Welcome, Guest |
You have to register before you can post on our site.
|
Online Users |
There are currently 101 online users. » 0 Member(s) | 100 Guest(s) Applebot
|
Latest Threads |
Dominica visa free countr...
Forum: Off Topic
Last Post: axied12
06-24-2025, 12:37 PM
» Replies: 0
» Views: 112
|
Advanced microneedling
Forum: Off Topic
Last Post: axied12
05-28-2025, 01:25 PM
» Replies: 0
» Views: 264
|
Caviar and cheese
Forum: Off Topic
Last Post: axied12
05-28-2025, 12:38 PM
» Replies: 0
» Views: 240
|
Top-rated countertop comp...
Forum: Off Topic
Last Post: axied12
05-04-2025, 06:42 AM
» Replies: 0
» Views: 384
|
Ryanair letenky levně do ...
Forum: Off Topic
Last Post: axied12
02-11-2025, 01:37 PM
» Replies: 0
» Views: 761
|
Trusted essay writing ser...
Forum: Off Topic
Last Post: axied12
01-30-2025, 08:16 AM
» Replies: 0
» Views: 696
|
Bootverkopers - actieve j...
Forum: Off Topic
Last Post: axied12
12-07-2024, 11:07 AM
» Replies: 0
» Views: 824
|
Services for individuals ...
Forum: Off Topic
Last Post: axied12
12-02-2024, 03:31 PM
» Replies: 0
» Views: 794
|
Used excavators
Forum: Off Topic
Last Post: axied12
11-13-2024, 09:22 AM
» Replies: 0
» Views: 748
|
Buy Higo Rocket in Dubai
Forum: Off Topic
Last Post: axied12
10-25-2024, 01:09 PM
» Replies: 0
» Views: 857
|
|
|
Solar Water Pumps: Things To Know andTips For Use |
Posted by: O789K - 09-28-2021, 01:03 AM - Forum: FPS and Shooters
- No Replies
|
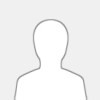 |
Solar Water Pumps: Things To Know andTips For Use
Solar Water Pumps: Things To Know andTips For Use
Mechanical pumps have a lot of uses nowadays. They are common in pumping water from wells, aquarium filtering, pond filtering and aeration. When it comes to water pumps, the main use of this device is the exchange of fluids such as water.
From agriculture to the energy industry, pumps are found in a wide range of applications. The main working principle of a water pump basically depends upon the positive displacement principle and kinetic energy which helps pushing the water.
Solar water pumps are a relatively new concept in mechanics. A solar water pump system is commonly seen in residential and commercial uses, as well as for irrigation of agricultural land. Through solar panels, the pump can eliminate the cost of energy and provide a more feasible option that uses energy from the sun (and not fuel-burning mechanisms) for pumping water.
Introducing solar-powered irrigation for poor and remote areas
In times when the entire world is switching to solar, using the sun’s energy in water pumping systems can significantly help and accelerate the development of agriculture in African countries and many other poor remote areas. This concept is known as solar-powered irrigation and is used in many regions nowadays.
The truth is, solar energy might be the easiest way for farmers to produce energy, especially for those living off the electricity grids with poor infrastructure around their homes. Therefore, the use of solar water pump in agriculture is becoming increasingly popular. The concept of solar irrigation represents a virtuous circle—when the sun shines, it feeds the irrigation system and feeds the crops which are dependant on water in sunny weather. Therefore, a large quantity of energy is being released right at the time when it is needed the most.
Solar irrigation is a concept that works through solar water pumps. Below, we are describing them in detail.
What is a solar water pump and what are the most popular types?
As we discussed before, solar pumps present a clean, simple and energy-efficient alternative to traditional electric and fuel-driven pump sets. They are part of an environmentally friendly approach in agriculture and can be used to exploit every region, whether its developed or poor.
Due to their immense potential for productive use and agricultural productivity, solar water pumps are now powering more and more agriculture projects. Knowing that 40% of the global population relies on agriculture as its main source of income, access to water remains an ongoing struggle for many people. This is what solar aims to change and introduce a cost-effective future for around 500 million small-scale farmers all around the world.
The main components in a solar pumping system include a photovoltaic (PV) array, an electric motor and a pump. Solar water pumping systems, on the other hand, are classified as either direct current (DC) or alternating current (AC) systems based on their motor’s ability. Recently, the concept of brushless DC (BLDC) motors for solar pumping water applications was presented as well.
Classification and types of solar pumps
When it comes to stand-alone solar pumping systems, the main types include rotating and positive displacement pumps or hybrid solar pump. Centrifugal pumps are the common choice for rotation and are designed for fixed head applications. Their output increases in proportion to their speed of rotation.
Additionally, pumps are also classified as submersible and surface pumps, based on their placement (underwater and above the waterline).
All in all, the main aspect related to the efficiency of a solar water pump is based on three variables including pressure, flow and input power to the pump. Wire-to-water efficiency is the commonly used metric that determines the overall efficiency of a solar water pump (as the ratio between the hydraulic energy that comes out of the pipe and the energy coming over the electrical wires through solar panels).
Why solar-powered water pumps are the ideal way to boost agriculture in remote areas (And Africa)
A solar-powered water pump is a concept that is environmentally-friendly. More importantly, it is a concept that gets rid of any power grids or fossil fuels used to pump water out of the ground. Below, we are listing the advantages and disadvantages of their use.
Advantages of solar water pumps
The first advantage of solar pumps is that they are reliable in regional and remote areas. A perfect example of this is Africa, which is one of the poorest remote regions in the world with an abundance of water—but also the most dominant region when it comes to most days of sun in the year. On the flip side, Africa is thought to possess 9% of the world’s freshwater resources which translates to around 4,000 km3 of water per year. Deploying solar water pumps in Africa is, therefore, the perfect alternative to any other fuel-based sources—and an alternative which can stimulate life in every part of this continent.
What Is the DC Submersible Pump?
The DC submersible pump as well as other types of submersible pumps look like a metal tube and their goal is to push the water to the surface. This type of pipe-look water pumps conceals the motor within the tube so that the liquid outside the pump does not get access to the electrical parts inside the pump.
The DC submersible pumps are versatile and can better accommodate with different working environments because they can be powered from a variety of independent DC power sources. The most common power sources for the DC submersible pumps are the solar modules, batteries, or generators. The DC submersible pumps with solar power supplies sometimes have a controller in order to enhance the current when the sunlight is low.
More Information on the Power Supply
Typically, the DC submersible pumps can operate on multiple volts of DC power such as 6V, 12V, 24V or 32V. There are some advantages of applying the direct current instead of the alternating current (AC). The first advantage is that the DC power system allows the submersible pumps to adapt to more power supply options such as batteries. It makes the machines portable and is more convenient to apply.
Also, the AC power system needs a controller to control the speed while the AC power system does not need such device. In most cases, the controller of the power system is only needed when the solar power modules are applied.
The DC submersible pumps are more energy efficient too; it takes less power to run a DC submersible pump than an Ac Dc submersible pump. However, there are limits to the DC machines as well. The DC submersible pumps have a shorter lifespan than the AC counterparts. Besides, though the DC machines are more energy efficient and easier to operate without a current controller, they tend to work in a rather lower speed and they are less powerful in pumping.
The Application of Submersible Pumps
The submersible pumps are applicable in multiple areas. For example, they can be used to pump sewage from the septic tanks and it is convenient because the pump deliver the sewage directly to tanks so that they can be transferred to treatment facilities and handled later on.
Secondly, they can be used both industrially and in buildings. Wherever there is too much unwanted water in a work site or when the basement of a building is flooded, the submersible pump can be applied to extract all the water out of the place easily.
The other common use of a submersible pump is for the oil wells. Whether it is an inland oil well or an offshore oil well, the submersible pump can pump out the oil from the ground and transfer it to the factory for further process. Some types of submersible pumps can also be used for drilling wells to a certain depth.
They are called the drilling pumps or borehole pumps. In addition to the industrial use, the submersible pumps can be used agriculturally as a part of the irrigation systems.
What Are the Advantages of a Submersible Pump?
The main goal of asubmersible pumpis to pump out liquids from the ground or from places under the surface level. The submersible pumps are best for job because of several reasons. For one thing, the submersible pump keeps almost all the components within the pipe-like body; therefore, it does not take up much space.
In other words, the submersible pumps can work best in a confined environment comparing to other types of pumps. The submersible pumps connect directly to the storage tanks with pipes or hoses which also take up very limited space as well. As a result, they accommodate with most working environments possible.
The other quality that the submersible pumps have which again comes from the design is that it is the safest options to operate among all other types of water pumps. Since all the working parts of the machine is contained within the body and the whole body will be in the pit of the work site, there is not much of a chance that the user around the machine gets hurt when it is running. This feature alone makes the submersible pumps stand out and become widely accepted.
Once again, because all the components are carried inside the pump body and they operate under the water in most cases, they do not make loud noises. Or to be specific, the noises made while the machine is running are all blocked by the water and the case of the machine. What’s more, the simplicity of the mechanism makes this kind of water pump more effective when it comes to pumping out liquids from underground.
In addition to the safety, the efficiency and the quietness a submersible pump have, the maintenance of the machine is also quite easy. In fact, it does not require much maintenance because the working parts and electrical components are all protected inside the case of the machine, the small contaminants are not likely to enter the body and harm the machine.
Moreover, because the submersible pumps are working in water, they are cooled by the water when running and the machine can last longer with this style of operation.
The application of the DC submersible pumps is mainly in the so called dewatering operations and because of the design and the power supply that they work with, there are a lot of advantages to the use of them.
The primary advantage of a DC submersible water pump is its convenience and ease of operation because the mechanism of the pump is simple and the power system allows more portability to the machine. If the users are looking for a reliable yet compact water pump with multiple power supply options, the Ac Dc screw submersible pump may just be the right choice for them.
|
|
|
What's New With Nonwovens in the Medical Industry? |
Posted by: O789K - 09-28-2021, 01:01 AM - Forum: FPS and Shooters
- No Replies
|
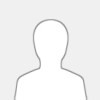 |
What's New With Nonwovens in the Medical Industry?
What's New With Nonwovens in the Medical Industry?
The utilization of medical nonwoven fabric has outpaced woven materials in recent years. Even when traced back to their rapid adoption during WWII, nonwovens were proven to be superior products in terms of adaptability, disposability, cost, and effectiveness. Manufacturing technology improved in the following decades until current-day use of nonwovens has placed them in a position to dominate the medical textile industry.
What are Nonwovens Fabrics?
Nonwovens are defined as sheets or web structures bonded together by the process of entangling fibers or filaments (and sometimes by perforating films) mechanically, chemically, or thermally. The fibers may be oriented randomly throughout the fabric or only following one direction.
Multiple layers may be combined to achieve the desired elongation, strength, and other mechanical properties. Porosity is controlled by varying fiber density, diameter, orientation, and the use of additional mechanical processing.
Key characteristics of nonwovens that justify their use and popularity:
durability
strength
resilience
dimensional stability
low elongation
specific processing to control porosity
Benefits of Nonwovens Driving this Market
With very deliberate care being taken to lower the incidence of hospital-acquired infection, nonwoven medical textiles are the clear winner in this category, thanks to their unique qualities. Medical textile technology is subject to intense monitoring since human lives are at stake. The intense scrutiny has resulted in better quality products and the development and implementation of innovative new uses in the medical field.
Nonwovens are preferred and poised to dominate the industry because they:
are effective barriers against bacteria
outperform linens for reducing airborne contaminants
can be tailored to changing specifications
help mitigate the risks of today's medical environments due to drug-resistant bacteria, worsening viral threats, polluted indoor and outdoor air, and increases in the numbers of blood-borne diseases
In 2014, nonwovens dominated the global medical textiles market. They accounted for over 55% of global volume, and are projected to gain market share through 2024 consistently.
What is SMS Material?
“SMS” stands for spunbond meltblown spunbond. SMS non woven fabric is a type of nonwoven fabric that combines spunbond and meltblown fabrics.When SMS material is created, it has great water repelling capabilities. This is why manufacturers choose to use SMS material in things like face masks, parts of baby diapers, sanitary napkins, and janitorial coveralls. It’s also used for caps, gowns, beddings, and other hospital accessories.
Why Combine Spunbond with Meltblown?
Spunbond polypropylene is a material that has great durability and strength, no matter if it’s wet or dry. It’s very resistant to fraying and is difficult to unravel, plus it barely absorbs any moisture if it becomes wet.
Meltblown, on the other hand, is softer and more pliable than spun bond polypropylene. Their main advantage is their web strength, which is why they’re usually combined with other nonwoven fibers. While spun bond polypropylene has its advantages, it can feel stiff and uncomfortable when it’s put in everyday applications such as coveralls.Since meltblown has a webbed structure and is softer, when you combine these two nonwoven fibers, it provides the wearer with water resistance while still retaining comfort. It’s also breathable, so even if you’re covered from head to toe (as with coveralls), your comfort won’t be compromised.
Applications for SMS Material
Because of how well SMS material repels water, it’s used in a number of industries where people need to block off fluids or other wet substances. Some areas that utilize SMS material’s benefits used are:
Protective apparel
Cleanroom coveralls
Filtration
Insulation
Medical healthcare
Sanitary products
Why The Future Is Nonwoven
Wherever you are sitting or standing right now, there’s bound to be at least one nonwoven fabric in your midst. Teabag or coffee filter, maybe? An air conditioning filter. Lens tissues, bleach wipes, diapers. Surely a face mask or seven.
Though the COVID-19 pandemic certainly pushed awareness of nonwoven fabrics to the forefront, we’ve had our eye on this growing market segment for years. Why? Because pressure-sensitive adhesive tape is often used to make or convert these textiles into usable everyday items.
Here’s our take on how non-wovens will continue to evolve and play a distinct role in the convenience economy.
What Is Non-Woven?
Nonwoven fabrics are the simplest and oldest textile fabrics. Neither woven nor knitted, as the name suggests, non-woven fabrics are broadly defined as sheet or web structures bonded together by entangling fiber or filaments (and by perforating films) mechanically, thermally or chemically.
They are flat or tufted porous sheets that are made directly from separate fibers, molten plastic, or plastic film. They are not made by weaving or knitting and do not require converting the fibers to yarn.
Typically, a certain percentage of recycled fabrics and oil-based materials are used in non-woven fabrics. The percentage of recycled fabrics varies based upon the strength of the material needed for the specific use. In addition, some nonwoven fabrics can be recycled after use, given the proper treatment and facilities. For this reason, some consider non-woven a more ecological fabric for certain applications, especially in fields and industries where disposable or single-use products are important, such as hospitals, schools, nursing homes, and luxury accommodations.
How are Nonwoven Fabrics Made?
Non-woven fabrics are made in two main methods: they are either felted or they are bonded. Felted non-woven fabric is produced by layering thin sheets, then applying heat, moisture, and pressure to compress the fibers into a thick matted cloth that will not ravel or fray.
There are there main methods of manufacturing bonded non-woven fabrics: Dry Laid, Wet Laid & Direct Spun.
In Dry Laid Non-woven Fabric manufacturing, a web of fibers is laid in a drum and hot air is injected to bond the fibers together.
In Wet-Laid, a web of fibers is mixed with a softening solvent that releases a glue-like substance that bonds the fibers together, and then the web is laid out to dry.
In Direct Spun, the fibers are spun on to a conveyer belt, and glues are sprayed on to the fibers, which are then pressed to bond. (In case of thermoplastic fibers, glue is not required.)
How are Non-Woven Fabrics Being Used?
Nonwoven fabrics penetrate a wide range of markets including medical, apparel, automotive, filtration, construction, geotextiles, and protective. Day by day the use of non-woven fabric is increasing and without them, our present life would be incomprehensible. Indeed, nonwovens play an integral role in the convenience economy.
Basically there are two types of nonwoven fabric: durable and disposal. Around 60% of nonwoven fabric is durable and the other 40% is disposal. These specialty fabrics are engineered to provide specific functions such as absorbency, sterility, liquid repellency, resilience, stretch, softness, strength, flame retardancy, cushioning, thermal insulation, acoustic insulation, and filtration. These properties are often combined to create fabrics suited for specific jobs while achieving a good balance between product use-life and cost. There are many kinds of it, such as non-woven fabrics for clothing, non-woven fabrics for packaging, and so on.
Non-woven fabric, is made of oriented or random fibers. It is a new generation of environmentally friendly materials. It is moisture-proof, breathable, flexible, light, non-combustible, easy to decompose, non-toxic and non-irritating, rich in color, and price. Low cost, recyclable, and so on. For example, polypropylene (pp material) pellets are used as raw materials, which are produced by high-temperature melting, spinning, paving, and hot-rolling and continuous one-step process. It is called cloth because it has the appearance and some properties of the cloth.
Therefore, in the non-woven fabric, S, SS,SSS, SMS mean the following:
S: spunbonded non-woven fabric = hot-rolled single-layer web;
SS: spunbonded nonwoven fabric + spunbonded nonwoven fabric = hot rolled from two layers of web;
SSS: spunbonded nonwoven fabric + spunbonded nonwoven fabric + spunbonded nonwoven fabric= hot rolled from three layers of web;
SMS: spunbond non-woven fabric + meltblown non-woven fabric + spunbond non-woven fabric = three-layer fiber mesh hot rolled
S and SS non woven fabric are mainly used for furniture, agriculture, hygenic products, and packaging products. And SMS nonwoven fabric is mainly for medical products, like surgical gowns. We are now exporting these non-woven fabrics to different countries in the world.
|
|
|
The Benefits of Stainless Steel Fittings |
Posted by: O789K - 09-28-2021, 12:58 AM - Forum: FPS and Shooters
- No Replies
|
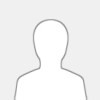 |
The Benefits of Stainless Steel Fittings
The Benefits of Stainless Steel Fittings
Stainless steel is a versatile material that is used in many different applications. The two most common types of stainless steel are austenitic which is highly corrosion resistant and ferritic which is magnetic.
In this blog we are going to break down the basics of what austenitic stainless steel is, the key benefits it provides and where the uses of stainless steel fittings can be most beneficial.
Stainless Steel
All steels have the same basic iron and carbon composition along with nickel, but stainless steel also contains chromium - the alloy that gives stainless steel its well-known corrosion resistance.
Austenitic stainless steel contains high levels of chromium and nickel and low levels of carbon providing a balance of strength, workability and corrosion resistance. The standard stainless steel alloys used in plumbing applications contains between 18-20% chromium and 8-12% nickel, as well as small amounts of carbon 0.08% and manganese 2%. Austenitic stainless steel has the highest corrosion resistance and are the most commonly used type of stainless steel around the world.
Stainless steel offers a wide range of benefits to the architect and designer of plumbing systems:
Material Benefits
The combining of corrosion resistance with high strength allows the reduction in wall thickness and weight. Stainless steel is resistant to heat and chemical damage. It can withstand very high flow rates - in excess of 40m/s, making it capable to withstand long-term exposure to the elements in almost any environment.
Environmental Benefits
Stainless steel can be used in all types of water, including drinking water in public supply. It has an excellent resistance to the full range of potable waters, including various chloride levels. At the end of its useful life, stainless steel is fully recyclable and retains a higher residual scrap value than ordinary steel.
Economic Benefits
Stainless steel is low maintenance and requires no additional coating, in both indoor and outdoor applications. The expected lifetime of a stainless steel system is more than 50 years, reducing system down time, replacement and maintenance costs over the life of the installation.
Stainless Steel Fitting Applications
With all the benefits that come with stainless steel there are equally just as many applications where stainless steel fitting can be utilized. Here are some key beneficial areas:
Residential & Commercial water systems that are subject to various stresses.
Commercial & Industrial piping systems that are needing to perform well under the toughest and harshest conditions.
Industrial Projects for sanitary or highly corrosive applications.
WHAT ARE THE BENEFITS OF USING STAINLESS STEEL VALVES?
There are many benefits of using stainless steel valve. There’s no doubt that stainless steel is a great material that is tougher than brass, copper, and cast iron when it comes to tolerating high pressures and temperature. Carbon steel is probably the only material that comes closest to stainless steel. Generally, stainless steel values have various applications due to their great performance in terms of temperature limits, corrosion resistance, and high-pressure tolerance.
APPLICATIONS OF STAINLESS STEEL BALL VALVES
Since stainless steel delivers phenomenally on all fronts, they are used in various industries. Here are a few applications of stainless steel ball valves.
OIL REFINING
Refining crude oil is a long and complicated process that is made much easier through the use of stainless steel ball valves. Crude oil may contain sulfur, carbon dioxide, and many microorganisms, which makes it an extremely corrosive substance. Over time, the constant movement of this substance can break down the metal of the valve. Therefore, you will need pipes and valves that can withstand corrosive crude oil for the longest time. Since stainless steel valves have very high corrosion resistance, they are the obvious choice of use in the oil refinery industry.
MARINE PROJECTS
Certain applications involving pipes and valves occur under or near seawater. Since seawater contains chloride and sodium, it is pretty corrosive to all materials, especially metals. That’s not all, marine environments naturally involve water, a substance that has a substantial impact on all metals.
In such applications, many prefer to use plastic valves since they are more resistant to water and other harsh chemicals compared to most metals. However, the main concern with using plastic valves is that they can’t withstand extreme temperatures and high pressures.
Stainless steel ball valves, on the other hand, have a high-temperature tolerance, are corrosion resistant, and can withstand high pressures. The only thing these valves require is proper maintenance to extend their lifespan under or around seawater.
BREWERIES
Stainless steel ball valves are widely used in breweries. These valves are typically situated on the kettle to help control the flow of liquid during transfers. The reason that stainless steel valves are a top choice in breweries is that during the mashing process, the valve comes into direct contact with a liquid known as wort, which is highly corrosive and can very easily wear down iron valves, and since plastic valves lack the ability to handle high temperatures, stainless steel valves are the best option.
WRAPPING UP
The industries mentioned above are just a few examples of the application that stainless steel valves have. These valves can be used in any process that involves the transfer of a corrosive, high temperature, or high-pressure substance such as gas or liquid.
Stainless steel 304 is one of the most common metals used nowadays. Stainless steel is well known and preferred over several other metals due to its physical properties including good corrosion resistance, durability, high strength, etc. Various types of commercial, industrial, and residential products are created using Stainless Steel. Stainless Steel 304 flanges are one of the most popular meteal products created out of this metal. There is a vast variety of flanges available for purchase. This article discusses eight important types of flanges and their uses.
Types of Stainless Steel Flanges
The following are the top 8 stainless steel flange used in stainless steel pipes:
Weld Neck Flanges: Flange is distinguished by their protruding necks. The weld neck flanges have the same angle and thickness as that of the pipe. Weld Neck Flanges are considered best for use in severe service conditions such as sub-zero or high temperatures and high pressure.
Slip-On Flanges: These are the most affordable range of flanges available for purchase. The slip-on flanges as the name suggests need to be easier to slip them over the pipe and hence they have a slightly larger diameter than the pipe. These stainless steel Slip On flanges are fillet welded to a position and are ideal for low-pressure applications.
Blind Flanges: The flanges are designed without a bore, and are used to seal vessel openings or piping systems. Blind Flanges are ideal for use where the piping systems or vessels require constant inspection. The blind flanges can be supplied with or without hubs. This SS 304 Blind Flanges can easily handle high stress caused due to internal pressure.
Threaded Flanges: Threaded Flanges also known as screwed flanges, and have a thread inside the flange bore which fits on the pipe with matching male thread on the pipe. Threaded flanges are used for special applications and can be easily assembled without welding. Stainless steel 304 threaded flanges are compatible with pipes with external threads.
Lap Joint Flanges: The lap joint flanges are the type of slip-on flanges that are used with stub end fittings. Lap Joint Flanges are ideal for piping systems that require regular inspection and maintenance such as low alloy steel pipes or carbon steel pipes.
Socket Weld Flanges: The flanges are designed for use on small diameter and high-pressure piping. The socket weld flanges have internal welds which contribute to their durability as well as endurance limit. These flanges are used in the chemical processing industry.
Orifice Flanges: The function of these steel flanges is to provide access to a line for metering liquids or gases. The orifice flanges are installed with orifice plates or flow nozzles.
Ring–Type Joint Flanges: These flanges are used for high pressure and temperature applications. The ring-type joint flanges has a specially designed grove that can be easily compressed on blind, slip-on or weld neck flange. The flanges help in avoiding leakages in pipelines where media is transferred at high pressure and high temperature.
|
|
|
Nonwovens for Home Textiles |
Posted by: O789K - 09-28-2021, 12:55 AM - Forum: FPS and Shooters
- No Replies
|
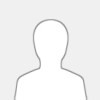 |
Nonwovens for Home Textiles
Nonwovens for Home Textiles
Nonwoven fabric is a fabric-like material made from lengthy fibers, bonded together by chemical, mechanical, heat or solvent treatment. In simple terms, they are textiles made from fibers or threads joined together without weaving. Nonwoven materials classically lack strength unless densified or toughened by a backing. In recent years, nonwovens have become an alternative to polyurethane foam.
Nowadays nonwoven fabrics are mostly used as home furnishing fabrics. Nonwoven fabrics are described as sheet or web structures bonded together by entangling fiber or filaments (and by perforating films) mechanically, thermally or chemically. They are flat, porous sheets that are made directly from separate fibers or from molten plastic or plastic film. They are not made by weaving or knitting and do not require converting the fibers to yarn. Typically, a certain percentage of recycled fabrics and oil-based materials are used in nonwoven fabrics. The percentage of recycled fabrics varies based upon the strength of material needed for the specific use. Conversely, some nonwoven fabrics can be recycled after use, given the proper treatment and facilities. For this reason, some consider nonwovens a more ecological fabric for certain applications, especially in fields and industries where disposable or single use products are important, such as hospitals, schools, nursing homes and luxury accommodations.
Nonwoven fabrics are engineered fabrics that may be a limited life, single-use fabric or a very durable fabric. Nonwoven fabrics provide specific functions such as absorbency, liquid repellence, resilience, stretch, softness, strength, flame retardancy, washability, cushioning, filtering, use as a bacterial barrier and sterility. These properties are often combined to create fabrics suited for specific jobs, while achieving a good balance between product life and cost. They can mimic the appearance, texture and strength of a woven fabric and can be as bulky as the thickest paddings. In combination with other materials they provide a spectrum of products with diverse properties and are used alone or as components of apparel, home furnishings, health care, engineering, industrial and consumer goods.
Types of nonwoven fabrics: Nonwovens, depending on the production process can be divided into:
? Materials produced by physicochemical methods; and
? Mechanically produced materials.
Materials produced by physicochemical methods
Most nonwoven materials, are made by binding fibers with adhesives. The most common glued materials are those based on fibrous cloth (a layer of textile fibers whose weight is 10–1000 gsm and more). The cloth is most often formed mechanically from several layers of combed fibers passing through the dotting drum of a combing machine. Fibrous cloth may be produced by the aerodynamic method in which the fibers are removed from the drum of the combing machine by a stream of air and transferred to a mesh drum (condenser) or a horizontal mesh with a maximum speed of up to 100 m/min, or by water dispersion of the fibers on the mesh of a paper machine.
A fibrous cloth is usually made of cotton, a mixture of viscose and polyamide fibers or the waste products of textile manufacture, including unspun fibers. The most common method of producing bonded nonwoven materials are to impregnate the cloth with a liquid adhesive or spraying/printing the adhesive over the surface of the cloth. Gluing the fibers includes saturate bonding and spray bonding or a latex adhesive is applied to the fibers and then the fabric is dried. The impregnated material is dried and treated in chambers heated by hot air or infrared radiation. The nonwoven materials made in this fashion (at a rate of 50 m/min and more) are used as interlacing and sealing materials, as heat and sound insulation materials for upholstery, bedding and drapery liners.
Melting fibers together can only be accomplished with synthetic, thermoplastic fibers or with a blend of fibers containing thermoplastic fibers or fusable powders. These methods include thermal bonding (heat applied to the web with or without pressure) a carded web, ther-mobonding a spunlaid web with a calendar, thermobonding a melt blown or flash spun web with a calender, thermal bonding a carded or air laid high loft web in an oven.In the hot-pressing process, the fibers are bonded by thermoplastics such as polyamides, polyethylene, and polyvinyl chloride at pressures of up to 2 mega newtons per sq m (MN/m2), or 20 kilograms-force per sq cm (kgf/cm2), at high temperatures, usually on special calenders. The bonding is preceded by thermal treatment of the fiber layer, which contains an adhesive that is applied to the fibrous cloth during its formation or after its formation.
In the spunbonded method, synthetic fibers are formed as they leave the spinnerets of spinning machines and pass through troughs in which they are stretched in an air current; they are then placed on a conveyor belt and form a sheet. The material formed in this way is most often bonded with an adhesive; in some cases the stickiness of the fibers themselves is sufficient.
SPUNBOUND/SPUNLACE
Spunlace nonwoven fabric is produced by depositing extruded, spun filaments onto a collection belt in a uniform random manner followed by bonding the fibres. The fibres are separated during the web laying process by air jets or electrostatic charges. The collecting service is usually perforated to prevent the air stream from deflecting and carrying the fibres in an uncontrolled manner. Bonding imparts strength and integrity to the web by applying heated rolls or hot needles to partially melt the polymer and fuse the fibres together. Since molecular orientation increases the melting point, fibres that are not highly drawn can be used as thermal binding fibres. Polyethelene or random ethylene-propylene copolymers are used as low melting bonding sites.
Spunbound products are employed in carpet backing, geotextiles, and disposable medical/hygiene products, automotive products, civil engineering and packaging products.
The process of Spunbound non-woven production tends to be more economical as the fabric production is combined with the fibre production.
AIRLAID
The process of airlaying is a non-woven web forming process that disperses into a fast moving stream and condenses them onto a moving screen by means of pressure or vacuum.
Airlaid fabrics is mainly composed of woodpulp and has a nature of absorbing well. It can be mixed with a definite proportion of SAP to improve its capabilities of absorbing wet. Airlaid non-woven is also referred to as dry paper non-woven. The nonwoven is made through the airlaying process. Transit the woodpulp into the bundle of airflow to make the fibres disperse and agglomeration on the floating web. Airlaid non-woven is reinforced of web.
Airlaid non-woven products are employed in a number of different products across a wide range of industry’s including; the interlining of clothes, medical and hygiene products, embroidery material and filter material.
DRYLAID
Dry laid webs are mainly produced using staple fibres natural or manmade. Dry laid webs formation mainly consists of 4 steps:
Staple fibre preparation –> Opening, cleaning, mixing & blending –> Carding –> Web laying.
Advantages of Drylaid non-woven production include; The isotropic structure of the web, voluminous webs can be produced and a wide variety of process able fibres such as natural, synthetic, glass, steel and carbon.
Drylaid non-woven products are employed by many products ranging from cosmetic wipes and baby diapers to beverage filtration products.
WETLAID
Wetlaid non-woven are non-wovens made by a modified papermaking process. That is, the fibres to be used are suspended in water. A major objective of wet laid nonwoven manufacturing is to produce structures with textile-fabric characteristics, primarily flexibility and strength, at speeds approaching those associate with papermaking.
Specialized paper machines are used to separate the water from the fibres to form a uniform sheet of material, which is then bonded and dried. In the roll good industry 5 -10% of nonwovens are made by using the wet laid technology.
Wetlaid is used for a wide ranging amount of industries and products. Some of the most common products that use wetlaying non-woven technology include; Tea bag paper, Face cloths, Shingling and Synthetic fibre paper.
NON-WOVEN CHARACTERISTICS
The particular set of properties that a printed nonwoven fabric may have is dependent upon the combination of factors in its production. Each different ttype of non-woven will consist of different characteristics.
The range of characteristics include
The appearance of non-woven fabrics may be paper like, felt like, or similar to that of woven fabrics.
They may have a soft, resilient hand, or they may be hard, stiff or broadly with little pliability.
They may be as thin as thin tissue paper or many times thicker.
They may also be translucent or opaque.
Their porosity may range from low tear and burst strength to very high tensile strength.
They may be fabricated by gluing, heat bonding or sewing.
The drapability of this type of fabrics varies from goof to none at all.
Some fabrics have excellent launderability; others have none. Some may be dry-cleaned.
Non-woven fabric is a material defined as
Sheet or web structures bonded together by entangling fiber or filaments (and by perforating films) mechanically, thermally or chemically.
Non-woven polypropylene fabric is, similarly, a thermoplastic polymer – like polypropylene – but made to look non-woven. One of its major applications is non-woven bags for shopping. Nevertheless, the non-woven fabrics gain more and more popularity in the fashion industry.
With so many plastic bags ban policies sweeping the world in their attempt to reduce plastic pollution, non-woven bags (either for shopping or for fashion) are becoming the norm. But are non-woven bags as eco-friendly as advertised?
Why Are Non-Woven Bags Environmentally Sustainable?
As we all know, the true sustainability of a product or a fabric resides in its recyclability and reusability. Just like canvas shopping bags or jute bags, non-woven carriers are reusable for very long periods. Polypropylene is recyclable, and so are non-woven polypropylene tote bags for shopping or drawstring bags for sports or leisure.
After years of use, you can throw away a broken, non-woven polypropylene office bag uses PP nonwoven fabric, for instance. As long it is collected and appropriately sorted, you can rest assured it will enter the recycling process and give life to a new item.
Non-woven bags for shopping come with plenty of eco-friendly advantages that are not available to plastic bags or natural fibers, for instance:
You can wash them and disinfect them without worrying about their resilience; as long as you wash it in cold water, your washing machine will not take its toll on it;
You can spray your non-woven bags with disinfectants and anti-bacterial substances for enhanced safety, especially during these times of global health concerns;
Both woven and non-woven polypropylene comes from recycled materials (plastic), so it is easy to understand why non-woven shopping bags come with high levels of sustainability. They are products of recycling and make products of recycling in their turn.
Before we move on to the next reason why non-woven bags are the sustainable answer to plastic bags, we have to say that no plastic whatsoever is biodegradable or ecologically friendly.
|
|
|
The evolution of plasma cutting |
Posted by: O789K - 09-28-2021, 12:52 AM - Forum: FPS and Shooters
- No Replies
|
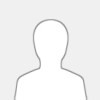 |
The evolution of plasma cutting
The evolution of plasma cutting
Plasma cutting has come a long way since it was first developed in the late 1950s by engineers at Union Carbide Corp. Today it is one of the most widely used metal plate cutting processes for a large variety of industries.
Early plasma cutting systems were used primarily for cutting stainless steel and aluminum plate from 0.5 to more than 6 in. thick. These systems, primitive by today’s design standards, were the most practical method for cutting heavy nonferrous plate. Most were mounted on XY cutting pantograph-style machines that used either photo-cell tracers to duplicate large black line engineering drawings of the parts to be cut, or a magnetic tracer to follow the path of a steel template.
Engineers continuously worked on the process throughout the 1960s with the goal of improving cut quality and the life of the consumable nozzles and electrodes in the cutting torch. Plasma began gaining momentum during this period as the process improved and as users became aware of its ability to cut complex shapes in nonferrous materials at very high speeds.
In 1968 radial water injection was introduced. This patented nozzle technology used pure water injected radially around the plasma jet to constrict the arc, increasing its energy density while improving nozzle cooling and thus allowing faster cut speeds, higher-quality cuts, and the ability to cut carbon steels at speeds four to six times faster than an oxyfuel cutting process.
At about that same time, XY coordinate drive cutting machine technology was being improved. Microprocessor control technology started to become the brains of the XY motion control machines, allowing for better accuracy, higher cutting speeds (necessary for the new-technology plasma systems), and higher levels of automation and productivity on the shop floor.
Through the 1970s plasma cutting technology replaced many oxyfuel-based steel cutting applications from 0.25 to 1 in. thick, while still maintaining its stronghold on the stainless and aluminum markets. While plasma could cut steel thicker than 1 in., the oxyfuel process still was a lower-cost alternative for heavier steel plate.
Timeline of Major Engineering Breakthroughs
With the baseline of plasma’s early history established, let’s take a look at some of the major engineering breakthroughs with this technology:
1957 The plasma cutting process was developed and patented by Union Carbide as an extension of the gas tungsten arc welding (GTAW) process.
1962-1967 Several new developments were completed in consumable design, and the dual flow torch was designed to help improve consumable life and cut quality on nonferrous materials.
1968 The water injection process was commercialized. This process allowed for cutting with clean, square-cut edges and faster speeds, as well as cutting of carbon steels with acceptable cut quality.
1970-1979 The water table and water muffler, designed to provide fume and smoke control, debuted. Automated arc voltage-based height controls for more consistent cut quality and longer consumable parts life emerged.
1980-1984 Oxygen-based plasma cutting systems that helped improve edge squareness and edge metallurgy (softer, weldable edge) and allowed for cutting carbon steels at lower power levels and higher cut speeds (see Figure 2) were introduced.
1984-1990 Many developments in the air plasma cutting process allowed for better portability and lower power levels for hand cutting and mechanized thin-sheet cutting.
1990 Better power supply designs using pulse width-modulated, current-controlled outputs were developed. Some systems started to use lighter-weight, smaller inverter technology power supplies suitable for portable, hand-held plasma systems.
1992 Long-life oxygen process technology was introduced. This was essentially a microprocessor-controlled method of controlling plasma gas ramping pressures as well as power supply output amperage. It helped increase typical oxygen plasma consumable parts life by four to six times; improved parts consistency; and helped lower the cost of plasma cutting.
1993 High-definition plasma, a technique that required the previous long-life oxygen technology to implement, was developed. This process allowed for a new nozzle design that increased the energy density of an oxygen plasma arc by as much as four times, allowing for squarer, cleaner cuts in all material thicknesses.
1996 Automated gas flow control systems emerged. They interfaced digitally with the machines’ CNCs. These gas flow controls eliminated some of the potential for machine operator-related errors in setting parameters for the cutting process.
1996-2006 Many developments occurred relating to improving cut quality and productivity and automating the many process cut parameters. These included integrated plasma, a system that closely coupled the CNC, the plasma power supply, the gas flow control, the CAM software, and the height control system to automate the process. With this expertise built into the system, the machine operator’s job became much simpler, and the process relied less on operator expertise.
Recent Technology Developments
In the last seven years, developments in plasma cutting technology have come at a fast pace. The latest revision on high-definition machines is their full integration with the CNC machines they are coupled with. New CNCs have touchscreen accessibility, minimizing the number of buttons involved in operating a plasma cutting machine and making operation as simple as almost any Windows?-based software. Operator training has been simplified on even the largest, most complex CNC plasma cutting machines.
The operator’s job also has been made easier with improvements in auto-calibrating height control functionality. The operator does not need to make adjustments as the consumable parts in the torch wear out.
Hole cutting has been improved with a large database of information in the CAM software that automatically recognizes CAD features and implements the best possible cut path and plasma cutting parameters, including on-the-fly shield gas changes that nearly eliminate the normal taper found in plasma-cut holes on steel (see Figure 3). This process is transparent to the machine operator and system programmer, eliminating the need for them to be experts.
Improvements in cut-to-cut cycle times have been incorporated into CAM software. The software automatically recognizes areas of a full cutting nest (multiple parts) and modifies the traverse time, torch retract time, and gas preflow time to decrease production times and improve product throughput.
Nesting software now applies the lead-in points in the most effective way to avoid traversing over areas prone to collisions with previously cut parts.
Improved plate beveling software has simplified the integration and operation of a bevel head with XY CNC cutting machines. This advancement, again associated with the system’s CAM software, saves much of the programmer/operator trial-and-error testing that has always been necessary to hold the best tolerances on plate edge beveling applications, such as weld prep.
Very new vented nozzle and gas mixing technology has helped improve stainless steel edge quality. Edges are squarer, shiny, and weldable.
Air plasma cutting systems from the major manufacturers also improved dramatically in terms of cut quality, consumable life, and duty cycles. These systems, primarily designed for portable and in-shop hand-held cutting applications, now are available with quick-change mechanized torches and interface easily to a variety of lower-cost CNC machines. Systems are available from a 30-amp, toaster-sized unit that operates on 120-V household current to sever materials up to 0.5 in. thick, to a 125-amp, 100 percent duty cycle industrial unit that can sever 2.25-in. materials. Both portable systems can be used with a hand torch or can be mechanized for a variety of automated cutting applications.
Industrial mechanized systems typically are 100 percent duty cycle, available with machine torches, and designed to use a variety of compressed gases to fine-tune the cut quality for different materials. These systems are available in various sizes and capacities from 130 to 800 amps.
Many other advances have been made to improve reliability, performance, consumable life, cut quality, and ease of use since the first plasma system was created. The process shares the cutting market with laser cutting, abrasive waterjet, and oxyfuel cutting, all of which deliver accuracy, productivity, and long-term cost-effectiveness when used for the appropriate applications.
What can be considered light duty?
A light duty plasma cutting machine can become a need for any workshop, artist, contractor, etc. that so far have been using oxy-fuel and is ready to make the leap to a better solution.
Actually, after experiencing a handheld plasma machine, almost nobody wants to return to oxy-fuel.
That is because even a light-duty plasma cutting system can make a big difference in efficiency and productivity.
So, in this post, we are going to consider what a light-duty plasma cutting system is and which one you should get.
But before getting into this amazing topic, let’s consider what plasma cutting is.
Most people classify plasma cutting systems in light, medium and heavy-duty. A handheld plasma cutting machine used in a small cutting table can be considered light-duty.
In general terms, a medium-size cutting table powered by some plasma cutting machine would be a medium-duty system.
A mechanized cutting system, which could occupy the heavy-duty slot, can be built in a stronger structure and composed by more than one cutting machine.
But that classification is not a general rule for plasma cutting manufacturers.
For the sake of this post, as quoted before, we are considering a handheld or portable plasma cutting machine as a light-duty one.
Now, before buying a light-duty plasma system, you may need to know when to use a portable and when to use an automated system. So, let’s consider some of it.
What Are The Advantages Of Fiber Laser Cutting Machine
Fiber laser is well received in the market now, because of its outstanding advantages of good beam quality and high conversion efficiency, it is widely loved in some finishing fields. At present, the proportion of fiber laser in the industrial field is close to 50%, which is also a kind of active choice for products in many industrial applications. Compared with traditional gas and solid-state lasers, fiber lasers have great advantages as frequency conversion light sources. In this article, we are going to talk about what is fiber laser cutting machine, what are the features, advantages & benefits of fiber laser cutting machine and applications & uses of fiber laser cutting machine.
What Is A Fiber Laser Cutting Machine?
Fiber laser cutting machine is a new type of machine in the world, which is used to output high energy density laser beam. The laser beam is concentrated on the surface of the workpiece, so that the area of ultra-fine focus on the workpiece is instantly melted and evaporated, and the spot is moved through the CNC mechanical system. Automatic cutting by illuminating the position. Compared with large volume gas laser and solid-state laser, it has obvious advantages and has gradually become an important choice in high-precision laser processing, lidar system, space technology, laser medicine and other fields.
The optical plate fiber laser cutting machine can be used for both plane cutting and oblique cutting, with neat and smooth edges. It is suitable for high precision cutting of metal plate. At the same time, the manipulator can replace the original five axis laser for 3D cutting. Compared with ordinary CO2 laser cutting machine, it saves more space and gas consumption, and has high photoelectric conversion rate. It is a new energy-saving and environmental protection product, and also one of the world’s leading technology products.
|
|
|
How we got duped into cooking with gas |
Posted by: O789K - 09-28-2021, 12:49 AM - Forum: FPS and Shooters
- No Replies
|
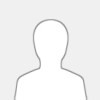 |
How we got duped into cooking with gas
How we got duped into cooking with gas
Gas stove actually unleash indoor air pollutants like soot, formaldehyde, carbon monoxide, and nitrogen dioxide. Beyond that, greenhouse gas emissions from fossil fuels like natural gas drive climate change. That’s why there’s a push now to electrify homes; electric stoves can run on clean energy.
The history of how “cooking with gas” campaigns have made a source of fossil fuel combustion in our homes seem completely innocuous gets pretty ridiculous. Leber dug up a rap video from 1988 that spends an entire four minutes hyping up gas stoves in rhyme. “Gas is so hot, it’s not on when it’s off / it’s the only way to cook, that’s what I was taught,” the rap starts off.
Fast forward to about two minutes into the video, however, and there’s a disclaimer in the lyrics that my colleague Sean O’Kane noticed: “Safe cooking begins with range location / avoid main traffic paths and also isolation.”
Today, gas groups pay social media influencers to advertise the supposed benefits of cooking with the fossil fuel, Leber reports. A public relations representative even posed as a resident in a neighborhood to stir up backlash against building codes that would discourage natural gas hookups in new construction, she writes.
You have to read the truly bizarre and alarming history of gas that Leber traces in her article. With many of us spending more time working and hanging out at home during the pandemic, it’s more important than ever to be aware of what we’re exposed to inside the place that’s supposed to be our refuge.
How to Deep Clean Your Gas Stove Burners Using Natural Cleaners
No library of kitchen cleaning tips would be complete without an article on deep cleaning gas and electric burners! Dirty, greasy gas burner grates and drip pans not only age the appliance, but they also can affect your cooking and present a fire hazard. Cleaning stove burners is simple when you use these tips from the pros. Read on to see how you can get your stove sparkling clean with gas stove cleaner made from natural ingredients.
How Often To Clean Gas Stove Burners
Tempered glass gas stove is easy to maintain. However, when the flow of gas gets blocked, the burner heads can’t burn efficiently. Check the gas burners for irregular flame patterns and yellow flames. These are the best indicators that it’s time to grab your gas stove cleaner and get to work. Other than that, cleaning your gas stove monthly should keep it working at its best.
Here’s what you’ll need to get your gas burners clean:
Dishwashing detergent
Baking soda
Non-abrasive scrub pad
Cleaning cloths
Old toothbrush
Paper clip
Cleaning Gas Stove Burners and Caps
If you have a cooktop with a pilot light, you’ll need to shut off the gas valve first. Gas burners have a removable ceramic cap that diffuses the flames. Beneath the caps, the burner head sits atop the gas tube. Remove the caps and the burner heads by carefully lifting them straight up. Avoid damaging the ignition electrode if you have one.
Soak the burner heads and caps in soap and warm water for 30 minutes. Scrub buildup from the burner heads and caps using a non-abrasive scrub pad and an old toothbrush. If the port openings are clogged, use a paper clip to clear them. Be careful not to damage the metal.
How To Clean Electric Stove Burners
Here’s what you’ll need to get your burner stand clean:
Dishwashing detergent
Baking soda
Non-abrasive scrub pad
Microfiber towel
Cleaning cloths
If your coils and drip pans have caked-on grime, turn the burners on for a few minutes to burn off residue. After they cool, wash the drip pans with warm soapy water and cover them completely with a mixture of 2 parts baking soda and 1 part water. Let the drip pans sit for 15 minutes.
While the drip pans are soaking, wipe down the stove coils with a damp cloth to remove stains and residue. Scrub the drip pans and rinse the baking soda mixture. Use fresh soapy water to wash off the residue, then rinse and dry. Buff them to a nice shiny finish with a microfiber towel. Now, on to your stovetop.
How to Clean Your Stovetop
For gas stovetops, use caution and avoid getting the electric starter wet. Degrease the stovetop by wiping it down with a damp cloth to loosen up the top layer of residue. Use a sponge and soapy water to cut through the grease and wipe down your stovetop with a damp cloth to remove the cleaning solution.
For tough buildup, turn to your homemade baking soda mixture. Spread your cleaning paste over the entire stovetop and let it sit for at least 15 minutes. Scrub the stovetop and wipe off the baking soda cleaner with a clean, damp cloth.
If you are intimidated by cleaning your gas or electric stove, or any other place in your kitchen, don’t fret. Call The Maids for a free estimate and get that good-as-new, clean home feeling you love.
Gas stove tops offer quick temperature control and are more affordable to use than electric stove tops.
The best material for a gas stove is one that can conduct and distribute heat evenly, and respond quickly to temperature changes.
For the best cookware for gas stoves, look for ones that are made of stainless steel with aluminum or copper layers.
The average household gas stove looks like it can handle quite a bit. Its sizable build, durable fabrication, rugged cast iron grates, all signify a hard-wearing kitchen appliance.
Still, as with any appliance, especially one used practically every day to prepare food, it’s important to handle gas stoves with care. This means making sure the stove is well-maintained, properly cleaned, and used with the right cookware.
While technically any pot or pan can be used on a gas stove, there are certain materials that are better suited for its open-flame style of cooking. We recommend our own stainless steel cookware for gas stoves. In this article, we’ll share what those materials are, explain why they work so well, and round up some of the best cookware for gas stoves available today.
The Features of a Gas Stove
Iron gas stove may be older than electric stoves, but they’re still the preferred option for a number of reasons.
First and most important is how easy it is to adjust the heat of a gas stove. A burner can be turned on and off in an instant. And every twist of the control knob creates an immediate corresponding change in the burner’s flame level — a lightning quick heat response that’s crucial in cooking.
Many cooks also like how the flames provide a convenient visual cue about the stove’s current heat setting. This can be a bit trickier to gauge with the dark glass tops of electric or induction cooktops.
An added bonus of the open flame is that it lends itself well to quickly roasting a few small items, like corn tortillas, bell peppers, or marshmallows.
Cooking with gas is also comparatively cheaper than cooking with electricity. Gas stoves generally run on propane, butane, petroleum, or natural gas, all of which are quite affordable. This gives gas stoves an advantage, not only for the cost-conscious home cook, but for anyone who finds themselves in the middle of a power outage.
As for cookware, gas stovetops easily accommodate a wide range. They can be used with just about any type of cookware material and shape — from small skillets to tall stockpots. Woks in particular were designed to be used over an open flame.
Flames, however, don't naturally distribute heat in a uniform manner. Some parts of a pan will have more contact with stronger flames than other parts, and the heat can be very concentrated, especially on a low setting.
Add this to a gas stove’s ability to change temperatures in an instant, and it's easy to see why it's so important to use cookware that can ably withstand these variations.
Choosing the Best Portable Gas Stove
Portable gas stoves are crucial gear for the gourmet on the go. These stoves usually come with a burner and a cooking surface, and they let you boil, simmer, sauté, and fry. If you can do it on a stovetop at home, you can do it on a portable stove.
Folding gas stove is different than a portable gas grills. Portable grills are similar to the grills you use at home. If you want to grill up hot dogs, chicken, or vegetables, you’re good to go with a portable grill. But sometimes you want more than your standard backyard barbecue menu, and that’s where a portable gas stove comes in. These have burners more like a traditional stove. They often come with containers to cook in, but many can also be used with other types of pots, pans, and skillets like a regular stovetop.
What Kind of Portable Gas Stove Do You Need?
The adventures you have on the trail aren’t like anyone else’s. Your needs and your priorities are unique. That’s why there are stoves for every type of outdoor explorer, from long-distance backpackers to car campers.
As you think about your needs, there are some specific features you may want to think about:
Size – If you’re hiking, you’ll want to save as much space and weight in your pack as possible. If you’re getting to base camp and setting up quickly, you might be more willing to haul a little more gear in the name of having the perfect home away from home.
Fuel type – There are three main liquid fuels. Each have their own considerations and limitations. Then there’s our Jetpower fuel, which combines the benefits of both.
Propane is the most common camp stove fuel. It’s high-performance, and you can find it just about everywhere. Propane is what powers the Genesis base camp system, and Jetlink technology lets you build a high-efficiency network of burners from one propane tank.
Isobutane has a lower boiling point, and it’s lighter. That means it’s easier to carry, and it’s more efficient in colder environments. However, it’s also more expensive.
Butane is the cheapest fuel for a portable gas stove, but it’s also the least efficient and reliable. It has the highest boiling point and the lowest vapor pressure of the three gases.
Jetpower is Jetboil’s engineered blend of propane and isobutane. It’s a unique mix that combines the best aspects of both, and it’s what we trust to power most of our stoves. Jetpower delivers high vapor pressure in all four seasons.
Cost – Cost is certainly a factor in choosing a portable gas stove, and there are options at every price point. However, it’s worth noting that sometimes paying more up front can save money in the long run. A high-efficiency stove means you’ll spend less on fuel over time, and durable equipment means you won’t have to buy a replacement for a long time.
Durability – Most people want a stove that holds up outdoors as well as they do. Knowing that you’ve got a well-engineered stove means knowing you’ve got a reliable one.
Number of burners – How big is the group that you’re feeding? If you’re solo, or just out with a partner, you can probably get away with one. But if you’re feeding a group, you may want a setup like the Genesis, which starts with two burners and can expand as your group dose.
Utility – What are you cooking? Are you boiling soup? Are you making a three-course meal? The meals you plan to cook may be the biggest factor of all in choosing the stove that suits your needs.
|
|
|
How to Choose a Transformer: Dry Type vs. Oil Cooled |
Posted by: O789K - 09-28-2021, 12:47 AM - Forum: FPS and Shooters
- No Replies
|
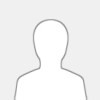 |
How to Choose a Transformer: Dry Type vs. Oil Cooled
How to Choose a Transformer: Dry Type vs. Oil Cooled
Transformers are common and useful devices which take high voltage electricity directly from a power station and convert it to a lower voltage. This allows the energy to be safely and efficiently used by machinery and appliances that can only handle low voltage in spaces such as offices, transportation hubs, schools and factories.
Through this process transformers generate a lot of heat that must be dissipated to keep them running safely. There are two types of transformers being used in the industry currently: Dry-type transformers and oil-cooled transformers. Dry-type uses air as a cooling medium, and liquid cooled uses oil. Although both types have the same end result there are a number of differences between them worth noting, that will affect which type you choose.
Maintenance: Oil cooled transformers required more maintenance procedures, which must be performed more often than dry-type. The oil needs to be sampled to test for contamination, whereas dry type transformer is very resistant to chemical contaminants.
Costs (Initial and Operating): Compared to oil cooled, dry type has a significantly higher operating loss. Oil filled transformers have a higher standard energy efficiency, and as a result have a higher lifespan than dry type.
Noise: Oil cooled transformers have a lower operating sound level, thus less noise pollution than dry-type.
Recyclability: The end of life recycling for dry type is limited, while oil units boast an easier core/coil reclamation. Oil cooled have superior operating life and maintainability, producing less waste and requiring less replacements and labor.
Efficiency: Dry type transformers are larger units, limited in voltage and size, making them more prone to overheating if they experience overload. As a result, they have higher electrical losses, and it is more expensive to maintain dry type power supply over time. Oil cooled units are smaller and more efficient. They require less demand and create a smaller environmental footprint.
Voltage Capabilities: Dry type transformers are designed to handle small to medium MVA and voltage ratings, making them ideal for smaller applications. Oil cooled transformers can handle heavier loads, so applications that require higher voltages will require oil units.
Location: Location of the transformer will be the biggest determinant for which type you will need. Dry type is specified for use in buildings and near buildings, simply because they are environmentally safer. Dry type transformers are less flammable and pose less of a fire risk, making them ideal for shopping malls, hospitals, residential complexes and other commercial areas. Oil cooled transformers are used in outdoor installations due to the possibility of oil leakage and spills which pose a fire risk, but these units are more environmentally friendly.
Taking these variables into account, oil units appear to be the better option overall with higher energy efficiency, recyclability, low noise pollution, lower operational costs and a small environmental foot print. However, oil units simply cannot be used in any situation. Dry type is the best and many times, required option for commercial and indoor operations, because they are safer units to operate around people and areas where fire hazards may exist.
Types of transformer
Oil Immersed Transformer
As the name suggests the coils in this type of transformers are immersed in oil (mostly mineral oil) which helps in keeping the temperature of the transformer under control. This oil type transformer dissipates the through the radiators which are attached on the tank of the transformer and are referred to as ONAN type transformer. To further improve the cooling of the transformer the radiators are installed with fans which helps in bringing down the temperature and referred to as ONAF type transformer. This type of transformer can reach high voltage capacity, in some cases 1000kV.
Dry Type Transformer
In this type of transformer, air is used as the cooling medium. They are made using vacuum pressure impregnation in polyester or silicone varnish. Some of them are also made using VPI epoxy and cast resin for tougher environmental conditions. Since they are limited with regards to cooling aspect the maximum voltage is limited up to 35kV.
Switchgear
Switchgear is electrical distribution equipment: it accepts power from a source, routes it to a number of outputs and provides overcurrent protection and control functions. Of the types of distribution equipment described in the NFPA 70: National Electrical Code Article 408: Switchboards, Switchgear and Panelboards, switchgear is generally the most robustly constructed, the largest and the most expensive. It’s typically applied in high-reliability facilities, like hospitals or data centers, where continuity of power is critical to effective operation.
Switchgear is available in a wide range of voltage ratings, from below 1,000 volts to more than 200 kilovolts. Medium-voltage switchgear, rated above 1,000 volts, is manufactured by producers in a variety of configurations. Assemblies are available for exterior padmount installation, vault installation or installed in dedicated freestanding metal buildings, with air, gas, vacuum or oil as insulating media. This discussion will focus on interior low-voltage switchgear.
The alternative to switchgear is switchboard construction. Switchboards generally require less space and are less expensive. Both are typically constructed of a number of vertical sections. Each section is enclosed in sheet metal, with openings in front for overcurrent protection devices, monitoring equipment and control devices. A section may contain a main overcurrent protection device, metering devices, automatic control and monitoring systems, overcurrent protection devices for distribution feeders or a combination of these or other equipment specific to the installation. Overcurrent protection is typically accomplished with circuit breakers, with fused switches are less frequently.
Electric power substation
An assembly of equipment in an electric power system through which electrical energy is passed for transmission, distribution, interconnection, transformation, conversion, or switching. See Electric power systems
Specifically, substations are used for some or all of the following purposes: connection of generators, transmission or distribution lines, and loads to each other; transformation of power from one voltage level to another; interconnection of alternate sources of power; switching for alternate connections and isolation of failed or overloaded lines and equipment; controlling system voltage and power flow; reactive power compensation; suppression of overvoltage; and detection of faults, monitoring, recording of information, power measurements, and remote communications. Minor distribution or transmission equipment installation is not referred to as a substation.
Substations are referred to by the main duty they perform. Broadly speaking, they are classified as: transmission substations, which are associated with high voltage levels; and distribution substations, associated with low voltage levels. See Electric distribution systems
Substations are also referred to in a variety of other ways:
1. Transformer substations are substations whose equipment includes transformers.
2. Switching substations are substations whose equipment is mainly for various connections and interconnections, and does not include transformers.
3. Customer substations are usually distribution substations on the premises of a larger customer, such as a shopping center, large office or commercial building, or industrial plant.
4. Converter stations are complex substations required for high-voltage direct-current (HVDC) transmission or interconnection of two ac systems which, for a variety of reasons, cannot be connected by an ac connection. The main function of converter stations is the conversion of power from ac to dc and vice versa. The main equipment includes converter valves usually located inside a large hall, transformers, filters, reactors, and capacitors.
5. Most substation is installed as air-insulated substations, implying that the bus-bars and equipment terminations are generally open to the air, and utilize insulation properties of ambient air for insulation to ground. Modern substations in urban areas are esthetically designed with low profiles and often within walls, or even indoors.
6. Metal-clad substations are also air-insulated, but for low voltage levels; they are housed in metal cabinets and may be indoors or outdoors.
7. Acquiring a substation site in an urban area is very difficult because land is either unavailable or very expensive. Therefore, there has been a trend toward increasing use of gas-insulated substations, which occupy only 5–20% of the space occupied by the air-insulated substations. In gas-insulated substations, all live equipment and bus-bars are housed in grounded metal enclosures, which are sealed and filled with sulfur hexafluoride (SF6) gas, which has excellent insulation properties.
8. For emergency replacement or maintenance of substation transformers, mobile substations are used by some utilities.
An appropriate switching arrangement for “connections” of generators, transformers, lines, and other major equipment is basic to any substation design. There are seven switching arrangements commonly used: single bus; double bus, single breaker; double bus, double breaker; main and transfer bus; ring bus; breaker-and-a-half; and breaker-and-a-third. Each breaker is usually accompanied by two disconnect switches, one on each side, for maintenance purposes. Selecting the switching arrangement involves considerations of cost, reliability, maintenance, and flexibility for expansion.
A substation includes a variety of equipment. The principal items are transformers, circuit breakers, disconnect switches, bus-bars, shunt reactors, shunt capacitors, current and potential transformers, and control and protection equipment. See Circuit breaker, Electric protective devices, Electric switch, Relay, Transformer
Good substation grounding is very important for effective relaying and insulation of equipment; but the safety of the personnel is the governing criterion in the design of substation grounding. It usually consists of a bare wire grid, laid in the ground; all equipment grounding points, tanks, support structures, fences, shielding wires and poles, and so forth, are securely connected to it. The grounding resistance is reduced enough that a fault from high voltage to ground does not create such high potential gradients on the ground, and from the structures to ground, to present a safety hazard. Good overhead shielding is also essential for outdoor substations, so as to virtually eliminate the possibility of lightning directly striking the equipment. Shielding is provided by overhead ground wires stretched across the substation or tall grounded poles. See Grounding, Lightning and surge protection
|
|
|
The Surprising History of the Tank Top |
Posted by: O789K - 09-28-2021, 12:44 AM - Forum: FPS and Shooters
- No Replies
|
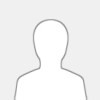 |
The Surprising History of the Tank Top
The Surprising History of the Tank Top
When the summer months are upon us, one of the most popular items in many wardrobes is the tank top.
It can be dressed up with a jacket and smart jeans, or dressed down with pajamas and worn to bed.
Tank tops keep your arms and neck cool while covering the rest of your upper body.
When the temperature is warm, they provide just the right amount of coverage.
When did tank tops make their way into modern society?
Before the 1920’s, men and women were not seen showing their arms off in public.
However, the Roaring Twenties brought about a revolution in the world of fashion and clothing.
Women were cutting their hair shorter, wearing dresses which were more revealing than the previous trends, and enjoying human contact (such as rebellious hand-holding!) with their male partners while they danced or walked down the street.
Tank Tops in the Olympic Games
The introduction of women’s swimming into the Olympic Games came along in 1912, held in Stockholm, Sweden.
A total of 27 women competed in the swimming events at these particular games, and their swimwear was deemed “immodest” by many news outlets and spectators.
The costumes they wore were very similar to modern-day tank tops, but with an added piece which resembled shorts to cover the top half of the thighs.
While we might call it a “swimming pool” these days, back in the 1920’s, it was known as a swimming “tank.”
Thus, the items worn by female swimmers were referred to as “tank suits,” in other words, a suit which was worn in the tank!
Tank suits were made from a variety of materials including silk, which was considered very immodest since it was often see-through after going in the water.
Cotton was also used, and heavy woolen materials were considered the most modest since they were so thick and concealing.
The top of a tank suit had straps which were almost identical to the straps we see on tank tops today.
The straps would keep the suit up, but the lack of sleeves gave female swimmers the freedom of movement and flexibility that they needed in order to perform to their full potential in the pool.
Definition
A waist trimmer is a shaping garment similar to a girdle. The waist trainer pulls a person’s midsection in as tight as possible. The idea behind a waist trainer is that the pulling action gives the person a sleeker, smaller waist.
Waist trainers usually consist of a combination of tough fabric and hard fibers. Hooks, Velcro, lacing, or other strong fasteners hold the trainer tightly in place.
Advocates believe that it is possible to “train” the waist to retain a slimmer shape after frequent wearing of the garment over an extended period. Some people suggest that wearing a waist trainer while working out can aid weight loss.
Do they work?
Waist trimmer of sweat work in a similar way to corsets, which fell out of fashion due to discomfort and health concerns.
A waist trainer can produce a temporary reduction in waist size or circumference, and a person will typically see immediate results. However, as soon as they take off the waist trainer, their waist will no longer look smaller.
Also, waist trainers do not reduce a person’s body fat. People looking to lose body fat around their midsection or lose substantial weight overall should not rely on wearing a waist trainer to do this.
However, a person may feel a loss of appetite while wearing a waist trainer. The garment puts pressure on the stomach, which can create an artificial feeling of fullness.
Short sleeve button up
shirts
and polos… they get a bad rap, man. I think that’s mostly because the nerds and dorks who wear them in TV shows and movies wear them all wrong.
The fit is off, the color is off, the length is off… everything is wrong.
But in warm weather, short sleeve
shirts
are a life-saver! Especially if you run hot, like myself.
In this article, we’re gonna cover every detail about how a short sleeve button up
shirt
and polo
shirt
should fit.
Let’s get into it!
By the way, click on any of the fit images below to enlarge in a new tab (for a more detailed view!)
HOW SHOULD A SHORT SLEEVE
SHIRT
FIT OVERALL?
Overall, your short sleeve button-up
shirt
should fit slim, but not too tight.
Try the sit down test. When trying on a new
shirt
, button it up like you normally would, and then sit down in a chair.
It should feel as comfortable (and have enough give) sitting down as it is while standing. The buttons shouldn’t be pulling apart; the
shirt
shouldn’t be stretching like spandex on your torso.
By the way, the short sleeve
shirts
you see in these photos are from Peter Manning. PMNYC is a long-time partner of EG and I’m psyched to have their short sleevers as the perfect example of a well-fitting short sleeve
shirt
in this article.
If you haven’t come across PMNYC yet and you’re a shorter / smaller guy, you’ve probably run into the issue of clothing proportions being off somehow… Whether it’s:
the shirt being too long
the sleeves being too long & wide
or the pockets being too big and low on your
shirts
and pants
Peter Manning’s taken care of all that with their clothing. They’re designed specifically for the guy of smaller stature (5’8″ and under), meaning everything—length, width, proportion, even pocket sizes!—are designed with the smaller man in mind.
16 Different Types of Sleeves
There are many different sleeve styles that can be loose and flowy, structured or puffy, long or short, and can be made from any kind of fabric.
Set-in sleeve. A set-in sleeve is a sleeve that is attached to the garment’s armhole and sewn all the way around. Most sleeves, if they are not continuous with the bodice’s fabric are set-in sleeves.
Bell sleeves. Also called peasant sleeves, this long sleeve is fitted around the shoulder and upper arm and flares out to the wrist, like a bell.
Cap sleeves. A cap sleeve is an extremely short sleeve that doesn’t extend very far from the shoulder and doesn’t go below the armpit. It can have a gathered, elastic seam or a loose seam.
Kimono sleeves. A kimono sleeve is a sleeve that is in one piece with the garment’s bodice and is not sewn on separately. The sleeve is generally wide with a uniform circumference throughout. These are generally used for Chinese-style robes, not Japanese kimonos, despite their name. For a Japanese kimono, the sleeves are usually sewn separately.
Raglan sleeves. A raglan sleeve extends from a garment's neckline, rather than from the shoulder, and this allows better movement. This type of sleeve is used for baseball t-shirts.
Bishop sleeves. A bishop sleeve flares out from the shoulder, giving volume to the sleeve all the way to the cuff, where the fabric is tightly gathered.
Butterfly sleeves. Like a bell sleeve, a butterfly sleeve flares out from the shoulder, but it usually does not fully cover the arm.
Flutter sleeves. A flutter sleeve is very similar to a butterfly sleeve except it is generally a little shorter and wider, falling loosely
Dolman sleeves. This is a type of sleeve that has a very deep armhole, and the sleeve gets progressively narrower to the wrist. This type of sleeve is also called a batwing sleeve, due to its likeness to wings.
Puffed sleeves. A puffed sleeve is gathered at the shoulder and at the seam but is full and “puffy” in the middle.
Cape sleeves. Cape sleeves are full and flowing sleeves that look like capes. The fabric is gathered at the shoulder and flares out like a cape from there.
Lantern sleeves. A lantern sleeve is a long sleeve that balloons out between the wrist and the elbow and then gathers again around the wrist.
Balloon sleeves. Balloon sleeves are long, puffed sleeves that are gathered at the shoulder and then puffed out and gather back at the wrist. Sometimes, the sleeve puffs out lower than the shoulder, but it is still a full puff rather than a tapered flare.
Slit sleeves. A slit sleeve is a sleeve that has a slit down the center usually exposing part of the arm. This sleeve can also be called a cold shoulder sleeve.
Leg-of-mutton sleeves. This sleeve is gathered and puffed by the shoulder and upper arm and then fitted on the forearm. This style of sleeve somewhat resembles a sheep’s leg, hence the name.
T-shirt sleeve. A t-shirt sleeve is a short, set-in sleeve that starts at the shoulder and ends at the middle of the upper arm.
|
|
|
Food Additives: What Parents Should Know |
Posted by: O789K - 09-28-2021, 12:39 AM - Forum: FPS and Shooters
- No Replies
|
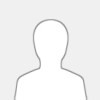 |
Food Additives: What Parents Should Know
Food Additives: What Parents Should Know
Food additives have been used for thousands of years, ever since people realized salt could keep meat from spoiling. Today, there are more than 10,000 additives approved by the U.S. Food and Drug Administration (FDA) to preserve, package, or modify the taste, look, texture, or nutrients in foods. But increasing evidence suggests some chemicals used as food additives should be avoided―especially for children.
How do food additives affect kids?
The American Academy of Pediatrics (AAP) policy, "Food Additives and Child Health," explains that a rising number of studies suggest some food additives may interfere with hormones, growth, and development Some may also raise a child's risk of obesity. Children may be particularly susceptible to the effects of these additives, given that they have more exposure than adults due to their size and dietary intake.
Below is a list of the most commonly used food additives and the current health concerns. This list includes indirect additives, which are used in processing or packaging, as well as direct additives that are put directly into foods.
How to reduce your family's exposure to food additives
Buy fresh or frozen. It's best to buy and serve fresh or frozen fruits and vegetables when possible.
Eat fewer processed meats. Try to avoid processed meats, such as hot dogs, ham and meats in pre-packaged meals, especially during pregnancy.
Wash plastic food containers and utensils by hand, rather than in the dishwasher. Heat can cause plastics to leak BPA and phthalates into food. Avoid microwaving food or beverages―including infant formula and breastmilk―in plastic, if possible.
Use glass and stainless steel. Especially when cooking or serving hot foods, use alternatives to plastic, such as glass or stainless steel, when possible.
Learn plastic recycling codes. Look at the recycling code on the bottom of products to find the plastic type. Try to avoid plastics with recycling codes 3 (phthalates), 6 (styrene), and 7 (bisphenols) unless plastics are labeled as "biobased" or "greenware," which means they are made from corn and do not contain bisphenols.
Wash your hands. Because chemicals from plastics are so common in items we touch throughout the day, be sure to wash your hands thoroughly before and after handling food.
Speak out. Join the AAP and other organizations calling for more research into food additives' safety, including improvements to the U.S. food additive regulatory program and retesting some previously approved additives. A recent review of nearly 4,000 food additives showed that 64% of them had had no research showing they were safe for people to eat or drink. While some change to the current law could be achieved by the FDA, some may require congressional action.
Common questions from parents about food additives
How do I find out which additives are in foods?
Additives that are put directly in foods are listed on ingredient labels, but often with their chemical names. For example, salt may be listed as sodium chloride, sugar as sucrose, vitamin C as ascorbic acid, and vitamin E as alpha-tocopherol. Artificial colors are usually listed by their numbers, such as Blue #2 or Yellow #5. However, there are also indirect additives from processing or packaging materials that are not listed on the ingredient labels. These can include chemicals from plastic, glues, dyes, paper, cardboard, and different types of coatings.
Are additives a problem in any baby products?
The FDA recently banned BPA from baby bottles and sippy cups, but the chemical is still used in some food and beverage containers. Many companies have voluntarily removed BPA from their products, but in many cases replaced it with chemicals such as bisphenol S (BPS) that may have similar health effects. In 2017, the Consumer Product Safety Commission banned the use of some phthalates in child-care products such as teething rings.
Do artificial food colors cause childhood hyperactivity?
More research is needed to better understand how artificial food colors (AFCs) may or may not impact a child's behavior. This is because much of the original research on these additives were animal studies that did not include behavioral affects. For some children with attention-deficit/hyperactivity disorder (ADHD) and other problem behaviors, the AAP says that until we know more, it may be helpful to eliminate AFCs from their diet if they seem to worsen symptoms.
The future of food additives
Many new techniques are being researched that will improve how additives are produced. One approach is the use of biotechnology, which can use simple organisms to produce food additives. These additives are the same as food components found in nature.
Talk with your pediatrician
Although there are ways to limit the amount of potentially harmful food additives in your family's diet, stronger federal food safety requirements will help keep all children healthy.
If you're concerned about food additives, talk with your pediatrician. Your regional Pediatric Environmental Health Specialty Unit (PEHSU) have staff who can also talk with parents about concerns over environmental toxins.
There are many different methods used to produce natural plant extract powder. Durning an extraction process a solvent is used to draw out the plant extracts, common solvents utilised are water or alcohol. Once the desired compounds are extracted the solvent is then removed. The plant extraction method used depends on whether specific compounds of the plant are desired to be extracted or the full range of plant compounds. Here we take a close look at the different methods of extraction.
1. LIPOPHILIC EXTACTION // Lipophilic are oil loving (fat soluble) and therefore soluble in oil. Macerated or Infused oil are Lipophilic extracts. This includes fat soluble vitamins (A, D, E, K), carotenoids, bisabolol and other lipophilic active ingredients. Note: Vitamin C is an extremely sensitive hydrophilic vitamin and therefore it is NOT present in plant oils, however some plant oils exhibit Vitamin C behaviours, research, I am sure one day may explain these 'effects'.
HOW IT WORKS // Plant material is added to a carrier oil. Maceration is performed as cold or warm-cold. Usually the procedure takes a few days to several weeks and the plant material is renewed several times during the maceration period. Heat or sun are applied as sources of energy.
Ingredient Example // St Johns Wort Infused Oil
2. SUPERCRITICAL EXTRACTION (CO2) //Supercritical extraction uses CO2 (Carbon dioxide - an oxygen-free process) instead of organic solvents.
HOW IT WORKS // At a temperature and pressure above its critical point, a molecule will become a supercritical fluid, which is not quite a gas, but not quite a liquid. Supercritical fluids can be used under high pressure to extract a full range of phytochemical types. CO2 has a high diffusion rate that can penetrate the material quickier than liquids. It is a pure substance found in nature and is, thus, easily removed from the final extract without leaving any residue.
Among its advantages, supercritical CO2 extraction has the flexibility to extract specific compounds, and it operates at temperatures lower than expeller press and organic solvent methods. It also involves no oxygen, thus better preserving the extracted compounds.
CO2 extraction delivers the superior active properties of the plant without the use of any chemical solvents or the production of residues & impurities or issues with rancidity. Supercritical CO2 extraction is not ideal for all ingredients, this method is only applicable to materials that are lipid soluble.
A natural instant fruit juice powder is a powder made from the juice of fresh fruit and then dried into a fine powder. Fruit juice powders are basically concentrated fruit juice dehydrated by spray-drying method. Its moisture content is 1%-3%. The spray drying process is considered a conventional method to convert fruit juices to powder form. It can be used in drinks, dressings, marinades, desserts, smoothies etc. One must not get confused between fruit powder and fruit juice powder as the two are totally different. Powders are made from drying the whole fruits while fruit juice powders are made from drying the pure juice.
What is an API?
An API is defined as a specification of possible interactions with a software component. What does that mean, exactly? Well, imagine that a car was a software component. Its API would include information about what it can do—accelerate, brake, turn on the radio, etc. It would also include information about how you could make it do those things. For instance, to accelerate, you put your foot on the gas pedal and push.
The API doesn’t have to explain what happens inside the engine when you put your foot on the accelerator. That’s why, if you learned to drive a car with an internal combustion engine, you can get behind the wheel of an electric car without having to learn a whole new set of skills. The what and how information come together in the API definition, which is abstract and separate from the car itself.
One thing to keep in mind is that the name of some APIs is often used to refer to both the specification of the interactions and to the actual software component you interact with. The phrase “Twitter API,” for example, not only refers to the set of rules for programmatically interacting with Twitter, but is generally understood to mean the thing you interact with, as in “We’re doing analysis on the tweets we got from the Twitter API.”
|
|
|
What Is Microfiber Leather |
Posted by: I678L - 09-27-2021, 02:16 AM - Forum: Off Topic
- No Replies
|
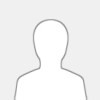 |
What Is Microfiber Leather
What Is Microfiber Leather
Microfiber leather is an abbreviation of ultrafine fiber PU synthetic leather. It is a non-woven fabric made of three-dimensional structure network by carding acupuncture with microfiber staple fiber. After wet processing, PU resin impregnation, alkali reduction, and dermabrasion and polishing And other processes eventually make microfiber leather. It is made by adding ultra-fine fiber to PU polyurethane, which makes the toughness, air permeability and abrasion resistance further strengthened; it has extremely excellent abrasion resistance, excellent cold resistance, breathability, and aging resistance. Eco-friendly, Comprehensive performance beyond real leather. Widely used for automotive, garment, bags, sofa, shoes, boots, basketball, belt, jewellery box and so on. We are specialize in microfiber leather production manufacture.We provide the optimal leather options, the best leather substitute and best leather alternatives for automotive seat covers and interiors, furniture & sofa upholstery, footwear and shoes, bags, garments, gloves, balls, etc.
While synthetic leather were once considered not suitable for high quality shoes, PU microfiber leather has changed how shoes are made.
Microfiber leather is designed to hold up against weather conditions and the wear and tear of walking and running over an extended period of time.
They can retain their form very well, and thus are usually very durable if cared for properly. They're also more water-resistant and lighter than real leather, making them great for long wear and outdoor activities.
We found this video, below, that tests how durable shoes made with suede microfiber leather are. Check it out!
Microfiber leather, or micro fiber leather, is the highest quality grade synthetic leather (faux leather or PU leather), a high-tech simulation of high-end leather material. WINIW Microfiber Leather is simulated the structure of natural leather, using sea-island superfine micro fiber (ultra-fine fiber bundle), and high-grade polyurethane resins as raw materials, using needle punched nonwoven technology of 3D structure, has a lot of similar characters as natural leather, however better physical & chemical performance, has been widely popular around the world. Because of superior performance, WINIW microfiber synthetic leather has been the best leather alternatives and the optimal leather substitute, material, best vegan leather and eco leather, can replace natural leather perfectly!
Compared to natural leather, microfiber synthetic leather has many excellent qualities, such as chemical resistance and physical and mechanical properties. However, preparation of microfiber synthetic leather with a high water vapor transmission rate (WVT), moisture absorption and wearing comfort property is still a challenge. In this study, we prepared thermoplastic polyurethane (TPU)/sulfonated polysulfone (SPSf) electrospun nanofibers and applied them to a microfiber synthetic leather base (MSLB). The effects of TPU/SPSf nanofiber content on the structure and properties of the MSLB were investigated. The results indicated that the TPU/SPSf nanofibers with an average diameter of 0.12?μm were well distributed at all directions in the MSLB. Differential scanning calorimetry analysis showed four Tg peaks, further demonstrating the existence of TPU/SPSf nanofibers. With the increase of TPU/SPSf nanofiber content from 0 to 30?wt%, the contact angles decreased gradually from 111.64° to 67.07°, leading to 55.19% improvement in the WVT value (from 2868.96 to 4452.24?g/(m2?24?h)) and 26.25% improvement in the moisture absorption (from 628.70% to 793.75% mm/s). Simultaneously, when the nanofiber content was 30?wt%, the nanofibers tended to bundle and 6.79% decrement of air permeability was observed. Specifically, the softness of the MSLB was improved by 88.55%. Moreover, the thermal stability and the tear strength were also obviously enhanced. Consequently, this research provided a feasible and promising way to prepare a high-performance MSLB using TPU/SPSf nanofibers.
The difficulty in dyeing microfiber base filled with ordinary polyurethane presents a significant challenge in maintaining the uniformity and highly realistic appearance of the resulting products. In the present study, a type of acid-dyeable polyurethane (PU-MDEA; MDEA=N-methyldiethanolamine) was synthesized, and its chemical structure and dyeing properties were investigated. Nuclear magnetic resonance analysis indicated that cationic groups were successfully incorporated into the PU-MDEA backbone via chain extension using MDEA. The amorphous nature of PU-MDEA was determined by differential scanning calorimetry, X-ray diffraction, and polarizing optical microscopy. Owing to the strong binding between these cationic groups and acid dye, as well as the reduced resistance to dye penetration, PU-MDEA showed better dyeability toward the acid dyes studied herein when compared with the control sample (microfiber synthetic leather filled with ordinary polyurethane). The adsorption isotherm experiment revealed that the dyeing process conformed to the Langmuir model, thereby indicating that the acid dyes attached to PU-MDEA via strong ionic bonding rather than van der Waals forces or hydrogen bonding. Additionally, it was found that the wastewater resulting from the dyeing of the microfiber synthetic leather filled with PU-MDEA exhibited environmentally friendly characteristics when compared with that displayed by the control sample (microfiber synthetic leather filled with ordinary polyurethane). Thus, the current results show the potential of PU-MDEA, as a filler, in the manufacture of microfiber synthetic leather to achieve fast dyeing rate, high dye uptake, and good color fastness, thereby improving the uniformity and highly realistic appearance of the resulting products.
Bonded leather is called ‘leather’ because it incorporates scraps of leather remnants, which comprise between 10-20% of its content. The scraps of leather are made into a pulp and stuck to a fibre or paper backer which is then coated with polyurethane and embossed to give it the appearance of genuine leather.
The price of an article is an immediate indication as to whether you are buying genuine leather. At a glance, bonded leather may look like the real thing but it will feel thin to the touch and will lack the softness of real leather, it may also exude a chemical smell.
WHAT IS BONDED LEATHER MATCH?
This term refers to the ability of bonded leather manufacturers to replicate the appearance of real leather, although it is likely that the product may be dyed in a striking range of unnatural colours.
For most people this will be a choice dictated by the comparative low cost of the product; some may choose bonded leather because it can be regarded as environmentally friendly, in so much as it uses left overs and does not involve additional farming and, potentially, reduces landfill. The product is also easy to clean and is likely to come in a wide range of design options.
Bonded leather should be wiped with a clean damp cloth and wiped dry with a different cloth. Spilt liquids should be cleaned immediately but no detergents or abrasive cleaners should be used. Non-alkaline cleaners and non-detergent soaps can be used but the material should always be tested for colour fastness on a small unobtrusive area first.
HOW DURABLE IS BONDED LEATHER?
Bonded leather is not a durable product. Generally, furniture made from bonded leather is likely to peel and crack within two to five years.
WHAT CAUSES BONDED LEATHER TO PEEL AND CRACK?
Bonded leather is a non-elastic material; therefore, it has a tendency to crack with use, strips of polyurethane and leather will then start to peel away from the backing.
WHY IS BONDED LEATHER BAD?
Compared with leather, bonded leather has a very short lifespan. It is prone to cracking and peeling and once it has deteriorated beyond a certain point it is impossible to repair. Although a bonded leather may be cheaper than real leather, it’s short life span means that in the long run the cost of replacing a bonded leather item can be more expensive. There is also the argument that this also makes it less environmentally friendly.
HOW TO REPAIR BONDED LEATHER
There are repair kits on the market which enable you to make small repairs to bonded leather. The affected area must be sanded to remove any protruding bits of leather, a patch can then be dyed to match or the fabric under the peel can be dyed and sealed to stop further peeling. The resulting repair will be noticeable but will be an improvement.
HOW TO FIX BONDED LEATHER SCRATCHES
First clean the area with a white cloth to ensure that no dye is transferred. Then mix a leather repair solution together with an appropriate tint. Add a small quantity of the mixture to the affected area and around the affected area. Then place leather grained paper, supplied with the kit, over the area and gently iron with a warm iron, this will transfer the pattern to the repair. Be careful to ensure that the iron is not too hot because it may discolour or damage the bonded leather. For minor scratches, it may be possible to affect a repair with the use of shoe polish. You should also check any new products on a small inconspicuous area of the leather item first.
Top Grain leather is the second highest grade quality of leather and is the lower part of the top layer of the hide. One removed it is sanded and refinished. It comes in two grades, aniline, which is natural soft leather which is vulnerable to stains and semi-aniline which has a protective coating. Top Grain leather is comprised of twelve to fourteen percent water and consequently it adjusts to body temperature: it is cool in summer and warm in winter. With bonded leather the reverse is the case.
BONDED LEATHER VERSUS REAL LEATHER
Real Leather, also referred to as Genuine Leather is the third grade of leather, taken from the lower, thinner layer of the hide. The surface is then reworked to resemble a higher-grade leather. It is not as tough as Full grain leather or Top Grain leather but is considerably more durable than bonded leather.
BONDED LEATHER VERSUS FAUX LEATHER
Faux leather, sometimes referred to as Pleather, contains no animal products and is made from polyurethane. It can be embossed with any texture and looks and feels like genuine leather. It is water resistant and easy to clean. Unlike bonded leather it does not crack or fade in sunlight, it is however, easy to tear or puncture. It is also considered less environmentally friendly due to the chemicals and toxins used in its production – although this varies depending on the exact process and materials used to produce it.
BONDED LEATHER VERSUS DURABLEND
Durablend is a low-cost leather alternative, similar to bonded leather and comprising of 57% polyurethane, 26% poly/cotton and 17% leather shavings. It is the trademark product of Ashley Furniture. Customer reviews suggest that it shares similar weaknesses with bonded leather in so much as it scratches easily and is prone to cracking.
BONDED LEATHER VERSUS VINYL
Polyvinyl chloride, popularly known as Vinyl or PVC is a faux leather which has been produced since the 1940’s by chemical companies like DuPont. It is used for shoes, car interiors and upholstery. Not as breathable as bonded leather, skin tends to stick to its surface, which makes it unpleasant seating in hot weather, it is easy to clean and maintain. Like bonded leather it cracks with use and is easy to puncture.
BONDED LEATHER VERSUS MICROFIBER
A much more sophisticated form of faux leather: polyurethane resin and ultra- fine microfiber leather for automotive are combined to replicate the microscopic structure of leather. The complexity of its construction mean that it is more expensive than other faux products but it does have a number of advantages over bonded leather. It doesn’t scratch or tear and is non-fading. It breathes like real leather but it also has ant -bacteria and anti-mildew properties. Unlike bonded leather it is completely odourless.
BONDED LEATHER VERSUS REXINE
Rexine is the registered trademark of a British artificial leather which has been produced since the 1920’s. Essentially a cloth backing is coated with cellulose nitrate and embossed to produce the illusion of leather. Primarily used for car interiors this is now regarded as retro faux leather and as such is sort out by collectors.
BONDED LEATHER VERSUS BICAST
Bicast is constructed using a split leather backing to which a layer of polyurethane is applied. The surface is then embossed to give the appearance of leather. It shares many of the qualities of bonded leather: it has a consistent texture and is easy to clean and maintain but it doesn’t breathe like leather and it lacks strength and durability.
BONDED LEATHER VERSUS LEATHERETTE
Leatherette is a plastic based synthetic leather. Unlike bonded leather it does not scratch and it does not fade in sunlight. Like most faux leather, it does not breathe and is unpleasant next to the skin. Although it might be the preferred choice of those who don’t like to use animal products, it is made from non- biodegradable, non-renewable materials and is therefore considered less environmentally friendly.
|
|
|
|