Welcome, Guest |
You have to register before you can post on our site.
|
Online Users |
There are currently 281 online users. » 0 Member(s) | 279 Guest(s) Bing, Google
|
Latest Threads |
Advanced microneedling
Forum: Off Topic
Last Post: axied12
05-28-2025, 01:25 PM
» Replies: 0
» Views: 146
|
Caviar and cheese
Forum: Off Topic
Last Post: axied12
05-28-2025, 12:38 PM
» Replies: 0
» Views: 139
|
Top-rated countertop comp...
Forum: Off Topic
Last Post: axied12
05-04-2025, 06:42 AM
» Replies: 0
» Views: 291
|
Ryanair letenky levně do ...
Forum: Off Topic
Last Post: axied12
02-11-2025, 01:37 PM
» Replies: 0
» Views: 684
|
Trusted essay writing ser...
Forum: Off Topic
Last Post: axied12
01-30-2025, 08:16 AM
» Replies: 0
» Views: 618
|
Bootverkopers - actieve j...
Forum: Off Topic
Last Post: axied12
12-07-2024, 11:07 AM
» Replies: 0
» Views: 746
|
Services for individuals ...
Forum: Off Topic
Last Post: axied12
12-02-2024, 03:31 PM
» Replies: 0
» Views: 704
|
Used excavators
Forum: Off Topic
Last Post: axied12
11-13-2024, 09:22 AM
» Replies: 0
» Views: 687
|
Buy Higo Rocket in Dubai
Forum: Off Topic
Last Post: axied12
10-25-2024, 01:09 PM
» Replies: 0
» Views: 790
|
Anime coloring pages
Forum: Off Topic
Last Post: axied12
10-13-2024, 05:10 PM
» Replies: 0
» Views: 831
|
|
|
Cotton Buds Making Business |
Posted by: R234V - 09-22-2021, 05:09 AM - Forum: Welcomes and Introductions
- No Replies
|
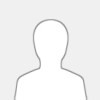 |
Cotton Buds Making Business
Cotton Buds Making Business
The cotton swab making machine business is rapidly progressing in India. Cotton is the staple fiber made from the natural fibers of cotton plants. The cotton made from the genus Gossypium is primarily composed of cellulose, which is an insoluble organic compound that is a soft and fluffy material. Cotton is the most important fiber crop, which provides the basic raw material to the cotton textile industry. Cotton is grown in tropic and sub-tropic parts and requires uniformly high temperature and is a Kharif crop; it is sown and harvested in different parts of India depending upon the climatic conditions.
China, the USA, and India are the world’s major cotton-producing countries, accounting for about 60% of the world’s production. China alone consumes around 40% of the world’s cotton, and it is a significant export revenue source for major cotton-producing countries of the world.
Cotton is cultivated around 117 lakh hectares in India and accounts for about 37.5% of the global cotton area, and contributes to 26% of the global cotton production. Cotton holds an essential place in the Indian textile mills, and it is used as a primary raw material of India. Cotton provides livelihood to around 60 million people of India by means of cotton cultivation, processing, marketing, and exports.
Cotton buds are the most common item which is used for cleaning the ear, first-aid, cosmetic application, cleaning, and arts and crafts. The cotton buds are composed of small wads of cotton which are wrapped around a rod made of wood, paper, or plastic. The cotton buds were developed in 1923 by a Polish-American Loe Gerstenzang which later became the most widely sold brand name of cotton swabs.
The cotton bud with a single tip on a wooden handle is mostly used in medical settings and is the traditional cotton buds. The cotton buds used for domestic purposes are usually short, about 3 inches long, and double-tipped. Traditionally, the handles of the cotton buds were made of woods while later it was made of the rolled paper and sold in large quantities. The cotton buds are available in a wide variety of colors, such as blue, pink, or green. The manufacturing of the test swabs in a record time of seven days is a dream come true under the ”Make in India” initiative which has conceptualized the production and provided employment to so many unemployed people in India.
The cotton buds are most commonly used for cleaning the ear by removing earwax. The cotton buds are used for domestic purposes such as cleaning and arts and crafts purposes. The medical buds are used to take microbiological cultures which are usually rubbed into the affected area and wiped where the bacteria grows across the culture medium. They can also be used to apply medicines to selective areas targeting to remove substances or clean them. They can be used as an applicator for applying cosmetics, ointments, or other substances.
The cotton buds are also used to take the DNA samples by scraping cells from the inner cheek in the case of humans. The cotton swabs are also often used in the construction of the plastic model kits while paintings. They are also frequently used for cleaning the laser diode lens of an optical drive in conjunction with rubbing alcohol. In addition to his, they are used to clear the large parts of the computer such as video cards and fans and also used widely to clean video games cartridges in the past.
With so many uses, the demand for cotton buds in the market is growing at a rapid rate and is an essential tool for the healthcare of all individuals irrespective of age, race, culture, or religion, etc. keeping this in mind, the idea to start the automatic cotton swab making machine business is a golden opportunity for the young and aspiring entrepreneurs.
With the increased diversity of product ranges from adult-centric to baby and child-centric and increased popularity of cotton buds in the modern as well as in traditional retailing has increased the sales of the cotton buds to grow. With the rising demand, the locally produced cotton buds have become popular across rural India. it has also become popular in small as well as in metropolitan cities because of the availability of the cotton buds at a much lower price as compared to the branded products have been a key focus for the small manufacturers in India. Therefore, it is an ideal business for employing in the Rural areas as well as it will promote the ‘Make in India” initiative of the Modi Government.
The Government of India is promoting all the manufacturing units, especially in the areas where China enjoys a big share in the global market. The government to achieve the Atma Nirbhar Bharat is pushing the exports by giving various aids to the small and marginal businessmen and it aims to reduce the dependency of the country on the imported goods.
The government through various joint ventures and supporting the local businesses is expanding India’s share in the global market. Keeping this in mind, the government has announced various production-linked incentives for manufacturing the earbuds. This is a great opportunity for Indian earbuds manufacturers to raise their business. It is a big step towards making India self-reliant and manufactures their products. Almost 260 schemes are contracted by the Tri-services at an approximate cost of Rs. 3.5 lakh crores and with the latest embargo on the import of 101 items, the contracts worth Rs 1, 30,000 crore is expected to be placed upon the domestic industries in India.
Registration:- To start the buds manufacturing business in India, the first and foremost thing is the registration of your firm either as a proprietorship company or as a partnership firm. One must register the company as a Proprietorship firm if he has to start his buds manufacturing business as One Person company. To start a partnership firm, one must get registered with the Registrar of companies (ROC) and register as a Limited Liability Partnership (LLP) or the Private Limited Company.
GST Registration:- To start a business, it is now mandatory for any business to obtain a GST number, tax identification number, and an insurance certificate.
License for Trade:- Trade license is very important to be acquired to start a buds manufacturing business. It can be obtained from the local bodies of the respective states.
MSME or SSI Registration:- To avail of the government schemes and benefits, one must obtain the MSME or SSI registration. This will help the businessman to receive all the governmental benefits arising from various schemes.
Trademark:- It is required to make sure to register the buds manufacturing business with the trademark which will help in protecting the brand name.
Before starting a semi automatic cotton swab making machine business, one has to make sure to select the proper machines which are proper for operations suitable for your business.
Following are the description of machines used in the cotton buds making business-
Automatic Cotton Swab Packing Machine : –
The automatic cotton bud making machine is the machine that uses the computer PLC process control and warm wind drying technology is used to help to absorb the coating layer. The microcomputer servo motor aids feed the cotton layer and wrap the absorbent material. In this technology, there is no requirement for a different packaging machine separately.
Spindle Fabrication Machine : –
The paper spindles are processed with the help of a dyeing cutting machine from a heavy grade paper and then a thin layered paper is rolled around it to make it light. While a wooden spindle is developed with the help of a lathe machine process. The plastic spindle is made from the extrusion molding process machine, where the plastic is melted and extruded through a die and sent to a hopper machine.
Packaging Machine : –
The cotton buds are sent through the packaging wheels where the buds are rolled with the pouch. A sensor is attached to the packaging wheel which counts the buds and places them into the packaging bag which is packed with the packaging wheel.
The automatic cotton swab packing machine does not require a lot of space for its operation and it can be started from home. Anyone can start the business even from home this will reduce the cost of investment. The cotton buds making business has the potential to give a good place in the market by becoming a high profit earning business in a short period. With the increased demand for cotton buds, the business is very ideal for start-ups and young entrepreneurs.
In the times like this where the pandemic has left no nation in a mess, India has started the manufacturing of indigenous swabs or cotton buds for the testing of Covid-19. A Mumbai based Micro, Small and Medium Enterprise (MSME) and Tulips has got a green signal from the Indian Council for Medical Research (ICMR) and the National Institute for Virology in Pune. These firms have started manufacturing the polyester-spun swabs which are way cheaper than the imported swabs from the US and China. This has helped various small and indigenous manufactures to retain their livelihood and it has also resulted in producing cheaper testing kits at an affordable price.
We Indians have in reality converted the deadly pandemic into an opportunity and the government through various initiatives has been aiding the cotton buds making business. The government is also being aided by various Non-governmental Organisations like Aatmnirbhar Sena is working very hard to provide finances and cheap credit to aspiring and innovative minds and fulfilling their dream of starting the business.
Therefore, the growth and development of cotton and cotton made products has a vital role in the overall development of the Indian economy.
|
|
|
Making process control valve choices |
Posted by: R234V - 09-22-2021, 05:06 AM - Forum: Welcomes and Introductions
- No Replies
|
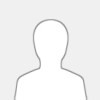 |
Making process control valve choices
Making process control valve choices
Today’s process control valves offer an ever wider range of features and benefits for industries that require precise control over fluids, steam and other gases. With so many control valves to choose from it is important to establish the features that will deliver the most cost-effective design for a particular application.
Control valves are used to manage the flow rate of a liquid or a gas and in-turn control the temperature, pressure or liquid level within a process. As such, they are defined by the way in which they operate to control flow and include globe valves, angle seat, diaphragm, quarter-turn, knife and needle valves, to name a few. In most cases the valve bodies are made from metal; either brass, forged steel or in hygienic applications 316 stainless steel.
Actuators will use an on-board system to measure the position of the valve with varying degrees of accuracy, depending on the application. A contactless, digital encoder can place the valve in any of a thousand positions, making it very accurate, while more rudimentary measurements can be applied to less sensitive designs.
One of the main areas of debate when specifying globe control valve is determining the size of the valve required. Often process engineers will know the pipe diameter used in an application and it is tempting to take that as the control valve’s defining characteristic. Of greater importance are the flow conditions within the system as these will dictate the size of the orifice within the control valve. The pressure either side of the valve and the expected flow rate are essential pieces of information when deciding on the valve design.
Inside the valve body, the actuator design is often either a piston or a diaphragm design. The piston design typically offers a smaller, more compact valve which is also lighter and easier to handle than the diaphragm designs. Actuators are usually made from stainless steel or polyphenolsulpide (PPS), which is a chemically-resistant plastic. The actuator is topped off by the control head or positioner.
Older, pneumatically operated positioners had a flapper/nozzle arrangement and operated on 3-15psi, so no matter what the state of the valve, open closed or somewhere in between, the system was always expelling some compressed air to the atmosphere.
Compressed air is an expensive commodity, requiring considerable energy to generate and when a manufacturing line is equipped with multiple process control valves all venting to the atmosphere, this can equate to a considerable waste of energy. It is important to not only establish the most appropriate valve design, but also a cost-effective solution that takes account of annual running costs.
Modern, digital, electro-pneumatic valves that use micro-solenoid valves to control the air in and out of the actuator have introduced significant improvements for operators. This design means that while the valve is fully open, fully closed or in a steady state, it is not consuming any air. This, and many other engineering improvements, have made substantial advances in both economy and precision.
Flexible designs
Valve seats can be interchangeable within a standard valve body, which allows the valve to fit existing pipework and the valve seat to the sized to the application more accurately. In some cases, this can be achieved after the valve has been installed, which would enable a process change to be accommodated without replacing the complete valve assembly.
Selecting the most appropriate seal materials is also an important step to ensure reliable operation; Steam processes would normally use metal-to-metal seals, whereas a process that included a sterilization stage may require chemically resistant seals.
Setting up and installing a new valve is now comparatively easy and much less time-consuming. In-built calibration procedures should be able perform the initial setup procedures automatically, measuring the air required to open and close the valve, the resistance of the piston seals on the valve stem and the response time of the valve itself.
Improving safety
Control valves should be specified so they operate in the 40-85% range so if the valve is commanded to a 10% setting, it can detect if something has potentially gone wrong with the control system and the best course of action is to close the valve completely. If the valve is commanded to a position of 10% or less this can cause very high fluid or gas velocities, which have damaging effects on the system and cause considerable noise and damage to the valve itself.
Modern control functionality can offer a solution that acts as a safety device to prevent damage to the process pipework and components. By building in a fail-safe mechanism, any valve position setting below a pre-set threshold will result in the valve closing completely, preventing damage to the surrounding system.
Control inputs can also include safety circuits to ensure safe operating conditions within the process equipment. For example, if an access panel on a vessel containing steam is opened, an interlock switch will open and the valve controlling the steam supply to the vessel can be automatically closed, helping mitigate any risks.
Improving reliability
Many process control environments offer less than ideal conditions for long-term reliability. Moisture-laden atmospheres, corrosive chemicals and regular wash-downs all have the capacity to shorten the service life of a process Self regulating control valve. One of the potential weaknesses of the actuator is the spring chamber where atmospheric air is drawn in each time the valve operates.
One solution is to use clean, instrument air to replenish the spring chamber, preventing any contamination from entering. This offers a defense against the ingress of airborne contaminants by diverting a small amount of clean control air into the control head, maintaining a slight positive pressure, thus achieving a simple, innovative solution. This prevents corrosion of the internal elements and can make a significant improvement to reliability and longevity in certain operating conditions.
While choosing the most appropriate process control valve can be a complex task, it is often best achieved with the assistance of expert knowledge. Working directly with manufacturers or knowledgeable distributors enables process control systems to be optimized for long-term reliability as well as precision and efficiency.
Damien Moran is field segment manager, Hygienic – Pharmaceutical at Bürkert. This article originally appeared on the Control Engineering Europe website. Edited by Chris Vavra, associate editor, Control Engineering, CFE Media and technology, cvavra@cfemedia.com.
Control valves are generally present whenever fluid flow regulation is required. The three way and angle control valve reliability is critical to the control quality and safety of a plant. An improved dynamic and static valve behaviour would have a major impact on the process output. In order to assess the dynamic performance of the control valve, a computer model of an electro-hydraulic control valve is developed. And the control valve characteristics are investigated through the use of mathematical simulations of the control valve dynamic performance. The results show that the electro-hydraulic driven control valve, which is developed to regulate the mixed-gas pressure in combined cycle power plant, can meet the challenge of the gas turbine.
Control valves play important roles in the control of the mixed-gas pressure in the combined cycle power plants (CCPP). In order to clarify the influence of coupling between the structure and the fluid system at the control valve, the coupling mechanism was presented, and the numerical investigations were carried out. At the same operating condition in which the pressure oscillation amplitude is greater when considering the coupling, the low-order natural frequencies of the plug assembly of the valve decrease obviously when considering the fluid-structure coupling action. The low-order natural frequencies at 25% valve opening, 50% valve opening, and 75% valve opening are reduced by 11.1%, 7.0%, and 3.8%, respectively. The results help understand the processes that occur in the valve flow path leading to the pressure control instability observed in the control valve in the CCPP.
1. Introduction
The steel mills generate vast amounts of blast furnace gas (BFG) and coke-oven gas (COG) in the production. In order to reduce the environmental pollution, some steel mills mix BFG with COG and build combined cycle power plants (CCPP) to make use of the gas [1]. For the normal operation of CCPP, the pressure of mixed gas delivered to the gas turbine should be kept in a steady range.
In CCPP, control valves play important roles in the control of the mixed-gas pressure. The signal of mixed-gas pressure measured using the pressure meter is compared to the signal of the desired pressure by the controller. The controller output accordingly adjusts the opening/closing actuator of the control valve in order to maintain the actual pressure close to the desired pressure. The opening of the control valve depends on the flow forces and the driving forces of the control-valve actuator, while the flow forces and the driving forces are affected by the valve opening. Therefore, there is strong coupling interaction between the fluid and the control valve structure.
According to Morita et al. (2007) and Yonezawa et al. (2008), the typical flow pattern around the Knife Gate Valve is transonic [2, 3]. When pressure fluctuations occur, large static and dynamic fluid forces will act on the valves. Consequently, problematic phenomena, such as valve vibrations and loud noises, can occur, with the worst cases resulting in damage of the valve plug and seal [4]. In order to understand the underlying physics of flow-induced vibrations in a steam control valve head, experimental investigations described by Yonezawa et al. (2012) are carried out. Misra et al. (2002) reported that the self-excited vibration of a piping system occurs due to the coincidence of water hammer, acoustic feedback in the downstream water piping, high acoustic resistance at the control valve, and negative hydraulic stiffness at the control valve [5]. Araki et al. (1981) reported that the steam control-valve head oscillation mechanism was forced vibration, while self-excited vibration was not observed [6].
Those studies cited previously are mainly aimed at the modeling of the self-excited vibration, the analysis of vibration parameters stability, and so on [7–11]. Whereas, the studies on the influence of nonlinear fluid-structure coupling of control valve on the valve control characteristics, such as the pressure regulation feature, are still very limited [12–17]. In the CCPP, the valve control characteristics affected by the fluid-structure coupling are particularly important for the stability of the mixed-gas pressure control. It has not been uncommon to see that the instability of the mixed-gas pressure causes a severe disturbance or even an emergency shutdown of the whole plant, and the handling of such an emergency often becomes a source of new problems and confusion. In this paper, numerical investigations are carried out to clarify the influence of fluid-structure coupling of control valve on not only the flow field but also the gas pressure regulation and the natural frequency changes of the control valve. This study helps understand the processes that occur in the valve flow path leading to the mixed-gas pressure pulsations, which is valuable for the pressure stability control of the mixed gas in the CCPP.
|
|
|
How are hybrid inverters used in solar projects? |
Posted by: R234V - 09-22-2021, 04:59 AM - Forum: Welcomes and Introductions
- No Replies
|
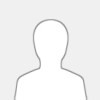 |
How are hybrid inverters used in solar projects?
How are hybrid inverters used in solar projects?
This paper proposes a new configuration of a single-phase hybrid inverter with an integrated battery energy storage, which is suitable for residential households to maximize local consumption of solar energy and thus reduce dependency on grid support. The hybrid inverter is called Direct Storage Hybrid (DSH) Inverter. A transformer-less topology such as HERIC, operating at low frequency to generate a three-level rectangular output voltage, is adopted to connect a photovoltaic (PV) panel to the load and/or the grid. A series active filter is employed to compensate the high harmonic components from the rectangular voltage and provide a sinusoidal voltage. A bidirectional dc/dc converter connects the battery to the PV panel to control the battery state of charge (SoC) and optimize the PV panel operation during both off-grid and grid-connected modes. The DSH inverter can let the battery bypass the dc/dc converter and connect directly to the inverter stage, leading to a significant improvement in throughput efficiency in battery utilization. This paper discusses the operation and loss analysis of the DSH inverter in off-grid mode.
This paper is designed in such a way that it overcomes this limitation by the use of solar energy. NA hybrid inverter lv with Solar Battery Charging System consists of an inverter powered by a 12V Battery. This inverter generates up to 230V AC with the help of driver circuitry and a heavy load transformer. This battery gets charged from two sources, first being the mains power supply itself and second from the solar power. If the mains power supply is available, then the relay switches to main power supply for supplying the load. This power supply also charges the battery for using it as back up the next time when there is a power outage. The use of solar panel to charge the battery gives an additional advantage of surplus power in case the power outage of mains is prolonging. Thus this inverter can last for longer duration’s and provide uninterrupted power supply to the user.
Hybrid inverters are commonly used in the developing world, but they are starting to make their way into daily use in certain areas of the U.S due to their ability to stabilize energy availability.
A solar inverter’s main job is to convert DC power generated from the array into usable AC power. Hybrid inverters go a step further and work with batteries to store excess power as well. This type of system solves issues renewable energy variability and unreliable grid structures.
“Inverters for grid-tied applications can only provide power based on what the array can immediately generate from the sun,” explained Bryan Whitton, product manager at Darfon. “Hybrid inverters can store power in batteries and then drawn upon it as needed for energy stabilization.”
Hybrid inverters can vary in size, performance and features. But Mara White, product manager for OutBack Power, said most models usually operate bi-directionally, meaning they can convert DC power from modules to usable AC power and then convert stored AC from the batteries to power loads when needed. “Hybrids can also remain grid-connected and use a mix of renewable and non-renewable energy to charge batteries and offset loads,” White added.
Some contractors have used hybrid inverters in the residential, remote home applications for the past decade or two. But Allan Gregg, VP of applications engineering at GreatWall—which manufactures Satcon inverters—said the range of applications has expanded over the past few years to include large capacity microgrids as well as grid-connected systems.
Historically, hybrid inverters have been used more frequently in developing countries that do not have access to a reliable power grid.
“In North America and Europe, hybrid inverter-based systems are usually elective,” White explained. “Users choose to use them for storing energy for self-consumption or provide back-up power during emergencies. But in the developing world, hybrids are more of a necessity to compensate for weak or intermittent grids or a lack of grid electricity all together. Microgrids in places such as India, Asia and Africa are also driving na hybrid inverter hv adaptation.”
Still, Whitton said hybrid models are beginning to be used on a more daily basis in areas of the U.S. where the grid is unpredictable, such as Hawaii, or in states where net-metering has been widely supported. “Applications with less than ideal solar characteristic are also good for hybrid-based systems because they can store power and redistribute it during peak times, improving payback,” he added. “Basically, if the site has the potential for losing the grid frequently, you should consider a hybrid for off-grid operation.”
Having the flexibility of a hybrid system can add initial cost to a project, though experts say this can be offset by the ability to self-consume all of one’s available PV electricity.
There are also important design considerations when using hybrid inverters. For example, Gregg warned that the battery bank voltage should be compatible with the DC input requirements of the inverter, and there should be enough solar capacity to supply the load as well as charge the batteries.
Wiring can also be more complex when using hybrid inverters, especially when panels are dedicated for critical backed-up loads. “And as with any device that does several jobs at once, a hybrid inverter is usually slightly less efficient,” White added, “although, improvements in other balance-of-system components can compensate for that slight loss easily.”
There are also specific electrical safety issues with any type of energy storage, so White recommended getting specialized training in energy storage techniques and design. “Most available training is focused on simple grid-tied systems because they have been the majority of U.S. solar installations until now,” she said. “But with incentives changing and the surge in energy storage interest and applications, it’s important to get ahead of the curve and get advanced training quickly.”
Andrew McCalla of Austin, Texas-based Meridian Solar, a Solar Power World top contractor, said he commonly used hybrids in the mid to late ’90s when the now standard grid-tie inverter sector was just a glimmer. “I can imagine that, when regulatory hurdles are fabricated to limit the consumer and societal benefits of bi-directional power flow from distributed generation, these battery-based platforms will become far more common. What is old is new again!”
Another segment of hybrid inverters includes inverters that can use two energy sources. For example, Ginlong offers a PV / wind lv battery hybrid inverter that has inputs for both sources, instead of having to use two inverters. In much of the United States, wind speeds are low in the summer when the sun shines brightest and longest. The wind is strong in the winter when less sunlight is available. Therefore, because the peak operating times for wind and solar systems occur at different times of the day and year, such hybrid systems have the potential to produce power when it’s needed, and reach a higher return on investment.
When you first consider getting solar or battery storage on your home or business, one of the first things you will discover is that you will require an inverter and that there are many different types of inverters available. This article is designed to provide an introduction to the different kinds of inverters available and help you to understand which one will suit your installation. So what does an inverter do? Simply put an Inverter converts DC power to AC power. Solar panels produce DC power and batteries store DC, however most of our appliances run on AC power, as does the electricity grid. This is why all solar systems and battery storage systems need an inverter however there are several different types of inverters depending on whether or not energy storage batteries are required.
On-grid solar installations are the most common and most affordable type of system available at present. These systems use a simple solar inverter, which convert the DC power from your solar panels into AC power which can be fed directly into the grid, or used in your home appliances.
Off-grid and hybrid systems are much more complex because they involve both solar panels as well as battery storage. Multiple inverters are often required in these installations such as a solar inverter and sophisticated battery inverter/charger to manage both grid connection and the charging and discharging of the batteries. These advanced inverter/chargers are known as interactive or multi-mode inverters. However, in recent years a new type of inverter has become available which integrates solar and battery inverter technology into what is known as an all-in-one hv battery hybrid inverter.
A micro-inverter is a very small inverter that is attached to the back of a solar panel. A micro-inverter only converts the power of one or two solar panels to AC so generally many microinverters are required in a single system. Micro-inverters have several advantages over string inverters including performance, safety and monitoring, however the upfront cost can be significantly greater. For more details about micro-inverters, check out our micro-inverters article.
String solar inverters come in single phase and three phase versions although most residential homes in the US and Australia use single phase power, while many homes in Europe use 3-phase power, also all businesses and factories will have three phase power. As a general rule most String solar inverters between 1-6kW are single phase and greater than 6kW are usually three phase.
As home energy storage systems have surged in popularity a new kind of advanced Inverter has emerged known as an hybrid inverter. Hybrid inverters combines a solar inverter and battery inverter/charger into one simple unit. These inverters are a very economical way to enable what is known as ‘self-use’ or 'load shifting' of energy. Allowing you to store solar or off-peak energy in a battery to be used during peak times. Although it is important to know that some all-in-one inverters cannot function during a power outage such as when there is a blackout. They can also have limited functionality and monitoring capabilities.The traditional off-grid solar system uses a simple battery inverter that converters DC power from a battery bank to AC power to supply your home or appliances, these systems need separate battery chargers and regulators. There are more advanced versions of these battery inverters with built in chargers known as inverter/chargers. In recent years very advanced inverters have become available which are inverter/chargers with in-built generator control systems, advanced monitoring capabilities and other features, these are known as interactive or multi-mode inverters. They are typically used in conjunction with a solar inverter to create what is known as an AC coupled system. You can learn more about these and other hybrid inverter types here.
|
|
|
Contact lenses: a look at the risks and recommendations |
Posted by: mmws256w - 09-22-2021, 04:33 AM - Forum: Welcomes and Introductions
- No Replies
|
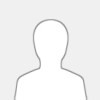 |
Thanks to the existence of contact lenses, it can sometimes be impossible to tell if someone has a visual impairment or not. These lenses can make huge differences to the lives of their wearers, providing a certain level of freedom that traditional glasses are unable to.
According to the Centers for Disease Control and Prevention (CDC), around 41 million people in the US wear contact PC lenses.
While they might feel like a relatively modern invention, rigid contact lenses made from plastic were first manufactured in the US between 1938 and 1940. The soft contact lenses currently worn by an estimated 93% of contact lens wearers were first introduced in 1971.
On a personal level, I first started wearing them as a temporary measure when my declining eyesight made playing sports difficult. However, no longer having my vision affected by raindrops and fogging up (along with the boost in self-esteem that came from not wearing glasses) meant that contact lenses quickly became my main method of improving my vision.
But despite their prevalence and the benefits they can provide, many people (myself included) wear contact lenses in a way that can compromise eye health, increasing the risk of damaged corneas and infection from microbes.
This week has marked the second annual Contact Lens Health Week – a week organized by the CDC to increase public awareness and promote healthy wearing and caring of contact lenses. In this Spotlight, we take a brief look at a few of the “do’s and don’t’s” of contact wear. In addition, we will have a look at some of the interesting “can’s and can’t yet’s” of new contact lens innovations.
Healthy habits mean healthy eyes
Although they are similarly effective at improving vision as glasses, contact Pc anti fog lens wearers can be more at risk of eye complications than those who use glasses. If wearers do not follow contact lens care instructions properly, they can put themselves at risk of serious eye infections that can lead to blindness.
The CDC have previously reported that between 40-90% of contact lens wearers do not properly follow their contact lens care instructions, which may explain why serious eye infections affect around 1 in 500 contact lens wearers each year.
Many people compromise their visual health due to bad habits when it comes to wearing contact lenses. While it is easy to manhandle glasses, contact lenses need to be afforded a greater level of care.
This means washing hands with soap and water and drying them comprehensively before ever touching contact lenses. Doing so prevents the transfer of germs from the hands to the lenses and consequently the eyes.
Exposing the lenses to water should be avoided as water can carry bacteria and other microbes that cause infection. With soft contact lenses, water can also alter the shape of the lens and potentially damage the cornea. As a result, contact lens wearers should remove their lenses before showering, swimming or using hot tubs, as tempting as it may be to keep them in.
One particular germ, an ameba called Acanthamoeba, is typically found in tap water as well as other water sources. If it causes infection (Acanthamoeba keratitis), patients can require a year or more of treatment, and possibly a corneal transplant.
Another bad habit that should be avoided where possible – unless prescribed by a doctor – is sleeping in contact PC super blue cut lens. In addition to making the eyes feel uncomfortable, sleeping in any type of lens increases the wearer’s risk of a corneal infection known as microbial keratitis by between four and five times.
Fast facts about keratitis
Keratitis is inflammation of the cornea, the clear tissue that covers the pupil and iris
Keratitis can be caused by infectious microbes or by minor injuries to the cornea
In severe cases, keratitis can permanently damage an individual’s vision.
This risk extends to the wearers of contact lenses that are designed to be slept in. Recently, the story of a man who went blind in one eye after sleeping in contact lenses for almost a week has come to the media’s attention.
“The kind of contacts I have are called ‘Night and Day’ contacts,” Chad Groeschen explained to USA Today, “and it was my impression you could leave them in for 30 days straight. I figured the less I was messing with my eyes, the better.”
While people can opt to use disposable lenses that are designed to be worn daily, many choose to wear lenses that last for longer periods and need to be stored properly when not in use. Unsurprisingly, many eye problems arise from bad habits pertaining to the storing of contact lens and associated products.
Contact lenses need to be kept clean if they are going to be used for multiple days. Lenses should be cleaned using a specific contact lens disinfecting solution and never water or saliva, as should the case that the lenses are stored in when not in use.
The CDC report that fewer than half of contact lens wearers report always cleaning their contact PC blue cut lens cases, and the number of moderate to severe lens-related infection could be halved if case cleaning practices were improved. Contact lens cases should also be replaced at least once every 3 months.
Contact lenses are stored in a purpose-built solution that is recommended by an eye care specialist. Contact lens wearers should stick to the recommended solution as the recommendation will be based upon the wearer’s eyes and medical history. Water should never be used, again due to the fact that it can increase the risk of infection.
Old solution in a lens case should never be “topped off” with new solution – instead, only fresh solution should be used. Solution can become contaminated with microbes that cause infections, and simply adding fresh solution to old solution reduces how effective it is at eradicating germs.
According to the results of a recent CDC study, these bad behaviors are incredibly prevalent. The Contact Lens Risk Survey was completed by approximately 1,000 contact lens wearers, and around 99% of respondents reported at least one behavior associated with an increased risk of eye infections.
“Good vision contributes to overall wellbeing and independence for people of all ages, so it’s important not to cut corners on healthy contact lens wear and care,” reports CDC Medical Epidemiologist Dr. Jennifer Cope. “We are finding that many wearers are unclear about how to properly wear and care for contact lenses.”
The following figures illustrate how prevalent some risky behaviors were among survey respondents:
Napping while wearing contact lenses – 87.1%
Showering while wearing contact lenses – 84.9%
Not replacing contact lens cases as frequently as recommended – 82.3%
Swimming while wearing contact lenses – 61.0%
“Topping off” contact lens solution – 55.1%
Sleeping in contact lenses overnight – 50.2%.
“Nearly one third of all wearers reported ever having experienced a contact lens-related red or painful eye that required a doctor’s visit,” the researchers write.
Considering how common contact lenses have become, the figures produced by the CDC’s study are significant, illustrating just how important it is that people become more aware of how contact lenses should be used and the impact bad practice can have on health.
The health problems that can be caused by risky contact lens behaviors may be enough to put some people off wearing them. However, there are a number of other benefits that specific types of contact lenses can provide that no other devices are able to.
Contact lens designs have become more sophisticated over time. While original products may have only been able to correct nearsightedness (myopia) and longsightedness, newer models of lens can be used to treat and monitor additional conditions that affect the eyes.
Orthokeratology, also known as Ortho-K, is a PC clear lens fitting procedure that offers a temporary degree of vision correction by changing the curvature of the cornea to improve its ability to focus on objects.
Altering the cornea’s curvature is achieved through the use of specially designed rigid contact lenses that are typically worn overnight. Ortho-K lenses are most commonly used to correct myopia.
Some people wear multifocal glasses because they have a condition known as presbyopia, whereby the eye’s ability to focus on nearby objects is lost. However, the condition can also be treated with multifocal contact lenses.
There are two main designs for these types of lenses. Alternating vision lenses have two distinct areas for short- and long-distance prescriptions. The pupil alternates between the two different prescriptions as the wearer’s gaze shifts up or down.
Simultaneous vision lenses involve the pupil looking through short- and long-distance prescriptions simultaneously. The two prescriptions can either be laid out in alternating concentric rings or blended together across the lens.
Presbyopia is one condition that a “smart lens” being developed by Google and Novartis should hopefully address. Last year, Novartis suggested that the use of technology such as noninvasive sensors and microchips contained within the lens could “provide accommodative vision correction” to restore the eye’s ability to focus.
Their smart lens might also provide benefit outside of visual health. Novartis stated that such a lens could provide a continuous measurement of glucose levels in diabetic patients and deliver this information to a mobile device using a wireless connection.
“We are looking forward to working with Google to bring together their advanced technology and our extensive knowledge of biology to meet unmet medical needs,” announced Novartis CEO Joseph Jimenez. “This is a key step for us to go beyond the confines of traditional disease management, starting with the eye.”
One of the most frequently repeated recommendations concerning contact lenses is that wearers should always follow the advice of their eye care providers. Unlike glasses, contact lenses are in direct contact with an opening into the human body, and as such there are far more things that could go wrong from a health perspective.
When used correctly, contact lenses can have a transformative effect on the wearer’s quality of life. The same can be said for when they are used incorrectly, only for wholly different and more unpleasant reasons.
It does not take much time to wash hands before handling lenses, to remove them before showering or to clean out a storage case properly, and yet by skipping these simple steps, thousands of contact lens wearers are putting their vision at risk. Follow the advice of eye care providers and vision can be protected for years to come.
Previously, Medical News Today reported on a study that suggested wearing contact lenses may alter the microbiome of the eye.
Once an optometrist has confirmed a diagnosis of myopia, several treatments are available. Speaking to an optometrist can help a person decide on the best option for them.
The sections below will discuss some of these treatment options in more detail.
Glasses and contact lenses
Glasses and contact lenses are the most common treatment options for myopia. An optometrist will order custom lenses that have the right prescription for that person. These will fit into the frame of the glasses and correct any nearsightedness.
Contact lenses are clear discs that sit on the surface of the eye. Like glasses, contact lenses are also customizable for different prescriptions.
Many people who do not like the look or feel of glasses will choose to have contact lenses, as they are a lot smaller and harder to notice. However, it is necessary to change and clean them regularly.
Orthokeratology
People with mild forms of myopia may benefit from a nonsurgical process called orthokeratology, or corneal refractive therapy. This treatment involves wearing a series of rigid contact lenses to reshape the cornea.
These lenses put pressure on the cornea to flatten it. This, in turn, changes how light focuses as it enters the eye. People tend to wear these contact lenses while sleeping.
This process can help people experience clear vision temporarily. However, it also carries a risk of eye infections.
Surgery
There are a couple of different types of surgery available to people who would rather not wear glasses, who want a more permanent solution, or who have severe forms of myopia.
One form of surgery is laser surgery, wherein an eye doctor will use a powerful beam of light to change the shape of the cornea.
Laser surgery adjusts how the eye focuses light, meaning that images that were once blurry should now be clear.
The surgery takes around 10 minutes per eye. This option can be expensive, but it is usually painless. Vision should return to normal within a day or so of the surgery.
However, it is normal to have occasional blurred vision or dry eyes for weeks or months afterward. Attending follow-up appointments after this procedure is important to make sure that the eyes are healing properly.
Other forms of surgery can involve placing a PC photochromic blue cut lens inside the eye, either in front of the person’s lens or in place of it. Eye doctors tend to recommend this form of surgery for more severe forms of myopia.
Prevention
Given that myopia has genetic links, it can be hard to prevent in people who have a history of nearsightedness in their family.
Spending time outside, in the daylight, could help lower the progression of myopia. Making sure not to spend too much time doing up-close work, such as reading or working on a computer, can also help.
Outlook
In most cases, myopia does not cause any further health problems. There are a range of treatments available that allow people to experience no symptoms of the condition in their daily lives.
For those who have more severe forms of myopia, it is important that they tell their optometrist about any changes in their vision. Without treatment, they could be at risk of developing additional eye problems, or even vision loss.
There is evidence that both genes and environmental factors, such as spending less time outdoors and more time indoors reading and using computers, can increase the risk of myopia. Before this study, however, it was not clear what the underlying molecular mechanisms were.
One way to observe the biological development of myopia or hyperopia is by altering the focal length of the eye in laboratory animals. Specialists can do this by placing a lens in front of the eye for several weeks.
Depending on the type of lens, the exposure causes the eye to develop to a length that is either too long or too short.
The scientists used this method in marmosets to study the development of myopia and hyperopia. They placed a PC photochromic lens in front of only one eye for up to 5 weeks and let the other eye develop normally for comparison.
|
|
|
What Is A Seed Tray? |
Posted by: mmws256w - 09-22-2021, 03:34 AM - Forum: Welcomes and Introductions
- No Replies
|
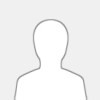 |
Starting your own plants from seed will often give you healthier plants at a lower cost. If you want to start seeds in bulk, you may want to consider a seed tray to help with germination.
So, what is a seed tray? A seed tray is a container used to sow multiple seeds at once. After seed germination, seedlings grow in the seedling tray until they are large enough for transplant. A single seed tray can hold anywhere from 6 seeds to over 1000 seeds!
Of course, when choosing a seed tray, there are lots of options for the material, the type of tray, and the number of cells.
In this article, we’ll talk about seed trays and the options that are available. We’ll also get into how to use seed trays and how to water the seeds and seedlings.
Let’s get going.
What Is A Seed Tray?
A seed tray is a container that is used to plant multiple seeds at once. A seed tray is sometimes called a seed starting tray.
A seed tray allows you to plant many seeds together in one container. This makes it much easier to water them and transport them.
After the seeds germinate, the seed tray holds seedlings as they grow, until they are ready for transplant outdoors or into larger containers.
There are a few different types of seed trays, including:
Mesh seed tray – a mesh seed tray allows water to drain out easily. A mesh seed tray is best for holding multiple individual containers (pots). A drawback is that the holes in a mesh seed tray are too large to hold soil without it falling through or washing away when watered. You can find mesh seed trays from Johnny’s Selected Seeds.
Solid seed tray with drainage holes – a solid seed tray with drainage holes allows for adequate drainage, but allows soil to stay moist enough for seed germination. A solid seed tray with drainage holes is best for planting multiple seeds together in one place. A drawback is that the seedlings do not have individual cells, so their roots can get tangled together as they grow. You can find solid seed trays with drainage holes from Johnny’s Selected Seeds.
Solid seed tray without drainage holes (leak proof seed tray) – a solid seed tray without drainage holes does not allow for any drainage. A solid seed tray without drainage holes is best for holding a cell flat (also called a plug flat). Since it holds water, it can be used to catch excess water from watering seeds, or it can be used to water from below (more detail on this later). You can find cell seed trays without drainage holes from Johnny’s Selected Seeds.
Another interesting option is this seed flat with 20 rows from Johnny’s Selected Seeds. Instead of separate cells, there are separate rows to keep different plant varieties from getting mixed up.
If you decide to use a cell flat for seed germination, each cell should have its own drainage hole. The tray below the cell flat should be solid without holes if you want to water the seeds from below.
The main problem of adapting the SRI techniques is high labor requirements for manual and lacking of mechanized system for planting single seedling in the field. The existing seedling preparation methods remain challenging among SRI practitioners due to traumatic condition. This study was intended to create modern techniques for increasing the quality and transplanting potentials to improve seedling preparation and reduce transplanting shock. It involved development of rectangular tray having 924 square growing cavities with sliding base to facilitate seedling transfer. Seed selection was conducted and 100% germination was obtained from the sunken MR219 seeds collected in 80 g/L of NaCl solution. SRI-tray seeding was 100% placed into cavities with SRI-seed picker at 150 g/L of tapioca solution. Two different media (Soil + Burnt husk (1:1) as M1 and Soil + Compost (1:1) as M2) were used to evaluate the growth performances for 10 days. The measured parameters (Seedling Height (SH), Leaf Length (LL), Leaf Number (LN), Root Length (RL) and Loosening Index (LI)) were compared between SRI-tray and conventional ones. The SAS revealed that M2 on SRI-tray had the highest significant values for SH, LL, RL and LI with the mean values of 155.6, 109.3, 89.3 and 75 sec when compared with conventional tray which had 125, 91 and 52 mm with no LI, respectively. The seed rate, nursery area and seedling age to support one hectare of planting area were found as 5.34 kg, 36 m2 and 8-10 days on SRI-tray against 15-50 kg, 250-500 m2 and 12-30 days on conventional practices.
The more pellets that are placed in the mould, the denser and stronger the seedling tray with lids.
In cheaper trays, there tend to be slightly bigger gaps between the expanded pellets, and fine plant roots can enter these, making it difficult to pull out the plants.
Damping off organisms can also lurk in these small spaces, and the growing plants can become infected and die. One of the Pythium species (fungus-type pathogens) is usually the main culprit, but it’s not the only one.
I have used horse manure compost as a medium for 23 years and have never had damping off problems. This may be because the medium is a rich source of beneficial organisms, which suppress development of pathogens. I also never get powdery mildew on Brassica seedlings.
Once the pathogen has appeared, the trays must be sterilised, or the problem will keep cropping up and possibly cause major losses.
The most effective way of sterilising trays is in a heat chamber. To save cost and effort, some growers wait until damping off starts before using heat sterilising.
Another solution is to use a commercial dip containing copper; this will also reduce the penetration of roots into the fine gaps in the polystyrene.
If you are a small grower, you can use a simple, home-made steriliser such as bleach mixed with water at a 10% solution, or hydrogen peroxide at 3% concentration. Leave the trays suspended in the solution for 20 minutes, then rinse and dry them.
The ideal sealant
One of the most effective ways of treating seedling trays is to dip them in a water-based roof paint when they are still new.
Obtain a flat receptacle slightly larger than the tray and dilute the paint with 10% water. Push the tray face down into the paint until the paint reaches the drainage holes. Lift and allow the excess paint to drip back into the tray, then place it face-up to dry. (It’s unnecessary to paint the base.) You should be able to coat about 10 trays per litre.
Some farmers are put off by the price of paint, but this treatment is well worth the cost: not only does it extend the life of the rice seedling tray by many years, but it seals the fine gaps in the polystyrene.
This reduces the risk of pathogens lurking in these crevices and also makes it much easier to pull out the seedlings.
Roof paints come in many colours, so you can use different colours for different years to keep track of the lifespan of each batch of styrofoam seed trays. There are often specials on roof paints and you can take advantage of these to cut the costs of the treatment.
Biodegradable plastics have been widely introduced into agricultural production, but their impacts on the soil ecosystem remain unclear. The present study investigated the impacts of a biodegradable seedling tray (BST) on the microbial communities in paddy soils. A 110-day rice culture experiment was conducted with three different paddy soils developed from black soil (BS, black chernozem soil), chao soil (CS, Fluvo-aquic) and red soil (RS, Alfisols) and three application rates of BST (0, 0.02 and 0.2 g kg−1). Soil phthalic acid ester (PAE) concentrations, physicochemical properties and enzyme activities were determined to evaluate the influence of BSTs on soil quality. 16S high-throughput sequencing was used to study bacterial community composition and the Biolog EcoPlate™ test was used to profile microbial activity and community function. Results show that the application of BSTs did not markedly affect soil quality, and the potential release of PAEs from BSTs was negligible. Interestingly, the microbial community was affected by BSTs in a soil-dependent and time-dependent pattern. The microbial community in RS was not significantly influenced by BSTs. Relative abundances of some predominant genera in BS (e.g. norank_f__BSV40) and CS (e.g. Norank_f__Nitrosomonadaceae) were significantly influenced by BSTs, and db-RDA results show that community composition in BS and CS was shaped mainly by BSTs. Community level profiling shows that BSTs significantly increased microbial activity and decreased functional diversity in BS after 55 days, but the impacts disappeared after 110 days. The results contribute to the knowledge of how biodegradable plastics influence microbial communities in paddy fields and provide information relevant to the practical use of BSTs under field condition.
This experiment investigated the effect of different plug-tray cell designs on root development of red maple (Acer rubrum), red oak (Quercus rubra), and quaking aspen (Populus tremuloides) seedlings. In April of 2015, seeds of each species were sown into three plug trays with different substrate volumes and grown for 17 weeks. Two trays had permeable walls for air-pruning, one with vertical ribs and one without. The third tray had impermeable plastic cell walls. Harvested seedlings were analyzed for root dry weight, length, volume, surface area and number of deflected roots. Root length per volume was highest in the impermeable-walled tray for red maple and quaking aspen. The total numbers of deflected root systems were higher for all species in the impermeable-walled tray. Seedlings grown in the air-pruning trays had smaller proportions of deflected root masses. Greater substrate volume did not influence root deflection development. The air-pruning tray without vertical ribs had the lowest total number of root masses with misdirected roots and lower proportions of root masses with misdirected roots for all species. These results indicate that improved root architecture in root-air pruning tray designs is achievable in tree propagation; however, vertical plastic structures in air-pruning trays can still cause root deflections.
|
|
|
What is a Ramadan crescent moon tree? |
Posted by: mmws256w - 09-22-2021, 03:29 AM - Forum: Welcomes and Introductions
- No Replies
|
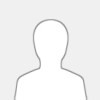 |
One particular decor element that has taken root – and is quickly gaining ground in the region this year – is the crescent tree.
Chances are you’ve come across it yourself: the artificial tree comes in a number of sizes and colours, with its defining feature being its distinct crescent moon shape.
With its Instagram-friendly appearance, it has blown up online under different names – moon tree, green ramadan eid crecsent moon tree, Ramadan tree and even Eid tree – as more families take to them. A search for #RamadanTree on Instagram turns up more than 1,000 posts, while one for #EidTree yields over 1,500; impressive since three years ago, they didn’t really exist.
So how did it all begin? It all seems to have started in Michigan, in the US, where resident Samar Baydoun Bazzi decided to mark the holy month with some festive cheer. As a mother, she wanted to create a special experience for her daughter, so she began incorporating Islamic-themed art into the home. When that wasn’t enough, she tried a Christmas tree, but that only confused her child further, she told local media.
That is how Bazzi ended up taking things into her own hands – by creating Ramadan trees in the shape of a crescent moon as a tribute to Islam. As the pictures of the trees circulated online, she started getting orders and the trend just picked up from there.
How did trend reach the UAE?
The crescent-shaped tree is making its way across to the UAE, too. Zahirah Marty, founder of brand development agency Think Liquorice, purchased one in 2020 through Amazon, but she found it quite difficult to source one at the time, and options were limited.
Today, however, it's easier, as a number of brands have starting selling them.
Crate & Barrel, which introduced the tree in 2020, saw sales of the crescent tree soar this year. The hugely popular item can be bought item both online and in-store, for Dh400.
Why get a crescent tree?
UAE resident and mum-of-four Taghred Chandab, who bought one before Ramadan from Kibsons, says it worked as a great way to start a conversation with little ones about Islam and Ramadan.
“We like to decorate for Ramadan and Eid, to give the children a sense of excitement around both the holy month and Eid. My youngest is 5 and she has asked over the years if we could have a Christmas tree at Christmas, but as Muslims we didn't feel this was appropriate as it didn't reflect our beliefs.
"She was really excited when the white ramadan eid crecsent moon tree arrived and we explained to her why the moon was important in Islam, particularly around Ramadan and Eid. She feels the spirit now. Sometimes kids need visual aids to understand."
When Marty posted a picture of her tree on social media last year, she received many queries from other parents, also looking for a way to “bring the month to life for their children and make it something tangible and memorable”.
"Growing up, we didn't have anything like this," she tells The National. "There weren't decorations and lights. At best we shared plates of food or dates with neighbours and family and waited for Eid; for a day of family and food. We did a little less that month, and besides the wave of energy at iftar, it was a pretty non-eventful month from a child's perspective.
“I want Ramadan to be a month-long celebration of who we are, and time at home together, and most importantly I want to create new traditions for my family based on our diversity and mixed cultural background, because that’s a part of our identity.
"It is a month to reflect, and reconnect with ourselves, our home, our family, our creator and I want that to be done in a lively and festive space. Having that centrepiece is a symbolic display of that for me."
Marty says she makes setting up the tree an educational and fun experience for her son Noah, who loves it, too. “While we decorate it, we chat about why it’s a moon and not a tree, why we have it out, what fasting means and how he has so much to look forward to with Eid.
“I want Noah to fall in love with his faith, and all that it comes with. We live in a very challenging world, and children today won’t accept things ‘because we say so’. I want my son to view religion as the beautiful part of his world it is from a young age, and creating reasons to celebrate, decorate and bring joy is how I choose to do it. Everything else will follow."
A response to criticism
Despite its popularity, the trend is not without its criticism. A cursory search online will find comments about it copying western traditions, while others believe it can be ostentatious.
“In any area of life there will always be critics, and I respect that as humans we will differ in our opinions," says Marty. "I prefer to focus on my intention to create happy, celebratory moments for my family as a medium of education, and a way of carving out our space with our circumstances.
“If a decorated moon sparks joy in my toddler to look forward to the month of Ramadan, ask me questions, and open his mind and heart to the lessons, stories and memories, then I’ve achieved my goal.”
How to decorate a Ramadan tree:
Some trees come pre-decorated, but if you prefer to decorate the gold ramadan eid crecsent moon tree together with your family, there are options in the UAE.
Marty recommends Daiso as a place where one can get a range of lights in the shapes of mosques, stars and moons. She drapes her family Ramadan tree with lights, camels and even baubles.
“I grew up with a childhood tradition of new Eid pyjamas and either money or gifts. I keep that tradition in our home. The silver ramadan eid crecsent moon tree is a place we have all this sitting until the night before Eid, which adds to the excitement of Eid day,” she says.
Other places where one can get Eid and Ramadan decorations, as well as trees, include Amazon, Kibsons and noon.com.
DEARBORN — Celebrating Ramadan in the U.S. doesn’t come as naturally as it does in Muslim-majority countries. From fasting during long summer days to lackluster holiday cheer and enduring anti-Muslim sentiments, Muslim Americans have to try just a little harder throughout Islam’s holiest month.
Samar Baydoun Bazzi, a 29-year-old Dearborn resident and nursing student, knows that all too well and is trying to change that— one crecsent tree decorations at a time.
Bazzi told The AANews she remembers feeling like the “odd one out” growing up as a Muslim in Michigan, especially after she began wearing the hijab. During Muslim holidays, she rarely would feel any enthusiasm as gatherings were mostly isolated to family and close friends. Her home would only light up with decorations during Christmas.
Although simple Ramadan-related decorations adorn some properties in Dearborn, Bazzi said she wants to bring a little extra Ramadan spirit to a city that’s home to one of the most concentrated Arab and Muslim American communities and one of the largest mosques in the nation.
“People can get more creative,” she said.
The project, now in its fourth year and selling nationwide, began when Bazzi’s daughter, 4-years-old at the time, thought it was Christmas when she put up a tree along with other banners and crafts, in preperation for Ramadan.
That same day, Bazzi said she took the tree apart and rearranged it in the shape of a crescent moon, a widely-recognized symbol in Islam.
“I wanted her to be excited about her own religion and holiday,” she said about her daughter.
Bazzi, who crafts the trees by hand in her basement, said she quickly learned that many Muslim households face the same obstacles and people wished they’d had such trees in their childhoods.
“The parents want their kids to feel like their own holiday is the most amazing time of the year,” Bazzi said. “It’s a time when they’re supposed to be closer to God, to pray and fast; we want them to fall in the love with the whole process.”
Bazzi said her intention was not to blend Anglo-Christian and Pagan traditions with Islamic ones by using a Christmas tree and that she initially only used a tree because that’s what she had available.
“It really makes no difference to me,” she said. “It doesn’t look like a Christmas tree anymore.”
At a time when political tensions are high and bigoted rhetoric is rampant, Bazzi said her goal is to ensure Muslim Americans, especially the youth, can be unabashedly proud and more openly celebrate their faith.
It takes her about five hours to make each tree. The six-foot-and-eight-inch-tall trees are available in white and green and include lights and a hanging star. They’re being sold nationwide, with requests for them coming from around the world.
Bazzi said the Ramadan Trees have garnered enough interest for a wait list to fill up, forcing her to stop accepting orders this year.
She said she hopes to partner with a manufacturer and expand the project into a large-scale business.
For Samar Baydoun Bazzi, the Ramadan Tree grew out of a desire to mark the Islamic holy month with festive cheer.
Growing up as a Muslim in the U.S., Baydoun Bazzi, 29, of Dearborn said she noticed a lack of decorations during the month-long holiday, which Muslims observe by fasting from sunrise to sundown to commemorate the revelation of the Quran to the prophet Muhammad.
“Obviously, Ramadan’s important,” Baydoun Bazzi said. “You gotta pray and fast, and you want to become closer to your creator. But I never as a kid felt like there was any decorations or like a celebration. I wanted something exciting.”
When she became a mother, she decided to take matters into her own hands and create the kind of Ramadan experience she wished for as a child.
She began by decorating her west Dearborn home with Islamic-themed art, like acrylic paintings of Arabic calligraphy and a cardboard model of a mosque.
It wasn’t enough.
So in 2014, she said, she decided to put up a Christmas tree.
It didn't last long.
“Oh, Christmas!” Baydoun Bazzi remembers her daughter Zahraa, then 4 years old, shouting.
“I knew that it was a mistake,” Baydoun Bazzi said of her decision. “So I looked at my tree and decided to take it apart.”
That’s when the Ramadan Tree first took root.
|
|
|
Are stinky inflatable pool toys putting your kids at risk? |
Posted by: mmws256w - 09-22-2021, 03:27 AM - Forum: Welcomes and Introductions
- No Replies
|
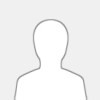 |
The researchers expressed concern that some of the products contain potentially hazardous chemicals that could pose a risk to children’s health, depending on the degree of exposure and concentration levels in the products.
The researchers conducted tests using an inflatable beach ball, a pair of swimming armbands and two bathing rings they bought off the shelf from local stores and online suppliers in Germany.(Shutterstock)
HEALTH
Are stinky inflatable kids' toys putting your kids at risk? Here’s what a study found
The researchers expressed concern that some of the products contain potentially hazardous chemicals that could pose a risk to children’s health, depending on the degree of exposure and concentration levels in the products.
Washington D.C. | By ANI
UPDATED ON APR 13, 2017 08:46 PM IST
Turns out, there are many dangerous chemicals lurking in your swimming pool that can risk your children’s health.
Inflatable sprinkler and swimming aids, like bathing rings and arm bands, often have a distinctive smell which could indicate that they contain a range of potentially hazardous substances.
Some of these compounds, which include carbonyl compounds, cyclohexanone, phenol and isophorone, might be critical when present in higher concentrations in children’s toys, said authors Christoph Wiedmer and Andrea Buettner.
Lead author Wiedmer from Fraunhofer Institute for Process Engineering and Packaging IVV in Germany and his team conducted tests using an inflatable pool, a pair of swimming armbands and two bathing rings they bought off the shelf from local stores and online suppliers in Germany.
A small piece of material from each sample was analysed using a variety of material analysis techniques, including one that takes infrared measurements, and it was concluded that the inflatable objects were all made from polyvinyl chloride (PVC).
The researchers then investigated the molecular make-up of the distinctive smells arising from the pool toys. They extracted detectable odours from each sample using solvent extraction and high vacuum distillation methods, and then identified the main odorants using a combination of sensory and common analytical approaches.
Between 32 and 46 odours were detected in each sample, of which up to thirteen were quite intense. The majority of these odorants were identified and among these were several fatty smelling mono- or di-unsaturated carbonyl compounds and their epoxidised derivatives, but also odouractive organic solvents such as cyclohexanone, isophorone, and phenol.
As part of the study, a panel of trained volunteers sniffed each product, and ascribed common odour attributes to these. They also rated the intensity of each odour, and had to guess whether these could be hazardous. Three of the products reminded the panellists of almonds, plastic and rubber, while the fourth more pungent one reminded them of glue and nail polish.
Wiedmer expressed his concern that some of the products contain potentially hazardous chemicals that could pose a risk to children’s health, depending on the degree of exposure and concentration levels in the products. Cyclohexanone can be harmful if inhaled, phenol is known to be acutely toxic and to presumably have mutagenic potential and isophorone is a category 2 carcinogen, which means that this is a suspect substance in the development of cancer in humans.
“A range of these substances are not yet resolved in their chemical structures. Likewise, potential negative effects on humans, such as irritation, smell nuisance, or other physiological or psychosomatic effects still need to be resolved,” said Wiedmer.
“Modern products such as toys and children’s products are sourced from a wide variety of chemical and physical manufacturing processes, and this complexity often makes it difficult for us to identify those containing contaminants and unwanted substances, and to determine their causes,” noted Wiedmer. “However, we found that in a number of cases our noses can guide us to ‘sniff out’ problematic products.”
The study appears in the journal Analytical and Bioanalytical Chemistry (ABC).
Backyards and patios have been working hard all year because of the pandemic, and this summer they can provide new ways to cool off and have fun in the water.
Whether you have a lot of space or a little, there’s gear ranging from water tables and tubs for kids to floating loungers with drink holders for adults.
One company, Minnidip, makes inflatable “adult kiddie pools” that aim to transport you to some exotic travel destination. Patterns on the Marrakesh pool reference Moroccan architectural details, while the Amalfi is a nod to the blue, yellow and white tile of the Italian coast.
“Because for me, having a pool on our urban Chicago rooftop felt like being transported to another place,” says company founder Emily Vaca. “I wanted to capture that feeling through design and pattern. “
Minnidip also offers inflatable drinks coolers and glam pool balls filled with gold confetti, among other offerings.
The only water table that lets you make waves, Little Tikes’ Island Wavemaker has a water wheel, plus cute sea creatures and a wee pirate to send paddling around the waterway or down the waterfall. Toddlers can practice their fine motor skills with Little Tikes’ Spinning Seas Water Table; small balls, a cup, a funnel and a water wheel set up the fun.
Step2’s two-sided Waterfall Discovery Wall has adjustable toggles, spinners and chutes to send the water tumbling in lots of different ways. And Lakeshore Learning’s Watch It Flow water table features three plastic logs that can be configured however you wish. Fill the logs using a hose or bucket; gates control the flow and can close up to make long tubs.
Foamo, also from the folks at Little Tikes, creates mountains of easy-to-clean-up foam when you add the nontoxic, biodegradable foam solution to water.
HOSE HAPPY
Turn on the hose and attach it to West Elm's inflatable car bed or giant shark mouth sprinklers. Fat Brain Toy’s Hydro Twist Pipeline Sprinkler has a couple of fountains, plus a bunch of wiggly worm hoses. Or hook up to BigMouth’s giant 6-foot-high unicorn, who shoots water out of her horn. There’s a ginormous ape, giraffe, dinosaur and giraffe here as well.
SWIM AND PADDLE
Giant inflatable water wheels let you find your inner hamster. You can find ones online for toddlers, while Wow Watersports has a grownup version they call the Aqua Treadmill.
Don’t forget the family pets; a nonporous, puncture-resistant floating dog bed at Frontgate comes in a bunch of colors and three sizes.
Chewy has ZippyPaws Floaterz sturdy turtle-shaped water toys for dogs, as well as rope-handled bumpers and a variety of floating balls.
A hard-sided kiddie pool can be a good non-inflatable option for cooling off; just hose it out and stow away. Other pluses: The doggos will also have fun splashing around in it, and it makes a great sand or snow play zone in colder weather. The Sun Squad Wading Kiddie Pool is inexpensive and has an embossed bottom, so it’s less slippery.
SLIDE AND RIDE
A basic heavy-duty plastic water slide or “slip and slide” can be set up in most backyards; if yours doesn’t come with an attached barrier at the bottom, make sure to put something soft there.
Studio 21 Graphix’s slide has a crash pad at the finish line, plus two lanes for racing and a sprinkler curtain to pass thru on the way down. Wow Watersports’ Strike Zone Water Slide is 25-by-6 feet of slipperiness; zigzag sprinkler patterns assure a wet ride, fat pontoons on either side keep riders inside, and two sleds are included. Got a really long yard? Get two; they can be interconnected.
If you’ve got lots of space, consider Costway’s inflatable Bounce House and Water Slide, with a bounce area, water gun, two slides, a basketball hoop and several balls. It comes with a storage bag for easy transport.
POOL STYLE
Marisa Issa of Los Angeles says her family’s favorite pool games are corn hole and a floating basketball hoop, but her favorite is a floating mat from Frontgate “that only mom can use,” she says. The sleek, minimalist white float has a headrest, and is made of marine-grade dense foam, suitable for chlorine or saltwater pools.
If you prefer sitting up a little, Frontgate’s got a floating armchair with attached ottoman. Choose from aqua, blue or flamingo pink. Or splash out on a full-size pool chaise kitted out with drink holders.
Want to hang out with a handful of friends in a backyard pool? Funboy has a 9-foot-wide floating metallic crown with drink holders. Or lounge luxuriously in the company’s Bali Cabana Lounger, with a curved integrated shade, a tropical leaf print, cup holders and handy grab ropes.
BigMouth has some food-related inflatables like a giant ice pop, pizza slice, donut, watermelon slice, cheeseburger and taco.
At first, glance, laying on an inflatable toy in shallow water seems pretty safe. After all, the water isn't deep, and there is a floating toy right there. Recently, a family's trip to the beach in Nova Scotia proved to be a harrowing reminder of why this is not the case. In August, two 5-year-olds played in shallow water – one in an inflatable ring, the other on an inflatable roller. Because the girls were in shallow water, their caregiver assumed the inflatable toys were enough. It wasn't until the girls began to drift away from that the complete danger of the situation became clear.
Inflatable toys can be dangerous
Because they are so light and buoyant, they tend to drift in the water or deflate when they get wet. That's when it's a problem. Kids don't know when their toys are deflated and cannot compensate when they're in the water. They can get trapped in the holes or strangle. When the girls got stuck, their caregiver did the right thing by calling for help. First responders rescued the girls and took them to the hospital to be treated for their injuries. While it's infrequent that inflatable toys are the source of injury to kids, it's good to know that they can pose a hazard. The numbers aren't obvious, but it seems that they're responsible for 1 in every 100 boating-related deaths in the U.S. and are one of the leading causes of drowning for children aged 4-6.
Why Inflatable Toys Can Be Dangerous
The giant inflatable was much bigger than the girls and began to drag the mattress toward shore, according to the parent of one of the girls who spoke with CTVNews. However, the inflatable ring wasn't nearly as big or heavy and was drifting with the current. The girls eventually lost hold of both and drifted a considerable distance. The girls' parents rushed to the scene and tried to retrieve their children, but the current was too firm, and the military eventually rescued them. The girls were found to be unharmed. Since this incident, many parents have expressed concerns about the safety of inflatable toys.
|
|
|
Wire Rope Slings |
Posted by: mmws256w - 09-22-2021, 03:26 AM - Forum: Welcomes and Introductions
- No Replies
|
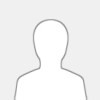 |
Wire rope is constructed of multiple strands of wire that are twisted and braided together to form a spiral design or helix. Once the separate wires are shaped into a solid form, they become a single wire with greater strength because the individual wires equalize pressure and have greater flexibility than the individual strands.
To further enhance the strength of wire ropes, they are grouped and wound together to produce cables, which adds to their usefulness as a means of support, ability to lift, and give structural stability.
A key factor in wire rope is the lay of the strands, which can be regular or lang. With regular lay, or right and ordinary lay, the strands are wound from left to right with the wires laid in the opposite direction of the lay of the strands. With lang lay, the wires are wound in the same direction.
The structure and design of wire rope produces a final product that has superior strength, excellent strength flexibility, and the ability to handle constant bending stress as well as being weather resistant.
Wire rope is one of those products that has found a place in a wide variety of industries since it can be adapted and shaped to fit several applications. It can be found as a tow cable for boats and airplanes or in the movie industry as a harness for stunt artists. The varied uses of wire rope have made it an essential part of operations that require a rope with strength, endurance, and flexibility.
Uses for Wire Rope
Aeronautics –
In the aerospace industry, wire ropes, or Bowden cables, connect pedals and levers in airplane cockpit to send power to aircraft systems to control the airplane. The things that are controlled by wire ropes are propeller pitch, cowl flaps, and throttle. Wire ropes on aircraft are insulated to avoid vibrations.
Wire rope is extensively used in the auto industry for a wide variety of applications due to its versatility and strength. It is used for raising windows and opening and closing sunroofs. Other uses include steering wheels, cables, exhausts, springs, sunroofs, doors, and seat components. In the manufacturing process, wire rope is used to hoist vehicles, move large body parts, and on hoists and cranes.
Construction –
The construction industry has a greatest reliance on wire rope because of the need to lift and lower heavy loads. Wire rope used in construction must have extremely high strength and exceptional performance for safety reasons and efficiency. Larger versions of wire rope are used for suspension bridges and supporting concrete columns.
Food Processing –
The main use of wire rope in food processing is for lifting, moving loads, and other heavy tasks. Finished products or raw materials require being moved in storage units and processing centers. The strength and endurance of wire rope makes it possible to move these materials. Wire rope for food processing must be able to withstand regular chemical cleaning.
Oil and Gas Industry –
As with other industries, the oil and gas industry needs strong and reliable equipment for moving heavy equipment. In ocean drilling, machinery is dropped into the ocean using wire rope to securely hold devices to be dropped to extreme depths. Wire ropes are designed to withstand the extreme pressure and stress required. A further use of wire ropes for drilling operations is to maintain stability in the drilling lines. One of the unique features of oil rig wire rope is its length, which can exceed 10,000 feet.
Marine Industry –
A very common use for wire rope is mooring and towing of sea and freshwater boats and vessels. In the shipbuilding industry, wire rope is used to secure lifeboats as well as lower them into the water. On sailboats, wire rope is used to lift and lower sails. The benefit of using wire rope is its resistance to corrosion and rust caused by salt water and ocean mist.
Skiing –
The skiing industry, much like heavy equipment industries, uses wire rope to hold cars, lifts, or chairs to transport skiers up the mountain. This type of wire rope comes in several varieties depending on the size of the mountain. The benefits of wire rope for skiing is its dependability, guaranteed safety, and reliability. The main challenge of wire rope for use in sports is the weather conditions it must endure.
Amusement Parks –
Since the beginnings of amusement parks, wire rope has been an essential part of attraction construction. It is used to bring roller coaster cars to the top of the ride, hold swings, and pull various vehicles through attractions. One of the main concerns of public amusement parks is safety since rides are filled with powerful machinery designed to operate continuously.
Stunt Work –
Making the dangerous and exciting shots in movies requires well planned safety precautions. One of the aspects of that planning is wire rope that is designed to protect performers when they are engaged in dangerous and life threatening shots. Dependable wire ropes are ideal since they have the flexibility, strength, endurance, and versatility to be adapted to any conditions.
The types of wire rope are determined by the number of wires in each strand and how many are in the rope, which is defined by a two number system with the first number being the number of wires and the second being the number of wires in each strand. For example, a 6x19 wire rope has 6 wires in 19 strands.
The wire below is a 7x7 stainless steel wire rope of grade 302 stainless steel. As can be seen in the diagram, it has seven wires and seven strands.
Types of Wire Rope Products
There are a wide variety of products that are produced using wire rope. The demand for wire rope products is due to its strength, durability, and reliability. Since the basic purpose of wire rope is to lift and move heavy materials and items, the most common type of wire rope product is the wire rope sling.
Wire Rope Slings –
Though the construction of soft eye wire rope sling is very similar for all types, there are certain variations applied to slings to adjust them to fit different applications. Slings are configured in various ways to fit different types of loads. These changes are referred to as hitches.
Hitches –
Vertical Hitch: A vertical hitch is where one eye of the wire rope is attached to the hook and the other eye is attached to the load.
Thimble hand spliced wire rope sling: To add to the strength of wire rope slings and lessen the stress on a small area of the eye, a thimble, a U shaped piece into which the wire rope fits, is placed in the eye, which helps the sling to retain its natural shape. The thimble is positioned to prevent the hook or load from coming in contact with the wire rope.
Coiled Wire Rope –
Coiled wire rope is made from bundles of small metal wires that are twisted into a coil. It comes in many varieties and is easy to store since it does not require a spool. Coiled wire rope is produced in coils. When it is not in use, it springs back into a coil, which makes it easy to handle.
Cable Wire Rope –
Cable wire rope is a type of high strength rope, made of several individual filaments. These filaments are twisted into strands and helically wrapped around a core. One of the most common types of wire rope cable is steel cable.
Push Pull Wire Rope –
Push pull wire rope assemblies are used to send force and are used in the aircraft, exercise, medical, automotive, and office equipment industries. Unlike using a single heavy wire, push pull assemblies made with wire rope are stiffer and have a larger bend radii for smoother motion of the wire.
Wire rope lanyards are a standard wire rope product that have a multitude of uses. They are produced using the same process that is used to produce wire rope with the same numbering categorizing system. Lanyards are used to hold fasteners, hardware, or components to prevent loss of an item or prevent injury.
As can be seen in the image below, lanyards come with a variety of connectors to specifically fit an application. Custom designed lanyards are designed for unusual and unique functions where a standard lanyard will not fit. The variety of connectors allows the lanyard to be easily connected.
Chapter Four – How Wire Rope Products are Made
In many ways, wire rope is a form of machine with multiple moving parts. Normally, when we think of a machine, we imagine a device with a motor, drives, and gears. Wire rope does not have any of those components but does fit the definition of being a complex mechanism. It has moving parts that work together to move heavy materials and loads.
The main function of wire rope is to do heavy lifting, which is very dependent on endless wire rope sling. The type of sling is determined by the quality of the wire rope used to form them and whether several ropes have been braided or wound together.
The Parts of Wire Rope
The parts of wire rope are wire, a core, strands, and lubricant.
Wire –
Wire is the smallest part of wire rope but makes up the various strands. The composition of the wire can be steel, iron, stainless steel, copper, or other types of metal wires and are produced in different grades. The individual wires can be coated or bright, meaning uncoated.
Strands –
Strands are sets of wires that are twisted together and are placed in a helical pattern around the core. The size of the wire determines its abrasive qualities with larger wires being more abrasive and less flexible than smaller ones.
Core –
The core is the center of the wire rope and serves as a support for the strands and helps the wire rope keep its position when it is under stress or bearing a load.
Lubrication –
Lubrication is applied during the manufacturing process to reduce friction between the wires and strands as well as protection from corrosion and rust. The tight winding of the wires enhances the ability of the wire rope to retain the lubrication which is essential to its longevity.
Manufacture of Wire Rope Slings
Of all of the products that are made from wire rope, slings are the most common and widely used. These looped wire ropes come in different varieties and grades depending on the type of wire used. Also, to enhance wire sling performance, several wire ropes may be wound together to form a sturdier and more reliable sling.
Unspooling –
For delivery for processing, wire rope is spooled. The production of grommet wire rope sling begins with unspooling the wire rope.
Installing the Compression Sleeve –
The tails and stray wires of the wire rope have to be straightened and properly formed before applying the compression sleeve. Once the sleeve has been placed, it is carefully checked to be sure that it is accurately engaged.
Swaging –
Prior to placing the wire rope sling in the swaging die, the die has to be thoroughly lubricated. Once the die is set, the wire rope’s compression sleeve and the wire rope are compressed using several hundred thousand pounds of force. The swaging process alters the dimensions of the wire rope and compression sleeve to form a tight connection for the correct diameter for the sling connection. As force is applied, the compression sleeve is turned so that pressure is evenly applied.
|
|
|
Practical Uses of Botanicals in Skin Care |
Posted by: mmws256w - 09-22-2021, 03:24 AM - Forum: Welcomes and Introductions
- No Replies
|
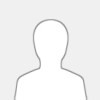 |
Cosmeceuticals are the fastest growing sector of the cosmetic industry, and the future of antiaging cosmeceuticals in particular is very promising. Botanical pesticide that support the health, texture, and integrity of the skin, hair, and nails are widely used in cosmetic formulations. They form the largest category of cosmeceutical additives found in the marketplace today due to the rising consumer interest and demand for natural products. Various plant extracts that formed the basis of medical treatments in ancient civilizations and many traditional cultures are still used today in cleansers, moisturizers, astringents, and many other skin care products. New botanical skin care treatments are emerging, presenting dermatologists and their patients the challenge of understanding the science behind these cosmeceuticals. Thus, dermatologists must have a working knowledge of these botanicals and keep up with how they evolve to provide optimal medical care and answer patient questions. The most popular botanicals commonly incorporated into skin care protocols are discussed.
The cosmeceutical market is one of constant fluctuation depending upon consumer demand. Skin care companies are continuously pressured to release new, innovative products that promise to transform the appearance of aging skin overnight. Over the past decade, there has been fervent interest in products found in nature because of their perceived safety. Skin care products are often developed from plants. Many believe that if a product can be safely ingested, it will also be safe for topical application. In general, plant-derived, botanical feed additives, cosmeceutical products tend to be antioxidant in action since these organisms must thrive in constant direct ultraviolet (UV) light, the Earth's most prolific manufacturer of free radicals. In this article, the authors review the most popular ingredients in this class and comment on their possible usefulness in skin care protocols.
Soy extract has positive research support for its antioxidant, antiproliferative, and anticarcinogenic activities. Topical application of soy has been used to reduce hyperpigmentation, enhance skin elasticity, control oil production, moisturize the skin, and delay hair regrowth.1 Soy also has the potential to decrease photoaging of the skin and prevent skin cancers through the estrogen-type and antioxidant effects of its metabolites.1
The major components of soy are phospholipids, such as phosphatidylcholine and essential fatty acids. The minor components of soy include the most active compounds, such as isoflavones, saponins, essential amino acids, phytosterols, calcium, potassium, iron, and proteases soybean trypsin inhibitor (STI) and Bowman-Birk inhibitor (BBI). The various components of soy have a variety of beneficial effects making them useful additions to skin care products. The most potent isoflavones are the phytoestrogens known as genistein and daidzein. Genistein is a potent antioxidant that inhibits lipid peroxidation and chemical and ultraviolet light B (UVB)-induced carcinogenesis. Genistein was shown to significantly inhibit chemical, carcinogen-induced, reactive oxygen species; oxidative DNA damage; and proto-oncogene expression, as well as the initiation and promotion of skin carcinogenesis in mouse skin.2 Topical estrogens have been shown to promote collagen synthesis and increase skin thickness, which may be beneficial for postmenopausal women who develop a thinner dermis and decreased collagen.3 The small proteases STI and BBI appear to promote skin lightening and reduce unwanted facial and body hair in human clinical trials.3,4 Beyond the depigmenting activity, STI, BBI, and soy milk were also found to prevent UV-induced pigmentation both in vitro and in vivo.5 In addition, soy lipids, lecithins, and phytosterols are believed to restore barrier function and replenish moisture.
Beyond its moisturizing ability, soy appears to be a safe and effective treatment for postmenopausal women and for hyperpigmentation disorders (other than melasma, which is somewhat estrogen mediated). Although further research is necessary, the antioxidant and anticarcinogenic activities of soy and its isoflavones show a promising role for this botanical fertilizer additives in the cosmeceutical industry. Soy has therefore become a popular addition to a wide variety of skin care products (see Table 1).
Green tea extracts are among the fastest-growing herbal products. While there has been enormous growth in green tea consumption as a dietary supplement, the use of tea extracts in cosmeceutical formulations is also on the rise. The complex polyphenolic compounds in tea provide the same protective effect for the skin as for internal organs. They have been shown to modulate biochemical pathways that are important in cell proliferation, inflammatory responses, and responses of tumor promoters.6 Green tea has been shown to have anti-inflammatory and antioxidant effects in both human and animal skin.
Since inflammation and oxidative stress appear to play a significant role in the aging process, green tea may also have antiaging effects by decreasing inflammation and scavenging free radicals. Researchers have found that the main active ingredient in green tea, epigallocatechin-3-gallate (EGCG), works well as an anti-inflammatory, antioxidant, and sunscreen. Topical green tea applied to human skin has been shown to provide a photoprotective effect, reduce the number of sunburn cells, protect epidermal Langerhans cells from UV damage, and reduce the DNA damage that formed after UV radiation.7 Green tea polyphenols, when combined with traditional sunscreens, may have an additive or synergistic photoprotective effect. Green tea has also been found to decrease melanoma cells in tissue culture and squamous cell carcinoma cell formation in mice with topical and oral administration. Additionally, it improves wound healing by increasing keratinocyte cell differentiation and has been shown to inhibit Streptococcus species and Escherichia coli.8
Natural flavonoids, such as green or black tea polyphenols have been show to reduce UVB-induced erythema, tumorigenesis, and immunosuppression in mice.9,10 White tea appears to be a more potent antioxidant than green tea. Black tea has a much lower content of catechins than green tea, but a higher content of other flavonoids, such as quercetin, theaflavin, and kaempferol. Black tea extracts applied before and after UV light challenge have been shown to decrease signs of cutaneous photodamage, carcinogenesis, and inflammation in human and mouse skin.3
Most cosmeceutical products containing tea extracts or phenols have not been tested in controlled clinical trials, but these substances have shown compelling evidence for antioxidant, anti-inflammatory, and anticarcinogenic activities. There are currently several products that contain green tea extract on the market (see Table 2). Unfortunately, the concentration of phenols is not standardized in these products; therefore, some products may have little-to-no therapeutic effect, making purchasing them a challenge for consumers. It is generally accepted that five-percent green tea extract or polyphenols in the 90-percent range is an effective concentration.
German chamomile, or Matricaria recutita, has been used throughout history as an herbal treatment for various skin conditions. It functions as an antimicrobial, antiallergic, anti-inflammatory, antioxidant, and analgesic and was approved by the German Commission E for inflammatory mucocutaneous diseases and wound and burn therapy.3 The active constituents of chamomile include the terpenoids (bisoprolol, matricine, levomenol, chamazulene), flavonoids (apigenin, luteolin, rutin, quercetin), hydroxycoumarins, mono- and oligosaccharides, and mucilages. Chamazulene exhibits anti-inflammatory activity and promotes wound healing. Levomenol is an anti-inflammatory and natural moisturizing agent that has been found to diminish the signs of photodamage, reduce pruritus, and ameliorate skin texture and elasticity. In addition to reports of anti-inflammatory effects, chamomile is also purported to have some antioxidant properties, which have been identified through chemical assays.11,12
While chamomile is generally considered a safe product, there have been reports of contact dermatitis and conjunctivitis following topical application of chamomile products, and there is a potential risk of angioedema and anaphylaxis. Chamomile can also interact with warfarin, promoting an additive anticoagulant effect.
Clinical studies appear to support the traditional uses and therapeutic benefit of topical chamomile. This herb has been included in a wide variety of cosmetic products including soothing moisturizers and cleansers as well as color-enhancing hair products (see Table 3).
Caffeine, the chemical pesticide in coffee, tea, and some soft drinks, has demonstrated both anticarcinogenic and antioxidant properties. Initially, caffeine's potential inhibitory role in cancer development was found through studying oral administration of black and green tea.13 This study illustrated that the oral administration of caffeine alone and the addition of caffeine to decaffeinated teas showed inhibitory effects of UVB-induced carcinogenesis. Oral administration of caffeine has also been associated with in-vivo upregulation of tumor suppressor genes.14
Continued research revealed that topical application of caffeine inhibits carcinogenesis and promotes apoptosis in sunburn cells of hairless SKH-1, UVB-pretreated mice.15 Researchers found that topical application of the tea constituents caffeine and (-)-epigallocatechin gallate (EGCG) decreased the number of nonmalignant and malignant skin tumors in SKH-1 hairless mice pretreated with UVB. While caffeine performed better than EGCG, both treatments resulted in elevated apoptosis in nonmalignant skin tumors and squamous cell carcinomas. The results suggest a need for further studies to determine whether topical applications of caffeine or EGCG can inhibit sunlight-induced skin cancer in humans. Further studies by the same authors found that topical application of caffeine sodium benzoate and caffeine have both a sunscreen effect and enhance UVB-induced apoptosis and may be good agents for inhibiting the formation of sunlight-induced skin cancer.16
These studies present a potential use for caffeine in formulations used to decrease the risk of skin cancer formation after cutaneous damage from UV exposure. More studies need to be done to further examine caffeine's antioxidant potential. The above findings have prompted many manufacturers to add this popular agent to various cosmeceutical products on the market today (see Table 4).
Coffeeberry, harvested from the fruit of the coffee plant Coffea arabica, is considered to be one of the richest sources of antioxidants and is well known for its skin-rejuvenation properties. Coffeeberry contains potent polyphenols including chlorogenic acid, ferrulic acid, quinic acid, and condensed proanthocyanidins. The dermatologic application of CoffeeBerry® (J&J Technologies LC) extract was first recognized at the American Academy of Dermatology's Annual Meeting in February 2007. The first product to enter the market with CoffeeBerry as the basic ingredient is RevaléSkin (Stiefel Laboratories, Inc., Coral Gables, Florida) (see Table 5).
According to Stiefel Laboratories, Inc., CoffeeBerry has demonstrated high antioxidant properties, outperforming green tea extract and vitamins C and E. Proprietary research from the manufacturer has also shown that the use of the RevaléSkin CoffeeBerry skin care system consisting of 0.1% CoffeeBerry cleanser and 1% day and night creams showed statistically significant improvement in fine lines, wrinkles, pigmentation, and overall appearance when compared to vehicle. In addition to the evidence of safety and efficacy provided by the randomized, double-blind trials, further support comes from positive pathologic and in-vitro studies showing enhanced collagen production by fibroblasts. Studies are currently in progress to evaluate the use of the CoffeeBerry skin care system in conjunction with retinoids and intense pulsed-light treatments.17 More clinical studies need to be performed to fully assess the topical preparations containing CoffeeBerry extract, but polyphenols have already demonstrated efficacy in photoaging and skin cancer prevention.
The inclusion of botanical animal remedy additives in skin care products is becoming ever more popular. Potential antioxidant and anti-inflammatory benefits may prove beneficial for a number of conditions that dermatologists routinely treat, such as rosacea, photoaging, and skin cancer. The published effectiveness of prescription retinoids is well known, but equally well known is the irritation and redness often caused by the initiation of therapy. Botanicals may hold the promise of utility to reduce such inflammation. This is one of the best and most practical reasons to include botanicals in skin care protocols. Dermatologists should be aware of these products and be able to discuss their uses and potential benefits with their patients.
|
|
|
Pipe Fittings |
Posted by: mmws256w - 09-22-2021, 03:21 AM - Forum: Welcomes and Introductions
- No Replies
|
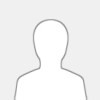 |
This chapter presents various types of pipe fittings. Of all the fittings, the elbow is the one most often used. Simply put, the elbow, or ell, is used when a pipe changes direction. Elbows can turn up, down, left, right, or any angle in between. When one finds it necessary to draw a 90° elbow or calculate how much space it will occupy in a routing configuration, knowing its length becomes essential. An elbow's length is commonly referred to as the center-to-end dimension and is measured from the centerpoint of its radius to the end of either opening. Dimensional sizes of fittings are typically provided by the manufacturer of the fitting. Manufacturers issue dimensioning charts containing lengths for a particular fitting. Another elbow that may be used under certain circumstances and with permission from the customer is the 90° short-radius elbow. The 90° short-radius ell makes a much sharper turn than does the long-radius ell.
Emissions from Pipe Fittings and Gaskets
Threaded pipe fittings in the seal flush line can be significant leak sources, with readings above 1,000 ppm.4,17 Similar emission levels may be measured near the gasket region on the seal chamber face. Any leakage from these areas may drift into the emission measurement area for the mechanical seal. The mechanical seal may then be erroneously implicated as a leaker. It should be standard practice to sniff nearby hydraulic fittings and the flange gasket area if excessive VOC concentrations are detected adjacent to the mechanical seal.
Leak-tight threaded pipe fittings can be more easily attained using anaerobic paste-type sealants rather than PTFE tape. The seal chamber face must be smooth to be emission tight. Gaskets and O-rings must be free of nicks and scratches.
32.16.2 Thermoplastic Fittings Manufacturing
Thermoplastic pipe fittings may be injection-molded, fabricated, rotomolded, or thermoformed. Injection-molded fittings are generally made in sizes through 12-in. nominal diameter. Typical molded fittings are tees, 45-degree and 90-degree elbows, reducers, couplings, caps, flange adapters, stub ends, branch saddles, service saddles, and self-tapping saddle tees. Electrofusion couplings and fittings are either made by injection molding or machined from pipe stock. Electrofusion fittings and couplings are made with a coil-like integral heating element incorporated into the fitting. Joining with other fittings uses an electrical fusion device that provides electricity into the heating element, which melts the adjacent thermoplastic material and creates a fusion-welded joint.
Larger-diameter fittings exceed the capabilities of injection molding and are typically fabricated. Rotomolding is used for the manufacture of polyethylene large-diameter (up to 60 in.) and custom fittings for polyethylene corrugated drainage piping applications.
Thermoformed fittings are made by heating a section of pipe and then using a forming tool to reshape the heated area. Examples of thermoformed fittings are sweep elbows, swaged reducers, and forged stub ends. Some polyethylene corrugated pipe fittings and appurtenances are also thermoformed.
All proprietary joints shall be made in accordance with the manufacturer’s instructions. Care shall be taken to establish satisfactory jointing techniques for all water service pipework. When making joints by welding, brazing, or soldering, precautions shall be taken to avoid the risk of fire. All burrs shall be removed from the ends of pipes and any jointing materials used shall be prevented from entering the waterways. All piping and fittings shall be cleaned internally and free from particles of sand, soil, metal filings, and chips, etc.
8.19.3 Cast iron pipes
Flexible mechanical joints shall be made in accordance with the manufacturer’s instructions.
For molten lead joints, the spigot and socket shall be centered with rings of dry yarn caulked tightly into the bottom of the spigot to prevent the entry of lead into the bore of the pipe and to prevent contact of lead with the water.
Synthetic yarns that do not promote the growth of bacteria shall be used to prevent contamination of the water. The remainder of the joint space shall be filled with molten lead (taking care that no dross enters the joint), cold wire, strip, or spun lead (lead wool). The joint shall be caulked to a smooth finish with pneumatic tools or a hand hammer of mass not less than 1.5 kg. When working with spun lead, caulking tools shall be of a thickness to fill the joint space, ensuring thorough consolidation of the material to the full depth of the socket.
Lead joints shall be finished about 3 mm inside the face of the socket.
Flange joints shall be made with screwed or cast on flanges.
8.19.4 Steel pipes
Welded joints shall not be used where a protective lining would be damaged by heat, or where the pipework is employed as a primary circulation to an indirect hot water heating system.
Screwed joints in steel piping shall be made with screwed socket joints using wrought iron, steel, or malleable double crimping fitting. A thread filler shall be used. Exposed threads left after jointing shall be painted or, where installed underground, thickly coated with bituminous or other suitable corrosion preventative agent.
Flange joints shall be made with screwed or welded flanges of steel or cast iron using jointing rings and, if necessary, a suitable jointing paste. The nuts shall be carefully tightened, in opposite pairs, until the jointing ring is sufficiently compressed between the flanges for a watertight joint.
8.19.5 Unplasticized PVC pipes
8.19.5.1 Mechanical joints
Mechanical joints in unplasticized PVC piping of sizes 2 and upwards shall be made in accordance with BS4346: Part 2, by the use of push-fit integral elastomeric sealing rings which are compressed when the plain ended pipes are inserted into the adjoining sockets. The plain pipe ends shall be chamfered and the surfaces cleaned and lubricated.
The chamfered pipe end shall be inserted fully into the adjoining socket (except where provision is to be made for expansion), or as far as any locating mark put on the spigot end by the manufacturer. The sealing rings shall comply with BS2494.
8.19.5.2 Compression joints
Compression joints shall only be used with unplasticized PVC piping of size 2 and smaller. The joints shall be of the nonmanipulative type. Care shall be taken to avoid overtightening.
8.19.5.3 Solvent cement welded joints
Solvent cement welded joints in unplasticized PVC piping shall be made using solvent cement complying with BS4346: Part 3 recommended by the manufacturer of the pipe. The dimensions of the spigots and sockets shall comply with BSEN1452: Part 1–5.
Joints may also be made using integral sockets formed in the pipes and solvent cemented.
8.19.5.4 Flanged joints
Flanged joints used for connections to valves and fittings shall use full-face flanges or stub flanges, both with corrosion resistant or immune backing rings and bolting.
8.19.5.5 Polyethylene pipes
Mechanical joints shall be either plastics or metal proprietary compression fittings, for example, brass, gunmetal, or malleable iron. These shall include insert liners to support the bore of the pipe except where the manufacturer of the fitting instructs otherwise.
To ensure satisfactory jointing of the materials from which the pipe and transition elbow are made compatibility shall be established. The manufacturer’s instructions shall be carefully followed.
No attempt shall be made to joint polyethylene piping by solvent cement welding.
Large pipe fittings and valve components must be press forged and will require extensive machining. Whereas small parts such as the flange previously described can be quickly heated and cooled, and given optimum process conditions, should exhibit microstructure and properties similar to pipe and tube, the properties of large forgings will be location and thickness dependent. While no large forged part has yet been made from 740H, the properties of a solution-annealed, water-quenched and aged 343-mm-diameter bar shown in Table 14.2 are informative. Yield strength near the surface is comparable to that of thin wall tube, but yield strength at the bar center, while meeting ASME minimum, is significantly lower. Ductility and toughness were good. A hardness traverse taken on the as quenched bar showed VHN 170 at the surface and VHN 290 at the center. This is indicative of strong auto-aging in the bar center. Because the γ′ that forms on slow cooling is relatively coarse, after the final aging treatment, the bar center will have lower strength than the surface. The microstructure and creep strength at the center of the bar has not been evaluated.
A calculated continuous cooling transformation diagram for alloy 740H is shown in Fig. 14.26. This diagram supports the notion that significant γ′ hardening will occur even during water quenching of a large forging. A cooling simulation was conducted for the bar heat treatment using DEFORM software [49]. The cooling rate at a depth of 25 mm was 315°C/min and at the bar center was 30°C/min. Based on the calculated CCT diagram, there should be about 10% γ′ in the center and no γ′ at the surface. That is consistent with the experimental results.
Filament-wound pipe fittings, such as elbows and tees have been used in the chemical, and oil industry since the 1980s.9 Traditionally, composite pipe fittings were produced manually or semi-manually, but the development of CNC winders with six or more axes has allowed automated production of pipe fittings since the 1990s. The efficiency of these advanced machines depends on methods and software to determine winding patterns and perform fabrication of the complex shape within manufacturing specifications. Winding pattern generation is particularly challenging since a substantial amount of data storage/processing is required to meet manufacturing requirements (e.g., fiber tension and full-coverage) of non-axisymmetric patterns, which are required for filament-wound elbows or tees.72 On the other hand, it is worth noting that CAM software capability, rather than hardware, is considered the limiting factor for improving the performance of automated winders of non-axisymmetric parts. Consequently, general-purpose filament winding systems for pipe fittings are currently deemed impractical due to the lack of universal mathematical models and design software for CAM.9,73 Although some progress has been made to determine closed-form solutions for efficient winding patterns on specific shapes, such as elbows,74,75 most CAM systems still implement approximate methods to design and produce specific pipe fitting geometries.73 An illustration of a software-generated winding pattern, and the resulting wound elbow, is included in Fig. 11.75
Leaking valves and pipe fittings are the next concern when pressure is dropping during a test. Test sections should be isolated at pipeline block valves by using slip blinds to insure no leakage. If the test section cannot be blinded but the valves are double blocked instead, the operator must measure pressure increase in the adjacent section between the double-blocked valves to insure a tight seal exists. You need to be careful when using a thin “fire blind” at an isolation valve because under pressure the thin blind will deform and the blind cannot be removed without removing the entire valve. This often requires calling in vacuum trucks to remove product on the opposite side of the test valve being removed.
So, leakage through valves and fittings jeopardizes the chances for a successful test and may lead to data that cannot be correlated, and in that situation, the pipeline must be retested.
Tree piping is defined as all pipe, fittings, or pressure conduits, excluding valves and chokes, from the vertical bores of the tree to the flowline connections. The piping may be used for production, pigging, monitoring, injection, servicing, or testing of the subsea tree. Inboard tree piping is upstream of the first tree wing valves. Outboard tree piping is downstream of the first tree wing valve and upstream of the flowline connector.
Tree piping is normally designed in accordance with ASME B31.3. The guidelines in the API specifications are general and, in many cases, open to interpretation. It is up to the manufacturer to apply his engineering judgment.
|
|
|
|