Welcome, Guest |
You have to register before you can post on our site.
|
Online Users |
There are currently 258 online users. » 0 Member(s) | 257 Guest(s) Bing
|
Latest Threads |
Dominica visa free countr...
Forum: Off Topic
Last Post: axied12
06-24-2025, 12:37 PM
» Replies: 0
» Views: 225
|
Advanced microneedling
Forum: Off Topic
Last Post: axied12
05-28-2025, 01:25 PM
» Replies: 0
» Views: 341
|
Caviar and cheese
Forum: Off Topic
Last Post: axied12
05-28-2025, 12:38 PM
» Replies: 0
» Views: 301
|
Top-rated countertop comp...
Forum: Off Topic
Last Post: axied12
05-04-2025, 06:42 AM
» Replies: 0
» Views: 451
|
Ryanair letenky levně do ...
Forum: Off Topic
Last Post: axied12
02-11-2025, 01:37 PM
» Replies: 0
» Views: 848
|
Trusted essay writing ser...
Forum: Off Topic
Last Post: axied12
01-30-2025, 08:16 AM
» Replies: 0
» Views: 763
|
Bootverkopers - actieve j...
Forum: Off Topic
Last Post: axied12
12-07-2024, 11:07 AM
» Replies: 0
» Views: 889
|
Services for individuals ...
Forum: Off Topic
Last Post: axied12
12-02-2024, 03:31 PM
» Replies: 0
» Views: 869
|
Used excavators
Forum: Off Topic
Last Post: axied12
11-13-2024, 09:22 AM
» Replies: 0
» Views: 808
|
Buy Higo Rocket in Dubai
Forum: Off Topic
Last Post: axied12
10-25-2024, 01:09 PM
» Replies: 0
» Views: 924
|
|
|
Pipe Fittings |
Posted by: mmws256w - 09-22-2021, 03:21 AM - Forum: Welcomes and Introductions
- No Replies
|
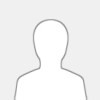 |
This chapter presents various types of pipe fittings. Of all the fittings, the elbow is the one most often used. Simply put, the elbow, or ell, is used when a pipe changes direction. Elbows can turn up, down, left, right, or any angle in between. When one finds it necessary to draw a 90° elbow or calculate how much space it will occupy in a routing configuration, knowing its length becomes essential. An elbow's length is commonly referred to as the center-to-end dimension and is measured from the centerpoint of its radius to the end of either opening. Dimensional sizes of fittings are typically provided by the manufacturer of the fitting. Manufacturers issue dimensioning charts containing lengths for a particular fitting. Another elbow that may be used under certain circumstances and with permission from the customer is the 90° short-radius elbow. The 90° short-radius ell makes a much sharper turn than does the long-radius ell.
Emissions from Pipe Fittings and Gaskets
Threaded pipe fittings in the seal flush line can be significant leak sources, with readings above 1,000 ppm.4,17 Similar emission levels may be measured near the gasket region on the seal chamber face. Any leakage from these areas may drift into the emission measurement area for the mechanical seal. The mechanical seal may then be erroneously implicated as a leaker. It should be standard practice to sniff nearby hydraulic fittings and the flange gasket area if excessive VOC concentrations are detected adjacent to the mechanical seal.
Leak-tight threaded pipe fittings can be more easily attained using anaerobic paste-type sealants rather than PTFE tape. The seal chamber face must be smooth to be emission tight. Gaskets and O-rings must be free of nicks and scratches.
32.16.2 Thermoplastic Fittings Manufacturing
Thermoplastic pipe fittings may be injection-molded, fabricated, rotomolded, or thermoformed. Injection-molded fittings are generally made in sizes through 12-in. nominal diameter. Typical molded fittings are tees, 45-degree and 90-degree elbows, reducers, couplings, caps, flange adapters, stub ends, branch saddles, service saddles, and self-tapping saddle tees. Electrofusion couplings and fittings are either made by injection molding or machined from pipe stock. Electrofusion fittings and couplings are made with a coil-like integral heating element incorporated into the fitting. Joining with other fittings uses an electrical fusion device that provides electricity into the heating element, which melts the adjacent thermoplastic material and creates a fusion-welded joint.
Larger-diameter fittings exceed the capabilities of injection molding and are typically fabricated. Rotomolding is used for the manufacture of polyethylene large-diameter (up to 60 in.) and custom fittings for polyethylene corrugated drainage piping applications.
Thermoformed fittings are made by heating a section of pipe and then using a forming tool to reshape the heated area. Examples of thermoformed fittings are sweep elbows, swaged reducers, and forged stub ends. Some polyethylene corrugated pipe fittings and appurtenances are also thermoformed.
All proprietary joints shall be made in accordance with the manufacturer’s instructions. Care shall be taken to establish satisfactory jointing techniques for all water service pipework. When making joints by welding, brazing, or soldering, precautions shall be taken to avoid the risk of fire. All burrs shall be removed from the ends of pipes and any jointing materials used shall be prevented from entering the waterways. All piping and fittings shall be cleaned internally and free from particles of sand, soil, metal filings, and chips, etc.
8.19.3 Cast iron pipes
Flexible mechanical joints shall be made in accordance with the manufacturer’s instructions.
For molten lead joints, the spigot and socket shall be centered with rings of dry yarn caulked tightly into the bottom of the spigot to prevent the entry of lead into the bore of the pipe and to prevent contact of lead with the water.
Synthetic yarns that do not promote the growth of bacteria shall be used to prevent contamination of the water. The remainder of the joint space shall be filled with molten lead (taking care that no dross enters the joint), cold wire, strip, or spun lead (lead wool). The joint shall be caulked to a smooth finish with pneumatic tools or a hand hammer of mass not less than 1.5 kg. When working with spun lead, caulking tools shall be of a thickness to fill the joint space, ensuring thorough consolidation of the material to the full depth of the socket.
Lead joints shall be finished about 3 mm inside the face of the socket.
Flange joints shall be made with screwed or cast on flanges.
8.19.4 Steel pipes
Welded joints shall not be used where a protective lining would be damaged by heat, or where the pipework is employed as a primary circulation to an indirect hot water heating system.
Screwed joints in steel piping shall be made with screwed socket joints using wrought iron, steel, or malleable double crimping fitting. A thread filler shall be used. Exposed threads left after jointing shall be painted or, where installed underground, thickly coated with bituminous or other suitable corrosion preventative agent.
Flange joints shall be made with screwed or welded flanges of steel or cast iron using jointing rings and, if necessary, a suitable jointing paste. The nuts shall be carefully tightened, in opposite pairs, until the jointing ring is sufficiently compressed between the flanges for a watertight joint.
8.19.5 Unplasticized PVC pipes
8.19.5.1 Mechanical joints
Mechanical joints in unplasticized PVC piping of sizes 2 and upwards shall be made in accordance with BS4346: Part 2, by the use of push-fit integral elastomeric sealing rings which are compressed when the plain ended pipes are inserted into the adjoining sockets. The plain pipe ends shall be chamfered and the surfaces cleaned and lubricated.
The chamfered pipe end shall be inserted fully into the adjoining socket (except where provision is to be made for expansion), or as far as any locating mark put on the spigot end by the manufacturer. The sealing rings shall comply with BS2494.
8.19.5.2 Compression joints
Compression joints shall only be used with unplasticized PVC piping of size 2 and smaller. The joints shall be of the nonmanipulative type. Care shall be taken to avoid overtightening.
8.19.5.3 Solvent cement welded joints
Solvent cement welded joints in unplasticized PVC piping shall be made using solvent cement complying with BS4346: Part 3 recommended by the manufacturer of the pipe. The dimensions of the spigots and sockets shall comply with BSEN1452: Part 1–5.
Joints may also be made using integral sockets formed in the pipes and solvent cemented.
8.19.5.4 Flanged joints
Flanged joints used for connections to valves and fittings shall use full-face flanges or stub flanges, both with corrosion resistant or immune backing rings and bolting.
8.19.5.5 Polyethylene pipes
Mechanical joints shall be either plastics or metal proprietary compression fittings, for example, brass, gunmetal, or malleable iron. These shall include insert liners to support the bore of the pipe except where the manufacturer of the fitting instructs otherwise.
To ensure satisfactory jointing of the materials from which the pipe and transition elbow are made compatibility shall be established. The manufacturer’s instructions shall be carefully followed.
No attempt shall be made to joint polyethylene piping by solvent cement welding.
Large pipe fittings and valve components must be press forged and will require extensive machining. Whereas small parts such as the flange previously described can be quickly heated and cooled, and given optimum process conditions, should exhibit microstructure and properties similar to pipe and tube, the properties of large forgings will be location and thickness dependent. While no large forged part has yet been made from 740H, the properties of a solution-annealed, water-quenched and aged 343-mm-diameter bar shown in Table 14.2 are informative. Yield strength near the surface is comparable to that of thin wall tube, but yield strength at the bar center, while meeting ASME minimum, is significantly lower. Ductility and toughness were good. A hardness traverse taken on the as quenched bar showed VHN 170 at the surface and VHN 290 at the center. This is indicative of strong auto-aging in the bar center. Because the γ′ that forms on slow cooling is relatively coarse, after the final aging treatment, the bar center will have lower strength than the surface. The microstructure and creep strength at the center of the bar has not been evaluated.
A calculated continuous cooling transformation diagram for alloy 740H is shown in Fig. 14.26. This diagram supports the notion that significant γ′ hardening will occur even during water quenching of a large forging. A cooling simulation was conducted for the bar heat treatment using DEFORM software [49]. The cooling rate at a depth of 25 mm was 315°C/min and at the bar center was 30°C/min. Based on the calculated CCT diagram, there should be about 10% γ′ in the center and no γ′ at the surface. That is consistent with the experimental results.
Filament-wound pipe fittings, such as elbows and tees have been used in the chemical, and oil industry since the 1980s.9 Traditionally, composite pipe fittings were produced manually or semi-manually, but the development of CNC winders with six or more axes has allowed automated production of pipe fittings since the 1990s. The efficiency of these advanced machines depends on methods and software to determine winding patterns and perform fabrication of the complex shape within manufacturing specifications. Winding pattern generation is particularly challenging since a substantial amount of data storage/processing is required to meet manufacturing requirements (e.g., fiber tension and full-coverage) of non-axisymmetric patterns, which are required for filament-wound elbows or tees.72 On the other hand, it is worth noting that CAM software capability, rather than hardware, is considered the limiting factor for improving the performance of automated winders of non-axisymmetric parts. Consequently, general-purpose filament winding systems for pipe fittings are currently deemed impractical due to the lack of universal mathematical models and design software for CAM.9,73 Although some progress has been made to determine closed-form solutions for efficient winding patterns on specific shapes, such as elbows,74,75 most CAM systems still implement approximate methods to design and produce specific pipe fitting geometries.73 An illustration of a software-generated winding pattern, and the resulting wound elbow, is included in Fig. 11.75
Leaking valves and pipe fittings are the next concern when pressure is dropping during a test. Test sections should be isolated at pipeline block valves by using slip blinds to insure no leakage. If the test section cannot be blinded but the valves are double blocked instead, the operator must measure pressure increase in the adjacent section between the double-blocked valves to insure a tight seal exists. You need to be careful when using a thin “fire blind” at an isolation valve because under pressure the thin blind will deform and the blind cannot be removed without removing the entire valve. This often requires calling in vacuum trucks to remove product on the opposite side of the test valve being removed.
So, leakage through valves and fittings jeopardizes the chances for a successful test and may lead to data that cannot be correlated, and in that situation, the pipeline must be retested.
Tree piping is defined as all pipe, fittings, or pressure conduits, excluding valves and chokes, from the vertical bores of the tree to the flowline connections. The piping may be used for production, pigging, monitoring, injection, servicing, or testing of the subsea tree. Inboard tree piping is upstream of the first tree wing valves. Outboard tree piping is downstream of the first tree wing valve and upstream of the flowline connector.
Tree piping is normally designed in accordance with ASME B31.3. The guidelines in the API specifications are general and, in many cases, open to interpretation. It is up to the manufacturer to apply his engineering judgment.
|
|
|
Best smart bulbs for your connected home |
Posted by: mmws256w - 09-22-2021, 03:20 AM - Forum: Welcomes and Introductions
- No Replies
|
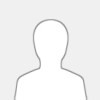 |
Smart LED bulbs that can be controlled by a hub or smartphone app are no longer a new idea. What is new is how far this technology has come since its advent just a few years ago. Also new: Products like the Nanoleaf Light Panels—a system of interlocking LED panels that let you decorate with light—fundamentally change the light-bulb concept.
Smart LED bulbs aren’t quite a commodity, but they are getting close to maturity as far as the market goes. Today’s bulbs are more compact, much brighter, have better color representation, and, for the most part, feature control apps that do more than ever and are easier to set up. Prices have also come down, with some no-name color-tunable bulbs now available for less than $10 each. (Buyer beware: You get what you pay for.)
With their rainbow of hues and myriad party tricks, color LEDs get all the press in the world of smart lighting. It’s fun stuff, but the reality is that most of us will rarely find much of a need to turn all the lights in the house blue or red—unless it’s time to celebrate our team winning the World Series. Even then, you’ll probably want to turn them all back to white after the celebration.
White light is also important in its own right, as today there is plenty of science to show how various shades of white—with variations in color temperature—impact our psychological state. Cool light that’s closer to blue has an energizing effect, and is best in the morning. Warm light is relaxing, and is best after the sun goes down. Note, however, that not every white smart LED light is color-temperature-tunable. Check out the specs before you buy.
White smart bulbs downplay the party features that are a staple of color-tunable bulbs. On the other hand, white smart bulbs are less expensive than color bulbs, making it more affordable to roll them out in multiple rooms.
We’ve tested just about every color and white smart LED bulb on the market. You’ll find links to all our reviews at the bottom of the page, and we’ll update this story as new models are introduced.
Philips was one of the first players in this market, and the company’s experience shows. Physically, its Hue Color and Ambiance bulbs haven’t changed much since their introduction in late 2012, but the latest generation lasts a lot longer and the company has added a Bluetooth radio that obviates the need for the Philips Hue Bridge (but most smart home denizens will want the Bridge anyway). The Philips Hue ecosystem is the industry’s deepest and broadest, including not only bulbs of every shape and size imaginable, but also indoor and outdoor fixtures as well, including the Philips Hue Calla pathway light and the Philips Hue Lily outdoor spotlight, both of which we like very much.
LIFX is a very strong competitor in the smart lighting space and comes a very close second place in our roundup. LIFX no longer has just A19 and BR30 form factors to offer, and we really like its unique LIFX+ (which has an array of infrared LEDs that will help your home security camera see in the dark), but Philips still delivers much more diversity in its ecosystem and universe of third-party support.
Our choice won’t surprise anyone who’s been following this market. Philips dominates this space and is also our top pick for best color LED smart bulb. The latest Hue bulbs can be controlled via Bluetooth or Zigbee (the latter requires the Philips Hue Bridge), they deliver high-quality light, and are backed by a strong warranty. We received the BR30 form factor for our review, but the bulb is also available in A19, candelabra, and even with vintage-style LED filaments.
The new Cree Connected Max line of smart bulbs is agressively priced and available in all the most popular form factors: A19, A21, BR30, and PAR38. The A19 Tunable White + Color Changing bulb we reviewed costs just $10, and it supports both Bluetooth and Wi-Fi, so you don’t need to factor in the added cost of a hub to integrate it into your smart home. It’s a very good product.
Most home security cameras are equipped with infrared LEDs to deliver a semblance of night vision. the LIFX+ is equipped with infrared LEDs of its own, which are active even when the bulb is turned off via software. Infrared light is invisible to the naked eye, but the LIFX+ can bathe a room in it so that your security camera can see more of the room and in more detail than it can with its own infrared LEDs.
The 2020 version of the Philips Hue Lightstrip Plus LED is the only strip light to support both Bluetooth and the more robust Zigbee protocol (if you’re willing to pay for the required bridge to connect it to your Wi-Fi network, that is). The very nature of LED light strips renders them delicate devices, and the first review product we received broke after a short amount of time (the second one is holding up just fine). But we haven’t encountered a competing device that’s as versatile as this one.
Smart light bulb protocols and features
Three control technologies continue to vie for leadership in the smart downlight market (Z-Wave is a major contender in smart lighting, but you won’t encounter it in bulbs—just in switches, plug-in modules, control panels, and smart-home hubs).
Zigbee: Bulbs that use the popular smart-home networking protocol require a bridge to communicate with your home Wi-Fi network. This is the technology Philips has adopted for its Hue lineup, but it’s not the only one.
Wi-Fi: This class of bulb talks directly to your Wi-Fi router, no hub or bridge required. LIFX and TP-Link both manufacture excellent Wi-Fi smart bulbs, but neither company comes close to Signify’s Philips Hue lineup in terms of the depth and breadth of the Hue ecosystem.
Bluetooth: These bulbs skip your home network altogether and pair directly with your smartphone or tablet. As such, they can’t be controlled from outside your home. GE and a number of other manufacturers make Bluetooth bulbs, some of better quality than others. Signify has recently added Bluetooth radios to its Philips Hue line of smart GU10 spotlight, which eliminates the need to deploy the Philips Hue Bridge. Taking the bridge out of the equation reduces the overall cost of deployment, but adds some limitations. You can read more in our review of the new Philips Hue bulbs.
Each of these technologies has pros and cons, so before you attempt to settle on a specific bulb, first try to determine which tech is right for you. If you want to hook your bulbs into a broader smart-home system—such as SmartThings or Nest—Bluetooth bulbs are out. You can control more than one bulb with your phone, but you can’t connect it to sensors or other systems inside your home. Don’t like the idea of pairing a bulb to your phone? A Wi-Fi bulb will work best for you, though you won’t have quite as many options as you’ll find with a Zigbee product.
Smart bulb, or smart switch?
There’s a significant argument about the best way to install smart lighting, and two approaches present themselves. You can either go with expensive smart bulbs and control them all individually, or you can use cheap dumb bulbs and install smart switches to control all the lights on that circuit. Both approaches make sense: With smart bulbs, the biggest issue is cost, but there’s also complexity to deal with. While bulbs can usually be grouped based on location, this is only as intuitive to manage as the bulb control app.
Smart switches, on the other hand, are far more complicated to install—to the point where some users might be uncomfortable dealing with exposed wiring and would prefer to hire an electrician. Smart switches, however, provide more flexibility in many installations.
Habituated from years of flipping hard-wired switches, many users (or their children) will instinctively use the wall switch to turn the lights out when they leave a room. Once that happens, all the apps in the world won’t be able to turn the light back on until the switch is returned to the on position. While this won’t be an issue if you install smart switches, they can’t change a bulb’s color or color temperature.
That said, smart bulbs, no matter what the technology, still won’t be right for everyone. Notably, most of these bulbs cannot be dimmed via a hardwired wall switch (it messes with the power going to the radio, rendering them useless). Some will fail even if a dimmer is present on the circuit and dialed up to full power. The quality of light from an LED bulb is likely to be much, much better.
The good news is that bulb prices are going down, so it’s easier to get started with 2.4G/IR LED bulb and less punishing should you find that a product doesn’t work for you. That said, we want to get you started on the right foot. So without further ado, here are deep dives into the most worthwhile color and white LED smart bulbs on the market.
|
|
|
How to Build a Boat Bench Seat? |
Posted by: mmws256w - 09-22-2021, 03:16 AM - Forum: Welcomes and Introductions
- No Replies
|
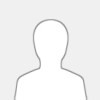 |
DIY projects allow you to achieve the result that you desire. Utilizing your skills and artistic talents is related to this matter, and it’s also a way to save some bucks. With regards to this, many boaters can manage how to build a boat bench seat by themselves.
You may have wood for building boat seats. Some upgrades can be done by adding cushion and vinyl. Once you choose a design, you can start collecting materials.
If you’re groping for design ideas, this article will show you DIY boat bench seats that will surely please you. You can follow them to refurbish or renovate a boat.
Various boat styles showcase different angles and lines. Wide and deep hulls are the main characteristics of workboats, while sailboats are thin and long. Nonetheless, a wooden banquette would be fantastic on both of these vessels. Here are the steps:
Step 1. Take off Metal and Trim
A banquette is a bench along the wall. Therefore, you have to consider the needed space and shape for it. The center section of the boat is where you need to lay down this project.
To get started, you have to remove metal or trim but you must keep the pieces for reconnection later on. You may also need to take off logos and insignias that are still useful.
Step 2. Cutting the Chosen Area
Use chalk to draw a line on your chosen area then you can run the chainsaw over it. Cutting the area should be even and consistent. You may need to tidy up the cutting with a circular saw.
You have to be attentive while doing it as there may be some screws. These tiny pieces of hardware may be hiding underwood plugs.
Step 3. Cleaning
Get rid of the debris created by cutting since it can block from cutting the bottom part.
Step 4. The Bench Base
Use two pieces of 2×4 wood and place them 16 inches above the pontoon boat furniture with the support from screws for wood. This step is not only for building the base but hull reinforcement as well.
Get ¾-inch plywood to be added over the 2×4 woods with screws. This will strengthen the structural integrity that may have temporarily gone due to the cuttings that were made.
Step 5. Seat Back
You may recycle some wood that just lay around or V-groove soffit panels. Get measurement from the seat to the boat anchor for the preparation of the seatback.
To ensure that you’re going to create comfortable seats, add horizontal wood blocks that tilt at a slight angle. Install the seatback with 15-gauge finish nails.
Step 6. Seat Attachment
You may choose any suitable wood for the seat. Mahogany and tropical hardwoods like ipe are the best examples. Pre-drilled screw holes should be done before assembling the parts. Make planks for the bench size that you like and fasten them with stainless wood screws.
Step 7. Painting the Banquette
If you use recycled wood with some paint on it, you need to sand it before applying a new coat.
Step 8. The Last Touch for Refinement
You have to add a routed edge over the wooden seat. Then, you can put back the metal and insignia that you removed when starting this project.
The finishing touches will be covering the back panels with new paint, applying oil on the wood to have an attractive sheen, and sealing the original parts with polyurethane.
When thinking of comfortable bench seats for boats, cushions and vinyl may be the first things that come into your mind. You can skip buying ones for your aluminum boat and instead, make them yourself for customization.
So, here’s a guide on how to make a boat rear bench seat if you don’t mind sewing some seat cover.
Making a rectangular box frame is the very first step. Make three sides for the lower portion, and they will touch the transom and the floor. Its top will be able to flip and access the engine.
Make some plywood strips based on the measurement of the bench seat. You may have a shop cut it for you. Some 1”x1.5” pressure treated lumber, waterproof wood glue, and 1” staples are the things that you need to put the pieces together.
After forming the box out of the plywood strips, get rid of splinters by sanding. This process can also break the edges to prevent damaging the vinyl. After sanding, you can apply two coatings of paint.
Once the glue has dried, place it on the designated area in your boat. It’s sturdy and it won’t give you problems.
Step 2. Setting the Vinyl Down
You don’t have to put vinyl at the bottom of the box. An extra piece is needed to be wrapped under the seat. Just apply more effort in working for a nice appearance and allow a vinyl skirt to hang.
Make sure to leave a margin of about half an inch for sewing the edges. This is enough to match the cording’s size. Use the double-sided tape to hold the cording and make it curved without twisting or binding.
If you know how to use the sewing machine, you’ll be fine. But if not, you can ask someone to do it for you. When vinyl is sewn properly, you can install the bench.
Step 3. Cutting the Foam
Measure the amount of foam that you need, then mark it. Cutting can be done with an electric knife. Give ½” extra to ensure that the vinyl cushion is stuffed nicely. When you have the right piece of foam, glue it on the top of the box.
Batting should be added on the sides for some cushioning with the roughly estimated size. It gives the seat a fuller look. Use a Loctite adhesive to glue it and trimming is needed once it sits in the right place.
Step 4. Adding the Vinyl by Stapling
Stapling creates a serious grip and adequate strength to hold the vinyl in place. It’s best to use stainless staples. You can begin on the opposing side and work your way to finish tucking the whole piece of vinyl.
Just keep pulling, stapling, and tucking to obtain a neat result. At this point, you have finished a bench seat or a motor box for your aluminum boat.
As long as you have time, resources, and willingness to work, there’s no reason that you won’t try following the steps on how to build a boat bench seat. You can choose the color, design, size, and materials that you like from these two guides.
Some boaters want to customize the looks of their boats to represent their personalities. No one is stopping you from doing so! It can be a technique to give life to an old boat. Also, you can always make a bench seat in a set-up that brings comfort.
Did you find this article helpful? If yes, share with anyone who would need this.
It’s the time of the year again when being out on the water is the best place to be. In the heat of the summer sun, there’s really nothing like sitting on a pontoon boat to just drift on a calm lake or spend an entire afternoon fishing. Pontoon boats get a lot of attention during the summer months, and it’s only right to take preventative measures in order to keep the health of your boat in check. One of the easiest ways you can do this is by protecting the pontoon’s seats using seat covers. If you’re thinking about buying pontoon folding boat seat covers, here is a quick guide on what you should look for.
Material
Pontoon seat covers are made out of many different kinds of materials. The lowest end in the spectrum would be a simple plastic tarp. Although plastic tarps will do the job of covering your seats, they aren’t particularly durable. Plastic tarps are great alternative for quick-fix solutions, but they are not permanent options.
The next step up to plastic would be canvas tarps. Canvas tarps have long been used as a general cover-up material in boating. They are more durable than plastic in many ways. However, they are also more susceptible to mildew and mold. Canvas tarps today are most often referred to as marine vinyl. It’s still a good alternative if you prefer to use it, but canvas is also easy to stain. Either way, your canvas will definitely protect your pontoon boat seats, but they won’t last as long untreated. If you want your marine vinyl to last longer and protect your flip up boat seat better, you can treat them a waterproof and/or UV spray. The best materials for pontoon seat covers are vinyl blends or polyester. These materials are highly durable and easy to take care of. They are also more resistant to the elements; therefore, they can protect your seats better. Most vinyl blends also offer some breathability factors, so mold and mildew won’t have much room to grow in—even in the most humid conditions.
Size
You might automatically think that larger is better when it comes to pontoon boat covers, but that’s not necessarily true. Although a larger size will allow you to cover more area, it’s important to measure fit more than anything. Since pontoon boats are exposed to the elements continually, a fitted seat cover will do a better job in protection. Any excess room caused by an unfitted cover will just be excess room for more water or air to enter and damage your pontoon seats.
This is why it’s important to measure your pontoon seats before you go out looking for seat covers. This article discusses how you can measure your seat covers properly. Once you have the dimensions written down, you can then continue shopping for pontoon seat covers. Make sure you check your dimensions against the size of the covers before you purchase. It also helps to read reviews regarding the size of the cover from those that have purchased the same product before. You can also get information from the manufacturer of both the seat cover and your low back folding boat seat.
Other things to look for
Apart from material and size to consider, you might want to also think about a few other things before you buy a pontoon seat cover. First, you might want to think about ease of use and storage. When you’re not using your pontoon seat covers, where are they going to go? Can they easily be folded up and stowed away someplace on your pontoon boat?
There are also seat covers that might utilize the use of zippers or elastic. Some people prefer seat covers that will just slip over your pontoon seats. But there are others that are so fitted; you’d have to zip them up in place. There are seat covers that come with enclosures and others that don’t. It might not matter to some people, but style and color matter to others. You might find that a lot of pontoon seat covers come in a white color, neutral, or blue color. Whites and neutral colors reflect the sunlight better than darker colors.
|
|
|
Development of a Wireless Temperature Sensor Using Polymer-Derived Ceramics |
Posted by: mmws256w - 09-22-2021, 03:15 AM - Forum: Welcomes and Introductions
- No Replies
|
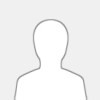 |
A temperature sensor has been developed using an embedded system and a sensor head made of polymer-derived SiAlCN ceramics (PDCs). PDC is a promising material for measuring high temperature and the embedded system features low-power consumption, compact size, and wireless temperature monitor. The developed temperature sensor has been experimentally tested to demonstrate the possibility of using such sensors for real world applications.
1. Introduction
Accurate temperature measurements are crucial for many applications, such as chemical processing, power generation, and engine monitoring. As a result, development of temperature sensors has always been a focus of microsensor field. A variety of materials have been studied for temperature sensor applications, for example, semiconducting silicon and silicon carbide. Silicon based sensors are typically used at temperatures lower than 350°C due to accelerated material degradation at higher temperature [1, 2]. Silicon carbide based sensors are better than silicon based sensors in high temperature measurement and can be applied in temperatures up to 500°C [3–5].
Polymer-derived SiAlCN ceramics (PDCs) are another widely studied material that demonstrate properties such as excellent high temperature stability [6] as well as good oxidation/corrosion resistance [7]. PDCs have been considered as a promising material for measuring high temperature [8]. Our early works have showed that PDC sensor head can accurately measure high temperature up to 830°C [9] using data acquisition system from National Instruments. The cost and size of the sensor system must be significantly reduced before it can be deployed for real world applications. In this paper, we develop a temperature sensor using PDC and an embedded system. Comparing to the National Instruments data acquisition equipment used in the previous paper, the newly developed embedded sensor is much smaller (9.7 dm3 versus 0.3 dm3), lighter (5.97 kg versus 0.19 kg), and cheaper (approximately $8000 versus $170). A WiFi module is also added so the temperature measurement can be transmitted wirelessly. The embedded board and WiFi module used in this paper are commercially available. The experiments in this paper demonstrate the possibility of deploying PDC based sensors for real world applications.
2. Fabrication of the PDC Sensor Head
In this study, the PDC sensor head is fabricated by following the procedure reported previously [9]. In brief, 8.8 g of commercially available liquid-phased polysilazane (HTT1800, Kion) and 1.0 g of aluminum-tri-sec-butoxide (ASB, Sigma-Aldrich) are first reacted together at 120°C for 24 hours under constant magnetic stirring to form the liquid precursor for SiAlCN. The precursor is then cooled down to room temperature, followed by adding 0.2 g of dicumyl peroxide (DP) into the liquid under sonication for 30 minutes. DP is the thermal initiator which can lower the solidification temperature and tailor the electrical properties [10]. The resultant liquid mixture is solidified by heat-treatment at 150°C for 24 hours. The disk-shaped green bodies are then prepared by ball-milling the solid into fine powder of ~1 μm and subsequently uniaxially pressing. A rectangular-shaped sample is cut from the discs and pyrolyzed at 1000°C for 4 hours. The entire fabrication is carried out in high-purity nitrogen to avoid any possible contamination.
Pt wires are attached to the sensor head by two ceramic fasteners on the two mounting holes on the diagonal of the sensor head. To improve the conductivity, both mounting holes are coated with Pt plasma; see Figure 1.
To measure temperature using the PDC sensor, the processor needs to perform the following tasks: () supply voltage to the circuit through DAC7724; () sample the circuit output using AD7656 and convert the output to temperature measurement; and () transmit data to readers from the RS232 port.
The input signal to the conversion circuit is a sinusoidal signal of ±10 V. The sinusoidal signal can bypass the parasitic capacitor in series to the PDC probe. The noise from the furnace coil can also be greatly subdued. The sensor output voltage is approximately sinusoidal as well and its magnitude can be computed using Fast Fourier Transformation (FFT) or curve fitting using recursive least square method (RLSM) [11]. Comparing to FFT, RLSM is more computationally efficient but may have numerical instability because TMS320F28335 only supports IEEE 754 floating-point arithmetic. Here we prefer FFT for fast prototyping purpose because Texas Instruments provides FPU library that performs floating FFT routines on C2000 series microcontroller. Next we explain how the sensor works.
A high-priority interrupt service request (ISR1) based on a CPU timer continues reading a look-up-table and drives the DAC7724 to generate the input signal . The frequency of is controlled by the frequency of ISR1. ISR1 also samples circuit output from AD7656 and adds the data to a 1024-point buffer if there is no FFT running. Once the buffer is filled up, ISR1 stops writing the buffer and the FFT routine starts. The FFT routine is implemented in another slower low-priority interrupt service (ISR2). Once the FFT routine is completed, ISR2 will give ISR1 the permission to clean and write the input buffer again. The magnitude from the FFT is used as the circuit output . The software flowchart is shown in Figure 4.
High temperature sensors capable of operating in harsh environments are needed in order to prevent disasters caused by structural or system functional failures due to increasing temperatures. Most existing temperature sensors do not satisfy the needs because they require either physical contact or a battery power supply for signal communication, and furthermore, neither of them can withstand high temperatures nor rotating applications. This paper presents a novel passive wireless temperature sensor, suitable for working in harsh environments for high temperature rotating component monitoring. A completely passive LC resonant telemetry scheme, relying on a frequency variation output, which has been applied successfully in pressure, humidity and chemical measurement, is integrated with a unique high-k temperature sensitive ceramic material, in order to measure the temperatures without contacts, active elements, or power supplies within the sensor. In this paper, the high temperature sensor design and performance analysis are conducted based on mechanical and electrical modeling, in order to maximize the sensing distance, the Q factor and the sensitivity. In the end, the sensor prototype is fabricated and calibrated successfully up to 235ºC, so that the concept of temperature sensing through passive wireless communication is proved.
This paper aims to develop a prototype for a web-based wireless remote temperature monitoring device for patients. This device uses a patient and coordinator set design approach involving the measurement, transmission, receipt and recording of patients’ temperatures via the MiWi wireless meter iot solution. The results of experimental tests on the proposed system indicated a wider distance coverage and reasonable temperature resolution and standard deviation. The system could display the temperature and patient information remotely via a graphical-user interface as shown in the tests on three healthy participants. By continuously monitoring participants’ temperatures, this device will likely improve the quality of the health care of the patients in normal ward as less human workload is involved.
Background
During the severe acute respiratory syndrome (SARS) outbreak in 2003, hospitals became treatment centres in most countries. Because a patient’s core body temperature is one vital parameter for monitoring the progress of the patient’s health, it is often measured manually at a frequency ranging from once every few hours to once a day [1]. However, such manual measurement of the temperature of patients requires the efforts of many staff members. In addition, when the patients suffer from conditions that result in abrupt changes of the core body temperature, e.g., due to infection at a surgical site after surgery, the staff on duty will not know such a temperature change occurred until the next temperature measurement. Such a delay may lead to patients being unnoticed while their health conditions worsen, which is dangerous because a difference of 1.5 degrees Celsius can result in adverse outcomes [2]. Furthermore, there is always a need to have a monitoring system to improve the quality of health care [3], such as temperature monitoring of elderly and challenged persons using a wireless remote temperature monitoring system.
Body temperature can be used to monitor the pain level of a patient following an operation [4] or after shoulder endoprosthesis [5]. In some cases, the tissue transient temperature was monitored during microwave liver ablation [6] for the treatment of liver metastases. Instead of using a temperature sensor, pulse-echo ultrasound [7] was used to visualize changes in the temperature of the patient’s body. In addition, a non-contact temperature-measuring device, such as a thermal imaging camera [8], was successfully used to detect human body temperature during the SARS outbreak. However, it can be quite expensive to equip each patient room with a thermal imaging camera. In addition, there are a few wireless temperature measuring solution (e.g., CADIT™, Primex™, and TempTrak™) on the market that are used to monitor and store a patient’s temperature for medical research by using body sensor networks [9]. Most of these systems consist of an electronic module and a temperature-sensing device. The systems include a stand-alone electronic module with a display screen that allows the temperature sensor data to be transmitted over a secure wireless network.
However, these systems can be difficult to reconfigure to suit the current database system used in the hospital. In addition, the current systems using short message service (SMS)-based telemedicine [10] systems with hardware equipment were developed to monitor the mobility of patients. However, proper hardware and software to manage the messages and the patient’s temperature for display on mobile phones are not widely available.
Hence, a medical device to continuously measure the body temperature of patients using a wireless temperature receiver [4,11,12] is required. With such a wireless temperature sensor system, nurses will no longer have to manually measure the temperature of patients, which will free their time for other tasks and also reduce the risk associated with coming into contact with patients with contagious diseases, such as SARS. The readings will be transmitted wirelessly to the central nurse station, where they can be monitored by the staff-on-duty. In addition, the current and past history of the body temperature measurements can be stored in an online database, which allows the medical staff to access the database when they are not in the hospital.
To the best of our knowledge, a MiWi wireless (besides using the Zigbee[11]) temperature-monitoring system using a patient and coordinator set design that provides remote internet access to the temperature database has not been reported in any publication. The objective is therefore to develop and implement a prototype temperature-monitoring system for patients using a MiWi wireless remote connection to the nurse’s station for frequent real-time monitoring. The temperature monitoring system was designed based on a proposed patient and coordinator set design approach. The proposed temperature-monitoring system for use in normal ward will likely to improve the quality of the health care of the patients as the nursing workload is reduced. In this paper, the discussion on medical regulations and policy will not be included.
|
|
|
Bapak Prediksi |
Posted by: bapakprediksi - 09-19-2021, 02:39 PM - Forum: Off Topic
- No Replies
|
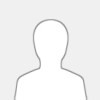 |
Silahkan ajak teman anda untuk melihat prediksi bola dan skor akurat malam ini berupa h2h, ou bersama situs resmi yang dapat dilihat secara gratis di bapakprediksi
|
|
|
How Do Air Compressors Work? |
Posted by: E234B - 09-18-2021, 06:10 AM - Forum: Off Topic
- No Replies
|
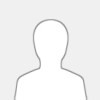 |
How Do Air Compressors Work?
How Do Air Compressors Work?
Air compressors are an invaluable tool for both industrial work and DIY at home, and there are several different types to choose from depending on the job you need doing. Air compressors have a number of uses, such as to fill gas cylinders for industrial purposes and scuba diving, to create the power needed to run pneumatic tools and spray guns, for pumping up automotive tyres, and within heating and air conditioning systems.
As we’ve touched on here, there are myriad uses for screw air compressor both in commercial and domestic environments. Within the category of air guns, there are several types, each of which is suitable for a different job. We’ve compiled a guide to all the major types of air compressor, how they work and how they differentiate from one another.
Whether you’re an engineering manager or in charge of facilities for your company, being informed about how air compressors function and what they’re used for is handy and can help you make the proper decisions for your business and industry.
Get all the information you need to know about air compressors, complete with the infographic below, with our comprehensive guide. We’ll address the benefits of using premium air compressors in your industry, as well as the questions of ‘what are compressors?’ and ‘how does a compressor work?’, covering all the essentials in one convenient place.
The infographic below shows how a Hydrovane series rotary sliding vane air compressor works
Since their invention in the 19th Century, mechanical, automated air compressors have continued to be one of the most widely used tools in industrial settings. Air compressors provide a continuous stream of power that is safer and cooler than many other forms of energy. For many industries, such as metal work and mining environments, air compressors are an absolutely essential tool. After the basic utilities of water, gas and electric, compressed air is actually considered to be the fourth utility.
Air compressors are also an affordable choice of tool for many manufacturing jobs, as they are durable, and high quality types require minimal maintenance and repairs.
Between the two main categories of compressor – the scroll (piston) compressor and the rotary screw (reciprocating) compressor, you have a tool for every type of industrial and commercial setting, as well as various domestic uses.
The most common types of regular screw air compressor are single and dual phase, both of which operate in the same fundamental way, only dual phase has one more step involved in the compression process. In a single phase compressor, there is one chamber and the air is compressed a single time; in a dual phase, there are two chambers and the air is put through compression twice.
Be careful not to confuse single and dual phase compressors with the number of cylinders a compressor has. Both types of compressor use two cylinders; one-cylinder compressors are less common, because air balancing is made easier with two cylinders. The difference between single and dual stage compressors is that in the former the cylinders are both the same size; in the latter they are different sizes.
How Do Single and Dual Phase Compressors Operate?
Single phase compressors, also referred to as piston air compressors, works in a relatively simple and straightforward way. First, air is drawn into the cylinder; from here, it is compressed once by a single piston movement within a vacuum system.
The power of this compression is measured in PSI (pounds per square inch) or Bar – the higher the PSI/Bar, the more power the compressor has. In a single stage air compressor, the air is typically compressed at a rate of around 120 PSI (8.2 Bar). After the air has been compressed, it is sent into the storage tank from where it is dispelled into various tools as a source of energy.
Dual phase compressors operate the same way, except there are two stages of compression, rather than just one. After the first round of compression, the air is sent into a second chamber, where it is compressed for the second time, at a rate of around 175 PSI (12.1 Bar). After this, the air is sent to a storage tank in which it is cooled down and ready for application.
Both types of compressor are typically powered by either an electric or petrol motor, which drives the piston and causes the compression to happen.
Single Phase and Dual Phase Applications
Both function in fundamentally the same way and can be used for similar tasks, such as operating a pneumatic drill or other high-powered tools such as those found in a manufacturing plant.
Single phase compressors tend to be used within domestic settings for smaller workshop jobs done with handheld tools, such as woodwork, metal work and general DIY.
Dual phase compressors, on the other hand, are better for larger scale work in operations such as operations needed in vehicle repair shops, pressing factories and other plants where parts are manufactured.
Oil-Free vs. Oil-lubricated Air Compressors
Another way to compare variable frequency air compressor is to look at whether they use oil or not – there are oil-free and oil-based / lubricated compressors and both are suited to slightly different jobs. For the air to be drawn into the chamber safely and effectively, the piston needs to be in top working order. To work properly, the piston must be lubricated with oil.
With regards to lubrication, there are two main types of compressor to choose from: oil-free and oil-based. The oil is used on the cylinder to ensure the compression goes smoothly.
The Difference Between Oil-Free and Oil-Based Compressors
Oil-free air compressors already have a lubricated cylinder (often with a non-stick material such as Teflon) and therefore require no further maintenance to work properly. Oil-based compressors require oil to be added to the piston area and changed regularly. Just how often you need to change the oil will be outlined in the manufacturer’s manual that came with your compressor.
On the whole, oil-free compressors tend to weigh a lot less than oil-based compressors, as not only do they not have the weight of the oil, but they are more compact machines, requiring fewer separate parts to make them work. Oil-free compressors, being less complex in design, also tend to be more affordable than oil-based compressors.
However, although they’re more weighty and expensive, oil-based compressors have their benefits. For one thing, they are strong and durable, and usually have a longer lifespan than their oil-free counterparts. This is usually because over time the greasing material (usually Teflon) begins to wear down and lose its lubrication abilities.
Another important factor that should be considered when choosing between an oil-free and oil-based compressor is that the oil-less version tends to heat up faster and to a higher temperature than those which use oil. Compressors without oil also make a lot more noise than those with, so if you want a less noisy workplace, this is a factor to consider too.
Oil-Free and Oil-based Compressor Applications
Oil-free compressors are a great option for those in need of a lightweight, low maintenance tool for home use. Oil-based compressors are better suited to heavy duty jobs and commercial and industrial use, as although they’re generally heavier and require more maintenance, they are also more robust and versatile.
For industrial purposes and extensive, day-long use, oil-based compressors are by far the best option. If you’re looking to invest in quality compressors for your business, opting for oil-based machines is almost certainly the best route to take.
Within an industrial or commercial setting, there are numerous uses for oil-based PM screw air compressor, including:
Vehicle painting and repairs
Sanding and woodwork
Creating snow banks in ski centres
Tools within dentistry and other medical environments
Pneumatic construction tools such as nail guns
Air cleaning tools such as blowguns
Oil-free compressors can be used for domestic use, such as small-scale jobs like blowing up balloons, home workshop and DIY jobs. They are also largely used in industries where there is a need to avoid the product or consumer coming into contact with oil: food and beverage, pharmaceutical and dental, for example. In these sensitive applications, the consequences of having oil contamination in the air are too high to risk, so having an oil free compressor is a must. There is compressed air quality testing from the International Organisation for Standardisation (ISO) which oil-free technology can help you achieve.
Fixed vs. Variable Air Compressors
Another factor to consider when choosing the right type of air compressor for your industry is whether they’re equipped with fixed or variable speed. Let’s take a closer look at what these different types of compressor can do for you.
The main difference between air compressors that use a fixed speed system and those that use variable speed is the manner in which the motor gets its power. The compression element is much the same across all machines, but the way the motor operates has an effect on the usability, efficiency and lifespan of the machine.
How Do VSD Compressors Work?
Variable speed compressors (often referred to as VSD (Variable Speed Drive) or VFD (Variable Frequency Drive) – compressors) operates by automatically adjusting the motor speed in accordance with the demand for air. This happens through a system that converts voltage from the mains power supply into a variable frequency.
Power is drawn through a converter, inside which it is converted twice. First, it converts AC power into DC power using diodes. A capacitor then cleans the AC, and then converts it to DC using a transistor, which acts as switches. These switches control the frequency of power sent to the motor, which in turn controls the speed of the motor.
A VSD air compressor contains this technology, allowing the speed of the motor and the amount of air compression used to be closely controlled. There are pros and cons to both variable speed compressors and their counterpart, fixed speed compressors – check them out below to decide which one is best for your industry.
Fixed Speed Pros and Cons
Fixed speed air compressors send a consistent, continuous stream of power into the motor, which gives you a reliable frequency in all your air compression jobs. The initial cost of fixed speed compressors is lower than that of variable speed compressors, is easier and cheaper to maintain and is a must-have within industries where the power demand is continuous.
This type of compressor is, however, less efficient than its variable speed counterpart. It is also less efficient at saving energy, and can therefore be more expensive to run, with fewer incentives available too.
Variable Speed Pros and Cons
Variable speed air compressors allow you to control the voltage and the frequency of the power in the motor, giving the user more agency over the tool. This type of compressor is more efficient when it comes to power usage, as you can easily control your output and only use what you need. Many industries will find that this type of air compressor is ideal, as it can be used in line with the demand of the job. When less power is needed, you can easily adjust the speed of the compressor, saving money and protecting the environment at the same time.
The downsides of a variable speed compressor are that there is a higher initial capital cost to pay, and maintenance and repairs are more expensive too. They are also not well suited to applications that require a continuous stream of power.
Piston Compressors, Scroll Compressors & Rotary Screw Compressors
So far in this article, all the compressors mentioned are operated using pistons, which is a generic system for one type of compressor – the scroll compressor, also known as a reciprocating air compressor. The other type is the rotary screw compressor, which doesn’t have pistons and operates in a slightly different way.
Here’s a quick overview of how scroll compressors and rotary screw / reciprocating compressors work, and what the unique benefits are of each of them.
Scroll Compressors
Scroll compressors are a type of piston compressor, and are also called reciprocating compressors. These are the most common type of two stage air compressor, due to affordability and general availability. But how does a reciprocating air compressor work? The piston system works by having a piston travel downwards, decreasing the pressure inside its internal cylinder through the creation of a vacuum. The sudden change in pressure causes the door of the cylinder to be forced open, and draw air in. When the piston travels up again, the air is forced out of the cylinder at a much higher pressure point. This continues in a reciprocating, ‘scroll’ pattern, hence its name.
Pros and Cons of Scroll Compressors
Pros:
Cools down quickly
More efficient use of energy
Cons:
Higher initial capital cost
More complex parts – harder to maintain
Rotary Screw Compressors
Rather than using pistons, rotary screw compressors rely on rollers to do the compression. Rollers are positioned just off the middle of the central shaft to ensure that one side of the roller is always in contact with the wall. The rollers are powered, rotating extremely fast, causing the same result as scroll compressors: they draw in air at a low pressure and force it out at a higher pressure.
Pros and Cons of Rotary Screw Compressors
Pros:
Good power capacity
Lower initial capital price
Easy to maintain
Cons:
Limited cooling abilities
Require continuous maintenance checks
How Do Low Noise Air Compressors Work?
One complaint often heard around air compressors is that some of them are noisy due to friction and a power source, which can be distracting and inconvenient for both commercial and domestic use. The industry has risen to deal with these complaints however, and there are several low noise air compressors to choose from, offering a decibel rating of around 40 dB.
40 dB is considered low noise; 60 dB is considered the safest decibel level for compressors; anything over 85 dB could cause long-lasting damage to your hearing, and you should avoid being exposed to this level for extended periods of time.
Low noise and silent air compressors are available in both oil-free and oil-based versions, so just how is the silencing effect achieved?
As well as choosing compressors with low decibel levels, one aspect of this technology that makes a big difference is the inclusion of an acoustic chamber for containing the noise. Another tip is to opt for electric-powered compressors, rather than gas-powered, as the former type of power source makes for a quieter machine.
The Bottom Line
Which type of air compressor you go for depends on a variety of factors. You first need to consider what application the compressors will be used for? Do you need it for continuous, ongoing use in large industrial machinery, or will it be used sporadically? Your answers to these questions will help you decide on whether to go for variable or fixed speed compressors.
Another question that you must factor into your decision is: how much do you want to spend? Remember that the initial price of a quality compressor is not the only expense associated with a compressor; consider also the cost of the power needed to run the machine, plus any related ongoing maintenance and repair costs. How much time and energy will investing in high quality compressors save your company? These are all important calculations that should be made before making your decision.
Get in touch below if you wish to find out more.
|
|
|
Bulk SMS – The Future of Mobile Advertising |
Posted by: jamesgood - 09-18-2021, 06:07 AM - Forum: Off Topic
- No Replies
|
 |
在互联网世界中,群发短信是继 澳大利亚手机号码数据库 电子邮件和即时消息(聊天)之后发生的第二件好事。今天,它的受欢迎程度已经成倍增长。每个行业,无论是企业还是教育机构,每个人都 澳大利亚手机号码数据库 知道它的重要性。这是与客户取得联系的最快方法之一。群发消息使您只需点击几下按钮,即可向目标客户发送产品发布、折扣销售和促销活动等信息。几分钟之内,这条短信就传到了全球成千上万的人。使用这项技术只需要一台个人电脑和一个互联网连接。随着移动 澳大利亚手机号码数据库 用户数量的迅猛增长,群发短信的前景一片光明。群发 SMS 服务提供商是提供启动移动营销活动所需设置的公司。它们构成了网络运 澳大利亚手机号码数据库 营商和最终用户之间的重要联系。这些实体与网络运营商合作,为最终用户提供一个轻松的平台,以便在全球范围内快速、高效和有效地发送大量消息。
批量 SMS 提供商通常提供基于 Web 的软件,该软件使用 SMS 网关 澳大利亚手机号码数据库 服务器发送短消息。该软件还内置了移动用户数据库。您还可以使用自己定制的手机号码列表。要知道什么是群发短信服务,您首先需要了解短信及其用途。嗯,SMS 代表短消息服务它通常在全球范围内从部手机 澳大利亚手机号码数据库 发送到另部手机然而营销人员认识到其作为联系潜在客户的绝佳工具的潜力很快,广告公司开始使用这项技术从台式电脑以短信的 澳大利亚手机号码数据库 形式向手机用户发送广告。批量 SMS 使用 SMS 网关服务器来完成此任务。移动广告已大举进入我们的生活。它被吹捧为增长最快的广告平台之一。随着越来越 澳大利亚手机号码数据库 多的人从传统和过时的手机转向智能手机,世界将会崛起。
智能手机允许用户下载和运行 澳大利亚手机号码数据库 第三方免费应用程序。这些应用程序在顶部带有横幅广告,可以快速建立品牌名称。然而,即使在今天,普通手机的数量仍然大大超过智能手机。这意味 澳大利亚手机号码数据库 着文字广告将继续在移动广告中发挥重要作用。另一个引起移动广告公司青睐的途径是视频。人们并不反对在他们的手机上观看视频。移动视频广告比其网络广告具有更高的参与商数,使其成为宣传产品发布和服务的有希望的候选者。另一个推动移动广告发展的 澳大利亚手机号码数据库 因素是平板电脑的普及。最终用户不介意在应用程序窗口顶部占据很小空间的横幅。只要广告不引人注目,用户就会继续 澳大利亚手机号码数据库 下载此类实用程序,这意味着他们将在不知不觉中与广告产品和服务进行交互。
|
|
|
Effectiveness of Air Filters and Air Cleaners in Allergic Respiratory Diseases |
Posted by: E234B - 09-18-2021, 06:05 AM - Forum: Off Topic
- No Replies
|
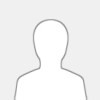 |
Effectiveness of Air Filters and Air Cleaners in Allergic Respiratory Diseases
Effectiveness of Air Filters and Air Cleaners in Allergic Respiratory Diseases
Air filtration is frequently recommended as a component of environmental control measures for patients with allergic respiratory disease. Residential air filtration can be provided by whole house filtration via the home’s heating, ventilation, or air conditioning system, by portable room air cleaners, or a combination of the two. Appliances to filter the sleep breathing zone also have been developed. High-efficiency whole house filtration, high-efficiency particulate air sleep zone air filtration, and high-efficiency particulate air room air cleaners all appear to provide various degrees of benefit. Recent studies of various types of filtration, used alone or as part of more comprehensive environmental control measures, are reviewed.
Keywords: Air cleaner, Air filter, Air filtration, Breathing zone, CADR, Clean air delivery rate, Environmental control, Furnace filter, HEPA, HVAC, Indoor air, Indoor allergens, Intervention measures, Ozone, Particulate matter, PM, Room air cleaner, Sleep breathing zone, Ventilation, Whole house filtration
Environmental control practices (ECPs) are a group of measures recommended to reduce exposure to indoor allergens (eg, dust mites, household pets, cockroaches, mold, mice) or nonallergic triggers (eg, environmental tobacco smoke [ETS], wood smoke, volatile organic compounds, particulate matter [PM]) [1]. Historically, many of the common suggestions have been empiric and not based on scientific data or evidence-based clinical trials. As a better understanding of the impact of the characteristics of housing stock [2, 3] and occupants [4] on the indoor living environment has evolved, more effective measures have been identified. These may include modification of the occupant’s habits, remediation, and/or modification of the dwelling and its furnishings, structure, or ventilation, including the use of air filtration. One major drawback in many ECP studies has been the focus on a single allergen (eg, dust mites [5]) or intervention (eg, room air filtration for cat or dog allergy [6–8]). In fact, most allergic individuals have polysensitivity to multiple allergens. ECPs are therefore much more likely to be beneficial if targeted against triggers or allergens known to be problematic for the individual.
In the case of filtration, little attention has been paid to variations among the various appliances themselves, and no clinical comparisons have been done between the benefits of whole house filtration (WHF) versus those of portable room air cleaners (PRACs). According to the most recent American Housing Survey, 75% of US housing units have ducted forced air heat, while 63% have ducted central air conditioning [9]. When used in combination, these ducted heating systems are termed heating, ventilation, air conditioning (HVAC) systems. HVAC systems offer the opportunity for WHF, but poorly maintained or contaminated systems may actually increase the risk of asthma and other allergic respiratory symptoms [10]. Simple forgetfulness by the occupants in replacing the filter at suggested maintenance intervals may be the most common issue. HVAC service technicians frequently find round air filter that have not been changed for years when providing repair or maintenance services [11]. Dirty filters themselves can become a source for air contamination by allergens, particularly fungal spores [12], and can then be trapped, colonized, and released downstream as the overloaded filter fails [13]. Other issues, including air bypass from poor filter fit and duct leakage, may further confound the effectiveness of filtration in HVAC systems.
A barrier to proof of effectiveness for ECPs is the complexity of the gene–host–environment interactions. Expectations have been tainted by the fact that short-term drug studies of only a few weeks’ or months’ duration can show statistical effectiveness for improvement of symptoms. However, despite major advances in the drugs available for the treatment of allergy and asthma, none have been shown to arrest disease progression permanently. Improved understanding on how to avoid or reduce triggers would be expected to have this benefit. This may not occur in the short term. Observational epidemiology has already led to the recognition of a wide range of triggers found in the indoor environment, ranging from dust mite to diesel exhaust particulates. Applied epidemiologic studies are helpful in understanding targeted avoidance and prevention of disease progression.
Morgan et al. [14], as part of the Inner-City Asthma Study Group, conducted a randomized controlled trial of comprehensive ECPs in 937 children with atopic asthma. All were sensitized, as demonstrated by positive skin test, to at least one indoor allergen. A baseline home evaluation included both direct visual inspections and dust collection from the child’s bedroom. Targeted ECPs were then implemented based on skin testing results and the home evaluation. Interventions included the use of a high-efficiency particulate air (HEPA) room air cleaner in the child’s bedroom if the child was exposed to ETS, sensitized and exposed to cat or dog allergens, or sensitized to mold. The intervention group reported significantly fewer symptoms of asthma during the intervention year and the follow-up year. The maximal number of days with symptoms was lower in the intervention group by 0.82 day per 2-week period in the first year (P?<?0.001) and 0.60 day per 2-week period in the second year (P?<?0.001). This effect is similar to that described in placebo-controlled studies of inhaled corticosteroids. The authors concluded that an “individualized, home-based, comprehensive environmental intervention decreases exposure to indoor allergens, and results in reduced asthma-associated morbidity.” This study and its outcomes represent the current thought that multiple ECPs, but not single interventions, are effective in modulating symptoms of allergic disease.
A recent review of 3,727 adults with asthma by Roy and Wisnivesky [15], using data from the Four-State National Asthma Survey, examined the association between preventive asthma care and comprehensive ECPs. Comprehensive management was defined as the implementation of combinations of at least five of eight measures. Air filtration was found to be the fourth (27.4%) most commonly implemented strategy, preceded only by no smoking (80%), no pets (53.9%), and washing sheets in hot water (43.2%), and followed by pillow covers (23.7%), mattress covers (23.4%), no carpets (14.5%), and use of a dehumidifier (13.8%). A similar study in the pediatric population found the same rate of air filtration (27.4%) use in the households of asthmatic children [16].
The role of air filtration in providing relief for individuals with allergic respiratory illness has been studied for more than 40 years [17, 18]. Prior reviews of air filtration have focused primarily on PRACs and the effect on patient symptom scores [19–21]. Reisman [19] stated that the studies should focus only on IgE-proven disease and HEPA PRACs. Wood [20] concluded that while HEPA PRACs may be an option for cat and dog allergy, there was no evidence they were effective for dust mite or mold allergy. Focusing only on allergies does not take into consideration the effects of PM and other indoor air pollutants. McDonald et al. [21] reported a meta-analysis of the only 10 randomized controlled trials on filtration published from 1973 through 1999. All 10 trials included asthmatic patients. The authors found a small statistically significant improvement in total symptoms and sleep disturbance associated with use of air cleaners, but no improvement in nasal symptoms, medication use, or peak expiratory flow (PEF) values.
In a 2010 rostrum article, Sublett et al. [22??] provided a comprehensive review of air filtration. The authors described the characteristics of airborne particulates, including allergens, to be filtered, and pointed out that the impact of inhalable PM and the effect on disease is not always IgE mediated. Residential air-cleaning products and devices are categorized into two broad categories: WHF (ie, filters or cleaners that are installed on the central HVAC system) and free-standing PRACs. Current standards for testing to determine the American Society of Heating, Refrigeration, and Air-Conditioning Engineer’s (ASHRAE) minimum efficiency rating value (MERV) for furnace filters and the Association of Home Appliance Manufacturers rating system clean air delivery rate (CADR) for room air cleaners are outlined. They also described the results of 18 studies on air filtration from 1973 to 2009, including some studies previously reviewed. The authors concluded that for the “optimal choice of cleaning devices, initial cost and ease of regular maintenance should be considered. PRACs with HEPA filters, especially those that air breather filter the breathing zone during sleep, appear to be beneficial. For the millions of households with forced air HVAC systems, regular maintenance schedules and the use of high-efficiency disposable filters appear to be the best choices.” They, as had previous reviewers, recommended that more rigorous study methods be applied to future research on air filtration and that the studies be of sufficient duration to show effectiveness.
Since the Wood [20] and McDonald et al. [21] reviews, there have been 14 studies (Table 1) published that are applicable to the role of air filtration as an environmental control measure for allergic respiratory diseases.
Urbanization increased population density in cities and consequently leads to severe indoor air pollution. As a result of these trends, the issue of sustainable and healthy indoor environment has received increasing attention. Various air filtration techniques have been adopted to optimize indoor air quality. Air filtration technique can remove air pollutants and effectively alleviate the deterioration of indoor air quality. This paper presents a comprehensive review on the synergistic effect of different air purification technologies, air filtration theory, materials and standards. It evaluated different air filtration technologies by considering factors such as air quality improvement, filtering performance, energy and economic behaviour, thermal comfort and acoustic impact. Current research development of air filtration technologies along with their advantages, limitations and challenges are discussed. This paper aims to drive the future of air filtration technology research and development in achieving sustainable and healthy building ventilation.
The most effective ways to improve your indoor air are to reduce or remove the sources of pollutants and to ventilate with clean outdoor air. In addition, research shows that filtration can be an effective supplement to source control and ventilation. Using a portable air cleaner and/or upgrading the cone air filter in your furnace or central heating, ventilation, and air-conditioning (HVAC) system can help to improve indoor air quality. Portable air cleaners, also known as air purifiers or air sanitizers, are designed to filter the air in a single room or area. Central furnace or HVAC filters are designed to filter air throughout a home. Portable air cleaners and HVAC filters can reduce indoor air pollution; however, they cannot remove all pollutants from the air.
The following publications provide information on portable air cleaners and on HVAC and furnace filters commonly used in homes.
Heating ventilation and air conditioning system (HVAC) is very important for offices building and human health. The combining filter method was used to reduce the air pollution indoor such as that particulate matter and gases pollution that affected in health and productivity. Using license plate frame in industrial HVAC systems (factories and manufacturing process) does not enough to remove all the indoor pollution. The main objective of this study is to investigate the impact of combination filters for particle and gases removal efficiency. The combining method is by using two filters (particulate filter pre-filter and carbon filter) to reduce particle matter and gases respectively. The purpose of this study is to use minimum efficiency reporting value (MERV filter) rating 13 and activated carbon filter (ACF) to remove indoor air pollution and controlling the air change rate to enhance the air quality and energy saving. It was concluded that the combination filter showed good removal efficiency of particle up to 90.76% and 89.25% for PM10 and PM2.5 respectively. The pressure drop across the filters was small compared with the high-efficiency filters. The filtration efficiency of combination filters after three months' was better than efficiency by the new MERV filter alone.
|
|
|
Recent trends and future of pharmaceutical packaging technology |
Posted by: E234B - 09-18-2021, 06:00 AM - Forum: Off Topic
- No Replies
|
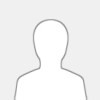 |
Recent trends and future of pharmaceutical packaging technology
Recent trends and future of pharmaceutical packaging technology
The pharmaceutical package market is constantly advancing and has experienced annual growth of at least five percent per annum in the past few years. The market is now reckoned to be worth over $20 billion a year. As with most other packaged goods, pharmaceuticals need reliable and speedy packaging solutions that deliver a combination of product protection, quality, tamper evidence, patient comfort and security needs. Constant innovations in the pharmaceuticals themselves such as, blow fill seal (BFS) vials, anti-counterfeit measures, plasma impulse chemical vapor deposition (PICVD) coating technology, snap off ampoules, unit dose vials, two-in-one prefilled vial design, prefilled syringes and child-resistant packs have a direct impact on the packaging. The review details several of the recent pharmaceutical packaging trends that are impacting packaging industry, and offers some predictions for the future.
Packaging is defined as the collection of different components which surround the pharmaceutical raw material from the time of production until its use. Packaging pharmaceutical products is a broad, encompassing, and multi-faceted task. Packaging is responsible for providing life-saving drugs, medical devices, medical treatments, and new products like medical nutritionals (nutraceuticals) in every imaginable dosage form to deliver every type of supplement, poultice, liquid, solid, powder, suspension, or drop to people the world over. It is transparent to the end user when done well and is open to criticism from all quarters when done poorly.[1,2]
Distribution of products is now more global than ever. Mass customization of packaging to permit its use in multiple markets is a topic that needs exposition and discussion. Environmental issues, including sustainability, will always be a subjective dimension to any packaging design.
Packaging is an emerging science, an emerging engineering discipline, and a success contributor to pharmaceutical industries.
Packaging can reside, or report through research and development (R and D), engineering, operations, purchasing, marketing, or the general administrative department of a company. For the majority of products produced in pharmaceutical industries it is probably the single largest aggregate purchase made by a company of materials critical to the protection, distribution, and sale of the product.
Containment - The containment of the product is the most fundamental function of packaging for medicinal products. The design of high-quality packaging must take into account both the needs of the product and of the manufacturing and distribution system. This requires the packaging: not to leak, nor allow diffusion and permeation of the product, to be strong enough to hold the contents when subjected to normal handling and not to be altered by the ingredients of the formulation in its final dosage form.[3]
Protection - The packaging must protect the product against all adverse external influences that may affect its quality or potency, such as light, moisture, oxygen, biological contamination, mechanical damage and counterfeiting/adulteration.
Presentation and information - Packaging is also an essential source of information on medicinal products. Such information is provided by labels and package inserts for patients.
Identification - The printed packs or its ancillary printed components serves the functions of providing both identity and information.
Convenience - The convenience is associated with product use or administration e.g., a unit dose eye drop which both eliminates the need for preservative and reduces risks associated with cross infection, by administering only a single dose.
Primary packaging system is the material that first envelops the product and holds it i.e., those package components and subcomponents that actually come in contact with the product, or those that may have a direct effect on the product shelf life e.g., ampoules and vials, prefilled syringes, IV containers, etc.
Secondary packaging system is outside the primary packaging and used to group primary packages together e.g., cartons, boxes, shipping containers, injection trays, etc.
Tertiary packaging system is used for bulk handling and shipping e.g., barrel, container, edge protectors, etc.
Traditionally, the majority of medicines (51%) have been taken orally by tablets or capsules, which are either packed in blister packs (very common in Europe and Asia) or fed into plastic pharmaceutical glass bottle (especially in the USA). Powders, pastilles and liquids also make up part of the oral veterinary medicine intake. However, other methods for taking medicines are now being more widely used. These include parentral or intravenous (29%), inhalation (17%), and transdermal (3%) methods.
These changes have made a big impact on the packaging industry and there is an increasing need to provide tailored, individual packaging solutions, which guarantee the effectiveness of medicines.[4]
The present review article details several key trends that are impacting packaging industry, and offers some predictions for the future packaging encompassing solid oral dosage forms and injectables.
Aseptic blow-fill-seal (BFS) technology is the process by which plastic containers are formed, filled with sterile filtered product and sealed in an uninterrupted sequence of operations within the controlled sterile environment of a single machine.[5,6]
The blow-fill-seal process is a robust, advanced aseptic processing technology, recognized by worldwide regulatory authorities for its inherent operational advantages over conventional aseptic production. Blow-fill-seal systems offer a unique combination of flexibility in packaging design, low operating cost and a high degree of sterility assurance. The machines require a minimum number of operating personnel and have a relatively small space requirement.
A variety of polymers may be used in the process, low and high-density polyethylene and polypropylene being the most popular. The innate ability to form the container/closure during the actual aseptic packaging process allows for custom design of the container to meet the specific needs of the application. This flexibility not only improves container ease of use, but provides a means of interfacing with many of today's emerging drug delivery technologies, most notably in the field of respiratory therapy.
Thermoplastic is continuously extruded in a tubular shape [Figure 1a]. When the tube reaches the correct length, the mold closes and the parison is cut [Figure 1b]. The bottom of the parison is pinched closed and the top is held in place with a set of holding jaws. The mold is then transferred to a position under the filling station.
The nozzle assembly lowers into the parison until the nozzles form a seal with the neck of the mold [Figure 1c]. Container formation is completed by applying a vacuum on the mold-side of the container and blowing sterile filtered air into the interior of the container. The patented electronic fill system delivers a precise dosage of product into the container. The nozzles then retract into their original position.
Container sealing
Following completion of the filling process, the top of the container remains semi-molten. Separate seal molds close to form the top and hermetically seal the container [Figure 1d]. The mold opens and the container is then conveyed out of the machine [Figure 1e].
The cycle is then repeated to produce another filled container. The filled containers are tested and checked to ensure that they meet the very strict specifications laid down for such products.
The duration of the complete cycle is between 10-18 seconds, depending on the container design and the amount of liquid to be filled.
BFS technology offers considerable advantages over conventional aseptic filling of preformed (plastic or other) containers, which are described as follows:
BFS technology reduces personnel intervention making it a more robust method for the aseptic preparation of saccharin sodium.
There is no need to purchase and stock a range of prefabricated containers and their closures. Bulk containers of plastic are required.
Cleaning and sterilization of prefabricated containers and closures is not required. A clean, sterile container is made within the BFS machine as it is required for filling.
The cost of material transport, storage and inventory control is reduced.
Validation requirements are reduced.
The technology allows the design of high-quality, custom-designed containers with tamper-evident closures in a variety of shapes and sizes.
There is a large choice of neck and opening device shapes.
A single compact BFS machine takes the place of several conventional machines, saving floor space. In addition, zones for transport to successive filling and closing procedures are not required because these operations all take place in the BFS machine itself.
The operation of BFS machines is less labor intensive than conventional aseptic filling.
The code numbers and variable data such as batch number and expiry date can be molded into the container itself rather than being added at a subsequent stage.
The process lends itself to the production of single dose containers and therefore preservatives are not necessary as they are with multi-dose containers.
Blow-fill-seal technology has gained much market focus in recent years due to the increased focus on biologics, proteins and other complex solutions. These important products often cannot withstand exposure to high temperatures for extended periods of time without degradation of their active components. Conventional terminal sterilization, therefore, is not an acceptable method to produce a ‘sterile’ product. Bulk sterilization, sterilization by gamma irradiation or filter sterilization followed by direct packaging utilizing the blow-fill-seal process are often used successfully for these types of products.
Counterfeiting means producing products and packaging similar to the originals and selling the fake as authentic products. Counterfeit is a problem of product security, with reference to packaging is not a problem in isolation; it is the part along with:
Duplication - i.e., copying labels, packaging, products, instructions and usage information,
Substitution - placing inferior products in authentic or reused packaging,
Tampering - by altering packages/labels and using spiked, pilfered, or stolen goods in place as real,
Returns and Warranty frauds they are addressed as Brand Theft.
The current numbers of anti-counterfeiting solutions are many and new options are introduced in the market with some variations. An attempt is made to explain the technologies for easy understanding on product packaging.
1. Overt (visible) features
Overt features are intended to enable end users to verify the authenticity of a pack. Such features will normally be prominently visible, and difficult or expensive to reproduce. They also require utmost security in supply, handling and disposal procedures to avoid unauthorized diversion. They are designed to be applied in such a way that they cannot be reused or removed without being defaced or causing damage to the pack for this reason an overt device might be incorporated within a tamper evident feature for added security.
Tamper evident packaging systems
Some packages are inherently tamper proof, like a tin can hermetically sealed, an aseptically packed multilayer carton or a vacuum or the retort pack. The tamper evident packaging systems are:
a) Film wrappers
A transparent film with a distinctive design is wrapped securely around a product or product container. The film must be cut or torn to open the container and remove the product. Substrates options include ultra destructible films, voidable films that provides image when removed. e.g., Solvent sensitive papers.
b) Shrink seals and bands
Bands or wrappers with a distinctive design are shrunk by heat or drying to seal the cap and container union. The seal must be cut or torn to remove the product.
c) Breakable caps
Such caps break when an attempt is made to open it. These caps provide external tamper evidence and can also be combined with the internal seals thereby providing double security.
d) Sealed tubes
The mouth of the tube is sealed, and the seal must be punctured to obtain the product.
2. Covert (hidden) features
The purpose of a covert feature is to enable the brand owner to identify counterfeited product. The general public will not be aware of its presence nor have the means to verify it. A covert feature should not be easy to detect or copy without specialist knowledge, and their details must be controlled on a “need to know” basis. If compromised or publicized, most covert features will lose some if not all of their security value [Figure 2].
Radio frequency identification (RFID) is hardly a new concept. For some, RFID is already a mainstream technology-it is used every day to pay tolls, secure building access, catch shop lifters etc., It allows the identification of objects through a wireless communications in a fixed frequency band. Three essential components in any RFID system are: the tag, the reader and the software. The tag is an integrated circuit containing a unique tracking identifier, called an electronic product code (EPC), which is transmitted via E.M. waves in the radio spectrum. The reader captures the transmitted signal and provides the network connectivity between tag data and the system software. The software can be tailor made for the purpose of anti-counterfeiting. For their track and trace usage, RFID tags are used [Figure 3].
When RFID tag is within the interrogation zone of the reader (i.e., interrogator) equipment; sufficient power is extracted from the interrogator to power up the tag or circuit, or a special reflective material. It then responds by transmitting data back to the interrogator.
b) Active tag
Such tags incorporate a battery to increase range for collating data, tag to tag communication, etc., But these are much more expensive.
c) Semi-active tag
In these tags batteries are used to back up the memory and data, but not to boost the range. With some active RFID tags, the batteries are only used when interrogated or when sending a homing pulse at fixed intervals to reduce cost and size.
4. Packaging designs: Materials/Substrates and other design options
a) Substrates
There are variety of substrates used in the design of packages with intent to provide counterfeit and tamper evident features starting from litho paper, polystyrenes, destructive vinyl's, acetate films synthetic paper and coatings etc., There are many ways of incorporating covert markers within a substrate, such as visible or UV fluorescing fibers, or chemical reagents in carton board or paper. Watermarks can be embedded in leaflet paper, or metallic threads interwoven in the base material, possibly including an overt optically variable devices (OVD) feature. These require a dedicated supply source and large volume production, which, if affordable, results in a very effective option. Micro-encapsulated distinctive odors can be applied as an additive to an ink or coating to provide a novel covert or semi-overt feature, as well as sound chips creates special opportunities in the design.
b) Packaging designs
Packaging designs like sealed cartons, aerosol containers have inherent strength against counterfeiting
c) Sealing systems
Special caps such as the outer tamper evident system or the foil seal as an internal tamper evident feature are commonly used for pharmaceutical products. Sealing options are lever-lidded tins, secure packaging tapes, lined cartons and tear tapes/bands.
5. Security labels
Tamper evident and security labels play an important role in providing some relief to the consumers against fakes. In self adhesive labels the substrate mostly performs as a complimentary interaction of the substrate and the pressure sensitive adhesive. While passive security labels have been extensively used, today one can find a greater application of functional labels such as printing plus anti-theft. Some label options are:
a) Paper labels with security cuts
The substrate used for these labels is ordinary coated/uncoated paper. The security features are built in by the label printer at the converting stage. With the help of a special cutting die, the face material is given cuts at various angles so that by any ways one tries to remove these labels the paper will tear off. A general purpose permanent adhesive works fine with such labels. Care is taken to ensure that the adhesive will adhere well and firmly to the surface on which the label has to be applied.
b) Destructible labels
Needs a special substrate designed for the purpose. Most of the high-end applications use a specially made cellulose acetate film. The film is very intricately designed so that it has adequate strength to undergo conversion into label stocks in roll form. It is available both in clear and opaque formats and further converted into labels using aggressive pressure sensitive adhesives. The labels can be automatically dispensed on automatic label dispensers and when attempted to be removed, break-up into very small fragmented pieces. The cost effective vinyl have replaced acetate film. A combination of various synthetic polymers can be used to impart low inherent strength to the substrate.
c) Void labels and tapes
The most important of the tamper evident security labels and have text built into them. When as a self adhesive label they are removed, they exhibit the word VOID both in the removed film and the adhesive layer left behind. These substrates gain importance as there can be customization built into the labels produced with it. One can use polyester or biaxially-oriented polypropylene (BOPP) as face materials. Variety of colors, even metallization is possible. The text VOID could be replaced by the customers brand, emblem or a message, which would normally be invisible till the label is opened. Due to the versatility of things that can be done with the product, these label substrates have found widespread usage worldwide. The substrates can even be designed to work as tapes for the final outer corrugated cartons to prevent pilferage.
d) Self destructing paper label
The labels are very similar to destructible labels as mentioned earlier. In this case, the substrate used is of very weak strength paper of low grammage. The paper is also heavily loaded with fillers creating a weak and brittle paper. Labels made from such papers fragment into pieces when attempted to be removed. However, converting it is a very tricky issue when using these substrates due to the lack of strength. The papers are very difficult to source since most of the paper mills are trying to develop papers with very high strength.
e) Holographic labels
The labels form a very large and important part of the security label market and are an ideal choice for product authentication. The holographic foil that is an optically variable device is largely made using a polyester film base. The optical interaction of the holographic image and the human eye makes it ideal for brand promotion and security. These products reveal the holographic image when tilted in light. The image so revealed can be customized to the need of the brand owners to make the maximum impact. The hologram production involves development of complex origination process and a lot of innovation to make it difficult for counterfeiters to duplicate. Many holograms are designed such that besides offering brand authentication they also have tamper evident properties. The top polyester layer has a special coating that if the hologram is attempted to be removed, the top layer peels off leaving the hologram behind on the product [Figure 4].
|
|
|
|