Welcome, Guest |
You have to register before you can post on our site.
|
Online Users |
There are currently 238 online users. » 0 Member(s) | 238 Guest(s)
|
Latest Threads |
Serious dating platform
Forum: Off Topic
Last Post: axied12
Yesterday, 05:05 AM
» Replies: 0
» Views: 22
|
Download mods for games
Forum: Off Topic
Last Post: axied12
08-10-2025, 05:59 AM
» Replies: 0
» Views: 183
|
Online gaming
Forum: Off Topic
Last Post: axied12
08-05-2025, 07:09 AM
» Replies: 0
» Views: 218
|
bespoke window film
Forum: Off Topic
Last Post: axied12
07-30-2025, 09:24 AM
» Replies: 0
» Views: 214
|
Dominica visa free countr...
Forum: Off Topic
Last Post: axied12
06-24-2025, 12:37 PM
» Replies: 0
» Views: 421
|
Advanced microneedling
Forum: Off Topic
Last Post: axied12
05-28-2025, 01:25 PM
» Replies: 0
» Views: 538
|
Caviar and cheese
Forum: Off Topic
Last Post: axied12
05-28-2025, 12:38 PM
» Replies: 0
» Views: 492
|
Top-rated countertop comp...
Forum: Off Topic
Last Post: axied12
05-04-2025, 06:42 AM
» Replies: 0
» Views: 648
|
Ryanair letenky levně do ...
Forum: Off Topic
Last Post: axied12
02-11-2025, 01:37 PM
» Replies: 0
» Views: 1,021
|
Trusted essay writing ser...
Forum: Off Topic
Last Post: axied12
01-30-2025, 08:16 AM
» Replies: 0
» Views: 934
|
|
|
Paribet Online Betting India |
Posted by: axied12 - 08-02-2024, 11:36 AM - Forum: Off Topic
- No Replies
|
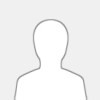 |
![[Image: 51cc68c3b8.jpg]](https://dl4.joxi.net/drive/2024/08/02/0053/2918/3529574/74/51cc68c3b8.jpg)
Do you want to find information about the sports betting website Paribet, which is a recognized leader in this area in India? Visit the paribet.in website, which offers useful information. Methods of registration in bookmakers, depositing money into a personal account and withdrawing it, installing mobile applications, features of choosing the best company with good bonuses and high odds, honest reviews - on the resource you can get data in one click. It is also worth noting the lack of registration, which is appreciated by many people. Other advantages of the site include such as a pleasant interface, reliability of information, uninterrupted operation of pages, convenient search for the desired section, the presence of recommendations for placing bets and the availability of materials 24/7. Visit paribet.in - we work for you!
Paribet Online Betting India https://paribet.in/
|
|
|
Unique prom dress |
Posted by: axied12 - 05-26-2024, 07:16 PM - Forum: Off Topic
- No Replies
|
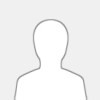 |
![[Image: 9ea9095466.jpg]](https://dl3.joxi.net/drive/2024/05/26/0053/2918/3529574/74/9ea9095466.jpg)
On the hunt for chic women's fashion? Look no further! If you're in need of a trustworthy seller, sunsetfashionla.com has got you covered. We offer appealing terms to all our customers. Our inventory is brimming with a wide range of options, including mini, midi, and maxi dresses, crop tops, bodysuits, skirts, cardigans, shirts, blouses, shorts, jackets, T-shirts, blazers, trousers, and activewear, ensuring every shopper finds their perfect fit. Our unwavering dedication to top-tier product quality is reflected in our stellar reviews. Enjoy speedy delivery and browse through our stunning collection of earrings, necklaces, bracelets, rings, footwear, bags, headwear, and sunglasses to elevate your look. With prices that won't break the bank, shopping at sunsetfashionla.com is both convenient and rewarding. Need more information? Don't hesitate to contact our dedicated team for swift assistance!
Buy unique prom dress.
|
|
|
Быстрые кредиты онлайн на карту |
Posted by: axied12 - 03-25-2024, 01:16 PM - Forum: Off Topic
- No Replies
|
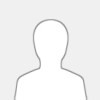 |
![[Image: 1711370667973.jpg]](https://seodoctor.org/images/1711370667973.jpg)
Онлайн-займы, дебетовые и кредитные карты бывает непросто подобрать. Хотите найти лучшие на сегодня условия? Заходите на портал credits-on-line.ru, где вы найдете массу надежных банков и микрофинансовых организаций РФ — мы предлагаем необходимые сведения о каждой из имеющихся в списке компаний: название банка, номер регистрационного свидетельства, процент одобрения, максимальная сумма, процентная ставка, минимальный возраст заемщика и пр. Немаловажным аргументом будет также большой выбор организаций, пришедшийся по душе многим пользователям. К иным достоинствам сайта стоит отнести такие, как отсутствие обязательных регистраций, доступность сведений в круглосуточном режиме, точность информации и возможность получить бесплатную консультацию специалистов при звонке на горячую линию. Ждем вас на портале credits-on-line.ru — мы работаем специально для вас!
Быстрые кредиты онлайн на карту https://credits-on-line.ru/
|
|
|
binebi dgiurad batumshi |
Posted by: axied12 - 02-12-2024, 09:21 AM - Forum: Off Topic
- No Replies
|
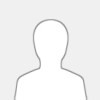 |
![[Image: 1707729651235.jpg]](https://seodoctor.org/images/1707729651235.jpg)
ბინები დღიურად ქირავდება ბათუმში: შენი სახლი სახლიდან შორს
შავი ზღვის სანაპიროზე მდებარე ბათუმი ერთ-ერთი ყველაზე მიმზიდველი ტურისტული ადგილია საქართველოში. არა მხოლოდ თავისი პლაჟებით, არამედ არქიტექტურით, სამზარეულოთი და ზოგადი ატმოსფეროთი ეს ქალაქი ყოველწლიურად ათასობით ტურისტს იზიდავს. მოგზაურობის დაგეგმვისას ერთ-ერთი მნიშვნელოვანი საკითხია საცხოვრებელი ადგილის არჩევანი. ამ მხრივ, ბათუმში ბინების დღიური გაქირავება გთავაზობთ შეუდარებელ შესაძლებლობებსა და კეთილმოწყობას. მოდით შევხედოთ, რატომ შეიძლება იყოს ეს შესანიშნავი ვარიანტი თქვენი ყოფნისთვის ამ ულამაზეს ქალაქში.
თავისუფლება და კომფორტი
ბათუმში დღიურად გაქირავებული ბინების გაქირავების ერთ-ერთი მთავარი უპირატესობაა საკუთარი ფართით სარგებლობის შესაძლებლობა. სასტუმროს ნომრებისგან განსხვავებით, აპარტამენტები გვთავაზობენ ბევრად მეტ სივრცეს, ასევე კეთილმოწყობას, როგორიცაა სამზარეულო, მისაღები და ცალკე საძინებლები. ეს ქმნის მყუდრო ატმოსფეროს, რომელსაც შეუძლია თქვენი დასვენება კიდევ უფრო სასიამოვნო გახადოს.
დაზოგვა და მოქნილობა
ბინის დღიურად დაქირავება ბათუმში ასევე შეიძლება იყოს ეფექტური გამოსავალი. ხშირად ბინაში ღამისთევის ფასი შეიძლება იყოს უფრო დაბალი, ვიდრე საშუალო სასტუმროში, განსაკუთრებით თუ მოგზაურობთ ჯგუფთან ან ოჯახთან ერთად. გარდა ამისა, ქირავნობის მოქნილი პირობები საშუალებას გაძლევთ აირჩიოთ თქვენი ყოფნის ხანგრძლივობა თქვენი გეგმებისა და პრეფერენციების მიხედვით.
ლოკალიზაცია და მრავალფეროვნება
ბათუმი გთავაზობთ საცხოვრებლის მრავალ ვარიანტს, ხოლო ბინის დღიურად დაქირავება საშუალებას გაძლევთ აირჩიოთ თქვენთვის საუკეთესო ადგილი. შეგიძლიათ აირჩიოთ ბინა ქალაქის ცენტრში, სანაპიროსთან ახლოს, ან წყნარ, თვალწარმტაც უბანში. ეს გაძლევთ შესაძლებლობას ისარგებლოთ ყველა იმ უპირატესობით, რომელსაც ქალაქი გთავაზობთ თქვენთვის შესაფერის ადგილას ყოფნისას.
ადგილობრივი გამოცდილება და მასპინძელი სტუმართმოყვარეობა
ნაქირავებ ბინაში ყოფნის ერთ-ერთი განსაკუთრებული ასპექტია ადგილობრივებთან ურთიერთობის შესაძლებლობა. ბინების მეპატრონეები ხშირად სთავაზობენ რეკომენდაციებს საუკეთესო მოსანახულებლად ადგილების, რესტორნებისა და მაღაზიების შესახებ, რაც ეხმარება სტუმრებს თავი ისე იგრძნონ უცხო ქალაქში.
დაჯავშნის სიმარტივე ონლაინ პლატფორმების საშუალებით
ბათუმში ბინის დღიურად გაქირავება გამარტივდა ონლაინ პლატფორმების წყალობით, როგორიცაა Airbnb, Booking.com და სხვა. თქვენ შეგიძლიათ მარტივად იპოვოთ და დაჯავშნოთ შესაფერისი ბინა სხვა სტუმრების ფოტოების, აღწერილობებისა და მიმოხილვების ნახვით.
მთლიანობაში, ბათუმში ბინის დღიურად დაქირავება გთავაზობთ უნიკალურ შესაძლებლობას დატკბეთ ამ ულამაზეს ქალაქში თქვენი საკუთარი პირობებით. თავისუფლება, კომფორტი, დანაზოგი და ადგილობრივ ცხოვრებაში ჩაძირვის შესაძლებლობა ამ საცხოვრებლის ვარიანტს აქცევს იდეალურ არჩევანს ყველა ასაკისა და პრიორიტეტის ტურისტებისთვის.
https://binebidgiurad.net/batumi
|
|
|
Sustainability training |
Posted by: axied12 - 02-01-2024, 09:23 AM - Forum: Off Topic
- No Replies
|
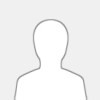 |
![[Image: 1706773454310.jpg]](https://seodoctor.org/images/1706773454310.jpg)
Enterprises are well aware of the challenge in expediting the adoption of sustainability practices among employees, encouraging the embrace of new behaviors grounded in knowledge and action. To overcome this obstacle, we recommend harnessing the capabilities of the 2030.builders platform. The process is simple – just submit your application, requiring minimal time investment. Among our numerous advantages, notable features include easy access to a unique methodology for sustainable development implementation, personalized content, training opportunities, holistic data analysis, targeted audience segmentation, a diverse service array, extensive industry experience, and exemplary support services. This list merely scratches the surface of what each 2030.builders user receives. Need assistance? Utilize our dedicated form for expert advice, provided free of charge!
Sustainability training https://2030.builders/
|
|
|
|