Welcome, Guest |
You have to register before you can post on our site.
|
Online Users |
There are currently 289 online users. » 0 Member(s) | 288 Guest(s) Google
|
Latest Threads |
Advanced microneedling
Forum: Off Topic
Last Post: axied12
05-28-2025, 01:25 PM
» Replies: 0
» Views: 165
|
Caviar and cheese
Forum: Off Topic
Last Post: axied12
05-28-2025, 12:38 PM
» Replies: 0
» Views: 159
|
Top-rated countertop comp...
Forum: Off Topic
Last Post: axied12
05-04-2025, 06:42 AM
» Replies: 0
» Views: 320
|
Ryanair letenky levně do ...
Forum: Off Topic
Last Post: axied12
02-11-2025, 01:37 PM
» Replies: 0
» Views: 706
|
Trusted essay writing ser...
Forum: Off Topic
Last Post: axied12
01-30-2025, 08:16 AM
» Replies: 0
» Views: 637
|
Bootverkopers - actieve j...
Forum: Off Topic
Last Post: axied12
12-07-2024, 11:07 AM
» Replies: 0
» Views: 762
|
Services for individuals ...
Forum: Off Topic
Last Post: axied12
12-02-2024, 03:31 PM
» Replies: 0
» Views: 730
|
Used excavators
Forum: Off Topic
Last Post: axied12
11-13-2024, 09:22 AM
» Replies: 0
» Views: 697
|
Buy Higo Rocket in Dubai
Forum: Off Topic
Last Post: axied12
10-25-2024, 01:09 PM
» Replies: 0
» Views: 805
|
Anime coloring pages
Forum: Off Topic
Last Post: axied12
10-13-2024, 05:10 PM
» Replies: 0
» Views: 850
|
|
|
How Music and Instruments Began? |
Posted by: vjfd26wds - 08-23-2021, 02:34 AM - Forum: Welcomes and Introductions
- No Replies
|
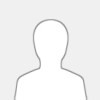 |
Music must first be defined and distinguished from speech, and from animal and bird cries. We discuss the stages of hominid anatomy that permit music to be perceived and created, with the likelihood of both Homo neanderthalensis and Homo sapiens both being capable. The earlier hominid ability to emit sounds of variable pitch with some meaning shows that music at its simplest level must have predated speech. The possibilities of anthropoid motor impulse suggest that rhythm may have preceded melody, though full control of rhythm may well not have come any earlier than the perception of music above. There are four evident purposes for music: dance, ritual, entertainment personal, and communal, and above all social cohesion, again on both personal and communal levels. We then proceed to how outdoor musical instrument began, with a brief survey of the surviving examples from the Mousterian period onward, including the possible Neanderthal evidence and the extent to which they showed “artistic” potential in other fields. We warn that our performance on replicas of surviving instruments may bear little or no resemblance to that of the original players. We continue with how later instruments, strings, and skin-drums began and developed into instruments we know in worldwide cultures today. The sound of music is then discussed, scales and intervals, and the lack of any consistency of consonant tonality around the world. This is followed by iconographic evidence of the instruments of later antiquity into the European Middle Ages, and finally, the history of public performance, again from the possibilities of early humanity into more modern times. This paper draws the ethnomusicological perspective on the entire development of music, instruments, and performance, from the times of H. neanderthalensis and H. sapiens into those of modern musical history, and it is written with the deliberate intention of informing readers who are without special education in music, and providing necessary information for inquiries into the origin of music by cognitive scientists.
But even those elementary questions are a step too far, because first we have to ask “What is music?” and this is a question that is almost impossible to answer. Your idea of music may be very different from mine, and our next-door neighbor’s will almost certainly be different again. Each of us can only answer for ourselves.
Mine is that it is “Sound that conveys emotion.”
We can probably most of us agree that it is sound; yes, silence is a part of that sound, but can there be any music without sound of some sort? For me, that sound has to do something—it cannot just be random noises meaning nothing. There must be some purpose to it, so I use the phrase “that conveys emotion.” What that emotion may be is largely irrelevant to the definition; there is an infinite range of possibilities. An obvious one is pleasure. But equally another could be fear or revulsion.
How do we distinguish that sound from speech, for speech can also convey emotion? It would seem that musical sound must have some sort of controlled variation of pitch, controlled because speech can also vary in pitch, especially when under overt emotion. So music should also have some element of rhythm, at least of pattern. But so has the recital of a sonnet, and this is why I said above that the question of “What is music?” is impossible to answer. Perhaps the answer is that each of us in our own way can say “Yes, this is music,” and “No, that is speech.”
Must the sound be organized? I have thought that it must be, and yet an unorganized series of sounds can create a sense of fear or of warning. Here, again, I must insert a personal explanation: I am what is called an ethno-organologist; my work is the study of musical tubular musical instrument (organology) and worldwide (hence the ethno-, as in ethnomusicology, the study of music worldwide). So to take just one example of an instrument, the ratchet or rattle, a blade, usually of wood, striking against the teeth of a cogwheel as the blade rotates round the handle that holds the cogwheel. This instrument is used by crowds at sporting matches of all sorts; it is used by farmers to scare the birds from the crops; it was and still is used by the Roman Catholic church in Holy Week when the bells “go to Rome to be blessed” (they do not of course actually go but they are silenced for that week); it was scored by Beethoven to represent musketry in his so-called Battle Symphony, a work more formally called Wellingtons Sieg oder die Schlacht bei Vittoria, Op.91, that was written originally for Maelzel’s giant musical box, the Panharmonicon. Beethoven also scored it out for live performance by orchestras and it is now often heard in our concert halls “with cannon and mortar effects” to attract people to popular concerts. And it was also, during the Second World War, used in Britain by Air-Raid Precaution wardens to warn of a gas attack, thus producing an emotion of fear. If it was scored by Beethoven, it must be regarded as a musical instrument, and there are many other noise-makers that, like it, which must be regarded as musical instruments.
And so, to return to our definition of music, organization may be regarded as desirable for musical sound, but that it cannot be deemed essential, and thus my definition remains “Sound that conveys emotion.”
But then another question arises: is music only ours? We can, I think, now agree that two elements of music are melody, i.e., variation of pitch, plus rhythmic impulse. But almost all animals can produce sounds that vary in pitch, and every animal has a heart beat. Can we regard bird song as music? It certainly conveys musical pleasure for us, it is copied musically (Beethoven again, in his Pastoral Symphony, no.6, op. 68, and in many works by other composers), and it conveys distinct signals for that bird and for other birds and, as a warning, for other animals also. Animal cries also convey signals, and both birds and animals have been observed moving apparently rhythmically. But here, we, as musicologists and ethnomusicologists alike, are generally agreed to ignore bird song, animal cries, and rhythmic movement as music even if, later, we may regard it as important when we are discussing origins below. We ignore these sounds, partly because they seem only to be signals, for example alarms etc, or “this is my territory,” and partly, although they are frequently parts of a mating display, this does not seem to impinge on society as a whole, a feature that, as we shall see, can be of prime importance in human music. Perhaps, too, we should admit to a prejudice: that we are human and animals are not…
So now, we can turn to the questions of vocalization versus motor impulse: which came first, singing or percussive rhythms? At least we can have no doubt whatsoever that for melody, singing must long have preceded instrumental performance, but did physical movement have the accompaniment of hand- or body-clapping and perhaps its amplification with clappers of sticks or stones, and which of them came first?
Here, we turn first to the study of the potentials of the human body. There is a large literature on this, but it has recently been summarized by Iain Morley in his The Prehistory of Music (Morley, 2013). So far as vocalization is concerned, at what point in our evolution was the vocal tract able to control the production of a range of musical pitch? For although my initial definition of music did not include the question of pitch, nor of rhythm, once we begin to discuss and amplify our ideas of music, one or other of these, does seem to be an essential—a single sound with no variation of pitch nor with any variation in time can hardly be described as musical.
All animals have the ability to produce sounds, and most of these sounds have meanings, at least to their ears. Surely, this is true also of the earliest hominims. If a mother emits sounds to soothe a baby, and if such sound inflects somewhat in pitch, however vaguely, is this song? An ethnomusicologist, those who study the music of exotic peoples, would probably say “yes,” while trying to analyze and record the pitches concerned. A biologist would also regard mother–infant vocalizations as prototypical of music (Fitch, 2006). There are peoples (or have been before the ever-contaminating influence of the electronic profusion of musical reproduction) whose music has consisted only of two or three pitches, and those pitches not always consistent, and these have always been accepted as music by ethnomusicologists. So we have to admit that vocal music of some sort may have existed from the earliest traces of humanity, long before the proper anatomical and physiological developments enabled the use of both speech and what we might call “music proper,” with control and appreciation of pitch.
In this context, it is clear also that “music” in this earliest form must surely have preceded speech. The ability to produce something melodic, a murmuration of sound, something between humming and crooning to a baby, must have long preceded the ability to form the consonants and vowels that are the essential constituents of speech. A meaning, yes: “Mama looks after you, darling,” “Oy, look out!” and other non-verbal signals convey meaning, but they are not speech.
The possibilities of motor impulse are also complex. Here, again, we need to look at the animal kingdom. Both animals and birds have been observed making movements that, if they were humans, would certainly be described as dance, especially for courtship, but also, with the higher apes in groups. Accompaniment for the latter can include foot-slapping, making more sound than is necessary just for locomotion, and also body-slapping (Williams, 1967). Can we regard such sounds as music? If they were humans, yes without doubt. So how far back in the evolutionary tree can we suggest that motor impulse and its sonorous accompaniment might go? I have already postulated in my Origins and Development of xylophone musical instrument (Montagu, 2007, p. 1) that this could go back as far as the earliest flint tools, that striking two stones together as a rhythmic accompaniment to movement might have produced the first flakes that were used as tools, or alternatively that interaction between two or more flint-knappers may have led to rhythms and counter-rhythms, such as we still hear between smiths and mortar-and-pestle millers of grains and coffee beans. This, of course, was kite-flying rather than a wholly serious suggestion, but the possibilities remain. At what stage did a hominim realize that it could make more sound, or could alleviate painful palms, by striking two sticks or stones together, rather than by simple clapping? Again we turn to Morley and to the capability of the physiological and neurological expression of rhythm.
The physiological must be presumed from the above animal observations. The neurological would again, at its simplest, seem to be pre-human. There is plenty of evidence for gorillas drumming their chests and for chimpanzees to move rhythmically in groups. However, apes’ capacity for keeping steady rhythm is very limited (Geissmann, 2000), suggesting that it constitutes a later evolutionary development in hominins. Perceptions of more detailed appreciation of rhythm, particularly of rhythmic variation, can only be hypothesized by studies of modern humans, especially of course of infantile behavior and perception.
From all this, it would seem that motor impulse, leading to rhythmic music and to dance could be at least as early as the simplest vocal inflection of sounds. Indeed, it could be earlier. We said above that animals have hearts, and certainly, all anthropoids have a heartbeat slow enough, and perceptible enough, to form some basis for rhythmic movement at a reasonable speed. Could this have been a basis for rhythmic movement such as we have just mentioned? This can only be a hypothesis, for there is no way to check it, but it does seem to me that almost all creatures seem to have an innate tendency to move together in the same rhythm when moving in groups, and this without any audible signal, so that some form of rhythmic movement may have preceded vocalization.
But Why Does Music Develop from Such Beginnings? What is the Purpose of Music?
There are four obvious purposes: dance, personal or communal entertainment, communication, and ritual.
Seemingly more important than these fairly obvious reasons for why music developed is one for why music began in the first place. This is something that Steven Mithen mentions again and again in his book, The Singing Neanderthals (Mithen, 2005): that music is not only cohesive on society but almost adhesive. Music leads to bonding, bonding between mother and child, bonding between groups who are working together or who are together for any other purpose. Work songs are a cohesive element in most pre-industrial societies, for they mean that everyone of the group moves together and thus increases the force of their work. Even today “Music while you Work” has a strong element of keeping workers happy when doing repetitive and otherwise boring work. Dancing or singing together before a hunt or warfare binds the participants into a cohesive group, and we all know how walking or marching in step helps to keep one going. It is even suggested that it was music, in causing such bonding, that created not only the family but society itself, bringing individuals together who might otherwise have led solitary lives, scattered at random over the landscape.
Thus, it may be that the whole purpose of music was cohesion, cohesion between parent and child, cohesion between father and mother, cohesion between one family and the next, and thus the creation of the whole organization of society.
Much of this above can only be theoretical—we know of much of its existence in our own time but we have no way of estimating its antiquity other than by the often-derided “evidence” of the anthropological records of isolated, pre-literate peoples. So let us now turn to the hard evidence of early musical practice, that of the surviving musical instruments.1
This can only be comparatively late in time, for it would seem to be obvious that sound makers of soft vegetal origin should have preceded those of harder materials that are more difficult to work, whereas it is only the hard materials that can survive through the millennia. Surely natural materials such as grasses, reeds, and wood preceded bone? That this is so is strongly supported by the advanced state of many early bone pipes—the makers clearly knew exactly what they were doing in making musical instruments, with years or generations of experiment behind them on the softer materials. For example, some end-blown and notch-blown flutes, the earliest undoubted ones that we have, from Geissenklösterle and Hohle Fels in Swabia, Germany, made from swan, vulture wing (radius) bones, and ivory in the earliest Aurignacian period (between 43,000 and 39,000 years BP), have their fingerholes recessed by thinning an area around the hole to ensure an airtight seal when the finger closes them. This can only be the result of long experience of flute making.
So how did tembos musical instrument begin? First a warning: with archeological material, we have what has been found; we do not have what has not been found. A site can be found and excavated, but if another site has not been found, then it will not have been excavated. Thus, absence of material does not mean that it did not exist, only that it has not been found yet. Geography is relevant too. Archeology has been a much older science in Europe than elsewhere, so that most of our evidence is European, whereas in Africa, where all species of Homo seem to have originated, site archeology is in its infancy. Also, we have much evidence of bone pipes simply because a piece of bone with a number of holes along its length is fairly obviously a probable musical instrument, whereas how can we tell whether some bone tubes without fingerholes might have been held together as panpipes? Or whether a number of pieces of bone found together might or might not have been struck together as idiophones? We shall find one complex of these later on here which certainly were instruments. And what about bullroarers, those blades of bone, with a hole or a constriction at one end for a cord, which were whirled around the player’s head to create a noise-like thunder or the bellowing of a bull, or if small and whirled faster sounded like the scream of a devil? We have many such bones, but how many were bullroarers, how many were used for some other purpose?
So how did pipes begin? Did someone hear the wind whistle over the top of a broken reed and then try to emulate that sound with his own breath? Did he or his successors eventually realize that a shorter piece of reed produced a higher pitch and a longer segment a lower one? Did he ever combine these into a group of tubes, either disjunctly, each played by a separate player, as among the Venda of South Africa and in Lithuania, or conjointly lashed together to form a panpipe for a single player? Did, over the generations, someone find that these grouped pipes could be replaced with a single tube by boring holes in it, with each hole representing the length of one of that group? All this is speculation, of course, but something like it must have happened.
Or were instruments first made to imitate cries? The idea of the hunting lure, the device to imitate an animal’s cry and so lure it within reach, is of unknown age. Or were they first made to imitate the animal in a ritual to call for the success of tomorrow’s hunt? Some cries can be imitated by the mouth; others need a tool, a short piece of cane, bits of reed or grass or bone blown across the end like a key or a pen-top. Others are made from a piece of bark held between the tongue and the lip (I have heard a credit card used in this way!). The piece of cane or bone would only produce a single sound, but the bark, or in Romania a carp scale, can produce the most beautiful music as well as being used as a hunting call. The softer materials will not have survived and with the many small segments of bone that we have, there is no way to tell whether they might have been used in this way or whether they are merely the detritus from the dining table.
This bone does raise the whole question of whether H. neanderthalensis knew of or practised music in any form. For rhythm, we can only say surely, as above—if earlier hominids could have, so could H. neanderthalensis. Could they have sung? A critical anatomical feature is the position of the larynx (Morley, 2013, 135ff); the lower the larynx in the throat the longer the vocal cords and thus the greater flexibility of pitch variation and of vowel sounds (to put it at its simplest). It would seem to have been that with H. heidelbergensis and its successors that the larynx was lower and thus that singing, as distinct from humming, could have been possible, but “seems to have been” is necessary because, as is so often, this is still the subject of controversy. However, it does seem fairly clear that H. neanderthalensis could indeed have sung. It follows, too, that while the Divje Babe “pipe” may or may not have been an instrument, others may yet be found that were ensemble musical instrument. There is evidence that the Neanderthals had at least artistic sensibilities, for there are bones with scratch marks on them that may have been some form of art, and certainly there is a number of small pierced objects, pieces of shell, animal teeth, and so forth, found in various excavations that can only have served as beads for a necklace or other ornamentation – or just possibly as rattles. There have also been found pieces of pigments of various colors, some of them showing wear marks and thus that they had been used to color something, and at least one that had been shaped into the form of a crayon, indicating that some reasonably delicate pigmentation had been desired. Burials have been found, with some small deposits of grave goods, though whether these reveal sensibilities or forms of ritual or belief, we cannot know (D’Errico et al., 2003, 19ff). There have also been found many bone awls, including some very delicate ones which, we may presume, had been used to pierce skins so that they could be sewn together. All this leads us to the conclusion that the Neanderthals had at least some artistic and other feelings, were capable of some musical practices, even if only vocal, and were clothed, rather than being the grunting, naked savages that have been assumed in the past.
|
|
|
What is velvet fabric? |
Posted by: vjfd26wds - 08-23-2021, 02:29 AM - Forum: Welcomes and Introductions
- No Replies
|
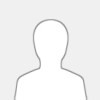 |
Velvet is a sleek, soft fabric that is commonly used in intimate garments, upholstery and other textile applications. Due to how expensive it was to produce velvet textiles in the past, this fabric is often associated with the aristocracy. Even though most types of modern velvet are adulterated with cheap synthetic materials, this unique fabric remains one of the sleekest, softest man-made materials ever engineered.
The first recorded mention of velvet fabric is from the 14th century, and scholars of the past mostly believed that this textile was originally produced in East Asia before making its way down the Silk Road into Europe. Traditional forms of velvet were made with pure silk, which made them incredibly popular. Asian silk was already very soft, but the unique production processes used to make velvet result in a material that’s even more sumptuous and luxurious than other silk products.
Until velvet gained popularity in Europe during the Renaissance, this fabric was commonly used in the Middle East. The records of many civilizations located within the borders of in modern Iraq and Iran, for instance, indicate that velvet was a favorite fabric among the royalty the region.
When machine looms were invented, velvet production became much less expensive, and the development of synthetic fabrics that somewhat approximate the properties of silk finally brought the wonders of velvet to even the lowest rungs of society. While today’s velvet may not be as pure or exotic as the velvet of the past, it remains prized as a material for curtains, blankets, stuffed animals, and all manner of other products that are supposed to be as soft and cuddly as possible.
While various materials can be used to make velvet, the process used to produce this burnout velvet fabric is the same regardless of which base textile is used. Velvet can only be woven on a unique type of loom that spins two layers of fabric simultaneously. These fabric layers are then separated, and they are wound up on rolls.
Velvet is made with vertical yarn, and velveteen is made with horizontal yarn, but otherwise, these two textiles are made with largely the same processes. Velveteen, however, is often mixed with normal cotton yarn, which reduces its quality and changes its texture.
Silk, one of the most popular velvet materials, is made by unraveling the cocoons of silkworms and spinning these threads into yarn. Synthetic textiles such as rayon are made by rendering petrochemicals into filaments. Once one of these yarn types is woven into velvet cloth, it can be dyed or treated depending on the intended application.
The main desirable attribute of velvet is its softness, so this textile is primarily used in applications in which fabric is placed close to the skin. At the same time, velvet also has a distinctive visual allure, so it’s commonly used in home decor in applications such as curtains and throw pillows. Unlike some other interior decor items, velvet feels as good as it looks, which makes this fabric a multi-sensory home design experience.
Due to its softness, velvet is sometimes used in bedding. In particular, this fabric is commonly used in the insulative blankets that are placed between sheets and duvets. Velvet is much more prevalent in womenswear than it is in clothing for men, and it is often used to accentuate womanly curves and create stunning eveningwear. Some stiff forms of velvet are used to make hats, and this material is popular in glove linings.
China leads the world as the most prolific producer of synthetic textiles. These and other reckless industrial practices have rapidly made this communist nation the world’s largest polluter as well, and China is lagging far behind the rest of the world’s gradual switch to sustainable fabrics and non-polluting production processes.
Since “velvet” refers to a fabric weave instead of a material, it can’t technically be said that velvet as a concept has any impact on the environment. The different materials used to make velvet, however, have varying degrees of environmental impact that should be carefully considered.
Environmental impact of silk
Silk is the closest thing we have to an ideal fabric from an environmental standpoint. This embossed velvet fabric is still, in most cases, produced the same way it has been produced for thousands of years, and since the production of silk is not aided by any pesticides, fertilizers, or other toxic substances, making this fabric does not have any significant negative environmental impact.
Environmental impact of rayon and other synthetic textiles
Rayon is the most commonly used substitute for silk in velvet and velvet-inspired fabrics, and the production of this synthetic substance is significantly harmful to the environment. The rayon production process involves multiple chemical washes, and the base material of this substance is petroleum.
Essentially, rayon is non-biodegradable fossil fuel product that introduces tons of harmful chemicals into the water supply as it is created. With these detractors in full view, the only reason that rayon is still produced is that it is inexpensive.
The term “velvety” means soft, and it takes its meaning from its namesake fabric: velvet. The soft, smooth fabric epitomizes luxury, with its smooth nap and shiny appearance. Velvet has been a fixture of fashion design and home decor for years, and its high-end feel and appearance make it an ideal textile for elevated design.
Velvet is a soft, luxurious fabric that is characterized by a dense pile of evenly cut fibers that have a smooth nap. Velvet has a beautiful drape and a unique soft and shiny appearance due to the characteristics of the short pile fibers.
Velvet fabric is popular for evening wear and dresses for special occasions, as the jaguar velvet fabric was initially made from silk. Cotton, linen, wool, mohair, and synthetic fibers can also be used to make velvet, making velvet less expensive and incorporated into daily-wear clothes. Velvet is also a fixture of home decor, where it’s used as upholstery fabric, curtains, pillows, and more.
The first velvets were made from silk and, as such, were incredibly expensive and only accessible by the royal and noble classes. The material was first introduced in Baghdad, around 750 A.D., but production eventually spread to the Mediterranean and the fabric was distributed throughout Europe.
New loom technology lowered the cost of production during the Renaissance. During this period, Florence, Italy became the dominant velvet production center.
Velvet is made on a special loom known as a double cloth, which produces two pieces of velvet simultaneously. Velvet is characterized by its even pile height, which is usually less than half a centimeter.
Velvet today is usually made from synthetic and natural fibers, but it was originally made from silk. Pure silk velvet is rare today, as it’s extremely expensive. Most velvet that is marketed as silk velvet combines both silk and rayon. Synthetic velvet can be made from polyester, nylon, viscose, or rayon.
There are several different Holland velvet fabric types, as the fabric can be woven from a variety of different materials using a variety of methods.
Crushed velvet. As the name suggests, crushed velvet has a “crushed” look that is achieved by twisting the fabric while wet or by pressing the pile in different directions. The appearance is patterned and shiny, and the material has a unique texture.
Panne velvet. Panne velvet is a type of crushed velvet for which heavy pressure is applied to the material to push the pile in one direction. The same pattern can appear in knit fabrics like velour, which is usually made from polyester and is not true velvet.
Embossed velvet. Embossed velvet is a printed fabric created via a heat stamp, which is used to apply pressure to velvet, pushing down the piles to create a pattern. Embossed velvet is popular in upholstery velvet materials, which are used in home decor and design.
Ciselé. This type of patterned velvet is created by cutting some looped threads and leaving others uncut.
Plain velvet. Plain velvet is usually a cotton velvet. It is heavy with very little stretch and doesn’t have the shine that velvet made from silk or synthetic fibers has.
Stretch velvet. Stretch velvet has spandex incorporated in the weave which makes the material more flexible and stretchy.
Pile-on-pile velvet. This type of velvet has piles of varying lengths that create a pattern. Velvet upholstery fabric usually contains this type of velvet.
Velvet, velveteen, and velour are all soft, drapey fabrics, but they differ in terms of weave and composition.
Velour is a knitted fabric made from cotton and polyester that resembles velvet. It has more stretch than velvet and is great for dance and sports clothes, particularly leotards and tracksuits.
Velveteen pile is much shorter pile than velvet pile, and instead of creating the pile from the vertical warp threads, velveteens pile comes from the horizontal weft threads. Velveteen is heavier and has less shine and drape than velvet, which is softer and smoother.
For budding fashion designers, understanding the characteristics and feel of different fabrics is key. In her 20s, Diane von Furstenberg convinced a textile factory owner in Italy to let her produce her first designs. With those samples, she flew to New York City to build one of the world’s most iconic and enduring fashion brands. In her fashion design MasterClass, Diane explains how to create a visual identity, stay true to your vision, and launch your product.
Become a better fashion designer with the MasterClass Annual Membership. Gain access to exclusive video lessons taught by fashion design masters including Marc Jacobs, Diane von Furstenberg, and more.
|
|
|
Roll forming of a high strength aluminum tube |
Posted by: vjfd26wds - 08-23-2021, 02:26 AM - Forum: Welcomes and Introductions
- No Replies
|
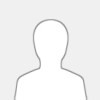 |
The presented paper provides a modelling strategy for roll forming of a high strength aluminum alloy tube. Roll forming allows the cost-effective production of large quantities of long profiles. Forming of high strength aluminum brings challenges like high springback and poor formability due to the low Young’s modulus, low ductility and high yield strength. Forming processes with high strength aluminum, such as the AA7075 alloy, therefore require a detailed process design. Three different forming strategies, one double radius strategy and two W-forming strategies are discussed in the paper. The paper addresses the question whether common roll forming strategies are appropriate for the challenge of roll forming of a high strength aluminum micro channel tube. For this purpose, different forming strategies are investigated numerically regarding buckling, longitudinal strain distribution and final geometry. While geometry is quite the same for all strategies, buckling and strain distribution differ with every strategy. The result of the numerical investigation is an open tube that can be welded into a closed tube in a subsequent step. Finally, roll forming experiments are conducted and compared with the numerical results.Current research in production technology focuses primarily on increasing resource efficiency and thus follows the approach of fundamental sustainability of processes and products. High strength aluminum alloys (e.g. AA7075) are commonly used in aerospace applications in spite of their high cost of about 5 €/kg and poor formability [1]. Due to ambitious legal requirements, such as the CO2 target in automotive engineering, new lightweight construction concepts are still needed [2]. An excellent basis is offered by the production of high strength AA7075 thin walled tubes as semi-finished products by roll forming. These can be further processed in subsequent customized processes such as welding, stamping, cutting or rotary swaging.
According to DIN 8586, roll forming is a bending technology with rotating tool motion to produce open and closed profiles [3]. Several pairs of forming rolls are aligned one behind the other for the forming process. The friction between the rotating forming rolls and the sheet metal causes a forward movement of the sheet. Simultaneously the sheet is formed in and between the stations. For the production of large quantities, roll forming is a cost-effective manufacturing process, compared to tube extrusion or tube drawing. Roll forming can also be competitive for smaller quantities, if the number of forming passes is small enough [4]. The incremental nature of the roll forming process also allows forming of high strength materials, such as ultra high strength steel (UHSS) [5].
During roll forming there is a limit for the amount of deformation regarding buckling limit strain (BLS), which can be reached in one forming station [6]. Abeyrathna [5], Park [7] and Bui [8] showed that longitudinal strain has a major impact on product defects, such as bow or buckling. The maximum longitudinal strain occurs in the area of the band edge. Plastic elongation in the roll gap between the forming rolls followed by compression when the sheet leaves the forming rolls leads to buckling. Figure 1 illustrates the elongation, followed by compression when forming a tube. To prevent buckling, the maximum longitudinal strain must be low. Once buckling takes place, welding of the formed tube becomes very difficult or even impossible [9]. Parameters with a large influence on buckling are the stiffness of the sheet and the yield strength of the material. According to Halmos [10], elongation of the band edge depends on the flange height and inter-station distance ld. High bending angles of a single forming station Θp and a small inter-station distance ld lead to large elongation of the band edge and thus to buckling. For circular sections (e.g. tube), the BLS is 5–10 times higher than the BLS for a U-profile [6].Groche et al. [11], Park et al. [7], Zou et al. [12] and Lee et al. [13] showed that roll forming of high strength materials and especially of high strength aluminum drawn tube brings challenges compared to commonly roll formed steel grades. High strength leads to high springback and thus to less dimensional accuracy in the processed part. Parameters, which have an influence on springback are shown in Table 1. Difficulties regarding aluminum include early fracture due to low ductility, higher springback and redundant deformation. This requires a well-designed forming strategy in order to get the lowest possible springback and buckling in the roll forming process and the best quality of the processed part. In contrast, aluminum shows a good-natured behavior with regard to buckling due to a higher value of BLS compared to steel [14].The single radius-forming strategy has the advantage to form tubes with different sheet thickness on the same tool. A flower pattern with constant bending radius over the entire cross-section of the sheet is characteristic for the single radius-forming. For high-strength materials, the single radius-forming strategy is not applicable due to high springback caused by the high elastic bending content [10, 18].
The double radius- and W-forming strategies are appropriate for high strength steels. For both strategies, two radii are combined in each pass, whereby the radius in the edge area is equal to the end radius already in the first pass of the process [18]. In contrast to double radius forming, a negative bending is initially introduced in the middle section in the W-forming process. The main advantage of this strategy is that the final radius can be formed into the band edge area at the first pass of the process [18]. Another approach is described by Jiang et al. [19] with a cage roll forming mill for the production of electric resistance welded pipes.
The height displacement of the profile is called “up-hill” or “down-hill”. During the down-hill strategy, the profile is lowered step by step in each pass. The use of a down-hill forming strategy can reduce plastic elongation in the band edge and thus the number of forming stations [10]. Based on the fundamental differences in roll forming between aluminum and steel, this publication addresses the question if one of the strategies suits for forming a tube of the high-strength aluminum alloy AA7075.
FE-Simulation of the roll forming process
The roll forming tools are designed by numerical simulation of the process. The target geometry is a tube with an outer diameter of d=54.98mm (ro=27,49mm/ri=25,99mm) and a wall thickness of s0=1.5mm. An AA7075-T6 aluminum alloy is used for the roll forming process. Table 2 shows the mechanical properties of the alloy.The first forming strategy suggested automatically by UBECO Profil after defining the target geometry is a double radius-forming strategy and has 27 passes in total. Based on tube forming sequences in literature [15, 16], the number of passes is reduced to 14 passes by skipping every second pass, in order to increase process efficiency. After the reduction to 14 passes, the edge strain is still below the critical limit in every stage of the process according to the PSA. The approach for the first forming strategy is to form the tube in uniform increments and to keep the longitudinal strain low in the band edge. The further approach is to calculate the stresses of the formed tube to arrive at the number of passes required. Forming strategy 2R is the first strategy numerically investigated by the FE-software Marc Mentat.In this paper, roll forming of a high strength extruded aluminum tube is investigated. Due to the difficult determination of the design parameters, roll forming of high strength aluminum is a challenge. Conventional roll forming strategies quickly reach their limits when forming aluminum or high strength steels. To form a tube out of high-strength aluminum alloys such as AA7075, a W-forming strategy is recommended. Another positive influence is the application of a down-hill strategy. The investigations have shown that an efficient roll forming production line for high strength aluminum tubes can be set up even with a small number of forming passes. The W-forming strategies showed a good behavior with regard to buckling, compared to the double radius forming strategy. Forming strategy W2 combines the advantages of few passes with a good final part geometry thanks to detailed process design. The numerical investigation and the following experiments demonstrated the feasibility of roll forming a high-strength aluminum tube. It is shown that conventional design methods are also valid for high-strength materials.A further result of the numerical investigation is that the design of the tools should not be based on longitudinal strain in the band edge alone. For a first estimation, the elongation of the band edge is a valid factor, but for an exact process design a numerical simulation should always be performed. In addition, BLS is material dependent, which makes an analytical calculation even more difficult.
Regarding the springback angle, the experimental investigations show little deviations from the FE-model. The reasons for this are the simplified material model, which does not consider combined hardening effects, the influence of the smaller modulus of elasticity after plastic deformation and compliance of the forming stand. Nevertheless, the simplified FE-model provides sufficiently accurate results regarding buckling and geometry of the tube.
Axial crash of thin-walled circular seamless aluminum tube is investigated in this study. These kinds of tubes usually are used in automobile and train structures to absorb the impact energy. An explicit finite element method (FEM) is used to model and analyse the behaviour. Formulation of the energy absorption and the mean crash force in the range of variables is presented using design of experiments (DOE) and response surface method (RSM). Comparison with experimental tests has been accomplished in some results for validation. Also, comparison with the analytical aspect of this problem has been done. Mean crash force has been considered as a constraint as its value is directly related to the crash severity and occupant injury. The results show that the triggering causes a decrease in the maximum force level during crash.
|
|
|
Vacuum contactor operation with parallel connection of independent consumers |
Posted by: kow65d - 08-20-2021, 06:52 AM - Forum: Welcomes and Introductions
- No Replies
|
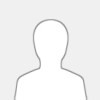 |
This work presents a model of a transformer substation with parallel connection of independent consumers via vacuum switches. Several options of an electric arc model are considered upon switching off a vacuum switch such as: KEMA model and "black box" model. Modern computer models of vacuum switches were analyzed. Since the model data were not suitable for the conditions of the experiment, a simulation computer model was developed that reflects the specifics of the operation of the substation and of the transition process upon disconnection of one or several vacuum switches. The results of the developed methodology of analyzing transition processes were verified. To check the results of computer simulation, an experimental model was constructed, it consisted of: an electric load (inductive nature), a power supply, two vacuum switches, and a measuring circuit. The circuit is switched on and off using a pneumatic system controlled by a microcontroller. The primary purpose of the work is to check mutual influence of vacuum switches upon parallel disconnection, since there may be a restrike caused by effects of switching overvoltage between neighboring switches upon irregular disconnection. The effects of a transition process in one switch on the total current of the entire system were identified. A stand for a projected trial was demonstrated as well.
With continuing development of science and technology, high voltage electrical equipment performance has been improved very fast, and dashed out some of the new switch gear, for example, the F-C circuit. Through understanding and analyzing the principle, characteristic and function, etc of F-C circuit , describes its advantages in some areas relative to the circuit breaker, For example, the protection of a more timely, overvoltage lower, functions in line with more reasonable; the lower cost for. Purpose is to allow engineers to correct reasonable selection of high voltage switch when used in the design and to promote domestic F-C circuit development.
The design, operation and use are characterized for high voltage vacuum contactors in underground coal mines endangered by methane and coal dust explosions. Design of a vacuum contactor is shown in a scheme. Vacuum contactors are superior to electromagnetic contactors. Vacuum contactors have a reduced size and weight and are characterized by improved commutation properties. Under vacuum conditions, intensity of electric discharges is lower than in an electromagnetic contactor. Reliability of vacuum contactors is 16 to 20 times higher than that of electromagnetic contactors (90% of metal vapors caused by an electric arc settle on contact surface). No time consuming buildup removal or cleaning is necessary. Optimizing contactor position in a power system in underground mines is discussed. Efficiency of using vacuum contactors and the RC systems is discussed.
Vacuum contactor is an electrically controlled switch that is used to make or break an electrical circuit with the help of vacuum interrupter, relay, and fuse. The drivers of the this market are influenced by the trends in the commercial sector and by the trends in the process and manufacturing industry. Growth in the related as well as complementary markets, such as motors, capacitors, switchgear, and transformer, also contribute towards the growth of vacuum contactors.
The global vacuum contactor market size is estimated to reach $4,814.6 Million by 2020 from $3,426.8 Million in 2015. Vacuum contactor is an electrically controlled switch that is used to make or break an electrical circuit with the help of vacuum interrupter, relay and fuse. It is mainly found in motor starters, switchgear and control gear of medium voltage fast switching devices. The drivers of the high voltage vacuum contactormarket are influenced by the trends in the process industries, manufacturing industries, commercial and large residential sectors that use HVAC systems.
This market study covers medium voltage vacuum contactors of various voltage ratings, applications, and end-users for arriving at the global market size from 2013 to 2020. In terms of voltage rating, the vacuum contactor market is segmented into four divisions: less than 5kV, 5-10 kV, 10-15 kV and more than 15kV.
On the basis of application the vacuum contactors market is classified into six segments: motors, transformers, capacitors, reactors, resistive loads and others (such as generators, pumps, variable frequency drives, feeders, power transmitters and switchgears). Motors, transformers and capacitors are the top three applications of this industry that covers more than 65% market share.
On the basis of end-use, the vacuum contactor market is segmented into six sectors: utilities, industrial, commercial, mining, oil & gas and other medium voltage end-users. The other sector includes marine, water & waste water pumping, street lighting and transportation sector.
In terms of region, the single phase vacuum contactor is segmented on the basis of its market presence in the following regions namely North America, South America, Europe, Asia-Pacific and Middle East & Africa. These regions are further classified on the basis of top countries and their end user analyses have been made. Asia-Pacific held the largest market share owing to growth in industrialization and urbanization, followed by Europe and North America.
The global vacuum contactor market is projected to witness high growth on account of rising energy demand, growing commercial and industrial sector, and increased up-gradation of electrical infrastructure. The market was valued at $3,210 Million globally in 2014 and is projected to grow at a CAGR of 7.04% from 2015 to 2020.
The Asia-Pacific region holds a majority of market share owing to urbanization and significant development in process industries such as paper & pulp, cement, metal processing industries, and growth in manufacturing industries, followed by North America and Europe. In terms of individual countries, the U.S. and China show high growth potential. This growth can be attributed to the increasing demand for reliable power and investments for replacing aging T&D infrastructure in the U.S. and progressive economic growth of China.
Amongst the end-users, utilities sector is estimated to hold the major market share owing to increasing installation of power infrastructure. North American region is currently focussing on grid modernization and replacement of existing power infrastructure. Few countries in Europe are shifting towards renewable sources for power generation that has boosted the low voltage vacuum contactor market in the region. Vacuum contactor finds vast application in industrial and commercial sectors as well.
In terms of growth strategies, market players have mainly been forming mergers and acquisitions in order to expand as well as strengthen their market foothold. Contracts & agreements is the most commonly adopted strategy that is followed by mergers & acquisitions, and expansions. This shows a mix of both organic and inorganic growth strategies.
Leading players in the industry, based on their recent developments and other strategic industrial activities, include ABB Ltd. (Switzerland), Eaton Corporation Plc. (Ireland), Mitsubishi Electric Corporation (Japan), Schneider Electric SE (France), and Siemens AG (Germany).
With continuing development of science and technology, high voltage electrical equipment performance has been improved very fast, and dashed out some of the new switch gear, for example, the F-C circuit. Through understanding and analyzing the principle, characteristic and function, etc of F-C circuit , describes its advantages in some areas relative to the circuit breaker, For example, the protection of a more timely, overvoltage lower, functions in line with more reasonable; the lower cost for. Purpose is to allow engineers to correct reasonable selection of high voltage switch when used in the design and to promote domestic F-C circuit development.
|
|
|
What are Flight Cases? |
Posted by: kow65d - 08-20-2021, 06:50 AM - Forum: Welcomes and Introductions
- No Replies
|
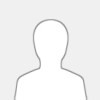 |
Flight cases, carrying cases or equipment cases are sturdy, rigid trunks or enclosures designed for protecting personal goods in transit and storage. They’re typically made from plastic or metal. Many models feature a range of additional options, like heavy-duty foam inserts or additional protective padding.
High-end transit equipment cases are widely used in a range of demanding industries and roles. This includes the avionics, transport, electronic, entertainment, photography and video, test and measurement, medical, security and military sectors, to name just a few.
Flight cases are primarily designed to shield and protect fragile or high-value items during transit. Some are specifically designed to house particular pieces of equipment or instruments. Others are more adaptable and can be used to protect almost any important goods that may otherwise be at risk of damage.
Because they’re chiefly used as a handy solution for long-distance travel, long-term storage or frequent location changes, rack flight case are also commonly known as shipping cases or transportation cases. You will sometimes see them referred to as roadie cases, as they make a popular solution for conveying musical instruments and technical equipment between different locations.Flight cases can be used to store, protect and transport a wide variety of equipment types and tools, depending on which sort of case you choose. As mentioned above, musical instruments are one of the common types of flight case hardware, but you will find all sorts of items being shipped in these robust, heavy-duty enclosures.
Flight Cases for Guitars
Flight cases for guitars are a popular choice among musicians. Many such equipment or roadie cases are specially designed to provide added protection for guitars in transit. Both acoustic and electric guitars require careful handling during shipping or air travel. Their weight, size, and relative fragility mean that they are prone to damage, and this is why protection with a quality flight case during a trip is essential.
Guitar flight cases tend to be built in such a way as to provide additional support and padding around the most vulnerable parts of the instrument. These normally include both the headstock and neck of the guitar, particularly at key joints and where cutaways on the body taper sharply.
You’ll often see flight cases intended specifically for travel with guitars that include a good deal of strong secondary bracing, packing or foam padding at these vital points. They’re usually designed to provide reliable cushioning and support around the bridge and headstock of the instrument. Additional reinforcement is sometimes focused on areas where the main sections of the head, neck and body join together.
Guitar flight cases are often made from fairly lightweight but sturdy materials, such as rigid plastic or aluminium. This generally provides a good level of overall protection, while also being more convenient to carry between locations. Cases designed for shipping multiple guitars together often include built-in racking systems. These typically come with wheels for easier manoeuvring on the ground.
Flight Cases for Guitar Amps
Just as with guitars themselves, flight cases for guitar amps are another important piece of kit for many travelling musicians and road crews.
A guitar amp flight case can come in many sizes and configurations, depending on the type and size of amp or speaker you need to pack up safely ready for shipping. Again, they tend to focus on delivering robust knock and fall protection, with heavy padding on the interior.
Like many such equipment cases, they’re often made from high-grade plastic or metals like cast aluminium. Their bodies may be ribbed for further strength and rigidity, offering an ideal combination of strength and a lighter carry weight for travel.
Additional features can include:
Sturdy comfort grip handles with increased lift capacities
Retaining straps
Toggle catches with wire seals and padlock facilities
Rubber seals for better waterproofing
Stacking locators in the lid, to help when you need to pack or store more than one crate together
Flight Cases for Drums
Flight cases for drums are also a popular choice as proper storage and transportation of drumkits is equally important. It’s particularly vital to protect drum kits in transit as their large size and hollow construction can leave them extremely vulnerable to damage if they are not properly protected.
The best drum and cymbal flight case options generally tend to include many similar features to guitar and amp lighting&speaker flight case. Look out for benefits such as watertight, airtight and crushproof certifications. These offer reassurance that the case will guard against damage from knocks or falls, water, humidity, and prolonged exposure to heat.
Additionally, some models may even offer functions such as an automatic pressure purge valve. This helps to ensure the shifting forces acting on delicate instruments during air travel remain balanced within safe limits.
Production Flight Cases
Production flight cases and equipment containers also include a wide range of products suitable for shipping important and valuable tech between locations. Common examples include mixer flight cases or sound desk flight cases.
As with all such items, you’ll usually want to look for a robust plastic or aluminium model. Rugged body reinforcement and a good amount of interior shock proofing provided by thick foam inserts are also important.
When buying flight cases for mixers, it’s vital to look out for designs offering features that directly benefit electronics in transit. Waterproof models are particularly popular for shipping mixers, PAs and other production equipment. Shop for cases with sturdier rubber seals and secure fastening/locking systems, helping to guard delicate electronics from humidity, moisture, dust and debris.
Padlock compatibility is another common feature for production flight cases. This makes the cases more secure and helps to prevent unauthorised access to the contents.
Different Flight Case Types
Flight Case Racks
A flight case rack can be extremely important when shipping multiple items together in the same crate or equipment box. Case racks may be integrated into some designs, often called rackmount flight cases. Alternatively, racks can be purchased as an additional accessory designed to fit inside an existing transit case.
Plastic or metal equipment containers featuring two or more racks are available for both larger and smaller items. These can include various types of electronic equipment, organised spaces for securing different tools, or any other fragile items that need to remain protected and separated during travel.
Quality rackmount flight cases often feature benefits such as panel-mounting capabilities for creating more robust compartments, with shock-mounted rack sleeving and suspension systems for added impact guard.
They make an ideal solution when used as a server flight case, as they’ll often allow for multiple units to be organised and shipped together. This helps you to keep track of exactly which components should be kept together. It also makes reassembly of servers and other computing or electronics arrays much easier when you reach your destination.
Lightweight Flight Cases
Since the items being stored and transported in equipment cases tend to be too large or heavy to carry easily outside of a case, the last thing you want is for the container itself to add a huge amount of bulk to the overall package.
Many of the best lightweight flight case options tend to be made from sturdy plastic or cast aluminium. These materials offer an ideal balance of strength, rigidity and durability while being easy to pick up and move around.
You may also be surprised at the manoeuvrability of some of the larger light flight cases. These also tend to be easily stackable when not in use. Some models even feature stacking locators embedded into their secure-latching lids to make the job even more straightforward.
Hard Carry Cases
Transporting delicate items like laptops or test equipment is an increasingly common necessity. In situations like this, hard carry cases are often chosen for travel with smaller individual pieces of technology or electronics equipment.
Equipment carrying cases are designed to hit the ideal middle ground between portability and protection. This type of hard carrying case tends to be constructed from lighter materials, with prominent easy-grip handles. They also commonly feature a range of additional locking, latching and security measures.
Useful features on cases in this category tend to include IP-rated rubber seals for all-round moisture and dirt protection, and various types of secure latching or locking systems. Whether you opt for a metal or plastic hard carrying case, other handy benefits might include:
Sturdy plug-in lid hinges
Stable and robust case feet
Ergonomic handle designs
High-grade foam inserts for enhanced impact protection Lcd tv flight case with wheels and castors are a popular choice due to their accessibility and ease of movement. Equipment cases with wheels tend to come in several different variants. Firstly, storage boxes with wheels added as an additional convenience tend to have smaller and potentially less sturdy castors and bearings. These are often recessed further into the body of the case, allowing for easier stacking. These models may be less suitable for wheeling over longer distances.
On the other hand, transport cases which feature more prominent wheels often cite full manoeuvrability as a key part of their overall design. This becomes increasingly important with large, heavy or bulky items.
Such models will frequently list features like heavy-duty wheels made from strong materials like polyurethane. Bearings will often be steel or reinforced with other rugged materials and may be self-oiling for smoother free-running action over a wider variety of terrains and surfaces.In addition to protecting against unwanted moisture, waterproof equipment cases also offer a fairly robust level of protection from dust and dirt ingress. When you’re looking for a waterproof hard case, paying attention to the all-important IP rating is key to finding the exact product you need for a particular job or environment. For assistance with this, you can read our comprehensive guide to IP ratings.
Once again, waterproof hard cases can be made from materials such as aluminium and plastic. Certain options are also graded for protection against chemicals, as well as against general environmental hazards such as humidity, rain, spillages and dust.
Regardless of the material you choose, among the most important things to look out for will be thick rubber seals or O-rings around openings, hinges and latches. These will allow you to maintain a watertight (and sometimes completely airtight) interior to your equipment case, even under varying pressures at different altitudes.
Similarly, some models also include automatic one-way pressure release valves. Again, this will help to keep conditions inside the trunk balanced within safe limits at all times.Small flight cases tend to be designed around both portability and protection. This means that they are normally focused on convenience and comfort during journeys, as well as being built sturdily enough to withstand various types of impact, damage or ingress.
Small carrying cases made from aluminium or rigid plastic will also commonly feature some arrangement of foam inserts or padding. This is ideal for protecting less bulky items such as electronics and tools, as well as preventing the contents from moving around too much in transit, and potentially sustaining damage from knocking against the interior of the case.
These smaller cases are less commonly found with wheels attached, as their size usually does not warrant this addition. However, they will often include sturdy feet and a full range of security measures such as latches, locks and wrist straps.Plastic flight cases are a highly popular option. This is due to the impressive combination of ruggedness and low weight offered by modern plastics and polymers. Many of the leading plastic carry cases in the UK and beyond are virtually indestructible under normal transport conditions. Plastic equipment cases offer robust protection against both knocks and impacts, as well as bringing a certain level of water and chemical resistance.
As with all flight case types, plastic equipment boxes can be bought in a wide range of configurations. Advanced IP ratings offer full guarding against moisture, humidity, dust and dirt. Many such products with higher levels of ingress protection will feature thick rubber seals and double-step latching, delivering an extremely reliable performance when closed and secured.Among the most common types of modern metal flight cases are aluminium flight cases with foam inserts. These, alongside other metal flight cases, can be found in widespread use across a huge range of industries and sectors.
Metal Equipment&tool Flight Case are available in both large and small sizes and offer a perfect solution for transporting a huge variety of delicate or high-value goods safely across long distances. Common uses include shipping fragile electronics, instruments and tools.
Lockable metal flight cases with foam padding are highly robust, often featuring reinforced or ribbed cast aluminium side and top panels for added strength. Hinged lids and secure latching mechanisms are frequently coupled with ergonomic comfort grip handles. Wheels or castors tend to be extremely sturdy and smooth-running.
You may notice that many models and types of aluminium flight case are also designed with corners made from toughened, impact-resistant plastic. Not only does this provide extra protection during travel, but it also allows for easier stacking, so you can reduce the amount of storage space needed.
As with all flight cases, metal versions typically include removable PE foam inserts around the walls, base and lid for advanced protection against damage.
|
|
|
Numerical Study of Aeroacoustic Sound on Performance of Bladeless Fan |
Posted by: kow65d - 08-20-2021, 06:47 AM - Forum: Welcomes and Introductions
- No Replies
|
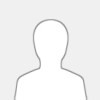 |
Aeroacoustic performance of fans is essential due to their widespread application. Therefore, the original aim of this paper is to evaluate the generated noise owing to different geometric parameters. In current study, effect of five geometric parameters was investigated on well performance of a Bladeless fan. Airflow through this fan was analyzed simulating a Bladeless fan within a 2 m×2 m×4 m room. Analysis of the flow field inside the fan and evaluating its performance were obtained by solving conservations of mass and momentum equations for aerodynamic investigations and FW-H noise equations for aeroacoustic analysis. In order to design table bladeless fan Eppler 473 airfoil profile was used as the cross section of this fan. Five distinct parameters, namely height of cross section of the fan, outlet angle of the flow relative to the fan axis, thickness of airflow outlet slit, hydraulic diameter and aspect ratio for circular and quadratic cross sections were considered. Validating acoustic code results, we compared numerical solution of FW-H noise equations for NACA0012 with experimental results. FW-H model was selected to predict the noise generated by the Bladeless fan as the numerical results indicated a good agreement with experimental ones for NACA0012. To validate 3-D numerical results, the experimental results of a round jet showed good agreement with those simulation data. In order to indicate the effect of each mentioned parameter on the fan performance, SPL and OASPL diagrams were illustrated.
Nowadays, the axial and radial fans are employed for various applications, such as cooling systems, air conditioning, ventilation of underground spaces, etc. The aeroacoustic performance of fans have been improved by increasing advancements in the computational fluid dynamics (CFD) and economic growth, then different types of fans with various applications and higher efficiency is offered. In 2009, a new fan was invented that its appearance and performance was different from conventional fans. The main differences of this fan with respect to conventional fans (axial and radial fans) are the multiplying intake air flow and lack of observable impeller [1]. This fan namely Bladeless/Air Multiplier fan was named on the basis of the two mentioned features. Until now, this fan is manufactured for domestic applications by diameter of 30 cm.
There are two typical fans widely used: axial and radial types, however Bladeless fans are completely distinct from those fans in mechanism aspect. Bladeless fan is similar to centrifugal fans in terms of radial impellers for intake air and also it is similar to axial fans in terms of preparing higher rate of outlet airflow. Although studies about wall and table bladeless fan are rare in the literature, numerous experimental and numerical studies have been performed on the axial and centrifugal fans. Lin, et al [2], designed a Forward–Curved (FC) centrifugal fan by numerical simulation and experimental tests. They selected NACA 0012 airfoil profile for its blade and indicated that this fan produces a higher maximum flow rate and static efficiency when the blade inlet angle is 16.5º. The influence of enlarged impeller on performance of a centrifugal fan was experimentally examined by Chunxi, et al [3]. By comparison of obtained results, they observed that flow rate, total pressure rise, shaft power and sound pressure level increased while the efficiency of fan decreased for larger blades. Govardhan, et al [4], investigated the flow field in a cross flow fan by three-dimensional simulation via the commercial software code, CFX. They simulated three impeller geometries for different radius ratio and blade angles, and then they compared their efficiency with each other. Sarraf, et al [5], experimentally studied axial fans performance for two identical fans but with different impeller thickness. They indicated that the overall performance of these two fans is same, but the fan with thicker blades contained higher rate of pressure loss by the means of 8%. Also the efficiency of the fan with thinner blades was 3% higher than the fan with thicker blade. Mohaideen [6] improved an axial fan blade by using the finite element method (FEM) and reduced 18.5% of the blade weight after optimizing on the blade thickness via stress analysis by ANSYS commercial software.
There are a lot of studies on the generated noise by various airfoils that is carried out by experimental and/or numerical approaches. Chong, et al [7], measured the generated noise by a 2-D NACA 0012 airfoil at the angles of attack 0º, 1.4º and 4.2º, in a wind tunnel. They performed their experiments for some Reynolds numbers between 1×105 and 6×105. The experimental results indicated that the pressure gradient was raised on the airfoil pressure surface by increasing of attack angle, so the noise can be produced by this phenomenon. Devenport, et al [8], carried out experimental tests on the noise propagation of NACA 0012, NACA 0015 and S831 airfoil. The obtained results indicated that the airfoils with more thickness made lower noise and revealed the different angles of attack had little influence on the sound production for NACA 0012 and NACA 0015 airfoil. Casper, et al [9], solved the equations of FW-H and developed new equations. They computed the produced noise by a NACA 0012 airfoil in a low Mach number flow. The analytical results and experimental data for NACA 0012 airfoil were in good agreement.
So far, many experimental and numerical studies have been performed on the generated sound by axial and centrifugal fans. Many researchers have used the FW-H equations to predict the sound radiation of fan by numerical simulation. Ballesteros-Tajadura, et al [10], measured the noise of a centrifugal fan via FW-H noise model using the CFD code, FLUENT. By comparing numerical and experimental noise results, they showed the FW-H model was able to predict the tonal noise with reasonable accuracy. Solving FW-H equations, Moon, et al [11] and Cho, et al [12] calculated the amount of radiated sound from an axial fan and a cross flow fan, respectively. Younsi, et al [13], used numerical simulation to predict the noise level in a HVAC forward centrifugal fan. By comparing numerical and experimental data, they showed the good agreement between simulation and the experimental data. In some papers, researchers have studied the source of generating noise in different fans by using the computational aeroacoustics (CAA) [14]. Khelladi, et al [15], calculated the noise of a high rotational speed centrifugal fan via FW-H analogy and solving the Reynolds Averaged Navier-Stokes (RANS) equations. They compared the numerical and experimental data and also evaluated the aerodynamic performance of fan. In 2009, Sorguven, et al [16], studied aerodynamic and aeroacoustic performance of two radial fans. Moreover in their study, LES turbulence modeling and FW-H noise modeling were employed. They showed a satisfied agreement of experimental and numerical results and reported FW-H model as a reasonable model for evaluating aeroacoustic performance of fans.
Although Bladeless fan is invented in 2009, but until now aeroacoustic performance of this fan has not been studied numerically or experimentally for different conditions. This fan is designed for home applications by diameter of 30 cm and the only available geometric information is mentioned in patent documentation [1]. In the present study, the effect of five geometric parameters is investigated on performance of a Bladeless fan by diameter 30 cm. The studied parameters are height of fan cross section, outlet angle of the flow relative to the fan axis, thickness of airflow outlet slit, hydraulic diameter and aspect ratio for circular and quadratic cross sections. The unsteady conservation of mass and momentum equations are solved to simulate three-dimensional incompressible flow in the Bladeless fan. The Ffowcs Williams and Hawkings (FW-H) formulation is solved to calculate the noise propagation of smart bladeless fan. Firstly, the generated noise of a NACA 0012 airfoil is computed to validate aeroacoustic results by experimental data [17]. The obtained numerical results and the experimental data are in the reasonable agreement, so the FW-H model is employed to measure the tonal noise of Bladeless fan. To validate 3-D numerical simulations, the experimental results of a round jet [18] are compared with numerical simulation results. Since there is not any experimental data about Bladeless fans, round jet is selected due to much similarity. The turbulence in the Bladeless fan is simulated by standard k−ε turbulence model. In order to design cross section of Bladeless fan, Eppler 473 airfoil is chosen among standard airfoils. Eppler 473 airfoil is selected because it is an appropriate airfoil for low Reynolds numbers and high similarity of this airfoil profile to original cross section (designed by inventor) [1]. The volume flow rate is calculated at a distance up to 3 times of nozzle diameter in front of the fan (around 1000 mm) [1]. The numerical results for Bladeless fan show that the investigated parameters in this study are very important to improve the fan performance. Thus these parameters should be considered to design a high performance Bladeless fan.
Mechanism of Bladeless Fan
This fan is produced for domestic applications and its diameter is 30 cm. The mechanism of inlet and outlet airflow from this fan is shown in Fig. 1. At the first stage, the airflow is sucked into the fan through a rotating DC brushless motor and a mixed flow impeller. The intake air is accelerated by passing through an annular aperture which the cross section of this fan is similar to an airfoil profile. Then air is pushed out from a ring shape region, so the air velocity is increased in this region. A considerable pressure difference is generated between both sides of the fan and the discharged air can be described by Bernoulli’s principle. This pressure difference draws the behind and surrounding air toward front of fan. Therefore, a smart tower bladeless fan amplifies the intake air by drawing the air behind and around the fan. Thereby the inventor of this fan claims that [1] this fan multiplies intake air at about 15 times at distance 3D front of fan (around 1000-1200 mm) [1, 19]. All of described stages are shown in Fig.
|
|
|
Manufacturing and development of a bolted GFRP flange joint for oil and gas applicati |
Posted by: kow65d - 08-20-2021, 06:43 AM - Forum: Welcomes and Introductions
- No Replies
|
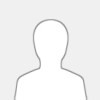 |
Manufacturing and development of a bolted GFRP flange joint for oil and gas applications
The manufacturing industry saw a significant rebound, and oil prices started to recover as well. Both of these trends are expected to continue in 2017.
At Allied Valve, we also saw some big changes this year. We expanded our product line to include Masoneilan control valves, CDC rupture discs, and Groth relief valves and flame arresters. We also beefed up our service capabilities with a new Mobile Lab trailer and new control valve testing systems.
Finally, we continued our initiative to bring you valuable content related to valves, actuators, and the many industries we serve. Here are our top 5 industrial valve articles of 2016.
Maximizing Your Control Valve Performance: A Guide to Control Valve Selection, Maintenance, and Repair
Process plants can contain thousands of control valves, responsible for keeping process variables like flow, level, pressure, and temperature within the desired operating range. Despite their importance to product quality, efficiency, and a company’s bottom line, control valves are often neglected. This article provides an in-depth look at the factors that affect control valve performance and how to keep your valves always working their best.
It came to our attention earlier this year that some safety valves containing Thermodiscs (e.g., Consolidated 1811 and Consolidated 1711 series) were being put through hydrostatic testing. These valve parts are designed for steam service only and water can cause damage, potentially beyond repair. This article describes the problems that hydrostatic testing can cause and what you can do to mitigate these problems.
The American National Standards Institute (ANSI) and the International Society of Automation (ISA) provide standards for the hydrostatic testing of control valves. The goal of the test is to verify the valves’ structural integrity and leak tightness. This article summarizes the fluid, pressure, and time requirements of hydrostatic testing as well as the standards for acceptable performance.
To work properly when they’re needed, all valves must be maintained. It used to be that preventative maintenance was the only option. But with the diagnostic tools available today, it’s possible in some cases to use a data-based predictive approach instead. Both of these approaches are part of an effective valve disc maintenance program. This article helps you understand when each of them is most appropriate.
Sand casting can be used for the majority of metals. Even highly reactive magnesium is sand cast provided care is taken and the correct materials used by adding what are called inhibitors into the sand.
Sand castings inevitably have a slow cooling rate because of the large insulating mass of sand surrounding the liquid metal as it cools. Grain sizes and dendrite arm spacings tend to be larger than in equivalent section sizes in die-castings.
Sand casting involves the pouring of molten metal into a cavity-shaped sand mould where it solidifies (Fig. 6.8). The mould is made of sand particles held together with an inorganic binding agent. After the metal has cooled to room temperature, the sand mould is broken open to remove the casting. The main advantage of sand casting is the low cost of the mould, which is a large expense with permanent mould casting methods. The process is suitable for low-volume production of castings with intricate shapes, although it does not permit close tolerances and the mechanical properties of the casting are relatively low owing to the coarse grain structure as a result of slow cooling rate.
The goal of this experimental study is to manufacture a bolted GFRP forged flange connection for composite pipes with high strength and performance. A mould was designed and manufactured, which ensures the quality of the composite materials and controls its surface grade. Based on the ASME Boiler and Pressure Vessel Code, Section X, this GFRP flange was fabricated using biaxial glass fibre braid and polyester resin in a vacuum infusion process. In addition, many experiments were carried out using another mould made of glass to solve process-related issues. Moreover, an investigation was conducted to compare the drilling of the GFRP flange using two types of tools; an Erbauer diamond tile drill bit and a Brad & Spur K10 drill. Six GFRP flanges were manufactured to reach the final product with acceptable quality and performance. The flange was adhesively bonded to a composite pipe after chamfering the end of the pipe. Another type of commercially-available composite flange was used to close the other end of the pipe. Finally, blind flanges were used to close both ends, making the pressure vessel that will be tested under the range of the bolt load and internal pressure.
In manufacturing of the steel bridge, fillet welded T-joint is widely used and angular distortion is often generated. So, reduction or control of angular distortion without additional processes to welding is strongly demanded because it takes great time and effort to correct the angular distortion. In this study, the effectiveness of welding with trailing reverse-side flame line heating for preventing angular distortion was investigated through the welding experiment and numerical simulation in submerged arc welding of fillet T-joint with three different thick flange plate. First, the heat source models for numerical analysis of both submerged arc welding and flame line heating were constructed based on the comparison with the measured temperature histories and angular distortion. And then, these heat source models were used in combination with various kinds of distance between two heat sources to make clear the appropriate distance condition for smallest angular distortion was 150 mm, and it does not depend on thickness of flange plate. It was also confirmed that the experimental angular distortions were in good agreement with those calculated. With a focus on the influence of thickness of flange plate, the reduction of angular distortion by welding with trailing reverse-side flame line heating becomes smaller with increasing thickness of flange plate. However, angular distortion could be adequately prevented under the appropriate flame line heating condition in either thickness of flange plate because the welding-induced angular distortion also becomes smaller with increasing thickness of flange plate. Thus, it was concluded that welding with trailing reverse-side flame line heating could be useful for preventing angular distortion of fillet T-joint, which is a component of steel bridge, enough not to correct it after welding.
Garlock offers a range of Butterfly Valves for different applications. Ranging from GAR-SEAL Butterfly Valves are used extensively where corrosive, abrasive and toxic media, to STERILE-SEAL valves are used in applications where sterile processes need to be maintained in the pharmaceutical and food industries.
Depending on your application, different air valve material and design type should be used. For a better understanding on which type of Garlock Butterfly Valve will best fit the application, you can refer to our Chart
The mechanism of opening of the aortic valve was investigated in dogs by attaching radiopaque markers to the commissures and the leaflets. Analysis of abnormal cardiac cycles demonstrated that, when the ventricular pressure first equalled the aortic pressure, the intercommissural distances increased 9 percent, and the valve opened with a stellate orifice without forward flow and without a rise in aortic pressure. Further opening of the aortic valve was dependent on forward flow over a narrow range. A new mechanism of aortic valve opening is proposed. This mechanism results in minimal flexion stresses on the leaflets and is important for the longevity of the normal aortic valve. It can occur only if the leaflets arise from an expansile aortic root.
Original LESER spare parts are the guarantee that also after maintenance works your safety valve precisely fulfills its task to protect people and environment. Learn with the spare pare finder which subassemblies are installed in your individual safety valve to be able to order the correct LESER spare part. The spare part finder shows the bill of materials of your individually configured valve body.
The list shown contains all components, regardless whether they are needed as spare parts. As initial spare parts supply for API, High Efficiency, High Performance, Compact Performance and Modulate Action safety relief valves, we recommend the Spare Part Kits. For the other product groups please contact us for an inital spare part offer. Find out more about LESER-Spare Parts Kits.
Please enter a combination of a serial number (SerNr.) and an article number (ArtNr.) to bring up the right spare parts (e.g. SerNr: 10202021, ArtNr: 4411.4443). You can find the serial and article numbers on the name plate of the valve or on the Certificate for Gobal Application, which you can download in the CERTIFICATES-area.
Please pay attention to the following user instruction:
The spare part finder currently only shows bills of materials for valves assembled in our Hohenwestedt plant. For spare parts lists of other valves, please contact your local partner.
Some items in the bill of materials are subassemblies which contain one or several of the following items. In most cases the subassembly should be ordered as a spare part.
|
|
|
Ultimate flexibility for scalable aseptic filling |
Posted by: kow65d - 08-20-2021, 06:41 AM - Forum: Welcomes and Introductions
- No Replies
|
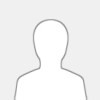 |
For more than 30 years, Flexicon has been established as the preferred choice for aseptic liquid filling for GMP regulated industries, such as biotechnology and diagnostics
Flexicon’s products scale with your business. From the intuitive, easy-to-use design of our ergonomic pumpheads, through to the modular design of manual, semi and automatic systems, our products feature a grow-with-me concept to meet your fill/finish needs.
Our experience in engineering accurate and reliable bottle filling machine for sensitive fluids in GMP production and cleanroom environments, means we provide solutions to optimise your fill/finish processes.
As part of the Watson-Marlow Fluid Technology Group, Flexicon’s engineering is backed by a global network of specialist and technical support engineers, who can help optimise your complete development and filling process, wherever you are in the world.
At the heart of all our filling systems is the gentle pumping action of our peristaltic fillers, which ensure your valuable product is transferred without cross contamination or damage to viability and product quality.
Leveraging our expertise in peristaltic engineering has helped to optimise the performance of companies filling processes worldwide. Whether those companies are developing Advanced Therapy Medical Products (ATMP) or looking to quickly—and safely—scale-up their batch production, we can help develop a system tailored to your needs.
Whether you’re a newcomer to the world of liquid filling equipment or an experienced user looking to upgrade or change your production line, browsing websites and product catalogues in the search to source a suitable machine can be more than a little confusing.
Overflow or gravity machine? Piston or pump? Automatic, semi-automatic or manual? Hot or cold-filling? In-line or rotary filling? Off-the-shelf or turnkey? Fortunately, with so many choices out there you’re likely to find the ideal solution for your particular application – however, finding it requires that you do a bit of homework and adopt a systematic approach.
To simplify the process, you may find this guide to liquid filling equipment useful. It identifies key questions which will help you narrow down your search and focus only on those systems that meet your objectives.
The first question to ask is what product is being filled?
Not all liquids are the same. Some are free-flowing, others are very viscous. Some contain particulates or flammable ingredients, others are foamy whilst the viscosity of some products may change when the temperature changes. The important thing to remember is that type of liquid filling equipment that you choose has to be compatible with the product type. For example, a gravity filler is more suitable for thin products, piston fillers are a better option for thick products than overflow automatic liquid filling machine and bottom-up filling machines are used for foamy products.
Another key question to ask is what type of container is being filled?
In many instances, the type of container or bottle will dictate the type of filling technique and the more you know about the attributes of the container, the better. What material is it made from (e.g. glass, aluminium, plastic) and what are its dimensions and characteristics? This information is important because it will determine the optimum performance of the equipment and the best equipment type. For example, an automatic bottle filler which grabs a container from the side may not actually be the best option if your container is very wide and a top filler may not work if your container has an unusually-shaped cap or lid.
You need to ask how many containers do you want to fill every hour?
Knowing your production rate is also a crucial factor in your equipment selection.
A semi-automatic filling machine would be a cost-effective and reliable solution for smaller production runs like those in a laboratory or in a start-up venture, whilst an automatic filling machine with a sizeable conveyor is ideal for larger-scale operations with much higher production rates. For operations with very low production rates and no expansion plans such as a home brewing venture or small-scale home-made sauce business, a manual machine could fit the bill.
You also need to ask yourself, how do you want the final fill-level in your container or bottles to look?
Appearance does count, and different filling systems have different outcomes. For example, a liquid level machine will fill every container to the same specified level regardless of the volume of the product, making it a preferred product where uniformity is important. On the other hand, a volumetric filler will fill a container with the identical volume of liquid even when the fill levels may appear to be variable. Volumetric fillers generally cost more as they require specialized instruments for calibration, balance and timing.
Some of the types of liquid filling machines include:
gravity fed fillers (a good, cost-effective option for efficient volumetric filling especially for low viscosity and foamy liquids);
piston fillers which use a highly accurate volumetric filling technique, ideal for thick or highly viscous liquids. These are divided into two types, namely check-valve piston fillers and rotary valve piston fillers;
pump fillers which are very versatile and suitable for a wide range of liquids and viscosities
in-line filling machines (a cost-effective choice for filling containers in a line) which are suitable for those operations where different container sizes are involved; and
rotary filling machines (which are often much larger and more specialized) for faster speeds and higher production rates.
Another question is whether your filling equipment can be modified if your needs change?
It’s often not necessary to buy new equipment just because your business has expanded or you want to add new products or packaging to your line. An experienced manufacturer will have the knowledge and skills to advise whether your liquid filling system can be modified and will make recommendations to future-proof your investment.
Choosing the best liquid filling equipment is a complex decision and many factors need to be considered. From product characteristics and container attributes to fill size, production rates, regulatory issues, safety requirements and expansion plans, if you answer the questions highlighted above, you’ll be in a strong position to make an informed choice which factors in all of these issues.
However, your best option is to talk directly to industry professionals, like AccuPak. They are one of Australia’s largest suppliers of all types of packing and filling equipment and they will work with you to identify the most cost-effective and practical solution. They know the critical factors required from all packing, filling, bagging and palletizing machinery and equipment - i.e. versatility, flexibility, reliability, accuracy and affordability - and if you’re interested in finding out how they can help you achieve your objectives, get in touch with them on 03 8804 1529 or visit accupak.com.au.
A walk down the grocery store aisle will exemplify the overwhelming amount of beverage products to choose from these days. Even with the existing wide variety of flavors and concepts within each drink category, consumers seem to want even more. For example, one of the fastest-growing segments in the beverage industry continues to be craft beer. Even after the beginning of its meteoric rise a few years back, the number of specialty beers with unique ingredients and different styles continues to proliferate with other craft alcohol producers, such as cider and spirits, following close behind. To keep up, many facilities are designing and installing additional liquid filling lines.
“As product lines continue to evolve to match expanding consumer demands, manufacturers are seeking flexible equipment that allows for product modifications—without breaking the bank,” says Paul Grainger, technical key account direct or North America for Tetra Pak. “Today’s equipment simply must be designed to accommodate a diverse range of products in order to be viable.”
Additionally, to maximize production efficiency, many are turning to high-capacity and more automated equipment that provides this flexibility. Still top of mind, though, are accuracy, minimizing product waste, reducing changeover times and simplifying sanitation. Liquid filling equipment providers are working to meet all these needs and more.When picking a specific 5 litre liquid filling machine, a good place to start is to know the exact characteristics of the liquid product. Is it a free-flowing liquid? This might work better with a timed-flow fill machine where the same volume of product is delivered each cycle. What if the product is more viscous? For that, a positive displacement liquid filler might be the way to go.
“Product specification is the most important parameter that we, at Bosch Packaging Technology, need in order to identify a suitable piece of filling equipment for our customers,” says Jonathan Viens, manager of North American sales and marketing. “We are talking about product characteristics, such as filling temperature, particulates, tendency of the product to splash or froth, etc.”
He explains that if a company is trying to dispense baby food into containers, Bosch would suggest servo-driven aseptic1 litre filling machine with full-metal pistons. This type of equipment helps address precision in filling a product that is highly viscous and particulate rich, but also avoids weight fluctuations or overfill issues.
For products that need special attention paid to minimizing microorganisms and ensuring food safety, such as juices, hot-fill technology for hygienic bottles will be needed. This was the case when Coca-Cola Canners in South Africa started bottling iced tea, sports drinks and juices with and without fruit chunks. The facility had two existing PET bottling lines, but due to the high-pulp content of the juice, a new line was needed.
The company employed KHS, a manufacturer of filling and packaging equipment, to install a hot-fill line. The content is heated to over 100°C and filled at a temperature of approximately 83°C. The line can fill up to 48,000 bottles per hour, sized between 0.3 and 1.5 liters. To avoid damaging the fruit chunks during the filling, the line was equipped with two precision volumetric fillers where the fruit pieces are first bottled with a small amount of juice before the second filler tops off the bottles with pure juice. This understanding of the filler’s impact on the final product is important, especially for sensitive liquids.
“Some yogurts tend to ‘shear’ when being forced through small openings,” says Jan Sundberg, applications development manager for JBT Corporation. “The filler needs to have gentle handling inside the filler bowl/hopper and also as the product flows through the valve. Larger porting and short, straight paths for the product flow are key to minimizing any damage.” For instance, features like extra elbows, pipes and pumps can change the viscosity of a product, so eliminating them for these applications could offer protection against damage.
“Products like creams or oily dressings can only be dosed with a specific dosing station, for example, positive valve,” says Viens. “Otherwise, the rotary movement in standard dosing stations could damage the product, or the pump design could separate the oil from the base product.”
When bottling a product like beer, which has a tendency to foam, gentle filling is paramount. Breweries want to limit the amount of oxygen picked up by the beer as much as possible during the filling process, but also want to maximize throughput. To help address these issues, Krones has equipped its Modulfill filler with a level probe that includes a swirl.
“The swirl gently guides the liquid to the bottle wall and in the bottle,” says Stefan Kraus, product manager for filling technology. “Additionally, the filling valve is equipped with two different filling speeds. The result is a gentle filling process with low turbulence and less foaming behavior.”
Product and container versatility
Because of the wide variety of products being packaged at plants, more processors are looking for fillers that can handle multiple concepts. Equipment providers understand this, but might not be able to deliver a panacea yet.
“In the world of food, the day of ‘one filler fits all’ still hasn’t arrived due to the wide range of product characteristics,” says Viens with Bosch, which acquired filling and sealing equipment manufacturer Osgood Industries, Inc. in 2015. When Bosch Osgood introduced its tank-style pump, part of the objective was to address this need for fillers to handle many different types of products. Thus, the tank-style pump can handle a range of products, from liquid juice to viscous vat-set yogurt. “With this solution, the pistons that are used to pump the product are located inside the hopper. An even distribution of product above each piston and tight tolerances offer the user excellent lane-to-lane repeatability and eliminate the need for dynamic O-rings on the piston head.”
“Customers are demanding that new filling equipment is more versatile and can handle a full range of varying products,” says Sundberg. As a result, the JBT Unifiller filler can handle products with a thin, watery consistency to thick, chunky products with high solid content and large particulates. “[It] is a unique volumetric piston filler with short product paths and larger porting.” Additionally, the fill nozzles are designed for specific applications and can be easily exchanged.
Krones 6 head liquid filling machine are also designed with flexibility in mind, says Kraus. As an example, he cites some of the company’s filling equipment that can be adjusted automatically via the filling probe, which addresses improved automatization as well.
For most of its filling machines, Serac uses net weight filling technology, which controls the amount of product dispensed into the container to give an accurate measure of what is inside. Alan Bonanno, marketing manager for Serac, says because aeration, temperature and viscosity do not affect the accuracy of a net weight filler, it can handle a variety of products with different characteristics.
Product flexibility isn’t the only filling demand, but the shapes, sizes and materials used in different containers being filled are also highly variable. Knowing the type of container is important for packaging providers to understand, says Viens, as it “will drive the configuration on numerous machine stations and the number of lanes required.”
|
|
|
The science behind wet wipes for infant skin |
Posted by: kow65d - 08-20-2021, 06:37 AM - Forum: Welcomes and Introductions
- No Replies
|
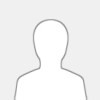 |
In the diapered area, the continuous exposure to excess moisture and irritants from urine and feces weakens the stratum corneum, making the skin more susceptible to irritation. The use of wet wipes for infants (baby wipes) is a common practice to clean skin after urine or a bowel movement, and this practice even extends to cleaning the hands and face, resulting in repeated daily use. Therefore, ensuring that baby wipes contain ingredients that are safe and mild on skin is important to help minimize skin irritation and discomfort. While disposable baby wipes have been shown to be effective and gentle at cleaning infant skin, even the skin of premature infants, there is growing public concern regarding their safety and tolerability. Not all products are made the same, as differences exist in manufacturing processes, ingredients, materials, safety, and quality testing. Therefore, it is important that healthcare professionals have accessible evidenced-based information on the safety and tolerability of common ingredients found in baby wipes to optimally educate their patients and families. Herein, we provide a review on best practices for ingredient selection, safety, and efficacy of baby wipes.
Skin irritation in the diapered region (commonly referred as diaper dermatitis) is one of the most common skin disorders found in infancy, with the highest incidence at 9-12 months of age.1 Overhydration and prolonged exposure to urine and feces are known to be the main contributors to skin irritation in the diapered area.2 However, an infant's diet, medications, underlying skin conditions, certain product ingredients, caretaker behavior, and practices such as infrequent diaper changes or ineffective cleaning can also influence the occurrence of diaper dermatitis. It has been reported that the diapering process can be a stressful event for an infant.3 The presence of skin irritation can exacerbate this response, leading to increased pain and discomfort. Ensuring the diapered area is kept dry and clean and that products used do not adversely impact the skin can help minimize the occurrence of dermatitis in the diapered region and, in turn, provide comfort to the infant.
Herein, we provide a review on best practices for ingredients selection, safety, and efficacy of runhe baby soft wet wipes to help make more informed decisions when selecting products for infant diapered skin care.
A disposable baby wipe consists of three main components—the basesheet (the cloth that makes the wipe), the formulation (the ingredients in the solution that make the wipe wet and help with cleaning), and package, as shown in Figure 1. The packaging (not discussed here) and the basesheet are the most physically obvious components of a wipe. There are three types of basesheets with differences in composition which translates into differences in thickness, absorbency, and softness to touch. These differences can impact cleaning performance but the materials themselves are quite common—wood pulp, polypropylene, polyester, or combinations thereof.
Over the last two decades, significant advances have been made to baby wipes. More recently, efforts have been centered on the removal of ingredients with irritation or skin-sensitizing potential such as methylisothiazolinone (MI) and phenoxyethanol.4 In fact, five clinical studies have demonstrated that the use of modern baby wipes is superior to using water and cloth to clean diapered skin (see Table 1). In 2016, a recommendation was made by the European Roundtable Meeting on Best Practice Healthy Infant Skin Care stating that a wet wipe for infant skin should contain pH buffers to maintain the slightly acidic pH of the skin, should be free of potential irritants, and should contain well-tolerated preservatives
Formulating a hypoallergenic, safe, gentle, and effective baby wipe can be challenging as the wipe must meet regulatory, safety, and performance measures while remaining aesthetically pleasing. It is preferred that baby wipes are formulated with a very large percentage of water. However, water alone is not enough to effectively remove water-insoluble residues from feces and prevent the growth of microorganisms or maintain a healthy skin pH. Thus, it is important that baby wipes also contain an extremely mild surfactant (detergent or cleanser) to lower surface tension for better cleaning, a preservation system to ensure product freshness before and during use, a pH adjusting (buffering) system to maintain a solution pH similar to infant skin, and, optionally, skin-benefiting ingredients that reduce frictional damage, replenish the skin lipids, etc A common misconception about baby wipes is that they contain drying alcohols such as ethanol and isopropanol. While ethanol and isopropanol can be found in some sanitizing wipes, these ingredients have not been used in branded baby wipes.
The water used in baby wipes should range from highly purified to reverse osmosis quality. The treatment process removes most of the salt content (CaCO3 and MgCO3, contributing to overall hardness) and other residual minerals that can serve as nutrients for microorganisms. Most water systems also employ ozone and ultraviolet light processing to sterilize the water before use. In addition, extensive filtration removes total dissolved solids and microbes. These intentional processes produce water that is of a higher quality than standard drinking water and some types of distilled water.
2.2.2 Surfactants
Surfactants are the molecules within the formulation that provide cleaning action. Surfactants contain hydrophilic moieties attached to hydrophobic end chains. It is the hydrophobic end chains that bind to oily residue on the skin surface and help remove it. For baby wipes, it is important to use a surfactant that can adequately remove the oily molecules within feces without removing skin lipids, which can lead to skin barrier damage with repeated or prolonged use. For runhe new arrival baby wipes, the surfactant fraction would not be expected to exceed 1% by weight of the formula and, in most cases, would be below 0.3% by weight.6 This is in stark contrast to bottled baby products (body wash, shampoo, hand soap) where the surfactant concentration is typically between 5% and 20% by weight as dilution is expected upon use followed by rinsing.6
Surfactants are typically classified as anionic (negatively charged), cationic (positively charged), and non-ionic (no net charge). Generally, non-ionic surfactants are the mildest on skin; however, there are examples of suitable surfactants in all classifications. Table 2 contains a list of typical baby wipe surfactants along with maximum use concentrations and references to full reviews on their safety profile as concluded by the Cosmetic Ingredient Review (CIR), an independent expert panel consisting of dermatologists, toxicologists, academic researchers in medicinal and pharmaceutical sciences, industrial scientists, and representatives from the FDA and consumer groups.
As baby wipes contain a large amount of water, this can allow microorganism growth. To prevent contamination, various manufacturing and testing practices are followed by major suppliers. The use of preservatives ensures the product is not contaminated before the consumer begins using it, and that it maintains a reasonable shelf life for use. Ensuring a consistent product, free of pathogenic microorganisms, should be of the highest concern, especially when cleaning infants with compromised skin.
In the personal care industry, the default listing of preservative chemicals is maintained by the European Union (EU) and is known as Annex V.7 Ingredients on this list are recognized for their antimicrobial action and listed with acceptable and safe usage concentrations. A subset of these chemicals applicable to baby wipes is shown in Table 3. Notably, many of the chemicals in Annex V are not allowed for use in children's products due to regulation at the state or country level. The US FDA does not maintain a list of approved preservatives but does have the authority to limit the use of ingredients in certain product classifications. After considering safety, allergenicity and irritation potential, the choice of preservative in a formulation depends on water solubility, effective concentration, pH compatibility, odor, and consumer expectation. A good example of regulatory and industrial response has been the removal of formaldehyde donating preservatives and MI from wipes and other leave-on products following many reports of contact dermatitis and sensitization in the diapered area and in other common areas of baby wipes use such as hands and face. Currently, it is rare to find this ingredient in mainstream baby soft wet wipes.
A critical part of ensuring baby wipes are safe and effective to clean infant skin is following specific microbiological quality standards prior to product distribution. As is the case with most non-sterile formulated personal care products, baby wipes require specific analyses to ensure they (1) do not contain harmful or high levels of microbes following manufacturing and (2) can control the growth of microbes introduced during use. Non-profit scientific organizations, such as the United States Pharmacopeia (USP) and the European Pharmacopeia (EP), have published guidelines on the preferred approaches for completing these analyses.
Prior to releasing baby wipes for sale to consumers, an evaluation of the final product should be completed for the presence and level of microbes within the product. For example, the USP recommends that methods used in the release of non-sterile products have data available that demonstrates the ability for methods to successfully recover and quantify Staphylococcus aureus, Bacillus subtilis, Pseudomonas aeruginosa, Candida albicans, and Aspergillus brasiliensis.21
Any products that have a water activity level of >0.90 are susceptible to the growth of microbes in the product as this is the minimum level of water required for bacteria and fungi to grow.22-24 As such, products at or exceeding this level of water, such as wipes, should include a preservative to prevent the growth of microbes that may be introduced post-manufacturing. A likely route of post-manufacturing product contamination is while dispensing the product during use,25 a reason why packaging is a key component. In this scenario, transient or normal flora from a wipes’ user can transfer from the hands onto the stack of wipes in the product package. To assure a newborn baby wipes product is effectively preserved and able to overcome this type of contamination, a confirmatory lab test must be utilized to ensure microbial growth will not occur during normal product use. Specifically, the test should involve adding a defined number of diverse organisms (at a minimum those recommended by USP/EP but others may be added) to a defined quantity of product and then monitoring the survival and/or growth of the added organisms over time.26 This test is commonly utilized on product that has been freshly made and on product aged under ambient or accelerated (high temperature, high relative humidity) conditions. While there is no universally applied approach in how this test is conducted for wipes, many manufacturers utilize USP and/or EP guidance as the basis for establishing their method and acceptance criteria.
The performance of the preservative system is one of the most important factors that go into determining the expiration date on the package. Baby wipes that do not have a proper preservative system should have a much shorter expiration date (or period after opening) as the product does not have a means to prevent microbial growth post-manufacturing. This is especially critical when the dispensing of the wipes requires significant contact by human hands, that is, transfer of normal flora into the package. Wipes should not be used outside of the printed expiration dating on the package and should be stored as directed by the labeling on the package.
|
|
|
Knit fabrics are constructed by interloping one or more sets of yarns |
Posted by: kow65d - 08-20-2021, 06:35 AM - Forum: Welcomes and Introductions
- No Replies
|
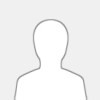 |
Common examples of apparel utilizing weft knitted fabric are socks. Knitting is a more versatile manufacturing process, as entire garments can be manufactured on a single knitting machine, and it is much faster than weaving. However, due to the looping, more yarn is required to manufacture a knitted garment than a comparable woven garment. Thus any cost savings gained in manufacturing speed are offset by the higher materials cost.
Knits are comfortable fabrics, as they adapt to body movement. The loop structure contributes to elasticity beyond what is capable of the yarns or fibers alone. A knit fabric is prone to snagging, and has a higher potential shrinkage than a woven fabric. The loop structure also provides many cells to trap air, and thus provides good insulation in still air. Knits are not typically very wind- or water-repellent.
Knit fabrics are composed of intermeshing loops of yarns. There are two major types of knits: weft knits and warp knits, as illustrated in Fig. 4.7. In weft knits, each weft yarn lies more or less at right angles to the direction in which the fabric is produced, and the intermeshing yarn traverses the fabric crosswise. In warp knits, each warp yarn is more or less in line with the direction in which the fabric is produced, and the intermeshing yarn traverses the fabric lengthwise. Similar to the way that woven fabrics have warps and wefts, knit fabrics have courses and wales, which lie in the crosswise and lengthwise direction, respectively. However, unlike woven fabrics, courses and wales are not composed of different sets of yarns; rather are formed by a single yarn.
Weft blend knitted fabrics are produced predominantly on circular knitting machines. The simplest of the two major weft knitting machines is a jersey machine. Generally, the terms circular knit and plain knit refer to jersey goods. The loops are formed by knitting needles and the jersey machine has one set of needles. Typical fabrics are hosiery, T-shirts, and sweaters.
Rib knitting machines have a second set of needles at approximately right angles to the set found in a jersey machine. They are used for the production of double-knit fabrics. In weft knits, design effects can be produced by altering needle movements to form tuck and miss stitches for texture and color patterns, respectively. Instead of a single yarn, several yarns can be used in the production of these structures. This increases the design possibilities.
‘Loop’ is the basic unit of knit fabric. As illustrated in Fig, 4.7a, in weft knits, a loop, called a needle loop, consists of a head and two legs, and the section of yarn connecting two adjacent needle loops is called the sinker. In warp knits, the needle loop is divided into overlap and underlap, as illustrated in Fig. 4.7b. Each loop in a printed fabric is a stitch. Alternative to fabric count for woven fabrics, cut (or gauge) and stitch density are used to represent the closeness of the intermeshing loops. Cut or gauge indicates the number of knitting needles per unit length along the crosswise or lengthwise direction. The greater the number, the closer together the loops are to each other. Stitch density is the number of stitches per unit area, obtained by multiplying the number of courses per inch (25 mm) by the number of wales per inch (25 mm). Like woven fabrics, a knit fabric also has a technical face and a technical back and can differ in appearance on each side. The technical face is the side where the loops are pulled toward the viewer. Knit fabric also has an effect side, which is intended to be used outermost on a garment or other textile product. In some cases, the technical face and the effect side are the same; but in others, they are opposite.
Gel Knit® fabric is a small diameter weft knitted tube. This is knitted on a small diameter circular knitting machine with the provision for the positive feeding of two separate yarns. Positive feeding is used to ensure the good quality assurance required for a medical product.
The main yarn that is knitted is a staple (spun) yarn of cellulose. This may be any normal cellulosic textile material such as cotton or a number of different reconstituted cellulose materials such as lyocel or viscose. As will be described later in this paper, the cellulose is the precursor material since it will be chemically converted after knitting into the Gel forming material.
The second yarn is a very thin continuous filament nylon which acts as reinforcement and holds the fabric together after the Gel has been formed and the Gel forming yarn has lost all form and stability. The total nylon content of the fabric is about 10%.
Warp knit fabric is similar to that of a woven fabric in that yarns are supplied from warp beams. The fabric is produced, however, by intermeshing loops in the knitting elements rather than interlacing warps and wefts as in a weaving machine. Warp knitted fabric is knitted at a constant continuous width. This is achieved by supplying each needle with a yarn (or yarns) and all needles knit at the same time, producing a complete course (row) at once. It is also possible to knit a large number of narrow width fabrics within a needle bed width to be separated after finishing. In comparison with weft-knit structures, warp knits are typically run-resistant and are closer, flatter and less elastic.
The two common warp-knit fabrics are tricot and raschel (Fig. 10.9). Tricot, solely composed of knit stitches, represents the largest quantity of warp knit. It is characterized by fine, vertical wales on the surface and crosswise ribs on the back. Tricot fabrics may be plain, loop-raised or corded, ribbed, cropped velour or patterned designs. It is commonly used for lingerie owing to its good drapability. It is used for underwear, night-wear, dresses, blouses and outerwear.4 Tricot fabric is used in household products such as sheets and pillowcases. It is also be used for upholstery fabrics for car interiors.Most warp cotton stripe jersey knit fabrics tend to curl, including the most important type known as Jersey stitch (in the USA) or Locknit stitch (in the UK). If they receive appropriate heat treatment, synthetic warp knit fabrics do not curl. In dyeing, finishing, cutting and sewing garments, it helps to know the face and back of the fabric and its curling propensity. When a greige nylon Jersey stitch fabric is put on a table technically upright (having the loop side up), the top and bottom edges of the fabric will curl upwards or towards the loop side or technical face. However, the side edges will curl under the fabric towards the float or technical backside of the fabric.
If nylon Jersey stitch fabric is heat set it will not curl, but if that fabric is laid on the table technically upright and it is pulled sideways on the top edge of the fabric, the fabric will curl towards the loop side. There are some warp knit structures that will not curl in the greige state.Plain warp-and weft-knitted structures are not commonly used for composite applications due to their inherent anisotropy in the wale and course directions. This causes the fabric preform to roll up on itself making handling and manufacturing more difficult. This problem is solved by using weft-knit structures such as the 1 × 1 rib and milano rib, which exhibit balanced properties because of their through-thickness symmetry. However, the highly curved fibre architecture, or crimp, present in these and any knitted structure, means that composites produced using these structures exhibit relatively poor mechanical performance. Characteristics of high conformability and low strength make them ideally suited to producing semi-structural complexly shaped components.
To help increase mechanical performance, insert yarns can be placed between the planes of loops in either the warp or weft direction. The technique can be used for both warp-and weft-knitted fabrics which allow the insert yarns to remain perfectly straight, giving a greater yarn to fabric translational strength. This results in an increase in the composite stiffness and strength along the insert direction. Warp-and weft-knitted fabrics with inlay yarns are termed unidirectional knitted fabrics and the incorporation of insert yarns in two directions creates biaxial knitted fabrics.
8.4.1 Multiaxial warp knits
Multiaxial Warp Knit (MWK) fabric is a further development of this idea by utilising layers of insertion yarns for the in-plane reinforcement and warp stitch yarns for the through-thickness reinforcement. They consist of one or more parallel layers of yarns held together by a warp knit loop system. Theoretically, as many layers as preferred can be used but typical commercially available machines only allow four layers (Du and Ko, 1996). The purpose of the knit loops is to hold the layers of unidirectional yarns together, but it has also been proven to be the key to increasing the damage tolerance of the material (Zhou et al., 2005).
These types of knitted structure are termed non-crimp structures and can be produced in a single knitting process (Du and Ko, 1996). They are particularly suitable for thin to medium thickness parts. The combination of the warp-knitted structure and non-crimp yarns means they have the ability to conform to complex shapes as well as the potential to meet the demands of primary load bearing applications.
MWKs have evolved through structural modifications of warp-knitted fabrics and are predominantly fabrics with inlay yarns in the warp (90°), wale (0°) and bias (± θ°) directions. Warp, weft and bias yarns are held together by a chain or tricot stitch through the thickness of the fabric (Du and Ko, 1996). Layers of 0° need to be placed somewhere other than the top or bottom layer to ensure structural integrity. The amount of fibre and the orientation of the inlay yarns can be controlled, which is advantageous for preform engineering. As a result, the insert yarns are made from a much higher linear density yarn than the stitch yarns, since they form the load-bearing component of the fleece fabric structure (Du and Ko, 1996). Figure 8.4 shows the configuration of the chain and tricot MWK structures.Yarns in a simple weft-knitted structure, as shown in Figure 11.13a, lack the long continuous paths found in woven fabrics and there would be stress concentrations where yarns cross one another. This limits their mechanical performance, but as shown in Chapter 3, they do have applications as composites. In the free state, the knit fabric shows a low resistance to extension and shear, with accompanying area change, until the yarns jam together. This means that they are easily draped into complex shapes.
|
|
|
|