Welcome, Guest |
You have to register before you can post on our site.
|
Online Users |
There are currently 223 online users. » 0 Member(s) | 221 Guest(s) Bing, Google
|
Latest Threads |
Dominica visa free countr...
Forum: Off Topic
Last Post: axied12
06-24-2025, 12:37 PM
» Replies: 0
» Views: 206
|
Advanced microneedling
Forum: Off Topic
Last Post: axied12
05-28-2025, 01:25 PM
» Replies: 0
» Views: 333
|
Caviar and cheese
Forum: Off Topic
Last Post: axied12
05-28-2025, 12:38 PM
» Replies: 0
» Views: 294
|
Top-rated countertop comp...
Forum: Off Topic
Last Post: axied12
05-04-2025, 06:42 AM
» Replies: 0
» Views: 445
|
Ryanair letenky levně do ...
Forum: Off Topic
Last Post: axied12
02-11-2025, 01:37 PM
» Replies: 0
» Views: 837
|
Trusted essay writing ser...
Forum: Off Topic
Last Post: axied12
01-30-2025, 08:16 AM
» Replies: 0
» Views: 752
|
Bootverkopers - actieve j...
Forum: Off Topic
Last Post: axied12
12-07-2024, 11:07 AM
» Replies: 0
» Views: 878
|
Services for individuals ...
Forum: Off Topic
Last Post: axied12
12-02-2024, 03:31 PM
» Replies: 0
» Views: 855
|
Used excavators
Forum: Off Topic
Last Post: axied12
11-13-2024, 09:22 AM
» Replies: 0
» Views: 800
|
Buy Higo Rocket in Dubai
Forum: Off Topic
Last Post: axied12
10-25-2024, 01:09 PM
» Replies: 0
» Views: 909
|
|
|
Are Hoverboards Dangerous? |
Posted by: D133H - 10-08-2021, 07:46 AM - Forum: FPS and Shooters
- No Replies
|
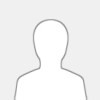 |
Are Hoverboards Dangerous?
Are Hoverboards Dangerous?
When hoverboards hit the scene in 2015, they were an immediate success. Also known as self-balancing or two-wheeled boards, these toys can be a fun way to get around. However, many parents began to wonder — just how dangerous are hoverboards?
Shortly after their debut, several manufacturers started selling hoverboard that were not inspected for quality or safety. News reports revealed potential hoverboard dangers — motorized boards spontaneously overheating, catching fire and causing burns. To date, more than 300 of these incidents have been reported to the Consumer Product Safety Commission.
Newer hoverboards don’t pose the same level of fire risk. If you have an older model, visit the Consumer Product Safety Commission to see if there’s been a recall. All hoverboards should be compliant with the UL 2272 safety standard.
However, even if your child has one of the newest models, there are still hoverboard dangers to consider. After all, two-wheeled boards can be difficult to balance on, and falls resulting in injuries are not at all uncommon.
A Look at Hoverboard Injury Statistics
How often does a fall result in a serious hoverboard injury? Statistics from the American Academy of Pediatrics study show that about 26,854 children visited an emergency department with a hoverboard injury during 2015 and 2016. The average age of an injured child was 11, with boys being slightly more common than girls (52 percent of the children seen were boys).
Children were most likely to injure their wrists, forearms and heads. The most common injuries were:
Fractures (40 percent)
Bruises (17 percent)
Strains/sprains (13 percent)
While these hoverboard injury statistics may seem alarming, many other wheeled toys — that have been around much longer — result in trips to the emergency room as well. During the same 2015 to 2016 time period, skateboards caused almost 121,400 injuries.
How Does a Hoverboard Work?
Do you ever daydream about the future? What might the world be like in a few decades? Could there be cars without drivers? Trucks that fly? Boats driving on land and water?
You may already know about self-driving cars and self balancing hoverboard. But what about hoverboards? Picture it: You’re flying down the sidewalk on an object that looks like a skateboard without wheels. You turn a corner, swerve around other people, and get home from school in record time, without ever touching the ground!
Does this sound like science fiction? Think again! Hoverboards are already a reality. But how do they work?
The “hoverboards” you may have seen friends riding are actually self-balancing scooters. These scooters don’t hover above the ground. Instead, they use two wheels to get around.
Okay, so why are they called HOVERboards? People call self-balancing scooters “hoverboards” because of the sensors that help them stay balanced. The board’s sensors find out which way the rider is leaning. They then tell the board’s motor how fast and in what direction to spin. That’s how this “hoverboard” stays balanced!
Self-balancing scooters rely on a battery pack for power, and each one contains a logic board. You can think of this as the “brain” of the hoverboard. It processes things like the speed of the board and the tilt of its wheels. The logic board also manages settings. For example, hoverboards can be put in beginner mode to limit their maximum speed.
If you’re not satisfied with a self-balancing scooter, have no fear! Hoverboards with no wheels are coming soon—and they’ll truly float above the ground. Some of these hoverboards may use the science of magnets. They will have hover engines that contain electrically charged magnets, or electromagnets. These use an inductor to create a powerful magnetic field. When the magnetic field is strong enough, the board will float in the air!
A company called Omni has also created a hoverboard that uses propellers. Their design even holds the Guinness World Record for the farthest flight by hoverboard. It traveled 275.9 meters (905.2 feet). The Omni hoverboard is expected to hit the shelves in late-2021.
Would you like to travel by hoverboard? Do you see a future of these vehicles zooming through the streets? Or do you imagine even better ways of getting around? Anything is possible!
What is an all terrain hoverboard?
These are similar to the original hoverboards in how they work, but they are generally bigger, stronger and more durable. Instead of being a traditional 6.5 inch hoverboard, most have 8.5 or 10 inch wheels. Instead of solid rubber tires (which are only suitable for smooth ground) they have pneumatic tires for travelling safely and smoothly over a variety of terrains including grass, gravel and sand for a more exciting riding experience. This makes them far more versatile and more fun because you can use them almost anywhere. Most all terrain hoverboards even come with builtin bluetooth hoverboard capability AND they’re suitable for kids and adults of all ages!
Back in 2015 hoverboards hit the market with a bang. These two wheeled self balancing scooters became THE hot product of the year, and although they hit a few blips along the way (inferior quality models with cheap batteries caused some fire problems in the early days), they have only gone from strength to strength since then. In 2016 Underwriter Laboratories introduced the UL 2272 hoverboard certification, so hoverboards are now safer and higher quality than ever. In 2021 technology has advanced to the stage where we now have all terrain hoverboards that can travel over grass, sand, gravel and more (the traditional hoverboards that first came on the market were only suitable for smooth pavement). In this article I’m going to be discussing which is the best off road hoverboard available today.
Hoverboard? Still in the Future
The hoverboard is fiction, the vision of screenwriters who created the film about Marty McFly, a teenager who travels from 1985 to Oct. 21, 2015, and uses a floating skateboard to flee a gang of bullies.
The movie had other futuristic items, like flying cars and self-tying shoes, but none touched the imagination as much as the hoverboard. For the last 25 years, garage tinkerers, physics professors and top engineers at Google have been trying to make one.
Inside a drab office park here in Northern California, Greg and Jill Henderson are working on the latest effort. On a recent visit the couple allowed a reporter to stand atop a noisy magnetic skateboard that can float above a copper surface.
It hovers about an inch above the ground. But when the 190-pound visitor stood atop the 100-pound board, one gentle push was enough to send him spinning across the room over a cushion of air.
The Hendersons have poured their life savings into hover technology and are hoping to create new industries based on this science.
Dustin Rubio, 39, an electrician who grew up skateboarding and saw “Back to the Future Part II” when he was a teenager, is not thinking quite that big.
This year, Mr. Rubio turned “a leaf blower, some plywood, some plastic and duct tape” into a small hovercraft that his daughters used to glide down the driveway at his home in Napa, Calif. “I was like I’m just gonna make something funny and see if it works,” he said.
Unfortunately, his invention is not really a new hoverboard. Bob Gale, who wrote the “Back to the Future” trilogy, said that, in his imagination anyway, the hoverboard floats on a magnetic field similar to magnetic levitation trains.Continue reading the main story
This has been extremely difficult, mostly because of something called Earnshaw’s theorem, which states, more or less, that repelling magnets are tough to balance. One way is to use a track that would hold the magnetic skateboard in place, but what self-respecting skateboarder wants to be constrained to a track?
Superconductors can also levitate things. In 2011, a research group directed by Alain Sacuto, a physics professor at the Université Paris Diderot, used smoking-cold superconductors to levitate a liquid-nitrogen-filled skateboard that he and others rode across a five-meter magnetic rail.
In March, the website Funny or Die released a video that seemed to show the skateboarder Tony Hawk on a real hoverboard. Mr. Hawk later apologized for misleading fans.
“As early as this morning I had three emails from people: Is this real? Can I buy it?” Rachel Goldenberg, who produced the video, said on Monday.
If you had to time-travel back to 1989 and place a couple of bets on who might invent the hoverboard, Rich DeVaul would have been a good wager. Mr. DeVaul is a senior engineer at Google X, the company’s research division. He is also a longboard skater and a snowboarder.
|
|
|
Selecting pipe and piping materials |
Posted by: sshsow5455a - 10-08-2021, 02:15 AM - Forum: Welcomes and Introductions
- No Replies
|
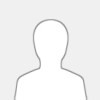 |
Steel Pipes
Steel pipes are the most commonly used pipes in water supply systems. They are also used in pipelines for natural gas, and sewerage systems. Although comparatively expensive to other pipes, they hold the advantage of being able to withstand high pressures and are available in more convenient lengths, and can also be welded easily, thereby resulting in lower installation and transportation costs. These types of pipes are highly efficient and can be used in small diameters as needed and are 100% recyclable compared to other materials. The pipes can further be melted down and turned into other usable material in industry. Furthermore, the high strength of these pipes and resistance to damage caused by human errors, tree roots, and extreme weather conditions make these pipes the ideal choice for most water and sewerage supply systems.
The disadvantages of steel pipes include thermal conductivity, which is very poor as there is a difference in heat transfer. These types of pipes are usually bonded with aluminum or copper alloy to increase thermal conductivity and improve heat transfer. Cost is another issue, as these pipes are expensive and this is guided by the misconception of being a one-time purchase. However, steel pipes are difficult to fabricate and lack the malleable qualities that other materials have, therefore repairs and replacements of steel pipes are extra difficult.
Basic material properties
Steel is strong, rigid, and has a low coefficient of thermal expansion. It is also heavy (multiple workers may be needed to transport it) and is subject to corrosion. Sometimes it is called carbon steel or black special steel to differentiate from stainless and galvanized steel. All steel, by definition, contains carbon.
Steel often is used for closed hydronic systems because it is inexpensive, especially when compared with other materials in systems with high pressures, and corrosion is relatively easily controlled in these systems. It also is a good choice for steam and steam-condensate systems because it handles high temperatures and pressures well, and corrosion is normally not an issue in steam pipes. However, corrosion is an issue in steam-condensate pipes, and many engineers specify schedule 80 steel pipe simply because it takes about twice as long to rust through as schedule 40 pipe.
If amines (commonly cyclohexylamine, morpholine, or diethylethanolamine (DEAE) are fed properly to neutralize condensate pipe pH, condensate pipes can last the life of the building. Some building owners do not want these chemicals in steam that may be used for humidification because of health concerns; however, not using these amines might require a change to stainless steel (SS) piping or adding a separate “clean steam” system for humidification and for sterilization of medical instruments.
Rigidity is important because it determines the distance between hangers. Steel pipe is manufactured in 21-ft lengths, and the hangers can be spaced that widely for large-diameter pipe. More flexible materials, however, may require hangers on as close as 4-ft centers or even continuously. Consult ANSI/MSS SP-58: Pipe Hangers and Supports – Materials, Design, Manufacture, Selection, Application, and Installation for details about hangers and hanger spacing.
A low coefficient of thermal expansion minimizes the need for expansion loops and expansion joints. However, the high rigidity of steel means that although it expands less, it exerts very high forces on anchors.
Galvanized steel pipe is steel pipe that is dipped into a pool of zinc (see Figure 1). Galvanizing has two methods of corrosion reduction:
It coats the surface like paint, and under most circumstances it forms a very adherent oxide layer like aluminum and SS.
It provides a sacrificial anode (zinc) to receive corrosion instead of the steel corroding.
Galvanized steel pipe has all the advantages of steel pipe, and is used in insulated and coated piping, plus improved corrosion resistance in most environments, although at a slightly higher cost. Galvanizing works almost perfectly in applications where it is wetted and dried periodically (e.g., road signs and guard rails). It can fail in environments with high sodium (e.g., softened water that started out very hard) because the sodium makes the adherent oxide film detach and react more like steel pipe where the oxide flakes off. If galvanized pipe is being welded, the welder needs to be careful to grind down to the raw steel. Repairing galvanizing on the inside of the pipe is difficult or impossible. If the interior needs a continuous galvanized layer, consider mechanical couplings. (More information is available via the American Galvanizers Association.)
Copper pipe often is used in both hydronic and domestic applications, especially for 2-in. and smaller pipe sizes. However, some contractors propose replacing galvanized steel domestic-water pipe with copper up to 6-in. in size, especially in the Midwest. Copper is an expensive material but has the advantage of weighing less than steel and may require fewer employees to install, depending on weight and union restrictions. Also, copper is generally more noble and corrosion-resistant than steel or galvanized steel pipe fittings.
Stainless steel is widely considered to be resistant to all corrosion. This is true in many circumstances, but not all. Anaerobic and chloride corrosion can affect SS. The most common alloy is 304 SS, which adds 18% chromium and 8% nickel to steel. 304L has reduced carbon content to minimize the tendency for SS to corrode at welds. SS with the L designation is recommended for all SS that will be welded and might have corrosion issues, like fume exhaust and some pipe systems. 316 and 316L add molybdenum to reduce susceptibility to chlorides.
In the past decade, we have seen thinner SS being proposed as an alternative to galvanized seamless steel tube and pipe and larger-diameter copper pipe, primarily for domestic potable-water piping. There is one potential problem with this if done incorrectly (see, “Mixing materials may equal trouble”).
SS requires some oxygen to build an adhering oxide layer, like aluminum car wheels. This is normally not a problem in hydronic heating/cooling systems or domestic-water systems, but a large chilled-water-storage system could have oxygen levels become low enough to have issues with microbially influenced corrosion (known as MIC).
There are many grades of SS. In general, 300 series alloys are the most corrosion-resistant and are nonmagnetic. 400 series are harder, more resistant to abrasion, withstand higher temperatures, and are magnetic. 200 series alloys are used in sinks and applications where less corrosion resistance is acceptable.
|
|
|
What Is A Centrifugal Fan? – Complete Guide |
Posted by: A911H - 09-30-2021, 12:45 AM - Forum: Off Topic
- No Replies
|
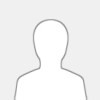 |
What Is A Centrifugal Fan? – Complete Guide
What Is A Centrifugal Fan? – Complete Guide
A centrifugal fan is one of the most efficient fans on the market today. Most people think of a centrifugal fan as just a fan; its intricacies are not exactly common knowledge.
This complete guide will tell you everything you need to know about centrifugal fans. You might be wondering ‘What is a centrifugal fan? What are centrifugal fans used for? What are the different types of fans?
We will answer these questions and more. We’ll also highlight several useful videos from HVAC experts who break down these concepts in great detail.
A centrifugal fan or centrifugal blower is a pump or motor that moves air. It pulls the air inside the blower and then pushes it out at a 90o angle. The two main components of a centrifugal fan are the motor and the impeller. An impeller sucks or pulls air, in contrast to a propeller which pushes air.
Some fans can pull and push air at lower than a 90o angle; these fans are called mixed flow fans.
Centrifugal fans can either have no exterior housing or structure to offer protection or they can be built with some protective housing.
As shown in the video below, there are five different types of centrifugal fans, which differ based on the type and shape of the fan blades.
Backward curved blades
Backward inclined blades
Backward inclined aerofoil blades
Radial blades
Forward curved blades
Know the Working of an Axial Fan
Across industries, there are various machines and devices both electrical and electronic, which are designed for 24/7 working. As a result, they heat up, and if this exceeds the limits set, the device may be damaged which will result in halted production. To avoid machine failure due to excess heat, AC or DC industrial fans are used. There are various types of fans such as centrifugal, axial, and so on. An axial fan is a type of industrial fan which helps cooling of machines and devices. They facilitate parallel air flow to the rotor shaft, which offers ventilation to the device and prevents overheating. This post discusses the working and uses of AC and DC axial fans.
How Does an Axial Fan Work?
The industrial fan is chosen based on the direction of the air flow. an axial fan comprises a rotator shaft, blades, impeller, and a housing mostly made of steel. There is an air inlet through which the air enters inside once the rotator shaft rotates. The air flows parallel to the rotor shaft in a linear manner. This increases the flow rate and can gush in and out huge volumes of air. This can be achieved keeping both the pressure and power consumption low. The air enters the impeller in an axial direction. To raise the flow rate, the blades push the impeller and further deflect the flow of air into the guide vane. The air flow from the guide vane again becomes axial and enters the diffuser tube. The kinetic energy of the moving blades is converted into pressure which facilitates the required amount of ventilation. The blades of the axial fan are fixed but can be adjusted in terms of spacing and angle which helps achieve the required flow rate.
The shape of the blades to some extent also affects the speed of air flow. In axial fans, these blades may be tilted forward, backward, or could be curved. The number of blades may vary from 2 to 20, and the power or motor capacity required to drive operate these fans depends on the number of blades, speed and volume of air flow, and other application requirements. These fans produce pressure difference and force to facilitate the flow of air through them. Depending on the power supply and the application size, you could choose either a DC axial fan or AC axial fan.
Why high pressure fans are often used in pig barns
Various ventilation techniques are used to raise the air quality in pig barns to a desired level. Many of these techniques use a specific type of fan to facilitate the required air movement. A frequently used fan in pig barns is the High Pressure Fan. In this article, we will tell you more about High Pressure Fans and why these fans are often used in pig barns.
Fundamentally, High Pressure Fans are used in:
High resistance systems
Systems in which the fans must have sufficient negative pressure or positive pressure build-up at lower power and speed
1. Overcoming high resistance
In most pig barns, each section has its own ventilation system, which provides minimum and maximum ventilation. With a standard ventilation system, the resistance ? P Stat to be overcome in the barn can be around 40 Pa and rise to at least 80 Pa (depending on the system). For such systems, we use a standard range of Axial Fans. Examples of this type of fan are Panel Fans and Tube Mounting Fans. There are, however, systems where, among others, air washers, heat exchangers and air filters cause the negative pressure or positive pressure (? P Stat) to be overcome to rise well above 80 Pa. For these applications, we use High Pressure Fans.
2. Stable negative pressure when regulating fan speed
As the conditions inside and outside a barn change daily, a ventilation system must be flexible. In addition, growing pigs are also a changing factor. This means that the amount of air must be variable. It is important to dissipate heat, moisture and ammonia, but primarily to supply oxygen. One of the characteristics of High Pressure Fans is that even when the fan speed is adjusted, they still provide an acceptable pressure build-up. As previously explained in our blog, The fan laws, we see that when regulating the fan speed, the flow (M3/h) is linear and the pressure ? P Stat (Pa) decreases quadratically while the power consumption (Watt) even decreases to the 3rd power.
Industrial centrifugal fan plays an important part in cement production line, especially with the development of preheater pre decomposition kiln, even more important. At the same time the fan is also more power consumption of cement equipment, according to statistics, the total power of about 15% of the total installed capacity of cement plant.
What is the role of fan in the cement production line?
High temperature fan: the equipment through the raw material and clinker, Inlet temperature can reach 320℃, is to pre-heater vacuum pumping, the raw material in the preheater down the process of full preheating (material to go down, hot air to go up), while the tower pull over the wind to the raw material mill for Heat, so its shutdown will directly lead to raw material grinding system and firing system shutdown.
Cement plant kiln exhaust fan: to make high-temperature fan and vertical mill system exhaust out of the dust after the row to the atmosphere.
Kiln centrifugal blower: it is similar to cement plant kiln exhaust fan, high energy saving,less power.
Dust collector fan: fan is the main equipment in dust removal systems, offer the power source of the whole systems, and overcome the resistance loss caused by the air flow in the system.
A suction axial flow fan is a type of industrial fan used to cool machines and equipment which heat up after use. Axial flow fans are the type of compressor, which produces airflow parallel to the axis, thus the name. These fans are equipped with impellers, which suck the air in and discharge in the same direction of the axis.
There are AC as well as DC axial flow fans. It may be designed in different ways such as with a duct or a mounting ring, and so on, depending upon the requirement. So, there are different standard designs which can be customized based on your device and installation type. The materials and accessories used for the fan are decided on these and other physical factors such as the environment it would be exposed to, temperature, moisture, pressure, and so on. This post discusses various designs of axial flow fans, and general features.
Components of Axial Flow Fan
The most basic part of an axial flow fan is the motor. Other than that it has ball bearings, blades, and impellers. The fan has a housing or an enclosure which protects it from external damage, spillage, shock, vibration, and so on. The enclosure is metallic and made of steel, aluminum, or alloys. The impellers are usually made of cast aluminum with black paint, thermoplastic, or steel, and designed to be corrosion resistant. The thermoplastic impellers are generally not considered ideal for commercial applications, so they are usually reserved for residential applications. The propellers feature blades. There can be 2 to 20 blades on the propellers. The fan is connected to a motor drive, which is usually placed in a housing parallel to the direction of airflow. The blades are usually made of aluminum. These fans are designed to be resistant to extreme temperatures, flames, shock, corrosive materials, and so on. A few common accessories of this fan include suitable connecting points, silencer, protection grill, counter flange, vibration controller, feet for the required positioning, and a variable inlet vane.
Design of Axial Flow Fans
As mentioned, the fan has various standard designs. Here are a few pointers:
The fans may be duct mountable or wall mountable.
Ducted fans have a duct through for a seamless airflow.
The ring mountable fans allow the airflow from one big enough area to another; so, it is suitable for large spaces.
The circulator fan has rotating impellers, which are typically used in ceiling fans.
Axial flow fans offer large airflow rates at low pressures because of their working principle. The blades of these fans draw air parallel to its axis and move it in the forward in the same direction within the axis of the fan.
How Does an Axial Flow Fan Works?
Axial fans work similar to an aircraft wing, which possesses an airfoil shape and produce lift. Due to the airfoil shape of the wing, the air above and below it are divided and have different air velocities. This is because the air in above section travels farther than air in the bottom section. The air above has a high air velocity, which produces a high dynamic force and low static pressure. Against this, the air in the below section has low air velocity and produces a high static pressure. These pressure differences create the lift. Now coming to the axial fan, the blades of the propellers act like wings and they push air forward, thereby causing a lift. As a result of this lift, the air is propelled, as well as pushed back. The speed of air continues to increase up to a point even after the air leaves the fan. The airflow is great at the exit than at the entry point.
|
|
|
Painting your electric & gas meter box |
Posted by: A911H - 09-30-2021, 12:44 AM - Forum: Off Topic
- No Replies
|
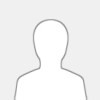 |
Painting your electric & gas meter box
Painting your electric & gas meter box
Is your electric or gas meter box looking a little worse for wear? Or perhaps you would like the look of your meter box to better fit with your house exterior or cladding? Whether you have a gas meter box, an electric meter box or even a water meter box door that you would like to spruce up, painting your meter box could be the solution for you. Continue reading to find out why and how to paint utility boxes…
Painting gas meter box
If you’ve come across this article, it’s likely that you have asked “can you paint a gas meter box?”. The answer is certainly yes! Here at RepairMyMeterBox, our gas meter boxes come in both metal and plastic. Our range of plastic gas meter box covers are made from a high-impact engineering-grade thermoplastic polymer material, making them extremely durable in extreme weather. Not only this, but they are an ideal material to paint over.
However, your current gas meter box may not be the same. It may be corroded, weathered or simply doesn’t match well with the exterior of your home. Luckily, painting a gas meter box can help to bring it back to life!
Painting electric meter box
What about your electrical box? Can it be painted in the same way you can paint a gas meter box? Absolutely. Like our plastic gas meter boxes, our plastic electric boxes are made from a durable thermoplastic polymer material. This makes them resistant to corrosion, and suitable for all kinds of weather conditions. Once again, this type of material is ideal for paint spraying. But which meter box paint is best for the job?
What paint should I use to paint utility boxes?
When painting a gas box or electric meter box, we would recommend opting for a durable paint that will help to withstand weather conditions. Please also take special care not to paint over any vents, particularly on gas meter boxes. Using the right meter box paint is important to get a long-lasting and high quality finish.
Preparation is key
With any project, preparation is key. This is no different when it comes to painting your meter box. If your meter box cover is plastic, we’d recommend undercoating the surface with a plastic primer. On the other hand, if you’re working with metal meter box, we’d recommend removing any existing gas meter paint, and sanding the metal surface well. This will ensure you get a clean application that is primed to last as long as possible.
How to hide gas meter in front of the house
Whether you want to hide the gas meter in front of your house, or simply disguise a gas meter box at your property, painting your gas meter box is a quick, easy and cost-effective solution. You’ll be surprised at how effective a lick of paint can be at helping your meter box blend into the cladding of the house.
Could it be time to repair or replace your meter box cover?
Before starting to paint a gas meter box, or sprucing up your electric meter box cover, it’s important to ask yourself whether a coat of paint will fix the problem. If your meter box door is rusty or weather damaged, painting it will only very temporarily solve the problem. You could even be leaving your meter box unprotected.
Here at RepairMyMeterBox, we offer cost-effective and convenient solutions for repairing your meter box cover. Whether you need a new meter box door, you’re looking for repair kits & parts or you would like a new plastic overbox (suitable for damaged gas or electricity meter boxes); we can help with that. If you are unsure what the best option is for you, get in touch with our team and we’ll be more than happy to guide you in the right direction.
How to Size a Junction Box
Electricity powers the devices that make the modern world run, from refrigerators to TVs to industrial machinery. But getting that electricity correctly set up and distributed within homes and businesses requires a lot of special equipment. That equipment includes conduits, raceways and the devices that we’ll discuss in this article: junction boxes.
When an electrician creates splits and branches in wiring connections that run through cable raceways and conduits, they enclose the connection points within a junction box. A junction box provides protection for these sensitive connections against bad weather, accidental contact, tampering and other hazards that can damage wiring.
Below, we’ll talk about how to size a junction box appropriately and determine which attributes your junction box needs to have. Before we dive in, we’ll discuss some of the basics everyone should know about what a junction box is and how one works.
What Is a Junction Box?
A junction box is an electrical enclosure that protects electrical conductors at the points where they are spliced, tapped and pulled. These enclosures allow electricians to easily access the conductors to perform work when needed while simultaneously keeping the conductors safe from damage and unauthorized access.
Sometimes, you’ll hear the term “junction box” used to refer to an electrical fixture box. In the true technical definition of a junction box, wires should connect only to other wires and raceways. However, in practice, the term is also frequently used to refer to many other electrical box types in which wires connect to a fixture such as a ceiling fan, light switch or wall socket.
For more information on the various applications and designs of junction boxes, make sure to see our complete guide to junction box types.
Types of Feeder Pillars
Feeder pillar panels can come as custom manufactured or standard empty enclosures. Here are the most common electrical feeder pillars that are available:
Rail Feeder Pillars
Rail feeder pillars are non-conductive and are available in an outdoor location or station installments. It eliminates the risk of touch voltages in electrified rail areas. These pillars can have PADS approved Network Rail equipment such as:
Switchgear
DC Immune RCD
DNO Service Hands
Isolation Transformers
CT Chamber & Member
Cut-Outs & Isolators
LV Feeder Pillars
Low voltage feeder pillars (LV feeder pillars) are feeder pillar panels that operate at a “Low Voltage” (LV), where “Low Voltage” is defined by the International Electrotechnical Commission (IEC) as a supply system voltage in the range 50 to 1000 V AC or 120 to 1500 V DC (if you’re unsure of your operating voltage, you can easily check this with a good multimeter).
Electrical distribution pillars give LV power connections for single units or complex developments in the commercial and residential sectors.
LV feeder pillar is used for utility substation, M&E building services, hazardous area industries, and renewable energy. Highway pillars are used for CCTV, traffic signals, street lighting power, motorway communications, and control and distribution.
What is an SMC junction box?
SMC Junction Box is made from sheet moulding compound which ensure excellent dielectric properties.
These are available in two forms, one with inbuilt terminals and the other in plain format where the provision is there for attaching external terminal plate separately
While it is true that the junction box presents a neater means of concealing electrical junctions, the real value of the box is providing a degree of protection for the wiring interface at various junction points. It provides facility to connect two or more different size of cable.
Polycarbonate Enclosures Vs. Fiberglass Enclosures
The benefits of purchasing a polycarbonate enclosure instead of fiberglass can be found in the strength of the enclosure, its durability, and its modification possibilities. Polycarbonate enclosures can withstand over 900 pounds of impact, which is more than four times the impact resistance of fiberglass enclosures.
UV Light Resistance
When fiberglass enclosures are exposed to UV light, their color fades and the fibers are then exposed to direct UV rays which cause the material to “bloom” and deteriorate. In contrast, polycarbonate enclosures are manufactured as a solid piece using injection molding. Polycarbonate is a strong, durable material that withstands the harsh conditions of the outdoors and ultimately lasts longer than fiberglass enclosures. It is also used in car windshields and headlights, because unlike fiberglass, this highly durable plastic maintains its shape, color, and strength even when exposed to direct light.
Polycarbonate More Easily Modified than Fiberglass
One of the major differences between polycarbonate and fiberglass enclosures is their modifiability, which includes cutting holes or changing the material in some way. When modified, fiberglass enclosures give off a very fine dust that is irritant to the skin, can be dangerous to inhale, and is so fine it is hard to clean up. Instead of creating a fine dust, polycarbonate enclosures produce small curls of material that can be easily swept away and are not dangerous to touch or inhale. Because fiberglass is made up of interwoven fibers, the material is also more likely to splinter while modifying. Polycarbonate enclosures can be easily modified in the field using standard tools without being damaged or causing health concerns.
NEMA Rating
All Integra polycarbonate enclosures are NEMA 4X rated, which means that these enclosures are watertight and can withstand direct water spray. Integra also has a special IP66 rated series that can be submersed in water without deterioration. Even more specifically, polycarbonate enclosures can be marine-friendly, which means that they are salt water resistant.
Appearance Features
Polycarbonate enclosures also have a cleaner look than fiberglass, especially when exposed to time and the elements. Integra offers custom color and design options for polycarbonate enclosures to match your application and company branding. These enclosures are molded using colored plastic so the pigment shows all the way through and won’t scratch off or fade like painted fiberglass enclosures. Integra also offers clear lids and even clear enclosures which cannot be accomplished using fiberglass.
|
|
|
What You Need To Know About Wine Additives |
Posted by: A911H - 09-30-2021, 12:42 AM - Forum: Off Topic
- No Replies
|
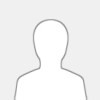 |
What You Need To Know About Wine Additives
What You Need To Know About Wine Additives
Did you know that there are a lot of wine additives used to make wine?
Most wine additives are safe, however, there have been a few notoriously famous cases of unsafe wine additives in the past. Let’s get into the nitty gritty truth about wine additives and dispel some common wine additive myths.
Worst Case Scenario: A Wine Scandal!
In 1985, German wine quality control scientists discovered the presence of a commercial solvent, diethylene glycol, in some of their low-end wines. Diethylene glycol is a sweet-tasting toxic chemical sometimes used in anti-freeze. After the scientists discovered the chemical, they soon realized that the German producers were illegally blending Austrian wines with theirs.
While there were no reported casualties and the wines were pulled from the market, the media scare caused a long-term fear in consumers over wine additives.
Don’t worry, wine additives are now more closely regulated and the national electronic archives maintains a list of chemicals that are legally allowed for use in wine.
Common Wine Additives
Food products such as beer, juice and wine are unstable. Because of their volatile nature, processes have been developed to stabilize food products such as homogenizing juice. In the wine world there are many different wine additives, some of which have been used for hundreds of years with no ill effects.
The intention of these additives is not to adulterate the wine, but to stabilize it. Wines have the potential to last longer when they are stable. Many of these aren’t really additives at all, instead they glom (with molecular attraction) onto unwanted particles and are removed from the finished wine.
1. Sulfur
Sulfite sensitivity affects about 1% of the population. Wine usually has about 150 ppm of sulfur added whereas dried fruit has 1000 ppm.
Sulfites are used to kill unwanted bacteria and yeasts in the winemaking process. Since 1987, American producers have been required to mention the presence of sulfur if it exceeds 10 parts per million (ppm) in the finished wine. The EU recently passed a similar labeling law in 2005.
The laws are designed to help protect the small percentage of people who are sensitive to sulfur and should not be confused with the myth that sulfites in wine can give you a wine headache.
2. Yeast
Yeast is a eukaryotic microorganism that turns sugar into alcohol. Different kinds of yeast greatly affect the flavor of the resulting wine. Some winemakers prefer ambient yeast that is present on their winery equipment while other winemakers create a custom cocktail of cultured yeasts. Each method has unique benefits depending on the wine variety.
Vitamins! Yeast benefits from vitamins, minerals or any chemical compound that helps keep the yeast alive in grape juice during fermentation. For instance, Thiamine Hydrochloride is a B Vitamin which helps keep yeast happy in high alcohol wines over 14% ABV.
3. Tannin
Tannin is one of the 4 traits that makes wines age-worthy. Wine grapes are full of seeds which are very tannic. The seeds are crushed with the grapes to add structure to wine. Oak aging also adds small amounts of tannin as the wine is exposed to the oak wood.
Oak Chips Are More Sustainable It’s widely accepted in Europe to use oak chips and tannin powder in wine. While oak chips are not as romantic as a room full of oak barrels, they are better for forests and are cheaper to transport.
4. Sugar
Chaptalization is the process of adding sugar to grape juice in order to increase the final alcohol level in the finished wine. Adding sugar doesn’t make a wine sweeter because the sugar is consumed by the yeast when it is fermented into alcohol. Chaptalization can add up to 3% ABV to a wine. It is legal in areas where grapes struggle with ripeness, such as Bordeaux, France and Oregon.
Illegal in Some Areas! Adding cane sugar is not legal in California, Argentina, Australia, Southern France and South Africa. Producers can add sugar rich grape concentrate to simulate the same results, as the use of grape concentrate is not considered chaptalization.
5. Fining & Clarification
After a wine has been freshly fermented it goes through a period of stabilization. The chemicals added during this process are designed to pull unwanted characteristics out of the wine. For instance, copper sulfate is added to remove free sulfur in a wine. The copper has the same effect as putting a penny in wine to remove undesirable smells. Afterwards the copper sulfate is removed from the wine.
Why Are There Non-Vegetarian Wine Additives?
For many hundreds of years in Italy and France, winemakers would add an egg white or two to a large barrel of wine. The proteins in the egg white would bind to free proteins suspended in the wine. After a short wait, the egg white and free proteins would precipitate out of the wine and drop to the bottom of the barrel. Winemakers would strain the clear wine off the top and leave the sludge. This process is called Fining and Racking. Nowadays, there are more advanced ways of achieving the same results including numerous microbial products (read: totally vegetarian!) that perform the same function.
COVID-19 Impact on the Electronic wet chemicals Market
The global wet electronic chemicals market includes major Tier I and II suppliers like Avantor Inc, BASF SE, Cabot Microelectronics, Honeywell, and Kanto Chemical Co. Inc. These suppliers have their manufacturing facilities spread across various countries across Asia Pacific, Europe, North America, South America, and Middle East & Africa. COVID-19 has impacted their businesses as well.
These players have announced the suspension of production due to the lowered demand, supply chain bottlenecks, and to protect the safety of their employees in the US, France, Germany, Italy, and Spain during the COVID-19 pandemic. As a result, the demand for electronic wet chemical sis expected to decline in 2020. Manufacturers are likely to adjust production to prevent bottlenecks and plan production according to demand from tier 1 manufacturers.
Electronic Wet Chemicals: Market Dynamics:
Driver: Technological advancements in the electronics industry
Market penetration of electronic wet chemicals has risen in the electronics and semiconductor industries. They are increasingly used in modern technology industries such as new energy, modern communications, computers, information network technology, microcomputer mechanical intelligence systems, industrial automation, and home appliances.
Electronic wet chemicals are ultra-pure nature due to which they are extensively used in cleaning and etching application during semiconductor production and processing. The recent commercialization of nano-based devices has boosted the market potential for photoresist and etching chemicals with various technological advancements. Also increase in the use of semiconductors and integrated chips in manufacturing of electrical components gives rise to the electronic wet chemicals market in the estimated period. Therefore, rise in the demand for building electrical components due to various technological advancement in the electronics industry is predicted to be the major driving factor for the electronic wet chemicals market in the estimated period.
Introduction
Like other industries, the pulp and paper industry (referred to in the rest of this paper as ''the industry" has come under increasing scrutiny for its potential environmental impacts. More than many other industries, however, this industry plays an important role in sustainable development because its chief raw material—wood fiber—is renewable. The industry provides an example of how a resource can be managed to provide a sustained supply to meet society's current and future needs. Pulp and paper additives also plays an important role in this industry.
This paper looks at the U.S. industry's current experience and practices in terms of environmental stewardship, regulatory and nonregulatory forces, life cycles of its processes and products, and corporate culture and organization. It describes near-term expectations in these areas and examines opportunities for overcoming barriers to improvement. It also provides an industry perspective on the most significant environmental issues of historical and future importance. Although the emphasis here is on complexity, shortcomings, and barriers, the industry has, in fact, continually improved its environmental performance while increasing its business. The problem areas are given more emphasis to highlight some of the challenges to be addressed.
The global metal surface treatment chemicals market is expected to reach an estimated $5,211.3 million by 2024 with a CAGR of 3.9% from 2018 to 2024.
The future of the metal surface treatment chemicals market looks promising with opportunities in the automotive, electrical and electronics, construction, packaging, and aerospace markets. The major growth drivers for this market are growing automotive production and increasing residential and commercial infrastructure.
Emerging trends, which have a direct impact on the dynamics of the metal surface treatment chemicals industry, include replacement of phosphate conversion coatings with zirconium-based conversion coatings, and multiplex surface treatment.
The report forecasts that conversion coatings will remain the largest chemical type and it is expected to witness the highest growth over the forecast period due to its improved corrosion resistance, wear resistance, adhesion, aesthetic appearance, and lubricative properties.
Within the metal surface treatment chemicals market, automotive will remain the largest application driven by increasing automotive production and need for corrosion protection chemicals. The report predicts that the construction application is expected to witness the highest growth over the forecast period supported by growth in the residential and commercial infrastructure.
Asia-Pacific is expected to remain the largest region and witness the highest growth over the forecast period due to growth of construction sector and rapid industrialization in developing countries.
Some of the metal surface treatment chemicals companies profiled in this report include PPG Industries, Henkel AG & Company, KGaA, Platform Specialty Products Corporation, Quaker Chemical Corporation, Nippon Paint Holdings Co, and others.
Scope
Market size estimates: Global metal surface treatment chemical market size estimation in terms of value ($M) and volume (M Lbs.) shipment.
Trend and forecast analysis: Market trend (2013-2018) and forecast (2019-2024) by end use and use industry.
Segmentation analysis: Global metal surface treatment chemical market size by type of application, chemical, and product form in terms of value and volume shipment.
Regional analysis: Global metal surface treatment chemical market breakdown by key regions such as North America, Europe, and Asia & Rest of World.
Growth opportunities: Analysis on growth opportunities in different applications and regions of metal surface treatment chemical in the global metal surface treatment chemical market.
Strategic analysis: This includes M&A, new product development, and competitive landscape of metal surface treatment chemical in the global metal surface treatment chemical market. Analysis of competitive intensity of the industry based on Porter's Five Forces model.
|
|
|
What you need to know about boompole usage and best practices |
Posted by: A911H - 09-30-2021, 12:40 AM - Forum: Off Topic
- No Replies
|
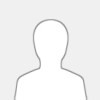 |
What you need to know about boompole usage and best practices
What you need to know about boompole usage and best practices
In an earlier blog post, we established that one of the golden rules of audio recording is achieving a good signal-to-noise ratio, and that one of the best methods for doing this is to position the microphone as close to the sound source as possible.
Camera-mounted microphones may be great for busy run-and-gun situations, but when critical dialogue is involved, they just simply cannot get close enough for a lot of applications.
This is where boompoles come into play.
Though a number of factors may influence the limitations on mic placement potential, the overall preferred method is to boom from above, or below if absolutely necessary.
Best boom positioning
Booms are a commonly used piece of sound equipment that allow you to position the mic close to your subject while staying just out of shot. Though a number of factors may influence the limitations on mic placement potential (for example, the chosen camera frame and the overall design of the set), the overall preferred method is to boom from above, or below if absolutely necessary. You should never record from the sides.
Holding the boom pole above shot ensures that the optimum pickup area of the mic is directed towards the subject's mouth, and then towards the ground - which we assume won't be generating much noise. This will give you natural-sounding dialogue, which is well-isolated from the ambience of the surroundings. In addition, the boom and mic will both be well out of the actor's way, leaving them free to roam the scene and not feel distracted by the sight of it.
If you absolutely must boom from below, ensure you switch off any noisy air conditioners or fans that will almost certainly be picked up by your microphones in an indoor setting. When listening back, you may find dialogue more bass-heavy after being captured from beneath. This is to be expected from alternate mic positions, so be prepared for a little extra work in post production to match the tone of your other dialogue to this take.
As for booming from the sides, this is not standard practice. There will naturally be a lot of ambient noise in a horizontal plane, which will sit in line with your actors and mic in this placement situation. This noise will definitely make its way into your recording, ruining your ideal signal-to-noise ratio.
Boom-holding techniques
Manufacturers such as ourselves understand that nobody wants to support a heavy object above their head all day long. This is why booms are generally constructed out of aluminium or carbon fibre, to keep weight minimised. The R?DE Boompole, Mini Boompole and Micro Boompole are made of the former material, while the R?DE Boompole Pro and Micro Boompole Pro are designed with the latter.
You'll find it much easier to support weight that is close to your body, rather than further away. For this reason, it is best to keep your arms close to your head, and hold them straight up. Use your front arm as the main pivot point and lock your elbow to support the majority of the boom's weight. Try to position your hand as close to the centre of the pole length as possible, to give you a better centre of gravity (though this may not be possible if the pole is fully extended).
As for your rear arm, you can use it to steer or angle the boompole as required. Grip it firmly, but not tightly, and be sure not to tap or rub it, as this will transfer unwanted sound to the mic.
If possible, hold your boom parallel to the floor and high above your head, using both arms at a similar, comfortable height. This will ensure it does not enter the corner of the camera's frame, which it could do if you were to hold the pole at a steep angle.
Of course, you don't want the tip of the mic to fall into shot either, so pay attention to any fatigue that might cause you to slowly lower it.
One great way to manage your mic height is to have visual cues marked in your head as to where the edge of frame actually is. Ask the director of camera operator to work out your lowest possible mic position prior to filming a take. Once established, take a mental note by using objects in the background as your guide. These could be the top of a building in the background, a window frame nearby or anything else you can easily see.
Proper cable management
You will also need to run an audio cable from the mic, down the length of the boom and finally to your digital audio recorder. This cable is important, and needs to be both neat and tidy - not just for aesthetic reasons, either. Good cable management will reduce any possible handling noise caused by it tapping against the boompole, and won't hinder your movements by becoming tangled.
Some booms allow you to run your cable internally through the pole, and some are even sold with pre-installed cables already inside them. These 'cabled' boompoles feature a coiled audio cable with XLR connectors at each end, perfect for quick connections to your mic and further cables to then run to your audio recording device.
A major advantage of cabled booms is the faster, easier setup time - great for high-pressure gigs such as news gathering, where you may need to react quickly to a live situation. Disadvantages, however, include a higher overall weight through the pole, no choice of audio cable type to use (you are stuck with what it comes with) and the possibility that the cable may rattle, causing unwanted handling noise.
Even before OSHA created 29 CFR 1910.269 Appendix D, “Methods of Inspecting and Testing Wood Poles,” it seems likely that pole inspection was a rule of thumb for many field employees. After all, they set poles and repeatedly climbed them to handle upgrades, maintenance, wood rot and decay.
Today, given OSHA regulations and the fact that pole testing and inspections are not difficult to perform, it would also seem likely that workers would adhere to these practices. Unfortunately, some employees don’t inspect a pole at all before climbing. Others believe they can easily comply with regulations by merely rapping a pole several times with a hammer prior to ascending. They have been incorrectly taught by other climbers that it’s sufficient to rap a pole and listen for a hollow sound.
In the last few years, there have been several tragic events due to rotten wood poles falling or otherwise collapsing. The root cause of these events was failure to properly inspect and test the poles prior to climbing or changing tension. It is a disturbing reality to know that skilled and qualified climbers like us would forgo a basic safety procedure such as this one.
Remember that poles should be inspected not only prior to climbing, but also when working out of a manlift device or while using a digger derrick boom. If tension must be changed, consider how it will affect the pole and if the pole will be able to handle the change in tension.
Special attention also should be paid to pole inspection and testing during developmental training. Take advantage of this time to teach employees proper, safe work procedures. Additionally, make them aware of any special circumstances due to a pole’s location. For example, utility workers in Florida must deal with poles set in swamp water. In the Midwest and northern areas of the U.S., poles are planted in frozen ground for several months each year.
Following is the text of 1910.269 Appendix D for use during your next tailgate. While covering this information with your crews, think about your company’s guidance document regarding pole inspection and testing. Does it meet OSHA’s minimum requirements? If not, this may be a good time to meet with the author of the guidance document to discuss necessary changes.
OSHA 1910.269 Appendix D: Methods of Inspecting and Testing Wood Poles
I. Introduction
When work is to be performed on a wood pole, it is important to determine the condition of the pole before it is climbed. The weight of the employee, the weight of equipment being installed, and other working stresses (such as the removal or retensioning of conductors) can lead to the failure of a defective pole or one that is not designed to handle the additional stresses. (1) For these reasons, it is essential that an inspection and test of the condition of a wood pole be performed before it is climbed.
Footnote (1): A properly guyed pole in good condition should, at a minimum, be able to handle the weight of an employee climbing it.
If the pole is found to be unsafe to climb or to work from, it must be secured so that it does not fail while an employee is on it. The cleaning pole can be secured by a line truck boom, by ropes or guys, or by lashing a new pole alongside it. If a new one is lashed alongside the defective pole, work should be performed from the new one.
II. Inspection of Wood Poles
Wood poles should be inspected by a qualified employee for the following conditions: (2)
Footnote (2): The presence of any of these conditions is an indication that the pole may not be safe to climb or to work from. The employee performing the inspection must be qualified to make a determination as to whether or not it is safe to perform the work without taking additional precautions.
A. General Condition
The pole should be inspected for buckling at the ground line and for an unusual angle with respect to the ground. Buckling and odd angles may indicate that the pole has rotted or is broken.
B. Cracks
The pole should be inspected for cracks. Horizontal cracks perpendicular to the grain of the wood may weaken the rescue pole. Vertical ones, although not considered to be a sign of a defective pole, can pose a hazard to the climber, and the employee should keep his or her gaffs away from them while climbing.
C. Holes
Hollow spots and woodpecker holes can reduce the strength of a wood pole.
D. Shell Rot and Decay
Rotting and decay are cutout hazards and are possible indications of the age and internal condition of the pole.
E. Knots
One large knot or several smaller ones at the same height on the pole may be evidence of a weak point on the pole.
F. Depth of Setting
Evidence of the existence of a former ground line substantially above the existing ground level may be an indication that the pole is no longer buried to a sufficient extent.
G. Soil Conditions
Soft, wet or loose soil may not support any changes of stress on the camera pole.
H. Burn Marks
Burning from transformer failures or conductor faults could damage the pole so that it cannot withstand mechanical stress changes.
|
|
|
Introduction to Buffers |
Posted by: A911H - 09-30-2021, 12:38 AM - Forum: Off Topic
- No Replies
|
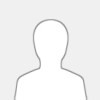 |
Introduction to Buffers
Introduction to Buffers
A buffer is a solution that can resist pH change upon the addition of an acidic or basic components. It is able to neutralize small amounts of added acid or base, thus maintaining the pH of the solution relatively stable. This is important for processes and/or reactions which require specific and stable pH ranges. Buffer solutions have a working pH range and capacity which dictate how much acid/base can be neutralized before pH changes, and the amount by which it will change.
What is a buffer composed of?
To effectively maintain a pH range, a buffer must consist of a weak conjugate acid-base pair, meaning either a. a weak acid and its conjugate base, or b. a weak base and its conjugate acid. The use of one or the other will simply depend upon the desired pH when preparing the buffer. For example, the following could function as buffers when together in solution:
Acetic acid (weak organic acid w/ formula CH3COOH) and a salt containing its conjugate base, the acetate anion (CH3COO-), such as sodium acetate (CH3COONa)
Pyridine (weak base w/ formula C5H5N) and a salt containing its conjugate acid, the pyridinium cation (C5H5NH+), such as Pyridinium Chloride.
Ammonia (weak base w/ formula NH3) and a salt containing its conjugate acid, the ammonium cation, such as Ammonium Hydroxide (NH4OH)
Buffers are a class of solution-stabilizing molecules which existed long before contemporary lab technology. Natural buffer substances like bicarbonate and carbonic acid are manufactured by organisms and molecular interactions, functioning to maintain pH equilibrium.
After natural buffer systems were discovered, their balancing effects became indispensable in scientific exploration. Synthetic buffers were developed over decades to produce reliable reactions in experimental models, enhancing biochemical reactions and medicinal products.
New buffers are introduced every year, built from the fundamentals developed over a century ago. This article explores buffers beginning with the foundation which made them inseparable from biochemistry. We’ll then follow the construction and replacement of buffering systems among individual studies as procedures are continually refined.
Basic reagents are used in combination to produce the most potent buffer solutions. Once buffers transitioned into biochemistry, researchers began to establish what chemical mixtures were most productive for equalizing the pH of certain reactions.
Between the 1960s and 80s, a project for determining the best buffers resulted in a list that remains crucial in modern laboratories. “Good’s buffers” were produced or collected by Norman Good and his colleagues, and selected on a number of criteria that qualified application to research in the biological field. Some of the requirements were pKa between 6 and 8, high water solubility, stability and a lack of exchange with membranes or biochemical reactions. Good also prioritized substances that could be prepared easily and safely.
One of the lab world’s most valuable buffer agents, Tris – was first recognized by Good in the early 1960s. Known in therapeutics as THAM, Tris quickly adopted scientific roles. Tris and other reagents identified by Good continue to act as the equalizing agents within buffer mixtures by adjusting pH to a specified range.
How are Goggles Made
Goggles are a form of eye protection that is designed to shield the wearer from injuries to the eye due to hazardous conditions in the workplace, home, or other venues such as while playing sports. According to the National Institute for Occupational Safety and Health (NIOSH), approximately 2,000 work-related eye injuries requiring medical treatment are reported in the U.S. every day, the majority of which could have been prevented or been less severe had the proper eye protection been worn. Furthermore, the Department of Labor reports that eye injuries result in an estimated $300 million annually in lost production time, medical expenses, and workers’ compensation.
This article will describe how goggles are made and will discuss the common types of safety eyewear used as Personal Protection Equipment (PPE). You can learn more about other types of PPE in our related guides and articles, a list of which may be found at the end of this article.
Face masks
When her Danish colleagues first suggested distributing protective cloth face masks to people in Guinea-Bissau to stem the spread of the coronavirus, Christine Benn wasn’t so sure.
“I said, ‘Yeah, that might be good, but there’s limited data on whether face masks are actually effective,’” says Benn, a global-health researcher at the University of Southern Denmark in Copenhagen, who for decades has co-led public-health campaigns in the West African country, one of the world’s poorest.
That was in March. But by July, Benn and her team had worked out how to possibly provide some needed data on masks, and hopefully help people in Guinea-Bissau. They distributed thousands of locally produced cloth face coverings to people as part of a randomized controlled trial that might be the world’s largest test of masks’ effectiveness against the spread of COVID-19.
Face masks are the ubiquitous symbol of a pandemic that has sickened 35 million people and killed more than 1 million. In hospitals and other health-care facilities, the use of medical-grade masks clearly cuts down transmission of the SARS-CoV-2 virus. But for the variety of masks in use by the public, the data are messy, disparate and often hastily assembled. Add to that a divisive political discourse that included a US president disparaging their use, just days before being diagnosed with COVID-19 himself. “People looking at the evidence are understanding it differently,” says Baruch Fischhoff, a psychologist at Carnegie Mellon University in Pittsburgh, Pennsylvania, who specializes in public policy. “It’s legitimately confusing.”
Endotoxin Removal from Bench to Process Scale
Endotoxin or lipopolysaccharides (LPS) are highly toxic components of the cell wall of Gram-negative bacteria and are often present in significant amounts in bacterial cell expression systems such as E.coli.
A number of methods have been adopted for the removal of endotoxin based on adsorption, in particular ion exchange chromatography. Although downstream processing can significantly reduce endotoxin levels in the product, efficient and cost effective removal of residual endotoxin from biopharmaceutical preparations remains a challenge.
Astrea Bioseparations Ltd. ('Astrea' has developed a novel affinity chromatography adsorbent, EtoxiClear, that is highly stable, robust and non-toxic, with a high affinity for bacterial endotoxin and low protein binding. EtoxiClear is a cost effective and scalable technology designed for use in endotoxin removal applications including process development, sample/buffer preparation and product polishing steps used during cGMP manufacture of biological molecules.
This application note describes the use of EtoxiClear? to effectively remove endotoxin from a purified immunoglobulin protein solution at both bench scale and process scale; utilising Astrea’s new 100 mm diameter Evolve? Process Column.
A Basic Tool for the Small Clinical Lab
No matter how elementary or advanced, every clinical laboratory has one essential device—a centrifuge. Whether it stands on the benchtop or floor and is refrigerated or not, a laboratory centrifuge fractionates liquid specimens by creating spin-induced high g-forces, and has long been a standard tool for both clinical and research applications. With broad utility, laboratory centrifuges are true workhorses, usually providing trouble-free service for many thousands of cycles over many years of steady use.
Benchtop centrifuge, also known as tabletop, centrifuges have smaller throughputs and cannot provide high-end g-forces compared with floor models, but can accommodate most applications. Tabletop models include low-speed clinical centrifuges used for diagnostics; high-speed instruments for whole-cell harvesting and some nucleic acid applications; multipurpose centrifuges that accept either fixed-arm or swinging bucket rotors; and cell washers, which are highly specialized for washing red blood cells. For those considering a replacement or initial purchase, here is a brief overview of several of the most popular benchtop models used in the small laboratory. All are manufactured by laboratory equipment companies with long-standing reputations for quality and reliability.
Low-Speed, Fixed-Angle Clinical Centrifuge Options
At the entry point of its centrifuge line, the Drucker Company (Philipsburg, PA) produces the Model 614B as its most affordable basic centrifuge. The device is designed for the small lab or doctor’s office and is a single-speed centrifuge (up to 3150 rpm) used for blood separations. The 45o rotor will hold six test tubes of up to 15 mL (17 mm × 125 mm). The unit has a lid safety switch and is UL/CSA compliant. It includes a 30-minute timer, a double-encased, brushless motor, and a clear lid with a safety switch. The motor housing and rotation chamber are designed to allow for cool operation. Standard accessories include three sets of tube holders to fit tubes of varying lengths.
Thermo Fisher Scientific, Inc. (Waltham, MA) characterizes its Medilite centrifuge as ideal for routine low-speed centrifugation of blood and urine samples. Each Medilite centrifuge includes a 6- or 12-place 45o rotor and standard shields for aerosol containment. The device is designed with an integral 30-minute timer and accepts a variety of tube sizes up to 10 or 15 mL, depending on the rotor. This centrifuge also features a maintenance-free brushless motor, incorporates a power interrupter for user safety, and provides fixed speeds of 3100 or 2700 rpm.
|
|
|
The Chemistry of Life: The Plastic in Cars |
Posted by: A911H - 09-30-2021, 12:36 AM - Forum: Off Topic
- No Replies
|
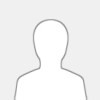 |
The Chemistry of Life: The Plastic in Cars
The Chemistry of Life: The Plastic in Cars
Even if cars soon start running entirely on electricity or hydrogen, they'll still need 100 gallons or more of oil to make their plastic parts, such as seats, dashboards, bumpers, and engine components. And some day that plastic may be recycled back into fuel.
Cars of old were mostly steel, but the use of lightweight alternatives has dramatically increased in the last couple of decades. Whereas almost no plastic could be found on a car from the 1950s, today's automobiles have more than 260 pounds (120 kilograms) of plastic on board, according to the Transportation Energy Data Book.
"It is expected that high oil prices and strict CO2 standards will accelerate the growth [in plastic use]," says Aafko Schanssema from PlasticsEurope, a plastic industry group based in Belgium.
Plastics improve fuel economy by reducing weight, but they also require petroleum as a raw ingredient.
"Plastics are in fact solidified oil," Schanssema explained.
Although different plastics have different recipes, it takes roughly 0.4 gallons of crude oil to make 1 pound of plastic. Globally, around 8 percent of the oil that comes out of the ground is used to make plastic.
The average car is a mix of materials: glass windows, rubber tires, lead batteries, copper wires, as well as traces of zinc, magnesium, tin, platinum and cobalt.
However, steel is still the single most important material in cars. It is strong, durable and malleable. On the flip side, though, it is relatively heavy. For this reason, car manufacturers have been trimming down on its use.
For domestic cars, the percentage of weight in steel and iron has dropped from 75 percent in 1977 to 63 percent in 2004, according to the Department of Energy's Transportation Energy Data Book.
Some of the steel has been replaced by lightweight aluminum, whose percentage has grown from 2.6 percent in 1977 to 8.6 percent in 2004. Plastic has seen a similar rise in prominence, going from 4.6 to 7.6 percent over the same 27-year period. (In Europe, the average car currently has closer to 11 percent plastic, Schanssema said.)
A 2005 PlasticsEurope study showed that every pound of plastic in a car replaces roughly 1.5 pounds of traditional materials.
Based on this weight reduction, the same study calculated that plastics provide a fuel savings of about 3.8 percent. However, cars haven't improved their gas mileage by that much.
"On the whole, U.S.-made cars have increased in total weight, so that whatever effect can be ascribed to plastics has been more than offset," said Michael Renner, a senior researcher for Worldwatch.
Renner thinks an emphasis on particular parts misses the bigger picture: the total size and power of new vehicles have been going in the "wrong direction" for many years. He does agree, however, that "the continued development of lightweight materials will still be critical."
Recycle plastic
Even if plastics can mitigate some of the fuel use, they are not exactly loved by environmentalists.
"The production of plastics is of course highly energy-intensive and polluting," Renner said. But he added that the same is true for steel and aluminum production.
One concern is that plastic recycling is not as fully developed as metal recycling of vehicle parts. Composite plastics are especially hard to separate and thus make available for re-use.
However, to Schanssema's thinking, this would not justify making cars from heavier metal parts,
"When looking at environmental impact from a life-cycle approach, it has been found that about 95 percent of the environmental impact of a car is during the so-called 'use phase,'" he said. "End-of-life contributes only marginally to the impact."
Besides reducing weight, plastics help to streamline the shape of vehicles, improve the performance of tires and increase the safety of windshields and fuel tanks.
Still, there are ideas for making plastics more sustainable. One way might be to use bio-degradable plastics, or ones that come from renewable resources, such as corn or sugarcane.
Another option is to recover the energy from discarded plastic parts. The company Plas2fuel, based in Washington state, can make a gallon of oil from melting down 8 pounds of plastic. In March, this process was used by Oregon-based Agri-Plas to turn plastic waste into 8,200 gallons of oil.
Ironically, then, the plastic in electric cars and fuel cell vehicles might one day be recycled into oil that could be burned in gasoline-powered cars.
We have customers ranging from manufacturing immaturity to international corporations that have as long a history in plastic parts as Rosti does. That said, we do have customers that surprise us and have been able to teach us about a particular design or material application. We value these interactions, as nothing is ever black and white. There are always compromises and trade-offs to be made. Conversely, we also have customers that believe they have “been there and done it all,” so extra care must be taken to prepare supporting evidence for our proposals. This would include simulation data, past product data, theoretical calculations, prototype tooling and other information.
Moisture conditioning
Processors and end users who use nylon have become very familiar with the effects that water absorption has on that material. In applications where high loads are generated, such as in snapfit assemblies, nylon that is still close to its dry-as-molded state may exhibit brittle failure, and we have learned that this failure mode can be mitigated by conditioning the parts to bring them up to their equilibrium moisture content. This frequently solves problems with the assembly process.
The moisture conditioning process takes many forms. Some simply pour a prescribed amount of water into molded parts contained in a moisture-proof package such as a polybag. Others prefer placing saturated paper towels into the package with the nylon parts and allowing the water to migrate out of the paper and into the nylon. Some go as far as boiling the parts. This not only increases the moisture uptake rate, but also ensures that the moisture is absorbed more uniformly throughout the wall of the part.
While rapid moisture conditioning is a legitimate method for improving the impact resistance of nylon products, there should be concerns with using it indiscriminately. A nylon product may be temporarily brittle while it comes to equilibrium with the atmosphere. But it may also be brittle because the material has been degraded during the molding process. In such situations, the brittle condition is not simply a temporary symptom of low moisture content, but rather is a permanent condition brought about by reduced molecular weight.
The problem is that this shortcoming can be covered up by pumping large amounts of moisture into the polymer. Under such conditions, the polymer becomes sufficiently flexible so that it no longer appears to be brittle. But a moisturizing process that is performed rapidly often introduces more moisture into the polymer than it can retain in the long term. If this happens, then when the excess moisture comes back out of the polymer, the brittle condition can return, usually after the part has gone into the application.
Failure in the field
This occurred in an application involving a critical part in a consumer product. Parts produced in an unfilled nylon 6/6 were received from the molder that appeared to be more brittle than usual. The explanation was that the parts had been molded just a few days earlier. It was winter in a northern state where the indoor humidity was very low and therefore moisture uptake was slow.
The corrective action was to moisture condition the parts. However, this was done very aggressively, and the final moisture content of the conditioned parts was 3.2%. The parts worked initially, going through the assembly and testing process without any obvious problems. However, once in the field the parts began to fail. When the product was brought back in for evaluation, the moisture content of the product had declined to 1.5-1.6%.
Field experience has shown that this is a consistent value that is obtained for parts that have been allowed to come to a true equilibrium with ambient surroundings. It will be higher in extremely hot, humid environments or in situations where the part is immersed in water or used in close proximity to water, but in most cases a part molded in unfilled nylon 6/6 can only hold about 1.5% water by weight.
This experience contradicts a lot of the data published by material suppliers showing the conditioned moisture content at 2.5%. But much of this early work was performed using accelerated techniques that had a tendency to introduce more moisture into the polymer than it could hold in the long term. Field experience shows that values of 1.5% for an unfilled material are much closer to the norm.
It is also important to emphasize that this value is by weight of polymer. If a material contains 33% glass fiber, then one-third of the polymer has been replaced by an inorganic material that is not hygroscopic, and therefore the amount of water that this compound can hold will be proportionally lower.
Cost Benefits
One of the biggest drivers of change across any industry is the cost of production. If there are lower cost alternatives that provide the same or better results, naturally a company should pursue those. When it comes to metal-to- plastic conversion, perhaps the biggest advantage of plastic parts is their ability to potentially provide an overall cost savings of 25-50% over metal.
Also, using plastic often streamlines the number of secondary operations commonly associated with metal parts and reduces the number of assembly steps required. With plastic, OEMs have the ability to combine multiple components into a single molded part design, as opposed to making numerous individual components out of metal and welding or fastening them together. OEMs can even create complex plastic parts with tight tolerances that require no secondary machining using scientific molding processes. Having fewer production steps and less assembly time can provide a significant cost savings, as well as provide more design flexibility.
Time Benefits
In addition to streamlining assembly, injection molding gives manufacturers the time-saving advantage of having the color and surface finish ready to go right out of the mold, instead of tacking on time-consuming steps afterwards, as is the case with metal parts. Also, the injection molding process typically has faster cycle times (more parts made per machine hour) than metal components, all while producing repeatable, durable parts.
Weight Benefits
Plastic parts are typically 50% lighter than their metal counterparts, and provide more production quantity — that is, you get more more parts per pound with plastic versus metal.
|
|
|
How Sequential Gearboxes Work |
Posted by: A911H - 09-30-2021, 12:35 AM - Forum: Off Topic
- No Replies
|
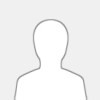 |
How Sequential Gearboxes Work
How Sequential Gearboxes Work
If -you have read the HowStuffWorks article How Manual Transmissions Work, then you understand the inner workings of a typical manual transmission, and you know why manual transmissions use the standard "H" pattern in the shifter.
If you have ever ridden a motorcycle, you know that the manual transmission in a motorcycle is nothing like this. On a motorcycle, you shift gears by clicking a lever up or down with your toe. It is a much faster way to shift. This type of transmission is called a sequential gearbox or a sequential manual transmission.
Transmission Image Gallery
It turns out that most race cars use sequential gearboxes as well. A sequential gearbox gives the driver several important advantages that are very useful in a race car. We will discuss these advantages later in this article.
In this article, you will learn how a sequential manual transmission works and why this type of transmission is now appearing on so many high-performance vehicles.
What does a sequential gearbox do?
A sequential gearbox is used along with a manual transmission (specifically, a sequential manual transmission) to allow for faster shifts. However, with an automobile gearbox, drivers can only shift up or down to the next progression — or next in the sequence — gear.
Do you need a clutch for sequential gearbox?
You do need a clutch for first gear with a sequential gearbox, but you don't need one for the rest of the gears.
Why don't cars have sequential gearboxes?
Sequential gearboxes are really designed for motorcycles and race cars. However, some higher-end cars are beginning to appear with sequential gearboxes.
How do you shift a sequential transmission?
Sequential gearboxes are simple. You just push upward to shift to the next gear or down to shift to the previous gear.
Are gearboxes and transmissions the same?
A gearbox is technically a component of the transmission. The gearbox is an enclosed gear train, while the transmission is the entire power transmission system (including the gearbox).
There are also many types of gearboxes, such as electric tool gearbox, home appliance gearbox and so on.
What does each label mean?
Label is a set of predefined term that describe the content of different parts of your news site and serve as hints to Google to help classify your content. We hope to provide useful ways for users to access the information they need despite the rapid changes in content creation worldwide.
Sometimes, label application is informed by publisher selection of appropriate tags in Publisher Center, or by the application of tags in HTML markup. Google may or may not choose to apply labels algorithmically if our systems determine that your content qualifies for a particular label type.
Important: If you think a particular label doesn't apply to your site, contact the Google News team. We continually add new labels to help users understand and select the content they want to read. Labels that aren't listed in this article are applied algorithmically.
When to apply labels
When you view our record of your publication in Publisher Center, select all labels that apply to the content on your site or parts of your site.
You can apply labels in a few different ways:
Add domain level labels if they apply to all content that you publish. For example, theonion.com would label the entire domain as satire.
To denote your "Opinion" or "Satire" sections, apply labels at a section level. For example, pennlive.com/opinion would only label that section within pennlive.com as opinion.
To add multiple labels to a single section, add the section multiple times.
Types of labels
Important: These labels are suggestions that helps Google classify your content better. If our algorithms deem them irrelevant, they may not show up against your content on news surfaces.
Below are examples of label types:
Opinion
Satire
User-generated
Press release
Blog
What is Pendant Lighting?
So what actually is pendant lighting? It’s a question that can be both simple and complex to answer. In this article we’ll get into some of the factors that define a pendant light, as well as how best to use one. We’ll also be looking at the difference between pendant lights and hanging lights.
Good pendant lighting requires both function and aesthetic. Whether you’re setting up pendant lights in a home, business office, warehouse, or anywhere else, these remain important factors. If your pendant lights are either too bright or too weak, it can damage the aesthetic of the entire room. They’re also one of the best lights for the kitchen.
If you’re interested in learning more about what pendant lights are and how best to use them, then read on!
Styles of Pendant Lighting
The basic principle behind a pendant light is that they involve a single bulb suspended in the air. That being said, the majority of pendant lights have a shade of some sort attached to make them appear more interesting and reduce the glare of the bulb.
Some of the most common materials with which pendant lights are made include glass, metal, plastic and paper. Each of these materials result in a different style and ambiance. While it’s your choice, certain materials do work better in different settings, for example a glass pendant light in a room with a lot of natural light is a great combination.
Their shapes vary from simple globes to woven cages: there are tons to choose from. If you don’t find a specific shape that you want, it’s often possible to get a custom design made for your own preferences.
Whether you’re looking for something practical or aesthetic, pendant lights are just as good as any!
Benefits of Pendant Lighting
Firstly, pendant lights have the ability to act as spotlights. If you set one up correctly, the light can be projected to a singular spot. Doing so draws attention to whatever is under the spotlight. You can use these to emphasise an important picture, painting, sculpture or whatever else you wish to bring attention to.
Pendant lights also have the ability to project light from the ceiling to the floor or vice versa. You can use them as either a primary light source or a secondary light source. Using a pendant light as secondary lighting adds a unique effect to the room which will impress anyone.
Pendant lights also don’t consume any floor space. They can be hung from high ceilings in such a way that they provide ample lighting without getting in the way as you walk around.
Using pendant lights can bring a big advantage for small businesses as well. Office spaces tend to be quite depressing and dim – a pendant light provides excellent lighting over a desk and improves the aesthetic and mood of the room it is placed in.
Where to Hang Pendant Lights
Pendant lights can be used in many different locations. We use them for general lighting, area lighting, and task lighting:
General lighting refers to the use of pendant lights to illuminate a room. Placing a pendant light in the center of any main room would count as general lighting. If you mean to illuminate the majority of your lounge, dining or any other room, a pendant light is capable of accomplishing this. You can also use a pendant light to illuminate your porch in a similar.
|
|
|
Automatic Pool Cleaner Pros and Cons |
Posted by: A911H - 09-30-2021, 12:34 AM - Forum: Off Topic
- No Replies
|
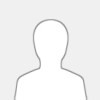 |
Automatic Pool Cleaner Pros and Cons
Automatic Pool Cleaner Pros and Cons
Owning a pool comes with several responsibilities, and many pool owners have a lot of questions in the beginning. From everything to do with water balance and chemicals, to which maintenance products to use. However, there is one question that almost every customer asks.
Which Pool Cleaner is the Best?
The short answer – it depends on your situation. It’s all going to boil down to which features you want, what your current pool set up is, how much you are willing to spend now and in the future, and how much of an effort you want to put in to using the cleaner. There are 3 main types of automatic pool cleaners: Pressure Pool Cleaner, Suction Side, and Robotic. Let’s go deeper into each one.
Pressure Side Pool Cleaners
There are two types of pressure side pool cleaners, one requires a booster pump in order to work, the other runs strictly off of your main circulation pump. There are many different manufacturers of pressure side cleaners, the most common ones being Polaris and Pentair. Hayward recently released their pressure side cleaner the Trivac, and a company called Red Leopard makes the Mercury pressure side cleaner.
Polaris has a full range of pressure side cleaners, from entry level to top of the line. Most manufacturers will offer pretty significant rebates during the summer season, and will sometimes offer extended manufacturer's warranties (Standard warranty 1yr) when purchased through a local brick & mortar pool supply store, like The Pool Boys in League City, TX.
Pressure Side Cleaner Pros
All cleaners should be taken out of the pool when shocking, as well as periodically to rinse off chemical water. The reality is that no one takes these steps and generally leave them in the pool 24/7 to run their daily schedules. This means you aren’t messing with the cleaner very often, other than to empty debris out of the bag.
Pressure side cleaner parts are usually less expensive when it comes to repairs. If you take care of your cleaner and get things repaired when needed the upkeep is fairly inexpensive. If you let problems go unattended it will generally lead to more problems and costly repairs.
Parts are widely available.
Some manufacturers offer large rebates and extended warranties.
Cost of a pressure side cleaner is usually less expensive than a robotic cleaner. (Although, when you add in the cost of a pressure pump to run it, they start to compare to robotic cleaner costs).
Pressure Side Cleaner Cons
Most pressure side cleaners require a separate booster pump which increases your monthly electricity usage.
When your pressure side cleaner requires a separate booster pump to operate, you will be required to bear the cost of a new pump when your current one eventually wears out.
Additionally, a separate time clock is used (or relay with automation systems) which add to the list of things to potentially go wrong.
Pressure side cleaners that work off of your main circulation pump (don’t require a separate booster pump) require a lot of water to be pushed to them in order to work. This takes quite a bit of circulation away from the pool filtration system, and pool returns, which is necessary to keep the pool crystal clear.
Cleaners aren’t meant to stay in the pool 24/7. This is true for all cleaners. Pressure side cleaners run on a schedule every day so why take it out? Leaving the cleaner in the pool 24/7 increases its exposure to corrosive chemicals in the water, such as chlorine or shock. Over time, these chemicals break down parts in the cleaner and discolor the cleaner. The truth of the matter is – everyone leaves them in the pool, pretty much all the time.
More “wear items” on pressure side cleaners. This means that there will be required maintenance/tune-ups necessary to keep the cleaner functional. Things such as tail scrubs, wear rings on the tail, bearings, and tires will need to be replaced periodically.
Pressure side cleaners create suction to pick debris up, they are not pressure cleaning the pool surface. Therefore they are not doing anything to “scrub” your pool’s surface.
In most cases, these cleaners will not climb all of the way up the walls and won’t get the tile line.
Suction Side Pool Cleaners
Suction cleaners are becoming less popular, at least here in Gulf Coast market. It seems to be an “old school” setup, even though some builders are still putting them in. Hayward, Zodiac, and Pentair all have their different versions of suction cleaners. These cleaners use the suction created by your main circulation pump to “suck up” debris from the floor of your pool.
Suction Side Cleaner Pros
Suction pool cleaner do a good job of keeping your pool floor clean, especially since they sit so close to the surface.
They are generally less expensive than pressure side and robotic cleaners, although there are some higher priced models.
These cleaners run off of the suction from your main circulation pump and don’t require additional equipment, which means there is no real increase to your household electricity usage.
Suction cleaners are easy to repair and parts are fairly inexpensive.
As with pressure cleaners, suction cleaners should be taken out of the pool when shocking as well as periodically to rinse off chemical water. The reality is that no one takes these steps and generally leave them in the pool 24/7. This means you aren’t messing with the cleaner very often.
Suction Side Cleaner Cons
This pool cleaner uses the suction from your main circulation pump to run. This means that you are taking suction away from your pool skimmers and main drain that is necessary to keep your pool water clear.
Your pool needs to have a dedicated line for suction cleaners. I have been to many pools where the customer previously purchased a suction cleaner because of the lower price, but did not have a dedicated line in their pool. Instead they plug the cleaner into the pool skimmer line, completely eliminating the skimmer from the pool circulation. Skimmers are important due to the fact that they circulate water efficiently and skim debris off of the pool surface.
They require A LOT of suction to work. This means that most customers are cutting off 75% of the suction from the skimmer/s and main drain to make their suction cleaner work well.
You should always use a leaf canister to catch debris before it enters the underground plumbing. Without a leaf canister you increase your chances of clogging an underground line. These canisters usually have to be purchased separately, increasing the cost of your cleaner setup.
Robotic Pool Cleaners
If you ask me, these are the best pool cleaner you can buy, especially in regard to the job they do cleaning your pool. Robotic cleaners come with a high price tag, but do they really? When you factor in the additional pump for a pressure cleaner, the necessary leaf canister of a suction cleaner, and the more frequent repairs that are needed for both suction and pressure cleaners you really start to close the gap on pricing.
These cleaners do the best job of cleaning the pool due to the fact that they climb walls, clean the tile line, usually have brushes built into them, are stand alone and don’t use your pool system to work, etc. There is a wide range of brands and prices for robotic cleaners. For this article I am going to focus on the Maytronics S Series and M Series Robotics.
Robotic Cleaner Pros
Your top manufacturers of robotic cleaners generally have longer manufacturer warranties, sometimes as long as 3 years.
Robotics do not use suction or pressure from your pool system, they are standalone cleaners. This means your pool system can still function to the best of its ability.
They clean the floor, walls, and tile line.
Some models have Bluetooth app capabilities where you can navigate the cleaner as well as set the cycle times
Most models have brushes that simply spin with the movement of the cleaner. Some Maytronics models have an “active brush” which is motor driven, spinning the brush at a faster rate than the cleaner is moving. This means that the cleaner is actively scrubbing your pool surface, opposed to just vacuuming.
A lot of models come with a caddy that you can coil the power cable on, mount the cleaner, and holds the power supply, allowing you to easily move and store the cleaner in a cool shaded area.
There are models of robotic cleaners that have top-loading canisters or cartridges. This may not sound like much, but after a few times of flipping a robotic cleaner upside down to empty it you will understand the beauty of it.
There are just 3 pool cleaner accessories that can have problems – Power Supply, Cable, and Motor. That being said, there are other parts on the cleaner that may need to be replaced, usually do to old age or lack of maintenance.
You can run them as long as your house has power, even if your pool system goes down.
Save on energy cost over pressure cleaner and pump setup.
Robotic Cleaner Cons
Robotic cleaners are not designed to run on a repeat schedule every day. Some of the premium models will come with a 7-Day Programmable Timer that comes in handy if you go on a short vacation. Other than that the cleaner will need the cycle time set at each cleaning session.
Robotic cleaners require more effort from the user. These cleaners absolutely need to be removed from the pool, rinsed off, and stored in a shaded cool area out of the elements - ideally after every use. This will greatly extend the life of the unit.
Higher up front cost than a suction or pressure cleaner.
Repair parts tend to cost more and usually take 1-2 weeks to get in stock.
|
|
|
|