Welcome, Guest |
You have to register before you can post on our site.
|
Online Users |
There are currently 115 online users. » 0 Member(s) | 114 Guest(s) Google
|
Latest Threads |
Dominica visa free countr...
Forum: Off Topic
Last Post: axied12
06-24-2025, 12:37 PM
» Replies: 0
» Views: 123
|
Advanced microneedling
Forum: Off Topic
Last Post: axied12
05-28-2025, 01:25 PM
» Replies: 0
» Views: 270
|
Caviar and cheese
Forum: Off Topic
Last Post: axied12
05-28-2025, 12:38 PM
» Replies: 0
» Views: 241
|
Top-rated countertop comp...
Forum: Off Topic
Last Post: axied12
05-04-2025, 06:42 AM
» Replies: 0
» Views: 385
|
Ryanair letenky levně do ...
Forum: Off Topic
Last Post: axied12
02-11-2025, 01:37 PM
» Replies: 0
» Views: 764
|
Trusted essay writing ser...
Forum: Off Topic
Last Post: axied12
01-30-2025, 08:16 AM
» Replies: 0
» Views: 701
|
Bootverkopers - actieve j...
Forum: Off Topic
Last Post: axied12
12-07-2024, 11:07 AM
» Replies: 0
» Views: 825
|
Services for individuals ...
Forum: Off Topic
Last Post: axied12
12-02-2024, 03:31 PM
» Replies: 0
» Views: 795
|
Used excavators
Forum: Off Topic
Last Post: axied12
11-13-2024, 09:22 AM
» Replies: 0
» Views: 749
|
Buy Higo Rocket in Dubai
Forum: Off Topic
Last Post: axied12
10-25-2024, 01:09 PM
» Replies: 0
» Views: 857
|
|
|
Special Issue Nanofiltration Membranes |
Posted by: A911H - 09-30-2021, 12:32 AM - Forum: Off Topic
- No Replies
|
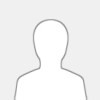 |
Special Issue Nanofiltration Membranes
Special Issue Nanofiltration Membranes
Nanofiltration (NF) is a de novo class of membrane filtrations with unique properties ranging from ultrafiltration to reverse osmosis. Thanks to their high removal performance, NF membranes have gained increasing attention from both academia and industry for various applications, especially in water and wastewater treatment and desalination. However, the NF process still requires further improvement in terms of selectivity, separation efficiency, membrane fabrication, operation requirements, and sustainability.
This Special Issue on “Nanofiltration Membranes: Recent Advances and Environmental Applications” of the Membranes seeks to include but is not limited to recent progress in emerging NF membranes fabrication and modification, polymeric and ceramic NF membrane, hybrid and composite NF membranes, organic solvent NF, positively charged NF membranes, NF module and process design, NF removal mechanisms, fouling mitigation strategies, new environmental applications of NF, and predictive modelling of NF membrane processes. Authors are invited to submit their latest original results as full papers or short communications. Furthermore, state-of-the-art and critical reviews and analysis papers are welcome.
Advantages of GRE pipes
Glass Reinforced Epoxy or GRE pipes are a valid alternative to carbon steel pipes especially for corrosive, aggressive and normal environments.
GRE pipe technology is based on the Discontinuous Filament Winding process using high strength fiberglass (E-glass) and amine cured epoxy resin as basic material. Numerically controlled machines manufacture the product on a mandrel according to the cross section filament winding process. The continuous glass fibers are helically wound at predetermined angles and bonded with the epoxy resin.
Lightweight and easy to handle and install GRE pipes have a smooth internal surface that reduces friction and enables a high pipe flow capacity. Low thermal conductivity of GRE pipes in comparison to steel (only 1% of steel values), minimizes the cost of insulation and the heat loss. Another major benefit of GRE pipes is that once installed they are virtually maintenance-free.
GRE pipe is well suited for environments where the corrosion resistance at competitive prices is required.
GRE pipes offer a unique combination of high mechanical, thermal and chemical resistance which is obtained by the selection of high performance components and a proper design of the structure. The inner liner, which is made by a resin rich layer reinforced with C-glass or synthetic veil, guarantees the pipe water tightness, its chemical and temperature resistance. The mechanical resistant layer is composed of successive layers of pre-stressed glass roving impregnated with epoxy resin and orientated with a precise, predetermined angle selected in order to achieve the properties required. The resin and the hardener system are selected with the consideration of the combination of properties required from the finished product. The glass reinforcement in the form of continuous roving is chosen base on its compatibility with epoxy resin. It is applied on the rotating mandrel following the hoop (radial) winding pattern combined with a helical winding pattern at an angle ranging from 45?° to 90?°.
Glass tape or unidirectional reinforcements can be used to obtain local reinforcement. An external resin coating reinforced with a synthetic veil adds a finish to the pipe. Should weathering be a problem a UV inhibitor will be added to the coating.
GRE pipes are generally manufactured with an integral joint, which means that the socket (for bonding, lock, or thread) is produced simultaneously with the pipe body by winding on a specially designed metallic mould fixed at one end of the mandrel. The pipes are wound on precisely machined steel mandrels, the mandrel is extracted only when the pipe is cured.
ADVANTAGES
Wide range of diameters from 1 " (25mm) up to and including 54 " (1400 mm).
Standard lengths of 12 m.
Adhesive, locked bell/spigot, lamination and flanged jointing systems.
Anti corrosion system
Long life (50 years) + zero maintenance = low life cycle cost.
UV Resistant - can be safely installed above-ground.
Conductive pipe and fittings are available.
Fast, low cost assembly due to light weight and simple jointing techniques.
Lighter support needed for above-ground systems.
Low Hazen williams number due to the smoother internal surface.
GENERAL CHARACTERISTICS OF THE PIPING
Excellent resistance to corrosion and long service life.
Superior Flow characteristics.
Low paraffin's and solid build-up.
Installation cost much lower than steel.
Installation unaffected by weather conditions.
The pipes weight about ?? the weight of steel.
Fast and reliable installation. API 8 RD EUE Threads and 4 TPI available.
Operational pressures in line pipe, tubing and casing up to 3500 PSI.
Exceptional performance against pressures and high capacity load.
USES OF GRE
Transport lines.
Fire Fighting networks.
Line for chemical disposal.
Injections lines.
Lines for gathering and gas transportation.
Line for universal insolutions and water injection in mines.
Acid transportation.
Line for recirculation.
Production wells, Tubing and casing.
Line for chemical transportation.
Water injection, tubing and casing.
Line for disposal formation waters.
The Early Rotor Blades
Early helicopters like the famous Bell 47 came with main rotor blades made of wood. The inherent characteristic of wood being strong and flexible provided the perfect material for early rotor blade designs.
There were problems however as wood can easily be damaged by woodpeckers, dust and stones, and even rain causing the blade to swell leading to severe vibrations from an out of balance rotor system.
As the realization of the versatility of the helicopter become more popular, the design and evolution of the airframe and the rotor blades began to move forward.
Materials Development
A rotor blade needs to be strong but also very flexible. You have probably seen that when a helicopter is parked the main rotor blades droop down, but in flight centrifugal force keeps them flat. Not only that, but the blades also flex in flight, especially when affected by turbulence and they need to be able to withstand these loads as well as keeping the helicopter in the air.
To be able to withstand these stresses placed on the blades they need to be designed to be strong in certain areas, but yet flexible in others. Although wood is great at doing this they are limited to the weight they can lift and the speed at which the tips can rotate. This is where new materials were needed.
One of the first advances into rotor blade design was the skinning of the blade’s leading edge with corrosion-resistant steel to aid in erosion control, especially towards the tips of the rotor blade where it is moving the fastest.
The Hiller UH -12B was one of these aircraft to adopt such a design on its blades during the 1950’s.
Metals
As testing and development into metals really began to take stride it became inevitable that rotor blades would find themselves made of them.
As metals solved some of the problems presented in wooden blades, they presented their own. Constant flexing of certain metals over time can cause it to break. Think of what happens to a paperclip when you twist it back and forth. The other problem with metal is that a crack can rapidly spread causing catastrophic failure – Which is not generally welcomed by pilots!
This was one of the first reasons that rotor blades started to have a time limit on their use. Until this point, wooden blades were considered to last indefinitely!
Honeycombs
The addition of honeycomb technology into rotor blades really helped to improve the design and lifespan of a rotor blade. Used in conjunction with other metals, rotor blades can be produced strong, flexible, light, and cheaper than their advanced composite younger brothers.
To ensure the long-term safe operation of the FRP membrane housing, please observe the following regulations and recommendations:
1. The shrinkage expansion rate of the FRP membrane housing is relatively small. Please observe the rated design pressure index during use. Operate it within the allowable pressure range.Long time overpressure operaton is strictly forbidden!
2. The service temperature of FRP membrane housing is generally from ﹣7 ℃ to 49 ℃. It is strictly forbidden to work under the condition beyond this temperature range.
3. The back pressure of the two-end permeate water outlet shall not exceed 125 PSI.
4. Strictly abide by the pressure level of each medium, such as clean water, sewage, seawater, etc. If you use water with special media, please contact our company in advance to avoid accidents.
5. When the RO system is working or there is pressure in the frp membrane housing, it is strictly prohibited to knock, disassemble or move the membrane housings. The surrounding vibration source environment must be strictly controlled.
6. It is strictly forbiden to apply pressure or gravity to the upper part of the membrane shell, or to its corresponding accessories.
7. In order to ensure the inner surface of the fiberglass membrane housing clean, manufacturer use a neutral cleaning solution to clean. It is strictly forbidden to use concentrated hydrochloric acid, concentrated sulfuric acid, etc. as cleaning fluid.
The above is all the content that the editor introduces to everyone, we need to maintain and clean the FRP membrane housings regularly during use.
|
|
|
Key Cabinet and Locker Management |
Posted by: A911H - 09-30-2021, 12:31 AM - Forum: Off Topic
- No Replies
|
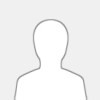 |
Key Cabinet and Locker Management
Key Cabinet and Locker Management
PACOM Unison is a market-leading platform with the ability to link with ASSA Abloy Traka intelligent key management system and lockers solutions to manage and control access to a company’s most important assets. When a conventional key is stolen, mislaid, or accidentally taken home, security is compromised and the organization is suddenly vulnerable. Even if nothing is stolen, and no damage is done, the cost and inconvenience of fitting new locks and the impact on productivity can be significant.
Traka can significantly reduce the cost of losses through accidental damage, theft, personal injury and downtime.
The integration between Unison and ASSA Abloy Traka allows for extensive key management at facilities such as data centers, healthcare facilities, universities, municipalities, governments and other similar applications.
The user presents an access card to a reader to open the key cabinet and access a selected key. All actions and events are logged in Unison and can be accessed at any time. Unison can be configured to activate an alarm if a key is not returned to the cabinet on time. Unison can also be programmed to activate an event once a key is borrowed or is returned late.
Unison’s integration with Traka supports automatic upload of configuration making it efficient to upload data to user tags or update time schedules.
Deister proxSafe Integration
Deister proxSafe is a key and asset management system used to effectively control and monitor valuable assets using high security, electronically controlled cabinets.
Monitoring who, when and where keys and assets are accessed adds confidence and peace of mind with control and immediate response to alerts that can be automatically raised when alarm conditions exist.
Integrating Deister proxSafe with the PACOM Unison system allows Unison operators to respond to alarms, perform actions and monitor the status of the key management system as part of their standard Unison security management solution.
Linking Unison cardholder data and proxSafe key users provide the ability to control access to individual keys using existing cardholder data and the automatic sharing of data between Unison and proxSafe ensures that secure access to critical assets is maintained at all times.
The electronically controlled key cabinets can be efficiently monitored from the convenience of the Unison client and operators can see who has accessed keys and assets at any time. More than 50 different events can be displayed as alarms in real-time, enabling Unison operators to take timely action.
Benefits
The aim of this article is inform you on how to implement proper key management and to answer 3 important questions regarding centralized and automated key management:
What is Centralized Key Management?
How can a centralized system help meet regulatory compliance?
How can automation further improve the life cycle management of keys?
Distributed key management systems make it very difficult to manage cryptographic keys. As your company grows, so does your data and the number of encryption keys you must manage to maintain data security.
By switching to a centralized key management system, you will remove these challenges, increase life cycle efficiency, and help your IT departments develop proper key management policies that scale with your organization.
First, let’s take a look at what it means to practice proper key management.
Proper management of cryptographic keys in hardware security modules.
Proper key management is an essential process of data security within any organization handling sensitive information. To avoid risks and efficiently scale operations, an organization should centralize its large intelligent key management system. This will result in good key generation and ensure key integrity within the system.
How to implement proper centralized key management policies and procedures:
Develop secure data policies within your organization
Define the processes necessary to implement those policies
Automate those processes for your hardware security modules with a dedicated KMS.
What is a Centralized Key Management System?
A centralized KMS offers more efficiency as opposed to a distributed or application-specific KMS. They are called centralized because they use a single point to secure key management, policies and access audit logs. To boot, your organization can develop uniform key management procedures across all of your departments.
Some benefits of a centralized key management system:
Provides tamper evident records for proof of compliance
Streamlines key management processes and reduces costs
Automatic key updates and distribution to any end-point
Reduces the risk of human errors with user & admin permissions
Dual control with asynchronous workflows
System-wide key control manages any key type and format
Offers High availability and scalability
Reduces costs with automation
Simple backup and recovery
Another key advantage of implementing a centralized system — it eases regulatory compliance by providing a complete record of every time a sensitive operation or key activity is administered from the server.
How can a centralized system help meet regulatory compliance?
Regulation is a topic brought up in any serious discussion regarding data security. Anytime sensitive information storage is involved, you must follow the standard security rules required by an exhaustive list of compliance authorities. The particular regulations/security standards relevant to encryption and key management depend on the type of information that is being stored or processed and what sector the business operates within. In order to pass compliance testing and audits, you need to keep your data security procedures documented and updated. For most companies, compliance can be a major hassle.
Here are some of the standards to consider for HSMs:
Federal Information Processing Standard (FIPS)
Common Criteria Evaluation Assurance Levels (CC EAL)
Payment Card Industry - Data Security Standards (PCI DSS)
Lite series key management system is typically developed with certain sectors/industries in mind, and therefore it is advisable to choose a centralized KMS that has a proven track record for supporting the security/regulatory standards of the particular sector that is relevant to the business.
A centralized KMS can help passing compliance audits by enforcing the security policies and automatic logging of all security sensitive operations. A unified overview and central control of all the essential logs makes demonstrating compliance much easier and quicker than auditing various disparate key management systems.
Compliance is non-negotiable. It is equally important for the system to support the complete life-cycle of cryptographic keys. Automating key management further reduces the need for time-consuming, manual key functions.
A system that puts high value keys under management needs to centralize, automate and optimize the encryption key management process through the entire life cycle. Proper management reduces overhead costs, ensures generated key quality, and protects these keys in storage and in transit.
WHAT IS A GUARD TOUR SYSTEM
A guard tour system is a system used to help companies and organizations to organize, log and execute guard tours and patrols in their assets ensuring that the officers will accomplish their tasks within the predefined time intervals. There is a wide variety of guard tour systems, which can be divided in two major categories: Wand guard tour systems based on handheld devices and cloud guard tour systems based on modern mobile and cloud technology.
Standalone guard tour system provides a means to check and record the time that a guard executes his guard tour by scanning specific checkpoints assigned on the area he patrols. Checkpoints are placed in certain points either on buildings or on other locations of a site or remote area and help the managing staff to identify each different location and each portion of a specific territory. The on-site officers can scan checkpoints, send SOS alerts, track and record events and conduct and send reports to the managing staff or the clients, even in real-time.
WHICH INDUSTRIES NEED A GUARD TOUR SYSTEM
The implementation of a guard tour system will help companies to monitor their officers accurately in time and manage their assets more effectively, upgrading their security services. So, many different industries can take advantage of the use of a guard tour system:
- Security companies, to monitor officers / Lone Workers, manage guard tours and conduct reports.
- Educational Institutes, to increase the safety of their students
- Real Estate organizations, to manage their buildings and protect them from damage
- Public transportation services, to direct activities and manage daily incidents
- Finance Institutes, to be safe from external threats
- Warehouse departments, to assure the security status of their merchandise
- Manufacturing facilities, to protect from damages and record incidents in every aspect of manufacture process
- Cleaning and maintenance services, to manage their installations and workers
|
|
|
Sports Wear: Between Fashion, Innovation and Sustainability |
Posted by: A911H - 09-30-2021, 12:30 AM - Forum: Off Topic
- No Replies
|
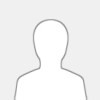 |
Sports Wear: Between Fashion, Innovation and Sustainability
Sports Wear: Between Fashion, Innovation and Sustainability
Sport is an important part of many people’s lives—as both recreation and entertainment. It is also a sizeable industry with political and economic ramifications in today’s world. Within the last half-century or so, sports wear has become a driving force for new trends in fashion and for textile innovation. This special issue of Fashion Practice was inspired by the “Spandex to Sportstech—Fashion and Innovation in Sportswear” conference, organized in 2011 by guest editor Mette Bielefeldt Bruun at the Danish National Research Foundation’s Centre for Textile Research at the University of Copenhagen.
The stated purpose of Fashion Practice is to provide a site for multidisciplinary treatments of the practices of fashion. “Spandex to Sportstech” was designed as a cross-disciplinary forum for renewed consideration of functional, social, aesthetic and environmental issues connected with sportswear, and some of the papers presented here are rooted in original conference contributions. This journal issue is truly cross-disciplinary, beginning with fashion history, represented by Michael A. Langkj?r with “Urban Fitness, Gendered Practices, and Fine Art: The Significance of Antonio Lopez’s Sporty Styling of Fashion” and moving on to the sportswear industry itself with its brands and markets, represented by Kristine Holm-Jensen with “Specialized in Sportswear: Transformations of the Generic Knitwear Industry in Post-War Denmark.” Several articles then consider fiber and textile technologies and their design applications. Jane McCann leads this group with her “Sportswear Design for the Active Ageing.” McCann is followed by Deborah A. Christel and Nicole H. O’Donnell with “Assessment of Women’s Plus-Size Swimwear for Industry Applications.” Alicia Potuck, Sarah Meyers, Ariana Levitt, Erik Beaudette, Hong Xiao, C. C. Chu, and Huiju Park complete the group with their “Development of Thermochromic Pigment Based Sportswear for Detection of Physical Exhaustion.” In “What’s the Problem? Odor-control and the Smell of Sweat in Sportswear,” Ingun Grimstad Klepp, Madeline Buck, Kirsi Laitala and Marit Kjeldsberg look at how fiber technologies connect with our social values associated with body odor and its suppression; in doing so, Klepp et al. also mention the issue of sustainability. A forthright appraisal of the problem of sustainability within the sportswear industry is given by an industry representative to Lena Erdnü? in “A Perspective on Sustainability Initiatives of a Swedish Outdoor Brand: An Interview with Lennart Ekberg from Hagl?fs.” Finally, Lauren Downing Peters has contributed a review of the Museum of the City of New York’s 2013 exhibition: “Stephen Burrows: When Fashion Danced.”
A 'tool to empower': The evolution of women's sportswear
Before the advent of designer activewear, women's sports wear ranked low on the list of fashion priorities. But a new exhibition demonstrates that sporting attire has long been a valuable tool for self-expression and an important path towards greater liberation."Sporting Fashion: Outdoor Girls 1800 to 1960" includes about 65 ensembles from mainland Europe, the UK, and the US, ranging from Victorian hunting dresses and couture-level leisure wear to tailor-made team uniforms. Organized by the FIDM Museum at the Fashion Institute of Design & Merchandising in Los Angeles and the American Federation of Arts, the show opens at the Frick Art Museum in Pittsburgh on July 3, before touring nationwide through 2024.
Design innovation
Garments from the early 1800s are tailored to strolling in parks, gardening, and ice skating -- easy, acceptable activities for women propelled outside by an interest in horticulture, health and fresh air.
The idea of a woman exerting herself was still taboo: In 1806, an article in the popular British magazine La Belle Assemblée, excerpted in the show's comprehensive catalog, warned that, "the constitution of women is adapted only to moderate exercise; their feeble arms cannot perform work too laborious and too long continued, and the graces cannot be reconciled with fatigue and sun-burning."
That's the outlook for men's sports wear as the fall wholesale buying season gets under way this week. And while merchants and manufacturers have been expressing their traditional optimism as the new lines open, the unknown factors resulting from President Nixon's economic stabilization program have brought a modicum of caution to the trade.
Consumer spending for men's and boys’ apparel amounted to approximately $16‐billion last year, with sportswear a major but undefinable percentage of the total. What is even more significant, however, is that while production of a number of other categories of men's wear, such as suits and dress shirts, declined during the year, sportswear manufacturing was greater in 1971 than ever before.
And while statistics on the sportswear category are not collected by any government agency or trade association, conversations with retailers last week indicated that 1971's volume advances would he continued at the same rapid pace in 1972.
WHY ARE SPORTS BRAS IMPORTANT
Physical activity makes breasts bounce up, down and even in a figure-eight. Continuous and repetitive movements can result in soreness, pain and sagging.
Women's sports bra is made to reduce this movement. Breasts have no muscle, yet without proper support, the skin and Cooper's ligaments (ligaments near the breast which give them their size and shape) can break down and cause sagging. Once your Cooper's ligaments stretch out, they do not bounce back.
It doesn't matter what size breasts you have, everyone experiences bouncing during physical activity. Therefore, every woman, no matter what size she is, should wear a sports bra while running or exercising.
TYPES OF SPORTS BRAS
Compression bras work the way they sound, by compressing breasts against the chest to restrict movement.
Encapsulation bras have individual cups. Each cup surrounds and supports each breast. Most regular bras are encapsulation bras and have no compression.
Combination compression/encapsulation bras combine compression with individual cups and offer the most support.
Bra tanks, also known as shimmels, are tank tops with a built-in shelf bra. These are okay for low impact activities, but not for running.
Finally, there are differences in straps. Spaghetti straps provide less support than wider straps. Racer-back straps are more supportive than both spaghetti and scoop back.
FITTING A SPORTS BRA
You want a sports bra that fits well, both in the band and cups. Overall, your sports bra should feel a bit tighter than a regular bra, however, you should be able to breathe deeply and comfortably. Hook it in the middle and take some deep breaths. Is this comfortable? Good. It should be.
The band shouldn't move. It should fit snugly and comfortably. Raise your hands above your head. Did the elastic band move? If it crept up your rib cage, try a smaller band. If the bra has straps, try adjusting them.
Your breasts shouldn't bulge, pay close attention to any bulging at the top or by the underarm. Furthermore, the cups shouldn't have any wrinkles or gaps. If the cup fabric is wrinkled, try a smaller size.
Make sure there is nothing rubbing or chafing around the armholes, straps, seams, hooks, clasps or anything else. Many sports bras offer adjustable straps. Adjust them to feel supportive, yet not uncomfortable. Furthermore, make sure the straps aren't digging into your shoulders.
Underwires are supposed to sit flat on your ribs, not on your breasts. The front (between the wire) should be against your chest bone.
Luckily, most newer sports bras use high-tech fabrics, including moisture wicking. This can improve breathability and help remove excess moisture from sweat which can cause chafing. Cotton bras will stay wet, this can lead to uncomfortable skin irritations.
For the last step, jump up and down, jog in place, do jumping jacks. If it feels supportive, you're set! If not, keep looking.
How Sportswear Took Over Your Wardrobe
“Sportswear as casualwear is essentially a preppy invention – the carryover from hearty WASP athletic pursuits which gave us the likes of the sweatshirt, sweatpants and letterman jacket,” says Josh Sims, author of books such as Men of Style. “Sportswear was appreciated for being tough and practical.”
Like military uniform, that other stalwart of menswear, mens sportswear set has long been valued for the rugged characteristics it both possesses in itself and indicates in its wearer. And in sport, like war, competition results in game-changing technological breakthroughs. What we wear on the fields of battle and play has advanced more dramatically than what we wear elsewhere. If sportswear is at the cutting edge of fashion right now, that’s because – in technical terms – it always has been.
The current, unprecedented sportswear boom though can also be seen as a pendulum swing away from the hashtag-menswear sartorialism that followed the economic downturn and increased competition for jobs – coinciding with the 2007 airing of Mad Men. As employment rose again, so did jobs that didn’t impose traditional dress codes and a social media-fuelled emphasis on individual creativity.Then there’s the swelling fashionability of fitness, which has given us a legitimate excuse to wear sportswear outside the gym beyond comfort and sheer laziness. Instead of spending valuable time fastidiously parting our hair and folding our pocket squares, we’re throwing on hoodies and baseball caps. And if you’re running around town all day, it makes sense to wear shoes designed specifically for marathons.
It’s arguably the luxury sector that’s setting the pace. Streetwear designers like Demna Gvasalia at Balenciaga and Virgil Abloh at Louis Vuitton are running the show(s), elevating previously utilitarian sportswear to the very height of fashion. T-shirts, down jackets and sneakers, which grew by 25%, 15% and 10% respectively, were “standout categories” in the 2017 Bain Luxury Study.
With its links to skateboarding, surfing and other sports, you could argue that streetwear – whatever that loaded term means – essentially is sportswear. “I’m not sure streetwear is the dominant mode, if you’re talking urban, hip-hop-driven streetwear,” contends Sims. “It’s sportswear with graphics, in effect.
“There’s not much original design in streetwear – unlike sportswear, then and now – and what there is tends to be driven by – ta-da – sport.”
|
|
|
Xylitol Research and Evidence |
Posted by: A911H - 09-30-2021, 12:28 AM - Forum: Off Topic
- No Replies
|
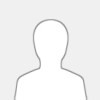 |
Xylitol Research and Evidence
Xylitol Research and Evidence
Xylitol is a non-sugar sweetener extracted from the birch tree. It is a five-carbon polyol that has effectively demonstrated itself to be cariogenic, by its action of neutralizing plaque acidity on teeth and repairing tooth enamel. Hence, it is also called the “magic bullet.”
The major production of xylitol goes to the pharmaceutical and oral hygiene industries and to confectionary manufacturers. It has 30% less calories compared to table sugar (calorific value of xylitol is 2.4 kcal/g, while that of sugar is 4 kcal/g) and is used in different food products for children like chewing gum, candies, gelatin, and in lozenges, toothpaste, and mouth rinses.
Xylitol and Dental Caries
Clinical trials on xylitol show that it plays a major role in prevention of dental caries in babies and teenaged children and in the fetus through the mother. Use of xylitol chewing gum is directly related to reduction of dental caries. Moreover, xylitol also reduces the s. mutans transmission from mother to infant.
Another research on children has found that xylitol candy, pops, ice, gums, puddings, and cookie help in arresting dental caries. Follow-up studies five years later showed that xylitol gum resulted in reduction of caries by 59% against no gum use.
Trials conducted in Finland, a major producer of xylitol, proved that children of xylitol-treated mothers’ had lower levels of s. mutans than those treated with fluoride varnish or chlorhexidine.
Other Impacts of Xylitol
Accumulation of excessive xylitol in the intestine leads to retention of water, which results in diarrhea. Consumption of excessive volumes of xylitol can lead to side effects such as gas and bloating. Xylitol which remains unabsorbed is eliminated after being broken into carbon dioxide. A report published by the European Union’s Scientific Committee on Food in 1985 stated that consuming 50 g of xylitol per day can lead to diarrhea. The Committee also affirmed that tabletop sweeteners that contain xylitol must be highlighted with a warning saying: “Too much of consumption may lead to laxative effects.”
The impact of xylitol is much less on the blood sugar levels compared with natural sugar, because of the gradual absorption rate of xylitol. This fact was approved in a xylitol review by the European Food Safety Authority (EFSA). This indicates that xylitol could help people with disrupted tolerance of glucose, a leading risk factor for cardiovascular disease and diabetes.
Health benefits and risks of chocolate
Chocolate is made from tropical Theobroma cacao tree seeds. Its earliest use dates back to the Olmec civilization in Mesoamerica.
After the European discovery of the Americas, chocolate became very popular in the wider world, and its demand exploded.
Chocolate has since become a popular food product that millions enjoy every day, thanks to its unique, rich, and sweet taste.
Fast facts on chocolate
Chocolate consumption has long been associated with conditions such as diabetes, coronary heart disease, and hypertension.
Chocolate is believed to contain high levels of antioxidants.
Some studies have suggested chocolate could lower cholesterol levels and prevent memory decline.
Chocolate contains a large number of calories.
People who are seeking to lose or maintain weight should eat chocolate only in moderation.
History of Candy
Candy is made by dissolving sugar in water or milk to form syrup. The final texture of candy depends on the different levels of temperatures and sugar concentrations. Hot temperatures make hard candy, medium heat make soft candy and cool temperatures make chewy candy. The English word ''candy'' is in use since the late 13th century and it derives from Arabic qandi, meaning ''made of sugar''.
Honey has been a favorite sweet treat throughout recorded history and is even mentioned in the Bible. The ancient Egyptians, Arabs and Chinese candied fruits and nuts in honey which was an early form of candy. One of the oldest hard candies is barley sugar which was made with barley grains. The Mayans and the Aztecs both prized the cocoa bean, and they were the first to drink chocolate. In 1519, Spanish explorers in Mexico discovered the cacao tree, and brought it to Europe. People in England and in America ate boiled sugar candy in the 17th century.
Sour candy trends
Sour candy has captured the attention and taste buds of consumers who look for confectionery experiences outside of the standard of sweet, says Steve Schuster, president of Wisconsin-based Schuster Products, which makes a line of sour products called Face Twisters.
“It is extreme, and people like to push their sensation of taste,” he said. “They are now accustomed to this taste sensation and seek it because it moves beyond the norm.”
Jenny Doan, director of marketing for Warheads maker Impact Confections, agreed. She pointed to consumers’ palates becoming increasingly daring, especially as consumers experience more global cuisine.
“Globalization has exposed consumers to more sour foods across many categories — examples include Greek yogurt, fermented Korean kimchi, Chinese sour plums, etc.” she said. “Also food preparation techniques such as fermentation and pickling are gaining in popularity and spurring development for more sour foods and beverages.”
And the products in development come from several confectionery categories, including chewing gum, hard candy and chewy candy. Chewy candy also has experienced steady growth over the last few years. IRI, a Chicago-based research firm, reported the $3.73 billion non-chocolate chewy category grew by 3 percent in the year ending Feb. 24, 2019.
Of the Top 20 non-chocolate chewy candy brands IRI tracks, a quarter of them are positioned as sour candy, and at least another quarter have sour line extensions. Mondelez International’s Sour Patch Kids pulled in just over $197 million in the reporting period, while Trolli Sour Brite Crawlers generated $133.6 million.
The Untold Truth Of Gummy Bears
There are the people who love to munch on chocolate bars, from Butterfingers to Snickers, indulging in the perfect combination of sweet and salty. And then there are the candy lovers who are obsessed with anything chewy, gooey, and gummy. Gummy candies only seem to be rising in popularity, and really, there's a gummy candy in pretty much every shape out there at this point.
But despite the introduction of gummy candies like frogs, butterflies, and even mini soda bottles, gummy bears will forever be one of the most iconic gummy candies we turn to.
But what's the story behind these little gummy bears? How did they get their start, and what's in them that makes them so perfectly chewy? They're a ridiculously satisfying sweet when you're trying to curb a craving, but as it turns out, there's a lot more to their story than meets the eye. We decided to grab a handful and dig a little deeper. This is the untold truth of gummy bears.
The History of Lollipop Candy
The first incarnation of the lollipop candy was probably created by cave people thousands of years ago who collected honey from beehives with a stick. Not wanting to waste the sweet nectar, they most likely licked the stick, thus inventing the world’s first lollipop. Good for them (good for us). Archaeologists believe that ancient Chinese, Arabs, and Egyptians all produced fruit and nut confections that they "candied" in honey, which serves as a preservative, and inserted sticks into to make easier to eat.If the 17th Century English version doesn’t count as the first modern lollipop, you could look to the Civil War era for another early forerunner, when hard candy was put on the tips of pencils for children. The early 20th Century was the era of automation, which is when the birth of the lollipop as we now know it begins in earnest, but there are still discrepancies as to who is the true creator.
What Is Chewing Gum?
Chewing gum is a soft, rubbery substance that’s designed to be chewed but not swallowed.
Recipes can vary between brands, but all chewing gums have the following basic ingredients:
Gum: The non-digestible, rubbery base used to give gum its chewy quality.
Resin: Usually added to strengthen gum and hold it together.
Fillers: Fillers, such as calcium carbonate or talc, are used to give gum texture.
Preservatives: These are added to extend shelf life. The most popular choice is an organic compound called butylated hydroxytoluene (BHT).
Softeners: These are used to retain moisture and prevent the gum from hardening. They can include waxes like paraffin or vegetable oils.
Sweeteners: Popular ones include cane sugar, beet sugar and corn syrup. Sugar-free gums use sugar alcohols like xylitol or artificial sweeteners like aspartame.
Flavorings: Added to give a desired flavor. They can be natural or synthetic.
Candy
candy, also called confectionery, sweet food product, the main constituent of which generally is sugar. The application of the terms candy and confectionery varies among English-speaking countries. In the United States candy refers to both chocolate products and sugar-based confections; elsewhere “chocolate confectionery” refers to chocolates, “sugar confectionery” to the various sugar-based products, and “flour confectionery” to products such as cakes and pastries. This article is primarily concerned with sugar confectionery. Other types of confections are discussed in the articles baking and cocoa.
|
|
|
The Importance Of Bandages And Emergency Pressure Dressings |
Posted by: P890J - 09-29-2021, 01:37 AM - Forum: FPS and Shooters
- No Replies
|
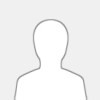 |
The Importance Of Bandages And Emergency Pressure Dressings
The Importance Of Bandages And Emergency Pressure Dressings
Shallow cuts, scrapes, and abrasions may be minor in the realm of workplace injuries, but they should be tended to immediately. A well-stocked first aid kit is important to have on hand so that workers can treat their wounds in a timely manner. They also help ensure that minor injuries do not become infected. Employers should be sure to make first aid kits available at any workplace.
Most minor injuries only require an adhesive bandage, such as a Band-Aid, or a small amount of gauze and tape. Bandages come in many varieties, and the appropriate should be used depending on the nature of the wound and the environment where a staff member works. There are waterproof adhesive bandages, ones made from flexible woven fabric, sheer strips, and heavyweight bandages for maximum strength that will not tear.
Larger wounds that can't be treated with a bandage and need more absorbency require an emergency pressure dressing. This type of first aid product is made from high-absorbency fabric or gauze. It should be applied with a great deal of pressure and wrapped tightly with a bandage roll.
In addition to emergency pressure dressings, some cuts and lacerations can be treated with alternative supplies. Steri-Strips and butterfly bandages are very small pieces of medical tape that can be used to bring the edges of a wound together to keep it closed and help reduce bleeding.
Severe wounds require medical attention. A doctor or medial professional should be called if:
? The edges of the wound are jagged
? The wound is on the face
? The edges of the wound gape open
? There is dirt in the wound that won't wash or rinse out
? The wound is draining pus
? The wound is tender and inflamed
? The area around the wound has gone numb
? Red streaks are forming near the wound
? Bleeding is profuse and won't stop in 20 minutes
For wounds that can be treated on-site, keeping first aid supplies in one central location, or multiple locations in larger facilities, is the basis for an effective and useful first aid program. Workers should be trained to know where these items are kept so that if an injury occurs, they will be able to quickly find and properly use bandages, Band-Aids, emergency pressure dressings, Steri-Strips, butterfly bandages, and other items. This knowledge, as well as the proper protocol for severe wounds, is essential to maintaining a sound and safe workplace.
When to Use an Elastic Bandage
ELASTIC BANDAGES FOR COMPRESSION AND SUPPORT AFTER AN INJURY
Joint injuries can often be initially treated with an elastic bandage for compression and support. But there are many reasons and ways to use an elastic bandage after an injury, and times when one shouldn’t be used at all. Here are some tips about when and how to use an elastic bandage.
ELASTIC BANDAGES ARE MULTITASKERS
When used immediately after injury, an elastic bandage can serve many functions:
- Control swelling around an injured joint
- Hold an ice pack in place
- Secure a splint after a fracture or severe sprain
- Keep other bandages secure and protected
HOW TO USE AN ELASTIC BANDAGE THE RIGHT WAY
- Elastic bandages should not be used over an open wound. Clean and dress the wound before applying any type of wrap, splint, or other support. Serious wounds need professional medical attention.
- Don’t wrap too tightly. A bandage that’s too tight can cut off circulation completely. Swelling at either end of the bandage, numbness or tingling, or discoloration means the bandage is too tight and needs to be adjusted.
- Leave the fingers and toes unwrapped, exposed, and free to move. This also helps you stay alert to any changes in the injured area like redness or increased swelling, which should be examined by a doctor.
- Adjust the bandage throughout the day. Unwrap the injured area, reapply the bandage, and secure with clips or tape, taking care that there aren’t any wrinkles or twists in the bandage as you wrap. A smooth wrap applies even pressure to the injured area.
KNOW WHEN TO STOP USING AN ELASTIC BANDAGE
The pain and swelling associated with a sprain can mask more serious underlying injuries, so know when to get more help.
- If swelling and pain gets worse, it’s time to seek professional treatment.
- If, after removing the bandage, the injured area still feels numb or tingles, see your doctor.
- If a fracture on a ligament sprain is suspected, an X-ray or MRI will allow your doctor to prescribe the right treatment for your injury
Six Good Reasons to Use Cohesive Bandage as a Strapping Tape
Cohesive bandage is one of the most useful strapping tapes for sport. It is widely used in other countries, but is less well-known here in the UK where adhesive tapes like EAB or zinc oxide tape are more popular. This is a shame, because cohesive bandage is actually the best choice for many touchline tape jobs. Here are six reasons why you should include cohesive bandage in your taping armoury…
1. Cohesive bandage does not stick to the skin
This might sound counter-intuitive; why would you want a strapping tape that doesn’t stick? Here’s the good part: cohesive bandage does not stick to the skin but it DOES stick to itself. When you wrap cohesive bandage over itself, it firmly coheres together (hence the name.) This makes it handy for any tape job that involves wrapping tape around a limb – i.e. most of the tape jobs you will ever need to perform on the touchline or in the changing room. And because it contains no adhesive, it will not inflict any damage to the skin or hair. One of our Rugby club customers who always buys cohesive bandage instead of adhesive tape puts it like this: ‘The lads don’t like to be waxed.’
2. It is very stretchy
Cohesive bandage stretches a lot – up to double its unstretched length. This allows you great flexibility to choose a level of compression to fit the situation. For instance, you could wrap it on with almost no stretch to give light support to a finger bend injury, or stretch it very tightly to provide heavy compression to a severely bleeding wound.
3. It offers variable levels of support
Cohesive bandage offers a range of support levels for weak or injured joints – from light to quite firm – depending on how many layers of tape you wrap on. For instance, when wrapping a sprained ankle, you would avoid applying the cohesive bandage with too much stretch because this would create constriction and cause swelling in the foot. However, you can acheive high levels of support without over-constriction just by adding more layers. One or two layers of cohesive bandage, applied without stretch, will provide quite light support. As you wrap over extra layers, the level of support quickly ‘firms up,’ especially if you press the layers together.
4. It does not ‘give’
With some other kinds of strapping tape, you often have to apply them more tightly than you want them to be to compensate for the fact they stretch out and loosen off a little during wear. Cohesive bandage, on the other hand, does not have this level of give. It stays exactly as you placed it until it is pulled off or unwrapped.
5. You can tear it by hand
Cohesive Bandage can easily be torn along its length and width. Because you don’t have to rumage around for your scissors, you can use it very quickly. Simply tear the tape from one edge in the same way you would tear a piece of paper.
6. It can be reapplied and reused
Because cohesive bandage doesn’t rely on adhesive for its sticking properties, it does not lose its stick. So if you don’t get the tape job right the first time you can just unpeel it and try again. This property also means that you can repeatedly reuse the same piece of cohesive bandage. (Although if you’ve used it to wrap a sweaty foot you might not want to…)
Dressing awkward areas
Hippocrates appreciated that bandages could be tricky to apply: ‘One ought to be well aware that every bandage has a tendency to fall off towards the part that declines or becomes smaller as, for example, upwards in the case of the head and downwards in the case of the leg.’
The heels, elbows, ears, head, chin, breast/chest and sacral areas are notoriously difficult to apply dressings to and skilled application is crucial if a bandage is to stay in place for any length of time. However, the introduction of shaped bandages and tapeless dressing retention products has made the task much easier in many cases.
With a few strategic cuts, different sizes of tubular bandage can be used to secure head, ear or chin dressings (Fig 3). Larger sizes with slits cut for the arms can be used as a vest to secure chest, back or complex breast dressings.
|
|
|
USB Flash Drives: Components, Uses, and Myths Dispelled |
Posted by: P890J - 09-29-2021, 01:35 AM - Forum: FPS and Shooters
- No Replies
|
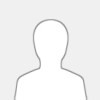 |
USB Flash Drives: Components, Uses, and Myths Dispelled
USB Flash Drives: Components, Uses, and Myths Dispelled
The USB flash drive—also known as a jump drive, data stick, or thumb drive—continues to be the most popular portable storage device, with sales estimated to exceed 500 million annually by 2020. Although cloud storage is making headway in the same market spaces, USB drives offer capacity, speed, and size that make them ideal for many uses beyond just storage, including some perhaps unexpected uses as well. This article explores what’s inside a USB flash drive, explores various uses, and dispels common myths.
A Look Inside
A typical USB flash drive includes a USB connector, a mass storage controller, one or more flash memory chips, and a crystal oscillator, as well as additional features such as jumpers, LEDs, switches, and unpopulated space.
The memory capacity and speed of USB drives continue to increase. As of the time of this writing, 512GB USB drives are becoming common, with 1TB capacity also available. The average speed for a highly-ranked 64GB USB 3.0 device is 104MB/s for a write operation and 171MB/s for a read operation.
Recently, USB drives incorporated the Type-C connector, which provides a yet even smaller and thinner connector compared to the Type-A connector. The Type-C connector has a rounded, symmetric shape that fits into ports easily yet securely, and works either way up (solving the problem that everyone has faced where they have to stick a USB plug in three times before it eventually goes in). Figure 2 shows a USB drive that accommodates both the old and the new sockets.
How to plug a thin promo USB Drive into a computer?
Technological advances have allowed a regular USB to become increasingly compact. While the more modern, state-of-the-art USBs are thinner, sleeker and sexier, they have a bit of a learning curve associated with using them. In particular, first time users often are not sure which direction the USB should be facing when plugged in to a USB port. Among other types of promo flash drives, these include our famous promotional Wafer USB Cards, and custom USB Clip.
Tired of losing your precious pen drives? Tired of spending hours searching for them, only to find them tucked away in some dingy corner? Or tired of having to finally give up and go run to the nearest store for another one? It seems like product designers Claire Pondard and Léa Pereyre have gone through the same dilemma innumerable times because they’ve decided to answer all our USB-related prayers! Their key-shaped intriguing product ‘Saint Antoine’ goes beyond any ordinary USB key. Deemed as common everyday products, due to their nimble size and consistent usage, pen drives are easily misplaced. However, Saint Antoine has been equipped with a crisp UDP chip. Now, what’s so special about this chip? After thorough calculations and necessary trial runs, the chip was customized to fit perfectly between the keys of a laptop/computer keyboard, ensuring it will be tightly fixed to it at all times. The grooved edges and branch-like structure of the pen drive allow it to sneakily merge into the crevices of the keyboard, without destroying the screen once the laptop is shut.
A Look at the MicroSD Card of the Future: Speed and Capacity meet Reliability
Manufacturers recently released the largest capacity and fastest microSD cards ever made. The 128 GB cards demonstrate more than a 1,000-fold increase in storage density over the last decade, and the fastest speeds of these microSD cards now rival other high-speed options for wireless computing.
The SD Association is made up of application developers and micro SD and component manufacturers. The organization determines microSD technology specifications and sets standards and roadmaps for the industry. SD Association President Brian Kumagai explained some of the new features and recent technology trends that help ensure microSD cards remain relevant and offer viable storage for many products and markets in the future.
Markets driving standardization
MicroSD cards are predominantly used in smartphones and other mobile devices that have limited space. When microSD cards first arrived on the scene, they quickly became the most popular form factor for mobile devices, and according to Kumagai, that is what drove their success. The microSD market is rapidly growing as more smartphones ship with microSD card slots. Even though the newest phones made by industry giant Apple do not currently accommodate microSD cards, those made by Samsung and many others do.
Over time, smartphone manufacturers have reduced the amount of on-board memory that ships with smartphones, thus lowering their hardware costs. Consumers have compensated by adding additional storage, often using 8 GB microSD cards. In fact, the bulk of microSD cards sold is used in smartphones, but sales of larger cards (16 and 32 GB) continue to grow. MicroSD card use is also growing in other devices that need small form factors, such as consumer digital imaging and video cameras like the GoPro action camera, night-vision IP security cameras, nanny cameras, automotive in-dash cameras and tablets. MicroSD is still the storage space of choice as devices become smaller and cards gain higher capacity, become faster and exhibit better performance.
Capacity: It’s all in the flash memory technology
The fundamental technology in all SD cards and any type of solid-state storage device today is NAND flash memory. Current NAND flash memory chips use floating-gate processes that all manufacturers support. Over the years, decreasing the horizontal line width of the lithography technology used in NAND memory production has created higher density storage capacities. The industry roadmap shrank design-rule dimensions for memory features from 110 nm down to the current size of 19 nm, making smaller NAND chips and allowing microSD cards to use more of them to hold more data. At these thin-line widths, there are only a few electrons of charge inside a single level cell. NAND chips using 16 nm line widths will be coming soon, but Kumagai says the industry is starting to see the limitations of scaling to smaller lithography.
Within the next year, NAND suppliers are expected to roll out the next generation technology that will go vertical and offer much higher densities than the current technology. The 3-D concept involves grinding individual cells so they are much thinner and stacking more of them so there is more than one cell in the same horizontal plane. “This technology is more difficult to produce. The thinner it is, the more difficult it is to read all the different levels, and error correction becomes needed,” says Kumagai.
All major NAND suppliers have 3-D technologies in development now. “The microSD card will look the same on the outside and at the interface, but the new 3-D NAND processes may help reliability and have other impacts on the industry if the technology is cheaper,” Kumagai says.
One way higher reliability processes will change the industry is that it will create new uses for microSD cards. They will be used in high-end automotive or industrial applications such as bar-code readers and scanners that need to store important data.
Strategies for higher speeds
While memory manufacturers are increasing the storage capacity by improving NAND technologies, they are also increasing microSD card speed with a combination of hardware and software strategies. One way is through the interface. A new high-speed serial interface (UH-II) handles the speed by having a second row of pins connect to the outside world and a new file system that supports much larger micro XSDHC or SDXC cards that are 32 GB to 2 TB. The newest second-generation ultra-high-speed (UHS2) cards using this interface have much faster read and write times at up to 312 mbps, up from 104 mbps on older generation cards.
Another area where speed can be gained is in the flash-memory controllers. This component manages the NANDs and does a handshake to the outside world. The controllers in the fastest-speed-class microSD cards use strategies to help both functions, such as using multiple channels and interleaving data.
What is an SSD?
A solid state drive (SSD) is an external storage device for your computer that works like a USB flash drive.
An SSD has no moving parts and is more reliable than the traditional hard drives it's replacing.
Visit Business Insider's Tech Reference library for more stories.
How an SSD works
Like a hard drive, an SSD is used to store large volumes of data whether the system is on or off, for extended periods of time. But unlike hard drives, an SSD has no moving parts, and is more akin to a flash drive.
Instead of reading and writing data to a spinning platter, an SSD stores data on flash memory chips (sometimes referred to as NAND flash memory). In this way, an SSD is essentially no different than a USB flash drive, or the memory you'd find in a smartphone or tablet.
In addition to memory chips, an SSD also has a controller chip. The controller is responsible for knowing where data is stored on the device and can find requested data in nanoseconds — almost instantly — which makes SSDs very fast storage devices.
Difference Between Flash Drive and Pen Drive
Flash drives and pen drives are two terms that we use interchangeably today. However, that was not the case 15 years ago.
Flash drives were devices that ran on flash memory. Their sole purpose was to store information and transfer it between the connected computers. The connection takes place through the USB port that is on the hardware.
Pen USB flash drive, on the other hand, were bulkier than flash drives and had more length to it. Due to their elongated size, they were given the name Pen Drives. They also ran on flash memory and had a USB interface to communicate with the computer.
Nowadays, the difference in size is no more. All the flash drives and pen drives of today have the same function, the same internals, and the compact form factor. So there is no real distinction you can draw from them. Hence, the pen drives and flash drives of today are essentially the same.
Next, we will go over the different types of USB flash drives. Please note that they can be categorized according to their uses, or physical characteristics. We attempt to find a balance between the two.
|
|
|
What Are the Applications of LED Downlights in Homes and Businesses? |
Posted by: P890J - 09-29-2021, 01:31 AM - Forum: FPS and Shooters
- No Replies
|
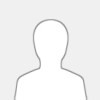 |
What Are the Applications of LED Downlights in Homes and Businesses?
What Are the Applications of LED Downlights in Homes and Businesses?
LED downlight, also known as can lights or recessed lights, is embedded into the ceiling to become a seamless accessory in any room. While you might be fond of this sleek look, you may not know all of the factors that contribute to creating perfect lighting in your home or business.
Where Should I Put LED Downlights?
LED downlights are a great option for large rooms and/or rooms with low ceilings. Recessed lights blend in with the ceiling, so they will not use as much space as traditional hanging light fixtures.
Lights can be spaced evenly throughout a room, and since they are recessed, they are discreet enough that you can install more fixtures than you otherwise would. This means that light can reach all corners of the room.
How Do I Install an LED Downlight?
LED downlights require you to insert holes in the ceiling to install a new light fixture, or you can retrofit a preexisting ceiling lighting fixture.
You will most likely require a new junction box if you do not already have one in the area you want to install the recessed lighting fixtures. A junction box is placed in the ceiling above the light fixture and contains electric wires and cables necessary to connect the light to the main power source of the building.
Architecture and building regulations vary, so you must check your downlight’s Insulation Contact (IC) rating to ensure that it is compatible with the type of insulation used in your home or business.
If you still need help, try reading our blog on recessed lighting installation!
Do I Need a Special Downlight for Showers and Outdoor Areas?
For outdoor recessed lighting and shower recessed lighting, you want to find light fixtures and bulbs that can withstand dust and water exposure, which is indicated by the Ingress Protection (IP) rating.
The right IP rating will reduce hazards by shielding your recessed lighting fixture from the elements. For dust and water protection, a rating of IP65 is recommended.
What Kind of LED Light Bulb Do I Need for My Downlight?
To avoid a fire hazard, never choose a light bulb with a higher wattage than is recommended for the light fixture. LED light bulbs produce more light (measured in lumens) for less energy (measured in watts) when compared to fluorescent and incandescent bulbs.
Choosing LED bulbs will allow you to maximize light output and reduce maintenance costs. LED bulbs also remain cool, which will further protect your home or business from fire.
Can I Control the Beam Angle of My LED Downlight?
LED downlights require you to insert holes in the ceiling to install a new light fixture, or you can retrofit a preexisting ceiling lighting fixture.
You will most likely require a new junction box if you do not already have one in the area you want to install the recessed lighting fixtures. A junction box is placed in the ceiling above the light fixture and contains electric wires and cables necessary to connect the light to the main power source of the building.
Architecture and building regulations vary, so you must check your downlight’s Insulation Contact (IC) rating to ensure that it is compatible with the type of insulation used in your home or business.
If you still need help, try reading our blog on recessed lighting installation!
Do I Need a Special Downlight for Showers and Outdoor Areas?
For outdoor recessed lighting and shower recessed lighting, you want to find light fixtures and bulbs that can withstand dust and water exposure, which is indicated by the Ingress Protection (IP) rating.
The right IP rating will reduce hazards by shielding your recessed lighting fixture from the elements. For dust and water protection, a rating of IP65 is recommended.
What Kind of LED Light Bulb Do I Need for My Downlight?
To avoid a fire hazard, never choose a light bulb with a higher wattage than is recommended for the light fixture. LED light bulbs produce more light (measured in lumens) for less energy (measured in watts) when compared to fluorescent and incandescent bulbs.
Choosing LED bulbs will allow you to maximize light output and reduce maintenance costs. LED bulbs also remain cool, which will further protect your home or business from fire.
Can I Control the Beam Angle of My LED Downlight?
The Structural Analysis and Notes of LED Panel Light
With the development of LED light industry, LED panel light is derived from LED backlight with the characteristics of uniform source of light, no glare and exquisite structure, which is very popular among us. Shenzhen Hoyol Opto Electronic Co.,Ltd makes some suggestions about the structural design and notes of LED panel light with the hope of helping you.
The main materials of LED panel light structure are as following
Aluminum Frame
Appearance structure and the main structure of LED heat dissipation generally use AL6063, aluminum extrusion mold, low initial investment cost, good surface appearance, good heat dissipation. We participated the show several days ago and got to know that some manufacturers have produced the LED light with casting framework, thus IP grade can be a little higher with better efficiency of light and more attractive appearance, but the initial investment cost is higher.
2 Diffuser plate
Emitting the uniform light of light guide plate plays a roll in blocking screen dot. Diffuser plate generally uses acrylic diffuser plate or PC 2.0 materials. Acrylic diffuser plate with lower cost but higher light transmission than PC, is poor in anti-aging. The price of PC is slightly higher, but it is good at anti-aging. After installation of the diffuser plate, the screen dot should not be seen and its light transmission rate should be up to 90%. Acrylic light transmission rate is 92% and that of PC is 88% .We can choose the materials of diffuser plate according to different requirement and usually use the acrylic materials.
3 light guide plate
The side LED light changes the angle of light ray by light refraction of screen dot. Light guide plate is the heart of the LED panel light and its screen dot design is very important. If the screen dot design is not good, the overall lighting effect will be bad. The questions will generally include:1. Bright in the middle and dark in both sides. 2. bright in the bright side and dark in the middle.
4.Rear Cover
Sealing lamp body usually uses AL aluminum. The overall texture is good and it plays a role of dissipating heat.
5.LED lighting source
Generally speaking,3528 is the usual light source. Besides, there are 5630 and 5050 . The luminous efficiency of 5630 and 5050 is not high and the design of their screen dot is difficult but their cost is lower. The lighting effect of 3528 is high and the screen dot is universal. Usually, when just beginning to produce the panel light, you can buy other manufacturers’ light guide plate to use and not be necessary to design the samples.
6.drive power
Light-driven power- there are two kinds of power modes: first, directly using cross-flow power (this mode has high efficiency and PF value is up to 0.95, so it is cost-effective);second, constant pressure with cross-flow mode (this mode is stable, but with low efficiency and high cost). Generally speaking, the second mode is designed for customers who require certification. Because the lamp is of 24V input voltage and doesn’t need to do safety certificate. It can be shipped to each shelf by using the power supply with safety certificate.
The Common Notes of LED Panel Light during its designing process
1. thermal adhesive needs to be as thin as possible and using thermal adhesive with glue will be better, or the thermal conductivity will be affected;
2. the selection of diffuser plate. Now many manufacturers of LED panel light usually choose smooth diffuser plate with matte board. There is a drawback of this diffuser plate---more static. It will be easy to attract ash and produce bright during the process of production; moreover, the dust will enter the lamp through various ways in a long-term use, which will cause the intense bright. The double diffuser plate was used at the early stage and this kind of diffuser through various ways in a long-term use, which will cause the intense bright. The double diffuser plate was used at the early stage and this kind of diffuser plate has less static with good lighting effect, so it is good to avoid dust in the lamp.
3. The selection of LED light. Try to use the light with high efficiency. Because the side emitting panel light has limitations in heat dissipation and luminous flux output. The heat dissipation will be affected if the power is high and the light efficiency is low.
4. Avoid gluing the reflective paper into the smooth. Because the glue will absorb the light and it is prone to produce light into the smooth side. But a large area of light guide plate needs to glue, or it will have shadow. If the reflective paper is not sticky, the mentioned will happen when the reflective paper is warped in the lamp.
Light-emitting diode (LED) technology offers bright illumination while using a fraction of the electricity used by incandescent bulbs. You’ve likely been replacing the old bulbs in your light fixtures with LED bulbs over the past few years. That’s still a good idea, but you can also purchase LED ceiling light fixtures that emit light without the need for standard-size LED bulbs.
The best LED ceiling light for your home depends on the fixture type and what brightness is most suitable for a particular room; for instance, kitchens and bathrooms typically require more intense lighting than family rooms and bedrooms.
Ahead, learn essential considerations when shopping for an LED ceiling light and find out why these top picks are among the best available.
Operation
Most indoor led ceiling light operate in the same manner as other ceiling lights. After installation, you flip a wall switch to turn the light on and off. Some, but not all, are also compatible with dimmer switches, allowing you to dim the light in the room to conserve even more energy. Still others operate by remote control or come with Bluetooth or Wi-Fi connectivity so you can turn them on and off or program them in advance from a smartphone or other digital device.
Our Top Picks
To qualify as a top pick, outdoor led ceiling light should be constructed from quality materials, well designed, reasonably priced, and built to last. The best LED ceiling light for your home will depend on your preferences and where you plan to install it. The following LED lights are suitable for various uses, and one (or more) should provide an energy-saving addition to your home.
|
|
|
Why thin wall cup mould so expensive? |
Posted by: P890J - 09-29-2021, 01:29 AM - Forum: FPS and Shooters
- No Replies
|
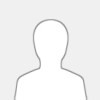 |
Why thin wall cup mould so expensive?
Why thin wall cup mould so expensive?
Why thin wall cup mould price is so high? General speaking, thin wall cup mould are using better steel, hot runner, better cooling, better venting and better demolding effectiveness.
The thin wall cup mould runs on high speed machine which needs withstand high pressure during cup molding, so the mould moving plate and fixed plate thickness are thicker than common mould. There need many interlocks inside the thin wall mould to ensure accuracy and pillar support to avoid deform and eccentric. The plastic airline cup mould need use high hardness steel, high-wear and high-erosion with HRC 55 or above. This means thin wall mould steel cost is higher.
The hot runner design is larger than the common plastic moulds, and at the same time, need limit the melt residence tome to prevent the resin degradation. When the mould is mult-cavities, the gating balance is much higher than that of common molds. Which means thin wall cup mould hot runner cost is higher.
Thin-walled products do not withstand the large residual stresses due to heat transfer irregularities like traditional wall thickness parts. In order to ensure the dimensional stability of the product, and to control the shrinkage and warpage within an acceptable range, it is necessary to strengthen the cooling of the mold to ensure the cooling balance. Which means need better cooling design to enhance the cooling effect, adding high conductivity metal inserts where necessary to accelerate heat transfer, like BeCu beryllium copper. The cooling cost is higher than common moulds.
Due to the short filling time and high injection speed, it is very important to fully exhaust the mold, especially the exhaust in the flow front gathering area, to prevent air trap. The air is usually discharged through mould cores, rams, ribs, studs, and parting surfaces.
The airline cup walls and ribs are very thin, they are very easy to damage, and the shrinkage in the thickness direction is small, the ribs and other small structures are hard to separate, to avoid sticking, there need use more ejector pins when thin wall injection molding.
In a word, thin wall mould structure is more complicated than common moulds. That’s why the thin wall cup mould is so expensive.
Cutlery mould exhaust problem
In the process of producing cutlery mould, sometimes will have unfilled parts, air bubbles etc, this is caused by air exhaust.
1. The source of air in the injection cutlery mold.
(1) The air contained in the gating system and the mould cavity. (2) Some raw materials contain moisture that is not removed by drying, and they are vaporized into water vapor at a high temperature. (3) Air generated by decomposition of some unstable plastics due to excessive temperature during injection molding. (4) Air formed by volatilization or chemical reaction of certain additives in plastic raw materials.
Poor exhaust of the knife and fork mold will bring a series of hazards to the quality of the plastic parts. The main performance is as follows:
(1) In the injection molding process, the melt will replace the air in the cavity. If the air is not discharged in time, the melt filling will be difficult, resulting in insufficient injection volume to fill the cavity.
(2) Excluding the unsatisfactory air will form a high pressure in the cavity and penetrate into the plastic inside under a certain degree of compression, resulting in quality defects such as pores, voids, tissue sparseness, and silver streaks.
(3) Due to the high compression of the air, the temperature in the cavity rises sharply, which causes decomposition and burning of the surrounding melt, causing local carbonization and charring of the plastic part. It mainly occurs at the junction of the two melts at the gate flange.
(4) The air is not well removed, so that the melt velocity entering each cavity is different, so flow marks and fusion marks are easily formed, and the mechanical properties of the plastic parts are lowered.
(5) Due to the obstruction of air in the cavity, the filling speed will be reduced, the molding cycle will be affected, and the taxation efficiency will be reduced.
Distribution of bubbles in plastic parts
(1) The bubbles generated by the accumulation of air in the mould cavity of the cutlery spoon are often distributed on the opposite part of the gate.
(2) Bubbles generated by decomposition or chemical reaction in the plastic raw material are distributed along the thickness of the plastic part.
(3) The bubbles generated by the vaporization of residual water in the plastic raw material are irregularly distributed on the entire plastic part.
Injection molding is a process in which a molten plastic is injected into a closed mold having a relatively low temperature through a nozzle under high pressure. Both thermoplastics and thermosets can be injection molded. It can be used to make various box-type packaging buckets and pails, such as various pails boxes and small boxes mould. For box-type packaging containers, China bucket mold manufacturers will consider the following aspects in bucket mould structural design.
1. The wall thickness of the bucket mould
The design of the wall thickness mainly considers three aspects: one is thickness; the other is uniformity; the third is gentle transition.
1 Thickness: The wall thickness of the bucket is mainly determined by its use, plastic type, structure and so on. For thermoplastics, generally not less than 0. 6mm, often choose 2~4mm; for thermosetting plastics, because of its poor fluidity, the thickness is larger, the small pieces are 1. 6~2. 5ram, the large pieces are 3. 2 ~ 8mm, the maximum is no more than 10mm.
2 Uniformity: The uniformity of wall thickness has a great influence on the quality of the bucket. If the thickness difference of a bucket is too large, the shrinkage will be uneven, causing defects such as deformation and crack. Therefore, the structure should be designed with an equal thickness structure.
3 Smooth transition: In some buckets, some parts must have different thicknesses due to structural requirements, such as the bucket turning point. At this time, a gentle transition should be adopted to avoid the sudden change of the section.
2. Improve stiffness of the bucket
The plastic is relatively flexible, the bucket is made of poor rigidity, and the turnover box type container sometimes has a large load capacity, so various measures for improving the rigidity should be adopted in the structure.
1 Add reinforcement: Reinforcement can enhance the strength and rigidity of the container. The basic requirements for the ribs are: the number should be more, the wall thickness should be thin, the height should be short, and the slope should be sufficient. The bottom of the rib should be a circular arc transition. The direction of the rib should be consistent with the flow direction to improve the plastic. toughness;
2 Improve the shape: the box-shaped bucket is mostly rectangular thin-walled parts, which are easy to be deformed. Various reinforcement measures should be taken to slightly extend the four side walls of the bucket to improve the rigidity; it is a strip shape on the side wall to prevent distortion. Enhancement; edge reinforcement at the edge of the bucket to prevent deformation of the mouth; bottom reinforcement at the bottom of the bucket designed in a corrugated, arched shape.
3 Reasonable support: The bottom area of the box-shaped bucket is large, but it is unreasonable to use the whole bottom surface as the support. Because the bottom is slightly curved, it is not flat. Therefore, the surface support should be changed into a line support or a point support, and the convex side support (ie, the line) Support); raised foot support (ie point support); the height of the protrusion is generally 0. 3 ~ 0. 5mm.
4 Corner: The corner is the intersection of two faces or three faces. Regardless of the shape of the bucket, the intersection of the faces must be rounded, which can greatly improve the rigidity of the bucket and improve the plastic filling model. Sex, and can disperse stress and reduce deformation.
3. Demoulding slope
In order to facilitate the demolding of the molded part, a suitable draft angle must be considered when designing the bucket. The draft is too small, the demoulding is difficult, and the surface of the bucket is damaged; if it is too large, the dimensional accuracy is affected.
The draft angle varies depending on the shape of the plastic part, the type of plastic, the mold structure, the surface roughness, the molding method, and the like. Generally speaking, the commonly used slope of the plastic part along the demolding direction is 1o~1.5o, and the minimum is not less than 0.5o.
Household molds are a form of fungus. There are many different types, and they can occur both indoors and outdoors.
Molds produce spores, which spread by floating around in the air. Mold spores are present in all indoor environments. There is no way to prevent spores, and they can persist in conditions where mold itself cannot grow.
Mold spores thrive in environments that are moist and warm, so when they land on a damp spot, they begin to grow.
Molds can grow on a variety of different surfaces, including fabric, paper, wood, glass, and plastic. As they grow, they may digest the material they are growing on.
|
|
|
What is Aerogel? |
Posted by: P890J - 09-29-2021, 01:27 AM - Forum: FPS and Shooters
- No Replies
|
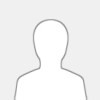 |
What is Aerogel?
What is Aerogel?
Aerogel is a broad term used to talk about an extraordinary group of materials that have been used since the 1960s in space travel, but are now finding uses across a whole range of industries. ‘Aerogel’ is not a specific mineral or material with a set chemical formula-rather, the term is used to encompass all materials with a specific geometrical structure. This structure is an extremely porous, solid foam, with high connectivity between branched structures of a few nanometres across.
Though aerogel is technically a foam, it can take many different shapes and forms. The majority of aerogel is composed of silica, but carbon, iron oxide, organic polymers, semiconductor nanostructures, gold and copper can also form aerogel. However, within the aerogel structure, very little is solid material, with up to 99.8% of the structure consisting of nothing but air. This unique composition gives aerogel an almost ghostly appearance; hence it is often referred to as ‘frozen smoke’.
Applications of Aerogel
As aerogel has such diverse chemical and physical properties, it is no surprise that it also has a wide range of applications. Since the 1960’s, aerogel has been used as the insulating material in spacesuits of NASA astronauts as, despite its wispy appearance, it is extremely strong and can survive take-off conditions easily.
In the early 21st century, aerogel was employed in a very special role by NASA- to capture space dust. Aerogel is being used in conjunction with the ‘Stardust’ mission, which aims to bring back particles from space from beyond the Moon for the first time. This dust is being primarily collected from the comet ‘Wild 2’. Aerogel is being used to capture this comet dust, as it will be able to trap the small particles without physically altering them. When the particle hits the aerogel, it will be traveling at speeds of up to 6 times that of a rifle bullet, which means most substances would not be able to slow the dust down without heating and thus alteration taking place. With aerogel, however, the dust buries itself into the porous material and is gradually brought to a stop as it loses momentum.
ABOUT THE DIFFERENCE
Silica Aerogel Insulation Blanket are the least dense solid in the world today. Pyrogel Aerogel insulation blanket have low thermal conductivity, high temperature resistance, flame retardancy, low density, and also have certain waterproof effect.
Silica aerogel insulation blanket is the best thermal insulation blanket material so far, its pore size is lower than the atmospheric pressure under normal pressure, so the air molecules in aerogel gap are in a static state, thus avoiding the convection heat transfer of the air. The very low volume density of the Silica Aerogel Insulation and the bending path of the nanoscale structure also prevent the gas and solid heat conduction, and the “infinitely many” void walls can minimize the thermal radiation. Together, these three functions almost blocked all the ways of heat transfer, which is the adiabatic effect of aerogels to other materials.
1st advantage is Excellent heat insulation effect
The heat insulation effect of Silica Aerogel Insulation Felt is 2-5 times that of traditional insulation material, and the theoretical lifetime measured by Arrhenius experiment is 20 years. It’s almost the same life as the building.
2, reduce the thickness of insulation layer
The aerogel felt has the same thermal insulation effect and the thickness is only a fraction of the traditional material. After heat preservation, the heat loss is small and the utilization rate of space is high. And at high temperatures, the above performance advantages are more obvious.
3, hydrophobicity and fire resistance
Aerogel blanket water repellent, which can effectively prevent moisture from entering pipes and equipment. At the same time, it has the fireproof performance of the building A1, and the three-dimensional network structure of the aerogel avoids the heat insulation effect of other thermal insulation materials in the long-term high temperature use, such as sinter deformation, settlement and so on.
4. Convenient construction
The aerogel blanket is light, easy to cut and sewn to adapt to various forms of pipes and equipment for thermal insulation, and the installation time and manpower are less.
5, save transportation cost
Aerogels can be used in an environment of -200~650 degrees Celsius, but it is usually used in aerogel insulation blanket. Based on the fiber’s fire resistance temperature, in principle we will control the temperature of 200 degrees Celsius. The hot melt adhesive used for aluminum foil or cloth and insulation blanket will not melt and ensure normal use. Of course, we keep insulation on the exterior wall. Aerogel insulation will also be done when other fixed, plate, screw and so on will be used.
There will be other conditions in the aerogel insulation blanket in practical applications, but the effectiveness will always come in and out of the ideal, but Gallic aerogel insulation blanket for all users, designed in all aspects, such as the hydrophilic and hydrophobicity of aerogel insulation blanket, can be done.
Uses of Fiberglass Fabrics
When it comes to composite construction or boat building, many people turn to fiberglass fabrics to get the job done right. Whether used for reinforcement, coating or laminating, professionals and DIY enthusiasts all over the world are quickly recognizing the benefits of this versatile composite. If you are new to composite materials or considering using fiberglass for a project, you came to the perfect place. In this guide, we will explore the properties and uses of fiberglass fabrics to help you better understand this convenient and cost-effective material.
[[image1,left/right]]Fundamentals of Fiberglass Fabric
With so many composites to choose from, understanding what each textile is and means for your project can be difficult or even daunting. Fortunately, the composite experts are here to help. Fiberglass cloth consists of bulk, chopped fibers or continuous strands of different kinds of glass. Whether in bulk form or a continuous strand, the combined physical strength of those glass fibers exceeds the properties that each of them has individually. This fiber-reinforced composite is typically flattened into sheets or randomly arranged and woven into fabrics for use in all sorts of applications. Fiberglass fabric is lightweight, strong, and less brittle than other composite materials. One of the most prized properties of fiberglass is its ability to be molded into various complicated shapes.
Applications and Uses of Fiberglass Fabrics
Across a wide range of industries, professionals look for materials with high-temperature insulation to ensure an effective thermal barrier for industrial gaskets. Because fiberglass offers high thermal insulation, it has become a prized and preferred material for protecting machinery. In our research, we discovered all sorts of ways this material is used!
Production of NBR
At first, we have the raw material. The raw material is yellow. After the manufacturing process, the material can be orange or red-tinted. At the end of the procedure, we have hot NBR Foam!
The hot NBR rubber has radical generating activators & added catalyst to polymerization vessels.
There is no major difference between the production of hot NBR & cold NBR. In fact, the cold NBR or hot NBR Foam is distinguishable with the number of branches.
In the procedure of monomer recovery, the unwanted solids were removed by latex which is sent through numbers of filters where it stabilized with “antioxidant”.
You can understand the difference between NBR rubber & any other kind of foam-like EVA Foam immediately.
In fact, when you get a piece of NBR foam from suppliers, you will find out the difference between the NBR foam & any other kind of foams like EVA foam , etc.
After the production of PVC Nitrile, we have a very smooth & soft outer skin on both sides.
This surface has a resilient touch and good flexibility. You can even use this resilient surface for some applications like yoga.
The cells of the foam are clear on the surface sheets.
The final product of NBR is a black piece of foam. You can also work with cutting & fabrication machinery like foam lamination (PSA) & Die-Cutting system.
In the whole procedure of NBR production, you will be able to transform the NBR to different kinds of foam products like gaskets, mats, tapes & seals.
The “Hong Kong Foam” company can produce customized products according to customer requirements.
The NBR has opened cell structure & closed cell structure that the closed cell is more popular & more efficient for producing the different kind of foams.
Mineral Wool Production
To make mineral wool insulation, basalt and industrial slag are melted in a 3,000° F furnace. (Slag is a by-product of steel production that usually ends up in landfills.) Next, the super-heated liquid is exposed to a high-pressure stream of air and then spun into long fiber strands. The strands are compressed into thick, dense mats and then cut into batts of insulation.
Now that you have a basic understanding of fiberglass and mineral wool, let’s take a look at the differences between these two popular types of insulation.
Fiberglass vs. Mineral Wool: How They Stack Up
R-Value: The thermal resistance of insulation is measured by what’s commonly known as the R-value, and the higher the R-value, the better. Fiberglass has an R-value of approximately 2.2 to 2.7 per inch of thickness. Mineral wool has a slightly higher R-value, ranging between 3.0 and 3.3 per inch.
Size: Fiberglass insulation is available in a wider range of sizes and types than mineral wool. Mineral wool insulation is typically only available in unfaced batts.
Sustainability: Mineral wool is composed of 70 percent or more recycled content. Fiberglass insulation typically contains 20 to 30 percent recycled content.
Cost: Fiberglass insulation costs 25 to 50 percent less than mineral wool. Fiberglass insulation for a 2×6 wall costs between 57 cents and 72 cents per square foot. Mineral wool insulation for the same wall runs about $1 to $1.10 per square foot.
Density: Mineral wool insulation has superior sound-deadening properties. It has a density of 1.7 pounds per cubic foot, as compared to 0.5 to 1.0 for fiberglass. Because of its density, mineral wool is hard to compress. Fiberglass, on the other hand, will lose some of its insulating value if it’s compressed too tightly.
Weight: Fiberglass is lightweight and easy to carry, but the batts are rather limp and can be challenging to set into place. Mineral wool is heavier than fiberglass, but the batts are also stiffer, so they don’t bend or flop over as easily.
Water Resistance: Mineral wool insulation is hydrophobic, meaning it’s highly resistant to moisture and water. Since it doesn’t absorb moisture, mineral wool doesn’t promote rot, corrosion, fungi, mold, mildew or bacterial growth. If fiberglass insulation gets wet, it becomes soggy, and its insulating value drops significantly.
Loose-Fill: Loose-fill fiberglass insulation provides a quick, easy and economical way to insulate attic floors and wall cavities. Loose-fill mineral wool does exist, but it’s difficult to find.
Installation: Mineral wool comes in dense, firm batts that are friction-fit into place; no stapling required. Fiberglass batts must be secured with staples or wire. To cut fiberglass insulation, compress it flat with a board or metal straightedge, then slice it with a utility knife. Use a serrated bread knife or woodcutting handsaw to cut mineral wool insulation. It’s recommended that you wear a dust mask when cutting and handling any type of insulation, including fiberglass and mineral wool.
Fire Resistance: Mineral wool is extremely fire resistant and can be used as a firestop. Fiberglass insulation is noncombustible, but not nearly as fire resistant as mineral wool.
Glass wool is a kind of fibrous material made from the melted glass raw materials or cullet. It consists of two types: loose wool and superfine wool. The fiber of the loose wool is 50 ~ 150 mm in length and 12 × 10- 3 mm in diameter. By contrast, the fiber of the superfine wool is much thinner in diameter, normally under 4 × 10- 3 mm. And it is also called superfine glass wool.
The loose wool can be used to make glass wool blanket and glass wool board. The superfine glass wool can be used to make common superfine glass blanket, glass wool board, alkali free superfine glass blanket, hyperoxic silica superfine glass blanket, and it is also used to preserve heat in the exterior-protected construction and the pipelines.
|
|
|
A Brief History of Men's Fashion |
Posted by: P890J - 09-29-2021, 01:25 AM - Forum: FPS and Shooters
- No Replies
|
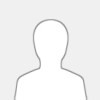 |
A Brief History of Men's Fashion
A Brief History of Men's Fashion
We’ve said it time and time again, men's wear is ruled by history and tradition. Every person in menswear (designer, stylist, editor, etc) has taken inspiration from the past at one time or another. And no era has been overlooked.
Therefore, as we continue to explore the foundations of personal style, I thought we’d take a quick look back at the last hundred-or-so years in men’s fashion. Perhaps this will provide a little insight or context as to how menswear shifts, and more importantly, how we can make informed decisions when it comes to buying clothing and developing personal style.
LATE 1800S: LAST OF THE VICTORIANS
As the nineteenth century came to an end men were slowly shaking-off the Victorian influence which still had them wearing tophats, frock coats, and pocket watches while carrying walking sticks. This may seem like an elaborate and restrictive way to dress, but it was a big step in the right direction considering the Georgian period that proceeded it had men wearing feathers, panty hose, and high heels. And you thought you were a “dandy”.
1900S: TALL, LONG & LEAN
As we moved into the 1900s men’s clothing was predominantly utilitarian and rather unimaginative. The long, lean, and athletic silhouette of the late 1890s persisted, and tall, stiff collars characterize the period. Three-piece suits consisting of a sack coat with matching waistcoat and trousers were worn, as were matching coat and waistcoat with contrasting trousers, or matching coat and trousers with contrasting waistcoat. Sounds familiar, right? Trousers were shorter than before, often had “turn-ups” or “cuffs“, and were creased front and back using the newly-invented trouser press.
After the war (which introduced numerous classic menswear designs which are still used today, like trench coats and cargos), business started to pick-up and Americans had more money. More money allowed them to travel more and broaden their horizons culturally and aesthetically. Many crossed the Atlantic to England and France. Naturally they returned with suitcases full of the latest fashions being worn overseas.
Of all the countries, England had the most influence on American menswear. In the 1920s American college students began putting their own spin on pieces being worn at the legendary Oxford University, including button-down shirts, natural-shouldered jackets, regimental ties, and colorful argyle socks. Furthermore, the Prince of Wales, who later became the Duke of Windsor, was the world’s most important and influential menswear figure. Through newsreels, newspapers, and magazines the elegant Prince became the first international “style icon” and became widely known and renowned for his impeccable taste in clothing. He was a legitimate trendsetter for every day people and it was the first time in history that clothing advertisers would use a celebrity face to sell clothing, shamelessly plugging their items “as worn by the Prince”.
3 BENEFITS TO WEARING SILK SCARVES VS COTTON SCARVES
If you're confused by whether a silk scarf is better than a cotton scarf, then you will want to be able to weight the pros and cons of silk and cotton scarves. In this post, you will find our list of benefits and drawbacks of wearing a silk scarf over a cotton scarf.
1. SILK WILL NOT IRRITATE YOUR SKIN
First of all, silk will not irritate your skin. Silk is much more delicate than cotton. The roughness of cotton can sometimes cause or worsen pimples.
This is in part due to the fact that silk is hydrophobic, meaning it does not hold water well. Cotton absorbs the moisture it is exposed to. That is why wearing cotton can cause acne, as cotton clothing retains oils that creates pimples. But moisture rolls right off of silk.
2. SILK IS HYPOALLERGENIC
Another benefit of silk is that silk is hypoallergenic. Silk resists dust, mold, and fungus. You are unlikely to have an allergic reaction to wearing silk.
3. SILK IS A FASHIONABLE, LUXURY MATERIAL
Last but not least, silk fabrics shine in a way cotton cannot match. This makes silk an excellent choice for showing brilliant colours and artistic patterns.
How To Wear A Square Scarf
1)The Basic Fold:
There are many ways to tie a scarf, this one is one of the most popular ways all of them. This fold is the starting point of three easy ways of putting on the square scarf. They are not only simple for everyday use but also look effortless with any casual outfits.
Lay down your square scarf on a surface
Folds two sides to form triangles and lay as they just touch the tips
Fold each of the triangles to create a rectangle and align as they reach side by side.
Fold from the half to pack it up, as shown in the last photo.
2) Simple Loop around Neck:
Place a basic folded scarf around your neck with the two corners facing down. Take one of the corners and twist it around your neck. Adjust the length of each side.
3) Simple Neck Tie Knot:
Place a basic folded scarf around your neck with the two corners facing down. Take the edges and make a knot, take one of the sides and face it up to hide the knot behind the tie.
How to Choose Yoga Clothes
Refining a downward dog or trying a new balance pose at the yoga studio is challenging enough on its own, but it’s made even harder when you’re fiddling with sagging, too tight or uncomfortable yoga clothes. That’s why it’s important to purchase clothes that are breathable, flexible and comfortable.
Your yoga vest purchases will depend largely on personal preference, as well as the style of yoga you plan to practice. But at a high level, here’s what to wear to yoga (see below for a more detailed discussion of these yoga basics):
Breathable, flexible bottoms like yoga pants or shorts
A breathable, narrow- or form-fitting top that won’t hang over your head when you’re upside down.
For women, a sports bra or built-in shelf bra that offers enough support for the type of yoga you’re practicing
A comfortable, warm top layer for end-of-class savasana (corpse pose) or after class when you’ve cooled down
What to Look For in Yoga Clothing
Many yoga clothes are made with polyester-nylon-spandex blends, and for good reason—these fabrics offer the right balance of comfort, breathability and flexibility:
Comfort: There’s nothing worse than practicing yoga in an uncomfortable piece of clothing. As you tune into your body, you don’t want to focus on itchy seams and tags, saggy or too tight waistbands, or fabric that binds and chafes.
Breathability: Depending on the type of yoga you practice, you may sweat a little or a lot. Particularly if you’re sweating a lot, it’s important to wear breathable and moisture-wicking materials to keep you cool and comfortable. Tank tops, shirts with cutouts and yoga slim pants with mesh pockets will all improve breathability and venting. Avoid cotton, which holds moisture, makes you feel hot and damp, then leaves you prone to chafing or getting chilled when class winds down.
Flexibility: Yoga involves bending, stretching, binding, lunging, reaching and rolling. Your clothes need to be able to keep up with these movements, which means they’ll probably be made with at least 15 percent spandex.
There are few things as empowering as sexy lingerie. Throw on a pair of lacy knickers and a tulle bra and sit back as your confidence immediately skyrockets. It doesn’t matter if you’re in a relationship, dating (in a pandemic!) or single this Valentine's Day, because we all now know that lingerie – even the sexiest – is actually all about you.
Sure, our undies are well hidden under a tracksuit right now... but knowing that a sexy lingerie set is working its magic under your oversized hoodie and joggers is not only a confidence-booster – but a mood lifter, too. And there's no better time than the most romantic weekend of the year to invest. After all, how much more together does your life feel when you actually manage to put on a pair of knickers and a bra that match?
While there will always be space in our underwear drawer (and hearts) for a big Bridget Jones-style knicker and wireless bra, a cute new bra and brief set is a season-less purchase, rendering it a wise buy always and something you can absolutely justify investing in. That pair of designer shoes you’ve been saving for might be out of style come next winter, but some ladies sexy lingerie? Timeless. Granted, everyone has different preferences when it comes to underwear, so it's lucky that there are tonnes of lingerie brands out there, each offering sexy designs in their own right.
We thought we'd save you the legwork and hunt down the very best sexy lingerie that money can buy for Valentine's Day (you should also check out our dedicated guide to Valentine's Day lingerie if you haven't already), from the best lingerie brands in the business. We’ve got balconette bras, suspenders, high-waist knickers, wireless bras, matching sets and all the sheer/lacy/tulle fabric. We’ve even thrown in a few one-pieces for good measure.
High up on our wish list right now is this Carine Gilson teal and lace silk satin bra (with sexy matching briefs) to boot which have both been crafted in her Brussels atelier. There's also this plum lace body from the name in sexy lingerie, Agent Provocateur - which is not only currently half price, but in stock in ALL sizes. A true lingerie miracle.
|
|
|
|