Welcome, Guest |
You have to register before you can post on our site.
|
Online Users |
There are currently 107 online users. » 0 Member(s) | 105 Guest(s) Bing, Google
|
Latest Threads |
Dominica visa free countr...
Forum: Off Topic
Last Post: axied12
06-24-2025, 12:37 PM
» Replies: 0
» Views: 123
|
Advanced microneedling
Forum: Off Topic
Last Post: axied12
05-28-2025, 01:25 PM
» Replies: 0
» Views: 270
|
Caviar and cheese
Forum: Off Topic
Last Post: axied12
05-28-2025, 12:38 PM
» Replies: 0
» Views: 242
|
Top-rated countertop comp...
Forum: Off Topic
Last Post: axied12
05-04-2025, 06:42 AM
» Replies: 0
» Views: 385
|
Ryanair letenky levně do ...
Forum: Off Topic
Last Post: axied12
02-11-2025, 01:37 PM
» Replies: 0
» Views: 764
|
Trusted essay writing ser...
Forum: Off Topic
Last Post: axied12
01-30-2025, 08:16 AM
» Replies: 0
» Views: 701
|
Bootverkopers - actieve j...
Forum: Off Topic
Last Post: axied12
12-07-2024, 11:07 AM
» Replies: 0
» Views: 825
|
Services for individuals ...
Forum: Off Topic
Last Post: axied12
12-02-2024, 03:31 PM
» Replies: 0
» Views: 795
|
Used excavators
Forum: Off Topic
Last Post: axied12
11-13-2024, 09:22 AM
» Replies: 0
» Views: 749
|
Buy Higo Rocket in Dubai
Forum: Off Topic
Last Post: axied12
10-25-2024, 01:09 PM
» Replies: 0
» Views: 857
|
|
|
Food additives |
Posted by: eeksw4411a - 09-06-2021, 02:39 AM - Forum: Welcomes and Introductions
- No Replies
|
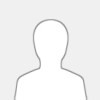 |
Food additives are chemicals added to foods to keep them fresh or to enhance their colour, flavour or texture. They may include food colourings (such as tartrazine or cochineal), flavour enhancers (such as MSG) or a range of preservatives.
Safety tests for food additives
Food Standards Australia New Zealand (FSANZ) is responsible for the approval of which food additives are allowed in Australian foods. All food additives used in Australia undergo a safety assessment, which includes rigorous testing before they are approved.
Toxicological tests on animals are used to determine the amount of the additive that is expected to be safe when consumed by humans. This is usually an amount 100 times less than the maximum daily dose at which ‘no observable effects’ are produced by an additive consumed over the test animal’s lifetime.
If there is any doubt over the safety of an additive, approval is not given. If new scientific information becomes available suggesting that a food additive is no longer safe, the approval to use the food additive would be withdrawn.
Most food additives are tested in isolation, rather than in combination with other additives. The long-term effects of consuming a combination of different additives are currently unknown.
Plant Extracts: The Original Food Additives
Plant and herb extracts have long been used to enhance the healthfulness, color, and even taste and flavor of foods, beverages and supplements. With an often “natural” positioning, their popularity is assured.
Ginny Bank, Contributing Editor
October 2011/NutraSolutions -- In 399 BC, the Greek philosopher Socrates was executed by drinking an infusion of the poisonous hemlock plant. In ancient Egypt, Cleopatra used henbane extract to dilate her eyes and make her appear more alluring. Also in Egypt, red fabric found in the tomb of King Tut contained alizarin, a pigment extracted from the roots of the madder plant. While such historical accounts documenting human use of plant-based extracts can be traced back over 3,000 years, their use is possibly as old as civilization itself. From the very first Chinese dynasties, Mesopotamia and ancient Greece, and westward to the empires of Mesoamerica, early civilizations had a surprisingly sophisticated understanding of botanicals and their extracts, especially for use as medicine. Flowers, fruits, roots, bark and leaves of plant material were extracted by various techniques to concentrate not only their therapeutic properties, but also their pigments, aromas and flavors. The simplest method of extraction, used for plants that have high oil content, was the expression of the essential oils. Other techniques included steeping the plant part in water to make an infusion (also known as a tisane) or mashing them and boiling in water to make a decoction. This method was also used to make natural dyes, sometimes boiling the decoction for days to concentrate the pigments further. Elixirs were produced by extracting the plant parts in alcoholic beverages to dissolve the active components.
Today, the use of plant extracts to flavor, color and improve health are not that different from ancient times. Even the extraction methods are fundamentally the same. And, with hundreds, if not thousands, of years of traditional use behind many plant extracts, their safety (and often their efficacy) has been well-documented. Even so, when one takes into account the massive number of plant-based extracts used in traditional medicinal systems, such as Ayurveda and traditional Chinese medicine, very few are approved for use in foods or have Generally Recognized as Safe (GRAS) status. This may be changing, as self-affirmation of GRAS status for such ingredients is steadily increasing. Within the last 18 months alone, a number of extracts received GRAS status through self-affirmation, with or without FDA notification
Pharmaceutical manufacturing is a strictly regulated, process-driven industry. A mistake in manufacturing can be costly in the best-case scenario and at worst, it can be life-threatening, particularly if a product has reached consumers.
The industry must adhere to numerous guidelines that are laid out by the Food & Drug Administration (FDA), for example, the Current Good Manufacturing Practices (cGMP). Product quality is at the center of cGMP, which assures the correct monitoring, design, and control of manufacturing facilities and processes.
cGMP also supplies guidance for how to attain quality raw materials, in addition to the preferred management processes and systems for maintaining optimum laboratory testing procedures. All factors play a key part in the effectiveness and safety of pharmaceutical raw materials.
For manufacturers, adherence to cGMP is a necessity, and while quality and safety are top priorities in the pharmaceutical industry, these guidelines do introduce more challenges in the manufacturing process.
Medical apparatus and instruments refer to instruments, instruments, implants, extracorporeal reagents or similar or related items used to diagnose, prevent or treat diseases or other medical conditions, and are not achieved by chemical effects (such as drugs) in the body or in the body Its purpose. The main goal of any medical device is to improve the patient’s daily quality of life or well-being during diagnosis, treatment, and/or medication. Over the last decade, the medical device industry is a fast-growing and demanding industry. Advances in design, materials, and technologies have increased the potential to develop improved solutions for all medical applications. These advances have managed to supply the clinicians with new products, tools, and procedures, supporting them in their work by making surgery, diagnosis, or treatment processes easier than ever before. These advances have also aimed to reduce both lead times and costs in the production of existing medical devices, reducing global healthcare costs. Due to this fact, medical devices are a hot topic among the industrial and academic domains regarding issues such as design, materials, prototypes, or manufacturing processes.
Fine and specialty chemicals are a not sharply defined chemical substances that are usually produced in small quantities and on special customer request. Fine chemicals are chemical substances that are obtained by means of complex syntheses and have a guaranteed degree of purity. Specialty chemicals is the broader term and generally includes chemical substances for special applications where the effect is what counts most.
You can use disposable protective gloves to protect your hands from any kind of hazard. There are three main types of disposable safety gloves. There are latex gloves, which are manufactured from natural rubber. Nitrile gloves are produced from synthetic nitrile rubber. And vinyl gloves are made from synthetic plastic polymer. Whichever type of glove you decide to use, you should always ensure that it is suitable for your kind of industrial application. Disposable gloves are usually manufactured with a service grading. The service grade of a disposable glove indicates the type of industry that it should be used. This article looks at the various uses of disposable gloves according to industry.
Medical Usage
Disposable safety gloves are some of the most commonly used safety products in the healthcare industry. These gloves are worn to prevent cross-contamination between patients and medical staff. They are also used for general hand protection when handling various sensitive things in a medical setting. Disposable gloves that are used in the healthcare industry are referred to as medical gloves. Medical disposable gloves are tested and approved by the U.S. Food and Drug Administration (FDA). These gloves are worn by surgeons, doctors, laboratory technicians, nurses, caregivers, dentists and all other medical personnel. Blue disposable gloves are most popular for healthcare use, but you can also get medical safety gloves in various shades of pink, purple, and even grey. These gloves undergo several rounds of testing including leak and puncture testing, and visual defect examination. The FDA allows only premium grade medical safety gloves to be marketed.
Food Service Usage
There are special disposable gloves for use in the food service industry and restaurants. These gloves are also tested and approved by the FDA. Food service gloves are worn by chefs, waiters, and various hospitality personnel. Food service gloves are used to prevent cross-contaminating during food preparation and service. Like the medical disposable gloves discussed above, food service gloves undergo serious testing before they can hit the market. Food service gloves are usually white in color to Accenture the cleanliness or sterility of the hospitality industry.
|
|
|
Some packaging types to consider |
Posted by: eeksw4411a - 09-06-2021, 02:38 AM - Forum: Welcomes and Introductions
- No Replies
|
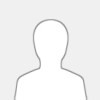 |
Remember the feeling when you picked up your first iPhone? Taking off the plastic seal and feeling the sleek white box? By touching the box for the very first time you already felt the importance, quality & significance of this device. This is no coincidence! We meticulously strategized how they were going to package their product to align with their branding of providing top of the line product innovation & consumer experience!
It is clear that packaging plays a large role in the perceived value of a product and as a whole, the packaging industry really hasn’t changed too much in the past years, compared to the constant innovations made in portable technology. With all the packaging and box choices available in today’s market, it often becomes difficult to select the most appropriate packaging solution for your product. Let’s take a look at some of the different types of packaging options you can use to enhance your product & customer experience!
1. Cardboard boxes
Paperboard is a paper-based material that is lightweight, yet strong. It can be easily cut and manipulated to create custom shapes and structures. These characteristics make it ideal to be used in personalized packaging. It is made by turning fibrous materials that come from wood or from recycled waste paper into pulp, and then bleaching it. Paperboard packaging comes in various grades, each suitable for different packaging requirements.
SBS (or solid bleached sulfate) paperboard can be used for packing cosmetics, medicines, milk and juice, cosmetics, frozen food and more. Choosing kraft, or CUK (coated unbleached kraft) paperboard packaging are for those who prefer the natural and environmentally-friendly look of recycled paper, which can be used for similar packaging applications. Kraft is often seen to be less resistant to moisture, making it less suitable for food-related products, or frozen-goods packaging. With the right combination of design options, paperboard packaging can look high-end, without high-end pricing.
2. Corrugated boxes
Corrugated boxes simply refer to what is commonly known as: Cardboard. Corrugated boxes are the ones many probably consider as ‘cardboard’ as it produces the large shipping, shoe & storage boxes. What a lot of people do not realize is that corrugated boxes also come in different types depending on the durability and strength of the box. Identifying a certain corrugated material, however, is easy. How do you determine the material? Through its corrugated medium (also known as fluting). Identifying a corrugated material is easy. It consists of 3 layers of paper, an outside liner, an inside liner and a corrugated medium (also known as fluting). The corrugated medium that gives it strength and rigidity.
3. PVC boxes
Plastic is used in a wide range of products, from spaceships to paper clips. A number of traditional materials, such as wood, leather, glass, ceramic, and so on, have already been replaced by plastic. PVC box packaging has many advantages in which they can be recycled, and generally they are much more durable than paperboard boxes. Airtight plastic packaging containers can help to preserve the quality of food and eliminate any contamination issues. Plastic packaging also does not break easily and can be stored with food under extreme conditions.
Another reason why plastic is a popular choice for packing material is because of its ability to showcase the product at any angle without necessarily opening the packaging. It is also flexible, lightweight and can be applied with films or coating to enhance packaging appearance.
Contrary to popular belief, plastic is in fact recyclable, in the sense that it takes less energy to produce new plastic, compared to glass, and other materials. Best of all, it is very cost effective!
4. Paper tube packaging
Paper tube packaging is becoming popular globally. It provides a unique packaging alternative. Paper tube packaging is lightweight that makes it easier to transport. They also provide good protection to the packaged product from damage and contamination. It is also eco-friendly and thus contributes to conserving the environment. Paper tube packaging is being widely used in different industries like cosmetics, food products, etc.
The packaging industry has seen a move towards sustainable packaging. Product packaging that is not eco-friendly creates unnecessary junk that ends up either in landfills or into ocean beds. Such packaging is harmful to the environment. Customers are becoming more aware of the dangers of non-degradable packaging and are preferring products using eco-friendly packaging.
Paper tube packaging is 100% eco-friendly. It is biodegradable and does not leave behind harmful packaging waste. Paper tube packaging can be easily recycled which saves a lot of energy and resources that would have gone into preparing fresh packaging. Using paper tube packaging helps you to position your brand and product as eco-friendly. This will provide you a competitive edge in the market and attract more customers into buying your product.
5. Paper bags
Paper bags have been part of trade and commerce for more than centuries. Traditionally cloth and jute bags were used to pack goods in larger quantities during its transfer from manufacturer or farms to retailers and shopkeepers then used the paper bags to distribute smaller quantity goods to end customers. In fact, paper bags are still used by small food retailers like – sweetshop owners, street food vendors, bakers and by small vegetable sellers.
On the other hand, a waterproof paper gift bag’s structural firmness and surface feature made it ideal to print high-quality images, logo, designs better as compared to a plastic bag, and that made paper bags a hit for fashion, luxury and premium gift packaging industry.
This trend has gained popularity owing to the people and businesses becoming more aware of the ecological surroundings. Also, several individuals want to use paper bags because they are easy to carry, clean and can hold items for a good duration of time.
|
|
|
Material Handling Equipment: Why Steel Containers |
Posted by: eeksw4411a - 09-06-2021, 02:35 AM - Forum: Welcomes and Introductions
- No Replies
|
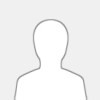 |
As you can imagine, there are several ways to move, stack, carry, store and prep material when deciding upon the correct material handling equipment. This may seem a bit more simplistic than it is but, in general, it takes a lot of consideration when creating the specific product material flow. Additionally, there are a lot of choices when it comes to the equipment used to move material, store it and potentially assemble it.
Material handling equipment can be any apparatus that helps move, store, protect and even control material. The options seem limitless.
Categories of Material Handling Equipment
There are four generalized categories of material handling equipment. The first is wire container. Generally, it consists of the JP wire containers and EU mesh containers.
The next category of material handling equipment is any roll container.
The third category of material handling equipment consists of pallet containers.
The last material handling equipment category refers to storage racking systems.
Determining the Right Container for Material Handling
When companies purchase containers for material handling, they tend to shop based on container type, size and availability. The size of the container depends on required holding capacity and the footprint of shop storage space. This is generally the starting point for many purchasing departments who receive specifications from their shop personnel for container use.
Pallet racks have played an essential role in maximizing storage capacity at warehouses and distribution centers for decades. An important part of industrial pallet racking design is the selection of rack decking, which acts as a base for storing cases or non-palletized items in conjunction with palletized products. By increasing the number of contact points between the product being stored and the storage media, decking reduces the chance of products falling – increasing overall warehouse safety. Naturally, not all decking solutions are created equal. One of the most versatile and popular choices, and the topic of this article, is wire decking.
If you’ve decided wire decking is the best option for your warehouse or distribution center, you still need to decide which options will work best. Below are 4 things to consider when selecting the best wire decking for your application.
1. What are you storing?
The most important factors when selecting wire decking are the weights and overall dimensions of the products that will be stored on it. Unless specifically designed to do so, wire decking is not intended to support the full weight of a pallet (point load) and can warp or collapse under the pressure. This creates a significant safety risk and is one of the most common mistakes we see in the field.
2. How will you be using your wire decking?
Will you be storing full pallets, individual pieces of equipment, or loose cases? Pallet racking can accommodate all the above, but it is important you consider the overall use of decking in your design. One very common use of wire decking is the storage of individual cases. Some companies refer to this as “hand stack”. If this is your intended use, you should consider increasing the density of the wire mesh grid. Standard grid densities are typically 2”x4”, 2.4”x4” or 2.5”x4.5”. When “hand stacking,” consider selecting a grid size of 1”x2” or 1”x4”. There are also design enhancements that can be incorporated into wire decking to help with your specific application. For example, the 90-degree turn at the front and rear edges of the wire deck, called waterfalls, can be configured upwards to help prevent products from sliding off the deck. There are also different accessories like dividers that clip onto the wire deck itself to help with organization. If your intended use is order picking, you could also consider sloping the wire decking to make it easier to access products.
3. In what type of storage media will the wire decking be going?
Are these wire decks for bulk shelving or pallet box? If the answer is pallet racking, is it roll-formed or structural? Manufacturers can differ slightly on the overall dimensions of their beams (horizontal members) and uprights (vertical members), so it’s important to check the sizing to ensure a good fit. Bastian Solutions has many years of experience working with all pallet racking manufacturers and can help in this selection process.
4. In what environment will the wire decking be going?
Is the wire decking going into a freezer or cooler? Will it be stored outside or in a facility where food is present? In most applications, a standard paint finish of backed on or powder coated enamel is fine. However, in environments where moisture or oxidation are concerns, galvanized or stainless steel should be considered.
Another consideration is whether wire deck channels should be inverted or flipped upside down. By inverting the wire decking channel, you can help mitigate the buildup of moisture, dust, dirt and other debris. This practice is commonly found in the food storage industry to promote a cleaner environment.
|
|
|
What is amino acids and vitamins |
Posted by: bbkowj258a - 09-03-2021, 07:16 AM - Forum: Welcomes and Introductions
- No Replies
|
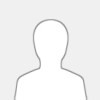 |
Amino acids function: building blocks of proteins
Proteins are of primary importance to the continuing functioning of life on Earth. Proteins catalyze the vast majority of chemical reactions that occur in the cell. They provide many of the structural elements of a cell, and they help to bind cells together into tissues. Some proteins act as contractile elements to make movement possible. Others are responsible for the transport of vital materials from the outside of the cell (“extracellular”) to its inside (“intracellular”). Proteins, in the form of antibodies, protect animals from disease and, in the form of interferon, mount an intracellular attack against viruses that have eluded destruction by the antibodies and other immune system defenses. Many hormones are proteins. Last but certainly not least, proteins control the activity of genes (“gene expression”).
This plethora of vital tasks is reflected in the incredible spectrum of known proteins that vary markedly in their overall size, shape, and charge. By the end of the 19th century, scientists appreciated that, although there exist many different kinds of proteins in nature, all proteins upon their hydrolysis yield a class of simpler compounds, the building blocks of proteins, called amino acids. The simplest amino acid is called glycine, named for its sweet taste (glyco, “sugar”). It was one of the first amino acids to be identified, having been isolated from the protein gelatin in 1820. In the mid-1950s scientists involved in elucidating the relationship between proteins and genes agreed that 20 amino acids (called standard or common amino acids) were to be considered the essential building blocks of all proteins. The last of these to be discovered, threonine, had been identified in 1935.
Chirality
All the amino acids but glycine are chiral molecules. That is, they exist in two optically active asymmetric forms (called enantiomers) that are the mirror images of each other. (This property is conceptually similar to the spatial relationship of the left hand to the right hand.) One enantiomer is designated D and the other L. It is important to note that the amino acids found in proteins almost always possess only the L-configuration. This reflects the fact that the enzymes responsible for protein synthesis have evolved to utilize only the L-enantiomers. Reflecting this near universality, the prefix L is usually omitted. Some D-amino acids are found in microorganisms, particularly in the cell walls of bacteria and in several of the antibiotics. However, these are not synthesized in the ribosome.
Acid-base properties
Another important feature of free amino acids is the existence of both a basic and an acidic group at the α-carbon. Compounds such as amino acids that can act as either an acid or a base are called amphoteric. The basic amino group typically has a pKa between 9 and 10, while the acidic α-carboxyl group has a pKa that is usually close to 2 (a very low value for carboxyls). The pKa of a group is the pH value at which the concentration of the protonated group equals that of the unprotonated group. Thus, at physiological pH (about 7–7.4), the free amino acids exist largely as dipolar ions or “zwitterions” (German for “hybrid ions”; a zwitterion carries an equal number of positively and negatively charged groups). Any free amino acid and likewise any protein will, at some specific pH, exist in the form of a zwitterion. That is, all amino acids and all proteins, when subjected to changes in pH, pass through a state at which there is an equal number of positive and negative charges on the molecule. The pH at which this occurs is known as the isoelectric point (or isoelectric pH) and is denoted as pI. When dissolved in water, all amino acids and all proteins are present predominantly in their isoelectric form. Stated another way, there is a pH (the isoelectric point) at which the molecule has a net zero charge (equal number of positive and negative charges), but there is no pH at which the molecule has an absolute zero charge (complete absence of positive and negative charges). That is, amino acids and proteins are always in the form of ions; they always carry charged groups. This fact is vitally important in considering further the biochemistry of amino acids and proteins.
What are vitamins, and how do they work?
Vitamins are organic compounds that people need in small quantities. Most vitamins need to come from food because the body either does not produce them or produces very little. Each organism has different vitamin requirements. For example, humans need to get vitamin C from their diets — while dogs can produce all the vitamin C that they need.
For humans, vitamin D is not available in large enough quantities in food. The human body synthesizes the vitamin when exposed to sunlight, and this is the best source of vitamin D. Different vitamins play different roles in the body, and a person requires a different amount of each vitamin to stay healthy.
This article explains what vitamins are, what they do, and which foods are good sources. Follow the links in blue below for more information about each vitamin. Vitamins are organic substances present in minute amounts in natural foodstuffs. Having too little of any particular vitamin may increase the risk of developing certain health issues. A vitamin is an organic compound, which means that it contains carbon. It is also an essential nutrient that the body may need to get from food.
Fat-soluble vitamins
Vitamins A, D, E, and K are fat-soluble. The body storesTrusted Source fat-soluble vitamins in fatty tissue and the liver, and reserves of these vitamins can stay in the body for days and sometimes months. Dietary fats help the body absorb fat-soluble vitamins through the intestinal tract.
Water-soluble vitamins
Water-soluble vitamins do not stayTrusted Source in the body for long and cannot be stored. They leave the body via the urine. Because of this, people need a more regular supply of water-soluble vitamins than fat-soluble ones.
|
|
|
What are Moisture Analyzers and How do They Work? |
Posted by: bbkowj258a - 09-03-2021, 07:14 AM - Forum: Welcomes and Introductions
- No Replies
|
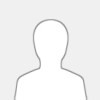 |
A moisture balance, also called a moisture analyzer, measures the amount of moisture in a substance. This is particularly helpful in food processing lab consumables as the amount of moisture can be an indicator of freshness and quality for some foods. These analyzers are also commonly used in environmental, pharmaceutical, and materials science labs. There are several techniques that may be used to measure moisture. Some techniques used include measuring water vapor released following combustion of the sample, measuring the difference in weight after removal of moisture from the sample, and measuring the equilibrium of water vapor of the sample in a closed system. Some things to take into consideration when purchasing a moisture analytical balance include capacity, precision, speed, method of measurement, software, and whether the samples to be measured come in solid or liquid form.
Moisture analyzers, sometimes called “moisture balances”, are used to measure the moisture content in various types of samples including solids, liquids, and gases. Trace moisture in solids must be controlled for plastics, pharmaceuticals and heat treatment processes. Gas or liquid measurement applications include dry air, hydrocarbon processing, pure semiconductor gases, bulk pure gases, dielectric gases such as those in transformers and power plants, and natural gas pipeline transport.
Due to the slow pace of traditional and manual laboratory moisture testing methods, automated moisture analyzers have been developed and can reduce the time necessary for a test from hours to just a few minutes.
Moisture analyzers are utilized in different industries for many different purposes. They can be used in food industry to control the moisture. Excess amount of moisture in food may lead to staleness or bacterial growth. Furthermore, there are many food items which are sold by their weight; thus, it is important to make sure customers aren’t overpaying for water weight. On the other hand, too little moisture can reduce the calorie count or make the food dry. Moisture is an important factor affecting the consistency, taste, shelf appearance and many other factors in food.
Moisture analyzers, as industrial weighing scale, are also frequently used in quality control and other laboratories. Moisture analysis is used in many fields to determine the water content in crude oil, fuel, sewage sludge and many other chemicals, solids and liquids.
Most moisture analyzers have a computer interface to assist with the observation and analyse in the drying process and its effects on the sample. They have the capacity to save the tests in their memory to repeat frequent testing parameters without having to set them up over and over again to assist with the elimination of down time.
How moisture analyzers work
Moisture analyzers utilize Loss On Drying (LOD) method to measure moisture. In this method, the moisture analyzer weighs a sample, heats it up to dry it, and weighs it again once it’s dry. The weight after drying is subtracted from the weight before, so the loss of moisture is determined using the loss of mass.
The heat generating system can vary from analyzer to analyzer. Some moisture analyzers use halogen and some use infrared or glass-free metal heaters positioned above a precision electronic balance. Halogen moisture analyzers are quick, efficient and responsive. These types of moisture analyzers are ideal to use where there is no single setting that heats all samples evenly.
Density balances decide the density in liquid and solid materials as per the buoyancy method. Density balances are mainly electronic, maintain accuracy and beneficial to know the density in ceramics, glass, rubber, plastics, sintered metals and other non-metallic materials.
The method of density determination, like textile balance, is denoted by high veracity and quick results. Liquid Density is measured via the buoyancy test with the glass element. On the other hand, the density in solid materials is decided by using the weight and volume of a sample.
In Density Balances, the weighing unit determines the weight. The density of the Liquid must be ensured prior because the volume is obtained when the pressure of the sample is put in the liquid.
The process of selecting chromatography sample vials for your laboratory can be complicated because there are many factors to consider as well as numerous options to choose from. This article offers guidance by providing an overview of chromatography vial options and how each can suit specific needs.
When choosing a chromatography vial, the product material is of paramount importance. Depending upon the use, either glass or plastic testing vials may be best. Begin by considering the facts and benefits regarding glass ultra clean vials.
Glass Vials
Glass vials are pure, meaning they have no traces of contaminants within their components, for example metal, which could potentially interfere with an experiment. Glass is also heat resistant, which is vital because glass chromatography vials may be heated to over 500 degrees Celsius. That makes glass vials a common choice for many labs.
Plastic Vials
Plastic vials have their own set of specifications and benefits. It is important to note that the type of plastic makes a difference in the storage vial and its uses. Plastic vials can be made of either polypropylene or poly methyl pentene (PMP). Polypropylene is the most popular plastic material available. To put it in perspective, the recyclable containers you store your dinner leftovers in are commonly made of this as well as the plastic lid on a box of Tic Tacs. Polypropylene vials have a heat resistance of up to 135 degrees Celsius, are translucent and are used commonly in chromatography experiments.
PMP has a higher heat resistance—up to 175 degrees Celsius—and is transparent, which increases visibility of the sample within the vial. Aside from scientific uses, PMP is used in the making of cookware, microwave components and even some windows.
Plastic vials provide the benefits of good chemical resistance, light weight construction, durability and affordability.
|
|
|
Why Get Home Security Cameras? |
Posted by: bbkowj258a - 09-03-2021, 07:12 AM - Forum: Welcomes and Introductions
- No Replies
|
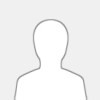 |
Home security cameras keep watch over your home from both inside and outside, acting as an extra pair of eyes and ears to monitor your property. In this guide, we'll look at the benefits of installing indoor and outdoor security cameras, from their potential to deter criminals to other applications such as pet and baby monitors. We'll also explore the necessary and optional features of security cameras, as well as their drawbacks. Finally, we’ll discuss some of the other ways to protect your home if you’re not sure about installing cameras.
What Are the Benefits of Home Security Cameras?
Peace of mind is one of the main benefits of security cameras, whether you choose to install cameras that are wired or wireless. They can increase your home security by letting you check in on your property from wherever you are, see a live feed of your home on a smartphone or computer, and get immediate alerts of any unusual activity.
While the number of burglaries in the U.S. continued to decline recently, the value of the property stolen increased in 2018 to $2,799 (the most recent year for which this information is available). These studies indicate that although burglary rates are dropping, more valuable items are being stolen. This makes home security cameras an important tool in our home protection kit, as they can help with recovery as well as detection.
Security cameras are recognized as an excellent deterrent to criminals. The experts we spoke with don't recommend relying solely on cameras for security, saying a complete home security system is the best defense. However, cameras are still important. “If I had to choose, I would go with an alarm system over a camera system first,” says Jordan Frankel, vice president of security consulting firm Global Security Experts Inc. “But I do think cameras are a great addition, primarily because they're a psychological deterrence. A bad guy sees the camera and may skip your home and move on to an easier target.”
Research backs this up. A study of incarcerated burglars by the University of North Carolina at Charlotte’s Department of Criminal Justice and Criminology showed that indicators of increased security, such as outdoor surveillance cameras, were considered by most burglars when selecting a target.
Home security cameras aren’t just useful for policing your property; they’re also helpful for keeping an eye on children and pets when you can’t be there. A security camera with facial recognition by your front door can send you a push notification saying, “John is at the front door,” so you know your child is home safely. Two-way audio on indoor cameras can act as an intercom, allowing you to see and talk to your family when you’re not home.
For more on the benefits for home security cameras check out How to Buy Home Security Cameras and How Home Security Cameras Work.
What Are the Drawbacks of Home Security Cameras?
Privacy is a big concern when putting cameras around your home. “Whatever it records is technically on the internet forever,” says David VanWert, a home technology consultant and founder of VanWert Technology Designs Inc. “Once it's stored in the cloud, in theory, it never goes away.” But as VanWert points out, you likely already have a number of devices in your home with cameras that can record what you’re doing, such as smartphones and computers. There are steps you can take to minimize the security and privacy risks of installing security cameras, however. If you're concerned, consider only installing cameras on the outside of your home, and don’t put them in personal spaces such as bedrooms.
Liability can be another drawback. “If you;re just watching your own property, you’re probably fine,” says Jeff Welch, a former corrections officer and founder of Grab The Axe security consultants LLC. “But if your neighbor believes or has evidence that you have one pointed towards his bedroom window or front door, then you have an issue on your end for liability for their privacy.”
Also, if you record someone’s conversation without their knowledge – even on your own property – you could be breaking the law, depending on where you live. Denise Howell, an internet and technology lawyer, says that under federal law, as long as you’re a party to the conversation and you consent to it being recorded, it doesn’t matter what the other parties think. However, several states have two-party consent laws that make it illegal to record audio conversations without the consent of everyone involved. Plus, it’s almost always illegal to record a conversation if you’re not participating in it at all. A good rule of thumb is to let any visitors know when they are being recorded and consider posting notices on your property indicating it’s being surveilled by audio and video recording technology. Additionally, specific features such as facial recognition (found on Nest cameras) are illegal in some states. Check the applicable laws where you live.
Another drawback is that home security cameras can be costly. While their prices have come down a lot in recent years, to outfit your entire property with security cameras can cost thousands of dollars. Additionally, these high-value items on the outside of your house can be a target for theft themselves.
Are Home Security Cameras Good for Home Protection?
A home security camera system is an excellent tool for home protection, and it can work both as a deterrent and a recovery tool. Burglars are wary of properties with visible security cameras. Plus, if a crime does occur, security cameras can help gather evidence. From property damage to potentially identifying criminals who break in, if you capture the action on camera, you're more likely to be able to remedy it.
If you want to be able to identify cars, people, and other moving objects, it’s worth investing in a camera with super or ultra-high definition video (2K or 4K, respectively). This technology uses more pixels in the image, meaning you can zoom in to see more detail on license plates and identify more physical characteristics. An HD or full HD camera won’t get you that type of clarity, especially at night.
Ultimately, home security cameras work best to protect your property when they're integrated with a home security system. To save their batteries, wireless security cameras only start to record when they detect motion, which means they may not record everything you'd want them to. With a home security system, cameras, especially mini camera, can be set to start recording as soon as any part of the security system is triggered, such as a contact sensor, a glass-break sensor, or a motion sensor. This makes it more likely the cameras will record everything that’s happening on your property and not just the few seconds of motion that occurred right in front of them.
For more on home security systems, read our guide to Best Home Security Systems of 2021.
What Are the Most Important Home Security Camera Features?
First, decide whether you want your home security camera to record footage continuously or based on a trigger, such as motion. Recording continuously will make sure yo don't miss anything, but it will require a lot of Wi-Fi bandwidth and isn't suitable for battery-powered wire-free cameras. The footage should be stored either on the camera itself or on a cloud-based server where you can access it for a period of time. The camera also should alert you to motion by sending a notification to your smartphone or tablet and quickly deliver clear, good-quality video of the event. “Any camera that can record footage at full high definition or above is going to be good,” says VanWert. “Some can record at 4 and 5 megapixels, and then you’re talking about 4K resolution. It depends on what level of detail you're looking for, such as whether you want to be able to zoom in on your camera and see a license plate.”
The power source is another key feature of a security camera. If you're buying a wireless camera, look for one that's powered by batteries or AC (which means it plugs into a wall outlet). AC power is preferable but not always available where you want to install a camera. As a result, the ability to use both allows for maximum placement flexibility.
What Are Less Important Home Security Camera Features?
Continuous video recording, also called 24/7 recording, is a luxury that you most likely don’t need. Unless you want to record every moment of the day on your property, you can skip this feature, which can be expensive on wireless indoor surveillance cameras and uses a lot of Wi-Fi bandwidth and internet data.
Another feature you probably don't need is an extremely wide field of view, which can distort the image. A 130-degree field of view is usually sufficient.
Finally, modern Wi-Fi security IP cameras have a host of smart features to give you more detailed information about what’s going on in your home without you having to pull up the video feed. These software-based features tend to increase the price of the camera and aren't essential, although they're nice to have. They include features such as person detection, which allows the camera to alert you that a person is on your property, rather than just telling you motion was detected. The ability to set activity zones means the camera will only notify you about motion in a certain area of the image (ignoring, for example, a tree that frequently blows in the wind). Other nice-to-have smart features include the ability to work with smart home systems, such as Amazon’s Alexa Google’s Assistant and Apple’s HomeKit, and to integrate with smart door locks to allow for secure in-home deliveries.
What Are the Privacy Concerns of Home Security Cameras?
Cameras can record video all the time or when they detect motion, which means every time you or someone else walks into your garden or past your video doorbell. Before installing cameras in and around your home, make sure every member of your household knows they're there and is comfortable with them. Cameras can be hacked, with your footage monitored or even posted to the internet. However, the measures we discuss in How to Keep Your Security Cameras Safe will reduce this risk considerably.
We strongly recommend that you enable any built-in privacy features that the camera offers, and it can be perfect as baby monitor. For example, cameras can be turned off in the mobile app or geofencing technology can turn them off automatically when someone in your family with a smartphone is home.
What Are Some Uses of Home Security Cameras Besides Preventing Burglary?
Today’s home security cameras, including outdoor surveillance camera, are multifunctional and can be used for much more than just monitoring your property for intruders. Here are just a few other uses for home security cameras:
Baby Monitor: Set up an indoor camera in your baby’s room and view a live feed wherever you are, as long as you have an internet connection. You’ll need a camera capable of recording 24/7 and it will need to be plugged in, but as long as it has two-way audio and will send alerts on sound or motion it will work as a reliable monitor.
Pet Cam: Indoor, outdoor or other cameras can be used to keep an eye on your dogs, cats, chicken coop, or bunny hutch. Some cameras can specifically alert you to the noise of a dog barking so you can talk to your pet with a two-way talk feature.
Wildlife Cam: Place a battery-powered camera with night vision capabilities at the end of your garden and keep an eye on destructive deer or predatory raccoons, or enjoy the sights and sounds of nocturnal nature on your property.
Smart Home Trigger: If you have other smart home devices in your home, your camera, or action monitor, can be linked with them so they can respond automatically. For example, the motion sensor in an outdoor camera can turn smart lights inside if it detects motion in your driveway when you come home.
What Are Some Other Ways to Prevent Burglary?
One of the most effective ways to prevent burglary is to install a home security system with door and window sensors and a connection to a monitoring station, so the authorities can be notified even if you're not there. Less expensive ways to prevent burglary include installing basic physical security devices such as padlocks, door and window locks, grates, bars, and bolts on any accessible entries. “If you have a limited budget, focus on physical security devices, such as a security door brace that prevents a door from being kicked, says security consultant Frankel. Another option is to apply clear security film to windows to make them shatter-resistant.
Light is also a good deterrent. Outdoor lighting, motion-activated or programmed to come on at sunset and turn off at sunrise, can keep your home illuminated and make it harder for a thief to stay out of sight. Keeping your landscaping tidy and trimmed will help remove potential hiding spots.
Maintaining signs of occupancy even when you are gone can help deter potential thieves. Some ways to do this include using automated shades and programmed smart lighting to simulate someone being home, and making sure to cancel any newspaper or package deliveries when you're gone. A loud (although not necessarily large) dog is also a great deterrent.
|
|
|
Connect Your Car Lights To Your Trailer Lights The Easy Way |
Posted by: bbkowj258a - 09-03-2021, 07:09 AM - Forum: Welcomes and Introductions
- No Replies
|
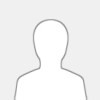 |
Trailer lighting has come a long way. Whether talking about exterior trailer lights, including markers and stop/tail/turn lamps, or interior trailer dome lights, you've made it clear to lighting suppliers you want longer lasting products for your truck fleets. Now you have them.
Last fall, Truck-Lite introduced for the reefer market two LED trailer dome lights whose diodes have a rated life of over 100,000 hr. The first product, the 80250C, is designed with the same dimensions as current fluorescent lamps, making it easy for retrofitting or use as a new product straight from the OE. The white LED uses multi-volt technology, Truck-Lite explains, rated to run between 10 and 30 volts.
LED technology, Truck-Lite points out, is an excellent fit for refrigerated trailers since LEDs work extremely well in cold temperatures. The manufacturer also states it has given the LED dome light a low profile design so drivers loading/unloading the trailer won't have a problem with insufficient overhead clearance.
The company says another advantage of the LED design is its “instant-on” technology. As soon as the operator turns the switch on, the LED is on and as bright as it will get, according to Truck-Lite, meaning the driver doesn't have to wait for the dome LED RV lights to warm up before unloading cargo.
The second product from Truck-Lite is the LED truck trailer light. It has all the benefits of the first dome lamp, but offers fleets flexibility in where they can mount it inside the trailer. The strip lamp has a low-profile design and comes in 2- and 4-ft. lengths that can be mounted in the upper corner at a 45-deg. angle or surface-mounted flat against the ceiling.
Truck-Lite says that with the introduction of the two new white LEDs it now has LED lamps available to cover any lighting application on a trailer a fleet could want. The company adds that the trend among fleets toward the use of more LEDs continues and most are spec'ing them in one position or another on their trucks.
For trailers that operate in non-refrigerated and other higher-temperature applications, Phillips Industries offers its fluorescent Permalite dome lamp. The manufacturer says that for safety, the light is designed to withstand higher temperatures than other similar units.
Late last summer the company launched another product called Permalogic, which is designed to control the trailer's dome light, such as LED marine lights. According to Phillips, fleets can save on energy and voltage by having these lamps switched off when the trailer is moving down the road. They can also prevent overheating of the lights and subsequent problems from that.
Since the dome lights run off the same blue wire as the ABS, Phillips reports that Permalogic can also avoid service problems in a panic situation by making sure there's enough power reserve to activate the ABS when needed. The controller unit in Permalogic shuts the lights off automatically if voltage gets too low, or at pre-determined elapsed time intervals, Phillips explains.
And as an added safety feature should a driver forget to turn the LED truck stop tail lights off after loading or unloading the trailer, Permalogic will turn them off for him/her the first time the driver steps on the truck brakes. Permalogic works with Permalite and competitive makes fluorescent and LED dome lights.
Phillips says its next step will be to develop a whole system — through the use of newer electronic technology in lighting products, including LED side marker clearance lights — capable of conserving the most power so fleets can run LED combination lights and other accessories longer without having to recharge the batteries.
Connect Your Car Lights, such as LED license plate lights, To Your Trailer Lights The Easy Way
When it comes to "electricity", many people are either scared silly of it, or run the other way rather than try to learn about it. Since it is a powerful force, it certainly is something to be respected. For us vehicle owners, perhaps we understand that our cars and trucks have a battery under the hood that needs occasional replacement, and light bulbs that may burn out after several years. Beyond that, many of us are ready to leave any electrical work to the "experts".
If you have recently purchased a trailer, "electricity" will eventually become a question you'll need to answer, as in, how do I connect my trailer's lights to my tow vehicle's lights? It may seem obvious that your trailer has tail, turn, and brake lights at the rear which need to operate in sync with your car's lights. That isn't going to happen by magic. We are here to share some wonderful news with you: for the vast majority of vehicles on the road, CARiD has made it quite easy to 'make the connection'. Follow along and discover how simple it is to connect these two systems together. We will be looking at specific components within our Trailer Hitch Wiring & Electrical Store.
The scope of this article will presume that your trailer has what the industry calls a "4-flat" wiring connector, which is the standard on many new trailers sold in the U.S. This article will explain the purchase of the correct harness for your vehicle, so that the two can be joined. The trailer plug should be a '3-male, 1-female', and the tow vehicle plug should be the opposite, or '3-female, 1-male'.
|
|
|
Different kinds of industrial used belts |
Posted by: bbkowj258a - 09-03-2021, 07:07 AM - Forum: Welcomes and Introductions
- No Replies
|
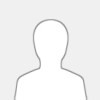 |
Conveyor Systems are mechanical devices or assemblies that transport material with minimal effort. While there are many different kinds of conveyor systems, they usually consist of a frame that supports either rollers, wheels, or a belt, upon which materials move from one place to another. They may be powered by a motor, by gravity, or manually. These material handling systems come in many different varieties to suit the different products or materials that need to be transported.
Conveyor Belt System Speed/Rated Speed
Belt conveyors are typically rated in terms of belt speed in ft/min. while powered roller conveyors described the linear velocity in similar units to a package, carton, etc. moving over the powered rollers. Rated speed applies to apron/slat conveyors and drag/chain/tow conveyors as well.
Belt Conveyors are material handling systems that use continuous belts to convey products or material. The belt is extended in an endless loop between two end-pulleys. Usually, one or both ends have a roll underneath. The conveyor belting is supported by either a metal slider pan for light loads where no friction would be applied to the belt to cause drag or on rollers. Power is provided by motors that use either variable or constant speed reduction gears.
The belts themselves can be made from numerous materials, which should correspond to the conditions under which the belt will be operating. Common conveyor belting materials include rubber, plastic, leather, fabric, and metal. Transporting a heavier load means a thicker and stronger construction of conveyor belting material is required. Belt conveyors are typically powered and can be operated at various speeds depending on the throughput required. The conveyors can be operated horizontally or can be inclined as well. Belt conveyors can be troughed for bulk or large materials.
A rubber v-belt is a flexible machine element used to transmit power between a set of grooved pulleys or sheaves. They are characterized as belts having a trapezium cross-section. V-belts are the most widely used belt drives since their geometry causes them to wedge tightly into the groove as the tension is increased. As the belt wedges into the groove, friction between the surface of the belt is increased, allowing high torques to be transmitted. The increased friction minimizes the loss of power through slippage.
Before going deeper into v-belts, it is important to know an overview of belt drives. Belt drives are machine elements that are used to transmit power between two or more rotating shafts, usually with parallel axes of rotation. The belts are looped over pulleys attached to the driver and follower shafts. These pulleys are placed at a certain distance to create an initial tension on the belt. When in operation, the friction causes the belt to grip onto the pulley. The rotation of the driver pulley increases the tension on one side of the belt creating a tight side. This tight side applies a tangential force to the follower pulley. Torque is then applied to the driven shaft. Opposite the tight side is the slack side where the belt experiences less tension.
There are many types of belt drives used today., such as agricultural harvester V belts, The earliest type of belt drive uses a flat belt made from leather or fabric. Flat belts operate satisfactorily in low-power applications such as farm equipment, mining, and logging. At higher loads and speeds, they tend to slip on the surface of the pulleys and climb out of the pulley. Another early type of belt drive is a rope drive made from cotton or hemp. Rope drives are used on two pulleys with a V-shaped groove. This solved the problem of climbing out of the pulley enabling belt drives to be used over large distances. Later, this was developed into round beltswhich are made from elastomeric materials such as rubber, nylon, or urethane. The development of these elastomeric materials also brought the progress of belt drive technology. Belts such as v-belts, ribbed belts, multi-groove belts, and timing beltswere made to solve the problems of previous belt drives.
An entire v-belt can be regarded as a composite material composed of different types of rubber and reinforcements. In its usual application, a v-belt is subjected to combined tensile and compressive stresses. The top side of a v-belt is subjected to a tensile force directed longitudinally, while the bottom side is compressed due to the compression against the grooves and bending as a belt segment passes the pulley. Moreover, a different type of material is also needed at the surface of the belt. Ideal material for the surface must have a high coefficient of friction and increased wear resistance.
Understanding All the Automotive Belts in Your Car
Your car’s engine has a number of mechanical parts attached to it that perform essential functions like delivering power (the alternator), cooling your engine (the water pump), helping you to drive more easily (the power steering pump) and keeping you comfortable (the air conditioner compressor). Without a drive belt, none of these parts would work.
The purpose of drive belts is to deliver power between different engine components. They work by means of friction between the belt and pulley, which is why loose belts can cause various components to work poorly, or not at all.
That’s a very basic overview of car belts, and by no means all-inclusive. Let’s talk in a bit more detail about different types of belts and how they work in your car.
Some vehicles have multiple belts, called v-belts, including motorcycle belts, that come off the crankshaft of the engine to drive the alternator, the air conditioning compressor, the power steering pump and the water pump. In older vehicles, v-belts were the standard.
Timing belts
The timing belt is also sometimes called a camshaft drive belt or a Gilmer belt. It is a notched belt, made of rubber, that enables the crankshaft to turn the camshaft, and opens and closes the engine valves synchronously with the pistons. In late model vehicles, the timing belt has essentially replaced the metal timing chain.
The advantage of the timing belt over the timing chain is that if the timing belt fails, there is less potential for damage to valves and pistons.
Symptoms, causes, and effects of failed or failing drive belts
V-belts: If a v-belt is failing, it will squeak, and accessories may not work properly. If it fails, the accessories that it powers will stop working. Causes can include ordinary wear or fluid contamination. Belts are also widely used in other electronics, like lawn mower belts.
Serpentine belts: If a serpentine belt is failing, accessories may not work properly, car may be hard to start or not start at all, and the belt may emit a squeaking, screeching or chirping sound. Causes can include cracking, wear or stripping, fluid contamination and poor belt tension.
Timing belts: If a timing belt is failing, your car may idle rough, or you may hear a slapping sound from the motor compartment. If it fails, your car will not work at all. There is also a possibility of serious damage to the valves and pistons. Causes can include wear, slipping or fluid contamination.
|
|
|
How prefab houses work? |
Posted by: bbkowj258a - 09-03-2021, 07:06 AM - Forum: Welcomes and Introductions
- No Replies
|
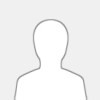 |
With historic wildfires sweeping the West Coast and burning over 3.2 million acres in California alone, it is clear in 2020 that the climate change emergency is upon us. Dvele Cofounder and CEO Kurt Goodjohn's purpose is to create a new generation of ultra-energy-efficient, self-powered prefabricated homes that will inspire society’s transition to a clean energy future. The company not only manufactures the prefab container houses, but also has designed technology to ensure that the homes can be reproduced consistently and affordably at scale.
All Dvele prefab homes are completely self-powered by solar energy, thus addressing climate change and eliminating dependency on the power grid. The homes utilize advanced materials and assembly techniques in order to ensure that they require 84% less energy per square foot than a traditionally-built home. With such efficiency, Dvele homes are capable of utilizing the solar array and battery backup system to make them fully grid-independent and insulated from the inconveniences and safety risks associated with long-term power outages, not to mention significant financial savings.
“We've redesigned the home from the ground up,” says Goodjohn. “Our approach not only results in ultra-efficient living environments that can generate more energy than it takes to operate, but also ensures the safety, health and wellness of occupants.”
Kurt Goodjohn and his brother Kris Goodjohn stumbled into the construction industry, starting off building luxury homes using traditional, stick-built construction. Quickly, they realized how outdated, inefficient, and uninspiring these methods were. They had seen prefab construction projects on a trip to Europe and wondered why the homes weren’t more popular in North America. So over beers one night, they decided to found a company in the prefab industry.
Now, Kurt Goodjohn feels he has tapped into his life purpose. “I have always been a strong advocate for the notion that everyone should leave the world better off than they found it,” he says. “At Dvele, we are accomplishing this by disrupting an age-old industry and bringing it into the modern age. Our company contributes to minimizing the overall environmental impact of homes and enhances the way they function to benefit the health and wellness of occupants.”
As a result, Goodjohn never feels that he really is “working” because he is pursuing something truly important. “There’s absolutely nothing my brother and I would rather be doing than building this company. We passionately believe that what we are doing will have a positive impact on the world and we have an unwavering determination to lead the change necessary in the new home space,” he says.
In the beginning, the greatest challenge the Goodjohns faced was getting other people to believe in the value of what they were doing with Dvele. However, they remained determined. “Trust your gut,” Kurt Goodjohn advises other aspiring entrepreneurs and changemakers. “When you're young, you really don't have a lot of experience, you don't know what will work or what will fail. So, it's actually the best time to just do what you think is right and learn as you go. My brother and I wouldn't be doing what we are doing today had we listened to all of the naysayers who told us it could never be done.”
Prefab house construction
Prefab houses are constructed from the inside out. They are manufactured in the following order in a couple of days or less, with inspections following each step (the process can take longer if the buyer has customized the home):
The floors are assembled first. There is usually a wood frame under the floor for attachment of wall panels.
Wall panels are attached next with bolts and nails. Panels are insulated and windows cut out before the panels are attached.
Once the house structure is in place, the plumbing, electrical wiring and drywall (including the ceiling) are installed.
The roof, typically constructed in another part of the factory, is set on top of the walls. In some prefabs, workers attach the roof on-site after the rest of the house is constructed.
Exterior and interior finishes are added, including siding, cabinets, vanities and backsplashes. The walls are also painted.
Once the housing units are constructed, they need to get to the owner's land. The transportation of the modules is limited by roadways, overhangs and power lines. The builders have to scout out all these factors before delivery, but in general each unit must be less than 16 feet wide, 60 feet long and 11 feet high. Because travel can be unpredictable, buyers are usually on site with independent contractors to inspect the units for scrapes and cracks.
The house has to have someplace to sit, so a foundation is required. Before the home arrives, homeowners must have the land excavated and have a foundation in place. The foundation can be poured concrete, concrete blocks, basements or crawl spaces.
The house arrives and is placed by crane on the foundation. Workers use heavy-duty cables to move the units, which come together at points called marriage walls. The marriage walls tie the house together and ensure that it is level and properly bolted together. At this point, the roof is placed if it was not factory-installed. A hinged roof, also made in the factory, is unfolded onto the house. The entire delivery and placement of the house can usually be completed in about a day. After that, decks, staircases and extras can be installed.
Variables such as customization, financing and factory schedules can contribute to the process, but from choosing the house to completion, most manufacturers give a timeframe of a few months.
Modern prefab houses
Although the concept of modern prefab design has been around since the 60s, the architectural movement didn't take off until early 2000. As technological advances like SIP panels (structural insulating that is precut and can be locked together) were made and interest in residential architectural design blossomed, architects turned their attention to prefab houses. The goal was to create a home that could be transported to a building site, be easily erected and look like modern architecture -- all within a reasonable budget.
To further stoke the flames of interest, Dwell magazine held a modern prefab invitational in 2003 to create an economical flat pack container house that could be mass-produced. Allison Arieff, the former editor of Dwell, had written the 2002 book Prefab, which profiled modern prefab prototypes. Nathan Wieler and Ingrid Tung contacted Arieff with the hopes of obtaining more information about how to build a modern prefab home. Instead, Arieff asked the couple if they'd be interested in using their land in Pittsboro, N.C., as the site for a design competition. With an initial construction budget of $200,000, the couple agreed and soon was helping the magazine create the criteria for the home and judging designs [source: Boston Globe].
The Dwell invitational created an opportunity to take the modern prefab concept and make it a reality, with the goal of introducing mass-produced prefab homes with architectural modern flair to the market. However, challenges remained. The architectural firm Resolution: 4 Architecture delivered the design, but the project went $50,000 over budget, resulting in the reduction of the homes footprint in order to stay within budget [source: Dwell].
The cost of a modern prefab home remains the chief complaint today, with the average modern prefab home running about $175 to $250 per square foot [source: BusinessWeek]. In fact, Dwell magazine is now offering modern prefab homes through their company Empyrean. Proponents of the movement point out that although many of the products available cost as much as, if not more than, stick-built homes, homeowners can save money in design and construction costs. Many architect-designed homes exceed $300 per square foot, not including design fees [source: The New Yorker] . After all, you're not paying for one-of-a-kind architecture. The architect is reselling the design, and even if modifications are needed, those costs are usually small.
When it comes to mass-producing affordable modern prefab homes, Rocio Romero is one of the most recognized architects. Romero's company, located in Perryville, Mo., creates flat-packed cubelike houses with sleek, modern exteriors. House kits range from $23,650 to $45,255 [source: Rocio Romero]. Finishes and amenities also impact the price. Romero uses a series of interlocking panels for ease of building construction. The company also sends a videotape along with instructions for the general contractor or the handy homeowner who goes it alone.
While some prefabs qualify as "traditional homes" to mortgage companies because they use some of the methods of stick-built homes, others do not. But many new modern prefabs are being introduced to home-builders, with shipping container room included. The Swedish company, IKEA, introduced its modern prefab home, the BoKlok, to the European market. In 2006, the Walker Art Museum presented an exhibit around modern prefab, "Some Assembly Required: Contemporary Prefabricated Houses." And as the market demands more environment- and wallet-friendly housing choices, the modern prefab market should continue to grow in the scope of its offerings.
|
|
|
4 Amazing Health Benefits of Sunflower Seeds |
Posted by: bbkowj258a - 09-03-2021, 07:03 AM - Forum: Welcomes and Introductions
- No Replies
|
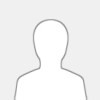 |
Sunflower seeds may conjure up memories of baseball games growing up, but they are actually a much more wholesome food than the hot dogs and other foods that may also remind you of ballpark fare. Adding sunflower seeds to your diet could do wonders for your skin, heart, immunity and overall health. Read below to find out four good reasons to start adding them to your favorite snacks for a serious health boost.
Sunflower Seeds Nutrition
The following nutritional information is for a one-ounce serving of dry roasted sunflower seeds, without salt:
Calories: 165
Total Fat: 14 grams
Saturated Fat: 1.5 grams
Monounsaturated Fat: 3 grams
Polyunsaturated Fat: 9 grams
Cholesterol: 0 milligrams
Sodium: 1 milligram
Carbs: 7 grams
Fiber: 3 grams
Sugars: 0 grams
Protein: 5.5 grams
Vitamin A: 2.5 IU (0% Daily Value)
Vitamin C: 0.5 mg (4% DV)
Calcium: 20 milligrams (2% DV)
Iron: 1 milligram (6% DV)
While sunflower seeds are pretty high in fat for a one-ounce serving, they are made of mostly mono- and polyunsaturated fats, which are a great anti-inflammatory and heart-healthy source of fats our bodies need. Additionally, they are a good source of fiber and protein, adding a nice nutrition boost to your favorite granola bars, salads and other recipes.
Sunflower seeds are also almost negligent in sodium on their own, but many packaged sunflower seed products are loaded with salt—one popular brand packs 79% of your daily sodium limit per serving! It's important to be mindful of the nutrition label whenever you're stocking up on sunflower seeds to use for snacking or in a recipe.
Sunflower Seeds Boast Anti-Inflammatory Benefits
You don't just have to eat the trendy seeds—like chia and hemp—to reap the anti-inflammatory benefits they have to offer. A study out of Columbia University found consuming sunflower and other seeds, like roasted shine skin pumpkin seeds, five or more times per week to be associated with lower levels of inflammation—which the authors of the study may be why consumption of them is also related to a reduced risk for several chronic diseases.
Sunflower Seeds Boost Your Heart Health
Unlike saturated fat, moderate unsaturated fat consumption has actually shown to improve one's heart health. A study out of Harvard University found increased seed consumption—sunflower seeds included—to be associated with a lower risk for cardiovascular disease, as well as CVD risk factors, such as high cholesterol and blood pressure. Making the effort to consume more heart-healthy fats, like the mono- and polyunsaturated fats found in sunflower seeds and sunflower seed kernels, can make a huge impact on your heart health (learn more about the best and worst foods to eat for heart health).
Sunflower Seeds Help to Prevent and Fight Sickness
Sunflower seeds are a good or excellent source of nearly a dozen essential vitamins and minerals, two of them being zinc and selenium. Zinc is an integral part of the immune system, as it helps both to develop and maintain proper function of immune cells. Additionally, zinc functions as an antioxidant to fight off free radicals.
Selenium also plays a role in fighting inflammation and infection, along with boosting immunity, to ensure our bodies are producing a proper response to any intruders in the body. This mineral is an important part of achieving mental health and preventing neurodegenerative disorders (like Alzheimer's) as well.
Sunflower Seeds Are a Great Food for Expecting Mothers
Whether you're hoping to have a baby, are pregnant or are just trying to follow a well-balanced diet, sunflower seeds have a lot to offer. These seeds are a good source of zinc and folate, while being an excellent source of vitamin E. Vitamin E is essential for prenatal health, as it helps the fetus develop and use red blood cells and muscles. Folate supports the placenta and helps prevent spina bifida, while zinc helps produce insulin and enzymes.
Vitamin E is also a key nutrient for achieving that pregnancy glow. , which is abundant in walnuts. You've likely purchased a skincare product that touts having vitamin E in it, as it fights against UV damage and nourishes your largest organ. Sunflower seeds pack more than one-third of your daily needs.
Shine skin pumpkin seeds may be tiny, but they are densely packed with useful nutrients and nutraceuticals such as amino acids, phytosterols, unsaturated fatty acids, phenolic compounds, tocopherols, cucurbitacins and valuable minerals. All these bioactive compounds are important to a healthy life and well-being. The purpose of this review is to merge the evidence-based information on the potential use pumpkin seeds as a functional food ingredient and associated biological mechanisms, collected from electronic databases (ScienceDirect, ResearchGate, PubMed, Scopus and Google Scholar) up to January 2020. Bioactive compounds in pumpkin seeds exhibit promising activities such as anthelmintic, antidiabetic, antidepressant, antioxidant, antitumor and cytoprotective. Furthermore, these bioactives carry potential in ameliorating microbiological infections, hepatic and prostate disorders. As evidenced from literature, pumpkin seeds, like roasted almond kernel, show potential to be used as both a traditional and functional food ingredient provided further animal and clinical investigations are carried out to establish the respective molecular mechanisms and safety profile.
|
|
|
|