Welcome, Guest |
You have to register before you can post on our site.
|
Online Users |
There are currently 245 online users. » 0 Member(s) | 244 Guest(s) Bing
|
Latest Threads |
Advanced microneedling
Forum: Off Topic
Last Post: axied12
05-28-2025, 01:25 PM
» Replies: 0
» Views: 149
|
Caviar and cheese
Forum: Off Topic
Last Post: axied12
05-28-2025, 12:38 PM
» Replies: 0
» Views: 139
|
Top-rated countertop comp...
Forum: Off Topic
Last Post: axied12
05-04-2025, 06:42 AM
» Replies: 0
» Views: 292
|
Ryanair letenky levně do ...
Forum: Off Topic
Last Post: axied12
02-11-2025, 01:37 PM
» Replies: 0
» Views: 686
|
Trusted essay writing ser...
Forum: Off Topic
Last Post: axied12
01-30-2025, 08:16 AM
» Replies: 0
» Views: 618
|
Bootverkopers - actieve j...
Forum: Off Topic
Last Post: axied12
12-07-2024, 11:07 AM
» Replies: 0
» Views: 746
|
Services for individuals ...
Forum: Off Topic
Last Post: axied12
12-02-2024, 03:31 PM
» Replies: 0
» Views: 705
|
Used excavators
Forum: Off Topic
Last Post: axied12
11-13-2024, 09:22 AM
» Replies: 0
» Views: 687
|
Buy Higo Rocket in Dubai
Forum: Off Topic
Last Post: axied12
10-25-2024, 01:09 PM
» Replies: 0
» Views: 790
|
Anime coloring pages
Forum: Off Topic
Last Post: axied12
10-13-2024, 05:10 PM
» Replies: 0
» Views: 832
|
|
|
Making process control valve choices |
Posted by: mfkw565a - 09-17-2021, 02:51 AM - Forum: Welcomes and Introductions
- No Replies
|
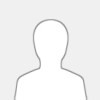 |
Today’s process control valves offer an ever wider range of features and benefits for industries that require precise control over fluids, steam and other gases. With so many control valves to choose from it is important to establish the features that will deliver the most cost-effective design for a particular application.
Control valves are used to manage the flow rate of a liquid or a gas and in-turn control the temperature, pressure or liquid level within a process. As such, they are defined by the way in which they operate to control flow and include globe valves, angle seat, diaphragm, quarter-turn, knife and needle valves, to name a few. In most cases the valve bodies are made from metal; either brass, forged steel or in hygienic applications 316 stainless steel.
Actuators will use an on-board system to measure the position of the valve with varying degrees of accuracy, depending on the application. A contactless, digital encoder can place the valve in any of a thousand positions, making it very accurate, while more rudimentary measurements can be applied to less sensitive designs.
One of the main areas of debate when specifying globe control valve is determining the size of the valve required. Often process engineers will know the pipe diameter used in an application and it is tempting to take that as the control valve’s defining characteristic. Of greater importance are the flow conditions within the system as these will dictate the size of the orifice within the control valve. The pressure either side of the valve and the expected flow rate are essential pieces of information when deciding on the valve design.
Inside the valve body, the actuator design is often either a piston or a diaphragm design. The piston design typically offers a smaller, more compact valve which is also lighter and easier to handle than the diaphragm designs. Actuators are usually made from stainless steel or polyphenolsulpide (PPS), which is a chemically-resistant plastic. The actuator is topped off by the control head or positioner.
Older, pneumatically operated positioners had a flapper/nozzle arrangement and operated on 3-15psi, so no matter what the state of the valve, open closed or somewhere in between, the system was always expelling some compressed air to the atmosphere.
Compressed air is an expensive commodity, requiring considerable energy to generate and when a manufacturing line is equipped with multiple process control valves all venting to the atmosphere, this can equate to a considerable waste of energy. It is important to not only establish the most appropriate valve design, but also a cost-effective solution that takes account of annual running costs.
Modern, digital, electro-pneumatic valves that use micro-solenoid valves to control the air in and out of the actuator have introduced significant improvements for operators. This design means that while the valve is fully open, fully closed or in a steady state, it is not consuming any air. This, and many other engineering improvements, have made substantial advances in both economy and precision.
Flexible designs
Valve seats can be interchangeable within a standard valve body, which allows the valve to fit existing pipework and the valve seat to the sized to the application more accurately. In some cases, this can be achieved after the valve has been installed, which would enable a process change to be accommodated without replacing the complete valve assembly.
Selecting the most appropriate seal materials is also an important step to ensure reliable operation; Steam processes would normally use metal-to-metal seals, whereas a process that included a sterilization stage may require chemically resistant seals.
Setting up and installing a new valve is now comparatively easy and much less time-consuming. In-built calibration procedures should be able perform the initial setup procedures automatically, measuring the air required to open and close the valve, the resistance of the piston seals on the valve stem and the response time of the valve itself.
Improving safety
Control valves should be specified so they operate in the 40-85% range so if the valve is commanded to a 10% setting, it can detect if something has potentially gone wrong with the control system and the best course of action is to close the valve completely. If the valve is commanded to a position of 10% or less this can cause very high fluid or gas velocities, which have damaging effects on the system and cause considerable noise and damage to the valve itself.
Modern control functionality can offer a solution that acts as a safety device to prevent damage to the process pipework and components. By building in a fail-safe mechanism, any valve position setting below a pre-set threshold will result in the valve closing completely, preventing damage to the surrounding system.
Control inputs can also include safety circuits to ensure safe operating conditions within the process equipment. For example, if an access panel on a vessel containing steam is opened, an interlock switch will open and the valve controlling the steam supply to the vessel can be automatically closed, helping mitigate any risks.
Improving reliability
Many process control environments offer less than ideal conditions for long-term reliability. Moisture-laden atmospheres, corrosive chemicals and regular wash-downs all have the capacity to shorten the service life of a process Self regulating control valve. One of the potential weaknesses of the actuator is the spring chamber where atmospheric air is drawn in each time the valve operates.
One solution is to use clean, instrument air to replenish the spring chamber, preventing any contamination from entering. This offers a defense against the ingress of airborne contaminants by diverting a small amount of clean control air into the control head, maintaining a slight positive pressure, thus achieving a simple, innovative solution. This prevents corrosion of the internal elements and can make a significant improvement to reliability and longevity in certain operating conditions.
While choosing the most appropriate process control valve can be a complex task, it is often best achieved with the assistance of expert knowledge. Working directly with manufacturers or knowledgeable distributors enables process control systems to be optimized for long-term reliability as well as precision and efficiency.
Damien Moran is field segment manager, Hygienic – Pharmaceutical at Bürkert. This article originally appeared on the Control Engineering Europe website. Edited by Chris Vavra, associate editor, Control Engineering, CFE Media and technology, cvavra@cfemedia.com.
Control valves are generally present whenever fluid flow regulation is required. The three way and angle control valve reliability is critical to the control quality and safety of a plant. An improved dynamic and static valve behaviour would have a major impact on the process output. In order to assess the dynamic performance of the control valve, a computer model of an electro-hydraulic control valve is developed. And the control valve characteristics are investigated through the use of mathematical simulations of the control valve dynamic performance. The results show that the electro-hydraulic driven control valve, which is developed to regulate the mixed-gas pressure in combined cycle power plant, can meet the challenge of the gas turbine.
Control valves play important roles in the control of the mixed-gas pressure in the combined cycle power plants (CCPP). In order to clarify the influence of coupling between the structure and the fluid system at the control valve, the coupling mechanism was presented, and the numerical investigations were carried out. At the same operating condition in which the pressure oscillation amplitude is greater when considering the coupling, the low-order natural frequencies of the plug assembly of the valve decrease obviously when considering the fluid-structure coupling action. The low-order natural frequencies at 25% valve opening, 50% valve opening, and 75% valve opening are reduced by 11.1%, 7.0%, and 3.8%, respectively. The results help understand the processes that occur in the valve flow path leading to the pressure control instability observed in the control valve in the CCPP.
1. Introduction
The steel mills generate vast amounts of blast furnace gas (BFG) and coke-oven gas (COG) in the production. In order to reduce the environmental pollution, some steel mills mix BFG with COG and build combined cycle power plants (CCPP) to make use of the gas [1]. For the normal operation of CCPP, the pressure of mixed gas delivered to the gas turbine should be kept in a steady range.
In CCPP, control valves play important roles in the control of the mixed-gas pressure. The signal of mixed-gas pressure measured using the pressure meter is compared to the signal of the desired pressure by the controller. The controller output accordingly adjusts the opening/closing actuator of the control valve in order to maintain the actual pressure close to the desired pressure. The opening of the control valve depends on the flow forces and the driving forces of the control-valve actuator, while the flow forces and the driving forces are affected by the valve opening. Therefore, there is strong coupling interaction between the fluid and the control valve structure.
According to Morita et al. (2007) and Yonezawa et al. (2008), the typical flow pattern around the Knife Gate Valve is transonic [2, 3]. When pressure fluctuations occur, large static and dynamic fluid forces will act on the valves. Consequently, problematic phenomena, such as valve vibrations and loud noises, can occur, with the worst cases resulting in damage of the valve plug and seal [4]. In order to understand the underlying physics of flow-induced vibrations in a steam control valve head, experimental investigations described by Yonezawa et al. (2012) are carried out. Misra et al. (2002) reported that the self-excited vibration of a piping system occurs due to the coincidence of water hammer, acoustic feedback in the downstream water piping, high acoustic resistance at the control valve, and negative hydraulic stiffness at the control valve [5]. Araki et al. (1981) reported that the steam control-valve head oscillation mechanism was forced vibration, while self-excited vibration was not observed [6].
Those studies cited previously are mainly aimed at the modeling of the self-excited vibration, the analysis of vibration parameters stability, and so on [7–11]. Whereas, the studies on the influence of nonlinear fluid-structure coupling of control valve on the valve control characteristics, such as the pressure regulation feature, are still very limited [12–17]. In the CCPP, the valve control characteristics affected by the fluid-structure coupling are particularly important for the stability of the mixed-gas pressure control. It has not been uncommon to see that the instability of the mixed-gas pressure causes a severe disturbance or even an emergency shutdown of the whole plant, and the handling of such an emergency often becomes a source of new problems and confusion. In this paper, numerical investigations are carried out to clarify the influence of fluid-structure coupling of control valve on not only the flow field but also the gas pressure regulation and the natural frequency changes of the control valve. This study helps understand the processes that occur in the valve flow path leading to the mixed-gas pressure pulsations, which is valuable for the pressure stability control of the mixed gas in the CCPP.
|
|
|
How are hybrid inverters used in solar projects? |
Posted by: mfkw565a - 09-17-2021, 02:48 AM - Forum: Welcomes and Introductions
- No Replies
|
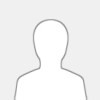 |
This paper proposes a new configuration of a single-phase hybrid inverter with an integrated battery energy storage, which is suitable for residential households to maximize local consumption of solar energy and thus reduce dependency on grid support. The hybrid inverter is called Direct Storage Hybrid (DSH) Inverter. A transformer-less topology such as HERIC, operating at low frequency to generate a three-level rectangular output voltage, is adopted to connect a photovoltaic (PV) panel to the load and/or the grid. A series active filter is employed to compensate the high harmonic components from the rectangular voltage and provide a sinusoidal voltage. A bidirectional dc/dc converter connects the battery to the PV panel to control the battery state of charge (SoC) and optimize the PV panel operation during both off-grid and grid-connected modes. The DSH inverter can let the battery bypass the dc/dc converter and connect directly to the inverter stage, leading to a significant improvement in throughput efficiency in battery utilization. This paper discusses the operation and loss analysis of the DSH inverter in off-grid mode.
This paper is designed in such a way that it overcomes this limitation by the use of solar energy. NA hybrid inverter lv with Solar Battery Charging System consists of an inverter powered by a 12V Battery. This inverter generates up to 230V AC with the help of driver circuitry and a heavy load transformer. This battery gets charged from two sources, first being the mains power supply itself and second from the solar power. If the mains power supply is available, then the relay switches to main power supply for supplying the load. This power supply also charges the battery for using it as back up the next time when there is a power outage. The use of solar panel to charge the battery gives an additional advantage of surplus power in case the power outage of mains is prolonging. Thus this inverter can last for longer duration’s and provide uninterrupted power supply to the user.
Hybrid inverters are commonly used in the developing world, but they are starting to make their way into daily use in certain areas of the U.S due to their ability to stabilize energy availability.
A solar inverter’s main job is to convert DC power generated from the array into usable AC power. Hybrid inverters go a step further and work with batteries to store excess power as well. This type of system solves issues renewable energy variability and unreliable grid structures.
“Inverters for grid-tied applications can only provide power based on what the array can immediately generate from the sun,” explained Bryan Whitton, product manager at Darfon. “Hybrid inverters can store power in batteries and then drawn upon it as needed for energy stabilization.”
Hybrid inverters can vary in size, performance and features. But Mara White, product manager for OutBack Power, said most models usually operate bi-directionally, meaning they can convert DC power from modules to usable AC power and then convert stored AC from the batteries to power loads when needed. “Hybrids can also remain grid-connected and use a mix of renewable and non-renewable energy to charge batteries and offset loads,” White added.
Some contractors have used hybrid inverters in the residential, remote home applications for the past decade or two. But Allan Gregg, VP of applications engineering at GreatWall—which manufactures Satcon inverters—said the range of applications has expanded over the past few years to include large capacity microgrids as well as grid-connected systems.
Historically, hybrid inverters have been used more frequently in developing countries that do not have access to a reliable power grid.
“In North America and Europe, hybrid inverter-based systems are usually elective,” White explained. “Users choose to use them for storing energy for self-consumption or provide back-up power during emergencies. But in the developing world, hybrids are more of a necessity to compensate for weak or intermittent grids or a lack of grid electricity all together. Microgrids in places such as India, Asia and Africa are also driving na hybrid inverter hv adaptation.”
Still, Whitton said hybrid models are beginning to be used on a more daily basis in areas of the U.S. where the grid is unpredictable, such as Hawaii, or in states where net-metering has been widely supported. “Applications with less than ideal solar characteristic are also good for hybrid-based systems because they can store power and redistribute it during peak times, improving payback,” he added. “Basically, if the site has the potential for losing the grid frequently, you should consider a hybrid for off-grid operation.”
Having the flexibility of a hybrid system can add initial cost to a project, though experts say this can be offset by the ability to self-consume all of one’s available PV electricity.
There are also important design considerations when using hybrid inverters. For example, Gregg warned that the battery bank voltage should be compatible with the DC input requirements of the inverter, and there should be enough solar capacity to supply the load as well as charge the batteries.
Wiring can also be more complex when using hybrid inverters, especially when panels are dedicated for critical backed-up loads. “And as with any device that does several jobs at once, a hybrid inverter is usually slightly less efficient,” White added, “although, improvements in other balance-of-system components can compensate for that slight loss easily.”
There are also specific electrical safety issues with any type of energy storage, so White recommended getting specialized training in energy storage techniques and design. “Most available training is focused on simple grid-tied systems because they have been the majority of U.S. solar installations until now,” she said. “But with incentives changing and the surge in energy storage interest and applications, it’s important to get ahead of the curve and get advanced training quickly.”
Andrew McCalla of Austin, Texas-based Meridian Solar, a Solar Power World top contractor, said he commonly used hybrids in the mid to late ’90s when the now standard grid-tie inverter sector was just a glimmer. “I can imagine that, when regulatory hurdles are fabricated to limit the consumer and societal benefits of bi-directional power flow from distributed generation, these battery-based platforms will become far more common. What is old is new again!”
Another segment of hybrid inverters includes inverters that can use two energy sources. For example, Ginlong offers a PV / wind lv battery hybrid inverter that has inputs for both sources, instead of having to use two inverters. In much of the United States, wind speeds are low in the summer when the sun shines brightest and longest. The wind is strong in the winter when less sunlight is available. Therefore, because the peak operating times for wind and solar systems occur at different times of the day and year, such hybrid systems have the potential to produce power when it’s needed, and reach a higher return on investment.
When you first consider getting solar or battery storage on your home or business, one of the first things you will discover is that you will require an inverter and that there are many different types of inverters available. This article is designed to provide an introduction to the different kinds of inverters available and help you to understand which one will suit your installation. So what does an inverter do? Simply put an Inverter converts DC power to AC power. Solar panels produce DC power and batteries store DC, however most of our appliances run on AC power, as does the electricity grid. This is why all solar systems and battery storage systems need an inverter however there are several different types of inverters depending on whether or not energy storage batteries are required.
On-grid solar installations are the most common and most affordable type of system available at present. These systems use a simple solar inverter, which convert the DC power from your solar panels into AC power which can be fed directly into the grid, or used in your home appliances.
Off-grid and hybrid systems are much more complex because they involve both solar panels as well as battery storage. Multiple inverters are often required in these installations such as a solar inverter and sophisticated battery inverter/charger to manage both grid connection and the charging and discharging of the batteries. These advanced inverter/chargers are known as interactive or multi-mode inverters. However, in recent years a new type of inverter has become available which integrates solar and battery inverter technology into what is known as an all-in-one hv battery hybrid inverter.
A micro-inverter is a very small inverter that is attached to the back of a solar panel. A micro-inverter only converts the power of one or two solar panels to AC so generally many microinverters are required in a single system. Micro-inverters have several advantages over string inverters including performance, safety and monitoring, however the upfront cost can be significantly greater. For more details about micro-inverters, check out our micro-inverters article.
String solar inverters come in single phase and three phase versions although most residential homes in the US and Australia use single phase power, while many homes in Europe use 3-phase power, also all businesses and factories will have three phase power. As a general rule most String solar inverters between 1-6kW are single phase and greater than 6kW are usually three phase.
As home energy storage systems have surged in popularity a new kind of advanced Inverter has emerged known as an hybrid inverter. Hybrid inverters combines a solar inverter and battery inverter/charger into one simple unit. These inverters are a very economical way to enable what is known as ‘self-use’ or 'load shifting' of energy. Allowing you to store solar or off-peak energy in a battery to be used during peak times. Although it is important to know that some all-in-one inverters cannot function during a power outage such as when there is a blackout. They can also have limited functionality and monitoring capabilities.The traditional off-grid solar system uses a simple battery inverter that converters DC power from a battery bank to AC power to supply your home or appliances, these systems need separate battery chargers and regulators. There are more advanced versions of these battery inverters with built in chargers known as inverter/chargers. In recent years very advanced inverters have become available which are inverter/chargers with in-built generator control systems, advanced monitoring capabilities and other features, these are known as interactive or multi-mode inverters. They are typically used in conjunction with a solar inverter to create what is known as an AC coupled system. You can learn more about these and other hybrid inverter types here.
|
|
|
Antioxidants Explained in Simple Terms |
Posted by: jjkkj871 - 09-16-2021, 08:17 AM - Forum: FPS and Shooters
- No Replies
|
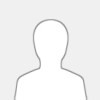 |
What are antioxidants?
Antioxidants are molecules that fight free radicals in the body. Free radicals are compounds that can cause harm if they are too high in your body. They are related to a variety of diseases, including diabetes, heart disease and cancer. Your body has its own antioxidant defense system to control free radicals.
However, antioxidants ingredients are also present in foods, especially in fruits, vegetables and other whole plant foods. Several vitamins, such as vitamins E and C, are effective antioxidants. Antioxidant preservatives also play a vital role in food production by extending shelf life.
How do free radicals work
Free radicals are constantly forming in your body. Without antioxidants, free radicals can quickly cause serious damage and eventually death. However, free radicals also have important functions vital to health. For example, your immune cells use free radicals to fight infection. Therefore, your body needs to maintain a certain balance between free radicals and antioxidants. When the number of free radicals exceeds that of antioxidants, it leads to a state called oxidative stress.
Prolonged oxidative stress can damage your DNA and other important molecules in your body. Sometimes it even leads to cell death. DNA damage increases the risk of cancer, and some scientists speculate that it plays a key role in aging. Long-term oxidative stress can lead to an increased risk of negative health outcomes, such as cardiovascular disease and some types of cancer.
While COVID accelerated the trend of adding Immunity Enhancement Ingredients to processed food, it is not exactly a new concept. Products with such characteristics—think probiotic yogurt products and gummy bears spiked with zinc and echinacea—have been growing in popularity for years. And food processors have grown in their understanding of how their products can improve the immune system.
Cnidium is a native Chinese plant that has also been identified in the US in Oregon. Cnidium is a Traditional Chinese Medicine (TCM) that has been used for thousands of years, especially for dermatological conditions. It has been a common ingredient in Chinese lotions, creams, and ointments. A pro-erectile herb, Cindium monnieri extract and its main bioactive known as osthole appear to have mechanisms similar to Viagra in penile tissue and the hippocampus. The usable parts of cnidium are the fruit, seed, and whole plant. Active properties of cnidium are the coumarin derivatives including: - Osthol
- Imperatorin
- Isopimpinellin
- Xanthotoxin
- Bergapten
Additional coumarins have also been identified including cnidimonal, cnidimarin, and others. Cnidium is used orally for increasing sexual performance and libido, erectile dysfunction, infertility, body building, increasing energy, cancer, osteoporosis, and fungal and bacterial infections. Cnidium is used topically for pruritus, rashes, eczema, and ringworm.
Monk fruit is also called Luo Han Guo or swingle. It looks like a small gourd, and it grows on a vine.
Monk fruit is native to regions of Southeast Asia, including some parts of Thailand and China. Buddhist monks in the 13th century were the first to cultivate the fruit, which is the reason for its name.
Fresh monk fruit spoils rather quickly. Traditionally, people used dried monk fruit in herbal medicines.
Today, monk fruit is the most popular natural sweetener ingredients. The fruit extract contains substances called mogrosides, which are intensely sweet.
According to the International Food Information Council Foundation, monk fruit is around 150–200 times sweeter than sugar. Some manufacturers mix the extract with different sugars to balance out the intensity.
A variety of monk fruit sweeteners are available to purchase online.
Monk fruit pros
A monk fruit sweetener has several benefits when compared with sugar:- Zero calories. Monk fruit extract contains no calories, which is helpful for people on diets that restrict a person’s caloric intake.
- Zero carbohydrates. The extract also contains no carbohydrates, which may make it ideal for people on low-carb or keto diets.
- Zero sugar. There is no sugar in pure monk fruit extract, which means that consuming it will not affect blood sugar levels.
- No harmful side effects. The U.S. Food and Drug Administration (FDA)Trusted Source considers monk fruit sweeteners to be generally regarded as safe. There appears to be no evidence that monk fruit sweeteners cause harmful side effects.
- Available in multiple forms. Monk fruit sweeteners are marketed as granules, powders, and liquids. Some products may be easy to carry and use throughout the day.
Nutraceutical ingredients find a wide variety of applications, such as functional food & beverages, animal nutrition, pharmaceuticals, and personal care products. However, the inclusion of nutraceutical ingredients in food & beverage products, feed products, pharmaceuticals, and personal care products results in an increase in the prices of these end products. This, in turn, leads to lower adoption of such products, thereby stunting market growth. Over the past few years, there has been an increase in the demand for healthy alternatives of consumables as consumers have become increasingly conscious about the correct diet. Nutraceutical ingredients, when added to any kind of food & beverage product, result in the formation of functional food & beverages, which, in some way, impart a health benefit.
|
|
|
Multi-Cookers For Every Kind of Household |
Posted by: Q123M - 09-16-2021, 07:00 AM - Forum: FPS and Shooters
- No Replies
|
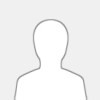 |
Multi-Cookers For Every Kind of Household
Whether you have a large family or live alone, there is always a magic multicooker to suit every kind of home. It could be a one-person pot, or a big sharing one - these popular Electric Multi Cookers do the cooking for you so you spend less time on great meals.
Not all of us are fortunate enough to be spending these lockdown times with our family or housemates. For those who are alone at home, under quarantine, or simply a healthcare worker living solo to protect their family, cooking for oneself can be a huge chore. Almost the same amount of preparation and cleaning goes into making a solo meal as cooking for two or more people. That is why this portable multi-cooker is an amazing find! Small, portable and easy-to-clean, this multi cooker is perfect for studio flats, tiny rental rooms, or just those without access to a kitchen. A dual cookware system allows you to both fry and boil – so you can whip up an automatic stir fry cooker to pair with a hearty carrot ginger turmeric soup. We love how both the pot and non-stick frying pan can be stacked together and used as a take-away container – ideal for all you hardworking essential services folks who still want to eat home-cooked food. Even the handles can be folded in when not in use, saving you precious storage space. What is more, you can brew a soothing Luo Han Guo Tea in a flat-based teapot (not included) for rainy days. It is definitely one of the best solo multi cookers out there!
It is important to keep your grill clean, but using a wire grill brush can be more dangerous than helpful.
Wire brushes have always been the standard for cleaning grill grates. However, it is been found that the bristles can actually break off and wind up in your food. Consumer Reports even issued a warning against using these brushes a couple of years ago.
Here is what you need to know about wire grill brush danger.
Why a Wire Grill Brush Can Be Dangerous
As you might expect, wire barbecue grill brush bristles are sharp. And one study revealed that between 2002 and 2014, around 1,700 Americans had to go to the emergency room after accidentally ingesting wire bristles. And those were just the reported cases! They can cause severe damage internally, and may even require emergency surgery.
Health Canada even pushed for a new national standard to help stop these incidents from happening.
Wire Grill Brush Alternatives
Luckily, this is a problem with an easy solution, because it is possible to clean your grill tools without a wire brush. There are plenty of other methods that work just as well, if not better.
For people with smaller grills, a giant brush isn’t really necessary. This expert metal grill brush and scrub pad is perfect for quick cleans between uses and really gets the job done.
How to Reduce Wire Grill Brush Danger
If you currently have a wire brush, give it a good once-over. If it has any loose or missing bristles, toss it. It is better to use some aluminum foil on the fly than take a chance with the wire grill cleaning brush. Make sure to double-check your grill as well and to check for stray bristles stuck on the grates.
So you might agree with me that health is the most important concern for everyone. But do you know that most of the fruit and vegetable we consume are contaminated with unknown pathogens, artificial waxes and harmful chemicals which comes from pesticides and negligence manhandling? One good way to reduce the chances of ingesting harmful substances and live a healthier lifestyle is to clean your vegetables and fruits before consuming them. You can achieve this without stress by using an ultrasonic vegetable and fruit cleaner.
The Vegetable Washing Machine is built to be portable, measuring only 4.5 inches. The size makes it perfect to take along when traveling. It helps to take care of your laundry, and that is why it is regarded as the smallest ultrasonic portable washing machine in the world. The device is constructed with medical-grade, high-quality stainless steel which makes it possible to serve you a lifetime.
|
|
|
Socket or portable battery |
Posted by: Q123M - 09-16-2021, 06:58 AM - Forum: FPS and Shooters
- No Replies
|
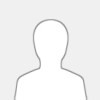 |
Socket or portable battery
A USB fan is a small and portable device that's handy for personal, close-proximity cooling. As the name suggests, it's powered through a USB connection, such as the one in your computer, a power adapter that you plug into a wall outlet or a portable battery. Some can be self-powered using an internal battery that you recharge — over USB, of course — and, in turn, some of these models can even be used as a portable battery to add some charge to a phone.
Despite their size, USB portable mini fans can be powerful, and most offer different speed settings. They won't cool down an entire room, but they can keep you comfortable when used at a close distance, such as an office desk or bedside table. Best of all, they are inexpensive.
This small desk fan has three-speed settings — soft, natural wind, and strong wind — to keep you cool. Depending on the speed setting, the 2,200mAh battery provides between three and nine hours on one charge. There's blue backlighting you can use at night and emergency light for when you're in a critical situation.
Some people experience respiratory symptoms in the summer months, when the weather is hot, and the air contains more allergens. Air conditioners and fans can circulate dry air through the room, and air conditioners remove any moisture from the air. A humidifier may be beneficial during this season.
However, people are more likely to benefit from a humidifier in the cold months, when cold air dries out the lungs, nose, and lips. Also, some types of central heating can dry out the air indoors.
Insect repellent maintenance cost is low, and it is easy to use mosquito killer products. All you have to do is plug the mosquito trap into the USB and observe all the annoying and annoying mosquitoes in your area. The mosquito killer has a series of photocatalyst lamps, and the mosquitoes cannot resist and are attracted by the trap. The fan then sucks the mosquitoes inside and prevents them from escaping.
The countertop blender has a pitcher with spinning blades in the bottom that mounts onto a motorized base. More powerful and with more settings than immersion blenders, they can blend, mix, puree, grind, chop and even crush ice. If you cook often with vegetable purees or you love frozen drinks and smoothies, you will definitely want a countertop blender. Their reputation of being difficult to clean is a myth. Which blender you choose depends on your kitchen series needs. If you find that you do not work with frozen or hard ingredients often, the immersion blender is a space-saving gadget that can work in ways a countertop blender can not. Likewise, if you would rather have a larger appliance that can do more, you might prefer to get just a countertop blender.
If you have to sleep with a night light lamp on you might think that blue and white lights might create a calming sensation and help you sleep best. However, a new study involving hamsters suggests that blue light had the worst effects on mood, followed closely by white light.
For years, consumer electronics companies have competed primarily through technology, by cramming ever more features into products in a race to offer consumers the latest and greatest. But this approach can be fruitless. Even in the best of times, many manufacturers struggle to make money: despite falling component costs, intense competition can restrain price increases, and rapid obsolescence often makes it necessary to discount all but the very newest products.
|
|
|
Some ways to improve your sheet metal parts |
Posted by: Q123M - 09-16-2021, 06:56 AM - Forum: FPS and Shooters
- No Replies
|
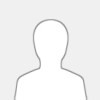 |
Some ways to improve your sheet metal parts
Sheet metal fabrication is a handy set of manufacturing processes used to create parts from flat pieces of metal. Sheet metal comes in a range of materials and thicknesses, and can be used to create parts like appliances, enclosures, brackets, panels and chassis.
For those new to sheet metal fabrication, the process can seem daunting. Unlike versatile processes such as 3D printing and CNC machining, sheet metal fabrication is dictated by fairly strict design conventions. Sheet metal must be bent and cut in particular ways, and is only suitable for certain parts and products.
As such, it is important to learn some basic principles of sheet metal fabrication before embarking upon a project. Courtesy of rapid prototyping specialist 3ERP, this guide offers five simple tips to improve Sheet Metal Parts, turning ordinary designs into professional-quality sheet metal products.
What is sheet metal fabrication?
Sheet metal fabrication is a set of manufacturing processes that share one common trait: they all use sheet metal — as opposed to blocks, powder or molten metal — as feedstock. Different machines form the sheet metal in different ways: some make holes or incisions in the sheet metal; others bend, stamp or spin the metal to turn it into various shapes.
Using sheet metal fabrication, engineers can create durable, low-cost parts from a wide variety of metals. These stamping parts can be used across a range of industries, from aerospace to medicine to robotics.
The sheet metal used in the manufacturing process is usually between 0.006 and 0.25 inches (0.015 and 0.635 centimeters) thick, with the chosen size dependent on the given material and end-use of the part.
Improving sheet metal parts
Sheet metal fabrication is unique amongst the various manufacturing processes because its feedstock is unlike any other. For this reason, it can be difficult to design sheet metal parts when one is used to designing parts for machining, molding and other common manufacturing processes.
While the best way to ensure high-quality sheet metal parts is to consult and utilize a sheet metal specialist like 3ERP, it is also advantageous to follow certain design principles from the outset. By observing the following five tips, designers can create sheet metal parts that are strong, easy to fabricate and resistant to breakage.
Aluminum casting is a method for producing high tolerance and high-quality casting parts by inserting molten aluminum into a precisely designed and precision-engineered die, mold, or form. It is an efficient process for the production of complex, intricate, detailed parts that exactly match the specifications of the original design.
A positive benefit of aluminum casting parts is the layer of aluminum oxide that forms immediately after the part is removed from the mold, which provides a wall of protection against corrosion and rust.
Thanks to a wide range of machines and materials, CNC machining is capable of creating a vast array of professional parts for use in many industries. However, engineers must be careful to design parts in a way that suits the manufacturing process.
Considering the possibilities and limitations of the CNC machine — whether it’s a mill, a lathe or a high-end 5-axis machining center — leads to better machining parts, even if compromises have to be reached. A part is both enabled and constrained by its manufacturing process.
With that in mind, designing for manufacturability, by following certain design principles, ensures that parts will come out in the best way possible, will not break during machining, will not damage the machine itself, and will be fabricated in an efficient and cost-effective manner.
|
|
|
Coronavirus Face Masks & Protection FAQs |
Posted by: Q123M - 09-16-2021, 06:54 AM - Forum: FPS and Shooters
- No Replies
|
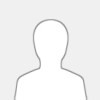 |
Coronavirus Face Masks & Protection FAQs
The CDC continues to monitor the spread of COVID-19 and makes recommendations for wearing face face masks, both for those who are fully vaccinated as well as those who are not fully vaccinated.
The CDC also recommends that masks and physical distancing are required when going to the doctor’s office, hospitals or long-term care facilities, including all Johns Hopkins hospitals, care centers and offices.
Can wear a face mask prevent coronavirus from spreading?
Yes. Although being fully vaccinated greatly reduces your chance of catching or spreading the coronavirus, it doesn’t eliminate it entirely. If you are infected with the coronavirus and do not know it, a protective face mask is very good at keeping your respiratory droplets and particles from infecting others. If you haven’t yet received your COVID-19 vaccine, wearing a mask can also help prevent germs that come from another person’s respiratory droplets from getting into your nose and mouth.
Since the coronavirus can spread through droplets and particles released into the air by speaking, singing, coughing or sneezing, medical face masks are still a good idea in crowded indoor public places that contain a mixture of vaccinated and unvaccinated individuals.
Wearing a mask is still recommended in health care settings and other places where people around you may have risk factors for severe consequences of COVID-19. These include people over age 65 and those living with heart disease, diabetes, obesity, chronic lung disease, immunity problems or cancer.
Do I need to wear a face mask if I currently have COVID-19?
Yes. If you are actively infected with the coronavirus and cannot stay completely away from others in your home, droplets from your nose or mouth could infect another person who has not been vaccinated yet or who has a weakened immune system. Stay away from others as much as possible and wear your disposable face mask around others until your doctor says it’s safe to discontinue wearing it.
Medical gauze is a type of thin medical fabric with a loose open weave used in wound care. Both gauze pads and gauze sponges are made of 100% cotton. They wick vertically to draw exudates out of wounds and are stronger than other types of dressings due to their longer fibers. Our gauze is offered in both sterile and non-sterile forms. For open wounds, it is recommended to use sterile gauze only.
Do I need to bandage a cut or scrape?
You do not need to bandage every cut and scrape. Some heal more quickly when left uncovered to stay dry. But if the cut is on a part of the body that might get dirty or rub against clothes, put on a bandage to protect it. Change the bandage every day or whenever it gets wet or dirty.
Pure absorbent cotton wool has many uses in personal care and medical care. Pure cotton wool is used in a wide variety of nonwovens, such as baby and adult diapers, incontinence products, feminine hygiene pads, disinfection and disinfection wipes. Cotton wool balls are also household items and have a variety of uses, such as cleaning wounds and using skin care products. In health care, you'll see a wide range of applications for pure cotton, including dressings, bandages, and fillers. Cotton wool is also the basic fiber of choice for patients and medical staff in robes, curtains, gloves, masks, tooth rolls, and balls. Cotton wool can be used in all of these products, whether 100% cotton, cotton mixed with other fibers, or fabric composites.
The use of nonwovens in the medical arena goes back to the time of Second World War when need for new and large volumes of the medical products had arisen. In several reports published, nonwovens were regarded as the most effective materials for bacterial barriers. They were also found superior to linens in the reduction of air-borne contamination.
After significant development of non woven products, they were designed in a way to suit the medical needs and give a performance much better than their woven counterparts in terms of cost, effectiveness, disability, etc. In hospitals, cross-contamination is always one of the biggest problems which were attributed largely to re-using of woven gowns, masks and other similar articles which would get contaminated and potentially spread the germs. The advent of nonwovens facilitated the development of a more cost effective alternative that was disposable and reduced the problem of cross-contamination greatly.
Preparedness is a key element of first aid. While every home, auto, and boat should be equipped with a basic emergency kit that includes first aid supplies and a first aid manual, special circumstances may necessitate more advanced or specific degrees of preparation for an emergency.
For example, residents of certain geographic areas where natural disasters (such as hurricanes, earthquakes, tornados, floods, landslides, or tsunamis) may occur should prepare for emergencies by assembling disaster preparedness kits such as earthquake kits, flood kits, and evacuation kits.
Travelers should also prepare to administer first aid in the region they plan to visit. In many developed countries, this may amount to packing standard first aid kits and manuals with your belongings.
Medicines to prevent motion sickness and advanced awareness about the management of traveler's diarrhea are also helpful to travelers.
There are lots of types of wound care dressing, with hundreds of brands offering a range of products – some highly similar to each other. The most basic requirements for a dressing are that it protects against further damage or infection and that it promotes a good healing environment. A good healing environment is one with the right amount of moisture – dry wounds don’t heal as well as moist wounds, but wounds that are too wet can cause skin breakdown around the wound and prevent healing. The absorbency of the dressing, therefore, needs to be chosen based on the assessment of each individual wound.
|
|
|
Medical Protective Clothing: The Complete Guide |
Posted by: Q123M - 09-16-2021, 06:52 AM - Forum: FPS and Shooters
- No Replies
|
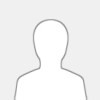 |
Medical Protective Clothing: The Complete Guide
Medical protective clothing, also known as medical protective suit, disposable protective coverall, or antivirus suit. Medical protective clothing refers to the protective clothing used by medical personnel (doctors, nurses, public health personnel, cleaners, etc.) and people entering a specific health areas (such as patients, hospital visitors, persons entering the infected area, etc.). Medical protective clothing has good moisture permeability and barrier, has the function of resisting the penetration of alcohol, blood, body fluid, air dust particles, and bacterial virus, effectively protect the safety of personnel and keep the environment clean.
Medical protective clothing is a combination of hats, tops, and trousers. There are two kinds of medical protective clothing: isolation gown and protective clothing. The main difference between medical protective clothing and isolation gown is that medical protective clothing is more durable than isolation clothing, the protection grade is higher, the protection performance is better, the protection purpose and the protection principle of them are different.
The common materials used in disposable medical protective clothing are polypropylene textile adhesive fabric, new polyester fiber, polymer coated fabric, SMS nonwovens, polyethylene breathable film/nonwoven composite. At present, most of them use polytetrafluoroethylene (PTFE) material to make medical protective clothing, PTFE is a kind of high-performance polymer, which cannot only resist water pressure but also discharge water vapor through micropores.
There are many kinds of coatings for protective fabrics, such as PVC, polyethylene and so on. The waterproof, barrier bacteria of this kind of protective clothing is good, it can be reused, but the moisture permeability is poor and uncomfortable. The high-end laminated fabric is PTFE, super waterproof and moisture permeable composite fabric.
Antimicrobial technology adds a durable defense barrier on fabric, which helps fight odor-causing bacteria, mold and mildew. This makes a product with antimicrobial fabric stay fresher longer so you can wear it with confidence. This lasting, continual protection against potentially harmful microbes lasts wash after wash. The antibacterial fabric stays cleaner for longer and in between washings. If a towel stinks less, you will wash it less because it maintains that just laundered feeling. New energy-efficient washing practices do not get fabrics as clean. Adding antimicrobial product protection reduces the growth of odor-causing microbes that remain on your clothes even after washing.
Your clothing doesn’t just look great. It also absorbs or blocks harmful UV radiation and remains one of the most effective forms of protection against sun damage and skin cancer.
What's more, sun protective clothing is the simplest way to stay safe; unlike sunscreen, you never need to reapply!
Ultraviolet Protection Factor (UPF) indicates how much UV radiation (both UVB and UVA) a fabric allows to reach your skin. For example, a UPF 50 fabric blocks 98 percent of the sun’s rays and allows two percent (1/50th) to penetrate, thus reducing your exposure risk significantly. UPF measures the amount of UV radiation that can penetrate fabric and reach your skin. Sun Protection Factor, or SPF, is based on the time it takes for UV-exposed skin to redden; if you burn after 20 minutes, if used correctly, an SPF 15 sunscreen may protect your skin 15 times longer.
The textile industry is considered the most ecologically harmful industry in the world. The eco-problems in textile industry occur during some production processes and are carried forward right to the finished product. In the production process like bleaching and then dyeing, the subsequent fabric makes a toxin that swells into our ecosystem. During the production process controlling pollution is as vital as making a product free from the toxic effect. The utilization of rayon for clothing has added to the fast depleting forests. Petroleum-based products are harmful to the environment. In order to safeguard our environment from these effects, an integrated pollution control approach is needed. Luckily there is an availability of more substitutes.
Hemp, wool, organic cotton, soy silk, bamboo fabrics, jute, corn fiber, etc are considered eco-friendly fabrics due to their availability from nature without any harmful effects of chemicals or toxins. Moreover, as compared to other synthetic fibers they are available at a cheaper rate.
Clothing has been used for protection since time immemorial, shielding the human body from social, physical and emotional threats. The term protective clothing defines everything used for physical protection of the body.
Today, the array of physical threats is endless and so is the availability of protective wear. It can be worn in any situation to provide protection and make the wearer stand against any hazardous condition. Many individuals with injuries or handicaps use protective clothing to prevent further possible damage.
Clothing psychology and comfort have changed the way people look at protective clothing. Consumers are embracing fashionable protective clothing to participate in sports and adventurous activities. They are ready to risk their life trusting advanced protective wear. On the other hand, protective wear are building trust by boosting the consumer's performance.
|
|
|
The relation between shaker screen mesh and the hole diameter |
Posted by: Q123M - 09-16-2021, 06:50 AM - Forum: FPS and Shooters
- No Replies
|
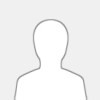 |
The relation between shaker screen mesh and the hole diameter
A shale shaker screen is a vulnerable spare part of a shale shaker. But the shaker screen is very important in the drilling mud recycling system. The shaker screens design and quality determined the separation performance of the shale shaker. Generally speaking, the working environment and the drilling mud contents are the most determining factors to choose a suitable MI-SWACO shaker screen. The other factor is the size of the particle in the drilling mud fluid to be separated. If you know the particle size, so the shaker screen mesh is determined.
What is the shaker screen mesh?
Shaker screen mesh refers to the quantity of holes per square inch. So the Derrick shaker screen mesh has an inverse proportional relation with the hole quantity. That is to say, the larger the shaker screen mesh, the smaller the screen hole size. Commonly speaking, the relation between them is: Mesh x Hole Diameter(micron)=15000
For example, if the shaker screen mesh is 200, then we can estimate that the screen hole diameter is about 75 microns. This is very useful for us to choose the proper shale shaker screen according to the mud fluid contents.
Other shaker screens or you can say shale shaker screens too, are a type of mechanical screen, aim to take solids out or separate solids from drilling fluid (mud). Usually, a composite frame shaker screen is made of stainless steel, polyurethane or composite frame. It is a spare part of a shale shaker and a combined shaker frame by stainless screw and wedge block.
Shale shaker spring is a component that provides a damping effect. The spring quality and feature will help us to get a better process when stopping the shaker. Most of the springs are made of high-quality special spring steel. However, some of the springs or we call it float amount/absorber is made of rubber or combined rubber and steel.
In minerals processing, one of the most important hydrocyclone applications is within closed circuit grinding operations, classifying particles leaving the mill. Incorrect particle classification has a detrimental impact on plant efficiency and can unnecessarily consume circuit capacity.
Feed pellet machines can bring benefits to your poultry farming. Choosing a suitable feed pelletizer machine and using it properly will significantly improve the quality of the feed. It will soon reflect a benign effect in the production process. If you can further master the technology of making animal feed pellets, you can also greatly reduce the cost of materials, thereby increasing profits.
It is agreed upon in the trucking industry that ratchet straps are the most secure way to tie down a heavy load, providing the most strength and security for oversized gear! The best heavy-duty ratchet straps wrap, hook, or clip to your trailer rub rail or D-rings. These tie-down straps tighten using a ratcheting system so you can apply the right amount of pressure over or around your cargo to ensure it will stay firmly in place. Having reliable, high-quality ratchet straps is integral to making sure you deliver your cargo safely and securely!
Are you planning your next overhead lifting project and unsure about the best type of industrial lifing sling to use? Or, maybe you are not getting the service life you would expect out of the slings that you’re currently using? Alloy chain slings, wire rope slings, synthetic slings, and metal mesh slings can all be used to safely and efficiently lift, move, and position a load.
But, choosing the right type of lifting sling is dependent on a complete understanding of the application, the environment it is being used in, and how the sling will be used to support and lift the load. Wire rope is a preferred lifting device for many reasons. Its unique design consists of multiple steel wires that form individual strands laid in a helical pattern around a fiber or steel core. This structure provides strength, flexibility, and the ability to handle bending stresses.
Regardless of the time spent on a roof, the risk of falling is high. Any fall is likely to result in a serious injury. Industrial rope and nets installed below a high-level work area reduce the distance that a worker can fall. They absorb the impact of the fall and provide a soft landing to reduce the likelihood of a person being injured. Safety nets are collective fall arrest systems, not fall restraint systems. That is, they provide passive protection from falls while allowing people to work at height without restricting their movement. A safety rope passes through each mesh around the perimeter of the net and determines the net's overall dimensions.
|
|
|
What are Precision Stamping Machines? |
Posted by: Q123M - 09-16-2021, 06:47 AM - Forum: FPS and Shooters
- No Replies
|
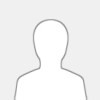 |
What are Precision Stamping Machines?
Precision metal stamping is a process for punching markings, three-dimensional shapes, or other designs into material surfaces, and precision stamping machines exert a high level of force to engrave dies and forms onto the surface material. Metals such as steel, copper, and aluminum are the most commonly stamped materials, though other metals, plastics, and cement can also undergo precision stamping.
Benefits of Precision Metal Stamping
Along with machining, die-casting, forging, and many other examples, precision metal stamping is a standard and ubiquitous manufacturing process. Some of its major benefits include:
Lower die cost: Precision metal stamping dies tend to be relatively less expensive to produce and maintain than those used in other common processes.
Lower secondary costs: Cleaning and plating precision stamping machines are cheaper than similar treatments for other metal forming techniques.
High level of automation: Precision metal stamping machines are relatively easy to automate, and can employ high-end computer-control programs that provide greater precision, faster production, and quicker turnaround times.
Precision Stamping Industries and Applications
Precision stamping machines are useful in a variety of applications, especially those involving three-dimensional designs, lettering, or other surface engraving features. Such terminal stamping products are commonly produced for home appliance manufacturers, automotive companies, telecommunications services, aerospace industries, medical equipment manufacturers, and electronics companies.
The specific products and components can range from simple metal stamping parts, such as metal clips, springs, weights, washers, and brackets, to more complex designs, such as those found in engine bases or friction plates.
Operated with Computer Numerical Control (CNC) systems and provided with precise design instructions, CNC Lathes are machine tools where the material or part is clamped and rotated by the main spindle, while the cutting tool work on the material, is mounted and moved in various axis.
CNC Lathe services are normally used for machining parts, where the material/part is clamped and rotated whereas the cutting tool is stationarily mounted for OD (Outer Diameter) and ID (Inner Diameter) operations, e.g. shafts and pipes. They are ideal for parts that have the same symmetry around an axis that could be chucked up (i.e. radially clamped) in the spindle.
Most subtractive CNC machines such as mills, water jets, and plasma cutters have the workpiece secured to a bed and the cutting done by a spinning tool. To cut, the tool moves across the workpiece or a tool head shoots at it. In contrast, CNC turning company reverses that process by rotating the workpiece and cutting away at it (by moving a static cutting bit against the workpiece).
Because of how they operate, CNC mills are primarily used for creating complicated geometries, while CNC lathes are used for creating cylindrical or oblong shapes. A CNC lathe is usually chosen over a CNC milling service or 3D printer because of its ability to make multiples of the same part incredibly fast and from one stock piece of material. Check out this mesmerizing video of a CNC lathe in action:
Horizontal turning centers are enclosed CNC lathes that integrate milling and drilling capabilities. A turning center can also include a traveling tool turret, more tooling axes, coolant flooding, a tailstock that is separated from the carriage, and sometimes a conveyor belt.
Injection molding processing is a manufacturing process that is commonly used to create plastic components. Its ability to produce thousands of complex parts quickly makes it the perfect process for the mass production of plastic components. Essentially, the process involves the injection of plastic at high speed and pressure into a mold, which is clamped under pressure and cooled to form the final part.
By melting thermoplastic and injecting it into an aluminum mold at high speed and pressure, manufacturers can create multiple complex parts at once. When the parameters of the process are controlled correctly, there’s also little need for finishing and processing the manufactured part, making it more cost-effective and efficient.
|
|
|
|