Welcome, Guest |
You have to register before you can post on our site.
|
Online Users |
There are currently 292 online users. » 0 Member(s) | 291 Guest(s) Google
|
Latest Threads |
Dominica visa free countr...
Forum: Off Topic
Last Post: axied12
06-24-2025, 12:37 PM
» Replies: 0
» Views: 156
|
Advanced microneedling
Forum: Off Topic
Last Post: axied12
05-28-2025, 01:25 PM
» Replies: 0
» Views: 290
|
Caviar and cheese
Forum: Off Topic
Last Post: axied12
05-28-2025, 12:38 PM
» Replies: 0
» Views: 256
|
Top-rated countertop comp...
Forum: Off Topic
Last Post: axied12
05-04-2025, 06:42 AM
» Replies: 0
» Views: 391
|
Ryanair letenky levně do ...
Forum: Off Topic
Last Post: axied12
02-11-2025, 01:37 PM
» Replies: 0
» Views: 789
|
Trusted essay writing ser...
Forum: Off Topic
Last Post: axied12
01-30-2025, 08:16 AM
» Replies: 0
» Views: 718
|
Bootverkopers - actieve j...
Forum: Off Topic
Last Post: axied12
12-07-2024, 11:07 AM
» Replies: 0
» Views: 841
|
Services for individuals ...
Forum: Off Topic
Last Post: axied12
12-02-2024, 03:31 PM
» Replies: 0
» Views: 813
|
Used excavators
Forum: Off Topic
Last Post: axied12
11-13-2024, 09:22 AM
» Replies: 0
» Views: 764
|
Buy Higo Rocket in Dubai
Forum: Off Topic
Last Post: axied12
10-25-2024, 01:09 PM
» Replies: 0
» Views: 876
|
|
|
Is Rockwool Harmful? Yes, But… |
Posted by: aakfk2665s - 08-26-2021, 04:57 AM - Forum: Welcomes and Introductions
- No Replies
|
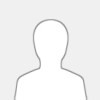 |
Rock wool has long been a popular media for growing hydroponic fruits, vegetables and herbs. However, I’m going to make the case against rockwool and argue why you should never use rockwool again because rockwool is harmful.
This post has gotten a lot of attention recently, and as a result is in the process of being updated to include more information. I cite studies and in no way reference any particular company – I am talking about mineral wool as a growing media in this post.
If you want better alternatives to rockwool, please check out my hydroponic media guide.
It’s Not Environmentally Friendly
[/url]
I believe in environmental sustainability – it’s one of the reasons I’ve chosen to grow hydroponically. Rockwool doesn’t score well on the environmental scale. It’s not a natural material. [url=http://www.suntherm-industry.com/]Manufacturers use combine chalk and rock and then heat them up to around 3,000 degrees Fahrenheit. Next a stream of air is blown through it, resulting in extremely thin fibers of the rocky material. As the strings are blown out, they bunch together and form the material that you see for sale at the local hydroponics store.
Basically, they are taking two materials that are 100% natural (chalk and rock) and turning them into a hybrid material that will remain in that form forever. When you throw away your old rockwool it’s going to sit in a landfill looking just like that for a long, LONG time. If you absolutely insist on using it, try to save your rockwool in between your growing season and reuse it.
It’s Not Healthy To Be Around
Not only is rockwool unfriendly to the environment – it’s also potentially harmful to your health. New blocks can contain a lot of dust and loose fibers that can get in your eyes, mouth, skin and lungs. It’s similar to asbestos in the sense that the little fibers can lodge themselves in your lungs if you’re working with it a lot. It may not be as toxic as asbestos, but why take the risk? Not something that I’m willing to gamble with if I don’t have to – there are plenty of other hydroponic media choices! If you’re using rockwool, you should be using a mask, goggles and gloves when you work with it to protect yourself.
Ceramic fibers
Ceramic fiber was designed and developed for applications in which the composite matrix/resin temperature can go, for example, as high as 1000°C in a corrosive and oxidizing environment.
The ceramic fibers are made from precursor fibers or a very thin tungsten-core wire. Materials like boron and silicon carbide vapors are deposited onto a red-hot precursor moving very slowly. Some of the ceramic fibers are large-diameter monofilaments.
The ceramic fibers show high-strength and high-modulus properties in both tension and compression applications. In compression, unidirectional boron composite stress–strain curves are linear to failure (400,000 psi failing stress) and exhibit a modulus of 30 million psi.
Because ceramic fibers have large diameters, prepreg tapes formed from the fibers are usually unidirectional only.
The ceramic fibers are uniquely suited to handle the high-temperature consolidation conditions of titanium and ceramic matrix composites. Only limited quantities of ceramic fibers are manufactured annually but production can be rapidly expanded to meet new demands.
Bio-soluble fiber paper SUNTHERM HB (Bio-soluble) Fiber Paper
is a new develop at the basic of the traditional ceramic fiber, the main components is MgO, CaO, and contains a small amount of organic binder, with integrated fire resistance, heat separation and thermal insulation functions, can be used at higher temperatures filed, bio-soluble fiber can replace part of the traditional ceramic fiber, the use of temperature can reach 1050C, and have excellent eco-friendly performance.
Applications
?Furnace expansion joint filler
?High temperature gasket
?High-temperature insulation backing
?Fire protection facilities
?Molten metal splash protection
?High-end household appliances insulation device
Features
?Easy twisting, shaping and cutting
?Excellent machining performance
?Excellent tensile strength
?Acoustic performance
?Good anti-spalling properties
?Low thermal conductivity, low thermal capacity
?Resistance to wind and erosion, long service life
?Excellent thermal insulation, fire protection,
thermal insulation and acoustic performance
What is Ceramic Fiber Bulk?
Ceramic Fiber Bulk is a high temperature refractory insulation material manufactured from high purity alumina and silica raw materials on computer-controlled furnaces to provide consistent fiber properties. Fibers are lightweight, chemically inert, and have all the positive characteristics of ceramic fiber. Bulk insulation is the perfect solution for insulating intricate spaces, parts, or shape forming for various commercial and industrial applications. Our office currently stocks “spun” ceramic fiber bulk rated for temperatures up to 2300o F and 2600o F. If a different temperature rating or grade is needed, please contact our office directly for a custom quote.
Blown vs Spun vs Chopped Fibers?
In addition to varying temperature grades, Ceramic Fiber bulk is available in blown, spun, or chopped fibers. Blown fiber has the smallest fiber size and is more flexible in comparison to the other grades. Spun fiber is very similar to blown, with the exception of longer fibers and a greater rupture / tensile strength. Spun fiber is still light and airy in appearance and is the most commonly used fiber in applications. Chopped fiber has the largest fiber size and is bulky in appearance. Our office currently stocks spun fiber but if another grade is required, please contact us for a custom quote.
|
|
|
Aluminum Foil Rolling Mill — Produce high-quality foils with high efficiency and low |
Posted by: aakfk2665s - 08-26-2021, 04:55 AM - Forum: Welcomes and Introductions
- No Replies
|
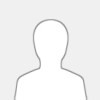 |
Aluminum Foil Rolling Mill — Produce high-quality foils with high efficiency and low cost
As the requirements for aluminum foil output and quality continue to increase, the requirements for aluminum foil production equipment, such as aluminum strip and foils mill tools, are becoming more and more stringent. Today, rolling mills are required to produce foil products with a thickness of less than 6 microns and a width of more than 2 meters, and the speed should reach more than 2,000 meters per minute. In order to meet these requirements, the aluminum foil rolling mill is equipped with the most advanced high-speed rolling technology, and provides comprehensive process support, so that the rolling mill can be put into production at a record speed, and after changing the rolling mill settings, it can be produced from the first coil. The technical indicators of the qualified products for sale are better than the industry standards.
It’s a well-established question and one that we’ve been too afraid to ask our mothers: Should we use the shiny or the dull side of aluminum foil when we cook? And have we been doing it wrong this entire time?!
Concerned cooks, you can breathe a sigh of relief: As it turns out, there’s no “correct” side of aluminum foil to use when cooking so using it on either side is not one of the cooking mistakes that could ruin your food. According to the Huffington Post, they’re both equally effective at heating your food—so just choose whatever side you prefer.
If there’s no trick to it, then why, exactly, does aluminum foil have a shiny and a dull side in the first place? Experts at Reynold’s Kitchen say that the difference between the two sides is due to a manufacturing process called milling, during which heat and tension is applied to stretch and shape the foil. Two layers of foil are pressed together and milled at the same time, because otherwise, it would break.
“Where the foil is in contact with another layer, that’s the ‘dull’ side,” Reynold’s explains. “The ‘shiny’ side is the side milled without being in contact with another sheet of metal. The performance of the foil is the same, whichever side you use.”
But pay attention if you are using non-stick foil; in that case, there is a difference between the two sides. Since the non-stick coating is only applied to one side, you’ll want to use the dull side. Side note: There will be a label that designates the “non-stick side” in case you forget.
However, aluminum foil could pose a serious risk to your health—so maybe you should stop cooking with it altogether.
Aluminum foil might be one of our favorite inventions ever. Whether we're grilling up some fresh veggies in a neatly-wrapped parcel or folding a leftover slice of pizza to save for later, it's the perfect solution to pretty much any kitchen situation. Seriously, our list of uses for this shiny staple is endless.
We noticed that the handy tool comes with two distinct sides: a shiny, reflective side and a dull, matte side. That got us thinking. Is there a purpose behind the two different textures? Should we be using different sides for certain reasons? Have we been doing everything wrong for years?!
"Regardless of the side, both sides do the same job cooking, freezing and storing food," Mike Mazza, marketing director for Reynolds Wrap, told TODAY Home via email. "It makes no difference which side of the foil you use unless you're using Reynolds Wrap Non-Stick Aluminum Foil."
Non-Stick foil actually has a protective coating on one side, so the company recommends only placing food on the side marked "non-stick" for maximum efficiency.
Aluminum foil, or tin foil, is a paper-thin, shiny sheet of aluminum metal. It’s made by rolling large slabs of aluminum until they are less than 0.2 mm thick.
It’s used industrially for a variety of purposes, including packing, insulation and transportation. It’s also widely available in grocery stores for household use.
At home, people use aluminum foil for food storage, to cover baking surfaces and to wrap foods, such as meats, to prevent them from losing moisture while cooking.
People may also use aluminum foil to wrap and protect more delicate foods, like vegetables, when grilling them.
Lastly, it can be used to line grill trays to keep things tidy and for scrubbing pans or grill grates to remove stubborn stains and residue.
[/url]
Aluminum is one of the most abundant metals on earth.
In its natural state, it is bound to other elements like phosphate and sulfate in soil, rocks and clay.
However, it’s also found in small amounts in the air, water and in your food.
In fact, it’s naturally occurring in most foods, including fruits, vegetables, meats, fish, grains and dairy products.
Some foods, such as tea leaves, mushrooms, spinach and radishes, are also more likely to absorb and accumulate aluminum than other foods.
Additionally, some of the aluminum you eat comes from processed food additives, such as preservatives, coloring agents, anti-caking agents and thickeners.
Note that commercially produced foods containing food additives may contain more aluminum than home-cooked foods.
The actual amount of aluminum present in the food you eat depends largely on the following factors: - Absorption: How readily a food absorbs and holds on to aluminum
- Soil: The aluminum content of the soil the food was grown in
- Packaging: If the food has been packaged and stored in aluminum packaging
- Additives: Whether the food has had certain additives added during processing
Aluminum is also ingested through medications that have a high aluminum content, like antacids.
Regardless, the aluminum content of food and medication isn’t considered to be a problem, as only a tiny amount of the aluminum you ingest is actually absorbed.
The rest is passed in your feces. Furthermore, in healthy people, absorbed aluminum is later excreted in your urine.
Generally, the small amount of aluminum you ingest daily is considered safe
[url=http://www.metalgoldshell.com/seamless-steel-pipe-production-line/]Seamless steel pipe production line is mainly single-chain type cooling bed cooling bed, a double-stranded cooling bed, the new chain cooling bed, stepping rack cooling bed, screw-type cooling bed.
1, single-chain cooling bed
More use of single-chain cooling bed climbing structure. Cooling bed and fixed by the forward rail transport chain composed of a set of transmission. Placed between two steel dial grip forward transport chain, fixed steel rails bear the weight of the body. Single chain cooling bed transport chain finger means of the forward thrust friction of the steel pipe and the fixed rail to generate rotary motion, while relying on the weight of steel and the angle of lift, the steel pipe is always abutted against the forward transport chain finger, achieve a smooth pipe rotation.
2, double-stranded cooling bed
Duplexes cooling bed transport chain from the forward and reverse transport chains, positive and negative chain of transmission of each set. Placed between two steel dial grip forward transport chain, the reverse chain bear weight steel body. Duplexes cooling bed transport chain use the forward thrust of the steel pipe pulling claw run forward, using the inverse chain steel pipe friction generated continuous rotary motion. Reverse chain movement also makes steel always leaning forward transport chain, finger, smooth rotation and uniform cooling.
3, the new chain cooling bed
A combination of single-stranded and double-stranded cooling bed features cooling bed, cooling bed into the uphill sections and downhill sections. The uphill sections of the transport chain by the forward and reverse transport chain consisting of a double-stranded structure, positive and negative together to make steel continues to rotate forward, doing sport climbing. Downhill section of the forward transport chain and single-stranded structures arranged in parallel steel rails, relying on weight to achieve rotation, do landslide movement.
4, stepping rack cooling bed
Stepping rack cooling bed bed composed by two racks, assembled in a fixed beam, called static rack, another assembly in moving the beam, called the move a rack. L The agency action, moving the pipe rack will hold up the rise, due to an inclined angle, steel rolling when it is lifted once along the tooth. Move up to the highest gear position, stepping body movements so that the moving direction of the rack to the cooling bed one step away from the output. Lifting mechanism continues to operate, drive and move the rack dropped into a given rack alveolar steel, steel toothed rack along a fixed rolling once again, after moving back to the initial position of the rack, complete a cycle.
5. Screw the cooling bed
Main drive screw is cooled by means of the screw and fix the cooling of the gantry and other components, the screw including a screw rod and screw helix. Face fixed cooling gantry above the spiral rod above and below the spiral, steel body weight is borne by the fixed cooling stand. Main drive screw driven synchronous rotation, spiral screw driven steel roll forward on the fixed bench cooling, cooling. Single chain does not fit the cooling bed continuous operation, better cooling bed duplexes, the new cooling bed chain effect and low cost, stepping rack cooling bed is generally used in large or high profile production line[img]/Content/upload/2021797717/202108251334033471709.gif[/img], screw-type cooling bed are generally smaller diameter seamless steel pipe for cooling.
Heat treatment services for stainless steel and metal alloys
Solution annealing (also referred to as solution treating) is a common heat-treatment process for many different families of metals. Stainless steels, aluminum alloys, nickel-based superalloys, titanium alloys, and some copper-based alloys all may require solution annealing.
The purpose of solution annealing is to dissolve any precipitates present in the material, and transform the material at the solution annealing temperature into a single phase structure. At the end of the solution annealing process, the material is rapidly quenched down to room temperature to avoid any precipitation from occurring during cooling through lower temperature ranges. The single phase solution annealed material will be in a soft state after treatment.
The solution annealing treatment is required prior age hardening / precipitation hardening. The single phase microstructure created during solution annealing is required prior to age hardening, such that only the precipitates formed during age hardening will be present in the final product. The composition, size, and quantities of those precipitates formed during aging will determine the final product's hardness, strength, and mechanical properties after aging. It is critical that the structure be properly solution treated prior to aging in order to meet all of these requirements.
High-quality solution heat treatment
We recognize how important it is to our clients that the finished product we create demonstrates exceptional quality, and purity. To achieve this goal, we have invested heavily in our machinery, as well as implemented rigorous quality-control standards that ensure your work is completed to the very highest standard at every stage of solution heat treating. Our experienced team is able to successfully undertake heat treatment solution on a wide-variety of projects.
Definition of Cast Roll and Forged Roll
We will introduce cast roll and forged roll.
Forged rolls offer outstanding internal and surface soundness and meet customers’ requirements for strength, hardness, and reliability. Manufacturer produces forged rolls on advanced liquid forging hydraulic presses and heat treat by means of double and progressive induction to guarantee that our products have excellent levels of chemical pureness, solid metallurgic structure, and high resistance. The Reinosa steel plant’s latest developments in forged back-up rolls produces a superior product compared to cast back-up rolls. The structural homogeneity of forged rolls enables optimal performance in the mill.
The twin-roll plate casti roll is not completely equivalent to the roll on the twin-roll plate and strip casting machine. It is a deformation tool and also functions as a water-cooled crystallizer in the process of casting the roll. When working, the outer surface of the roll sleeve of the casting roll is in contact with the hot molten metal, and the inside of the roll sleeve is washed by powerful cooling water to quickly take away a large amount of heat, and there is a strong heat exchange between them. Casting rolls not only bear the rolling pressure of deformed metal, but also bear huge heat exchange stress. Therefore, special requirements are put forward for the cast roll sleeve material and the cast roll structure. The selected roll sleeve material can withstand the alternating heat. Load, have sufficient heat transfer capacity, do not chemically react with molten metal, and have sufficient strength and rigidity to ensure the smooth progress of the casting and rolling process.
|
|
|
Gaming chair guide: Expert shares how to buy a gaming chair |
Posted by: aakfk2665s - 08-26-2021, 04:54 AM - Forum: Welcomes and Introductions
- No Replies
|
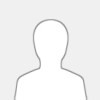 |
What is a gaming chair?
[/url]
There's nothing particularly unique about gaming chairs, except the style. Sure, you'll find everything fromgaming armchairstogaming chairs that bring you down close to the floorand everything in between. But these days, the term "gaming chair" tends to denote a specific type of office chair with a leather or faux-leather build, a high-back race car-style seat and colorful patterns.
1. DXRacer Racing Series Gaming Chair
DXRacer was the first brand to produce this style of gaming chair back in 2006 and has grown to offer many different shapes and styles — most built on the same race car chair design. This model uses an artificial polyurethane leather with high density foam and a carbon fiber texture on the seat. You also get strap-on lumbar and neck pillows, and a number of colors and patterns to choose from.
Since their inception, gaming chairs have grown incredibly common behind esports teams, Twitch streamers, YouTubers and other gaming personalities — leading to a surge in popularity.
Are gaming chairs ergonomic?
The word "ergonomic" gets thrown a lot in marketing — especially when it comes to chairs — ultimately, ergonomics is all about customizability.
"If I had to pick one important thing, it's that a chair be easily adjustable" said Karen Jacobs, a board-certified professional ergonomist and clinical professor occupational therapist at Boston University. Specifically, she explained, you want a chair whose height, tilt and armrests are versatile, and then you want to actually learn and use those adjustments so you can get that ideal sitting position at a desk. In fact, it's best if you adjust it throughout the day to vary your posture just a bit, rather than staying in one formation. So, in summary, adjustability is key.
2. GTRACING Gaming Chair
There are dozens of chairs using this racing seat design, but with different features. Many more affordable chairs like this popular model on Amazon — whose more than 18,500 reviewers left it a 4.5-star average rating — allow the back to recline but don't allow for the full seat to tilt. If you're sitting at a desk for long periods, you’ll likely want that full tilt mechanism.
It can be tempting to lean forward during an intense gaming session, too, but you don't want to sit like this for very long. "The chair isn't providing the support you need," noted Jacobs. You want to be able to tilt the chair back and forth to promote some movement. In addition, she said, you want some cushion in the armrest and a porous, breathable material in the seat, neither of which is particularly common among gaming chairs. The lower the price, in fact, the quicker the faux-leather will start peeling and the seat cushion will wear down to its rock-hard bottom.
None of this is to say gaming chairs are terrible. Certain models do allow you to lean back and elevate your legs, much as you would on a couch, which will be decently comfortable. Jacobs also mentioned that if you're sitting back, the extra high back support can be nice, provided you have support for your neck, too — a lot of gaming chairs come with neck pillows, though some may be more comfortable than others.
3. Secretlab Titan Gaming Chair
Unlike more affordable models, the SecretLab Titan — built primarily for medium-to-larger folks — has full tilt functionality and adjustable lumbar support within the backrest. It also comes in fabric and NAPA leather variations, giving you a few more options in terms of materials.
Gaming chair versus office chair?
I get it: Gaming chairs look cool, and might feel a bit more comfortable at first blush. But just because a seat is comfortable when you first sit down doesn't mean it's going to be good for longer sessions at your desk.
"Typically, it can take a week or longer to really evaluate a chair for comfort," noted Jacobs. If you can, find a company and retailer that will let you try the chair out for at least a week, if not more so you can dial in the adjustments and decide whether it's right for you.
Ultimately, the chair you get will probably depend on your use case. If you want a chair that'll let you kick back on soft leather for an hour or two, a gaming chair may fit the bill. But if you're working from home or gaming for hours on end, you're probably going to get more for your money with an [url=http://www.hzjiemax.com/office-chair/]office chair designed for long sitting sessions. High-end, well-known office chairs like the Herman Miller Aeron and Steelcase Gesture are hard to beat when it comes to adjustability, comfort and long-term durability, but more affordable models like the Komene Mesh or HON Ignition can do the trick, as well.
How to Choose the Right Bar Stool
Choosing the right type of commercial furniture is crucial, as it does not only define the entire look of your shop or office, but also influences customer impression of your business. This is even more important for businesses in the food and dining industry; bar and restaurant furniture are integral in creating the perfect ambience and theme for your interiors, which can make or break the customer’s dining experience.
For owners in the process of designing their bars or restaurants, one of the first things to look at are the chairs and bar stools. These are the cornerstone of your establishment’s dining space and are crucial to the entire dining experience. Selecting chairs is actually easy as they are often sold in sets. For bar chair, however, the process of choosing can actually get tricky. To help you decide which type of stool to use, we have rounded up some do’s and don’ts that you ought to follow:
Do: Measure your counter or table height.
For bars and restaurants, table height is usually at 40 to 45 inches. In this case, you can easily narrow down your selection to 30-inch bar stools. At the same time, measure its width and make sure that there’s still space for your customers to comfortable ease their way into or out of their seats.
Don’t: Choose a bar stool with no back if your table is not high enough.
Bar stool without backs is usually used when customers are more likely to lean on the table while watching the game, drinking, chatting, etc. However, they might get uncomfortable if there is not enough support, so you’d better choose a stool with arms and a back in this case.
Do: Consider using metal bar stools for your bar.
Metal is easy to clean, affordable, and stylish enough to match most countertops and tables. If you have a wooden floor and counter, it creates a contrast between modern and rustic design. An example of a very simple and minimalist metal barstool is our Kellis Stool.
Don’t: Use a metal bar stool with back and arms support for small spaces.
Metal bar stools with back and arms support may limit the space and are more appropriate for a home kitchen or bar (but this can work if you have swiveling bar stools). As much as possible, choose stools that occupy minimal amount of space, but make sure they’re still comfortable enough to accommodate even people with larger body types.
Do: Go for wooden bar stools if you want a more country and rustic look
Wood and woven stools offer a more traditional feel, usually made of dark woods, painted woods, and sometimes with leather cushion. These stools are the top choice for designers going for the vibe of sports bars, classic 50’s bars, or European-styled restaurants. Nextrend offers several wooden barstools such as the Destiny Barstools.
内容:
|
|
|
Steel Gratings vs Stone Gratings: Which Is Best For You? |
Posted by: aakfk2665s - 08-26-2021, 04:52 AM - Forum: Welcomes and Introductions
- No Replies
|
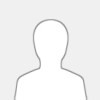 |
Gratings are designed for high impact and high load applications. The most common materials for grates are steel or stone.
Steel grating is an essential structural component of many builds, particularly in commercial and industrial spaces.
Steel is used in grating due to the following reasons:
Strength:
Steel has exceptionally high tensile strength. It is a durable alloy that is made up of active materials that discourage dislocation at an atomic level.
Durability:
Due to its insusceptibility to rot, pests are kept at bay. You can count on steel whether in high heat, extreme cold, gale force winds or torrential rain.
Sustainability:
Steel is one of the world's most recycled materials. It can be melted down and re-fabricated an infinite amount of times without losing its structural integrity and highly sustainable. It has a global recycling rate of 90%. However, some critics have pointed out that the high energy used in melting down the steel for reuse may cause more harm in the long run.
However, there are several downsides to steel gratings, namely:
Susceptibility to theft:
Due to the rising value in scrap metal globally, steel grates have often become a target for theft.
Susceptibility to rust or extremely expensive:
There are several types of steel grates, all of which are susceptible to rust except for stainless steel or galvanized steel. Maintenance costs will need to be taken into account if replacements are required, as rust weakens the metals grates over time. However, if designers choose stainless steel or galvanized steel, they run into the risk of going over their budgets because these metals are costly.
Slippery surfaces:
Some bumpers and designs may be added to increase friction. However, these steel gratings are still very slippery when wet.
Higher heat absorption:
Due to its metallic properties, steel grates tend to absorb and retain heat rapidly. Steel grating could lead to an uncomfortable environment for users over prolonged periods, as the ambient temperature could rise as the day passes.
Not aesthetically pleasing:
There are limitations to colors and design applications for steel gratings. The overall perception of steel gratings is also more industrial-looking and less premium-looking.
Stainless steel is one of the world's most versatile and valuable materials for many good reasons. It can be used in a variety of ways. It is widely used in bathrooms and toilets due to its sanitary value. Here are the top 5 benefits of stainless steel gratings:
Strength:
Stainless steel has a force that can be retained at both high and low temperatures.
Cleanliness:
Stainless steel is one of the most hygienic materials because it doesn't support the growth of bacteria. Also, it is effortless to clean.
Corrosion Resistance:
Stainless steel is very hardy because this metal stands up well against corrosion, rust, and water. A protective film over the metal prevents it from reacting with other organic materials.
Recyclability:
Stainless steel can be recycled, which is great for sustainability efforts.
Durability:
Due to its strength and resistance to corrosion, stainless steel is very durable.
However, as most already know, its biggest drawback is that stainless steel is extremely expensive and will not be feasible for most applications. On top of that, as with other metal grates, stainless steel grates absorb heat rapidly, causing heat rings and may raise ambient temperature artificially.
Mild Steel Grating
These gratings can be used in many different ways. It can keep many chosen structures clean and tidy. However, it has weak tensile strength compared to its counterparts.
Galvanised Steel Grating
Galvanized steel gratings have a glossy look and finish. It is ideal for industrial purposes because of its advantages. Here are some benefits of galvanized steel gratings:
Extended Service Life:
Galvanized steel gratings can last for more than 30 years, even when exposed to the most corrosive environment.
Maintenance Costs:
Its maintenance costs are relatively low because it doesn't need painting and further maintenance.
Scratch Protection:
Galvanized steel grates are protected from scratches or abrasion when they come into physical contact with machinery or footfall.
Adaptability:
This grating could be applied to any structure of any shape and size.
However, it is costly and does not look aesthetically pleasing compared to stone gratings.
Aluminum Grating
Aluminum grating is an ideal choice as it is a lightweight and corrosion-resistant material. We use aluminum for a variety of industrial applications due to its versatility and durability. Again, aesthetics is the main issue with architects.
Steel gratings are the most common form of gratings in the world today. However, many architects are increasingly choosing to use stone gratings over steel grating because of its dramatic style and beautiful aesthetics. With stone gratings, designs can achieve the following effects:
Rust and corrosion prevention
Absorb less heat
Sustain load specification
Achieve greater slip-resistance
Less susceptible to theft
Rise Requirements
The IRC code does not allow a distance greater than 7-? of an inch from one step/tread to the next.
Run Requirements
The “run” is the measurement of the tread, which needs to be a minimum of 10 inches if the tread has an overhang on it (see image). This is a measurement from the nose of the tread to nose of the tread. You are not required to have a nosing/overhang on your stair treads. But if your stairs don’t have a nosing you are required to have a tread that is at least 11 inches long.
Variances
From the top flight of stairs to the bottom of the stairs, each individual riser cannot exceed a difference of 3/8 of an inch.
Nosing Requirements
The nosing on treads, believe it or not, has a code minimum and maximum of how far the nosing projects over the next stair. Nosings are required to overhang a minimum of ?-in. to a maximum of 1-?-in. Also the maximum nosing radius cannot exceed 9/16 of an inch.
Remember to Include Flooring
All of these measurements include the finished flooring, so don’t forget to take those thicknesses into account when planning your stair dimensions.
New anti-slip, non-pinned, self weighted reinforced plastic trench cover
This new Oxford Plastics trench cover has an innovative Flexi-Edge system which greatly reduces trip hazards for pedestrians.
The underside and edge of the Oxford Low Pro are made from a soft flexible material which grips the surface underneath the board and helps to reduce any unwanted movement.
These rubber edges can be replaced and recycled, so you can extend the life of your Oxford Low Pro.
Its innovative design reduces installation time as there is no need to bolt the product down, but is still very stable.
FEATURES AND ADVANTAGES
Heavier that traditional trench covers thanks to its PVC anti slip edge
Central section made from glass reinforced composite
Very stable without bolting
Takes up any cambers in the pavement.
Greatly reduced trip hazard for pedestrians.
Covers a 27.5 in trench.
Supports a weight up to 553 lbs
Shock resistant.
Long lasting product - Flexible edges can be replaced.
Anti-trip flexible edge.
Quick installation - does not need to be bolted down.
|
|
|
How to Choose the Right Bed for Your Bedroom |
Posted by: aakfk2665s - 08-26-2021, 04:51 AM - Forum: Welcomes and Introductions
- No Replies
|
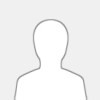 |
Beds – we all love them, don’t we? Getting a good night’s rest is paramount to living a productive and healthy life. It’s important to choose a bed that fits your lifestyle and sleeping preferences. You also want a bed that’s comfortable to lounge in on the weekends.
Choosing a bed is kind of like choosing a sofa. There’s so much to consider about this central and important piece of furniture that it can be quite stressful. Beds are often the focus of a bedroom because they are usually the largest piece of furniture that goes inside one. Because we use them on a daily basis, we really can’t get away with making the wrong decision and just living with it, the way we could with an accent chair or side table.
If you’re thinking about buying a new bed, then this article will help guide you through the process of selecting the right bed for your bedroom and lifestyle habits!
Bed vs. Headboard
The first step in your bed buying process is to determine whether you would like a bed or a headboard.
Beds are great at ensuring a consistent style of design on the whole piece of furniture from the headboard to the feet. They sometimes require a bit more coordination for the installation and logistics. If you want to move a bedroom bed, it’s usually tougher because you would need to take it apart (if you can) and then move each part separately.
On the other hand, headboards will require an attaching a separate bed frame to hold the mattress. Headboards are easier to move around than beds. You can purchase a bed frame that hides underneath your mattress so that the headboard is the only item that you see around your bed. Relocating a headboard and bed frame is typically easier because all you have to do is detach the headboard from the bed frame itself. You can also change out your headboard pretty easily if you want to change the decor style of your bedroom!
Beds are a bit more luxurious and give the bedroom a more complete look. Some people opt for beds in their master bedroom as it is the largest, and headboards in the secondary bedrooms which have less space.
Types of Beds
Platform Bed: Platform beds are great because they don’t require a box spring. They come in a variety of styles to suit your bedroom decor theme. Platform beds typically sit very low off the ground so you’ll have to buy risers if you need room for storage underneath your bed. Because of their boxy nature, platforms are often associated with mid-century modern design. It is often made of wood and finished in a warm brown hue.
Canopy Beds: Canopy beds are great for bedrooms with high ceilings. Canopy beds feature four poles at each corner of the bed connected by four beams. The beams are sometimes left bare and other times, sheer curtains are hung from them, giving privacy to the bed itself. This is definitely one of the larger choices for a bedroom so make sure your room is quite spacious!
Poster Beds: Poster beds, or four-poster beds are made with four poles at each corner. Poster beds date back to the 16th century. The posters at each corner are typically curved, giving them a traditional look.
Bed Materials
Your bed or headboard can be made out of many different materials. Here are a few common ideas for what kind of bed to choose for your home:
Metal Bed
A metal bed is great for a farmhouse bedroom. They give a vintage appeal and look. It is also much easier to clean and take care of than a fabric headboard which tends to attract dust!
Bed Accessories
Once you’ve decided on a bed, there are a few bed accessories you’ll need to consider purchasing.
Box Spring: Box springs are commonly used for support and height for your mattress. They raise your mattress up so you are not getting in to bed at a very low height from the ground.
Mattress: Of course, you can’t purchase a bed without thinking about the mattress you will put on it!
Bed Sheets: Several sets of bed sheets will be necessary for your bed, as well. We recommend purchasing linen or cotton sheets for the spring and summer, and flannel sheets for the cold winters!
Pillows: It’s a good idea to buy at least two pillows for each bed in your home!
Experts agree that getting good sleep is one of the single best ways to maintain and improve our health. A mattress is a huge factor in our ability to sleep well, yet many people overlook its importance and keep using a mattress that fails to provide enough support and comfort.
How to Choose a Mattress
A new mattress can be a sizable investment, but taking this step can unlock your ability to sleep better. As with any major purchase, you want to make sure that you choose wisely.
To help you get a handle on how to choose a mattress, we break down the key information piece-by-piece. With this guide, you’ll have the knowledge to find a top-performing mattress with the right firmness and features to suit your needs and deliver great sleep night after night.
Mattress Types
If you’re just getting started looking for a new mattress, you’ve probably noticed that the number of options can be dizzying. A helpful way to get your bearings is to start by thinking about mattress types.
Almost all mattresses can be identified as one of five types — foam, innerspring, hybrid, latex, or airbed. Innersprings are the most well-known and traditionally were the mainstay in homes nationwide. In recent years, though, other mattress types have surged in popularity.
These other mattress types have expanded their reach primarily by offering a more dynamic performance. They’ve also become more affordable and accessible with the growth of the online mattress industry.
Knowing the basics about each of these types can serve as a foundation upon which you can continue your search for the best mattress.
Foam: Foam mattress is made entirely with foam and no coils. They tend to provide above-average contouring to the body, pressure relief, and motion isolation, making them a good fit for side sleepers and couples. Among foams that are used in these mattresses, memory foam is the most well-known.
Innerspring: An innerspring mattress has a coil-based support system and few other layers. While the coils offer some support, innersprings often lack in pressure relief. Their sleeping surface is bouncier and has limited motion isolation. With a lower price point, these are more popular among budget shoppers.
Hybrid: Hybrids have two central elements: an innerspring support core and a substantial foam comfort system. The comfort layers can include foam or latex, and sometimes will even include a shorter layer of coils (called micro-coils). These mattresses provide a blend of bounce and contouring with low heat retention and can be a good fit for sleepers in any position depending on exactly how they are built.
Latex: When all of the layers of a mattress are made with latex rubber, some call it an all-latex or true-latex mattress. For simplicity’s sake, we just use the term latex mattress. These offer top-notch bounce and durability with moderate contouring. When made with natural and organic latex, they are a top pick among eco-conscious shoppers.
Airbed: Airbeds are built with an air chamber as their support core. A pump — controlled by a smartphone or remote — is built into the mattress to add or remove air with the push of a button, giving sleepers the utmost in firmness flexibility. Couples love airbeds because each side can be set to a different firmness level.
What’s a Pocket Spring Mattress?
A pocket-coil or spring mattress has metal coils or springs, each wrapped in fabric. Pocket spring beds allow the coils to respond with the shape and weight it feels. This is the main difference between pocket spring and open coil mattresses.
Beds with pocketed coil systems differ from traditional spring beds. Innerspring beds feature generalized support, while pocket springs offer targeted support. These beds even have a memory or latex foam comfort layer to add a bit of cushioning to your bed. This kind of pocket spring bed is known as a hybrid mattress.
Pocket Spring Mattresses
Pocket spring mattress responds better to pain from pressure points than innerspring mattresses. They also reduce motion transfer so you can sleep soundly throughout the night.
Combination sleepers are better suited for pocket spring beds. The coil layers provide your bed with plenty of bounce. The added responsiveness makes it easier to switch sleeping positions. Plus, pocket spring beds promote proper spinal alignment.
Couples can also appreciate a pocket coil mattress. Not only does the design promote good posture, but it also isolates movements. One partner’s movements won’t disturb the other’s rest.
The downside of purchasing a pocket spring bed is they do not contour to your curves. Furthermore, some layers consist of wool and other fibers. This can create an environment for allergens and dust mites to settle and grow. The invasion of allergens can ruin your mattress.
|
|
|
Taking an Inside Look at TDMoIP: A Tutorial |
Posted by: pjwij745s - 08-26-2021, 12:46 AM - Forum: Welcomes and Introductions
- No Replies
|
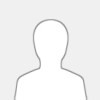 |
Service providers are presently seeking to increase their profits through low cost deployment of voice and leased line services over more efficient Ethernet and IP infrastructures. At the same time enterprises are looking for ways to take advantage of the promise of convergence by integrating their voice and data networks while preserving their investment in traditional PBX and TDM equipment. The voice-over-IP (VoIP) approach is maturing, but its deployment requires a certain level of investment in new network infrastructure and/or customer premises equipment (CPE).
TDM-over-IP (TDMoIP) is a technology that enables voice and leased-line services such as video and data to be offered inexpensively over service provider IP networks while retaining the reliability and quality of the public switched telephone network (PSTN). In this article, we'll discuss the technical challenges inherent in transporting TDM circuits over IP networks, how TDMoIP technology meets those challenges, and the standards shaping TDMoIP and related technologies.
Challenges of Transporting TDM
Conventional TDM networks are highly deterministic. A source device transmits one or more octets to a destination device via a dedicated-bandwidth channel every 125 μs. The circuit delay through a TDM network is predictably low and constant throughout the life of a connection. Timing is delivered along with the data, and the permitted variability (jitter and wander) of TDM clocks is tightly defined. In addition, the infrastructure supports a rich set of user features via a vast set of signaling protocols.
Packet-switched networks (PSNs), such as IP/multi-protocol label switching (MPLS) systems, are more efficient than TDM networks due to bandwidth sharing. However, this sharing leads to PSNs being inherently non-deterministic.
Packets entering and transiting the network must compete for bandwidth and switch/router ports, leading to packet delay variation (PDV) and lost packets. A source device may inject packets into the network at regular intervals, but the network offers no guarantee that these packets will arrive at the destination edge device spaced at the same intervals, in the same order, or even that they will arrive at all.
In addition, IP networks were designed for transport of arbitrary data. Thus, TDM-related signaling is not supported.
There are two main ways that designers are trying to integrate TDM services into IP-based networks. On one hand, designers can completely replace the TDM network and end-user equipment with a new infrastructure that provides innovative mechanisms for voice transport and signaling. The other approach leaves the end-user equipment and protocols intact, tunneling TDM data through the packet network.
In the end, this second approach could provide an easier and most cost-effective migration path for carriers and equipment vendors. With that in mind, let's dive into how TDMoIP works.
Diving into TDMoIP
TDMoIP emulates T1, E1, T3, E3, and N*64K links by adapting and encapsulating the TDM traffic at the network ingress. Adaptation denotes mechanisms that modify the payload to enable its proper restoration at the PSN egress. By using proper adaptation, the TDM signaling and timing can be recovered, and a certain amount of packet loss can be accommodated.
Encapsulation signifies placing the adapted payload into packets of the format required by the underlying PSN technology. TDMoIP encapsulations are presently defined for user datagram protocol (UDP)/IP, MPLS, and Layer 2 tunneling protocol (L2TP)/IP networks, and even pure Ethernet can be utilized with minimal adjustments. Let's take a closer look at adaptation and encapsulation.
How Adaptation Works
TDMoIP can utilize several different adaptation techniques, depending on the TDM traffic characteristics. Whenever possible, TDMoIP draws on proven adaptation mechanisms originally developed for ATM. A side benefit of this choice of payload types is simplified interworking with circuit emulation services carried over ATM networks.
For statically allocated, constant bit-rate (CBR) TDM links, TDMoIP employs ATM adaptation layer 1 (AAL1). This mechanism, defined in ITU-T standard I.363.1 and ATM Forum specification atm-vtoa-0078, was developed for carrying CBR services over ATM.
AAL1 operates by segmenting the continuous stream of TDM data into small 48-byte cells and inserting sequencing, timing, error recovery, and synchronization information into them. For example, if the original TDM stream consisted of a DS1 with channel associated signaling (CAS), the AAL1 adaptation inserts a pointer to the beginning of the next superframe. Thus, even if cells are lost, the pointer will enable recovery from the next superframe.
TDMoIP allows concatenation of any number of AAL1 cells into a packet (note that these are AAL1 cells and not ATM cells, i.e. they do not include the five-byte “cell tax”). By allowing multiple cells per packet, TDMoIP facilitates flexible tradeoffs of buffering delay (which decreases with fewer cells per packet) for bandwidth efficiency (which increases with more cells per packet, due to the per packet overhead).
For dynamically allocated TDM links, whether the information rate varies due to activation of time slots or due to voice activity detection, TDMoIP employs ATM adaptation layer 2 (AAL2). This mechanism, defined in ITU-T standard I.366.2, was developed for carrying variable bit rate (VBR) services over ATM.
AAL2 operates by buffering each TDM time slot into short minicells, inserting the time slot identifier and length indication, sequencing, and then sending this minicell only if it carries valid information. TDMoIP concatenates the minicells from all active time slots into a single packet.
For time slots carrying high-level data link control (HDLC) data, such as data for common channel signaling (CCS), a special adaptation is provided that spots areas of non-idle data, which can then be directly encapsulated.
Encapsulating TDM Data
In TDMoIP packets, payload information is immediately preceded by a control word. This 32-bit control word, shown in Figure 1 , contains the packet sequence number (needed to detect packet re-ordering and packet loss), the payload type, payload length, and alarm indications.
PCM
(1) See phase change memory.
(2) See also PMC ( programmable metallization cell).
(3) (Plug Compatible Manufacturer) An organization that makes a computer or electronic device that is compatible with an existing machine.
(4) (Pulse Code Modulation) The primary way analog audio signals are converted into digital form by taking samples of the waveforms from 8 to 192 thousand times per second (8 to 192 kHz) and recording each sample as a digital number from 8 to 24 bits long (see sampling). PCM data are pure digital audio samples, and they are the underlying data in several music and surround sound formats (see WAV, FLAC, AIFF and surround sound).
Sound Cards Support PCM
For output, a sound card's audio-out port provides an analog signal to the speakers. Compressed formats such as MP3 and AAC are first converted to PCM, and the PCM data are then converted to analog (see D/A converter). Sound cards may also output PCM and other digital signals such as Dolby Digital (see S/PDIF). For input, an analog microphone is plugged into the audio-in port, and the sound card converts the analog signals to PCM.
PCM Ports on A/V Equipment
When ports on set-top boxes and Blu-ray/DVD players are labeled PCM or linear PCM (LPCM), they refer to uncompressed audio channels rather than encoded formats such as Dolby Digital, TrueHD, DTS and DTS-HD. PCM can be mono, stereo or have multiple channels for surround sound. See Bitstream mode and linear PCM.
It Started With the Telcos
PCM was introduced in the U.S. in the early 1960s when the telephone companies began converting voice to digital for transport over intercity trunks. See mu-Law.
Strong Third-Quarter Results
DXC posted earnings of 84 cents a share as revenue fell 14.5% year-on-year to $4.29 billion. Both figures beat consensus estimates. Investors who bought the stock after the report did well so far. The stock is up by around 30% in the quarter. Still, the stock is undervalued, trading at a forward price-to-earnings ratio of 9.79 times.
DXC attributed its stronger adjusted EBIT margin to cost optimization efforts. Book-to-bill of 1.13 times could rise from here. The "new DXC" is gaining momentum and brand recognition:
Source: DXC Q3 Earnings Presentation
Oftentimes, companies in a turnaround spend too much effort on cost-cutting instead of service quality. DXC focused on its customers in the quarter. This led to a stabilization in revenues, earning DXC more work from its existing customer base.
Outlook
DXC will deliver around ~$550 million in cost savings for the fiscal year. In the current period (Q4), expect margins to expand. EBIT margin of 7% posted last quarter should rise from here. Chief Financial Officer Ken Sharp pointed to the new management team led by its Chief Executive Officer, Mike Salvino, in leading DXC's transformation. The enterprise technology stack performance is at the core of DXC's turnaround:
Source: DXC Q3 Earnings Presentation
Quarterly sequential growth will reverse from negative to positive going into Q3/FY2021. DXC's customer relationship building is paying off. Instead of losing customers and watching businesses shrink, the opposite is now happening. For example, DXC's work is from 55% new work and 45% from renewals. And since the renewals are sole-sourced, profit margins improve.
Opportunity
DXC's growth will come primarily from expanding work from existing customers. Around 20% of the customer base needs to move to the cloud over the next two years. Of the 80% remaining, 60% want to see their technology stock modernized.
E1 protection switch allows the user to connect a single E1 line from the telephone company to an "active", as well as to a "standby" E1 terminal, such as data server / router etc. at the customer premises.
In the event of the failure of the data server(s) / equipment connected to the "A / active" ports, the T1 Protection (Fail-Over) Switch shall automatically switch and connect the T1 line(s) from the telephone company to the data server(s) / equipment connected to "B / standby" ports. This ensures minimum downtime -that would have otherwise occurred due to equipment failure. Enhances the efficiency of that network.
Features and Highlights
Allows the user to connect an E1 line from the Telephone Company and to switch it automatically between an "active" and a "standby" E1 terminal at the customer premises. The user programmable switching criterion may be Loss Of E1 Signal, AIS and Loss Of E1 Frame.
Can accommodate upto four E1 lines - may be used switch between "active" and "standby" E1 terminals connected to upto four (or fewer) E1 lines.
Independent switching for each of the four E1 lines.
User programmable switching criterion - independent for each E1 line.
Built-in real-time clock / real-time logging maintains a history of all events.
Remotely accessible over a TCP-IP networks. Allows the user to access and carry out maintenance, or / and switch the E1 line(s) between the "active" and "standby" E1 terminals, remotely, if required.
Allows the users to install and maintain active/standby/duplicate customer premises data networks/data servers, without bearing the recurring $$ expense of leasing additional expensive E1 lines from the telephone company.
Automatically switches the E1 line from the Telephone Company between the "active" and "standby" E1 equipment at the customer premises, according to the customer-programmed criterion.
Improves equipment and data security.
Allows the user to co-locate the "backup / standby" equipment in a different room/building and prevent any data loss arising out of conditions of natural calamity such as fire, flooding etc.
Increases the reliability of the customer's data/IT networks without having to bear the recurring and additional cost of leasing additional E1 lines from the telephone company. The equipment may be used to create secondary/backup systems at the customer premises to provide virtually uninterrupted service.
|
|
|
Valves 101: Two Types of Ball Valves |
Posted by: pjwij745s - 08-26-2021, 12:44 AM - Forum: Welcomes and Introductions
- No Replies
|
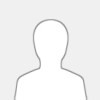 |
Small-size valve balls are a type of piping equipment that shuts off or controls the flow in a pipeline by using a hollow sphere and round seats held in a valve body. There are two basic technologies for the design of ball valves, floating ball design and trunnion mounted ball design.
The major components of a ball valve include:
Valve body – A pressure vessel that contains the components needed to control or shut off the flow through a pipe. It is designed to connect two or more sections of pipe or tubing to each other.
Ball – A sphere with a flow path (hole or tunnel) through the center of it and a connection point for a shaft to rotate it.
Seats – Round donut-shaped discs that form a seal between the body and ball.
Stem – A shaft that connects the internal ball to the outside of the valve to facilitate rotation of the ball.
Packing – Flexible seals that fit around the shaft and prevent the media traveling through the valve from escaping externally.
Bonnet – The part of the valve body that houses the stem and packing.
Operator or Actuator – An external device designed to rotate the stem of the valve. This can be a lever, a gear, a motor-operated gear (electric actuator), or a pneumatic/hydraulic actuator.
Floating Ball Design
A floating design ball valve sandwiches the hollow ball between two or more cupped seats that form a tight seal between the body and the ball at the inlet and outlet ports of the valve body.
The floating valve balls are rotated (usually 90 degrees) by a shaft that protrudes outside of the valve body and is connected to some form of operator. For this reason, most ball valves are referred to as quarter-turn valves. This shaft is not rigidly attached to the ball in order for the ball to pivot on the end of the shaft as it rotates on the axis of the ball. This is usually accomplished with a slot on top of the ball, perpendicular to the ball’s flow path. The cupped portion of the seats cradle the ball prevents it from moving down in the valve body.
The valve packing prevents the media from escaping the valve body through the stem opening in the bonnet. The most common type of packing today is chevron v-ring type packing. If you look at the cross section profile of this packing, it resembles the letter “V”. The outer diameter of the packing matches the bore of the bonnet. The inside diameter matches the outer diameter of the stem. Multiple rings of this packing are stacked on top of each other and the stem is inserted through the packing. A packing gland on top of the bonnet pushes down on the top of the “V” and causes the packing to expand and seals agains the stem and bonnet.
When the ball is in the closed position, the flow path in the ball is perpendicular to the flow path in the valve body. The solid parts of the ball covers both upstream and downstream cupped seat openings. The pressure in the upstream pipe pushes against the solid part of the ball which moves on its pivot point and is forced tightly against the downstream seat. This shuts off flow.
As the operator rotates the ball from the closed position, the ports in the body in relation to the ports in the ball create a variable size orifice which, as it gets larger, will increase the flow through the pipe. When moving from open to close, this orifice gets smaller and decreases flow.
Floating ball design valves are the most economical valves, but are limited by the amount of pressure the seats can handle.
Trunnion Mounted Ball Design
The Trunnion Valve Balls work nearly the same way as the floating ball except the seats are spring loaded against the ball and the ball does not pivot. The ball only rotates on its axis in this design.
In the trunnion mounted ball valve, the ball utilizes a second shaft and bearing on the bottom of the ball. This stem or “post” holds the bottom of the valve in place. The top of the ball is not slotted and the upper stem is rigidly attached to the ball. This prevents the ball from moving into the downstream seat.
Since the ball does not move into the seats, the seats must move towards the ball. Springs behind the seat push them tightly into the ball in order to make the seal.
Trunnion valves are very effective at sealing off very low pressures that would not be strong enough to move a floating ball into the downstream seat. They are also required on large diameter valves and high-pressure valves. The reason for this is the contact area of the seats in a floating ball is relatively small. From physics, we know force = Pressure x Area. The force on the downstream seat in a floating ball is derived from the process pressure in the upstream pipe pushing on the solid area of the ball in the closed position. If the pressure is high or the area is large, the downstream seat will be destroyed.
The tradeoff is that trunnion valves are much more expensive than floating ball designs.
Both floating ball and trunnion designs are available as multi-port valves by using elaborate flow paths in the ball and additional ports in the body.
Are you looking for ball valves for your facility? Our team has years of experience in selecting the perfect valve for any application. Contact us today to discuss your specific valve needs!
HOLLOW VS. SOLID BALL VALVE
The ball valve is available with many different options, and one of the most important distinctions is in how the ball is made. Manufacturers either join two hollow hemispheres or machine a hole through a solid ball. Machining takes more work, but it produces a valve with better flow characteristics. Here’s why.
Ball construction
In a solid ball valve, the hole is the same diameter all the way through. That helps the fluid flow smoothly at a constant velocity. Hollow valve balls are, as the name implies, hollow inside. That creates a bigger space for the fluid to fill, which changes its velocity and creates turbulence.
Turbulence is almost always undesirable. It creates noise and it’s inefficient. The Cv drops, and it takes more energy to pump fluid through the system.
In a few applications, valve weight is an issue. In such cases, the hollow ball may have an appreciable advantage, especially in larger valves.
Solid ball, better flow
When evaluating ball valves, check the Cv values and be sure to compare identical port formats. In most cases, the solid ball will give a higher Cv than the hollow ball.
Advantages of V-Ball Valves
Ball valves are designed to be used in a variety of applications and markets, but V opening valve balls offer the added ability to be used as a control valve where necessary. The main differentiator is a contoured V-port in the ball, most commonly available with a 15°, 30°, 45°, 60°, or 90° angle, which produces an equal percentage flow characteristic for better control. V-ball valves are known to offer a variety of advantages in flow control applications, especially when compared to larger and more expensive control valves.
Low Pressure Drop
The V-port design allows material to flow straight through the valve, minimizing pressure drop across the valve. V-ball valves also have higher flow coefficients (Cv) compared to other control valve types of a similar size; this means that a smaller V-ball valve can be used to achieve the same flow rates as a comparable control valve of a larger size.
Bubble Tight Shut-Off
V-port ball valves use the “floating ball principle, which will provide a bubble tight shut-off in addition to the modulating flow control. When the valve is closed, upstream pressure pushes the ball against the downstream seat, thus enhancing the seal. These can control or shut off bi-directional flow, which proves to be especially beneficial in gas applications. Comparable control valves often require additional shut-off valves; V-ball valves eliminate the need for these additional valves, saving the user cost and reducing the number of overall components in the system.
Precise Flow Control
Precision machined V-ball valves are available with 60° and 90° V openings and offer equal percentage flow characteristics. As the ball rotates, desired flow rates can be achieved by positioning the ball anywhere between 0° and 90°. Response time is also increased due to the ability to use smaller actuators with these valves.
High Shut-Off Pressure
V-ball valves feature a quarter turn (90°) ball rotation, allowing them to operate and shut off at much higher working pressures. Because of this, smaller lower torque actuators can be used, which results in cost savings and higher efficiency in the user’s application.
Ball Valves Defined
Ball valves use a handle to turn a ball in the valve, with a hole or port through it. The ball is used to allow or prevent flow through the valve depending on its position. If the hole is aligned with the pipe, flow continues through the valve; if the hole is perpendicular to the pipe, flow will stop at the valve. It’s really that simple!
Not all ball valves look the same and some have special uses, but they all have the same concept.
Did you know? Ball valves are considered ? turn valves because of the quarter turn that is required to close the valve.
The Benefits of Ball Valves
Easy to see if it is open or closed. When the handle is in line with the pipe you can easily tell that the valve is open; and when the handle is perpendicular to the pipe the valve is closed. This is a great visual indication of whether there is flow through the valve or not.
Operation after years of disuse is easy. The durability of ball valves allows them to work and completely shut off flow after years of disuse. This provides extra peace of mind.
Quick shut off. The motion that is required to operate a ? turn the valve is quick and minimal compared to gate valves. Water hammer is a possibility if the flow through the valve is strong enough to vibrate the line when it comes to an abrupt stop as the valve is quickly shut off.
A more compact and economical valve. Thanks to the design of ball valves they are more compact than gate valves. Gate valves are taller and require more space, as the gate needs a place to go to allow the flow to travel through the valve. By using a rotating ball, ball valves are smaller and require less material.
Different Types of Balls
There are three different types of balls that can be found in ball valves. For each of these three types, the outside of the ball needs to be smooth and the surface gets ground down to remove any dips or imperfections on the surface. As the material cools, the shape may change, resulting in more or less grinding. The three types are hollow, solid, and cored, so let's take a closer look at each of them.
Hollow Ball
The hollow ball has a cavity that goes from an open hole in the bottom of the ball to the top where the valve stem is inserted. Hollow balls require less material to construct, making them more economical, but may require more grinding to get the dips out.
Solid Ball
The solid ball is molded as one solid ball, larger than required, to account for any shrinkage and grinding. Solid balls are usually more expensive to manufacture as they require more raw material and grinding to get them to the perfect round shape.
Cored Ball
The cored ball is cored through the center, leaving a consistent wall thickness around the whole ball. This ensures that the ball cools more evenly, again decreasing the amount of grinding required once it has fully cooled. These types of balls are becoming more popular due to the cost savings compared to solid balls.
|
|
|
Oxygen Absorbers: Their Function and Use |
Posted by: pjwij745s - 08-26-2021, 12:42 AM - Forum: Welcomes and Introductions
- No Replies
|
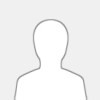 |
Oxygen absorbers are little packets of iron powder packaged in a material that keeps the iron in, but allows oxygen and moisture to enter and be absorbed. The iron absorbs the oxygen causing the iron to rust. As it rusts, or oxidizes, it absorbs any oxygen that may be present.
Why do I need Oxygen Absorbers?
Oxygen and moisture are two factors that destroy the value of dehydrated and freeze-dried foods. Theses elements have a detrimental effect on color, flavor, vitamin content, and fats of stored foods. Oxygen will enhance the growth of insects, bacteria, mold, and yeast in your food, accelerating spoilage. Oxygen absorber help to remove the oxygen in your container, leaving nitrogen. Dry foods are protected against spoilage and bacteria growth in a nitrogen environment. A “nitrogen flush” is often used to force the oxygen out of a product before it is sealed for storage. But even when a nitrogen flush has been done, it's still wise to include an oxygen absorber inside the container to help eliminate any remaining moisture. During the freeze-drying or dehydrating process, much of the moisture causing molding or spoilage is eliminated. An oxygen absorber will help to mitigate any moisture that remains once the food is packaged. Foods with a high moisture or oil content should not be stored in reduced oxygen packaging because it can cause botulism poisoning. Only store foods with in low moisture (10% or less) with oxygen absorbers. Oxygen absorbers actually remove oxygen more effectively than vacuum packaging because they only remove the oxygen rather than all the air.
What Type of Containers do I Need?
[Metallized cans] with seamed lids, [metallized bags], PETE plastic bottles with airtight, screw-on lids, and glass canning jars with metal lids and gaskets all do well with oxygen absorbers. Do not use plastic containers that are not identified as PETE or PET under the recycling triangle on the bottom of the container. Metallized cans and bags prevent light, another source of spoilage, from reaching your food with the added help of your oxygen absorbers. Oxygen absorber packets come in different sizes, two of the most common are 500cc and 2000cc. To decide which size is right for you, consider the size of the container you'll store your food in and the amount of empty space between the food particles and between the top of the food and the lid of the container. Some companies that manufacture absorber packets rate them according to their oxygen absorption capacity in milliliters, while others do so by the equivalent air volume (the actual total amount of air between the product pieces).
How do I Preserve the Life of my Absorbers?
Store unused absorbers in small glass jars that have a lid and ring seal. A one-pint jar will hold 25 absorbers. You can also heat-seal them back into the bag they came in. Or you can store them in plastic freezer bags, but you must use them within the next few months because the plastic will slowly admit oxygen and shorten the lifespan of your absorbers. When using a combo like the Do-it-Yourself Superpail Kit, do not plan to package more food than you can in 20 minutes. Prolonged exposure to air in the room will speed up the demise of your absorbers. Instead, place the number of absorbers you expect to need for one batch of packaging on a tray . Use one absorber per package of food, and work as quickly as possible to preserve the life of the absorbers. When you are ready to do another batch, remove enough absorbers from their bag or jar for that batch. You'll know the lifespan of your oxygen absorber by its color. Some absorber packages turn pink when they're working properly and are still absorbing the oxygen in your can. Some turn purple or blue when they're used up.
COMMON DESICCANTS AND THEIR PROPERTIES
A desiccant is a substance that promotes drying by absorbing moisture or water vapor from the air. Consumers are probably most familiar with small paper packets of desiccants that are often packed with items so that they will not rust or mold during shipment, especially for imported items that will spend time in the hold of a ship between the time they leave the factory and arrive at the store.
In industrial settings, desiccants are used for the same reason in compressed air systems: to dry the air. The changes in pressure when air is compressed will cause water to condense, and this moisture must be removed. To do this, compressed air is passed over desiccant material to dry it out. There are several types of desiccants:
Silica Gel
Silica occurs in nature as Silica dioxide, SiO2. It is processed into gel-like beads for use as a desiccant dryer. Silica gel was first used in World War I to absorb vapor in gas mask canisters. Pure silica gel is one of the few desiccants that is safe for use around food.
Indicating Silica Gel
Indicating silica gel is silica gel that is processed with cobalt chloride. The cobalt chloride will change color from blue to pink as the silica gel absorbs moisture. This ‘indicates’ when the silica gel is becoming saturated. Because cobalt chloride is a heavy metal salt, it cannot be safely used around food.
Clay
Clay that is high in magnesium aluminum silicate, a naturally occurring mineral, is processed into Montmorillonite clay for use in drying. It works best at room temperature or below. Clay is one of the most inexpensive desiccants, which makes it popular for industrial use
Quicklime and Gypsum
Quicklime is a common term for Calcium Oxide. It is alkaline and highly caustic, so special care in handling is necessary. Its chief benefit is that it can be used to gradually drop the humidity to a very low state. Gypsum is Calcium Sulfate.
Molecular Sieve
Molecular Sieve is a synthetic desiccant manufactured from alumino silicates. Like the name sounds, it has many tiny holes or pores the absorb liquid and gas. It is a highly effective desiccant that can absorb water up to 22% of its own weight.
Most of these various types of desiccant dehumidifiers can be recharged and recycled by using a heating process to dry them for reuse.
Ethylene Absorber
Through extensive research, ethylene absorber has been able to provide innovative technologies that extend the freshness and quality of fresh food and flowers. Such thorough research has enabled us to launch our first commercialised product, a discreet but high-tech filter that removes the ripening hormone from around fresh produce.This is helping the global supply chain maximise value from growing, transporting and retailing top-quality produce for consumers, by extending quality, prolonging freshness and enhancing flavour in a secure and sustainable way.
It's Fresh! helps to address the key industry challenges of food security, profitability and global food waste.
It's Fresh! is a division of Food Freshness Technology Holdings a world class business that has invested over $20min areas such as the research and development of unique technologies and delivery systems, to bring to market a range of ground-breaking products that help leading retail groups and their supply chains to make a positive change to the fresh produce industry and to people around the world. These unique technologies are delivered via state-of-the-art materials science developed in partnership with world leading research & technology organisations.
To learn more about our research and what it means for the future of the 'fruit industry', check out our research page here
Our filter absorbs the ethylene gas given off normally as fruit ripens. By capturing this gas (before the fruit does) research has shown that your fruit will be kept in peak condition for longer, naturally. Proven across five continents to reduce waste and costs within the supply chain network It's Fresh! can deliver enhanced yields and returns;
For Growers and suppliers, by helping them to benefit from consistency and management of maturity, reducing grade-outs and rejections to deliver superior quality and extended product life.
For Retailers, by providing extended quality freshness and shelf-life, delivering reduced in-store waste, greater availability on-shelf and increased sales as satisfied consumers return to buy more fruit more often.
CO2 absorber has been used in anesthesiology for many years. However, this process is not limited to this field of medicine. Removing carbon dioxide from human environment is used in other areas as well: mining industry, submarines, scuba diving, space travel and many others. The rationale to remove carbon dioxide from confined spaces is that cannot be eliminated otherwise. Anesthesia practitioners are well aware of this component of the circle system, the carbon dioxide absorber. In daily practice the clinician is less concerned with what kind of substance fills the dedicated canister, as this is usually in the care of the maintenance personnel. The appearance of Sevoflurane and Desflurane, with their own chemical characteristics, prompted the clinician to dedicate new attention to these absorbents. The classical substances used for this purpose are different combinations of limes. The practical concern of the anesthesiologist is to notice when the absorbent is consumed and call for its replacement. Still, many other aspects remain: compound A formation with Sevoflurane, carbon monoxide formation with Desflurane and dry absorbent for instance. The latest member of these products in the medical field is the LiOH carbon dioxide absorbent. Although used for many years in the space exploration, its way into the operating room is a rather recent achievement. Special chemical properties and high absorptive capacity make this new type of absorbent an attractive option for modern anesthesia practice.
|
|
|
How Leak Testing Works |
Posted by: pjwij745s - 08-26-2021, 12:41 AM - Forum: Welcomes and Introductions
- No Replies
|
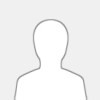 |
Leak testing is a broad term that includes a multitude of technologies. For the purposes of this article, different leak test methods will be referenced but not described in full detail. This article defines the broad term leak test and takes a closer look at the pressure decay leak test method. Furthermore, this article will describe how a pressure decay test works, considerations for the pressure decay method, and how recent technological advancements have impacted manufacturing environments.
What is Leak Testing?
A fixed head leak tester is a procedure used to determine if an object, product, or system functions within a specified leak limit. A leak occurs when a gas or liquid flows through an object via an imperfection or manufacturing defect such as a hole, crack or weak seal. These imperfections create high- and low-pressure zones within a product, forcing the gas or liquid to flow from the high-pressure area to the low-pressure area. The primary leak test method discussed in this article uses pressurized air to identify leaks.
Leak Testing Methods
There are many different types of leak test methods, which have different detectable leak rate limits. This article will primarily discuss the pressure decay leak test method. A pressure decay test identifies if a part is leaking or not within a predetermined leak rate limit. The smallest detectable leak rate for the pressure decay method is 10-4 mbar*l/s or 0.0059 SCCM.
The benefits of pressure decay leak testing include:
Economical
Fast (depending on the internal test volume of a part)
Easy to set up
Only requires compressed clean,
dry air
Quantitative
Nondestructive
No pre or post processing required
Determining a leak rate is vital to selecting the best leak test method.
Typical industries for pressure decay leak test methods include:
Automotive
Sealed Electronics
Medical Devices
Packaging
Consumer Goods
How a pressure decay test works
During a pressure decay test, a product is attached to a leak test system and filled with air. Once pressurized, the air source is closed off and the pressure is allowed to settle. During the test any decrease in air pressure over time signifies a leak.
Variations of pressure decay methods
Pressure Decay – Measures the pressure change of an object under positive pressure
Vacuum Decay – Measures the pressure change of an object under negative pressure
Occlusion – Checks for a blockage in the gas flow path of an object
Burst – A destructive or nondestructive ramping pressure test that measures the point at which the device opens or has a catastrophic event (rupture).
Crack – Typically performed on check valves to detect weeping prior to reaching the opening pressure. A downstream sensor monitors for weeping.
Chamber – Finds leaks in sealed packaging or devices that do not include an opening for filling.
Depending on the functional use of an object or part, any of the above tests may be required.
Considerations for leak testing:
What is the intended use of the part?
What medium is being constrained inside or outside of a part? A medical device manufacturer designing an IV set may try to keep saline inside the IV set. An automotive manufacturer may have designed their manifold to prevent exhaust gases from escaping the exhaust manifold. An acceptable hole or porosity in these parts is contingent upon the application by which a leak limit will be determined.
Medium
An oil molecule is larger than a water molecule and a water molecule is larger than an air molecule. If an eight micron hole is subjected to 45 psi of pressure, air will create a noticeable leak, whereas water will only create a droplet and oil may not leak at all.
What pressure range is a part subjected to during use? What safety factor is required? Finding the appropriate pressure range for an application is vital. If the test pressure is too low, quality may be affected, and faulty parts may pass the leak test and go on to fail during use. Conversely, selecting a pressure range that is too high will extend the time it takes to complete the test and possibly damage the part.
Internal Volume
The test volume plays a significant role in creating a repeatable and sensitive test. Reducing the overall volume enables shorter test times with greater sensitivity. Parts that cannot have a volume reduction will benefit from pneumatic and sensor assemblies appropriately sized to meet test cycle expectations.
Acceptable Leak Rate
Everything leaks but what leak rate is acceptable for an application? Leak rates are most often specified by regulatory requirements specific to an industry. Often when testing a new product some trial and error is involved in finding what leak rate is acceptable for the product’s application.
Material
The material of the part under test affects test time. Compliance influences both the fill and settle steps in a leak test. If a malleable object is subjected to pressure and is not given enough time to settle before a test begins, the part may be expanding or contracting during the leak test, yielding inconsistent results.
Design
During the design and development of a product it is important to consider the test criteria to ensure a part has been manufactured correctly. Design criteria such as test pressures, access ports, shared walls or vessels, internal test volumes, and leak rate specifications all have an impact on the complexity and time required for a leak test. How the object connects to a leak test system helps to determine what kind of leak test will be run on the object. A fully enclosed object with no port to fill the item, such as a waterproof enclosed electronic device, requires a chamber test which includes a sealing fixture. An object with one port or opening, such as a catheter, can be directly connected to the front port of a leak tester without a fixture.
Conveyor has been a staple in the materials handling industry for decades. As the demand for reduced cost, increased throughput and integrated automation grows, so does the need for conveyor systems of all types.
Conveyor is available in many styles and is used in countless applications. In this Equipment 101 article, Modern spotlights the basics of some of the most common conveyor types:
? Non-powered skatewheel and roller conveyor
? Powered, or live, belt and roller conveyor used in handling packages and other small products
? Powered chain and roller conveyor used in handling pallet loads of goods
NON-POWERED CONVEYOR
Non-powered conveyor, the simplest form of conveyor, uses the natural forces of inertia and/or gravity to keep products moving.
Portable sections of non-powered conveyor are often used for loading packages onto the back of an over-the-road truck. Non-powered conveyor can also serve as takeaway conveyor for cartons coming out of an automated sorter, and it’s often used in workstations and pick modules where employees complete their tasks and then push their work along to the next zone or station. The two most common types of non-powered conveyor are skatewheel and roller.
Skatewheel conveyor
Only a little energy is needed to turn the small wheels of a skatewheel conveyor, and that makes skatewheel good at maintaining the speed of a product. Because each wheel turns independently, skatewheel conveyor is also a good choice for the curved sections of a conveyor line.
Roller conveyor
Non-powered roller conveyor is commonly used for workstations and pick modules because it provides a better working surface and is often less expensive than skatewheel conveyor. It’s also good at slowing the inertia of products coming out of a high-speed sorter.
Whether it’s skatewheel or roller, non-powered conveyor that relies on gravity to move product is still used a lot in the market, says Russ Devilbiss, sales manager for Carter Controls and chair of the Material Handling Industry of America’s (MHIA) Conveyor & Sortation Systems industry group. The limitation with non-powered conveyor, however, is control. “With gravity, you can’t control the force, and you always want to be in control of your product,” says Devilbiss.
POWERED PACKAGE-HANDLING CONVEYOR
When it comes to moving packages and other relatively small items, two styles of conveyor dominate the market: belt conveyor and powered roller conveyor.
Traditionally, belt conveyor has been used for transporting products, while roller conveyor has been used for accumulating products.
Another factor taken into consideration when choosing between belt or roller conveyor depends on the size of the product being moved.
Belt conveyor
In traditional belt conveyor, an AC motor drives a pulley that then turns a long, looped belt. Underneath the belt sits either a bed of non-powered rollers or a sheet of metal known as a slider bed. The belt can be made of a variety of materials with a variety of surfaces, depending on the items it is intended to convey.
For example, according to Ken Ruehrdanz, warehousing and distribution market manager for Dematic, a belt surface can be smooth where you need to slide an item off a conveyor easily or ribbed to give it more gripping power, like on inclines and declines.
And, belted incline or decline conveyor can be used to move product from one level of a facility to another. Spiral conveyor is another way to move product from one level to another. If floor space is limited, spiral conveyors are often a good solution.
Regardless, traditional belt conveyor is a simple, time-tested technology. It’s less expensive than powered buffer conveyor, it provides a more stable surface, and it can convey a variety of products. Poly bags, envelopes and electronics are examples of products handled easily by belt conveyor that are often too small or too light to be conveyed directly on rollers.
Roller conveyor
Despite the advantages of belt conveyor, many of today’s distribution centers are filled with roller conveyor because it allows accumulation of products. Accumulation is a way to make the conveyor store product for a determined amount of time then released into an automated sorter or palletizer, for example.
Zero pressure accumulation means products on the conveyor do not touch each other. Minimum pressure accumulation, however, allows the products to make contact, but with a determined degree of impact that will not cause damage.
Powered roller conveyor falls into a number of different categories, depending on the way the rollers are driven. Three common categories are line-shaft, belt-driven and motorized roller.
Line-shaft conveyor: In a section of line-shaft conveyor, a long metal shaft runs below the bed of rollers. Rubber o-rings connect the rollers to the shaft so that when the motor turns the shaft, the shaft turns the rollers.
Line-shaft conveyor is the least expensive type of roller conveyor. It has been in the market for a long time, but it has limitations. Even though line-shaft flexible conveyor costs less, explains Don Erickson, director engineering for Automotion, it is parts-intensive, which leads to high maintenance requirements.
|
|
|
Monitor Display Panel |
Posted by: pjwij745s - 08-26-2021, 12:40 AM - Forum: Welcomes and Introductions
- No Replies
|
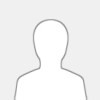 |
BOE monitor display panels cover a full range of products from 18.5 inches to 43 inches, with high image quality, wide viewing angles, high refresh rate, low power consumption, a borderless design, and other features. Resolution of up to 8K can be achieved. The products are widely used in entertainment, office, professional design, and other fields.
BOE LCD panel offers super sharp pictures and great color. But do the pros outweigh the cons when it comes to LCD TV displays? Before deciding on a thumbs up or thumbs down, you should understand how an LCD display works.
Liquid crystal display (LCD), electronic display device that operates by applying a varying electric voltage to a layer of liquid crystal, thereby inducing changes in its optical properties. LCDs are commonly used for portable electronic games, as viewfinders for digital cameras and camcorders, in video projection systems, for electronic billboards, as monitors for computers, and in flat-panel televisions.
Electro-optical effects in liquid crystals
Liquid crystals are materials with a structure that is intermediate between that of liquids and crystalline solids. As in liquids, the molecules of a liquid crystal can flow past one another. As in solid crystals, however, they arrange themselves in recognizably ordered patterns. In common with solid crystals, liquid crystals can exhibit polymorphism; i.e., they can take on different structural patterns, each with unique properties. LCDs utilize either nematic or smectic liquid crystals. The molecules of nematic liquid crystals align themselves with their axes in parallel, as shown in the figure. Smectic liquid crystals, on the other hand, arrange themselves in layered sheets; within different smectic phases, as shown in the figure, the molecules may take on different alignments relative to the plane of the sheets. (For further details on the physics of liquid crystalline matter, see the article liquid crystal.)
The optical properties of liquid crystals depend on the direction light travels through a layer of the material. An electric field (induced by a small electric voltage) can change the orientation of molecules in a layer of liquid crystal and thus affect its optical properties. Such a process is termed an electro-optical effect, and it forms the basis for LCDs. For nematic LCDs, the change in optical properties results from orienting the molecular axes either along or perpendicular to the applied electric field, the preferred direction being determined by the details of the molecule’s chemical structure. Liquid crystal materials that align either parallel or perpendicular to an applied field can be selected to suit particular applications. The small electric voltages necessary to orient liquid crystal molecules have been a key feature of the commercial success of LCDs; other display technologies have rarely matched their low power consumption.
Mechanics of an LCD display
The LCD consists of a large number of pixels, or picture elements, consisting of liquid crystal molecules held between two sets of transparent electrodes.
The liquid crystals react in predictable ways when the electrical charge running between those electrodes is changed — meaning they twist and move in ways that let different amounts (and colors) of light through the crystals. The LCD has a control system that translates your video signals into the proper charges for each electrode. A light source shines through the TV LCD panel and creates your picture.
When compared to the other type of flat-panel display (plasma), LCDs tend to be found on the smaller size of the spectrum. You’ll rarely find a plasma TV smaller than 42 inches, but you can find LCDs at sizes as small as 13 inches.
Benefits of LCD displays
LCD displays have some strong points when it comes to playing video:
· Extremely high resolutions: LCDs can easily reach HDTV resolutions (in fact, most LCD displays do). You can find a 1080p-capable LCD display in all but the smallest sizes — while many plasma displays are still 720p.
· Excellent color: LCDs offer exceptional reproduction of colors, with the potential for beautifully re-created colors across the spectrum. This differs from other flat-panel displays (such as plasma systems), which often tend to display certain colors inaccurately.
· Great picture: The newest and most expensive LCDs use an LED (light emitting diode) instead of a traditional bulb for their light source. These LEDs produce a higher-quality picture because the LED itself emits a more natural (closer to daylight) light than a bulb (which tends to be yellowish, not true white).
· Energy efficiency: LCD HDTVs are perhaps the greenest HDTVs. Compared to plasmas, LCD HDTVs use less electricity to run. You can probably expect to use about 30 percent less power for an LCD than for a similar-sized plasma.
· PC monitor-capable: Most LCD television displays can also do double-duty as a PC monitor, plugging directly into any PC with a standard PC video cable.
· No burn-in: If you play a lot of video games, watch the stock ticker on MSNBC, or do other things with your display that involve a lot of static content (images that don’t change or move around) on a CRT display, you can end up with those images permanently burned into the phosphors on your screen. Because LCDs use a separate backlight instead of creating their own light with phosphors, they are immune to this problem (plasmas are not, by the way).
· Inherently progressive: Unlike direct-view systems, LCDs don’t display their picture using electron guns scanning lines across a screen. Instead, LCDs use millions of tiny transistors that can be individually controlled by the “brains” inside the display. This means that LCDs can easily handle progressive-scan sources, such as progressive-scan DVD and HDTV.
We learned in school that there are three common states of matter: solid, liquid or gaseous. Solids act the way they do because their molecules always maintain their orientation and stay in the same position with respect to one another. The molecules in liquids are just the opposite: They can change their orientation and move anywhere in the liquid. But there are some substances that can exist in an odd state that is sort of like a liquid and sort of like a solid. When they are in this state, their molecules tend to maintain their orientation, like the molecules in a solid, but also move around to different positions, like the molecules in a liquid. This means that liquid crystals are neither a solid nor a liquid. That's how they ended up with their seemingly contradictory name.
So, do liquid crystals act like solids or liquids or something else? It turns out that liquid crystals are closer to a liquid state than a solid. It takes a fair amount of heat to change a suitable substance from a solid into a liquid crystal, and it only takes a little more heat to turn that same liquid crystal into a real liquid. This explains why liquid crystals are very sensitive to temperature and why they are used to make thermometers and mood rings. It also explains why a laptop computer display may act funny in cold weather or during a hot day at the beach.
Drawbacks of LCD displays
Consider the following problem areas before you buy an LCD system as your primary display in a home theater:
Slightly more expensive for their size: Inch for viewing inch, LCDs tend to be a bit more expensive than plasma flat-panels.
Poor reproduction of blacks: Compared with direct-view tube displays, LCDs do a poor job of reproducing black images. Darker screen images never show up as true black, but rather as various shades of gray, and actions happening in these darker areas are difficult to discern.
Limited viewing angle: Although they are getting better due to some intensive efforts by manufacturers, LCDs typically have a poor viewing angle. If you are not sitting almost directly in front of the screen, you don’t get a good picture.
Limited brightness: Because LCDs use a backlight shining through the liquid crystal, most of the light is absorbed. As a result, the LCD displays have lower contrast and are harder to view in a brightly lit room (the picture appears washed out), compared with plasma TVs. LCD TVs with LED backlights do better in this regard.
SEOUL (Reuters) - Samsung Electronics’ display unit said on Tuesday it will extend production of liquid crystal display (LCD) panels for TVs and monitors, as more people sought home entertainment during the coronavirus pandemic.
Samsung Display’s decision to extend LCD production in South Korea for an unspecified period of time overrides its announcement in March that it would end all production by the end of the year to focus on more advanced technology.
Samsung Display said the length of the extension would depend on profitability considerations and market conditions. It had said in late October that it was considering a “short-term” extension.
Local media outlet IT Chosun reported earlier on Tuesday that production would be extended by a year at the request of Samsung Electronics’ set manufacturing division, citing unnamed tech industry sources.
A spokeswoman for Samsung Display declined to comment on the IT Chosun report.
The stay-at-home trend sparked by the coronavirus pandemic led to a 30% quarter-on-quarter spike in global panel demand in the third quarter of the year amid more TV and notebook demand, according to technology research firm TrendForce.
However, the firm added that the influx of more production capacities from Chinese LCD makers was likely to worsen a supply glut next year.
SAMSUNG LCD panel is in both South Korea and China, but it earlier this year sold a majority stake in its Suzhou LCD production unit to TCL Technology Group Corp’s China Star Optoelectronics Technology unit.
LG Display has changed its CEO in its bid to reorganise its businesses amid declining LCD profits and lackluster OLED display panel sales.
The company, which is the display panel-making affiliate of LG Group, approved the motion to name LG Chem President Jeong Ho-young as its new CEO in an emergency board meeting on Monday, LG Display said in a statement.
Current CEO and Vice Chairman Han Sang-beom had expressed his desire to resign in order to take responsibility for the company's recent profits decline, LG said.
Jeong is expected to officially take over the CEO position in the shareholders meeting in March next year but will become the acting CEO on Tuesday.
The move is highly unusual as it normally makes leadership changes during its group-wide year-end reshuffle.
LG Display had once been a profit darling for the group, but its fortunes have drastically changed since 2018 from intensifying competition in both its traditional LCD business as well as the newer OLED one.
It is losing out to Chinese rival BOE in the LCD market, while its large-sized OLED display panel business has suffered from slower than expected sales from increased competition by Samsung's QLED counterpart.
LG Electronics' TV business saw its operating profit halved in the second quarter from slower than expected OLED TV sales.
In regards to the small-sized LCD and OLED display panels used in smartphones and tablets, Chinese clients are increasingly relying on local suppliers over LG. At the same time, the South Korean tech giant cannot match Samsung's volume and yield rate when it comes to providing display panels for the more profitable mobile OLEDs.
LG Display posted operating losses of 369 billion won in the second quarter of 2019 with revenues of 5.35 trillion won, which was much lower than analysts' expectations.
But the company has increased the production capacity of its OLED factories in China and South Korea, with the goal of moving 10 million large-sized panels by 2022 to decrease unit cost and increase sales.
LG Display has also commenced the restructuring of its LCD business, halting some of its factory lines and lowering production output, and will likely now make even tougher measures under new leadership.
RELATED COVERAGE
LG's Q2 profit drops due to low OLED and mobile sales
LG's second quarter profit saw a 15.4% decline from lower TV profits and sales and losses from mobile, but overall sales increased 4.1% thanks to record sales from its home appliances business.
LG's OLED TV strategy needs to change or face mobile's plight
LG's second quarter profit has been hit hard by declines in OLED TV sales and rival Samsung's QLED onslaught. It's time for LG LCD panel to drop its over-confidence and pursue a more aggressive pricing model and better warranties for its OLED TVs.
Fear and Trembling: LG Display faces the axe for OLED burn-in and market squeeze
After seven years of ignoring the warning signs, LG Display's OLED TV panel business is facing a reckoning by LG Group's leadership and the market as rival Samsung jumps to MicroLED and QD-OLED panels.
LG to unveil V60 ThinQ smartphone at IFA 2019
LG has sent out an invitation for the unveiling of its yet unnamed next flagship smartphone to take place at IFA on September 6 that hints at strong gaming feature and dual-screen support.
Samsung, Huawei, LG, and Sony phones vulnerable to rogue 'provisioning' messages
Fake phone provisioning messages can allow hackers to hijack email or web traffic from legitimate devices. Nearly half of all Android smartphones impacted.
|
|
|
|