Welcome, Guest |
You have to register before you can post on our site.
|
Online Users |
There are currently 194 online users. » 0 Member(s) | 192 Guest(s) Bing, Google
|
Latest Threads |
Dominica visa free countr...
Forum: Off Topic
Last Post: axied12
06-24-2025, 12:37 PM
» Replies: 0
» Views: 207
|
Advanced microneedling
Forum: Off Topic
Last Post: axied12
05-28-2025, 01:25 PM
» Replies: 0
» Views: 333
|
Caviar and cheese
Forum: Off Topic
Last Post: axied12
05-28-2025, 12:38 PM
» Replies: 0
» Views: 294
|
Top-rated countertop comp...
Forum: Off Topic
Last Post: axied12
05-04-2025, 06:42 AM
» Replies: 0
» Views: 445
|
Ryanair letenky levně do ...
Forum: Off Topic
Last Post: axied12
02-11-2025, 01:37 PM
» Replies: 0
» Views: 838
|
Trusted essay writing ser...
Forum: Off Topic
Last Post: axied12
01-30-2025, 08:16 AM
» Replies: 0
» Views: 754
|
Bootverkopers - actieve j...
Forum: Off Topic
Last Post: axied12
12-07-2024, 11:07 AM
» Replies: 0
» Views: 880
|
Services for individuals ...
Forum: Off Topic
Last Post: axied12
12-02-2024, 03:31 PM
» Replies: 0
» Views: 855
|
Used excavators
Forum: Off Topic
Last Post: axied12
11-13-2024, 09:22 AM
» Replies: 0
» Views: 802
|
Buy Higo Rocket in Dubai
Forum: Off Topic
Last Post: axied12
10-25-2024, 01:09 PM
» Replies: 0
» Views: 910
|
|
|
What is an efficient carburetor design and other machinery parts |
Posted by: bbkowj258a - 09-03-2021, 07:01 AM - Forum: Welcomes and Introductions
- No Replies
|
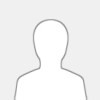 |
A carburetor is a mechanical device that mixes a certain percentage of gasoline with air under the action of a vacuum generated by engine operation. As a precise mechanical device, the carburetor uses the kinetic energy of the inhaled air flow to atomize the gasoline. Its important role for the engine can be called the heart of the engine. Its complete device should include starting device, idling device, medium load device, full load device, acceleration device. The carburetor will automatically proportion the corresponding concentration and output the corresponding amount of mixture according to the different working conditions of the engine. In order to make the mixture more uniform, the carburetor also has the effect of atomizing the fuel for the normal operation of the machine.
The clutch assembly is located in the flywheel housing between the engine and the gearbox. The clutch assembly is fixed on the rear plane of the flywheel with screws. The output shaft of the clutch is the input shaft of the gearbox. When the car is running, the driver can step on or release the clutch pedal as needed to temporarily separate and gradually engage the engine and the gearbox, so as to cut off or transmit the power input from the engine to the transmission. Clutch is a common component in mechanical transmission, which can separate or engage the transmission system at any time. Its basic requirements are: smooth joining, rapid and thorough separation; convenient adjustment and repair; small outline size; small quality; good wear resistance and sufficient heat dissipation capacity; convenient operation and labor saving. Commonly used are divided into jaw type and there are two types of friction.
Caliper disc brake is a type of disc brake. Its rotating element is a metal disc that works on the end face, called a brake disc. The fixed element is a brake block composed of a friction block with a small working area and its metal back plate. There are 2 to 4 in each brake. These brake blocks and their actuating devices are installed on both sides of the brake disc. In the clamp-shaped bracket, it is collectively called a brake caliper. The brake disc and the brake caliper together constitute a caliper disc brake.
Muffler means that for airflow pipes that have noise transmission at the same time, you can use pipes and elbows with sound-absorbing linings, or use noise-reducing devices such as pipes with sudden changes in cross-sectional area and other discontinuous acoustic impedance to attenuate or reduce the noise in the pipe. Reflect back. The former is called a resistive muffler, and the latter is called a resistive muffler. There are also impedance composite mufflers.
Starter and igniter coil are the lighting devices of fluorescent lamps. It is composed of a neon bulb and a small capacitor equipped with a fixed static contact piece and a moving contact piece made of a hot bimetallic piece. Connected to the starting circuit of the fluorescent lamp. A device installed in the gas discharge light source circuit to start and ignite the discharge lamp, also known as a trigger.
Durability is very important for current diesel engines. Diesel engine parts manufacturers are trying to make the engines live as long as possible before overhaul. The time to overhaul for an engine is usually dictated by high oil consumption or blowby. Therefore, it is necessary to understand how wear affects the cylinder kit dynamics, oil consumption, and blowby in an engine. This paper explores the effect of power cylinder component (rings and cylinder bore) wear by using a cylinder kit dynamics model. The model predicts how wear will affect ring motion, inter-ring gas pressure, blowby, etc. The parameters studied were: liner wear, ring face wear, and ring side wear. Two different engines were modeled. The characteristics of these two engines are very different. As a result, the effects of wear are different and the corresponding durability will be different. This illustrates the need to model each individual type of engine separately. The modeling shows that top ring face wear is very significant for maintaining good oil and blowby control. Liner wear is important, but does not have as large an effect as ring wear. The effects of side wear are significant for these two cases.
The design of an engine carburetor is traditionally based on a mechanical device that uses a shutter to control the amount of fuel intake. The fuel is mixed with air to form fuel mixture that is burnt in engine cylinders. This approach has several inherent issues. First, the shutter opening is controlled by creating a vacuum that results in required amount of fuel injected into carburetor chamber. As the speed of a vehicle increases by pressing accelerator, more fuel is required in the carburetor chamber. The rate of increase in fuel cannot be accurately calculated by a mechanical device. Second, the amount of air intake results in an imbalance in fuel mixture ratio. Third, the carburetor's efficiency degrades with age, resulting poor fuel efficiency. This paper proposes EFI for small vehicles. A test case was developed for a two-wheel motor-bike by using an ARDUINO board. The proposed solution was implemented in the engine of motor-bike with minor changes in the carburetor. The cost was quite comparable with mechanical carburetor, and the results were quite promising.
|
|
|
Understanding Auto Parts |
Posted by: bbkowj258a - 09-03-2021, 06:59 AM - Forum: Welcomes and Introductions
- No Replies
|
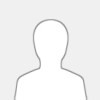 |
The basic idea of a car is pretty simple — turn wheels to pull you down the road. But, as illustrated by the hundreds of individual auto parts for sale at your local Pep Boys, AutoZone or Napa Auto Parts, it actually takes a lot of machinery to make cars work.
If you're trying to figure out what all the parts in your car do, HowStuffWorks AutoStuff is the place for you. Here's a collection of our key car part articles.
Engine System
How Car Engines Work
It's the reason you can put the pedal to the metal and go from zero to 60 in about 8 seconds. The car engine is a piece of engineering genius and one of the most amazing machines we use on a daily basis. Learn how the four-stroke internal combustion engine works.
How Diesel Engines Work
Ever wonder what the difference is between a gasoline engine and a diesel engine? Diesels are more efficient and cheaper to run than gasoline engines. Instead of using carburetion or port fuel injection, diesel engines use direct fuel injection. Find out what else makes diesel engines different! A turbocharger is actually an air compressor that compresses air to increase the air intake with turbocharger assy. It uses the inertial impulse of the exhaust gas from the engine to push the turbine inside the turbine chamber
How Hemi Engines Work
The HEMI engine has an awesome design and great performance, and it's pretty unique in operation. With the revitalization of the HEMI in the 2003 Dodge trucks, industry and consumer attention is once again on this interesting configuration. Check out how the HEMI works and see what makes it different from the typical engine design.
How Rotary Engine blocks Work
A rotary engine is an internal combustion engine, but it's not like the one in most cars. Also called a Wankel engine, this type of engine performs intake, compression, combustion and exhaust in a different part of the housing. Learn about the unique rotary setup and how it compares performance-wise to a piston engine.
How Radial Engines Work
Radial engines reached their zenith during WWII. But today they are not that common. One place where you can still see the radial engine's influence is in the two-cylinder engine of a Harley-Davidson motorcycle. This remarkable engine can be thought of, in a way, as two pistons from a radial engine. Find out about radial engines.
How Quasiturbine Engines Work
The quasiturbine engine takes the Wankel concept and improves on it: Instead of three combustion chambers, it has four, and the setup of a quasiturbine allows for continual combustion. That means greater efficiency than any other engine in its class. Learn about the quasiturbine and why it might be the most promising internal combustion engine yet.
The automobile transmission system is composed of a series of crankshaft, flywheel, clutch, transmission, drive shaft, drive axle, etc. with elasticity and rotational inertia. The power is outputted by the engine and transmitted to the drive wheels through the clutch, transmission after the torque increase and change, drive shaft, main reducer, differential and half shaft.
How Camshafts Work
The camshaft has a huge effect on engine performance. It helps let the air/fuel mixture into the engine and get the exhaust out. Learn all about the camshaft and how a new one can radically change an engine's behavior.
How Superchargers Work
Overhal gaskets are parts used for sealing in automobiles, mainly made of elastomers
Since the invention of the internal combustion engine, automotive engineers, speed junkies and race car designers have been searching for ways to boost its power. One way is by installing a supercharger, which forces more air into the combustion chamber. Learn how superchargers can make an engine more efficient.
How Turbochargers Work
When people talk about race cars, or high-performance sports cars, the topic of turbochargers almost always comes up. Turbochargers use some very cool technology to make an engine more powerful, but the concept is really quite simple. Find out how turbos increase the speed. The engine repair kit is very necessary.
How Fuel Injection Systems Work
The last carburetor-equipped car came off the assembly line in 1990. Since then, fuel injectors have been the primary means of getting gasoline into the engine cylinder so it can combust and you can drive. Find out how fuel-injection systems work.
Power Train
How Manual Transmissions Work
The cylinder head is mounted on top of the cylinder block, sealing the cylinder from above and forming the combustion chamber. It is often in contact with high temperature and high pressure gas, so bear a large thermal and mechanical load.
If you drive a stick-shift car, then you may have a few questions floating around in your head. Have you ever wondered, What would happen if I were to accidentally shift into reverse while I am speeding down the freeway? Would the entire transmission explode? Find out all about manual transmissions.
How Automatic Transmissions Work
Automatic transmissions take the work out of shifting. A truly amazing mechanical system, the automatic transmission in a car accomplishes everything a manual transmission does, but it does it with one set of gears. Learn how the whole setup works.
How Clutches Work
You probably know that any car with a manual transmission has a clutch -- it connects and disconnects the engine and transmission. But did you know that automatics have clutches, too? Learn how the clutch in your car works, and find out about some interesting and perhaps surprising places where clutches can be found.
How CVTs Work
In a regular transmission, the gears are literal gears -- interlocking, toothed wheels. Continuously variable transmissions, on the other hand, don't have interlocking gears. The most common type operates on a pulley system. Learn all about the smooth-operating, ultra-efficient CVT.
How Differentials Work
Without a differential, the driven wheels (front wheels on a front-wheel drive car or rear wheels on a rear-wheel drive car) would have to be locked together, forced to spin at the same speed. Find out how this essential component allows the wheels to rotate at different speeds.
Braking System (including braking pads and braking shoe)
In the cylinder block of the car engine, there are several waterways for cooling water circulation, and placed in the front of the car radiator (commonly known as the water tank) through the water pipe connected to form a large water circulation system, the upper outlet of the engine, equipped with a water pump, driven by the fan belt, the engine block waterway hot water pump out, the cold water pumped into.
A car’s brakes are probably the most critical system on the vehicle -- if they go out, you have a major problem. Thanks to leverage, hydraulics and friction, braking systems provide incredible stopping power. Find out what happens after you push the brake pedal.
How Disc Brakes Work
Disc brakes are the most common brakes found on a car's front wheels, and they're often on all four. This is the part of the brake system that does the actual work of stopping the car. Find out all about disc brakes -- even when to replace the pads.
How Anti-lock Brakes Work
Stopping a car in a hurry on a slippery road can be challenging at best and at worst, very, very scary. Anti-lock braking systems (ABS) help alleviate the danger. Learn how anti-lock brakes prevent skidding, check out what that sputtering is and find out how effective they really are.
How Power Brakes Work
Power brakes are fairly ingenious machines -- they let you stop a car with a simple twitch of your foot. The concept at the heart of the power braking system is force multiplication -- a whole lot of force multiplication. Get inside the black cannister that provides the power.
How Master Cylinders and Combination Valves Work
We all know that pushing down on the brake pedal slows a car to a stop. We depend on that every day when we drive. But how does this happen? The master cylinder provides the pressure that engages your car brakes. Learn how the master cylinder works with the combination valve to make sure you can brake safely.
Steering, Suspension and Tires
How Steering Works
When it comes to crucial automotive systems, steering is right up there with the engine and the brakes. Power steering systems make the job a whole lot easier, and the internal workings are pretty cool. What happens when you turn your car is not as simple as you might think. Find out all about car steering systems.
How Car Suspensions Work
All of the power generated by a car engine is useless if the driver can't control the car. The job of a car suspension is enormous: maximize the friction between the tires and the road surface, provide steering stability and ensure the comfort of the passengers. Learn how car suspensions work and where the design is headed in the future.
How Tires Work
In the market for new set of tires? All of the different tire specifications and confusing jargon the tire sales clerks or "experts" are shouting at you making your head feel like a tire spinning out of control? Find out all about car tires, including what those sidewall symbols mean!
How Self-inflating Tires Work
Self-inflating tires perform two crucial functions: They automatically maintain ideal tire pressure for safety and performance in standard conditions, and they allow the driver to alter psi on the fly to adjust to changing terrain. Learn how self-inflating systems like the Hummer's CTIS work.
How Sequential Gearboxes Work
Combine the ease of an automatic with the driver control of a manual, and what you've got is a sequential manual transmission. Instead of having to navigate an H pattern, a simple forward push advances the gear. It's the transmission used by race cars and an increasing number of high-performance street cars. Learn all about the sequential gearbox.
How Torque Converters Work
Cars with an automatic transmission have no clutch that disconnects the transmission from the engine. Instead, they use an amazing device called a torque converter. Find out all about the torque converter.
Electrical System
How Wires, Fuses and Connectors Work
Wires, fuses and connectors - they may sound like the most mundane parts on your car, but they are essential. Yeah, they help keep the tunes going for a long ride, and they make reading that map at night a lot easier. But, they're also necessary for things like the cooling fan in the engine and your anti-lock brakes. Learn why wires, fuses and connectors are so important!
How Ignition Systems Work
A car's ignition system is the key component that helps the engine produce maximum power and minimum pollution. Find out how much is riding on a well-timed spark.
How Car Computers Work
Cars seem to get more complicated with each passing year. Today's cars might have as many as 50 microprocessors on them. Essentially, you're driving around in a giant computer. Learn all about the various computer systems that control your car.
How Windshield Wipers Work
Without windshield wipers, a rain storm would make cars pretty much useless. What began as a hand-cranked system is now automatic, and only getting more so: There are now some windshield wipers that can actually sense rain. Learn the mechanics behind this essential automotive tool.
Exhaust System
How Catalytic Converters Work
A catalytic converter is one of the most important parts of a car's emissions control system. It treats the exhaust before it leaves the car and removes a lot of the pollution. Learn how catalytic converters reduce pollutants and help you pass the emissions test.
How Mufflers Work
Every car out there has a muffler -- it performs the crucial job of turning thousands of explosions per minute into a quiet purr. Mufflers use some pretty neat technology to dim the roar of an engine. Learn about the principles that make it work.
Other Car Parts
How Odometers Work
Mechanical odometers have been counting the miles for centuries. Although they are a dying breed, they are incredibly cool inside. Learn how this simple device tracks distance and find out about digital odometers.
How Cooling Systems Work
A car engine produces so much heat that there is an entire system in your car designed to cool the engine down to its ideal temperature. In fact, the cooling system on a car driving down the freeway dissipates enough heat to heat two average-sized houses! Learn all about fluid-based cooling systems.
|
|
|
Understanding Compressors |
Posted by: bbkowj258a - 09-03-2021, 06:55 AM - Forum: Welcomes and Introductions
- No Replies
|
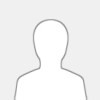 |
Compressors are mechanical devices used to increase pressure in a variety of compressible fluids, or gases, the most common of these being air. Compressors are used throughout industry to provide shop or instrument air; to power air tools, paint sprayers, and abrasive blast equipment; to phase shift refrigerants for air conditioning and refrigeration; to propel gas through pipelines; etc. As with pumps, compressors are divided into centrifugal (or dynamic or kinetic) and positive-displacement types; but where pumps are predominately represented by centrifugal varieties, compressors are more often of the positive- displacement type. They can range in size from the fits-in-a-glovebox unit that inflates tires to the giant reciprocating or turbocompressor machines found in pipeline service. Positive-displacement compressors can be further broken out into reciprocating types, where the piston style predominates, and rotary types such as the helical screw and rotary vane.
In this guide, we will use both of the terms compressors and air compressors to refer mainly to air compressors, and in a few specialized cases will speak to more specific gases for which compressors are used.
Types of Air Compressor
Compressors may be characterized in several different ways, but are commonly divided into types based on the functional method used to generate the compressed air or gas. In the sections below, we outline and present the common compressor types. The types covered include:
Piston
Diaphragm
Helical Screw
Sliding vane
Scroll
Rotary Lobe
Centrifugal
Axial
Due to the nature of the compressor designs, a market also exists for the rebuilding of air compressors, and reconditioned air compressors may be available as an option over a newly purchased compressor, including special process gas compressors.
Piston Compressors
Piston compressors, or reciprocating compressors, rely on the reciprocating action of one or more pistons to compress gas within a cylinder (or cylinders) and discharge it through valving into high pressure receiving tanks. In many instances, the tank and compressor are mounted in a common frame or skid as a so-called packaged unit. While the major application of piston compressors is providing compressed air as an energy source, piston compressors are also used by pipeline operators for natural gas transmission. Piston compressors are generally selected on the pressure required (psi) and the flow rate (scfm). A typical plant-air system provides compressed air in the 90-110 psi range, with volumes anywhere from 30 to 2500 cfm; these ranges are generally attainable through commercial, off-the-shelf units. Plant-air systems can be sized around a single unit or can be based on multiple smaller units which are spaced throughout the plant.
To achieve higher air pressures than can be provided by a single stage compressor, two-stage units are available. Compressed air entering the second stage normally passes through an intercooler beforehand to eliminate some of the heat generated during the first-stage cycle.
Speaking of heat, many piston compressors are designed to operate within a duty cycle, rather than continuously. Such cycles allow heat generated during the operation to dissipate, in many instances, through air-cooled fins.
Piston compressors are available as both oil-lubricated and oil-free designs. For some applications which require oil-free air of the highest quality, other designs are better suited.
Diaphragm Compressors
A somewhat specialized reciprocating design, the diaphragm compressor uses a motor-mounted concentric that oscillates a flexible disc which alternately expands and contracts the volume of the compression chamber. Much like a diaphragm pump, the drive is sealed from the process fluid by the flexible disc, and thus there is no possibility of lubricant coming into contact with any gas. Diaphragm air compressors with spare parts are relatively low capacity machines that have applications where very clean air is required, as in many laboratory and medical settings.
Helical Screw Compressors
Helical-screw compressors are rotary compressor machines known for their capacity to operate on 100% duty cycle, making them good choices for trailerable applications such as construction or road building. Using geared, meshing male and female rotors, these units pull gas in at the drive end, compress it as the rotors form a cell and the gas travels their length axially, and discharge the compressed gas through a discharge port on the non-drive end of the compressor casing. The rotary screw compressor action makes it quieter than a reciprocating compressor owing to reduced vibration. Another advantage of the screw compressor over piston types is the discharge air is free of pulsations. These units can be oil- or water- lubricated, or they can be designed to make oil-free air. These designs can meet the demands of critical oil-free service.
Sliding Vane Compressors
A sliding-vane compressor relies on a series of vanes, mounted in a rotor, which sweep along the inside wall of an eccentric cavity. The vanes, as they rotate from the suction side to the discharge side of the eccentric cavity, reduce the volume of space they are sweeping past, compressing the gas trapped within the space. The vanes glide along on an oil film which forms on the wall of the eccentric cavity, providing a seal. Sliding-vane compressors cannot be made to provide oil-free air, but they are capable of providing compressed air that is free of pulsations. They are also forgiving of contaminants in their environments owing to the use of bushings rather than bearings and their relatively slow-speed operation compared to screw compressors. They are relatively quiet, reliable, and capable of operating at 100% duty cycles. Some sources claim that rotary vane compressors have been largely overtaken by screw compressors in air-compressor applications. They are used in many non-air applications in the oil and gas and other process industries.
Scroll Compressors
Scroll air compressors use stationary and orbiting spirals which decrease the volume of space between them as the orbiting spirals trace the path of the fixed spirals. Intake of gas occurs at the outer edge of the scrolls and discharge of the compressed gas takes place near the center. Because the scrolls do not contact, no lubricating oil is needed, making the compressor intrinsically oil-free. However, because no oil is used in removing the heat of compression as it is with other designs, capacities for scroll compressors are somewhat limited. They are often used in low-end air compressors and home air-conditioning compressors.
Rotary Lobe Compressors
Rotary-lobe compressors are high-volume, low-pressure devices more appropriately classified as blowers. To learn more about blowers, download the free Thomas Blowers Buying Guide.
Centrifugal Compressors
Centrifugal compressors rely on high-speed pump-like impellers to impart velocity to gases to produce an increase in pressure. They are seen mainly in high-volume applications such as commercial refrigeration units in the 100+ hp ranges and in large processing plants where they can get as large as 20,000 hp and deliver volumes in the 200,000 cfm range. Almost identical in construction to centrifugal pumps, centrifugal compressors increase the velocity of gas by throwing it outward by the action of a spinning impeller. The gas expands in a casing volute, where its velocity slows and its pressure rises.
Centrifugal compressors have lower compression ratios than displacement compressors, but they handle vast volumes of gas. Many centrifugal compressors use multiple stages to improve the compression ratio. In these multi-stage compressors, the gas usually passes through intercoolers between stages.
Axial Compressors
The axial Low-Pressure Water Lubricating Oil-free Compressor achieves the highest volumes of delivered air, ranging from 8000 to 13 million cfm in industrial machines. Jet engines use compressors of this kind to produce volumes over an even wider range. To a greater extent than centrifugal compressors, axial compressors tend toward multi-stage designs, owing to their relatively low compression ratios. As with centrifugal units, axial compressors increase pressure by first increasing the velocity of the gas. Axial compressors then slow the gas down by passing it through curved, fixed blades, which increases its pressure.
Power and Fuel Options
Air compressors may be powered electrically, with common options being 12 volt DC air compressors or 24 volt DC air compressors. Compressors are also available that operate from standard AC voltage levels such as 120V, 220V, or 440V.
Alternative fuel options include air compressors that operate from an engine that is driven off of a combustible fuel source such as gasoline or diesel fuel. Generally, electrically-powered compressors are desirable in cases where it is important to eliminate exhaust fumes or to provide for operation in settings where the use or presence of combustible fuels is not desired. Noise considerations also play a role in the choice of fuel option, as electrically driven air compressors typical exhibit lower acoustical noise levels over their engine-driven counterparts.
Additionally, some air compressors may be powered hydraulically, which also avoids the use of combustible fuel sources and the resulting exhaust gas issues.
Compressor Machine Selection in an Industrial Setting
In selecting air compressors for general shop use, the choice will generally come down to a piston compressor or a helical-screw compressor. Piston compressors tend to be less expensive than screw compressors, require less sophisticated maintenance, and hold up well under dirty operating conditions. They are much noisier than screw compressors, however, and are more susceptible to passing oil into the compressed air supply, a phenomenon known as “carryover.” Because piston compressors generate a great deal of heat in operation, they have to be sized according to a duty cycle—a rule of thumb prescribes 25% rest and 75% run. Radial-screw Variable Frequency Water Lubricating Oil-Free Screw Compressor can run 100% of the time and almost prefer it. A potential problem with screw compressors, though, is that oversizing one with the idea of growing into its capacity can lead to trouble as they are not particularly suited to frequent starting and stopping. Close tolerance between rotors means that compressor needs to remain at operating temperature to achieve effective compression. Sizing one takes a little more attention to air usage; a piston compressor may be oversized without similar worries.
An autobody shop which uses air constantly for painting might find a radial-screw compressor with its lower carryover rate and desire to run continuously an asset; a general auto-repair business with more infrequent air use and low concern for the cleanliness of the supplied air might be better served with a piston compressor.
Regardless of the compressor type, compressed air is usually cooled, dried, and filtered before it is distributed through pipes. Specifiers of plant-air systems will need to select these components based on the size of the system they design. In addition, they will need to consider installing filter-regulator-lubricators at the supply drops.
Larger job site compressors mounted on trailers are typically rotary-screw varieties with engine drives. They are intended to run continuously whether the air is used or dumped.
Although dominant in lower-end refrigeration systems and air compressors, scroll compressors are beginning to make inroads into other markets. They are particularly suited to manufacturing processes that demand very clean air (class 0) such as pharmaceutical, food, electronics, etc. and to cleanroom, laboratory, and medical/dental settings. Manufactures offer units up to 40 hp that deliver nearly 100 cfm at up 145 psi. The larger capacity units generally incorporate multiple scroll compressors as the technology does not scale up well once beyond 3-5 hp.
If the application involves compressing hazardous gases, specifiers often consider diaphragm or sliding-vane compressors, or, for very large volumes to compress, kinetic types.
|
|
|
Basics of acid dyes, disperse dyes, and reactive dyes. |
Posted by: bbkowj258a - 09-03-2021, 06:53 AM - Forum: Welcomes and Introductions
- No Replies
|
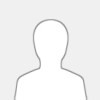 |
Acid dyes with improved light fastness have become important particularly in connection with the usage of acid dyes in information recording systems. The inferior light fastness may be due to several reasons. Auto oxidation reaction of dyes is generally considered to occur on exposure to ultraviolet (UV) radiation and prevented by the addition of UV absorbers or antioxidants such as hindered phenols or naphthylamines. In recent years as an approach to the photostabilisation of dyes attempts have been made to prepare dyes with built-in photostabilising moiety.
Acid dyes, named for their application under acid conditions, are reasonably easy to apply, have a wide range of colours and, depending on dye selection, can have good colour fastness properties. The dyes are divided into three categories according to their levelling and fastness properties, namely levelling, milling and super milling dyes.
Levelling, or equalising, acid dyes have good levelling properties and are applied from a bath containing sulphuric acid to achieve exhaustion. Because of the ease of migration of dye molecules into and out of the fibre, equalising acid dyes have poor fastness to washing, and are normally used for pale, bright shades where fastness is not paramount.
Milling acid dyes have a greater substantivity for the fibre than levelling dyes, and therefore have poorer levelling properties. These dyes have better fastness properties than levelling acid dyes, and have reasonable wet fastness, particularly if alkaline milling is to take place in a subsequent process.
Super milling acid, or neutral dyeing, dyes are applied in a similar way to milling acid dyes, except that greater control over the strike rate of the dye is exercised. Super milling dyes give very good fastness and, with an appropriate after-treatment, can satisfy requirements for shades of medium depth, especially where reasonable brightness is needed.
Thus there are considerablef differences in the properties and application methods within the whole range of acid dyes. The dyer must take care to ensure that the dyes chosen in combination are from the same group and have very similar properties.
Disperse dyes are characterised by the absence of solubilising groups and low molecular weight. From a chemical point of view more than 50% of disperse dyes are simple azo compounds, about 25% are anthraquinones and the rest are methine, nitro or naphthoquinone dyes. Disperse dyes are used mainly for polyester, but also for cellulose acetate and triacetate, polyamide and acrylic fibres. Disperse dyes are supplied as powder and liquid products. Powder dyes contain 40–60% of dispersing agents, while in liquid formulations the content of these substances is in the range of 10–30%. Formaldehyde condensation products and lignin sulphonates are widely used for this purpose. The following chemicals and auxiliaries are used for dyeing with disperse dyes;
Dispersants: although all disperse dyes already have a high content of dispersants, they are further added to the dyeing liquor and in the final washing step.
Carriers: for polyester fibre, dyeing with disperse dyes at temperatures up to 100°C requires the use of carriers. Because of environmental problems associated with the use of carriers, polyester is preferably dyed under pressure at temperature >100°C without carriers. However, carrier dyeing is still important for polyester-wool blends.
Thickeners: polyacrylates or alginates are usually added to the dye liquor in padding processes.
Reducing agents (mainly sodium hydrosulphite) are added in solution with alkali in the final washing step for the removal of unfixed surface dye.
Owing to their low water solubility, disperse dyes are largely eliminated by adsorption on activated sludge in waste water treatment plants. Some disperse dyes contain organic halogen, but they are not expected to be found in the effluent after waste water treatment because of their adsorption on activated sludge.
Reactive dye introduced on 1956 and for the first time dyeing became possible by direct chemical linkage between dye and fiber (Shenai, 1993). But all classes of reactive dye do not react in the same manner. So the group of dyes used for a ternary shade should have compatibility among themselves. Importantly, reactive dyes in a mixture should all exhaust and react with the fiber at about the same rate so that the shade builds up accurately. Dyes which are from different ranges, with different reactive groups, should not be used together because of their different dyeing character and reactivity.
Compatible dyeing performance requires careful control of the dyeing parameters such as temperature, salt and alkali concentrations, the dyeing time and the liquor ratio. There is often a doubt about the particular reactive group presents in a reactive dye. For that reason in most of the cases selection of dyes depends on the maker’s recommendations (Broadbent, 2001).
Shenai (1997) discussed in detail about the chemistry of vinyl sulphone dyes like Remazol class. Common salt and alkali plays the vital role in exhaustion and fixation of these dyes and addition of salt to the dye bath before adding the alkali is also essential. In reactive dyeing, though water is the competitor for reaction with the dye, cellulose fiber takes part in the reaction in majority. Because the substantivity of reactive dye to the fiber is greater than that to water (Chinta and Vijaykumar 2013).
But factually all the reactive dyes do not have the same range of substantivity and reactivity, and intermediates are usually used. Reactivity is compulsory for these dyes but higher reactivity of a dye can spoil the dyeing due to hydrolysis. So the compatibility of the dyes used for ternary shades should be analyzed carefully to make the maximum utilization of each dyestuff especially when the reactive groups in them are different.
|
|
|
What is injection molding? |
Posted by: bbkowj258a - 09-03-2021, 06:52 AM - Forum: Welcomes and Introductions
- No Replies
|
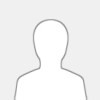 |
Precision injection molding of high performance components requires primary error sources affected the molded component to be identified and isolated such that these errors can be reduced if needed. To systematically isolate and quantify the contribution of misalignment, thermal variation and component warpage to the accumulated error observed on the component, a methodology is presented and tested around an existing mold which produced parts with high dimensional variability. The mold featured two concentric guide pillars on opposite sides of the parting plane and rectangular centering block elements at three locations. Mold displacements at the parting plane were measured through the incorporation of three eddy-current linear displacement sensors. Thermal error sensitivity was investigated using FEM simulations such that the induced variability from thermal expansion and filling phase was identified and quantified. Finally, molded component warpage was isolated and quantified, again by the means of FEM simulation. The results were confirmed by using the mold on two injection molding machines to produce an array of parts whose key dimensions were measured.
Micro/nanostructured components play an important role in micro-optics and optical engineering, tribology and surface engineering, and biological and biomedical engineering, among other fields. Precision glass molding technology is the most efficient method of manufacturing micro/nanostructured glass components, the premise of which is meld manufacturing with complementary micro/nanostructures. Numerous mold manufacturing methods have been developed to fabricate extremely small and high-quality micro/nanostructures to satisfy the demands of functional micro/nanostructured glass components for various applications. Moreover, the service performance of the mold should also be carefully considered. This paper reviews a variety of technologies for manufacturing micro/nanostructured molds. The authors begin with an introduction of the extreme requirements of mold materials. The following section provides a detailed survey of the existing micro/nanostructured automotive mold components manufacturing techniques and their corresponding mold materials, including fixtures and mechanical parts methods. This paper concludes with a detailed discussion of the authors recent research on nickel-phosphorus (Ni-P) mold manufacturing and its service performance.
What is injection molding?
Injection molding is a manufacturing process which is commonly used to create plastic components.
Its ability to produce thousands of complex parts quickly makes it the perfect process for the mass production of plastic components. Essentially, the process involves the injection of plastic at high speed and pressure into a precision mechanical gear parts, which is clamped under pressure and cooled to form the final part.
By melting thermoplastic and injecting it into an aluminium mold at high speed and pressure, manufacturers can create multiple complex parts at once. When the parameters of the process are controlled correctly, there’s also little need for finishing and processing the manufactured part, making it more cost effective and efficient.
Although it’s one of the oldest manufacturing processes around, its speed and cost-efficiency is what continues to make it a popular choice with worldwide manufacturers. Today’s injection molding machines are fast, accurate and produce consistently high-quality components at scale.
How does injection molding work?
Although the process may seem simple, there are many elements involved which can alter and ruin the overall quality of the plastic component produced. In order to make a high-quality part, experienced manufacturers select the right thermoplastic (the material used to create the part), connector mold parts (which shapes the part), temperature and injection pressures to ensure the final part meets customer requirements.
Before we talk about the specific parameters that need to be controlled within the process, how does injection molding actually work?
Step 1: Feeding and heating the plastic
To start, a thermoplastic or combination of thermoplastics are fed into an injection molding machine. The plastics, which turn to liquid when heated, are fed into the hopper at the top of the machine in solid pellet form.
The pellets pass through the machine and into a temperature-controlled cylinder called the machine barrel. Here, the plastic pellets are heated until the thermoplastic is molten.
The temperature of the barrel and the plastic needs to be carefully monitored to make sure the thermoplastic doesn’t overheat and burn or scorch the final part.
Step 2: Pre-injection process
Before the molten plastic is injected, the tool, which is usually made up of a fixed half called the cavity and a moving half called the core, closes.
When closed, a clamp applies pressure to the tool, ready for the injection of the plastic.
The screw within the barrel of the machine also screws back to its set point so the plastic can enter the barrel, ready to be injected.
Step 3: Plastic injection
Once the clamp pressure is at an optimum level, the plastic is injected by the screw at high speed and pressure into the cavity. A gate inside the tool helps to control the flow of the plastic.
To make sure no damage is done to the final components, it’s important that the manufacturer monitors the injection pressure of the plastic and that they have the expertise to maintain and use the molds and tools correctly.
This ensures they are creating high-quality and consistent parts from their injection molding process, like packaging mold components.
Step 4: Forming the part
When the tool cavity is mostly full of liquid, a holding phase begins. This is where the part in held under high pressure so it can start to take its final form.
After a set holding time, the screw will screw back to its set point. This happens at the same time as the cooling phase of the cycle, which allows the thermoplastic to set in its final form.
Once the set cooling time has passed, the mold opens and ejector pins or plates push the new part out of the tool, and there are also custom mold components. These fall on to a conveyor belt ready to be finished and packed.
Step 5: Part finishing
Depending on the final application of the part, the molded component may require some finishing, including dyeing, polishing, or removing of excess material.
These processes are unique to each part and are completed before they’re packed and distributed to customers.
By picking and checking products by hand, as well as performing regular quality checks, experienced manufacturers can make sure they’re producing consistent, high-quality parts for their customers.
|
|
|
What is Grinding? |
Posted by: fw115ww - 09-03-2021, 03:23 AM - Forum: Welcomes and Introductions
- No Replies
|
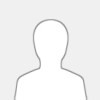 |
Grinding takes an abrasive — often attached to a grinding wheel — and uses its many grains to cut a workpiece. Variations on this process are useful for a wide variety of applications.
On its surface, grinding seems simple: a machine takes a rotating tool (usually a wheel) with abrasive grains and applies it to a workpiece’s surface to remove material. Each grain is its own miniature cutting tool, and as grains dull, they tear from the tool and make new, sharp grains prominent.
But there are many variations, approaches and considerations for this type of machining, each of which is particularly effective for certain applications with certain materials.
Principles of Grinding
In all forms of grinding, three different interactions occur between the abrasive and the machined material. Cutting occurs where the abrasive grain is sufficiently exposed to penetrate the workpiece material and curl a chip, and sufficient clearance exists between the grain, bond and workpiece to flush the chip with coolant or throw it away by wheel action. Plowing takes place when the grain is unable to get enough penetration to lift a chip, instead pushing the material ahead of the abrasive edge. Sliding happens when a lack of cut depth, insufficient clearance or a grit staying on the wheel after dulling results in rubbing or creating slide marks on the workpiece surface. Grinding process control balances these three interactions to achieve the desired parameters.
These interactions feed into three major commercial grinding processes: rough grinding, precision grinding and ultra-precision grinding. Rough grinding maximizes the metal removed at the cost of surface finish. It primarily sees use in cutting off billets, grinding weld beads smooth and snagging gates and risers from castings. Additional surface finishing passes typically take place afterward — in particular, a “spark-out” pass relieves some of the stress on the machine tool and uses plowing to impart a better surface finish and size tolerance. Precision grinding is a middle-ground between metal removal and part size control, and serves as the basis for creep feed grinding, slot grinding and high-efficiency deep grinding. In ultra-precision grinding, little to no actual cutting occurs, but sliding action from very fine grains rubs the workpiece surface to a high finish. Most surface finishing processes, such as lapping and polishing, are examples of this type of grinding.
Hundreds of different variables can affect the interaction between the abrasive and the workpiece, but they generally come down to machine tool, work material, wheel selection and operational factors. Balancing these by setting up a part run that fits within the known parameters of all four categories provides a baseline that gradual parameter adjustment can improve.
Grinding Wheels
Grinding wheels have two major components: the abrasive grains and the bond. The relative percentages of grain and bond, and their spacing on the wheel, determine the wheel’s structure. Different types of grains work better on different projects, as do different types and “grades” (i.e. strengths) of bond. Broad areas of grinding need coarser grits and softer grades, with smaller areas requiring finer grits and harder grades to withstand the greater unit pressure.
Straight wheels are the most traditional type of grinding wheel, with the grinding face on the periphery of the wheel. Recessed wheels are variations on this form, featuring a recessed center to fit on a machine spindle flange assembly. The other major type of wheel shape uses a cutting face on the side of the wheel — names for this type of wheel include cylinder wheels, cup wheels and dish wheels, depending on the particular shape. For these wheels, bonded abrasive sections of various shapes, also known as “segments,” are assembled to form a continuous or intermittent side grinding wheel.
Operational Basics
Although speeds for grinding wheels and cutting wheels are measured in sfm or smm, wheels are often rated in rpm. It is important never to operate a grinding wheel over its rpm limit — most experts recommend never mounting a wheel on a machine that can exceed the wheel’s limit.
As speeds increase, each grain cuts and wears less. This emulates a harder grade. Vitrified bonds work up to 6,500 sfm, with organic bonds handling up to around 9,500 sfm. Higher speeds will require specially made grains.
Work speed defines the speed at which a grinding wheel passes over a workpiece or rotates around a center. High work speeds lower the heat retention and reduce the risk of thermal damage. Both high work speeds and reducing the diameter of the wheel result in increased grain depth of cut, performing like a softer grade wheel.
Traverse distance, or crossfeed, is the distance a workpiece moves across the face of the wheel. Lowering the traverse distance to no more than one-quarter of the wheel width improves surface finish, but slows down productivity. Increasing the crossfeed to one-half the wheel’s width or above boosts productivity, but lowers surface finish.
Different types of grinding use different methodologies to determine the work material removal per unit of width, but one consistently useful metric for shops is the grinding gratio, or g-ratio. This is the ratio of volume of work removed to volume of wheel consumed (or, volume of work removed ÷ volume of wheel worn). From a cost standpoint, a higher g-ratio is better.
Types of Grinding
Grinding operations come in many types, with this article covering six major types and several of the subtypes within.
Cylindrical grinding is a common type of grinding in which both the wheel and the workpiece rotate. The workpiece is either fixed and driven between centers, or driven by a revolving chuck or collet while supported in a center. This operation can take place with either traverse movements, where the wheel traverses axially along the part, or plunge movements, where the wheel is thrust into the part. Straight wheels are most commonly used in cylindrical grinding, with common cylindrical grinding machines being plain cylindrical (or roll) grinders, centerless grinders and inside- or outside-diameter grinders. Internal cylindrical grinding does the internal diameter grinding of bores and holes, generating size and concentricity within millionths of an inch. The grinding wheels tend to range in diameter from half an inch to three inches. This small size introduces rapid wear, making CBN and diamond wheels in crush dressable and vitrified form popular for these applications.
Surface grinding, such as stainless steel grinding, involves grinding a plane surface by feeding the workpiece beneath a rotating grinding wheel. Like cylindrical grinding, it operates in two general formats. The workpiece may travel traversely under the wheel and move back and forth beneath a grinding wheel mounted on a horizontal spindle, or it may move in circles on a rotary table beneath a vertical spindle that cuts on the face of the grinding wheel or grinding segment. Applications for this grinding type may grind a surface flat or introduce grooves by grinding straight channels into the workpiece. While milling can complete these tasks, grinding improves surface finish, has less expensive tooling and allows contours to be dressed into the profile of the wheel — making it much more cost-effective for very hard or abrasive surfaces.
Centerless grinding creates cylindrical forms at extremely close tolerances. This type of grinding eliminates the need for center holding by supporting the workpiece at three separate points: the grinding wheel, feed wheel and work support blade. Nothing actually clamps the workpiece in place, so each piece flows freely for continuous production (also known as “throughfeed centerless grinding”). The grinding wheel, during ordinary metal grinding, and the feed wheel rotate in the same direction, while the workpiece rotates in the opposite direction between them. The rotation keeps the workpiece down, while the work support blade (slightly angled to raise the workpiece above the centerline for better cylindricity) holds it up. The work support blade should always be at least as long as the grinding wheel is wide. Centerless grinding also comes in three forms. Throughfeed centerless grinding is used on straight cylindrical workpieces without interfering shoulder or projections, and involves the offset axis feed wheel feed the workpiece past the grinding wheel to a discharge position. Infeed grinding (also called plunge centerless grinding) is best when a workpiece has projections, irregular shapes, varying diameters or shoulders, and works best for profiles and multi-diameter workpieces. In this submethod, feed wheels above the grinding wheel feed the workpiece downward, with no lateral movement during grinding. Endfeed centerless grinding grinds conically tapered cylindrical sections like shanks on A and B taper drill bits. Here, the feed wheel, grinding wheel and work blade are set up in a fixed relationship to each other, then two wheels are dressed to a shape matching the end taper of the workpiece and the workpiece is fed from the front of the grinding machine until it reaches an end stop.
Creep feed grinding is a slow, one-pass operation that makes a deep cut of up to one inch in steel materials at low table speeds between 0.5 and 1 ipm. It is not suitable for conventional grinding machines, but for those which are compatible with it, it offers high productivity and cost effectiveness. Creep feed grinding is a plunge operation with high horsepower requirements, and which also requires a heavy flow of cutting fluid close to the nip to remove chips and cool the work. Continuous dressing at about 20 to 60 millionths per revolution — preferably with a diamond roll — reduces cutting times of fixed machine cutting and keeps the wheel sharp. When a second pass is required, it is typically of no more than 0.002 inch deep to “clean up” the workpiece.
Snagging is a rough grinding application that removes unwanted metal with little consideration of surface finish. As such, it uses durable straight and straight cup wheels in horizontal and straight shaft grinding machines, although flaring cup wheels are used in right-angle grinders and various round and square-tipped cones and plugs also see use. Typical applications include removing unwanted metal on castings; removing flaws and cracks; removing gates, risers and parting lines; rough beveling; grinding down heavy welds; and preparing surfaces for cleaning or painting.
Cut-off operations use an abrasive wheel as an alternative to the laser, abrasive water jet, metal saw, friction saw and oxyacetylene or plasma arc torch. A study from Norton Abrasives demonstrated that the abrasive wheel can outperform these other methods with ferrous materials, and that the abrasive wheel is faster and less expensive for nonferrous materials than the common metal saw choice. The abrasive wheel provides more cutting points than a saw, and cuts just as thoroughly at a speed of 2 or 3 miles per minute. Cut-off wheels should run at the highest possible speed, with one horsepower for every inch of wheel diameter. If this proves impossible, use a softer wheel. Production jobs use non-reinforced wheels, with non-reinforced shellac wheels for applications requiring extreme versatility and quality of cut. Reinforced wheels are compatible with portable cut-off, swingframe, locked head push-through and foundry chop stroke operations.
|
|
|
Key Door Hardware Components for Safety and Security |
Posted by: fw115ww - 09-03-2021, 03:22 AM - Forum: Welcomes and Introductions
- No Replies
|
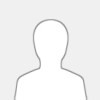 |
Understanding door hardware options and opportunities is the first step in turning threats and weaknesses into strengths. Entry doors with window mesh might be in bad condition, with broken closers, loose hinges, doors that sag or are sticking, latches that do not align properly with the strike, and wide gaps between the door and frame that pry open easily. Other access points might use old technology.
Poorly maintained hardware offers the easiest path for unauthorized entry. Old technology is next and soon might become a weakness. Vendors know the best options for meeting ASTM/BHMA standards for the manufacture and testing commercial grade hardware. ANSI Grade 1 hardware is specifically designed for high-traffic areas because it can withstand the highest number of life cycles and is much harder for an active shooter to break through.
Upgrades that deliver greater safety and security include replacing Grade 2 and 3 components with Grade 1 hardware. A further upgrade involves integrating the latest generation of commercial electronic UPVC door locksets, closers, hinge hardware and alarms with a central control system.
Managers need to pay special attention to levels of access to facilities. Authorized personnel need access and, in emergency situations, rapid and safe egress, while unauthorized personnel have to be kept out. Firefighters and other emergency personnel need ease of entry to locate and evacuate people rapidly.
Increasingly, managers are installing card and PIN UPVC door lock systems, and they are rearranging traffic flows to channel visitor traffic at elevator lobbies toward properly staffed, secure reception areas. Only authorized personnel should be able to enter the main building through locked lobby doors.
Among the most common door hardware components upgraded for improved security are the following:
Closers.
Standard and custom door closers include surface-mounted and hidden, heavy-duty closers for high-cycle or windy and drafty conditions, as well as ADA-compliant maximum-force-to-operate closers. A closer’s open cycle compresses the spring and positions the fluid through the open valve for closing. The delay valve allows slower-moving traffic to pass. The closing valve slows closing speed to within 6 inches of the stop. The latching valve accelerates closing for the last 6 inches. Closers need regular adjustment to keep the cycles operating as designed.
Hinges. (UPVC door window hinges)
By removing the hinge pins, an attacker can gain access to a facility through a hinged door with window hinge, even when it is locked. Removing a screw and inserting a special pin prevents an attacker from removing the door from its frame, even if door hinge pins are removed.
Locksets.
Deadbolts, knobs, lock cylinders, levers, and entry handsets are wired and wireless devices that operate via remote-open and turn-on devices and cell phone applications. Replacing mechanical keyed locksets with electro-mechanical locks in the same housing is a low-cost upgrade option. Managers are using electronic remote-controlled devices, such as door roller, cameras, motion sensors, and tamper alarms, to give early warning.
They also can upgrade unguarded remote entry points from mechanical locks and keys to systems that incorporate CCTV and sound. A security guard at a remote point directs the person seeking entry to place his or her badge in front of the camera, verifies the person has the proper clearance and is the same person as shown on the picture badge, and remotely actuates the lock allowing entry.
In an emergency requiring rapid evacuation of the building, all evacuation route doors with window roller are remotely unlocked immediately and simultaneously from a central control. Other common upgrades include the installation of biometric fingerprint readers, facial-recognition systems, and floor-to-ceiling locked turnstiles.
Alarms. Radio-wave tamper alarms can be activated by a vehicle or a person moving through and disturbing a radio wave field. The power source sends radio waves through the antenna surrounding anything the antenna touches , including a door, window door hand tools, fence, vehicle, or unattended building. Audio alarms can be attached or silent-connected to a police station or can activate CCTV or access -control systems.
Cybersecurity. An organization’s access control computer must have no internet route that might allow hackers to take control. Experts advise preventing malware attacks through Wi-Fi that blocks phishing and spear phishing and prevents malware entry into a system. A cybersecurity expert can a wise safeguard against such attacks.
The list of upgrades might exceed what managers can implement immediately because of cost or time constraints. One effective strategy is to start at the top of the organization’s priority list and work down as far as possible this year, updating the list for budgeting year after year. The main take-away from a successful security strategy is the safety of occupants, but the payback also can include lower lost-opportunity costs and better continuity of normal operations.
|
|
|
Importance of Using Paper Bags |
Posted by: fw115ww - 09-03-2021, 03:20 AM - Forum: Welcomes and Introductions
- No Replies
|
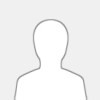 |
Carrybags has become a more convenient way to carry daily necessities and for packaging in small quantities. The well-known form of such bags is in the form of plastic bags. Despite of all known hazards of plastic pollution, it’s prevalent and pervasive in India. Plastic bags are one of the worst and most unnecessary plastic polluters of the earth. Plastic bags are used on a large scale by retailers for a simple reason that plastic bags are much cheaper than paper, cloth or other eco-friendly bags. This paper presents the designing and development of asystem to automate the procedure of paper bags production so as to make its production cost comparable to plastic bags and inherently increase its production rate so as to fulfill the ever increasing demand. We have used micro-controller based design approach which has kept the cost of the system significantly low as compared to PLC based designs and have automated the manufacturing process.
We need small size bags every day for various purposes like grocery, fruits, and vegetables. We use plastic bags for such purposes. Plastic shopping bags have a surprisingly significant environmental impact for something so seemingly innocuous. Plastic shopping bags kill large numbers of wildlife each year. One of the most dramatic impacts is on marine life.So to avoid above harmful effects of Plastic Bags, viable alternative is required which is Paper Bag. Actually, Paper Bag is being used but in very small scale. Conventional Paper Bags requirespecial paper which increases the overall cost of the Paper Bag. This is the main cause due to which use of Paper Bag is less. Also initial investment cost is very much in conventional paper bag making machine. So it cannot be used for small scale production.All these problems are eliminated in the presented machine. Amachine whose initial cost is less, which does not require any special paper, which can be used for small scale production, is developed. Thismachine willhelp a poor family to earn money through small scale production of paper bags.
Paper bags have been gaining popularity since then plastic bags have been banned in various countries and cities. The product is made in two ways; traditionally, i.e. manual which is a manual or technical means i.e. with the help of automated equipment. The second method is much larger. In other words, it requires less workers and more money to buy land and equipment. Based on the core business of nonwoven bag making machine Manufacturers, the machine has 2 different output capabilities with good finish and seamless quality.
Amazing Benefits of Using a Paper Bag Production Machine: -
Excellent Quality: The great advantage of producing a paper bag from an automated machine is the excellent quality one can achieve throughout the production process. When we make paper bags in traditional ways, the quality of the product does not always match the whole production process. It is difficult to maintain the same level of quality per unit. Machine paper bags offer the same quality and precision each time.
Save on Work Expenditure: The introduction of an automated production process machine including slitting machine has reduced the need for workers in the paper industry. One only needs to change the paper roll and collect the finished product after the production process is completed. This saves unnecessary costs on jobs and you can invest in machinery and land instead of workers. Too much machinery and land can lead to a double standard of business production at the same time.
Distributed Production Level: Quality and fast production are two of the most important factors in any production process and automated production for the purpose of the product satisfies both of these factors while improving the quality of production. Save real time financially and increase your productivity compared to handmade methods. You can actually upgrade your product over time.
Energy Saving: An automated machine saves human energy and helps increase productivity. Both man and machine have different working powers. The machine can work more efficiently than man and requires fewer working breaks than man. You can have a good level of mechanical production. The machine can double your production rate at the same time. However, one can only increase the product because everyone has a different working capacity.
Paper bags are gaining importance as these bags are 100% reusable, recyclable and biodegradable and at the same time environment friendly and pose less threat to wildlife. it requires less energy for paper bags to be recycled than plastic bags. Paper bags have come a long way since their beginnings in the mid-eighteenth century when some paper bag manufacturers started developing paper bags that are more hardy and long lasting. The paper bags are generally box-shaped in design that allows them to stand upright and hold more goods. Corporates are using paper bags for promotions, seminars, product packaging and branding purposes.
By selecting high quality paper bag manufacturer can deliver recycled brown color paper bags in big and small quantities, regular and premium paper bags which add a professional touch that consumers love and appreciate. Besides, you can add your own custom brand to any paper bag to promote your business. Read on to discover the importance of paper bags.
1. Plastic bags cause environmental damage such as increase the level of air pollution. Plastic bags not only have adverse effects on our natural habitats, death of many animals. Plastic bags are not renewable and you need UV rays to destroy it, which is harmful for environment.Paper bags on the other hand are environment friendly and can be recycled.
2. Paper bags are usually made from wood. So, these bags can be produced into a new paper like newspapers, magazines or books. Waste papers are also biodegradable so they can be easily degenerate and do not pile up on dump sites.
3. You can also buy them at a very cheap price particularly if they are bought wholesale.
4. Possessing a paper bag is practical and you can use them to bring your groceries and the premium quality paper bags can be used as paper gift bags.
5. Most people nowadays prefer using paper bags because they are easy to carry, neat and can hold lot of items. It adds to your status symbol as they can be embossed and grained to enhance the look.
6. Paper bags are usually used extensively in malls and exhibitions for delivering over the counter products as research shows that paper bags contain at least 35% recycled material.
7. Corporates are nowadays using paper bags for promotions, seminars, product packaging, and branding purposes as they are competitively priced.
8. Paper bag manufacturers can help you to decide the right size and type of paper bags as per your project, budget and quantity.
9. You can choose paper bags with special properties that will seal the freshness and give an aesthetic look to your brand as offset and screen printing is possible.
10. When your product is properly packaged with premium quality paper bags, you can attract more customers which will help in promoting your brand to the targetaudience.
So, if you are ecofriendly and at the same time want to be ahead of your competitors, start using paper bags.
|
|
|
The chemistry of cosmetics |
Posted by: fw115ww - 09-03-2021, 03:18 AM - Forum: Welcomes and Introductions
- No Replies
|
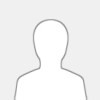 |
Cosmetics materials are not a modern invention. Humans have used various substances to alter their appearance or accentuate their features for at least 10,000 years, and possibly a lot longer.
Women in Ancient Egypt used kohl, a substance containing powdered galena (lead sulphide—PbS) to darken their eyelids, and Cleopatra is said to have bathed in milk to whiten and soften her skin. By 3000 B.C men and women in China had begun to stain their fingernails with colours according to their social class, while Greek women used poisonous lead carbonate (PbCO3) to achieve a pale complexion. Clays were ground into pastes for cosmetic use in traditional African societies and indigenous Australians still use a wide range of crushed rocks and minerals to create body paint for ceremonies and initiations.
Today, cosmetics are big business. According to the 2011 Household Expenditure Survey, conducted every five years by the Australian Bureau of Statistics, Australians spend around $4.5 billion on toiletries and cosmetic products every year. Cosmetic advertising, previously directed mainly at women, is now targeting a wider audience than ever.
What is a cosmetic?
In Australia, a cosmetic is defined under the Industrial Chemical (Notification and Assessment) Act 1989 as ‘a substance or preparation intended for placement in contact with any external part of the human body' (this includes the mouth and teeth). We use cosmetics to cleanse, perfume, protect and change the appearance of our bodies or to alter its odours. In contrast, products that claim to ‘modify a bodily process or prevent, diagnose, cure or alleviate any disease, ailment or defect’ are called therapeutics. This distinction means that shampoos and deodorants are placed in the cosmetics category, whilst anti-dandruff shampoos and antiperspirants are considered to be therapeutics.
Regulation and safety
In Australia, the importation, manufacture and use of chemicals—including those used in cosmetics—are regulated by the Australian Government’s National Industrial Chemicals Notification and Assessment Scheme (NICNAS). NICNAS works to ensure that chemicals used in consumer products do not cause significant harm to users or to the environment.
In the case of cosmetics, every ingredient contained within the product must be scientifically assessed and approved by NICNAS before being manufactured or imported into Australia and before they can be used in consumer products. Where appropriate, NICNAS sets limits on the level at which a chemical can be used in a product and also conducts reviews on chemicals when new evidence arises.
Cosmetic products that make an additional therapeutic claim (such as moisturisers that also lighten the skin) are regulated by a different organisation—the Therapeutic Goods Administration (TGA).
Cosmetics and other personal care items must also be labelled in accordance with the Trade Practices (Consumer Product Information Standards, Cosmetics) Regulations 1991. This regulation requires that all intentionally added ingredients are listed on the product label, and is enforced by the Australian Competition and Consumer Commission (ACCC).
What do cosmetics contain?
There are thousands of different cosmetic products on the market, all with differing combinations of ingredients. In the United States alone there are approximately 12,500 unique chemical ingredients approved for use in the manufacture of personal care products.
A typical product will contain anything from 15–50 ingredients. Considering the average woman uses between 9 and 15 personal care products per day, researchers have estimated that, when combined with the addition of perfumes, women place around 515 individual chemicals on their skin each day through cosmetic use.
But what exactly are we putting on our skin? What do those long names on the ingredient list mean and what do they do? While the formula of each product differs slightly, most cosmetics contain a combination of at least some of the following core ingredients: water, emulsifier, preservative, thickener, emollient, colour, flavors and fragrances and pH stabilisers.
Water
If your product comes in a bottle, chances are the first ingredient on the list is going to be water. That’s right, good old H2O. Water forms the basis of almost every type of cosmetic product, including creams, lotions, makeup, deodorants, shampoos and conditioners. Water plays an important part in the process, often acting as a solvent to dissolve other ingredients and forming emulsions for consistency.
Water used in the formulation of cosmetic materials is not your everyday, regular tap water. It must be ‘ultra-pure’—that is, free from microbes, toxins and other pollutants. For this reason your label may refer to it as distilled water, purified water or just aqua.
Emulsifiers
The term emulsifiers refers to any ingredient that helps to keep unlike substances (such as oil and water) from separating. Many cosmetic products are based on emulsions—small droplets of oil dispersed in water or small droplets of water dispersed in oil. Since oil and water don't mix no matter how much you shake, blend or stir, emulsifiers are added to change the surface tension with surfactant materials between the water and the oil, producing a homogeneous and well-mixed product with an even texture. Examples of emulsifiers used in cosmetics include polysorbates, laureth-4, and potassium cetyl sulfate.
Preservatives
Preservatives are important ingredients. They are added to cosmetics to extend their shelf life and prevent the growth of microorganisms such as bacteria and fungi, which can spoil the product and possibly harm the user. Since most microbes live in water, the preservatives used need to be water-soluble, and this helps to determine which ones are used. Preservatives used in cosmetics can be natural or synthetic (man-made), and perform differently depending on the formulation of the product. Some will require low levels of around 0.01%, while other will require levels as high as 5%.
Some of the more popular preservatives include parabens, benzyl alcohol, salicylic kojic acid, formaldehyde and tetrasodium EDTA (ethylenediaminetetra-acetic acid).
Consumers who purchase ‘preservative-free’ products should be aware of their shorter shelf life and be conscious of any changes to the look, feel or odour of the product that may indicate it has gone off.
Thickeners
Thickening agents work to give products an appealing consistency. They can come from four different chemical families:
Lipid thickeners are usually solid at room temperature but can be liquefied and added to cosmetic emulsions. They work by imparting their natural thickness to the formula. Examples include cetyl alcohol, stearic acid and carnauba wax.
Naturally derived thickeners come, as the name suggests, from nature. They are polymers that absorb water, causing them to swell up and increase the viscosity of a product. Examples include hydroxyethyl cellulose, guar gum, xanthan gum and gelatin. Cosmetics with a consistency that is too thick can be diluted with solvents such as water or alcohol.
Mineral thickeners are also natural, and as with the naturally derived thickeners mentioned above, they absorb water and oils to increase viscosity, but give a different result to the final emulsion than the gums. Popular mineral thickeners include magnesium aluminium silicate, silica and bentonite.
The final group are the synthetic thickeners. They are often used in lotion and cream products. The most common synthetic thickener is carbomer, an acrylic acid polymer that is water-swellable and can be used to form clear gels. Other examples include cetyl palmitate, and ammonium acryloyldimethyltaurate.
Emollient
Emollients soften the skin by preventing water loss. They are used in a wide range of lipsticks, lotions and cosmetics. A number of different natural and synthetic chemicals work as emollients, including beeswax, olive oil, coconut oil and lanolin, as well as petrolatum (petroleum jelly), mineral oil, almond oil, glycerine, zinc oxide, butyl stearate and diglycol laurate.
Colouring agents/pigments
Ruby lips, smoky eyes and rosy cheeks; it is the purpose of many cosmetics to accentuate or alter a person’s natural colouring. A huge range of substances are used to provide the rainbow of appealing colours you find in the makeup stand. Mineral ingredients can include iron oxide, mica flakes, manganese, chromium oxide and coal tar. Natural colours can come from plants, such as beet powder, or from animals, like the cochineal insect. The latter is often used in red lipsticks and referred to on your ingredient list as carmine, cochineal extract or natural red 4.
Pigments can be split into two main categories: organic, which are carbon-based molecules (i.e. organic in the chemistry context, not to be confused with the use of the word to promote ‘natural’ or ‘non-synthetic’ or ‘chemical-free’ products) and inorganic which are generally metal oxides (metal + oxygen and often some other elements too). Inorganic should not be confused with ‘synthetic’ or ‘unnatural’ as most of the inorganic metal oxide pigments do occur naturally as mineral compounds.
The two most common organic pigments are lakes and toners. The lake pigments are made by combining a dye colour with an insoluble substance like alumina hydrate. This causes the dye to become insoluble in water, making it suitable for cosmetics where water-resistant or waterproof properties are desired.
A toner pigment is an organic pigment that has not been combined with any other substance.
The inorganic metal oxide pigments are usually duller than the organic intermediate pigments, but are more resistant to heat and light, providing a longer-lasting colour.
Glimmer and shine
Shimmering effects can be created via a range of materials. Some of the most common ones are mica and bismuth oxychloride.
Cosmetic mica typically comes from muscovite (KAl2(AlSi3O10)(F,OH)2) also known as white mica. It naturally forms in flaky sheets and these are crushed up into fine powders. The tiny particles in the powders refract (bend) light, which creates the shimmering effect common in many cosmetics. Mica coated with titanium dioxide gives a whitish appearance when looked at straight on, but then produces a range of iridescent colours when viewed from an angle.
Bismuth oxychloride (BiClO) is used to create a silver grey pearly effect. This compound occurs naturally in the rare mineral bismoclite, but is usually produced synthetically and so is also known as synthetic pearl.
The size of the particles used to create pearly and shimmering looks affect the degree of glimmer the product has. The smaller the particle size (15–60 microns, where one micron is one millionth of a meter), the less lustrous the powder will be, and more coverage it gives. Larger particle sizes, up to 500 microns, give a more glittery lustre and are more transparent.
Fragrances
No matter how effective a cosmetic may be, no one will want to use it if it smells unpleasant. Consumer research indicates that smell is one of the key factors in a consumer’s decision to purchase and/or use a product.
Chemicals, both natural and synthetic, are added to cosmetics to provide an appealing fragrance. Even ‘unscented’ products may contain masking fragrances to mask the smell of other chemicals.
The term ‘fragrance’ is often a generic term used by manufacturers. A single listing of fragrance on your product’s ingredient list could represent dozens or even hundreds of unlisted chemical compounds which were used to create the final individual fragrance.
Manufacturers do not have to list these individual ingredients as fragrance is considered to be a trade secret.
There are over 3,000 chemicals used to formulate the huge range of fragrances used in consumer products worldwide. A comprehensive list has been published by the fragrance industry. All the ingredients on this list have passed the International Fragrance Association (IFRA) safety standards for use in commercial products. However, without knowing which individual ingredients went in to making up the fragrance of a product, consumers can find it difficult to make informed choices. If consumers are concerned they should look for fragrance free products and buy from companies that label their products more comprehensively.
Are cosmetics dangerous?
There’s nothing like a bit of controversy to generate some media buzz. For over a decade there have been recurring reports in both the media and on hundreds of internet sites relating to potentially toxic substances present in cosmetics (lead, mercury, parabens) and the dangers they pose to the public. Should consumers be worried? Are these claims backed up by reputable, published scientific research or have the findings been misinterpreted and exaggerated? Let’s take a look …
Parabens
Parabens are a class of chemicals commonly used as preservatives in food, therapeutic and cosmetic products. They are derived from para-hydroxybenzoic acid (PHBA), which occurs naturally in many fruits and vegetables. Parabens come in several forms: methylparaben, ethylparaben, propylparaben, butylparaben and isobutylparaben. They are the most widely used preservative in personal care products. This is because they are incredibly good at doing their job—keeping your products mould and bacteria free—and are also cost effective.
The use of parabens in cosmetics hit the media in 2004 after a research study conducted by Dr. Philippa Darbre of the University of Reading in England reported findings that 18 out of 20 breast cancer tissue samples contained parabens. As parabens can weakly mimic the actions of oestrogen, and as oestrogen can enhance tumour growth, this was thought to be a problem. The presence of parabens in breast tumours was picked up by the media and presented as evidence that parabens contribute to breast cancer. This was incorrect.
While the presence of parabens is notable, the study found no direct evidence that they had caused the cancer or contributed to its growth. Breast tumours have a large blood supply, so it is likely that any chemical found in the blood stream will be present in the tumour.
In a later statement to the media, Dr. Darbre, referring to her 2004 study, said ‘No claim was made that the presence of parabens has caused the breast cancers.’
There have since been dozens of studies undertaken around the globe on the safety of parabens, which time and again have exhaustively demonstrated that parabens are broken down, metabolised and excreted harmlessly from the body.
Currently, both in Australia and internationally, the science community consider the use of parabens in cosmetics to be safe.
In response to consumer demand, some companies have begun to manufacture paraben free products, which consumers can purchase if they are concerned.
Aluminium
Concerns regarding cancer are also linked to the use of aluminium in deodorants and anti-perspirants. In the early 2000s various news outlets reported apparent links between the use of antiperspirants containing aluminium and breast cancer. Similar reports connected the use of such products to the onset of Alzheimer’s disease. These supposed links have never been scientifically proven despite multiple studies.
Aluminium works to block the sweat ducts to reduce sweating. Some argue that this process prevents us from releasing toxins, causing them to build up within our lymph glands. However, breast cancer tumours do not originate in the lymph nodes, they start in the breast, and travel to the lymph nodes later. Another study found no difference in the concentration of aluminium between the cancer and the surrounding tissue.
Currently there is no clear link between the use of under-arm products containing aluminium and breast cancer.
Likewise, studies have shown no relationship between Alzheimer’s disease and deodorant/antiperspirant use. Every day, humans are exposed to aluminium through food, packaging, pots and pans, medicine and even air and water. The official position of both the Alzheimer’s Society (US) and Alzheimer’s Australia is that a link between environmental aluminium absorption and Alzheimer’s disease seems ‘increasingly unlikely’.
Despite these findings, some manufacturers have begun producing aluminium-free products for consumers who still hold concerns.
Triclosan
Triclosan was originally developed as an anti-bacterial agent for use in hospitals, primarily as a surgical scrub. However its usefulness has seen it increasingly added to a wide range of consumer products including deodorant, soap, toothpaste, cosmetics and general house-hold cleaning products. Triclosan is also used as a pesticide and can, under certain circumstances, break down into potentially toxic chemicals such as dioxins.
Triclosan hit the news in 2000 after findings published by the National Academy of Sciences (US) noted rising levels of the chemical being detected in the environment and its increasingly broad use in everyday products as concerns.
Studies conducted by scientists at the University of California found that prolonged exposure to triclosan causes liver fibrosis and cancer in laboratory mice. Other studies have suggested triclosan can disrupt hormones, impair muscle contraction and reduce bacterial resistance.
Whilst the over-use of triclosan in products warrants further study, Australian experts have highlighted its value and importance when used correctly and in moderation. Professor of Dental Science at the University of Queensland, Dr. Laurie Walsh, noted that the chemical has been proven to fight various conditions such as gingivitis, inflammation and bleeding gums.
In Australia, a full risk assessment conducted by NICNAS found no cause for public concern in general, though did recommend controls for maximum concentrations of triclosan (0.3%) in personal care and cosmetic products. At present, cosmetic products containing more than 0.3% triclosan must clearly carry the word ‘poison’ on the label—not the best marketing strategy for producers.
The American Food and Drug Administration (FDA) is planning to release an updated report on Triclosan in 2016, though in the interim consumers may look for triclosan-free products if they wish.
Formaldehyde
Formaldehyde is an organic compound with a wide variety of uses. Although commonly associated with embalming, it is also used in the manufacture of building materials, textiles, household cleaning products, plastics, cosmetics and personal care products. It also occurs naturally in a wide range of foods, for example the humble egg.
Formaldehyde is not typically used in its pure form, but altered slightly and listed under the name formalin. It works as a preservative to protect products from contamination.
Formaldehyde is classified as a Group 1 carcinogen (known to cause cancer in humans) by the World Health Organization International Agency for Research on Cancer. It can also cause skin and sensory irritation and breathing difficulties in people when inhaled, ingested or if it comes into contact with skin. So why is it still used in everyday products?
As with other chemicals, it is the concentration present in a product that is important. NICNAS has assessed formaldehyde and set maximum safe limits for its use in cosmetics. Oral products such as toothpastes may only contain up to 0.1 percent formaldehyde, while nail hardeners can have up to 5 percent. All other cosmetic products (such as shampoos and straightening solutions) can have up to 0.2 percent. At these low levels, the use of formaldehyde is deemed to be safe.
NICNAS has noted that people with particularly sensitive skin may still experience irritation even at these low concentrations.
In 2010, the Australian Competition and Consumer Commission (ACCC) conducted a survey of the formaldehyde concentrations of several cosmetic products that resulted in the voluntary recall of two products that contained unacceptably high concentrations of the chemical.
Phthalates
Phthalates (pronounced THAL-ates) are another group of chemicals found in some cosmetics that have been red-flagged by environmental groups. They are generally used to make plastic products soft and flexible but can also be found in cosmetics like nail polish, hair spray (to make the products less brittle or stiff) and perfumes.
Phthalates are produced from oil and there are more than 20 types in common use. As the various phthalates have different chemical structures, toxicity profiles and uses, their safety should not be generalised as a group, but looked at on an individual basis. Some studies have indicated that at high, recurring concentrations different phthalates can act as endocrine disruptors—this means they upset the hormonal balance in the body and can lead to developmental problems, particularly in males. Other studies have indicated there may be a link between phthalates and type 2 diabetes.
In response, the European Union and the United States have imposed bans on some types of phthalates for use in cosmetics. Research conducted in Australia has identified a small level of risk in relation to one phthalate, bis(2-ethylhexyl) phthalate or DEHP, and as a result NICNAS has prohibited products that contain DEHP above the prescribed level—this generally relates to children’s toys.
Lead in your lipstick?
News reports detailing levels of lead and other metals in lipsticks are persistent and recurring, but should consumers be worried? A 2013 study by the University of California Berkley examined the metal content of 32 different lipsticks. Researchers found traces of aluminium, manganese (which can cause neurological problems) and titanium in all the products they tested, while three-quarters of the products contained lead (which affects the nervous system, and can cause learning disabilities in children). Many of the lipsticks and lip glosses also contained nickel and cobalt, as well as cadmium and chromium—both known carcinogens.
Why would manufacturers add these ingredients to their products? The answer is—they don’t. They exist in the products as ‘impurities’, that is, they are present in other ingredients such as the wax, oils or the mineral pigments used in the formula. Because of the persistent nature of these substances and the fact they occur in the natural environment, including in water, it is almost impossible to remove all traces of them.
However don’t throw your lippy away just yet. The presence of these naturally-occurring elements in lipsticks is not necessarily a problem—the important issue is the level or concentration. Are the the levels high enough to be considered toxic, or are they low enough to be deemed safe? Remember, sunlight is also a proven carcinogen (skin cancer)—but you still go outside and you might even sunbathe. It all comes down to dose.
With the exception of chromium, the study concluded that the metal concentrations were comfortably within the ‘acceptable daily allowances’ as determined by the researchers via a comparison with accepted water and air contamination levels. Basically, you will consume more lead from drinking water than you will from applying lipstick. However, the study did conclude that further research into the metal content of cosmetic products is necessary, particularly with respect to chromium.
Sun creams
While sun creams are not officially cosmetics (they are considered to be therapeutics), we will include them here as their use is so common, particularly in Australia.
Sunscreens play an important role in protecting our skin from the harmful UVA and UVB rays emitted by the sun. Their use has been proven to help prevent certain skin cancers including melanomas and basal cell carcinomas.
In recent years there has been some concern about nanoparticles (NP) in sunscreens. This relates particularly to zinc oxide (ZnO) and titanium dioxide (TiO₂) nanoparticles and their ability to penetrate the skin to reach cells and the potential toxicity exerted by these chemicals.
The position of the Therapeutic Goods Administration (TGA), based on several published papers (up to May 2013) as well as reviews of international authorities, is that nano-particles are safe. ‘Several in vitro and in vivo studies using both animal and human skin have shown that these NPs do not penetrate the underlying layers of skin, with penetration limited to the stratum corneum. This suggests that systemic absorption is unlikely.’
A further study published in 2014 found that when exposed to zinc oxide nanoparticles, human immune cells (called macrophages) effectively absorbed the nanoparticles and broke them down.
Based on current evidence, neither TiO2 nor ZnO nanoparticles are likely to cause harm when used as ingredients in sunscreens. There are more risks associated with avoiding suncreams (sunburn, skin cancers) than there are posed by nanoparticles.
|
|
|
Here's the Truth About Wood Veneers |
Posted by: fw115ww - 09-03-2021, 03:16 AM - Forum: Welcomes and Introductions
- No Replies
|
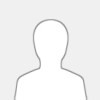 |
When you learn that a piece of furniture has a veneer, does it make you cringe a little? Admittedly us, too. But wood veneers, in fact, are a traditional and structurally significant aspect of furniture-making that still come into play in contemporary design. Wood veneers have been used in furniture-making and millwork techniques for over 200 years, says interior designer Cate Caruso, of Studio C, who uses them for all kinds of high-quality custom furnishings. In woodworking, a veneer is actually a paper thin cut of wood that's applied to both sides of a strong core surface, like furniture-grade MDF or substrate material, to seal and stabilize it—which is critically important when you're fashioning built-in furniture or anything with a mechanism. The reason is simple: Solid wood expands and contracts as the temperature changes, and your apartment isn't temperature controlled no matter how powerful your A.C. unit is. A dining table, for instance, can be made from solid wood (and many are), but a wood piece with moving parts cannot. With kitchen cabinetry, drawers, and anything built-in or paneled, you really have to have veneers, Caruso explains. A solid piece of wood just isn’t always structurally sound enough to fabricate a millwork.
What she is not using is fake wood. Oftentimes, when people see a veneered furnishing that’s cheap, it’s actually not wood at all—it’s a laminate material, Caruso explains, putting a name to the faux surface that gave all veneers a bad rap somewhere along the line. (Those are made from plastic, paper, or even foil that's been printed with a wood grain pattern that often wears away at the edges—a sure way to spot them.) But of course, there's also a range in quality of proper veneers depending on who makes them. All woodworking can be done well or it can be done poorly—but an expert millworker will make veneers look seamless, with perfect corners, Caruso says, which explains the misconception that a wood engineered veneer is cheap when it’s anything but.
Besides keeping a wood panel stable, veneers have other perks and purposes. They're considered an environmentally conscious option because you're maximizing that log in thin little sheets, Caruso says, and then the core is furniture grade MDF or substrate material. In extreme cases, they can even be cost-saving. Think about Brazilian rosewood, which is rare, endangered, very hard to get, and very expensive, says Patrick Muecke, Caruso's general contractor, who was a millworker for 15+ years before opening his own GC and management company. If you want to do a rosewood paneled room in solid wood, you’d have to be the Sultan of Brunei in order to afford it. The same would go for any project in an expensive wood; veneers would bring down the cost. Beyond millwork, natural bamboo veneers are also required for certain special techniques: Book-matched wood doors (or book-matched wood anything) would have to be fashioned using bamboo veneers because you'd never find wood planks with grains that perfectly match—it's necessary instead to have a series of veneers cut from the same log. Then there are labor-intensive inlay arts like marquetry and parquetry, which require veneers cut to certain sizes and shapes that are then fit into the top of a structure. A far cry from laminate surfaces, right?
When you’re choosing your residence hall furniture and deciding on the specs, you’ll inevitably choose what materials you want.
Should it be totally solid wood or a laminate variety?
If you choose to go with the latter, you’ll have to answer another important question.
What kind of wood edge banding do you want?
For many people who are new to buying residence hall furniture, that’s going to elicit some questioning faces.
What’s edge banding? Good question.
Or, if you’re a veteran, you already know how painful the wrong edge banding choice can be. That is to say, peeling, ongoing maintenance, and mounting work orders.
What Is Edge Banding?
So let’s start at the beginning. What is edge banding?
It’s actually kind of simple, and the video below will help you understand it even better, but this is a simple overview to get you started.
Here’s the basic non-technical idea.
Plywood, particle board, and other manufactured wood cores like MDF have rough, unfinished, unprotected, and generally unsightly edges.
To account for that, some clever folks developed technologies that allow you to glue different bands of glossy finished material to those rough edges to match the tops and sides.
Those narrow bands or strips are called edging tape, and they range in thickness from 0.018-inch to 5mm thick and in 250 ft rolls.
The thicker edging is used in high traffic and commercial environments because it provides greater resilience and impact resistance. For example, the military requires a thicker ⅜” solid wood edge banding for maximum impact resistance.
And edge banders are the industrial grade machines that apply the edging tape to the raw edges of the wood panels with a hot-melt adhesive or glue.
The Purpose of Edge Banding
Edge banding serves both functional and aesthetic purposes.
Functionally, edge bands perform some key duties for your furniture. First, it keeps moisture out serving as a de facto seal on the edge of the core material. Second, edge banding improves durability and resilience by providing impact resistance. If you’re using solid wood edging, it can also add to the overall strength of the furniture.
Aesthetically, edge banding covers up unsightly rough edges and creates a glossy finish to match your tops and sides. You can also create radial edges to soften sharp angles.
What Is Edge Banding Made From?
What are the edging tapes made from? There are different materials, and we’ll just focus on a few here.
1. PVC is the most popular material for edge banding. Pros: It’s inexpensive, durable, and boasts a long life. It doesn’t require any finishing process. It’s also easy, albeit tedious, to repair. Cons: You can’t recycle it. It doesn’t biodegrade. Once it’s blemished, you can’t refinish it. (NB: ABS—Acrylonitrile Butadiene Styrene—is an eco friendly alternative to PVC because it’s both recyclable and safe to incinerate.)
When it comes to PVC, we recommend 3mm edging in general because it goes on cleaner, quicker, and with better adhesion. Another advantage is that you get a graceful radius and a nice soft-looking finish. In general, we avoid .5mm edging because the corners tend to be too sharp.
2. Solid Wood is still a favorite in many woodworking camps. It’s durable, recyclable, easy to fix and refinish, strong, stiff, and economical. Benefits: is more resistant to chipping than veneer edge tape. Solid wood glues are more reliable and less prone to peeling than veneer and PVC. It provides additional dimensional support to plywood and mdf. Climate neutral manufacturing. Cons: Difficult to use for curves.
When it comes to solid wood we recommend 9.5mm on case good tops.
As we explain below, at DCI, we believe the best way to apply wood edge banding is “internally” with a HPL top. Why? Because in our experience, it’s incredibly durable and never requires additional service.
Wood Veneer
3. Wood Veneer, including reconstituted veneer is another common edge banding material. It’s made from thin slices of wood—typically oak, maple, ash, walnut, birch, and mahogany—that are joined together in a roll using finger jointing. It usually features a heat-sensitive glue backing.
Pros: It’s attractive, durable, and strong. It provides a clean solid-wood look, and it’s pre-sanded to easily absorb stains and finishes to seamlessly match your wood. Cons: It’s not heat resistant. Avoid putting it near a heater. It doesn’t do well in high-use environments.
|
|
|
|