Welcome, Guest |
You have to register before you can post on our site.
|
Online Users |
There are currently 190 online users. » 0 Member(s) | 188 Guest(s) Applebot, Bing
|
Latest Threads |
Advanced microneedling
Forum: Off Topic
Last Post: axied12
05-28-2025, 01:25 PM
» Replies: 0
» Views: 148
|
Caviar and cheese
Forum: Off Topic
Last Post: axied12
05-28-2025, 12:38 PM
» Replies: 0
» Views: 139
|
Top-rated countertop comp...
Forum: Off Topic
Last Post: axied12
05-04-2025, 06:42 AM
» Replies: 0
» Views: 292
|
Ryanair letenky levně do ...
Forum: Off Topic
Last Post: axied12
02-11-2025, 01:37 PM
» Replies: 0
» Views: 686
|
Trusted essay writing ser...
Forum: Off Topic
Last Post: axied12
01-30-2025, 08:16 AM
» Replies: 0
» Views: 618
|
Bootverkopers - actieve j...
Forum: Off Topic
Last Post: axied12
12-07-2024, 11:07 AM
» Replies: 0
» Views: 746
|
Services for individuals ...
Forum: Off Topic
Last Post: axied12
12-02-2024, 03:31 PM
» Replies: 0
» Views: 705
|
Used excavators
Forum: Off Topic
Last Post: axied12
11-13-2024, 09:22 AM
» Replies: 0
» Views: 687
|
Buy Higo Rocket in Dubai
Forum: Off Topic
Last Post: axied12
10-25-2024, 01:09 PM
» Replies: 0
» Views: 790
|
Anime coloring pages
Forum: Off Topic
Last Post: axied12
10-13-2024, 05:10 PM
» Replies: 0
» Views: 832
|
|
|
A review on RO membrane technology: Developments and challenges |
Posted by: ppfd15151s - 09-23-2021, 03:00 AM - Forum: Welcomes and Introductions
- No Replies
|
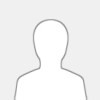 |
Reverse osmosis (RO) based desalination is one of the most important and widely recognized technologies for production of fresh water from saline water. Since its conception and initiation, a significant development has been witnessed in this technology w.r.t. materials, synthesis techniques, modification and modules over the last few decades. The working of a RO plant inclusive of the pretreatment and post-treatment procedures has been briefly discussed in the article. The main objective of this review is to highlight the historical milestones achieved in RO technology in terms of membrane performance, the developments seen over the last few years and the challenges perceived.
The material properties of the membrane dominate the performance of a RO process. The emergence of nano-technology and biomimetic RO membranes as the futuristic tools is capable of revolutionizing the entire RO process. Hence the development of nano-structured membranes involving thin film nano-composite membranes, carbon-nanotube membranes and aquaporin-based membranes has been focussed in detail. The problems associated with a RO process such as scaling, brine disposal and boron removal are briefed and the measures adopted to address the same have been discussed.
In response to the escalating world water demand and aiming to promote equal opportunities, reverse osmosis desalination has been widely implemented. Desalination is however constantly subjected to fouling and scaling which increase the cost of desalination by increasing the differential pressure of the membrane and reducing the permeate flux. A bench-scale desalination equipment has been used in this research to investigate the mitigation of fouling and scaling. This study involved the performance of membrane autopsy for fouling characterisation with special attention to flux decline due to sulphate precipitation and biofouling. Visual inspection, scanning electron microscopy (SEM), energy-dispersive x-ray spectroscopy (EDS), Fourier transform infrared spectroscopy (FTIR) and microbiology tests (API) were performed. Results obtained showed the presence of diatoms, pseudomonas and polysaccharides as the main foulants causing biofouling. Analysis revealed sulphate deposits as well as aluminium, calcium and silica as the main elements contributing to inorganic scaling. Findings pointed out that the pre-treatment system of the small-scale reverse osmosis water treatment was inefficient and that selection of pre-treatment chemicals should be based on its compatibility with the membrane structure. The importance of characterisation for the verification of fouling mechanisms is emphasised.
This research was conducted to determine the performance of Reverse Osmosis (RO) membranes in producing pure water, pure water known as mineral-free water or water with zero dissolved solids (TDS = 0 ppm).PDAM (Regional Drinking Water Company) Tirta Musi in Palembang, South Sumatra and water from the Micro Filtration (MF) and Ultrafiltration (UF) processes are fed to the RO process using two feeding methods, namely a single pass and a circulation feed. In a single pass feed, the operating pressure is set at 20 - 50 Psig, where an increase in the product rate and the rejection rate so that the flux increases. Rejection of TDS obtained increased from 96.6% - 97.5%. Furthermore, the circulating feed system with a constant pressure of 50 Psig decreases TDS and Conductivity. Rejection of TDS 96.1% for PDAM water feed and Rejection of TDS for feed water from MF&UF 97.3% in subsequent feedings there was a decrease in TDS and conductivity but not significantly. The purified water produced has a TDS content of 0.16 - 0.48 ppm, a conductivity of 0.17 - 0.49 μs/cm, a pH of 6.99 - 7.2 and a resistivity of 177 - 185 kΩ, the characteristics of this pure water are according to the standard pure water in ASTM D1193 - 99e1 and NCCLS.
Clean water obtained by desalinating sea water or by purifying wastewater, constitutes a major technological objective in the so-called water century. In this work, a high-performance reverse osmosis (RO) composite thin membrane using multi-walled carbon nanotubes (MWCNT) and aromatic polyamide (PA), was successfully prepared by interfacial polymerization. The effect of MWCNT on the chlorine resistance, antifouling and desalination performances of the nanocomposite membranes were studied. We found that a suitable amount of MWCNT in PA, 15.5 wt.%, not only improves the membrane performance in terms of flow and antifouling, but also inhibits the chlorine degradation on these membranes. Therefore, the present results clearly establish a solid foundation towards more efficient large-scale water desalination and other water treatment processes.
Introduction
The availability of clean water has become a global problem because of the continuously increasing costs of energy and increasing scarcity of water resources1. This problem has been exacerbated in recent years in the so-called century of water. By far, the domestic ro membrane process persists as the most reliable and cost-effective water desalination technique and numerous large-scale RO plants have been constructed around the world2,3. A wide range of polymers have shown potential for fabricating desalination membranes to be used in RO4. However, PA-based membranes tend to exhibit the best performance in terms of selectivity, flow, chemical stability and ease of large-scale fabrication. PA membrane technology was developed in the mid-70 s and has become the commercial benchmark in RO membranes5. In order to improve the membrane performances, the recent trend in polymer-based membrane research has been to investigate various types of nanocomposite films as an active layer of RO membrane, so-called nanocomposite membranes, in which these films are fabricated using a nanosized filler such as MWCNT, graphene, graphene oxide, silica, or zeolite6. In this regard, MWCNT·PA-based membranes have been prepared by several groups and in general, these membranes have exhibited some level of improved performance7,8,9,10,11,12. The advantages claimed for these membranes range from increased salt rejection, large fluxes, greater durability and even antimicrobial properties.
MWCNT synthesized by catalytic chemical vapour deposition13,14 have been widely studied due to their fascinating chemical and physical properties and among all nanocarbon materials, they can be mass-produced for commercially available applications, such as the electrode additives in high performance lithium ion batteries15. Interestingly, while the structure of the fully aromatic PA-based commercial ro membrane derived from m-phenylendiamine (MPD)-trimesoyl chloride (TMC) is constrained due to its stoichiometry; the addition of MWCNT can significantly vary their performance due to their unique features such as dispersability diameter, length, straightness and chemical functionalities, among many others. Therefore, although these past reports acknowledge the key role of MWCNT in aromatic PA nanocomposite membranes, still little attention has been devoted to the mechanisms related to the improvement of flow rate, selectivity and chlorine tolerance2. Carbon nanotubes inducing chlorine tolerance are particularly interesting because chlorine sensitivity has been recognized as a major drawback of PA-based RO membranes16,17. During long-term operation, chlorine is often added as a pre-treatment to reduce algae biofouling18 and is particularly needed for drinking water purification. Moreover, high-concentration short-term exposure to chlorine is also common during domestic nf membrane backwashing. For these reasons, several studies have been carried out and the degradation mechanism of aromatic PA membranes during chlorine exposure is relatively well-known19,20. Recently, our group demonstrated that the addition of MWCNT to rubber can considerably reduce the chlorine-induced degradation of the polymer matrix21. Although the degradation mechanism of rubber by chlorine is different from that of PA, particularly due to the lack of hydrolysis, covalent chlorination is a common problem for both polyamide and rubber. For rubber, we found that MWCNT effectively restricted the adsorption of chlorine within the polymer matrix, thus resulting in a limited exposure of the polymer to this reactive reagent and thereby decreasing the oxidative degradation. For these reasons, we believe MWCNT are not only promising composite fillers with chlorine protective properties, but might also help to provide mechanical robustness to PA-based RO membranes.
Results and Discussion
We prepared aromatic PA membranes using a support consisting of a porous polysulfone layer deposited on a polypropylene nonwoven. These support membranes were soaked sequentially in MPD and TMC solutions, to synthesize the aromatic PA membrane by interfacial polymerization. In order to incorporate MWCNT into the PA membrane, an anionically stabilized dispersion of MWCNT (Supplementary Fig. S1) was mixed with the MPD solution and the synthesis was conducted similarly. Figure 1a shows an image of the resulting membranes, with and without MWCNT. The black color developed in the membrane prepared using surfactant dispersed MWCNT is characteristic of the high carbon nanotube content of the present membrane (Fig. 1a). Thermogravimetry of the active layer (Supplementary Fig. S2) of the black color membrane indicates that it contains ca. 15.5 wt. % of MWCNT, which is at least 150 times higher than previously reported MWCNT-filled RO PA membranes7,8,12. The SEM image showing the surface morphology of the membrane is typical for the interfacial PA polymerization22, consisting of the multi-layered ridge-and-valley (Fig. 1b); the morphology of this membrane clearly changed after the addition of MWCNT (Fig. 1c). The thickness of the membranes was measured using SEM (Supplementary Fig. S3). The addition of MWCNT did not modify the thickness of the active layer and both samples were approximately 100 nm thick. However, water contact angle measurements showed a slight increase in wettability upon addition of MWCNT to the PA membrane (Supplementary Fig. S4). Notably, no MWCNT were visible on the surface, thus indicating that they were perfectly embedded within the PA matrix, a key factor needed for avoiding MWCNT leakage during operation. Flow permeation rates, as indicated below and SEM images confirmed that the membranes can be produced pinhole-free in a reproducible way. After the membrane was dried for SEM studies, cracks were generated by manual deformation of the membrane (Fig. 1d) and MWCNT embedded, parallel along the membrane surface, were observed bridging the fracture within the polymer matrix. The apparent diameter of these nanotubes are ca. 20 nm, which is about two times larger than the pristine nanotubes (Fig. S1a). These facts suggest that the nanotubes must be coated with polymer to achieve a good matrix-nanotube adhesion. In order to support our proposed structure consisting of a polymeric network with aromatic moieties in parallel arrangement to the MWCNT walls, we performed theoretical simulations of the monomer molecules orientation in the vicinity of a carbon nanotube surface, see Supplementary Fig. S5. Here, four different cases, consisting of two geometrical configurations, are demonstrated: horizontal and vertical alignments with respect to the MWCNT surface (modelled as a graphene surface), for both monomers (MPD and TMC). The results indicate a clear energetic preference for the horizontal arrangements of these molecules interacting with sp2 hybridized carbon networks; these preferences are related to π-π stacking and are known to be common for aromatic compounds on sp2 hybridized carbon surfaces. Similarly, Fig. S5b shows a simulation of 50 MPD molecules absorbed on a graphene surface and it can be seen that the molecules adopt a similar geometrical orientation after relaxation (Fig. S5c). In order to rule out curvature effects, we carried the simulations using a (10,10) single-walled carbon nanotube (Fig. S5d), which evidently has a higher curvature than the 10 nm diameter MWCNT experimentally used in the membrane fabrication. It can be seen on Fig. S5e that after relaxation, the aromatic ring of the MPD molecules lies parallel to the carbon nanotube surface. We confirmed the strong affinity of MPD with MWCNT by filtering the solution and carrying out UV-Vis spectroscopy. We found that 16.7% of the MPD monomer remained attached to the MWCNT. These MPD functionalized MWCNT were polymerized in TMC solution. Supplementary Fig. S6a shows a homogeneous PA coating on the MWCNT. Supplementary Fig. S6b depicts a higher resolution image showing a coating of about 5 nm thick on the MWCNT surface. We used fast Fourier transformation (FFT) of the HRTEM images to analyze the orientation of the PA network and it is clear that PA regions that do not contain MWCNT, show an anisotropic molecular arranged structure (Supplementary Fig. S6c), whereas the PA coating the nanotubes show a preferential orientation of PA molecules along the MWCNT surface (Supplementary Fig. S6d). These experiments strongly support a templating effect caused by MWCNT. To assess the distribution of the MWCNT within the membrane, a Raman mapping of the characteristic D- and G- bands of MWCNT was conducted (see Fig. 1e,f). Through all the studied areas only the D- and G- peaks could be observed, indicating a homogenous mixture and a high content of MWCNT, which is not common in these type of nanocomposites, because the MWCNT are prone to aggregation even when loading at low concentrations. Commercial NF membrane exhibited a lower contact angle; however in this case, the presence of wetting additives or a surface treatment is likely responsible for this phenomena. The method used to synthesize the MWCNT·PA nanocomposite relies on the transport of the MWCNT to the organic/aqueous interface during polymerization23. Indeed, the presence of a limited amount of anionic surfactant has been recently reported to improve PA membrane formation, resulting in better performance24. This is most likely due to a reduction of the oil/water interfacial tension, a process that in our case is also promoted by the small amount of surfactant that provides amphiphilicity to the nanotubes It is important to emphasize that we did not used covalent functionalization of MWCNT, in contrast to some previous reports8,11.
|
|
|
What is a combiner box? |
Posted by: ppfd15151s - 09-23-2021, 02:58 AM - Forum: Welcomes and Introductions
- No Replies
|
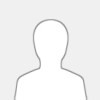 |
The role of the combiner box is to bring the output of several solar strings together. Daniel Sherwood, director of product management at SolarBOS, explained that each string conductor lands on a fuse terminal and the output of the fused inputs are combined onto a single conductor that connects the box to the inverter. “This is a combiner box at its most basic, but once you have one in your solar project, there are additional features typically integrated into the box,” he said. Disconnect switches, monitoring equipment and remote rapid shutdown devices are examples of additional equipment.
Solar combiner boxes also consolidate incoming power into one main feed that distributes to a solar inverter, added Patrick Kane, product manager at Eaton. This saves labor and material costs through wire reductions. “Solar combiner boxes are engineered to provide overcurrent and overvoltage protection to enhance inverter protection and reliability,” he said.
“If a project only has two or three strings, like a typical home, a solar combiner box isn’t required. Rather, you’ll attach the string directly to an inverter,” Sherwood said. “It is only for larger projects, anywhere from four to 4,000 strings that combiner boxes become necessary.” However, combiner boxes can have advantages in projects of all sizes. In residential applications, combiner boxes can bring a small number of strings to a central location for easy installation, disconnect and maintenance. In commercial applications, differently sized combiner boxes are often used to capture power from unorthodox layouts of varying building types. For utility-scale projects, combiner boxes allow site designers to maximize power and reduce material and labor costs by distributing the combined connections.
The combiner box should reside between the solar modules and inverter. When optimally positioned in the array, it can limit power loss. Position can also be important to price. “Location is highly important because a combiner in a non-optimal location may potentially increase DC BOS costs from losses in voltage and power,” Kane explained. “It only constitutes a few cents per watt, but it’s important to get right,” Sherwood agreed.
Little maintenance is required for combiner boxes. “The environment and frequency of use should determine the levels of maintenance,” Kane explained. “It is a good idea to inspect them periodically for leaks or loose connections, but if a combiner box is installed properly it should continue to function for the lifetime of the solar project,” Sherwood added.
The quality of the combiner box is the most important consideration when selecting one, especially since it’s the first piece of equipment connected to the output of the solar modules. “Combiner boxes are not expensive compared to other equipment in a solar project, but a faulty AC combiner box can fail in a dramatic way, involving shooting flames and smoke,” Sherwood warned. “All should be third-party certified to conform to UL1741, the relevant standard for this type of equipment,” Sherwood said. Also be sure to pick a combiner box that meets the technical requirements for your project.
A new trend is the incorporation of a whip: a length of wire with a solar connector on the end. “Rather than a contractor drilling holes in the combiner box and installing fittings in the field, we install whips at the factory that allow the installer to simply connect the output conductors to the box using a mating solar connector,” Sherwood explained. “It’s as easy as plugging in a toaster.”
This year arc-fault protection and remote rapid shutdown devices are more popular than ever, due to recent changes in the National Electrical Code that require them in many solar applications. “New technologies and components are driven by the NEC changes, as well as the desire for enhanced energy efficiency and reduction of labor costs,” Kane said. Some of these new components include: higher voltage components, integral mounting hardware and custom grounding options.
A photovoltaic power plant is a photovoltaic power generation system that uses the sun's light energy and electronic components such as crystalline silicon panels and inverters to generate electricity that is connected to the power grid and delivers power to the grid.
The PV power generation system consists of solar arrays, battery packs, charge/discharge controllers, inverters, AC power distribution cabinets, solar tracking control systems, and other equipment. The PV power generation system usually consists of PV modules, inverters, PV distribution boxes, meters, and power grids, and the distribution boxes, although the surge protective device is not accounting for a high percentage of the total system cost, but play an important role in the PV power generation system.
solar system
Photovoltaic Applications
Solar energy is an inexhaustible source of renewable energy, which is sufficiently clean, absolutely safe, relatively widespread, really long-lived and maintenance-free, resource-sufficient and potentially economical, etc., and plays an important role in long-term energy strategies. Photovoltaic power plants are currently among the most strongly encouraged green power development energy projects. The use of limited resources to achieve the maximum amount of energy for human use.
Power Distribution Boxes in Photovoltaic Power Plants
Photovoltaic power generation is developing rapidly in China, and the application of photovoltaic in all aspects of life has been reflected. Household photovoltaic power stations, large photovoltaic ground power stations, photovoltaic buildings, photovoltaic street lights, photovoltaic traffic lights, photovoltaic caravans, photovoltaic electric vehicles, photovoltaic carports, and more and more electricity-using environments have a photovoltaic figure, in which the photovoltaic box plays a vital role in the entire photovoltaic system, the main functions of which are as follows:
Combiner box
1. Power isolation function
Switchboards require a physical isolation device that allows the circuit to have a sharp break-point for the safety of personnel in service and maintenance situations. This device is called an isolation switch, which could ensure safety while the electricity has a short circuit, and the current increases and cause the cut off of the isolation switch.
2、Short circuit protection function
Once a short-circuit occurs in a circuit, it will cause a sudden increase in current, which will burn out the appliance and generate a lot of heat, making it susceptible to fires, with serious consequences. Therefore, when a short circuit occurs, a device is needed to cut off the power. The air switch is the device, which occupies an important role in the PV box. When you choose the air switch, please try to use reliable products and choose reliable manufacturers to ensure safety.
3、Energy measurement
Generally, PV energy meters are installed together with the DC surge protective device. There are also some places where the meter is separate from the distribution box. You can choose according to the local power supply department.
4、Over-voltage protection
The majority of distributed PV power generation is connected to the rural power grid. One of the characteristics of rural grids is that they are unstable, it is common that the power outages usually, and the voltage fluctuates greatly. In this case, the PV distribution box has a device indispensable, that is, an under-voltage protector. In the case of over-or under-voltage, it acts as a circuit breaker to protect other components. Under-voltage protection in the entire photovoltaic box, is more prone to failure of accessories, even if maintenance and replacement are required.
5、Lightning protection
Lightning is also a common natural phenomenon in life, especially in the summer, the thunderstorms are frequent happened and many accidents happened to people, Lightning is a scary thing in life, and there are lightning protectors in many places. There is also an important lightning protection device in the distribution box - the surge protector. A surge protector, also called a lightning protector, is an electronic device that provides safety protection for different electronic equipment, instruments, and communication lines. When the electrical circuit or communication lines because of external interference in the sudden generation of current or voltage, the surge protector can be turned on in a very short period of time to shunt, thereby reducing the circuit damage to other equipment, is an indispensable component.
6、About the cabinet
Generally speaking, the design service life of photovoltaic power generation is 25 years, so the distribution box should be used for 25 years, requiring a waterproof and dust-proof function. With the development of society and the progress of the times, the original distribution box made of cheap tin was not up to the requirements. Now the power supply bureau generally requires to use the of galvanized plate spray plastic, iron plate spray plastic, stainless steel, plastic steel, and other materials of the distribution box. Otherwise, you will forbid to the parallel network, in order for your safety, choose the appropriate box is very important.
|
|
|
Operator Essentials |
Posted by: ppfd15151s - 09-23-2021, 02:53 AM - Forum: Welcomes and Introductions
- No Replies
|
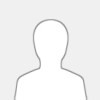 |
You’ve heard the term before; tactical backpack. It’s hard to avoid, in fact. It’s impossible to deny that “tactical” packs are a trend that isn’t going away any time soon in the carry world. In fact, at this point it may not even be a trend, but one of the pillar groups. How did this happen? Well, as long as there has been military, there have been people who want to use the gear for their civilian lives (the common day tshirt is a perfect example of gear popularized by military design and use). And just to be clear, civilians using military gear is awesome. As long as you’re not going around claiming you’re a soldier when you’re not. That’s not cool. Otherwise, feel free to enjoy the benefits of these awesome packs and gear. In one way or another, you’ve already paid for them via taxes!
People are drawn to this rugged gear for good reason too. Packs, clothing, and kit that is designed specifically for armed forces are all meant to go to war. Literally. They’re focused on strength, durability, modularity, high activity, and premium quality materials/hardware. Fashion is not even considered. It’s all pure function here. That being said, some may think tactical packs are a bit loud/attention grabbing, so they’ll want something a bit more subdued. Everyone has their own preferences, which we dig.
Long story short, in this particular case the term “tactical” is essentially another word for “military” or “military inspired”.
As the title states, this is a breakdown of tactical thigh bag for beginners. An introduction. So let’s dig in and explore what makes one functional tactical pack great versus a cheap knock-off for fashion’s sake.
We’re material geeks over here. And generally military tactical packs all should be made from quality fabrics that can take a beating. As a general rule of thumb, they should be made from 500D – 1200D CORDURA nylon fabric (or better). Not 200D. Not Kodra. Not polyester. This is an easy one. Some packs may even use nicer materials, such as X-Pac (VX) fabric. Usually these fabrics are heavier (not always), but they’re weather resistant and take a fall down a mountain or twenty.
Zippers/Hardware:
Look for brand names listed in the pack’s specifications. Brands to look for are YKK, TiZip, ITW Nexus, AustriAlpin, and more. If you haven’t heard of the brand (or if it’s intentionally left off), it probably doesn’t have a reputation of having a great track record. These parts can make or break (literally) a pack, so you’ll want something you can trust. If you’re deep in the wilderness and a buckle that keeps your shoulder straps attached busts on you, you’re out of luck.
Whether you’re looking for a bag for day hiking or an everyday go-everywhere pack, the right tactical backpack offers a perfect combination of ample storage, practical features, and all-day comfort.
It’s simple. If you’re going to be spending a lot of time wearing a backpack, choose a reliable one. Unlike many other backpack categories, tactical backpacks offer lots of utility for a wide variety of activities including long hikes, military deployment, traveling, and cycling.
Good tactical backpacks have numerous pockets, compartments, and clever features. Features to look for include external ports for nozzles and headphones, hydration bladder compatibility, two-way radio holders, compartments for medical supplies, and more. Furthermore, all-weather capability and durable materials define the characteristics of high-quality tactical backpacks.
For both professional and recreational applications, tactical vest offer carefully structured layouts that carry comfortably and keep gear secure, even when packed with heavy loads.
We’ve examined and reviewed options from across the tactical backpack market and determined which packs rank among the best in 2021.
Scroll through our list to view our picks, or jump ahead to the specific category that you’re interested in.
This 27L pack from Mystery Ranch is one of the most versatile tactical packs on the market in 2021. Thanks to its lightweight profile and compact size, the 2-Day Assault Pack ($200) is the perfect choice for a weekend of camping when you don’t want to lug around a full-size backpacking pack.
Firstly, it’s both comfortable and secure on your back, thanks to removable hip straps and shoulder straps. And second, at just 3 pounds, it won’t weigh you down while hiking.
For professional and urban use, an integrated and padded laptop sleeve and robust YKK zippers add impressive multiuse utility. For water storage, the 2-Day Assault Pack is compatible with water bladders. Each pack also includes dual water bottle holders.
We love that this pack is made from hardy material. Its premium 500-denier Cordura fabric is field-tested and built to last.
For quick overnight adventures or practical everyday use, the 2-Day Assault Pack from Mystery Ranch offers great features and overall value at $200.
A backpack is a bag for holding things. It’s hard to make that tactical, since one bag is very like another. When discussing turning a piece luggage into a lean, combat-equipped fighter, the first question that must be answered is: How? It’s a simple matter to put a few MOLLE straps onto a rucksack and call it battle-ready, but that does not fit the bill. True tactical packs are build with missions in mind, giving operators a lot of customization of the inside depending on if they’re doing recon, hunter/killer missions, sabotage, or simply going on a day hike. Real tactical suits also step up the durability to the point that they’re nigh indestructible, and are replete with hidden stash spots for secreting away a weapon, a jump drive with the Death Star plans, or a message to the wetwork pro who will find your body.
Finding the level of flexibility and resiliency that a tac-op bag should have can take a lot of digging, and if you’re serious about needing it, your life could be put in jeopardy should you pick a pretender. Don’t gamble with your blood, sweat, and more blood. Take one of the 16 top tactical backpacks and get to work.
If your spouse just brought one of these home, get ready for them to leave you, because this is a serious bag for serious people who are seriously never coming back. Though you can go bigger than the 2,100 cubic centimeters, it’s the webbing and handles atop, around, down, and under this bag that make it clear it’s just the base. The triple straps are the tale here, giving adjustable relief that makes this bearable for hours of trail wear.
Though not as traditionally “tactical” as the other options here, the Recon is a smart backpack in that it uses tactical elements to create a good day pack that is cost efficient and doesn’t have the miles of MOLLE or extra features that average tac-pack users don’t actually need. If you aren’t headed for a survival mission but would like some 210 Denier Cordura in a slick, sleek, go to the end of the world bag that’s dressed down and modern, here’s how to do it up right.
7 compartments intended to carry every survival item you require for living out of this for 3 solid days, this is the bug out bag serious survivalists suggest. More than 3,000 cubic inches of space inside outfitted with sleeves for hydration bladders, D-rings for expansion and extension packs, and it has a deep foam back panel for both support and ventilation that guards against sweaty-back syndrome. Ooh-Rah or bust.
Going in an asymmetrical direction, the Javelin looks a little awkward at first, but the design is intended to land at your body’s natural load-bearing points for an even distribution across your entire back to prevent walking cock-eyed. Built with 1000 Denier cordura and neoprene handles, the large number of small compartments makes this a good field bag for medical, electrical, demolition, or photography work. Top or side access gives it a convertibility that’s welcome in a tactical bag.
We can’t force Snugpak to change their name, but it’s on our To Do list. In spite of the cutesy label, this is a serious sack for people with serious sack. It’s only 1,400 grams, having been made for rangers who must move quickly across varied terrain. Unlike most tactical backpacks, this is made for keeping your survival essentials only, which is why it has a huge central compartment, but few pockets for organization. The huge range of MOLLE straps all over this bag are where you do your organizing.
Though not traditionally a backpack, the Plan-B’s cross-body build allows for quick access from the left or right, which adds field facility, even if it breaks from the mold a bit. 1080 cubic inches worth of gear storage, webbing from tip to tail, and an integrated system that can work with your favorite water bag, this can make a traditionalist into a sling-bag convert.
You’ll never go wrong carrying a Maxpedition, so it’s buyer’s pick. We prefer the Falcon-II because it uses a Y-shaped compression strap in the middle, unique to its design. Using that seems to distribute weight more evenly, keeps parcels in place during serious action, such as taking a tumble down a ravine slope, and makes the carrying feel incredible. That’s to say nothing of the side-buckles, dual-open zippers for clamshell storage and easy access, as well as the 1050 Denier build. Whew, it’s a piece of work.
Weight concerns brought the Dragon Egg from it’s original design, which called for 1000 Denier Cordura was downgraded to 500-D, because this bag needed to be light as gossamer to achieve its goal. The balance of the 500-D means a tad less rip resistance – though you’ll be hard-pressed to notice it – but far less weight than many similar bags. This mixture creates a capacity of 1,500 cubic inches that can be carried by smaller soldiers comfortably.
You’ll never stray far from quality with 5.11’s tactical belt. Though their Rush line gets more attention, the more basic All Hazards Prime has a straighter build. Constructed using input from MACTAC (Multi-Assault Counter-Terrorism Action Capabilities) instructors, the layout is made specifically to give you access to all your gear, and keep it precisely where you expect it to be. Should you drop something, hi-vis orange lining makes it pop out, day or night.
|
|
|
Building efficiency begins with lighting design and controls in step with the space |
Posted by: ppfd15151s - 09-23-2021, 02:51 AM - Forum: Welcomes and Introductions
- No Replies
|
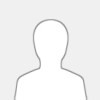 |
At the surface level, lighting is the application of light to spaces and simply serves as a prerequisite for visualization. However, because our impression of a space happens via sight, commercial lighting not only becomes a necessity for vision but a medium for perception. This means the type of lighting fixtures selected, in what location they are installed, and at what light levels they are set can drastically impact people’s perception of a building and the work being done within it.
At this point in LED technology development, there is no shortage of literature on the many benefits of LED highbay light. Objectives of LED lighting increasing comfort in spaces, boosting morale, and reducing energy waste have been well documented and the evidence in favor of LED solutions over outdated fixture types is overwhelming. With the maturity of the LED market and reduction in product costs that aid in generating competitive return on investment (ROI), there is no argument against the investment. However, a successful LED lighting project lies at the intersection of design, product selection, and the fundamental client necessity for light in a space. The lighting designer/specifier or installer needs to clearly align the objectives and the value of each criterion considered for the space in collaboration with the facilities manager or building owner.
Designing solutions to fit the space
At the core of every lighting project is the solutions design. True to the title, LED panel light design is the process of delivering the necessary lighting to an area, but to better expatiate on the importance of the job, it is important to differentiate between the commodity of “light” versus the asset of “lighting.” Lighting is an investment that can be very advantageous to an organization and should be carefully considered. Every project starts with a conversation about necessity.
In order for the lighting to best support the client’s goals, project managers and designers need to know the organization, who will be using the space and their lighting needs, characteristics of the building, importance of energy efficiency and budget, restrictions based on geographical location, and much more. Based on what the owner wants to communicate through lighting, decisions on quantity of light, color quality, brightness, and direction can be determined.
The importance of an open dialogue between a building owner and the project manager cannot be stressed enough. Lighting designs cater to the building and work being done which in turn leads every project to a custom solution in terms of size, style, and programmatic requirements. In addition to discussion, it is beneficial for a facility to take advantage of audits in which experts can determine the heavier traffic areas of the building and select the fixture types that would be most advantageous. With proper identification of LED opportunities for retrofits and thoughtful coordination of the building systems, solutions can be designed with consideration to specific needs.
For example, spaces without access to natural sunlight, such as warehouses and mechanical shops, may place importance on implementing LEDs with color temperatures that mimic daylight and allow for circadian stimulus. Advantages like this — which can only be gained through the creation of custom LED design — are leveraged to create an environment that is more sustainable, flexible, and enhances the experience of inhabitants while still meeting safety and visibility requirements.
Product specification
Design works in concurrence with product selection, or specification. While considering the more human-centric aspects of lighting needs, it is also critical to assess the quality of the product, longevity, and controllability. Is there a chance the space may change over time? If so, how will the lighting demonstrate flexibility and ability to augment? To reiterate, deploying LED solutions is an investment, so it is important that the lighting fixtures both fit the logistical needs of the building and abide despite future changes. Incorporating these considerations into a lighting design will not hinder finding the perfect fit, either. Due to the advancement in LED technology, clients are able to select from a wide variety of LED products, but must make sure to prioritize the appropriate light levels for their building.
Ample lighting in an office space, for example, keeps employees alert and the higher visibility allows them to yield accurate results. If the space is underlit, it may have adverse effects on productivity, health, motivation, and even employee retention. Light levels that are too high prove to be just as bad and consume unnecessary energy. Successful lighting design and product selection takes efficiency into account to best make a building sustainable while maintaining an attractive ROI. This can be done by investing in LED light fixtures with higher lumens per watt that provide sufficient light while consuming less energy. For the slightly higher initial cost of efficient LED lighting, organizations can save significantly in the long run through decreased maintenance costs, lower utility bills, and utility incentive programs intended to help offset the initial installation cost of such solutions.
As established, lighting plays a critical role in how a space is perceived. However, lighting decisions can influence performance, mood, morale, safety, security, decisions, and actions as well. Lighting design and product selection allows for optimal lighting depending on the goal of the building and people within.
For example, fixtures with low color temperatures, which are considered warm and relaxing, may be specified for homes and restaurants where the goal is to feel at ease and there is generally no reason to be on high alert. The same fixtures would not be suitable for a commercial and industrial (C&I) environment since the effect from the lights would be counterproductive. Instead, the fixtures in C&I settings are often designed with high color temperatures that can increase awareness and energize. These spaces rely heavily on visibility in order to perform high-precision manufacturing tasks. LED flood light in spaces in which people are expected to concentrate for long periods of time, such as classrooms and offices, are typically designed to have a neutral color temperature so as not to be over- or under-stimulating.
When it comes to specifics like a warehouse facility or a laboratory, they differ quite a bit. There are many aspects of the two workspaces that contribute to the lighting choices. For example, the core differentiating features of a warehouse facility is overall building design, ceiling height, and loading capability. Warehouses are also the largest industrial real estate category, which sets it apart in terms of number of fixtures and light levels. To maximize space utilization, most warehouses employ rows of tall shelving, which results in narrow aisles that are challenging to light, with a "cavernous" effect. In designing a lighting solution, the top priority is visibility as it correlates to employee morale, productivity, and reduction in error, which in turn decreases cost.
While working with precision and delicate materials in a laboratory, visibility is paramount but for different tasks and in a completely different environment. Lighting for a laboratory would be designed to be extremely bright for the essential work as well as to contribute to the perception of cleanliness and making the space look sterile.
Even if two light sources have the same correlated color temperature, the color rendering index (CRI), which is used to describe how faithfully the light source renders the color of objects, may still differ. CRI is especially important when designing lighting for places such as grocery stores and other retail locations where the product appearance greatly influences the business. The same strong light in a retail store that favorably accentuates the merchandise and influences customers to purchase more may be fatiguing in an office space.
Controls are key to lighting success
Controls are paramount when discussing LED canopy light design and product selection. Lighting controls are integrated, programmable systems that allow fixtures to deliver the correct levels of light at the correct time to best maximize efficiency. They can practically be broken down into levels that allow options for managing lighting systems.
The first level can be described as relying on manual adjustment in which users can manage individual programmed occupancy sensors or non-programmable ceiling sensors. On this basic tier of controls, there is no ability to control lighting levels beyond a simple wall dimmer switch. Tier two allows for wireless integration directly from the fixture to a device. This level of controls can include sensors that have the capability to identify occupancy and vacancy of rooms and change levels based on select settings. In other words, unoccupied rooms will reduce light levels by a certain amount to conserve energy.
The second level of controls also allow for high-end trimming or output adjustment of lights. Since LED fixtures typically produce higher lumen output than the fixtures they replace, the fixture output can be raised to match the standard needs for the space. Along with this, the trim can account for the LED’s degradation over time and provide the originally desired light level. The low-end trim defines the lowest light level and ensures that the lights do not turn off when dimmed to the lowest capability. This is important for datacenter facilities, for example, as they contain rows of equipment that can obscure a person from motion sensor control. If the system goes into an unoccupied mode, the trim prevents all the lights from turning off and creating a safety hazard. The design may include that the trim be 10%, which would provide visibility even if the sensors are obscured and the lights are not at the optimal levels. Additionally, datacenters often control lighting by grouping fixtures and programming different sets based on various needs by using individual auxiliary sensors. This allows for control concurrency and can be regrouped depending on the layout of the space.
The highest level of controls includes all the benefits mentioned previously in the second level, with the added benefit of being integrated directly into the building management system. In other words, a building manager could potentially have its HVAC system respond in direct relation to the occupancy sensor used for the LED lighting system, which would provide much more granular control of the building’s total mechanical system. Depending on what is needed in the space, controls can be used as a powerful means to customize lighting further than initial product selection and installations.
|
|
|
The Importance of Good Makeup Brushes |
Posted by: ppfd15151s - 09-23-2021, 02:50 AM - Forum: Welcomes and Introductions
- No Replies
|
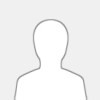 |
All products and services featured are independently chosen by editors. However, WWD may receive a commission on orders placed through its retail links, and the retailer may receive certain auditable data for accounting purposes.
An artist is only as good as their tools, and we’re not just talking about painters. The same rule applies in the realm of cosmetics: Your makeup can only be as good as your applicators, which is why you should upgrade your collection to include the best makeup brush sets — to ensure that your every beauty need is met.
Expertly curated makeup brush sets come stocked with high-quality options that cater to the face, cheeks, eyes, brows, and more, but if you’ve yet to master the art of contouring, defining, shading, highlighting, no worries; you don’t have to be a professional to operate this fine equipment. According to celebrity makeup artist and brow expert, Danielle Kimiko Vincent, founder of KIMIKO, everyone from beginner makeup moguls to celebrity artists can benefit from investing in a complete set.
“I love a good brush set because it can encourage you to start experimenting with new techniques that you might not have otherwise considered,” Vincent tells WWD over email. “For example, an angled eyeshadow brush can be used in many more ways than a standard flat brush. You might learn to create a color wash with the wide section of the brush, and then use the narrow side to create an accent with a darker color.”
It also helps that there’s “usually a price break,” when you opt to purchase an entire set versus individual brushes, Vincent adds. “Even if one of the brushes doesn’t become a favorite, you’ll likely make use of most of them, so the value is there.”
How To Shop for the Best Makeup Brush Sets
While makeup brush sets are an excellent investment, like anything else, not all sets are created equally. Ergo, when shopping for the best Makeup Brush Set, there are some key details to consider.
Synthetic vs. Natural Hair
In an exclusive interview with WWD, global makeup artist for Jane Iredale, Nechelle Turner explains that bristles on silicone mask brush are either natural (sourced from animals like squirrels, goats, and ponies) or synthetically made from nylon, polyester, or other synthetic fibers. Natural hair brushes, Turner says, have cuticles, making them porous, therefore, they attract and keep the product in the brush, which ultimately results in a more sheer application. “Their porous nature can also make them a breeding ground for bacteria,” Turner says, adding that natural hair brushes also tend to be a higher price point and their longevity is questionable.
Synthetic brushes feel more like natural hair brushes and are nonporous, therefore they “pick up and distribute more product on the skin for a more defined and more precise application,” Turner tells WWD. That being said, because synthetic brushes pick up and distribute more product, Turner advises using a lighter hand. It’s also worth noting that synthetic brushes that are stiff or have a shiny coating can result in a streaky makeup application, so you want to look for fluffy, softer bristles.
“In either case look for shedding,” Turner warns. “Shedding or lack of shedding bristles is a good indication of the quality of the fibers in both cases.”
Brush Count
Be realistic about how many brushes you need and how many brushes you’ll actually use. “If you’re advanced and like to try new techniques and looks, then a larger set with a wide range of variety will suit you best,” Vincent tells WWD. “If you’re relatively simple with your makeup, then an edited set will be great for you.”
Vincent tells WWD that as far as length goes, for a personal makeup bag, medium or shorter handles work well overall, but for a professional makeup artist, longer handles are ideal for powder and blush application. “This allows me to view my client from slightly further back, giving me a fuller picture of what I’m creating,” she says.
As for handle material, there are two options: wooden or plastic. “This may not be important for everyone,” Vincent prefaces, “but specifically for natural brushes, I prefer a beautiful wooden handle and brush hairs that have been hand cut and tied. This usually means high attention to detail has been taken with the taper and placement of the brush hairs, which I find translates to a more refined lay-down of powdered products.”
With sets geared towards beginners, pros, and every mastery level in between, the best makeup brush sets accommodate a wide range of beauty abilities with their basic, essential, and expert brush pairings. Below, find the best makeup brush sets that will satisfy every beauty buff’s skillset and budget.
1. BS-Mall Premium 14-Piece Brush Set
The BS-Mall Premium 14-piece brush set is one of the best makeup brush sets on amazon. With over 79,000 reviews (the majority of which are 5-star) to date, customers rave BS-Mall synthetic hair brushes are “soft,” “high quality,” and “comparable to high end brushes.” The 14-pc collection includes nine precise beard brush for shaving, as well as five chunky kabuki brushes for blush, bronzer, foundation, and other face product application. A travel case is also included with every purchase for easy storage.
One of the best affordable makeup brush sets on the market, EcoTools brushes are also (as its name would suggest) eco-friendly. Each tool is constructed from 100% recycled, vegan-friendly, cruelty-free materials and the collection comes packaged in tree-free paper made from cotton and bamboo fibers. The Day Beautifully Brush Set consists of the brands core collection of five brushes (including an angled foundation brush, blurring brush, defining crease brush, angled liner brush, and full blush brush), as well as three how-to beauty look cards to help simplify your routine.
Vincent tells WWD her brand’s essential brush collection is particularly excellent for “stepping up your brush game while keeping your makeup bag curated.” Each brush included in the set is hand cut, constructed with cruelty-free materials, and is designed to be multifunctional, ensuring you can create more looks with limited tools: “Three of the four brushes are dual-ended (with caps), so you’re actually getting seven brushes; a do-it-all brush for face, two essentials for eyes, a synthetic concealer and lip brush, and a brow and lash brush.”
Bridal and celebrity makeup artist, Cara Lovello tells WWD this set from EIGSHOW is one of the best makeup brush sets for beginners available on Amazon. “The brushes are affordable and good quality,” Lovello says, adding, “they don’t shed or fall apart.” The brand’s 15-piece Jade Series kit includes all the tools needed to create precise, flawless looks, from a foundation brush to various eye makeup tools. The brushes are made with vegan-friendly bristles sourced from corn silk fibers and birch wood handles, and come packaged (and separated) in a cosmetic bag made from recycled clothing and linen fibers.
The Tarte Cosmetics Goal Getters Contour Brush Set features five complexion brushes the brand guarantees will “sculpt, strobe, and perfect” your complexion. Inside, you’ll find the Bronzer Brush, Contour Brush, Foundation Brush, Concealer Brush and the Highlighter Brush, all decked out in rose gold sequins and topped with baby pink bristles. Reviewers give the set just shy of a 5-star rating, and love the set for its quality, as well as its overall aesthetic.
A number-one bestseller on Amazon, the Bestope Makeup Brush Set is stocked with 16 brushes that cater to the face, lips and eyes. Available in five colors and featuring soft and dense synthetic fiber-made brushes, this versatile set ensures that you have everything you need to contour, highlight, blend and shade.
Perfect for beginners, the Real Techniques Everyday Essentials makeup brush set covers all of the basics with its pro-curated pairings. Featuring brushes for the face, cheeks and eyes, the set includes the brand’s RT 400 Blush, RT 300 Deluxe Crease, RT 402 Setting and RT 200 Expert Face brushes, plus the Miracle Complexion Sponge.
Created with the eyes in mind, the Sigma Beauty Basic Eye Brush Set features seven brushes designed for eyeliner, eyeshadow and brows. Made with the brand’s exclusive synthetic antimicrobial fibers, securing them as one of the best vegan makeup brush sets on the market, these quality brushes are engineered to better hold, apply and blend products. The set includes the E40 Tapered Blending Brush, the E55 Eye Shading Brush, the E60 Large Shader Brush, the E70 Medium Angled Shading Brush, the E30 Pencil Brush, the E65 Small Angle Brush and the E05 Liner Brush.
Renowned for their exceptional blending, innovative Cosmefibre technology and ergonomic construction, the Artis Elite Makeup Brush Set is easily one of the best professional makeup brush sets available. It features the brand’s best-selling brushes for seamless, expert-level application. Inside, you’ll find the Oval 10, Oval 8, Oval 6, Oval 4, Oval 3, Linear 6, Linear 3, Linear 1, Circle 1 and Circle 1R brushes.
Jenny Patinkin’s Luxury Six-Piece Vegan Cosmetic Brush Set includes a curated collection of multipurpose, multiuse makeup brushes that can be used with cream, liquid gel and powder products. According to the brand, the brushes features synthetic fibers that are finer than natural hair alternatives and packed with 2.5 times more bristles than conventional brushes for a soft feel and seamless application. The set also comes with a stylish vegan croc-embossed case for travel.
A travel-sized makeup brush collection that is available in five colorways, the Spectrum Collections Jet Setter set ensures that you’ve got all of your makeup tools in one convenient place. The eight-piece kit includes the B01 Buffing Foundation Brush, the C03 Tulip Power Brush, the A05 Angled Blush Brush, the B08 Magic Wand Powder Brush, the B06 Tapered Blender Brush, the B04 Angled Shader Brush, the A16 Precision Crease Brush and A24 Double Ended Brow Styler Brush.
If you’re new to the makeup scene or you’re not a regular makeup user, you need to understand the importance of quality makeup brushes. A lot of makeup newbies and amateurs do not realize the importance of quality tools and brushes, and this should not be so. Most of them do not even know which tools and brushes to buy, and this article will help them through a number of issues, including identifying the right tools to buy, and the importance of these tools.
Many people need makeup for a number of reasons, and no matter your reason for using makeup, you need the right tools, and you need tools of the best quality. When starting out, you need original and high-quality brushes, including (the basics) a liquid foundation brush, a powder brush, a concealer brush, a number of eyeshadow brushes, false eyelashes some lip brushes, eyeshadow brushes, and a buffing brush.
Why are quality brushes actually important? Why are they better than cheap brushes? A lot of people ask these questions, and there are many reasons why quality brushes are important. These reasons include:
Quality brushes are better for your skin: Your skin deserves the best, and quality brushes will give your skin the very best. Quality brushes should feel soft and gentle against your skin. If a brush feels rough and scratchy, then it is of low quality and should not be used on your skin. If it’s also a brush with bristles that fall out all the time, it is not of good quality. When you use these low-quality brushes, it will lead to skin irritation and visibly faster aging.
Buying quality brushes saves you money: While it might seem expensive at first, making the decision to buy quality brushes will actually save you money in the long run. If you decide to buy cheap brushes of low quality, you will have to keep replacing them, and this will cost you a lot more money than if you had just gotten the slightly more expensive ones at first. Also, quality brushes have the ability to last for years.
Your makeup turns out better when you use quality brushes: Quality brushes improve the final look of your makeup. They make application and blending easier, and you end up having a smoother, well-done, and more attractive look. If, for instance, you use bad eyeshadow brushes, your eyeshadow will come out looking tacky and totally unattractive. Once you make use of quality brushes, however, your eyeshadow will look as great as possible.
Even though it is expensive, you have to invest in great brushes. You get to save money, quality brushes have longevity, quality brushes are good for our skin, and they’re better for your makeup in general. For these reasons, you need to make the decision to get quality brushes today.
|
|
|
28 Types of Fabrics and Their Uses |
Posted by: ppfd15151s - 09-23-2021, 02:47 AM - Forum: Welcomes and Introductions
- No Replies
|
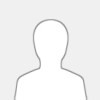 |
Deciding which type of fabric to make an item with is an important decision, as fabrics can have countless qualities. From natural to synthetic fibers and from knit to woven, here’s a look at different fabric types and how to identify them.
Canvas. Canvas is a plain-weave fabric typically made out of heavy cotton yarn and, to a lesser extent, linen yarn. Canvas fabric is known for being durable, sturdy, and heavy duty. By blending cotton with synthetic fibers, canvas can become water resistant or even waterproof, making it a great outdoor fabric.
Cashmere. Cashmere is a type of wool fabric that is made from cashmere goats and pashmina goats. Cashmere is a natural fiber known for its extremely soft feel and great insulation. The fibers are very fine and delicate, feeling almost like a silk oxford fabric to the touch. Cashmere is significantly warmer and lighter than sheep’s wool. Often cashmere is made into a wool blend and mixed with other types of wool, like merino, to give it added weight, since cashmere fibers are very fine and thin.
Chenille. Chenille is the name for both the type of yarn and the recycled fabric that makes the soft material. The threads are purposefully piled when creating the yarn, which resembles the fuzzy exterior of the caterpillar. Chenille is also a woven fabric that can be made from a variety of different fibers, including cotton, silk, wool, and rayon.
Chiffon. Chiffon a lightweight, plain-woven fabric with a slight shine. Chiffon has small puckers that make the fabric a little rough to the touch. These puckers are created through the use of s-twist and z-twist crepe yarns, which are twisted counter-clockwise and clockwise respectively. Crepe yarns are also twisted much tighter than standard yarns. The yarns are then woven in a plain weave, which means a single weft thread alternates over and under a single warp thread. The sheer fabric can be woven from a variety of textile types, both synthetic and natural, like silk, nylon, rayon, or polyester.
Cotton. Cotton is a staple fiber, which means it is composed of different, varying lengths of fibers. Cotton is made from the natural fibers of cotton plants. Cotton is primarily composed of cellulose, an insoluble organic compound crucial to plant structure, and is a soft and fluffy material. The term cotton refers to the part of the cotton plant that grows in the boil, the encasing for the fluffy cotton fibers. Cotton is spun into yarn that is then woven to create a soft, durable fabric used for everyday garments, like t-shirts, and home items, such as bed sheets. Cotton prints and cotton solids are both available designs.
Crêpe. Crêpe is a silk, wool, or synthetic fabric with a distinctive wrinkled and bumpy appearance. Crêpe is usually a light-to- medium-weight fabric. Crêpe fabric can be used to make clothes, like dresses, suits, blouses, pants, and more. Crêpe is also popular in home decor for items like curtains, window treatments, and pillows.
Damask. Damask is a reversible, jacquard-patterned fabric, meaning that the pattern is woven into the polyester taffeta fabric, instead of printed on it. The fabric’s design is created through the weave, which is a combination of two different weaving techniques—the design is woven using a satin weave, while the background is achieved through a plain, twill, or sateen weave. Damask patterns can be either multi-colored or single colored. Damasks can be made from a variety of different textiles, including silk, linen, cotton, wool, or synthetic fibers, like rayon. Learn more about damask fabric here.
Georgette. Georgette is a type of crêpe fabric that is typically made from pure silk but can also be made from synthetic fibers like rayon, viscose, and polyester. Crêpe georgette is woven using tightly twisted yarns, which create a slight crinkle effect on the surface Georgette is sheer and lightweight and has a dull, matte finish.. Silk georgette is very similar to silk chiffon, which is also a type of crêpe fabric, but georgette is not as sheer as chiffon because of the tighter weave. Georgette fabrics are sometimes sold in solid colors but often georgette is printed and boasts colorful, floral prints.
Gingham. Gingham is a cotton fabric, or sometimes a cotton blend fabric, made with dyed yarn woven using a plain weave to form a checked pattern. Gingham is usually a two-color pattern, and popular combinations are red and white gingham or blue and white gingham. The checked pattern can come in a variety of sizes. Gingham pattern is reversible and appears the same on both sides. Gingham is a popular fabric due to its low cost and ease of production. Gingham is used frequently for button-down shirts, dresses, and tablecloths.
Jersey. Jersey is a soft stretchy, knit fabric that was originally made from wool. Today, jersey is also made from cotton, cotton blends, and synthetic fibers. The right side of jersey knit fabric is smooth with a slight single rib knit, while the backside of jersey is piled with loops. The fabric is usually light-to-medium weight and is used for a variety of clothing and household items, like sweatshirts or bed sheets.
Lace. Lace is a delicate fabric made from yarn or thread, characterised by open-weave designs and patterns created through a variety of different methods. Lace fabric was originally made from silk and linen, but today cotton thread and synthetic fibers are both used. Lace is a decorative fabric used to accent and embellish clothing and home decor items. Lace is traditionally considered a luxury textile, as it takes a lot of time and expertise to make.
Leather. Leather is any fabric that is made from animal hides or skins, and different leathers result from different types of animals and different treatment techniques. While cowhide is the most popular animal skin used for leather, comprising about 65 percent of all leather produced, almost any animal can be made into leather, from crocodiles to pigs to stingrays. Leather is a durable, wrinkle-resistant fabric, and it can take on many different looks and feels based on the type of animal, grade, and treatment.
Linen. Linen is an extremely strong, lightweight fabric made from the flax plant. Linen is a common material used for towels, tablecloths, napkins, and bedsheets, and the term “linens,” i.e. bed linens, still refers to these household items, though they are not always made out of linen fabric. The material is also used for the inner layer of jackets, hence the name “lining.” It’s an incredibly absorbent and breathable fabric, which makes it ideal for summer clothing, as the lightweight qualities allow air to pass through and moderate the body temperature.
Merino Wool. Merino wool is a type of wool gathered from the coats of Merino sheep. T While traditional wool is notorious for being itchy, merino wool is one of the softest forms of wool and doesn’t aggravate the skin. This is because of the small diameter of the fine merino fibers, which makes it more flexible and pliable and therefore less itchy. Merino wool is considered a luxurious fiber and is used frequently for socks and outdoor clothing. Merino wool is known for being odor-resistant, moisture-wicking, and breathable.
Modal. Modal fabric is a semi-synthetic fabric made from beech tree pulp that is used primarily for clothing, such as underwear and pajamas, and household items, like bed sheets and towels. Modal is a form of rayon, another plant-based textile, though it is slightly more durable and flexible than rayon. Modal is often blended with other fibers like cotton and spandex for added strength. Modal is considered a luxurious textile thanks to both its soft feel and high cost, as it is more expensive than either cotton or viscose. Learn more about modal fabric in our complete guide here.
Muslin. Muslin is a loosely-woven cotton fabric. It’s made using the plain weave technique, which means that a single weft yarn alternates over and under a single warp yarn. Muslin is known as the material used in fashion prototypes to test patterns before cutting and stitching the final product. Muslin is ideal for testing patterns, as its lightweight and gauzy, therefore it can mimic drape and fit well and is simple to sew with.
Organza. Organza is a lightweight, sheer, plain-woven fabric that was originally made from silk. The material can also be made from synthetic fibers, primarily polyester and nylon. Synthetic fabrics are slightly more durable, but the fabric is very delicate and prone to frays and tears. Organza is also characterized by very small holes throughout the home textile fabric, which are the spaces between the warp and weft thread in the plain-weave pattern. The quality of organza is defined as the number of holes per inch—more holes indicate better quality organza. Organza is extremely popular for wedding gowns and evening wear, as it is shimmery and translucent quality which creates decadent silhouettes.
Polyester. Polyester is a man-made synthetic fiber created from petrochemicals, like coal and petroleum. Polyester fabric is characterized by its durable nature; however it is not breathable and doesn’t absorb liquids, like sweat, well. Polyester blends are also very popular as the durable fiber can add strength to another fabric, while the other fabric makes polyester more breathable.
Satin. Satin is one of the three major textile weaves, along plain weave and twill. The satin weave creates an elastic, shiny, soft fabric with a beautiful drape. Satin fabric is characterized by a soft, lustrous surface on one side, with a duller surface on the other side. This is a result of the satin weaving technique, and there are many variations on what defines a satin weave.
Silk. Silk is a natural fiber produced by the silk worm, an insect, as a material for their nests and cocoons. Silk is known for its shine and softness as a material. It is an incredibly durable and strong material with a beautiful drape and sheen. Silk is used for formal attire, accessories, bedding, upholstery, and more.
Spandex. Also known as Lycra or elastane, Spandex is a synthetic fiber characterized by its extreme elasticity. Spandex is blended with several types of fibers to add stretch and is used for everything from jeans to athleisure to hosiery.
Suede. Suede is a type of leather made from the underside of the animal skin, giving it a soft surface. Suede is usually made from lambskin, but it is also made from other types of animals, including goats, pigs, calves, and deer. Suede is softer thinner, and not as strong as full-grain, traditional leather. However, suede is very durable, and due to its thin nature, it’s pliable and can be molded and crafted easily. Suede is used for footwear, jackets, and accessories, like belts and bags.
Taffeta. Taffeta is a crisp, plain-woven spandex fabric made most often from silk, but it can also be woven with polyester, nylon, acetate, or other synthetic fibers. Taffeta fabric typically has a lustrous, shiny appearance. Taffeta can vary in weight from light to medium and in levels of sheerness, depending on the type of fiber used and the tightness of the weave. Taffeta is a popular lining fabric, as the material is decorative and soft, and it is also used for evening wear and home decor.
Toile. Toile de Jouy, or simply toile, was a specific type of linen printed with romantic, pastoral patterns in a single color—usually black, blue, or red—on an unbleached fabric. Although the word toile means fabric in French, the word toile has evolved to also refer to the original design aesthetic of the fabric, which gained popularity in France in the 1700s. Toile designs are popular for non-fabric items like wallpaper and fine china. Toile fabric is used for clothing, upholstery, window treatments, and bedding.
Tweed. Tweed is a rough woven fabric usually made from wool. The fibers can be woven using a plain weave or twill weaves. It is an extremely warm, hard-wearing fabric that is thick and stiff. Wool tweed is often woven using different colored threads to achieve dynamic patterns and colors, frequently with small squares and vertical lines. Tweed is very popular for suiting and jackets, which were originally made out of the material for hunting activities.
Twill. Twill is one of the three major types of textile weaves, along with satin and plain weaves. The distinguishing characteristic of the twill weave is a diagonal rib pattern. Twill weaves have a distinct, often darker colored front side (called the wale) with a lighter back. Twill has high thread count, which means that the fabric is opaque, thick, and durable. Twill fabrics are rarely printed on, though multiple colored yarns can be used to achieve designs like tweed and houndstooth. The fabric is durable with a beautiful drape, and it is used for denim, chinos, upholstery, and bed linens.
Velvet. Velvet is a soft, luxurious fabric that is characterized by a dense pile of evenly cut fibers that have a smooth nap. Velvet has a beautiful drape and a unique soft and shiny appearance due to the characteristics of the short pile fibers. Velvet fabric is popular for evening wear and dresses for special occasions, as the polyester oxford fabric was initially made from silk. Cotton, linen, wool, mohair, and synthetic fibers can also be used to make velvet, making velvet less expensive and incorporated into daily-wear clothes. Velvet is also a fixture of home decor, where it’s used as upholstery fabric, curtains, pillows, and more.
Viscose. Viscose is a semi-synthetic type of rayon fabric made from wood pulp that is used as a silk substitute, as it has a similar drape and smooth feel to the luxury material. It is a silk-like fabric and is appealing because it is much cheaper to produce. Viscose is a versatile fabric used for clothing items such as blouses, dresses, and jackets, and around the home in carpets and upholstery.
|
|
|
8 Benefits of Spin Class That’ll Convince You to Finally Try One |
Posted by: R234V - 09-22-2021, 05:23 AM - Forum: Welcomes and Introductions
- No Replies
|
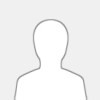 |
8 Benefits of Spin Class That’ll Convince You to Finally Try One
8 Benefits of Spin Class That’ll Convince You to Finally Try One
One of the many reasons we love cycling is that it allows us to get outside and explore. But with winter at our doorstep, sometimes the weather is just plain awful or there’s just not enough time in the day. The next best option? A Spin class, of course.
Most studios offer a variety of class options—some as short as 20 minutes or as long as 90 minutes—so you’re always able to fit a workout into your schedule. Nowadays, there are even at-home magnetic spinning bike available that stream classes directly into your living room from companies like Peloton, NordicTrack, and Technogym. Peloton’s beginner-friendly classes, for example, teach participants the correct form and technique that will translate to every other level.
Plus, the work you do in a class—whether that’s at home or in a gym—complements your on-the-road training perfectly, according to Peloton instructor Jess King. “It’s an opportunity for you to play around with your training—there’s something for you to hear, learn, and experience that you can take with you back on the road. So why not dip into both worlds?” she says.
Spinning is one of those things that seems a bit intimidating if you’ve never done it before. But as long as you have access to a gym or a bike, you can take classes that range from beginner to expert, King says, each of which helps build the main muscle groups used for cycling and your cardiovascular system.
“We have this unique opportunity to create something for everyone,” King says. But most studios and instructors offer a variety of options that will suit your needs or experience level.
And if you’ve already got the stamina to climb hills and ride long outside, you’re that much more ready to conquer a Spin class. Both studios and at-home options offer longer, more advanced classes as well.
This content is imported from {embed-name}. You may be able to find the same content in another format, or you may be able to find more information, at their web site.
It goes without saying that taking a Spin class is not the same as riding outside. While you can still experience similar terrain (hills and flat ground), King says in-studio and virtual Spin classes can feel more like a party than a workout.
“There’s music from all different decades—from classic rock to EDM—and we use interval training, tabata training, and heart rate training, so it’s still a great workout,” she says about Peloton, though competitors offer a similar experience.
A lot of times when you’re out on the road, it’s just you and the voice that’s in your head. That can be a good thing when you want to escape to nature and clear your mind, but it can be a bad thing when the voice is telling you to turn home. Being in a class setting changes things up—especially when you have the motivation of an instructor cheering you on. (Because let’s be real, there are times when you just really don’t want to do that interval workout on your own.)
“Spin gives you a new perspective on how to ride, breathe, and think about your body,” King says.
When you take an indoor cycling class, everyone from the instructor to the other participants are there to encourage and support you.
“Everyone is rooting for you—you’re not alone in this experience,” King says. “We’re using the bike as the medium for that connection and energy.”
And Charlee Atkins, C.S.C.S., former master instructor at SoulCycle and founder of Le Sweat, agrees. “[Everyone] is very supportive—they hold each other accountable and celebrate each other’s wins and losses,” she says. “They oftentimes can become an ‘extended family’ of sorts.”
It can be really tough to be out on your indoor cycle spinning bike alone, struggling to finish a particularly challenging ride. Sometimes your first instinct is to give up. But when there are other people around you, it makes you want to keep going and prove you can finish what you started. That’s exactly what taking a Spin class does. And that mindset can and will benefit you on the road, too.
If you’ve already found a great community of riders outdoors, indoor classes offer the same camaraderie and accountability, just in a different setting.
4. It’s a great total-body workout.
Not only does a Spin class benefit your muscles—everything from your legs to your core—but it’s also a great low-impact cardiovascular workout, which improves your blood flow, increases your stamina, boosts your mood, and prevents against chronic issues such as high blood pressure, heart disease, stroke, and diabetes, according to Mayo Clinic.
And because of this intense cardio workout, you’ll burn a ton of calories, too. While King says the average is about 400 to 600 calories per class, she’s seen some riders burn more if they’re going particularly hard and long.
Some indoor cycling classes even incorporate the use of hand weights to “promote upper-body work, since cycling is a predominantly lower-body workout,” Atkins adds. So in one 45-minute session, you can challenge your upper body, lower body, and core.
5. It’s convenient.
Riding outside can take a couple of hours to complete, and most people don’t have that kind of time during the week. So taking an indoor cycling class either at home, at a gym, or in a studio is a great option for when your schedule is packed, and you only have an hour or less to work out.
But don’t worry—exercising for a shorter amount of time doesn’t mean you aren’t reaping the same benefits as a longer workout. Many classes feature high-intensity intervals which help you build increased cardiovascular and muscular fitness in less time than a longer but steady-state ride out on the road.
6. It’s low impact.
Indoor cycling won’t beat up your joints like other forms of cardio such as running. “It’s great for people who are coming back from an injury,” says Atkins, because your hips, knees, and ankles won’t take all the impact. This makes it a great choice for those who aren’t yet functioning at 100 percent after getting hurt, older adults looking for a way to stay active without putting extra pressure on their joints, or those who suffer from arthritis.
7. You can make it your own.
Out on the roads, you can’t lower the grade of a mountain if you’re not up for climbing it that day. But the beauty of a Spin class is that you can customize it to your own needs. The Spin instructor is there to guide you, but you can always modify the workout.
For example, you don’t have to stay on the bike during the upper-body workout portion of the class if you feel safer on solid ground. You can also go slower if you need to—you don’t have to worry about getting dropped. And if the class motivates you to push yourself even harder, maybe try racing your friend next to you. Everyone in class is there to work out to the best of their ability while enjoying the motivational vibes of the group. So whatever you’re feeling, go ahead and do your thing.
8. It gives your bike a break.
Switching it up with some Spin classes will also give your commercial spinning bike a break from the elements, not just your body. Rain, dirt, and snow will take their toll on your components over time. Replacing just some of your workouts with Spin classes will give you the opportunity to buy and install new parts, or time to take your bike into the shop for a tuneup.
Spinning might look about the same as outdoor cycling or riding a stationary bike, but in many ways, it’s a far more intense workout—and one of the easiest to overdo.
First, there aren’t many (if any) breaks in spin class. “When you’re biking outside, you have to be aware of road dangers like water and cars, so you have to slow down at times,” says Dr. Maureen Brogan, an assistant professor of medicine at New York Medical College who has conducted research into spinning. Especially if you’re a novice road rider, it’s going to take some time before you’re comfortable enough on two wheels to really push yourself hard for long distances. That’s not the case on a spinning bike, where newbies can hop on and ride hard from the start.
Popular spinning studios like Flywheel and SoulCycle have their riders clip their feet into the stationary bikes. As long as the wheels turn, legs keep pumping. Combine this always-working aspect with the thumping music, enthusiastic instructors and energetic group atmosphere of most spinning studios, and it’s easy to get intense exercise and burn calories by the bucketful.
“The muscles you use on spinning bikes, the gluteus maximus and the quadriceps, are some of the largest in your body, so you’re using a lot of energy,” Brogan says—600 calories an hour, and sometimes more.
This puts spinning near the top of the list when it comes to high-intensity workouts. A study from Sweden found that one hour of spinning was enough to trigger the release of blood chemicals associated with heart stress or changes. While that may sound like a bad thing, these blood chemicals—or biomarkers—signal the heart is getting a good workout. “These kinds of findings have also been seen with prolonged exertion such as marathons,” says study author Dr. Smita Dutta Roy of Sahlgrenska University Hospital in Sweden. While more research is needed to tease out the risks or benefits associated with exercise of this intensity, she says that some of the biomarker shifts her team observed could lead to blood vessel repair and renewal.
It can also help improve body composition, decrease fat mass and lower blood pressure and cholesterol, says Jinger Gottschall, an associate professor of kinesiology at Penn State University. Some of her research has shown that high-intensity spinning can increase fitness levels even in trained athletes. “In every study we’ve done, we’ve seen increases in heart and lung capacity,” she says. She calls spinning “the optimal cardio workout,” and says you can get all the intensity of a treadmill or stair-climber without the impact.
The low-impact nature of spinning makes it great exercise for older adults or people recovering from orthopedic injuries, she adds. “Because you can adjust the resistance and moderate the pace and intensity of your ride, it opens the door for many people to participate,” she says.
But it’s also easy for people who are new to spinning to overexert themselves. “If you’re not used to vigorous exercise, or to exercising the large lower-body muscles involved in spinning, you can overdo it,” Brogan says. She’s a kidney expert by training, and some of her research has linked spinning to rhabdomyolysis, a condition in which muscles break down to the point that they release a protein that can poison the kidneys. “People have swollen legs or trouble walking, and sometimes they take aspirin or NSAIDs for the muscle pain, which is the last thing they should do because those can also damage the kidneys,” she says. Problems like this can set in a day or two after spin class, she says.
While overexertion is possible with any form of exercise, she says the risks during spinning may be higher—especially when you consider that some spinners lose up to a liter of water during an hour-long session.
Even for trained athletes, there’s some evidence that spinning too often may lead to trouble. A study in the Journal of Strength and Conditioning Research concluded that spinning may push some people past the threshold at which the exercise is beneficial. “If indoor cycling were used as an everyday training activity, it is possible that the overall intensity would be too high and possibly contribute to developing nonfunctional overreaching,” the authors of that study write. (“Nonfunctional overreaching” is sports science lingo for a workout that’s so strenuous it leads to fatigue and performance declines, rather than fitness improvements.)
Overall, spinning is exceptional exercise. But if you’re new to it, you need to ease in and give your muscles time to adapt to its intensity. Even if you’re an experienced athlete, pushing yourself to your limit the first or second time you get on a spinning bike may be risky, Brogan says. Even once you’ve found your spinning legs, daily sessions may still be overkill.
But if you’re looking for a high-intensity workout a few days a week—and especially if running or other forms of vigorous aerobic exercise hurt your joints—spinning may be the ideal way to keep your heart and body in shape.
|
|
|
Top Industrial Belt Conveyor Issues |
Posted by: R234V - 09-22-2021, 05:20 AM - Forum: Welcomes and Introductions
- No Replies
|
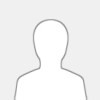 |
Top Industrial Belt Conveyor Issues
Top Industrial Belt Conveyor Issues
The advent of troughed belt conveyors fundamentally changed industrial processing, increasing efficiencies, reducing labor requirements, improving safety, and streamlining production. These flexible devices have become the standard for moving product and material around a facility and are found in every industry imaginable.
While belt conveyors provide a reliable, efficient bulk handling solution, they can experience occasional problems. And when issues arise, they can wreak havoc on a production line. Below are some of the most commonly seen issues when working with belt conveyors, including what causes these problems and how to prevent them.
Note: This is not a comprehensive list and does not substitute for the expertise of a professional. Always consult your original equipment manufacturer or manual to ensure all necessary safety, maintenance, and troubleshooting guidelines are followed. Maintenance and storage procedures should always be carried out by a trained professional. FEECO does not make any representations or warranties (implied or otherwise) regarding the accuracy and completeness of this guide and shall in no event be liable for any loss of profit or any commercial damage, including but not limited to special, incidental, consequential, or other damage.
Carryback is the material that remains on the belt after discharge and is perhaps the most common struggle among conveyor pulley. Typically all conveyors experience carryback to some extent, but given its potential for serious consequences, keeping it to a minimum is essential.
WHY CARRYBACK IS AN ISSUE
Carryback creates a messy and potentially hazardous work environment, as it gets into the undercarriage and surrounding area of the conveyor. This can cause outages and increase the time devoted to cleaning and maintenance.
Not only does carryback create a mess, but material allowed to build up on rollers, idlers, and pulleys degrades these components, causing excessive wear. Further, a buildup of carryback can also cause belt tracking issues, potentially wearing and damaging the belt.
WHAT CAUSES CARRYBACK
Carryback is largely a result of the conveyed material’s characteristics and propensity for sticking. In general, a material with a higher moisture content is more likely to stick to the belt. Similarly, carryback can be more of a problem in humid environments where hygroscopic materials pull moisture from the air, increasing the likelihood of sticking.
Sticking can also occur when condensation is produced as a result of extreme temperature differences between the material and the belt.
HOW TO PREVENT CARRYBACK
The best way to prevent carryback is to utilize one or more belt cleaners. Belt cleaners can be installed at both the head and tail pulley and serve to ride against the conveyor belt, dislodging any material that may be adhered to the belt. These devices substantially reduce buildup on the belt, and depending on the level of carryback, several options may be appropriate. Common options include a self-cleaning tail pulley, return side belt plow (v-plow), and dual belt cleaners.
Routine cleaning should also be prioritized as part of a conveyor head pulley maintenance program in order to minimize any remaining buildup on components.
CONVEYOR BELT MISTRACKING
Tracking, or training, refers to the way in which the belt rides on the rollers. Conveyor belts should always track centrally. Mistracking occurs when the conveyor rubber belt rides unevenly on rollers, favoring one side over the other.
Like carryback, mistracking can cause several issues in a conveyor system. This includes uneven belt wear, belt damage resulting from catching or rubbing on surrounding infrastructure, material spillage, warped belting or belts that are not square, and more.
Mistracking is also recognized as a safety violation by the US Department of Labor’s Mine Safety and Health Administration (MSHA). When a belt is not tracking properly, areas that are normally safe can become pinch points, presenting a hazard to workers. Mistracking can also cause material to fall off of the conveyor, falling on to workers and equipment, or creating piles that present a safety risk.
WHAT CAUSES MISTRACKING
Since conveyor bend pulley are carefully balanced, any number of factors may be the source of mistracking, making it difficult to identify the origin of the problem. Potential causes of mistracking include improper idler spacing, seized or worn rollers, a misaligned frame, material buildup on any part of the conveyor, excessive belt tensioning, and a worn or damaged belt, to name a few.
HOW TO PREVENT MISTRACKING
The range of possible mistracking causes make a blanket solution to prevention impossible. There are, however, measures that can help to reduce the potential for this issue to occur.
Conveyors can fall out of perfect alignment through normal wear and tear. As a result, routinely inspecting alignment of the conveyor structure and its many components helps to prevent mistracking. Off-center loading can also create an alignment issue, so ensure that chutes are positioned centrally over loading areas.
Since mistracking can be caused by material buildup, it’s also important to keep the belt conveyor, idlers, and pulleys clean. This will reduce wear on components, which could also cause mistracking.
Slight off-tracking issues can be remedied by “knocking idlers,” a practice in which idlers are skewed a small amount to correct an off-tracking belt.
SLIPPAGE
Belt slippage typically occurs around the drive/head pulley and happens when the belt and pulley do not have enough grip to adequately turn the belt around the pulley.
WHY BELT SLIPPING IS AN ISSUE
Belt slipping reduces productivity and efficiency, causing process upsets, or preventing the proper amount of material from being conveyed. It can also cause belt wear and damage, and put added stress on the motor, resulting in premature failure.
WHAT CAUSES SLIPPAGE
There are several reasons why a belt experiences slipping. This includes:
Low temperatures (cold temperatures can reduce the amount of grip between the pulley and belt)
Improperly installed pulley lagging
Buildup on pulley
Inadequate belt tension
Worn head pulley
Smooth pulley surface
Load that is too heavy for conveyor
HOW TO PREVENT SLIPPAGE
There are several ways to prevent slippage. Maintaining an adequate belt tension is critical to preventing slippage. It’s important to note, however, that while over-tensioning the belt may seem like an easy fix, this should be avoided, as it can stretch and damage the belt, as well as put added stress on the motor.
When there is not enough grip between the pulley and the belt, consider installing lagging. Lagging is a material added to the surface of the pulley for increased traction.
Alternatively, a snub pulley may be installed. A snub pulley is simply an idler installed at a point which increases the arc between the belt and pulley to improve friction between the two.
MATERIAL SPILLAGE
Material spilling off of the conveyor is also a commonly encountered problem. While spillage can occur at any point along the conveyor path, not surprisingly, it is most common at load and transfer points.
WHY SPILLAGE IS AN ISSUE
As with other issues, material spilling off of the conveyor belt reduces productivity and efficiency, encourages product/material loss, and increases wear on equipment. Further, as mentioned, spillage can be a significant safety hazard, falling on employees and increasing the likelihood of employees slipping or falling.
WHAT CAUSES SPILLAGE
In general, it is not uncommon to see some level of material spillage. Excessive fugitive material, however, likely indicates an underlying issue. Typical causes of excess spillage include belt misalignment, belt damage or wear, high-impact loading, and chute misalignment.
HOW TO PREVENT SPILLAGE
Spillage in general is managed by a well-designed conveyor system. The use of skirtboards and dust pick-off points are useful in reducing the potential for material spillage.
Ensuring that chutes are clear and located centrally above the loading zone will also help to prevent spillage. Additionally, impact beds for heavy loading prevent the belt from sagging, which can also release fugitive material.
Keeping conveyors aligned and in proper working order will also help to prevent excess fugitive material from escaping, as any deviation from proper operation has the potential to spill material.
PREVENTION IS KEY
Any one of the aforementioned issues has the potential to cause serious problems: premature equipment failure, unexpected downtime, employee injuries, and more. Even if problems do not reach a high level of severity, however, they still represent unnecessary hazards and losses in productivity and efficiency. For these reasons, a preventative approach to conveyor problems is always the best policy.
Regularly inspect the steel cord conveyor belt to look for signs of trouble: excessive material spillage, abnormal sounds, visual indicators, or other abnormalities. Always ensure that the equipment, as well as the surrounding area, are kept clean. Replace conveyor components that begin to show signs of wear.
By taking these measures, the potential for unexpected downtime and lengthy repairs is greatly reduced.
CONCLUSION
Troughed belt conveyors offer reliable handling in nearly any setting, but they can occasionally exhibit issues, particularly if not kept clean and maintained; carryback, mistracking, slippage, and spillage are some of the most commonly encountered issues when working with belt conveyors. While each issue presents significant risk and potential for damage, these issues are largely prevented by keeping a close eye on conveyor operation and performance, and promptly addressing any issues that arise.
FEECO manufactures custom belt conveyors and conveyor systems for use in nearly every industry, with expertise around hundreds of materials. Our Customer Service Team offers a full range of services for conveyors, from replacement parts, to repairs, and even inspections and conveyor audits. For more information on our belt conveyors or conveyor parts and service support, contact us today!
|
|
|
Tiller mortality and its relationship to grain yield in spring wheat |
Posted by: R234V - 09-22-2021, 05:17 AM - Forum: Welcomes and Introductions
- No Replies
|
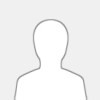 |
Tiller mortality and its relationship to grain yield in spring wheat
Tiller mortality and its relationship to grain yield in spring wheat
A primary determinant of grain yield in barley (Hordeum vulgare L. emm. Lam) is the number of ear-bearing tillers per plant at harvest, which depends both on the production of tillers and on their subsequent survival to form ears. This three-year field study compares tiller production and survival in relation to final grain yield in three types of barley: 2-rowed winter (2rw), 6-rowed winter (6rw) and 2-rowed spring (2rs), grown in two contrasting environments. These three types differed significantly in shoot and ear number, the winter barleys showing higher tiller production, with the maximum number of tillers ranging from 798 to 2315 m?2 in 2rw, 711 to 1527 in 6rw and 605 to 1190 in 2rs. Grain yield across environments and years was strongly correlated () with the number of ears at harvest. The maximum number of shoots produced by each type of barley was inversely related to the mean temperature during the tillering phase. Tiller mortality was inversely related to the maximum shoot production, being significantly lower in barleys with less tillering capacity, i.e. the spring type (with average values of 34.3% and 42.7% in the two environments). The highest tiller mortality occurred before anthesis and, to a lesser extent, from anthesis to maturity. These data support the hypothesis that the principal cause for tiller mortality in barley grown under Mediterranean conditions is the competition between tillers for a limited supply of resources.
Spikeless tillers of wheat (Triticum aestivum L.) affect grain yield because of less than optimum effective plant population. This study was conducted to examine the genetic variability for tiller mortality, and its relationship to grain yield in diverse wheat lines. Twenty lines were evaluated in replicated field tests in 4 years at Rampur, Nepal. The characters investigated were maximum number of tiller produced, the number of reproductive tillers, tiller mortality, and grain yield. The lines differed significantly for all characters. The tiller mortality ranged from 7 to 30%. There were substantial effects of environment on all four characters. The entry-by-year interactions were significant for all traits, primarily because of changes in the relative genotypic differences for these traits in the four years. However, certain lines consistently ranked low or high for tiller mortality. There was a significant negative correlation between front tine tiller and grain yield in 3 out of 4 years. There was a positive correlation of highest tiller number with reproductive tiller number and with tiller mortality. Grain yield showed a nonsignificant positive correlation with maximum tiller number. The reproductive tiller number was positively correlated with grain yield. Results of this study indicate that spikeless tillers contribute negatively to grain yield and that genetic variation exists for tiller mortality in spring wheat.
Vegetative growth in the form of tillers is crucial to final yield in winter wheat (Triticum aestivum L.). To understand the impact management practices have on tiller initiation, a study was conducted using two seeding rates (1.9 × 106 vs. 6.8 × 106 ha?1) and two N timing applications (single vs. split). Tillers initiated in the fall made up the majority of spikes compared to tillers initiated from 1 January to the start of jointing (GS 30). Tillers initiated in March at either seeding rate produced very few kernels spike–1, low kernel weight, and contributed little to yield. At the high seeding rate, tillers initiated prior to 1 January were responsible for more than 87% of the grain yield. Tillers produced in January– February produced 5 to 11% of the final yield, while tillers produced in March contributed less than 2%. In contrast, at the low seeding rate tillers produced in January–February made up 20 to almost 60% of the final yield. Overall, this study shows the timing and rate of leaf initiation impacts yield and yield components. Earlier tillers have an advantage in that they have shorter periods of leaf development that result in more leaf area which in turn supports more kernel spike–1 and heavier kernels, thus more grain weight per spike. Timing of N (single vs. split) application resulted in no significant impact on tiller development, spike number, kernel number, kernel weight, or grain yield.
The number of spikes ha–1 is a critical yield component of wheat yield. Two factors contribute to the total number of spikes ha–1 at harvest, number of mainstem (MS) spikes and number of tillers plant–1. The number of tillers produced per plant is controlled by the environment during the period of tiller development from three-leaf stage to jointing (GS13–GS30) (Klepper et al., 1982) and the amount of tiller mortality that occurs from jointing to anthesis (GS30–GS69) (Jewiss, 1972; Rawson, 1971). Recent research has shown that the timing of tiller initiation and management factors such as seeding rate influence the rate of leaf development on each tiller which, in turn, influences tiller size and mortality (Tilley et al., 2015). The timing of tiller initiation and management factors such as planting date (Oakes et al., 2016) that promote leaf development could also influence other yield components such as kernels spike–1 and kernel weight. An understanding of when the most spikes are formed and the management factors that promote tiller formation during this critical period would help growers improve wheat yield.
Tillers can be formed at multiple nodes on the MS, and secondary and tertiary tillers can form from nodes on the tillers themselves (Klepper et al., 1982; Evers and Vos, 2013). Under glasshouse conditions Klepper et al. (1982) found that once a tiller is initiated, leaf development on the tiller proceeded at the same rate as leaf development on the MS. However, subsequent research has found that leaf development on each tiller proceeds at a slower rate than that on the MS or even on preceding tillers (Tilley et al., 2015). This indicates that tillers initiated first will always have an advantage in growth and development compared to those initiated later. This advantage will increase as time passes resulting in more leaf area. It is likely that tillers with more leaf area will produce more kernels, heavier kernels, and will be less likely to be lost to tiller mortality.
Timing of tiller initiation can also influence tiller mortality. Charles-Edwards (1984) concluded that self-thinning within plant communities is largely due to the lack of assimilate needed to continue growth and development within the individual stem which, in turn, can lead to a decrease in plant weight and eventually a decrease in plant yield. Some works have explored the purpose of rear tine tiller and the effects it may have on the plant as a whole and concluded tillers that abort may have benefited the plant due to assimilate and nutrient accumulation (Lupton and Pinthus, 1969; Palfi and Dezsi, 1960). However, Langer and Dougherty (1976) concluded that dead tillers had a negative effect on grain yield due to competition for assimilates and nutrients (Sharma, 1995).
Management practices such seeding rate and N application timing can influence the timing and rate of leaf and tiller development (Bauer et al., 1984; Tilley et al., 2015) and grain yield. Tompkins et al. (1991) concluded that grain yields will decline as seeding rates decline. This in part is due to a decrease in spikes. However, it was determined that grain yield can decrease at high seeding rate (HSR) (Gooding et al., 2002) due to a decrease in kernels spike–1 and a decrease in kernel weight (Puckridge and Donald, 1967; Tompkins et al., 1991). Tilley et al. (2015) found that seeding rates influenced the rate of leaf development. Phyllochron intervals (PI) were shorter for each tiller at a low seed rate (LSR) compared to the same tillers at a HSR. This resulted in more leaves on each tiller, more tillers produced and fewer tillers lost to tiller mortality.
Nitrogen is recognized as a vital nutrient needed for growth and development (Miller, 1939; Wilhelm et al., 2002). Nitrogen application timing recommendations for winter wheat in North Carolina (NC) are based on the tiller density (Weisz et al., 2001, 2011). Winter split applications are encouraged if tiller density <550 m–2. Otherwise the standard NC recommendation is to apply N at GS 30, the time when the wheat stem begins to elongate. Maidl et al. (1998) confirms that early N application increased plant density and concluded that N fertilizer treatment applied during stem elongation not only reduced tiller mortality but also led to high grain yield in both MS and tillers.
To understand the impact of the timing of tiller initiation and management practices on kernel development and yield, a method of counting and marking leaves and tillers was created to monitor tiller growth and decline. This monitoring of individual tillers resulted in the ability to measure the number of heads, kernel number and kernel weight each tiller produced, and its contribution to final yield. The objectives of this study were to: (i) measure yield and yield components of tillers initiated at different periods during the growth of wheat and how tillers initiated at different periods contribute to overall grain yield, and (ii) determine the impact of seeding rate and timing of N applications on the productivity and sustainability of tillers initiated at different periods during the growth cycle of wheat.
MATERIALS AND METHODS
Field Experiment
Field experiments were conducted at two sites in eastern NC and one site in western NC. At the Tidewater Research Station (TRS) in Plymouth, NC, experiments were conducted in 2009, 2010, and 2011. On a private farm in Beaufort County (BC) experiments were conducted in 2009 and 2010. On the third site in western NC (Piedmont Research Station [PRS] in Salisbury, NC) a single trial was conducted in 2011. The soil at TRS was a Cape Fear loam (clayey, mixed, thermic Typic Umbraqult) soil. At the BC site in 2009 and 2010 the experiment was conducted on a Cape Fear fine sandy loam (clayey, mixed, thermic Typic Umbraqult). The 2011 experiment at PRS was conducted on a Mecklenburg clay loam (fine, mixed, thermic Ultic Hapludult). In 2009, plots were planted on 3 November at TRS and 4 November in BC. In 2010, plots were planted on 10 November at TRS and 11 November in BC. In 2011, plots were planted on 10 November at TRS and 15 November at PRS.
At each site, Pioneer 26R12, a high yielding wheat variety in NC, was planted in 16.9-cm rows into a conventional tilled field following corn. The experimental design at all sites was a split plot design with main plots consisting of two seeding rates, 1.9 × 106 and 6.8 × 106 ha–1, and subplots consisting of 134 kg N ha–1 applied either as a single application in March or a split application with half applied in late January or early February and the remaining half applied by late March. In 2009–2010, the first N application was made on 15 February with the second split and single N application made on 22 March. In 2010–2011, the first N application was applied on 4 February while the remaining split and single applications were completed on 18 March. During the 2011–2012 growing season at TRS, the first split application was applied on 19 January with the final split and single N applications applied on 12 March. Applications at the PRS were applied 1 wk later on 26 January and 19 March. All treatments were replicated five times.
Disease pressure was minimum across all three site years and did not reach current threshold recommendations (Weisz et al., 2011). However, weed and insect control practices were applied. In 2009–2010 at TRS, thifensulfuren-methyl/tribenuron-methyl was applied POST at 0.04 kg a.i. ha–1 on 8 Mar. 2010. The BC location received the same application on 9 Mar. 2010. In 2010–2011 at both TRS and BC, thifensulfuren-methyl/tribenuron-methyl was applied POST at 0.04 kg a.i. ha–1 on 14 Mar. 2011. In 2011–2012 at TRS, mesosulfuren-methyl was applied POST at 0.33 kg a.i. ha–1 on 6 Dec. 2011 and thifensulfuren-methyl/tribenuron-methyl applied POST at 0.05 kg a.i. ha–1 on 1 Jan. 2012. At the PRS, chlorsulfuron/metsulfuron-methyl was applied PPE at 0.03 kg a.i. ha–1 on 3 Nov. 2011 and thifensulfuren-methyl/tribenuron-methyl was applied POST at 0.05 kg a.i. ha–1 on 28 Feb. 2012.
Individual plots were 24.4-m long and 1.98-m wide equaling a total of 48.31m2. Each plot was divided into three sections. The first 18.01 m2 section was designated for grain yield and grain sampling. This section of the plot was harvested using a Gleaner K2 combine with a Harvestmaster Graingage (Juniper Systems, Logan, UT) that recorded moisture, grain weight, and test weight. The TRS in 2010–2011 was harvested on 20 June and on 22 June during 2011–2012. Beaufort County in 2010–2011 was harvested on 23 June and PRS was harvested on 29 June during the 2011–2012 season. Grain weight was adjusted to 15.5% moisture before calculating yield.
The second section equaling 9.12 m2 was designated for marked samples. Five plants from each plot were marked and the number of full and partial leaves on each MS and tiller were recorded along with the total number of tillers at current growth stage. This was done once a month from planting to harvest. Throughout the 2009–2010 growing season, observations were made at TRS and BC on 22 December, 28 January, 1 March, 19 March, 7 April, and 26 April. During the 2010–2011 growing season, observations were made on 7 December, 31 January, 4 March, 2 April, and 30 April. During the 2011 growing season, leaf and Garden Tiller and Cultivator counts were recorded on 9 December, 2 January, 11 February, and 3 April at TRS and 15 December, 9 January, 24 February, and 13 April at PRS. Each new and existing tiller was noted using either a black, silver, or red permanent marker to mark leaf number. Black markings represented tillers that were initiated from planting through the end of December. Silver markings represented early winter tillers that developed from the first of January to the beginning of March. Red markings represented late spring tillers produced from March till growth stage GS30. The three colors used to track tillers helped categorize each individual tiller and determined whether or not they initiated in the fall, winter, or spring. Furthermore, tillers were marked on each subsequent leaf to track the number of leaves produced throughout the growing season. Harvest samples were taken in 2010–2011 and 2011–2012 at TRS, BC, and PRS on the same dates that the larger plots were harvested. At harvest, each of these five plants were clipped and placed in individual bags. For each plant, the MS and tillers were separated by color markings (black, silver, red) counted and hand threshed to determine the number of spikes and grain weight spike–1 for each tiller initiation period. The data for all five plants were averaged to represent values for each plot.
The last 21.18 m2 of each plot was reserved for destructive sampling. Method for destructive sampling consisted of a 2-m stick and a garden shovel. A trench, encamping an area of 0.33 m2, was carefully dug around plants to a depth of 15 cm and the plants were then excavated from the destructive sampling area. Samples were taken on 17 June 2010, at TRS and BC. On 15 and 20 June 2011, destructive samples were taken at TRS and BC. Destructive samples were taken at TRS and PRS in 3012 but were destroyed before they could be processed. Leaf counts were taken from each individual stem and recorded. Leaf numbers were determined by counting the nodes on the plant. This was done by splitting the plant at the base and finding the small (0.6–1.25 cm) gap between the compressed nodes and the first separated node. The first separated node was counted as the fifth node (fifth leaf) and subsequent nodes (leaves) were counted in ascending order. Plants were separated into classes corresponding to the periods of tiller initiation (black, silver, and red) based on leaf number and the ratio of stems found in each initiation period in the marked samples. This ratio was determined by counting the number of MS or tillers from each category (black, silver, and red) in the five marked plants described above and dividing that number by the total number of MS or tillers produced in these same plants. Using the ratio of MS or tillers that were initiated from planting to the end of December (Black), the same ratio of plants with the highest leaf numbers in the destructive sample were designated as having been initiated during this period. Plants with the next highest leaf number were considered initiated during the period from 1 January to the end of February; and plants with the fewest leaves were considered initiated after 1 March. Spikes from samples representing each initiation period were hand threshed and grain weight, kernel number and 100 kernel seed weight were measured.
Statistical Procedures
For the marked plant samples the data taken from TRS in 2010–2011 and 2011–2012 at BC in 2010–2011 and PRS in 2011–2012 were analyzed using a repeated measures design with the Proc Mixed procedure in SAS (SAS Institute, Inc., Cary, NC) to determine if there were differences in the number of spikes plant–1 and grain weight spike–1 among site-year, tiller initiation periods (planting to 31 December, 1 January to 28 February, and after 1 March) seeding rate, and N application timing. In all cases, site-year, seeding rate and N timing were treated as fixed effects, while blocks and the interactions with blocks were treated as random. When differences were detected, Fisher’s Protected LSD was used to separate means.
In the destructive sample plots some samples were lost in 2011–2012. Therefore, only samples taken in 2009–2010 and 2010–2011 at TRS and BC were used in the analysis. The Proc Mixed procedure in SAS (SAS Institute, Inc.) was used to determine if there were differences in spikes m–2, kernels spike–1, weight per 100 kernels, and grain yield among site-years, mini power tiller tractor initiation period, seeding rate and N application timing. As with previous analysis, site-year, seeding rate, and N timing were treated as fixed effects; while blocks and the interactions with blocks were treated as random. When differences were detected, Fisher’s Protected LSD was used to separate means.
Grain yield from the large 18.01 m2 section of each plot for the 2010–2011 and 2011–2012 seasons at TRS and BC were analyzed using the Proc Mixed procedure in SAS (SAS Institute, Inc.) to determine if there were differences in grain yield among site-years, seeding rate, and N application timing. These site-years were chosen so that the grain yield from the large samples could be compared with that calculated from the small 2-m samples.
|
|
|
Solving problems on the tube mill |
Posted by: R234V - 09-22-2021, 05:12 AM - Forum: Welcomes and Introductions
- No Replies
|
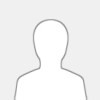 |
Solving problems on the tube mill
Solving problems on the tube mill
Tube mill machine line face a variety of challenges every day in their effort to produce high-quality tubing in a cost-effective and productive way.
This article examines some of the typical problems producers encounter, some common causes of these problems, and some ideas for how to solve these problems.
Lost Mill Time During Operation and Changeovers
Often, excessive downtime during normal operation or tooling/job changeover can be attributed to one or more of the following causes:
1. No written procedures for setup. Every mill should have written procedures for all operators to follow. The machine, tooling, and steel are fixed factors in the mill setup equation; the only variable is the human factor. This is why it is so important to have written procedures in place to control the process. Written procedures also provide a tool for troubleshooting when problems arise.
2. No setup chart. Tweaking the mill during setup loses valuable setup time. Operators must work the tooling the way it was designed. This means setting up to the parameters of a setup chart.
3. Lack of formal training. Formal training helps operators perform the procedures for carbon steel tube mill machine and maintenance and ensures that all operators are on the same track.
4. Disregard of parameters from previous setup. If the Galvanized tube mill machine has been set up according to the written procedures and setup chart, the operator can write down the numbers from the digital readout on the single-point adjustment (SPA) unit, allowing the next operator to set up where the first left off. Setting up to the numbers can save as much as 75 percent of total setup time, as long as all the other tips discussed in this article are followed.
5. Mill in poor condition. A poorly maintained mill costs valuable time and scrap during setup and operation. The mill must be dependable so that the operator is not chasing mechanical problems during normal operation and setup. A good maintenance program, as well as rebuilds or upgrades when necessary, is essential.
6. Mill in misalignment. Tube mill misalignment, poor mill condition, and inaccurate setup account for 95 percent of all problems in tube production. Most mills should be aligned at least once a year.
7. Tooling in poor condition. Operators must know how much life is left in the tooling before the next scheduled rework. Running the tooling until it cannot produce tubing anymore not only wastes valuable mill time, but produces scrap and affects delivery schedules. All tube production companies should have a tooling maintenance program in place.
Any of these causes of lost time on the mill can have varying degrees of value, depending on the severity of the conditions. The bottom line is, the more of these items that are in control, the less downtime on the mill.
Splitting in the Weld Zone
Weld zone splitting can be a result of some or all of the following:
Overly narrow strip with insufficient material to forge
Poor alignment or setup
Insufficiently worked fin passes, so the edge is not prepared for welding
Poor slit edge
Off-center strip approach (strip rolled over) to the weld box, preventing forging between the weld rolls
Nonparallel edges entering the welding machine
Inappropriate weld power for mill speed
Poor-quality steel with improper chemistry
Irregular Size in the Sizing Section
When irregular size occurs in the sizing section, the problem may not necessarily be in the sizing section itself. The operator also must check the setup in the breakdown, fin, and welding section of the mill to ensure proper presentation to the sizing section. If the forming section sends improperly formed tube to the sizing section, irregular tube size can result.
The operator also should check for bent shafts, oversized bores on the tooling, or undersized outside diameters (ODs) on the driven shafts. The integrity of the side roll boxes also should be checked.
In addition to these checks, the operator should consider the following questions:
Is the weld size in accordance with the setup chart?
Is the weld size round?
Are the strip edges parallel, with no step going into the weld rolls?
Is the weld scarf smooth?
Are rework shims installed under the bottom driven shafts to maintain the metal line?
Are the correct spacers installed on the driven shafts and to the correct length?
Are the bearings and bearing blocks tight?
Are the side rolls parallel?
Is the tube being cooled properly?
Are all the drives coordinated and adjusted to match the rework of the tooling?
Has the chemistry or hardness of the material changed?
Weld Chatter
Weld chatter is the inability to achieve a clean cut of the outside weld bead after welding. The scarf knife chatters and produces a ribbed or rough cut on the OD of the tube. This is unacceptable in most of the end products produced by the tube and pipe industry.
Several techniques can be used to prevent weld chatter.
The scarf knife should have a slightly larger radius than the tube OD. This will provide a concentric, clean cut.
An ironing pass should be used after the scarf stand. As the name implies, this stand irons out any hot imperfections the scarf knife may leave behind. It also adds a tremendous amount of stability to the scarfing operation.
On mills that employ induction welding, moving the induction coil upstream a bit and away from the weld rolls helps temper the edges of the strip by preheating them before welding. This results in a more malleable material that is softer and easier for the scarf knife to cut.
The heel of the scarf knife or insert should be ground to an angle of 18 degrees from the horizontal, and the tool should be set at an angle of 15 degrees from the vertical. This provides the proper clearance so the knife does not drag on the tube or pipe. A straight up-and-down approach to the tube or pipe invites chatter.
In general, several tube mill components should be checked on a regular basis. This should be done at least monthly, but should be based on the usage. A higher production rate or running heavier metals through the mill requires more frequent checks. Shafts should be checked for OD, looseness, bending, and parallelism. Shoulder alignment should be checked, and the integrity of the entry table, drive stands, side roll boxes, weld box, and Turk's head units should be ensured. Of course, rolls should be checked to ensure they have been installed on the correct stands.
Once a year, the mill should be aligned. A mill alignment usually takes one or two days and is most often done by a professional. Every day, the mill operator should use a setup chart and follow all operating procedures.
The operator also should know the chemistry, Rockwell hardness, width, and thickness of the strip entering the mill and should document these values. Tube size should be measured between each pass.
Most important, for high-quality, consistent results in tube producing, an operation standard should be established for all employees to follow.
High‐frequency welded carbon tube mill machine line is designed to produce round tube diameter of 10.0 – 38.1mm, and wall thickness of 0.4 ‐1.8mm.This line utilizes roll forming to process steel strip into various shapes. Using high frequency induction heating, this line is capable of producing section material of various diameters and sizes by squeezing weld seam together into closed shape. The application of advanced aperture technology, PLC automatic control system and British Eurasia Digital speed‐regulating unit ensure that the production line works reliably and operates and maintains easily.
Every detail is the evidence of showing our company's strength and works's hardworking and it is the basical assurance of every machine we are producing.We are targeting to provide our customers with high-quality equipment or machines.
Botou Boheng Metallurgical Equipment Manufacturing Co.,Ltd was established in 2003, and located in Botou city Hebei province. Boheng is a high and new-techonology enterprise specialized in design,development and manufacture of ERW welded pipe equipment,high precision slitting & crossing-cutting equipment,spiral welded pipe equipment,cold forming equipment and crossing-cutting equipment,spiral welded pipe equipment,cold forming equipment and rollers. Boheng is the pioneer that had the key processing technology of the international advanced whole set welded pipe mill. Boheng always adhere to the enterprise policy "contribute to the society with excellent techniques,high quality products and perfect service".
Technology capability:
(1)Engineer able to service overseas
(2)Work out reasonable investment scheme,selecting rational model unit
(3)Provide free equipment layout,factory planning for you
(4)Provide free equipment foundation drawing,if necessary,offer technical guidance on-site for equipment foundation construction
(5)Provide equipment installation and commission,ensure the normal operation of production line
(6)Provide professional technical training to help your stuff familiar with equipment ASAP
|
|
|
|