Welcome, Guest |
You have to register before you can post on our site.
|
Online Users |
There are currently 163 online users. » 0 Member(s) | 162 Guest(s) Applebot
|
Latest Threads |
Dominica visa free countr...
Forum: Off Topic
Last Post: axied12
06-24-2025, 12:37 PM
» Replies: 0
» Views: 112
|
Advanced microneedling
Forum: Off Topic
Last Post: axied12
05-28-2025, 01:25 PM
» Replies: 0
» Views: 264
|
Caviar and cheese
Forum: Off Topic
Last Post: axied12
05-28-2025, 12:38 PM
» Replies: 0
» Views: 240
|
Top-rated countertop comp...
Forum: Off Topic
Last Post: axied12
05-04-2025, 06:42 AM
» Replies: 0
» Views: 384
|
Ryanair letenky levně do ...
Forum: Off Topic
Last Post: axied12
02-11-2025, 01:37 PM
» Replies: 0
» Views: 761
|
Trusted essay writing ser...
Forum: Off Topic
Last Post: axied12
01-30-2025, 08:16 AM
» Replies: 0
» Views: 696
|
Bootverkopers - actieve j...
Forum: Off Topic
Last Post: axied12
12-07-2024, 11:07 AM
» Replies: 0
» Views: 824
|
Services for individuals ...
Forum: Off Topic
Last Post: axied12
12-02-2024, 03:31 PM
» Replies: 0
» Views: 794
|
Used excavators
Forum: Off Topic
Last Post: axied12
11-13-2024, 09:22 AM
» Replies: 0
» Views: 748
|
Buy Higo Rocket in Dubai
Forum: Off Topic
Last Post: axied12
10-25-2024, 01:09 PM
» Replies: 0
» Views: 857
|
|
|
Cast Iron Pipe |
Posted by: I678L - 09-27-2021, 02:14 AM - Forum: Off Topic
- No Replies
|
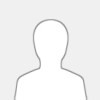 |
Cast Iron Pipe
Cast Iron Pipe
Cast iron pipes can fail in many modes which in general can be summarized into two categories: loss of strength due to the reduction of wall thickness of the pipes, and loss of toughness due to the stress concentration at the tips of cracks or defects. Even in one category there can be many mechanisms that cause failure. The strength failure can be caused by hoop stress or axial stress in the pipes. A review of recent research literature (Sadiq et al., 2004; Moglia et al., 2008; Yamini, 2009; Clair and Sinha, 2012) suggests that current research on pipe failures focuses more on loss of strength than loss of toughness. As was mentioned in Section 3.3.7(b), the literature review also revealed that in most reliability analyses for buried pipes, multifailure modes are rarely considered although in practice this is the reality. Therefore the aim of this section is to consider multifailure modes in reliability analysis and service life prediction for ductile iron pipe. Both loss of strength and toughness of the pipe are considered. A system reliability method is employed in calculating the probability of pipe failure over time, based on which the service life of the pipe can be estimated. Sensitivity analysis is also carried out to identify those factors that affect the pipe behavior most.
Buried pipes are not only subjected to mechanical actions (loads) but also environmental actions that cause the corrosion of pipes. Corrosion related defects would subsequently cause fracture of cast iron pipes. In the presence of corrosion pit, failure of a pipe can be attributed to two mechanisms: (i) the stresses in the pipe exceed the corresponding strength; or (ii) the stress intensity exceeds fracture toughness of the pipe. Based on these two failure modes, two limit state functions can be established as follows.
Steel pipe is manufactured by the pit, horizontal or centrifugal method. In the vertical pit method, a mold is made by ramming sand around a pattern and drying the mold in an oven. A core is inserted in the mold and molten iron is poured between the core and the mold. In the horizontal method, a machine is used to ram sand around horizontal molds that have core bars running through them. The molten iron is poured into the molds from multiple-lipped ladle designed to draw the iron from the bottom to eliminate the introduction of impurities. In the centrifugal method (Figure 3.4), sand-lined molds are used that are placed horizontally in centrifugal casting machines. While the mold revolves, an exact quantity of molten iron is introduced, which, by action of the speed of rotation, distributes itself on the walls of the mold to produce pipe within a few seconds.
Many cast iron pipes made towards the end of the nineteenth century are still in use; their walls were relatively thick and not always of uniform, ‘Spun’ grey iron pipes were formed by spinning in a mould and produced a denser iron with pipes of more uniform wall thickness; they comprise a large proportion of the distribution mains in many countries. Three classes of such pipes were available: B, C, and D for working pressures of 60, 90, and 120 m respectively; classes B and C were more widespread. Carbon is present in the iron matrix substantially in lamellar or flaky form; therefore, the pipes are brittle and relatively weak in tension and liable to fracture. The manufacture of grey iron pipes has been discontinued in most countries, except for the production of non-pressure drainage pipes.
Since cast iron pipes are deteriorating rapidly and causing so many maintenance problems (Section 4.3.2), the distribution network is currently undergoing an extensive replacement scheme with old, leaking and corroded cast iron pipes being replaced by MDPE and uPVC. These new plastic pipe materials are thought to support fewer bacteria than the old hubless cast iron pipe. Their surface is smoother and therefore the surface area smaller and they are not subject to corrosion or biodeterioration.
In addition, the effectiveness of a disinfectant is greatly influenced by the pipe material. Biofilms grown on copper or PVC pipe surfaces were inactivated by a 1 mg/l dose of free chlorine or monochloramine. However, on iron pipes 3-4 mg/l of chlorine or monochloramine was ineffective in controlling the biofilm (LeChevallier et al., 1990) because, as discussed before, the chlorine will preferentially react with the iron surface (LeChevallier et al., 1993). It appears that the option of changing pipe materials to ones with lower biofilm-forming potentials would reduce the biofilm problem.
Many cast iron pipes made towards the end of the 19th century are still in use; their walls were relatively thick and not always of uniform, ‘Spun’ grey iron pipes were formed by spinning in a mould and produced a denser iron with pipes of more uniform wall thickness; they comprise a large proportion of the distribution mains in many countries. Three classes of such pipes were available in the UK: B, C and D for working pressures of 60, 90 and 120 m, respectively; classes B and C were more widespread. Carbon is present in the iron matrix substantially in lamellar or flaky form; therefore, the pipes are brittle and relatively weak in tension and liable to fracture. The manufacture of grey iron pipes has been discontinued in most countries, except for the production of non-pressure drainage pipes.
Lead joint (a) is accomplished by melting and pouring lead around the spigot in the bell end of the pipe. After the lead has cooled to the temperature of the pipe, the joint is caulked using pneumatic or hand tools until thoroughly compacted with the caulking material and made water tight.
Cement joint (b) is started at the bottom with the cement mixture, and the mixture then caulked. Pipe with cement joints must not be filled with water until after 12 h has elapsed.
Roll-on joint © requires a round rubber gasket that is slipped over the spigot before it is pushed in the bell. Braided jute is tamped behind the gasket, after which the remaining space is filled with a bituminous compound.
Push-on gasket joint (d) is made by seating a circular rubber gasket inside the contour of the socket bell. The slightly tapered pipe end permits the gasket to fit over the internal bead in the socket. A special lever action tool, manually operated, then allows the bell and spigot past the gasket, which is thereby compressed as it makes contact with the bottom of the socket.
Mechanical joint and pipe joint should be thoroughly cleaned to remove oil, grit, and excess coating and then painted with a soap solution. Cast iron gland is then slipped on the spigot end with the lip extension toward the socket (or bell) end. The rubber gasket, also painted with the soap solution, is placed on the spigot end but with its thick end toward the gland. The entire section of the pipe is pushed forward to seat the spigot into the bell; the cast iron gland is moved into position for bolting.
The Putney gas explosion was a real wake-up call, and accelerated the replacement of old gray ductile iron pipe fittings by polymers such as medium-density polyethylene (MDPE), high-density polyethylene (HDPE), and unplasticized polyvinylchloride (UPVC). HDPE has a tensile strength of ≈20–37 MN m?2 (which is more than adequate for typical internal pressures). Most importantly, though, it has a Young’s modulus which is ≈150–300 times less than cast iron. This means that HDPE pipes can deflect under misalignments of the kind experienced in the Putney explosion without reaching the fracture stress. Even better, over a long time the polymer also creeps, which further dissipates the stresses caused by misalignment. Polymers are also very resistant to corrosion, so should last indefinitely in the ground.
But how are lengths of polymer pipe joined together? The following clip shows how:
http://www.youtube.com/watch?v=83PTUoFBq...re=related
The steps in the process are shown in Figure 27.11. First, the ends of the pipe to be joined are machined flat and parallel using a double-sided rotating disk planer. Then the ends are heated with an electric hotplate. Finally, the hot faces are pushed together using a hydraulic ram. The softened thermoplastics fuse together, making a high-strength leak-proof joint. This is a quick, reproducible method, which requires little skill on the part of the operator—in marked contrast to the lead-filled spigot-and-socket joints of the old cast iron system. Figures 27.12 and 27.13 show an alternative joining method, where one end of the pipe has an enlarged bore into which the mating pipe can be inserted. This overlapping joint can then be fixed and sealed with polymer adhesive. It would be hard to envisage any replacement materials so well adapted to this challenging environment than thermoplastics.
The earliest oil pipelines in the United States, laid in the 1860s, were typically constructed of 2-in cast-iron pipe threaded and screwed together in short segments. Oil was propelled through the pipeline using steam-driven, single cylinder pumps, or by gravity feed. These early pipelines, seldom more than 15 mi in length, were prone to bursting, thread stripping at the pipe joints, and frequent pump breakdowns mainly due to the percussive strain on the lines caused by each stroke of the pump which “resembled the report of a rifled gun.” Development of the four-cylinder Worthington pump revolutionized the transportation of petroleum by pipeline with its constant flow and uniform pressure (The Engineering and Building Record, 1890; Scientific American, 1892; Herrick, 1949; Williamson and Daum, 1959).
By the 1870s, a 2000-mi network of small-diameter gathering lines connected the oil-producing areas with regional refineries and storage points on the railroads and rivers where the oil could be shipped to refineries via railcars or ships and barges. Typical crude oil trunk lines were constructed of 18-ft sections of lap-welded wrought steel pipe fittings 5 or 6 in in diameter joined with tapered, threaded joints manufactured specifically for pipeline service. The pipe was generally buried 2 or 3 ft below the ground surface. Worthington-type pumps were used as the motive power for the lines, and the pumps were powered by steam generated by coal-fired boilers. Pump stations were spaced as needed to maintain the flow of oil over the terrain crossed by the lines. At the pump stations, oil was withdrawn from the lines and passed through riveted steel receiving tanks some of which were 90 ft in diameter and 30 ft high holding about 35,000 barrels (The Engineering and Building Record, 1890; Scientific American, 1892; Herrick, 1949). Diesel-powered pumps began to replace steam power around 1913–1914 (Williamson et al., 1963).
It was not until May 1879 that the Tidewater Pipe Company, Ltd. began operation of the first long-distance crude oil pipeline covering the 100 mi between Coryville and Williamsport, Pennsylvania, to connect with the Reading Railroad. The line was constructed of 6-in wrought-iron pipe laid on the surface of the ground (except when crossing cultivated land) and relied on only two pumping stations, one at Coryville and the other near Coudersport. The expansion of the oil under the hot summer sun caused the line to shift as much as 15–20 ft from its intended position, knocking over telegraph poles and small trees, but no serious breaks occurred. In the spring of 1880, Tidewater buried the entire line (Williamson and Daum, 1959).
The success of the Tidewater pipeline set the pattern for the construction of other long-distance crude oil “trunk” lines which sprang up in the early 1880s connecting the oil regions of Pennsylvania with refining centers in Cleveland, Pittsburg, Buffalo, Philadelphia, Bayonne, and New York City (Williamson and Daum, 1959).
By 1905, the oil fields in the Oil Regions of Appalachia stretching from Wellsville, New York, through western Pennsylvania, West Virginia, eastern Ohio, Kentucky, and Tennessee were becoming depleted. The new oil fields discovered during the early 1900s in Ohio, Indiana, Illinois, southeastern Kansas, northeastern Oklahoma, and eastern Texas were quickly connected by trunk lines to the eastern refining centers as well as the new western refineries in Lima, Ohio; Whiting, Indiana; Sugar Creek, Missouri; and Neodesha, Kansas (Johnson, 1967).
The proximity of the prolific Spindle Top Field to the Gulf coast made the area around Houston, Port Arthur and Beaumont, Texas, and Baton Rouge, Louisiana into a petroleum refining center. Regional pipelines were built to carry crude oil the relatively short distances to the Gulf coast refineries (Johnson, 1967). The oil tanker ships operating from the Gulf coast ports competed for and obtained control of most of the long-distance oil transport to the refineries and markets along the eastern seaboard by the mid-1920s (Williamson et al., 1963; Johnson, 1967).
Until the 1930s, when large-diameter steel pipe was in widespread use, the carrying capacity of oil pipelines was increased by laying an additional line or lines alongside the original pipe within the same right-of-way. This practice was known as “looping.” The carrying capacity of 8-in lines was about 20,000 barrels per day, while 12-in lines handled 60,000 barrels per day. Since the largest refineries operating in that era were designed to handle crude at the rate of approximately 80,000–100,000 barrels per day, the carrying capacity of the pipelines built by a refiner were carefully gauged to support the refinery with little excess capacity to offer to others (Wolbert, 1979; Willson, 1925).
By 1941, just prior to the United States’ entry into World War II, there were about 127,000 mi of oil pipeline in the United States composed of about 63,000 mi of crude oil trunk lines, about 9000 mi of refined product lines, and about 55,000 mi of crude gathering lines (Frey and Ide, 1946). From February through May 1942, 50 oil tankers serving the Atlantic seaboard were sunk by German submarines. The continuing attrition of the tanker fleet by enemy action and the diversion of tankers to serve military operations abroad caused a tremendous increase in the use of pipelines to transport both crude oil and refined products to the east coast which consumed about 40% of the petroleum produced in the United States. In June 1941, before the Pearl Harbor attack, pipelines delivered about 2% of the petroleum needed by the east coast; by April 1945, pipelines carried 40% of this critical supply (Frey and Ide, 1946).
The wartime expansion of the pipeline network added more than 11,000 mi of trunk and gathering lines, repurposed over 3000 mi of existing pipelines in new locations and reversed the direction of flow of more than 3000 mi of other lines (Frey and Ide, 1946). One of the pipelines converted from products delivery and reversed in flow direction to convey crude oil to east coast refineries during the war was the Tuscarora pipeline. After the war, it was reconverted and its direction of flow was again reversed to convey gasoline from the coastal refineries to the interior (Johnson, 1967).
Noteworthy wartime pipelines owned by the federal government were the “Big Inch” crude oil line, the largest pipeline in the world at that time measuring 24 in in diameter for much of its 1254 mi length; and the “Little Big Inch,” the longest refined products pipeline in the world at 1475 mi of 20-in diameter pipeline (Frey and Ide, 1946). Only during World War II did the federal government finance oil pipeline construction (Johnson, 1967).
With the proven success of long, large-diameter crude and refined products pipelines during World War II, the rapid growth in demand for petroleum products in the post-World War II era prompted a great expansion in construction of large pipelines. The number of refined products pipelines increased about 78% from 9000 mi in 1944 to 16,000 mi in 1950. Crude oil trunk lines expanded from about 63,000 mi in 1941 to about 65,000 mi 1950. The postwar increase in the diameter of the crude oil trunk lines, and therefore their carrying capacity, far outweighed the relatively modest increase in mileage (Johnson, 1967) (Table 24.1).
|
|
|
Rethinking the bottle |
Posted by: I678L - 09-27-2021, 02:10 AM - Forum: Off Topic
- No Replies
|
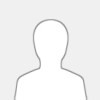 |
Rethinking the bottle
Rethinking the bottle
When I was younger, wine came in a glass bottle, and—outside of a few value-priced boxed options—that was that. But now, quality wine comes in all sorts of packaging: boxes, cans, pouches, even slim wine bottles that can fit through a mail slot. Of course, the bottle is still king—but even that classic container isn’t beyond innovation. The British company Frugalpac has just launched a standard-sized wine bottle made mostly out of recycled paper.
The Frugal Bottle is a 750 milliliter bottle “made from 94 percent recycled paperboard with a food-grade liner to hold the wine or spirit,” according to Frugalpac. Not only is it “comparable in cost to a labelled glass bottle,” but it can also “be refrigerated and keeps the liquid cooler for longer.”
Naturally, the company offers an environmental pitch, as well. “Our mission is to design, develop and supply sustainable packaging. The Frugal Bottle is up to five times lighter than a glass bottle, has a carbon footprint up to six times lower and is easy to recycle again,” explained Frugalpac chief executive Malcolm Waugh. “We’ve had fantastic feedback from people who’ve trialed the Frugal Bottle. As well as the superior environmental benefits, it looks and feels like no other bottle you have ever seen.”
Digging into the specifics, a Frugal Bottle weighs about 3 ounces, whereas burgundy bottles can weigh about a pound. Additionally, Frugalpac says that beyond offering a carbon footprint that is 84 percent lower than a glass bottle, it’s also “more than a third less than a bottle made from 100 paper recycled plastic,” with a “water footprint is also at least four times lower than glass.” And, yes, the paper bottle is easy to recycle—because the liner inside is removable: “Simply separate the plastic food-grade liner from the paper bottle and put them in your respective recycling bins.”
The new Frugal Bottle has debuted with Italy’s Cantina Goccia who is using it for their 2017 3Q wine—a Sangiovese retailing in the UK for about $16. On top of its other benefits, this first bottle shows off another intriguing trait: The artwork can easily cover the entire surface.
“When some of our top hotel customers saw samples of our paper wine bottle, there was no hesitation in their minds that this type of bottle would be well received in their dining rooms,” said Cantina Goccia owner Ceri Parke. “It’s much lighter than glass, easier to transport and friendlier to the planet."
As of right now, Frugal Bottle doesn’t appear slated to arrive in the United States in the near future, but that could easily change. Frugalpac is currently taking orders for the machines used to produce the bottles, with delivery planned for next year—and though right now interest is primarily in the U.K. and Europe, nothing seems to preclude American companies from getting on board.
“Frugalpac’s business model is to supply Frugal Bottle machines for wine producers or packaging companies to manufacture the bordeaux bottles on their site, cutting carbon emissions even further,” Waugh added. “Materials can be purchased locally through existing paperboard printers to give maximum freedom of design and the best commercial offering.”
Naturally, the company offers an environmental pitch, as well. “Our mission is to design, develop and supply sustainable packaging. The Frugal Bottle is up to five times lighter than a glass bottle, has a carbon footprint up to six times lower and is easy to recycle again,” explained Frugalpac chief executive Malcolm Waugh. “We’ve had fantastic feedback from people who’ve trialed the Frugal Bottle. As well as the superior environmental benefits, it looks and feels like no other bottle you have ever seen.”
Digging into the specifics, a Frugal Bottle weighs about 3 ounces, whereas ice wine bottles can weigh about a pound. Additionally, Frugalpac says that beyond offering a carbon footprint that is 84 percent lower than a glass bottle, it’s also “more than a third less than a bottle made from 100 paper recycled plastic,” with a “water footprint is also at least four times lower than glass.” And, yes, the paper bottle is easy to recycle—because the liner inside is removable: “Simply separate the plastic food-grade liner from the paper bottle and put them in your respective recycling bins.”
Shops in Scotland have become the first place in the UK to stock wine in paper bottles in a move which aims to reduce the carbon footprint associated with glass bottles.
Three Scottish off licences will sell the Italian wine in its new lightweight, recyclable container, which the manufacturers say has a carbon footprint up to six times (84 per cent) lower than a glass bottle and more than a third less than a bottle made from 100 per cent recycled plastic.
The 75cl bottle, manufactured by Ipswitch-based company Frugalpac is made from 94 per cent recycled paperboard and has gone on sale for the first time at Woodwinters Wine and Whiskies stores.
The wine is from Italian vineyard Cantina Goccia and is a blend of Sangiovese, Merlot and Cabernet Sauvignon grapes.
But the manufacturers said the bottle can also be used for spirits such as whisky, gin, vodka and rum, and has already sparked a interest in a drinks industry keen to cut their emissions and appeal to a new audience of consumers interested in sustainability.
Please use the sharing tools found via the share button at the top or side of articles. Copying articles to share with others is a breach of FT.com T&Cs and Copyright Policy. Email licensing@ft.com to buy additional rights. Subscribers may share up to 10 or 20 articles per month using the gift article service. More information can be found at https://www.ft.com/tour.
https://www.ft.com/content/a5cf1075-5bc1...06214111f4
For many of us wine drinkers, our first conscious act towards saving the planet was to separate champagne bottles from the rest of our rubbish. It made us feel pretty good, even though most of us were — and continue to be — shockingly ignorant about what then happens to them.
Today, few really understand the relative merits of different forms of packaging for wine in terms of sustainability. And this is hardly surprising, since even those whose job it is to study such things admit that the whole subject is hugely complex and definitive statistics are extremely difficult to come by.
To the average consumer, a glass bottle may seem virtuous because they generally assume that it’s both recycled and recyclable. Hence when the European glass manufacturers association, FEVE, commissioned a consumer research project last year involving 10,000 15-minute interviews in 13 European countries, it was able to boast that 91 per cent of interviewees agreed glass is the best packaging material for wine. (Brits are the most sceptical about glass, apparently — only 82 per cent of us agreed.)
On the strength of this research, Europe’s glass manufacturers have come up with a new hallmark on bottles that, as far as I can make out, merely confirms that the bottle you have in your hand is indeed made of glass, even if the design of the logo vaguely suggests recyclability.
The official online presentation of this innovation last November skipped lightly over the massive carbon footprint of producing and transporting glass bottles, the biggest factors in any winemaker’s carbon audit. A greener sort of furnace, which relies more on electric power than fossil fuels, is being piloted in Germany over the next few years, yet it will require considerable effort and investment for bottle manufacturers to reach FEVE’s ambition of carbon neutrality by 2050.
Please use the sharing tools found via the share button at the top or side of articles. Copying articles to share with others is a breach of FT.com T&Cs and Copyright Policy. Email licensing@ft.com to buy additional rights. Subscribers may share up to 10 or 20 articles per month using the gift article service. More information can be found at https://www.ft.com/tour.
https://www.ft.com/content/a5cf1075-5bc1...06214111f4
One of the keys to this is, of course, recycling rates. The figure FEVE likes to quote is that Europe’s “average glass collection for recycling rate” is 76 per cent (which it would like to see reach 90 per cent by 2030), though it acknowledges that not all of this will ultimately be recycled.
In the UK, each local authority is in charge of contracting waste management, which means that standards and practices can vary enormously from place to place. Overall, only 68 per cent of all glass containers in the UK are recycled, compared with well over 90 per cent in Switzerland and Scandinavia. (Swiss citizens are incentivised by a combination of free glass collection points and a tax on bags for general rubbish.) The British Standards Institution, which sets national standards for everything from financial services to medical devices, would like to see recycling protocols harmonised.
Recycling bottles is complicated. They come in all sorts of colours which have to be separated from each other, while labels and foils have to be removed. The farsighted Torres winemaking family in Catalonia is pressing for a standard wine bottle that could be recycled and reused anywhere in the world — or at least anywhere in Europe to begin with.
Yet this would require EU legislation, admits Miguel Torres, which seems a very distant possibility to me, when so many wine producers choose to use bottle design and weight — especially weight — to try to carve out a distinctive identity for their wines. (It was notable in a recent online forum on the future of wine that the greatest opprobrium was directed towards those who use heavy bottles unnecessarily.)
Increased awareness of sustainability issues has also resulted in a flurry of new designs for wine packaging. These include a replica of a standard bottle from Frugalpac, which is made from 94 per cent recycled paperboard (and “a food-grade liner”) that can in turn be recycled.
Please use the sharing tools found via the share button at the top or side of articles. Copying articles to share with others is a breach of FT.com T&Cs and Copyright Policy. Email licensing@ft.com to buy additional rights. Subscribers may share up to 10 or 20 articles per month using the gift article service. More information can be found at https://www.ft.com/tour.
https://www.ft.com/content/a5cf1075-5bc1...06214111f4
One of the most energetic and thoughtful innovators on this side of the Atlantic has been Santiago Navarro, chief executive of Gar?on Wines. He has designed an almost flat wine bottle that can fit through a letter box and is much lighter, considerably more space-saving and less fragile than the traditional glass bottle. If the option of an active oxygen scavenger is applied, the wine will stay fresh for more than 12 months before opening, he claims.
A keen diver, he is well aware of the problems of plastic waste, as highlighted so vividly by David Attenborough in his Blue Planet series. Even though the food-friendly PET plastic from which Navarro’s smooth, olive-green bottle is moulded has already been used once — and in general plastic has a much lower carbon footprint than single-use glass — some consumers are convinced that all plastic is evil.
In fact, there are many different forms of plastic, of which PET is arguably the most sustainable, and Navarro treasures the letter he received from Sir David congratulating him on his novel design.
The problem with plastic is not so much the material itself but how to manage it after use. According to the British Plastics Federation, about 50 per cent of all plastic in the UK is recycled. Yet unlike glass, which can be recycled many times, plastic can be recycled effectively much less often because it degrades — though work is ongoing to improve this.
Please use the sharing tools found via the share button at the top or side of articles. Copying articles to share with others is a breach of FT.com T&Cs and Copyright Policy. Email licensing@ft.com to buy additional rights. Subscribers may share up to 10 or 20 articles per month using the gift article service. More information can be found at https://www.ft.com/tour.
https://www.ft.com/content/a5cf1075-5bc1...06214111f4
Wine in cans is becoming popular in the US, where a high proportion of all drinks is sold in cans already. They tend to be much smaller than a regular bottle and, let’s face it, there are some pretty huge disadvantages to the 75cl bottle. It’s way too much for one person, often too much for two at a single sitting, and the unit price is far higher than a can’s, which some younger potential wine drinkers in particular find off-putting. Cans are convenient: they can easily be popped into a picnic bag or even, should we return to office life, a briefcase.
Made from steel or aluminium, they can also be recycled almost infinitely. Still, like glass, the manufacturing process is heavy on energy and resources.
Glass, so usefully inert, will surely remain the material of choice for fine wine that deserves long ageing, but for the sake of the planet we do need to look more favourably on the alternatives for that which is drunk within days or weeks of purchase — which constitutes by far the majority of all wine sold.
Borough Wines in London deserves mention for its work founding Sustainable Wine Solutions, which offers a bottle return scheme, a refillable box (a “zero-waste alternative to bag-in-box”) and what it claims are “the UK’s only 100 per cent reusable kegs”. The latter are a fine solution for restaurants and bars — should they ever be in business again.
This article has been amended since publication to make clear that latest government figures show 68 per cent of glass in the UK is recycled, not 50 per cent as originally stated
Tasting notes on Purple Pages of JancisRobinson.com
Follow Jancis on Twitter @JancisRobinson
Follow @FTMag on Twitter to find out about our latest stories first. Listen to our podcast, Culture Call, where FT editors and special guests discuss life and art in the time of coronavirus. Subscribe on Apple, Spotify, or wherever you listen.
|
|
|
What are the advantages of time recording machine in an office ? |
Posted by: I678L - 09-27-2021, 02:07 AM - Forum: Off Topic
- No Replies
|
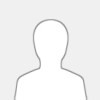 |
What are the advantages of time recording machine in an office ?
What are the advantages of time recording machine in an office ?
Showing up for work punctually, at an official time, became expected behavior toward the end of the 19th century, as more and more people worked for others rather than for themselves. Not just the work force's punctuality was at issue. Cost accounting and analysis--recording and scrutinizing expenses for labor, materials and overhead--were getting more attention than ever before. Time was money.
In the 1890s, timekeepers-- clerks who kept track of employees' hours in handwritten logs --found that machines were beginning to replace them, especially in workplaces with large numbers of employees. Thanks to the influence of the advocates of scientific management, nearly every industrial workplace had a time clock, after about 1910. So did many offices. By the early twentieth century the International Time Recording Company supplied an entire line of timekeeping devices, including master clocks, several types of time clocks, and time stamps. Founded in 1900, the firm continuously expanded its product line, underwent several reorganizations and name changes, and emerged in 1924 as the International Business Machine Corporation, familiar today as IBM.One of the firm's most popular products was the card punch time recorder, a clock that could furnish a daily or weekly record of up to 150 employees. Based on the 1888 patent of physician Alexander Dey, the dial time recorder was essentially a spring-driven clock with a cast-iron wheel affixed to its dial side. The rim of the wheel was perforated with numbered holes. As employees pressed a rotating pointer into the hole at their assigned number, the machine recorded the time on a preprinted sheet and rang a bell with each punch. A two-color ribbon printed all regular time in green and all tardiness, early departures, and overtime in red.This International digital card punch time recorder hung in a factory in the garment district of New York City.
Time recording clock is a time recording machine used to record the lime of arrival and departure of an employee. The time is recorded on the card allotted to each employee of the organisation. The card is punched in this machine, which records the time of arrival and departure automatically. These machines are fitted with a clock to show the time. The advantages of the use of time recording machines are:
(a) It records the actual time of arrival and departure.
(b) It is not possible to manipulate the time in case of late arrival or early departure.
It is necessary to keep proper record of time for each worker as it ensures discipline, increases morale and makes him punctual.
This function of keeping proper record of time is looked after by the time-keeping department. In a small organisation, such a department may not exist at all since the time of coming and going can be easily regulated by the person in changes of operations in the factory or the office.
Time keeping is a system of recording the time of arrival and departure of workers; it provides a record of total time spent by each worker engaged in the factory. On the basis of this record, wages are paid to the workers under time rate system.
The regal contains the columns like name and identity no. of the worker, the department in which he is working, arrival and departure time. As soon as a worker enters into the preprint of the factory, the necessary entries in the attendance register are completed. If workers are literate; they are required to sign the attendance register.
After the reports time workers are marked late or absent as the case may be. Similar entries are made the time of departure.
This method is very simple and inexpensive. But in a large factory this meth may become inconvenient. Moreover, this method is liable for many undesirable’ practices on the part of the persons who record the attendance in collusion with sour workers. This method is suitable for small factories and out-doors workers.
Under this method, each worker is allotted a metal disc or token bearing his identification. On each disc or token the name and number of the worker is engraved or painted. All the tokens 01; discs are hung on a board at the gate or at the entrance of the department.
As soon as a worker reports for duty, he removes his disc and puts it in a box provided nearby. Immediately after the scheduled time of entry, the board is removed and a list is prepared for all such discs or tokens not collected and dropped into the box by the workers.
The late-comers collect their discs and hand over the same personally to the time keeper. The list of late-comers is prepared separately. The discs not removed from the boards represent the absentee workers.
This method is simple and economical. But it is not free from abuses. A worker may remove the disc of his fellow-worker to ensure his presence who is either late or absent.
There is no certainty that the exact arrival time of the workers has been recorded. The time keeper marking the attendance may commit errors deliberately or through carelessness and this may create disputes. Time keeper may include the dummy or ghost workers in the muster roll that cannot be easily detected except by close supervision.
2. Mechanical Methods
Different mechanical devices have been designed for recording the exact time of the workers. These include:
(a) Time Recording Clocks
(b) analogue card punch time recorder
(a) Time Recording Clocks
This method has been developed to remove some of the difficulties faced in case of manual methods. Under this method, the attendance is marked by a time recording clock on a card. Every worker is allotted a time card usually for one week duration.
These time cards are serially arranged in a tray at the gate of the factory. On arrival the worker picks up his card from the tray and inserts the same into the time recording clock which prints the exact arrival time at the space provided on the card against the particular day.
This process is repeated when the worker leaves the factory after day’s work. Other particulars of time in respect of late arrival, lunch, and overtime are printed is red colour so as to distinguish these from normal period spent in the factory.
This method is useful when the number of workers is fairly large. There are also no chances of disputes arising due to recording of time of workers as it is recorded by the clock and not by the time keeper.
But there are chances that a worker may get his friend’s card from the tray and mark him present in time when he is actually late or absent. Any mechanical defect may adversely affect the working of time recording system.
The dial time recorder is a machine which records the correct attendance time of the worker automatically. It has a dial around the clock with a number of hold (usually about 150), each of which bears a number corresponding to the identification number of the worker concerned.
There is a radial arm at the centre of the dial. While a worker enters into the factory; he is required to press the radial arm after placing ill at the appropriate hole. The time recorder then automatically records the time on a roll of paper within the machine against the number of the worker.
This machine can also! calculate the wages of the workers with greater accuracy and avoids much loss of time, I But a heavy capital investment is needed and hence only large organisations can use It is also necessary to have a close supervision on every worker to prevent fraud and I irregularities.
Make employee scheduling and pay calculation easier with this fingerprint time attendance. A perfect choice for tracking hours in busy workplaces, this time stamp keeps accurate time within fractions of a second by automatically syncing with codes from the National Institute of Standards and Technology. This device automatically adjusts for Daylight Saving Time and ensures consistent accuracy during power failures using an internal battery backup. Featuring over 150 print configurations and 13 messages in four languages, this device makes it easy to print custom messages in two hour formats and a variety of font sizes. Compatible with a variety of forms and time cards, this flexible machine aligns any document perfectly with an internal LED and a window over the print area. This Acroprint time recorder informs users of the time and date with a large, bold display.
Black/gray punch card time clock system for unlimited number of employees
LCD display helps you keep track of time by showing the time and date in 24- or 12-hour format
Durable construction and key lock help protect clock and settings from damage or tampering
Employees use printable time cards
Dimensions: 5.63"H x 6.45"W x 6.77"D
Desk- or wall-mountable for flexible and convenient placement
Battery backup protects data and settings during power outages
Selectable language format: English, French, Portuguese, and Spanish
2-year manufacturer limited warranty
No resetting needed.The LCD backlight digital time punching machine synchronizes automatically with time codes transmitted by the National Institute of Standards and Technology, keeping it incredibly accurate. The internal battery backup keeps the clock on time, even during power outages.Flexible options.With over 150 possible print configurations and 13 preset messages in your choice of four languages, the ES700 easily supports a wide variety of time & attendance and document control applications. This time stamp accomodates virtually any time card, document or form, offering adjustable print font size, your choice of automatic, semi-automatic or manual print operation, and left or right hand print. The power supply is switchable from 120V to 240V.Easy to use.Cards and documents are a snap to align correctly, thanks to a handy window in the cover and a bright internal LED illuminating the document print area.
|
|
|
All About Knitted Hats |
Posted by: I678L - 09-27-2021, 02:02 AM - Forum: Off Topic
- No Replies
|
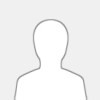 |
All About Knitted Hats
All About Knitted Hats
Quarantine has sparked plenty of new at-home hobbies. Maybe you picked up a paintbrush and tapped into your inner artist. Or, you might have transformed your kitchen into a bakery. For some, perfecting their knitting and crocheting skills even led to a business — which is why you're likely seeing the knit hat trend unexpectedly taking off on Instagram.
For Delsy Gouw, founder of Brooklyn-based label Its Memorial day, crocheting started out as a fun activity. "[It] originally started as an online Depop vintage shop [in 2019] but when Covid hit, I wasn’t able to source any goods," she tells TZR. "I also lost my job and found myself with a lot of time on my hands." Gouw picked up the old hobby of hers and began making items for friends, and then her friends' friends were requesting pieces, too. She then began crafting knit hats because she believed the demand was there. "I started with bags but when I posted them so many of my friends and followers asked when or if I’d be open to making hats and taking customs for hats," Gouw tells TZR. While trends typically fade away and come back later on, Gouw hopes this style will stay long-term. "[I] can’t speak for knitting, but the way crochet is done is truly so intricate, unique, and is made to last," she explains. "Crochet can only be done by hand so I think there is something special about having an accessory that is unique and handmade." Fans of Gouw's emerging brand include influencers like Reese Blutstein, Jo Rosenthal, and Ella Emhoff.
Who knows when the first person decided to put something over their head to keep it warm, but knitters know that knitted hats for women are some of the most fun and easy things to knit.
When they’re worked in the round there is little in the way of shaping, except when you get to the crown.
Most hats are worked from the bottom up, with stitches cast-on and worked in a snug stitch pattern such as ribbing, or in stockinette for a rolled bring hat, using a smaller size needle than is used for the head portion of the hat.
In many hat patterns, the hat is worked straight for the desired length of the crown, then nearly all of the stitches are evenly decreased over the course of just a few rounds.
The yarn is cut, the tail threaded through the remaining stitches, pulled tight, and fastened off to the inside of the hat.
The hat can be topped with a pom pom, i-cord, tassel, or whatever embellishment strikes your fancy.
A great book for learning to make hats is Ann Budd’s Handy Book of Patterns, from which some of the material on this page is excerpted. There are chapters on basic hats as well as the type of hats called “tams.”
There are several types of hats, but the most popular knitted hats for men are beanie-type caps, tams (sometimes called “berets”), slouch hats, earflap hats, and tuques.
Beanies: These hats can be super simple or dressed up with a lace or cable patterns. In cooler climates, they’re wonderful gifts for knitters to make.
Tams/Berets: There are so many different stitch patterns to use in this style. Tams and berets can be plain stockinette or intricate Fair Isle. This style of hat is really flattering on just about every face shape, too.
Earflap Hats: These hats are popular in cold climates. They’re great for keeping ears warm and they’re fun to knit. The knitters of Peru specialize in these hats, as shown in the photo at right.
Often a knitted hats for children will have a finished size that is smaller than the average adult head. That’s because hats meant to fit closely at the brim need a bit of negative ease to help them fit snugly and keep them on the head.
The amount of negative ease refers to the difference between the finished size of the object and the size of body part on which it will be worn. A hat that measures 19″ (48.5 cm) around and is worn on a 22″ (56 cm) head has 3″ (7.5 cm) of negative ease.
A beret-type hat might have negative ease at the brim, but a few inches of positive ease in the body of the hat. The extra fabric is what creates its loose, flowing shape, while the tighter brim keeps it fitted to the head.
Hats are a natural for circular knitting (or knitting in the round). This project for circular-knit adult hats offers three brim styles: hemmed, ribbed, and rolled stockinette. Whichever brim you choose, the directions call for shaping the top. Work this hat in plain stockinette stitch in a colorful or fashion yarn, or customize it by working the colorwork pattern included here. But don’t feel tied to those two options — use this hat as a canvas to express yourself.
If you knit the hat on one 16-inch circular needle, you’ll need to switch to double-pointed needles (or one of the other methods) at some point during the crown decreases because the stitches will no longer reach comfortably around the needle. It is easiest to knit hats using the magic-loop method with one long circular needle.
Choose a size
Determine the circumference you want for the hat. Most hats should be knit with negative ease (. Measure around the widest part of the intended wearer’s head and subtract 1?2 to 1-1?2 inches from that measurement to calculate the hat circumference.
A hemmed brim is not as stretchy as a rolled or ribbed brim, so it’s best not to include too much negative ease when using this hem.
Choose yarn and determine the gauge
Yarn for adult hats can run the gamut from practical to frivolous and fun. If you want a warm winter hat, for example, choose a yarn that is warm and durable, and knit it at a tighter gauge than recommended on the ball band. This results in a denser fabric that better retains heat. If, on the other hand, you are creating a fun accessory, you might choose a fashion yarn that adds a little flair. Because this hat is such a simple shape, it’s a great way to show off variegated or self-striping yarns.
To keep cool but stay warm during winter, you can’t skimp on great outerwear or outfit-making boots. The same goes for cold-weather accessories too: Because for the majority of the season, coats, boots, and, in this case, winter hats do most of the talking when it comes to bundling up while keeping things stylish. In order to break free from your standard winter-outfit formulas—and to keep your looks from looking like, well, everybody else—consider accessorizing functionally and fashionably this season. Here, find four headwear trends not to be missed, and shop 24 of the best winter hats, inspired by the most stylish women on the streets, from New York to Paris.
Buckets and Beyond
After runway debuts at Fendi and Loewe, the winter-ready hand knitted hat took over the streets last February—and this season the ’90s trend has continued to gain momentum. From shaggy faux furs to fuzzy angoras, from shearling to sherpa styles, the winter bucket hat is one of the cutest and coziest accessories of the season.
The ribbed-knit beanie has earned its place as a winter style staple for everyone from downtown urbanites to alpine skiers. New Yorkers might prefer sleek styles in a neutral color palette like black and speckled gray. Meanwhile, a pop of color would bring the perfect amount of joyous street-style-inspired Scandi chic to any drab winter look. And for those who wish to channel a bit of après-ski flair in their daily commute, look no further than one with a floppy, fluffy pom-pom.
The trapper hat is no longer just for the rugged outdoorsman or Elmer Fudd. Not convinced? The trapper has been deemed stylish enough for even the Parisians—in fact a black faux-fur version was spotted on the streets topping off a geometric-print coat, leather pants, and blue ankle booties for the ultimate in warmth and style. Et voilà! Not to mention everyone from classic winter-weather brands to It labels are backing the trapper trend—Heurueh, Kule, and R13 to name just a few. You heard it here first: The trapper is the ultimate winter hat for women this season.
On the tiny Peruvian island of Taquile, a man's worth isn't measured in his ability to hunt or fish, but in his ability to knit.
Alejandro Flores Huatta was born on the 1,300-person island, which is located on the Peruvian side of Lake Titicaca, a three-hour boat ride from the nearest city of Puno. The 67-year-old learned how to knit the iconic chullo (a tall, floppy Andean hat) as a child, with his older brother and grandfather teaching him by using the thorns of a cactus as knitting needles.
"Most of the people learn by looking, watching. Because I don't have a father, my older brother [and grandfather] taught me to knit. So by watching, I learned little by little," he said, speaking through a Quechua translator.
Taquile is famous for its textiles and clothing, and while women weave and tend to the sheep that provide the wool, men are the ones who exclusively produce the island's knitting cap for baby. The chullos are seen as culturally significant, playing a key role in the island's social structure and allowing men to show their creativity while also displaying their marital status, dreams and aspirations – some men even use it to show their mood. It's a tradition that islanders are working hard to preserve.
Residents were relatively cut off from the mainland until the 1950s, and the island's isolation has helped to keep its heritage and way of life intact. Locals abide by the Inca code of "Ama sua, ama llulla, ama qhilla", (Quechua for, "Do not steal, do not lie, do not be lazy" . Taquileans are farmers traditionally; the six island communities take turns to rotate crops of potato, corn, beans and barley in terraces on the mountainsides. They raise sheep, guinea pigs, chickens and pigs on the land and fish in the lake. Tourism kicked off in the 1970s, giving locals a source of income with tens of thousands of visitors drawn to the island annually to tour the villages and surrounding lake. Visitors typically stay with locals in humble, family-run accommodations; lend a hand-harvesting crops; try local specialties like fried trout and potatoes with rice, beans and mint tea; and purchase the island's famous handmade textiles.
Hats reveal men's marital status, dreams and aspirations
In 2005, Taquile's textile art was deemed so valuable that Unesco deemed it an Intangible Cultural Heritage of Humanity. Alejandro is one of the seven men on the island recognised as a Master of Textiles, along with the island's president, Juan Quispe Huatta.
The tradition has been around for the better part of 500 years, with roots in the ancient civilisations of the Inca, Pukara and Colla peoples. The Inca in particular, used their headdresses in a similar way to the Taquilean chullo, to display the specific insignia of their particular province – but that’s where the similarities end. The Taquilean chullo and the Inca headdresses look vastly different. The elders of the island tell of the chullo design arriving with the Spanish conquest in 1535, and Alejandro's grandfather passed on stories of the early conquerors wearing similar hats that were white with ear covers, "but not the same patterns or symbols," Alejandro said.
|
|
|
Effective cleaning of rust stained marble |
Posted by: I678L - 09-27-2021, 01:58 AM - Forum: Off Topic
- No Replies
|
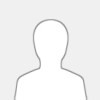 |
Effective cleaning of rust stained marble
Effective cleaning of rust stained marble
Calcareous materials, like marble used in
connection with cultural heritage objects such as statues and pedestals, or as wall facings on buildings, often show a
brownish staining owing to contact with iron metal or iron-containing minerals in the stone. The discolouration alters the
appearance of the stone, which is undesirable from an aesthetic point of view. Despite rust staining being a conspicuous
phenomenon and numerous works that have dealt with the problem of removing rust stains, a simple and non-toxic method has so
far been missing. This paper describes a highly efficient method for cleaning rust stains from marble by introducing the
chelating amino acid cysteine in a Laponite poultice in combination with the strong reducing agent sodium dithionite.
Results
Cleaning experiments were performed on artificially discoloured samples of various types of Carrara Bianco marble and on
naturally rust stained marble. To begin with, solutions of cysteine in combination with sodium dithionite and ammonium
carbonate were tested by immersion of samples into the different solutions. Secondly, solutions of cysteine and sodium
dithionite with and without buffering were used in a poultice consisting of Laponite? RD, Arbocel? BC1000 and CMC. The
poultice was applied on three different marble types: Carrara Fabricotti, Carrara Vagli and Carrara La Piana. Thirdly, the
optimized method was tested on original rust stained material of luxury marble, which has been used as wall facing, and finally in situ in Copenhagen on a larger
area of The Marble Church showing rust stains due to pyrite oxidation. The cleaning results were evaluated by visual
observations, cross sections, and etching of the surface by testing on high gloss marble.
Conclusion
Cleaning of iron-discoloured marble surfaces has been investigated and a new method for removal of rust stained marble
has been developed. A solution of 0.1 M cysteine and 0.1 M sodium dithionite in a poultice consisting of Laponite?
RD/Arbocel? BC1000/CMC = 10:10:1 has shown to be a fast, simple, cheap, and non-toxic, do-it-yourself method.
Since ancient times, white marble has been used as a popular material for sculptural artefacts such as statues, busts,
and friezes as well as an architectural building material with numerous applications from flooring, wall facings, and
pedestals, to columns and fountains. Although marble is a relatively stable material, the desired white surface is
unfortunately prone to tarnishing when used in outdoor environments [1]. One of the major sources of tarnishing is iron. In
addition to the oxidation of internal iron compounds present in stone like pyrite (FeS2) and siderite (FeCO3) [1, 2], contact
with iron-rich ground water when Full
Body Marble is used in, for example, garden fountains, results in severe and unsightly discolouration [3]. Another cause
is the proximity to iron metal, which is oxidized by air in the presence of rain. The solubilized ions are then transported
by rain onto the marble surface, resulting in rust formation [4].
The detailed mechanism for rust formation is highly complex; depending on the pH value, different species, all
characterized by a brownish colour, are formed. The atmospheric corrosion of iron, regardless of the pH value of the reaction
may, however, be summarized by the overall stoichiometric reaction (1) where the product FeOOH represents the generic formula
for rust [5].
The general name rust consists of a variety of iron(III) oxyhydroxides or hydrated oxides of high stability and low
solubility. The actual species formed depend as mentioned on the pH value and the presence of different anions [6–8]. The
thermodynamic parameters and solubility products have been estimated for many of the rust species, such as ferrihydrite and
α-, β- and γ-FeOOH (goethite, akaganeite and lepidocrocite). These investigations have shown that goethite defines a
thermodynamic minimum of the rust system [7, 9] and the solubility product of goethite (Ksp = 10?41) is the lowest among the
different rust species [7]. This means, from a thermodynamic point of view, that rust can be examined as goethite, and thus
the cleaning of rust can be considered as removal of goethite.
Rust discolouration of marble is characterized by areas or stains having an orange to brownish colour, which alters the
appearance of the stone. From an aesthetic point of view, the discolouration is undesirable and stone conservators and
conservation scientists have therefore worked for several decades with various cleaning methods in attempts to remove rust
stains from marble and calcareous stone materials [3, 10–12].
Due to the nature of the discoloration and the possibility of damaging the stone, the stain can only be removed by
chemical cleaning. The current method for rust cleaning involves application of different ligands and reducing agents mixed
in a poultice and placed onto the stone surface. One of the ligands most widely used is the citrate ion [10, 11, 13], though
salts of other carboxylic acids, such as oxalic and tartaric acid, have also been used [10]. Other methods involve the use of
fluoride [10] or EDTA [12]. A relatively new method is the use of the hexadentate ligand tpen, which, in contrast to EDTA,
has a high affinity towards iron and a low affinity towards calcium [3]. This ligand has shown excellent results when tested
on a discoloured marble fountain, however this method is rather expensive. The ligands are used either alone or in
combination with reducing agents like thiosulfate, dithionite or polythiophene [3, 10]. Thioglycolic acid and ammonium
thioglycolate have been applied in several conservation treatments of calcareous stone [12]. Thioglycolate is presumably the
most efficient ligand for cleaning rust stained marble [12, 13]. However, thioglycolic acid is a toxic chemical, and is thus
difficult to acquire for private stone conservators without access to a laboratory. In addition to this, a slightly violet
colour may appear on the marble when cleaning with thioglycolic acid, which demands a second cleaning [12].
In this study, we have aimed to investigate and develop a new method for rust cleaning of simm marble. The focus has been on the use of
cheap and commercially available chemicals. Another target was reduction of Fe(III) to Fe(II) while cleaning. Efficient
removal of a slightly soluble material requires a ligand having an overall stability constant comparable to the reciprocal
value of the solubility product in order to achieve a favourable equilibrium constant. Based on the solubility product of
goethite, efficient removal of rust in Fe(III) stage requires a ligand having a stability constant approaching 1041, whereas
removal of Fe(OH)2 only requires a stability constant of 1014. Additionally, the ligand should possess low affinity towards
Ca(II) to prevent dissolution of calcite.
Introducing new chemistry for rust cleaning
In the search for an efficient method for rust cleaning, the focus has been both on a ligand showing strong complex
formation with iron and weak binding to the major constituent ions in marble i.e. Ca(II) and Mg(II), as well as on the
identification of a fast reducing agent able to reduce Fe(III) to Fe(II). Among the reducing chemicals, sodium dithionite
(SD), Na2S2O4, has been successfully used in combination with different ligands as a dissolving agent for goethite in soil
analyses [14, 15] and for removal of rust from paper [16]. Furthermore, the use of dithionite in conservation science in
general is well described [17].
The standard reduction potential, e°, of dithionite in the basic solution given in Eq. (2) has been determined to ?1.12
V (vs. NHE) [15, 17] and is thereby one of the strongest reducing agents among the simple, cheap, commercial reagents. The
reducing power decreases with lower pH values and using pKa2 = 7 for hydrogen sulphite the potential can be calculated to e°
′ = ?0.29 V at pH = 7.
In aqueous solution dithionite partly dissociates, forming the highly reactive monomeric sulphur dioxide radical anion
with the dissociation equilibrium constant K = 10?9 [18].
Even though the amount of the radical anion is relatively small and can be estimated to 10?5 M in a 0.1 M dithionite
solution, the anion has shown to be the dominant reducing species in the reduction and dissolution of iron oxides [14, 15].
From biochemical experiments, the standard reduction potential of the radical anion has been determined to ?1.39 V (vs. NHE)
in basic solution [18, 19], giving a calculated value e°′ = ?0.56 V at pH = 7 in accordance with experimentally determined
values [18].
The reduction potential for reduction and dissolution of synthetic goethite has been calculated to e°′ = ?0.14 V (vs.
NHE) at pH = 7 [20]. Using this value and either dithionite or the sulfur dioxide radical anion in the reduction and
dissolution of goethite to Fe(II), the reactions can be written as in Eqs. (5), (6) with the electrochemical potentials of E
°′ = +0.15 V or E°′ = +0.42 V.
Both reactions are spontaneous processes with relatively large equilibrium constants, which can be calculated to K = 105
or K = 107, respectively. From a thermodynamic point of view, dissolution of rust could be achieved by SD solutions only.
However, the presence of a ligand for removal of the Fe(II) ions is preferable in order to avoid re-precipitation caused by
oxidation from oxygen.
In search of a ligand useful for rust removal, a sulphide-containing species similar to thioglycolate were examined. The
amino acid cysteine (cys), commonly found in natural proteins as the L-isomer, is commercially available and affordable.
Cysteine forms complexes with Fe(III) and Fe(II) with high stability constants and only very weak complexes with Ca(II) and
Mg(II) [21]. At the same time cysteine reacts as a reducing agent in the iron(III)-cysteine complexes with formation of
colourless Fe(II)-cysteine complexes [22]. The intense violet colour known for Fe(III) complexes with ligands containing
thiol groups like cys and thioglycolate [12, 22] may therefore be avoided. In addition to this, cys is also able to perform
reductive dissolution of iron(III) oxyhydroxides, thereby independently having a solubilizing effect of rust [23].
Table 1 shows the stability constants of the marble constituents Ca(II), Mg(II), Fe(II) and Fe(III), with the commonly used ligands for rust cleaning
i.e. citrate [24], oxalate [24], tartrate [24], edta [25], tpen [26, 27] and thioglycolate [24, 28], together with cys [21,
28]. The solubility products of CaCO3 [29], MgCO3 [29], Fe(OH)2 [29], and FeOOH [7] are also given. As seen from the
constants, only edta shows affinity towards Mg(II) and Ca(II) in an order resulting in serious dissolution of MgCO3 and
CaCO3, whereas the remaining ligands display relatively weak binding constants, causing little dissolution of marble itself.
The stability constants of cys are similar to the values of thioglycolate, and cys possess very high affinity towards iron
(III), which is even higher than for edta. Towards iron(II) the overall stability constant is of an order of magnitude close
to the value for tpen, thus making cys an ideal candidate for cleaning of rust stained marble.
Reduction of Fe(III) to Fe(II) by cys is accomplished by oxidation to cystine, which is insoluble in water, causing
unwanted precipitation. However, the presence of SD together with cys prevents precipitation of cystine due to the ability of
dithionite to re-reduce cystine formed. The reduction potential of cys is estimated to approximately e′ = ?0.25 V at pH = 7
[22] which is higher than the potential of dithionite. In Fig. 1, the reduction reaction from cystine to cys (zwitterion
form) is shown together with the acid dissociation of the thiol group, forming a cysteinate species. This anion may react as
a bidentate ligand towards metal ions via the sulphur and oxygen donor atoms [22], but other coordination involving O, N and
O, N, S donor atoms are also possible. The iron-cysteinate complexes are complicated and not straightforward due to redox
reactions similar to those observed for the iron-thioglycolate system [22, 28, 30–32].
The pKa values of three functional groups i.e. carboxylic, thiol and protonated amino group are 1.88, 8.15 and 10.29,
respectively [23]. Using the values of the first two pKa constants, pH in solution of the cys zwitterion can be estimated to
pH 5. In general this pH value is too low for cleaning marble, due to acid dissolution of CaCO3 [12, 13]. The pH value can be
adjusted by the addition of a base such as ammonia (NH3) or ammonia carbonate ((NH4)2CO3), and in some cases when the
cleaning mixture is used in a poultice, the poultice itself can act as a buffering agent. Laponite, for example, releases OH?
below its point of zero charge, which is obtained around pH = 11 and an aqueous suspension of Laponite is alkaline [33]
(measurement shows pH = 9.3). Since the dissolution of goethite consumes H+ (Eqs. 5 and 6), the pH is also raised during the
reaction. Considering that the oxidation of iron(II) and cys is eased with increasing pH favouring precipitation of both
iron(III) oxyhydroxides and cystine, a reaction value around pH = 7 may be preferred, although pH = 9?10 is desired with
respect to the solubility of calcite [3, 12].
Introducing a new poultice for rust cleaning
The chemicals used for cleaning of stained marble are commonly applied in a poultice and a wide range of poultice
material has been tested and applied in stone conservation. Clay materials, such as bentonite, attapulgite and sepiolite, are
widely used either alone or in combination with cellulose fibres [4, 10, 34]. Other methods use cellulose fibres alone [35,
36], MC (methyl cellulose) [37], CMC (carboxymethyl cellulose) [38], cotton pads [10, 38], and gels like glycerine [10], agar
[39], agarose [40], or xanthan gum [3]. One of the newer materials used for poultices is the synthetic magnesium silicate
clay Laponite? RD [41–44]. When dispersed in water, Laponite produces a colourless thixotropic gel that is easy to apply on
specific areas and on vertical surfaces. The high purity of Laponite and thereby the absence of natural iron impurities means
that discolouration of the marble surface from the poultices itself is avoided. In this study, Laponite? RD is mixed with
cellulose fibres (Arbocel? BC1000) with dimensions of 700 × 20 μm (lenght and thickness) in order to increase the porosity,
the absorbing properties and the water retention of the poultice. In addition to this, a small amount of sodium CMC
(carboxymethyl cellulose, sodium salt) was also added. This resulted in better mechanical properties, increasing both the
adherence and the cohesion of the poultice, making it easy to apply and remove in large pieces without crumbling. Another
advantage of this poultice composition was its shrinkage properties: when drying it shrank practically only in the direction
of thickness, leaving the area dimension intact. Hence a uniform cleaning from the centre to the edge of the poultice was
obtained.
Three different types of white Carrara marble (Carrara Bianco): Carrara Fabricotti, Carrara Vagli and Carrara La Piana
from the Carrara quarry in Italy were received. Prior to the study and the artificial discolouration, the marble samples were
characterised by the European Standards for water absorption, DS/EN 13755:2008 and water absorption coefficient by
capillarity, DS/EN 1925:1999. Original samples of naturally rust stained Greenlandic marble from 1937 were retrieved from the
government building of The Public Guardian in Copenhagen, Denmark in connection with restoration of the building. The marble
plates were used as wall facing and, when dismounted, a heavy iron discolouration was present on the backside of the plates.
A high gloss polished marble of the type Carrara Bianco, Lorano was used for etching experiments.
|
|
|
Recommended Lighting Kits for Photography |
Posted by: I678L - 09-27-2021, 01:54 AM - Forum: Off Topic
- No Replies
|
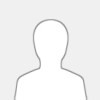 |
Recommended Lighting Kits for Photography
Recommended Lighting Kits for Photography
If you follow some basic lighting principles, you can get impressive results from even the cheapest of motorcycle light combo kit. This is great news for businesses with smaller budgets or folks just starting out with video. As an experiment, we went to Home Depot and built a lighting kit with clothespins, clip lights, and LED bulbs.
While this is not the be-all, end-all lighting kit, it is an attainable and repeatable setup that will keep people on camera looking sharp and well-lit.
Please allow us to introduce Wistia’s “Down and Dirty DIY Lighting Kit” – all for under $100.
Our trip to Home Depot
You can build almost an entire DIY lighting kit with items you can find at any hardware store. Places like Home Depot, Lowes, and ACE should readily stock everything you’ll need.
The effectiveness of this motorcycle fog led light kit hinges on good quality bulbs. Look for daylight balanced bulbs with a high CRI (color rendering index). This will help to produce the highest quality and most flattering light possible. Also, make sure you purchase bulbs that are dimmable. We’ll explain more about this later.
Lights, lights, lights, lights, and more lights. You’ll find them all here at B&H and, even if you are a professional photographer with decades of experience, the sheer number of lighting options today can drive you mad. It drives us mad. You might be thinking, “Where do I even start and how do I find the great auxiliary light combo kit?” Well, today’s your lucky day, because the place to start is right here, with this list of 14 recommended lighting kits—seven flashes and seven continuous—that will help photographers get the job done.
Flash Lighting
We are going to start with a staple of photography: flash. Also known as strobes, these are awesome for photographers because they provide plenty of power, can help freeze motion, and come in nearly any size. Also, the various sync methods—and the fact that now many have built-in radio receivers, make multi-light setups easy. There are plenty of variables to guide your decision, including recycle time, battery versus AC power, accessories, wireless system, and power, so here’s a healthy helping of different types to peruse.
In the very beginning of your lighting journey, you will want something versatile and with the ability to mount directly on your camera. Something like the Bolt VB-11 Bare-Bulb Flash. Being bare bulb means that it can provide a similar look to classic strobes with 360° coverage and high power at 180Ws. It benefits greatly from accessories to modify the light, all of which are included in the Flash and Accessory Kit. Another advantage is the ease with which you can set it up on a light stand or slide it into the hot shoe of your camera, depending on how you want to use it that day. Want something easier to start out with? Go with the Bolt VD-410 Manual Flash and read up about speedlights.
Need something that’s portable, like a speedlight? How about a bare-bulb design that gives the 360 degrees of coverage? Get both with the Godox AD200Pro TTL Pocket Flash Kit. It has the basic form of a speedlight, though without the bounce functions, and has the ability to swap the head from a standard rectangular speedlight to a bare-bulb flash. It’s good and affordable with an excellent 200Ws of power that should be ample, and it runs on a rechargeable Li-ion battery pack that’s good for 500 full-power flashes on a single charge. It also features a built-in X Wireless System Receiver so you can use optional X Series TTL Transmitters to control and trigger the flash remotely. Adding this also enables high-speed sync via TTL. It’s an awesome and versatile lighting choice.
Among Profoto’s latest releases as they push forward with their off-camera flash, or OCF, range is the stellar B10. Available in a two-light kit complete with backpack, the ultra-compact light is battery powered for use nearly anywhere you can stick it. The B10 is rated to 250Ws and has a 10-stop power range. Tack on a 0.05-22 second recycle time, freeze mode with a 1/50,000-second T0.5 flash duration, AirTTL support, and you have a seriously good flash to work with. Oh yeah, it also has LED modeling with with adjustable color temperature and CRI of up to 96 for video shooting on the side. All you need to complete the setup are any of Profoto’s highly regarded OCF Light Shaping Tools and a Profoto Connect for wireless TTL.
A more conventional dirt bike light combo kit comes from the well-known and reliable Elinchrom. By conventional I mean the D-Lite RX 4/4 Softbox To Go Kit is close to what many picture when they think of advanced LED light kit—a couple of monolights with stands and softboxes. These strobes are no slouch, with each of the two heads including offering 400Ws of power. They run on standard AC power and can recycle in just 0.35-1.6 seconds, depending on power. Also, the D-Lite RX 4 has an EL-Skyport Receiver built in, so that you can trigger the camera remotely—easily—via the included EL-Skyport Transmitter Plus. Completing the kit are stands, an octagonal softbox, and a square softbox. Everything you need.
When you hear the name of some brands, you just know you are getting a solid product. In lighting, one such brand is Broncolor, and one of its more recent releases is the Siros L 800Ws Barry-Powered Monolight, which we recommend in the 2-Light Outdoor Kit 2. These are among the most powerful battery-powered strobes, with a rating of 800Ws and benefits from Enhanced Color Temperature Control that ensures the ultimate in consistent color with repeated shots. This is something that Broncolor is known for and something that makes its lights so appealing to professionals. However, if you need some extra speed, there is a mode that will forgo these protections to provide faster recycle times and shorter flash durations, up to a minimum of 1/18,000-second. Optional RES2.2 Transmitters open the door for Broncolor HS, enabling sync speeds at up to 1/8000-second with supported systems. And, you can control multiple lights from your tablet or smartphone using the bronControl app.
Regarding equipment for the rest of us, Dynalite has made the solid Baja A6-600 Monolight 2-Light Kit. This more affordable system can be very enticing, partially because it offers an impressive 600Ws output, which is more powerful than many of its competitors. These are AC-powered monolights, but the added power and 300W modeling light should be appealing for many studio shooters. Also, it comes with a wireless receiver that can work at distances of up to 590' when used with an optional transmitter. The transmitter also unlocks High Speed Sync with Canon or Nikon cameras. It is very much a traditional monolight, but it is a good one and a quite affordable kit, too.
Speedlights and monolights changed the way photographers worked with lights by making them more portable and user-friendly. For the ultimate in performance, it is tough to beat your standard power pack, and the Profoto Pro-10 2400 AirTTL is among the best you can get today. Two outlets, a max of 2400Ws, a built-in Air receiver with TTL support, flash durations that can be as short as 1/80,000(!) second, and recycle times of just 0.02-0.7 seconds make this pack an absolute monster if you need the best of the best. There aren’t any pre-built kits, considering the super-pro nature of the Pro-10, so build your own by adding a couple of ProHead Plus Flash Heads to your bag.
These days, many photographers are spending a healthy portion of their time working with video. Unfortunately, all those awesome flashes and strobes we just talked about can’t do both, since you need a continuous light to work with motion. While, yes, some strobes are packing LEDs that can serve as your video source—the recent Profoto B10 Plus comes to mind—it will be tough to beat dedicated tools such as the ones below.
Relative newcomer Luxli has been killing it lately, and one of its latest is the awesome on-camera option that is the Viola2 5" On-Camera RGBAW LED Light. Its small size and outstanding color controls make it exceptionally versatile. For standard white adjustment there is a variable 3000-10000K temperature range, while the RGBAW nature of the fixture enables complete color tuning, including the ability to set 150 digital gel filters and 10 different special effects. This is ideal for a portable, on-camera light because it eliminates the need for other accessories in your bag. One other thing to consider is this kit with a softbox and diffusion filter. Additionally, it’s part of the Orchestra series, which can be controlled via a mobile app on your smartphone and work in sync with any other members of the band.
Litepanels was one of the first major brands on the scene when LEDs first began to make inroads into photographic and cinematic lighting. It all had to do with the now-ubiquitous 1 x 1' LED panel, now having been updated to the Astra Bi-Color LED Panel. By using an array of high-quality LEDs, Litepanels was able to create a fixture that was lightweight, powerful, and could produce a soft output—all beneficial qualities when considering lights for photography. They could even run on batteries if you needed to use one on the go, and are practically silent. The shape is now classic, and if you want to pick up more than one, Litepanels has numerous Astra Traveler LED Panel Kits available.
Hot lights made Lowel popular for decades. Now, the company is taking a good shot at the LED world by bringing out a new version of one of its most popular lights ever. The TotaLED Daylight LED Light is this reimagining, though it makes sure to maintain similar features to its predecessor. This includes an equivalent output to that of a 750W tungsten bulb, a beam angle of ~65° that can be expanded to 100° via the included diffuser, built-in barndoors, and more. Where this one differs is in its native 5600K color temperature, quite cool operation—no need for gloves with LEDs—and the ability to run on batteries, as well as AC power. If you want, there are two-light and three-light kits ready for purchase.
Go beyond the panel with the Aputure Light Storm LS C120D II LED Light Kit. Using a chip-on-board (COB) LED, it effectively creates a single-point light source, which is more akin to classic tungsten fixtures with a single bulb. No worries about multiple shadows here, and the LS C120D II is exceptionally powerful with the equivalence of a 1000W hot light, while consuming just 180W of power. It also has DMX control, a redesigned handbrake-locking yoke, and can accept all types of Bowens S-mount accessories natively, including Aputure’s popular Light Dome II. Photographers on the go will appreciate the ability to run on either V-mount or Gold-mount batteries. You can pick it up by itself, or in two-light and three-light kits.
Making the list as a personal favorite is the Light & Motion Stella Wedding Photographer Kit. The reason I like them so much that they were included here is that the company is one of very few that makes highly capable lights that are completely waterproof. They really mean waterproof, too. The Stella Pro 5000 and Stella 2000 in this kit are ready to go diving with ratings that make them usable down to 328' underwater. Tough lights can survive some of your crazier ideas and the Light & Motion ones are perfect for it. Both are battery powered and feature a COB LED with excellent, high CRI output that makes them a solid option for photographers working on location. They are also great, compact lights, and the Stella 500 can accept an optional Profoto Adapter to use your more conventional modifiers on it.
The thing about LEDs is that they can be used in ways you never would’ve imagined. One such light that follows through on this is the Westcott Flex Bi-Color LED Mat Cine Set. It’s a completely flexible LED panel measuring 1 x 1', and there are plenty of other sizes available. Why would you want a flexible light? I would counter with a, “Why wouldn’t you want a flexible light?” It can be used on a stand just like your standard panels, yet, when the moment requires it, you can use it in very niche ways. It’s light enough to be taped up to a wall and thin enough to stay out of the shot. You can tuck it down into a case and fold it up so the light is directed a specific way. And that just touches the surface, I’m sure plenty of more imaginative photographers will find even more exciting ways to use it.
LEDs are dominant, though we shouldn’t forget about classic tungsten, HMI, and fluorescent lighting. I’d like to draw your attention to one in particular: the Kino Flo 4Bank 4' Gaffer 2-Light Kit. Essentially the name to know when it comes to fluorescent lighting, Kino Flo’s lights are long revered in the industry for their soft, flicker-free output. Using True Match Fluorescent Lamps, the 4Bank can create a large, soft, and daylight-balanced fixture that has the equivalent output of a 1000W soft light with a fraction of the draw. The separated ballast can be located in an easy-to-access position, as well, while the fixtures’ flexible barndoors provide a simple way to control the light. These are great fixtures, and this kit gives you everything you need except the lamps.
|
|
|
Understanding Pipe Fittings |
Posted by: I678L - 09-27-2021, 01:48 AM - Forum: Off Topic
- No Replies
|
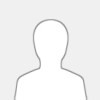 |
Understanding Pipe Fittings
Understanding Pipe Fittings
Pipe fittings are components used to join pipe sections together with other fluid control products like valves and pumps to create pipelines. The common connotation for the term fittings is associated with the ones used for metal and plastic pipes which carry fluids. There are also other forms of malleable iron pipe fitting that can be used to connect pipes for handrails and other architectural elements, where providing a leak-proof connection is not a requirement. Pipe fittings may be welded or threaded, mechanically joined, or chemically adhered, to name the most common mechanisms, depending on the material of the pipe.
There is some inconsistency in terminology surrounding the terms pipe, tube, and tubing. Therefore, the term Carbon Steel Pipe Fitting will sometimes be mentioned in the context of tubing as well as pipe. While similar in shape to tube fittings, pipe fittings are seldom joined by methods such as soldering. Some methods overlap, such as the use of compression fittings, but where these are commonplace for connecting tubes or tubing, their use in pipe connections is rarer. It suffices to say that while there are general distinctions, the common usage of terms can differ from supplier-to-supplier, although they represent the same items.
In this article, the concentration will be on discussing typical fittings and connection methods associated with rigid pipe and piping, with a limited presentation of the fittings that are associated with flexible tubes, tubing, or hose.
To learn more about the varieties of pipe, consult our related guide to pipe and piping.
Pipe Fittings Explained: Fitting Materials and Manufacturing Processes
Cast and malleable iron
Fittings for cast iron pipe fall under hubless and bell-and-spigot styles. Hubless designs rely on elastomeric couplers that are secured to the outer diameters of the pipe or fitting by clamps, usually a stainless steel band clamp that compresses the elastomeric material and forms a seal. These hubless or no hub designs are sometimes referred to as rubber pipe couplings or rubber plumbing couplings and are especially popular for transitioning from one material to another—from copper to cast iron, for instance. Bell-and-spigot, or sometimes, hub-and-spigot, fittings are joined today primarily with elastomeric gaskets that fit inside the bell and accommodate the insertion of the plain pipe end or fitting. Older systems before the 1950s were caulked using a combination of molten lead and a fibrous material such as oakum. Cast iron pipe is sometimes joined with bolted flanges, or in some cases, mechanical compression connections. Flanged joints employed in underground applications can subject the pipe to settlement stresses unless the pipe is adequately supported.
While there are both malleable iron pipe fittings and ductile iron pipe fittings available, the improved mechanical properties and lower cost of ductile iron is causing a shift towards greater use of that material.
Fittings for steel (aka, “black pipe”) and galvanized pipe as found in residential and commercial plumbing work are generally cast and referred to as “malleable iron fittings." They can be galvanized. Although standards list threaded fittings up to fairly large diameters, these generally are not used today as the threading of large-diameter pipe is considered needlessly difficult.
Steel and steel alloys
Galvanized malleable iron pipe fittings are often extruded or drawn over a mandrel from welded or seamless pipe. In smaller sizes they are often threaded to match threads on the ends of pipe. As sizes and pressures increase, they are often welded in place by either butt-weld or socket-weld methods. Socket-weld fittings, usually forged, are restricted to smaller pipe diameters (up to NPS 4, but usually NPS 2 or smaller) and are available in 3000, 6000, and 9000 class pressure ratings, corresponding to Schedule 40, 80, and 160 pipe. Socket fittings are welded into place with fillet welds, which makes them weaker than butt- welded fittings, but still preferable to threaded fittings for high-end work. The need for an expansion gap in the fitting precludes their use in high-pressure food applications.
Flanges are also used, with the resulting flanged sections of pipe connected via bolts. The use of flanges makes breaking the pipeline feasible so as to enable replacement of valves, etc. Most pipeline equipment such as pumps and compressors are also connected via flanges for this same reason.
Flange fittings are available in a handful of styles, rated by pressure and temperature. These styles include lapped, weld neck, socket weld, ring-type joint, screwed, and slip-on. The threaded flange is suitable only for low- to medium-pressure applications. The other various welded-on flanges permit higher pressures to be used. Lapped flanges are often used where disconnections will be frequent as the flange can spin freely, simplifying bolt-hole alignment. A special case is the so-called blind flange, which is used to seal the end of a pipeline but allow connection to another pipe or piece of equipment later.
Flanges can incorporate several different methods to seal adjoining faces, including O-rings, seal rings, and gaskets. Seal rings provide an especially tight joint and for the same bolt stress applied to a flat-face gasket, can resist a higher pressure.
Primarily, three standards govern pipe flanges. ASME 16.5 defines the ANSI flange, the most commonly-used flange. ASME B16.47 covers two series, A and B, which represent large diameter applications. Series A flanges are heavier and thicker than Series B for the same pressure and size. Series B flanges are normally selected for refurbishment work. ASME B16.1 defines the AWWS flange, but it is only for flanges used in potable-water service at atmospheric temperatures. Then, there is the so-called Industry Standard flange which is not defined by a governing body but instead reflects historical practice. The dimensions for these flanges are covered by ASME B16.1, the standard for 25, 125, and 250 class cast-iron-pipe flange and flange fittings.
Stainless steel pipe fittings can be used for sanitary applications such as food and dairy processing, and are commonly fitted with quick-connect clamps to enable dismantling of the line for internal cleaning. The flanges for these clamping systems are available as weld-on entities or in many instances available as wyes, tees, etc. with the flange integral to the fitting.
Metal pipes sections may also be joined and built up as pipelines using pipe couplings and other standard black malleable iron pipe fitting such as metal pipe end caps or 180-degree pipe elbows.
Nonferrous
Aluminum fittings are typically cast. They are available in all the same forms or shapes as steel fittings. Aluminum threaded fittings such as caps or nipples are available, as are fittings that feature a combination of threaded and butt weld connection styles. Socket weld options also exist. Welding of aluminum fittings usually requires a MIG or TIG process.
Aluminum pipe is also a popular choice for use in creating handrails, and a host of fittings for structural applications are available, both weldable and slip on/clamp-on varieties.
Red brass fittings such as brass pipe nipples are available corresponding to pipe diameters, and these are often assembled by soldering or brazing.
Concrete
Concrete pipe fittings are available in a variety of styles suitable to their application in large civil projects such as storm-water control. Aside from the typical wye connections, specialized fittings include utility hole portals and various styles of vaults. Typical connections use shouldered ends on the fittings which mate with counterparts on the receiving pipes. A rubber gasket provides for a leakproof joint.
Plastics
Plastic pipe fittings are available in both socket weld (sometimes called solvent weld) and threaded styles, with the former the most common. Socket weld fittings are designed to be welded in place chemically, thereby making installation quick and straightforward to complete. Plastic pipes are usually dry fitted, then marked, as the solvent used to connect them is especially fast-acting. Couplings are typically used to connect and join straight lengths of pipe together.
Fittings are available in standard shapes and styles and with the dimensional size ranges of material common to plastic pipe, including PVC, CPVC, PE, PEX, PP, and ABS.
Common PVC pipe fittings include reducers, elbows, caps, tees, wyes, couplings, unions, and crosses, to name a few. The standard cross-sectional profile for most PVC pipe or tubing fittings is circular, but there are other profile shapes available, such as square PVC fittings. However, these alternative fitting profiles are usually associated with PVC pipe that is designated for structural use, such as fences, railings, or furniture grade use, and are not associated with PVC pipe that is fluid handling applications. Besides PVC, other materials may be used for structural fittings, one example being galvanized pipe railing fittings.
Other PVC fittings include barbed insert designs, which are intended to be used with tubing and are pressed into the tubing and secured with band clamps.
CPCV pipe fittings, as well as ABS pipe fittings (Acrylonitrile Butadiene Styrene), also are usually joined with fittings that are solvent welded. Suitable conversion adapters for changing material types, such as from CPVC to brass, are also commonly available.
In some applications using plastic pipe, such as in plumbing for sink drains, certain pipe fixtures such as p-traps may be joined with a threaded connection using nylon washers and a retaining or locking nut. This feature facilitates easy disassembly to clear clogs.
Polyethylene pipe fittings and polypropylene Galavanized carbon steel pipe fitting are usually available with both threaded style or barbed style connections, and socket weld or fused options being also available. Similarly, PDVF pipe fittings also are produced with socket or threaded connections.
Where an air or watertight seal is needed, nylon pipe fittings may be employed and can be used with nylon tube or pipe as well as with other types of plastic or metal pipe.
Glass
In some specialized industrial fluid process settings, glass pipe and fittings are employed. Borosilicate glass offers several key advantages over alternative forms of piping systems. The material has high purity, so it will not contaminate process fluids. The natural transparency of glass permits the inspection of the process as needed, while the smooth surface prevents the development of scale or other residues on the interior surface of the pipe.
Laboratory applications may also frequently employ glass tubing and glass profile fittings.
Glass pipe should not be confused with pipes that employ a glass lining, which would be more correctly identified as glass-lined pipe.
Vitrified clay
Fittings for vitrified clay pipe are available in the typical configurations required for sewer installations. Like cast iron, bell-and-spigot is the usual coupling method for these fittings, with an O-ring or gasket used to seal the joint.
Types of Pipe Fittings: Applications and Industries
Callouts
Threaded fittings follow a standardized format on drawings. The nominal dimension comes before the description. When two or more ends of the fitting are not of the same dimension, the dimension of the run precedes those of the branches, or for reducing fittings, the largest dimension precedes the smallest dimension. Thus, a 1 x 1 x 3/4 Street Tee; a 1 x 1x 3/4 45° Y Bend; a 1 x 3/4 x 1/2 x 1/4 Cross; and so forth. The thread size on threaded fittings will correspond to the nominal pipe size thread as specified by ANSI.
Thread Types
Most pipe applications use threaded fittings whose connections can be typically characterized by one of the following systems:
American National Standard Pipe Threads (NPT)
British Standard Pipe Threads (BSPT)
The principal difference between these two is the taper angle. The NPT system uses a thread taper angle of 60 degrees, whereas the British Standard Pipe Thread (BPST) fittings use a slightly lower taper angle of 55 degrees. In addition to threaded pipe fittings which are tapered, these systems also specify straight pipe thread fittings, which do not rely on a taper to seal against pressure loss or leaks. Generally, a suitable sealant is needed to assure that the seal integrity of the joint or connection is achieved. Most threaded pipe fittings are designed to be right-hand threads, but there are some left-handed (LH) thread options available.
Metric pipe fittings are also available, identified by the nominal outside diameter and the thread pitch. So an M12 x 1.5 metric pipe nipple would have an outside diameter of 12 millimeters and a thread pitch of 1.5 threads per millimeter.
Screw fittings are usually threaded internally. The exception is the street fitting, which, in the case of a simple elbow, has one external thread and one internal thread. Pipes are readily threaded in the field. Joining threaded pipes and fittings can be aided by Teflon tape or pipe compound. When applying the compound, it is recommended that it be placed on the external thread only, to avoid introducing any impurities into the pipeline during joint assembly.
Piping layouts are generally one-line or two-line drawings, depending on the complexity of the installation. Where clearances are tight,and for many shop-fabricated pipelines, the two-line drawing is used, which shows the pipe dimensionally to scale. For simpler installations, the one-line drawing suffices, with fittings, valves, etc. designated symbolically. Pipeline drawings are sometimes shown as “developed,” which assumes the vertical pipes are revolved into the horizontal plane, or vice versa, to allow the entire piping system to be shown in the same plane.
Weldolets
These small, weldable branch fittings reinforce the pipe where a hole is made, eliminating the need to add reinforcing. Different forms of these fittings are available under various trademarks, covering butt- and socket-welded styles, thread-on varieties, as well as some special designs which enable connections at elbows, etc.
Welding process
Pipe ends and flanges are prepared for butt welding according to pipe-wall thickness. For walls 3/4 inch thick or less, the walls are beveled to an included angle of 70° and a 3/16 inch gap is left between them. The welder makes a root pass, a fill pass (or passes), and a capping pass, often varying the filler material between passes. For larger thickness, the pipe is tapered to a similar angle but only partway up the wall. In addition, a small relief angle is ground on the inside wall, serving as the location for a backing ring. Socket welds are generally used for thinner-walled pipes. Welding procedures are spelled out by an engineer in Weld Procedure Specifications and the welder making the weld will be certified for the specific process. Pipes sometimes must be preheated prior to welding and heat-treated after to relieve heat stress.
The necessity of proper pipe-end preparation and the need for careful fit-up prior to joining butt-welded fittings makes the use of socket-weld fittings appealing. No bevel is required for socket-weld fittings and the socket itself serves to align the pipe. About the only special requirement is that the pipe must be backed out of the fitting slightly to allow for expansion during the weld.
Prefabrication of pipeline sections, called “spools,” is often done indoors where automation can be applied to the fabrication process. Pipes joints can be rolled on slow turning machines to bring the work to the welder. Robot welders can be used. Techniques such as submerged-arc welding can be applied for productivity gains.
There are non-welded pipe fittings or no weld pipe connectors available as alternatives to the traditionally welded piping systems. Using a combination of swaged mechanical fittings along with the cold bending of pipe or tubing, this solution eliminates the stresses to the pipeline from the welding operation, reduces costs, and can provide for a modular system that is easier to disassemble or modify as needed.
Plastic pipe, and HDPE pipe, in particular, can be joined by heat welding, sometimes referred to as electrofusion welding. Pipes can be butt-welded or socket-welded. This is a fairly common practice for large-diameter HDPE pipeline installations. A range of specialized equipment is available for producing these welds.
|
|
|
Are Blankets the New Going-Out Accessory? |
Posted by: I678L - 09-27-2021, 01:45 AM - Forum: Off Topic
- No Replies
|
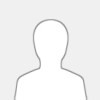 |
Are Blankets the New Going-Out Accessory?
Are Blankets the New Going-Out Accessory?
From Sarah Jessica Parker’s monogrammed Burberry poncho to Norma Kamali’s Sleeping Bag Coat, fashion has long embraced blanket-inspired styles. During a time when most socializing takes place outdoors, would you wear one outside the house?
A weighted blanket is exactly what it sounds like - it’s a blanket with extra weight in it. Weighted blankets are unique as instead of being filled with cotton or down, it contains materials like glass beads to make them heavier. This weight is evenly distributed across the body for a feeling of being gently hugged. The deep touch pressure offered by the weighted blanket is supposed to make you feel safe, relaxed, and comfortable.
Blankets, a symbol of coziness and warmth usually relegated to the indoors, can also be a great piece to layer for fall and winter outfits. Though temperatures are just starting to drop in New York City, WSJ. staffers have spotted a few in the wild—mostly while outdoor dining, which New York City recently extended permanently. (It was originally set to expire ahead of the winter months, on October 31.) For the first time in recent history, the preferred environment for socializing has become “anywhere outside.” And during a pandemic and period of worldwide unrest, most people are seeking comfort more than ever. As a replacement for the timeworn going-out top—obviously better suited to the indoors—the going-out blanket suddenly makes sense.
Over the years, blankets have inspired fashion, from the upscale double layers blanket poncho that Sarah Jessica Parker wore in 2014, personalized with her initials, to Norma Kamali’s famous blanket-adjacent Sleeping Bag Coat, which she first designed in 1973. In 2012, Lenny Kravitz went viral after being photographed by paparazzi while ensconced in an enormous scarf on his way to buy groceries. Six years later, he defended the accessory on an episode of The Tonight Show Starring Jimmy Fallon. “But Lenny,” Fallon said, “this is not a scarf. This is a blanket.”
After my sister gave me a weighted blanket for Christmas, it became the gift that I didn't know I needed. It's one of the best things ever to happen to me.
As someone with anxiety, I've struggled with restful sleep: Falling asleep can take up to two hours, or I wake up at least twice during the night.
The first night I started sleeping underneath a 15-pound flannel blanket, I slept straight through the night for the first time in months and felt more rested during the day. After a few days of good sleep, I learned that my sister had done her gift research — she had read that people with anxiety tended to feel more grounded when using the blankets.
Fascinated, I asked experts on mental health and sleep to explain why these heavy blankets — which are filled with plastic, glass or metal particles and layered with extra fabric — have eased the, ahem, weight of some people's anxiety-related sleep struggles.
Weighted blankets, which range from 5 to 30 pounds (2.27 to 13.6 kilograms), have been used by special needs educators and occupational therapists since the late 1990s, but have become mainstream in the last few years. Regular blankets can weigh around 3 to 5 pounds.
The dominant theory is that weighted blankets provide deep pressure stimulation, a feeling that resembles a "firm, but gentle, squeeze or holding sensation and ... triggers these feelings of relaxation and of being calm," said pulmonary and sleep specialist Dr. Raj Dasgupta, an assistant professor of clinical medicine at Keck School of Medicine at the University of Southern California. Feeling relaxed is what decreases cortisol, a stress hormone that typically runs high in people with chronic anxiety, stress and other disorders, he added.
There is evidence suggesting that deep pressure stimulation reduces sympathetic nervous system arousal — that's our fight-or-flight response — and increases parasympathetic activity, which may cause the calming effect, said Dr. Fariha Abbasi-Feinberg, the director of sleep medicine at Millennium Physician Group in Florida.
Pressure to stimulate the sensation of touch to muscles and joints is the same proposed mechanism behind massage and acupressure, added Abbasi-Feinberg, who is also a neurologist on the American Academy of Sleep Medicine's board of directors. "This calming (effect) can promote better quality sleep."
If you're interested in using a weighted blanket to aid sleep problems related to mental or sensory disorders, here's what you should know about their effectiveness, any caveats and how to choose one.
Weighted blankets have been growing in popularity, but there isn't actually much research on their effectiveness. That may be due to the newness of weighted blankets, their relative harmlessness and that other health issues are more urgent for researchers to study, Dasgupta said.
Some people with anxiety, depression, bipolar disorder or insomnia have reported improved quality of sleep and feeling more restful during the day, a few recent, small studies have found. Many study participants experienced a decrease of 50% or more in their Insomnia Severity Index scores after using a weighted blanket for four weeks, in comparison to 5.4% of the control group, according to a small study published in the Journal of Clinical Sleep Medicine last September.
In the follow-up phase of the study, which lasted one year, people who used fleece blanket continued to benefit. People who switched from lightweight control blankets to weighted blankets experienced similar effects. And those who used weighted blankets also reported better sleep maintenance, a higher daytime activity level, remission from insomnia symptoms and alleviated symptoms of anxiety, depression and fatigue.
Researchers who studied the effects of weighted blankets on children with attention-deficit/hyperactivity disorder or autism have found either some positive associations or no associations with better sleep or reduced symptoms.
"A 'grounded feeling' due to the use of weighted blankets may be attributed to the psychoanalytic 'holding environment' theory, which states that touch is a basic need that provides calming and comfort," Abbasi-Feinberg said via email. "Weighted blankets are designed to work similar to the way tight swaddling helps newborns feel snug and secure."
Many, if not all, of the available studies on weighted blankets used participants who had a psychiatric, developmental or sleep disorder such as anxiety, depression, autism, ADHD or insomnia. That's likely because of "the fact that these segments of the population are the ones who could benefit most from touch- or sensory-related therapies," Abbasi-Feinberg said.
However, given how weighted blankets might work to reduce cortisol levels, they could help to reduce general stress, too, Dasgupta said.
People have shared their fondness for weighted blankets in studies and online, but people with the same psychiatric disorders may not have the same relaxing experiences with weighted blankets. One person in the follow-up phase of the 2020 study discontinued their participation due to feelings of anxiety when using the blanket. People who are claustrophobic may also not fare well. More studies on factors that make individuals more or less helped by weighted blankets are needed, Dasgupta added.
A weighted blanket's calming abilities may help to regulate breathing, but some health professionals are hesitant to recommend weighted blankets to people with obstructive sleep apnea, asthma or other respiratory conditions. "You'd have to be pretty brittle and pretty sick if a blanket's going to stop your breathing," Dasgupta said. But if you're not sure, he added, be careful and talk to your pulmonologist first.
Children should be assessed by occupational therapists or pediatricians before they try sherpa blanket, as many weighted blankets haven't been tested for the effectiveness and safety for children.
"Weighted blankets shouldn't be used for toddlers under 2 years old, as it may increase the risk of suffocation," Abbasi-Feinberg said. "It's important for parents to always consult their pediatrician before trying a weighted blanket."
Dogs sometimes benefit from pressure-applying garments during storms or other anxiety-inducing events, but weighted blankets can be dangerous for pets, said Dr. Douglas Kratt, president of the American Veterinary Medical Association.
If you're looking for a weighted blanket, there are multiple options in terms of weight, materials and size. A blanket that weighs 7% to 12% of your body weight is typically the range to choose from, but that may depend on personal preference. "Some individuals might want a heavier weight to feel a sense of 'hugging' and calmness, while others might want something lighter," Abbasi-Feinberg said.
And there are weighted blankets for year-round use, she added — some are made with a higher proportion of fabric layers made from cotton, which is lighter than other materials and allows air to pass through its fibers, therefore better managing your body temperature.
Dasgupta thinks of sleep as a puzzle, and sometimes people with insomnia or mental disorders are missing some of the pieces needed for great sleep, but "no one really knows what puzzle pieces are missing."
Weighted blankets could help, but they're not a cure-all — a healthy sleep routine is still necessary for getting enough of both sleep time and the deeper stages that leave you refreshed. If you think that a weighted blanket could be your missing puzzle piece, "it's worth a try," Dasgupta said. The downside is that these blankets can be pricey.
During the pandemic, "sleep really took a hit" when it comes to insomnia, altered circadian rhythm and nightmares, Dasgupta said. "A weighted blanket is something that might have a role during this pandemic. ... That sense of the basic need to be touched and hugged could actually provide some comfort and security. Maybe that's why some people benefit from a weighted blanket."
|
|
|
Environmental impacts of wooden, plastic, and wood-polymer composite pallet: a life c |
Posted by: I678L - 09-27-2021, 01:41 AM - Forum: Off Topic
- No Replies
|
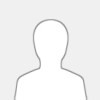 |
Environmental impacts of wooden, plastic, and wood-polymer composite pallet: a life cycle assessment approach
Environmental impacts of wooden, plastic, and wood-polymer composite pallet: a life cycle assessment approach
Waste recycling is one of the essential tools for the European Union’s transition towards a circular economy. One of the possibilities for recycling wood and plastic waste is to utilise it to produce composite product. This study analyses the environmental impacts of producing composite pallets made of wood and plastic waste from construction and demolition activities in Finland. It also compares these impacts with conventional wooden and plastic pallets made of virgin materials.
Methods
Two different life cycle assessment methods were used: attributional life cycle assessment and consequential life cycle assessment. In both of the life cycle assessment studies, 1000 trips were considered as the functional unit. Furthermore, end-of-life allocation formula such as 0:100 with a credit system had been used in this study. This study also used sensitivity analysis and normalisation calculation to determine the best performing pallet.
Result and discussion
In the attributional cradle-to-grave life cycle assessment, wood-polymer composite pallets had the lowest environmental impact in abiotic depletion potential (fossil), acidification potential, eutrophication potential, global warming potential (including biogenic carbon), global warming potential (including biogenic carbon) with indirect land-use change, and ozone depletion potential. In contrast, wooden pallets showed the lowest impact on global warming potential (excluding biogenic carbon). In the consequential life cycle assessment, wood-polymer composite pallets showed the best environmental impact in all impact categories. In both attributional and consequential life cycle assessments, plastic pallet had the maximum impact. The sensitivity analysis and normalisation calculation showed that wood-polymer composite pallets can be a better choice over plastic and wooden pallet.
Conclusions
The overall results of the pallets depends on the methodological approach of the LCA. However, it can be concluded that the wood-polymer composite pallet can be a better choice over the plastic pallet and, in most cases, over the wooden pallet. This study will be of use to the pallet industry and relevant stakeholders.
Pallets are used for storing, protecting, and transporting freight. They are the most common base for handling and moving the unit load, carried by materials handling units, such as forklifts. The pallet market is growing due to the rising standard of goods transportation, the adoption of modern material handling units in different industries, and market demand for palletised goods (McCrea 2016). It was estimated that the global pallet market reached 6.87 billion units in 2018 (Nichols 2020). More than 600 million European Pallets Association (EPAL) approved pallets are available to the global logistics industry. In 2019, 123 million wooden EPAL pallets and other carriers were produced, which is 1.2 million more compared to 2018 (EPAL 2020).
The global pallet market can be classified based on materials, sizes, and management strategies (Deviatkin et al. 2019). Among various segments of pallets, wooden pallets dominate the market share, followed by plastic pallets (Leblanc 2020). Wooden pallets are inexpensive and can easily be manufactured and repaired compared to rackable plastic pallets. One of the most significant downsides of wooden pallets is the cost to forests (Retallack 2019). Furthermore, wooden pallets are heavier than plastic pallets, imposing an environmental burden on freight shipment. Even though plastic pallets are lighter than wooden pallets, plastic pallets’ production is an energy-intensive process. In addition, repairing plastic pallets is impossible because the materials have to be melted down and remoulded in the plastic pallet repairing process.
Waste recycling is one of the pathways taken by the European Union to move towards a circular economy, as highlighted in the circular economy action plan (European Commission 2020). The central idea of a circular economy is to minimise the consumption of virgin materials, which means that an item that can be recycled should not be landfilled or incinerated. The EU is planning to recycle 50% plastic and 25% wood waste by 2025, which will increase to 55% for plastic and 30% for wood by 2030 (European Commission, 2018). By following the EU’s target, Finland’s objective is to fortify its role as a pioneer in the circular economy by implementing the strategic programme for circular economy (Ministry of Employment and the Economy 2021). The transition to a circular economy is essential for Finland to strengthen its export-driven economy with minimum environmental impact.
The environmental benefits of recycled-based plastic products are well known and quantifiable (WRAP 2019). Also, materials made from wood waste can deliver low carbon-based products with less pressure on forests (WWF 2016). One of the possibilities for reducing the environmental burden of plastic and wood waste is to utilise these wastes for wood-polymer composite (WPC) products, such as WPC pallets. However, analysing the environmental performance of WPC pallets requires a complete life cycle analysis. Furthermore, it is important to consider that different materials have different life expectancies, reuse capabilities, and recyclability.
According to International Organization for Standardization (ISO), life cycle assessment (LCA) is one of the environmental management techniques that “addresses the environmental aspects and potential environmental impacts throughout a product’s life cycle from raw material acquisition through production, use, end-of-life treatment, recycling, and final disposal” (EN ISO 14040:2006; EN ISO 14044:2006). Several LCA studies have been conducted on pallets focusing on pallet manufacturing, management strategies and supply chains, repair intensity, and pallets manufactured from various materials, such as wood, virgin plastic, cardboard, and waste plastic. Gasol et al. (2008) conducted an LCA study to compare the environmental performance of wooden pallets with high reuse intensity and low reuse intensity in the European context, and with the findings showing that due to transportation, high reuse intensity pallets have more adverse impacts on climate change than low reuse intensity pallets. Bengtsson and Logie (2015) performed an LCA comparing one-way wooden pallets, disposable compressed cardboard pallets, pooled softwood pallets, and plastic stackable pallets in Australia and China. The study results pointed out that pooled softwood pallets have the minimum environmental impact among all types of studied pallets. Tornese et al. (2018) examined pallets’ economic and climate change impacts, demonstrating that manufacturing a pallet causes more damage to the environment than repairing a pallet. The study also identified that the cross-docking system has equivalent emissions as the take-back system due to higher transportation distance. Almeida and Bengtsson (2017) compared the LCA of waste plastic-based pallets with wooden pallets and virgin plastic-based pallets and demonstrated that plastic waste-derived pallets outperform all other alternatives. Franklin Associates (2007) compared the environmental impacts of pooled pallets versus non-pooled pallets. The study indicated that pooled pallets have less of an environmental burden than non-pooled pallets. Ko?í (2019) studied the environmental impact of wooden pallets, primary plastic pallets, and secondary plastic pallets. The study found that wooden pallets have a better environmental impact than primary and secondary plastic pallets if energy recovery occurs. Furthermore, the study also showed that the weight of the pallet plays a significant role on its total environmental impact.
The authors of previously conducted LCA studies analysed various pallets, making their cross-comparison a difficult task. Previous literature, including the above mentioned studies, have conducted LCA from an attributional point of view and excluded consequential LCA, which is thought to be an important method for identifying the changes in the system as a consequence of using a particular pallet. It is important to investigate the differences in the results, conclusions, and suitability of attributional and consequential LCA for cases where waste recycling is included. Furthermore, all the former studies assumed that various pallets perform equally well during their life cycle. None of the studies considered that pallets made with different materials have different life expectancies, repairing times, and recycling rates. In addition, end-of-life (EoL) is an integral part of the cradle to grave LCA. The methodological difference of the EoL allocation might have a significant impact on the overall result of LCA. It is found that the allocation of the environmental burdens of the EoL of the pallets was absent in the studies as mentioned earlier.
The goal of this LCA study was to calculate and assess the environmental impacts of manufacturing, utilising, and disposal of pallets made of different materials. Both attributional LCA (ALCA) and consequential LCA (CLCA) methods were used in the study. An ALCA investigates the environmental impact of the physical flows to and from a product’s life cycle and its subsystems (Ekvall et al. 2016). In contrast, consequential LCA investigates the environmental impacts of the product system and the systems linked to it that are expected to change for production, consumption, and disposal of the product (Ekvall et al. 2016). Despite the ISO 14040/44 standards not explicitly distinguishing between the two types of LCAs, there is a clear difference in the definition of the scope for those assessments, as described below. The study results are intended to guide the selection of materials for the production of pallets.
Scope of the ALCA study
The attributional LCA follows the cradle-to-grave approach, meaning that the product system includes the processes starting with the provision of raw materials from the environment in the form of elementary flows, i.e. the flows created by nature, through the use of the pallets and ending with their disposal and with the release of emissions into air and water, and to the generation of waste.
The system boundary of the ALCA comparing the impacts of the pallet’s production, use, and EoL is shown in Fig. 1. The modelling started with producing the raw materials and the energy generation for the pallets, such as wood harvest, timber production, and plastic production. It should be noted that the system boundary for WPC starteds from the collection of waste. Once the materials are produced and delivered to the production facilities, the pallets are manufactured. Nails are used to secure the parts of the wooden pallets, whereas plastic and WPC pallets are compressed into the required shape and do not require any fixing elements. The pallets are then delivered to a pallet pooling company, which operates by delivering the produced pallets to customers who can use them for their own purposes. After which, the pooling company collects the pallets and repairs them in the case of wooden pallets, if needed. After being used, the pallets are crushed for incineration. In the case of wooden pallets, ferrous metals are separated before incineration. By incinerating wooden, plastic and WPC pallets’ waste, energy is substituted. Nevertheless, materials are also substituted by separated ferrous metals from wooden pallets.
EoL allocation
There are no strict or specific requirements for modelling the EoL in LCA, and several allocation methods exist, such as 0:100 approach, 100:0 approach, 100:100 approach, 50:50 approach, etc. (Allacker et al. 2017). 0:100 EoL method can be conducted in two different ways, such as 0:100 with no credit for avoiding virgin materials and 0:100 with credit for avoiding virgin materials (Allacker et al. 2017). The system boundary of the study ends at the recovery of energy and material from the EoL phase. Therefore, in this study, the 0:100 EoL method with credit system had been used.
In the CLCA, the correct way of modelling environmental impact is to use marginal production technology data for the substituted product. Marginal production technologies are those technologies that are changed by the small changes in demand (Weidema et al. 1999). It was found from this study that a significant amount of heat and electricity substitution was impacted when wood and plastic waste were not incinerated but used for WPC pallet production. In this case, marginal heat and electricity were used in the modelling of CLCA. Biomass will be the prime heat production source in Finland by 2030 (Ministry of Employment and the Economy 2017), and wind and solar power will provide the maximum share of electricity by 2030 (SKM Market Predictor 2019). Therefore, the biomass-based heat source was selected as the marginal heat source and wind, and solar-power-sourced electricity was selected as the marginal electricity source in CLCA modelling. The more detailed information on the selection of marginal heat and electricity is presented in the supplementary materials.
Selection of the pallets
A great variety of pallets exists, as dictated by the specific requirements of customers. However, this study exclusively focused on pooled pallets, with the dimension of 1200 mm?×?800 mm, made of either wood, plastic, or WPC. The pallets with the above-specified dimension are widely known as EUR pallets and are the most widely used type of pallets in Europe (EPAL 2019).
Table 1 specifies the key parameters of the studied pallets in their baseline scenario. Wooden pallets are made of virgin wood, which is a mixture of softwood and hardwood as specific to Finnish conditions. The studied wooden pallets were block-type pallets, which are commonly used in Europe. Based on the review of LCA studies of wooden and lightweight plastic pallet by Deviatkin et al. (2019), the expected lifetime of the wooden pallets is 20 cycles, yet the number ranged between 5 and 30 cycles in most of the publications reviewed. The repair need of 7 cycles was estimated based on the mass of produced EUR pallets in Finland (3.2?×?103 kg), alongside with repaired (25?×?103 kg) and reused (167?×?103 kg). The expert views from a Finnish pallet pooling company suggested that the expected lifetime of the wooden pallets is somewhat higher, whereas the repair need for the pallets occurs on average after every 12 cycles. The variations in the expected lifetime of the pallets were examined in the scenario analysis of this study. It was assumed that, at the EoL, 90% of wooden pallets are incinerated, whereas 10% are used as a bulking agent in composting facilities.
The plastic and WPC pallets are identical in structure and production method. Plastic pallets are manufactured using injection moulding, whereas WPC pallets are produced by extrusion followed by a compression moulding process. Both pallets are made to allow their nesting, thus saving the space occupied by the pallets. The exact height occupied by wooden stackable pallets can fit 1.7 times more plastic or WPC pallets. According to the literature on plastic pallets, plastic pallets are more durable than wooden pallets (Deviatkin et al. 2019). The expected lifetime of Double Sided Plastic Pallets could be 66 cycles, whereas the lifetime ranges from 50–100 in most of the studies reviewed (Deviatkin et al. 2019). In this study, the lifetime of plastic pallets was considered to be 66 cycles by following the review study conducted by Deviatkin et al. (2019). The WPC pallets were assumed to be of comparable properties as plastic pallets in these terms. Plastic and WPC pallets are suitable for demanding applications, such as those with expected exposure to water, or specific industrial demands, like those of the pharmaceutical industry. Such features of plastic and WPC pallets are, however, not considered in this study. Once damaged, neither plastic nor WPC pallets can be repaired.
|
|
|
The Science of LED Grow Lights for Your Indoor Garden |
Posted by: I678L - 09-27-2021, 01:35 AM - Forum: Off Topic
- No Replies
|
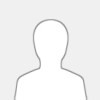 |
The Science of LED Grow Lights for Your Indoor Garden
The Science of LED Grow Lights for Your Indoor Garden
Indoor Gardening isn’t exactly a new thing, but LED’s are changing the way we light our indoor gardens. LED lights are more efficient than traditional fluorescent and incandescent lights. That’s because LED lights convert nearly all of their energy (95%) into light, while other lights turn a significant amount of energy into heat. But, there’s another very important reason that LED’s are more efficient when it comes to growing plants. With LED lights, we have the rather unique ability to customize the type of light that is emitted, and that means we’re not wasting energy to create light that doesn’t help our plants grow. At the end of this article, you’ll understand the science behind why spyder grow light series come in many different colors, as well as why some LED grow lights cost so much more than others.
Plants Only Use the Visible Light Spectrum for Photosynthesis
It’s important to know that plants only use visible light (the colors of light that we see every day) for photosynthesis. However, as the chart below demonstrates, the complete spectrum of light is far greater than just the visible light spectrum. On the outer edge of the visible light spectrum is Ultraviolet (UV) light and Infrared Radiation (IR). UV light is the invisible light emitted by the sun and other sources that will cause sunburns when we don’t wear sunblock. IR light can only be seen with special equipment, like night-vision goggles. Even further out from the visible light spectrum are light waves that we don’t traditionally think of as light. These include X rays, Microwaves and even Radio Waves.
One of the most important things to understand is that scientists have demonstrated over and over again that plants only absorb visible light for photosynthesis. Plants do react to other forms of light like UV, but that reaction is typically negative. I’m told that marijuana growers actually use UV light to induce the production of psychoactive chemicals like THC, which seem to be produced in part as a defense mechanism against the damaging effects of UV light to the plant.
What is PAR?
PAR stands for “photosynthetically available radiation.” PAR is made up only of visible light, because this is the only light that plants use for photosynthesis.
For decades, many indoor growers have used Lumens to measure a grow light’s efficacy, but the industry is getting smarter and turning to PAR. Lumens are used to measure the brightness of a lamp to the human eye. But plants and people see light differently. Humans see yellow and green more brightly than other colors. Therefore, yellow and green lamps may have higher Lumen values than red and blue lights that put out just as much actual light, and which plants are likely to respond better to.
PAR measures all light from the visible light spectrum equally, and does not measure light outside of the visible light spectrum, which does not help the plant photosynthesis. So, for plants, the PAR value of a light is currently the best basic measurement of a grow light’s brightness. Accurate PAR meters are quite expensive and generally cost $500 or more. Inaccurate PAR meters can be purchased for much less, but there’s really no point to owning an inaccurate PAR meter.
The best way to get PAR values for your 400W LED grow light, assuming you don’t want to purchase your own PAR meter, is to check with your reputable grow light manufacturer or provider for the PAR rating of their lights.
How Much PAR do My Plants Need to Grow?
The amount of PAR your plants require depends on what you are growing, as well as how far away from your plants the light is. Generally speaking, leafy greens like lettuce only need a PAR value of ~200, whereas tomatoes and other plants that flower and produce fruit require 400-500 or more PAR. Unless you place your 600W LED grow light right on top of your produce, you will need an even higher PAR rating from your grow light, to take into account the distance between your plant and the light source.
In the example below, you can see a very powerful grow light that puts out nearly 1,900 PAR (measured in umol) 8 inches from the source. Very few lights put out this much PAR, and they are typically quite expensive. This light will emit 1,900 umol every second. But at 23 inches from the source, the strength of the light is reduced to 890 umol. The PAR value is reduced further and further as you get further from the light source. When we get to 6 feet away from the light source, our PAR value is down to ~100umol, which means we would have trouble growing even lettuce well. So, always make sure you understand not just the PAR emitted from the light, but that every 8 inches or so away from your light, the PAR value will be reduced by ? or more.
There are many inexpensive grow lights on the market that make big claims, but they will ultimately leave their owners disappointed. This issue is especially rampant on the internet. Remember to check the PAR value of any light you purchase. Also, remember to take into account how far your light will be from your plant to ensure there is enough photosynthetically available radiation (PAR) for your plant to flourish.
Leafy Greens require 200 PAR for proper growth
Tomatoes, cucumbers and other flowering/fruiting vegetables require 400-500 PAR
Fruiting Trees should be given 600 PAR or more
What is the Temperature of Light I Should Use?
Interestingly, ‘Kelvin temperature’ is the metric used to describe the visual color that a light emits. As you can see in the chart below, ‘warmer’ light temperatures that have a red color have a lower Kelvin rating. On the other end of the spectrum are ‘cooler’ temperature lights which have a blue color and higher Kelvin rating.
Different temperatures of light have different impacts on plants. Generally, higher temperatures (blue) light encourages photosynthesis which leads to bushy plants that don’t feel inclined to elongate and reach for more light. This is great if you want to grow in a compact space. Lower temperature (red) light reduces photosynthesis and signals to plants that that it’s time to flower and produce fruit. Plants put under a red light will also be more inclined to stretch and grow taller, as opposed to growing bushier and more compact.
IGWorks focusses on providing full spectrum lights with a natural color temperature of between 4500K-6500K as these are most pleasing to the eye. They also allow plants to grow bushy and compact, without hindering the ability of plants to flower and fruit.
What Color of Light Should I Use?
LED lights can come in almost any color. Plants respond most to red and blue light. Interestingly, plants generally respond less well to green light. In fact, the reason that plants appear to be green is that they tend to reflect green light, while they absorb other parts of the light spectrum more readily. This is why a large scale or industrial grower of plants will often use a combination of red and blue lights to photosynthesize their plants. They don’t want to waste electricity producing green and even yellow light, which plants use less effectively.
However, for those of us growing produce in our living spaces, it’s probably worth the extra pennies it costs to produce a nice full-spectrum color that will be more natural and pleasing to the eyes. Full-spectrum grow lights will often come with a chart, which shows the distribution of blue, green, yellow and red light that is emitted. See the example below
Choosing the right grow light spectrum for your commercial operation can be a challenge. Many 800W LED grow light suppliers have conflicting information on the topic due to bad marketing or simply a lack of knowledge in plant and light research.
In this article, our light spectrum experts break down what light spectrum is, how plants respond to light, and how light spectrum influences plant growth.
What is Grow Light Spectrum?
Light spectrum is the range of wavelengths produced by a light source. When discussing light spectrum, the term ‘light’ refers to the visible wavelengths of the electromagnetic spectrum that humans can see from 380–740 nanometers (nm). Ultraviolet (100–400 nm), far-red (700–850 nm), and infra-red (700–106 nm) wavelengths are referred to as radiation.
As growers, we’re most interested in the wavelengths that are relevant to plants. Plants detect wavelengths that include ultraviolet radiation (260–380 nm) and the visible portion of the spectrum (380–740 nm) which includes PAR (400–700 nm), and far-red radiation (700–850 nm).
When considering light spectrum for horticultural applications, greenhouse and indoor environments will differ. With indoor environments your grow light’s spectrum will account for the total light spectrum that your crop receives. Whereas in a greenhouse you must consider that your plants are receiving a combination of folding grow light series and solar spectrum.
Either way, the amount of each waveband that your crop receives will have significant effects on growth. Let’s learn more about how this works.
Plants use light for photosynthesis and photomorphogenesis. Photosynthesis is the process by which plants and other organisms convert light energy into chemical energy. Photomorphogenesis refers to how plants modify their growth in response to light spectrum.
One example of photomorphogenesis is a plant bending toward a light source. Light also affects plants’ developmental stages, such as germination and flowering.
The light that plants predominately use for photosynthesis ranges from 400–700 nm. This range is referred to as Photosynthetically Active Radiation (PAR) and includes red, blue and green wavebands.
Photomorphogenesis occurs in a wider range from approximately 260–780 nm and includes UV and far-red radiation.
Although results are dependent on other factors, there are general rules of thumb that you can follow when using light spectrum to elicit different plant responses.
Outlined below is an overview of how each waveband is used for horticultural purposes so that you can trial light spectrum strategies in your own growth environment and with your chosen crop varieties.
Blue light has distinct effects on plant growth and flowering. In general, blue light can increase overall plant quality in many leafy green and ornamental crops.
A minimal amount of blue light is required to sustain normal plant development. In terms of adjustable spectrum lighting strategies, if we were to equate red light to the engine of your car, then blue light would be the steering wheel.
When combined with other light spectrum wavebands, blue light promotes plant compactness, root development, and the production of secondary metabolites. Blue light can be utilized as a growth regulator, which can reduce your need for chemical plant growth regulators (PGRs). Blue light can also increase chlorophyll accumulation and stomatal opening (facilitating gas exchange), which can improve overall plant health.
One example of blue light influencing secondary plant metabolite production is how blue wavebands promote anthocyanin development in leaves and flowers. Increased anthocyanin levels result in more pronounced color.
Blue light also promotes other secondary metabolic compounds associated with improved flavor, aroma and taste. For example, blue light treatments have been shown to improve terpene retention in some varieties of cannabis.
Higher intensities of blue light (>30 μmol·m-2·s-1) can inhibit or promote flowering in daylength-sensitive crops. Blue light does not regulate flowering at low light intensities (<30 μmol·m-2·s-1), so is safe to be applied at night to influence the other plant characteristics listed above
Since chlorophyll does not absorb green light as readily as other wavelengths, many have written off the green waveband as being less important to plant growth. This lower chlorophyll absorption rate, compared to blue and red light, is what makes most plants appear green. Depending on the plant, leaves generally reflect 10-50% of green waveband photons.
In contrast to assumptions, studies of green light in crop production have concluded that green light is important to photosynthesis, and especially in a plant’s lower leaves. Around 80% of green light transmits through chloroplasts, whereas leaves absorb approximately 90% and transmit less than 1% of red and blue light.
So what does this all mean? When light is plentiful, chlorophyll reaches a saturation point and can no longer absorb red and blue light. Yet, green light can still excite electrons within chlorophyll molecules located deep within a leaf, or within chloroplasts lower in the plant’s canopy. And so, green light enhances photosynthetic efficiency—potentially increasing crop yields, during bright light conditions.
Additionally, the ratio of green to blue and red wavelengths signals to the plant a leaf’s canopy position. This can induce morphological changes to maximize light absorption. Green light also plays a role in regulating stomatal aperture (opening and closing of plant pores that make gas exchange possible).
Greenhouse applications require less supplemental green light since plants receive adequate green light from solar radiation. Indoor environments may benefit more from supplemental green light since no sunlight is present.
|
|
|
|