Welcome, Guest |
You have to register before you can post on our site.
|
Online Users |
There are currently 284 online users. » 0 Member(s) | 282 Guest(s) Bing, Google
|
Latest Threads |
Advanced microneedling
Forum: Off Topic
Last Post: axied12
05-28-2025, 01:25 PM
» Replies: 0
» Views: 154
|
Caviar and cheese
Forum: Off Topic
Last Post: axied12
05-28-2025, 12:38 PM
» Replies: 0
» Views: 141
|
Top-rated countertop comp...
Forum: Off Topic
Last Post: axied12
05-04-2025, 06:42 AM
» Replies: 0
» Views: 294
|
Ryanair letenky levně do ...
Forum: Off Topic
Last Post: axied12
02-11-2025, 01:37 PM
» Replies: 0
» Views: 688
|
Trusted essay writing ser...
Forum: Off Topic
Last Post: axied12
01-30-2025, 08:16 AM
» Replies: 0
» Views: 619
|
Bootverkopers - actieve j...
Forum: Off Topic
Last Post: axied12
12-07-2024, 11:07 AM
» Replies: 0
» Views: 747
|
Services for individuals ...
Forum: Off Topic
Last Post: axied12
12-02-2024, 03:31 PM
» Replies: 0
» Views: 706
|
Used excavators
Forum: Off Topic
Last Post: axied12
11-13-2024, 09:22 AM
» Replies: 0
» Views: 688
|
Buy Higo Rocket in Dubai
Forum: Off Topic
Last Post: axied12
10-25-2024, 01:09 PM
» Replies: 0
» Views: 792
|
Anime coloring pages
Forum: Off Topic
Last Post: axied12
10-13-2024, 05:10 PM
» Replies: 0
» Views: 833
|
|
|
An Introduction to Machine Vision Systems |
Posted by: I676DDD - 09-13-2021, 08:11 AM - Forum: FPS and Shooters
- No Replies
|
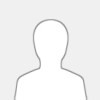 |
An Introduction to Machine Vision Systems
Machine vision systems are a set of integrated components that are designed to use information extracted from digital
images to automatically guide manufacturing and production operations such as go/no testing and quality control processes.
These systems can also play a role in automated assembly verification and inspection operations through their ability to
guide material handling equipment to position products or materials as needed in a given process. They have wide applications
across different industries and can be used to automate any mundane, repetitive tasks that would become tiring to a human
inspector or operator. The use of automatic vision measuring
machine allows for 100% inspection of products or parts in a process, resulting in improved yields, reductions in
defect rates, increased quality, lower costs, and greater consistency of process results.
How Machine Vision Systems Work
To understand how a manual vision measuring machine
works, it may be helpful to envision it performing a typical function, such as product inspection. First, the sensor detects
if a product is present. If there is indeed a product passing by the sensor, the sensor will trigger a camera to capture the
image, and a light source to highlight key features. Next, a digitizing device called a frame-grabber takes the camera’s
image and translates it into digital output, which is then stored in computer memory so it can be manipulated and processed
by software.
In order to process an image, computer software must perform several tasks. First, the image is reduced in gradation to a
simple black and white format. Next, the image is analyzed by system software to identify defects and proper components based
on predetermined criteria. After the image has been analyzed, the product will either pass or fail inspection based on the
machine vision system’s findings.
Measurement functions of the large-stroke
coordinate measuring instrument are done through the comparison of a recorded dimension from a digital image against a
standard valve to establish a tolerance or to determine if the observed value of the dimension is within acceptable levels of
tolerance as called for in the design specification for that part.
Video Motion Quality (VMQ) evaluates the relative motion quality of the distorted video generated from the reference
video based on all the frames from the two videos. VMQ uses any frame-based metric to compare frames from original video and
distorted video. It uses the timestamp of each frame to measure the intersection value. VMQ measuring machine combines the comparison value with the intersection value in the aggregate
function to produce the final result. To explore the efficiency of VMQ, we used a set of uncompressed original videos to
generate a new set of encoded videos. These encoded videos are then used to generate a new set of distorted videos that have
the same video bit rate and frame size, but the frame rate is reduced.
In modern machines, the gantry type vision measuring
machine superstructure has two legs and is often called a bridge. This moves freely along the granite table with one
leg (often referred to as the inside leg) following a guide rail attached to one side of the granite table. The opposite leg
(often outside leg) simply rests on the granite table following the vertical surface contour. Air bearings are the chosen
method for ensuring friction free travel. In these, compressed air is forced through a series of very small holes in a flat
bearing surface to provide a smooth but controlled air cushion on which the CMM can move in a near frictionless manner which
can be compensated for through software. The movement of the bridge or gantry along the granite table forms one axis of the
XY plane. The bridge of the gantry contains a carriage which traverses between the inside and outside legs and forms the
other X or Y horizontal axis. The third axis of movement (Z axis) is provided by the addition of a vertical quill or spindle
which moves up and down through the center of the carriage. The touch probe forms the sensing device on the end of the quill.
The movement of the X, Y and Z axes fully describes the measuring envelope. Optional rotary tables can be used to enhance the
approachability of the measuring probe to complicated workpieces. The rotary table as a fourth drive axis does not enhance
the measuring dimensions, which remain 3D, but it does provide a degree of flexibility. Some touch probes are themselves
powered rotary devices with the probe tip able to swivel vertically through more than 180 degrees and through a full 360
degree rotation.
Height gauges can be used to determine an object or workpiece’s height with
extremely high accuracy and precision. These precision measuring instruments also provide marked locations on an item
relative to one reference plane for subsequent use.
Center-line distances, internal/external diameters, and step heights are some of the different measuring tasks that can
be carried out by high-specification digital height gauges.
They claim consistency of ±0.0001 inch and can be extremely precise up to 0.001 inches. Of course, the consistency and
precision of such instruments still depend on their overall quality, so it’s essential only to source one from websites of
reliable manufacturers.
|
|
|
Rheometers: How and What do they Measure? |
Posted by: I676DDD - 09-13-2021, 08:09 AM - Forum: FPS and Shooters
- No Replies
|
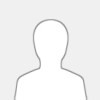 |
Rheometers: How and What do they Measure?
To measure the rheological properties of your sample with a rotational and oscillatory rheometer requires the
determination of the torque and deflection angle of the measuring bob. Your sample provides resistance or a reset torque to
the setting. The resulting deflection angle is then measured by the rheometer
encoder. The speed is calculated from the deflection angle and the time.
However, as the user, you are usually more interested in the rheological parameters. How do you get these? Rheological
parameters are calculated from the measured values torque, deflection angle, and speed using conversion factors. All further
parameters, such as viscosity, are not measured but calculated.
There is a new grading system for color concentrates and additive masterbatches. It is the European test of melt
dispersability known as FPV or Filter Pressure Value. It is reportedly more stringent than the ASTM dispersion test and a
more objective indicator of both dispersion quality in a concentrate and how well it will disperse in a polymer matrix. Above
all, it is a single number that shows how a concentrate compares with other products.
What is an FPV?
The basic principle is that you run compounded material through a screen mesh, which gradually blocks up with trapped
particles. The time it takes to block and the degree of pressure build-up are a good indication of how well dispersed the
masterbatch was. The filter pressure value tester
calls for feeding the lab extruder for a period of time only the
matrix polymer without masterbatch to get a baseline die-pressure reading. Then you introduce the masterbatch and record how
pressure builds as undispersed pigment or other additive is trapped on the screen pack. The test is a combination of time and
pressure peak. After a set time, you reintroduce virgin material into the extruder, and the pressure plot starts to drop to
show that you are ending the test.
The basic steps of compounding can perfectly be realized with a corotating lab compounding extruder. This makes modular co-rotating twin screw extruders the ideal companion
for plastics from synthesis up to recycling. Profit from the harmonized, modular conception of screws and barrels for
optimally realizing all processing steps (feeding, conveying, plasticizing, dispersing, reacting, venting, pressure build-
up). The system configuration of each model can easily be adapted to the individual processing task - anytime and at a low
cost. Or combine several processing steps within a continuously working extruder and use your twin screw extruder as a modern
in-line compounder. Depending on the extruder size, on the material to be tested, and on the processing task, throughputs up
to 60 kg/h can be reached. This opens up the entire application range to these extruders - from material development up to
small-scale production of sheets and films.
Detailed operating procedures of the lab cast film machine
:
1. Prepare related tools, such as copper sheet, alcohol, mold release agent, etc.
2. Check whether the die head, rollers, etc. of the casting machine and their surroundings are clean, then clean the die
head with alcohol, paraffin wax and gauze, or clean it with a copper sheet and spray it with a release agent.
3. Check whether the rotation and pressure of each roller of the cast film machines are normal and whether the heat
exchange system, pump and pressure gauges can work normally.
4. Wear each roller with a thick film through film, and then put the chilled roller in a closed state to press the film.
5. Start the cast film machine, check whether the thick sheet and the melt have adhered firmly and smoothly, and then
pull the thick sheet tightly toward the person standing at the exit.
6. Adjust the appropriate working position and carefully complete all operations.
7. After the production is over, manually adjust the cast film machine to the non-working position, and then introduce
the material into the receiving tray, and stop the machine.
With the rapid development of industrial science and technology, the lab blown film machine has also mastered the skilled manufacturing process, but compared with the advanced
technology level, there are still gaps in some aspects. If the film blowing machine is to achieve rapid development, then it
must absorb the advanced technology level, let the film blowing machine develop in a new direction.
The calenders employ two or more steel rolls that close under pressure to smooth, compress, and in some cases partially
bond a nonwoven, plastic, paper, or another substrate. The rollers may be mirror-smooth, embossed with a pattern, or porous,
and are usually heated with hot oil or electric elements. The lab
calender machines can be utilized in an independent converting setting or an integrated production facility.
|
|
|
Are polarized sunglasses right for you? |
Posted by: I676DDD - 09-13-2021, 08:07 AM - Forum: FPS and Shooters
- No Replies
|
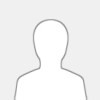 |
Are polarized sunglasses right for you?
The glare-reducing perks of polarized lenses
Polarized sunglasses are known for their ability to block the
glare that reflects off of certain surfaces. This makes them very popular among people who spend a lot of time outdoors, on
the road and around bodies of water.
But polarized sports sunglasses are not just for people who
love boating, fishing or lounging on the beach. Anyone who is bothered by outdoor glare can benefit from this type of
sunglass lens.
Polarized sunglasses can be helpful for driving too,
since they reduce the glare that reflects off of cars and light-colored pavement.
Some light-sensitive people, including those who have recently had cataract surgery, can also benefit from polarized
lenses.
What does polarized mean?
When a lens is polarized, it has a built-in filter that blocks bright, reflected light. This intense light is known as
glare.
When glare is reduced, your eyes feel more comfortable and you can see your surroundings more clearly.
Sunlight scatters in all directions. But when it strikes flat surfaces, the reflected light tends to become polarized,
meaning the reflected rays travel in a more uniform (usually horizontal) direction.
This creates an annoying, sometimes dangerous intensity of light that can reduce visibility.
Polarized sunglasses
Men polarized sunglasses offer
a few advantages when it comes to combating bright sunlight:
Excellent glare reduction around bodies of water
Better visibility while you're driving
More vibrant colors and contrast among outdoor scenery
People who spend a lot of time driving during the day should experience better comfort and visibility with polarized
glasses. That, in turn, can help them drive more safely and confidently.
However, keep in mind that drivers, boaters and pilots may experience problems seeing certain digital displays on
instrument panels while they are wearing polarized sunglasses. This can be a problem if a split-second decision depends on
the information displayed on a screen.
Different optical glasses frame materials greatly
expand your options for a new look. While shopping for new eyeglasses or sunglasses, ask your optician for advice about
variety in colors, durability, lightness, favorite brands, hypoallergenic materials, uniqueness and price.
In fact, finding eyeglasses with the qualities that are most important to you could be as simple as choosing the right
glasses frame material, since each type has
its own unique strengths. If you're shopping online, be sure to use the retailer's material filter while browsing
eyeglasses to ensure you find what you are looking for.
People have started to worry about the health effects of blue light emitting from screens. For this reason, more and
more people are wearing blue light glasses. These are glasses that contain lenses that partially block short-wave blue light.
Blue light blocking glasses
are glasses that manufacturers claim can filter out blue light. The glasses have filtering materials or surface
coatings on the lenses that block a portion of blue light. People who think that their eye and vision symptoms are due to
blue light exposure may wear them to decrease their exposure to it.
A majority of the children do not need to wear spectacles. But sometimes a child may need them. This article is about
children needing to wear glasses and has some ideas on how to make them wear their glasses without qualms.
How a pair of glasses fits your child is important. Kids glasses
are not to be considered as small versions of adult glasses. The cheeks and noses of adults are of different
proportions than children. Spectacle frames need to take these differences into account if they are to fit properly. When
assisting your child in choosing eyewear, experienced children opticians keep these factors in mind.
|
|
|
What Are Evaporative Coolers? Here’s Everything You Need to Know |
Posted by: I676DDD - 09-13-2021, 08:02 AM - Forum: FPS and Shooters
- No Replies
|
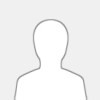 |
What Are Evaporative Coolers? Here’s Everything You Need to Know
Looking for a way to beat the heat? If you do not have a central air conditioning system in your home — or if you do but
are researching more environmentally friendly or affordable options — you might be wondering if evaporative
air coolers are right for you.
The answer is … it depends.
Understanding how evaporative coolers work is a crucial part of figuring out if one will work well in your home. If you
are new to evaporative cooling, there is a lot to learn. Here is everything you need to know about how evaporative coolers
work — and how to decide if you should invest in one.
What Are Evaporative Coolers?
An evaporative air cooler is a type of
air conditioner that works by harnessing the power of evaporation to cool air temperatures. When water evaporates, it turns
from liquid to gas. As it does so, the highest-energy particles leave the water first, and this leads to a drop in
temperature. This is why a moist cloth on your forehead feels good on a hot day — it is actually helping to lower your head
temperature as the water evaporates.
The same scientific principles apply to the evaporative cooling process when it comes to your home air. In a dry
environment, the simple process of evaporation can help lower the temperature of the air. You may have felt this for yourself
if you have ever misted the air around you to feel cooler on a hot summer day. An evaporative air conditioner uses the same
idea, but it adds technology to make the process more efficient — and less messy — than just spraying a room with water and
hoping for the best.
How do Evaporative Coolers Work?
An evaporative cooling system takes basic evaporation and automates it to efficiently lower the temperature of the air in
your home. In general, the machine will consist of a fan, a thick pad, a water reservoir and some additional controls for
fine-tuning the results. The fan draws dry, hot air into the machine and across the cooler pads. These thick pads absorb
water from the reservoir and have many layers to increase the surface area. As the hot air crosses the pad, the water
molecules on the surface evaporate, which causes the air temperature inside the
electric air cooler to drop — often by as
much as 20 degrees. The fan then blows that cold air into your room, where you can enjoy the chill on a hot day.
Evaporative coolers can have other useful parts built into them as well. Many utilize air filters and pads that are
designed to improve air quality by reducing allergens and minimizing mildew growth — an important consideration for anyone
with allergies or other respiratory concerns. A water pump, while not strictly necessary, can streamline the absorption into
the cooling pad. Some models offer the option of adding an ice pack to further cool the air the fan blows out into the room.
Varying fan speeds, oscillating functions and remote control are also useful features.
A portable air cooler is a great way to
see if evaporative cooling will work in your home without making a big investment upfront. Portable coolers come with wheels
to easily move them from room to room for a little extra chilling exactly where you need it. You can also use these outside
as long as you can reach an outlet to plug them in. This makes portable evaporative coolers welcome accessories to a picnic,
pool party or any other outdoor gathering where people would appreciate a cool breeze. They still work best in dry places,
but you won’t have to worry about any special venting (as with portable air conditioners) or humidity build-up (as with
indoor evaporative cooler use). If you’re interested in experimenting to see what evaporative coolers are all about, a
portable version is a fine way to get started.
A large industry ceiling fan pushes air
down to the living level by pulling from the air that it has above the blades to work with. The air is moved to the floor,
and then recirculated back up to above the blades after it spreads across the room and moves back up the walls. Thus, moving
back above the blades to repeat the process.
If a fan does not have enough space between the blades and walls or any other solid obstruction, there will be a vacuum
affect created above the blades, and there will be no air for the fan to continue to circulate. With no air to circulate
there will be no breeze below the ceiling fan.
Currently, a number of works and industries operate in a state of polluted air, which is not well ventilated. Therefore,
the necessary need is how to better deal with the environmental situation.
Industrial exhaust fans are the
solution to this requirement. This is an item with air circulation function to eliminate hot air, odors … This
industrial fan has a large capacity and wind flow. They are
suitable for areas with large acreage such as factories, warehouses, breeding facilities.
Electric heaters, the device for heating rooms that converts
electric current to heat by means of resistors that emit radiant energy. Resistors may be composed of metal-alloy wire,
nonmetallic carbon compounds, or printed circuits. Heating elements may have exposed resistor coils mounted on insulators,
metallic resistors embedded in refractory insulation and encased in protective metal, or a printed circuit encased in glass.
Fins may be used to increase the area that dissipates the heat. Home electric heaters also are used for domestic central heating and for materials processing in the
industry.
|
|
|
Using SMS and Email to Engage Your Customers |
Posted by: I676DDD - 09-13-2021, 08:00 AM - Forum: FPS and Shooters
- No Replies
|
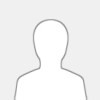 |
Using SMS and Email to Engage Your Customers
For companies around the world, email is the go-to channel for customer communications. Whether it is logins,
notifications, promotions, password resets, or policy updates, email is a tried-and-true platform with more global
accessibility than any other medium.
However, email is only one part of the customer engagement experience.
Regardless of who you are trying to contact or where they are, you can now complete the customer engagement package with
another robust API: SMS.
Alone, SMS PVA is a powerful engagement tool that allows businesses to send
concise, timely messages to their customers. Combined with email, the two create a seamless customer communication experience
that is reliable, scalable, and downright powerful.
What is an SMS?
SMS stands for Short Message Service and is a more technical term for what we know as a text message. The SMS API bridges
the gap between the Internet and the carrier network in order to send and receive SMS messages.
The Need for SMS
When it comes to business communications, consumers have varying preferences. According to our 2020 Global Messaging
Engagement Report, people across generations and borders prefer email and SMS for their communications. That is why
India SMS PVA and email both deserve a place in your
communication toolset.
Using multiple communication channels provides customers with a seamless experience. With multiple mediums to choose
from, customers can engage with your business on the channels they prefer.
Like email, Mexico SMS PVA needs to be used at the right
time and for the right message. Below are some of the most common use cases for leveraging SMS in addition to email.
The actual nuts and bolts of how the internet works are not something people often stop to consider. The problem with
that is the inherent danger of data security breaches and identity theft that come along with cute dog pictures, 24-hour news
updates, and great deals online.
But what actually happens when you browse the web? You might be using a proxy server at your office, on a Virtual Private
Network (VPN) or you could be one of the more tech-savvy who always use a proxy
server of some kind or another.
What is a Proxy Server?
A proxy server is any machine that translates traffic between networks or protocols. It is an intermediary server
separating end-user clients from the destinations that they browse. Proxy servers provide varying levels of functionality,
security, and privacy depending on your use case, needs, or company policy.
If you are using a proxy server, traffic flows through the proxy server on its way to the address you requested. The
request then comes back through that same proxy server (there are exceptions to this rule), and then the proxy server
forwards the data received from the website to you.
If that is all it does, why bother with a proxy server? Why not just go straight from to the website and back?
Modern proxy servers do much more than forwarding web requests, all in the name of data security and network performance.
Proxy servers act as a firewall and web filter, provide shared network connections, and cache data to speed up common
requests. A good proxy server keeps users and the internal network protected from the bad stuff that lives out in the wild
internet. Lastly, proxy servers can provide a high level of privacy.
How Does a Proxy Server Operate?
Every computer on the internet needs to have a unique Internet Protocol (IP) Address. Think of this IP address as your
computer street address. Just as the post office knows to deliver your mail to your street address, the internet knows how to
send the correct data to the correct computer by the IP address.
An India proxy server is basically a computer on the internet
with its own IP address that your computer knows. When you send a web request, your request goes to the proxy server first.
The proxy server then makes your web request on your behalf, collects the response from the webserver, and forwards you the
web page data so you can see the page in your browser.
When the proxy server forwards your web requests, it can make changes to the data you send and still get you the
information that you expect to see. A proxy server can change your IP address, so the web server does not know exactly where
you are in the world. It can encrypt your data, so your data is unreadable in transit. And lastly, a
Mexico cheap proxy provider can block access to
certain web pages, based on IP address.
|
|
|
Understanding Pipe Fittings |
Posted by: I676DDD - 09-13-2021, 07:58 AM - Forum: FPS and Shooters
- No Replies
|
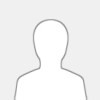 |
Understanding Pipe Fittings
Pipe fittings are components used to join pipe sections together with other fluid control products like valves and pumps
to create pipelines. The common connotation for the term fittings is associated with the ones used for metal and plastic
pipes which carry fluids. There are also other forms of pipe fittings that can be used to connect pipes for handrails and
other architectural elements, where providing a leak-proof connection is not a requirement. Pipe
link fittings may be welded or threaded, mechanically
joined, or chemically adhered, to name the most common mechanisms, depending on the material of the pipe.
There is some inconsistency in terminology surrounding the terms pipe, tube, and tubing. Therefore, the term pipe
fittings will sometimes be mentioned in the context of tubing as well as pipe. While similar in shape to tube fittings, pipe
fittings are seldom joined by methods such as soldering. Some methods overlap, such as the use of compression
power fittings, but where these are commonplace for
connecting tubes or tubing, their use in pipe connections is rarer. It suffices to say that while there are general
distinctions, the common usage of terms can differ from supplier to supplier, although they represent the same items.
Pipe Fittings Explained: Fitting Materials and Manufacturing Processes
Cast and malleable iron
Fittings for cast iron pipe fall under hubless and bell-and-spigot styles. Hubless designs rely on elastomeric couplers
that are secured to the outer diameters of the pipe or fitting by tension clamps, usually a stainless steel band clamp that compresses the elastomeric material and forms a seal.
These hubless or no hub designs are sometimes referred to as rubber pipe couplings or rubber plumbing couplings and are
especially popular for transitioning from one material to another—from copper to cast iron, for instance. Bell-and-spigot,
or sometimes, hub-and-spigot, overhead line fittings
are joined today primarily with elastomeric gaskets that fit inside the bell and accommodate the insertion of the
plain pipe end or fitting. Older systems before the 1950s were caulked using a combination of molten lead and a fibrous
material such as oakum. Cast iron pipe is sometimes joined with bolted flanges, or in some cases, mechanical compression
connections. Flanged joints employed in underground applications can subject the pipe to settlement stresses unless the pipe
is adequately supported.
The anti-vibration hammer is designed to
reduce wind-induced wire vibration. High-voltage overhead lines have high pole positions and large spans. When the wire is
subjected to wind, it vibrates. When the wire vibrates, the working conditions at the wire suspension are the most
unfavorable. Due to multiple vibrations, the wire will be fatigue damage due to periodic bending. When the span of the
overhead line is greater than 120 meters, vibration-resistant hammers are generally used to prevent vibration. The
installation position of the anti-vibration hammer should be determined according to the construction requirements. After the
anti-vibration hammer is installed, it can produce the movement opposite to the vibration of the wire, thus eliminating or
weakening the vibration of the wire.
Pole Line Hardware is Used in Multiple Industries
Pole line hardware is used in industries such
as telecommunication, aviation, electrical, automotive, fabrication, marine, medical, mining and aerospace. This hardware is
made of various materials including steel, aluminum, platinum, silver, titanium and copper.
Manufacturers of pole line hardware have been in existence since the 19th century. As such, the manufacture and design of
pole line hardware has improved over time. It is important to understand the different specifications and requirements of
your cables. Choosing fasteners that are suited to these exact tolerances is crucial to ensure stability.
Since pole lines support and distribute utilities for long periods of time, the hardware used in the making of pole lines
must be subjected to tests that enhance strength and eliminate the possibility of weakness. These tests include wet and dry
AC withstands, thermal imaging, compression, radio interference voltage and partial voltage tests.
With daily advancements in technology, distributors of pole line utilities have embraced safety and efficiency that goes
a long way in serving the general population. AMAC Equipment supplies tested and true high-quality hardware like crossover
clamps and drops hardware to suit multiple applications in the field.
Bolts are one of the most common elements used in
construction and machine design. They hold every-thing together – from screws in electric toothbrushes and door hinges to
massive bolts that secure concrete pillars in buildings. Yet, have you ever stopped to wonder where they actually came from?
What the majority of researchers on this topic do agree on, though, is that it was the Industrial Revolution that sped up
the development of the nuts and bolts and put them firmly on the
map as an important component in engineering and construction world.
|
|
|
Sit-Inside vs. Sit-On-Top Kayaks – 4 Reasons One is Better |
Posted by: I676DDD - 09-13-2021, 07:51 AM - Forum: FPS and Shooters
- No Replies
|
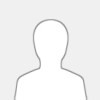 |
Sit-Inside vs. Sit-On-Top Kayaks – 4 Reasons One is Better
Both hardshell and inflatable kayaks can be categorized into two different styles:
Sit-on-top kayak (SOT) and
Sit-in kayak (SIT)
The two designs differ drastically from one another, and each suits a different purpose.
The differences between sit-on-top vs. sit-in kayaks
The most apparent distinction between sit-inside and sit-on-top inflatable kayaks (& hardshell models) is that SIKs have an enclosed cockpit that positions the paddler inside the boat at or below the water level. In contrast, SOT kayakers sit on top of the kayak above the water’s surface.
This fundamental divergence of design affects every aspect of their use and purpose.
The sit-on-top model is the most popular design among beginners and recreational kayakers because it does not make the paddler feel like they are trapped inside of the kayak’s cockpit if they capsize.
If they do tip over for some reason, they are far easier to reen
The sit-inside model is more prevalent among intermediate and advanced paddlers because its design provides a significantly lower center of gravity, resulting in enhanced secondary stability during specific activities (which I’ll talk about later).
The cockpit of a SIK kayak is surrounded by a rim for attaching a spray skirt to keep water out.
They have similarities as well
Even though there are some significant differences between the two styles, their main parts are similar:
The top of the kayak is called the deck, where you’ll often have bungees or deck lines.
The bottom is the hull.
The front is the bow.
The back is the stern.
Both types of kayaks have:
A seat (or seats in case of tandem kayaks).
Foot support like simple footwells or adjustable foot pedals (which are more comfortable on a full day of paddling).
Top of the line kayaks will additionally have a built-in backrest to make paddling for hours more comfortable.
The pros and cons of sit-inside & sit-on-top kayaks
Sit-Inside kayak pros
The most significant advantage of a sit-inside kayak is that its center of gravity is lower than that of a sit-on-top kayak, which provides better secondary stability. This enables you to lean the boat on its side edge for more efficient turning and stay upright in rough seas. There is a trade-off, though, which I’ll get to in the cons section.
Because sit-inside kayaks have a lower center of gravity, they can be made much narrower than a sit-on-top model. Being slimmer and longer means they are faster and easier to paddle than SOT kayaks, making them well suited for longer trips.
The lower profile also means that sit-inside kayaks are affected by wind to a lesser extent.
The enclosed cockpit provides protection from the sun or rough water.
A spray skirt can easily be attached to the cockpit coaming for full protection from rain, snow, or frigid water during winter paddling. A well-sealed high-quality spray skirt can also be a safety feature because it will keep water out of the cockpit in case you flip (providing you can roll back and correct your white water kayak).
Sitting inside a cockpit lets you place your legs against the side of the kayak & the underside of the deck. Your body effectively becomes one with the kayak’s body to enhance your control of the kayak, making it more maneuverable.
You will find there’s room inside the kayak to store your equipment and keep them dry. Water can’t get in through self-draining scupper holes found on SOK kayaks. Some sit-in kayaks even have integrated watertight storage compartments.
Due to the narrower beam of SIK kayaks, you can use a shorter paddle. This makes the boat easier to propel forward because the moment arm will be tighter. (The moment arm is the distance from your centerline to the part of the paddle entering the water. The shorter it is, the easier it is to paddle.)
Sit-Inside Kayak Cons
The single biggest con against sit-inside kayaks concerns floatation and ease of rescue, as the cockpit can take in a lot of water in case you capsize.
Touring kayaks have 1 or 2 integrated bulkheads to circumvent this. But “what is a bulkhead”, you ask?
A kayak bulkhead is a built-in compartment, which traps air inside of the kayak. The bulkhead limits how much water can get into the boat and acts as a floatation chamber to keep it afloat if you swamp. Additionally, bulkheads have a hatch so that you can use them to dry-store supplies as well.
Most recreational SIT kayaks will not have a bulkhead, but the better ones have a single one behind the seat.
If you are alone, flipping a swamped kayak back is very difficult, and so is getting the water out of it. Paddling a kayak filled with water is close to impossible unless it has bulkheads that stayed dry. For this reason, beginners using a SIK kayaks should paddle close to shore, so they can swim out and empty their kayak if they capsize.
If you plan on going out on open water, you need a touring kayak with bulkheads, and first, learn how to correct your capsized kayak and get back into it. Coastal paddling is a treat, but you have to prepare to stay safe.
You can only carry items that fit through the cockpit and other hatches. Tieing larger items on deck degrades performance and your balance.
Remember the increased secondary stability of SIK kayaks due to their lower center of gravity? Well, here is the flip side. The low sitting position causes them to have less primary stability.
Sit-On-Top Kayak Pros
They have a wider beam, giving them an advantage in initial stability. This makes them easier to use and more stable than sit-in kayaks.
They are easy to get in and out of. You can safely jump into the water for a swim and climb back whenever you wish.
If a SOT kayak flips over, it doesn’t swamp (fill up) since it doesn’t have a cockpit. You can quickly flip it back over and climb back on.
Any water left on the deck will drain away through self-bailing drain holes.
The design is convenient when launching, as well as for landing. You can lower yourself onto the kayak’s seat and swing your legs on if you launch from knee-deep water. This makes SOK kayaks the choice for people with mobility issues.
There is no cockpit to fit into, which means they are better for larger people.
A SOT has more generous storage space; you can bungee anything on the deck, which is essential on multi-day camping trips.
And because everything is on the deck, access to your gear is more comfortable. You won’t have to struggle and reach deep into your cockpit to get your things. This is especially important for fishermen, who need space to store their gear and freedom of movement to use their equipment. All fishing kayaks are of the sit-on-top variety.
Sit-on-top kayaks are cheaper than their sit-inside counterparts.
Stand-up paddleboarding is becoming more popular each year. Hawaiians have been using it for years as a means to keep fit when the waves are not adequate for surfing. By using a paddleboard surfers were able to enjoy the water and obtain some exercise simultaneously. In the last several years millions of people have begun to enjoy paddle boarding while standing (SUP). People now engage in stand-up paddling to enjoy the water, spend time with friends, and improve their fitness level.
SUP board can provide you with a very good overall workout. You will make use of balance and strength in order to remain upright and propel yourself in the water. The level of intensity you will experience will be variable and be dependent on your venue. If you are paddling in the ocean and there are a lot of waves and an ocean current, your workout will be intense. If you are simply drifting in relatively placid waters, it will not be so hard-core.
|
|
|
Introduction to Pressure Seal valves |
Posted by: jjwko565s - 09-13-2021, 03:47 AM - Forum: Welcomes and Introductions
- No Replies
|
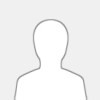 |
Pressure seal construction is adopted for Valves for high pressure service, typically in excess of above 170 bar. The unique feature about the pressure seal Bonnet is that the body-Bonnet joints seals improves as the internal pressure in the Valve increases, compared to other constructions where the increase in internal pressure tends to create leaks in the body-Bonnet joint.
The higher the internal pressure, the greater the sealing force. Easy dismantling is made possible by dropping the Bonnet assembly into the body cavity and driving out the four-segmental thrust rings by means of a push pin.
Relying on fairly simple design principles, pressure seal valves have proven their capability to handle increasingly demanding fossil and combined-cycle steam isolation applications, as designers continue to push boiler, HRSG, and piping system pressure/temperature envelopes. Pressure seal Valves are typically available in size ranges from 2 inches to 24 inches and ASME B16.34 pressure classes from #600 to #2500, although some manufacturers can accommodate the need for larger diameters and higher ratings for special applications.
Pressure seal gate valves are available in many material qualities such as A105 forged and Gr.WCB cast, alloy F22 forged and Gr.WC9 cast; F11 forged and Gr.WC6 cast, austenitic stainless F316 forged and Gr.CF8M cast; for over 500°C, F316H forged and suitable austenitic cast grades.
The pressure seal design concept can be traced back to the mid-1900s, when, faced with ever increasing pressures and temperatures (primarily in power applications), Valve manufacturers began designing alternatives to the traditional bolted-Bonnet approach to sealing the body/Bonnet joint. Along with providing a higher level of pressure boundary sealing integrity, many of the pressure seal globe valves design weighed significantly less than their bolted Bonnet Valve counterparts.
Bolted Bonnets vs. Pressure Seals
To better understand the pressure seal design concept, let's contrast the body-to-Bonnet sealing mechanism between bolted Bonnets and pressure seals. FIG. 1 depicts the typical Bolted Bonnet valve. The body flange and Bonnet flange are joined by studs and nuts, with a gasket of suitable design/material inserted between the flange faces to facilitate sealing. Studs/nuts/bolts are tightened to prescribed torques in a pattern defined by the manufacturer to affect optimal sealing. However, as system pressure increases, the potential for leakage through the body/Bonnet joint also increases.
Pressure Seal Gaskets
One of the primary components involved in sealing the pressure seal Valve is the gasket itself. Early pressure seal gaskets were manufactured from iron or soft steel. These gaskets were subsequently silver-plated to take advantage of the softer plating material's ability to provide a tighter seal. Due to the pressure applied during the Valve's hydrotest, a set (or deformation of the gasket profile) between the Bonnet and gasket was taken. Because of the inherent Bonnet take-up bolt and pressure seal joint elasticity, the potential for the Bonnet to move and break that set when subjected to system pressure increases/ decreases existed, with body/Bonnet joint leakage the result.
This problem could be effectively negated by utilizing the practice of "hot torquing" the Bonnet take-up bolts after system pressure and temperature equalization, but it required owner/user maintenance personnel to do so after plant startup. If this practice was not adhered to, the potential for leakage through the body/Bonnet joint existed, which could damage the pressure seal gasket, the Bonnet and/or the I.D. of the Valve body, as well as creating compounding problems and inefficiencies that the steam leakage could have on plant operations. As a result, Valve designers took several steps to address this problem.
Although many manufacturers still recommend hot torquing, the potential for leakage when this is not done is greatly diminished. The seating surfaces in pressure seal Valves, as in many power plant Valves, are subjected to, comparatively speaking, very high seating loads. Seat integrity is maintained as a function of tight machining tolerances on component parts, means of providing the requisite torque to open/close as a function of gears or actuation, and selection/ application of proper materials for seating surfaces.
Cobalt, nickel, and iron-based hardfacing alloys are utilized for optimal wear resistance of the wedge/disc and seat ring seating surfaces. Most commonly used are the CoCr-A (e.g., Stellite) materials. These materials are applied with a variety of processes, including shielded metal arc, gas metal arc, gas tungsten arc, and plasma (transferred) arc. Many pressure seal Globe Valves are designed having integral hardfaced seats, while the Gate Valves and Check Valves typically have hardfaced seat rings that are welded into the Valve body.
Both butterfly valves and ball valves offer unique benefits, so choosing between them in certain processes isn't a hard choice. It can be problematic when a process requires valve characteristics that both valves have. We need a deeper understanding of the butterfly valve vs ball valve in order to pick the correct valve.
Teflon is a polymer compound formed by the polymerization of tetrafluoroethylene with excellent chemical stability, corrosion resistance, sealing, high lubrication and non-viscosity, electrical insulation and good aging resistance for media such as strong acid, strong alkali, strong oxidant. Its operating temperature is -200 ~ 180℃, poor fluidity, large thermal expansion. Teflon lined valves ensures extremely high chemical resistance and longevity, can be widely used in corrosive applications in the chemical, electric machinery,harmaceutical, petrochemical, fertilizer, pulp and paper, and metallurgical industries.
|
|
|
SUSTAINABLE PACKAGING IN THE BEAUTY INDUSTRY: THE PROS & CONS OF PLASTIC. |
Posted by: jjwko565s - 09-13-2021, 03:45 AM - Forum: Welcomes and Introductions
- No Replies
|
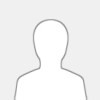 |
Plastic is one of the most polarizing topics in sustainability today, and each year continues to reveal more about its place in the beauty industry. Sustainability is a constantly evolving conversation and the rate at which cosmetic plastic bottle is produced, used and disposed of has long outpaced the research, technology and innovation needed to understand the consequences of our actions, making it quite challenging to gather data that’s specific to cosmetics. Yet, we do know that the volume of plastic which can accumulate during the process of making a single product is sometimes staggering - if you make cosmetics products for-profit and are looking to grow, hardly any brand is exempt from the presence of plastic.
In a roadmap for sustainability released by the United Nations Environment Programme in 2018, the executive summary reads: The benefits of plastic are undeniable. The material is cheap, lightweight and easy to make. These qualities have led to a boom in the production of plastic over the past century since the 1950s. We are already unable to cope with the amount of plastic waste we generate unless we rethink the way we manufacture, use and manage plastics. Ultimately, tackling one of the biggest challenges of our time will require governments to regulate, businesses to innovate and individuals to act.
Let’s admit that plastic has gathered a bad reputation - you might even say it’s been demonized in some cases. To be clear, there is no denying that waste is a problem, but to blanket shame plastic without context is to miss an opportunity for a closer look. If you want to dive deeper into all the factors that contribute to plastic waste, take a look at this hugely informative and fascinating collaboration from Oxford University and the Global Change Data Lab:
Particularly in 2020, single-use consumption of plastics across multiple industries has seen a massive increase due to essential sanitary and safety precautions needed to manage the spread of COVID-19. It’s important to note that single-use plastic lotion bottle is a cornerstone of essential hygiene measures within the medical industry from masks, gloves, gowns and medical instruments. We doubt that we will comprehend the waste consequences of single use plastic throughout 2020 for sometime to come.
As a beauty brand this is undeniably a charged conversation to have, as plastic is dotted across our packaging chain and understanding the trade-offs is key. From health effects, to degradation, to ecosystems impact, plastic could easily be a whole PhD dissertation, and it is challenging to limit our focus when this material is a global common denominator of modern consumption. We are attempting to share a simplified perspective on the presence of plastics within the cosmetics industry to better understand the benefits and pitfalls of this material.
We are interested in the life cycle of plastic packaging in cosmetics - more specifically, the contrast between the production of plastic, versus the use of plastic, versus the end-of-life for plastic. As PET (Polyethylene Terephthalate) is the most commonly used plastic in cosmetic packaging and for Josh Rosebrook products, we will be focusing on this material to exemplify the pros and cons of plastic packaging.
Specializing in life cycle assessment (LCA) and solid waste management, a US independent consulting firm, Franklin Associates, has conducted multiple research studies on PET across various industries. In a 2009 study on the comparison of beverage containers (very similar to cosmetic containers), Franklin Associates found that the production of a PET bottle was far more energy efficient when compared to the production of an aluminum can and glass bottle, respectively. The amount of energy it took to create a PET bottle was 11 million BTU, vs. 16 million BTU for the aluminium can and 26.6 BTU for the glass bottle. The CO2 equivalent (think greenhouse gas emissions) was 1,125 for the PET bottle, 2,766 for the aluminum can, and 4,848 for the cosmetic glass bottle. When ranking material production in relation to energy efficiency, plastic is second right after wood, and aluminum and glass are last. There is conflicting evidence regarding how the world’s oil production contributes to the manufacturing of plastic.
A large majority of finished cosmetic products housed in plastic are multi-use: they are not disposed of after a single use and the amount of times they are used according to function can range into several hundred uses. Depending on the size and type, the product could also be kept in use for several weeks to multiple months. It is interesting to note that to bring a cosmetic product to market, the formula has to undergo a packaging compatibility test - depending on the ingredients and the function of the product, plastic might be a necessity to safely protect the formula over time and ensure a safe customer experience. For example, glass liquid bottles intended for use in the shower could be troublesome to manage safely.
With the growing importance of appearance for both men and women, there is a huge demand for cosmetics in today’s market. However, a manufacturer of specialty cosmetics needs to be able to make an impression on the consumer and ensure that they try the wonderful product first. Additionally, consumers now look for more than a terrific cosmetic, they want it at a lower price, and are also eco-conscious. Using tube packaging for specialty cosmetics meets multiple requirements of manufacturers.
Consumers prefer the convenience that cosmetic tube packaging provides. While cosmetic squeeze tubes were originally used for food products such as jams, jellies, ad mayonnaise, they are now being used by cosmetics manufacturers. Consumers love the convenience of tube packaging that comes with a variety of heads that makes dispensing cosmetics much easier. Consumers can easily dispense the right amount of cosmetics they need, reducing wasted products.
We offer glass and cosmetic parts for glass bottles, informing you of what format or material is most recommended in each case.
Glass bottles for oils and vinegar respond to particular characteristics in shape, color and height that can contribute to creating brand branding alone. In a company, an exclusive design is a guarantee of sales.
Glass bottles for oils preserve and protect the properties of the oil in order not to spoil its natural conditions, taking into account that many factors increase the process of oxidation and oil thickening.
Those skilled in the art recommend glass bottles for opaque oils to protect liquid gold from light, although transparent glass bottles sell the product better. Ultraviolet rays should be prevented from damaging the oil by protecting the bottle in cardboard containers.
|
|
|
The Best iPhone Cases From Apple To Casetify, Mous To Pipetto |
Posted by: jjwko565s - 09-13-2021, 03:44 AM - Forum: Welcomes and Introductions
- No Replies
|
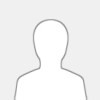 |
The new Apple iPhone 12 is a gorgeous smartphone. So, you’ll want to keep it that way, with a decent case—read on for a round-up of the very best Apple iPhone 12 kevlar cases you can buy right now.
When it comes to phone cases, what’s your favorite style? Folio? Sleeve? Back protector? Or something so slim and smooth you think there’s nothing there at all. Do you like something bright and solid, or something light but strong and ultra-protective? How hard are they to slide on and off if you fancy a change? Do they protect the display as well as the back? How sumptuous do they feel in your hand and how much do they weigh your new iPhone down? Whatever kind of case you prefer, you’ll find them all here. I’ve been testing iPhone 13 new cases for looks, fit, effectiveness and design appeal.
Also, there is a new element to cases this year: MagSafe. The name may be familiar from the cool way power cables connected to previous Mac laptops, but it’s now revived as a wireless charging pad. If you’ve ever used a wireless charging pad you’ll know that if you put the phone down in the wrong place last thing at night, you’ll wake to find the phone didn’t charge. MagSafe clamps the iPhone in place magnetically so that danger is gone. But MagSafe has other benefits, too: it tells your iPhone what you’re connecting to it and it holds an iPhone 8~xsmax case in place magnetically, so it’s much easier to slip the case on and off.
The iPhone 12 is amazingly good value, but it’s still not a cheap purchase. So, you’ll want to protect it. Even though the arrival of Ceramic Shield means the front glass is intensely more durable and resistant to being dropped, you may feel it’s not worth taking any chances. Here are the very best cases offering extra protection (and, therefore, extra peace of mind).
A suitable Apple Smartwatch is very precious. Not only because of its impressive features, but also because of its unparalleled style and luxurious price tag. More importantly, Apple Watch is a one-time investment for many people, which is why ensuring its safety is the top priority. Much like the iPhone, Apple Watch also has countless protective cases, from subtle to statement, you can have everything. Apple Watch case can protect your investment and protect you from panic attacks every time something hits your precious smartwatch. Therefore, if you want to be able to continue to wear your Apple Watch without worrying about damage, you can consider buying a sturdy smartwatch case.
If you are entrenched in the Apple ecosystem and love listening to music with great over-ear headphones, the AirPods Max is probably for you. However, they come with a case that resembles, shall we say, some undergarments. A good Airpods pro&max case is needed if you want to protect your headphones and don't like the case that was shipped with them. Let's explore the best AirPods Max cases on the market today.
Cigars are hand-rolled fermented tobacco. Compared with ordinary cigarettes, they have less nicotine content, less than 2%. Pure natural tobacco, which contains no chemical substances, has little harm to human body and is welcomed by business people. In many Western movies, we can see such a plot, the protagonist takes out a cigar from a well-decorated cigar box and ignites it to smoke. Cigar boxes were first made of high-quality wood. They can also be made of plastics, ox bones, carbon fibers and other materials.
Cigars are like alcoholic drinks. They do not fade away with time, but become stronger and stronger. A common cigar can be stored in a suitable environment for more than ten or twenty years, and its price can be doubled several times. The most suitable conditions for preserving cigars are temperature 18 degrees and humidity 70 degrees. Cigar boxes can isolate cigars from the outside world and keep them in their best condition. Top-grade wooden cigar boxes are made of cigar or mahogany, walnut and rosewood, which are exquisite in shape and expensive in price. Carbon fiber cigar boxes were invented relatively late, and only recently began to rise. They are light in weight, small in size, easy to carry with you, and will not have the problem of moist and moth-like wood. Its shape is streamlined and can closely fit the cigar inside, saving space to the greatest extent.
If you want to buy a new or used CNC router, you want the machine to solve your manufacturing challenges. We provide manufacturers of all sizes with cutting-edge technology from all woodworking technologies from world market leaders. We offer superior wood CNC processing technology and equipment for the highly efficient production of furniture, interior fittings, construction elements, and millwork, for panel processing, plastics and solid wood processing.
|
|
|
|