Welcome, Guest |
You have to register before you can post on our site.
|
Online Users |
There are currently 256 online users. » 0 Member(s) | 255 Guest(s) Bing
|
Latest Threads |
Dominica visa free countr...
Forum: Off Topic
Last Post: axied12
06-24-2025, 12:37 PM
» Replies: 0
» Views: 165
|
Advanced microneedling
Forum: Off Topic
Last Post: axied12
05-28-2025, 01:25 PM
» Replies: 0
» Views: 292
|
Caviar and cheese
Forum: Off Topic
Last Post: axied12
05-28-2025, 12:38 PM
» Replies: 0
» Views: 258
|
Top-rated countertop comp...
Forum: Off Topic
Last Post: axied12
05-04-2025, 06:42 AM
» Replies: 0
» Views: 398
|
Ryanair letenky levně do ...
Forum: Off Topic
Last Post: axied12
02-11-2025, 01:37 PM
» Replies: 0
» Views: 796
|
Trusted essay writing ser...
Forum: Off Topic
Last Post: axied12
01-30-2025, 08:16 AM
» Replies: 0
» Views: 721
|
Bootverkopers - actieve j...
Forum: Off Topic
Last Post: axied12
12-07-2024, 11:07 AM
» Replies: 0
» Views: 849
|
Services for individuals ...
Forum: Off Topic
Last Post: axied12
12-02-2024, 03:31 PM
» Replies: 0
» Views: 820
|
Used excavators
Forum: Off Topic
Last Post: axied12
11-13-2024, 09:22 AM
» Replies: 0
» Views: 768
|
Buy Higo Rocket in Dubai
Forum: Off Topic
Last Post: axied12
10-25-2024, 01:09 PM
» Replies: 0
» Views: 881
|
|
|
HOW DO GLOW PLUGS WORK? |
Posted by: fowjw558 - 08-17-2021, 02:45 AM - Forum: Welcomes and Introductions
- No Replies
|
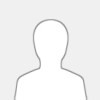 |
No matter how you look at it, car technology has come on leaps and bounds over the past decades. And, while some of these advances are immediately noticeable and appreciated, such as electric windows and smoother suspension systems, others, like glow plugs, are hidden under the bonnet and forgotten about unless something goes wrong. This shouldn’t be the case. Heat glow plug technology has significantly improved, with BERU, for example, dramatically improving the time it takes to start your diesel car – especially on cold mornings.
So, let’s appreciate the hidden and take a look at BERU glow plugs – what are they, the different types available and how they compare to the competition.
What is a glow plug?
To get started, we need to go back to basics: what is a glow plug? And, what does a glow plug do?
A glow plug is a heating element that heats incoming fuel and air to encourage efficient fuel combustion in a diesel engine. The fuel combustion starts your engine so that you can drive. Each cylinder of your engine has one glow plug, either in the pre-chamber (pre-chambered engines) or in the combustion chamber (direct-injection engines).
GLOW PLUG SYSTEMS
The starting process of an engine heavily influences the exhaust gas values of a vehicle. Together, glow plugs and their connected components (glow plug control modules, glow plug relays and glow plug combustion sensors) play an important role in reducing emissions helping to protect the environment.
Glow plug is specialized heating devices used to aid in the starting of diesel engines. They are similar to spark plugs in design; however, they differ in their primary function. Instead of producing a timed spark to ignite the fuel mixture, like spark plugs do, glow plugs simply serve to produce additional heat that aids the diesel engine combustion process during cold starts.
Diesel engines rely entirely on the heat generated by cylinder compression to ignite the fuel mixture. When glow plugs begin to fail, this additional heat that aids the combustion process is gone, and the engine may become more difficult to start, especially in cold weather.
Another symptom of faulty glow plugs is black smoke being observed during start up, indicating the presence of unburned fuel due to an incomplete combustion process. In this guide, we will cover how to test the resistance of glow plugs to determine if they are functioning properly.
Part 1 of 1: Testing your glow plugs
tep 1: Determine the multimeter’s resistance value. Before testing the terminals, you must determine the resistance value of your digital multimeter. To do this, turn the multimeter on, and set it to read in Ohms.
Once the multimeter is set to read in Ohms, touch the two leads of the multimeter together and examine the resistance reading that is displayed.
If the multimeter reads zero, try changing the setting of the multimeter to a higher sensitivity until a reading is obtained.
Record this value on a piece of paper, as this will be an important value in calculating the resistance of your glow plugs later on.
Step 2: Locate the glow plugs in your engine. Most glow plugs are installed in the cylinder heads and will have a heavy gauge wire, similar to a regular spark plug wire, attached to them.
Remove any covers that may be obstructing access to the glow plugs, and use the flashlight for additional illumination if necessary.
Step 3: Disconnect the glow plug wires. Once all of the glow plugs have been located, disconnect any wires or caps attached to them.
Step 4: Touch the negative terminal. Take your multimeter and touch the negative leads to the negative terminal on your vehicle’s battery.
If possible, secure the lead to the terminal by tucking it inside or underneath the clamping mechanism of the post.
Step 5: Touch the positive terminal. Take the positive lead of your multimeter and touch it to the terminal on your Mitsubishi glow plugs.
Step 6: Record the glow plug’s resistance. With both leads touching the terminals, record the resistance reading that is indicated on the multimeter.
Again, the reading that you get should be measured in Ohms (Ω).
If no reading is obtained when you touch the glow plug, make sure that the negative lead is still in contact with the negative battery terminal.
Step 7: Calculate the resistance value. Calculate the true resistance value of the glow plug by subtracting.
The true resistance value of the glow plug can be determined by taking the resistance value of your multimeter (recorded in Step 2) and subtracting it from your glow plug resistance value (recorded in Step 6).
Step 8: Evaluate the resistance value. Compare your calculated true resistance value of your glow plug with the factory specification.
If the glow plug resistance exceeds the specification or falls out of the acceptable range, then the glow plug must be replaced.
Step 9: Repeat for other glow plugs. Repeat the procedure for the remaining glow plugs, until they have all been tested.
If any of the glow plugs fail the test, it is recommended that the entire set be replaced.
Replacing just one, or a few, of the glow plugs may cause engine problems similar to a faulty glow plug if the resistance readings are too far apart.
For most vehicles testing the resistance of a glow plug is a pretty simple procedure, granted the glow plugs are in an accessible location. However if they are not, or this task is not something that you feel comfortable taking up on your own, this is a service that any professional technician, such as one from YourMechanic, should be able to perform quickly and easily. If necessary, they can also replace your Isuzu Glow Plugs so that you can start your car like normal.
There are very few glow plugs that are considered universal plugs (OS' #8 plug is an example). For the most part, the type of fuel you are running will impact the kind of glow plug you need to use. Another component in the nitro fuel is nitromethane. The Nitro Percentage of your fuel determines the ignition point as well; in other words, the more nitro you run, the more you advance the ignition point. Ideally, the ignition point will be when the engine is at top dead center (TDC). This will force the piston down and back up again for another stroke. But when you run higher nitro content and don't switch to a colder plug, you will advance the ignition point and result in less-than-optimum performance, since the piston is still on its compression stroke (the upward stroke) when the air/fuel mixture is ignited.
In general, the higher the the nitro percentage, the colder the plug should be. Conversely, the lower the nitro percentage, the hotter the plug should be.
Glow plugs are an engine management component that is found on vehicles equipped with diesel engines. Their purpose is to preheat, and help warm up the engine’s cylinders so that diesel combustion can occur more easily. They play an especially important part in warming the vehicle’s cylinders during cold starts, where starting the engine is most difficult. Glow plugs use an electrode which will warm up and glow orange when current is applied. When the glow plugs have an issue, they can usually cause problems with the driveability of the vehicle. Usually bad or failing glow plugs will produce a few symptoms that can alert the driver of a potential issue.
1. Engine misfires or decrease in power and acceleration
Engine misfires are one of the first symptoms of an issue with the vehicle’s glow plugs. If the Mazda Glow Plugs malfunction they will not provide the additional heat that aids in diesel combustion, which may cause the engine to experience misfires. The misfires may cause a loss in power, acceleration, and even fuel efficiency.
2. Hard starting
Another symptom of an issue with the vehicle’s glow plugs is hard starting. Unlike gasoline engines, which use a spark to ignite the fuel mixture, diesel engines rely solely on cylinder pressures to ignite the diesel fuel mixture. If the glow plugs fail, the engine will have to overcome additional pressure in order to ignite the mixture, which may result in hard starting.
3. Black smoke from the exhaust
Another symptom of an issue with the glow plugs is black smoke from the exhaust. Faulty glow plugs may disturb the sensitive diesel combustion process, which may cause the engine to produce black smoke from the tailpipe. Black smoke can also be caused by a wide variety of other issues, so having the engine properly diagnosed is highly recommended.
Glow plugs are found on virtually all diesel engines, and play an important role in starting and operating the engine. If your vehicle is displaying any of the symptoms above, or you suspect that your glow plugs may be having an issue, have the vehicle inspected by a professional technician, such as one from yourMechanic, to determine if the glow plugs need to be replaced.
Continuous Improvement
The diesel engine is continuously being improved, in terms of its fuel consumption, power outputs and, ultimately, refinement. Drivers of modern diesel vehicles expect to be able to just jump in, turn the key and go. It’s no longer acceptable to have to wait 8 to 10 seconds for a glow plug light to go out before you can start the engine. One of the reasons this is possible is because of the technical advances that have been made in glow plug design, in particular with the development of both twincoil technology and the latest third generation of glow plug – the New High Temperature Ceramic type, or NHTC. In this article we take a closer look at these latest types of plugs in more detail; the manufacturers spearheading the new technologies, and the major motor manufacturers adopting them as OE.
Twin -coil Technology
Using twin-coil technology, Toyota Glow Plugs can be made to heat more quickly and then self-stabilise at the correct temperature. This type of plug is more resistant to misuse, as it will prevent overheating of the main coil and allows longer post glow periods, giving cleaner exhaust emissions.
Each twin-coil glow plug has been designed and tested to 7,000 heating cycles before being approved for production. This means that if the engine is started from cold twice per day, the glow plug could have a life expectancy of 10 years or more.
Glow plugs are probably far more intricate than you may imagine them to be. It takes precision laser welding to join the heating coils, which are then tested for maximum temperature and rate of temperature rise. This is to ensure that the glow plugs reach 850°C within a specified time.
|
|
|
Road Bike Vs. Mountain Bike |
Posted by: fowjw558 - 08-17-2021, 02:44 AM - Forum: Welcomes and Introductions
- No Replies
|
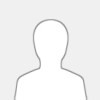 |
Breakthroughs in technology have made them much more efficient and comfortable while simultaneously making them much more affordable when it comes to cost to benefit ratios. This makes it a great time to buy a cycle!
The dilemma most people face when purchasing a bike is the type of bike to buy. Avid cyclists generally have a different bike for each different style of cycling that they will be doing, but hobbyists and recreationists can’t really afford to do that.
If you can only get one bike, what should it be?
Unfortunately, there isn’t a right answer to that question.
Everyone is different, and so are their needs. Most casual cyclists will want to purchase bike, but once you have the options narrowed down this far, it’s a matter of purpose and preference.
In this article, we can help you determine whether a road bike or a mountain bike is the better choice for your needs. We will take a look at some of the factors and circumstances that can help you to determine which choice would be more prudent.
By the end, you will be familiar with the questions to ask yourself before purchasing a bike and the type of things you can do with each bike.
Before you can compare the 2 different types of bikes, you need to be aware of your own cycling style. After all, knowing what you intend to use your bike for is one of the most important pieces of information to help you make your choice.
First, you should ask yourself how you will be using the bike.
Are you hoping to get some exercise without the shock to your joints that running provides?
Do you want to cruise and explore some of the trails nearby, or take it through some mountains?
Are you trying to cut down on time in traffic, so you want to use a bike to get around the city and replace your car for short-distance commuting? Do you hope to do more than one of these things with your bike?
Knowing your primary use will point you in the right direction. If you plan to stick to roads, then you may not need a mountain bike. Road bikes are great commuter bikes that can go pretty quickly and cover a lot of ground.
If you plan to use your bike for exploration as well as exercise and commuting, though, you will need the more versatile mountain bike.
Road bikes are optimized for pavement, so you can’t use them in the mountains. Their tires are very narrow and thin, so a single pebble or stick will send you flying head over heels.
It’s dangerous to use them on unknown or uneven terrain.
On the other hand, mountain bikes are not optimized for riding on the road, but they are capable of doing so as long as you put the extra effort into making them go.
They’re not as fast on the road, and they’re not as efficient, but unlike road bikes, which can’t take mountain paths at all, these bikes won’t put you in danger if you do ride them on the road… They just get a lot harder to handle and a lot less comfortable.
Now that you’ve (hopefully) determined how you’ll be using your bike, let’s take a look at these 2 bikes in more detail.
This will give you a better idea of all the things you can do with them.
Road Bikes
Road bike (occasionally known as racing bikes) are designed for speed.
These are great options for commuters because the narrow tires can roll very quickly along paved surfaces as long as there aren’t any obstacles in the way. They are becoming very popular and being made with disc brake.
These bikes have a few different types. Aero bikes are designed to minimize the drag you experience during a ride.
These are professional racing bikes that are more concerned with speed than comfort or other features. Ultralight bikes are designed for climbing uphill. They’re extremely lightweight but they’re not very versatile.
Endurance bikes are built more for touring racing. These are designed for riders who plan to travel longer distances per ride, with a focus on comfort over speed and climbing.
Mountain Bikes
These bikes are much more versatile and durable than road bikes. They’re made for handling dirt trails and different terrains.
These bikes have wider handlebars and usually come with forks that will absorb the shocks you take. They can handle pebbles and twigs and little bumps in the path without sending you flying.
These usually have wide tires and a lot of treads, so you will have traction when riding. They also include hydraulic disc braking and drivetrains that can handle steeper climbs and descents.
Hardtail bikes come with a rigid frame and suspension forks. These are the most common and most affordable ones.
They also make XC full suspension mountain bikes. These are for people who are not riding as far. The rear suspension on these bikes keeps the frame light so you can get extra efficiency when powering up climbs.
The trail full suspension bikes are for riding longer distances because they balance efficiency climbing with going downhill. These have wide tires and plenty of stopping power on the brakes. Finally, full suspensions put a lot of power in the rear wheel.
These can go for very long rides without causing exhaustion. They’re designed to be very balanced and handle any terrain for long rides.
Mountain bikes are very versatile. They can be used to ride just about anywhere – including roads. Some people like using them for unpaved roads. Others like using them to power up steeper hills without the same level of effort road bikes require.
E-bike
The first thing you should know about e-bikes is that they’re here to stay. Electric bike sales jumped by an incredible 145 percent from 2019 to 2020 alone, according to the market research firm NPD Group. It’s a nearly $244 billion industry as of last year, and there’s no sign of a slowdown.
Some view the rise of e-bikes as a threat, as though standard bikes will go the way of the penny-farthing once everyone goes electric. But fear not: E-bikes aren’t here to rob us of our human-powered way of life. In fact, they may very well enhance it—especially as travel and commuting habits change following the global pandemic and shift of work commuting. So as we roll our way into peak riding season, here’s everything you need to know about the electric revolution.
Generally speaking, E bicycle are bicycles with a battery-powered “assist” that comes via pedaling and, in some cases, a throttle. When you push the pedals on a pedal-assist e-bike, a small motor engages and gives you a boost, so you can zip up hills and cruise over tough terrain without gassing yourself. Called “pedelecs,” they feel just like conventional bikes—but better, says Ed Benjamin, senior managing director at the consulting firm eCycleElectric. “You control your speed with your feet, like with a regular bike,” he says. “You just feel really powerful and accelerate easily.”
In addition to the pedal-assist feature, some e-bikes come with a throttle that engages the motor with the press of a button. These belong to a separate class of e-bike that, obviously, doesn’t offer a pure cycling experience; they’re also illegal in some municipalities. Interestingly, Benjamin says, people who aren’t already “cyclists” tend to gravitate toward throttle bikes at first, but then turn around and choose a pedal-assist for their next purchase.
“People are buying electric bicycle as a way to reduce car trips,” Benjamin says. The data backs him up: 28 percent of survey respondents said they bought an e-bike specifically to replace driving a car. And many other reasons buyers listed for wanting an e-bike—including carrying cargo and kids, avoiding parking and traffic, and environmental concerns—also indicate a desire to get out from behind the wheel. Plus, you don’t need to change clothes or clean up when you arrive at your destination, because you don’t have to work up as much of a sweat.
Consider, too, that more than half of all driving trips are shorter than 10 miles, with some surveys reporting that the average single trip amounts to just 5.95 miles. That’s a no-brainer distance to cover by e-bike. In fact, the survey found that owners replaced 46 percent of their car commutes and 30 percent of their driving errands with e-bike rides. All you need is a great commuter bag to carry your stuff, and you’re set.
Getting an e-bike can dramatically increase how often you ride, according to a survey of nearly 1,800 e-bike owners in North America. Beforehand, 55 percent of respondents said they rode daily or weekly. After buying an e-bike, that number soared to 91 percent. It makes sense: Even if you’re super fit, you still get tired (likely from training or racing) and remounting your bike can feel like a chore. If you have an e-bike, you can continue riding while giving your knackered legs a bit of a break. You can also go faster, which makes biking for longer trips more attractive, even when you’re pressed for time.
For those who aren’t frequent riders, e-bikes open up a whole new world. While you may not be conditioned to ride 5-10 miles at a time, you can cover those distances easily with an electric assist, which is a great way to build endurance and confidence. That same survey found that 94 percent of non-cyclists rode daily or weekly after getting an e-bike.
Name a type of riding, and there’s an e-bike for that. If you have zero interest in an electric road bike, you may find yourself head over heels for a high-capacity e-cargo bike that can haul 400 pounds of stuff while still cruising at a cool 15 mph. E-bikes are available in fat, cargo, commuter, recreational, hardtail, full-suspension mountain, and even performance road bike styles. For proof, here are a dozen e-bikes we love for every type of cyclist.
|
|
|
Keyboard and mouse basics |
Posted by: fowjw558 - 08-17-2021, 02:41 AM - Forum: Welcomes and Introductions
- No Replies
|
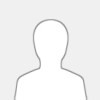 |
This article is about the introduction of the keyboard mouse PC item.
Using a keyboard
Whenever you use a desktop computer or laptop, you’ll probably use a computer keyboard. The most common kind is called a ‘QWERTY’ keyboard. QWERTY describes the top row of letters on the keyboard.
What a keyboard looks like
A keyboard is for putting information including letters, words and numbers into your computer. You press the individual buttons on the keyboard when you type.
The number keys across the top of the keyboard are also found on the right of the keyboard.
The letter keys are in the centre of the keyboard.
The symbol keys to the right of the letters include symbols such as the question mark and full stop.
The keys that surround the letters, numbers and symbol keys on the left, right and bottom of the keyboard help you to choose where and how you type.
There are several types of keyboards, such as gaming mechanical keyboard, keyboard and so on.
Using the keys
When you open a document or click in a box to type, you will see a vertical flashing line. This is the cursor, it shows you where you are about to start typing on a page or screen.
Pressing the 'shift' key allows you to type capital letters and the symbols at the top of the keys.
The 'shift' keys are on the left and right of the keyboard, with the arrow pointing upwards.
For capital letters, hold down the 'shift' key and hold and type the letter.
For symbols at the top of a number key, press down the symbol key and then type the symbol. You can use the 'shift' key to type any symbol at the top of a key.
The 'caps lock' key allows you to write in capital letters. To turn it on, press it once and type. To turn it off, press it again.
Putting in spaces, moving your cursor and deleting text
The 'space bar' puts a space between words. Press it once to put in a space.
The 'tab' key puts a bigger space between words. Press it once to put in a space.
The 'enter' key moves your cursor down a line.
The 'arrow' keys allow you to move your cursor in all directions on the page or screen - up, down, left and right.
To delete your typing you need to put your cursor to the right of a word. Press the 'backspace' button to delete your word. The cursor will move to the left and delete as it goes.
Using a mouse
There are lots of different styles of computer mouse, but most have a left and a right button.
To hold your mouse, rest your hand over it and put your index finger on the left button and your thumb resting on the side. The cable needs to be pointing towards the computer. The mouse needs to always be in contact with a mouse mat, desk or hard surface.
You use your mouse to move the cursor around the screen. The cursor changes, depending on what you are doing on the computer. As an arrow you use it for moving and selecting things, as a hand for clicking on links when you are on the internet and it becomes an hourglass when you are waiting for the computer to do something.
Single clicking
You single click with the left mouse button to select things. Just quickly left click and then let go of the button.
Double clicking
You double click with the left mouse button to open things, such as a folder. You need to double click quickly, think about the ‘knock, knock’ you do on a door.
Drag and drop
Drag and drop is when you move something from one place to another.
First select the item with the left mouse button and keep the button pressed down. Then move the mouse and the item on screen will move with the cursor. When you have the cursor and item in the position you want, release the left mouse button.
The item will now be dropped to where the cursor is positioned on the screen.
You use drag and drop to move things around your computer, such as files between folders.
Right button
If you ever accidently click the right mouse button, a list of computer commands will appear. To remove the list just move the mouse and single click the left button.
Laptop trackpad or touchpad
Laptops can have a built in mouse within the keyboard. This is operated by finger touch. This specialised surface is used instead of a mouse and needs only very short finger movements to move the cursor across the display screen.
Improve your computer skills
Why not develop your computer skills - there are courses for beginners and beyond. These range from free online learning through to training, which can lead to qualifications.
While the gaming keyboard mouse industry has almost completed its quest for true gaming perfection, many of today’s gamers still find themselves asking that age-old question – should I choose a wired or wireless gaming mouse?
It’s a question that has plagued many over the last couple of decades, with consumers struggling to decide whether or not the benefits of wireless technology actually outweigh the reduction in gaming performance they sadly lose.
That being said, thanks to huge leaps forward in technology, the gap between wired vs wireless gaming mice has now become much less apparent. Today’s mice come equipped with new technologies that offer Lightspeed connectivity and an almost unlimited amount of battery life – making wireless gaming mice more popular than ever before. Furthermore, wireless mice now bring fantastic gaming performance to the table that really does give their wired alternatives a run for their money.
With the current batch of high-performance gaming mice giving consumers the ultimate headache when deciding which one to choose, we thought we’d whip this article together explaining the differences between wired and wireless gaming mice. We’ll be looking at the main specifications that affect gaming performance, the main differences between the two technologies, and whether or not you should choose wired or wireless for your next gaming mouse purchase.
So, with that in mind, let’s waste no further time and dive straight into it
THE BEST WIRED OR WIRELESS GAMING HEADSETS TO BUY
If you’re shopping for a gaming headset, you have a lot of options. While there are some great ones out there, it’s easy to pay too much, to accidentally purchase a headset that doesn’t work with your desired console or platform, or to get one that’s just uncomfortable. Knowing a thing or two about headphones might aid in your search, but gaming headsets have only gotten more complicated to shop for — especially the wireless ones.
For instance, wireless headsets made for Xbox operate without a dongle via Microsoft’s proprietary wireless protocol. They’ll only work on Xbox consoles or a PC that has one of Microsoft’s Xbox Wireless Adapters plugged in, in most cases. Conversely, if you get a multiplatform wireless headset that includes a 2.4GHz wireless dongle, it’ll likely work on the likes of the PS4, PS5, Nintendo Switch (when plugged into the console’s TV dock), and PC — but not Xbox. It’s best to buy the headset that mentions support for your preferred platform(s) explicitly, or else there’s a good chance you’ll run into some compatibility issues. Of course, you can eliminate most of the guesswork by buying a wired gaming headset instead.
This guide focuses on newer options that you’re more likely to encounter at stores as opposed to older models that, while possibly still being worthy of your money, are often tougher to find affordably and easily online. Also, just to mention it at the top, I have a large-ish head and that factor obviously played a major role in how I judge the comfort of these headsets.
You’ll find a few categories below, including the best multiplatform wireless headsets that are compatible with PC, PS4, PS5, and Nintendo Switch via its dock, the best Xbox wireless gaming headsets, the best PlayStation wireless gaming headsets, and the best wired gaming headsets that support the widest variety of platforms, from console controllers to phones, tablets, and VR headsets that feature a 3.5mm headphone jack.
If you have ever found yourself searching for a new pair of headsets, you have encountered the overwhelming variety of choice that you are nowadays faced with. Over-the-ear, on-the-ear, noise-cancelling, wireless, wired… the market seems to be oversaturated with terms, that needs further clarification.
So, how to choose the best headset?
To start with, there is no such thing as the best headset. Rather, it all depends on your usage and needs. How much time you spend on the phone, what kind of job you do, whether you work in an open office or what type of phone you’re using – all of these factors will influence your choice.
But let’s take one step at a time and focus on how to choose between wired and wireless headsets in the first place. For that purpose, we will need to look at different work styles, as they play a key role in your choice between wired and wireless headsets.
If you spend most of your time at your desk, you are probably what is generally defined as desk worker. You are often on calls with customers, colleagues or other stakeholders. You probably use desk phones most, but Microsoft Teams or Skype for Business are also part of your daily routine. For you, clear audio has the utmost importance – there is no place for questions like “What? Could you repeat, please?”. Perceiving the slightest change in the tone of voice of your caller can make a great difference in your job. You don’t want to worry about your equipment – it should work easily and instantly, allowing you to simply focus on the call and the customer.
If you find this description to be an accurate representation of your workstyle and needs, you will then be satisfied with wired headset.
Wired headsets often offer a higher definition audio quality than wireless headsets, while also minimizing the risk of interferences that can happen with wireless signals. This guarantees perfectly clear audio. At the same time, being plug-and-play, wired headsets can be put in use in no time – avoiding wasting precious seconds in setting up and connecting your device.
But what if you would consider yourself a road warrior instead? You spend most of your time on-the-go – in your car, on public transport – running around to different meetings in the city. Being able to make use of the time you have in between meetings is of extreme importance to you. That is why you need a device that enables you to easily take calls from both, your PC and mobile, in the office and on-the-road. You need to be able to move quickly between working situations, while still hearing and being heard clearly.
Or maybe you’re a corridor worker. You spend most of your time working in the office, both at your desk and in meetings. You walk a lot around the office building, and you need a device that allows you to talk while freely roaming office corridors.
In both cases, a wireless headset would be more suitable for you.
Office headset give you the freedom to move as you like, walking or even running around without the risk of getting tangled in any cords – and still being able to hear and be heard perfectly. And with most devices nowadays being Bluetooth-enabled, you will be able to easily connect your wireless headset to both, your mobile and PC.
|
|
|
Insulation parts |
Posted by: fowjw558 - 08-17-2021, 02:38 AM - Forum: Welcomes and Introductions
- No Replies
|
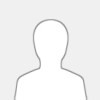 |
As a professional manufacturer of insulation parts. Our factory is equipped with 3,4 and 5-axis machining on a range of CNC Milling machines. One of our advantages is that we are not only offering insulation tube or insulation rod, but also secondary machining service for our customers. Therefore, we can help on cost down and shortening lead time.
Learn about the following insulation parts:
Epoxy Glass Tube
Epoxy Glass Tubes are highly economical insulating tubes that offer a combination of excellent mechanical strength and good electrical performance. Like our Epoxy Glass Rods, our Epoxy Glass Tube is capable of withstanding continuous temperatures up to 130oC (though other grades of material, such as our Isoval Tube, with higher temperature ratings are also available upon request).
The combination of electrical performance and mechanical strength offered by our epoxy glass tube allows them to often be utilised in the manufacture of insulating bushings as well as insulating sleeves. Yellow in colour, our Epoxy Glass Tube can be machined to tight tolerances and thin wall thicknesses.
Epoxy Fiberglass Rod
12 foot long epoxy fiberglass rod 11 16 diameter is made of high strength aramid fiber and glass fiber, impregnated with epoxy resin by pultruding under high temperature. It has ultra-high strength, excellent wear resistance, acid and alkaline resistance, corrosion resistance and other excellent high temperature performance characteristics. It is suitable for electrolytic aluminum plant, steel works, high temperature metallurgical equipment, ultra-high voltage electrical equipment, aerospace and aerospace fields, transformers, capacitors, reactors, high voltage switches and other high voltage electrical appliances.
CNC machining is a term commonly used in manufacturing and industrial applications. But exactly what is CNC? And what is a CNC machine?
CNC 101: The term CNC stands for 'computer numerical control', and the CNC machining definition is that it is a subtractive manufacturing process which typically employs computerized controls and machine tools to remove layers of material from a stock piece—known as the blank or workpiece—and produces a custom-designed part. This process is suitable for a wide range of materials, including metals, plastics, wood, glass, foam, and composites, and finds application in a variety of industries, such as large CNC machining, machining of parts and prototypes for telecommunications, and CNC machining parts, which require tighter tolerances than other industries. Note there is a difference between the CNC machining definition and the CNC machine definition- one is a process and the other is a machine. A CNC machine is a programmable machine that is capable of autonomously performing the operations of CNC machining.
Subtractive manufacturing processes, such as CNC machining, are often presented in contrast to additive manufacturing processes, such as 3D printing, or formative manufacturing processes, such as liquid injection molding. While subtractive processes remove layers of material from the workpiece to produce custom shapes and designs, additive processes assemble layers of material to produce the desired form and formative processes deform and displace stock material into the desired shape. The automated nature of CNC machining enables the production of high precision and high accuracy, simple parts and cost-effectiveness when fulfilling one-off and medium-volume production runs. However, while CNC machining demonstrates certain advantages over other manufacturing processes, the degree of complexity and intricacy attainable for part design and the cost-effectiveness of producing complex parts is limited.
While each type of manufacturing process has its advantages and disadvantages, this article focuses on the CNC machining process, outlining the basics of the process, and the various components and tooling of the CNC machine (sometimes incorrectly known as a C and C machine). Additionally, this article explores various mechanical CNC machining operations and presents alternatives to the CNC machining process.
Are you between jobs right now or an employer looking to hire? We've got you covered with our in-depth collections of resources for industrial job seekers and employers looking to fill roles. If you have an open position, you can also fill out our form for a chance to have it featured in the Thomas Monthly Update newsletter.
Overview of CNC Machining Process
Evolving from the numerical control (NC) machining process which utilized punched tape cards, CNC machining is a manufacturing process which utilizes computerized controls to operate and manipulate machine and cutting tools to shape stock material—e.g., metal, plastic, wood, foam, composite, etc.—into custom parts and designs. While the CNC machining process offers various capabilities and operations, the fundamental principles of the process remain largely the same throughout all of them. The basic CNC machining process includes the following stages: - Designing the CAD model
- Converting the CAD file to a CNC program
- Preparing the CNC machine
- Executing the machining operation
CAD Model Design
The CNC machining process begins with the creation of a 2D vector or 3D solid part CAD design either in-house or by a CAD/CAM design service company. Computer-aided design (CAD) software allows designers and manufacturers to produce a model or rendering of their parts and products along with the necessary technical specifications, such as dimensions and geometries, for producing the part or product.
Designs for CNC machined parts are restricted by the capabilities (or inabilities) of the CNC machine and tooling. For example, most CNC machine tooling is cylindrical therefore the part geometries possible via the CNC machining process are limited as the tooling creates curved corner sections. Additionally, the properties of the material being machined, tooling design, and workholding capabilities of the machine further restrict the design possibilities, such as the minimum part thicknesses, maximum part size, and inclusion and complexity of internal cavities and features.
Once the CAD design is completed, the designer exports it to a CNC-compatible file format, such as STEP or IGES.
CNC Machining Tolerances Tables
When specifying parts to a machine shop, it's important to include any necessary tolerances. Though CNC machines are very accurate, they still leave some slight variation between duplicates of the same part, generally around + or - .005 in (.127 mm), which is roughly twice the width of a human hair. To save on costs, buyers should only specify tolerances in areas of the part that will need to be especially accurate because they will come into contact with other parts. While there are standard tolerances for different levels of machining (as shown in the tables below), not all tolerances are equal. If, for example, a part absolutely cannot be larger than the measurement, it might have a specified tolerance of +0.0/-0.5 to show it can be slightly smaller, but no larger in that area.
|
|
|
Does the colour of the mug influence the taste of the coffee? |
Posted by: fowjw558 - 08-17-2021, 02:37 AM - Forum: Welcomes and Introductions
- No Replies
|
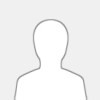 |
In experiment 1, the white travel mug enhanced the rated “intensity” of the coffee flavour relative to the transparent mug. However, given slight physical differences in the mugs used, a second experiment was conducted using identical glass mugs with coloured sleeves. Once again, the colour of the mug was shown to influence participants’ rating of the coffee. In particular, the coffee was rated as less sweet in the white mug as compared to the transparent and blue mugs.
Both experiments demonstrate that the colour of the mug affects people’s ratings of a hot beverage. Given that ratings associated with the transparent glass mug were not significantly different from those associated with the blue mug in either experiment, an explanation in terms of simultaneous contrast can be ruled out. However, it is possible that colour contrast between the mug and the coffee may have affected the perceived intensity/sweetness of the coffee. That is, the white mug may have influenced the perceived brownness of the coffee and this, in turn, may have influenced the perceived intensity (and sweetness) of the coffee. These results support the view that the colour of the mug should be considered by those serving coffee as it can influence the consumer’s multisensory coffee drinking experience. These results add to a large and growing body of research highlighting the influence of product-extrinsic colour on the multisensory perception of food and drink.
In Australia alone, around a billion cups of coffee are consumed in cafés, restaurants and other outlets each and every year. Even Britain, a nation famous for its fondness for tea, has, in recent years, seen a dramatic rise in its coffee consumption, with an estimated 70 million cups drunk each day. Given the economic incentive to keep consumers drinking coffee, café owners, restaurateurs, crockery designers and manufacturers ought, presumably, to be interested in anything that can help to enhance the multisensory coffee drinking experience for their clientele cf.
The idea behind experiment 1 came about serendipitously. During a conversation between the first author (GV) and a barista, the latter reported that when coffee is consumed from a white, ceramic mug, it tastes more bitter than when drunk from a clear, glass mug instead; note that these two mug types are amongst the most commonly used vessels to serve coffee in Australian cafés and restaurants. In the present study, we therefore sought to establish the validity of this claim which, to our knowledge, has not been described previously. Indeed, as recently highlighted by Spence and Wan, there is a paucity of research on the psychological impact of the receptacles that we use to drink from.
The notion that the colour of the receptacle/plateware can impact taste/flavour perception might relate to Piqueras-Fiszman et al.’s research putatively showing that colour contrast resulted in a red, strawberry-flavoured mousse presented on a white plate being rated as 10% sweeter and 15% more flavourful than when exactly the same food was presented on a black plate, see for an extension of this work; see for an explicit attempt to evaluate the colour contrast account. While contrast represents one plausible explanation for such results, it is important to note that there are also several other possible mechanisms (e.g., priming) that may explain the influence of product-extrinsic colour on taste/flavour ratings. Taking the principal of colour contrast one stage further, and given the conversation with the barista, it was proposed that brown may be associated with bitterness (or, perhaps, is negatively associated with sweetness). If taste were to be affected crossmodally by colour contrast, then coffee that is tasted from a white coffee mug should be rated as somewhat more bitter than exactly the same coffee when consumed from a transparent mug instead.
It is possible that another contrast mechanism (i.e., simultaneous contrast) might affect the perception of taste . Here, if light, opaque, milky brown coffee were to be associated with bitterness, then a light blue mug/surrounding should intensify the brown of the coffee because blue is brown’s complementary colour . This, in turn, would be expected to elevate ratings of bitterness relative to the same coffee when served in a transparent mug. Some famous examples of the use of simultaneous contrast are Heinz’s™ use of a greenish-blue can to set off the red-orange colour of their beans and sauce and Cadbury’s™ use of purple packaging to enhance the colour of their chocolate.
Although many studies have been published on colour-flavour interactions over the years, see for a review, very little has been published to date specifically looking at crossmodal influences on the perception of coffee. This absence is surprising given, as we saw above, how many cups of coffee are drunk every day. In terms of the limited research that has been conducted specifically in this area, Favre and November offered 200 people coffee from four different jars, i.e., brown, red, blue and yellow. Seventy-three percent of the participants reported that the coffee served from the brown container was too strong, whereas 80% of women felt that the coffee served from the red receptacle had a richer, fuller aroma. The blue jar suggested a milder aroma to most and the coffee in the yellow container was rated as coming from a weaker blend.
Meanwhile, Guéguen and Jacob had 120 people drink coffee from four different coloured cups (blue, green, yellow and red). The participants had to indicate which coffee was the warmest (in terms of its temperature). Thirty-eight percent of the participants reported that the coffee served from the red cup was the warmest, followed by yellow (28.3%), green (20.0%) and, finally, blue (13.3%). Note that these differences were statistically significant. In summary, the colour of the cup can be added to the list of factors that have now been demonstrated to influence various aspects of the coffee drinking experience. This list also includes whether or not the coffee had an eco-friendly origin and any branding cues.
Based on previous work and anecdotal evidence, we explored the impact of the colour of a receptacle on people’s coffee drinking experience. If extrinsic cues influence a consumer’s experience of coffee, and if taste is affected by contrast effects, coffee tasted/drunk from a white mini mug should be rated as more bitter than from a clear mug instead. Given Piqueras-Fiszman et al.’s and Stewart and Goss’work with strawberry mousse and cheesecake, respectively, we thought that it is possible that the brown-bitter association might be enhanced by colour contrast. However, and with regard to the colour of coffee and the colour of the immediate surroundings against which it is presented, simultaneous contrast might be at work. Specifically, the brown of the coffee may be intensified if the coffee is served from a light blue mug. It should be noted that factors other than contrast effects can influence perception. For example, the cup in which the coffee is served may affect us as a function of our perception of the general properties of the cup (i.e., cheap vs. expensive , flimsy vs. strong). We have attempted to control these potentially confounding variables in the present study. That said, and to borrow from Piqueras-Fiszman et al., if the colour of the mug affects the way in which people perceive the colour of the coffee, and the colour of the coffee affects the perception of flavour, then the colour of the mug (and any contrast effect that it elicits) would be expected to influence the perceived properties of the coffee (e.g., bitterness).
The travel mug type exerted a significant influence on participants’ ratings of the perceived intensity of the café latté, F(2,15) = 4.78, p = .025 (see Figure Bonferroni-corrected post hoc tests revealed that the café latté was rated as significantly more intense (p = .026) when served from the white, ceramic mug than when served from the clear, glass mug. None of the other comparisons reached statistical significance. The mug type failed to exert any influence on participants’ ratings of the other attributes of the café latté (see Table .
The white mug enhanced the perceived “intensity” of the coffee flavour relative to the transparent mug. Our hypothesis was that a crossmodal association between brown and bitter exists and that bitterness, and possibly other attributes, would be enhanced by the colour contrast. Although there was no simultaneous contrast effect (i.e., coffee surrounded by its complementary colour was not rated as any more bitter than the coffee presented in either the clear or white mug), it is possible that colour contrast influenced the intensity of the coffee flavour in experiment 1.
The mug type exerted a significant influence on participants’ ratings of the perceived sweetness of the café latté, F(2,33) = 3.57, p = .040 (see Figure. Bonferroni-corrected post hoc tests established that the drink was rated as significantly less sweet (p = .041) when served from the white mug relative to the see-through, glass mug or the blue mug. None of the other comparisons reached statistical significance. The mug type failed to exert any influence on participants’ ratings of the other attributes of the café latté (see Table.
Crossmodal influences refer to the effects that information from one sensory modality can have on the perception of information from another. The main issue explored in this study was whether consumers’ perception of a warm café latté would be influenced by the colour (transparent, white or blue) of the mug from which it was served and consumed. Our results clearly demonstrate that the colour of the mug does influence the perceived taste/flavour of coffee.
In the two experiments presented here, it was hypothesised that a crossmodal association between brown and bitter exists and that bitterness, and possibly other attributes, would be enhanced by the colour contrast. In experiment 1, the white mug was found to enhance the perceived “intensity” of the coffee’s flavour relative to the transparent mug. However, given slight differences in the mugs used in experiment 1, we decided to conduct a follow-up study with identical mugs. Experiment 2 revealed that the white mug diminished the “sweetness” of the coffee flavour relative to the transparent and blue mugs.
Given that ratings associated with the transparent glass mug were not significantly different from those associated with the light blue mug in either experiment, it seems as though simultaneous contrast cannot be used to explain the observed results. However, it is possible that colour contrast influenced the intensity/sweetness of the coffee’s flavour. That said, an alternative mechanism (i.e., sensation transference) might also be at play in experiment 1 In short, implicit judgments regarding the intensity of the white mug may be transferred to the coffee causing it to be perceived as more intense than the coffee served in the other mugs. Given Favre and November’s finding that people report coffee served from a brown container to be too strong (i.e., too intense) and our results from experiment 2, it seems unlikely that (1) people would hold an implicit “intensity” judgement for both white and brown colours and (2) ‘sensation transference’ is the mechanism at work here. Similar to an argument made by Piqueras-Fiszman et al., it seems more plausible to suggest that the white background of the coffee mug may have influenced the perceived brownness of the coffee and that this, in turn, was what influenced the perceived intensity (and sweetness) of the coffee. As we replicate the basic finding that the colour of the mug makes a difference, the correspondence between the visual appearance of the mug and aspects of the flavour suggests that colour contrast mechanisms may be at work here.
Two findings are worth highlighting here: (1) that there is a general trend in experiment 2 towards an increased “intensity” rating (i.e., ratings of intensity were greater for coffee served in the white mug), but this effect failed to reach significance, and (2) the significant intensity and sweetness results of experiments 1 and 2, respectively, might be connected. Note that consumers, as compared to baristas, appear to blur the distinction between ‘intensity’ and ‘bitterness’. Dijksterhuis has suggested that because of the use of the word ‘strong’ in advertising, consumers often confuse a coffee’s strength or intensity with its ‘bitterness’—in fact, visual inspection of Tables 1 and 2 reveals that there is a trend in bitterness ratings that mirrors intensity ratings that would support such a view. Furthermore, any reduction in the “sweetness” of the coffee when presented from a white mug might also be expected to signify an increase in perceived bitterness (or strength). As mentioned above, Koch and Koch also found that brown, amongst other colours, was negatively associated with sweetness.
Marketers such as Favre and November have reported an effect of jar colour on perceived coffee aroma. Coffee served in a blue jar was more often judged as having a milder aroma than the same coffee when presented in jars of other colours. By contrast, we observed no effect of blue on aroma or any of the other attributes. Favre and November seem to have documented a simultaneous contrast effect for “mildness” which might be considered to lie at the opposite end of an “intensity” rating scale. Elsewhere, researchers have demonstrated that the colour of plastic vending cups influences people’s perception of hot chocolate, such that orange (with a white interior) enhanced the chocolate flavour, as did dark-cream coloured cups which also enhanced sweetness and aroma . Although our findings differ in their details from those of Piqueras-Fiszman and Spence , they nevertheless concur at a more general level in demonstrating the importance of the colour of the container/plateware on the consumer’s experience of a variety of food and drink products, see also. Our results also help to address the relative paucity of literature on the influence of drinking receptacles as recently highlighted by Spence and Wan .
|
|
|
What is a Filter Press and How Does it Work? |
Posted by: fowjw558 - 08-17-2021, 02:35 AM - Forum: Welcomes and Introductions
- No Replies
|
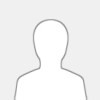 |
A filter press is one of the oldest and most trusted pieces of dewatering equipment. It’s used for wastewater treatment across a variety of industries and applications. A filter press works by separating out solids from liquids, removing impurities, and suspended solids from industrial wastewater. This allows plant managers to easily handle and dispose of waste while returning clean water to their systems.
Filter presses separate liquids and solids. Specifically, the filter press separates the liquids and solids using pressure filtration across a filter media. Afterward, the slurry is pumped into the filter press and then dewaters under pressure.
Basically, the concentrate filter press design is based on the dewatering volume and type of slurry. ChemREADY is an expert in liquid and solid separation and offers a wide range of filter press types and capacities to suit specific application needs for trouble-free, economical dewatering.
The origin of the filter press dates to around the mid-19th century in the United Kingdom, where a rudimentary form of the press was used to obtain vegetable oil from seeds. However, it wasn’t until major developments in the mid-20th century that engineers were able to develop the world’s first automatic horizontal-type filter press.
It’s this long history of advancements that’s allowed the filter presses of today to achieve significantly lower energy and maintenance costs compared to their belt press and centrifuge counterparts. In fact, the total operating filtration cost for a filter press can easily be 1/6 the cost of what it would be for a belt press or centrifuge.
While there are many different styles of modern filter presses, the plate and frame filter press are one of the oldest and most tested types of dewatering equipment available. You can read more on this type of filter press, along with a more detailed comparison between different types of dewatering equipment, in our Water Facts blog on How Industrial Wastewater Pretreatment Works.
Filter presses are especially useful as the leftover solids are cheaper and easier to move than the entire slurry. With the clean water that filter presses return, plant managers can discharge that to their local municipalities, watersheds or use the water in their own closed-loop systems, creating highly efficient processes.
Without a filter press or similar pieces of dewatering equipment, a settling pond is often the first option for water treatment. Not only do ponds require a large amount of real estate to use, but they also lose their ability to clean water over time as the solids that you remove build up in the pond water. This gives ponds an unfavorable long-term ROI as dirty water will eventually start coming back into your process unless you dredge the pond or make a new pond. At ChemREADY, we advise the use of a filter press and other dewatering equipment over a pond in most applications.
During the fill cycle, the slurry pumps into the filter press and distributes evenly during the fill cycle. Solids build up on the filter cloth, forming the filter cake in the void volume of the plate. The filtrate, or clean water, exits the filter plates through the ports and discharges clean water out the side of the plates.
Filter presses are a pressure filtration method. As the filter press feed pump builds pressure, the solids build within the chambers until they are completely full of solids. This forms the cake. The filter cakes release when the plates are full, and the cycle is complete. Also, many higher capacity filter presses use fast action automatic plate shifters which speeding cycle time. Matec specifically designs their filter presses for fully automatic, 24-hour operation in a harsh environment such as mines or chemical manufacturing plants for wastewater treatment.
While the various styles of filter presses work differently, they all operate under similar principles. Slurries of water mixed with solids are pumped into the press by using a feeding pump. Once inside the press, pressure – often from a centrifugal pump or similar device – pushes the slurry through chambers made of filter plates. This removes impurities from the water as “filter cakes” of solids build up on the machine’s filters.
Once the chambers of a filter press are full, its filtration cycle is complete, and the machine releases the filter cakes. These cakes are easily removed, allowing you to filter your water at high efficiencies. In filter presses, fast action automatic plate shifters may be used to help speed up cake removal and cycle time. In harsher environments where continuous operation is required – like in mining processes or chemical manufacturing plants – a fully automatic filter press design is needed to handle the 24-hour workloads.
To get the best performance out of your filter press, the cloth of the filter should be specifically designed for your application and the types of solids that you are filtering.
The following can also be customized to fit your individual needs:
In addition to these, you can use additional systems such as cloth washing systems, drip trays, and cake shields to further increase filter press performance and functionality. Ultimately, each filter press should be designed based on the expected volume and type of slurry that it will be handling.
Since filter presses work using pressure, equipment that increase pressure through the means of high-pressure technology are great for optimizing your dry tailings filter press system. That’s the secret to success for Matec® filter presses, which use pressures of 21 to 30 bar to handle even the most difficult and hard to treat slurries, no matter the sector or application.
Filter presses can be built in a wide range of sizes, from small, lab-scale presses, to those with much larger capacities, such as those with 2000×2000 mm plates.
While filter presses are great pieces of dewatering equipment, they are best used on a slurry made up of about 50-60 percent solids. Lower solids concentration requires running the water through a clarifier first.
Clarifiers are best described as large settling tanks, preferably used in the initial dewatering phase. Here, water can enter at a much lower solids concentration, typically around 5-10 percent solids. Using gravity and polymers, clarifiers cause solids to build up at the bottom of the tank, where they can be discharged as sludge.
The two main types of clarifiers are the horizontal rake style clarifier and the vertical deep cone clarifier. Vertical deep cone clarifiers use the principle of static decantation for a natural precipitation of solid material, while horizontal rake style clarifiers use a rake mechanism that stirs the sludge through rotation. Determining which type of clarifier is best for you depends on your clarifying needs, driven by maintenance costs, material types and solids requirements. You can read more on the two different types of clarifiers in our Water Facts blog, Deep Cone vs. Rake Style Clarifiers.
When used in combination with each other, a clarifier and chemical filter press can recover 90-95 percent of your water as clean water. The remaining water will discharge with the solids from the filter press.
Here at ChemREADY, our team of water treatment experts can help bring your dewatering efforts together with a total water treatment that optimizes your systems. We can analyze your water from a chemical perspective to find the right flocculants, coagulants, and pH balancers that we can used to treat your water before it goes through mechanical separation. This helps to optimize the performance of your clarifiers and filter presses, giving you a better and more efficient total water treatment.
Apart from our chemical products, we also can help get you setup with the best dewatering devices, including the Matec filter press.
Compared to standard filter presses, the Matec filter press offers: - Complete treatment with real automatic washing
- Fully automated systems
- Remote monitoring and assistance
- High-pressure technology (HPT) that works at 30 bar
- Open filtrate design, which allows for the simple and rapid identification of bad filter cloths
- Perfect cake discharge with gasser shakers
Are you running a smaller business and wondering if a high efficiency filter press is right for you?
Read our useful Water Facts blog Can my Small Operation Afford a Filter Press? to learn more.
The Filter Press is one of the oldest filtration technologies still in use today. It was first developed in the mid 1800’s. Unlike vacuum filters, which operate continually, the Filter Press and many other pressure filters run in batches. After a batch of slurry has run through the filter, and the filtrate drained out, it must shut down, open the filter pack, and discharge the solid cake.
The components of a featured filter press include the frame or skeleton and the filter pack. The filter pack consists of plates, sometimes frames, and filter media.
Stationary Head- The side of the frame without the closure system has a head that aligns with the filter pack. It is also known as the fixed head. It has a feed hole for the slurry to enter and drain hole for filtrate to exit.
Follower Head- The hydraulic ram pushes the follower head, or thrust head against the filter pack. There are no feed or drain holes on this head.
Closure System- A hydraulic ram is used to press the plates together and hold the filter together during operation. It creates a positive seal and prevents leaks.
Sidebars- The smelting washing filter press plates rest on sidebars to keep alignment and bear weight.
Pump- Necessary to create the pressure which drives the process, it is usually a positive displacement pump or a centrifugal feed pump.
Extra Features- Newer models can include additional components like plate shifters, spray bars, and automatic cake dischargers.
While cotton was the main filter media, in the 1960’s synthetic fibers created better performing and longer lasting press cloths. National Filter Media has a wide variety of fibers, and weave types. Please contact Shane in the link on the Navbar if you would like to ensure that the cloth your filter uses is the best one for your application.
Here is a list of configurations for Media.
Drape over cloth- Twice the length of a plate, a Drape Over Cloth sits on top of the plate and lays down each side. It can be held in place by small nubs, or “dog ears”.
Drape over paper- If cake has a tendency to blind filter media after one batch, a filter paper can be draped on top of the cloth. When the Filter Press opens to discharge, the paper is thrown out with the cake.
Duplex cloth- Two separate cloths, each the size of a plate’s single face, are sewn to a gusset that covers the feed hole that runs through a plate. The top and side edges of the cloth either have grommets or Velcro to secure both side of the cloth to the plate.
CGR Cloth- This duplex cloth is shaped to fit in the groove of a CGR Plate. There is a rope sewn into the cloth’s border that gets caulked into each side of the plate.
As filtrate passes through the filter cloth it collects on the plate panel and drains into outlet holes on the corner(s) of the panel. The outlet holes have a channel that goes into the adjacent corner eye. The channel runs between the packing surfaces. Another function of the system is to allow the cake to be dried “blown down” by compressed air. The manifold piping at the end of the press can be valved to let air into the even numbered plates pushing the liquid thru the cloth/cake/cloth out the odd numbered plates. Sometimes particles of precoat and bodyfeed pass through the filter cloth and become trapped within the drainage channels plugging or partially blocking them. It can be easy to overlook, since you can’t see into the channels unaided.
The plug likely occurs after a filter cloth tear or if the filter media is too permeable for the precoat and body feed used. The best time to check is when you notice a chamber has not formed a dry, firm cake as it usually does. If some chambers in the filter pack form great cakes and others form wet partial cakes, this could indicate which plates are plugged.
[url=http://www.getchemready.com/contact-us/][/url]
|
|
|
All You Need to Know About GFCI Outlets |
Posted by: fowjw558 - 08-17-2021, 02:33 AM - Forum: Welcomes and Introductions
- No Replies
|
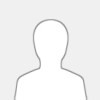 |
When it comes to electricity, safety has always been a major concern, but thanks to the development of ground fault circuit interrupter GFCI outlet (GFCIs), the risk of being severely shocked or electrocuted is greatly reduced. According to the Electrical Safety Foundation International (ESFI), electrocutions are down 83 percent since the 1970s when GFCIs were introduced. These quick-to-react outlets are required by law in new home construction, and it’s a good idea to put them in older homes as well. Read on for must-know info on GFCIs—what they are, how they work, and where to install them.
In your home, the flow of electricity is contained within wires covered with rubber- or plastic-based insulating material. When everything goes as planned, the electrical current runs safely through the insulated wires to switches and wall plate outlets and on to the many appliances and gadgets we take for granted today. But in its raw state, electricity has a “mind” of its own, and left to its own devices—as evidenced by most lightning strikes—it makes a beeline for the ground.
A ground fault is the occurrence of electricity taking an unintended path to the ground. It occurs when the electrical current escapes the insulated wires, as a result of a damaged cord or faulty wiring, and flows through a different conductor. If that different conductor is a human being, the result can be a serious electrical shock or electrocution. Because water is an excellent conductor of electricity, the risk of a ground fault occurring is greater in areas of your home where water is commonly used, such as near a kitchen sink.
The singular purpose of a new GFCI outlet is to prevent electrical injury to humans, something regular outlets are not equipped to do. A standard household outlet features two, three-prong plug-in slots, while a GFCI outlet features the same plug-in configuration plus two buttons on its face: a “TEST” button and a “RESET” button. The rules requiring the installation of the GFCI outlets in new construction has expanded over the years to include more applicable locations:
Normally, electrical current flows at a uniform rate through wiring, but when a ground fault occurs, the flow of electricity surges as it jumps to the unintended conductor. A GFCI outlet contains a sensor that monitors the flow of the electrical current through the wires, and when it senses a ground fault (in electrical terms, “fault” means any variation from the normal current), the GFCI, which also contains an internal switch, shuts off the flow of electricity in the outlet.
While you may still receive a painful shock, the South America GFCI outlet will prevent a prolonged surge of electricity, the type that injures and kills. A standard outlet, like the type in your bedroom, doesn’t have a sensor.
The National Electric Code (NEC) requires the installation of GFCI outlets in new construction in areas where electrical outlets are in close proximity to water. Older homes are not required to have GFCI outlets unless the wiring is being updated, but it’s a good idea to install them anyway.
The NEC requires GFCIs on all exterior and bathroom receptacles (another term for outlets). GFCIs are also required on all receptacles serving kitchen countertops. In laundry rooms and utility rooms, GFCIs should be installed on outlets within six feet of sinks, washing machines, and water heaters. They should also be installed within six feet of a wet bar and in garages and unfinished basements.
In bedrooms, living rooms, and other areas where water fixtures are not found, regular outlets are fine—and they are still installed in today’s new homes. The ESFI estimates that approximately 43 million homes in the U.S. still do not have GFCIs installed in “wet” rooms, and notes that as many as 47 percent of today’s electrocutions could be prevented in older homes if GFCIs were installed.
A DIYer with basic knowledge of electrical wiring may be able to replace an existing outlet with a decorative GFCI plate (instructions below), but only when swapping out a three-prong outlet—two plugin slots and a hole. Outlets with only two slots and no third hole indicate the presence of older wiring that should only be replaced by a licensed electrician.
The other caveat is that only outlets connected to three wires are suitable for DIY replacement. Outlets with three attached wires (remove the outlet plate to determine the number of attached wires) indicate that the outlet is located at the end of an electrical circuit (a wiring loop that starts and finishes at the breaker panel). An outlet with five attached wires is located in the middle of an electric circuit, and the wiring process is more complicated—only a licensed electrician should replace those outlets.
Replacing an existing outlet at the end of a circuit (as explained above) is not particularly difficult, but the task requires some experience. You should understand how outlets are wired and how electrical current travels from the breaker panel through each electrical circuit (wiring loop) in your home. Some communities prohibit homeowners from doing their own wiring, so check with your local building authority before you start.
During the recent 2020 code review, panel members of the National Electrical Code (NEC) approved changes to ground fault circuit interrupter (GFCI) protection. Those changes dramatically reduce the dangers associated with electrical hazard and shock. The most significant change is the increase of amp protection ratings across all receptacle outlets, both indoor and outdoor, wherever GFCI protection is required.
The 2020 change
Code-making panel 2 (CMP 2) updated text to read, “All 125-volt through 250-volt receptacles installed in the locations specified in 210.8(A) (1) through (11) and supplied by single-phase branch circuits rated 150 volts or less to ground shall have ground fault circuit interrupter protection for personnel.” In layman’s terms, the NEC removed amp values across all amp-rated receptacle outlets requiring GFCI protection in the areas listed in this section.
The rationale for change
NEC 2017 language only accounts for 15- and 20-amp receptacle outlets for dwelling units. During 2020 code review meetings, panel members agreed that hazards always exist; if 15- and 20-amp receptacle outlets present a hazard, that hazard also exists on 30-amp and higher receptacle outlets. However, it was difficult to understand the likelihood of a hazardous occurrence when weighed against expanded requirements. Recent home-based electrocution accidents – a 10-year-old girl behind an energized appliance, a child in Oklahoma retrieving a pet behind a clothes dryer, a 10-year-old Houston boy playing hide and seek — helped panel members realize the need for change. In light of these tragic events, we now have a requirement that sets a higher standard across more areas of the Code, though there are some exceptions discussed later in this blog.
What might the future hold?
The NEC mandates GFCI protection in many areas of the home: bathrooms, garages, outdoor receptacles, crawl spaces, basements, kitchens and anything within six feet of a sink or water source. While that may seem like a lot, the entirety of a home is not covered. The reality is when people have a problem with a tripped circuit, it's entirely possible they’ll use an extension cord to plug into a receptacle outlet that's not GFCI protected. Doing so does nothing to eliminate the original hazard potentially caused by the device in use. I hope that NEC members account for the human factor and require GFCI coverage throughout the home during the next code review.
The 2020 change
The NEC expanded GFCI protection for dwelling units with basements both finished and unfinished.
The rationale for change
Often afterthoughts that present unique hazards, basements are typically not as well maintained as other areas of the home. Further, environments are often wet and damp, and moisture is a great conductor. These code updates help ensure that accidents due to factors such as leakage current and contact with water are considerably lessened or eliminated.
What might the future hold?
Many rooms in a home are already required to have GFCI protection. While it feels like the most logical code progression, others in the industry still pushback on requiring GFCIs throughout a home claiming financial concerns or installation problems. As with the parental language update, I believe this code change can inspire discussions to include GFCIs throughout the home.
The NEC expanded GFCI protection under Article 210.63(A) for HVAC equipment and Article 210.63(B) for indoor service equipment and indoor equipment requiring dedicated space.
The rationale for change
Equipment location is at the crux of this update. While HVAC equipment in the basement is covered now that all basement circuits are GFCI protected, HVAC equipment located in attics and other areas would likely not have GFCI protection. CMP 2 recognized that many HVAC areas are typically tight working spaces where technicians perform justified energized work (they can’t troubleshoot a de-energized circuit). In essence, the update assures equipment requiring service has a GFCI-protected receptacle outlet for ready access.
What might the future hold?
Because this is the NEC’s first venture into expanding 210.63, I expect some inspectors and contractors may not see eye to eye on code language. Industry discussions across the country and during future review cycles will help the NEC make future improvements.
The NEC updated the Code for outdoor electrical outlet plates supplied by single-phase branch circuits rated 150 volts to ground or less, 50 amps or less. Key to this update: it extends beyond receptacle outlets to include all outlets. Now all hard-wired equipment falls under the Code’s purview.
The rationale for change
One downfall of the electrical business is that it’s more reactive than proactive, with accidents often the catalyst for change. Numerous incidents inspired this code change, including an accident involving a 12-year-old boy who jumped over a fence and touched an AC condenser unit with an electrical fault. The outer metal housing was electrified and the child was fatally electrocuted immediately upon coming in contact with the condenser and fence simultaneously.
What might the future hold?
GFCI technology is unforgiving in that it’s built to detect even the slightest power variance, and when expanded to include outlets impacting new types of loads, questions arise. With GFCIs installed, leakage-current trips may be near constant, rendering large equipment unusable. In the future, I hope industries rethink products with acceptable leakage current, hertz and frequency values to reduce future compatibility issues.
Further, this change will likely spur discussions related to current GFCI requirements focusing only on receptacle outlets. Hardwiring equipment does not eliminate the electrical hazard. I venture someone will propose public inputs during the next code-review cycle to
The NEC reviewed all locations with a GFCI requirement and aligned with Article 210.8. Updates were made in many locations to include text, such as “in addition to the requirements of 210.8” and similar, to clarify language and eliminate misinterpretation.
The rationale for change
The NEC included Article 210.8(B) for other than dwelling units in 1993. Before its inclusion, builders relied on requirements in later chapters of the Code (chapters five through seven), for safety guidance. For example, RV Park GFCI requirements added in 1978 aligned with 210.8’s 15- and 20-amp receptacle outlet GFCI protection philosophy at that time. NEC 2017 created some confusion when 210.8(B) increased GFCI protection requirements beyond 15- and 20-amp receptacle outlets for other than dwelling units. This presented a challenge: a chapter two requirement applied a generally wider level of GFCI protection. This conflicted with chapter five, which has less coverage of GFCI protection.
The correlating committee recognized similar conflicts exist across industries and formulated a task group that challenged every code panel to look at their GFCI requirements and attempt to align them with 210.8’s 50-amp increase.
What might the future hold?
Each code panel performed their review; some made changes, others did not. There is room for discussion in future revisions of the Code regarding shock hazards in the special other than dwelling unit applications. I believe the NEC will soon increase its focus on GFCIs and hopefully add clarity as each application in chapters five through seven approaches GFCI protection differently.
While representatives in agriculture and RV industries have valid concerns about nuisance tripping, I believe the NEC should revisit Article 547 for agricultural buildings and Article 551 for RVs and RV parks to address valid shock hazard concerns and consider increasing GFCI protection to 50 amps.
The rationale for change
Farming and RV industries rely on circuits that operate at well over 20 amps, yet no safety requirements exist. Much of the equipment used in these industries can be quite old with leakage current a serious concern. In my opinion, the Code lacks parity in how safety requirements exist in some industries and not in others. That must change.
The studies needed to promote change exist. The University of Iowa and the University of Nebraska have uncovered many incidents where farmers lost their lives due to faulty agricultural electrical equipment. Further, RV “hot skin,” a situation where the entirety of an RV’s outer housing becomes energized due to electrical faults, can kill in an instant, as was the case when a young boy died when touching an RV. If RV parks and farms running 30- to 50-amp receptacles without GFCI protection is not deemed a concern worth addressing, how can anyone claim running 30- to 50-amp receptacles outside of dwelling units is a hazard? Common sense dictates both are hazards and change is necessary.
What might the future hold?
I appreciate that equipment compatibility issues on farms and at RV parks may require much time and financial capital to resolve. However, I cannot condone sitting idle as lives are lost. I hope a series of discussions during the next code review cycle inspires commissioning an NFPA Fire Protection Research Foundation study to further understand the implications of expanding GFCI protection beyond 15 and 20 amps in RV parks and farms. Let’s study the problem, understand the challenges and determine solutions that increase safety.
|
|
|
Pressure Transmitter |
Posted by: fowjw558 - 08-17-2021, 02:30 AM - Forum: Welcomes and Introductions
- No Replies
|
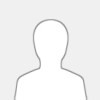 |
Pressure transmitters are a common and well understood technology especially within the petroleum, petrochemical, refrigeration and fuel gas markets and they are extremely economical compared to other technologies.
Pressure transmitters are a common and well understood technology especially within the petroleum, petrochemical, refrigeration and fuel gas markets and they are extremely economical compared to other technologies. If a level is to be made in an open vessel a pressure transmitter (PT) is placed at the bottom and the head pressure caused by the weight of the liquid can be used to calculate the height of the liquid. Differential pressure transmitters can be used on pressurised vessels using the same principles (9).
Level measurement using pressure transmitters cannot be deployed in primary separators as the change in temperature will impact the measurement, the change in density of the oil during operation will impact the measurement and any fluctuation of the oil/gas differential pressure control valve or pressure disturbances would also impact on the reading.
Portable dP gauges are used to monitor the dP across strainers, online densitometers, DB&B valves, prover interchange valves, and other devices. All pressure gauges shall be equipped with calibration stickers indicating the last test or calibration date and who performed the calibration. The calibration sticker should be clearly visible and constructed of a rugged material. All recordings on the sticker should be made with indelible ink. The dial gauge cover should be clear and abrasive resistant. The pressure gauge should be readable with permanent figures and markings and equipped with a blowout disc for safety. The scale shall be in graduations of no greater than 2 psig with longer graduations at each 5 psig and numbered at not greater than 10 psig intervals. The error at any point on the scale should not exceed ±2 psig. The maximum allowable working pressure (MAWP) of the dP gauge should be at least equal to the MAWP for the measurement facility.
A differential pressure transmitter is a device that translates physical force to an electrical signal. The most common type of force transducer uses a diaphragm, piston, bourdon tube, or bellows to sense the physical force and various strain/force-sensing devices to convert the deflection of the physical element to an electrical signal. Traditional strain-sensing devices include the following: capacitive cells, piezoresistive strain gauges, piezoelectric quartz material, and electromagnetic devices.
In the United States, companies such as Rosemount, Cameron/Barton, Foxboro, and Ultrasystems have provided transmitters that specialize in safety system pressure measurements. These transmitters may still function successfully on some iPWR designs, but many will have to be reengineered for different mounting configurations, size constraints, and environments. Many iPWR designers, when faced with a modification program, may choose to go with new technologies rather than modifying the old ones. The new technologies may offer advantages in size, redundancy, accuracy, and environmental resilience. Some of these new technologies include microelectromechanical system (MEMS) sensors, fiber optic sensors, and ultrasonic sensors.
In the optical fiber category, a company called Luna Innovations has developed and successfully tested fiber optic pressure sensors, like the one shown in Fig. 6.1, in a research reactor environment. These fiber optic pressure sensors have been shown to operate in radiation environments with flux levels much higher than those compatible with most electronic pressure sensors. With traditional technology, it is necessary to protect traditional electronic gauge pressure transmitter from harsh radiation conditions near the core; this requires the use of long pressure sensing lines, which limit the response time to pressure transients and increase the number of wall penetrations. Luna’s fiber optic pressure sensors are designed to operate in harsh environments. When these pressure sensors were combined with Etalon-based fiber optic temperature sensors providing temperature compensation, drift effects were minimized. The attractiveness of this technology for iPWRs is obvious, with the elimination of sensing lines, the minimization of penetrations, the small size of the sensor, the rapid response to pressure fluctuations, and the operability in high radiation fields. With these attributes, this technology bears merit for primary and secondary side pressure measurement (Dickerson et al., 2009).
Pressure or DPT transmitters have been used to measure liquid levels of open or pressurized tanks, respectively, with proper calibration taking care of the density value of the subject liquid. These types are used for level measurements of boiler drums, all heaters, deaerators, condenser hotwells, condenser surge tanks, and all dosing tanks.
For open tanks, a pressure tapping at a suitable location is connected through the impulse line, to the high-pressure port of the DPT with the low-pressure port open to atmosphere. The pressure (or DP) sensed by the DPT is proportional to the level with a known liquid density (ρ) and force due to (earth’s) gravity (g). With proper calibration, the potential transform can now be used as a level transmitter.
Regarding the pressurized tank or vessel, single-pressure tapping does not serve this purpose as it senses the pressure of the vessel and the pressure of the liquid level. To balance out the vessel pressure, another pressure tapping for sensing it is connected, through the impulse line, to the low-pressure port of a DPT so that the output will only be proportional to the liquid level only with known ρ and g.
Another new technology for pressure sensing is the polymer-derived ceramic MEMS sensor. At the forefront of this technology, a company, Sporian Microsystems, has developed a pressure/temperature sensor made to survive high temperatures (Fig. 6.2). This technology offers a solution for pressure sensing in iPWRs due to its hardy environment survivability and its small size. The small size allows for the installation of redundant units and the measurement of pressure at many points, possibly with fewer penetrations than traditional sensors.
These new technologies have attributes like small size, heat survivability, radiation hardness, fast response, and low maintenance. These attributes are highly valued in iPWR designs for obvious reasons.
The Series-211 differential absolute pressure transmitter can accurately measure positive, negative or differential pressure and send the corresponding 4–20 mA output signal to a recording system. It is not position sensitive and can be mounted in any orientation without compromising accuracy. It also features a power LED, so one always knows when the transmitter is operating. The compact, light-weight design makes installation simple and easy. Two inlets for the pressure connections are located on the front of the unit, labeled “High” and “Low”. For differential pressure measurement, the higher pressure should be connected to the “High” pressure port. For positive pressure, the “Low” pressure port should be left vented to atmospheric pressure. Periodically, it is necessary to recalibrate the gauge to maintain the accuracy. For “zero” gauge, the pressure connection needs to be removed from both pressure ports and to adjust the zero potentiometer until the output is 4 mA. To span the gauge, the full scale pressure to be applied to “High” pressure port and to adjust the span potentiometer until the output is 20 mA. The salient features of the pressure transmitter are compact design, LED power indication, 2-wire design, 4–20 mA output, ± 0.25% accuracy level, 0–90 mmHg pressure range, –25 °C to 70 °C operating temperature ranges, 2-wire output signal and 12–30 VDC power supply.
Drum level is measured by differential thermowell temperature transmitter installed in line with Figures XII/3.5-1(a,b). Note that for drum-level measurement a temperature-equalizing column has been used to ensure that in both limbs of DPTs temperatures are equal, meaning that the densities are equal. So far, the discussion has been about installation and making the two limbs’ temperatures equal. Now level is measured by because there is an incumbent pressure P1 at the top, which needs to be subtracted to get the level. So, finally, one is left with P1 at the top and P1 + pressure due to water head (P) on the other limb. Therefore DP = pressure due to water head, P = h × ρ × g.
For a particular place, g is always constant. So water head P varies with h (level) and density, which in turn depends on temperature. In the drum, incumbent pressure is due to saturated steam pressure, and for saturated steam for each pressure there is a particular temperature. Therefore, saturation pressure is chosen to compensate/correct the density effect. Temperature is a sluggish parameter, so pressure is chosen to compensate.
Degradation of the transmitter’s accuracy and response time (two uncorrelated phenomena) are the two most important consequences of ageing. Ageing caused by heat and humidity can cause the transmitter sealing materials to fail, allowing moisture to enter the transmitter housing. This can cause calibration shifts and high-frequency noise at the transmitter’s output, which can render the transmitter inoperable or unreliable. Though NPP I&C failure data indicates that calibration drift accounts for anywhere from 59% to 77% of all age-related failure in pressure transmitters (fow blockage, fatigue, and other factors accounting for the remaining age-related failures), a survey of the nuclear industry in the early 1990s showed that fewer than 10% of NPP pressure transmitters actually drift out of tolerance and that in a typical two-year fuel cycle only about 1–3% of transmitters suffer calibration failure.
The analog signal operates over a 4–20 mA range (0 to 5 Vdc with a 250 Ω high-precision pull-up resistor). For proper analog signal discrimination, the tertiary device should be equipped with at least a 12-bit ADC converter. Digital signals are preferred over analog signals for accuracy. However, the tertiary device must be able to communicate with the secondary devices using a common communications protocol. The status signals typically are used for indicating block valve status (fully open, fully closed, in travel), generating commands to obtain a sample (activation of sample extractor), and alarm status.
The transmitters should be equipped with a display of the current readings at the transmitter housing in appropriate engineering units. The transmitters should be equipped with both analog and digital output to the tertiary device.
For analog communications to the tertiary device, a 4–20 mA signal is preferred and requires a high-precision 250 Ω pull-up resistor (to convert from 0 to 5 Vdc). The dampening parameters should be turned off or set to its lower limit. For digital communications to the tertiary device, the update interval of the transmitter should be less than or equal to 1 second. The transmitters should be equipped with an appropriate communications protocol and the dampening parameters should be turned off or set to its lower limit.
The sensing lines that bring the pressure signals from the process to the transmitter can become partially or totally blocked due to sludge, boron solidification (PWRs), and other debris in the reactor coolant, causing sluggish dynamic performance in the transmitter. According to NRC data, blockages, voids, and leaks account for nearly 70% of the age-related problems in sensing lines. Nevertheless, the effects of ageing on response time are even less significant than the effects on calibration. The response times of 84% of transmitters tested in a 1994 study written by the author for Nuclear safety were unaffected by ageing. Of the remainder, only 4% delivered response times that could be considered failing.
|
|
|
The Best Razors, According to Barbers |
Posted by: fowjw558 - 08-17-2021, 02:22 AM - Forum: Welcomes and Introductions
- No Replies
|
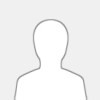 |
Getting the best shave comes down to having the best tools for the job. You’ll want to use a good shaving cream, of course, but the most important thing is to choose the right men's razor. A cartridge razor with disposable blades is the method most men learn first (and stick to), and replacement blades are available pretty much anywhere. An electric razor might be best for someone who wants to be as quick and efficient as possible. There are also safety razors, which have been around for more than 100 years and have recently surged in popularity because many feel they provide a better shave — plus, they’re more eco-friendly and economical. And there are straight razors, which are typically the domain of professionals, but may also appeal to passionate shavers because of the unique control they offer. The fact that countless different brands make different models of the same type of razor can make choosing the right one even more overwhelming.
To help folks find the best razors on the market, we asked 14 men’s-grooming experts — including ten barbers — about their favorites and combed through our archives to find other worthy options recommended to us before. The resulting selection of razors (below) features a style for pretty much everyone, including cartridge, electric, and safety razors, along with hybrid styles, and razors to use on sensitive skin. No matter which style of razor you choose, Tony DeAngelis, a co-owner of Blue&Black barbershop in Carroll Gardens, says there are two other important factors for getting a good shave: heat and stretching the skin. As he explains, “heat, whether from running the shower or the sink, allows hair to come off easier, which means less irritation. And stretching the skin while you shave means fewer chances of nicks and scratches, because you’re creating a tighter, smoother surface for the blade to move across.”
Even though cartridge single blade razor for men may be the most ubiquitous (and what most men learn how to shave with), 12 of the 14 experts we spoke with say that a safety razor is actually the best kind to use. The main thing it boils down to is the fact that with a safety razor, you’re shaving with only one blade — many of our experts told us that more blades do not necessarily mean a better shave, and that using multi-blade cartridges can increase the likelihood of ingrown hairs and razor burn. “The safety razor is the absolute way to go,” says Chad Beightol, the owner of New York City–based men’s-grooming store Consigliere. “You’re working with a single blade that is sharp, instead of relying on a multi-blade cartridge that is trying to trap the hair between the blades.” Paul Langevin of barbershop Mildred New York adds, “The single blade minimizes irritation.” Another plus is that safety razor blades (the best of which you can find here) are far less expensive to replace than disposable cartridges, and they don’t generate any plastic waste. The experts do admit that, at first, using a safety razor won’t be quite as effortless as shaving with a Gilette or Shick (and if you’d rather stick to those cartridge razors, there are some on this list, too). But they say most people are quick converts once they get the hang of it. We’ve written about safety razors before, and German razor manufacturer Merkur was the brand that came most recommended. The Merkur 34C remains our experts’ top pick, with many saying it’s an especially good choice for beginners because the short handle makes it easy to maneuver.
Bevel is a newer safety-razor company that both barber Julien Howard and Beightol recommend. You can purchase the twin blade razor for men and blades on their own, but they also have subscription options for scheduled blade replacement, along with a full line of shaving products. The Bevel razor also has a bit of a sleeker, more contemporary look than the others on this list, and a slightly longer and narrower handle that might be more comfortable for some.
Standard safety razors are pretty straightforward: The head of the razor closes around the flexible metal blade, which is then locked into a predetermined angle. This construction works well for most people, but some may benefit from being able to customize the angle at which the blade meets the skin. For someone with sensitive skin, a lower angle will allow for a gentler shave with less irritation. Someone with coarse facial hair, on the other hand, might prefer a more aggressive angle. It all comes down to personal preference, and that’s why Xavier Rodriguez of Fellow Barber and Peter Solomon of Tweed Barbers of Boston both recommend the adjustable Merkur Progress to anyone who thinks their safety-razor shave might benefit from some customization. It has five different blade-angle settings, and you simply twist the dial at the bottom to toggle between them. If you decide this is the razor for you, you’ll want to get some blades for it as well.
Mike Gilman, the owner of the Grooming Lounge, agrees that a safety razor is going to provide the best shave when used properly. But he also notes that using one may simply not be practical for everyone. You need to be a bit more careful with a safety razor, so it’s going to take a little longer to shave; you also need to devote some time to learning proper technique. “For most guys, the method of shaving that works best, and that they are most used to, is shaving with a cartridge razor. The blades and razors are available everywhere, and they’re super-easy to use.” If you want to go the cartridge-razor route, Gilman says it’s wise to stick with a classic. His pick, the Gillette Mach 3, uses a three-blade cartridge, which is a nice compromise between the single blade of a safety razor and the five blades of some of the newest cartridge razors. “I just think the Mach 3 is the way to go,” he says.
Langevin agrees with Gilman that a cartridge razor would be a better choice for “people who don’t want to master shaving with a safety razor.” He likes Harry’s, however, which he says makes a good “disposable-blade system.” Like Bevel’s razors, Harry’s razors and blades are available à la carte, but you can also sign up for a subscription blade-replacement plan through the brand’s website.
Editor’s note: While Amazon sells the women's razor with two blade refills, if purchased from Harry’s, you’ll only get the razor, hence the cheaper price.
Groomer and makeup artist Robert Reyes says that while “safety razors are great for sensitive skin, they can be a bit time-consuming.” So if you’ve got sensitive skin but prefer a cartridge razor, he suggests this Schick model that he personally uses. “It has lubricated skin guards that help protect the skin,” Reyes explains.
For the fastest and easiest shave, an electric triple blade razor for women will likely be the best bet, and some of our experts say that using one can also reduce the occurrence of ingrown hairs. “For those who don’t like the traditional methods, I recommend foil shavers,” says Langevin. Foil shavers have a thin perforated sheet of metal covering the blades; individual hairs are fed through the tiny holes and cut by the blade below. According to Langevin, the resulting shave is the closest you can get with an electric style, and comparable to that of an analog razor. “Foil shavers get almost as close as a traditional razor, sometimes even closer,” he adds. Langevin, barber Karac Ruleau of Mott NYC, and Heather Manto of Austin’s Independence Barber Co. all recommend the Andis Cordless Profoil Shaver — Langevin uses the Andis 17200 and Manto and Ruleau use the slightly older 17150, but they are essentially the same. (The Andis Profoil, perhaps not surprisingly, also appears on our list of the best electric razors). The shaver is designed with commercial use in mind, but Manto says she would recommend it for home use as well. “It helps to pull out ingrown hairs, doesn’t cause razor bumps, and can be used wet or dry,” she says. Adds Ruleau: “It gives you a super-close shave without any razor burn, is light, durable, and inexpensive, and doesn’t require a frequent charge.” But one note from all of our experts: Foil shavers like this aren’t designed to cut long hair and only work on short, “stubble length” facial hair. While that might seem limiting, Manto thinks it makes them a great choice for people who shave regularly.
If you’re looking for an electric option to tackle longer hair (or use on sensitive skin), four experts have told us that Wahl’s Peanut is the best because it has a powerful motor, is easy to maneuver, and comes with four guards that will help you achieve the exact facial-hair length you want. (The Peanut, according to even more experts, is also great for shaving your head and manscaping.) DeAngelis calls it a “compact, sturdy machine that is going to cut what you need it to cut, but still allow you to work safely around your mustache and lips.” If used without those guards, the trimmer will cut facial hair down to that coveted five-o’clock-shadow length, add the pros, who note that a trimmer like this is also the best style of electric razor for people with sensitive skin (because of the fact that it doesn’t cut so close results in less irritation). While Wahl also sells a cordless version of the Peanut, most of our barbers prefer the corded style because they say it offers more consistent power.
Marissa Machado, a celebrity groomer and makeup artist, and two regular guys — Strategist contributor Kurt Soller and New Scientist editor Conrad Quilty-Harper — like the OneBlade electric razor from Philips Norelco, another classic brand. The OneBlade uses cartridges that are meant to be replaced every four months and is shaped like a more maneuverable cartridge razor, but it’s battery powered and features a vibrating blade, so it also recalls electric styles. Machado says that “it gives a smooth finish” and, unlike other electric razors, it’s designed to “be used with or without shaving cream.” She also praises its customizability: “It comes with trimming attachments, so it’s really an all-in-one product.”
|
|
|
How to use mica band heater and how does a cartridge heater work |
Posted by: fowjw558 - 08-17-2021, 02:19 AM - Forum: Welcomes and Introductions
- No Replies
|
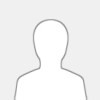 |
With different electrical termination styles, clamping mechanisms and the ability to accommodate holes and cutouts, mica-insulated band heaters are used successfully in many applications, particularly plastics.
Loss Prevention for Band Heaters
Most band heaters with heating plate do not “burn out”; instead, environmental factors create a short, cause hot spots to develop, or simply push the heater beyond its normal operating temperature. All of these factors cause a heater to fail prematurely and require replacement. Obviously, minimizing these environmental factors can reduce the frequency of replacing band heaters in your operation.
Contamination.By far, the most frequent culprit of band heater failure is contamination. Liquid plastic, hydraulic oil and moisture (often from high ambient humidity) are three main causes of premature failure from contamination. Obviously, keeping the heaters free of contaminants will reduce failure and replacement rates. In applications where liquid plastic and oil exposure are frequent and difficult to manage, the best solution may be to select a low cost band -- the heater will be replaced often, but the financial loss will be minimized. Alternatively, a band heater designed to resist contamination can be used. Keep in mind, though, that most heaters fail from lead wire damage caused by contamination -- not from contaminants finding their way inside the band -- and contaminant-resistant heaters will not prevent lead wire damage.
Poor Contact Between Heater and Barrel.The second most common cause of premature failure is poor contact between the machine barrel and the band heater. A tight fit is critical. Without it, localized hot spots can form on the band and cause the resistance wire to fail.
There are two steps you can take to ensure good contact with the machine barrel. First, make sure the machine barrel outer diameter (OD) measurement is accurate; then, order band heaters with that same measurement. The heater manufacturer will factor in a 0.25" gap, so there is no need to undersize the band’s dimensions.
Second, follow a strict installation and tightening procedure for mica, high watt density or extruded aluminum band heaters. Before installation, clean and smooth the machine barrel surface, removing any plastic residue. To install, tighten the heater snugly to the barrel using a clamping bolt torque of 10 ft/lb. Next, apply power to the heaters and allow them to reach halfway to setpoint temperature or approximately 300°F (149°C). Once at this temperature, cut the power and retighten the bands at 10 ft/lb torque. Retightening the band at an elevated temperature will account for the heater’s thermal expansion. (Remember, ceramic band heaters are radiant heaters and should not be tighten in this manner.)
Handling Procedures.Often, failing to understand a heater’s internal design leads to heater losses. For instance, stretching a one-piece mica band over a barrel during installation can damage the internal mica, resulting in a short circuit. Some manufacturers offer band heaters similar to mica bands that can be stretched for installation, but using installation techniques inappropriate for a specific heater type will cause problems. So, in cases where one heater design will not work -- for example, a machine setup that requires stretching the band over the end of the machine barrel, which would damage a mica band heater -- use a heater that is better suited to application such as a two-piece mica or a one-piece expandable band. A two-piece design also is a good choice when a large diameter band is required as the design minimizes the chance that air gaps will develop. Two-piece ceramic bands also can be used on large diameter barrels.
Another simple handling tip is to use two wrenches to install the wiring onto the band’s post terminations. This practice can eliminate failures because the wrench on the post’s lower nut acts as a strain relief. If this procedure is not followed, the post’s internal connection to the resistance wire can be damaged and become a weak link within the heater.
Runaway Temperatures.Heaters, like finned heaters, are extremely obedient entities. If a controller tells them to produce temperatures beyond their limitations, they will do so -- until their demise. Runaway temperature commands often occur when the thermocouple or RTD does not make solid contact with the surface measured. If the sensor becomes loose or disconnected from the surface, its readings may be hundreds of degrees lower than the process or barrel’s actual temperature. This faulty input then is received by the control device, which calls for full output from the heaters when in fact the process is already up to appropriate temperature.
Given the range of products plant maintenance and engineering personnel encounter, is not realistic for them to become experts on every piece of equipment used. This article only touches the surface of band heater design, options, performance expectations and loss prevention. Users should link up with a qualified supplier that can help design a new system or perform a design analysis on an existing system, then make recommendations to ensure the best performance for the given application. Systems arising from a good supplier/user partnership will extend equipment life and allow critical production schedules to be reached.
Sidebar: Understanding Watt Density Calculations
When designing a system, it is a good idea to match the total wattage applied to the actual wattage required. This practice decreases cycling frequency and temperature overshoots while increasing the heater’s life span. When possible, it also is good practice to specify strap-style clamping devices to hold the heater in place. These devices have a lower thermal expansion rate than the heater, so they can help hold the heater, or the defrost heater, tightly against the barrel during operation.
The durability and performance of a heater depends on selecting the appropriate wattage by using resistance thermometer. Exceeding the maximum allowable watt density for the specified heater size will result in premature heater failure. While calculating watt densities, remove the area of the cold section form the overall calculated surface area of the heater.
Watt Density (W/in2) = Wattage / (3.14 x Inner Diameter x Width) - (Cold Section)
Other points to consider while selecting watt density include: - The watt density should be selected in accordance with the operating temperature.
- To avoid short cycling and inefficient operation, select a wattage as close to the needed capacity as possible.
- The wattage should be in accordance with the voltage and current rating of the controls.
- The safe heating pattern,and heating elelment of the material heated, thermal conductivity and coefficient of expansion of the cylinder are other factors that should be taken into consideration while deciding wattage.
A cartridge heater is a tube-shaped, industrial heating element that can be inserted into drilled holes. Cartridge heaters provide localized and precise heating and are commonly used in the heating process industry. Typically, cartridge heaters are used to heat a metal block from the inside and can be custom manufactured to a specific watt density based on the requirements of the application.
Cartridge heaters are most frequently used for heating metal parts by insertion into drilled holes. For easy installation, the heaters are made slightly undersize relative to their nominal diameter.
How does a Cartridge Heater work?
A cartridge heater consists of resistance coil wound around a ceramic core that is surround by dielectric and encased in a metal sheath. Powered heat transferred through the coil to the sheath causes the sheath to heat up. This heat is then transferred to the inside metal part requiring heat.
To fit a cartridge heater in a low or medium temperature application (600°F or less), general purpose drills are usually adequate for drilling holes. Holes can be drilled .003” to .008” over the nominal size of the drill, resulting in fits of .009” to .014.” While this fit is slightly looser than would permit optimal heat transfer, it aids in the installation and removal of the cartridge heaters with heating cable, especially those with long sheaths. At high watt densities, a close fit is much more important. The holes should be drilled and reamed rather than just drilled with a general purpose bit. With a tighter fit, the heater will run cooler and have a longer life expectancy.
|
|
|
|