Welcome, Guest |
You have to register before you can post on our site.
|
Online Users |
There are currently 79 online users. » 0 Member(s) | 78 Guest(s) Bing
|
Latest Threads |
Used excavators
Forum: Off Topic
Last Post: axied12
11-13-2024, 09:22 AM
» Replies: 0
» Views: 57
|
Buy Higo Rocket in Dubai
Forum: Off Topic
Last Post: axied12
10-25-2024, 01:09 PM
» Replies: 0
» Views: 110
|
Anime coloring pages
Forum: Off Topic
Last Post: axied12
10-13-2024, 05:10 PM
» Replies: 0
» Views: 160
|
Buy modest prom dresses
Forum: Off Topic
Last Post: axied12
10-07-2024, 06:03 PM
» Replies: 0
» Views: 194
|
Caviar subscription
Forum: Off Topic
Last Post: axied12
10-02-2024, 11:45 AM
» Replies: 0
» Views: 191
|
Programs for individuals ...
Forum: Off Topic
Last Post: axied12
09-23-2024, 08:46 AM
» Replies: 0
» Views: 181
|
Car detailing
Forum: Off Topic
Last Post: axied12
09-03-2024, 08:49 AM
» Replies: 0
» Views: 280
|
Buy self-aligning bearing...
Forum: Off Topic
Last Post: axied12
09-03-2024, 08:11 AM
» Replies: 0
» Views: 240
|
Support services for inte...
Forum: Off Topic
Last Post: axied12
08-21-2024, 09:17 AM
» Replies: 0
» Views: 244
|
Paribet Online Betting In...
Forum: Off Topic
Last Post: axied12
08-02-2024, 11:36 AM
» Replies: 0
» Views: 300
|
|
|
An Introduction to Textile Processing Auxiliaries |
Posted by: ttois155ssa - 09-08-2021, 01:44 AM - Forum: Welcomes and Introductions
- No Replies
|
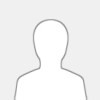 |
Although auxiliaries have been a key component of immersion dyeing processes for many years the precise mode of action of many auxiliaries has not been fully resolved. This part of the paper discusses the various types of auxiliary available and the nature of the assistance they provide in immersion dyeing processes, together with both environmental and financial aspects associated with their use, as well as a discussion of the relationship between liquor ratio and the use of auxiliaries in immersion dyeing.
The purpose of functional additives is to facilitate a textile process and/or increase its efficiency. They serve as sizing materials, lubricants, wetting agents, emulsifiers, agents accelerating or decelerating the dyeing rate, thickeners, binders, etc. often with considerable overlap in the functions and abilities of a specific chemical. Compounds used encompass many different chemical classes, some of which are affected by enzymes and thus can be regarded as substrates, and some of which remain unaffected. Owing to environment and economical concerns, pre-treatment auxiliaries are used as sparingly as possible.
Once the respective process is terminated they are to be removed completely from the treated material; however, traces could still be present and interfere negatively with subsequent processing steps.
Sizing compounds and lubricants are applied to yarns before fabric formation to protect the integrity of the yarns. While increasingly faster weaving processes demand more enduring sizes, acrylic-based compounds, natural sizes that can be decomposed are still on the market.
Such compounds comprise starch and starch derivatives, as well as soluble. Cellulose derivatives, with waxes often admixed.Desizing with amylases is one of the oldest enzymatic processes used in the textile industry. A comprehensive description of the process can be found in Uhlig (1998).
Starch has also been very useful as a thickener in printing pastes and as a component of adhesives. In printing processes, starches are applied to guarantee a defined design and to avoid spreading of the printing paste. In the paper industry, starches increase sheet strength and, as coatings, improve the writing and printing properties of high quality paper.
Dyeing and printing auxiliaries may be defined as substances that, when applied to a substrate provide color by a process that alters, at least temporarily, any crystal structure of the colored substances. Such substances with considerable coloring capacity are widely employed in the textile, pharmaceutical, food, cosmetics, plastics, photographic and paper industries. The dyes can adhere to compatible surfaces by solution, by forming covalent bond or complexes with salts or metals, by physical adsorption or by mechanical retention. Dyes are classified according to their application and chemical structure, and are composed of a group of atoms known as chromophores, responsible for the dye color. These chromophore-containing centers are based on diverse functional groups, such as azo, anthraquinone, methine, nitro, arilmethane, carbonyl and others. In addition, electrons withdrawing or donating substituents so as to generate or intensify the color of the chromophores are denominated as auxochromes. The most common auxochromes are amine, carboxyl, sulfonate and hydroxyl.
It is estimated that over 10,000 different dyes and pigments are used industrially and over 7 x 105 tons of synthetic dyes are annually produced worldwide. Textile materials can be dyed using batch, continuous or semi-continuous processes. The kind of process used depends on many characteristics including type of material as such fiber, yarn, fabric, fabric construction and garment, as also the generic type of fiber, size of dye lots and quality requirements in the dyed fabric. Among these processes, the batch process is the most common method used to dye textile materials.
In the textile industry, up to 200,000 tons of these dyes are lost to effluents every year during the dyeing and finishing operations, due to the inefficiency of the dyeing process. Unfortunately, most of these dyes escape conventional wastewater treatment processes and persist in the environment as a result of their high stability to light, temperature, water, detergents, chemicals, soap and other parameters such as bleach and perspiration. In addition, anti-microbial agents resistant to biological degradation are frequently used in the manufacture of textiles, particularly for natural fibers such as cotton. The synthetic origin and complex aromatic structure of these agents make them more recalcitrant to biodegradation. However, environmental legislation obliges industries to eliminate color from their dye-containing effluents, before disposal into water bodies.
The textile industry consumes a substantial amount of water in its manufacturing processes used mainly in the dyeing and finishing operations of the plants. The wastewater from textile plants is classified as the most polluting of all the industrial sectors, considering the volume generated as well as the effluent composition. In addition, the increased demand for textile products and the proportional increase in their production, and the use of synthetic dyes have together contributed to dye wastewater becoming one of the substantial sources of severe pollution problems in current times.
Textile wastewaters are characterized by extreme fluctuations in many parameters such as chemical oxygen demand (COD), biochemical oxygen demand (BOD), pH, color and salinity. The composition of the wastewater will depend on the different organic-based compounds, chemicals and dyes used in the dry and wet-processing steps. Recalcitrant organic, colored, toxicant, surfactant and chlorinated compounds and salts are the main pollutants in textile effluents.
In addition, the effects caused by other pollutants in textile wastewater, and the presence of very small amounts of dyes (<1 mg/L for some dyes) in the water, which are nevertheless highly visible, seriously affects the aesthetic quality and transparency of water bodies such as lakes, rivers and others, leading to damage to the aquatic environment.
During the dyeing process it has been estimated that the losses of colorants to the environment can reach 10–50%. It is noteworthy that some dyes are highly toxic and mutagenic, and also decrease light penetration and photosynthetic activity, causing oxygen deficiency and limiting downstream beneficial uses such as recreation, drinking water and irrigation.
With respect to the number and production volumes, azo dyes are the largest group of colorants, constituting 60-70% of all organic dyes produced in the world. The success of azo dyes is due to the their ease and cost effectiveness for synthesis as compared to natural dyes, and also their great structural diversity, high molar extinction coefficient, and medium-to-high fastness properties in relation to light as well as to wetness. They have a wide range of applications in the textile, pharmaceutical and cosmetic industries, and are also used in food, paper, leather and paints. However, some azo dyes can show toxic effects, especially carcinogenic and mutagenic events.
|
|
|
What is a Brushless DC Motor and How Does It Work? |
Posted by: ttois155ssa - 09-08-2021, 01:42 AM - Forum: Welcomes and Introductions
- No Replies
|
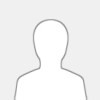 |
At present, DC brushless blowers mostly use brushless DC motors, which greatly simplify the structure of brushless DC motors by eliminating the collector ring and brushes for excitation. It not only improves the technical performance of the motor, but also greatly improves the mechanical reliability and life of the motor. Not only that, it also has excellent control performance compared with other motors. This is because the torque constant, torque inertia ratio, and power density of the motor have been greatly improved due to the high performance of permanent magnet materials.
Through reasonable design, the inertia and electromechanical time constant can be greatly reduced and greatly improved as the main index of servo control performance. The design of modern permanent magnet circuit has been improved, and the coercivity of permanent magnet material is high. As a result, the armature response and demagnetization resistance of permanent magnet motors have been greatly improved, and the control parameters of the motors have been greatly reduced under the influence of external disturbances.
Since permanent magnet is used instead of electric excitation, the design of excitation winding and magnetic field is reduced, thus reducing the parameters such as excitation flux, excitation winding inductance and excitation current, thus enabling the control variables or parameters to meet the design requirements. Direct reduction. All these factors can be said that DC brushless blowers have good controllability.
DC brushless motors are widely used in daily life, so do you know the advantages of DC brushless motors, the following I introduce you to the characteristics of DC brushless motors.
1, no carbon brushes, low interference DC brushless motor in addition to carbon brushes, the most direct change is that there is no brush geared motor operation generated by electric sparks, which greatly reduces the interference of electric sparks to remote radio equipment.
2, low noise, smooth operation DC brushless motor without brushes, friction is greatly reduced when running, smooth operation, noise will be much lower, this advantage for brushless geared motor running stability is a huge support.
3, long life, low maintenance costs DC brushless motor less carbon brushes, brushless geared motor wear is mainly on the bearings, from a mechanical point of view, brushless geared motor is almost a maintenance-free motor, when necessary, only need to do some dusting maintenance can be. Brushless DC motor life is generally between several tens of thousands of hours, while the ordinary brush motor life is generally between 1000-2000 hours.
4、Energy saving and noise reduction DC brushless motor adopts frequency control and stepless speed regulation to realize indoor constant temperature control, which saves energy up to 50% or more than traditional AC fan coils.
The blower is mainly composed of the following six parts: motor, air filter, blower body, air chamber, base (and oil tank), and drip nozzle. The blower runs eccentrically by the rotor offset in the cylinder and makes the volume change between the blades in the rotor slot to suck in, compress and spit out the air. In the operation of the blower using the pressure difference between the automatic lubrication to the drip nozzle, drip into the cylinder to reduce friction and noise, while maintaining the cylinder gas does not flow back, this blower is also known as the slide blower. The blower's types can be classified acccording to its applications, including, CPAP blower, Bipap blower, ICU ventilator blower, Purifying respirator blower, Air bed blower, Home appliance blower, etc.
Application prospects of brushless DC motor
Brushless DC motors have superior performance compared with other types of motors. Brushless DC motors are widely used in home ventilator motors, oxygen generators, small medical blowers and so on. Brushless DC motors have a good application prospect. However, there are still many problems to be solved and further research is needed. At present, the development of brushless DC motors has reached a relatively mature stage, but along with the continuous impact on materials, electronics and control technology, it is bound to develop in the direction of miniaturization, digitalization, long life and high reliability, and will certainly play a greater role in industrial production.
Brushless DC motors are common in industrial applications across the world. At the most basic level, there are brushed and brushless motors and there are DC and AC motors. Brushless DC motors, as you may imagine, do not contain brushes and use a DC current.
These motors provide many specific advantages over other types of electrical motors, but, going beyond the basics, what exactly is a brushless DC motor? How does it work and what’s it used for?
How a Brushless DC Motor Works
It often helps to explain how a brushed DC motor works first, as they were used for some time before brushless DC motors were available. A brushed DC motor has permanent magnets on the outside of its structure, with a spinning armature on the inside. The permanent magnets, which are stationary on the outside, are called the stator. The armature, which rotates and contains an electromagnet, is called the rotor.
In a brushed DC motor, the rotor spins 180-degrees when an electric current is run to the armature. To go any further, the poles of the electromagnet must flip. The brushes, as the rotor spins, make contact with the stator, flipping the magnetic field and allowing the rotor to spin a full 360-degrees.
A brushless DC motor is essentially flipped inside out, eliminating the need for brushes to flip the electromagnetic field. In brushless DC motors, the permanent magnets are on the rotor, and the electromagnets are on the stator. A computer then charges the electromagnets in the stator to rotate the rotor a full 360-degrees.
What are Brushless DC Motors Used For?
Brushless DC motors typically have an efficiency of 85-90%, while brushed motors are usually only 75-80% efficient. Brushes eventually wear out, sometimes causing dangerous sparking, limiting the lifespan of a brushed motor. Brushless DC motors are quiet, lighter and have much longer lifespans. Because computers control the electrical current, brushless DC motors can achieve much more precise motion control.
Because of all these advantages, brushless DC motors are often used in modern devices where low noise and low heat are required, especially in devices that run continuously. This may include washing machines, air conditioners and other consumer electronics. They may even be the main power source for service robots, which will require very careful control of force for safety reasons.
Brushless DC motors provide several distinct advantages over other types of electric motors, which is why they’ve made their way into so many household items and may be a major factor in the growth of service robots inside and outside of the industrial sector.
|
|
|
Mini excavators: Small size, big popularity |
Posted by: ttois155ssa - 09-08-2021, 01:41 AM - Forum: Welcomes and Introductions
- No Replies
|
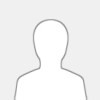 |
Mini excavators are one of the quickest growing equipment types, with the machine’s popularity seemingly ever-increasing. According to data from Off-Highway Research, global sales for the mini excavator were at their highest point ever last year, at over 300,000 units.
The major markets for mini excavators have traditionally been developed countries, such as Japan and those in Western Europe, but the last decade has seen their popularity rise in many emerging economies. Most notable of these is China, which is now by far the biggest mini excavator market in the world.
Considering that mini excavators essentially replace manual labour, this is perhaps a surprising turnaround in the most populous country in the world where there is certainly no shortage of workers. Although all is perhaps not as it seems in the Chinese market – see the box out ‘China and mini excavators’ for more details.
One of the reasons for the mini excavator’s popularity is that it is easier to power a smaller and more compact machine with electricity rather than the traditional diesel power. It is the case that, especially in city centres of developed economies, there are often strict regulations regarding noise and emissions pollution.
There is no shortage of OEMs that are currently working on, or have released electric mini excavators – back in January 2019 Volvo Construction Equipment (Volvo CE) announced that, by mid-2020, it will begin to launch a range of electric compact excavators (EC15 to EC27) and wheeled loaders (L20 to L28) and stop new diesel engine-based development of these models.
Another OEM looking at electric power for this equipment segment is JCB, with the company’s 19C-1E electric mini excavators. The JCB 19C-1E is powered by four lithium-ion batteries, providing 20kWh of energy storage. This is enough for a full working shift for the majority of mini excavator customers on a single charge. The 19C-1E itself is a powerful, compact model with zero exhaust emissions at point of use and one that is considerably quieter than a standard machine.
Small machine is a relatively light and fast mechanical equipment. Like hand-held power tools, concrete vibrator, frog tamper, mini transporter, woodworking machinery, steel machinery, mini dumper, motorized dump truck, welding, etc. are all small machines.
In addition to large machinery and equipment in construction should pay attention to the safe use, to prevent injury, a variety of medium and small machines also have different degrees of danger, must be used in accordance with the safety requirements.
Going electric
JCB recently sold two models to London-based J Coffey Plant, with Coffey Plant Division Operations Manager Tim Rayner commenting, “The major benefit is no emissions at point of use. Our workers are not subjected to diesel emissions when using the 19C-1E. Confined areas are now clearer and safer to work in too, as there is no longer a need for emissions control equipment such as extraction units and ducting. The JCB electric minis bring value to the business and the industry as a whole.”
Another OEM looking at electric power is Kubota. “In recent years mini excavators powered by alternative fuel sources – such as electric – have seen a surge in popularity,” says Glen Hampson, business development manager construction at Kubota UK.
“The main driver behind this is that electric equipment gives the operator the ability to work in regulated low emission zones. Electric machinery can also enable work to be carried out in confined spaces underground without producing harmful emissions. It’s reduced noise output also makes it great for construction work in urban or heavily populated environments.”
Kubota launched a prototype electric compact mini excavator in Kyoto City, Japan, at the start of the year and Hampson adds, “At Kubota, our main priority will always be the development of machines that match the needs of our customers – the development of electric machines will allow us to do just this.”
Bobcat recently announced that it was launching a new R-Series mini excavators from 2-4 tonne with a new range of five compact excavator models: the E26, E27z, E27, E34 and E35z. One of the standout features for this range is said by the company to be the Cylinder-Inside-Boom (CIB) design concept.
According to Miroslav Konas, product manager, Bobcat Excavators Europe, Middle East and Africa (EMEA), “The CIB system aims to overcome what has been one of the weakest points in any mini-excavator – the vulnerability of the boom cylinder to damage such as that caused by colliding with the sides of trucks and other vehicles when loading waste and building materials.
“It does this by enclosing the hydraulic cylinder inside an extended boom structure, thus avoiding collisions with the top of the blade and the sides of vehicles. In fact, the boom structure protects the hydraulic boom cylinder in any position of its movement.”
Wood chipper is a kind of special equipment for producing wood chips, wood chipper is also called wood slicer, which is one of the wood processing series equipment.
Trenching machine, such as mini trencher, is one of the main types of construction machinery, a kind of trenching machinery used in earthwork construction, widely used in agricultural water conservancy construction, laying of communication cables and petroleum pipelines, municipal construction and military engineering, etc.
Useful tools and machines in home agriculture also include log splitter, stump grinder, etc.
Operator comfort
With the lack of skilled operators in the industry, keeping those behind the stick happy has never been more important. Volvo CE claim that the new 6-tonne ECR58 F generation compact excavator has the most spacious cab in the industry.
Operator well-being, confidence, and safety are supported through a simplified workstation and user-friendly experience. The seat-to-joystick position has been revised and improved, while still being suspended together – a technic that Volvo CE says it introduced to the industry.
Designed to offer the highest levels of operator convenience, the cab features soundproofing, numerous storage areas, and 12V and USB ports. A fully opening front window and slide side window contribute to all-around visibility and operators have an automotive style jog wheel, five inch colour display and easy-to-navigate menus.
Operator comfort is indeed important, but another reason for the general popularity of the mini excavator segment is the ever-increasing range of attachments on offer. For instance, Volvo CE’s ECR58 has a wide range of attachments which are easy to switch over, including buckets, breakers, thumbs, and the new Tilt Quick Coupler.
Talking about the mini excavator’s rise in popularity, Chris Sleight, managing director, Off-Highways Research, highlights attachments, saying, “At the lighter end, the range of attachments available mean it [a mini excavator] is often favoured over workers using hand-held air-powered tools. This is partly because this can be helpful in reducing workers’ exposure to noise and vibration, and also because it removes the worker from the immediate vicinity of the tool.”
Sleight also adds that, “In Europe and even North America the mini excavator is replacing other types of equipment. At the top end of the scale, its smaller footprint and ability to slew through 360 degrees means it is often now favoured over backhoe loaders.”
Bobcat’s Konas agrees with the importance of attachments, saying, “The various types of bucket we offer are still the main ‘tool’ from among the 25 different families of attachments we offer for our mini excavators, but we see a trend developing with more advanced hydraulic attachments growing in popularity. That’s why we developed our A-SAC system, which together with up to five independent auxiliary circuits available on our machines, we believe makes Bobcat the most advanced brand on the market to operate such complex attachments.
“Combining the arm-mounted hydraulic auxiliary lines and the optional A-SAC technology together enables a wide choice of machine customisation options to match any attachment requirement, further enhancing the role of these excavators as excellent tool carriers.”
Remote monitoring as a growing trend?
Hitachi Construction Machinery (Europe) has published a white paper on the future of the compact equipment segment in Europe. In it they point out that 70% of the mini excavators sold in Europe are under three tonnes, helped by the fact that it is relatively straightforward to obtain a licence to tow one of these models on a trailer with a regular driving licence.
The White Paper predicts that remote monitoring will play an increasingly important role in the compact construction equipment market, of which mini excavators are an important part. The report says, “Tracking the location of compact equipment is particularly important, given that it moves frequently from one job site to another.
“Location and working hours data can therefore help owners, especially rental companies, with planning, enhancing efficiency and scheduling maintenance. Accurate location information is also vital from a security point of view – it’s much easier to steal a smaller machine than a larger model, and theft of compact equipment is therefore more commonplace.”
Different manufacturers offer various telematics packages with their mini excavators and mini roller; there is no industry standard. Hitachi mini excavators are connected to its remote monitoring system, Global e-Service, and the data can also be accessed via smartphone.
While location and working hours are key bits of information, the report speculates that the next-generation of equipment owners will want to view more detailed data. “Owners want access to more data from manufacturers. One reason for this is the influx of a younger, more tech-savvy generation of customers, who can better understand and analyse data to improve productivity and efficiency.”
|
|
|
Designing for Injection Molding |
Posted by: ttois155ssa - 09-08-2021, 01:40 AM - Forum: Welcomes and Introductions
- No Replies
|
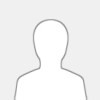 |
Injection molding machines perform a wide range of mechanical movements with differing characteristics. Mold opening is a low-force high-speed movement, and mold closing a high-force low-speed movement. Plasticizing involves high torque and low rotational speed, while injection requires high force and medium speed. A source of motive power is needed to drive these movements. The modern injection molding machine is virtually always a self-contained unit incorporating its own power source. Early machine frequency ran from a centralized source serving an entire shop or factory. In this respect, injection molding machines have undergone the same metamorphosis as machine tools.
Oil hydraulics has become firmly established as the drive system for the vast majority of injection molding machines and until recently was almost unchallenged as the power source. Put at its simplest, the injection molding machine contains a reservoir of hydraulic oil which is pumped by an electrically-driven pump at high pressure, typically at up to 2000 psi, to actuating cylinders and motors. High and low pressure linear movements are performed by hydraulic cylinders, and rotary movements for screw drive and other purposes are achieved by hydraulic motors. Hybrid machines, in which the screw is driven by electric motor while the linear movements remain hydraulically powered, are not uncommon.
In recent years, the supremacy of the hydraulic machine has been challenged by all-electric machines. These use new brushless servo motor technology to power the various machine movements. The capital cost of all-electric machines is higher than that of conventional machines but the energy consumption in production is much lower. This is because the electric motors run only on demand, and there are no losses due to energy conversion, pipelines, or throttling. The elimination of hydraulic oil makes the all-electric machine inherently cleaner, so these machines are attractive for sterile or clean room use. There is also evidence that all-electric machine movements can be resolved with a higher degree of precision and repeatability than hydraulic systems.
The Process
The process may involve either a thermoplast or a duroplast as the polymeric binder. With a thermoplast, solidification of the melt occurs on cooling; with a duroplast, a hardener is added to the feed mixture and solidification results from a binder-hardener reaction that occurs at elevated temperature. Figure 1 shows the viscosity-temperature relation for each type of binder. The reversibility of a thermoplast in terms of solidification makes recycling the reject a possibility but can lead to deformation of the compact during the subsequent burnout stage (see Sect. 3). For the duroplast process, solidification is irreversible and no deformation can occur during reheating, but the time for hardening is relatively long and the mold temperature is relatively high, and the reject cannot, of course, be recycled. The thermoplast process is the most widely used for ceramics and so this is discussed here.
Injection molding,such as commodity mold, is a prevalent manufacturing process utilized across a variety of applications, from full-scale productions of consumer products to smaller volume production of large components like car body panels.
The process involves a tool or mold, typically constructed from hardened steel or aluminum. The mold is precision machined to form the features of the desired auto part, and thermoplastic material is fed into a heated barrel, mixed and forced into the metal mold cavity where it cools and hardens.
With precise tooling and high-quality results, thin wall injection parts molding produces parts reliably and cost-effectively at large volumes.
Stratasys Direct has decades of experience in all phases of tooling, including part design, tool design, material sciences, post-processing and project management. Capabilities include injection molding, pad printing, silk screening, painting, EMI/RFI shielding and light assembly.
For streamlined operations, we offer Fast Track tooling, an operation that delivers parts in as little as ten days at volumes of 25 to 1,000 units.
Whatever the project, industrial designers, engineers and product designers may face some challenges when designing for plastic injection parts molding. The following details three mistakes designers should avoid for successful injection auto molded parts.
Non-Uniform Walls
On average, the minimum wall thickness of an injection molded part ranges from 2mm to 4mm (.080 inch to .160 inch). Parts with uniform walls thickness allow the mold cavity to fill more precisely since the molten plastic does not have to be forced through varying restrictions as it fills.
If the walls are not uniform, the thinner sections cool first. As the thicker sections cool and shrink, stresses occur between the boundaries of the thin and thick walls. The thin section doesn’t yield to the stress because the thin section has already hardened. As the thick sections yields, warping and twisting of the part occurs, which can cause cracks.
If design limitations make it impossible to have uniform wall thicknesses, the change in thickness should be as gradual as possible. Coring is a helpful method where plastic is removed from the thick area, which helps to keep wall sections uniform. Gussets support structures can also be designed into the part to reduce the possibility of warping.
Not Utilizing Draft
Mold drafts facilitate part removal from the metal thin wall mold. The draft must be in an offset angle that is parallel to the mold opening and closing. The ideal draft angle for a given part depends on the depth of the part in the mold and its required end-use function.
Allowing for as much draft as possible will permit parts to release from the mold easily. Typically, one to two degrees of drafts with an additional 1.5 degrees per 0.25mm depth of texture is sufficient.The mold part line will need to be located in a way that splits the draft in order to minimize it.
Sharp Corners
Sharp corners greatly increase stress concentration, which, when high enough, can lead to part failure. Sharp corners often come about in non-obvious places, such as a boss attached to a surface, or a strengthening rib, and the medical parts.
The radii of sharp corners needs to be watched closely because stress concentration varies with radius for a given thickness. The stress concentration factor is high for R/T values, less than 0.5, but for R/T values over 0.5 the concentration lowers. It is recommended that an inside radius be a minimum of 1 times the thickness.
In addition to reducing stresses, the fillet radius provides a streamlined flow path for the molten plastic, resulting in an easier fill of the mold, such as fiberglass mold. At corners, the suggested inside radius is 0.5 times the material thickness and the outside radius is 1.5 times the material thickness. A bigger radius should be used if part design allows.
Working with customers across a variety of industries, Stratasys Direct has developed thorough methods to provide solutions for fast tooling in order to serve your versatile needs.
|
|
|
Selecting Carbon Black for Paints, Coatings and Inks |
Posted by: ttois155ssa - 09-08-2021, 01:39 AM - Forum: Welcomes and Introductions
- No Replies
|
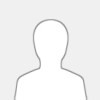 |
Adding carbon black (CB) particles to elastomeric polymers is essential to the successful industrial use of rubber in many applications, and the mechanical reinforcing effect of CB in rubber has been studied for nearly 100 years. Despite these many decades of investigations, the origin of stiffness enhancement of elastomers from incorporating nanometer-scale CB particles is still debated. It is not universally accepted whether the interactions between polymer chains and CB surfaces are purely physical adsorption or whether some polymer–particle chemical bonds are also introduced in the process of mixing and curing the CB-filled rubber compounds. We review key experimental observations of rubber reinforced with CB, including the finding that heat treatment of CB can greatly reduce the filler reinforcement effect in rubber. The details of the particle morphology and surface chemistry are described to give insights into the nature of the CB–elastomer interfaces. This is followed by a discussion of rubber processing effects, the influence of CB on crosslinking, and various chemical modification approaches that have been employed to improve polymer–filler interactions and reinforcement. Finally, we contrast various models that have been proposed for rationalizing the CB reinforcement of elastomers.
Natural rubber composite has been continuously developed due to its advantages such as a good combination of strength and damping property. Most of carbon black (CB)/Natural Rubber (NR) composite were used as material in tyre industry. The addition of CB in natural rubber is very important to enhance the strength of natural rubber. The particle loading and different structure of CB can affect the composite strength. The effects of CB particle loading of 20, 25 and 30 wt% and the effects of CB structures of N220, N330, N550 and N660 series on tensile property of composite were investigated. The result shows that the tensile strength and elastic modulus of natural rubber/CB composite was higher than pure natural rubber. From SEM observation the agglomeration of CB aggregate increases with particle loading. It leads to decrease of tensile strength of composite as more particle was added. High structure of CB particle i.e. N220 resulted in highest tensile stress. In fact, composite reinforced by N660 CB particle shown a comparable tensile strength and elastic modulus with N220 CB particle. SEM observation shows that agglomeration of CB aggregates of N330 and N550 results in lower stress of associate NR/CB composite.
Carbon black is a highly engineered form of carbon widely used in paints as paint carbon black, coatings and inks to achieve a spectrum ranging from gray to deep black. Over the time, the properties of carbon black pigment have been modified to achieve required properties in the final product, such as increased tinting strength, improved the level of jetness or blue undertone and conductivity.
Explore the different carbon black production processes and the properties to consider while selecting the right carbon black for your formulations.
Properties and End-uses of Carbon Black
Carbon black is used in many products and articles we use and see around us on a daily basis, such as: rubbers, plastics, coatings, tires, ink carbon clack.
Thus, the requirements for the carbon black are different for each application and influence the specific properties in the final application.
For the coating carbon blacks market, there is a wide range of carbon black grades available. This can make it difficult to choose the most suitable carbon black for your final application. For example, when aiming for automotive paint with a blue undertone, the carbon black of choice will have a high jetness. However, normally these types of carbon black grades are the most difficult to disperse correctly into the desired particle size.
The carbon black producers are addressing these issues by developing specialty carbon black grades that have been surface-modified and/or are pre-treated to overcome these difficulties.
How Carbon Black is Produced?
The properties of the carbon black are influenced by the method of preparation. The different processes used for channel carbon black production are discussed below.
Furnace Black Process: It is the most common method which uses (aromatic) hydrocarbon oil as the raw material. Due to its high yield and possibility to control the particle size and structure, it is most suitable for mass production of carbon black.
In the reactor the conditions (e.g. pressure and temperature) are controlled to provide a number of reactions. The most important reactions include: particle nucleation, particle growth, aggregate formation. Water injection rapidly reduces the temperature and ends the reaction. The primary particle size and structure of the carbon black is controlled by tuning the conditions in the reactor and the time allowed before the reaction is quenched.
Thermal Black Process: It is the most common method used for carbon black production after the furnace black process. It is a discontinuous or cyclical process.
This process uses natural methane gas as raw material. When the natural gas is injected into the furnace at an inert atmosphere, the gas decomposes into carbon black and hydrogen. The carbon black produced using this method has the largest particle size and the lowest degree of aggregates or structure. Due to the nature of the raw material, this carbon black is the purest form available on the industrial scale.
Channel Process: This process uses partially combusted fuel which is brought into contact with H-shaped channel steel. It is not the most used method anymore because of its:
The benefit of this process is that it provides carbon black with a lot of functional groups.
Acetylene Black Process: This process uses acetylene gas as raw material. It produces mainly high structure and higher crystallinity, making this type of carbon black suitable for electric conductive applications.
Lampblack Process: It is the oldest industrial process for making carbon black. It uses mineral/vegetable oils as its raw material.
Recovered Carbon Black from End-of-life Tires
Recovered carbon black or ®CB is a fast-expanding market. Recovered high purity carbon black is obtained through the pyrolysis process of end-of-life tires. The importance of companies in the production and use of recovered carbon black is three-fold:
The growing global problems arising with end-of-life tires (ELT)
Companies shifting strategy to fulfill the targets ensuring a green economy
Price changes of regular carbon black due to fluctuations in oil pricing
Depending on the composition, the content of carbon black in tires can be up to 30%. Next to carbon black, the tires consists:
Rubber
Rubber processing additives
Metal
Textile
Fillers such as silica
The amount of silica depends on the type of tire, for example winter or summer tire, racing tire, or tire for agricultural vehicles, and will not be separated from the carbon black during the pyrolysis process, which will result in higher ash content.
In a typical car tire, up to 15 different types of conductive carbon blacks can be used, each attributing to the different properties required. This blend of environmental carbon blacks will then also be the make-up of the final ®CB composition. Besides tires, other sources that can be used are rubber conveyor belts or other technical rubber products.
The main differences in the properties of recovered carbon black are:
The ash content is higher for ®CB caused by the fillers being used in tire production.
A blend of rubber carbon black properties as a result of the carbon black used in the tire.
Residual hydrocarbons on the carbon black surface, depending on the quality of the pyrolysis process.
To understand how the properties of ®CB influence the final applications and to know which plastic carbon black is used in which category, we need to understand the fundamental differences between the available carbon blacks.
|
|
|
How ice cream is made? |
Posted by: ttois155ssa - 09-08-2021, 01:34 AM - Forum: Welcomes and Introductions
- No Replies
|
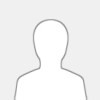 |
With longer, warmer days approaching, the sounds of summer are finally here: the drone of lawn mowers, the thwack of leather on willow and the incessant screams of young children demanding ice cream. To be fair though, there are plenty of adults who can’t pass a gelato shop, park cafe or ice cream van without succumbing to temptation either. There is just something so satisfying and refreshing about an ice cream on a hot day, to stay with a refrigerator, or you can call it refrigerator-freezer.
Ice cream has been around a long time. Some sources mention ice cream-like foods originating in Persia in about 550BC. Some even believe that the Roman Emperor Nero had snow collected from the mountains and mixed with honey and wine to make sorbet. These days we have hundreds of different types of ice cream, from the usual ice cream van favourites to gourmet gelatos and experimental savoury flavours.
On the face of it, the main ingredients of ice cream as we know it are really simple using a cooler: milk, cream and sugar. But just mixing these with some flavouring and putting it in the ice cream freezer is not going to give you a good result. The secret to great ice cream lies in how the mixture is mixed, how quickly it’s frozen and some key extra ingredients that change things like viscosity and freezing point – all important for the right texture and taste.
Emulsifiers
Brent Murray, professor of food colloids at the University of Leeds, believes understanding ice cream chemistry begins with realising that it’s an emulsion and a foam mixed together. ‘Your basic ice cream mix is just milk, cream, sugar and flavourings, which gets homogenised to form an emulsion of fat droplets in water, which wouldn’t ordinarily mix,’ he says. ‘There are natural emulsifiers present in the form of milk proteins, which surround the globules of fat and aid this process.
‘Some artisan ice creams leave it there, but most commercial recipes need to add extra emulsifier, like glycerol monostearate [GMS],’ Brent continues. ‘The confusing thing is that the role of this extra emulsifier isn’t to stabilise the emulsion even further, but rather to destabilise it a bit.’
Emulsifiers like GMS replace some of the milk protein molecules that surround each fat globule. ‘These small molecules, with lower molecular weight, will always outcompete the larger milk protein molecules, partially displacing them, and this can make the droplets slightly less stable. They stick together a bit more and that, in turn, helps the mixture to stabilise and retain air bubbles of small enough size,’ says Brent.
Air bubbles
As the mixture is stirred and frozen in the ice cream machine, it is also whipped to aerate it. Most ice creams have a significant amount of air trapped in them – up to 125% of the volume of the ingredients in some supermarket ‘value’ products, though less in gourmet-style gelatos.
‘To get the right creaminess and stability, the air bubbles in ice cream need to be about 20 µm in size, and as uniform as possible,’ continues Brent. ‘An air bubble that size in water would dissolve quickly – perhaps in a couple of minutes – because air is quite soluble in water. A combination of natural foaming agents (proteins again), the aggregated fat droplets, plus freezing as fast as possible to increase viscosity, helps to trap the bubbles at that small size.’You can use one type of freezer- Curverd Glass Type Ice Cream Chest Freezer.
Ice crystals
As well as air bubble size, another factor that affects the creaminess of ice cream is the amount of fat included in the first place, says Ruben Proto, founder of Manchester-based Rogue Artisan Ice Cream, who is famous for his scientific approach to gelato. ‘The amount of fat in the mixture masks the presence of any large ice crystals, so the end product is perceived as smooth and creamy in the mouth,’ he says.
While ice crystals are always present in ice cream, keeping them small (just as with air bubbles) is really important for a creamy result. ‘That’s really down to two things,’ Ruben continues, ‘the viscosity of the mixture and the rate of freezing. The more viscous the mixture, the creamier it is. You can control the viscosity either by upping the total amount of solids in the mix, like fat and sugar, or by using a stabiliser – I tend to use alginate.’
The rate of freezing has a big effect on the finished ice cream because it affects how large the ice crystals can grow. Large crystals can cause the end product to taste watery or icy, with a coarse, rough texture. The secret to great ice cream is to keep the crystals small. ‘There are two types of freezing,’ explains Ruben, ‘dynamic freezing, where the mixture is moved around at about -6˚C, usually in the ice-cream mixer, and static freezing, which is much colder and doesn’t involve any stirring. Ice crystals will grow in the dynamic freezing stage, but not during static freezing. So, you want to get your ice cream out of the machine as quickly as you can and into a cold chest or blast ice cream freezer at about -18˚C.’
‘If your freezer takes eight hours to get the mixture down to -18˚C then you are going to have more ice crystals in it than if you achieve that in two or four hours,’ Ruben says.
The walls of an ice-cream maker are pretty cold, about -32˚C with a fridge, but the mixture is moving all the time, so it never reaches this temperature. Of course, colder substances, which you’d usually find in the lab and not the kitchen, have also been tried, such as liquid nitrogen. ‘That’s terrific theatre!’ says Ruben. ‘And it creates an incredibly creamy product. With liquid nitrogen you only need one or two minutes in the ice machine before you can transfer to the deep freeze. The rate of crystal nucleation – the birth of ice crystals – is much faster, so there are more of them, but they are much smaller.’
What’s the alternative?
Experimental chefs like Heston Blumenthal were among the first to try approaches like liquid nitrogen freezing, alongside novel combinations of flavours. Who can forget Heston’s famous bacon and egg ice cream, which was on the menu at his restaurant The Fat Duck for years.
‘The secret with that kind of thing is to pick two flavours that have the same kind of flavour molecules in them, even if they don’t immediately sound compatible,’ says Ruben. ‘I had great success with chocolate and blue cheese ice cream and I’ve even experimented with roasted cricket.’
|
|
|
Steel, Glass, and Plastic Bottles: What is the best choice? |
Posted by: ttois155ssa - 09-08-2021, 01:32 AM - Forum: Welcomes and Introductions
- No Replies
|
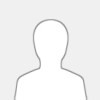 |
Earlier this year I published a three-part article series titled “What to do with all this plastic?” (Part One, Part Two, and Part Three), which looked at the global problem with plastics accumulating in different areas around the world and innovative concepts communities have adopted to help deal with the abundance of plastic products and manage the growing problem.
Some looked at the creative reuse of plastic water bottles by communities in Uganda, the Philippines, and right here in Macomb County, Michigan. Plant pots, salt shakers, lighting fixtures, irrigation, and even walls for a greenhouse were concepts communities came up with. While the articles highlighted some steps international and local communities are taking to curb the plastic problem it also provided steps to help eliminate it from every day use. One of those steps is to simply carry your own reusable bottle, which we are seeing more and more of these days. In fact, traditional public water fountains are becoming equipped to refill personal water bottles as well.
But between steel, plastic and glass, which is the best? The truth of the matter is that there are pros and cons to owning each.
Stainless steel bottles have a number of pros and cons. Typically, they last longer than glass or plastic because they are corrosion resistant, and do not leach chemicals when exposed to sun/heat. They are generally more expensive than plastic, as the cost to produce them is much higher due to being energy intensive. However, stainless steel is 100 percent recyclable. The best option for selecting stainless steel water bottles is food grade #304 or 18/8, which means there are 18 percent chromium and 8 percent nickel. Additional information on stainless steel water bottles can be found online.
Glass is another option when choosing water bottles. Most of us know that just about every beverage tastes better out of a glass bottle or cup, but the downside is that they are breakable and less likely to last a long time compared to plastic or stainless steel. In addition, recycling rate is low and some public places do not allow glass too. However, in addition to tasting great glass does not leach when left in the sun/heat, but the cost of a glass water bottle is generally much higher than our other two options.
Plastic seems to be the most popular reusable water bottle, although glass and stainless are gaining in popularity for the reasons listed here. Plastic water bottles, or water mugs are cheaper to produce than stainless steel and glass, which makes them very attractive for consumers. However, the recycling rate of some plastic water mugs is low and the life cycles are short too. Plastic water bottles often end up in landfills and can take nearly 700 years before they start to decompose. One of the biggest downsides to plastic water bottles is that they leach, whereas glass and stainless steel do not. Consumers with apprehensions over plastics leaching chemicals may want to review the U.S. Food and Drug Administration for more information, such as the use of Bisphenol A (BPA)-a chemical component often found in polycarbonate plastic. Some manufacturers of reusable water bottles do produce products free of this chemical and typically note that on labels or the item itself. In addition, plastics made with BPA will often have a resin code of 7 appearing on the item.
Additional information on plastics and problems associated with it can be found on Dr. Lee’s website devoted to health and sustainability related challenges.
Whatever reusable water bottle you decide to select in the end will be of overall benefit to you and our environment too. Reusing a water bottle will help keep plastics out of landfills, reduce your urge to purchase beverages in plastic bottles, and in the long-run save you money.
How are you ensuring safe drinking water when away from home and your preferred water treatment system? When it comes to drinking water, Ontario residents often invest in water systems and coolers to ensure a fresh supply of clean drinking water in the home. However, some fill plastic bottles with filtered drinking water and then reuse those bottles over and over. Unfortunately, this practice could be unsanitary. In addition, there are many concerns about the safety of BPA found in some plastic water bottles. While you could buy a BPA-free plastic water bottle, steel water bottles are a better choice. Below are just a few of the many benefits of stainless steel water bottles.
Stainless Steel Water Mugs are Eco-Friendly
Stainless steel is made out of natural elements to start with, and they can be easily recycled into new products when the time comes. Though plastic bottles are often made from recycled materials and can be recycled themselves, both creating and recycling plastic is less friendly to the environment than stainless steel production and recycling.
Stainless Steel Water Bottles are Much More Durable than Plastic
If you’ve ever used a plastic water bottle, you know how flimsy they can be. Some plastic water bottles are meant for one-time use and crush easily. Others are made to be used multiple times. However, those can melt when washed in the dishwasher. Even if you run over a stainless steel water bottle with your truck, it will survive.
Stainless steel bottles can be used under virtually any condition. Because of their versatility and durability, stainless steel water bottles are the bottles of choice for many athletes and adventurers, also are some glass water mugs.
Stainless Steel Water Bottles are Safe
The plastics in recyclable plastic water bottles are thought to be a health risk. Harmful chemicals are emitted from these bottles, and these chemicals might cause cancer. By switching to stainless steel, you can prevent harmful carcinogens from leaching into your drinking water.
Stainless Steel Water Bottles Keep Your Drinking Water Cold or Hot
Why drink lukewarm drinking water from a plastic water bottle when you could use a stainless steel water bottle that insulates the contents for hours? The insulating properties of stainless steel water bottles mean that you can enjoy cool drinking water up to 24 hours after filling the bottle from your water cooler. Hot water stays warm for nearly six hours in a stainless steel bottle.
You Can Wash Stainless Steel Water Bottles in the Dishwasher
Maintain sanitation by regularly washing your stainless steel water bottle in the dishwasher. Stainless steel is completely dishwasher safe, unlike plastic water bottles which could melt or lose their shape. Regular washing eliminates germs that accumulate after usage.
Environmentally friendly, durable, safe, and easy-to-clean, stainless steel water bottles are an excellent alternative to using plastic water bottles. The steel will not rust, and many desirable features are available such as special caps, cool colours, carrying straps, spouts, handles, clips, and unique shapes. You can even get a customised bottle if you’d like.
Don’t make the same mistake that many people who have invested in water systems in Ontario have made. Use stainless steel water bottles when venturing away from home.
|
|
|
Why Should You Use a Proper Wine Glass for Serving Wine? |
Posted by: ttois155ssa - 09-08-2021, 01:30 AM - Forum: Welcomes and Introductions
- No Replies
|
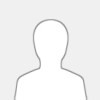 |
A large part of enjoying wine lies in savoring its aroma. The wine glass has to gather the wine’s aroma so you can savor it when you drink.
If you use a regular mug and fill it to the brim, all the characteristic vapors of the wine will be gone by the time you start to sip.
But, there’s more to it than just enjoying the wine’s aroma.
First, let’s step back to see how the modern wine glass came to be.
A Brief History of the Wine Glass
The earliest form of wine glasses are believed to be the silver and pottery goblets used by the Romans in the third century.
The wine glass that you know today, with the base, stem, and bowl, originated in the 1400s in Venice, Italy, where some of the best glass makers were centered.
But it was Claus Riedel in the 20th century, who was the first to acknowledge the correlation between the wine’s taste and the wine glass shape. He launched the first series of glasses designed to suit a wine’s character.
Since then, the wine glass has evolved to suit the different shapes and styles to suit the character of different types of wine, and Riedel continues to be a leading glassware brand.
Wine Glasses: Anatomy and Materials Used
How does a wine glass shape influence the drinking experience?
The wine glass shape is not only meant to collect the wine’s aroma but also influences how much wine flows into your mouth. It determines whether the wine moves across the tongue or spreads to the side.
This can actually make the same wine taste quite different indeed!
Parts of a wine glass
The wine glass can be a machine-blown or handmade glass and has these four parts, from bottom to top:
1. Foot
This is the flat base section of the glass that will hold the glass upright on your dining table. A small foot can make the champagne glass imbalanced, and the glass will easily topple on your dining tables. Too large a foot might get stuck under your platters and flatware or tableware.
2. Stem
The stem is the thin, neck section where you usually hold the wine glass or stemware. Holding it there prevents you from heating the wine with your fingers. It also keeps you from smudging the bowl with your fingerprints.
3. Bowl
The bowl is where you’ll see the most variation in wine glasses. The opening will usually be smaller than the shoulder (widest part of the bowl). This shape captures the aroma of the wine.
The bowl’s width determines the surface area of the wine. Some wines should be allowed to “breathe” more than others — this is typical of aged reds with intense, complex aromas.
4. Rim
The thinness of the rim can affect how you perceive the wine’s taste. A glass with a thin rim is much better than a thick rim glass, as it’ll let the wine flow smoothly into your mouth.
Wine glass materials
Wine glasses can be made of many different materials. While glass and crystal are the most common, alternate materials like acrylic and silicone are also used.
1. Soda-lime glass
Most glasses are of the soda-lime variety. It’s the same type of glass you’ll find on your window panes or food jars.
When used for wine glasses, it has the advantage of being more affordable than crystal. It’s inert and nonporous, meaning it won’t absorb chemical aromas, so it’s always dishwasher safe. That said, soda-lime wine glasses will tend to be thicker than crystal stemware and are more durable.
2. Crystal
Crystal wine glasses contain 2-30% of added minerals, which is its primary difference from regular whiskey glasses. Those minerals could be lead, magnesium, or zinc, allowing the crystal to be spun much thinner than glass but still retain structural strength.
Crystal glassware also refracts light better, making your wine look sparkly in the glass.
However, the addition of minerals to the crystal makes it porous and not always dishwasher safe.
You also have the option of leaded vs. lead-free crystal stemware:
Historically, all crystal glasses had lead added, and many still do. Leaded crystal wine glasses are safe, as your wine won’t stay long enough in the glass for the lead to leach into it.
But some glass manufacturers have moved to lead-free crystal because of the potential health concerns (like storing liquor in a leaded decanter for a longer period).
Lead-free crystal glasses typically have magnesium or zinc additions and are usually dishwasher safe.
Manufacturers like Schott Zwiesel have gone a step further, patenting a crystal called Tritan®, which has infused titanium and zirconium. This makes a highly break-resistant lead-free glass.
3. Alternative materials
Other materials commonly used for lower-end wine drinking glasses would be acrylics, metals like stainless steel and silicone.
Wine glass decoration
Most high-end wine glasses won’t have designs on the bowl, as you don’t want to distract the view of the wine. You may come across a few exceptions like the Mikasa Cheer White Wine Glasses that have designs on the bowl.
However, you’ll often find finely decorated stems on some of the wine glasses.
In the 18th century, glassmakers would draw spiral patterns on the stem. You’ll find these even now on antique and vintage glassware.
What is a “Standard Pour” of Wine?
Usually, in restaurants, a tumbler glass would be around 5oz (~150ml). This portions a 750ml bottle of wine into five servings.
For wine tastings, the standard is around 2oz, which is enough to experience the wine’s aroma and flavor without being affected by the alcohol too fast.
Dessert wine servings are around 2oz, too, as these wines are much sweeter and have more alcohol than other wines.
1. Red Wine Glass
Red wine glass has a round, wide bowl, like balloon glasses. The shape increases the exposed surface area of the wine, allowing more oxygen to interact with the liquid. Brief exposure to oxygen helps smoothen the complex flavors and tannins in red wine.
There are three types of red wine glasses:
A. Bordeaux glass
This tall glass with wine decanter is meant for bold, full bodied red wines like Cabernet Sauvignon, Cabernet Franc, Merlot, or Bordeaux Blends.
The glass is tall, but the bowl isn’t quite as large. The bowl’s height creates more space between the wine and nose, allowing room for ethanol vapors to escape, letting you get more of the wine’s aroma and less alcohol vapors.
Some Bordeaux wine glasses to consider:
Zalto Denk Art Bordeaux Glass with glass charger plate
Schott Zwiesel Tritan Pure Bordeaux Glass
B. Standard (Medium-bodied) wine glass
This is an excellent choice for medium- to full-bodied red wine, like Syrah or Malbec. The smaller opening will soften the spicy expression of some of these wines as it hits your tongue, but it keeps the aroma in the shot glass.
C. Burgundy (Bourgogne) glass
The Burgundy glass is designed for light, delicate red wine like Montrachet. The broad bowl creates space for aromas to collect, and a shorter lip directs the wine to the tip of the tongue so that you can taste more of its subtle flavors. The Pinot Noir glass is an example of the Burgundy glass. Also, there is bear glass.
|
|
|
Which type of PVC sheet do I need for my application? |
Posted by: ttois155ssa - 09-08-2021, 01:28 AM - Forum: Welcomes and Introductions
- No Replies
|
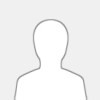 |
What is PVC (PolyVinyl Chloride)?
Polyvinyl Chloride (PVC or Vinyl) is an economical and versatile thermoplastic polymer widely used in building and construction industry to produce door and window profiles, pipes (drinking and wastewater), wire and cable insulation, medical devices, etc. It is the world’s third largest thermoplastic material by volume after polyethylene and polypropylene.
It is a white, brittle solid material available in powder form or granules. Due to its versatile properties, such as lightweight, durable, low cost and easy processability, PVC sheet is now replacing traditional building materials like wood, metal, concrete, rubber, ceramics, etc. in several applications.
Basic Forms of PVC(including PVC rod)
Polyvinyl Chloride is widely available in two broad categories: Flexible and Rigid. But, there are more types like CPVC, PVC-O and PVC-M.
Plasticized or Flexible PVC (Density: 1.1-1.35 g/cm3): Flexible PVC is formed by the addition of compatible plasticizers to PVC which lower the crystallinity. These plasticizers act like lubricants resulting in a much clearer and flexible plastic. This type of PVC is sometimes called as PVC-P.
Unplasticized or Rigid PVC (Density: 1.3-1.45 g/cm3): It is a stiff and cost-effective plastic with high resistance to impact, water, weather, chemicals and corrosive environments. This type of PVC is also known as UPVC, PVC-U or uPVC.
Chlorinated Polyvinyl Chloride or perchlorovinyl: It is prepared by chlorination of PVC resin. High chlorine content imparts high durability, chemical stability and flame retardancy. CPVC can withstand a wider range of temperatures.
Molecular Oriented PVC or PVC-O: It is formed by reorganizing the amorphous structure of PVC-U into a layered structured. Bi-axially oriented PVC has enhanced physical characteristics (stiffness, fatigue resistance, lightweight, etc.).
Modified PVC or PVC-M: It is an alloy of PVC formed by addition of modifying agents, resulting in enhanced toughness and impact properties.
Polyvinyl Chloride (PVC) is one of the most widely used polymers in the world. Due to its versatile nature, PVC, or other plastic rod, is used extensively across a broad range of industrial, technical and everyday applications including widespread use in building, transport, packaging, electrical/electronic and healthcare applications.
PVC, including soft PVC sheet roll, is a very durable and long lasting material which can be used in a variety of applications, either rigid or flexible, white or black and a wide range of colours in between.
The essential raw materials for PVC are derived from salt and oil. The electrolysis of salt water produces chlorine, which is combined with ethylene (obtained from oil) to form vinyl chloride monomer (VCM). Molecules of VCM are polymerised to form PVC resin, to which appropriate additives are incorporated to make a customised PVC compound .
The PVC production process consists of 5 steps:
The extraction of salt and hydrocarbon resources
The production of ethylene and chlorine from these resources
The combination of chlorine and ethylene to make the vinyl chloride monomer (VCM)
The polymerisation of VCM to make poly-vinyl-chloride (PVC)
The blending of PVC polymer with other materials to produce different formulations providing a wide range of physical properties.
PVC sheet, PE sheet and PP sheet have excellent corrosion resistance and weather resistance. The working temp is 33 deg F to 160 deg F. and the forming temperatures of 245 deg F. It is good electrical and thermal insulator and has a self-extinguishing per UL Test 94. PVC applications are almost unlimited. It's the most widely used member of the vinyl family. It is excellent when used for corrosion-resistant tanks, ducts, fume hoods, and pipe. Ideal for self-supporting tanks, fabricated parts, tank linings, and spacers. It is not UV stabilized and has a tolerance of +or 10%. Not FDA approved materials. Colors available: Gray PVC Type 1 Sheet, White PVC, Clear PVC.
|
|
|
What Is a Brake Caliper |
Posted by: ttois155ssa - 09-08-2021, 01:26 AM - Forum: Welcomes and Introductions
- No Replies
|
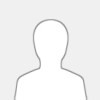 |
If your car is equipped with disc brakes, brake calipers are critical to slowing and stopping your car. Here's what you need to know.
The brake caliper plays a central role in a disc-brake system and has two functions. First, it acts either as a bracket to support the brake pads on either side of the rotor or to support the caliper bracket itself — there are other designs, but these are the two most common. Second, it uses pistons to convert pressure exerted on the brake fluid by the master cylinder into friction on the rotor.
In simple terms, a brake caliper’s purpose is to squeeze the brake pads against the rotor to stop the car. There are two main types of calipers, a single piston and a dual piston. Most front calipers are dual piston but many cars use single piston calipers on the rear, where less braking force is needed.
Stepping on the brake pedal forces the master cylinder piston forward, compressing the brake fluid. The brake fluid forces the brake caliper pistons toward the rotors, pinching the rotors in between the brake pads, which creates friction and slows the vehicle.
When Brake Calipers Go Bad
In general, brake pads and rotors wear out and need replacement far more often than calipers. A leading cause for damaged calipers, however, stems from driving a vehicle on worn-out pads or warped rotors. Both prevent the system from dissipating the heat of friction, as they’re designed to do, which can damage the calipers.
If the pads fail to insulate the caliper from excessive heat, the piston can be damaged or the heat can be passed through the piston to the brake fluid, which can cause it to degrade. The latter can result in brake failure.
A damaged piston, or one that is simply corroded, may get stuck in one position. If it sticks in the retracted position, that wheel will lose braking ability. If it sticks in the engaged position, the wheel will brake continuously until freed.
How to Tell That a Caliper Has Failed
With a retracted piston, the car may pull toward the side of the car with operating brakes when they are engaged. You may also notice that braking distance increases. Conversely, an engaged piston will cause the car to pull toward the engaged brake when driving. (Note: A stuck caliper can cause pulling, but there are many other possible causes as well.) Excess heat will be present, and the brake pad will quickly wear down. Any of these symptoms indicate immediate need for service.
Another sign of caliper failure could include leaking brake fluid, as a damaged piston may no longer seal completely. If enough fluid escapes from the system, the warning light on the dashboard will call your attention to it. If you check your pad wear regularly, you may note uneven wear on the pads, comparing one side of the rotor to the other, or even left wheel to right wheel. If the pads show uneven wear, check the caliper function. And yet another sign of a seized caliper is excessive brake dust on one wheel compared to the other.
In the rarest form of failure, the caliper bracket could snap, causing a clunking sound when the brakes engage. If you hear this, stop immediately and do not operate the vehicle.
Ignoring any of these symptoms can magnify the damage. The cost and effort required to address the problem increases proportionally. Make an effort to examine the problem as soon as possible or have it evaluated by a qualified technician.
Important Maintenance Points
• As the brake pads wear, the caliper needs to stay centered on the rotor to allow for even pressure on both sides. There are different ways manufacturers accomplish this, and some designs are better than others at keeping the calipers sliding to compensate for pad wear. When brake service is done, always clean and grease the sliding mechanisms with a high-temp brake grease to preserve the full range of travel. If not properly lubricated, calipers can lock in one position, resulting in only one pad getting proper pressure on the rotor.
• Whenever possible, inspect the dust boots protecting the caliper piston and the two slide pins. These flexible covers prevent dirt and moisture from fouling the action of the associated parts. Any damage or tears found in the boots must be addressed quickly, before dirt and corrosion cause the parts to seize. It is possible to disassemble the caliper, clean the parts and replace the boots if you have some skill as a DIYer. Labor charges, however, make this impractical in most auto shop situations, so the most common resolution is full replacement of the caliper and bracket.
Regardless of the type of support, it is designed to have parts that withstand increased wear. The pads and discs we have not considered because they are considered consumables. As for the support, the return movement of the piston is provided by a rubber sleeve. When the driver depresses the brake pedal, the piston comes out of the body and deforms the brake sleeve kit, when the pedal is released, the cuff tends to present a starting position and drags the piston.
The brake system includes brake calipers, brake discs, brake pads(including brake pad fitting kits), steel pipes, brake fluid, etc. There are also brake rubber dust cover kits.
|
|
|
|