Welcome, Guest |
You have to register before you can post on our site.
|
Online Users |
There are currently 289 online users. » 0 Member(s) | 287 Guest(s) Bing, Google
|
Latest Threads |
Advanced microneedling
Forum: Off Topic
Last Post: axied12
05-28-2025, 01:25 PM
» Replies: 0
» Views: 155
|
Caviar and cheese
Forum: Off Topic
Last Post: axied12
05-28-2025, 12:38 PM
» Replies: 0
» Views: 142
|
Top-rated countertop comp...
Forum: Off Topic
Last Post: axied12
05-04-2025, 06:42 AM
» Replies: 0
» Views: 295
|
Ryanair letenky levně do ...
Forum: Off Topic
Last Post: axied12
02-11-2025, 01:37 PM
» Replies: 0
» Views: 689
|
Trusted essay writing ser...
Forum: Off Topic
Last Post: axied12
01-30-2025, 08:16 AM
» Replies: 0
» Views: 620
|
Bootverkopers - actieve j...
Forum: Off Topic
Last Post: axied12
12-07-2024, 11:07 AM
» Replies: 0
» Views: 748
|
Services for individuals ...
Forum: Off Topic
Last Post: axied12
12-02-2024, 03:31 PM
» Replies: 0
» Views: 707
|
Used excavators
Forum: Off Topic
Last Post: axied12
11-13-2024, 09:22 AM
» Replies: 0
» Views: 689
|
Buy Higo Rocket in Dubai
Forum: Off Topic
Last Post: axied12
10-25-2024, 01:09 PM
» Replies: 0
» Views: 793
|
Anime coloring pages
Forum: Off Topic
Last Post: axied12
10-13-2024, 05:10 PM
» Replies: 0
» Views: 834
|
|
|
GOLF CART OR UTV? (WHICH IS RIGHT FOR YOU & HOW TO CHOOSE) |
Posted by: jjwko565s - 09-13-2021, 03:42 AM - Forum: Welcomes and Introductions
- No Replies
|
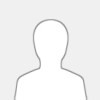 |
Golf carts and UTV are pleasant means of transportation. Comparing electric and gas golf carts is common, but you rarely see comparing golf carts with UTV. This is mainly because these two vehicles can be used for very different purposes. However, some intersections may make people wonder which is better, golf cart or UTV. We have compiled a guide to help you identify differences and which one better meets your needs. Before you decide which is the better choice, you need to consider a few things.
1. Speed
The speed will be affected by the power supply mode of your shopping cart or UTV and the modifications made to it. Some normal golf carts do not run very fast. If UTV has many functions, it will drag it down, and you may lose some speed. You can use gasoline or electric UTV and golf cart at the same time, but gasoline will be faster. A gas-driven UTV golf cart is often a little faster than a gas-driven golf cart.
However, some owners can make some adjustments to their golf cart to get faster speed. There are some golf carts and UTV that can play very well. Some faster vehicles run at about 25 mph.
Of course, on rough terrain, you will find that you cannot get these numbers, but on flat roads, you will get them. It is difficult to decide whether a golf cart or UTV is more suitable for you only based on speed. In terms of speed, both can choose to provide you with very similar numbers.
2. Haulage
There is no doubt that UTV hauls better than off-road golf cart. In most cases, golf carts are made for hauling golf clubs, some players and their equipment. In addition, golf carts are not known for being able to move heavy objects.
However, some working golf carts can carry several boxes from one area of the maintenance facility to other areas. Speaking of UTV, part of their design is to help you drag things. When we talk about traction, we mean how much UTV can carry, and then traction is how much it can pull.
In terms of traction and traction, UTV has more capabilities than vintage golf cart. Some utvs can carry or tow thousands of pounds. This is not the case with golf carts. If you use UTV on the farm and move products around the farm, there is no doubt that UTV will be more suitable. The manufacturer's recommendations must be checked when towing and towing restrictions are involved. You donnot want to try a project just to find that your vehicle cannot do what you want to do.
3. Gas/electricity
In the past few years, only golf carts can use gasoline and electricity at the same time. It is a relatively new concept to see that UTV can also be used in power. Although electricity is cleaner and better for the environment, it is usually not so powerful. This is partly why UTV is used for natural gas. The new electric UTV began to become quite popular.
Compared with gasoline UTV, they are quiet, which helps to make them more attractive to those who spend a lot of time on their vehicles. The noise of gasoline UTV cars can start to wear you a little. This is what makes electric models more popular.
Whether you want gas or electricity will depend on how much you expect from your UTV or cart Trailer. Electric golf cart is more suitable for people who play a round of golf. Their mobility, speed and functionality enable golfers on the golf course. The natural gas-driven UTV was not built on the same idea. The way you choose to use your car will determine whether gas or electric is more suitable for you. If you buy a UTV for power and stability, it is best to go with the gas version.
Human driven sightseeing buses have had a good 100-year run. Throughout this period the urban consumer product has not changed – a city bus tour you took 100 years ago is pretty much the same as a bus tour you can take today. All the digital innovations and changes we have brought to market over recent years have been about retail and distribution, plus some ticket redemption adjustments. Nothing with the product experience itself (adding Wifi doesn’t count!).
|
|
|
What are Defoamers? |
Posted by: jjwko565s - 09-13-2021, 03:41 AM - Forum: Welcomes and Introductions
- No Replies
|
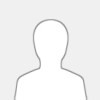 |
Defoamers are chemical additives that reduce and/or prevent the formation of foam in industrial process liquids such as paints, inks, adhesives and even construction products. The terms antifoam agent and defoamer are often used interchangeably, however, antifoam agents more accurately refer to materials that inhibit the generation and formation of bubbles. Dependent upon the application and performance requirements, they consist of polydimethylsiloxanes and other silicones, insoluble oils, stearates and glycols, as well as inorganics, such as silicates and talc.
What is Foam?
Foam is a coarse dispersion of a gas in a liquid, where the volume fraction of gas is greater than that of the liquid. The bubbles will migrate to the surface, as their density is less than that of the liquid. As the bubbles coalesce and collect at the air/surface interface, the bubble walls thin and break. Silicone defoamers accelerate the process and break the smaller bubbles as well. Generally, a defoamer is insoluble in the foaming medium and has surface-active properties. An essential feature of a polyether defoamer is the ability to spread rapidly on foamy surfaces.
In industrial processes, foams pose serious problems. They cause defects on surface coatings. They prevent the efficient filling of containers. Some of the sources of foam formation include: - Inclusion of air through agitation during production, filling, mixing of two-pack systems (often high-viscosity (epoxies, adhesives);
- Air inclusion on the pigment surface, resulting in poor wetting of pigments;
- Application: roller, spraying, brushing;
- Filtration through a sieve or anything with air on the surface;
- Generation/liberation of gases during chemical curing processes; e.g. polyisocyanates;
- Introduction of air through substrate wetting (wood coatings, other highly porous substrates).
In the papermaking process, fibers, fillers and some additives are not water-insoluble, so they are easy to accumulate in an aqueous solution. Moreover between the different materials as far as possible from the incompatibility away, so it is difficult to get uniform performance and ideal strengthen paper. In order to solve the long fiber in the process of this problem, the use of polyacrylamide has the following advantages:
- to improve the retention rate of fillers, pigments and so on. To reduce the loss of raw materials and environmental pollution.
- to improve the strength of the paper (including dry and wet strength).
- to improve the tear resistance and porosity to improve visual and printing performance.
The advantages of using polyacrylamide as a paper dispersant are also manifested in the fact that the product is soluble in water and forms a high viscosity liquid which promotes good dispersion of papermaking fibers and excellent paper forming effect at low added levels to improve pulp consistency And the softness of the paper, but also to improve the strength of the paper performance.
Adipic acid is one of the most commercially important aliphatic dicarboxylic acids. It is produced on a large scale primarily to supply the nylon 6,6 production chain. Other applications include the manufacture of coatings, synthetic lubricants, fibers, plastics, plasticizers and polyurethane resins. Adipic acid production has been predominantly based on cyclohexane and, to a lesser extent, phenol. Shifts in the hydrocarbon market and growing environmental concerns have resulted in the development of alternative production routes for adipic acid from renewable resources, such as sugar and fatty acids.
Epoxy propanol (EP), also known as glycidol, is an organic compound used in the manufacture of a range of products, such as detergents, industrial paints and coatings, and healthcare products. It is primarily manufactured in Japan and, to a much lesser degree, in the United States. Traditionally, EP is produced by one of two methods: epoxidation of allyl alcohol with hydrogen peroxide, or the reaction of epichlorohydrin with a caustic agent. However, allyl alcohol is extremely toxic and epichlorohydrin is made from hydrocarbon feedstocks, such as propylene. Both methods generate toxic by-products, such as hydrochloric acid, requiring costly purification processes to prevent the acid residues from entering the environment.
|
|
|
COPPER CABLE LUGS FOR SPECIAL APPLICATIONS |
Posted by: jjwko565s - 09-13-2021, 03:38 AM - Forum: Welcomes and Introductions
- No Replies
|
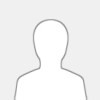 |
A well known problem for every electrician or cable jointer is trying to insert a stranded or fine stranded conductor into the cable lug connector or cable splice and some wires cannot be inserted. To avoid this problem renowned manufacturers offer specialist application connectors and cable lugs for the jointing and termination of LV MV HV cables.
CABLE LUGS, STRANDINGS CONDUCTORS
With these specialist application cable lugs all types of cables can be used – the design and construction of the copper tubular lugs to be selected is determined by the cable stranding and conductor type. The cable conductor characteristics of cable types are as classified in the DIN Standard 57295.
CABLE LUGS FOR FINE VERY FINE STRANDED CONDUCTORS
The above mentioned problem of spliced cables per Class 5 and Class 6 according to DIN 57295 is being avoided when using Klauke “F” type series cable lugs. These lugs are designed for processing larger cross section conductors in voltage applications up to the short circuit tested rating of the cable lug.
Compared with standard tubular cable lugs the F type lugs have a larger tube diameter – the cable lugs have a flared entry which eases cable location into the barrel of the lug. F-type cable lugs and butt connectors conform to the normative requirements of the EN 13600 standard and are manufactured from electrolytic copper for excellent conductivity.
For processing and crimping solid conductors (Class 1 DIN VDE 57295) the use of tubular cable lugs E-type is recommended which are also manufactured from electrolytic tin plated copper. Their tube diameter is matched to the conductor size to guarantee a professional cable crimp.
Especially for adverse environments and for crimping copper conductors stainless steel and nickel tubular cable lugs have been designed. Aluminum lugs are particularly acid and corrosion resistant and are typically used in chemical industries in areas exposed to sea water i.e. the earthing of masts on sailing yachts.
An additional benefit of these cable lugs is the temperature resistance. Consequently these lugs can be used in ambient temperatures up to 400°C.
At higher temperatures of up to 650°C – common in the construction of furnaces – nickel cable lugs represent the best solution. Both stainless steel and nickel cable lugs can be used for all common cable types.
We offer electrical solutions to our customers. Solutions come from finding what works best for you. By carrying a range of insulation types, we offer you the chance to build a custom solution. Sure, we could only carry nylon insulated terminals and nothing else, but maybe you need vinyl. Maybe you need heat shrink. The point is that by offering you choice, we’re not locking you into a single set of products. We’re giving you the freedom to make an educated decision based on your particular needs. If you have any questions about terminals, insulation types, or any other of our products, contact us today.
High-strength composite cable joint clamps are just as strong as metal clamps, offer significant weight and installation time savings, and exceed expectations when sourced from a trusted supplier. To identify the best composite cable clamps for harsh-environment and military applications, evaluate the options in terms of these five key characteristics: performance, weight, ease of use, durability, and reliability.
|
|
|
UNDERSTANDING ULTRAVIOLET LED APPLICATIONS AND PRECAUTIONS |
Posted by: jjwko565s - 09-13-2021, 03:35 AM - Forum: Welcomes and Introductions
- No Replies
|
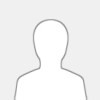 |
Ultraviolet light occurs between the visible and x-ray spectrums. The Ultraviolet wavelength range is specified as 10 nm to 400 nm; however, many optoelectronic companies also consider wavelengths as high as 430nm to be in the UV range. Ultraviolet light gets its name due to the violet color it produces in the visible portion of the spectrum although much of the output of UV light is not visible to the human eye.
UV LEDs have seen tremendous growth over the past several years. This is not only the result of technological advances in the manufacturing of solid state UV devices, but the ever increasing demand for environmentally friendly methods of producing UV light which is currently dominated by mercury lamps. The current offering of UV LED modules in the optoelectronics market consists of product ranging from approximately 265nm – 420nm with a variety of package styles including through-hole, surface mount and COB (Chip-On-Board). There are many unique applications for UV LED emitters; however, each is greatly dependent on wavelength and output power. In general, UV light for LEDs can be broken down into 3 general areas.
The upper UVA type devices have been available since the late 1990s. These LEDs have been traditionally used in applications such as counterfeit detection or validation (Currency, Driver’s license, Documents etc) and Forensics (Crime scene investigations) to name a few. The power output requirements for these applications are very low and the actual wavelengths used are in the 390nm – 420nm range. Lower wavelengths were not available at that time for production use. As a result of their longevity in the market and the ease of manufacturing, these type LEDs are readily available from a variety of sources and the least expensive of all UV product. The middle UVA LED component area has seen the greatest growth over the past several years. The majority of applications in this wavelength range (approximately 350nm – 390nm) are for UV curing of both commercial and industrial materials such as adhesives, coatings and inks. LEDs offer significant advantages over traditional curing technologies such as mercury or fluorescent due to increased efficiency, lower cost of ownership and system miniaturization. The trend to utilizing LEDs for curing is increasing as the supply chain is continually pushing to adopt LED technology. Although the costs of this wavelength range is significantly greater than the upper UVA LED module area, rapid advances in manufacturing as well as increasing volumes are steadily driving down prices.
The lower UVA and upper UVB ranges (approximately 300nm – 350nm) are the most recent introduction to the market place. These devices offer the potential to be used in a variety of applications including UV curing, biomedical, DNA analysis and various types of sensing. There is significant overlap in all 3 of the UV spectral ranges; therefore, one must consider not only what is best for the application, but also what is the most cost-effective solution, since the lower in wavelength, typically the higher the LED cost. The lower UVB LED and upper UVC ranges (approximately 250nm – 300nm) is an area that is still very much in its infancy, however, there is great enthusiasm and demand for this product in air and water purification systems. There are currently only a handful of companies that are capable of manufacturing UV LEDs in this wavelength range and even a smaller amount that are producing product with sufficient lifetime, reliability and performance characteristics.
As a result, the costs of devices in the UVC/B range are still very high and can be cost prohibitive in some applications. The introduction of the first commercial UVC LED based disinfection system in 2012 has helped to move the market forward to where many companies are now seriously pursing LED based products. Precautions A common question regarding ultraviolet LEDs is: Do they pose any safety risks? As described above, there are different levels of UV light. One of the most commonly used and familiar sources for producing UV output is the black light bulb. This product has been used for decades to produce a glowing or fluorescence affect on specific types of posters as well as for other applications such as the authentication of paintings and currency.
|
|
|
Are Electric Scooters the Future? How Do They Actually Work? |
Posted by: jjwko565s - 09-13-2021, 03:34 AM - Forum: Welcomes and Introductions
- No Replies
|
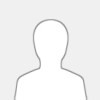 |
If you’re a particular age, then you might have memories of riding a scooter. Those flimsy, two-wheeled scooters that gave you freedom on the sidewalk in front of your house before your acquisition of a bike opened up the whole neighborhood.
Until recently, that image of a scooter as a nothing more than a child’s toy was the one most people carried. Now, several companies, such as Bird, LimeBike, and Spin, are out to change that perception. They are banking big on the idea that the small, compact electric riding scooters is a viable personal transportation device. But is it? Let’s take a look at where e-scooters are at today, from their fundamental appeal to how they work to their practicality beyond ordinary weekend fun.
The Rise of the Electric Scooter
Although manual and electric kick- or push-start scooters have both been around for some time, the popularity of the latter has risen steadily over the past two decades.
Perhaps the central development in the design and marketing of today’s dual motor electric scooter is children are no longer the primary audience.
Make no mistake, the targets are still young. They just happen to have a different set of priorities.
College students on campus.
Young professionals who live and work in urban environments.
People looking for alternative means of transportation in those same cities.
Each of these groups offer a market segment that tends to eschew the norms and traditions of the past. Zipping around town on a low-speed, zero-emission scooter certainly caters to those demanding alternatives.
With a unifying factor that everyone over a certain age will probably look a little goofy riding one, it’s easy to see the appeal. It also doesn’t hurt that foldable electric scooters come across as simple and easily accessible devices that are even easier to operate.
How Do Electric Scooters Work?
E-scooters, much like their non-powered siblings are about as straightforward as it gets when it comes to personal transportation devices.
In their simplest form scooters are composed of a narrow platform or deck, t-stem handlebars with a throttle and hand brakes, two wheels (although some models come with three or four), and front and rear suspension. Most scooters are fold-able, and some models also include a seat.
When it comes to variation, harley electric scooters are what they are. Alter the design too much, and they become an entirely different form of transportation. However, they do possess a few key areas where a slight difference makes a significant impact on performance.
As with most personal e-vehicles, such as hoverboards, self-balancing unicycles, and Segways, the individual riding the device most often determines just how safe it is. However, staying upright on a scooter is less fraught with danger versus those other options.
The primary safety issue with scooters is when you place them among large groups of pedestrians and cars, which is happening now in a number of major cities across the U.S.
This intermingling of people on foot and those scooting by at a top speed of 15 mph has created an uptick in accidents between the two, though reliable data does not yet exist on the exact numbers.
Beyond possible run-ins with non-riders, another primary safety concern revolves around the attire of the actual riders. Though every off road electric scooter manufacturer and ride-sharing company recommend the use of a helmet, and many cities dictate the wearing of headgear, very few e-scooter riders do so.
|
|
|
Plating |
Posted by: jjwko565s - 09-13-2021, 03:30 AM - Forum: Welcomes and Introductions
- No Replies
|
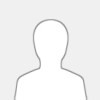 |
There s no such thing as alchemy—magically changing common chemical elements into rare and valuable ones—but water plating is possibly the next best thing. The idea is to use electricity to coat a relatively mundane metal, such as copper, with a thin layer of another, more precious metal, such as gold or silver. Water plating has lots of other uses, besides making cheap metals look expensive. We can use it to make things rust-resistant, for example, to produce a variety of useful alloys like brass and bronze, and even to make plastic look like metal. How does this amazing process work? Let s take a closer look!
Plastic water plating involves passing an electric current through a solution called an electrolyte. This is done by dipping two terminals called electrodes into the electrolyte and connecting them into a circuit with a battery or other power supply. The electrodes and electrolyte are made from carefully chosen elements or compounds. When the electricity flows through the circuit they make, the electrolyte splits up and some of the metal atoms it contains are deposited in a thin layer on top of one of the electrodes—it becomes electroplated. All kinds of metals can be plated in this way, including gold, silver, tin, zinc, copper, cadmium, chromium, nickel, platinum, and lead.
Water plating is very similar to electrolysis (using electricity to split up a chemical solution), which is the reverse of the process by which batteries produce electric currents. All these things are examples of electrochemistry: chemical reactions caused by or producing electricity that give scientifically or industrially useful plastic water plating products.
How does water plating work?
First, you have to choose the right electrodes and electrolyte by figuring out the chemical reaction or reactions you want to happen when the electric current is switched on. The metal atoms that plate your object come from out of the electrolyte, so if you want to copper plate something you need an electrolyte made from a solution of a copper salt, while for gold plating you need a gold-based electrolyte—and so on.
Next, you have to ensure the electronic products shell plastic water plating you want to plate is completely clean. Otherwise, when metal atoms from the electrolyte are deposited onto it, they won t form a good bond and they may simply rub off again. Generally, cleaning is done by dipping the electrode into a strong acid or alkaline solution or by (briefly) connecting the Water plating circuit in reverse. If the electrode is really clean, atoms from the two-color material plating bond to it effectively by joining very strongly onto the outside edges of its crystalline structure.
Now we re ready for the main part of two-color material twice molding water plating. We need two electrodes made from different conducting materials, an electrolyte, and an electricity supply. Generally, one of the electrodes is made from the metal we re trying to plate and the electrolyte is a solution of a salt of the same metal. So, for example, if we re copper plating some brass, we need a copper electrode, a brass electrode, and a solution of a copper-based compound such as copper sulfate solution. Metals such as gold and silver don t easily dissolve so have to be made into solutions using strong and dangerously unpleasant cyanide-based chemicals. The electrode that will be plated is generally made from a cheaper metal or a nonmetal coated with a conducting material such as graphite. Either way, it has to conduct electricity or no electric current will flow and no plating will occur.
How are plastics electroplated?
If you know anything about plastic, you ll spot the obvious problem straightaway: plastic product molding generally don t conduct electricity. In theory, that should completely rule out electroplating; in practice, it simply means we have to give our plastic an extra treatment to make it electrically conducting before we start. There are several different steps involved. First, the plastic surface treatment has to be scrupulously cleaned to remove things like dust, dirt, grease, and surface marks. Next, it s etched with acid and treated with a catalyst (a chemical reaction accelerator) to make sure that a coating will stick to its surface. Then it s dipped in a bath of copper or nickel (copper is more common) to give it a very thin coating of electrically conducting metal (less than a micron, 1μm, or one thousandth of a millimeter thick). Once that s done, it can be electroplated just like a metal. Depending on how much wear and tear the plated part has to withstand, the coating can be anything from about 10–30 microns thick.
|
|
|
New RO modules from Hydranautics |
Posted by: jjwko565s - 09-13-2021, 03:25 AM - Forum: Welcomes and Introductions
- No Replies
|
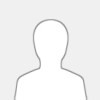 |
We are one of the global leaders in the field of integrated membrane solutions, providing complete membrane solutions for water, wastewater and process treatment and applications, such as reverse osmosis, nanofiltration, ultrafiltration and microfiltration. Our membrane-based solutions are currently used in various applications on seven continents around the world, such as seawater desalination, industrial high-purity water, surface water treatment, wastewater treatment, special process applications, etc.
Residential membranes are manufactured using advanced RO membrane technology. These membranes are available in five variants, 50, 75, 100, 150 and 500 gallons per day (GPD). These membranes can repel salt and other minerals while reducing the flow problems normally associated with membranes.
Hydranautics is a worldwide supplier of separation membrane technology with a comprehensive list of top-performing filtration products for various industries. Applications of Hydranautics RO membrane include boiler feedwater treatment, wastewater treatment, seawater desalination, surface water treatment, drinking water purification, agricultural water treatment, and pharmaceutical water purification.
Hydranautic membrane products are designed with the goal of delivering unmatched quality in terms of product and technical mastery. They are depended upon by several large manufacturing sites throughout the world in countries such as USA, China, Canada, Japan, Mexico, etc.
Proponents of water filters say the water is cleaner and healthier, with impurities removed and minerals added. Replace water filter and alkaline water companies also advertise a laundry list of claims, from improved gastrointestinal health to detoxification and even cancer prevention.
Water filter housings are casings around your filter cartridge that directs the flow of water. In this article, we will take a look at some of the most frequently asked questions about our water filter housings.
They come in a wide range of types. Mainly water filter housings are of two types. However, there can be subcategories based on size, material, and purpose.
RO membrane housings will filter your water right where you use it. For example, an individual tap or faucet. So the systems cover filters under the sink, filters attached to your faucets, or filtration pitchers. The housings for POU water systems serve this purpose
Water filter clear housings, especially whole housing systems, offer a versatile large capacity filtration. Since they are geared towards high flow, they can remove heavy sediments easily. By installing large water filter housings, you can reduce the number of vessels needed for high-flow applications. It can also withstand variations in water pressure. The large cartridge capacity will be very helpful for you.
Reverse Osmosis works by using a high pressure RO pump to increase the pressure on the salt side of the RO and force the water across the semi-permeable RO membrane, leaving almost all (around 95% to 99%) of dissolved salts behind in the reject stream. The amount of pressure required depends on the salt concentration of the feed water. The more concentrated the feed water, the more pressure is required to overcome the osmotic pressure.
|
|
|
Compact Wheel Loader Design Competes with Skid-steer Dominance |
Posted by: jjwko565s - 09-13-2021, 03:24 AM - Forum: Welcomes and Introductions
- No Replies
|
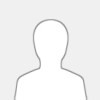 |
Compact wheel loaders generally lag behind skid steer loaders, even though compact wheel loaders are more productive in certain applications. Compact wheel loaders can be a good complement or substitute for skid steer loaders. Benefits include excellent visibility, improved tire wear and fuel economy, driving speed and overall operator comfort. There are also some disadvantages that need to be considered, such as the height of the cab, operating weight and transport capacity. The versatility of the wheel loader is very important.
The definition of a compact wheel loader varies from manufacturer to manufacturer, but machines with less than 125 horsepower usually fall into this category. The real difference between these loaders and their main competitors skid steer and compact track loaders is the higher rated working load capacity, significantly higher travel speeds, superior lift and reach distances, longer wheelbases and more High fuel efficiency.
Due to the characteristics of steering machinery, compact articulated medium wheel loaders work well on hard surfaces because of low tire wear. Compared with similar slip diverters, they also burn less fuel. Between tires and fuel, your end result is reduced daily operating costs.
Visibility on the job site is a safety advantage. From the operator station of the large wheel loader, your field of view is much less than any skid steering system claims. Speed is also an important advantage when working on a site with a large number of ground shots. When comparing compact wheel loaders, there are many configurations and options that can really distinguish performance. Investigate all options before making a choice.
The modern backhoe-loader traces its lineage to a hydraulic digging attachment developed in the late 1940s. Lee Horton and Dave Willens, co-authors of Wain-Roy and the Invention of the Backhoe conducted extensive research into the history of this machine and the associated patents. Look for future designs to provide more car-style functions. With the popularity of backhoe loaders among owners/operators and the platform most similar to the trucks these people travel to and from the site every day, you will continue to see the impact of cars on the cabs and controls of these machines. This includes everything from seat and fabric options to the inclusion of Bluetooth radios and related functions, as well as a constant focus on visibility and site awareness.
Excavators can be divided into many types, such as crawler excavator, wheeled excavator and towed and rail excavator, etc. But they all consist of a boom, dipper, bucket and cab. The crawler excavator is a tracked vehicle that moves upon crawler tracks. In contrast, the wheel excavator is moved upon wheels. They both can be used in many working conditions, such as the digging of the trenches, holes; material handling, forestry work, demolition.
Powered industrial trucks, more commonly known as forklifts trucks, are the worker bees in many manufacturing and warehousing operations. Although primarily used to move materials, they also can be used to raise, lower or remove large objects or a number of smaller objects on pallets or in boxes, crates or other containers. In other words, they do the heavy lifting for us.
Powered industrial trucks can either be ridden by the operator or controlled by a walking operator, and there are many types of powered industrial trucks. Each type presents different operating hazards. For example, a sit-down, counterbalanced high-lift rider truck is more likely than a motorized hand truck to be involved in a falling load accident because the sit-down rider truck can lift a load much higher than a hand truck.
|
|
|
TYPES OF ELASTIC AND WHEN TO USE THEM |
Posted by: jjwko565s - 09-13-2021, 03:00 AM - Forum: Welcomes and Introductions
- No Replies
|
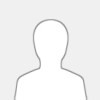 |
Hey y’all, in keeping with this month’s theme of what’s underneath? today we’re going to talk about types of elastic. Being confronted with a wall of elastic or hundreds of online choices can be intimidating for a beginner, so today’s post is meant to demystify those choices.
Types of Elastic
There are three basic types of elastic: braided, woven and knitted. These refer to how the yarns are put together, and the different methods of construction give the resulting elastics different properties.
Braided Elastic
Elastic braided tape has lengthwise, parallel ridges. Those ridges make this elastic have more grip but they also mean that braided elastic tends to narrow as it is stretched. Braided elastic also rolls more easily than woven or knitted elastics, and tends to lose stretch if it is sewn through. For this reason braided elastic rope is typically recommended for use in casings, not for sewing directly to fabric. But in some casings (like waists) braided elastic isn’t the best choice because of its tendency toward rolling. It’s better in sleeves, necklines, or other areas where rolling isn’t a big issue.
Knitted Elastic
Knitted elastic tape is made by knitting the fibers together. Knitted elastic tends to be softer than braided or woven elastic, and it retains its width when stretched. It also works well even when pierced by needles, so it’s a good choice for sew on applications. It rolls more than woven elastic, but less than braided elastic. Since this elastic is softer, it’s suitable for light to midweight fabrics, but doesn’t have the grip needed for heavier fabrics. With knit elastic, I may cut the elastic slightly shorter than the finished measurement in order to have it grip properly, particularly when I use it for waistbands or bra bands.
Woven Elastic
Also referred to as non-roll elastic, woven elastic tape is usually the firmest of the three basic elastic types. It retains width as it is stretched, and is suitable for sew on applications as well as use in casings. Because it tends to be very firm, it is also suitable for heavier weight fabrics. I generally don’t cut woven elastic with much negative ease, because it will pull too much. In other words, if I’m using it in a waistband, I’ll cut the elastic to the body measurement where the waist hits, not any less.
The zipper is such a great invention no dressmaker can ever imagine what life in the sewing room would be like without the zipper. Then of course the famous zipper needs a useful foot to ensure it sews up perfectly. That’s where the zipper foot makes its entrance. If you are going to sew a zipper into your garment don’t attempt this process without a zipper foot. The zipper foot enables the sewing needle to stitch close to the raised edge of the zipper. The gadget itself can be attached to the machine’s presser foot shaft. The zipper foot has the added advantage of being able to attach to the right or the left side of the presser foot holder. Use your zipper foot to insert piping as well as cording.
There are two types of sewing pins. The most commonly used is the straight pin, also know as the hemming pin or basting pin. The key facets of straight pins that differ and can help you choose the type you need are length, thickness, and type of head and tip. The metal or finish of the straight pin is typically brass, steel, nickel, or a combination thereof. The metal used with sewing pins determines whether the pins will stick to a magnet - a plus for making sure there are none on the floor. Nickel plating is useful for steel pins as it helps the pin stick to a magnet and prevents it from rusting.
A crochet hook is the basic tool you'll need to get started on your journey as you learn to crochet. Made from metal, plastic or wood with a small hook at one end, crochet hooks are used to turn a lovely skein of yarn into cosy jumpers, snuggly blankets and beautiful home accessories. All crochet hooks have similar basic features, in the same way knitting needles do, but different brands may modify them slightly for extra comfort or a more eye-catching design.
|
|
|
|