.
Trimming: Flashing is generally evident in extrusion blow molding. Most blow molding machines have auto deflashing features as the dies clamp the preform. But in some instances, flash is present at the top and bottom parts of the product, especially at the opening where compressed air is injected. This excess material is trimmed by a rotating knife. To minimize wastage, some systems collect the excess materials, grind them, and feed them back to the extrusion machine.
Leak Test: This is the typical quality control method used in manufacturing bottles or packaging materials. In this step, either vacuum or compression is generated inside the container. The machine will then check if air enters or escapes the container by monitoring the pressure. If a leak is sensed from the container, it is rejected and fed back into the system.
|
|
|
|