Welcome, Guest |
You have to register before you can post on our site.
|
Online Users |
There are currently 273 online users. » 0 Member(s) | 272 Guest(s) Google
|
Latest Threads |
Dominica visa free countr...
Forum: Off Topic
Last Post: axied12
06-24-2025, 12:37 PM
» Replies: 0
» Views: 207
|
Advanced microneedling
Forum: Off Topic
Last Post: axied12
05-28-2025, 01:25 PM
» Replies: 0
» Views: 333
|
Caviar and cheese
Forum: Off Topic
Last Post: axied12
05-28-2025, 12:38 PM
» Replies: 0
» Views: 294
|
Top-rated countertop comp...
Forum: Off Topic
Last Post: axied12
05-04-2025, 06:42 AM
» Replies: 0
» Views: 445
|
Ryanair letenky levně do ...
Forum: Off Topic
Last Post: axied12
02-11-2025, 01:37 PM
» Replies: 0
» Views: 838
|
Trusted essay writing ser...
Forum: Off Topic
Last Post: axied12
01-30-2025, 08:16 AM
» Replies: 0
» Views: 753
|
Bootverkopers - actieve j...
Forum: Off Topic
Last Post: axied12
12-07-2024, 11:07 AM
» Replies: 0
» Views: 880
|
Services for individuals ...
Forum: Off Topic
Last Post: axied12
12-02-2024, 03:31 PM
» Replies: 0
» Views: 855
|
Used excavators
Forum: Off Topic
Last Post: axied12
11-13-2024, 09:22 AM
» Replies: 0
» Views: 801
|
Buy Higo Rocket in Dubai
Forum: Off Topic
Last Post: axied12
10-25-2024, 01:09 PM
» Replies: 0
» Views: 910
|
|
|
How to buy your first disposable diaper machine. |
Posted by: yyoijw484s - 09-10-2021, 02:39 AM - Forum: Welcomes and Introductions
- No Replies
|
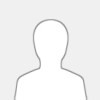 |
Every disposable diaper manufacturer knows that the most difficult machine to buy is always the first one. Based on their earned experience with this first machine, diaper manufacturers become more knowledgeable and more cautious when buying their second or third machine. If only this level of knowledge was available to them from the beginning, they would have saved tens of thousands and in many cases even hundreds of thousands of dollars.
Make sure you ask for the same exact items or the same diaper machine modules from all potential vendors; make sure each machine module is really equivalent in terms of the technology and process control; the acceptable performance for your equipment has to be well defined as part of the purchasing contract. It is easy to promise, some vendors do whatever it takes to try to close a deal, but to deliver against a well-defined contract is something else, few will take the risk. It is always better to visit an actual factory running the equipment instead of just visiting the equipment manufacturer. Of course, this is not always possible, but at least try.
Make sure you have enough money left after the purchase of the machine to use for working capital. Keep in mind that the baby diaper machine and the building are probably just half of the total investment you will need to operate your new business, that is unless you already have excellent credit ratings to use for working capital. Starting up a new diaper factory without money in your pocket is the very worst thing you can do.
Processing wood into tissue paper is a complex technological procedure. However, using complex machines to transform big jumbo reels of tissue paper into the form of high-quality napkins or toilet tissue is real high tech. The tissue paper machines perform many work steps to manufacture the finished product. They unwind, print, emboss, rewind, fold, cut, wrap and bundle within seconds and fully automatically.
According to a specific application inside a market segment, the hygienic tissue paper products are manufactured to meet the desired performance. The most important properties used to evaluate the performance of tissue products are - softness, water absorbency, disintegration, and strength (dry or wet). A vast number of fiber types, chemical additives, sanitary machine technologies are available in the market for the manufacturing of tissue products. The right combination of additives, fibers, additives, and technologies have to be chosen by the tissue paper manufacturers to produce specific tissue products capable of achieving the desired performance while providing enough profitability to the producer. Paper products can be placed in three main categories, based on their function.
Even if you’re fully vaccinated, you’ll likely run into situations in which masks are strongly recommended, if not required. Which means unfortunately we’ll all need to have some masks on hand. While not as sustainable as reusable cloth masks, disposable masks are also a good option — especially if you find the right ones.
The very best disposable face masks, of course, are KN95 masks — the gold-standard pandemic masks, approved by the National Institute for Occupational Safety and Health (NIOSH), which filter out 95 percent of airborne particles. These are closely followed by the disposable surgical masks worn by doctors and other health-care professionals, which are cleared by the FDA as meeting certain standards.
Early in the pandemic, the CDC did not recommend that the public buy these masks in order to ensure a steady supply for health-care workers, but those restrictions have relaxed slightly now that such masks are more regularly available. So while it’s still not a good idea to hoard KN95 or medical masks, you can feel better keeping one or two around for especially high-risk occasions, like a plane ride or spending a long period of time in a crowded enclosed space. Our mask making machine is sold well in the world market and worth recommendation for its excellent quality and reasonable price.
|
|
|
Basketball Goal / Basketball Stand |
Posted by: yyoijw484s - 09-10-2021, 02:37 AM - Forum: Welcomes and Introductions
- No Replies
|
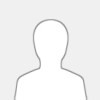 |
Basketball goal and basketball stand are two terms that are often used interchangeably. Our customers frequently ask us if there is a difference between basketball stands and basketball goals. When it is time to shop for sports equipment, it is helpful to understand the terminology, after all. Technically, the movable basketball stand refers to the orange rim that is mounted to the backboard, but in common language, the terms are used when people are referring to the complete sets that make up basketball systems. Here at First Team Sports, we use the term basketball goals when referring to either complete basketball goal systems or the rims themselves. We offer a comprehensive line of made in the USA indoor and outdoor sports equipment: basketball backboard systems (wall mount basketball goals or on a post) for team sports, adjustable goals for kids, portable goals for indoor games and driveway outdoor play, and commercial basketball goals that can stand up to the most aggressive playgrounds. Our basketball buying guide and basketball goal pictures can help you understand the differences between the types of basketball equipment for sale. Call First Team today to get started!
Parts of a Basketball System
A complete basketball system consists of the same general parts, whether it is an in ground basketball goal, a portable basketball goal, or an adjustable portable goal.
What are the basic elements of a basketball goal system?
- Backboard: Backboards can be rectangular or fan shaped, and are available in many different sizes and materials. First Team offers everything from regulation size tempered glass wall mount backboards for colleges to an affordable acrylic backboard and rim combo-portable basketball system units for home use. (Acrylic provides a better rebound than a polycarbonate backboard). We also offer backboards in steel, perforated aluminum, fiberglass, and smoked tempered glass.
- Rim: The orange basketball ring from which the net hangs. Can also be called the goal or stand. Options include the competition breakaway steel rim, heavy-duty or recreation flex goal, and the fixed rim. First Team also offers ultra heavy double rims for playgrounds where aggressive play is the norm.
- Net: Made of nylon or metal chain (for playgrounds).
- Extension Arm (or boom): The extension arm projects forward from the vertical post to create the overhang for the safe play area. On fixed inground basketball goals, the extension arm does not move. On a First Team portable basketball goal, the extension arm folds down to a height that can easily fit under a door frame for storage next to your outdoor power equipment in the garage or roll into a storage closet in your gymnasium. Many of our wall mount acrylic or glass backboards offer an adjustable arm that allows you to set a custom distance from wall to backboard to align with your existing basketball court markings. Some models also feature an arm that folds back to one side to store the backboard safely to make room for other sports in multi-use facilities.
- Post / Pole: Also called the support structure or standard, this is the vertical piece to which the backboard is attached. Depending on the model, our adjustable units can easily moved from as low 5'6” up to the full 10' regulation basketball goal height. Wall mount and roof mount products will not have a vertical post.
Quality Counts
The basketball goal vs. basketball stand terminology can also have to do with the quality of the basketball training equipment. If you are shopping online for a cheap portable unit for a toddler or little kid, it will be called a foldable basketball stand. The same is true for a table basketball game, a cheap pro mini stand with over-the-door mounts, flimsy plastic units for pools, or a product like the Spalding acrylic backboard set or Spalding polycarbonate portable basketball goal Walmart sells. Top brands in the sport generally call their equipment basketball goals or systems. At First Team, we take great pride in manufacturing the most well-made goals and accessories for your home, school, recreational facility, gymnasium, playground, and even your pool. Read the reviews to learn how different a heavy duty American made basketball system is as compared to lightweight units. When you want sports equipment that will last for years, or even a lifetime, call First Team. From ultra-safe and sturdy patio basketball goals for kids to a regulation tempered glass backboard with a breakaway basketball goal that meets all standards for NCAA men and women's competition, we manufacture it all to the most exacting standards right here in the USA. If you are training basketball players to excel at their sport, get on board with the best!
Adult outdoor fitness spaces are a relatively new yet popular amenity in the world of fitness. The trend emerged in 2012 in parks worldwide. Today, outdoor fitness equipment is an essential element of many park plans. Considering the concept of an outdoor gym is new to many, some parks departments and city planners struggle with where to start with planning such a space. This article looks into what to consider when planning an outdoor gym and answers a frequent question - how much does outdoor fitness equipment cost?
: Is There a Difference? 内容:
|
|
|
3 Things to Consider when Choosing a Centrifuge Tube |
Posted by: yyoijw484s - 09-10-2021, 02:36 AM - Forum: Welcomes and Introductions
- No Replies
|
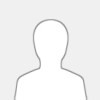 |
Centrifuge tubes range a lot in terms of quality and performance. There are multiple factors that contribute to the overall quality of the tube that we will discuss in this article. It’s important to take into account your own requirements of a tube medical and then choose a tube that is going to best suit these requirements.
Relative Centrifugal Force
A centrifuge tube will have a maximum speed rating at which the tube can withstand. The speed capacities of tubes will vary greatly between brands so it is important to determine what speeds you will require and go for a tube that will be able to withstand these speeds. When looking at speeds, it is best to look at RCF rather than RPM as RCF takes into account the gravitational force being applied. RPM, on the other hand, only takes into account the rotors spinning speed.
Pricing can vary depending on the maximum RCF a tube can handle so firstly, work out the RCF you will require and find a tube that fits to these requirements. If you are not dealing with high speeds, you may be able to choose a tube with a lower RCF to save on costs of the tubes. If you are a volume user, any potential savings on the tubes can add up to a sizeable amount over time.
Chemical Compatibility
Depending on the type of material the centrifuge tube is made out of, it will obviously have different resistance capabilities to different chemicals. It is important to take into account the types of chemicals you will be using and ensure that the tube you choose has satisfactory resistance to these chemicals. Centrifuge tubes are available in an array of materials such as polypropylene (PP), polyallomer (PA), polycarbonate (PC), and polyethylene terephthalate (PET). PP is a popular type of tube due to its ability to be used for high speed applications, is autoclavable, and is resistance to most organic solvents. Be sure to check a chemical resistance chart to determine what tube will be most suitable for your laboratory.
Volume
Note that you should never overfill a centrifuge tube as it can cause leakages. The maximum you should ever fill a centrifuge tube is ¾ full. Some ultracentrifuge tubes, however, must be filled to the top to prevent collapse. You also need to ensure that you don’t underfill the tubes either. It is always best to make sure you check the product specifications from the manufacturer as they will provide filling guidelines. With this is mind, the tube you select will need to be based on the volume you will be using. If you find that the tube most suitable for the volume you are using will not fit the rotor capacity of your centrifuge then consider an adapter for the rotor. Most manufacturers will have these adapters available so speak to your supplier about an adapter to suit your needs.
A centrifuge tube is an important consumable in any laboratory and the decision upon what tube will best suit your laboratory should not be taken lightly. Suppliers will be able to provide samples for testing prior to committing to order. This gives you the opportunity to put the tube through its paces to ensure that it performs. If you can, get a few different brands to sample and run the same tests on each, this will further assist you in making your decision.
There are many questions about what a rapid test, swab and PCR are and how they are different. All three are terms related to the diagnosis of Covid-19. Equipping yourself with knowledge about these three things is important in this pandemic. Swab and PCR are inseparable test methods to diagnose Covid-19. Swab medical is a way to obtain examination material (sample). Swab is done on the nasopharynx and/or oropharynx. This collection is done by rubbing the nasopharyngeal cavity and/or oropharynx using a tool such as a special cotton swab.
The collection of whole air or gas "grab samples" with commercially available gas sampling bags is a widely used sampling method in fields such as environmental science and industrial hygiene, as well as in a variety of laboratory and technical applications.
The traditional grab sampling method with gas sample bags requires the use of a pump to fill the sampling bag in one of two ways. The Direct Method uses a vacuum pump to draw air from the ambient air being sampled, which then passes through the pump and is loaded into the sample bag. This method is easy to use but allows for potential cross-contamination from the inner parts of the pump fittings and any connection tubing. The Indirect Method employs a hard-walled, hermetically sealed box that is commonly referred to as a lung box. The sampling bag is fixed inside the lung box and connected to the interior fitting inlet. When the lung box is evacuated by a vacuum pump, the sample bag inflates and a sample is collected.
For many researchers, selecting a sample collection kit is one of the first steps in beginning a small- or large-scale clinical study/biobanking project. Deciding how to go about collecting and storing patient/donor samples is paramount to ensuring the success of future assays, and there are a lot of factors to consider. Commercially available collection kits are a good option, but some researchers may prefer to rely on bulk collection supplies.
The Petri dish has been around for over a decade and yet the simple cell growing tools remain a permanent fixture in many laboratories around the world. The shallow cylindrical glass or plastic lidded dishes are most commonly used by biologists to make agar plates, which bacteria can be cultured upon. They are also useful for examining the efficacy of antibiotic drugs in development.
Finding the perfect pipettte and optimizing its use depends on a myriad of factors—some obvious, like the importance of precision and accuracy, and some more specific, like the ability to use the pipette while it is charging.
|
|
|
Hand Held Bidet – Benefits |
Posted by: yyoijw484s - 09-10-2021, 02:35 AM - Forum: Welcomes and Introductions
- No Replies
|
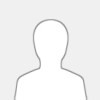 |
When the world is moving towards healthier choices, you shouldn’t be left behind either. Let’s take a peek at the what's and whys of this Bidet sprayer and you can see for yourself if it is worth all its hype!
What is a bidet spray?
The bathtub sprayer is essentially a hand-held toilet shower, which is used for cleaning after relaxation.
The shower head is connected to the end of the long hose connected to the water inlet. By pressing the trigger, the water flow can be easily controlled from mild injection to high-pressure injection. Release the lever to turn off the water immediately.
Bidet shower is very common in India, most other Asian countries and Islamic countries. It is also called sanitary faucet, shattaf bidet spray or layman's burning gun.
Why consider installing one?
There are many reasons for choosing to use a handheld bathing basin spray. We list two important issues below.
Reduce the chance of bacterial infection: wiping with toilet paper may still leave some feces. Washing with water is just like washing your hands after going to the toilet. It is cleaner, so it is safer and more hygienic.
Eco friendly: as you may have realized, it no longer needs to spend a lot of money on toilet paper. This is fully manually controlled and therefore replaces the electric water jet toilet being used.
This is a perfect DIY project!
If setting up and repairing things is your business, then setting up the handheld bathtub sprayer kit in the toilet may be your next project, or even your first project, because it is very simple!
The kit includes a T valve adapter, a flexible hose, a sprayer bracket, an oil tank side hook and a sprinkler head.
Buying and installing a hand-held bidet shower is a one-time cost, and the increased water consumption will not be offset by your savings. Therefore, this zinc shattaf bidet spray will certainly reduce your pocket, especially considering the long life of the product.
As you search for a new bathroom & kitchen faucet, you’ll see a number of other options to choose from that influence the overall style and operation of the faucet in your home. It’s a good idea to understand the basic configurations before you choose, to be aware of the product information and ensure you get exactly the features you want.
In a counter- or deck-mounted installation, kitchen faucets can be mounted on the counter or sink edge. Deck mounted is the more common style, and it helps draw attention to the sink as a design element in your kitchen. Here you’ll find the largest variety of faucets, ranging from single-hole mounts to up to three-hole mounts, in all sizes and finishes. Wall-mounted kitchen faucets are often found in more commercial or industrial locations, with a unique and modern style. Home kitchens, laundry rooms, garages, and greenhouses often rely on wall-mounted faucets for their space-saving design. In smaller kitchens with limited counter space, wall-mounted faucets free up the counter and allow different design options for the sink, and unique plumbing profile lines.
Valves are mechanical or electro-mechanical devices that are used to control the movement of liquids, gases, powders, etc. through pipes or tubes, or from tanks or other containers. In most instances, valves rely on some form of mechanical barrier—a plate, a ball, a diaphragm, for example—that can be inserted and removed from the flow stream of the material passing by. Some valves are designed as on-off varieties, while others allow very fine control of the passage of media.
Ball Valves are quarter-turn valves incorporating ported spheres that swivel in the pipe stream to either block, or allow, flow. Special designs are available which enable a degree of flow regulation. Key specifications include the number of ports, port configuration, port connections, valve size, and the materials that make up the valve body, its seat, seal, and stem packing. Ball valves are used practically anywhere a fluid flow must be shut off, from a compressed-air line to a high-pressure, hydraulic system. Ball valves can provide low head-loss characteristics as the port can exactly match the pipe diameter. Ball valves also tend to seal better than butterfly valves, but they can be costlier to purchase and maintain. Typically they are actuated with a lever which provides a visual indication of the valve status.
Float Valves are mechanical devices that use hollow spheres or other shapes mounted on levers or tracks which open and close fluid inlets. A float valve is used primarily for maintaining fluid in a tank at a specific level. Key specifications include the intended application, port connections, valve size, float size, and the materials that make up the valve body, its seal and float. Float valves are used in bathroom toilets to replenish the water level after a flush and in many tank-level control systems.
Globe valves are used for shut-off and regulating, and are used in wastewater plants, food processing facilities, and process plants, for example. The most common variety is the Z-style valve, so-called because of the path through which the fluid follows through the valve body. These two right-angle turns that the fluid must make through the valve account for the design’s relatively high head losses. A less restrictive design is the Y-style valve, which orients the valve stem at 45° to the valve body. Another style is the angle valve, which turns the flow 90°.
|
|
|
What Are the Different Types of Light Bulb Fittings, Caps and Bases? |
Posted by: yyoijw484s - 09-10-2021, 02:33 AM - Forum: Welcomes and Introductions
- No Replies
|
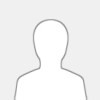 |
The part of the oven lamp or light bulb that connects into the light fitting is generally known either as the cap or base. Caps provide the electrical contact to conduct electricity to the light bulb but it also helps to secure the light bulb into its fitting.
There are a vast variety of caps and bases that exist in order to help make sure that only the correct type of lamp is used in any given fitting. This section shows many of the most popular fittings.
Named after the pioneering inventor Thomas Edison, the Edison screw oven lamp or ES lamp fitting is used worldwide in a vast range of applications. The most popular ES or E27 fitting is 27mm diameter and is widely used in UK and Europe. This cap is the standard 27mm diameter screw cap for UK 240V light bulbs – not to be confused with E26, which is a 26mm size and is designed for the 120V US market.
The G9 Oven lamp is specifically used for 240V capsule light bulbs. The light bulb can be identified by measuring the distance between the center points of the pins. The distance of a G9 measures 9mm.
LED Capsule Bulbs are now also available as an energy-efficient alternative to light bulbs. The fitments on LED capsules are exactly the same as those on halogen capsules, so if you’re replacing your current light bulbs with LED light bulbs and your fitting accepts one of the standard types listed here, you should be able to install them without an issue.
Different light bulbs are designed for different needs, environments, and situations. If you need a bulb that will last a long time, save you money and deliver bright light, then an LED light bulb with a high lumen output is best for you. If you want a light bulb that is budget-friendly, stylish and great for decorative lighting, then a candle-shaped halogen bulb with a low colour temperature is what you need.
UNDERSTANDING LIGHT BULB CAP TYPES AND BASE FITTINGS
Choosing the correct cap type or base fitting is the most important step when it comes to finding the right light bulb. The cap type or base fitting both conducts electricity to the light bulb and secures it into the fixture. Buying a bulb with the wrong Oven lamp holder simply means your lamp will not fit into the fixture – so it’s incredibly important you get it right.
The first letter of the code tells you the base or cap type of the bulb - such as a Bayonet Cap or Edison Screw Base.
The numbers reveal the diameter of the base, or the distance between the pins. This is listed in millimeters.
Some codes will also have additional letters after the numbers. This shows the number of pins or contacts the base has – such as ‘s’ for single, or ‘d’ for double.
So for example, the most common Bayonet Cap base fitting is listed as a B22d fitting. The ‘B’ stands for Bayonet Collar, while the ‘22’ means the base is 22mm in diameter. The ‘d’ at the end of the code means the base has two pins.
Candlelight bulbs feature a design based off the flame of a candle. This attractive ‘flame’ shape naturally gives them a decorative, elegant and vintage look perfect for ornamental lighting in hotels, restaurants and bars. As such, candle bulbs are most commonly used as decorative light bulbs in chandeliers, wall lights and exposed fixtures. Candle light bulbs are generally fitted with an E27 Edison screw base, E14 Oven lamp holder or B22 bayonet cap.
The Edison screw base is another of the most commonly seen base fittings in the UK. As their name suggests, Edison screw bulbs simply screw into the socket of a light fixture.
The most frequently seen size of the Edison screw is the E27 – a fitting that measures 27mm in diameter across its base. Other sizes of Edison screw are available, such as the E17, E26 and E39, but the E27 is the most commonly used in the UK and Europe.
E27s are available in a wide range of wattages and are used for a variety of applications.
Capsule bulbs sometimes called capsule lamps, use a push-fit base. Rather than being screwed or twisted into the fitting, these capsules have two pins in the base that allows them to be pushed into a fixture.
These small capsules are named and categorised by the distance between their two connecting pins. The G4 is one of the most frequently used bases for capsule lamps, and has pins that are 4mm apart. The G9 Oven lamp holder is also used for capsule bulbs, and features pins measuring 9mm apart.
|
|
|
Introduction to Pressure Seal valves |
Posted by: Y454AAA - 09-09-2021, 08:34 AM - Forum: Welcomes and Introductions
- No Replies
|
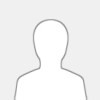 |
Introduction to Pressure Seal valves
Pressure seal construction is adopted for Valves for high pressure service, typically in excess of above 170 bar. The
unique feature about the pressure seal Bonnet is that the body-Bonnet joints seals improves as the internal pressure in the
Valve increases, compared to other constructions where the increase in internal pressure tends to create leaks in the body-
Bonnet joint.
The higher the internal pressure, the greater the sealing force. Easy dismantling is made possible by dropping the
Bonnet assembly into the body cavity and driving out the four-segmental thrust rings by means of a push pin.
Relying on fairly simple design principles, pressure seal
valves have proven their capability to handle increasingly demanding fossil and combined-cycle steam isolation
applications, as designers continue to push boiler, HRSG, and piping system pressure/temperature envelopes. Pressure seal
Valves are typically available in size ranges from 2 inches to 24 inches and ASME B16.34 pressure classes from #600 to #2500,
although some manufacturers can accommodate the need for larger diameters and higher ratings for special applications.
Pressure seal gate valves are
available in many material qualities such as A105 forged and Gr.WCB cast, alloy F22 forged and Gr.WC9 cast; F11 forged and
Gr.WC6 cast, austenitic stainless F316 forged and Gr.CF8M cast; for over 500°C, F316H forged and suitable austenitic cast
grades.
The pressure seal design concept can be traced back to the mid-1900s, when, faced with ever increasing pressures and
temperatures (primarily in power applications), Valve manufacturers began designing alternatives to the traditional bolted-
Bonnet approach to sealing the body/Bonnet joint. Along with providing a higher level of pressure boundary sealing integrity,
many of the pressure seal globe valves
design weighed significantly less than their bolted Bonnet Valve counterparts.
Bolted Bonnets vs. Pressure Seals
To better understand the pressure seal design concept, let's contrast the body-to-Bonnet sealing mechanism between
bolted Bonnets and pressure seals. FIG. 1 depicts the typical Bolted Bonnet valve. The body flange and Bonnet flange are
joined by studs and nuts, with a gasket of suitable design/material inserted between the flange faces to facilitate sealing.
Studs/nuts/bolts are tightened to prescribed torques in a pattern defined by the manufacturer to affect optimal sealing.
However, as system pressure increases, the potential for leakage through the body/Bonnet joint also increases.
Pressure Seal Gaskets
One of the primary components involved in sealing the pressure seal Valve is the gasket itself. Early pressure seal
gaskets were manufactured from iron or soft steel. These gaskets were subsequently silver-plated to take advantage of the
softer plating material's ability to provide a tighter seal. Due to the pressure applied during the Valve's
hydrotest, a set (or deformation of the gasket profile) between the Bonnet and gasket was taken. Because of the inherent
Bonnet take-up bolt and pressure seal joint elasticity, the potential for the Bonnet to move and break that set when
subjected to system pressure increases/ decreases existed, with body/Bonnet joint leakage the result.
This problem could be effectively negated by utilizing the practice of "hot torquing" the Bonnet take-up bolts
after system pressure and temperature equalization, but it required owner/user maintenance personnel to do so after plant
startup. If this practice was not adhered to, the potential for leakage through the body/Bonnet joint existed, which could
damage the pressure seal gasket, the Bonnet and/or the I.D. of the Valve body, as well as creating compounding problems and
inefficiencies that the steam leakage could have on plant operations. As a result, Valve designers took several steps to
address this problem.
Although many manufacturers still recommend hot torquing, the potential for leakage when this is not done is greatly
diminished. The seating surfaces in pressure seal Valves, as in many power plant Valves, are subjected to, comparatively
speaking, very high seating loads. Seat integrity is maintained as a function of tight machining tolerances on component
parts, means of providing the requisite torque to open/close as a function of gears or actuation, and selection/ application
of proper materials for seating surfaces.
Cobalt, nickel, and iron-based hardfacing alloys are utilized for optimal wear resistance of the wedge/disc and seat ring
seating surfaces. Most commonly used are the CoCr-A (e.g., Stellite) materials. These materials are applied with a variety of
processes, including shielded metal arc, gas metal arc, gas tungsten arc, and plasma (transferred) arc. Many pressure seal
Globe Valves are designed having integral hardfaced seats, while the
Gate Valves and
Check Valves typically have hardfaced seat rings that are welded into the Valve body.
Both butterfly valves and
ball valves offer unique benefits, so choosing between them in
certain processes isn't a hard choice. It can be problematic when a process requires valve characteristics that both
valves have. We need a deeper understanding of the butterfly valve vs ball valve in order to pick the correct valve.
Teflon is a polymer compound formed by the polymerization of tetrafluoroethylene with excellent chemical stability,
corrosion resistance, sealing, high lubrication and non-viscosity, electrical insulation and good aging resistance for media
such as strong acid, strong alkali, strong oxidant. Its operating temperature is -200 ~ 180℃, poor fluidity, large thermal
expansion. Teflon lined valves ensures extremely high
chemical resistance and longevity, can be widely used in corrosive applications in the chemical, electric machinery,
harmaceutical, petrochemical, fertilizer, pulp and paper, and metallurgical industries.
|
|
|
GOLF CART OR UTV? (WHICH IS RIGHT FOR YOU & HOW TO CHOOSE) |
Posted by: Y454AAA - 09-09-2021, 08:32 AM - Forum: Welcomes and Introductions
- No Replies
|
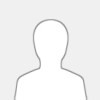 |
GOLF CART OR UTV? (WHICH IS RIGHT FOR YOU & HOW TO CHOOSE)
Golf carts and UTV are pleasant means of transportation. Comparing
electric and gas golf carts is common, but you rarely see comparing golf carts with UTV. This is mainly because these two
vehicles can be used for very different purposes. However, some intersections may make people wonder which is better, golf
cart or UTV. We have compiled a guide to help you identify differences and which one better meets your needs. Before you
decide which is the better choice, you need to consider a few things.
1. Speed
The speed will be affected by the power supply mode of your shopping cart or UTV and the modifications made to it. Some
normal golf carts do not run very fast. If UTV has many
functions, it will drag it down, and you may lose some speed. You can use gasoline or electric UTV and golf cart at the same
time, but gasoline will be faster. A gas-driven UTV golf cart is often a
little faster than a gas-driven golf cart.
However, some owners can make some adjustments to their golf cart to get faster speed. There are some golf carts and UTV
that can play very well. Some faster vehicles run at about 25 mph.
Of course, on rough terrain, you will find that you cannot get these numbers, but on flat roads, you will get them. It is
difficult to decide whether a golf cart or UTV is more suitable for you only based on speed. In terms of speed, both can
choose to provide you with very similar numbers.
2. Haulage
There is no doubt that UTV hauls better than off-road golf
cart. In most cases, golf carts are made for hauling golf clubs, some players and their equipment. In addition, golf
carts are not known for being able to move heavy objects.
However, some working golf carts can carry several boxes from one area of the maintenance facility to other areas.
Speaking of UTV, part of their design is to help you drag things. When we talk about traction, we mean how much UTV can
carry, and then traction is how much it can pull.
In terms of traction and traction, UTV has more capabilities than
vintage golf cart. Some utvs can carry or tow thousands of pounds. This is not the case with golf carts. If you use UTV
on the farm and move products around the farm, there is no doubt that UTV will be more suitable. The manufacturer's
recommendations must be checked when towing and towing restrictions are involved. You donnot want to try a project just to
find that your vehicle cannot do what you want to do.
3. Gas/electricity
In the past few years, only golf carts can use gasoline and electricity at the same time. It is a relatively new concept
to see that UTV can also be used in power. Although electricity is cleaner and better for the environment, it is usually not
so powerful. This is partly why UTV is used for natural gas. The new electric UTV began to become quite popular.
Compared with gasoline UTV, they are quiet, which helps
to make them more attractive to those who spend a lot of time on their vehicles. The noise of gasoline UTV cars can start to
wear you a little. This is what makes electric models more popular.
Whether you want gas or electricity will depend on how much you expect from your UTV or cart Trailer. Electric golf cart
is more suitable for people who play a round of golf. Their mobility, speed and functionality enable golfers on the golf
course. The natural gas-driven UTV was not built on the same idea. The way you choose to use your car will determine whether
gas or electric is more suitable for you. If you buy a UTV for power and stability, it is best to go with the gas version.
Human driven sightseeing buses have had a good 100-year run.
Throughout this period the urban consumer product has not changed – a city bus tour you took 100 years ago is pretty much
the same as a bus tour you can take today. All the digital innovations and changes we have brought to market over recent
years have been about retail and distribution, plus some ticket redemption adjustments. Nothing with the product experience
itself (adding Wifi doesn’t count!).
|
|
|
The Best iPhone Cases From Apple To Casetify, Mous To Pipetto |
Posted by: Y454AAA - 09-09-2021, 08:31 AM - Forum: Welcomes and Introductions
- No Replies
|
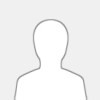 |
The Best iPhone Cases From Apple To Casetify, Mous To Pipetto
The new Apple iPhone 12 is a gorgeous smartphone. So, you’ll want to keep it that way, with a decent case—read on for a
round-up of the very best Apple iPhone 12 kevlar cases you can buy
right now.
When it comes to phone cases, what’s your favorite style? Folio? Sleeve? Back protector? Or something so slim and smooth
you think there’s nothing there at all. Do you like something bright and solid, or something light but strong and ultra-
protective? How hard are they to slide on and off if you fancy a change? Do they protect the display as well as the back? How
sumptuous do they feel in your hand and how much do they weigh your new iPhone down? Whatever kind of case you prefer,
you’ll find them all here. I’ve been testing iPhone 13 new case
s for looks, fit, effectiveness and design appeal.
Also, there is a new element to cases this year: MagSafe. The name may be familiar from the cool way power cables
connected to previous Mac laptops, but it’s now revived as a wireless charging pad. If you’ve ever used a wireless charging
pad you’ll know that if you put the phone down in the wrong place last thing at night, you’ll wake to find the phone didn’
t charge. MagSafe clamps the iPhone in place magnetically so that danger is gone. But MagSafe has other benefits, too: it
tells your iPhone what you’re connecting to it and it holds an iPhone 8~xsmax
case in place magnetically, so it’s much easier to slip the case on and off.
The iPhone 12 is amazingly good value, but it’s still not a cheap purchase. So, you’ll want to protect it. Even though
the arrival of Ceramic Shield means the front glass is intensely more durable and resistant to being dropped, you may feel it
’s not worth taking any chances. Here are the very best cases offering extra protection (and, therefore, extra peace of
mind).
A suitable Apple Smartwatch is very precious. Not only because of its impressive features, but also because of its
unparalleled style and luxurious price tag. More importantly, Apple Watch is a one-time investment for many people, which is
why ensuring its safety is the top priority. Much like the iPhone, Apple Watch also has countless protective cases, from
subtle to statement, you can have everything. Apple Watch case can
protect your investment and protect you from panic attacks every time something hits your precious smartwatch. Therefore, if
you want to be able to continue to wear your Apple Watch without worrying about damage, you can consider buying a sturdy
smartwatch case.
If you are entrenched in the Apple ecosystem and love listening to music with great over-ear headphones, the AirPods Max
is probably for you. However, they come with a case that resembles, shall we say, some undergarments. A good
Airpods pro&max case is needed if you want to protect your headphones
and don't like the case that was shipped with them. Let's explore the best AirPods Max cases on the market today.
Cigars are hand-rolled fermented tobacco. Compared with ordinary cigarettes, they have less nicotine content, less than
2%. Pure natural tobacco, which contains no chemical substances, has little harm to human body and is welcomed by business
people. In many Western movies, we can see such a plot, the protagonist takes out a cigar from a well-decorated cigar box and
ignites it to smoke. Cigar boxes were first made of high-quality wood. They can also be made of plastics, ox bones, carbon
fibers and other materials.
Cigars are like alcoholic drinks. They do not fade away with time, but become stronger and stronger. A common cigar can
be stored in a suitable environment for more than ten or twenty years, and its price can be doubled several times. The most
suitable conditions for preserving cigars are temperature 18 degrees and humidity 70 degrees. Cigar boxes can isolate cigars
from the outside world and keep them in their best condition. Top-grade wooden cigar boxes are made of cigar or mahogany,
walnut and rosewood, which are exquisite in shape and expensive in price. Carbon fiber cigar boxes were invented relatively late, and only recently began to rise. They are light in weight,
small in size, easy to carry with you, and will not have the problem of moist and moth-like wood. Its shape is streamlined
and can closely fit the cigar inside, saving space to the greatest extent.
If you want to buy a new or used CNC router, you want the machine to solve your manufacturing challenges. We provide
manufacturers of all sizes with cutting-edge technology from all woodworking technologies from world market leaders. We offer
superior wood CNC processing technology and equipment for the highly
efficient production of furniture, interior fittings, construction elements, and millwork, for panel processing, plastics and
solid wood processing.
|
|
|
What are Defoamers? |
Posted by: Y454AAA - 09-09-2021, 08:29 AM - Forum: Welcomes and Introductions
- No Replies
|
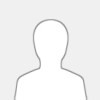 |
What are Defoamers?
Defoamers are chemical additives that reduce and/or prevent the formation
of foam in industrial process liquids such as paints, inks, adhesives and even construction products. The terms antifoam
agent and defoamer are often used interchangeably, however, antifoam agents more accurately refer to materials that inhibit
the generation and formation of bubbles. Dependent upon the application and performance requirements, they consist of
polydimethylsiloxanes and other silicones, insoluble oils, stearates and glycols, as well as inorganics, such as silicates
and talc.
What is Foam?
Foam is a coarse dispersion of a gas in a liquid, where the volume fraction of gas is greater than that of the liquid.
The bubbles will migrate to the surface, as their density is less than that of the liquid. As the bubbles coalesce and
collect at the air/surface interface, the bubble walls thin and break. Silicone defoamers accelerate the process and break the smaller bubbles as well. Generally, a defoamer is
insoluble in the foaming medium and has surface-active properties. An essential feature of a
polyether defoamer is the ability to spread rapidly on
foamy surfaces.
In industrial processes, foams pose serious problems. They cause defects on surface coatings. They prevent the efficient
filling of containers. Some of the sources of foam formation include:
Inclusion of air through agitation during production, filling, mixing of two-pack systems (often high-viscosity
(epoxies, adhesives);
Air inclusion on the pigment surface, resulting in poor wetting of pigments;
Application: roller, spraying, brushing;
Filtration through a sieve or anything with air on the surface;
Generation/liberation of gases during chemical curing processes; e.g. polyisocyanates;
Introduction of air through substrate wetting (wood coatings, other highly porous substrates).
In the papermaking process, fibers, fillers and some additives are not water-insoluble, so they are easy to accumulate in
an aqueous solution. Moreover between the different materials as far as possible from the incompatibility away, so it is
difficult to get uniform performance and ideal strengthen paper. In order to solve the long fiber in the process of this
problem, the use of polyacrylamide has the following advantages:
to improve the retention rate of fillers, pigments and so on. To reduce the loss of raw materials and
environmental pollution.
to improve the strength of the paper (including dry and wet strength).
to improve the tear resistance and porosity to improve visual and printing performance.
The advantages of using polyacrylamide as a paper dispersant are also manifested in the fact that the product is soluble
in water and forms a high viscosity liquid which promotes good dispersion of papermaking fibers and excellent paper forming
effect at low added levels to improve pulp consistency And the softness of the paper, but also to improve the strength of the
paper performance.
Adipic acid is one of the most commercially important aliphatic
dicarboxylic acids. It is produced on a large scale primarily to supply the nylon 6,6 production chain. Other applications
include the manufacture of coatings, synthetic lubricants, fibers, plastics, plasticizers and polyurethane resins. Adipic
acid production has been predominantly based on cyclohexane and, to a lesser extent, phenol. Shifts in the hydrocarbon market
and growing environmental concerns have resulted in the development of alternative production routes for adipic acid from
renewable resources, such as sugar and fatty acids.
Epoxy propanol (EP), also known as glycidol, is an organic compound used in the manufacture of a range of products, such
as detergents, industrial paints and coatings, and healthcare products. It is primarily manufactured in Japan and, to a much
lesser degree, in the United States. Traditionally, EP is produced by one of two methods: epoxidation of allyl alcohol with
hydrogen peroxide, or the reaction of epichlorohydrin with a caustic
agent. However, allyl alcohol is extremely toxic and epichlorohydrin is made from hydrocarbon feedstocks, such as propylene.
Both methods generate toxic by-products, such as hydrochloric acid, requiring costly purification processes to prevent the
acid residues from entering the environment.
|
|
|
UNDERSTANDING ULTRAVIOLET LED APPLICATIONS AND PRECAUTIONS |
Posted by: Y454AAA - 09-09-2021, 08:26 AM - Forum: Welcomes and Introductions
- No Replies
|
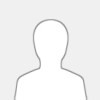 |
UNDERSTANDING ULTRAVIOLET LED APPLICATIONS AND PRECAUTIONS
Ultraviolet light occurs between the visible and x-ray spectrums. The Ultraviolet wavelength range is specified as 10 nm
to 400 nm; however, many optoelectronic companies also consider wavelengths as high as 430nm to be in the UV range.
Ultraviolet light gets its name due to the violet color it produces in the visible portion of the spectrum although much of
the output of UV light is not visible to the human eye.
UV LEDs have seen tremendous growth over the past several years. This is
not only the result of technological advances in the manufacturing of solid state UV devices, but the ever increasing demand
for environmentally friendly methods of producing UV light which is currently dominated by mercury lamps. The current
offering of UV LED modules in the optoelectronics market consists
of product ranging from approximately 265nm – 420nm with a variety of package styles including through-hole, surface mount
and COB (Chip-On-Board). There are many unique applications for UV LED emitters; however, each is greatly dependent on
wavelength and output power. In general, UV light for LEDs can be broken down into 3 general areas.
The upper UVA type devices have been available since the late 1990s. These LEDs have been traditionally used in
applications such as counterfeit detection or validation (Currency, Driver’s license, Documents etc) and Forensics (Crime
scene investigations) to name a few. The power output requirements for these applications are very low and the actual
wavelengths used are in the 390nm – 420nm range. Lower wavelengths were not available at that time for production use. As a
result of their longevity in the market and the ease of manufacturing, these type LEDs are readily available from a variety
of sources and the least expensive of all UV product. The middle UVA LED
component area has seen the greatest growth over the past several years. The majority of applications in this
wavelength range (approximately 350nm – 390nm) are for UV curing of both commercial and industrial materials such as
adhesives, coatings and inks. LEDs offer significant advantages over traditional curing technologies such as mercury or
fluorescent due to increased efficiency, lower cost of ownership and system miniaturization. The trend to utilizing LEDs for
curing is increasing as the supply chain is continually pushing to adopt LED technology. Although the costs of this
wavelength range is significantly greater than the upper UVA
LED module area, rapid advances in manufacturing as well as increasing volumes are steadily driving down prices.
The lower UVA and upper UVB ranges (approximately 300nm – 350nm) are the most recent introduction to the market place.
These devices offer the potential to be used in a variety of applications including UV curing, biomedical, DNA analysis and
various types of sensing. There is significant overlap in all 3 of the UV spectral ranges; therefore, one must consider not
only what is best for the application, but also what is the most cost-effective solution, since the lower in wavelength,
typically the higher the LED cost. The lower UVB LED and upper UVC
ranges (approximately 250nm – 300nm) is an area that is still very much in its infancy, however, there is great enthusiasm
and demand for this product in air and water purification systems. There are currently only a handful of companies that are
capable of manufacturing UV LEDs in this wavelength range and even a smaller amount that are producing product with
sufficient lifetime, reliability and performance characteristics.
As a result, the costs of devices in the UVC/B range are still very high and can be cost prohibitive in some
applications. The introduction of the first commercial UVC LED based
disinfection system in 2012 has helped to move the market forward to where many companies are now seriously pursing LED based
products. Precautions A common question regarding ultraviolet LEDs is: Do they pose any safety risks? As described
above, there are different levels of UV light. One of the most commonly used and familiar sources for producing UV output is
the black light bulb. This product has been used for decades to produce a glowing or fluorescence affect on specific types of
posters as well as for other applications such as the authentication of paintings and currency.
|
|
|
|