Welcome, Guest |
You have to register before you can post on our site.
|
Online Users |
There are currently 271 online users. » 0 Member(s) | 270 Guest(s) Google
|
Latest Threads |
Dominica visa free countr...
Forum: Off Topic
Last Post: axied12
06-24-2025, 12:37 PM
» Replies: 0
» Views: 160
|
Advanced microneedling
Forum: Off Topic
Last Post: axied12
05-28-2025, 01:25 PM
» Replies: 0
» Views: 290
|
Caviar and cheese
Forum: Off Topic
Last Post: axied12
05-28-2025, 12:38 PM
» Replies: 0
» Views: 257
|
Top-rated countertop comp...
Forum: Off Topic
Last Post: axied12
05-04-2025, 06:42 AM
» Replies: 0
» Views: 393
|
Ryanair letenky levně do ...
Forum: Off Topic
Last Post: axied12
02-11-2025, 01:37 PM
» Replies: 0
» Views: 789
|
Trusted essay writing ser...
Forum: Off Topic
Last Post: axied12
01-30-2025, 08:16 AM
» Replies: 0
» Views: 719
|
Bootverkopers - actieve j...
Forum: Off Topic
Last Post: axied12
12-07-2024, 11:07 AM
» Replies: 0
» Views: 843
|
Services for individuals ...
Forum: Off Topic
Last Post: axied12
12-02-2024, 03:31 PM
» Replies: 0
» Views: 815
|
Used excavators
Forum: Off Topic
Last Post: axied12
11-13-2024, 09:22 AM
» Replies: 0
» Views: 766
|
Buy Higo Rocket in Dubai
Forum: Off Topic
Last Post: axied12
10-25-2024, 01:09 PM
» Replies: 0
» Views: 876
|
|
|
Roll forming of a high strength aluminum tube |
Posted by: nsj5521sw - 08-24-2021, 03:01 AM - Forum: Welcomes and Introductions
- No Replies
|
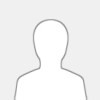 |
The presented paper provides a modelling strategy for roll forming of a high strength aluminum alloy tube. Roll forming allows the cost-effective production of large quantities of long profiles. Forming of high strength aluminum brings challenges like high springback and poor formability due to the low Young’s modulus, low ductility and high yield strength. Forming processes with high strength aluminum, such as the AA7075 alloy, therefore require a detailed process design. Three different forming strategies, one double radius strategy and two W-forming strategies are discussed in the paper. The paper addresses the question whether common roll forming strategies are appropriate for the challenge of roll forming of a high strength aluminum micro channel tube. For this purpose, different forming strategies are investigated numerically regarding buckling, longitudinal strain distribution and final geometry. While geometry is quite the same for all strategies, buckling and strain distribution differ with every strategy. The result of the numerical investigation is an open tube that can be welded into a closed tube in a subsequent step. Finally, roll forming experiments are conducted and compared with the numerical results.Current research in production technology focuses primarily on increasing resource efficiency and thus follows the approach of fundamental sustainability of processes and products. High strength aluminum alloys (e.g. AA7075) are commonly used in aerospace applications in spite of their high cost of about 5 €/kg and poor formability [1]. Due to ambitious legal requirements, such as the CO2 target in automotive engineering, new lightweight construction concepts are still needed [2]. An excellent basis is offered by the production of high strength AA7075 thin walled tubes as semi-finished products by roll forming. These can be further processed in subsequent customized processes such as welding, stamping, cutting or rotary swaging.
According to DIN 8586, roll forming is a bending technology with rotating tool motion to produce open and closed profiles [3]. Several pairs of forming rolls are aligned one behind the other for the forming process. The friction between the rotating forming rolls and the sheet metal causes a forward movement of the sheet. Simultaneously the sheet is formed in and between the stations. For the production of large quantities, roll forming is a cost-effective manufacturing process, compared to tube extrusion or tube drawing. Roll forming can also be competitive for smaller quantities, if the number of forming passes is small enough [4]. The incremental nature of the roll forming process also allows forming of high strength materials, such as ultra high strength steel (UHSS) [5].
During roll forming there is a limit for the amount of deformation regarding buckling limit strain (BLS), which can be reached in one forming station [6]. Abeyrathna [5], Park [7] and Bui [8] showed that longitudinal strain has a major impact on product defects, such as bow or buckling. The maximum longitudinal strain occurs in the area of the band edge. Plastic elongation in the roll gap between the forming rolls followed by compression when the sheet leaves the forming rolls leads to buckling. Figure 1 illustrates the elongation, followed by compression when forming a tube. To prevent buckling, the maximum longitudinal strain must be low. Once buckling takes place, welding of the formed tube becomes very difficult or even impossible [9]. Parameters with a large influence on buckling are the stiffness of the sheet and the yield strength of the material. According to Halmos [10], elongation of the band edge depends on the flange height and inter-station distance ld. High bending angles of a single forming station Θp and a small inter-station distance ld lead to large elongation of the band edge and thus to buckling. For circular sections (e.g. tube), the BLS is 5–10 times higher than the BLS for a U-profile [6].Groche et al. [11], Park et al. [7], Zou et al. [12] and Lee et al. [13] showed that roll forming of high strength materials and especially of high strength aluminum drawn tube brings challenges compared to commonly roll formed steel grades. High strength leads to high springback and thus to less dimensional accuracy in the processed part. Parameters, which have an influence on springback are shown in Table 1. Difficulties regarding aluminum include early fracture due to low ductility, higher springback and redundant deformation. This requires a well-designed forming strategy in order to get the lowest possible springback and buckling in the roll forming process and the best quality of the processed part. In contrast, aluminum shows a good-natured behavior with regard to buckling due to a higher value of BLS compared to steel [14].The single radius-forming strategy has the advantage to form tubes with different sheet thickness on the same tool. A flower pattern with constant bending radius over the entire cross-section of the sheet is characteristic for the single radius-forming. For high-strength materials, the single radius-forming strategy is not applicable due to high springback caused by the high elastic bending content [10, 18].
The double radius- and W-forming strategies are appropriate for high strength steels. For both strategies, two radii are combined in each pass, whereby the radius in the edge area is equal to the end radius already in the first pass of the process [18]. In contrast to double radius forming, a negative bending is initially introduced in the middle section in the W-forming process. The main advantage of this strategy is that the final radius can be formed into the band edge area at the first pass of the process [18]. Another approach is described by Jiang et al. [19] with a cage roll forming mill for the production of electric resistance welded pipes.
The height displacement of the profile is called “up-hill” or “down-hill”. During the down-hill strategy, the profile is lowered step by step in each pass. The use of a down-hill forming strategy can reduce plastic elongation in the band edge and thus the number of forming stations [10]. Based on the fundamental differences in roll forming between aluminum and steel, this publication addresses the question if one of the strategies suits for forming a tube of the high-strength aluminum alloy AA7075.
FE-Simulation of the roll forming process
The roll forming tools are designed by numerical simulation of the process. The target geometry is a tube with an outer diameter of d=54.98mm (ro=27,49mm/ri=25,99mm) and a wall thickness of s0=1.5mm. An AA7075-T6 aluminum alloy is used for the roll forming process. Table 2 shows the mechanical properties of the alloy.The first forming strategy suggested automatically by UBECO Profil after defining the target geometry is a double radius-forming strategy and has 27 passes in total. Based on tube forming sequences in literature [15, 16], the number of passes is reduced to 14 passes by skipping every second pass, in order to increase process efficiency. After the reduction to 14 passes, the edge strain is still below the critical limit in every stage of the process according to the PSA. The approach for the first forming strategy is to form the tube in uniform increments and to keep the longitudinal strain low in the band edge. The further approach is to calculate the stresses of the formed tube to arrive at the number of passes required. Forming strategy 2R is the first strategy numerically investigated by the FE-software Marc Mentat.In this paper, roll forming of a high strength extruded aluminum tube is investigated. Due to the difficult determination of the design parameters, roll forming of high strength aluminum is a challenge. Conventional roll forming strategies quickly reach their limits when forming aluminum or high strength steels. To form a tube out of high-strength aluminum alloys such as AA7075, a W-forming strategy is recommended. Another positive influence is the application of a down-hill strategy. The investigations have shown that an efficient roll forming production line for high strength aluminum tubes can be set up even with a small number of forming passes. The W-forming strategies showed a good behavior with regard to buckling, compared to the double radius forming strategy. Forming strategy W2 combines the advantages of few passes with a good final part geometry thanks to detailed process design. The numerical investigation and the following experiments demonstrated the feasibility of roll forming a high-strength aluminum tube. It is shown that conventional design methods are also valid for high-strength materials.A further result of the numerical investigation is that the design of the tools should not be based on longitudinal strain in the band edge alone. For a first estimation, the elongation of the band edge is a valid factor, but for an exact process design a numerical simulation should always be performed. In addition, BLS is material dependent, which makes an analytical calculation even more difficult.
Regarding the springback angle, the experimental investigations show little deviations from the FE-model. The reasons for this are the simplified material model, which does not consider combined hardening effects, the influence of the smaller modulus of elasticity after plastic deformation and compliance of the forming stand. Nevertheless, the simplified FE-model provides sufficiently accurate results regarding buckling and geometry of the tube.
Axial crash of thin-walled circular seamless aluminum tube is investigated in this study. These kinds of tubes usually are used in automobile and train structures to absorb the impact energy. An explicit finite element method (FEM) is used to model and analyse the behaviour. Formulation of the energy absorption and the mean crash force in the range of variables is presented using design of experiments (DOE) and response surface method (RSM). Comparison with experimental tests has been accomplished in some results for validation. Also, comparison with the analytical aspect of this problem has been done. Mean crash force has been considered as a constraint as its value is directly related to the crash severity and occupant injury. The results show that the triggering causes a decrease in the maximum force level during crash.
|
|
|
Electric cables are normally installed on the assumption of a safe working life |
Posted by: zjjsw25ss - 08-23-2021, 07:06 AM - Forum: Welcomes and Introductions
- No Replies
|
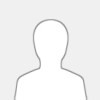 |
Electric cables are normally installed on the assumption of a safe working life of at least 20 years. Changes in the insulating material take place with the passing of time and these changes, which may eventually result in an electrical breakdown, are accelerated at higher temperatures. Thus, if the working life is fixed, the limiting factor is the temperature at which the cable is required to operate.
During operation, the temperature at which the cable will operate depends upon the ambient temperature and the heating effects of the current produced due to the resistance of the cable conductors.
The heat dissipation of buried cables depends on the depth of laying, ground ambient temperature and its thermal resistivity, these being dependent on their geographical location and the season of the year. Nearby cables would also affect the ground temperature. Cables in air reach steady operating temperatures more quickly than similar cables underground and large cables take longer than small ones.
The heat may cause a change in the properties of an insulating material or in extreme cases, deformation may occur. It is important, therefore, to realise that there is “a cable for the job”.
There is a very wide range of cables designed to operate at voltages up to 400 kV. It is not possible to discuss all these in this book, but the reader is referred to a publication, Copper Cables, published by the Copper Development Association.
The majority of cables have copper conductors and in a cable these may vary from a single conductor to stranded construction.
The number of electric wire contained in most common conductors is 3, 7, 19, 37, 61 or 91. Thus, 37/0·083 indicates that the conductor has 37 wires each having a diameter of 0·083 in.
Study of electric cable used for 18 years outdoors in Romania shows that only 2% of original quantity of di-(2-ethylhexyl) phthalate has been lost during service life. Formulation was stabilized with lead stabilizer. Twenty percent of original stabilizer was used and required replacement in recycling process.3
A similar study in Sweden (see formulation in the next section) showed that only 1% of extractable matter was lost during 30-40 years of cable use, material was thermally stable, and mechanical performance measured by elongation changed very little. Experimental studies conducted in laboratory which simulated service life by thermal aging at 80°C and considering activation energy in Arrhenius equation at 95 kJ/mol showed that cables should perform for at least 44 years. The cables collected from field are suitable for recycling with minimal adjustments to formulation. Figure 13.19 shows that stability of insulation has linear relationship with duration of aging. Figure 13.20 shows that changes in elongation are very small.4
Degradation of insulation performance of electric cables is basically evaluated by tests and analyses. Based on the result of equipment qualification tests, subsequent analyses to confirm the integrity after a 60-year service period of cables and the result of insulation resistance measurement and insulation diagnostic tests, it has been concluded that immediate degradation of insulation performance is unlikely to occur for most types of cables.
Degradation of insulation performance is detected by the insulation resistance measurement, insulation diagnostic tests and performance tests of systems and components, which are performed during the inspection.
The Japanese government commenced a national R&D project on cable ageing to have more accurate prediction. Under this project many experiments are being performed to acquire time dependent data of cable ageing. Superposition of the time dependent data proposed by IEC 1244-2 is proposed as a suitable method to predict cable ageing.
The Japanese plant utilities conduct measurement of insulation resistance to monitor degradation of insulation performance and are planning to perform sample investigation to acquire actual degradation data of cable insulations.
An area of rubber cable technology where much research and development work has been concentrated in recent years is that of the behaviour of cables in fires. Although they may overheat when subject to current overloads or mechanical damage, electric cables in themselves do not present a primary fire hazard. However, cables are frequently involved in outbreaks of fire from other causes which can eventually ignite the cables. The result can be the propagation of flames and production of noxious fumes and smoke. This result, added to the fact that cables can be carrying power control circuits which it is essential to protect during a fire to ensure an orderly shutdown of plant and equipment, has led to a large amount of development work by cablemakers. This work has included investigations on a wide range of materials and cable designs, together with the establishment of new test and assessment techniques.
Although PVC is essentially flame retardant, it has been found that, where groups of cables occupy long vertical shafts and there is a substantial airflow, fire can be propagated along the cables. Besides delaying the spread of fire by sealing ducts at spaced intervals, an additional safeguard is the use of cables with reduced flame propagating properties. Attention has also been focused on potential hazards in underground railways, where smoke and toxic fumes could distress passengers and hinder their rescue. Initially, compounds with reduced acidic products of combustion were incorporated in cables which have barrier layers to significantly reduce the smoke generated. In the meantime, other cablemaking materials have been developed which contain no halogens and which also produce low levels of smoke and toxic fumes as well as having reduced flame propagating properties. These are now incorporated in British Standards such as BS 6724 and BS 7211.
A different requirement in many installations, such as in ships, aircraft, nuclear plant and the petrochemical industry (both on and off-shore), is that critical circuits should continue to function during and after a fire. Amongst the cables with excellent fire withstand performance, mineral insulated metal sheathed cables are particularly suited for use in emergency lighting systems and industrial installations where ‘fire survival’ is required. As fire survival requirements on oil rigs and petrochemical plants become more severe, new control cable designs have been developed to meet fire tests at 1000°C for 3h with impact and water spray also applied, and also to have low smoke and low toxic properties.
Another novel approach to fire protection in power stations and warehouses is the use of fire detector cables (Figure 31.4). These are used in a system which both detects and initiates the extinction of a fire in the relatively early stages of its growth. These cables have also been installed in shops, offices and public buildings, where the cables can be used to operate warning lights or alarms.
The starting point is the real-life cable installations, simply because any fire regulation aims at addressing real-life fires. However, realistic cable installations cannot be used in a testing and classification system. The costs will be enormous as the number of different installations is almost infinite. The solution is therefore based on the assumption that certain large-scale reference scenarios can be representative of real-life hazards and that performance requirements of the cables can be identified in these reference scenarios. The term reference scenario is here used for an experimental set-up that is deemed to represent real life.
In exact terms the representation will never be true. However, a reference scenario is created in such a way that experimental fires in the scenario will be representative of a large number of real practical cases sufficiently accurately for a regulator. The burning behaviour of cables in the reference scenarios can then be linked to the burning behaviour in standardised test procedures. This is achieved by analysing fire parameters like heat release rate, flame spread and smoke production from experiments in the reference scenario and comparing them to the standard rate. When this link is established it is possible to use measurements in the standardised tests for classification. Thus the classification of a table in a standard test will reflect a certain burning behaviour in the reference scenario which in turn is linked to real-life hazard situations.
The test used to determine the flame resistance of electric cables, signal cables, and cable splice kits is described in Title 30, Code of Federal Regulations, Part 7, Subpart K (CFR 30, 2005). The principal parts of the apparatus are a test chamber or a rectangular enclosure measuring 17 inches deep by 14 inches high by 39 inches wide (43.2 cm deep by 35.6 cm high by 99.1 cm wide) and open at the top and front. The floor or base of the chamber is lined with a noncombustible material to contain burning matter which may fall from the test specimen during a test. Permanent connections are mounted to the chamber and extend to the sample end location. The connections are used to energize the electric cable and splice specimens. The connections are not used when testing signaling cables. A rack consisting of three metal rods, each measuring approximately 3/16 inch (0.48 cm) in diameter is used to support the specimen during a test. The horizontal portion of the rod which contacts the test specimen shall be approximately 12 inches (30.5 cm) in length. A natural gas type Tirrill burner, with a nominal inside diameter of 3/8 inch (0.95 cm), is used to apply the flame to the test specimen.
For tests of electric cables and splices, a source of either alternating current or direct current is used for heating the power conductors of the test specimen. The current flow through the test specimen is regulated and the open circuit voltage is not to exceed the voltage rating of the test specimen. An instrument is used to monitor the effective value of heating current flow through the power conductors of the specimen. Also, a thermocouple is used to measure conductor temperature while the cable or cable splice kit is being electrically heated to 400 °F (204.4 °C). For the electric cable test, three specimens each three feet (0.91 m) in length are prepared by removing five inches of jacket material and two inches of conductor insulation from both ends of each test specimen.
For splice kits, a splice is prepared in each of three sections of a MSHA-approved flame-resistant cable. The cable used is the type that the splice kit is designed to repair. The finished splice must not exceed 18 inches (45.7 cm) or be less than 6 inches (15.2 cm) in length for test purposes. The spliced cables are three feet in length with the midpoint of the splice located 14 inches (35.6 cm) from one end. Both ends of each of the spliced cables are prepared by removing five inches of jacket material and two inches of conductor insulation. The type, amperage, voltage rating, and construction of the power cable must be compatible with the splice kit design.
The test specimen is centered horizontally in the test chamber on the three rods. The three rods are positioned perpendicular to the longitudinal axis of the test specimen and at the same height. This arrangement permits the tip of the inner cone from the flame of the gas burner to touch the jacket of the test specimen. For splices, the third rod is placed between the splice and the temperature monitoring location at a distance 8 inches (20.3 cm) from the midpoint of the splice. The gas burner is adjusted to produce an overall blue flame five inches (12.7 cm) high with a three-inch (7.6 cm) inner cone and without the persistence of yellow coloration. The power conductors of the test specimen are connected to the current source. The connections must be compatible with the size of the cable's power conductors to reduce contact resistance. The power conductors of the test specimen are energized with an effective heating current value of five times the power conductor ampacity rating at an ambient temperature of 104 °F (40 °C).
The electric current is monitored through the power conductors of the test specimen with the current measuring device. The amount of heating current is adjusted to maintain the proper effective heating current value until the power conductors reach a temperature of 400 °F (204.4 °C). For electric cables, the tip of the inner cone from the flame of the gas burner is applied directly beneath the test specimen for 60 seconds at a location 14 inches (35.6 cm) from one end of the cable and between the supports separated by a 16 inch (40.6 cm) distance. For the splices made from the splice kits, the tip of the inner cone from the flame of a gas burner is applied for 60 seconds beneath the midpoint of the splice jacket. After subjecting the test specimen to the external flame for the specified time, the burner flame is removed from beneath the specimen while simultaneously turning off the heating current. The amount of time the test specimen continues to burn is recorded after the flame from the burner has been removed. The burn time of any material that falls from the test specimen after the flame from the burner has been removed is added to the total duration of flame. The length of burned (charred) area of each test specimen is measured longitudinally along the cable axis. The procedure is repeated for the remaining two specimens. For a cable or splice kit to qualify as flame resistant, the three test specimens must not exceed a duration of burning of 240 seconds and the length of the burned (charred) area must not exceed 6 inches (15.2 cm). The flame test of an electric cable is shown in Fig. 13.4 – the electric cable did not meet the test criteria.
|
|
|
The performance of a centrifugal fan with enlarged impeller |
Posted by: zjjsw25ss - 08-23-2021, 07:03 AM - Forum: Welcomes and Introductions
- No Replies
|
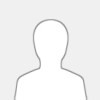 |
The influence of enlarged impeller in unchanged volute on G4-73 type centrifugal fan performance is investigated in this paper. Comparisons are conducted between the fan with original impeller and two larger impellers with the increments in impeller outlet diameter of 5% and 10% respectively in the numerical and experimental investigations. The internal characteristics are obtained by the numerical simulation, which indicate there is more volute loss in the fan with larger impeller. Experiment results show that the flow rate, total pressure rise, shaft power and sound pressure level have increased, while the efficiency have decreased when the fan operates with larger impeller. Variation equations on the performance of the operation points for the fan with enlarged impellers are suggested. Comparisons between experiment results and the trimming laws show that the trimming laws for usual situation can predict the performance of the enlarged fan impeller with less error for higher flow rate, although the situation of application is not in agreement. The noise frequency analysis shows that higher noise level with the larger impeller fan is caused by the reduced impeller–volute gap.
An implicit, time-accurate 3D Reynolds-averaged Navier-Stokes (RANS) solver is used to simulate the rotating stall phenomenon in a plastic centrifugal fan. The goal of the present work is to shed light on the flow field and particularly the aerodynamic noise at different stall conditions. Aerodynamic characteristics, frequency domain characteristics, and the contours of sound power level under two different stall conditions are discussed in this paper. The results show that, with the decrease of valve opening, the amplitude of full pressure and flow fluctuations tends to be larger and the stall frequency remains the same. The flow field analysis indicates that the area occupied by stall cells expands with the decrease of flow rate. The noise calculation based on the simulation underlines the role of vortex noise after the occurrence of rotating stall, showing that the high noise area rotates along with the stall cell in the circumferential direction.
As the power source of the air and gas system in the thermal power plant, the operation status of the centrifugal fan is directly related to the safe and economic operation of the power plant. Rotating stall in the centrifugal fan is a local instabilities phenomenon in which one or more cells propagate along the blade row in the circumferential direction. The nonuniform flow, the so-called stall cell, rotates as a fraction of the shaft speed, typically between 20% and 70%. This running mode is responsible for strong vibrations which could damage the blades [1]. Meanwhile, it will increase the aerodynamic noise.
In order to reveal the generation mechanism of rotating stall, lots of models and theories have been proposed since the 1960s. Especially, experimental methods were widely used to illustrate the characteristics of internal flow field during stall. Lennemann and Howard discussed the causes of stall cells in low flow rate condition through the hydrogen bubble flow visualization method [2]. Lucius and Brenner experimentally studied the speed variation of a centrifugal pump in rotating stall stage [3]. For the centrifugal turbomachine, multiple factors can affect the characteristics of stall. Vaneless diffuser, for example, has significant influence on stall. Hasmatuchi et al. experimentally investigated the effect of blowing technology on the flow field of a centrifugal pump under rotating stall [4]. Rodgers conducted an experimental research on rotating stall in a centrifugal compressor with a vaneless diffuser and found that the stall margin can be improved through adjusting the expansion pressure factor [5]. Abidogun carried out an experiment to investigate the influence of vaneless diffuser on the stall characteristics. The results showed that increasing the length of diffuser can improve the rotating speed of stall, and the change of width showed no effect on stall [6].
Further efforts were made to study the stall inception in order to avoid the occurrence or minimize the effect of stall. As well accepted, two types of stall inception proposed by Camp and Day modal wave inception and spike inception were investigated experimentally [7]. Leinhos et al. studied development process of stall inception under instantaneous inflow distortion in an axial compressor [8].
With the rapid development of computer technology, numerical simulation has become an important method for flow field research of turbomachine under rotating stall conditions. Gourdain et al. investigated the ability of an unsteady flow solver to simulate the rotating stall phenomenon in an axial compressor and found that it was necessary to take the whole geometry into consideration to correctly predict the stall frequency [1]. Choi et al. investigated the effects of fan speed on rotating stall inception; the results showed that, at 60% speed (subsonic), tip leakage flow spillage occurred successively in the trailing blades of the mis-staggered blades [9]. Zhang et al. numerically studied the stall inception in a centrifugal fan, and the results showed that the stall inception experienced probably 50 rotor cycles developing into a stall group. The inception showed significant modal waveform. The importance of volute for generation of stall inception was illustrated through flow field analysis [10].
Aerodynamic noise is mainly caused by vortex and flow separation. So the unsteady behavior of rotating stall may have an influence on the noise of centrifugal fan. In capturing the physical mechanism of the fan noise associated with rotating stall, the primary work is to characterize the noise. During the 1960s, the interaction between noise and turbulence was discussed by Powell, and the vortex sound theory was proposed to explain the generation of acoustic sound. Then, Lighthill made a breakthrough in aerodynamic noise theory research by proposing the acoustic analogy [11]. Based on these works, Díaz et al. put forward a prediction of the tonal noise generation in an axial flow fan, and the noise level in the plastic centrifugal blower far-field region was estimated by means of acoustic analogy [12]. Scheit et al. analyzed the far-field noise in a metal centrifugal fan with an acoustic analogy method and presented design guidelines to optimize the radiated noise of the impeller [13]. The global control of subsonic axial fan at the blade passing frequency was also discussed by Gérard et al. [14]. He aimed at cancelling the tonal noise by using a single loudspeaker in front of the fan with a single-input-single-output adaptive feedforward controller. According to Ouyang et al.’s work, the far-field noise generated by cross-flow fan with different impellers was measured and it showed the great influence of blade angles on the inflow pattern [15]. Based on the previous research, a new method to predict the fan noise and performance is developed by Lee et al., and through an acoustic analogy, the acoustic pressures from the unsteady force fluctuations of the blades are obtained [16].
In summary, a wide range of flow characteristics on rotating stall in compressor have been investigated and the researches concentrated on stall inception. The present work focuses on two aspects: simulation of the rotating stall phenomenon with a 3D flow solver and seeking the deep physical mechanism of this instability in a centrifugal fan. The numerical method is presented with the model and the particular boundary conditions are used. Results from the whole geometry simulation are then analyzed. In the first part, aerodynamic characteristics and frequency domain characteristics of the centrifugal fan under different stall conditions are analyzed. In the second part, the velocity vector field distributions in the centrifugal fan are discussed. Finally, noise characteristics of the centrifugal fan under different stall conditions are studied. And the noise characteristics during the circumferential propagation of stall cells are also discussed.
2. Centrifugal Fan Description
The configuration of range hood centrifugal fan studied in this work is shown in Figure 1. It is composed of current collector, impeller with 12 airfoil blades, and the volute. The inlet and outlet diameter of the impeller are 568 mm and 800 mm, respectively. The inlet and outlet width of impeller are 271 mm and 200 mm, respectively. The nominal rotation speed is 1450 rpm. The volute tongue gap is 1% of the impeller outlet diameter. The width of the rectangular volute is 520 mm, and a simple antivortex ring is set inside the volute to reduce the generation of vortex. At the design operating point, the volume flow is 6.32 m3/s and the full pressure is 1870 Pa.
As shown in Figure 8(b), under the combining influence of both stall cell and volute tongue, the high noise area is gradually elongated. Due to the propagation of stall cell, it gradually gets away from the area of volute tongue, resulting in weakening the superimposing effect. As time goes by, the high noise area in Figure 8© gets further elongated with a trend of separation and the sound power level of high noise areas decreases. In Figure 8(d), the high noise areas corresponding to the vortex noise and volute tongue noise basically separate. And the sound power level corresponding to volute tongue greatly declines.
It can be drawn from Figure 8 that while the impeller passes three passages along clockwise direction, the high noise area passes two impeller passages along the clockwise direction. It indicates that, in the absolute coordinate reference system, the high noise area occupying about three impeller passages rotates in the same direction with impeller under rotating stall. It also has the same speed with stall cells, while in the relative coordinate reference system, high noise area spreads in the opposite direction of the rotation of the impeller.
Through the analysis above, there are two major sources of noise in a centrifugal fan under rotating stall, namely, the vortex noise caused by stall and the volute tongue noise caused by the rotation of impeller. When the stall cell spreads to the volute tongue, due to the superimposing effect of vortex noise and volute tongue noise, the sound power level is the highest and the high noise area is the largest. While the stall cell is away from the volute tongue, the corresponding high noise areas separate gradually. Along with that, the sound power level decreases and the high noise area becomes smaller. Therefore, the aerodynamic noise of the centrifugal fan under rotating stall changes periodically over time, and the fluctuation period is the same with the rotating period of the stall cell.
The authors declare that they have no financial or personal relationships with other people or organizations that can inappropriately influence their work; there is no professional or other personal interests of any nature or kind in any product, service, and/or company that could be construed as influencing the position presented in, or the review of, this paper.
|
|
|
3 Ways Suspended Platforms Increase Efficiency for Vertical-Vessel Maintenance |
Posted by: zjjsw25ss - 08-23-2021, 06:56 AM - Forum: Welcomes and Introductions
- No Replies
|
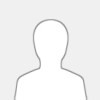 |
It’s time to upgrade maintenance practices for vertical vessels. Like any routine maintenance, inspecting, removing and replacing refractory in vertical vessels places a costly burden on facilities in terms of downtime and lost productivity. One of the main reasons for this is the traditional solution for accessing vertical surfaces – scaffolding – severely limits efficiency. It also increases safety risks for employees.
Processing facilities are taking action to reclaim maintenance productivity and safety by investing in custom-manufactured suspended platforms for vertical-vessel operations. These systems feature a lightweight, heavy-duty metal platform that is erected inside the vessel and raised or lowered using manual or electric hoists for hassle-free maintenance and relining applications.
Suspended platforms offer a number of benefits over scaffolding systems, starting with effectively eliminating the protracted setup times that dominate scaffolding-based maintenance schedules. Here’s how these customized systems can boost productivity and safety throughout the maintenance process.
Speedy Setup
The amount of time scaffolding systems take to erect is their biggest deterrent and the greatest drain on maintenance productivity. This is due in part to the sheer complexity of the operation, which includes juggling a variety of pipes, hardware, boards and other materials to create the structure. Erection times vary based on vessel size and configuration, but even with an experienced crew, scaffolding can take several shifts all the way up to an entire week to construct. This puts significant stress on maintenance budgets and timelines.
To simplify the process and decrease setup times, steel suspended platform implement a modular design and pin-together construction. This greatly reduces the number of components and tools required for erection and allows crews to complete setup in as little as two hours.
Modular components manufactured from high-strength 6061-T6 aluminum provide the same strength as steel at one-third of the weight. And, because vertical vessels often feature small access points, manufacturers limit the size of modular components. The resulting pieces are easy to maneuver, weighing 40 pounds (18 kg) or less, and fit through a 22-inch-diameter (560-mm-diameter) access hole. This provides a lighter, more easily maneuverable solution than scaffolding’s heavy wooden planks and steel pipes, some of which are up to 14 feet long.
In addition, pin connections allow for fast assembly and improve platform strength over welded connections by allowing for some flexibility while the platform is being raised or lowered. Welded joints are rigid, which increases stress on risers at platform joints. Pin-together joints are a better solution to help maintain safety and stability when dealing with varying speeds from the climbing hoists.
It is worth noting that suspended platforms require some initial site preparations. This can increase setup times the first go-round – sometimes up to a full shift for complicated systems. But in the long run, a suspended platform can save facilities significant time and effort with each use, leading to significant ROI potential.
For example, a copper plant replaced the scaffold system for their smelter with a custom suspended platform. This increased productivity and safety. Overall, the plant was able to save 320 man-hours per shutdown with the new system.
Room to Move
Even after the platform is assembled, the productivity benefits continue to add up. With scaffolding, tools and materials need to be hoisted up to working height a little at a time, often manually. This is a slow process with a heavy physical toll. It also limits productivity by restricting supply lines for materials, such as refractory brick, gunning equipment or other necessities.
A suspended platform, on the other hand, can easily transport up to 6,000 pounds (2,722 kg) up and down, and the open design provides ample space for personnel, tools and materials. This allows several workers to operate in the same area comfortably, as well as have everything they need close at hand for efficient maintenance. Crews simply load all necessary materials at the start of the shift while the platform is positioned at the vessel’s access point. When more brick or other supplies are required, the crew lowers the platform, loads the necessary materials and then easily returns to height. This saves considerable time and energy and can increase productivity by limiting the number of trips up and down.
The platform also provides more room and easier positioning for equipment such as gunning machines for shotcrete applications. Crews simply set up the machine directly on the platform and maneuver the entire system up and down, eliminating downtime from repositioning while maintaining an ideal distance from the vessel surface for proper adhesion. Using a suspended platform for this application also eliminates the physical toll and risk to crews from heavy hoses hanging from the scaffolding.
In addition, the open platform and electric hoist system allow for infinitely variable height, resulting in unrivaled access for inspection, removal and replacement of refractory materials.
Scaffolding is inherently rigid. It has to be to create a sturdy base of operations. However, this rigidity restricts crew access to the burn surface. Pipes inhibit visual inspection and make it difficult to work on the area directly behind them. The scaffolding structure can also obstruct small flaws, causing them to be overlooked. Crews must squat down or reach up high when working on surfaces in between 8-foot scaffolding stories.
Suspended platforms provide crews with 360-degree access at a comfortable working height, regardless of the task at hand. To optimize accessibility and productivity for a particular facility, manufacturers also customize designs to fit vessels up to 22 feet in diameter, so crews can get directly against the burn surface without risk of falling. This allows crews to inspect every inch, catching even the small flaws that could lead to bigger problems down the line if overlooked. Also, some suspended platforms allow crews to adjust the size of the platform by up to 3 feet while suspended by changing the outer panels. This results in better accessibility and easy transition between different widths of a vessel.
Ergonomics for Better Economics
It goes without saying that having a platform, rather than a narrow scaffold, increases worker safety.
Falls continue to rank number one in workplace injury reports, and refractory repair is not immune to tragic accidents. Recent U.S. Bureau of Labor Statistics data identified 338 fatal falls to the lower level among 1,038 total construction fatalities for the year. That same year, falls on the same level or to lower levels amounted to $17.1 billion (29.2%) of the nearly $60 billion spent by employers on serious, non-fatal workplace injuries.
A suspended platform replaces narrow wooden catwalks with an aluminum surface that spans the entire vessel, eliminating the risk of falls or dropped objects. It also eliminates the need for workers to climb up and down carrying small tools and the need to haul materials and larger equipment up to height, hand over hand, resulting in a much safer jobsite.
There are long-term safety benefits that go beyond this. From setup through all aspects of refractory maintenance, an aluminum suspended platform puts less physical strain on employees. The lightweight, modular components are less cumbersome than long poles and heavy wooden planks. Easy access to materials and tools reduces the risk of repetitive-motion injuries as well as minor cuts, bruises or scrapes that come with manually moving refractory materials. Being able to position the platform at the ideal working height for the job at hand limits bending or reaching, providing an ergonomic solution instead.
All of these small but significant safety benefits lead to long-term savings in the form of worker’s compensation claims and insurance premiums.
Making the switch to a ZLP500 rope suspended platform requires some initial planning, but positive returns are almost immediate. Facilities that have made the switch save tens of thousands of dollars with each maintenance cycle, providing a return on investment in one or two uses. The key is working with a reputable manufacturer that can provide a customized platform that fits a facility’s needs perfectly. Working together, these partners can revolutionize refractory maintenance in vertical vessels.
Mr. Jayesh Vadukiya, M.D, New Age Construction Equipment Engineering Company
New Age Construction Equipment Engineering Company is one of the leading manufacturers of construction equipment like Rope Suspended Working Platforms (Gondolas/ Cradles), Bar Bending Machines, Bar Cutting Machines, etc. The company is strictly complying with ISO 9001:2008 certification and its products have also received CE certificates. The stringent quality standards conforming to “OE” standards enable it to guarantee 100% satisfaction for the entire range of products.
New Age believes in innovation, technology, and customization of its products, based on market research and end-users’ expectations, and has a strong sales & service team of professionals. The company has many instances of innovation and customization, especially of its Rope Suspended Platforms (RSP) / Gondolas/ Cradles. Presenting here two success stories on customized RSP for Dam & Silo Project.
The job was to clean the wall of the dam. It was a very difficult job because of the wind pressure and the height of the wall. The width of the road on the dam was too short to fix a standard upper mechanism of RSP. Another problem was the customer’s requirement of designing the upper mechanism in such a way that vehicles should also pass through the upper mechanism and their movement should not be stopped during the cleaning.
Moreover, the upper mechanism was so heavy that it was next to impossible to shift it. The customer wanted to move the wall machine (upper mechanism + cradle) from one place to another in a short time, and we did that without the help of any laborers.
We designed the RSP in such a way that the client’s requirement was fulfilled, and work was done timely. We had also provided specially designed Motorized device for shifting of wall machine without any requirement of labor. With our vast experience of doing challenging projects, we are always ready to take new assignments and try to resolve all issues through our customized solutions.
|
|
|
Simulation of tin penetration in the float glass process |
Posted by: zjjsw25ss - 08-23-2021, 06:55 AM - Forum: Welcomes and Introductions
- No Replies
|
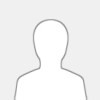 |
The flat glass produced by the float glass process has a tin-rich surface due to the contact with molten tin. The penetration of tin into the glass surface is assumed to involve coupled diffusion of stannous (Sn2+) and stannic (Sn4+) ions. The diffusion coefficients of these ions were calculated using the modified Stocks–Einstein relation with the oxidation velocity of stannous ions depending on the oxygen activity in the glass. The ion diffusion was analyzed using a coupled diffusion simulation with a modified diffusion coefficient to compensate for the negative effect of the glass ribbon’s stretching or compressing in the glass forming process. Tin penetration simulations for both green glass and clear glass show an internal local tin concentration maximum in green glass which is quite different from that in clear glass. The local maximum in the profile is associated with the accumulation of stannic ions where the greatest oxygen activity gradient occurs. Since more float time is needed in the manufacture of thicker glass plate, the tin penetrates to a greater depth with the maximum deeper in the glass and the size of the maximum larger for thicker glass.
The float glass process, which was originally developed by Pilkington Brothers in 1959 (Haldimann et al., 2008), is the most common manufacturing process of flat glass sheets. More than 80–85% of the global production of float glass is used in the construction industry (Glass for Europe, 2015a). In the float glass process, the ingredients (silica, lime, soda, etc.) are first blended with cullet (recycled broken glass) and then heated in a furnace to around 1600°C to form molten glass. The molten glass is then fed onto the top of a molten tin bath. A flat glass ribbon of uniform thickness is produced by flowing molten glass on the tin bath under controlled heating. At the end of the tin bath, the glass is slowly cooled down, and is then fed into the annealing lehr for further controlled gradual cooling down. The thickness of the glass ribbon is controlled by changing the speed at which the glass ribbon moves into the annealing lehr. Typically, glass is cut to large sheets of 3 m × 6 m. Flat glass sheets of thickness 2–22 mm are commercially produced from this process. Usually, glass of thickness up to 12 mm is available in the market, and much thicker glass may be available on request. A schematic diagram of the production process of float glass is shown in Fig. 5.2.The float glass process was invented in the 1950s in response to a pressing need for an economical method to create flat glass for automotive as well as architectural applications. Existing flat glass production methods created glass with irregular surfaces; extensive grinding and polishing was needed for many applications. The float glass process involves floating a glass ribbon on a bath of molten tin and creates a smooth surface naturally. Floating is possible because the density of a typical soda-lime-silica glass (~2.3 g/cm3) is much less than that of tin (~6.5 g/cm3) at the process temperature. After cooling and annealing, glass sheets with uniform thicknesses in the ~1–25 mm range and flat surfaces are produced. The ultra clear float glass process is used to produce virtually all window glass as well as mirrors and other items that originate from flat glass. Since float glass is ordinarily soda-lime-silica, the reference temperatures and behavior of this glass are used in the discussion below.
Figure 3.48 shows the basic layout of the clear float glass line. The glass furnace is a horizontal type, as described above. For a float line, the glass furnace is typically on the order of ~150 ft long by 30 ft wide and holds around 1200 tons of glass. To achieve good chemical homogeneity, the glass is heated to ~1550–1600°C in the furnace, but is then brought to about 1100–1200°C in the forehearth. From there, the glass flows through a channel over a refractory lipstone or spout onto the tin bath. As it flows, the glass has a temperature of about 1050°C and viscosity of about 1000 Paradical dots. A device, called a tweel, meters the flow of the molten glass.Imperfections include bubbles (or ‘seeds’) that may have a number of possible sources, the most common being gas evolved during firing. Bubbles may contain crystalline materials formed during cooling of the glass that may provide clues to the origin of the bubbles. Cords are linear features within the glass that may result either from imperfectly homogenized raw materials, dissolved refractories or devitrified material. Figure 360 shows the appearance of soda–lime–silica glass that exhibits bubbles and cords. ‘Stones’ are solid crystalline substances occurring in glass that are regarded as defects. They are usually derived either from the batch material, refractories, or devitrification. Figure 361 shows the appearance of soda–lime–silica glass that contains a devitrification ‘stone’. These may develop as the result of incomplete mixing of the molten glass constituents and/or too low a firing temperature. The ‘stone’ shown in Figure 361 contains an aggregation of tridymite crystals (see 362).
As the floating glass ribbon traverses down the length of the tin bath, its properties change dramatically. The glass enters as a viscous liquid and exits virtually a solid at a temperature very close to its glass transition temperature. The details of how the temperature changes and the viscosity builds are complicated. On one side, the free surface of the glass is exposed the atmosphere; heat can leave this surface by radiation or convection. Cooling and heating apparatuses are stationed above the glass ribbon down the length of the bath to allow adjustment of the ribbon temperature. On the other side, the glass is in contact with the tin bath, which can absorb some of the heat and transport it away from the ribbon. The tin bath is in constant motion due to the moving glass above it as well as the thermal convection currents. Unfortunately, no simple approximations can be made to make the modeling of the heat transfer.
The thickness of the tinted float glass sheet is adjusted by controlling flow onto the tin bath as well as by tension exerted along the length of the bath by rollers in the annealing lehr and sometimes by rollers in the bath unit itself. In the Pilkington design, the melt enters the bath and spreads out laterally to a thickness near the equilibrium value. If a sheet thicker than the equilibrium is required, then this spreading is constrained with physical barriers. If a sheet thinner than equilibrium is needed. then the glass ribbon is pulled in tension by rollers. In the PPG design, thickness is regulated by the tweel position and by tension from rollers in the lehr. The thermal profile allows the thinning deformation to take place effectively. A short distance away from the entry point, the temperature of the ribbon drops and the viscosity rises. Overhead coolers help this process. The glass viscosity is high enough so that knurled rollers contact the glass ribbon and pull it forward (and in some operations, laterally as well). Heaters are placed shortly downstream of these edge rollers to raise the temperature of the ribbon and create a deformable zone. This zone is followed by coolers that again lower the temperature and raise the viscosity. At exit from the lehr, the ribbon is virtually solid. The main deformation is due to the rollers in the lehr, which pull on the glass ribbon from the lehr to the edge rollers; extension takes place in the deformation zone. Example 3.15 considers the exit velocity of glass from the process.
For many years, however, the glass industry has been trying to solve a problem which affects almost every building in the world. How do you maintain the fundamental characteristics of glass, such as optical clarity and external esthetics without constant and costly maintenance? Whether the building is for commercial or residential use, the one constant requirement is for regular cleaning to be undertaken to ensure the glass maintains its optimum appearance.
The challenge for the glass industry is increased as a result of architects finding ever more resourceful and novel uses for glass. The use of glass in atria and overhead glazing can sometimes result in complex areas, which can make maintenance more difficult.
In addition to the esthetic issues it is a well-known phenomenon that if glass is not cleaned regularly then over a period of time the glass can weather, which makes it almost impossible to restore its esthetic properties. In extreme circumstances this can lead to the glass needing replacement.
The process of cleaning windows can also lead to safety and environmental issues. Window cleaning generally involves the use of portable ladders for cleaning windows on ground, first, and second floors. Figures for accidents reported to the Health and Safety Executive (HSE) and local authorities reveal that unfortunately between two and seven window cleaners have been killed every year in Great Britain and around 20–30 suffer major injuries due to falls involving ladders. From an environmental aspect window cleaning can involve the use of harsh chemicals. These are often washed off during the cleaning process and can ultimately lead to ground contamination.
Recently, self-cleaning coatings have been developed, which are designed to reduce the amount of maintenance required by working with the forces of nature to clean dirt from the glass. These coatings are based on a well-known metal oxide called titanium dioxide, which is regularly used in paints, toothpaste, and sunscreens.
Tin is an ideal bath material because it has the right set of physical properties. Tin melts at 232°C, has relatively low volatility, and does not boil until over 2000°C. Molten tin is denser than molten glass and is not miscible or reactive with molten glass. The gas atmosphere is controlled so that tin does not oxidize at a fast rate. Any oxide that does form is collected in a dross container on the bath.
Regulating the flow of the wired glass is important at this stage, both from the entry point and the lateral flow. The glass flow onto the tin bath is regulated by a gate, called a tweel, which is located in the canal between the forehearth and spout. The glass flows down the spout or lipstone onto the tin surface. There is some pressure driving this flow through the gap of the tweel. See Example 3.14. As the glass flows onto the tin bath, the thickness of the glass sheet depends on how that flow is controlled laterally and along the length of the bath. The first step to understanding thickness control is to examine the equilibrium thickness.
|
|
|
A review on the durability of PVC sewer pipes |
Posted by: zjjsw25ss - 08-23-2021, 06:52 AM - Forum: Welcomes and Introductions
- No Replies
|
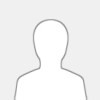 |
Polyvinyl chloride (PVC) has become one of the dominant construction materials for sewer systems over the past decades, as a result of its reputed merits. However, since PVC sewer pipes have operated for decades in a hostile environment, concern over their longevity has been lately raised by sewer managers in the Netherlands. Towards that direction, the main factors and mechanisms that affect a PVC pipe’s lifetime are discussed in this article, along with the current lifetime prediction methods and their limitations. The review of relevant case studies indicates that material degradation, if any, occurs slowly. However, inspection (CCTV) data of three Dutch municipalities reveals that severe defects have already surfaced and degradation evolves at an unexpected fast rate. A main reason of this gap between literature and practice is the fact that comprehensive material testing of PVC sewer pipes is rarely found in the literature although it proves to be essential in order to trustfully assess the level of degradation and its origins.
Plastics are used for a wide range of commercial and industrial piping applications. The most known are polyvinyl chloride (PVC), polyethylene (PE), polypropylene (PP), acrylonitrile–butadiene–styrene (ABS), polybutylene (PB) and glass–fibre-reinforced polyester (GRP or FRP). Concerning piping systems for drinking water supply, gas distribution and sewage disposal, PVC, PE and PP are the most popular polymer materials (PlasticsEurope, 2017). Especially for gravity sewer pipes, PVC has been extensively used over the past decades and has become the dominant construction material. Cost efficiency, ease of installation, range of available diameters (40–630 mm) and its reputed chemical resistance favour its wide acceptance by decision makers in urban drainage (Davidovski, 2016).
Since there are PVC sewer pipes in operation for at least four decades, concern over their longevity has been lately raised in the Netherlands. It is still unknown whether the expectations of long-lasting PVC pipes (Folkman, 2014) will prove realistic or new asset management strategies should be established in the near future. Knowledge of the current structural integrity of sewer systems is a key issue for establishing successful asset management strategies, leading to better decision making and more affordable investments. In practice, sewer managers currently base their strategies mainly on visual (CCTV) inspections (Van Riel, Langeveld, Herder, & Clemens, 2014). Subsequently, decisions are taken whether replacement, rehabilitation or a near future inspection should take place. However, linking the observed defects in CCTV to the actual physical state of a pipe is challenging (Van Riel, 2017). A necessary condition for achieving this is comprehensive understanding of the mechanisms that affect a PVC pipe’s lifetime, their combined effects and eventually their results, which are the defects found in practice. An overview of these mechanisms and their origins is included in this article. Lifetime prediction methods for UPVC pipes are also utilised to describe specific types of failure, while their ability to provide trustful lifetime prediction is discussed.
The main aim of this article is to present case studies of PVC sewer pipes found in the literature and to compare the derived conclusions on PVC durability with findings in inspection (CCTV) data. Emphasis is given on the studies that investigate the properties that define the structural integrity and overall performance of a sewer system. The inspection data concerns three different municipalities in The Netherlands: Almere, Amstelveen and Breda. The main discrepancies between literature and inspection data are discussed, as a step towards bridging results from scientific research and observations from practice.
Suspension polymerisation is the most applied process for PVC particles production (80%), whereas emulsion and mass polymerisation provide 12 and 8% of the world production, respectively (Fischer, Schmitt, Porth, Allsopp, & Vianello, 2014). Although the specific details of the PVC particles size slightly differ in the literature (Benjamin, 1980; Butters, 1982; Faulkner, 1975), the microstructure follows the same pattern. This can be described in three stages (Butters, 1982): the stage III-PVC particle (∼100–150 μm), the stage II-primary particle (∼0.1–2 μm) and the stage I particle (∼10 nm). The conversion of the material to a homogeneous product requires that the boundaries of the primary particles disappear and a new continuous entanglement network is developed (Visser, 2009). This procedure is known as the gelation process and its quality is expressed by the gelation level. There are several methods to obtain information about the gelation level (Castillo, 2016; Choi, Lynch, Rudin, Teh, & Batiste, 1992; Fillot, Hajji, Gauthier, & Masenelli-Varlot, 2006; Gilbert & Vyvoda, 1981; Gramann, Cruz, & Ralston, 2010; Johansson & Törnell, 1986; Kim, Cotterell, & Mai, 1987; Marshall & Birch, 1982; Real, João, Pimenta, & Diogo, 2018; Terselius, Jansson, & Bystedt, 1981; Van der Heuvel, 1982).
A general accepted opinion suggests optimum gelation levels of 60–85% (Benjamin, 1980; Breen, 2006). A temperature of >250 °C is needed for this purpose (Guerrero & Keller, 1981), much higher than the degradation temperature of PVC which is ∼205 °C (Wypych, 2015). Due to this fact, thermal energy is complemented with mechanical energy (high shear stresses) by the use of twin rotating screws, so as to accelerate this process without extensive exposure of the material to high temperatures (Visser, 2009). Subsequently, the molten material is introduced in a die so that the final pipe is shaped and cooled. This manufacturing technique is called extrusion and is extensively used to form pipes. Fittings, such as joints, are formed by the injection moulding technique. In the injection moulding process, the melted plastic is injected in a mould, which gives the desired form to the PVC fitting, and after cooling the product is ejected.
During the production process, several additives and fillers may be incorporated in the polymers structure in order to enhance its chemical and physical properties, respectively. Plasticisers and stabilisers are the main additives as they affect the behaviour and degradation rate of the material through its lifecycle. Plasticisers are utilised in order to replace some monomers of the polymer chain, offering a higher degree of mobility and, hence, more flexibility. For sewer applications unplasticised rigid PVC pipes are used. Stabilisers are added for increased resistance to e.g.: UV rays, chemical attack and other relevant external factors (Cardarelli, 2008). For pvc pipework in Europe, lead has been used until the early 2000s, when it was replaced by calcium-based stabilisers in most countries (Anders, 2014).
Every step within the production of PVC pipes and furniture PVC fittings can have an effect on the long-term performance of the final product. The levels of water and oxygen during polymerisation could influence the formation and quality of the produced PVC particles (Butters, 1982). Subsequently, the gelation process, already affected by the degree of polymerisation (Fujiyama & Kondou, 2004), plays a major role in the mechanical properties (Mandell, Darwish, & McGarry, 1982; Moghri, Garmabi, & Akbarian, 2003; Truss, 1985; Van der Heuvel, 1982). These properties are determined by the morphology of the material (Benjamin, 1980; Kuriyama, Narisawa, Shina, & Kotaki, 1998) and by the polymer’s orientation and molecular mobility (Fillot, Hajji, Gauthier, & Masenelli-Varlot, 2007). Additionally, impurities and voids in the polymer structure, frequently referred to as inherent defects, are introduced during production, resulting in crack initiators, and their presence seems to be inevitable (Johansson & Törnell, 1987). The wear observed at the polymer pipes extruders (Gladchenko, Shevelya, Kiyanitsa, & Derkach, 1997) might also contribute to the occurrence of inherent defects.
Residual stresses are also introduced during production, as a result of different cooling rates between the inner and the outer pipe surface (Siegmann, Buchman, & Kenig, 1981), and constitute another parameter that affects the mechanical properties of the produced pipe (Siegmann, Buchman, & Kenig, 1982). Relevant research on residual stresses in PVC pipes (Breen, 2006; Meerman, 2008; Scholten, van der Stok, Gerets, Wenzel, & Boege, 2016) has revealed that their magnitude is in a range of 0.9–4.8 MPa for tensile and 3.9–9.4 for compressive stresses (Table 1). In principle, a faster cooling rate or a thicker pipe wall thickness will lead to higher levels of residual stresses (Janson, 2003; Scholten et al., 2016). However, irrespective of their magnitude, residual stresses affect the crack propagation as they change the stress profile through the pipe (Burn, 1992; Chaoui, Chudnovsky, & Moet, 1987), increase the brittle–ductile temperature (Scholten et al., 2016), and, consequently, they seem to have a tremendous effect on the lifetime of pressurised plastic pipes (Hutař et al., 2013; Poduška et al., 2016).
|
|
|
Metal Forging Tools and Equipment and Parts Supplies |
Posted by: zjjsw25ss - 08-23-2021, 06:51 AM - Forum: Welcomes and Introductions
- No Replies
|
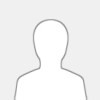 |
This article discusses the significant factors in the selection of forging equipment for a particular process. It describes the characteristics of forging hydraulic presses, mechanical presses, screw presses, and hammers. The article discusses the significant characteristics of these machines that comprise all machine design and performance data, which are pertinent to the economic use of the machines, including the characteristics for load and energy, time-related characteristics, and characteristics for accuracy.
The forging of metals and alloys is one of the oldest metal forming techniques used by humankind. Forging processes were improved over the centuries and are still being refined. Today, we are certain that there is no limit to these improvements and that we will never reach the point when we can say that nothing more is to be done. Despite the enormous knowledge and experience gained over the centuries, we still face new challenges arising from civilizational progress. One of them is the necessity to produce parts that are more and more complex in terms of shape and properties, which requires not only a deep insight into phenomena that accompany forging processes, but also the development of new techniques, riveting machine and equipment, materials, research methods, and tools, as well as the improvement of the existing ones. With the Special Issue on “Forging Processes of Materials”, the Editorial Board of Materials offers authors the possibility of presenting their findings in this field. As the Guest Editor for the Special Issue, I would like to invite you to contribute to this publication, which, I hope, will serve as a source of knowledge for both theoreticians and practitioners. Hence, I encourage authors to submit papers exploring, in a broad sense, the theory and practice of forging metals and alloys. I wish to assure you that we will make every effort to ensure the highest quality of this Special Issue.
Forging is a hot or cold metal deformation process used to produce metal parts where strength is a paramount concern, engine connecting rods and hand tools being two such examples. The process itself involves using compressive forces to mold and deform metal into the desired shape. For most applications, forging entails heating the base metal until it is malleable enough to work with, although cold and warm forging are also done.
The forge, sometimes called a hearth, is the component that heats the metal prior to forming. In its most fundamental form, forging can be understood in the manner of making horseshoes. The blacksmith heats the metal in the hearth, then pounds it with a hammer against an anvil to flatten it, curve it, pierce it, and generally shape it, repeatedly reheating the metal to maintain plasticity. Small gas-fired forges are available for blacksmiths though many forgers choose to build their own.
Modern industrial forging relies on sophisticated, heavy-duty equipment capable of producing small accurate parts as well as large pieces weighing many tons. As with castings and weldments, many forgings are machined after they are made to achieve their final forms.
An anvil is a large slab of metal, usually made of steel, which serves as the workbench for the blacksmith or automated hydraulic closed die forging hammer device. The metal is placed on the anvil, where it is hammered into the correct shape. Anvils traditionally provide a flat hammering surface, though curved anvil tops are available. A hardy hole and punch hole can sometimes be found on an anvil – the hardy hole serves as the square socket for accepting the shank of a hardy, an interchangeable tool in a variety of shapes used for cutoff, bending, etc. The punch hole provides clearance for punching holes in the metal.
Chisels
Chisels are cutting supplies that chip away at metal. They are traditionally made of high-carbon steel and consist of a long octagonal cross-section with a tapered cutting edge on one end. There are two types of chisels—hot chisels and cold chisels. Cold chisels are typically thinner in construction, and better suited for cold forging. Hot chisels, on the other hand, assist in hot forging processes. Chisels are traditionally applicable in manual forging applications.
Tongs
Tongs assist in the transportation of the heated metal from the forge to the anvil. Many different tong shapes are available to provide adequate gripping of multiple metal shapes and sizes.
Fullers
Forming tools that create grooves or indentions in the forging process are known as fullers. Fullers also help round out corners and stretch the metal. Traditionally used in pairs, fullers work through placing one beneath the metal, and the other on top. This enables the indentation of both sides of the metal component to occur simultaneously.
Forging Hammers
Different forging processes are appropriate for different applications—options such as hot forging, cold forging, closed die forging, upset forging, and press forging are simply a few examples. Many of these forging processes require the use of a hammer to enable compression and shaping of the metal. Forging hammers vary in shape, size, and material based on the particular application, but all industrial hammers typically apply force with a large ram. Two basic types of hammers are:
Drop hammers: Gravity allows the heavy ram to fall onto the metal.
Power hammers: Compressed air, hydraulics, or electricity drive the hammer.
Hammers are capable of delivering percussive impact blows with forces of up to 50,000 lbs. in their largest incarnations, with smaller capacity units also available. For increased forging forces, forgers turn to presses.
Forging Presses
A forging press creates force through mechanical or hydraulic energy without relying on the weight of a hammer and the assistance of gravity to pound metal into the desired shape. Whereas hammers shape a localized portion of the metal, a forging press can forge the entire product at once in a process known as closed-die forging. Forging presses also duplicate the action of hammers in the open die forging process. Both horizontal and vertical forging presses are available. The horizontal presses are called upsetters. Two types of forging presses include:
Mechanical forging press: A mechanical device (often a crank) propels a motor-driven flywheel, forcing the ram against the metal. Mechanical presses are not suited for forging large or complex items but are beneficial in applications that require simple shaping effects. They are capable of producing forces of up to 20,000 tons.
Hydraulic forging press: High-pressure fluid propelled by hydraulic pumps forces the ram against the metal. Hydraulic presses can provide higher forces than mechanical presses, and are sometimes preferred for applications that create large or complex components. Small hydraulic presses are available for blacksmithing operations with forces starting around 10 tons and they grow increasingly more forceful from there, with some very large presses operating in the 50,000-ton range and beyond.
Forging Dies
Forging presses used for closed-die forging require forging dies to properly mold the metal. Dies act as molds into which the hot, malleable metal is pressed. Since dies are unique to each forging project, they are expensive and can lead to high set-up costs prior to forging – forging with dies is best suited for moderate to large production runs. There are two main types of forging dies:
Open die: Open dies are akin to the blacksmith’s hammer and anvil and are usually available in shapes that accomplish specific tasks such as squaring. They do not completely encase the metal, providing free flow everywhere except where the metal meets the die. Open die forging is a good choice for custom metalworking applications as it can be used to produce as few as a single forging. It is also useful in forging very large parts. Where a blacksmith might use tongs to grapple the hot metal forging, many larger forgings are handled by mechanical manipulators because of their immense weight. Open die forging depends a great deal on the skill of the forger to produce the desired shapes. In addition to producing stepped shafting, rings, and cylindrical hollows, open die forging is often used to produce the hemispherical ends of pressure vessels.
Closed die: Here, the metal is completely encased. When the CNC hydraulic die forging hammer or press pushes against the metal, the metal flows and fills the die cavity or cavities. Typically, the pre-forged part will have some resemblance to the final forging before it is placed in the die, preformed by a series of so-called blocker dies.
Summary
This article presents a brief discussion of metal forging tools and equipment. For more information on other products, consult our other guides or visit the Thomas Supplier Discovery Platform to locate potential sources. More information on forging and forging equipment may be found at the Forging Industry Association website.
Modern science and industry have accumulated many efficient methods of forming by hammer forging, such as setting with shift or torsion, sectional forging, expansion by rolls etc. However, they are difficult for realization on forging equipment, what hampers their adoption in industry. Hence technological conservatism in forging. Even state-off-the-art forging complexes have brought no fundamental change into the hammer forging process.
Within the present work we have developed a new composition structure of a forging machine suitable for conventional operations of hammer forging as well as for new operations, unusual for hammer and press forging. The structure of the machine, hereinafter referred to as an automated forging center (AFC) permits to solve the problems of combining external forces, producing new shapes of deformation zones, efficient use of the tool magazine.
Physical and mathematical simulation of technological operations have been carried out to estimate forming and forse parameters, some results being presented in the paper.
|
|
|
Best Wine Glasses of 2020 |
Posted by: zjjsw25ss - 08-23-2021, 06:49 AM - Forum: Welcomes and Introductions
- No Replies
|
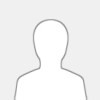 |
As if learning the vocabulary, geography, and producers in the wine world isn’t challenging enough, there are also different types of glassware—and figuring out the best wine glasses is no small feat. In the last couple of decades, glass manufacturers have made a killing off of creating dozens of glassware lines and convincing wine drinkers we need multiple types of glasses to be serious about wine. Although the glassware section of my book, Wine for Normal People, wound up on the cutting room floor, this is a topic my podcast listeners love to ask about and one I was excited to reexamine.
I guess we should start with the most important question: Does a glass really make a difference to a wine’s taste? After copious research and testing, I can tell you that glassware does matter to your enjoyment of wine. Certain glass shapes and materials do enhance wine’s aroma and flavor—and some even detract from it! I tested several highly regarded wine glasses and found the best premium, mid-tier, and affordable options for all kinds of wine drinkers.
Ahead, discover all the winners and a thorough breakdown of our testing methods. We’ve also included a primer on the merits of different liquor glass shapes.
Zalto is widely considered the gold standard of glassware by wine connoisseurs and professionals alike. It is made of mouth blown, nonleaded crystal; it’s incredibly light; and it’s shaped like a piece of art. It’s beyond fragile and using this glass is a bit unnerving, but in test after test with wine after wine, it not only allowed the wine to express itself, but in many cases it made the wine taste better than all the other glasses.
From white and red Burgundy to white and red Bordeaux, Italian white to California rosé, Chilean Pinot Noir to Spanish Rioja, the Zalto glass improved the naturally occurring aromas and flavors of each wine effortlessly. But to go a step further, the amazing thing about the Zalto is that it seems to elevate the wine’s subtleties and nuances, introducing new or stronger positive aromas and flavors that the other glasses don’t. For instance, you may get notes of an old medieval church incense and black pepper in a northern Rhône Syrah with the Zalto, but just an herbal note from other glasses (I know it’s crazy but it’s true).
The experience of swirling with Zalto is unlike any other—the lightweight construction and virtually spill-proof bowl (it tapers significantly) made for the most effortless spin, allowing for great aeration and giving it huge points for ease of use. The tapering at the top made every wine’s aromas shine so completely, to the point where the wines felt actually transformed and seemed to transcend themselves.
Although this is technically a Burgundy glass, I found that it improved a variety of wines almost universally. In a lineup of 10 glasses, even done blindfolded, this glass over-performed on experience, flavor, aroma, and comfort. Although the delicate quality of these glasses had me a bit stressed with each use and especially each (hand) wash, it wasn’t enough to deter me from grabbing it over every other glass, every night. It is, despite its fragility, the undisputed best wine glass you can get for your wine.
Because it is so expensive, we recommend just the Burgundy glass as the one you need, but if you have some extra change lying around and drink white wine, pick up those too.
Okay, so, it’s no Zalto, but the Riedel Veritas is half the cost and was a consistent runner-up in test after test. This glass is still fragile thanks to a spindly stem the company has become known for, but the leaded crystal has a slightly sturdier construction than the Zalto while still boasting a narrow rim that feels luxurious and comfortable for sipping.
The Pinot Noir glass did equally well with red Burgundy, Nebbiolo, Bordeaux and more tannic reds. Fuller whites were even slightly better in this one than in the Zalto. The white wine glass enhances the aromas of German Riesling, Italian whites like Fiano, and New Zealand Sauvignon Blanc.
The Veritas does exactly what a great glass should do: allow ample swirling room and enhance the wine’s natural characteristics for both the white glass and the red. The difference between this and the Zalto, for reds specifically, is that the Veritas doesn’t add the nuance and subtleties the Zalto does. It doesn’t improve the wine or allow the more intricate notes to come out. But what it lacks in whatever magic of the Zalto is, it makes up for in affordability and the fact that this glass is less nerve-racking to drink from. That said, Riedel claims these are dishwasher-safe, but unless you plan to make these stemless glasses (My take on that below!), the stem is imminently breakable. These have to be hand-washed.
This little glass (the company is owned by Riedel now, though it was once their biggest competition!) outperformed much more expensive glasses with its thin lip, excellent bowl for swirling, and ability to concentrate aromas. The red and white glasses are thin, but felt sturdy enough that I never worried about breaking them. They go into the dishwasher and come out in one piece. For the money, these glasses are the little engine that could. They came in third or fourth place in tasting every single wine—from Nebbiolo to Malbec, Chardonnay to Grüner Veltliner. This is an elegant everyday glass and it blows away its competitors (Schott-Zwiesel, Stozle, Libbey, and the more expensive Gabriel-Glas). I will warn that although the white glass is spectacular, it is quite small in comparison to the Burgundy glass. It works great, but it can be surprising when you open it, especially in comparison to the ample size of the brandy glass.
You don’t need a glass for every region or grape but depending on what and how you drink, there are four standard glass shapes you should consider. The combination of these shapes plus the cost, fragility, washability, and comfort in holding and drinking will be the keys to getting the best wine glass for you.
The White Wine Glass
Shaped like a tulip, this glass has a round bowl and goes straight up before tapering slightly at the top. The bottom of the glass allows you to swirl without spilling, but the real magic of a white wine glass is that it concentrates aromas of the wine at the rim and traps them slightly so we can sniff the (hopefully) delicious things the wine has to offer.
The standard white glass is a bit smaller than the red: Because whites don’t need as much aeration (swirling), they’re smaller. Also, whites are almost always served colder than reds. Pouring smaller quantities into the glass will ensure that what you have in the glass always stays at a cool temperature. This Vodka glass type will work for almost all white wines, except for fuller whites like oaked Chardonnay and white blends from the Rhône Valley, for example.
Shaped a bit like an upside-down mushroom, these glasses have wide bowls and then taper at the top to a narrow rim. The huge bowl allows for tons of swirling. With reds and the fuller whites, you want to introduce a lot of air into the wine. The swirling motion jostles the esters and aldehydes in wines, which are the things that make the juice smell so good. In very aromatic but less mouth-drying tannic reds, you want to concentrate the aromas at the rim of the glass to maximize the intensity of smell compounds your nose can sense. The wider base allows room to swirl (you should never fill these glasses above the bulge in the glass or it’s spill city), but the top ensures that delicate aromas of red Burgundy (Pinot Noir), Beaujolais (Gamay), or Nebbiolo, for instance, aren’t lost.
The Bordeaux Glass
This is a giant version of the tulip shape we find in the white wine glass, although it tapers less at the top. The relatively straight sides of this glass and large bowl allow air to penetrate before, during, and after swirling, allowing harsh tannins to dance with the oxygen and soften up—exactly what you need to enjoy a Cabernet Sauvignon, a Bordeaux blend, a Rioja from Spain, or a Syrah from the northern Rhône of France.
The Champagne Flute
This is actually quite a controversial opinion among wine snobs: Flutes are festive, fun, and they do, in fact, help keep the sparkle in your glass for longer. There are some practical issues with these party-perfect glasses: Unless you drink sparkling wine a lot, they tend to gather dust; if you have a beak like mine, that can be an issue for drinking; and—the dork argument—they have no room for swirling. Nevertheless, I love enjoying sparkling out of them and I drink enough of it to have them around. Still, they are optional. A white wine glass works just as well.
What About Universal Wine Glasses?
Try as they might, over and over again, the universal glass always makes one wine or another a loser. They are too narrow for tannic reds and sometimes don’t aerate the wine as much as they should. They are too wide and open for aromatic reds or delicate whites (although they are better for whites than reds most of the time). Regardless of how high-quality the glass, the shape matters too much for these glasses to work for all wine types. My advice: Buy a set of whites and reds (I think Burgundy glasses are more useful than Bordeaux) and leave the universals to people who didn’t read this article.
What About Stemless Wine Glasses?
We did not include any stemless glasses in our tests of the best red wine glass simply because we do not feel they belong in that elevated tier. Because there is no stem, the drinker holds the bowl of the glass in their hand—and that direct contact can possibly increase the temperature of the wine, and that increase in temperature can mess up the flavor of the wine.
|
|
|
Stress Distribution at the Fillet of an Internal Flange |
Posted by: zjjsw25ss - 08-23-2021, 06:48 AM - Forum: Welcomes and Introductions
- No Replies
|
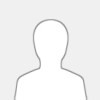 |
This paper deals with the determination of the stress distribution at the fillet of a ANSI B16.5 flanges attached internally to a hollow cylinder. A load parallel to the axis of the cylinder and of variable eccentricity acts on a bearing plate which rests on the flange. The strains are measured by means of electrical resistance wire strain gages. The ratios of the mean cylinder diameter to the cylinder wall thickness and of the mean cylinder diameter to the flange thickness are varied. The principal stresses at the fillet are given as functions of these parameters. The experimental results are compared with the stresses calculated on the basis of an approximate theoretical solution for both an axial and an eccentric load.
Abstract Joining of steel pipes and pipe flanges use today the conventional method of fusion welding, where the flange is girth-welded onto the pipe. However, fusion welding of flanges to pipes is associated with many disadvantages such as the final quality of the weld, degradation of the mechanical properties of the base pipe near the heat affected zone, defects and cracks appearing in the weld, misalignments, to mention a few. The current study proposes a novel pipe-flange connection to replace the fusion welding process of steel pipes with a method based on cold working. The method is based on that the steel pipe is inserted into the neck of the flange, in which two circumferential grooves are manufactured. An expansion tool having two teeth is entered from the open side of the connection and is expanded hydraulically such that the teeth deform the pipe and cold work it plastically into the grooves. This will provide a strong joint between the flange and pipe. In this study the performance of the connection is maximized by optimizing the design of the flange and the expansion tool.
The use of bolted flange connections in the offshore wind industry has steeply risen in the last few years. This trend is because of failings observed in other modes of joints such as grouted joints, coupled with enormous economic losses associated with such failures. As many aspects of bolted flange connections for the offshore wind industry are yet to be understood in full, the current study undertakes a comprehensive review of the lessons learned about bolted connections from a range of industries such as nuclear, aerospace, and onshore wind for application in offshore wind industry. Subsequently, the collected information could be used to effectively address and investigate ways to improve bolted flange connections in the offshore wind industry. As monopiles constitute an overwhelming majority of foundation types used in the current offshore wind market, this work focusses on large ANSI welding neck flanges in the primary load path of a wind turbine foundation, such as those typically found at the base of turbine towers, or at monopile to transition piece connections. Finally, a summary of issues associated with flanges as well as bolted connections is provided, and insights are recommended on the direction to be followed to address these concerns.
As per recent reports, the offshore wind sector could bring in £17.5 bn investment to the U.K. economy over the next few years after faster than expected cost-cutting slashed subsidies for the technology by half [1]. On top of that, the baseline scenario for the United Kingdom’s installations by the end of 2030 is to reach the capacity levels of 40 GW, four times the current state [2]. Additionally, the target of £100 per MWh set for the year 2020 regarding the levelised cost of energy (LCOE) of offshore wind was achieved in U.K. projects four years earlier in 2016 [3]. The above figures reinforce the need for new technological developments that will enable the utilisation of larger and more efficient offshore wind turbines (OWTs). In this direction, one of the most important concerns is the support structure of the turbine’s tower, which requires further study concerning not only the feasibility of future installations, but also current problems that need to be better understood and addressed.
OWT structures, which are quite large in thickness and diameter, operate in the hostile marine environment, where variable amplitude loads are constantly applied on different parts of the structure [4,5]. In the offshore industry, grouted connections were initially used to charge the transition piece (TP), with a certain overlap length, on the monopile (MP) foundations. Therefore, there is a tube-in-tube connection, wherein the space between the two tubes is filled with grout (Figure 1) [6]. Towards the end of last decade, numerous grouted connection joints between large diameter monopiles and connecting tubular steel transition pieces at the base of overlying support towers were found to be failing. For the majority of U.K. offshore MPs that experienced grout cracking and failures, the issue was recognised to be primarily owing to the widespread absence of shear keys (or weld beads) on straight MP and TP surfaces. Bending moments as a result of complex wind (which was the main difference in loading conditions compared with oil and gas platforms) and wave loading were important design considerations that were not accounted for during design of grouted connections for OWTs. Furthermore, axial connection capacity was found to be significantly lower than that assumed previously owing to the MP scale effect, lack of manufacturing and installation tolerances, and abrasive wear due to the sliding of contact surfaces when subjected to large moments. Typical failure modes included dis-bonding, cracking, wear, and compressive grout crushing failure.
The number of bolts depends on the ANSI plate flanges radius and thickness, type of tool used, size of the bolts, and predicted loads on the structure. These bolts serve the purpose of exerting a clamping force to keep the joint together [20]. The behaviour and life of the bolted joint depend on the magnitude and stability of that clamping force. The preload is created by the tightening process during the assembly of bolt and nut in the joint to provide enough clamping force on the joint. Therefore, the bolts need to be preloaded at the assembly stage in the flange connection. An intuitive analogy would be to think of the bolts and the joint members as elastic parts. In that way, they can be modelled as spring elements, where the bolts are stretched in their elastic region when tightened, in order to compress the joint. The joint has a much stiffer elastic constant compared with the bolts, depending on material and dimensions.
It is possible to consider the bolt as an energy storage device, which accumulates the necessary potential energy to clamp the joint and is subjected to several environmental and operative conditions that may affect its behaviour [20]. The objective is for the preload on the bolt to be maintained at a certain level, but, owing to a large number of influencing factors, it is almost impossible to achieve or retain the desired state. It must be noted though, that the main concern is not the value of preload on the bolt, but maintaining the sufficient level of clamping force that holds the joint together. Moreover, if the clamping force is too low, the joint could loosen and be subjected to more severe consequences owing to cyclic loads. On the other hand, if the bolt is over-tight, it could exceed its proof load and may break under external load. In fact, during the tightening process, a torque is applied to turn the nut and the bolt stretches. This operation creates preload in the bolted joint. This sequence of events, at any point, controls the preload. It is possible to control the preload through torque or turn or stretch or through a combination of all of them. In all of the control strategies, the torque is used to tighten the fastener even if other mechanisms are used to control the tightening. There are a lot of uncertainties in the relationship between the control parameters like torque and the preload, which could be minimised by measuring and controlling the build-up of bolt tension. This is the motivation for creating the family of tools called bolt tensioners. Using the bolt tensioner is nowadays a common practice during the installation of offshore wind turbines.
The employment of ANSI blind flanges connections for OWTs has considerably increased in the past decade owing to the failures and subsequent economic losses associated with grouted connections. In this study, the issues and opportunities associated with bolted flange connections have been thoroughly reviewed and discussed for application in the offshore wind industry. The key conclusions drawn from this study are as follows:
The advantages of bolted flange connections include the provision of direct load path through the primary steel alone, thereby avoiding slippage, reducing steel requirements compared with grouted connections, the absence of curing time, and easiness to inspect and monitor the MP–TP connection.
The challenges associated with bolted flange connections include material selection issues, short-term relaxation of bolts, issues associated with load distribution in threads, and static failure of bolted flange.
The main cause of short-term relaxation is the embedment that occurs mostly owing to surface irregularities as well as time-dependent creep deformation.
The consequence of temperature differential can either increase or decrease the clamping force depending on the thermal expansion and contraction coefficient of the materials employed in bolted connections.
The setups associated with bolted joint such as washers, lubricants, coatings, and gaskets play a pivotal role in creating and maintaining integrity in bolted joints.
The failure modes observed in bolted joints include self-loosening, fatigue failure, corrosion, and galling.
An expected trend in the bolted flange connection is the increased usage of tensioning tools compared with torqueing applications.
Further studies in the offshore wind industry can enable the optimal use of ANSI threaded flanges connections in design, manufacturing, installation, operation, maintenance, and decommissioning phases.
Ring flange connections for tubular towers, like those for wind turbines or chimneys, are subjected to significant fatigue loading. Next to the bolts, the weld connecting the flange to the tower shell also needs to be checked against fatigue failure. The flange causes local bending moments in the shell, which increase the meridional stress, i. e. stress concentrations occur. In this paper, the influence of geometrical imperfections on such stress concentrations is quantified and the influence of flange geometry on resulting stress is investigated. Recommendations are given for flange dimensions and the design procedure.
|
|
|
|