Welcome, Guest |
You have to register before you can post on our site.
|
Online Users |
There are currently 276 online users. » 0 Member(s) | 274 Guest(s) Bing, Google
|
Latest Threads |
Dominica visa free countr...
Forum: Off Topic
Last Post: axied12
06-24-2025, 12:37 PM
» Replies: 0
» Views: 207
|
Advanced microneedling
Forum: Off Topic
Last Post: axied12
05-28-2025, 01:25 PM
» Replies: 0
» Views: 333
|
Caviar and cheese
Forum: Off Topic
Last Post: axied12
05-28-2025, 12:38 PM
» Replies: 0
» Views: 294
|
Top-rated countertop comp...
Forum: Off Topic
Last Post: axied12
05-04-2025, 06:42 AM
» Replies: 0
» Views: 447
|
Ryanair letenky levně do ...
Forum: Off Topic
Last Post: axied12
02-11-2025, 01:37 PM
» Replies: 0
» Views: 838
|
Trusted essay writing ser...
Forum: Off Topic
Last Post: axied12
01-30-2025, 08:16 AM
» Replies: 0
» Views: 754
|
Bootverkopers - actieve j...
Forum: Off Topic
Last Post: axied12
12-07-2024, 11:07 AM
» Replies: 0
» Views: 881
|
Services for individuals ...
Forum: Off Topic
Last Post: axied12
12-02-2024, 03:31 PM
» Replies: 0
» Views: 856
|
Used excavators
Forum: Off Topic
Last Post: axied12
11-13-2024, 09:22 AM
» Replies: 0
» Views: 802
|
Buy Higo Rocket in Dubai
Forum: Off Topic
Last Post: axied12
10-25-2024, 01:09 PM
» Replies: 0
» Views: 911
|
|
|
How to Choose a Backpack |
Posted by: pjwij745s - 08-26-2021, 12:38 AM - Forum: Welcomes and Introductions
- No Replies
|
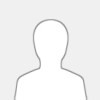 |
Planning to buy a new backpack for backpacking? There are three main areas where you’ll need to make choices.
Backpack capacity: The size of the pack you’ll need is tied to the length of your trip and how much weight and bulk you want to carry.
Backpack features: These are the refinements that affect how the pack works for you.
Backpack fit: Torso length—not your height—matters most.
Frame Type
Internal-frame backpacks: The majority of packs sold at REI today are body-hugging, internal-frame packs where the structure is hidden inside the back panel. They are designed to keep a hiker stable on uneven, off-kilter terrain and may incorporate a variety of load-support technologies that all function to transfer the load to the wearer’s hips.
External-frame backpacks: With an external-frame pack, you can see the structure that supports the load: aluminum (usually) hardware on the outside. Because the frame extends beyond the packbag, a backpack like this may be an appropriate choice if you’re carrying a heavy, irregular load (like an oversize tent or inflatable kayak). External-frame packs also offer good ventilation and lots of gear organization options.
Frameless backpacks: Ultralight devotees who like to hike fast and light might choose a frameless pack or a climbing pack where the frame is removable for weight savings. But packs without a frame are much more uncomfortable under heavy loads.
Ventilation
Some packs feature a suspended mesh back panel to combat the sweaty-back syndrome you tend to get with internal-frame packs that ride against your body. Also called a “tension-mesh suspension,” this is a trampoline-like design where the frame-supported packbag rides a few inches away from your back, which instead rests against the highly breathable mesh. Other packs will have ventilation channels (sometimes called “chimneys”) in the back panel to solve the same issue.
Why the Shoulder Bag Is Perfect for Post-Pandemic Life
The shoulder bag is back. As we reemerge—whether that entails a return to office life, resuming dinner dates with old friends, or planning travels for the summer—there’s an appetite for the best slouchy handbags that are soft yet comfortable to carry. Recently during the resort 2022 collections, Louis Vuitton made a case for the silhouette, as did Khaite and Balmain, which showcased their own iterations on the catwalk: Louis Vuitton presented its signature monogrammed versions, Khaite displayed its classic minimalist take, and over at Balmain, slouchy bags were oversized and front and center. And just last week Altuzarra released its new Duo bag collection, which features its own unstructured shoulder bag. Altuzarra’s version, however, takes it a step further by offering it in a reversible option—why choose just one color when you can have two?This accessories trend seems to wink at the comfort we’ve all been seeking as of late. We need practicality in our handbags, but that doesn’t mean they can’t be cushy and soft. Just as our wardrobes are shifting from cozy pajamas to double-duty dresses and our winter slippers to summer shoes, we’re all looking to ease back rather than rush. Ahead, shop 24 of the best slouchy handbags for post-pandemic life, perfect for all occasions—work, play, travel, and beyond.
What is a hobo bag?
While hobo bag is characterized by its crescent shape, slouchy posture and a long strap designed to be worn over the shoulder. This type of bag is typically large-size and are made from soft, flexible material that tends to slump or slouch when it is set down.
This bag is called hobo bag since it looks the same shape with the bindle on a stick that hobos are portrayed as carrying over their shoulder in cartoons and drawings.
But if you are getting bored with your regular totes, satchels and other purses, a Hobo bag can be an exciting addition to your collection. Legend has it that a late fashionista took note from the cartoon characters, the hobos, and tied her belongings in a stylish handkerchief, giving birth the hobo bag.
WHY IS IT CALLED A BUCKET BAG?
Wondering why is it called a bucket bag? Simple! The bag literally resembles a bucket with its roughly cylindrical shape, deep interior and tall sturdy sides. Typically, the bucket bag’s wide brim is closed by a convenient drawstring that makes it easy to use.
WHAT IS A BUCKET BAG?
The bucket bag might look as striking as any totally modern and fresh style, but actually, it’s been around for quite a while.
Major names in fashion have been playing around with versions of the bucket bag since the 1940s. One of the first bucket bags to popularize the style, from Hermès, took the name quite literally. They removed the bag’s typical drawstring and used stiff material to design a look essentially indistinguishable from a bucket tooled out of leather.
With contemporary brands always looking to re-image dazzling silhouettes, the bucket bag has undergone many transformations. It came back onto the radar of fashionistas in a big way when Mansur Gavriel, a New York City brand founded in 2012, introduced their own take on the bucket bag. Their take on the bag was refined, but still glittering with personality—a perfect companion to anyone who dresses with intention.
HOW TO WEAR A BUCKET BAG?
This quirky but somehow still oh-so elegant bag has quickly made its name as a cult favorite. Since the fashion world fell back in love with bucket bags, designers have been putting their own twist on the look, softening the shape to create a more elegant look or applying minimalism to create a more stripped-down statement piece.
There is really no wrong way to wear a bucket bag. You have to love its versatility. Because it is the bag’s shape, not material or print that defines what is a bucket bag, there is endless room for brands to bring their own take to the design.
Some bucket bags, like Hozen’s mini bucket bag come with two straps so that the silhouette can be adjusted to different lengths to make it a perfect partner for a variety of styles. Whether you want to wear it as a chic shoulder bag, or as a longer across the body bag, the bucket shape can fill out any outfit perfectly. Plus, the utility of the design has been modernized with super user-friendly features like drawstrings and weather-proof materials.
Bucket bags are a great choice for a weekend get-away because their functional size can easily fit everything you need in the interior’s ample storage space. The wide and round top also makes it a great beach-side companion because it’s easy to access your phone or lipstick without having to dig around and risk dragging in dreaded sand.
ARE BUCKET BAGS IN STYLE?
Even though the design-new PU bucket bag has a rather minimal shape, it can be endlessly customized to suit any style. From bright and bold patterns to vegan eco-friendly leathers, to canvas and woven raffias, there’s a bucket bag out there for every look.
The bucket bag is the perfect solution for girls who prefer bold individual looks but cannot afford the high price tags of adventurous bags that might quickly go out of style. The timeless quality is essential to what is a bucket bag.
Because the bucket bag can so easily be re-imagined by fashion brands, it’s an amazing opportunity for eco-conscious designers to introduce looks that are just as ethical as they are cute. At Hozen, their delightful stripe bucket bags are made of pi?atex, a leather look-a-like that’s made from recycled pineapple crop. As times change, innovative future-thinking designers will keep bucket bags in style.
ARE BUCKET BAGS MORE OF A SPRING OR A WINTER ACCESSORY?
The minimal look can be dressed down or dressed up—and shines in every season. In dark winter colors or light flirty spring patterns, this classic look seems to radiate style.
Something to love about bucket bags is that most have minimal logos and do without signature patterns that would detract from the individuality of the person who is wearing it. Just another reason the bucket bag is oh so desirable.
So rain or shine, snow or sun, these sleek, utilitarian bags won’t be going out of style anytime soon. They may have been a hit on spring runways last year, but their timeless shape can be worn effortlessly even in the dead of winter.
CONVINCED YET
Bucket bags aren’t exactly new, despite what trend-setters might have you think. They are one of those classic shapes that will always appeal to lovers of beauty. So, when the twenty-first century fell back in love with the bucket bag, we fell hard.
These days, it’s almost impossible to walk into a top fashion brand’s store without seeing one. The classic drawstring PU bucket bag is undeniably a solid choice investment for the new decade, as one of spring’s most coveted trends.
Whether you like to keep things classic, experiment with bold prints and patterns, or if you are the kind of person who goes for an elegant formal look, then our vegan leather bucket bags are an excellent choice. From high couture to lifestyle wear: the bucket bag has a place in every closet! Curious about vegan leather? Then head this way to learn more about vegan leather and the benefits.
|
|
|
Indoor And Outdoor LED Display(s): How Are They Different? |
Posted by: pjwij745s - 08-26-2021, 12:37 AM - Forum: Welcomes and Introductions
- No Replies
|
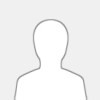 |
LED displays are versatile communication tools. Businesses speak to their clients via these amazing LED billboards and screens. These displays also serve educational and awareness-building objectives. The outdoor screen displays are often used as highway billboards, in stadiums and during outdoor celebrations, while indoor LED screens are widely used inside places of worship, offices, conference halls, restaurants, malls and retail outlets. Other applications of LED displays are in retail, transportation, sports arenas, corporate campuses, institutions of higher education, at gaming hubs and casinos.
Indoor LED display screens also provide seamless displays that are ideal for ambient lighting and shorter viewing distances. LED video walls make the indoor environment more interesting by delivering a spectacular viewing experience—in retail stores, corporate lobbies, etc.
Besides typical indoor and outdoor LED display screens, there are also semi-outdoor screens. These are seen in open halls, under eaves, sometimes beneath sun roofs or even under an outdoor canopy. However, despite giving the same ultra-high brightness as outdoor LED displays, these semi-outdoor screens are not resistant to adverse weather conditions.
Differences between indoor and outdoor LEDs
Outdoor LED screens are mostly used at venues where a mega show is on—for brand advertisements, for instance, as they can offer full colour and very high brightness. Indoor LED screens, on the other hand, cannot address the needs of mega outdoor display projects but are ideal for indoor applications. They offer better spectrophotometric colour. Besides this, they also provide high colour saturation.
The factors that differentiate outdoor and indoor LED displays are explored in this article.
Brightness
This is undoubtedly one of the striking differences between indoor and outdoor LED display screens. Bright sunlight can make it difficult to read dull or less bright LED signs. Thus, to provide ultra-high brightness, outdoor LED display screens are power-packed with many bright LEDs in one pixel. Since indoor signs are not viewed under the harsh glare of the sun, they need to be less bright, by default. Outdoor displays offer several times more brightness than indoor LED screens. Brightness is measured by units called nits or candelas per square metre. The higher the luminosity level, the higher the level of brightness.
Resilience to external weather conditions
Outdoor LED display screens should be highly leak-proof, waterproof, dust-proof, readable in sunlight, anti-lightning and resistant to high temperatures. Indoor LED display screens do not need to offer the same resistance to the outside environment and hence do not come with such features. The outdoor LED screens normally have IP65 water-proof levels while indoor screens have IP20 waterproof levels.
Display resolution
Outdoor LED screen displays will be typically viewed from further distances as compared to their indoor counterparts, thus they have a lower resolution. Since the distance between the viewer and an indoor LED screen is shorter, typically, the resolution for indoor LED displays needs to be high. The greater the resolution the better the picture quality. The pixel pitch, which describes the density of the pixels on an LED display, is another differentiating factor between indoor and outdoor display screens. Outdoor displays have a larger pixel pitch and a lower resolution, whereas indoor displays that need a high resolution for close viewing have a smaller pixel pitch.
Points to remember while choosing LED moving displays
Indoor LED screen displays can be designed in several ways, depending upon the configuration and architectural needs. This is because they don’t require a cabinet for installation. On the other hand, outdoor LED signs cannot be assembled panel by panel on the site. The entire installation is based on the design (as a sign or billboard) or is placed on a building.
The type of LED display chosen should depend on whether it will be positioned indoors or outdoors. Then factor in the size of the placement area or installation site, check if there is a remote control requirement via a PC, and find out the minimum or least viewing distance. The default design of indoor LED display screens is for easy and rapid integration with several input resources and third-party players. However, outdoor LED screen displays need a rugged regulator or controller for playback purposes. They are normally regulated via a copyrighted software suite, which also provides remote access along with sign diagnostics.
Screens with higher brightness are costly and consume more electrical power. Hence, it is important to choose a screen with the right brightness for your needs, so that you don’t pay more for something that is not necessary. Non-weatherproof small pitch LED screen uses LEDs with lower light output, but water-resistant outdoor LED screens need to use brighter LEDs.
Growth in the outdoor LED display market
The outdoor LED display market is expected to boom by 2021.
All outdoor LED displays offer the primary features of energy efficiency and durability. Governments across the globe, like in India, China, Malaysia and the GCC (Gulf Cooperation Council) countries, are encouraging energy conservation measures. LED displays to reduce power consumption considerably. These countries are also formulating regulatory policies for a flourishing LED industry.
Modern multiplexes and shopping malls incorporate LED displays as an integral part of their overall design. Outdoor LED displays that deliver dynamic and audio-backed content are more attention-grabbing. Businesses invest heavily in LED displays to grab the maximum attention of their customers. The huge screens that show flashy images along with thunderous sounds never fail to catch the attention of visitors in a mall.
Real-time advertising has further increased the demand for outdoor LED screens. The advertisers carefully monitor their clients’ choices, the market trends as well as consumer responses to the messages displayed and can alter the content accordingly.
Indoor applications of video walls are diverse, as can be seen in transportation (airports, bus terminals, subways, etc), which was an early adopter. However, there’s been increased adoption of these walls at shopping malls and other retailers, hotels, casinos, museums and galleries.
Robust high brightness outdoor LED walls are designed to convey information in a visually appealing manner even in tough outdoor conditions like extreme heat, rain and dust. Unlike other conventional displays, these video walls are highly customisable in shape and size and provide daytime visibility even under direct sunlight.
Indoor And Outdoor LED Display(s): How Are They Different?
Outdoor LED billboard, screens and other products are getting more popular by the day. LED displays have become an important part of the way modern businesses communicate with their customers. Their high brightness, low power consumption, and longer shelf life are just some of the characteristics that give them an edge over the earlier LCD screens. Indoor LED displays, however, are different from outdoor displays in a number of ways.
What are the main 3D technologies for 3D LED displays?
The 3D LED display can express the details of dark and light parts incisively and vividly. It is characterized by high refresh, high gray scale and high contrast, so that the audience can enjoy the content with the immersive experience effect of scenery but no screen in their eyes.
3D LED display is a kind of 3D effect on the screen that can be viewed with naked eyes without wearing professional glasses. The effect presented by the naked eye 3D LED display is very realistic, which can perfectly display the broadcast content and attract the eyes of pedestrians.
As a brilliant LED display in the display market in recent years, with its more and more into the indoor high-definition display field, how to achieve the 3D display technology suitable for LED display has also begun to attract much attention.
So, do you know what are the main 3D technologies for 3D LED displays?
1. 3D display technology of glasses:Glass 3D technology, we can subdivide into three main types: chromatic aberration, polarized light and active shutter, which is commonly known as color division, light division and time division method.
2. Color difference 3D technology: Passive red-blue filter 3D glasses are used together.
The technology is the oldest, the imaging principle is simple, and the cost of implementation is relatively low -- the glasses cost only a few dollars -- but the 3D results are also among the worst.
3. Polarized 3D technology: Also called Polarized 3D technology, it uses passive polarized glasses.
Polarized light type 3 d is the use of light have "vibration" principle to decompose the original image, first through the level of the image is divided into vertical polarized light and polarized light images in both groups, and then about 3 d glasses with different polarization direction of the polarized lenses, so that people around the eyes can receive two sets of pictures, after brain synthetic stereo images.
4. Shutter-type 3D technology: This 3D technology is most widely used in TV and projector, with relatively more resources and excellent image effect. It is highly praised and adopted by many manufacturers, but its matching 3D glasses are relatively expensive.
At present, including LG, Samsung, Panasonic, Skyworth and other brands launched 3D TV, using active shutter 3D technology.
The unique 3D LED display mode creates a sense of spatial dimension. Combined with the stage lighting, it creates an immersive lighting and movie feast, which brings a strong visual impact to the audience.
In addition, in recent years, the demand for artistic performance has been on the rise, and the future prospects of the immersive visual performance stage are very bright.
1. What is LED module?
LED module is a basic unit of led display, which has complete drive circuit and certain appearance.
Outdoor LED module
2. LED module classification.
a.Classifying from the application environment, there are two types led modules. One is indoor LED module and another one is outdoor LED module. The latter module must be water-proof.
b.LED module can also be classified from its color, such as single color led module, tricolor LED module and full color led module.
c.According to the type of LED, the LED module can be classified into DIP LED module and SMD LED module.
3. The composition of LED module.
The LED module is consisted of the following parts & components:
a.LED
b.IC. Generally the driving IC model we used include,
ⅰ.Macroblock MBI5020, Macroblock MBI5024;
ⅱ.Macroblock high refresh rate MBI5042, MBI5050;
ⅲ.Macroblock energy saving MBI5035;
ⅳ.Macroblock error detection MBI5036;
ⅴ.Toshiba TB62726;
ⅵ.Philip 74HCXXX;
ⅶ.ANPEC4953.
c.PCB. There are so many kinds of PCB in the market, such as single layer board, double layers board and four layers board etc. And the PCB we adopt to our led display modules: FR-4; 1.6mm thickness; Copper foil thickness 35(1oz), SMOBC&HAL, black or green surface painting.
d.Signal connector. There are three types as following,
ⅰ. Contact pin. It has price advantage, low cost.
We use only the best type connector to ensure the stability of our led displays. And if there's no special requirement, the power connector we use is VH4 to give the great convenience of the maintenance to the led displays.
e.Module kit.
ⅰ. Bottom case. It is just like a carrier of the LED screen module, the whole LED PCB will be put in it. It seems like a container when the LED module is used to outdoor environment, since the waterproof silicon glue will be poured into it and seal around the LED to realize waterproof.
It is LED's basic structure and whether there is cabinet or not the LED module will be installed on the cabinet or frame through it. The bottom case also can protect the LED from damage when under the working state.
ⅱ. Mask. There are three kinds of mask in the market.
1)Conventional hard plastic cement mask.
2)Soft mask. It is usually for sport perimeter led display usage. Considering the athletes' safety and the intactness of the LED display, at the first layer of the LED display the PC mask will be used and then the soft mask will be attached on the surface.
3) Silica gel mask. It is mainly used to the smaller pixel pitch LED display and can be pasted on the LED PCB with 3M glue.
f. Resistor and capacitor.
ⅰ. Resistor model: 0603, 0805, 1206 etc.
ⅱ.Capacitor types: electrolytic capacitor, SMD ceramic capacitor.
We use high precision resistor to ensure the color of LED display to be disposable, and to make our products more reliable.
|
|
|
Extrusion and Thermoplastics |
Posted by: pjwij745s - 08-26-2021, 12:32 AM - Forum: Welcomes and Introductions
- No Replies
|
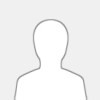 |
In a thermoplastic extrusion, the material is first softened by heating so that it can be shaped. This process is performed by the extruder, or extrusion machine. This heat softening is referred to by different names, such as ‘thermal softening’, ‘plasticization’, or ‘plastication’.
Most extruders are single screw machines. The screw is what forces the material towards, and then through, the die. Shape is imparted by the die, and/or by post-extrusion forming, and the product is then set to shape by cooling while maintaining its shape. The equipment used to perform this process is known as the post extrusion equipment, while the entire system is known as an extrusion line. In addition, there are food extruder machine and feed extruder machine.
Extruder Classification
Extruders may be categorized by three figures, for instance, 1-60-24. The first number specifies the amount of screws the machine has, the second number indicates the screw diameter in millimeters (mm), and the third number indicates the effective screw length as a multiple of the screw diameter. Therefore, in the given example, a single screw machine is being described that has a screw diameter of 60 mm and a length of 24 (i.e., a L/D ratio of 24/1).
Machine Construction
Figure 1 shows a cut-away diagram of a simple single screw machine. This diagram shows the arrangement the different parts of the machine. The two units - screw and barrel - interact together to convey the plastic material, melt the material, and then push it through the die.
The screw is rotated at a predetermined speed with the electric motor drive unit and gearbox. Temperature controllers are connected to heating/cooling elements on the barrel to maintain the temperature at the set-point temperatures.
The capability of the screw and barrel assembly to extrude a given material is based on the characteristics or construction of the barrel and screw, the characteristics of the plastics material, and the circumstances under which the system is operated.
Post Extrusion Equipment
When the extrudate leaves the die, it can either be set to the desired shape or its shape can be altered and then set to shape. The equipment that performs this process is known as the ‘post extrusion equipment’ or the ‘haul off’, and in terms of size, it is generally much larger than that of the extruder. This is because plastics take a considerable amount of time to cool, and this cooling process determines the speed the line will operate.
Pet Feed Machinery
The growing demands of today’s pet food market require increasingly specialized knowledge combined with advanced processing technologies. As a longtime partner to hundreds of premium pet food producers worldwide, we provides comprehensive processing solutions and aftermarket services to keep your operations ahead of the curve. All to guarantee easy, safe, and efficient operations that can quickly adapt to the next market trend.
We offers a full range of pet feed machinery – from raw material intake to finished feed bagging – as single unit or complete plant solution. The individual process machines offered are selected from the standardized and proven range of product families.
A wide variety of food products is produced worldwide on our complete twin screw extrusion processing lines to answer increasing consumers demands : cereals, snacks, crispy breads and crackers, baby food, textured proteins and food ingredients.
At the same time, we also offer pasta machinery and couscous turn-key processing lines integrating our specific design Rotante hot air drying technology.
To enable our partners in the Food industry to gain market shares and leveradge their brands, our expert teams are continuously innovating to develop and produce high-quality food products with new flavors and taste combinations.
Pasta Production Line
Over 50 years, pasta production line has offered complete production solutions for a wide range of typical short-cut pasta shapes. Over the years, Clextral experts have continuously refined every component in the production process, building high-performance lines to customer specifications, including its exclusive VHT (Very High Temperature) drying system. Clextral short pasta extruders are particularly adapted to the modern requirements of production in terms of cost-effectiveness, flexibility, ease of use, hygiene and maintenance.
HOW IS PASTA MADE ?
The raw materials are mixed with a precise dosing mechanism to maintain constant flow and obtain homogenous dough in the pasta extruder. The pressing phase is carried out with a single screw system specially designed to ensure optimal semolina hydration, mixing, compression and extrusion. Once the dough is kneaded to the required consistency it is put through fitted dies to produce the required shapes and cut to length. Drying is achieved in two phases : first, the pre-drying Trabatto is used to crust the dough surface in order to avoid sticking. The second phase is done on Rotante drying units which include a VHT (Very High Temperature) drying system, which offers several advantages, including faster pasta producton, heightened quality of the final product (especially for pasta made with soft wheat), reduced product loss, short changeover times and very hygienic processing. After drying, the pasta is cooled and stabilized in the industrial pasta machine and then transported to storage or packaged directly.
STATE-OF-THE-ART PRODUCTION OF PASTA
Clextral pasta extruders are designed and manufactured to strict production standards ensuring: - Quality construction and superior hygienic standards – stainless steel parts, easy cleaning, low loss of raw materials, etc.
- Quick and easy on-site assembly – modular pre-mounted parts
- End-to-end process control – full automation to guarantee product consistency
- Flexibility – quick changeover, easy shape changes and adjustment of production parameters, capacity varies from 1,500kg to 6,000kg/h
- Efficient maintenance – standardized extrusion and drying parts, easy access for servicing
- Follow-up services –training, support, new product design expertise
- Sustainability – intensified processing to generate energy and water savings, as well as cost-effectiveness
High-Quality Modified Starch Products
Microtec Engineering Group is an eminent name in the modified starch industry. With a vision to be one of the world-leading Provider of premium modified starch technology, our focus is to increase our penetration in global markets by helping clients to manufacture quality modified starch products using the latest technology and strictly adhering to the Industrial Standards. Using our advanced equipment and processing technology ,you’ll obtain starch products that are distinguished from the rest. Our starch modifying equipment is designed to produce top-of-the-line products that cater to the requirements of a widening customer base.
Industrial Application of Our Modified Starch Technology
Our modified starch machinery serves a wide range of industrial applications. These include:
1. Food
Modified starches are excellent thickening agents. Our advanced starch modifying technology will enable you to provide the required thickness, stretch ability, crispness, stabilizing and binding properties as well as texture to numerous food products related to:- Bakery
- Coating
- Confectionary
- Soups, sauces & gravies
- Pasta & noodles
- Snacks
2. Textile
Textile industry relies on the use of modified starch products as they reduce the breakage of fibre and wastage. Especially when used on fabrics like polyester, cotton and acrylic, they yield satisfying results. Advanced starch enhancing technology like ours can also help you to manufacture a wide number of products like:- Thin boiled starch
- Binder
- Softener
- Lubricants
3. Paper & Packaging- Paper – The demand for modified starch in the paper making industry is never less. The reason? Because modified starch increases the bonding strength of paperboard and plain white paper. Our top-of-the-line technology is instrumental in enhancing the strength, quality and brightness of the paper.
- Packaging – The adhesive property of modified starch is remarkable. Modified starch is an essential component in packaging glue which, in turn, is used for making boxes and cartons. Our unique starch modifying equipment enables you to impart excellent adhesive property to your packaging glue.
|
|
|
Hair Chalk: How to Use It & Remove It |
Posted by: bbsiw25se - 08-25-2021, 05:02 AM - Forum: Welcomes and Introductions
- No Replies
|
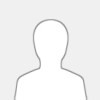 |
Perhaps it’s all the gorgeous festival beauty looks on our Pinterest feeds, but lately we’ve had the urge to go full-on cotton candy with our locks. There’s something about pastel-hued, hair-chalked strands that speaks to our inner wild child—and we’ll be honest, the lack of commitment makes them even more appealing. But with new formulas springing up left and right, how are you supposed to know how to use (and more importantly, remove the remnants of) each one? We did the research for you, and found out exactly how to apply and wash out each type of hair chalk, leaving you more time to fishtail and dip-dye to your heart’s content.
Liquid Hair Chalk
Liquid hair chalk lasts anywhere from 2-10 shampoos. It will usually come with a sponge-tipped or foam applicator. To apply, place a towel over your shoulders and put on gloves to prevent staining your clothes and hands. Next, use the applicator to apply the formula to your locks. wait 30 seconds for product to absorb fully, then blow-dry with a styling brush. To remove it, you're supposed to just wash your hair as you would normally. However, you can also massage a hair oil like Sachajuan's Intensive Hair Oil ($33) into your strands before shampooing and conditioning, in order to speed up the removal process.
Hair Chalk Compact
A hair chalk compact can be used on wet or dry hair, but applying to wet hair will give you a more intense color. Take a one-inch section of hair and slide the hair chalk compact over the length you’d like to color. Seal the pigment in with a spritz of hairspray. Depending on how light your hair is, it'll last one to three shampoos to get it out of your hair. Hair chalk that comes in a compact will usually wash out quickly and easily with shampoo, though blondes may have to shampoo a few times more to rinse out all of the pigment.
Hair Chalk Pen
The traditional hair chalk pen can be used on wet or dry hair, and lasts from 2-4 shampoos, depending on how light your hair is. Place a towel on your shoulders and use gloves to prevent staining. If you're brunette, wet the section of hair you’d like to color before applying the chalk. Blondes can do that too, but it'll make the pigment stay on much longer. Apply the chalk to the strand of hair you'd like to color, twisting the hair into itself as you go. Allow for the color to dry, or just give it a cool blast of air with your hairdryer. Style as usual, but if you want to lock in the color, finish it with hairspray. It can be removed with normal shampoo, but a clarifying shampoo (like Verb's Reset, $16) will rinse it out quick.
Hair Chalk Spray
Hair chalk spray is likely the easiest to use, because you just spray it on dry hair right before going out. It typically only lasts a few shampoos, but that also means it's super easy to get out of your hair. Just mist the color directly on your hair, wherever you would like a pop of color, and style it like normal.
Marker
Markers, or felt-tip pens, serve a variety of functions. Children use them to make bright, colorful drawings. The stereotypical teacher uses a glaring, unmistakable red felt-tip to grade papers. Retail employees, roadside vendors, performers, and protestors rely on the indelible, eye-catching shades and thick inking surface of these writing and drawing utensils to announce sales, prices, and productions, or to create strongly worded posterboard signs to convey dissatisfaction. Markers are also useful for permanently marking surfaces, which is often necessary for identification purposes—putting names on clothing tags, boxes, and tape which can be adhered to almost any item.
Raw Materials
The marker body, cap, and plugs are formed from plastic resin. The marker reservoir, which holds the ink, is formed from polyester. Powder and water are used to form the felt writing tip. In addition, markers require ink, and the pigments and synthetic substances used to make it. Toluol and xylol used to be common synthetics used as solvents in dye, but due to their toxic nature these substances have largely been replaced with safer chemicals such as cyclic alkylene carbonates, although these chemicals are still used to make the indelible ink contained in permanent markers. The solvent is the substance into which the dye is diluted. Water also acts as a solvent in ink. Additives may also be used in an ink mixture to act as wetting agents.
Making the marker
3 To make the body of the marker, plastic resin is injection-molded into a marker body. Injection molding involves heating a substance, in this case plastic resin, into a molten state and forcing (injecting) it into a mold of the desired shape, then allowing it to cool and harden. Marker caps and plugs are formed in the same manner as the barrel.
4 The nib, or tip, of the marker is made from powder which is mixed with water, molded, and baked into its pointed or flat form.
5 Using one machine for all the following functions, an assembler then places a polyester cylinder inside the marker barrel to form a reservoir for the ink, fills the reservoir with ink, and inserts the nib at the bottom and the cap at the top.
6 The markers are then placed into color assortment and packaged for retail marketing.
[/url]The highlighter’s appeal has flourished in the digital age. Most word-processing and e-reader software products have a highlighter function. And the hand-held [url=http://www.jialaitefc.com/highlighter/]highlighter continues to evolve, too. In the early ’80s, the fiber tip gave way to polyethylene beads molded into porous heads. (The plastic squeaks less, and the ink flows more smoothly.) When the highlighter business saw that it wasn’t being embraced by holdouts who preferred pens, it made the dual highlighter/pen. There are now retractable highlighters. And flat ones. And ones that smell like pizza.
LIGHTING UP THE BIBLE
Due to the thin paper used in most Bibles, typical highlighters often bleed through. For that reason, G.T. Luscombe, a distributor of Bible-study accessories based in Frankfort, Ill., got into the business of Bible-paper-friendly highlighters. John Luscombe, the president and chief executive, explains:
Is there a particular color code? There are different types of coding depending on how many colors there are. But for the most common four colors, we recommend that yellow represents blessings, blue represents the Holy Spirit, pink represents salvation and green represents growth and new life.
How to Choose a Paint Starter Set for Beginners
With so many paint colours available and new ranges being released every week, which paint set should you buy when you first start painting?
The overwhelming feeling that descends when trying to buy paint colours either online or in your local art store can often lead to the safe bet…
The pre-boxed starter set.
The paint companies have designed them to help you, right? The best paints for your needs when you are just beginning…or so you would think.
But are they a good choice?
Are you getting the best value for money or are they sending you down the wrong path? I’ve devised a simple technique to help you decide which starter palette is right for you.
Ready for a little paint history lesson to understand what you should be thinking about on your next trip to the art store?…
Boxed starter sets are designed to give you a varied approach, a range of colours that can give you the widest colour gambit with the minimum amount of outlay.
But here’s the rub.
It depends on what you’re aiming for with your end result. If you think about the paintings that you want to achieve, the subject matter you are most drawn to before you actually buy your paints then you can make an educated guess which colour palette is going to be right for you.
The Old Masters
In Renaissance times, the Old Masters learnt their trade of painting as a craft.
The tradition of the craft had a system of apprenticeship.
Colour mixes were kept secret and passed on from generation to generation, some painters even created their own codes to keep the secret mixes safe.
Working under apprenticeships in individual Ateliers (the French word for “workshop”) was the norm. Artists learnt how to grind their own paints from the natural earth pigments surrounding them. Working from dry pigments, they had to be mixed with oil and then ground into a paste by hand to make paint.
The colour choice was limited and paintings relied on the use of dramatic lighting and tonal value to produce great works. (see: The Importance of contrast in painting)
Working with this limited available palette can teach you a great deal about colour mixing and warm and cool colours. I’ve made a free still life video course that shows you a classical approach to painting using just burnt sienna, ultramarine blue & titanium white.
Masters Palette – Perfect for portraits & understanding the importance of tone.
When the Old Masters were mixing colours, the pigments came from the earth, literally ground up rocks and minerals – hence the muted palette being called the earth colours.
When painting portraits, they couldn’t just go out to buy ‘flesh tint’ they looked, observed and mixed it.
Burnt umber, raw umber, yellow ochre, burnt sienna, red ochre, these are the sorts of colours they would have been using.
If you want to try and recreate an Old Master-style painting, using the pigments they used, gives you an immediate head start. In my article on ‘How to choose a basic portrait palette’ I use a muted collection of colours.
Skin tones are muted, so start with a muted colour. It seems obvious right? But when you’re painting the urge to try and ‘fix it’ by adding an extra colour is huge.
Don’t feel like it’s only you, I still do it now after 20 years, even though I should know better!
The Holiday Season brings with it plenty of gifts… and then there are the actual gifts themselves! Yes, we know it. Christmas is not just about presents and shopping alone. It is definitely not a time to just run around from one store to another looking for that elusive gift. But we all do it anyway. Then comes the time to wrap it all up and put it under the giant tree so that it all feels picture-perfect. And for some us, this is undoubtedly the part that we most enjoy. Wrapping your Christmas gift feels so very serene, relaxing, and enjoyable. Maybe it is because you know that finally the shopping is all done. Maybe because you can marvel at the DIY Gift Box you just crafted. And once you’ve completed your DIY gift set you can choose from this pack of 20 different Holiday Grosgrain Ribbon patterns as the final touch.
This is right; this Holiday Season, it is time to give your presents a homemade box. A festive DIY gift box makes it all more personal and you will see that every member of your family and our friends will love the custom box as much as they cherish the gift inside. Handmade gift boxes also give you greater creative freedom when it comes to ‘saying it just right’.
|
|
|
Design and Development of Telescopic Conveyor |
Posted by: bbsiw25se - 08-25-2021, 05:00 AM - Forum: Welcomes and Introductions
- No Replies
|
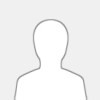 |
This telescopic belt conveyor is an effective and ergonomic alternative to labour-intensive routines. Operators can move heavy or awkward packages into or out of a container/truck rapidly with little effort. Extending some 20 meters/65 ft., telescopic belt conveyors can be used to load/unload any type of loose-loaded cargo - typically parcels, boxes, sacks & tyres. An intuitive smart-pad on either side enables precise control of the boom's elevation and telescopic movement. Push buttons at the operator end of the boom control activation, lights, belt direction etc.
A telescopic belt conveyor is an effective and ergonomic alternative to labour-intensive routines. Operators can move heavy or awkward packages into or out of a container/truck rapidly with little effort. Extending some 20 meters/65 ft., telescopic belt conveyors can be used to load/unload any type of loose-loaded cargo - typically parcels, boxes, sacks & tyres. An intuitive smart-pad on either side enables precise control of the boom's elevation and telescopic movement. Push buttons at the operator end of the boom control activation, lights, belt direction etc. Exceptionally small base sections combined with up to five extending sections enables us to provide custom telescopic conveyors to suit your requirements.
Wheel Sorter
Wheel Sorter is used for belt conveyor system or roller conveyor system. The characteristics of this design is to track conveyed goods accurately and stably as well as set sorting positions at any position along both sides of conveyor lines conveniently to satisfy customers with different sorting requirements. Achieve maximum sorting rate at the same time its best economical efficiency.
Durable: Our O-Belt is made in a whole piece, without any gaps to ensure a longer service life!
§High Sorting Rate: Designed for high speed and bidirectional for sorting operation on both sides at the same time. Maximum Sorting Rate can be 7200 pieces/hour.
§Low Noise: Use new material and noise elimination technology which can be friendly for Environment, noise can be less than 75dB.
§Energy Conservation and Environmental Protection: Light weight material and low energy consumption structure as well as low power and source power (conveyor) drive to achieve successful operation.
§Flexible and Stable Sorting Operation: Online double-row swivel wheel technology prevents conveyed goods from vibration and damage. Stably and flexibly sort goods from light duty to maximum 50kg heavy duty range.
§Easy Layout and Maintenance: Use unit modular design and embedding combination structure, easy for sorting positions be placed at any position along both sides of conveyor line. Product is more reasonable, simple, conveniently used and maintained.
DWS Systems makes its international show debut at IFAT
DWS System, the joint venture between Siltbuster, the water treatment specialist and the German recycling equipment giant, Doppstadt, , will be exhibiting at IFAT 2016 in Munich. This will be the first time DWS Systems has taken part in an international show, since the company was formed in 2015.
Located in hall B1.404, DWS Systems will be exhibiting the latest Gritbuster WT-250 road sweepings recycling system. The WT-250 is uniquely engineered to handle road sweepings, gully waste and trommel fines on a commercial scale, handling up to 25 tonnes per hour. It cleverly uses water to further separate out recyclable materials - washed gravel and sand products - making it easier for materials recycling facilities to separate out on a large scale the constituent elements of the waste they handle. This boosts the level of material reuse and minimises waste going to landfill. Thanks to this level of innovation, the WT-250 is in the running for a prestigious MRW National Recycling Award.
DWS Systems will also be showing its range of water treatment technologies including the HB40R lamella clarifier. This is specifically designed for the removal of suspended solids and other matter from process waters, so that the water can be reused. As a result, those using DWS Systems’ water treatment kit can operate a closed loop process; they don’t have to rely on large settlement lagoons to naturally treat their waste water. The net result is compact solutions which can be rapidly deployed on small sites to reprocess a range of waste materials to a higher standard than can be achieved by the current dry processing techniques.
Commenting on the company’s presence at the exhibition, Dr Richard Coulton, founder of Siltbuster and CEO of DWS Systems UK said: “As just these two products show, we have some powerful solutions for the world’s recycling industry. The collaboration between our two businesses means we can roll them out to an international audience much faster, which is important as the recycling sector faces some real challenges which our systems address. Our presence at IFAT is an important first step in that process. It’s a great opportunity to showcase both the new business and most importantly, the technologies we offer.”
Chapter One - What is a Conveyor Belt?
A conveyor belt is a material handling system designed to move supplies, materials, and components using an efficient and effortless process that saves on time, energy, and cost. The design of conveyor belts includes two motorized pulleys with the conveyor material looped over them. The pulleys operate at the same speed and move in the same direction to activate the motion of the conveyor belt.
There is an endless number of types and uses for conveyor belts. All of the varieties serve the purpose of transporting materials and goods along a continuously moving path. Though motorized conveyor belts are the traditional form of a conveying system, there are systems that use rollers without a motor to move materials.
Chapter Two - Types of Conveyor Belts
The range and uses of conveyor belts cover several industrial settings and applications. The efficiency of conveyor belt systems assists in improving productivity, saves on labor costs, and decreases lead times. Conveyor belts move large quantities of goods quickly and reliably for transport, further assembly, or storage.
The principal reasons so many conveyor systems are in use are the savings in labor costs, efficient movement of goods, and their ability to keep products and materials from damage. They provide the best possible service at the lowest possible cost.
Types of Conveyor Belts
Roller Bed Conveyor Belt
The surface of a roller bed conveyor belt is a set of rollers that match the weight and speed required by the product. The length of the roller bed conveyor belt determines the number of rollers to be used.
A roller bed conveyor belt is designed for applications where materials are loaded by gravity. They are an ideal solution for conditions where materials have to be moved over long distances since they are designed to reduce friction.
Flat Belt Conveyor Belt
A flat belt conveyor belt uses a series of pulleys to move materials and supplies. Its belt is made of natural or synthetic materials; this makes it versatile and adaptable to varying conditions and applications. In some instances, a flat belt conveyor belt may have a center drive and nose bars.
Modular Conveyor Belt
A modular belt conveyor consists of interlocked pieces made of hard plastic with segments that can be easily removed and replaced. The design of modular belt conveyors makes it easier to clean, and the material is resistant to sharp and abrasive substances. Modular belt conveyors come in varying configurations and use a single belt to go around corners, in a straight line, up inclines, and down declines.
Cleated Conveyor Belt
Cleated belt conveyors have sections, pockets, or dividers that secure granular products when the belt declines or inclines. The cleats have equal spacing between them and come in various styles and shapes depending on the product to be moved and the design of the belt.
Inverted Capital T
An inverted T cleat stands perpendicular to the belt and provides support for delicate and fragile materials.
Forward Leaning Capital L
A leaning capital L has a wide base that can be curved to scoop up granular materials. The design of the capital L makes it less resistant to leverage forces.
Inverted V
Inverted V cleats are two inches or less to create a trough like effect and are used for heavy, abrasive, and larger pieces of bulk materials.
Lugs and Pegs
Lugs and pegs are designed to meet the specific needs of a product and are a cost effective solution for products that do not require continuous support, such as cartons. They can be selectively placed to move products of varying sizes.
Sidewall
The purpose of sidewalls on a conveyor belt is to keep the material being moved on the belt. Sidewall conveyor belts are ideal for incline and decline belts and help increase product load capacity to improve conveyor system efficiency. There are a wide variety of sidewall materials, and they can be corrugated at various depths to fit the needs of the product and application.
Curved Conveyor Belt
The curves in conveyor belts are used to carry products around corners, make transfers, and make efficient use of floor space. Curved conveyor belts can make “U” turns to face the direction from which they came. They are made with flat belts and can make turns at 45o, 90o, 135o, and 180o angles.
Incline Conveyor Belt
Incline conveyor belts have a rough, uneven surface to hold materials and prevent them from slipping or falling back. The underside of the belt is smooth to allow the belt to glide smoothly along the bed. Modular belt and timing belt conveyors can be used for this purpose. Depending on the material to be moved, cleats may be included for increased slippage prevention.
Decline Conveyor Belt
The purpose of a decline conveyor belt is to move products or materials down or change its height. As with the incline version of conveyor belts, a decline conveyor belt has a rough surface or cleats to prevent materials from slipping or falling.
Decline conveyor belts are a continuous operating conveyor system with an articulated frame with a section that is pivoted or placed downward to accommodate downward movement of products from an upper location.
An advancement in conveyor belt technology is the electroadhesion conveyor belt, which acts like a magnet that is activated by a switch to create a strong and secure holding force between the container and the belt. Two low amp power strips placed in the conveyor belt powers its holding force. Materials with an electrically conductive pattern are knitted into the belt to produce the force that holds materials in place.
Filter Conveyor Belt
Unlike conventional conveyor belts, filter conveyor belts allow materials to pass through in order to drain excess liquid from components or filter out toxins and contaminants. Filter conveyor belts are constructed with lateral grooves and holes in the center of the belt to allow liquids and fluids to escape. Drainage holes are placed in a fabric free zone down the center of the belt or sealed to prevent the liquid from soaking into the belt fabric.
Much like a sidewall conveyor belt, filter conveyor belts can have sidewalls to prevent liquids and fluids from spilling over the sides of the belt. They are made of heated polyester, polypropylene, polyolefin, or stainless steel mesh for dewatering applications.
Vacuum filter belts are used for washing coal and other ores to assist in the separation of fluids and solids.
|
|
|
How To Use A Plate Bevelling Machine |
Posted by: bbsiw25se - 08-25-2021, 04:58 AM - Forum: Welcomes and Introductions
- No Replies
|
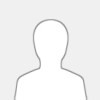 |
Here is a professional guide about how to use a manual feed plate beveller aka plate bevelling machine and it’s setting up, tool change, cleaning, and maintenance.
This is a step by step complete guide on how to use plate beveling machines. In brief, this article covers the following points, - Components of the SKF 25 plate beveling machine
- Safety measure before setting up the plate beveller
- Checking the workpiece
- Setting the milling head of the plate beveller
- Setting the chamfer width plate beveller
- Mounting the rollers of the plate beveller
- Milling with the plate beveller
- Using the plate beveller
- Tool change of the bevelling machine
- Cleaning of the bevelling machine
- Maintainance of the bevelling machine
Safety measure before setting up the plate beveller
The beveling machine may only be operated in a horizontal position. Secure the workpiece.
Checking the properties of the workpiece.
The surface of the workpiece must meet the following require- ments. The surface must be smooth and may not have any burn points, slag, welding joints or similar. Before beginning with milling, remove surface unevenness.
Setting the milling head
Place the machine onto the upper side (power connecting cable ). Release the locking mechanism (2) on both sides of the machine. Set the desired milling angle. The milling angle can be viewed on the scale (1). Tighten the locking mechanism (2) on both sides of the machine.
Setting the chamfer width
Place the machine onto the upper side (power connecting cable ). Release the locking mechanism (1). Set the desired chamfer angle by turning the adjusting screw (3). The chamfer width can be viewed on the scale (2). Tighten the locking mechanism (1).
Mounting the guide roller for milling plates
Mount the plate (3) according to the illustration. Fix the guide rollers (2) in the borehole (1) with the washer and nut.
What is Pipe Beveling? How to Bevel a Pipe?
Pipe beveling is an angle forming between the edge of the end of a pipe or tube. When the pipe end is formed with a certain degree of an angle, it is called a bevel end or beveled end. Pipe beveling is an essential step in the welding preparation process of pipe joining. The quality of the beveled pipe directly affects the quality of the welding, so that proper pipe preparation ensures the best possible weld joint. Other than welding, beveling can also be used for deburring the cut pipe ends for aesthetic and safety reasons.
There are several pipe end preparation methods for welding. In this article, the types and pros, and cons of pipe beveling machine will be discussed.
What is correct, beveling, or bevelling?
Both beveling and bevelling are correct. 'Pipe bevelling' is the English UK spelling and 'pipe beveling' is the English US. Also, the wording pipe chamfering, pipe end working, pipe end preparation, and pipe prepping are other common terms for this application method.
Beveling vs. Chamfering: What is the difference?
Pipe chamfering is technically a type of pipe beveling. Both terms refer to an edge forming between two faces of a pipe or tube. However, the main difference between pipe chamfering and pipe beveling is that a chamfer is an edge that connects two faces at a 45 degrees angle, whereas the bevel's slope can be any angle except 45 or 90 degrees.
How to Bevel a Pipe?
There are various ways to bevel a pipe. Using a portable or stationary beveling machines, doing it by a hand grinder, or by a plasma or torch cutter.
The hand grinding method of pipe beveling is the cheapest and the most dangerous method compared to using a pipe beveling machine. It is time-consuming, and a skilled operator is required to perform a bevel on a pipe by a hand grinder. Moreover, it is nearly impossible to keep the bevel quality the same for each pipe operation while creating a lot of mess.
Using a torch or plasma cutter is another type of pipe end preparation machine. It provides faster results compared to a hand grinder, however; it also has some drawbacks. The flat land at the end of the pipe needs to prepared by hand, which is not a safe process. Yet again, the command produced will be inconsistent.
Also, this pipe beveling method cannot be used on all materials, which would affect your flexibility in production.
A portable beveling machine comes in different configurations and is notably safer than the previous two methods. The biggest advantage of these portable machines is that they are portable so that it's time-efficient since the user can take the machine to the pipe. They are convenient to use for maintenance work, or on a construction site. However, they are inadequate to meet high production requirements.
Stationary beveling machines provide the most options and flexibility for pipe beveling. Almost all kinds of pipe bevel shapescan be created with different combinations of tools. They are designed to meet high production requirements in a safe working environment. Also, stationary pipe beveling machines are easy to integrate with automated production lines, so that the operator does not even have to be on the machine all the time. There are various benefits of stationary beveling machines such as; standard carbide cutting inserts are inexpensive to replace when needed, easy to set up and requires low maintenance, ensures the lowest cost and fastest cycle time per bevel, provides safe working environment without creating a mess, offers a broad range of machining options and can machine several pipe or tube materials, and does not require a skilled operator. Last but not least, stationary pipe beveling machines ensure constant pipe bevel quality that directly affects the quality of pipe welding.
The pipe cutting machine developed in this study is a portable device used to cut a steel pipe. The machine, which is attached to the steel pipe by magnetic force, is moving around the pip e using four wheels. It also works for straight cutting of a steel plate. For the higher precision and labor time reduction, the automation of a pipe-cutting process is needed. However, it is not easily achieved because of vibrations and the loss of track. It is also found that the problems of the automation arise from the coupling of the functional requirements for the pipe-cutting machine. So, it is very difficult io solve the problems by a conventional design method.
Manufacturers of all types of industrial products go to great lengths when promoting the features and benefits of their products on their websites. But many fall short of offering any real guidance on how to choose the right machine for each individual customer’s needs. So, to help out, we’re pleased to offer guidance to people wanting to know more about flange facing products. Included are answers to some of the commonest questions our technical sales team encounter.
SECTION 1: BEGINNER BASICS
If you’re new to flange facing. Here are answers to some of the more fundamental questions;
Why is there a need for flange facing machines?
Although flanges are mass-produced with machined surfaces, damage to the flange surface during transit and installation can occur. This results in scratches and dents to the sealing surface. Damage like this puts the integrity of the joint at risk – with potentially disastrous consequences. Even after pipelines have become operational, a joint’s integrity can be compromised by corrosion inside the joint. When this happens, the flange often needs to be replaced and can be removed using a split frame/clamshell cutter.
What are the main industries using flange facing machines?
These include petrochemical and pharmaceutical production plants, oil wells, pipelines and power generation plants.
How do flange facers work?
They work in a similar way to a gramophone player, with the cutting tool traveling in a spiral path across the face of the flange. This surface finish is commonly specified for flanges in the oil and gas industries, with the gasket material being compressed to fill the spiral groove. A flange with a spiral grooved finish is less liable to leakage, as any gas or liquid is forced to travel in the long spiral path rather than across the flange face.
How are they powered?
Pneumatic is the standard method, but hydraulic versions can be provided as an option on many machines in the range.
How do I know if the flange surface needs machining?
We recommend you read our previous blog article which includes a section covering what ASME states as acceptable flange damage.
SECTION 2: APPLICATIONS FOR A FLANGE FACING MACHINE
Raised Face Flanges, Heat Exchanger Flanges, Techlok Flanges, Recessed Gaskets & Spigots, Weld Preps, Hub Profiles, RTJ Flanges, Lens Ring Joints, SPO Compact Flanges, Swivel Ring Flanges.
Note: to carry out some of the above applications you will need additional options and accessories.
What options and accessories are available?
Optional components for widening the usage of the flange facing machine include:- Compact flange machining kit to convert your existing flange facer. Alternatively you can specify a dedicated compact flange facing machine at the time of order.
- Journal/end shaft turning kit
- Heat exchanger mounting kit
- Heat exchanger back facing kit
- Lens ring machining kit
- Orbital milling kit, replacing the single point tool post with a milling head.
- Hydraulic conversion kit – to convert a pneumatic machine to hydraulic drive.
Can a flange facing machine work in a subsea environment?
Yes, however it will need to be a hydraulically powered.
SECTION 3: CHOOSING A FLANGE FACING MACHINE
What size machine do I need?
There are many different sized flange facing machines available, for example smaller machines can be used on flanges from 2” up to 12” and the larger machines covers sizes from 45” up to 120”. Additionally, the MM1080ie is a unique design which can be mounted internally or externally and used to machine flanges from 0” all the way up to 157” diameter.
Pipe Cutting and Beveling Machine
This user pipe cutting and beveling machine is used for cutting and blanking of offshore wind power jackets. The jacket has been in the ocean for a long time, and the environmental conditions such as wind, waves, currents and ice are very harsh, so the manufacturing quality requirements are very strict. As the scale of wind power jackets tends to be larger, the corresponding pipe diameters and wall thicknesses of the pipes, ties, and columns have also increased. During the processing process, the pipe end intersecting lines have various mouth shapes, and the cutting difficulty and accuracy are also increasing. High, ordinary manual cutting methods can no longer meet the requirements. Aiming at the shortcomings of manual processing methods such as low production efficiency, high labor intensity, and poor product quality, the Kasirui technical team has developed a large pipe diameter intersecting wire cutting machine equipment to solve the problem of difficult cutting of large pipe diameter pipes!
What is pipe beveling?
Pipe beveling is the process where an angle is formed between the edge of the end of a pipe or tube and a plane perpendicular to the surface. A standard pipe bevel angle for welding is 37.5 degrees. Other angles and special forms such as J-Bevels can also be produced on the ends of pipe or tube using automatic pipe bevelling machines.
Why bevel a pipe?
Bevelling of pipe or tubing is most commonly used to prepare the ends for welding. It can also be used for deburring the cut ends for safety and aesthetic reasons.
Why we need to automized pipe bevelling?
? Save time – stationary pipe cutting and beveling machine is many times faster than other methods such as hand grinding, flame cutting, hand held bevelers, or loading into a lathe.
? No more dirty operations such as hand grinding or torching.
? Consistent accurate pipe bevels each time, will face the end of the pipe square and bevel or deburr ID as needed.
? Cycle time normally in the 5 to 20 second range depending on size
? Eliminates ergonomic issues from operator handling hand tools
? Safer than hand grinding or torching, all chips are contained within the machine.
? Low operating cost, uses mostly industry standard carbide tooling
? Easily bevels stainless and materials not suitable for torching.
? Special forms such as J-bevels are easily produced.
? Can be operated by a non-skilled operator once setup.
|
|
|
How Liquid Filling Machines Benefit the Paint and Coatings Industry |
Posted by: bbsiw25se - 08-25-2021, 04:57 AM - Forum: Welcomes and Introductions
- No Replies
|
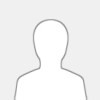 |
Using Filling Machines to Increase Efficiency and Profitability
Liquid fillers are integral to liquid packaging lines, with automated models capable of maximizing efficiency. Without this equipment, the filling process wouldn’t be reliable enough to ensure that no product loss occurs because of inaccurate fill levels.
Technological developments that are creating more automation and computerizing many of the components in filling machines have made them more dependable than ever before, with many of the best models designed to allow for full customization and user friendliness.
One type of liquid filler that can meet the needs of the paint and coatings industry is the net weigh filling machine. Designed to handle products of low to high viscosity, net weigh fillers are ideal for filling liquids in bulk quantities, such as 5-gallon pails, with consistent weight levels for each container.
Net weigh fillers work by using independently timed valves with custom programming through the filler’s computer. They can then fill precise amounts of liquid by gravity into containers, stopping once the liquid reaches the specified weight.
These fillers can fill many different types and sizes of containers, with many of the top models capable of lasting for many years.
What is a Piston Filling Machine?
At Liquid Packaging Solutions, there are a number of different types of filling machines manufactured to handle different product viscosities, different fill sizes and other variations in packaging projects. The piston filling machine can solve many issues for products with particulates or high viscosity liquids, though it can also handle thin and medium viscosity products as well.
As product sits in the hopper, the valve, which sits between the hopper and the nozzle, will be open from the hopper to the cylinder. The piston will begin to withdraw from the cylinder, typically after an operator activates the fill by stepping on a foot switch. As the piston withdraws, product from the hopper will fill the empty cylinder. Once the piston has withdrawn to the desired point, the valve will rotate to allow product to move through the nozzle. At this point the piston push back in to the cylinder and move product through the nozzle and in to the waiting bottles or other containers. This process creates a highly accurate volumetric fill as the interior volume of the cylinder will never change, meaning the volume of product released to the bottles will never change.
The hopper sizes can vary from project to project based on the size of the containers or fills. Not all piston filling machines, and in particular, the automatic piston fillers, will use a hopper from which to pull product. Automatic lines will likely include a tank or pull from a bulk source. The cylinder and piston combination are also available in different sizes to accommodate different projects. The speed with which the piston moves can be adjusted, different piston sizes can be used to meet volume requirements and even multi-piston, automatic filling machines can be designed for use with inline packaging systems. LPS piston fillers allow the operator to adjust the length of the piston stroke, which in turn adjusts the volume of product that is pulled in to the cylider with each fill cycle. This way a single piston size can handle a range of container sizes. While multiple strokes of the piston can also be used for larger fills, at some point the efficiency of using multiple strokes will become low enough that simply changing out the piston for large containers will be the better solution.
The nozzle used on any piston filler will be chosen to meet the needs of the particular project at hand. For instance, a product with large chunks of fruit or vegetables will not work well if a narrow nozzle is used to move product in to the bottles. On the other hand, a very large nozzle will be cumbersome with a small mouthed bottle. There is virtually no limit to the type of nozzles that can be used, including custom manufactured nozzles where special projects are concerned.
Though a simple concept, the piston filler can be an ideal solution for many projects and for liquids thick and thin. Though these machines are known for handling viscous products, in the right circumstances they will handle free-flowing liquids as well. For assistance finding the best type of filling machine for your own packaging project, contact Liquid Packaging Solutions today.
Overflow fillers, gravity fillers, automatic piston filling machine and other liquid fillers all vary in the way that they move product into a bottle or container. However, the automatic versions of these machines almost always have certain features in common. These features are intended to add efficiency, consistency and reliability to the packaging equipment. Below are a few of the most common features of found on Liquid Packaging Solutions' bottle fillers.
Heavy Duty and Portable Stainless Steel Frame
For consistent and reliable fills, the machine must be stabile throughout the process. The heavy duty stainless steel frame protects against shifting, vibrating and other movement that might effect the volume or the level of the fill, while also avoiding splashes and spills. The stainless steel material is compatible with a vast majority of products, though there are exceptions. When corrosive liquids are run on the machinery, other construction materials may be used for the frame, including HDPE. Ultimately, the material used will be that material which will better extend the useful life of the equipment.
Easy Adjustments From Height to Heads
Many packagers fill more than a single product, or at the very least fill into bottles of multiple sizes and shapes. Changing over from one product or bottle to another means stopping production on the liquid filler. These machines include simple adjustments to minimize downtime and maximize production. Fill heads can typically be moved using simple fingertip adjustment knobs, while power height comes standard on automatic equipment, allowing up and down movement with the flip of a switch. Even auxillary equipment such as power conveyors include knob adjustments or other simple components for railing and other changes. Other adjustments, such as time and delay settings, can easily be made from the operator control panel, discussed in more detail below.
Gravity filling is the simplest filling method. The uncomplicated construction and operation of gravity filling machines permits them to run with a minimum of maintenance. The supply tank (more properly called the filler bowl) is the upper, central part of the machine. Filling stems are attached to the bottom surface of the bowl at each container filling point. A vent tube extends upward into the filler bowl to a point above the liquid level. To begin the filling operation, the container is raised by the platform until it contacts the filling stem. The platform then continues to raise the container against the stem, opening the filling valve. With the filling valve open, the liquid drains into the container. The air in the container flows out trough the vent tube into the space above the liquid in the filler bowl. Although the container becomes filled, the liquid continues to flow in. The excess fluid rises in the vent tube until it reaches the same height as the liquid level in the bowl. Because the vent tube extends above the bowl liquid level, there is no overflow of liquid from the container into the bowl. If the product is foamy, the foam will rise in the vent tube above the liquid level in the bowl. If it is stable foam and will not break down, it will ultimately overflow into the bowl. For this reason, gravity fillers are not often used for foamy products. At the predetermined time after the container is filled, it is lowered from its filling position, closing the filling valve. Liquid left in the filling stem is removed from the vent tube in several ways. For most applications the liquid will fill drain into the next container. For high viscosity (thick) liquids, the vent tube is usually brought out beyond the side or top of the bowl. Here its outer end can be connected to a device that applies pressure or vacuum to the liquid in the tube to assist in the liquid removal. The total differential pressure that allows the fluid to flow is caused by the gravity head pressure in the bowl. This is usually no more than two or three feet of head, or about one psi. On this basis, it can be seen that these fillers will not permit rapid filling of viscous liquids unless they have larger diameter filling stems. To accommodate the stem, the container must also have a large neck opening; otherwise machine modifications have to be made. ElGravity 150x150 Gravity Filling Machine PrinciplesAnother type of gravity filler uses electronics. It consists of a fixed liquid reservoir or bowl with open-end filling stems. The containers are conveyed on the filling line with an intermittent motion, stopping beneath the filling stems. Inside each filling stem is a ball check connected to a long rod. A pencil shaped magnetic block is attached to the top of the rod and passes through a magnetic coil. As the container moves under the stem, it is detected by a sensing device such as a limit switch or electric eye. This device stops the conveyor, and energizes the magnetic coil. The magnetic field causes the magnetic blocks to lift, raising the rod and the ball check from its seat inside the stem. The rate and amount of fill is controlled by the size of the stem orifice and time delay relay connected to the magnetic coil. Because a direct insertion filling tube is not used on this type of gravity filler the filling stem orifice must be smaller than the inside diameter of the container being filled. On small size containers a more positive means for positioning the bottle beneath the filling stem is used. Fill Height Control In addition to controlling fluid flow, control of the filling height is also important. In general filling machines that elevate the container control the fill height from the bottom of the bottle to the liquid level. The rise of the container is positive, and variations in overall container height are compensated for by greater or lesser seal compression. On rising container machines, a compression spring is often built into the tray elevating mechanism. In this case, container height variations are compensated for by the spring, and the fill height is then controlled from the top of the bottle to the liquid level. Controlling the fluid level from the top can be important if the bottle to be filled has square shoulders, because even a slight under fill is noticeable. In rising stem fillers, variation in container height is taken up by the stem itself. It is usually lowered by gravity or light spring pressure, so the fill height is controlled from the top of the bottle to the liquid level. If the product contains a volatile liquid, such as alcohol, control of the fill height is especially important. In this instance, excessive headspace could allow dangerous vapors to form and the bottle would possibly burst if it were stored in a hot warehouse. Therefore, controlling the fill height is an important function of the filling machine. Normally, a fill height tolerance of 1/32″ is acceptable. Container Control There are several devices used to control the containers coming into the filling area. Included are star wheels, worm or screw sorters, and lug chains. They can be used independently or in combination, depending on the type of container, the filling machine, and the product being placed in the container. The majority of all liquid filling machines operate as continuous filling devices. In most applications the machine has a large rotating filling head, which must be constantly supplied with containers. This is accomplished by a continuously running flat top chain conveyor feeding a star wheel or lead screw device. From here the containers are fed into the filling section. Star wheels when used alone separate the containers so they will be properly located beneath the filling stem. They can be made to handle a variety of container designs, although in some cases, the containers may have to be guided into the star wheel to ensure proper separation. Worm sorters are often used to guide containers into a star wheel. They can be short in length and only located near the machine in feed, or they may be full length of the machine’s main conveyor. The amount of container control determines the worm length. In most cases, worm sorters are very much like a wood screw; starting out small in diameter and then increasing to full diameter. A continuous pocket is formed at the root between the raised portion or crest of the thread. This pocket carries the container into its position on the filling machine by a rotating action. Because each container is different in design, worm sorters are usually made for individual applications and are not an “off-the-shelf” item. Lugged chains are normally used with inclined conveyors and semiautomatic filling machines. These machines can be either continuous or intermittent motion devices. The chain lugs are spaced to match the filling nozzles or stems. For example, if the filling stems are on four-inch centers. The chain is adjustable at the drive sprocket for timing purpose only. Position adjustments are usually made by moving the filling heads. Whatever method is used for container control, it is an important part of proper machine operation.
|
|
|
The Benefits and Drawbacks of an Air Suspension System |
Posted by: bbsiw25se - 08-25-2021, 04:55 AM - Forum: Welcomes and Introductions
- No Replies
|
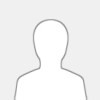 |
he United States developed the air suspension system during World War II specifically for heavy aircraft. The original purpose of air suspension was to save weight with a compact construction. Back then, air suspension systems were also used in other aircraft and some heavy trucks to achieve a self-leveling suspension. This would ultimately result in a vehicle with an axle height independent of the weight of a vehicle's cargo.
Ultimately, the air suspension system offers several benefits and drawbacks for drivers who rely on larger trucks and vehicles to carry heavy loads.
What Is an Air Suspension System?
An air suspension system is a style of vehicle suspension that's powered by an electric pump or compressor that pumps air into flexible bellows that are typically made out of a textile-reinforced type of rubber. Additionally, Pro Car Mechanics describes air suspension as a replacement to the leaf suspension or coil spring system with airbags composed of polyurethane and rubber. A compressor inflates the bags to a certain pressure in order to behave like springs. Air suspension also differs from hydropneumatic suspension because it uses pressurized air instead of pressurized liquid.
What's the Purpose of an Air Suspension System?
In most cases, air suspension is used to achieve a smooth and constant driving quality, but in some instances, sports suspensions feature an air suspension system too. Similarly, air suspension replaces a conventional steel spring suspension in heavier vehicle applications, like trucks, tractor-trailers, passenger buses, and even passenger trains. Air suspension has also become popular in low-riding trucks like this gorgeous 1982 Dodge D200 Camper Special.
What Is Electronically Controlled Air Suspension?
According to the company now known as Dunlop Systems and Components, at the start of the 1990s, Dunlop developed and installed the Electronic Controlled Air Suspension (ECAS) system on the 1993 Range Rover Classic and again on the Range Rover P38A. The United Kingdom-based company developed the ECAS to include several key features:
Vulcanized, heavy-duty rubber air springs at each of the vehicle's wheels
An air compressor in the vehicle's trunk or under the hood of the vehicle
A storage tank for compressed air, which allows you to store air at around an average of 150 PSI
Valve blocks which direct air to the four springs from the storage reservoir through a set of solenoids, valves, and o-rings
ECAS computer that communicates between the vehicle's main computer to calculate where to direct air pressure
Air pipes connecting from the storage tank to the air springs that channel the flow of air throughout the suspension system
A desiccant-filled drier canister to keep the internal recesses of the system dry
The electronically controlled air suspension also features height sensors that are based on sensing resistance in contact with the terrain on all four of the vehicle's corners to provide height reference for all corners. Additionally, further advancements are beginning to feature some Electronic Control Units (ECUs) that are able to fit under the vehicle's floorboard, making air suspension more widely featured in everyday driving.
The Benefits and Drawbacks of Air Suspension Systems
According to Future Marketing Insights, the total value of the air suspension market at the end of 2017 was around $4.3 million. So whether it's a manual or electronic air suspension system, the benefits can greatly improve the ride of the vehicle. Take a look of some of the benefits of air suspension:
More driver comfort due to the reduction in noise, harshness, and vibration on the road that can cause driver discomfort and fatigue
Less wear and tear on the suspension system due to reduced harshness and vibration of heavy-duty driving
Trailers last longer with air suspension because the system components don't take on as much vibration
Front air suspenions reduce the tendency of short wheelbase trucks to bounce over rougher roads and terrain when the vehicle is empty
Air suspension improves the ride height based on the load weight and a vehicle's speed
Higher corner speeds due to air suspension being better suited to the surface of the road
Air suspension increases the transport capabilities of trucks and trailers by providing a better grip that levels the entire suspension. An air suspension system can also be adjusted for feel, so drivers can choose between a softer feel for highway cruising or a harder ride for improved handling on more demanding roads.
In the case of hauling heavy loads, air suspension offers more consistency and keeps all wheels even. The air suspension system keeps trucks level from side to side, especially in cases where cargo is difficult to level. This results in reduced body roll when turning corners and curves.
Even with the benefits of an air suspension system, Driving Tests New Zealand suggests several drawbacks. Some of these disadvantages that so and so reports include:
The initial costs of purchasing and installing an air suspension system — air suspension can also sometimes reach three times the cost in repairs as a leaf suspension system over 10 years' time
Fuel overheads for running compressors for occasionally pumping air to the correct pressure
Fuel efficiency can suffer from the heavier weight of rear air suspensions over the weight of leaf suspension
An air suspension system's vulnerability to air leaks can result in malfunctions
Some of the drawbacks of air suspension systems are because of some of the mechanical issues they can be vulnerable to. Several of the common issues with air suspension systems that can require repair include:
Rust or moisture damage from the inside that can lead to the air struts or bags to malfunction
Failure of the air suspension tubing connecting the air struts or bags to the air system
Air fitting failure resulting from initial fitting or infrequent use
Compressor burn out due to air leaks in the springs or air struts from the compressor constantly engaging to maintain the proper air pressure
Even with these common mechanical problems, the benefits can far outweigh the drawbacks.
Understanding Compressors
Compressors are mechanical devices used to increase pressure in a variety of compressible fluids, or gases, the most common of these being air. Compressors are used throughout industry to provide shop or instrument air; to power air tools, paint sprayers, and abrasive blast equipment; to phase shift refrigerants for air conditioning and refrigeration; to propel gas through pipelines; etc. As with pumps, compressors are divided into centrifugal (or dynamic or kinetic) and positive-displacement types; but where pumps are predominately represented by centrifugal varieties, compressors are more often of the positive- displacement type. They can range in size from the fits-in-a-glovebox unit that inflates tires to the giant reciprocating or turbocompressor machines found in pipeline service. Positive-displacement compressors can be further broken out into reciprocating types, where the piston style predominates, and rotary types such as the helical screw and rotary vane.
In this guide, we will use both of the terms compressors and air compressors to refer mainly to air compressors, and in a few specialized cases will speak to more specific gases for which compressors are used.
Types of Air Compressor
Compressors may be characterized in several different ways, but are commonly divided into types based on the functional method used to generate the compressed air or gas. In the sections below, we outline and present the common compressor types. The types covered include: - Piston
- Diaphragm
- Helical Screw
- Sliding vane
- Scroll
- Rotary Lobe
- Centrifugal
- Axial
Due to the nature of the compressor designs, a market also exists for the rebuilding of air compressors, and reconditioned air compressors may be available as an option over a newly purchased compressor.
Piston Compressors
Piston compressors, or reciprocating compressors, rely on the reciprocating action of one or more pistons to compress gas within a cylinder (or cylinders) and discharge it through valving into high pressure receiving tanks. In many instances, the tank and compressor are mounted in a common frame or skid as a so-called packaged unit. While the major application of piston compressors is providing compressed air as an energy source, piston compressors are also used by pipeline operators for natural gas transmission. Piston compressors are generally selected on the pressure required (psi) and the flow rate (scfm). A typical plant-air system provides compressed air in the 90-110 psi range, with volumes anywhere from 30 to 2500 cfm; these ranges are generally attainable through commercial, off-the-shelf units. Plant-air systems can be sized around a single unit or can be based on multiple smaller units which are spaced throughout the plant.
To achieve higher air pressures than can be provided by a single stage compressor, two-stage units are available. Compressed air entering the second stage normally passes through an intercooler beforehand to eliminate some of the heat generated during the first-stage cycle.
Speaking of heat, many piston compressors are designed to operate within a duty cycle, rather than continuously. Such cycles allow heat generated during the operation to dissipate, in many instances, through air-cooled fins.
Piston compressors are available as both oil-lubricated and oil-free designs. For some applications which require oil-free air of the highest quality, other designs are better suited.
Diaphragm Compressors
A somewhat specialized reciprocating design, the diaphragm compressor uses a motor-mounted concentric that oscillates a flexible disc which alternately expands and contracts the volume of the compression chamber. Much like a diaphragm pump, the drive is sealed from the process fluid by the flexible disc, and thus there is no possibility of lubricant coming into contact with any gas. Diaphragm air compressors are relatively low capacity machines that have applications where very clean air is required, as in many laboratory and medical settings.
Helical Screw Compressors
Helical-screw compressors are rotary compressor machines known for their capacity to operate on 100% duty cycle, making them good choices for trailerable applications such as construction or road building. Using geared, meshing male and female rotors, these units pull gas in at the drive end, compress it as the rotors form a cell and the gas travels their length axially, and discharge the compressed gas through a discharge port on the non-drive end of the compressor casing. The rotary screw compressor action makes it quieter than a reciprocating compressor owing to reduced vibration. Another advantage of the screw compressor over piston types is the discharge air is free of pulsations. These units can be oil- or water- lubricated, or they can be designed to make oil-free air. These designs can meet the demands of critical oil-free service.
|
|
|
PA Speaker Buying Guide |
Posted by: bbsiw25se - 08-25-2021, 04:54 AM - Forum: Welcomes and Introductions
- No Replies
|
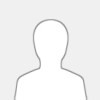 |
How to Choose PA Speakers
Achieving consistently high-quality live sound can be a challenge. Your choice of PA speakers can determine whether you’re mixing to make something good sound great or struggling to solve sound-reinforcement problems. There are three basic categories of PA systems:
Personal PAs
Medium-sized PAs
Full-scale PAs
Personal PAs consist of single speakers or mini speaker arrays, which serve as both main speakers and monitors. Medium-sized PAs consist of a pair of stand-mounted speakers on either side of the stage plus simple monitor wedges. Full-scale PA systems involve multi-speaker line arrays and complex monitoring systems.
We’ve created this Sweetwater Buying Guide to provide you with the information you’ll need when you’re ready to invest in new PA speakers. Since there’s so much more to consider than what we can possibly cover here, give your Sales Engineer a call at (800) 222-4700 after checking out this guide. They can help you choose the best PA speakers for your situation.
How Much Power Do I Need?
At Sweetwater, we’re often asked how much power is required for a PA system. But the real question is “How loud do you need it to be?” as your power requirements will vary according to your situation. Are you performing low-volume acoustic folk or high-volume progressive metal? A classical presentation or an EDM performance? The size of the venue is also important, as is the number of people attending (human bodies make terrific sound absorbers). A medium-sized venue (250–500 people) may require 2,000 watts or as much as 20,000 watts, based on these factors.
So, is it all about wattage? Not necessarily. After all, more power doesn’t necessarily mean more output. While a speaker’s wattage definitely affects its volume, its maximum SPL (Sound Pressure Level) is a better indicator of how loud the speaker can go. Understanding a speaker’s coverage angle is also important. A powerful speaker with a narrow coverage angle will reach fewer people than a less powerful one with a broader coverage angle. It’s also vital that you consider the speaker’s sensitivity, which is a measurement of its ability to effectively convert power into sound. In a nutshell, sensitivity refers to the SPL that a speaker can produce from a 1-watt signal at a distance of 1 meter. This sensitivity spec measures “efficiency” and is a strong indicator of a speaker’s loudness, which is why a less efficient 1,000-watt speaker isn’t necessarily louder than an efficient 500-watt speaker. In fact, a 500-watt speaker with a sensitivity of 98dB will actually be the same volume as a 1,000-watt speaker with a sensitivity of 95dB.
soundbar
A TV or home theater speaker system in a single cabinet. Soundbar speakers are designed for apartments or venues where discrete speakers are not desired throughout the room. Self powered, soundbars often support a wireless subwoofer for maximum bass response, which can be conveniently located anywhere in the room. In the more sophisticated systems, "virtual surround sound" is produced by psychoacoustic effects that adjust the timing and volume of the various speakers. Some units bounce the sound off side and back walls, which can be effective in small rooms, while others do not rely on precise placement.
The Soundbase
A soundbase is a soundbar that is deeper and flat so the TV stand can be placed on it. See home theater, home theater speakers and home theater in a box.
Why Ceiling Speakers Are Good (Worth It) For Surround Sound
While I was remodeling my home theater, I decided to take a look at ceiling speakers to increase my surround sound, but I found they were going to take a lot of work. This got me wondering whether ceiling speakers were worth the hassle.
So, are ceiling speakers any good?
Ceiling speakers make a great addition to a home theater, particularly if you’re looking for a more immersive sound experience. They need to be specifically designed for ceilings, but they make an excellent addition to a surround sound setup.
When Are Ceiling Speakers A Good Addition?
It’s fair to say that not everyone’s home theater will benefit from ceiling speakers. After all, if you’ve only got a small room dedicated to your home theater, you might already have enough speakers.
Also, if you live in a rented property, you might not be able to carry out the work necessary to install them. These are some of the situations when you’ll probably see the most benefit from ceiling speakers:
1. They’re less messy
Sure, speakers aren’t usually considered ugly, but many people prefer to minimize clutter as much as possible.
If you’re building a home theater, you’ll inevitably have cables running everywhere, and so at least mounting your speakers in the ceiling means you have a few less cables to worry about.
2. They’re a good way of completing a surround sound system
You’ve already got a set of “normal” speakers (think bookshelf speakers or monitors) then you might not want to go out and buy a new surround sound system.
Ceiling speakers are a potentially easier way of completing this, as you can mount them behind your seating area and use them as the rear channels.
3. They allow you to be more flexible with your layout
If you choose to mount your speakers in the ceiling, then you won’t have to worry as much about positioning your furniture around floor speakers.
Not only will this mean fewer cables, but if you get swiveling ceiling speakers, then you’ll have plenty of freedom over where to put your furniture.
4. They give you a more immersive experience
Surround sound is all about immersion, so why not get the most out of your home theater? Cinemas use ceiling speakers for the same reason, so it makes sense to splash out on some if you can.
Woofers
A woofer is a speaker that is sized and constructed so that it can reproduce low and mid-range frequencies. Woofers do most of the work in reproducing the frequencies you hear, such as voices, most musical instruments, and sound effects.
Depending on the size of the enclosure, a woofer can be as small as 4 inches in diameter or as large as 15 inches. Woofers with 6.5-inch to 8-inch diameters are common in floor standing speakers. Woofers with diameters in the 4-inch and 5-inch range are common in bookshelf speakers.
Tweeters
A tweeter is a specially designed speaker that is smaller than a woofer. It only reproduces audio frequencies above a certain threshold, including, in some cases, sounds that human ears cannot hear but only sense.
Because high-frequencies are highly directional, tweeters disperse high-frequency sounds into the room so that the sounds are heard accurately. If the dispersion is too narrow, the listener has a limited amount of listening position options. If the dispersion is too wide, the sense of direction of where the sound is coming from is lost.
These are the different types of tweeters: - Cone: A smaller version of a standard speaker.
- Dome: The voice coil is attached to a dome that is made of fabric or a compatible metal.
- Piezo: Instead of a voice coil and cone or dome, an electrical connection is applied to a piezoelectric crystal, which in turn vibrates a diaphragm.
- Ribbon: Instead of a traditional diaphragm, a magnetic force is applied to a thin ribbon to create sound.
- Electrostatic: A thin diaphragm is suspended between two metal screens. The screens react to an electrical signal in such a way that the screens become out-of-phase. This alternately attracts and repels the suspended diaphragm, creating the needed vibration to create sound.
Mid-Range Speakers
A speaker enclosure may incorporate a woofer and tweeter to cover the entire frequency range. However, some speaker makers add a third speaker that further separates the low-range and mid-range frequencies. This is referred to as a mid-range speaker.
There are many ways to add new life to your music in the car, but new speakers offers one of the fastest and most cost-effective ways to upgrade your sound. We have what you need, whether you just want to replace your factory speakers or if you plan to install an amplifier and need speakers that can handle a lot of power.
Shopping for car speakers can be confusing, so we try to make the process as straightforward as possible. Watch the video below for an overview on how to shop for new car speakers.
Crutchfield makes it easy to shop for car speakers
The first thing you'll need to do is use our vehicle selector to tell us what you drive. We'll ask a few questions and then show you the best options for your vehicle.
The Crutchfield car speaker recommender
Once you've told us what you drive, you'll find the car speaker recommender at the top of the car speakers category page.
The recommender is a great tool that could land you the perfect set of speakers in minutes.
How many car speakers do I need?
There's no standard for the number of car speakers that are factory-installed in a vehicle. In fact, they seem to get more numerous every year as car makers introduce premium factory sound systems with perks like noise cancellation and simulated engine noise. But for this article, we'll stick to the basics.
When replacing front and rear speakers, a good goal is to have a voice-matched system. That means having the same brand and series of speakers in the front and rear. If you're on a budget, that doesn't have to happen all at once. Focus on your front speakers first. When you're ready, update the rear with speakers from the same speaker series (or at least, the same brand) for consistent sound characteristics.
Speakers for the front of your vehicle
Some vehicles only have two speakers in the front, one per door. They use a full-range design. Other vehicles feature four speakers in the front, two per side. This is typically woofers in the door and a tweeter either higher up in the door or in the corner pillar or dash.
Many vehicles also have a center dash speaker, which typically handles vehicle essentials like door chimes and navigation prompts, in addition to playing music. Many people opt to leave the original speaker in this spot.
Speakers for the rear of your vehicle
Rear door speakers, rear deck speakers, and tailgate speakers are often full-range, although components have become increasingly popular. Rear speakers provide sound to backseat passengers and "rear fill" for the front row. Rear speakers generally don't make a significant contribution to the sound experience in the front seats. As a result they can be less important to drivers who don't have passengers very often or to sound enthusiasts who don't want any interference with their front soundstage.
What size speakers should I buy?
It's easy to feel overwhelmed by a long list of car speakers, all with different sizes. The good news is you don't have to sweat speaker size too much once you've told us what vehicle you're shopping for and whether you're shopping for front or rear speakers (or both).
Sometimes you'll have a choice of a couple speaker sizes for a given location. In that case our rule of thumb is, "the bigger the better." So, given the choice between a 5-1/4" using a bracket or a 6"x9", we'll usually say go with the 6"x9" for more oomph.
The finer points of fitting car speakers
When looking at speaker fit, we're not just talking about the diameter of the speaker opening. We're also considering the allowable depth of that opening, sufficient room for the tweeter in front of the speaker, and several other factors. You can learn more about the details in our article about understanding speaker sizes. If speaker brackets are required to install your speakers, we'll include them.
Full-range vs. components — what type of speakers should I get?
Aftermarket car speakers can be divided into two main categories: full-range speakers and component speaker systems. Let's take a look at each.
Full-range speakers
Full-range speakers contain all the speaker elements in one basket. In their simplest form, they consist of a woofer for the lows, and a tweeter mounted onto the woofer to produce the highs. Some models will have additional drivers, like a midrange and/or supertweeter – these are referred to as "3-way" or "4-way" speakers.
|
|
|
Choosing a High-Resolution Graphic Design Monitor |
Posted by: bbsiw25se - 08-25-2021, 04:52 AM - Forum: Welcomes and Introductions
- No Replies
|
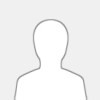 |
A graphic monitor is one of the most important pieces of hardware a design professional can buy. Look for the right technical specifications, including color accuracy, screen size, panel type, resolution, and more.
Use our guide below to streamline the process of buying a professional graphic design monitor. Or see how ViewSonic put it all together into making professional monitors.
Those new to graphic design may not place picking a graphic design monitor at the top of their priority list, but it might be the difference between success and failure. Graphic design is all about creating designs that leave lasting impressions and communicate a message to the viewer. In essence, it creates a bridge between the designer and the viewer.
If you’re a graphic designer, then you know the ins and outs of the world of graphic design and the significance that presentation plays. Getting positive reviews on any form of graphic design work is all about how the design is visually presented.
What Are Graphic Design Monitors, and What Are They Good For
Would you design graphics with your shades on? Probably not. Portraying the wrong colors on-screen is exactly why having the wrong monitor can be perilous to your work. As such, obtaining a high-resolution graphic design monitor is one of the best ways you can ensure that your work will stand out visually. Needless to say, this is one investment you definitely want to make for the sake of your career path as a graphic designer.
The Drawbacks of Graphic Design Monitors
Before getting into the areas you should be looking into prior to purchasing an ideal graphic design monitor, let’s consider the drawbacks.
Oftentimes, when it comes to purchasing electronics, customers are duped into purchasing products with unnecessary features. Of course, avoidance of this issue is easier said than done. That said, it’s understandable. In today’s well-marketed and materialistic world, it is easy to find yourself wrongly swayed. Though, if you read up on graphic design monitors, the following factors should help keep your decision-making on the level. - Design
Don’t ever select a monitor simply because it looks cooler than the others. A monitor that is very slim may look attractive, but that’s pretty much as far as it goes. The graphic drawing pen monitor’s internal specifications are what determines how well it will perform, not the exterior. As they say, “don’t judge a book by its cover”, so too, don’t judge a monitor solely on its looks.
- Bloated qualities
Built-in speakers, a good range of USB ports, and a proper TV Tuner shouldn’t distract you from considering a monitor’s internal setup. Even though these are great features for a monitor to possess, they do not guarantee an overall high-quality product.
- Response time
If you are a certified graphic designer, as opposed to a professional gamer, response time shouldn’t really matter. Basically, the response time determines the time delay when a rapid action takes place on the screen. For gamers, as many actions are taking place on-screen within short periods of time, a good response time ensures the gamer’s ability to play at the proper speed, without lags on screen.
What to Look for in Potential Graphic Design Monitors
Serious graphic designers want a display that not only brings an optimal level of performance but also includes a high resolution. In today’s world of wireless connections, a good display is properly wired with the newest routes for connectivity. After all, the world runs on the ability to remain connected and linked. When it comes to purchasing the right monitor, a serious graphic designer knows that there’s more to it than simple numbers. That’s part of what makes ViewSonic’s VP line of monitors so attractive.
As with all other technology, purchasing a monitor requires you to do some background reading. While there are quite a few selections out there, unless you know the exact specifications, you might end up purchasing an LCD that doesn’t present your work with justice.
The following provides you with a list of things you want to consider before finalizing any monitor purchases.
A graphics drawing tablet used for sketching new images or tracing old ones. Also called a "graphic tablet," the user contacts the surface of the device with a wired or wireless pen or puck. Often mistakenly called a mouse, the puck is officially the "tablet cursor."
For sketching, either the pen or puck is used. For tracing, the puck is preferred because its crosshairs, visible through a clear glass lens, lets you precisely pinpoint ends and corners of detailed drawings.
Most tablets allow parts of the tablet surface to be customized into buttons that can be tapped to select menus and functions in the application.
Digitizer Mode and Mouse Mode
Tablets typically support two modes of operation. "Digitizer mode" creates a one-for-one correspondence between tablet and screen. Wherever the tablet is touched, the screen is drawn in the exact same location. In contrast, "mouse mode" moves the screen pointer (cursor) relative to any starting position on the tablet surface, just like an ordinary computer mouse.
The Output Is X-Y Coordinates
When drawing or tracing on the tablet, a series of x-y coordinates (vector graphics) are created, either as a continuous stream of coordinates, or as end points. See pen tablet, tablet PC and touchscreen.
What Are All-In-One Personal Computers?
All in one Pc is like conventional desktop computer systems in terms of features and functionality. The only difference between an all-in-one vs. a desktop PC is the number of components. While desktops are comprised of the computer case plus a separate monitor, all-in-ones combine the display and the computer into one package. This consolidation gives the all-in-one computer system a smaller profile than a desktop computer system.
What Are All-In-One PCs?
The earliest form of computer displays used large cathode-ray tubes. Because of the size of the displays, computer systems were comprised of three key components: the monitor, the computer case, and the input devices.
As the size of the monitors decreased and the computer market consolidated into IBM-compatible and Apple-compatible product lines, computer companies started to integrate the computer case into the monitor to create all-in-one designs. These first all-in-one computer systems were still large and cost more than a standard desktop setup.
The most successful of the all-in-one personal computers was the Apple iMac. The original design used the cathode-ray monitor with the computer boards and components integrated below the tube.
With the advent of LCD monitors for displays and mobile parts getting smaller and more powerful, the size of the all-in-one computer system has decreased dramatically. Now, the computer components can be easily integrated behind the LCD panel or into the base of the display.
All-In-One vs. Desktop PCs
Buying a desktop offers several advantages over purchasing an all-in-one PC. Many all-in-one PCs feature processors (CPUs), drives, memory (RAM), and other components designed for laptops. Such architecture makes the all-in-one compact, but they also hinder the overall performance of the system. Typically, these laptop components will not perform as well as a desktop benchmark.
Another challenge with all-in-one computers is the lack of upgrade options. While most desktop computer cases can be opened to install and replace components, all-in-one systems feature a closed design. This design approach typically limits the systems to having only their memory upgraded.
With the rise of high-speed external peripheral connectors such as USB 3.0 and Thunderbolt, internal upgrade options are not as critical as they once were, but they still make a difference for some components such as the graphics processor.
All-In-Ones vs. Laptops
The all-in-one is smaller than a desktop, but it still is tethered to a desktop space. Laptops, conversely, move between locations and supply power through their battery packs. This portability makes them more flexible than the all-in-one.
Because many all-in-one PCs use all the same components as laptops, the performance levels are mostly identical between the two types of computers. The only advantage that an all-in-one PC might hold is the size of the screen. While all in one drawing Pc generally come with screen sizes between 20 and 27 inches, laptops are still generally restricted to 17-inch and smaller displays.
All-in-one systems used to be less expensive than laptops, but with technological advancements, the tables are now almost turned. You'll find many laptop computers for less than $500 while the typical all-in-one system now costs roughly $750 or more.
How Wacom Tablets Work
Let's get our definitions straight here, folks: Unlike the iPad, the Kindle Fire or the Nook, online teaching graphic tablet is not your average tablet PCs. Nor do they strive to be -- they're graphics tablets (also called pen tablets), devices generally used in the graphic design industry or by digital artists that allow a person to draw by hand, capturing an image or graphic in digital form. The information is displayed on the monitor of a connected PC or Mac.
Sounds a little complicated, but imagine this: You're working at your computer when the fancy strikes you to doodle a picture of a cartoon chicken eating broccoli. (Doodles don't have to make sense.) You use the pen and paper next to you. After sitting there for a day or so, it's absent-mindedly put in the trash, only to decompose slowly in a landfill, your artistic genius never recognized.
Unacceptable. Wacom tablets, which comprise many different models that we'll detail in this article, are designed so you can digitally doodle straight into your computer (among far more important tasks). Basically, they're the technological mating of a computer mouse with a pencil and a computer monitor with a college-ruled notebook.
Not a perfect analogy. But graphic designers, artists, illustrators and many other hobbyists and professionals need a device that allows their hand-drawn work to be digitized or their digital image to be manipulated with an old-fashioned hand. The technology powering Wacom tablets provides a few advantages over click-and-point navigation. The pen, or stylus, that comes with the tablets can communicate much more effectively. Its pressure-sensitive system will let you determine things like how thick or thin a line should be, and it can instantly capture handwritten notations. The tablet communicates with the pen, plotting its location in microseconds as it makes your adjustments on screen.
Graphic designers could benefit from the ease of turning concepts into digital reality. A photographer might like to be able to manipulate an image by hand more carefully. And pretty much everyone thinks it's cool to have their hand-written notes or doodles appear on their computer in the time it takes to put pen to paper.
Unlike an iPad-like tablet, Wacom offers several different lines and models. Let's first take a look at the technology and hardware that's common to all of the tablets to grasp exactly how a Wacom tablet functions.
We really have to start with the pen; Wacom refers to the pen's system as Penabled Technology. Sure, it looks like a regular pen but inside lurks a digital chip, a modulator and a transmitter. All of those components work in a complicated manner, but we can break it down: The tip of the pen tells the tablet what to do. And it's done with magnets! Well, not exactly. The sensor board of the tablet has a magnetic field, and the pen produces its own magnetic field -- and energy -- from it. (That's why no batteries or power adapter is needed.)
The magnetic field emanating from the pen is recognized by the sensor board. From that, it can track the pen's location, pressure and speed. The sensor board itself is made up of a lot of little antenna coils, but it also has a control board that monitors the coils to determine where the current is (i.e., where the pen is). And that's what tells your computer that you want to add a moustache to the picture of your sister that you're photoshopping. Wacom calls this patented technology EMR, or electromagnetic resonance technology.
It's a little different if an LCD screen is used, which is the case with the Cintiq line of tablets. In that case, backlighting or a component that gives off its own field could disrupt the pen's magnetic field. As such, all metal or problem parts must be tightly shielded to block out the field. The metal frame around the LCD screen -- which undoubtedly affects magnetic fields -- is accounted for in the control board, which recognizes a "weak" signal from the pen and corrects it so it follows a predictive course.
|
|
|
|