Welcome, Guest |
You have to register before you can post on our site.
|
Online Users |
There are currently 278 online users. » 0 Member(s) | 276 Guest(s) Bing, Google
|
Latest Threads |
Dominica visa free countr...
Forum: Off Topic
Last Post: axied12
06-24-2025, 12:37 PM
» Replies: 0
» Views: 207
|
Advanced microneedling
Forum: Off Topic
Last Post: axied12
05-28-2025, 01:25 PM
» Replies: 0
» Views: 333
|
Caviar and cheese
Forum: Off Topic
Last Post: axied12
05-28-2025, 12:38 PM
» Replies: 0
» Views: 294
|
Top-rated countertop comp...
Forum: Off Topic
Last Post: axied12
05-04-2025, 06:42 AM
» Replies: 0
» Views: 445
|
Ryanair letenky levně do ...
Forum: Off Topic
Last Post: axied12
02-11-2025, 01:37 PM
» Replies: 0
» Views: 837
|
Trusted essay writing ser...
Forum: Off Topic
Last Post: axied12
01-30-2025, 08:16 AM
» Replies: 0
» Views: 753
|
Bootverkopers - actieve j...
Forum: Off Topic
Last Post: axied12
12-07-2024, 11:07 AM
» Replies: 0
» Views: 880
|
Services for individuals ...
Forum: Off Topic
Last Post: axied12
12-02-2024, 03:31 PM
» Replies: 0
» Views: 855
|
Used excavators
Forum: Off Topic
Last Post: axied12
11-13-2024, 09:22 AM
» Replies: 0
» Views: 801
|
Buy Higo Rocket in Dubai
Forum: Off Topic
Last Post: axied12
10-25-2024, 01:09 PM
» Replies: 0
» Views: 909
|
|
|
Absolute Bathroom Necessities |
Posted by: D133H - 10-08-2021, 08:12 AM - Forum: FPS and Shooters
- No Replies
|
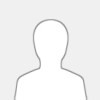 |
Absolute Bathroom Necessities
Absolute Bathroom Necessities
No matter how big or small the space is, the top items on your bathroom supplies list should include:
Mirror
Wastebasket
Natural Hand Soap
Bath towels, hand towels, washcloths (2 each)
Non-skid bath mat
Toothbrush holder
Over-the-door and/or wall hooks
Extra toilet paper
Toilet paper storage
Toilet brush & container
Plunger (tucked out of sight)
Green cleaning supplies
These are just the basic things you need in your bathroom. Depending on your budget and size of the room, there are plenty of ways to add more personality. Why not try an essential oil diffuser, softer light bulbs, or a colorful shower curtain?
Bathroom Shelves Types By Material
A common way to look at shelving types is by the material. When it comes to bathroom organizing and decor options, the color and material of your shelving does matter. Let’s take a look at some of the more popular shelf ideas by material.
1. Wood Bathroom Shelves
Furniture made from wood is prized for its durability, easy maintenance, and versatility. A wood shelf in the bathroom quickly becomes a point of visual interest because of the grain, staining, and design. Depending on the quality of wood used for a shelf, it could end up becoming an heirloom in the future.
Brown Wall Mounted Shelves By SODUKU
Create a more inviting bathroom with a modern flair when you install these attractive. floating wood shelves in a dark brown finish. The wood is treated to be both dampproof and heat resistant. The metal elements on the shelves retain an architectural design, acts as a protective guard, and includes space to hang towels underneath the wood panel.
2. Teak Bathroom Shelves
A sub-category of the former, teak is one of the most valuable woods for making exquisite furniture, and it is a sought-after material because it is resistant to dry rot. Due to the intense harvesting of teak wood, newer furniture is constructed using sustainable sources to create beautiful, sophisticated furniture.
3. Teak Bath Shelf By AquaTeak
Go with a highly reviewed company when choosing a shelf for the bathroom. Take advantage of the corners of your bathroom with this Architectural Digest featured furniture. Comprised of teak wood, this naturally water-resistant shelf is suitable for modern, contemporary, and classic bathrooms without taking up excess space.
4.Plastic Shelving For The Bathroom
Plastic furniture is valued for being inexpensive, flexible, lightweight, and resistant to breaking easily when dropped. When choosing plastic bathroom shelf for a bathroom, a plastic fixture is ideal because it is easy to clean by wiping down, but still strong enough to store towels, toiletries, and knick-knacks.
White Slim Storage Cart By SPACEKEEPER
If you are short on space but need extra storage in your bathroom, check out this slim design rolling cart. Since this shelving unit is on wheels, it’s easy to rearrange your bathroom and move it about as needed. The four high-quality plastic shelves provide ample space for bathroom accessories, towels, and soaps.
These Are the Only Kitchen Tools You Need
LIGHTS UP on an empty apartment. You (reader) are sitting on the floor in an empty kitchen, eating takeout straight from the container. Glancing around at the bare cabinets and a box of hand-me-down utensils from an unnamed parental figure, you think to yourself, somewhat discouraged: “Where do I even begin?”
A booming voice breaks through off-stage, startling you. “This is Epicurious, fear not. We have put together a guide containing the essential kitchen supplies for beginners. Let us help you through this journey.”
SCENE
Okay, maybe you’re newly independent, a recent grad, or just settling into your first apartment. Every home cook has to start somewhere. Here’s everything you need: a comprehensive list of cookware and tools to keep you well-equipped in the kitchen as you begin your cooking journey.
Nonstick 10-Inch Pan
If you really are building a kitchen from scratch, the first thing you’ll need is a nonstick pan. For a rookie cook, these pans are low-maintenance to clean and very forgiving, provided you take care of them properly (no metal utensils or scrubbers!) They are also the pan to use to cook eggs, which tend to stick to stainless steel and cast iron.
Stock/Soup Pot
A standard soup pot can often function as the one pot in a one-pot meal. You will rely on a 6-quart pot to boil pasta, make soups and stews, or, if you are feeling bold, simmer homemade chicken stock. Okay, maybe you’re not making your own stock now, but someday you will. And when that day comes, you will say, “Oh! I’m glad I have this stock pot on hand already. Thanks, food website!”
Black beauty-supply stores have long been the first stop in a multi-step haircare ritual for Black women, from wash day to crochet braids to box braids and back again. It’s here that we find aisles of products that cater to our curls and kinks; some of them are things we’ve read online rave reviews about, some we grew up with, and some we’ve never seen before. We may walk in certain about the tools we need for our next look and end up leaving with even bigger, bolder ideas often rooted in newfound appreciation for the freedom of expression our hair allows us. But while beauty-supply stores may sound like Black-girl sanctuaries, many of these shops also greet us with built-in microaggressions. For Black women, navigating beauty spaces where we are the target customer but rarely the owner is often a balancing act—a paradox of convenient, low-cost options for our specific beauty needs that exist in a physical space where we nevertheless find ourselves feeling excluded.
Depending on the city you live in, it’s common to see beauty-supply stores that are tailored to the needs of Black hair owned by non-Black people, namely Korean Americans. With a stronghold on the wig market dating back to the 1950s, Korean immigrants recognized the gold mine of Black buying power early on. Simply put, selling Black beauty supplies is good business: a market full of specialized products that are, for the most part, not widely available at more generalized health and beauty retailers. According to a report from 2017, Black shoppers spend a whopping $473 million on hair care every year—nine times more than their white counterparts. Yet they own less than 1 percent of the market share. Despite their inherent reliance on Black consumers as a means of profit, the dynamics of the beauty-supply retailer are skewed on either side of the cash-out counter. Black customers have reported being followed, profiled, and even attacked by store employees; it’s not uncommon to see signage limiting how many members of a group can come into a store at a time.
Black employees at non-Black–owned beauty-supply stores report being restricted in everything from hours to advancement opportunities to not being permitted to cash customers out. Despite being the demographic for these stores and knowledgeable about the products they sell, there are limits to what Black employees are able to do in these spaces, and some find themselves walking on eggshells. “You can help [shoppers] out as far as making suggestions for products or directing them around the store, but that is as far that went. If you helped a customer, you had to walk and hand their items over to the cashier,” reports Elysha, a former employee of a popular Toronto-based beauty-supply store. And though she’s seen a slight shift, the lack of trust still looms large: “I am noticing more Black girls behind the cash [register], but they still have a non-Black staff member hovering around them.”
Shower Head Holder
Shower head holder is amazing to hold your shower heads and make it convenient to use handheld showers. While you take a bath while playing songs on your best shower speaker or clean your foot with foot scrubber, a shower head holder can be there for you.
Now, if you have a waterfall shower head or an automatic shower cleaner, you may be thinking where to keep it safe and sound where it is easily accessible and gives a neat appearance to your bathroom.
Well, having the best toilet brush or rain shower head is not enough. You need to add accessories like Shower head holders that are pretty convenient. With your shower stool and shower mirror, you can also have a shower head holder. Now you must be thinking that there are so many of them available in the market, so which one to choose? Well, don’t worry because we have got you covered.
We have come up with a list of 7 best shower head holders that you can put up near your shower shelves. You can adjust the shower head height of these and make the most use of them. But before checking out the daily necessities product, let’s discuss some of the benefits of a shower head holder.
Advantages of the best shower head holder:
1. They give an elegant look to your bathroom
2. They are useful for kids, older people, and even adults
3. Also, they are pretty easy to install and adjust
4. They are affordable
5. They are easily accessible
6. They are highly durable
7. They can enhance the interior of your house
|
|
|
Choosing Stainless Steel Sheet |
Posted by: D133H - 10-08-2021, 08:10 AM - Forum: FPS and Shooters
- No Replies
|
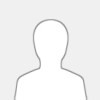 |
Choosing Stainless Steel Sheet
Choosing Stainless Steel Sheet
Stainless steels are iron-based alloys containing at least 10.5% chromium which forms a protective oxide film for corrosion resistance. This oxide film provides the stainless-ness of stainless steel. Stainless steel sheet is typically manufactured in roll or plate form depending on thickness, or gauge.
Stainless steel sheet is produced by rolling the material through a mill, creating a thinner and longer outcome. Thickness is gradually reduced through this process and the stainless steel product is wound into a coil at the end of the production line or cut into plates. Stainless steel coil can then be cold rolled in cold rolling mills. The coils can be heat treated in a furnace to further soften the material for cold rolling or to produce the mechanical properties desired.
For some stainless steel sheet products cold rolling is the last step in the process. However, other fabrications of stainless steel sheet, like stainless steel foil tape, require more processing. In this case, they undergo further elevated temperature processing in order to increase their strength.
Learn more about All Foils assortment of stainless steel foil, sheeting and tape.
Types of Stainless Steel Alloys
Choosing the right stainless steel alloy for your application is an important step. There are a variety of stainless steel alloys available, and selecting one means considering a variety details such as application, density, tensile strength, workability, acid-resistance and more. Luckily, the experts at All Foils have been helping partners determine the ideal types of metal alloys for their unique applications for decades.
All Foils maintains an inventory of stainless steel alloys in the 300-grade-range including 302, 304, 309, 316, 321 and 347. These excellent choices for sheeting and rolling have been relied upon for some of the greatest feats of modern engineering as well as every-day applications. The pinnacle of the Chrysler Building is clad with a form of 302 stainless steel. 316 stainless steel encases the Petronas Towers in Malaysia, the world’s tallest buildings from 1998-2004.
302 Stainless Steel
302 Stainless Steel is corrosion resistant, making it perfect for applications like heat exchangers, tanks, and other process equipment. In addition, this alloy is commonly used in small quantities for food and beverage, cryogenic, and pressure-containing applications.
304 Stainless Steel
This alloy is the most commonly used type of stainless steel sheet. That’s because it’s weldable, machineable and has good corrosion resistance. Some common applications of 304 stainless steel sheeting include food processing equipment, heat exchangers, springs, chemical containers, and more. Can be used in temperatures up to 1800°F.
309 Stainless Steel
309 stainless steel sheet is known for good strength, oxidation resistance, and excellent heat resistance. This alloy is commonly used in heating elements, heat exchangers, furnace parts, and more. Can be used in temperatures up to 2240°F.
316 Stainless Steel
This alloy has excellent forming and welding characteristics, and is durable. Common applications of 316 stainless steel sheet includes heat exchangers, chemical containers, food preparation equipment, and more.
321 Stainless Steel
321 stainless steel sheet is similar to 304 stainless steel, but is somewhat easier to machine. Some typical applications include chemical processing equipment, welded equipment, and more. Can be used in temperatures up to 2000°F.
347 Stainless Steel
347 stainless steel sheet maintains good corrosion resistance in applications with high temperatures. These attributes make this alloy perfect for high temperature gaskets, chemical production equipment, aircraft equipment, and more.
Stainless Steel Pipe Types
Stainless steel is a versatile material comprised of a steel alloy and a small percentage of chromium — the addition of chromium adds to the material’s corrosion resistance, a trait that earned stainless steel its name. Because stainless steel is also low-maintenance, oxidation resistant, and doesn’t affect other metals it comes in contact with, it is frequently used in a large array of applications, especially in piping and tubing manufacturing. Based on the end use of the pipe, stainless steel piping is broken down into several categories.
Different Types of Steel Tubing and Stainless Steel Piping
Pipes and tubes are sometimes difficult to classify, and tend to be distinguished based on function. In addition to these classifications, stainless steel is also distinguished by type and grade.
304 Stainless Steel Pipe
For tubing and piping applications, type 304 stainless steel is a common selection because it is highly chemical- and corrosion-resistant. However, type 304 stainless steel is not compatible with applications where temperatures fall between 800 and 1640 degrees Fahrenheit (F) because it is prone to carbide precipitation, a result of the material’s .08 percent carbon content limit. Stainless steel type 304L circumvents this problem because it has a lower carbon content limit, and therefore can be subjected to welding and higher temperature applications. Other types of stainless steel often possess additives (such as nickel or molybdenum) which strengthen traits that are desirable in particular applications.
Stainless Steel Tubing for General Corrosion-Resistance
This general category of steel is appropriate for applications that require corrosion resistance above other traits. Ferritic or martensitic types of steel (those made with the most chromium) are manufactured to be either heat-treated or annealed. Austenitic Stainless steels (those with high chromium and nickel contents) offer even more resistance, and can be used under the same general conditions as ferritic and martensitic types.
Stainless Steel Pressure Pipe
This type of stainless steel pipe is made from either solid chromium or a chromium and nickel combination. Types of stainless steel pressure pipe include seamless and welded pipe, electric fusion welded pipe for high-pressure applications, large diameter welded pipe for corrosive or high-temperature applications, and seamless and welded ferritic and austenitic stainless steel pipe.
What Is Aluminum Coil?
Unlike flat sheets, a coil is a coiled piece of aluminum material. The core is a hollow cylinder on which the coiled material is wound, thereby forming the interior diameter of the coil itself. Depending on the application, coils can be heat treated, non-heat treated, diamond coated or tread, or pre-painted.
These coils also come in a wide range of grades, such as 1100, 3003, 5052, 5083, and 8011. Because of their strength and durability, these coils can withstand significant use and abuse. A coil is also available in different thicknesses, from 0.002 to 0.276 inches, and widths range from 0.79 to 120 inches.f
Different Uses
Multiple industries rely on coils made out of aluminum for a variety of applications, including construction, electronics, automotive, pharmaceutical, food service, manufacturing, transportation, and more. Compared to other materials, aluminum is a far superior material in many instances. Aluminum is about one-third lighter than mild steel and noncorrosive. It has high thermal conductivity, and an expert can form it without much resistance.
In addition to standard stock, the best aluminum coil suppliers sometimes carry customized components. If not, they have good relationships with top manufacturing companies to get what the customer needs. The best manufacturers can slit coils, meaning they cut them to length based on what the customer needs. Not only does the customer get an exactly sized coil, this reduces the amount of waste that typically occurs.
Because aluminum is so durable and malleable, it is easily machined into sheets or coils. Although aluminum is much lighter than other metals, it provides consistent strength and unmatched value. For that reason, in coil form, it is in high demand. Before choosing just any coil, it is important to understand some of the strains that this material could face. In particular, you want to focus on weldability, wettability, tensile strength, corrosion resistance, and formability.
If you are interested in the best aluminum coil on the market, you can always count on Offshore Direct Metals. For coils, sheets, and other aluminum products, we offer our customers only the best. With product expertise, logistical experience, and an immeasurable network of supply partners from around the globe, we provide our customers with what they need but at a reduced price.
|
|
|
The Rising Popularity of Safety Helmets?on the Jobsite |
Posted by: D133H - 10-08-2021, 08:08 AM - Forum: FPS and Shooters
- No Replies
|
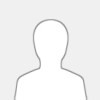 |
The Rising Popularity of Safety Helmets?on the Jobsite
The Rising Popularity of Safety Helmets?on the Jobsite
Hard hats have?come a long way since shipbuilders would cover their hats with tar to create a layer of protection from tools and objects falling from ships.?Today, the hard hat has become an iconic symbol to represent the construction industry.?Hard hats?are?typically?made?of polyethylene?and?additional?accessories such as shields, visors, hearing?protection and lights can be attached.?OSHA?requires?that?head protection must be worn whenever working in an area with potential injury to the head from falling objects.?Signs reading, “Hard Hat Required,” welcome each worker?to the?site, where every individual is wearing one, regardless of?their?trade or the task they are doing. And while hard?hats?have?typically?been?the longstanding?go-to?choice?for protection?against permanent, life-changing injuries or death,?more and more,?they?are being replaced by safety helmet. These helmets,?derived from the ones used in?extreme sports such as rock climbing or even?whitewater?rafting,?attach?more closely?on the?head?and?have?built-in chin straps.?This?‘helmet revolution’?has?some?safety managers?looking beyond the typical hard hat when?choosing?the best protective headgear to fit?their?crews’?needs while keeping them safe?on the job.
The Importance of Head Protection
Advancements in PPE can be invaluable for workers,?their?employers and?insurance companies.?With no shortage of ways to get injured on a jobsite, head protection is essential to defend against falling objects?such as?tools and debris,?fixed objects such as pipes or?electrical hazards,?and trips, slips?or falls. Yet, despite it being?a well-known fact that head protection is crucial to workplace safety,?head injuries continue to be one of the most?frequent?injuries on the job. The most common head injuries include concussions, head contusions, brain hemorrhage, hematoma and skull fractures. Remote Medical International (RMI) states most head injuries within the construction and manufacturing industry are caused by slips and falls. According to OSHA, in 2016, 38 percent of all fatalities in the workplace were caused by falls, making it the leading cause of fatalities in the workplace.
Will a Face Shield Protect You From the Coronavirus?
Face shields have been used in healthcare settings for a while now, but they’ve become a staple for medical personnel who have to intubate patients with COVID-19. Face shields are often worn during a wide variety of medical procedures. This includes surgeries or any procedure where bone fragments, blood or other bodily fluids could get into the eyes, nose and mouth.
A face shield is simply a curved plastic or Plexiglas panel attached to a headband that can be worn over the face. It should fit securely so there isn’t a gap between the band and the forehead. The shield should also extend beyond the chin.
“Because they extend down from the forehead, shields protect the eyes as well as the nose and mouth,” says pediatric infectious disease specialist Frank Esper, MD. The coverage that face shields offer is ideal since the new coronavirus can enter the body through those points. We provide many protective products.
Are face shields effective?
A 2014 study showed that when tested against an influenza-infused aerosol from a distance of 18 inches away, a face shield reduced exposure by 96% during the period immediately after a cough. The face shield also reduced the surface contamination of a respirator by 97%.“It protects you, the wearer,” Dr. Esper says. “But if you cough, because the face shield is away from your face, those droplets can still get out better than if you have a mask on.”
Are face shields good for everyday use?
CDC does not recommend wearing face shields for normal everyday activities or as a substitute for cloth face coverings. However, some people may choose to use a face shield when they know that they’ll be in sustained close contact with others. In these cases, it’s best to wear a mask underneath the face shield and maintain physical distancing when possible. This will help minimize the risk of infection since face shields have openings at the bottom.
Safety Glasses and Protective Eyewear
Eye protection means more than just wearing the contact lenses or glasses you may use for vision correction. The type of eye protection needed will depend on what you are doing, from attending public protests to playing paintball. Your regular eyeglasses do not protect your eyes from impact, debris or damage. In fact, some eye glasses can shatter if damaged, causing even more eye injury. Protective eye wear should be made from polycarbonate material because it resists shattering and can provide UV (ultraviolet light) protection.
For most repair projects and activities around the home, it's enough to wear safety glasses that meet the criteria set by the American National Standards Institute (ANSI). For many work situations, that same protection is enough, but there are important exceptions. Sports eye protection should meet the specific requirements of that sport. The sport's governing body may set and certify these requirements. The American Society for Testing and Materials (ASTM) may as well. In some cases, both organizations may be involved.
At Home: Safety Glasses, Goggles and Other Protective Eyewear
Every household should have at least one pair of ANSI-approved protective eyewear. You should wear it when doing projects or activities that could create a risk for eye injuries at home.
Choose protective eyewear with "ANSI Z87.1" marked on the lens or frame. This means the glasses, safety goggles or face shield meets the American National Standards Institute (ANSI) Z87.1 safety standard. You can buy ANSI-approved protective eyewear from most hardware stores nationwide.
You should use eye protection if the activity involves:
Hazardous chemicals or other substances that could damage your eyes upon contact
Flying debris or other small particles that could hit participants or bystanders
Projectiles or objects that could become projectiles and fly into the eyes unexpectedly
Bottom line: use common sense, especially if there are children around. You should protect them and set an example by making a smart choice.
Hearing Protection Devices and Solutions
Millions of workers are exposed to hearing hazards every year, and even though OSHA regulations and NIOSH recommendations in the U.S. specify hearing protection, occupational hearing loss is still the number one reported worker illness in manufacturing. Moreover, noise-induced hearing loss is permanent and irreversible, but avoidable with the help of proper hearing protection and other measures. Here we will explore some hearing protection devices (HPD) and other steps that can be taken to help protect workers’ hearing in a wide variety of industries.
Earplugs
When workers are exposed to loud noise, earplugs can offer low-cost, effective hearing protection. These are soft foam or elastic plugs worn inside the ear canal to help block out hazardous sounds. Earplugs come in a wide variety of shapes and sizes so there are many choices for workers. With the right fit and insertion techniques, earplugs can provide adequate protection for many types of noisy situations.
Disposable foam earplugs are the most widely used type of HPD. The soft foam is rolled into a tightly compressed cylinder then inserted into the ear so that it conforms to the unique shape of ear canal. They are relatively low price per pair and can result in a high noise reduction when worn correctly.
Push-to-Fit earplugs are soft foam tips with a flexible stem where there is no need to roll down the foam tips before inserting into the ears. This works well for employees who have difficulty rolling and inserting disposable foam earplugs and can even be inserted when hands are dirty or when wearing gloves.
Reusable earplugs are washable with flexible, elastic flanges attached to a stem and can be reused multiple times and therefore replaced less, potentially resulting in lower long-term cost. The elastic material doesn’t absorb moisture and works well in wet conditions or when employees perspire heavily.
You Shouldn't Ignore These Warning Lights if They Show Up on Your Car's Instrument Cluster
Cars today have lots of bells and whistles. If you are used to driving an older car, some of the new warning lights can seem confusing. While there are indeed new warning lights that have been added with new technology, many haven't changed over the decades. Ignoring these warning lights, which are there to alert you to a potential problem, can leave you stranded or cause further costly damage.
THERMOMETER OR TEMPERATURE LIGHT
The thermometer or temperature light should be an indication for you to immediately pull over and turn off your engine. If your thermometer light is illuminated, your engine is overheating and serious damage could result. The problem can be anything from a stuck thermostat, a coolant leak, a malfunctioning temperature sensor or even too much oil in the engine. If your car is overheating and you have sufficient coolant, you can turn your heater on to maximum to help cool the engine just enough to make it to a safe place. Continuing to operate an engine that may be overheating can cause serious damage to the vehicle, damage that might cost more to repair than buying a replacement vehicle.
OIL LIGHT
An oil warning light should also be taken very seriously. It means your oil level in the engine is low or that the oil pump is not circulating oil properly and at the correct pressures. In either case, engine damage is likely to occur and the vehicle should be inspected to determine the cause of the problem. You may have a minor oil leak, a malfunctioning oil pressure sensor, restricted oil passages, an improper oil level, or a number of other mechanical issues.
BATTERY LIGHT
If the battery light comes on, it means that your alternator is not charging the battery sufficiently. The car might still run, but it probably won't run for very long. Keeping the vehicle running with an insufficient charge can discharge your battery, leading to a vehicle stall and no power to restart the engine. Batteries that discharge, even a little, run the risk of damage.
CHECK ENGINE OR SERVICE ENGINE SOON LIGHT
This light is a little bit of a mystery. It can be anything from a loose gas cap to a damaged catalytic converter. There's no way of really having any idea of what the problem is without having the vehicle diagnosed by a professional. And you should have the problem repaired. Most problems that trigger this light also cause a drop in power and a reduction in gas mileage. If this light indicates a problem in your emissions system and your bumper-to-bumper warranty is expired, you may qualify for free repairs under the federal emissions warranty.
You should be OK to drive with the light on, but you should still have it checked out as soon as possible. If the problem is only temporary (e.g. loose gas cap), the light will go out on its own after a few ignition cycles.
If this light is flashing, pull over and turn the engine off immediately. A flashing light indicates a problem that can potentially cause serious and costly damage to the engine or emissions components.
BRAKE LIGHT
Brakes are important to safe vehicle operation. Most of the time this light indicates an electronic problem in the braking system, but it can also indicate low brake fluid. Have this problem checked soon because your braking ability may be compromised. If the problem is due to brake fluid leaking into electronics components, you run the risk of a fire that can happen long after you turn off and park your vehicle.
AIRBAG LIGHT
The airbag light being illuminated means that there is a problem with the airbag system in your vehicle. One or more of the airbags may not function in the event of a crash. This should be checked as soon as possible. The problem is usually related to an electrical problem, such as a bad sensor or a corroded or broken wire. Replacement of the air bag itself may be needed, but it is not a very common repair.
TIRE PRESSURE LIGHT
If your tire pressure light is on, one or more of your tires may be critically low (or high) in pressure. The tolerances vary between manufacturers, but the light indicates that at least one of the tires is off by at least 25% from the target pressure or from the other tires. You probably picked up a nail somewhere, which is relatively easy and inexpensive to fix. Or you could be looking at a faulty tire pressure sensor inside the tire. In any case, you should be checking your tire pressure regularly.
|
|
|
Pet Food: The Good, the Bad, and the Healthy |
Posted by: D133H - 10-08-2021, 08:05 AM - Forum: FPS and Shooters
- No Replies
|
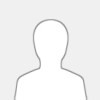 |
Pet Food: The Good, the Bad, and the Healthy
Pet Food: The Good, the Bad, and the Healthy
Most dogs and cats in the U.S. eat food and treats manufactured specifically for their particular species. Holistic veterinarians focus on the quality of nutrients entering pets’ bodies and strive to get them on whole-food-based diets with the same grade of nutrients consumed by humans. By providing their pets with commercially available dry and moist foods and treats – and under a barrage of buzzwords highlighting their supposedly nutritious nature -- pet parents are lulled into a false sense that their pet’s best health is being served. That is not always the case. In fact, pet parents can inadvertently poison their furry family members.
Let’s consider why pet food may be a good or bad choice for your pet, starting with ‘the good.’
The Good
Automatic feeders can make feeding your pets even more convenient. Even with a busy schedule, you won't have to worry if your pet has had their breakfast or dinner.
Convenience
When feeding most commercial foods, pet owners benefit from the convenience of opening a bag of dry food or a can of wet food, or defrosting and serving frozen pet food. As our society has become more focused on convenience instead of health, processed foods requiring little to no preparation have become popular among pet owners.
Nutritionally Complete and Balanced
Commercially available pet food is required to be nutritionally complete and balanced for all life stages, which gives the pet owner a degree of certainty that their companion animal will consume a combination of proteins, fats, carbohydrates, fiber, vitamins, and minerals to meet their nutritional needs.
Labeled List of Ingredients and Recommended Feeding Guidelines
Commercial diets and treats are regulated by the Food and Drug Administration (FDA) and the product’s label is legally required to include “proper listing of all the ingredients in the product in order from most to least, based on weight” along with Guaranteed Analysis (percentages of crude protein, fat, fiber, and moisture).There is also a guideline for the daily quantity of food recommended to be fed based on pet body weight. Now let’s move onto ‘the bad.’
The Bad
Feed-Grade Ingredients Cooked at Nutrient-Destroying Temperatures
Unfortunately for our pets, nearly all commercially available dog and cat food is made with ingredients considered to be feed-grade instead of human-grade. Feed-grade ingredients are lower quality than human-grade.
Additionally, feed-grade ingredients have allowances for toxins, such as mold-produced mycotoxins, that are acceptable in significantly reduced quantities in human-grade foods. Meat ‘meals’ such as ‘meat and bone meal’ and ‘by-products’ come from the rendering process and can contain “dead animals from farms, ranches, feedlots, marketing barns, animal shelters, and other facilities; and fats, grease, and other food waste from restaurants and stores.” (according to the National Agricultural Law Center).
Another contaminant that can come along with these dead animals is pentobarbital, an anesthetic used to euthanize animals (confirmed through FDA testing of dog foods). Even the less questionable ingredients may not be as nutritious as you think. Dry (kibble) and canned foods are cooked at high temperatures to kill bacteria, but which also deactivates beneficial enzymes and denatures protein’s more bioavailable form. Similar to microwaving or “nuking” your food, this reduces the nutrients in your pet’s food.
Chemicals & Preservatives
Butylated Hydroxyanisole (BHA), Butylated Hydroxytoluene (BHT), and Ethoxyquin are 3 nasty chemical preservatives. BHA and BHT are chemicals added to oils (fats) as preservatives that can be found in pet foods and treats. According to California’s Office of Environmental Health Hazard Assessment, BHA is on the list of Known Carcinogens and Reproductive Toxicants. BHT is also a carcinogen and causes kidney and liver damage in rats.
Ethoxyquin is another chemical preservative which is illegal to use in human foods in the United States, yet can still legally be added to pet foods. Human safety data reports Ethoxyquin to be harmful if it is swallowed or directly contacts skin. Ethoxyquin often enters through ‘fish meal’ and may not even appear on a label. It’s best that your pet’s food and treats have no preservatives, but natural options like Vitamins C and E are safer choices.
Propylene Glycol (PG) is a humectant (moistening agent) found in some soft dog foods and treats. It is chemically derived from ethylene glycol (EG), also known as antifreeze, which is extremely toxic to animals.PG is touted as non-toxic and non-absorbent for your pet, but consuming ‘pet-safe’ antifreeze’ will not improve your pet’s health. We also provide many other pet products.
Why some dry dog foods could be hazardous for your pet’s health
There’s very little oversight into what goes into pet feed, the authors write. A bag of dry dog food needs to contain only 25 percent of the meat listed, so long as the packaging contains a descriptor such as “dinner,” “formula,” or “platter.” If one of these descriptors is used and water is added for processing, as is the case with canned food, the food must only contain 10 percent of the specified protein. And, the authors write, diseased, or disabled animals — is allowable, as are additives like melamine, peanut shells and dehydrated chicken feces.
“We’re using our four-legged family members .?.?. as walking recycling machines,” Chavez, an adjunct professor of veterinary clinical nutrition at California State Polytechnic University, Pomona, told The Post. “Everyone has this illusion that [the pet-food industry is] super tightly regulated and controlled. And that’s just not the case.”
Veterinary nutrition is a relatively new field. Cornell University, with one of the top vet schools in the country, does not require students to take a course in animal nutrition to graduate. Plus, large pet-food companies actively court veterinarians and their loyalty, donating huge sums to schools and providing discounts to students.
Wet vs. Dry Cat Food: Which is Better?
If you’ve wondered which is better when it comes to wet vs. dry cat food, they’re both excellent choices. Just make sure the food you select is 100 percent complete and balanced for your cat’s age and life stage. While some cats (and cat owners) prefer one over the other, the best option may be to feed your cat both.
Wet Cat Food
You’re probably familiar with the wet food in cans, but you may also find it in pouches. Both “come in small sizes, making it easy to provide a variety of different flavors, and for some, smaller sizes may make portion control easier,” says Purina Veterinary Nutritionist Dr. Dorothy Laflamme.
Wet cat food has at least 65 percent or more moisture content. As a result, “wet food should not be left out for more than 30 to 60 minutes at a time to prevent bacterial growth,” according to Laflamme.
Wet cat food offers many benefits, though, including:
Textures and ingredients cats love
Easier for cats to chew
More variety in diet
Helps increase total water intake
Although feeding wet food to your cat seems special or indulgent, it’s more than a snack or treat. Wet cat food is 100 percent complete and balanced and can be an essential part of any cat’s diet.
Dry Cat Food
Dry kibble is popular among many cat owners because it’s convenient. It comes in larger bags and because its moisture content is less than 20 percent, it has a longer shelf life, even after opening. This makes it more cost effective.
There’s less risk of bacterial growth with dry food, so you can leave it out all day for your cat to graze on while you’re at work. Crunchy kibble also helps reduce plaque and tartar buildup on cats’ teeth. Dry cat food may be more difficult for older cats to chew, however.
Is Wet or Dry Food Better for Cats?
Ultimately, your cat will decide whether she prefers dry or wet cat food. Purina nutritionists recommend feeding a combination of wet and dry food, though. This helps ensure she gets plenty of moisture in her diet, plus the dental benefits of dry food, all while adding variety to keep her interested.
Cats are neophiliacs, meaning they appreciate trying new things. They may get bored eating the same food the same way day in and day out. Mixing wet and dry cat food for a meal or feeding them at separate meals is a good way to give your cat the variety she not only wants, but also needs.
Catering to your cat’s needs and desires also strengthens your emotional connection. One reviewer wrote: “My kitties love Fancy Feast already and they quickly gobbled up the Creamy Delights! Received extra kitty lovin’ after this awesome treat!”
Shop Wet Cat Food
If you’ve never tried feeding wet cat food, explore the wide variety of options Purina offers. You may need to try several brands until you find a couple your cat likes. Fortunately, Laflamme reminds, “there are hundreds—if not thousands—of good quality cat foods available at grocery stores, pet specialty stores, online and through veterinarians.”
It’s also a good idea to try a few different serving methods. Some cats prefer their wet food “fluffed” and served on a flat plate or wide, low-edged bowl. Others will eat straight out of the can. Once you find a food and serving method your cat loves, she’ll enjoy eating a mix of wet and dry cat food on a regular basis.
Litter Matters Because of Texture
A big issue for cats is the texture of the litter. If a cat litter is too rough or the granules are too big, a cat will reject it because it doesn’t feel good under their paws. Remember, they love to dig around in their litter before and after they go, and if the litter is too harsh, they’ll reject it in favor of something else… like your favorite blanket.
Litter Matters Because of Smell
If you’ve ever walked into a bathroom and made a swift exit because of the smell, your cat can relate. A cat will avoid the litter box if it’s too full of waste, so make sure that it’s cleaned every day, especially if you have multiple cats. Alternatively, cats will reject the box if the litter is perfumed too heavily. It’s a delicate balance!
Litter Matters Because of Dust
Dust from clay litter is a big issue for cats and humans alike because both species can suffer from asthma. If you know your cat suffers from asthma, definitely stop using dusty cat litter as it can exacerbate the issue. It can also cause asthma, not just make it worse. Similarly, if you or anyone in your home suffers from asthma, COPD, allergies or other respiratory problems, avoid clay litter and use something else.
|
|
|
What a Fiber Laser Marking Machine Can Do For You |
Posted by: D133H - 10-08-2021, 08:03 AM - Forum: FPS and Shooters
- No Replies
|
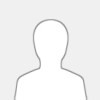 |
What a Fiber Laser Marking Machine Can Do For You
What a Fiber Laser Marking Machine Can Do For You
In this article, we are going to introduction the technology of Fiber Laser marking Machine, understand its scientific background, its applications, materials targeted and its challenges.
After reading this article, you should be able to discern how best to use this machine for your own applications.
Understanding Fiber Laser Marking
A fiber laser machine essentially has three main parts, including the pump, the resonator and the beam delivery system.
The pump comprises of laser diodes from which a light beam is emitted and transmitted through fiber optics to a resonator which contains what is known as the gain medium.
The resonator hosts the gain medium, which in simple terms is a fiber optics medium doped with rare earth elements.
The main differences between different fiber laser applications are based on the wavelengths produced, which determines the surfaces that each type can mark on.
Metal markers are mainly Ytterbium doped, giving them the wavelength that is needed for optimal absorptivity for material marking various metals and plastics.
The resonator combines the gain medium with a set of full and semi-reflecting bragg grating components, that allow for refraction, amplification and filtering light waves to get the right wavelength required for marking.
The filtered beam is then transmitted to the beam delivery system, which is simply a beam expander and a lens contained in a beam head. This is the ‘laser pen’ that does the marking
Flexibility is the main advantage of fiber laser marking, thereby making it the most preferred engraving and marking technique in the industry, due to its versatility in marking diverse materials.
The information marked can also be chosen freely, ranging from text, numbers, logos, codes, images and photos.
Color change is a common process used in Laser Marking.
The process provides high contrast labelling on any material without damaging its surface.
In this process, the laser heats the material at the precise intended areas, exciting atoms and vaporizing the required parts, thereby providing a high quality contrast color-change on the material.
Industrial Applications of Fiber Laser Marking Machine
Automotive industry
The automotive industry has become one of the largest users of this technology. It is estimated that a car is made of roughly 30,000 parts, which are either made up of steel, aluminum, copper, special fiber or plastic, all varying in shape and size.
The following are some of the applications where part marking is achieved using a fiber laser marker in the automotive industry;
Marking seat belt components with information such as country of origin, serial numbers and barcodes.
Marking various components and button on the dashboard. These need to be well visible during the day and illuminated at night. Therefore, day and night markings are used.
Other materials such as ceramics used to make spark plugs can also be marked using these method too.
You’ll also find Fiber Laser markings on engine blocks, automotive sensors, chassis VIN number and motorcycle parts.
One of the biggest concerns with markings in this industry is readability and traceability. Parts ought to be traced to their country of origins and markings be machine readable. It is for this reason Fiber Lasers have noted increased usage in the recent past.
Integrated Circuit Industry
Integrated circuit elements are the most important units used to build circuits and systems. This Laser marking machine can be used to make markings on Integrated Circuits boards and semiconductor components, including text and graphics.
The Laser Cutting Machine and Process
Laser cutting is a non-contact, thermal-based fabrication process suitable for metal and non-metal materials. For the laser cutting process to run smoothly and at optimum capacity, several factors should be taken into consideration, such as the laser cutting machine’s configuration and settings, the material being cut and its properties, and the type of laser and assist gas employed.
Overview of Laser Machine Components and Mechanics
In contrast to mechanical cutting, which utilizes cutting tools and power-driven equipment, and waterjet cutting, which utilizes pressurized water and abrasive material, laser cutting employs a laser cutting machine to produce cuts, engravings, and markings. While laser cutting machines vary from model to model and application to application, the typical setup includes a laser resonator assembly, mirrors, and a laser cutting head which contains a laser focusing lens, a pressurized gas assembly, and a nozzle.
Laser cutting of metal has been around for a couple of decades now, but there still appears to be some confusion of which laser is suitable for which application. Although metal can be successfully cut using plasma or water jet cutting machines, when it comes to accuracy and consistency it has to be a fiber laser cutting machine.
Today’s manufacturing industry is majorly concentrating on precision and pace of manufacturing the component. It is the fact that different tool is required to perform different operations on the component, hence there is a time factor involved in changing the tool. This ultimately results in loss of time which incurs cost. To minimize this time, fiber laser metal cutting machines have been introduced in the metal manufacturing industry. Here, the machine doesn’t get in contact with the materials, which means there is no wear and tear of tool, where the cost of renewing tool is zero.
There is a huge market for laser machines in industrial activities as the manufacturers are realizing the advantages of switching to the laser technology. We at MORN promote fiber laser machines which reduce time and cost of manufacturing, which is advantageous to the manufacturer as well as the buyer.
The benefits of a fiber laser cutting system include:
There are no moving parts or mirrors in the light generating source. This reduces the maintenance requirements and operating costs.
The electrical efficiency is high which results in lower running cost.
The speed of cutting thin materials is high.
It has the ability to cut reflective materials and there is no problem of back reflection.
Introduction
Laser welding machines and laser welding technology is becoming very popular with the advent of the latest laser generation technologies. In short, laser welding is the process of joining metallic bodies or thermoplastics using a laser beam.However, unlike the other conventional welding processes, laser welding can complete the job in much lesser time.
Categorization of Laser Welders
There are multiple modes of laser welding that we can categorize the machines into. Therefore, we can categorize laser welding technology in various ways. Let’s start defining the laser welding machines by the different categories:
Categorization is based on the type of laser
Pulsed Laser
The pulsed laser mechanism is ideal for metals that are light in nature and have low thickness. Thus, the pulsed laser makes intermittent exposure on the metallic body. Keeping it safe from burning or melting.
Furthermore, this type of laser welding is ideal for welding sheets of metal, razors, jewelry, and even medical prosthetics like screws.
The continuous laser
The continuous laser is ideal for welding on parts that have a high thickness and are strong. Moreover, this welding technology is good for refractory surface metals too.
This type of welding is costlier than the pulsed type welding but in the long run, saves a lot of money and labor for you.
Categorization based on the source of laser
Currently, there are three main types of sources of laser for laser welding machines that use one of these laser sources i.e. Fiber laser, CO2 laser, and Nd: YAG laser. Each of these laser sources has their own benefits and are suitable for the different types of welding materials.
Fiber Laser Welding Machine
The fiber laser welding machine is ideal for working on metallic parts. Furthermore, it offers great reliability and efficiency. According to estimates, the accuracy of the laser welding machine using fiber laser is close to 25%.
CO2 Laser Welders
The CO2 laser welders can provide a great continuous welding beam that creates efficient and durable welds. It can easily penetrate metals and non-metallic bodies.
Nd: YAG Laser welders
The Nd: YAG lasers are less energy efficient as compare to the fiber laser welding machines. However, there are certain applications like greater laser control that you cannot achieve with other types of laser sources.
Summing up, you will get laser welders of all types, technologies, and sources. You will have to decide which type of laser welder will suit your business the best.
Before discussing the selection of the best laser welders, let’s have a look at the main applications of laser welding machines in the industry.
How to Choose the Right Laser Cleaning Machine?
Introduction
Laser cleaning machine is finding great applications in the industry today. It is often seen that rust, grease, and other such substrates form a layer with time over metals and non-metallic products. And with increasing time the laser rust cleaning and metallic parts cleaning technologies have evolved.
What is Laser Cleaning Machine?
Before moving on with other specifications of rust-removing laser machines, first, let’s discover a little about the technology and how it works. Rust laser cleaning or simply laser cleaning is a very safe way to remove rut and other substrates from the affected material. All of it without damaging or having to scrape your original material.
The laser rust cleaners work in the same way as the laser etching machines work. Meaning that the laser applies focused energy on a part of the material that is to be cleaned.
Thus, removing a very fine layer of the surface and exposing the clean material inside. Laser cleaning rust machines are very popular now in industries. Let’s have a look at the major applications of the laser cleaning system and major industries that use the technique.
|
|
|
HOW DOES A TFT MODULE WORK? |
Posted by: D133H - 10-08-2021, 08:00 AM - Forum: FPS and Shooters
- No Replies
|
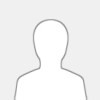 |
HOW DOES A TFT MODULE WORK?
HOW DOES A TFT MODULE WORK?
How does a TFT module operate? First, TFT stands for “Thin Film Transistor,” and it describes the control elements that actively control the pixels. Because of that, you hear a lot said about active matrix TFTs. How do the images get produced? It operates on a basic principle. You have the TFT LCD display, which has many pixels, and each pixel has the ability to reveal differing colors.
TFT displays also use a backlight that comprises fluorescent tubes to light a single pixel. When a small shutter gets opened, the light passes through. Of course, this technology is more detailed than what can fit in this article, but a simple explanation can give you an idea of how it works.
Just like LCD
Ever heard of an LCD monitor? LCD stands for a monitor technology based on liquid crystals that change in molecular structure as it is used. As a result of the liquid crystal changing their molecular structure, they allow for varying levels of light to pass through them, which is what gives the picture.
Explaining RGB
Every pixel on any screen is made up of three components: Red, green and blue. You might also sometimes see this stated as RGB, which means the same thing. Twisted Nematic TFTs are the most common device that employ this tech. Without voltage applied, the molecular structure will be in its natural state, but twisted by 90 degrees, which is why they call it a Twisted Nematic TFT. When the light gets emitted by the backlight, it passes through the structure. Once the voltage gets applied, it creates an electric field, and the voltage twists the liquid crystals so that they align vertically.
When it comes to the color filters of red, green and blue, each pixel will be made of the color cells. With a resolution of 1280×1024 pixels, you will have exactly 3840×1024 transistors. Pixels are decisive, and if you have a smaller spacing, it will give you the highest possible resolution, which means better picture quality. What happens if you have to switch to a lower resolution, which is often the case when playing video games? When that happens, the electronics scales the electronic size up to the maximum display panel size.
To learn more about TFT LCD display or TFT technology, get in touch with manufacturers such as Microtips Technology. So Contact Microtips Technology Representative today to find out which LCD module is best for your needs.
What is an OLED?
OLED (Organic Light Emitting Diodes) is a flat light emitting technology, made by placing a series of organic thin films between two conductors. When electrical current is applied, a bright light is emitted. OLEDs are emissive displays that do not require a backlight and so are thinner and more efficient than LCD displays (which do require a white backlight).
OLED displays are not just thin and efficient - they provide the best image quality ever and they can also be made transparent, flexible, foldable and even rollable and stretchable in the future. OLEDs represent the future of display technology!
OLED vs LCD
An OLED display have the following advantages over an LCD display:
Improved image quality - better contrast, higher brightness, fuller viewing angle, a wider color range and much faster refresh rates.
Lower power consumption.
Simpler design that enables ultra-thin, flexible, foldable and transparent displays
Better durability - OLEDs are very durable and can operate in a broader temperature range
Surface Mount Adapter Boards
In electronics design, the worst assumption a designer can make is building a "foolproof" circuit that ends up not working. The process of troubleshooting can be a lot of trouble especially when you have no idea what the problem may be. There are wires everywhere, tiny pins to count, and many components to check and test. The last thing you want to do is bring out the iron and desolder any ICs.
That's where surface mount adapter boards come in very handy. With the majority of new ICs these days emerging on the market in only surface mount packages, being able to build new prototypes requires designers to use only SMD components or make use of specialty SMD protoboards. Instead of using the old, trusted and familiar DIP-friendly breadboard.
With the new Jameco ValuePro surface mount adapter boards, designers are able to make use of multiple surface mount packages with one single board, you will save money over using multiple adapter boards, save time by soldering less, and ease your troubleshooting headaches if you are soldering SMD ICs directly into your breadboard.
SOIC and TSSOP-packaged ICs can be great for finished products; they take up much less real estate and allow the end product to be more easily manageable from a size perspective. During the design phase, it's much more convenient to work with ICs without needing a magnifying glass. The SOIC/TSSOP-to-DIP adapter board has both footprints on either side of the board so that you can design with either package without needing to purchase another adapter board. It comes in 8, 16, and 28-pin footprints and can easily snap apart at your convenience.
For those who want to work with more than just SOIC and TSSOP packages, the multiple footprint adapter board can accommodate SOIC, SOT, TO, TSSOP, as well as various SMT passive component packages. Just solder on some headers and you're ready to go.
A better automotive display from pixel to picture with local dimming
Automotive specifications and environmental conditions have caused the automotive display market to lag behind the consumer display industry in contrast ratio, black levels, resolution, curvature and form factor. Automakers are trying to differentiate their infotainment human-machine interface (HMI) displays and catch up to the technological advances now common in smartphone, tablet and television displays.
LCDs now pervade many aspects of modern life and are becoming more prevalent in vehicles, replacing analog and hybrid gauge clusters and becoming standard in the center information display and passenger entertainment areas of the vehicle. However, these displays lack the image quality and contrast ratio that consumers experience with their personal electronics.
If you look at the personal electronics market, you might assume that emissive displays such as organic LEDs (OLEDs) or micro LEDs are the best way to achieve the ideal automotive display. But numerous design and fabrication challenges – including lifetime, cost and peak brightness concerns – have delayed the implementation of OLED displays in automotive systems.
How can automakers meet modern display expectations? A full-array, locally dimmed backlight architecture has the potential to improve the contrast ratio of LCDs to near-OLED levels, while consuming less power than traditional backlight methods.
Uses for Outdoor LCD Displays
For a long time now, LCD displays have become the screen of choice for home use. Most TVs are now LCD as are computer screens used in homes and offices, but indoor locations are nor the only area where LCD displays are being used. This article is about the rise of outdoor LCD displays, which are now cropping up in all sorts of outdoor locations.
For a long time now, LCD displays have become the screen of choice for home use. Most TVs are now LCD as are computer screens used in homes and offices, but indoor locations are nor the only area where LCD displays are being used. This article is about the rise of outdoor LCD displays, which are now cropping up in all sorts of outdoor locations.
LCD displays (liquid crystal displays) have several advantages over their CRT predecessors (cathode ray tube). Lighter, flatter and cheaper to buy, it is no wonder LCD displays are now the screen of choice for most homes and offices. Used as TVs and computer monitors, LCD displays take up less room than CRT monitors and are now ubiquitous.
Because of the light, flat design, LCD displays are seen outside the home too. Airports, shopping malls and other retail locations are now full of digital signage-LCDs displaying advertising and promotional content.
Digital signage is an effective method of advertising, able to reach large audiences by connecting with the commuters and shoppers around town. With moving imagery and HD technology, these screens provide a more noticeable form of out of home advertising than traditional static signs and posters.
While digital signage inside shopping malls and retail stores can reach large audiences, even greater numbers of people are available outside along high streets, which is why more and more digital signage displays are being erected in outdoor locations.
Using a standard LCD display outside is of course, not possible. Rain and other elements will soon disable a standard LCD, while the variable temperatures and risk of damage through vandalism means that any outdoor LCD display needs to be tough and contain sophisticated climate control systems to prevent the screen overheating or freezing.
Outdoor LCD displays need also to cope with sunlight. Because of the sun’s brightness and its ability to make a standard screen unreadable, an outdoor LCD display is often several times brighter than an indoor LCD. LCD brightness is measured in nits (a unit of luminance) and most indoor screens have nit value of around 400; outdoor displays on the other-hand have a nit value exceeding 1200, giving them the power to cope with even the brightest of sunshine.
|
|
|
Static Var Generator (SVG) |
Posted by: D133H - 10-08-2021, 07:58 AM - Forum: FPS and Shooters
- No Replies
|
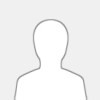 |
Static Var Generator (SVG)
Static Var Generator (SVG)
SVG Principle
The principle of the SVG static var generator is very similar to that of Active Power Filter, as demonstrated in the picture below. When the load is generating inductive or capacitive current, it makes load current lagging or leading the voltage. SVG detects the phase angle difference and generates leading or lagging current into the grid, making the phase angle of current almost the same as that of voltage on the transformer side, which means fundamental power factor is unit.
Delta’s PQC series SVG is also capable of correcting load imbalance.
SVG Structure
Delta PQC Series SVG static var generator is also modular in design, and the Delta SVG system consists of one or several SVG modules and an optional Liquid Crystal Monitor & Control Panel (LCM). Each SVG module is an independent reactive power compensation system, and users can change the SVG rating by adding or removing SVG modules.
SVG modules and LCM panel can be embedded in Delta’s standard SVG cabinet or in a customized cabinet. There are usually breakers, cable terminals and Surge Protection Device (SPD) in the SVG cabinet.
Active harmonic filters are more of a system solution. How do they work?
Harmonics come from the nonlinear load. Active harmonic filter, also called harmonic correction units, is parallel devices that act like a noise cancellation system and inject equal and opposite frequencies to mitigate harmonics. The filters can also provide additional current to correct the power factor. So, what’s left coming from the source flowing back to the utility is only a nice, clean current that is in phase.
For example, if we run four 6-pulse variable frequency drives at the same time, we have a harmonic spectrum of 5th and 7th and 11th and 13th harmonics. The waveform will show a significant amount of harmonic current in the total harmonic distortion. When the active harmonic filter is turned on, it will inject equal and opposite harmonics to cancel what’s there. The waveform now will be clean and in phase. If we go back and look at the harmonic spectrum, the current distortion is very low.
Adding active harmonic filters can be a good harmonic solution for power systems. Though more costly than other options, if you have multiple drives running all the time and multiple drives as backup, harmonic filters would be a reliable way to capture any and all of the harmonics coming from the loads. However, one important thing to know from a system design standpoint is that your drive should have either a DC choke or an AC line reactor to minimize the harmonics coming out of the drives.
Active harmonic filters typically come in 50, 60, 100, 200 and 300 ampere units that you can parallel. Another benefit to using active harmonic filters is that you cannot overload them, because once they put out the maximum harmonic current and power factor correction that they can, they stop producing at that level—whether it’s 100 or 120 amperes, whatever the case may be.
Using active harmonic filters on your power system provides a system-level solution for internal and external harmonic protection.
What are active harmonic filters?
Active harmonic filters are parallel filters (which means the current doesn’t go through the filter) that are used to reduce, or mitigate, harmonics to tolerable levels as defined by IEEE-519. Active filters use a set of transistors and capacitors to filter (or clean) the current wave by injecting inverse currents to cancel out the undesired harmonic components. Active filters are significantly more expensive than passive filters and take up more space. Size is an immense factor in system design today and should be accounted for when deciding on what type of harmonic filter is right for you.
Active filters can work with multiple drives; when the active filter reaches its limit, it won’t overload. In addition, if an active filter breaks, it won’t stop the motor (since current isn’t going through the filter); it just won’t filter the current wave.
Active harmonic filters can effectively cancel harmonic distortions from the network. This blog post will explain the key criteria that should be kept in mind when buying an active harmonic filter.
1.1. Inverter topology
Most modern AHFs are built on 3-level NPC inverter topology which brings several benefits compared to AHFs built on the conventional 2-level topology. In 3-level topology, the switching frequency and voltage stress are distributed among the IGBTs. Reduced stress extends the lifetime of the power electronics. Higher efficiency, lower losses and lower noise levels are also achieved. These make the overall cost of ownership much lower.
1.2. Losses
Depending on design and topology, AHFs can have higher or lower losses. Checking the losses is important as they will reduce the life cycle cost of the investment. Usually AHFs have about 2-3% losses (depending on rated power). AHFs built on 3-level NPC inverter topology have lower losses than 2-level ones. Depending on the user profile, reduced losses create a potential for considerable financial savings if the LCC is calculated over a period of few years.
1.3. Response time
Some power quality phenomena occur extremely fast, requiring the mitigation to be even faster. If the process is affected by fast voltage fluctuations or transients, it is very important to evaluate the AHF’s overall response time.
1.4. Interharmonics
Interharmonics are usually caused by synchronization issues. If the installation includes interharmonic sources, the manufacturer should be consulted as not all AHFs can deal with this. It is a common issue with cycloconverters or some types of older wind turbine generators.
1.5. Harmonic compensation capacity
Harmonics can be seen in the odd and even orders. Common capacity for AHFs is 25th or 50th harmonic order. Sometimes there is a claim of being able to mitigate the 51st harmonic, which has little value as harmonic orders of 51st and above do not appear in electric power systems. An important issue is that the AHF can offer the possibility of selecting which harmonic order to compensate. For some devices, it is possible to select the whole harmonic spectrum (1st to 50th, odd and even), but for some others only few harmonic orders can be selected. Depending on the application, the capacity to compensate a certain harmonic order is a critical issue affecting the performance of the whole system.
1.6. Electromagnetic compatibility (EMC)
In some countries there are strict guidelines regarding the EMC. To be sure that the AHF is not causing interference it must be fitted with a properly designed EMC filter.
1.7. Derating according to harmonic order
The rating of an AHF is usually defined at nominal load (at 50/60Hz). As the AHF works further up the harmonics, its capacity compared to nominal starts to derate. For example, a derating of 50% at the 13th harmonic order means that a 100A AHF has only the capability to compensate 50A at the 13th harmonic order.
Derating is a matter of how robustly the AHF is designed. This capability is more dependent on the change rate of the current than just the frequency and magnitude of the current (all different frequencies, their magnitude and phase have an effect). Because of this, a derating curve cannot show the capability of the AHF. The only way to verify the real compensating capability of a device is to check its di/dt capacity. This compensating capability is clearly better in 3-level NPC inverter topology AHFs compared to 2-level topology devices.
1.8. Physical footprint and modularity
Most suppliers offer several installation alternatives: Cubicle type, wall mount or loose modules that can be locally installed inside new or existing cubicles. A modular AHF design allows customers to adapt to potential changes in future harmonic filtering and reactive power compensation needs. Modular design means that it is possible to add easily to the AHF’s capacity within the existing configuration, saving both costs and space.
1.9. Voltage
AHFs are offered in a range of voltages, most common is 200V up to 690V. Some manufacturers can produce AHFs for higher voltages, up to 1000V, without step-up transformer, reducing costs and footprint. It is possible to connect AHFs to high voltage (over 1kV) systems using a suitable step-up transformer. Step-up (or step-down) transformers can reduce compensation performance due to increased impedance between the AHF and network.
1.10. HMI
There are different HMI setups for AHFs. Some have a very simple front HMI while others include graphs showing the current and voltage waveforms and many further functions in different languages. A great added value is to have at least a web-based interface allowing in-depth monitoring and control functionality.
1.11. Commissioning software
Commissioning and service of AHFs without proper tools can be time consuming. Some suppliers provide software for this. Minimum required functionality should be that the system performs a self-check of voltage and CT phase order, CT polarity check, self-diagnosis and self-calibration. Such features will find installation errors before they can cause problems and will shorten the commissioning time. If the AHF does not have this type of software the commissioning becomes more complex and might require external support adding to the system costs.
1.12. Smart Grid functionality
Some AHFs have a built-in power quality analyser to calculate the required compensation. Some suppliers enable the user to connect all AHFs on site through a web-based architecture. An operator can then have an overview of the status of all connected AHFs and log them. This enables the possibility to log events that could have caused production disturbances, monitor individual AHFs, and remote monitoring and analysis capability.
1.13. Control of detuned capacitor banks
Very often AHFs are installed at sites together with existing or new contactor or thyristor switched detuned capacitor banks. Some suppliers offer the possibility to control the steps of these banks directly from the AHF’s control system through dedicated digital outputs in the AHF. By doing this it is possible to use the comprehensive power quality monitoring and reporting features of AHFs to accurately monitor all the parameters of the installation and control the total power quality improvement needs. This brings an optimal system integration, efficient operation, cost savings on the control system, and the possibility to build hybrid var compensators (HVC).
1.14. Cancellation of harmonics in neutral (4W)
Typically, active harmonic filters are installed to cancel harmonics distortions created by AC and DC drives or UPS systems. However, use of LED lighting as well as other single-phase loads in the buildings also produces tripplen harmonics which accumulate in the neutral wire and should also be mitigated. Therefore, active harmonic filter should be easily configurable to 3W or 4W applications.
|
|
|
How to Maintain Your Dust Collector |
Posted by: D133H - 10-08-2021, 07:56 AM - Forum: FPS and Shooters
- No Replies
|
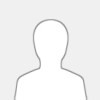 |
How to Maintain Your Dust Collector
How to Maintain Your Dust Collector
The inception of the dust collector has allowed companies to effectively capture airborne particulate from an air stream. This has become more important for several reasons. First, containing particulate — toxic or not — is necessary to provide a healthy and clean work environment. Second, increasing local and global awareness of air pollution, containment and the process dust in industrial applications has emphasized the importance of dust collectors. Finally, expanding regulations have pressured companies to properly design, install, operate and maintain dust collection equipment.
To ensure dust collector bags are functioning properly, you need to perform periodic inspections, as well as repair and replace damaged or malfunctioning equipment. A routine inspection and maintenance program will boost your equipment's performance and life. To maintain the health and effectiveness of your dust collector, follow our helpful list of procedures.
1. Create an inspection/maintenance program — A typical program consists of a schedule for periodic inspections that are performed on a daily, weekly, monthly, semi-annual and annual basis. Failing to periodically inspect the dust collector can hurt its performance. Subsequently, the dust collector may not meet EPA outlet emissions standards.
2. Don't exceed recommended pressure drop — Sometimes called differential pressure, it's the amount of static resistance across filters when operating a positive- or negative-pressure dust collector. Pressure drop, typically measured in inches of water column (in w.c.), is a good indicator of the amount of dust that has collected on the filter media and, if continually monitored, the condition of the filters.
New filters have the lowest pressure drop because of the inherent permeability of the media. As the bags develop a dust cake, some particulate embeds itself into the filter media, increasing pressure drop accordingly. The filtering of the airstream through this accumulated dust cake provides high-efficiency collection of fine particulate. In fact, the highest efficiency a dust collector can offer is just before the cleaning is initiated. However, high differential pressures can cause filter media bleed-through or blinding. Therefore, do not to exceed the manufacturer's recommended operating pressure drop.
3. Ensure cleaning system functions properly — Equipment use a variety of cleaning systems to dislodge accumulated dust cake from the filter media. Systems include reverse air, shaker or pulse clean. Regardless of the style of cleaning, it is imperative that this system function properly at all times. Without an effective cleaning system, dust will continue to build on the bags. The result will be an increased pressure drop and reduced volume of ventilation air at the pick-up points. Further, airstream velocities within the ductwork will decrease and cause dropout of dust in the ducts. This may choke the entire system and render it ineffective.
4. Watch for visible emissions — This includes any particulate that can be seen discharging from the exhaust stack. These emissions indicate a breach in a seal or a broken (torn) filter. In either case, you must find and correct the leak immediately. Not only will the emission cause a health concern and damage the property outside the plant, but it may also bring about monetary fines imposed by local, state and federal environmental agencies. Additionally, fans located downstream of the collector can be damaged from abrasion or become imbalanced if you don't correct this condition quickly.
Continually monitor exhaust from the dust collector. Besides visual inspections, consider incorporating a broken bag detector into the clean air ductwork. If a bag begins to fail, or there's a leak in the bag seal, you'll detect the particles that bypass the media. Typically, these detectors use triboelectric technology. These devices can be wired to an alarm horn, siren or PLC.
5. Select the right exhaust fan — Dust collection systems require an exhaust fan to accelerate ventilation air from the point of pick-up, through the ductwork and dust collector filter media and out the exhaust stack. Fans are selected to accommodate volume (SCFM) and pressure drop throughout the system. Calculate the pressure drop by evaluating the static resistance of the dust collector, ductwork and pick-up points/hoods.
6. Inspect the filter media — This is the most important item in a dust collector because it accumulates and supports a dust cake. This dust cake is what provides high filtering efficiencies during operation. Inspect the clean-air side of the dust collector for leaks and the bags for tears. If pressure-drop within a dust collector becomes extremely high relative to historical data, it may be caused by excessive dust cake or blinding of the filter bags.
Depending on the application, differential pressure may take a number of hours or even days to develop. It is essential that you keep filtering velocities low for new filter media. Reducing the volume decreases the airstream's velocity, thus protecting the bags from high-velocity impingement of dust. If you expose bags to the fan's full volume, fine particles may embed themselves into the bags' inner fibers and begin blinding. This can also reduce the life of the bags by damaging the fibers of the media. So make sure to season a collector's filter bags.
This is not an all-inclusive list. Each piece of equipment and application is different, and each has its own unique components and features. But these simple procedures can help you monitor and maintain your dust collector's heath, as well as prevent shutdowns due to inefficiencies, prolong filter life and prevent costly EPA fines.
Dust Filter Bag
The welding of the filter bag cage is not standardized. The unevenness of the welding frame of the filter bag cage or friction with the cabinet will cause the dust filter bag to be worn out during shaking. Generally, the uneven surface of the filter bag cage refers to burrs or edges at the welding place;
The dust bag installation is not standard. The dust filter bags are too loose when suspended, which may cause the dust filter bag to collide or friction with other components, resulting in damage to itself;
The disassembly and assembly of the dust filter bag is not standard. When the dust filter bag is disassembled or installed, it is likely to collide with metal edges and wear the cloth bag. This kind of injury is not easy to detect, but ash will appear during work;
The cleaning cycle is unreasonable. The dust removal cycle is too short and the dust removal method is wrong, which will increase the burden on the dust filter bag and cause the dust filter bag to be easily damaged;
Dust-containing gas properties. The temperature of the dusty gas is too high, the concentration is too high, and the wind speed is too high, etc., it will increase the burden of the dust filter bag and easily cause premature damage to the dust filter bag. In addition, if the dust filter bag used fails to match this working condition, it is easy to burn. On the contrary, if the temperature is too low and the wind speed is low, it is easy to cause condensation and dust removal of the dust filter bag. The high dust filter bag needs to be replaced.
Five Things You Should Know about Dust Collection Filter Media
#1: Most industrial dust collection manufacturers design filters or collectors. Few design both.
The customer wins when a manufacturer understands the behavior of both the filter media and the dust collector and designs both. When a supplier can optimize the interaction between the filter media’s performance and the collector’s performance as a single consolidated system, the customer benefits by a more stable and dependable operation and lower operating costs.
#2: Effective filter media designs may require thousands of computer simulations before initial lab samples are produced or final media grades are released to production.
Filter media development is very involved and includes the testing of raw materials and properties of filter media blends. Raw material testing and media development labs often evaluate media components using: high-performance liquid chromatography (HPLC), FTIR (Fourier Transform Infrared) Spectroscopy, TD-GC-MS (Thermogravimetric Analyzer - Gas Chromatography - Mass Spectrometry), and SEM (Scanning Electron Microscopy). These tools help ensure the optimal design and materials are being used to appropriately match the application conditions.
Development of Donaldson media grades includes computer modeling to predict tensile strength, stiffness, permeability, and a variety of other filtration and efficiency levels. This modeling helps ensure a thorough understanding of the potential physical properties of a media recipe before a test recipe is even produced in the lab. When a recipe shows promise, samples are produced in the lab so physical testing can confirm the predicted properties.
Donaldson considers filter media development one of its core competencies. Even so, with all our background and experience, new media recipes still go through thousands of computer and lab iterations to achieve the optimized characteristics before we begin production of a new media grade.
#3: There’s more to manufacturing filter media than meets the eye.
The general process of developing any filter media should begin by identifying the application requirements. Then specifications are determined for not only the finished media grade, but for the final filtration product in which the dust filter media grade will be incorporated (i.e. cartridge, panel, or filter pack).
Factors to be considered in media recipe formulation include: a cost level which makes sense for the market; minimum efficiency levels needed to achieve acceptable emissions; the type and amount of material being filtered from the fluid stream by the media filter; and the physical environment to which the media will be exposed. Other factors include: pressure, vibration, temperature, humidity, and chemical composition of contaminants.
Pressure drop, or the resistance necessary to cause fluid flow through the media, is considered critical to media design because this impacts the energy it takes to move fluid through the media and, therefore, the operating cost of the filter developed.
All of these variables are considered important, and they must be balanced against one another to formulate an optimized media grade for an application. For example, a formulation may use expensive materials and provide high efficiency, yet the very dense filter media might be expensive to operate in the collector because of the high pressure drop of the filter and its replacement costs. A dense filter media design might also compromise the performance of a cleaning system and could result in shorter overall filter life and increased maintenance material and labor costs.
On the other end of the spectrum, a filter media comprised of low cost materials with low pressure resistance may offer initial benefits. However, if the media does not handle the physical challenges of the operation or becomes quickly plugged, the operational disruption and maintenance downtime and expense make it a poor choice. Optimizing the various performance measures is essential to overall collector performance.
#4: Some manufacturers offer 300+ grades of filter media from which to choose.
Some manufacturers are so serious about providing exactly what the customer needs they offer hundreds of choices to the market, each tailored to meet specific challenges and requirements. If an appropriate media does not exist for an application, new media development may be undertaken.
#5: Evaluating dust collection manufacturers pays off.
When evaluating dust collection manufacturers, look for one that offers media grades optimized for your application and for the collector in which they will operate. This will help optimize your filter efficiency performance, extend your filter life, and lower your cost of ownership. Choose a company with a strong history of providing expertise and technical support.
If you’re employed by a global company, consider a global dust collection manufacturer that can provide excellent customer support around the world – including stock inventory of common filters and parts so they are ready to ship when you need them. A company like this will provide you exactly what you need.
|
|
|
TCXO, Temperature Compensated Crystal Oscillator |
Posted by: D133H - 10-08-2021, 07:53 AM - Forum: FPS and Shooters
- No Replies
|
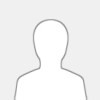 |
TCXO, Temperature Compensated Crystal Oscillator
TCXO, Temperature Compensated Crystal Oscillator
As the name indicated a temperature compensated crystal oscillator provides a means of counteracting the frequency change caused by temperature change in a crystal oscillator.
The letters TCXO stand for Temperature Compensated Xtal Oscillator - Xtal is short from crystal and implies a quartz crystal resonator. The TCXO module is able to provide considerably improved performance over that of a standard crystal oscillator, especially in terms of frequency stability over a temperature range.
By measuring the temperature and applying a correction voltage to a VCXO, the frequency stability over a temperature range is considerably improved whilst keeping costs low - using an oven controlled crystal oscillator, OCXO would be considerably more costly and much larger in size.
Often a wide range of TCXOs of varying frequencies, supply voltages and packages is available from many distributors, enabling these electronic components or modules to be used in many general electronic designs, RF circuit designs, etc.
Temperature performance of crystal oscillator
Crystal oscillators are able to provide a much better level of performance than that provided by LC resonator circuits. Nevertheless crystal oscillators are still affected by temperature.
The angle of the cut and other aspects of the quartz crystal have a major impact on the performance.
As a result special cuts are defined and one known as the AT cut is the most widely used for these and many other quartz crystal RF applications. This gives a good level of performance for RF circuits in terms of suppression of unwanted modes of vibration as well as the frequency range available, and also the temperature stability.
Despite this, AT cut crystals on their own cannot meet the requirements for many applications and temperature compensation is required if they are to perform satisfactorily over the required range - often 1 - 70°C at elast is needed.
The effects of temperature are, to a large degree, repeatable and definable. Therefore it is possible to have an electronic design to compensate for this. By adding additional electronic components to the basic oscillator, it is possible to considerably reduce the effects caused by temperature changes: a temperature compensated crystal oscillator, TCXO.
TCXO solution
A TCXO adjusts the frequency of the oscillator to compensate for the changes that will occur as a result of temperature changes. To achieve this, the main element within a TCXO is a Voltage Controlled Crystal Oscillator, VCXO. This is connected to a circuit that senses the temperature and applies a small correction voltage to the oscillator as shown below.
INTRODUCTION
The history of the development in crystal filter technology, from the initial concepts of Cady to the current wide range of products, provides a fascinating chapter in the development of today’s highly complex electronic products. The crystal filter has been a particularly critical element in the development of narrowband communications systems. The desire to send multiple voice messages on a single telephone line resulted in the introduction of carrier telephone systems in 1916. These early systems used LC filters in the 10 to 40 kHz frequency range. However, the bandwidth limitations caused by realizable coil Q’s were quickly recognized. In 1929, W.P. Mason of Bell Laboratories developed methods for incorporating crystals into LC lattice filter networks. This work resulted in the development of a 60 to 108 kHz basic group-band filter set used to frequency multiplex 12 voice channels. This work is described in Mason’s 1934 paper which was the basis for essentially all crystal filter designs generated during the next 20 years. During this period the major application for crystal filters was in carrier telephone equipment. However, in the mid-1950s, newer narrowband radio communications systems were developed both for military and commercial use which required high-frequency, stable, narrow-bandwidth filters. In most cases, crystal filters were the answer for these filtering applications and a new manufacturing industry was formed to supply these needs. Other applications quickly followed in navigation and radar equipment, in new fire-control systems, and missile control systems. This increased level of activity resulted in new filter design procedures and substantial improvement in the quality of high-frequency filter crystals.
In the 1960s another major technology step occurred with the development of monolithic crystal filters. Through the 1970s and ’80s evolutionary improvements were made with the development of multi-pole monolithic filters and the extension of the high frequency limits through continued process improvements. Significant theoretical work was also accomplished in this period in the area of device modeling. High frequency limits are still being pushed today with blank etching techniques and improved photo-lithography.
DESIGN EVOLUTION
Professor Walter Cady, who carried out much of the original development work on quartz crystals, was apparently the first to suggest the use of crystals as filter elements. In his 1922 paper he shows single-mode crystals with divided electrodes which could be used as coupling elements between adjacent circuits. However, in this configuration, only very narrow bandwidths are achievable and the filter would be useful only as a carrier-frequency filter. In 1927 patent disclosures were filed by L. Espenschied of AT&T and C. Hansell of RCA on the use of crystals in a filter structure. The Espenschied patent shows the use of crystals in a ladder filter structure in a variety of configurations. He also shows the use of inductors in series or in shunt with the crystals to widen the filter bandwidth. In Hansell’s patent the use of a bridge circuit is shown using all capacitors or a center-tapped transformer to balance out the crystal shunt capacitance. This is essentially the hybrid-lattice configuration which is commonly used in discrete crystal filters. He also proposed a method for widening the bandwidth by placing several crystals with slightly different frequencies in parallel. The challenge of providing filters with useful bandwidths was apparent from the earliest days and many techniques (usually unsuccessful, including Hansell’s) were attempted. In his patent Hansell makes the interesting observation that “The crystal filter has the advantage of being so sharply selective that the necessity for more than a single section probably will never arise.”
Ceramic Filtration
Locally manufactured ceramic filters have traditionally been used throughout the world to treat household water. Currently, the most widely implemented ceramic filter is the Potters for Peace design. The filter is flowerpot shaped, holds about 8-10 liters of water, and sits inside a plastic or ceramic receptacle. To use the ceramic filters, families fill the top receptacle or the ceramic filter itself with water, which flows through the ceramic filter or filters into a storage receptacle. The treated water is then accessed via a spigot embedded within the water storage receptacle. The filters are produced locally at ceramics facilities, and then impregnated with colloidal silver to ensure complete removal of bacteria in treated water and to prevent growth of bacteria within the filter itself. Numerous other locally-made and commercial ceramic filters are widely available in developed and developing countries. The filter is flowerpot shaped, holds about 8-10 liters of water, and sits inside a plastic or ceramic receptacle. To use the ceramic filters, families fill the top receptacle or the ceramic filter itself with water, which flows through the ceramic filter or filters into a storage receptacle. The treated water is then accessed via a spigot embedded within the water storage receptacle. The filters are produced locally at ceramics facilities, and then impregnated with colloidal silver to ensure complete removal of bacteria in treated water and to prevent growth of bacteria within the filter itself. Numerous other locally-made and commercial ceramic filters are widely available in developed and developing countries.
Lab Effectiveness, Field Effectiveness, and Health Impact
The effectiveness of ceramic filters at removing bacteria, viruses, and protozoa depends on the production quality of the ceramic filter. Most ceramic filters are effective at removing bacteria and the larger protozoans, but not at removing the viruses. Studies have shown adequate removal of bacterial pathogens in water filtered through high quality locally-produced or imported ceramic filters in developing countries. A 60-70% reduction in diarrheal disease incidence has been documented in users of these filters. Studies have also shown significant bacterial contamination when poor-quality locally produced filters are used, or when the receptacle is contaminated at the household level. Because there is no chlorine residual protection, it is important that users be trained to properly care for and maintain the ceramic filter and receptacle.
What Is a Ceramic Resonator?
A ceramic resonator is an electric component that exhibits a series resonant and a parallel resonant center frequency. It exhibits a piezoelectric characteristic that makes the ceramic material generate minute electrical energy when subjected to electromechanical expansion and compression. The resulting mechanical energy component produces the electric component and vice versa, and the result is a complex reactance that leads to resonance observed as the characteristic of having a center frequency. Materials such as lead zirconium titanate have a ceramic piezoelectric characteristic.
Oscillators are electronic circuits that generate periodic waveforms. The ceramic resonator may be used as a frequency reference in the electronic oscillator, wherein the accuracy of the resulting frequency is not as high as in the crystal oscillator. Error in frequency for the ceramic resonator circuit may be as high as 5%, while that for the crystal oscillator is less than 0.1%.
The ceramic resonator may also be used for intermediate frequency (IF) amplifier stages, which are found in heterodyne radio receivers that derive a common IF to receive a sub-band of frequencies. For instance, a radio receiver tuned to 1,000 kilohertz (kHz) or 1,000 cycles per second may generate a local oscillator frequency of 1,455 kHz so that the difference is 455 kHz, which is a typical IF frequency. To receive a 1,500 kHz signal, the local oscillator is tuned to 1,955 kHz and the resulting difference is still 455 kHz. This ceramic resonator is tuned or cut to resonate at around 455 kHz and will serve a sub-band like 550 to 1,600 kHz as in a typical amplitude modulation (AM) band.
A typical ceramic resonator has three terminals. The two main terminals are at each wide side of a thin ceramic material, while the middle terminal is usually connected to the thin side and may be grounded or used to tap signal into the rest of the oscillator circuit. There are, however, ceramic resonators as well as crystal resonators with only two terminals.
Amplifiers are the active parts of the oscillator. The ratio of the output voltage to the input voltage of an amplifier is known as the voltage gain, which is dependent on the frequency of interest. Very few amplifiers will maintain a constant gain over a wide range of frequency. When a ceramic resonator controls the oscillator frequency, the voltage gain at the ceramic resonator frequency has to be greater than 1. If the voltage gain is less than 1, the amplifier will not start oscillating.
In electronics, design amplifiers and oscillators have very common components. With design shortcomings, some amplifiers can be very close to oscillating. Meanwhile, some oscillators may just stop oscillating and behave like idle amplifiers. Ideally, amplifiers do not have output when there is no input signal.
|
|
|
Benefits of using a humidifier |
Posted by: D133H - 10-08-2021, 07:51 AM - Forum: FPS and Shooters
- No Replies
|
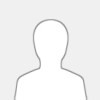 |
Benefits of using a humidifier
Benefits of using a humidifier
Humidifier adds moisture to the air, which can benefit people with respiratory symptoms or dry skin.
There are several ways to use humidifiers in the home or office, but there are also some risks.
In this article, learn about the benefits of humidifiers, how to use them correctly, and precautions to take.
Dryness and humidity
By adding moisture to the air, humidifiers may be beneficial for several medical conditions.
Dry air can cause moisture to evaporate from the skin and respiratory symptoms to worsen over time. Adding moisture to the air with a humidifier can counteract these problems.
Humidifiers can help people who experience:
dry skin
irritated eyes
dryness in the throat or airways
allergies
frequent coughs
bloody noses
sinus headaches
cracked lips
Five humidifier uses and their benefits
Some people experience respiratory symptoms in the summer months, when the weather is hot, and the air contains more allergens. Air conditioners and fans can circulate dry air through the room, and air conditioners remove any moisture from the air. A humidifier may be beneficial during this season.
However, people are more likely to benefit from a humidifier in the cold months, when cold air dries out the lungs, nose, and lips. Also, some types of central heating can dry out the air indoors.
Benefits of a humidifier may include:
1. Preventing influenza
Authors of one
studyTrusted Source
noted that humidifiers might reduce the risk of catching the flu. After adding the influenza virus to the air with a simulated cough, researchers found that humidity levels above 40 percent rapidly deactivated virus particles, making them much less likely to be infectious.
2. Making a cough more productive
Dry air can cause a person to have a dry, unproductive cough. Adding humidity to the air can get more moisture into the airways, which can make a cough more productive. A productive cough releases trapped or sticky phlegm.
3. Reducing snoring
Increasing the amount of moisture in the air can also reduce snoring. If the air is dry, a person’s airways are less likely to be sufficiently lubricated, which can make snoring worse.
Adding humidity to the air by running a humidifier at night may help to relieve some symptoms.
4. Keeping the skin and hair moist
Some people notice that their skin, lips, and hair become dry and fragile in the winter.
Many types of heating units pump hot, dry air through the house or office, which can make the skin dry, itchy, or flaky. Cold air outside can also dry out the skin.
Using a humidifier to add moisture to the indoor air may help to reduce the occurrence of dry, cracked skin.
5. Benefits for the home
Moisture from a humidifier can be helpful around the home. Any moisture-loving houseplants may become more vibrant, and wood floors or furniture may last longer. Humidity can also help to prevent wallpaper from cracking and static electricity from building up.
Humid air can also feel warmer than dry air, which could help a person to save money on utility bills in winter months.
Types of humidifiers
While most humidifiers have the same basic function, to add moisture to the air, many types are available:
Steam vaporizers: These use electricity to create steam, which cools before it leaves the unit. However, there is a risk of burning the skin, and people should avoid using steam vaporizers around children.
Ultrasonic humidifier: Instead of electricity, these units use vibrations to vaporize water.
Evaporators: These produce humidity by blowing air past evaporating water.
Impeller humidifiers: These are generally child-friendly and use rotating disks, rather than heat, to vaporize water.
Central humidifiers: A person connects one of these units to the central air conditioning in the home or office to add moisture to the entire space.
Sizes can vary. Console humidifiers are large enough to add moisture to an entire house or office, while personal humidifiers are portable and easy to carry.
What is an Industrial Humidifier?
An industrial humidifier is a system that is capable of providing adequate humidity levels in a manufacturing environment. High-speed production processes add to the heat load in a building, bringing down the humidity. This can lead to a dangerous buildup of static electricity in a plant where dust and other flammable materials may be in the air. Processes such as woodworking, printing, and electronic and microchip fabrication, — which involve gluing, coating, and bonding — benefit from humidity control. Energy efficiency is also a consideration with an industrial humidifier.
Related products include industrial steam humidifiers, as well as electric-powered and gas-fired models. Steam heat exchangers use a heat source for producing steam from tap water or pure water reserves. These are also designed to comply with indoor air quality requirements to ensure proper humidity levels along with clean air for workers.
Industrial humidifiers are also designed as fog systems that integrate with building automation systems. In this configuration, an industrial humidifier system can be integrated above the factory floor, with the moisture released via fog nozzles. This is a viable alternative to humidifying air traveling through ducts, because excessive heat loads can be managed at the source.
An industrial humidifier also can be a contamination control system. It can be capable of utilizing adiabatic humidification to control humidity and airborne particles, and reduce the buildup of electrostatic discharge that, when combined with particulates, can be a health hazard and a cause for major industrial accidents. Along with proper treatment of supply water, an industrial humidification system ensures a safe environment in which to work.
An industrial humidifier can be found in many manufacturing facilities. Plants that make electronic assemblies require humidification, because the air in buildings producing circuit boards and computer equipment must be free of particles. Semiconductor manufacturing is another major application, because integrated circuit printing requires tightly controlled temperatures, along with a relative humidity (RH) of around 35 percent to 45 percent with acceptable tolerances within a range of 1/2 percent to 5 percent RH.
What Does a Dehumidifier Do?
A dehumidifier is an appliance that takes moisture out of the air in your home.
If you or your family members have asthma or allergies, a dehumidifier might help relieve symptoms and make breathing easier.
This article will help you decide whether a dehumidifier is a worthwhile investment for your living space.
Dehumidifier uses and health benefits
You may remember the water cycle from elementary school science: evaporation, condensation, and precipitation. What you might not realize is that the water cycle is always taking place in the air you’re breathing, even when you’re spending time inside.
“Humidity” is a measure of water vapor in the air. Dehumidifiers remove or minimize this water vapor.
How a dehumidifier works
A dehumidifier works by drawing warm air currents into its coils via a fan. The warm air contracts as it’s fed through the refrigerated coils of the machine, and condensation is left inside the dehumidifier.
As this condensation collects, one droplet of water at a time, it falls into a storage tank attached to the dehumidifier. Cooler, drier air is then released back into your home through the other side of the machine.
Your dehumidifier should be able to bring the moisture in the air down to a relative humidity of 30 to 50 percent. Many dehumidifiers come with a meter that measures the relative humidity where it’s placed in your home, and you can set the humidity to the percentage you desire.
Application of Dehumidifiers for Various Industries
Food Industry:
Excess humidity causes condensation and a broad range of hygiene problems in the product. Be it powdered food, spices, processed meat, snack foods confectionery products or breweries, consistent and controlled moisture conditions are necessary. Using dry air from a Desiccant dehumidifier can help in controlling the moisture content, which leads to perfect coating and longer shelf life of the food products.
Lithium Batteries:
The primary requirement for manufacturing of lithium batteries is a dry room with very low humidity. Lithium is extremely sensitive to moisture; thus, high moisture content leads to a reduction in performance and life of the product. Industrial dehumidifier ensures that the processing areas have the required amount of moisture in the air which is less than 14gms of moisture per kg of dry air.
Pharmaceutical Industry:
During the processing stage, most of the medicines are in powdered form and are highly hygroscopic. Excess of moisture absorption leads to organic corrosion, biochemical reactions and micro-organism growth on the product. Dehumidifiers help in keeping the required humidity parameters for processing, drying, storing and transportation of medicines.
Cold Stores:
To prevent flowers, vegetables, fruits, milk and processed foods from deterioration they are cooled and stored in cold store under low moisture conditions. Since the cold stores experience the frequent movement of products, warm air with moisture from outside could enter the store. This results in ice and frost formation on the walls, floors and ceilings on the cold stores. Air curtain using Dehumidified air at the cold store doors helps in controlling the ingress of moisture laden entering the cold rooms.
Defense Industry:
Military equipment is highly prone to humidity damage when they are stored for long periods. Uncontrolled humidity causes corrosion and malfunctioning of equipment, fungal growth on maps, drawings and bacterial infection on rations. Storage rooms of standard equipment such as trucks, tanks, guns and ammunition require specific humidity levels and controlled temperature. Dehumidifiers help in preventing corrosion on the equipment by keeping humidity levels less than 35%.
Electronic and Semiconductors:
Components used in assembling or processing of semiconductors are hygroscopic and highly sensitive to excess humidity. Excess moisture results in corrosion of PCB, transistor failures, and condensation on integrated circuits. The RH in semiconductor manufacturing area must be 30% at 20oc. Industrial dehumidifiers also help in protecting the vacuum and EPI equipment.
Turbine Industry:
Moisture can corrode turbines, boilers, condensers and many other machines when they are kept for maintenance during the layup process. High humidity causes corrosion and rusting on the equipment leading to their malfunctioning. As the repair and downtime costs of these equipment are very high, moisture control becomes essential. Industrial dehumidifiers help in keeping moisture levels low during the storage of the product; thus, preventing corrosion.
Leather industry:
The Leather is a hygroscopic material; excess moisture leads to the growth of mold and mildew on leather. Without proper humidity control, leather loses its shine, produces the foul smell, loses its strength and starts decomposing. Relative humidity above 40% leads to micro-organism growth that results in decomposition of leather. Dehumidifiers help in providing controlled moisture conditions during the processing of leather products.
Ultrasonic Mist Maker
I needed a simple mist maker/humidifier for a project that I was working on. I found lots of ideas on the internet, but they all lacked in one area or another, so I decided to design one. The following lays out my easy-to-build ultrasonic mist maker. It works fine and is, by far, the easiest ultrasonic mist maker/humidifier that I’ve ever had to get going.
The misty head
In an ultrasonic mist maker/humidifier (also called an ultrasonic atomizer), a piezo atomizer disc/transducer (ceramic humidifier) works by transposing high-frequency sound waves into mechanical energy that is transferred into a liquid, creating standing waves. As the liquid exits the atomizing surface of the disc, it’s broken into a fine mist of uniform micron-sized droplets, so the key component required for this little project is a particular (20-mm, 113-kHz) ultrasonic atomizer disc/transducer (see below).
When buying the transducer, make sure that is has a 113-kHz (±3 kHz) resonance frequency — another popular transducer has a 1.65-MHz (±0.05 MHz) resonance frequency, which is not compatible with this project!
Circuit diagram of the transducer driver
Below is the circuit diagram of the final part of the project — the transducer driver. As shown in the circuit diagram, it’s a tricky oscillator design based on the ubiquitous tiny time chip NE555P (IC1) to generate proper drive pulse train for the atomizer transducer. In the circuit, the 5K multiturn trimpot (RP1) can be used to set the oscillator frequency to 113 kHz (±5 kHz) (TP1). Even though the ultrasonic mist maker device is configured to run on a single 5-Vdc to 12-Vdc input, this transducer driver needs a 20-Vdc to 26-Vdc (V_DRIVE) power supply channel in addition to a 5-V regulated DC supply rail. So a dedicated power supply circuitry will be introduced later to fulfill that crucial requirement.
|
|
|
|