Welcome, Guest |
You have to register before you can post on our site.
|
Online Users |
There are currently 266 online users. » 0 Member(s) | 264 Guest(s) Bing, Google
|
Latest Threads |
Dominica visa free countr...
Forum: Off Topic
Last Post: axied12
06-24-2025, 12:37 PM
» Replies: 0
» Views: 156
|
Advanced microneedling
Forum: Off Topic
Last Post: axied12
05-28-2025, 01:25 PM
» Replies: 0
» Views: 290
|
Caviar and cheese
Forum: Off Topic
Last Post: axied12
05-28-2025, 12:38 PM
» Replies: 0
» Views: 257
|
Top-rated countertop comp...
Forum: Off Topic
Last Post: axied12
05-04-2025, 06:42 AM
» Replies: 0
» Views: 393
|
Ryanair letenky levně do ...
Forum: Off Topic
Last Post: axied12
02-11-2025, 01:37 PM
» Replies: 0
» Views: 789
|
Trusted essay writing ser...
Forum: Off Topic
Last Post: axied12
01-30-2025, 08:16 AM
» Replies: 0
» Views: 718
|
Bootverkopers - actieve j...
Forum: Off Topic
Last Post: axied12
12-07-2024, 11:07 AM
» Replies: 0
» Views: 842
|
Services for individuals ...
Forum: Off Topic
Last Post: axied12
12-02-2024, 03:31 PM
» Replies: 0
» Views: 814
|
Used excavators
Forum: Off Topic
Last Post: axied12
11-13-2024, 09:22 AM
» Replies: 0
» Views: 765
|
Buy Higo Rocket in Dubai
Forum: Off Topic
Last Post: axied12
10-25-2024, 01:09 PM
» Replies: 0
» Views: 876
|
|
|
What Your Sunglasses Say About You |
Posted by: bbsiw25se - 08-25-2021, 04:49 AM - Forum: Welcomes and Introductions
- No Replies
|
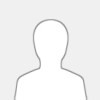 |
Sunglasses are a real character builder. Or at least they play a large roll in the character that you play to others. They’re front and center and they can literally change the shape of your face. So before you buy your next pair of shades, think about what you might be saying to the world.
With that said, here are some popular sunglass shapes along with what what they might be saying about your style.
Sunglasses are one of the world's most ubiquitous fashion accessory, but also play an important part in protecting our eyes from harmful UV rays. The earliest known use of glasses to protect eyes from the sun was the Inuit use of “sun goggles” to shield their eyes from the blinding glare of light reflected off the snow. These were made from carved driftwood, bone, walrus ivory, or caribou antler that formed a strip worn across the eye area, with thin slits that the wearer could see through. The goggles were cut so that they fit tightly to the face, and often soot or gunpowder was rubbed on the outside to absorb the light and further cut down on glare. The use of these goggles dates back to around 2,000 years ago, and as a bonus, even improved the wearers vision as the narrow slits helped focus eyesight.
unglasses protect your eyes from harmful ultraviolet (UV) rays, reduce eyestrain in bright conditions and protect you from flying debris and other hazards. Finding the right pair is key to your comfort, whether you’re driving to work or climbing a mountain.
All acetate sunglasses offered at REI block 100% of ultraviolet light. UV protection information should be printed on the hangtag or price sticker of any sunglasses you buy, no matter where you buy them. If it isn't, find a different pair.
Types of Sunglasses
Casual sunglasses: Best for everyday use and basic recreational activities, casual sunglasses do an excellent job of shading your eyes from the sun while you drive to work and walk through town. Casual sunglasses are typically not designed to handle the intensity of action sports.
Sport sunglasses: Designed for activities such as running, hiking and biking, sport sunglasses offer light weight and an excellent fit for fast-paced adventures. High-end frame and lens materials are more impact-resistant and flexible than casual sunglasses. Sport sunglasses also typically feature grippy nose pads and temple ends, a feature that helps keep the frames in place even when you're sweating. Some sport sunglasses include interchangeable lenses so you can make adjustments for different light conditions.
Glacier glasses: Glacier glasses are special sunglasses designed specifically to protect your eyes from the intense light at high altitudes and sunlight reflecting off snow. They often feature wrap-around extensions to block light from entering at the sides.
Sunglass Lens Features
Polarized lenses: Polarized lenses substantially reduce glare. Polarization is a great feature if you enjoy water sports or are especially sensitive to glare.
In some instances, polarized lenses react with the tints in windshields, creating blind spots and diminishing the visibility of LCD readouts. If this occurs, consider mirrored lenses as a glare-reducing alternative.
Photochromic lenses: Photochromic lenses automatically adjust to changing light intensities and conditions. These lenses actually get darker on bright days, and lighter when conditions get darker.
A couple of caveats: The photochromic process takes longer to work in cold conditions, and it doesn't work at all when driving a car because UVB rays do not penetrate your windshield.
Interchangeable lenses: Some sunglass styles come with interchangeable (removable) lenses of different colors. These multi-lens systems allow you to tailor your eye protection to your activities and conditions. Consider this option if you need reliable performance in a wide variety of situations.
The benefits of metal sunglasses
If you prefer to keep it lightweight and classic, you can’t go wrong with sunglasses with metal frames.
Metal frames are usually relatively thin, making them a great lightweight sunglasses option for everyday wear. Metal is also durable and resists corrosion. Metal frames also usually are outfitted with nose pads to help keep your sunglasses in place and prevent slippage (for a more comfortable fit).
Metal-frame sunglasses are typically made of aluminum, nickel, titanium or stainless steel, and come in a variety of styles, from iconic aviators to classic round frames.
When shopping for higher-end metal-frame sunglasses, consider aluminum and titanium. They’re both flexible, strong and corrosion resistant. Titanium sunglasses also are hypoallergenic, making titanium a great choice for those with skin sensitivities and allergies.
Metal sunglasses made from beryllium and stainless steel are also popular choices, due to their strength and resistance to corrosion. In fact, beryllium is especially appropriate for those who spend a lot of time in or around salt water and other abrasive environments.
Do you play sports or wear performance sunglasses? Look for metal sunglasses made with monel or flexon. Both are exceptionally malleable, and flexon will return to its original shape after twisting or bending.
Note that metal sunglasses may not work for lenses that require a strong prescription. Due to their thinner frame construction, metal frames may be unable to accommodat
WHAT IS TR90?
TR-90 Sunglasses has been manufactured using TR90, an incredible new material that you’re sure to love. So what is TR90?
TR90 was produced through Swiss technology as a thermoplastic material that is incredibly durable, flexible, and lightweight. Glasses made with TR90 are extremely comfortable because they have a flexible quality. Since they are flexible, they can bend under pressure and contour your face comfortably.
This flexibility also makes TR90 glasses resilient to damage. Because the material is pliable, they are far less likely to break or bend from impact. If you’re guilty of constantly dropping your glasses, fear not! TR90 frames can prevail!
Finally, and most remarkable of all, TR90 glasses are supremely lightweight! Even the boldest, biggest styles don’t feel bulky when made with TR90. The thermoplastic material has a barely-there feel that you truly have to wear to believe.
How Your Glasses Can Become Your Main Accessory
PC or CP sunglasses, although they are a necessity to some, don’t have to be a boring accessory to be stuck with. In 2020, we have seen a rise in popularity of amazing new glasses of all shapes and sizes. Don’t just stick with your old tired eyewear because you’re used to it; your glasses are the most noticeable accessory on your body, and they are the first thing people will see when they look at you. So, why not treat yourself to some cool, fresh glasses to revamp your look? Here is a short guide to help you along the way.
Before Choosing Glasses
It is so important to go for regular check-ups with your local eye doctor to see if anything needs changing in your prescription or if you have any eye health problems that need checking. You should go for an appointment at least every two years as not only could straining your eyes make your vision worse, it could be causing health problems like headaches and migraines too. If you have existing health problems with your eyes, you may have to visit slightly more regularly depending on the advice from your eye doctor.
Good Quality Frames
When looking for your next pair of glasses, it is so important to make sure you are getting some high-quality specs. Don’t be tricked by the price tag, as some extremely cheap glasses may not be very good quality and may break after a short time of having them. So, it is better to spend a little more to ensure you are getting the best quality you could possibly get. Sites like artofoptiks.com are experts in eyecare, and a great example of a supplier of high-quality glasses. There are so many on trend styles to choose from, so don’t limit yourself to basic frames.
On Trend Eyewear Styles
Transparent eyewear is definitely on the rise. Round shaped frames with transparent edging are such great alternatives if you just don’t like the idea of having a frame color to match your clothes with all the time. On the other hand, slightly tinted transparent frames are now becoming more and more popular, as they are like a slightly upgraded version of the clear version, with not so much color poking through, but just enough to give them a quirky edge.
Geometric glasses are another alternative option shape wise. If you’re bored of the classic round shape, maybe give these a try as they almost imitate the rounded shape but with a slight edge. You can get all manner of geometric shaped glasses including square, hexagonal and even octagonal.
Glasses a new fashion essential?
Judging from the plethora of eye-catching eyewear that’s been getting face time over the last few years — be it on the European ready-to-wear runways or in the adjoining office cubicle — it’s clear that glasses have gone from nerd necessity to chic accessory.
It’s a shift reflected in the current look-at-me trends — retro, vintage-inspired frames, chunky tortoise shells and geometric shapes that attract rather than deflect attention — and reinforced by the laundry list of fashion-focused brands with a presence in the eyewear arena. These include high-end European luxury labels like Prada, Giorgio Armani and Dolce & Gabbana as well as American contemporary brands Brooks Brothers, Tory Burch, Tiffany & Co. and Sperry Top-Sider, which aims to translate the brand’s footwear DNA into a line of licensed sunglass and ophthalmic frames due to hit the market next year.
While it might seem logical to blame the deteriorating eyesight of the aging baby boomer population or the ever-increasing computer- and smartphone-induced strain on our collective eyeballs, consumer behavior statistics don’t show a jump in the number of people who need prescriptions. What they do show, however, is an increase in the number of people who wear glasses without prescription lenses — presumably to look cool.
Dorothy Parker famously observed, “Men seldom make passes at girls who wear glasses.” How did we go from that image to bespectacled bombshells? How did eyewear go from the disguise that turns Superman into his milquetoast alter-ego to an individual expression of signature style?
Some in the eyewear industry point to the traditional pop-culture petri dishes of Hollywood celebrity and fashion runways. “Maybe they’re seeing more celebrities” wearing glasses, said Larry Leight, co-founder and creative director of boutique brand Oliver Peoples. “And there are more … fashion magazines and runway shows where designers are accessorizing their shows with ophthalmic glasses — the kind that aren’t sunglasses — with either clear lenses or only slightly tinted colored lenses.”
Milena Cavicchioli, vice president of marketing for Luxottica Group — the Milan-based eyewear company that owns Ray-Ban, Oakley and Oliver Peoples, among others, and which also makes eyewear and sunglasses under license for some 20 fashion labels — points to the recent Hollywood award show season as evidence. “Think of Meryl Streep on Oscar night,” Cavicchioli said. “She was wearing beautiful frames. And she’s not the only one. Jennifer Garner and Demi Moore are two I often see in clippings. When people are looking at [celebrities like] them to see what the latest trends are, them wearing frames is a huge support and endorsement.”
She said there have also been other factors at work over the last half decade, including fashion designers’ approach to eyewear both in the frames that bear their names and in the styled looks that hit the runways during fashion week.
“The [optical] collections themselves are becoming more elaborate,” she said. “There are some [styles] that are like jewelry pieces, that make a big fashion statement — like Prada’s Baroque frame, for example. The collections are being treated in a more fashion-forward way.”
Fashion designers have realized just how powerful a brand extension eyewear can be, especially in comparison to some other offshoots. “It’s difficult for a brand to be visible with a fragrance because you’re the only one who knows what you’re wearing,” she explained. “But when you wear a pair of blue light glasses or optical frames, the brand itself gets exposure in the most prominent way because this is something you wear on your face. It’s not like a wallet that you put in your bag. I would say that it is as powerful as a [designer hand]bag as a brand statement, as brand exposure.”
Not just a powerful statement, but an economical one too, points out David Rose, vice president of design and manufacturing at Costa Mesa-based Salt Optics. “A few years back, before the economy took a hit, people would spend a lot more money on their bags and their shoes,” Rose said. “But now eyewear is an accessible way to have a quality accessory.” Rose also said that switching out the spectacles provides a quick and easy way to create a whole new vibe. “It’s like getting a haircut — going from [having] long hair to buzzing your head — it really changes your overall look.”
It’s not just the designers who’ve seen the value of cultivating the eyewear-as-fashion-accessory notion. Cavicchioli said that over the last five years Luxottica has increased its advertising in fashion magazines and worked to get its brands noticed by influencers and trendsetters. “We’re using the category to make a statement as well,” she said.
|
|
|
Trenpro Technology: quality standard for switch plugs and sockets |
Posted by: nsj5521sw - 08-24-2021, 03:24 AM - Forum: Welcomes and Introductions
- No Replies
|
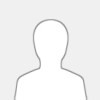 |
What is the quality judging standard of switch plug and socket? Switch socket is used to deal with electricity, so it has a great relationship with the safety of power consumption environment. If you buy a poor quality switch socket, it is easy to cause electric shock and fire. Look at the quality of American standard switches and sockets. First look at the appearance, the appearance should be smooth, and the material should be uniform. Look at which material is used and whether advanced plastics are used. Good quality switch sockets usually use PC because the material has some flame retardancy, insulation and impact resistance, and it is not easy to change color.
The quality of the switch plug and socket does not mean that the service life is long, so in addition to the quality, it also depends on the frequency of its use. The frequency of the use of switch sockets is standard, the national standard is 40000 times, some brands just conform to the national standards, some brands exceed the national standards, like the bull's switch sockets can be used 80000 times, is two times the national standard. That is to say, the service life of the same quality switch socket is different.
Electrical strength: when the metal panel American 1 gang 2 way switch is disconnected, an electrical attachment with a nominal voltage of more than 130V should be applied with a sinusoidal frequency of 50HZ2000V for 1 minutes and no scintillation breakdown may occur. Electrical accessories with rated voltage above 130V specified in the socket shall be applied sine wave frequency North 50HZ2000V voltage for 1 minutes. No flashover breakdown will occur.
What kind of switch socket is good when the quality and life span are quite good? It must be a high price ratio. Some people have always thought that the expensive is good, so the concept of consumption is wrong. The quality of the product is not rare, therefore, to buy the price is reasonable, in the quality, life and style of the same situation, the price can be considered.
Guangdong Trenpro Technology Co., Ltd. is a manufacturer specializing in R & D, production and sales of XLR Carnon socket, Carnon plug, microphone socket, audio and video socket, mainly engaged in electronic components, automotive electrical appliances from new products to production and assembly to finished products.
The current work is to conduct a design review on a multipurpose power socket for home application with the latest state of art features. Reviews are done in the areas of standard and codings, material selections, universal adapters, sensors and lighting technology. The standards for fabrication of BS 546 and BS 1363 plugs and sockets are essential for safety purposes. Together with selection of suitable material in production of plug and sockets, the occurrence of accidents can be averted. The invention of universal adapters was first coined by Rumble in year 1982 marks an evolution in the history of plugs and sockets. The main focus was to cater the different plug fixtures in various countries. Coupled to this, review works on the various types of sensors and lighting technologies is provided since it could be fused to the universal plug adapters for various applications. This paper then go on in proposing future works which could open new research pathways among worldwide researchers.
Light is an important element in human’s daily activities as it provides brightness in the dark. There are varieties of light source that are being adopted in today daily life such as fire, halogen lamp, fluorescent lamp and light emitting diode (LED) lamp. LED has been chosen as one of the most common lighting systems due to the advantage in energy saving, better luminous and it can be used for a longer period of time. Sensors is also focused in current lighting technology. Sensors will act as a residential 1 gang 1 way 16a light switch for Homes and only be functioned as it detects the gesture related to its specification such as motion or darkness. The usage of sensor in lighting system will further improve the efficiency of the system and provides an alternatives for energy saving.
The review works will start with a brief overview on the standards and codings implemented, followed by the types of material used on the development of universal adapters and their applications. On the other hand, different types of sensors and lighting technology will be discussed in this work. Last but not least, proposed future works will be presented which could help to open new research pathways in the future.
Standards are the regulations developed by International Standards Organizations (ISO). These standards act as the benchmark to be referred and used worldwide. Standards are documented to overcome differences among standards and technical regulations developed independently and separately by each nation or national standard organization. Codings is a set of rules that specify the standards that need to be followed to fabricate an object mentioned under the standard and codings.
Plugs and wall sockets are the electrical components that connect together to allow the flow of electricity and thus complete the circuit. Plug and sockets are invented in Britain in the beginning of 1880s and designed to have only 2 pins at that time. The official standards then come in when the idea of interchangeable compatible devices were proposed. BS 1363 is the British standards that is used in United Kingdom and mostly the Commonwealth countries. It is a type of single-phase AC power plugs and sockets that can support a voltage up to 250V and a variety of ampere such as 2A, 5A, 13A and 15A.
By referring to 13 A plugs, socket-outlets, adaptors and connection units, there are standards that need to be follow strictly in order to produce a marketable wall sockets with inspection on safety purposes. The sockets shall have marking the necessary information on the parts where it can be read and will not be easily spoiled.
There are specific safety requirements to be followed for BS 1363 wall adaptor. These can be divided according to 3 types of sockets which are 5A 3-round-pin adaptor, 12A 3-rectangulat-pin adaptor and 15A 3-round-pin adaptor.
5A 3-round-pin adaptors are referred to BS 546 as international standard. To design and manufacture BS 546, it must have protection from fuse-link conforming to BS 1362 together. Only an allowable current of not exceeding 5A is permitted for the operation of this adaptor. A 5A adaptor with not more than three 5A sockets protected by one 5A main fuse-link confirming to BS 646 or BS 1362 is permitted (International Organization for Standardization [ISO], 2007).
For 12A 3-rectangular-pin adaptor, the fabricating and designing process should be based on the BS 1363 Part 3 standard. The 13A adaptor that has one or two sockets for 13A plugs conforming to BS 1363 Part 1 need not be fused. For multiway 13A adaptor that has more than two sockets for 13A plug conforming to BS 1363 Part 1, it should have a 13A fuse-link conforming to BS 1363 as protection. For multiway 13A adaptor that has one socket for 12A plug and another socket for 5A plug conforming to both BS 1363 Part 1 and BS 546, respectively, an appropriate fuse-link complying with BS 546 and BS 1362 should be used to protect the outgoing circuits through 5A sockets (ISO, 2007).
While 15A 3-round-pin adaptor is manufactured and designed to BS 546 standard. A 15A adaptor is protected by fuse-link matching to BS 1362. Table 2 shows the number ratings and the current ratings of the socket configuration of 15A adaptor (ISO, 2007).
The safety features of BS 1363 adaptor or wall socket is further enhanced with the usage of safety shutters. The safety shutters is used as such that when a plug is withdrawn from it, the white American power electrical double wall socket contacts or the socket holes which carry current supply will be automatically closed. The shutters should be operated by mating the earth pin to the earth hole. The shutter for a particular socket aperture should not be able to closed the shutter for another socket aperture independently (ISO, 2007).
Figure 3 illustrates the standard dimension used in fabricating a BS 1362 type wall socket (Saudi Standards, Metrology and Quality Org [SASO], 2010). The dimension of the sockets must be strictly followed to ensure that the plug will fit firmly to the socket when using it to avoid accidents to be happened.
In Malaysia, the fabrication and manufacturing of wall sockets must follow the information booklet of Approval of Electrical Equipment (Electricity Regulation 1994).This regulation is established by Energy Commission Malaysia under the Energy Commission Act 2001 [Act 610]. Under this regulation, a socket outlet is described as an electrical device that is fixed at a point at which wiring terminates. It provides a detachable connection with the pins of a plug and it has two or three contacts with a maximum current rating of 15A. Table 3 shows the standard codes of wall socket used in Malaysia.
The abbreviation of MS in Table 3 refers to Malaysia Standard, IEC refers to International Electrotechnical Commission and BS refers to British Standard. By ensuing the procedure of these standards, the respective vendor can apply for certification of approval for electrical equipment with SIRIM Berhard. Upon obtaining the certifications, the vendors’ product is labelled as approved regulated electrical equipment and can be sold in Malaysia’s market.
Material selection is important in the fabrication works of a power socket. This is to ensure that the socket produced is durable and safe for its user. The main components of power socket are made up of plastics and brass. Plastics are used as the casing and inner structure for the socket. Brass is used as connectors to hold the plug pin to allow the flow of electricity to the electrical appliances.
Plastics can be divided into two type of categories which are synthetic or semi-synthetic organic compounds and this type of plastics are mostly derived from petrochemical. It is made by building up from simple chemical substances. To ensure the plastics bonding are tougher, safer, and cleaner, polymers that build up plastics are added with complex blend of materials known as “additives” (Talbot, 1941). These include biodegradable plasticisers, flame retardants, and heat stabilizers. The grade of plastics used in socket manufacturing is mainly thermoplastics or thermosetting polymers. Thermoplastics are plastics that will not undergo physical or chemical change in their composition upon heated (Gilleo, 2004). Thermosetting polymers, on the other hand can melt and take shape only once. They remains in solid once they have solidified. There are few common plastics grade that are used in fabricating power socket.
Phenolic is one of the plastics used in manufacturing process. It act as a good electrical insulators and able to withstand resistance against water, acid and most solvents. It has low thermal conductivity and rigid at room temperature. The normal operating temperature limit for phenolic molding is 150°C, but grades are available which will operate at up to 200°C for limited periods. These properties allow it to be used in electric appliances industry (Black, 2010). There are two main production methods. One reacts phenol and formaldehyde directly to produce a thermosetting network polymer, while the other restricts the formaldehyde to produce a prepolymer known as novolac which can be molded and then cured with the addition of more formaldehyde and heat (Gardziella, Pilato, & Knop, 2000; Hesse, 2004).
Melamine formaldehyde, or melamine is another type of plastics that is used due to its strong and glossy properties. Melamine shows good resistance to heat, chemicals, moisture, electricity and scratching which makes it to have excellent molding properties in producing power sockets and plugs (Black, 2010). Melamine formaldehyde was discovered by William F. Talbot and patent was applied on 12 December 1936 (Talbot, 1941).
Another type of plastics that is widely used is polyimide. Thermosetting polyimide is one of the highest performing engineering plastics, with superior performance in applications under severe conditions. The properties of polyimide materials include:
high temperature resistance that have operating temperature of 315°C,
high wear resistance,
low thermal expansion,
good thermal and electrical insulation,
relatively easy to machine,
With this properties, thermosetting polyimides are used in various types of manufacturing industries including automotive, electrical appliances, aircraft and aerospace (Black, 2010). These materials tend to be insoluble and have high softening temperatures, arising from charge-transfer interactions between the planar subunits (Liaw et al., 2012).
Brass is the material used as the electrical conductor inside the wall socket. Brass is a material that is made of copper and zinc. Copper-zinc solid solution alloy or brass retains good corrosion resistance and formability of copper but are relatively stronger (Fungal & Brody, 1996). Brass is used widely in the socket manufacturing due to its properties and it is a cheaper material compare to gold. Brass is generally soft which means that it can be machined without the use of cutting fluid, though there are exceptions to this (Faraday, 1832). Brass is used in situations where it is important that sparks are not struck, for example use as a fittings and tools that near flammable or explosive materials. CL 15000 99.85Cu-0.15Zr or zirconium-copper is one of the brass used in fabrication process. It has elastic modulus of 129 GPa and fatigue strength of 180 MPa. The density of CL 15000 is 8.89 g/cm3 and it has a liquidus temperature of 1080°C. The electrical conductivity of 93% IACS at 20°C. CL 15000 can withstand a temperature up to 1080°C before it melts 93% IACS shows that it is a good electrical conductor. Another similar brass or copper alloy, CL 15100 shows a similar properties as in CL 15000. This alloy is called ZHC copper and the elastic modulus is slightly smaller (121 GPa), the density is larger (8.94 g/cm3) and the liquidus temperature is the same at 1080°C. However, CL 15100 is a better conductor of electricity with 95% IACS if it is annealed and 90% if it is rolled with volumetric at 20°C (Fungal & Brody, 1996).
The material used for doing the conductors inside wall socket but be able to withstand overheating. If the holders are getting hotter relative to time, there will be a risk of fire. The heating comes from the current which is drawn by the appliance and the resistance of the conductor. The plug pin will be inserted to or removed from the socket when using it. If the material wears too much, the holder may not be able to hold the plug pins firmly. Besides, the material used must be in low cost to keep the material and processing costs down.
The material used to fabricate an electrical wall socket is crucial in safety purposes. Failure of the material used may possess danger like electrical sparking. Types of plastics used must be a good electrical insulator to avoid the electricity to be channelled into area other than the socket holes that fit in electrical plug. Types of brass used must have good ductility to ensure that the holder of the socket will always mate with the plug pin tightly and allow electricity to flows through efficiently.
By selecting the right material in fabrication, problems like electrical sparking can be avoided. Electric sparking is an abrupt electrical discharge that occurs when a sufficiently high electric field creates an ionized, electrically conductive channel through a normally insulating medium, often air or other gases or gas mixtures. Faraday described this phenomenon as “beautiful flash of light attending the discharge of common electricity (Faraday, 1832). By rapid transitioning of electric field from a non-conducting to a conductive stats, it will produce a brief emission of light and a sharp crack or snapping sound.
Fire is one of the major disasters around the world and electrical fire is the leading type of fire in terms of occurrence rate. An analysis is done in China and the leading type of fault resulting in major electrical fires is short circuit (43.89%) while the second leading fault is loose contact accounting for 8.89%. The second type of faulty is more difficult to discover as it is always covered by some illusions including short circuits. A study to such fires also known as sparking was conducted by Zi-Bo, Man, Chang-Zheng, and Ming (2011). First, two different types of loose contact fault, contact area reduction and contact vibrations are simulated tested and the temperature and some electrical parameters of contact resistance are tabulated during the testing. With this results, the characteristic identification criterion for loose contact is proposed (Zi-Bo et al., 2011).
In the experiment, plugs and American style single 3 pin socket of rated current 10A are used under conditions of reduction and contact areas and contact vibrations. External heating temperature of 100°C, 200°C, 300°C, 400°C, 500°C, 600°C and 700°C are used to determine the characteristic law of samples. Apparently the plastics insulations of shells are melted and deformed while the metal parts are carbonized but there is no sign of melting and deformation. From the analysis results, it can be concluded that under fault over a small contact area, the plug’s terminal could reach a temperature of 300–400°C and the contact area between plug and socket can reach a temperature of 200–300°C. The major problem in sparking is after melting and carbonizing of insulation material of wall socket, secondary fault including combustion and short circuit may happen directly (Techakittiroj, 2008).
The inductance of the wall sockets will result in creating sparks. When the outlet is unplugged, the inductance in the distributed system resists the change in the current. The path for the current has to be created and it is only active when the socket is unplugged. The rising voltage appears mainly at the outlet terminal and the major concern is to reduce the voltage at the socket. By reducing the voltage, the electrical sparks on the contact surface can be eliminated and this improves the socket lifetime. A capacitor is used to absorb energy from the inductance where the voltage will be regulated by the capacitor. By combining a capacitor with an inductor will result an oscillation at the voltage terminal and prolongs the durations of high voltage at the terminal. A resistor is used to damp the oscillation (Techakittiroj, 2008). Figure 4 shows the PSpice circuit for analysing a socket outlet.
|
|
|
The Methods of Distinguishing the Quality of Crusher Wear Parts |
Posted by: nsj5521sw - 08-24-2021, 03:21 AM - Forum: Welcomes and Introductions
- No Replies
|
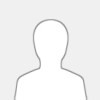 |
Optimized maintenance is a key competitive advantage for an aggregate producer. Dealing with multiple service providers and brands can become a significant risk as response times, quality and inventories vary across suppliers. For crushers, it’s the spare parts that ensure operational uptime; they enable the metso jaw crusher spares and the process to keep on going. Would it be beneficial to have one premium partner to provide parts and services for all your crushers? We say it is something to consider, but only with the right partner – here’s why.
For us, quality is not limited to parts’ features, but it means also our readiness to provide extended support when needed. Non-OEM part suppliers might have the capability to provide a certain missing part to the crusher, but is it of the right material? The exact right design? These things can’t be guaranteed, and the risk of malfunction in operation or additional servicing can start to climb if a sub-optimal supplier is used. We combined our expertise and heritage as the pioneer in many crusher technologies into a premium series of crusher parts for non-Metso Outotec crushers, the Contender™ Series. These parts are made to ensure an exact fit and they can be counted on to perform.
Another thing to consider is the warranty. If the part doesn’t live up to expectations, an OEM manufacturer like Metso Outotec has a strong warranty program in place. With warranty, the risk of unplanned costs for the crusher operator is minimized, and the performance is followed up on in a timely manner. Also, a partner like us with a strong footprint and background has more capabilities available to ensure that the right part, no matter which one it is, is in-stock when needed. We have large inventories quickly accessible and are not limited to certain parts only.
One of the main advantages of centralizing the maintenance activities of multi-brand crushers, including parts and services, is cost savings. Instead of dealing with multiple interfaces, aggregate producers can have one point of contact to take care of everything. That is our mentality, to provide a partner solution to our customers instead of just parts and products. It makes the planning a lot easier and makes the service more efficient, which helps in increasing the uptime and thus – as time is money – increase the profitability.
Sometimes, it might be enough to have the part replaced with the same solution but there could still be room for improvement in terms of performance. Contender™ Series spares are not limited to standard solutions as we incorporated multiple innovations in the design. In some cases, materials and safety aspects have been improved to enhance the durability and sustainability of the parts. These innovations aren’t accessible from part providers solely focused on replicating the existing ones.
For example, the enhanced spider bushings for non-Metso Outotec crushers are strengthened to have a longer than original operational life to help performance under the toughest operating conditions. Its material has a high residual value when recycled, compared to more traditional materials. Another example is the enhanced dust seal rings, which experience less wear on mating steel parts and less surface contamination from dust and particles due to the self-lubricating design and characteristics of the materials selected. We haven’t been limited to the conventional ways of doing this but have used upgraded metallurgy and for example enhanced wood materials in our design for the dust seal rings.
Sustainability should be considered in all steps of the way, from start to finish. We use certified beech from Europe as the base for our wooden components. Safety is improved by providing part features such as additional lifting lugs and also for example by providing a specialized lifting tool for Metso Outotec-made mantles for third party sandvik jaw crusher spares. Most importantly, your operations become sustainably efficient with one partner that can be trusted to be there now and also in the future.
Although crusher parts may look the same from the outside, they may be very different in terms of quality, fit or materials.
Using an incorrect part that does not perform as planned can be very costly – equipment can be damaged, the parts lifetime may be shortened or the equipment could fail, putting the safety of workers at risk.
This e-book looks at the 7 key areas you should consider when buying crusher spare parts to help you make a good decision when it comes to choosing the right supplier.
You will receive the e-book by filling out your contact information on the form and clicking the "Sign-up". The e-book will be automatically sent to the e-mail you provided.
Crushers are widely used in metallurgy, construction, mining and other industries, and wear parts play a crucial role in the crushing process. High quality wear parts help to cut costs and increase production. How can we distinguish the quality of crusher wear parts? We can start from three aspects as below,1.Appearance Quality: Checking the smoothness of the surface of the spare crusher parts, the cracks on the products, the dimension, shape and weight etc.. Each product is strictly inspected before shipping to ensure the products are in good condition to use. Gubt provides Dimension Inspection report for your review.
2.Internal Quality: Generally, GUBT detects the grain size of the crusher wear parts, chemical components, Metallographic structure, pores, etc.. The report below is Metallographic and Chemical test report for material Manganese.
3.Performance Quality: generally, performance quality refers to wear parts how long they last, and how effectively they can crush under difference circumstances (including wear resistance, heat resistance, corrosion resistance, impact resistance etc.). There are many factors affecting the quality of spare parts.1. The design of the products. When designing, the casting geometry and dimension is not only determined by the working condition and the metal materials, but we also need consider from the perspective of casting alloy and casting process characteristics to decrease the rate of scrap. 2. Casting process. Castings’ structure, weight, dimension etc. are the critical factors for castings. With these criteria, the best casting solution will be optimized (the molds, core-making method, cold iron, risers, pouring systems etc.). 3. The quality of the raw materials. The casting quality depends on the raw materials you use, including Mn material, refractory materials, fuel, molding sand, sand binder etc. If the raw material do not meet the standards, defects happen such as pores, slag inclusions, sand sticking, etc., which will affect the appearance quality and internal texture of the products, or the products will be scrapped.
Superior Industries Inc., a U.S. based manufacturer and global supplier of bulk material processing and handling systems, says it has entered into a strategic partnership with Europe's largest manufacturer of aftermarket crusher parts. For 40-plus years, CMS Cepcor has manufactured premium cone crusher spares spares for more than three dozen active and classic brands throughout Europe. The parts manufacturer recently expanded its global footprint when it launched CMS Cepcor Americas.
From its US headquarters in Pekin, Illinois, CMS Cepcor Americas will stock, sell and service aftermarket parts throughout North and South America. In addition to the greater market, they will work closely with Superior to supply crushing equipment spares to Superior's growing group of crushing dealers and customers.
"We have assembled a talented team of industry veterans who understand what it means to serve customers with high quality products backed by timely support," says Doug Parsons, the president of CMS Cepcor Americas. "Personally, my relationship with Superior goes back two decades and our trust and confidence in each other runs deep. We're excited to fill a gap in the market where customers are not being supported to the level they require."
Choosing the most appropriate profile is not simple and there are no rules, since each application has a number of different variables like feeding, opening, product needs and problems. All these will decide the type and service life of the jaw parts you are choosing.
Certain profile types decrease or increase the crusher’s hourly production. So, for the correct choice, it is necessary to have a good knowledge of crushing and to observe what happens inside the crusher’s chamber (very lamellar material, excessive humidity, fines, need of small opening, etc).
And also the stone type also decide what material you are choosing. As we all know when the same crusher deal with different type of stones, the performance and the service life of the jaw plates are different. Why? some stones are of higher grade of the hardness, some stones are of more silica inside, etc.
So to choose the right jaw plates material on different worksite is necessary.
When the wearing of the jaw crusher spares plates is severe, it is a known fact that crusher performance is not ideal, because the empty spaces between the teeth are reduced, encagement happens frequently, the crushing angle is changed or, in other words, production is affected.
This means that, a cost-benefit analysis for changing the worn symons jaw crusher spares plate should be seriously considered, because at a certain point, the difference in production justifies the investment in a new part. We have also observed users crushing even with cracked and perforated jaw plates, without carrying out the correct control and cost x production analysis.
To change the jaw plates in time is a very very important thing to do the good maintanance. And will cause to very bad effect if we don't change the jaw plates when it's time to.
Fixed jaw plate – use until wear of about 50% occurs in the lower area and make the first turn. Make the second turn when wear from 90% to 100% occurs in this new lower area. Conclude using the remaining 50% of the life cycle of this extremity.
|
|
|
A Look at Two Different Print Technologies: Dye Sublimation and UV |
Posted by: nsj5521sw - 08-24-2021, 03:20 AM - Forum: Welcomes and Introductions
- No Replies
|
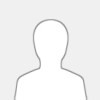 |
Since the introduction of the first personal computer, we have been ushered into the “digital age.” Technology has transformed virtually every aspect of our daily lives, and this phenomenon has been no different in the digital printing arena. Digital printing technology is pushing the envelope when it comes to what we can print on and how to do so more efficiently. “Can I print on that?” is the new mantra, as customization increasingly replaces mass production as the new norm.
Let’s take, for instance, a plain cellphone cover. There’s nothing spectacular about this generic piece of plastic. However, once it’s decorated, the perceived value of the product exponentially increases. The performance of the case hasn’t increased, yet people are willing to pay more, simply because it has been personalized.
There are a variety of methods used to decorate plastic products, with one of the most popular processes being dye sublimation. While most people associate dye sublimation paper with textiles and apparel, this is not solely the case, as this process also can be used to decorate a broad array of plastic or rigid substrates.
What is dye sublimation? Sublimation is defined as “a phase transition of a substance from a solid state to a gas while bypassing the intermediate liquid phase.” In the case of dye sublimation printing onto rigid substrates, the disperse dye inks are printed onto a coated medium, which is most often a “transfer paper,” but also can be a “transfer film.” Once printed, these water-insoluble dyes then dry and turn solid as the water solution evaporates. Heat (typically 400°F), pressure and time turn these solid dyes into gas which, upon release from the transfer paper or film, then penetrates the plastic or polyester coating. In addition to dyeing the plastic or rigid substrate, the sticky sublimation paper transforms the dull colors that were originally printed on the transfer paper into incredibly vibrant hues.
The end-product and volume will determine the type of heat press that should be purchased. If decorating mainly flat objects, then a flatbed press is ideal. Flatbed presses can be small (16×20″) presses or large-format presses that can accommodate 4×8′ panels.
If sublimating on 3D objects, then a 3D oven press will be needed. Once again, the oven presses can range from smaller “desktop” units to machines the size of a walk-in room. Instead of printing onto transfer paper, the images will be printed onto transfer film, which is able to conform around the edges of the object being decorated. A fixture is needed to hold both the object and printed film in place. A vacuum hose is attached so the printed film thermoforms around the object and, when the oven heats up to 400°F, the Inkjet Sublimation Paper process takes place.
With dye sublimation, the applications are seemingly endless. The important thing for users to remember is that dye-sublimation takes place at the heat press, not at the printer. However, a high-quality printer with premium RIP software is necessary to produce quality prints with accurate colors and ink drop placement. Dye sublimation ink droplets are extremely small. A colleague best described it by saying, “the largest dye-sublimation ink droplet is smaller than the smallest eco-solvent ink droplet.” What that basically means is that these ink droplets are small, and they need proper control when they jet from the piezo print head. Without proper control, it is not possible to achieve fine lines and details or smooth gradients.
Dye heat sublimation paper requires polyester or plastic for the inks to penetrate into the substrate and dye. The blanks must be able to withstand 400°F heat, pressure and time (which can range from 60 seconds to minutes, depending on size and type of object).
How does UV printing differ from other printing methods?
Ultraviolet (UV) printing is different from tacky sublimation paper or conventional printing methods – including both traditional pigment, solvent inkjet and commercial offset – in many ways. While it is still ink on “paper,” the ink cures through a completely different process and the “paper” ends up being no longer just paper. Instead of having solvents in the ink that evaporate into the air and absorb into the paper, UV inks dry through photoinitiators in the ink and are solidified by UV lamps. When the inks are exposed to ultraviolet energy, they turn from a liquid or paste into a solid. Thus, UV-curable inks are “cured” once they are exposed to the wavelengths of UV energy.
This curing process is advantageous for many reasons. One of the biggest benefits of UV printing is that it lowers emissions of volatile organic compounds into the environment, as the solvents don’t evaporate like conventional inks. Another advantage of UV printing is that the inks can cure on plastic and other nonporous substrates. Because the inks dry through this photomechanical process, it’s not necessary for the ink solvent to absorb into the stock. The UV process allows for printing on just about anything. Essentially, if the media or product can get through or under the printer, it can be printed.
But – and this is what I call my “but factor” – adhesion can still be an issue in UV printing. It is important to understand that, while UV printers can print to virtually anything, there may still be adhesion or durablity issues that need to be overcome.
Challenges in decorating with UV inks
UV printers can print on a variety of unusual substrates, ranging from wood and wooden veneer, glass and sheets of metal to fabrics and plastics of all shapes and sizes. Since UV inks dry or cure so quickly when exposed to UV energy, there’s no time for them to soak into the media. The ink dot sits on top of the uncoated sheet as a cleaner, less contaminated dot, ultimately allowing for a more vibrant and “crisp” color appearance.
Printing successfully with UV inks depends upon being able to expose the inks to enough ultraviolet energy for curing to take place without making the substrate too brittle, and at the same time ensuring an acceptable level of adhesion to the substrate. This can be extremely difficult, as each type of substrate has different surface tensions or dyne levels.
Dyne level or surface tension in UV printing is the property of a UV ink forming unbalanced molecular forces at or near the surface. If this is higher than the surface energy of a material, the liquid tends to form droplets rather than spread out. Plastic materials can have very different surface energies based on their composition and how they are formed. The surface tension is normally measured in energy units called dynes/cm.
If the ink has a dyne level lower than the material’s surface energy, then the ink will spread out over its entire surface in a uniform, wet layer. If the ink’s dyne level is equal to or higher than a material’s dyne level, the ink becomes cohesive and tends to remain in droplets, thus allowing for better adhesion to plastics.
So, how do we control the dyne levels of raw plastics or pre-formed plastic products? The development of adhesion promoters has dramatically increased the adhesion of UV ink to plastic products. Adhesion promoters, sometimes referred to as coupling agents, are bi-functional materials that increase adhesive strength between the coating and the substrate. Unlike priming systems, adhesion promoters are generally applied at thinner film thicknesses. An adhesion promoters effectiveness depends on both the substrate and the adhesive being used. Surface pretreatments, such as solvent cleaning or mechanical etching and corona treatment, can be used with adhesion promoters as part of a pretreatment method. Within a class of materials, the functionality on the backbone of the molecule surface will vary based on the resin system employed as well as the substrate to which it is attached.
Many ink manufacturers have developed adhesion promoters to aid in the printing process. Polypropylene (PP promoters) and polyethylene (PE promoters) are two adhesion promoters that are widely used in UV printing. Both of these promoters can help create a chemical bond to different types of plastics. While they are widely used within the UV printing industry, these promoters do have varying success factors that must be tested.
With the UV printing process, there are two useful tests that can be employed to evaluate adhesion – a traditional “scratch” test and a “cross-hatch” test. Each of these tests provides a different evaluation of the bond between the plastics product and the adhesion promoter and UV-cured ink printed to the object or raw material.
The scratch test is similar to a traditional abrasion test. A metal object, such as a penny, is vigorously rubbed on top of the UV print. Depending on the number of passes and vigor, it can be analyzed and given a “score” or rating. The better it performs against the abrasion, the higher the durable score.
The “cross-hatch” test is performed again after the adhesion promoter and UV-cured print have been output. Using a razor blade, knife or other sharp cutting tool such as a special crosshatch cutter, two cuts are made all the way through the UV print down to the substrate, forming an “X” mark with a 30- to 45-degree angle between the angles of the cuts.
An aggressive tape is placed at the center of the “X” and then quickly removed. The area is then examined to see if any UV ink has been removed. Again, it can be analyzed and given a “score” or rating. The better it performs against the “cross-hatch,” the higher the durable score.
While adhesion is a common issue with UV printing because of the vast amounts of printable objects or substrates, the acceptable level must be identified and tested on the final products the user is printing. Because UV printers can print onto just about anything, although they still may have adhesion or durability issues, it is important for the print provider to show the end user test prints to gauge the acceptable durability on the product based on two questions: 1) How long will the product be used, and 2) Will the product be handled for extended periods of time? The answers to these questions will provide the acceptance levels, which helps to ensure customer satisfaction.
UV print technology makes it simple to print on a vast array of rigid materials, including plastics. Being able to print directly to plastic objects – whether raw or pre-manufactured reduces both operation and delivery time. It also allows the user to incorporate white and gloss inks in glossy or matte finishes to create unique textures – enhancements that add value and sophistication to the end product. In addition, UV technology helps print providers expand their applications and product offerings by enabling them to print on wider variety of substrates.
|
|
|
Aluminium in the Building and Construction Industries |
Posted by: nsj5521sw - 08-24-2021, 03:17 AM - Forum: Welcomes and Introductions
- No Replies
|
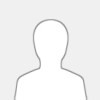 |
Aluminum building materials is widely used in building because of its intrinsic properties of lightness and corrosion resistance.
Aluminum is used in external facades, roofs and walls, in windows and doors, in staircases, railings, shelves, and other several applications.
Aluminium in building construction
Thanks to its features, there are many benefits that aluminum offers to the construction industry:
Alloys
Pure aluminum is a low-strength metal and consequently not suitable for building applications but thanks to the addition of alloying elements such as copper, manganese, magnesium, zinc etc. and thanks to specific production processes, it changes its physical and mechanical properties to meet requirements of a large number of applications.
Durability
Aluminum alloys for Building are resistant to water, corrosion and immune to the harmful effects of UV rays, thus ensuring a lasting endurance
Low maintenance costs
Aluminum does not require any special kind of maintenance, whether it is raw or lacquered aluminum
Finishes
Aluminum can be anodized or lacquered in any color, so it’s possible to get the most varied effects and thus meet the designer’s decorative needs. Aluminum treatments can increase the durability of the material and its corrosion resistance
Reflective properties
Aluminum is widely used for light management: its reflective properties help to reduce energy consumption for lighting and heating.
For example, it’s possible to reduce the use of air conditioning in summer season by using aluminum shielding devices.
Aluminum is not combustible
Aluminum does not burn and is therefore it’s classified as non-combustible material (A1 fire reaction class).
Nevertheless, aluminum alloys melt at about 650 ° C, but without releasing any harmful gases. And so, more and more often, the outer covers and external surfaces of industrial structures (and not) are made with thin aluminum panel finishes which are destined to merge only in case of fierce fire, thus allowing heat and smoke to escape and reducing damage Caused by the fire.
Certified studies have proved that the alloys, the surface treatments (coatings) and the materials used are all neutral. Aluminum used in the construction industry does not have any negative impacts either on the quality of the air inside buildings, on land or water.
These are just a few of the benefits of using aluminum, in a technical and technological development view the extraordinary properties of this metal will offer (potentially) endless possibilities for building engineering applications.
The aluminium element was discovered 200 years ago. After an initial period of technological development, aluminium alloys were used in many structural applications, including the civil engineering field. Aluminium is the second most widely specified metal in building after steel, and is used in all sectors from commercial building to domestic dwelling.
This paper contains complete overview of use of Aluminum corbel in building construction. How it is beneficial in modern age building construction. This paper also contains the properties, advantages. Some question arises that whether aluminium is sustainable, fabricated for fast track, requires maintenance, are explained in detail in this paper.
Aluminium is the second most widely specified metal in buildings after steel, and is used in all construction sectors, from commercial buildings to domestic dwellings. 40% of the UK annual production of aluminium is utilized within the construction industry, which equates to roughly 150,000 tonnes of aluminium per annum, of which approximately 65,000 tonnes is extruded products, and 25,000 tonnes sheet materials.
The main market sectors are windows, roofing, cladding, curtain walling and structural glazing, prefabricated buildings, architectural hardware, H&V, shop fitting and partitions. Aluminium is also used extensively in plant, ladders and scaffolding.
Primary smelter aluminium is pure and, as such, has a relatively low strength. For extrusions and other manufactured components, the material is alloyed to improve its strength, although even the most heavily alloyed wrought aluminium is still 92% pure.
The two series of alloys most widely used in construction are the 5000 series work-hardened magnesium alloys and the 6000 series heat-treatable magnesium silicone alloys. The latter are more extrudable and, therefore, offer greater scope for complex shapes. Silicone alloys (such as LM6) and manganese alloys (such as 3103) are also used for specific construction applications.
By selecting the right alloy, the designer is offered a wide range of properties including high strength (up to 400 MPa or 26 tonnes per sq inch), low density, high thermal conductivity, and good forming and joining characteristics. The choice of the most appropriate alloy of the 6000 series for a particular extrusion depends on the nature of the task it has to perform. A balance has to be struck between strength, ease of forming and finish. The 6063 alloy, for instance, has good extrudability, corrosion resistance and surface finish; and is thus widely used in fenestration. The properties of the individual alloys are amplified by the shape of the extruding die. Careful and knowledgeable design can take advantage of the ability of the extrusion process to distribute the material across the section to exactly where it is needed for a particular performance requirement.
Modern building and construction is more than merely erecting buildings as functionally as possible. In addition to functional and economic criteria, aesthetic and design considerations together with ecological demands placed on building projects play an equally important role. This means the materials used are of major significance. Aluminium, the building material for the modern age, established itself as an important factor in the building and construction industry during the course of the 20th century. Aluminium enables every possible architectural concept to be realised – regardless of whether it is a new build or a modernization. Possible applications range from façades and roof and wall manufacturers of Aluminium building products systems to interior decoration and the design of living are world leaders technologically – not least space, and include windows and doors, balconies because the companies have furthered the and conservatories development of modern windows and façades in the fields of surface treatment, thermal insulation and soundproofing, air conditioning and solar heating. With an annual domestic demand of about 500,000 tonnes, the building and construction industry is the second largest market for aluminium products in Germany. Its share of the total aluminium market is 15 percent.
One of Aluminium’s primary appeals to specifiers is its exceptional strength to weight ratio. At 2.7g/cm2, Aluminium is 66% lighter than steel. It is also far less susceptible to brittle fractures. Indeed, when aluminium and steel structures are compared, Aluminium’s greater modulus of elasticity means that weight ratios of 1:2 are easily attained.
While Aluminum railing has a relatively high co-efficient of linear expansion, at 24 X 10-6/’C – in its pure form, the material’s low modulus of elasticity (65,500N/mm2 for 6063 alloy) enables temperature induced stresses to be accommodated. Indeed, these are generally far lower than in a comparable steel structure (M of E = 210,000N/mm2). This is graphically illustrated by Aluminium’s load-deflection curve, which is continuous, without a yield point.
Aluminium sections are generally thinner and deeper than equivalent steel sections to achieve the required strength and rigidity since, Aluminium is not affected bymoisture and aluminium windows do not warp, stick or rot. In door construction, typically using hollow-section extrusions, sight lines are improved because multi-point locks and other door furniture can be fitted within the frame. This is in addition to the intrinsic lightness, strength and rigidity of Aluminium frames
2.2 Low maintenance – low cost-in-use
While Aluminium has a natural, built-in durability (it forms a protective layer of oxide as soon as it is exposed to air), most Aluminium construction products are treated or coated. One way in which the oxidization process can be enhanced is anodization; an electrolytic process which increases the thickness of the natural oxide layer from 0.00001mm to between 0.005 and 0.025mm (25 Microns). This enhances the ability of Aluminium to withstand attack in aggressive environments. Natural anodizing results in a similar silvery finish to oxidized Aluminium, but it can also introduce a range of colours.
This is because, after anodizing, the surface film remains porous, allowing it to accept colouring agents, such as organic dies, pigments, electrolytes or metallic. Attractive gold, bronze, gray, black and even blue finishes are commonly achieved in this way. For a wider choice of colours, most specifiers opt for an electrostatically sprayed polyester powder coating. This is a common finish for curtain walling, rainwater goods and cladding panels, where the powder coating is used to provide resistance to the acidity of rainwater. In this process, charged paint particles are blown onto the extrusion (which has undergone a twelve-stage pre-treatment process) and then stove, at between 200 and 210’C, for 10 to 12 minutes. This provides a high quality surface with excellent adhesion, accurate colouration and very even film thickness.
2.3 Fabricated for the fast track
One of the principal reasons for Aluminium’s enduring and growing popularity is its compatibility with today’s fast track construction techniques and just-in-time ordering. Nowhere is this seen more clearly than in curtain walling, where the accuracy of factory-finished sections allows rapid erection on site and, in him, allows internal finishing to proceed more quickly. The end result is earlier building occupancy and greater profit margins for the ultimate customer. Aluminium shop fronts, window systems and door assemblies offer comparable on-site benefits, which are now being enhanced by fabricators’ computer-controlled machining rigs which can drill, miter, grind and countersink to exact tolerances enabling the easiest possible installation of ironmongery, glazing beads and other secondary components.
2.4 Guaranteed performance through quality control
Although basic material costs will always be important to specifiers, they should be balanced against the cost of fabrication and subsequent service performance. This is an area where Aluminium, being ideally suited to highly automate manufacturing procedures to exact tolerances, offers many benefits. Aluminium door extrusions, for instance, are subjected to a rigorous quality regime, from hardness testing of the raw extrusion to conical bends, sawing, scratching, gouging, hammering and weight drops to guarantee coating performance. It is this combination of quality control, excellent cost in use and systems technology that has helped develop new markets for Aluminium roof companies in the health, education, leisure and transport sectors where changes in the funding of building procurement, such as PFI and fund-holding schools has changed the emphasis from lowest capital cost to lowest cost in use. Specifiers are increasingly looking for effective systems solutions by involving system suppliers early in the design process to ensure the most elegantly engineered solution at the lowest cost.
2.5 Aluminum recyclable at end of building’s life
The ability to recycle aluminum building products is also becoming more important as more building owners decide to deconstruct rather than demolish older buildings. Instead of simply going in with a wrecking ball, owners are now much more deliberate about how they take down a building in order to extract as much recyclable material as possible. By doing so, they not only retain the scrap value of a material such as aluminum but also eliminate the environmental impact and cost of dumping it in a landfill.
Aluminum recycling also reduces energy consumption. To produce aluminum from recycled material, for example, requires only 5% of the energy required to produce aluminum from bauxite. In addition, every ton of recycled aluminum saves four tons of bauxite.
|
|
|
The Best Window Curtains, According to Interior Designers |
Posted by: nsj5521sw - 08-24-2021, 03:14 AM - Forum: Welcomes and Introductions
- No Replies
|
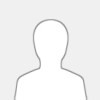 |
You may not appreciate the importance of window dressings — which, in addition to looks, provide privacy and block light — until you move into a place with naked windows. Luckily, adding curtains is one of the easier — and less expensive — projects you can undertake to transform a room. To help you dress your windows with the least amount of headache, we turned to 10 interior designers for their favorite curtains, lots of which are surprisingly quite budget friendly. (If you’re shopping for curtains, you’re likely looking at rods, and this list has a bunch of expert-recommended options to choose from.)
Before we get to the blackout curtain— which include a range of ready-made styles in different opacities, colors, and patterns, as well as a couple of custom options — some quick guidelines for how to size the drapery you choose for your space. When it comes to measuring your windows, Megan Hersch, the owner of Studio MG Interiors and online interior-design service RoomLift, says you should measure 12 to 24 inches beyond the window on either side to determine how wide each curtain panel should be, so that you have some gather. In determining the length of your curtain, Hersch says it depends on how formal you want them to look — and how much cleaning you want to do. “I typically measure the drapery so that it just ‘kisses’ the floor,” she says. “This way, nothing is dragging and trapping dirt, but you are sure they don’t look too short.” For a more formal look, she suggests adding an extra 1.5 inches so the drape just “breaks” on the floor. The most dramatic look is to have the panels “puddle” on the floor, which means adding anywhere from 8 to 12 inches to the length of the curtain (the type of fabric, whether stiff like taffeta or soft like velvet, will also determine how naturally it gathers on the floor).
A sheer curtain is a great choice if you want a little bit of everything from your window treatments — privacy, light, and looks — without having to commit too heavily to any one of those needs. As Megan Huffman, a designer with the online interior-design service Modsy, puts it, sheer curtains “provide the ability to allow natural light into a space and help brighten up dark rooms while still allowing privacy,” adding that, “there’s nothing I love more than a crisp, white, sheer curtain.” She recommends this pair from West Elm, which features a subtle crosshatch pattern that adds a bit of texture. If you like the look of sheer curtains during the day but also want to keep light pollution from coming through at night, Huffman says these can easily be hung on a double curtain rod with a pair of thicker, more opaque blackout curtains.
Interior designer Nicole Fuller also loves the sheer look, noting that sheer curtains made with linen in particular allow for that “gauzy feel” as the sun shines through the fabric. Linen drapes in general, she adds, “are incredibly timeless.” Fuller told us her favorite linen curtains come from Restoration Hardware’s Perennials line. But Hersch did us one better: She pointed us to these less expensive Perennials dupes from Restoration Hardware’s teen line, which she says will often have “very affordable,” premade drapery panels. (Hersch says Pottery Barn’s teen line is another source of affordable but expensive-looking curtains.) The curtains shown are made from a linen-cotton blend and cost about a third of their counterparts from the Perennials line.
For something more opaque (and still less expensive than Restoration’s regular line), try this linen-cotton style, which has the same look as the curtains above, but with a blackout lining that offers full privacy and light control.
For basic, neutral curtain panels that are less than $20 apiece, Dani Mulhearn, a senior designer at online interior-design service Havenly, recommends these curtains she uses in her own home. She says they “add a bit of softness and dress up standard window treatments in a space.” While Mulhearn cautions they are not true blackout curtains — just “room-darkening” — they still work great for privacy. She likes the pearl color, calling it “a great neutral that goes with any cool or warm color schemes.” (If pearl’s not your thing, there are 16 other colors available.) Mulhearn also appreciates the fact that they have grommets, which are “a super-functional” detail that negates the need to buy curtain rings, and makes opening and closing them easy.
For faux linen blackout curtain, these are Mulhearn’s go-tos. She likes that they’re affordable, come in a variety of neutral colors, and are available in various lengths, from 63 inches to 108 inches. They also have a grommet top, which means you don’t need to get additional curtain rings to hang them from a rod.
If you’re looking for solid curtains with more drama, Huffman recommends using velvet ones — specifically, these light-blocking matte velvet curtains from Anthropologie that come in an array of jewel tones. The fabric’s piled texture and more substantial feel add heft to a space, not to mention color, making them a functional and stylish choice, she says. Each panel is made to order, which accounts for the price tag (velvet is also generally a more expensive material because of the way it is made).
If you want to stick to neutral colors but crave a bit more personality, consider these cotton-canvas patterned curtains from West Elm that also come recommended by Mulhearn. She told us they “have a little sheen to them,” with a “subtle enough pattern to give your windows that ‘dressed up’ feel without being super flashy,” noting that they also block most light and help insulate windows.
This curtain is Decorilla design expert Devin Shaffer’s choice. He says the panel’s raised pattern, which is made with metallic threads and kind of looks like tree bark, reminds him of the outdoors. While noticeable, the neutral-colored pattern is subtle enough that it won’t overwhelm a room, he adds.
Pinstripes add a “casual and coastal feel” to otherwise straightforward drapery, according to Modsy designer Katherine Tlapa, who says these curtains “add height and brighten a space with their simple vertical striping” while still being “clean and classic.” Interior designer Bachman Brown agrees that patterned curtains like this can do wonders for a room. “A large-scale pattern is one of the best drapery treatments you can do for a window,” he says. “It sets the tone for the room, and nothing draws your eye more than a grand-scaled fabric.”
Decorist designer Katy Byrne likes experimenting with boldly patterned curtains because “unlike paint, drapes can add a lot of color to a room while being much easier to swap out with changing trends.” She recommends these ikat panels that she says “would add a fun highlight to a playroom or kids’ space.”
If you want to splurge on custom drapery, interior designer Betsy Burnham, who also prefers “clean, unfussy treatments,” recommends the Shade Store. She likes its solid linens, opting for those with “inverted pleat drapery,” like this one, “for its tailored feel.” If you don’t like the linen fabric, Burnham says these curtains can be customized with a range of other materials.
For many of us, lockdown means looking: gazing at the views outside our windows, the traffic and the trees, with thoughts of post-pandemic life dancing through our heads. We ought to give some thoughts to those windows too, whether they are panes, sheets, or entire walls of glass. As my mother once said regarding domestic architecture, “A house without a porch is like a man without a country.” To my mind, a similar rule applies to windows—without blinds or shades or shutters or curtains, many windows are just featureless voids. I’m not the only one who thinks this: Scores of AD100 interior designers from Manhattan’s Jeffrey Bilhuber to Milan’s Studio Peregalli consider a window undressed to be a window unfinished.
Historically speaking, windows have typically had some sort of covering, to regulate sunlight, protect interiors from inclement weather, and to provide privacy for you and yours. In the ancient world, they were simple fabric panels that could be folded back or lifted up and then held in place, in one manner or another, for the duration.
Time-travel thousands of years later to the minimalist Bauhaus era, where rejection was the rule yet curtains were still considered essential decorative components. Le Corbusier specified curtains and shades for his projects, and Dutch architect Gerrit Rietveld’s houses possessed their own complement of window treatments, from full-length to café short. Alas, Rietveld’s marvelous little 1924 house for and in collaboration with the young widow Truus Schröder in Utrecht, his very first architectural commission and now a museum, possesses no shades or sheer window treatments anymore—a curatorial mistake, to my mind, because that decision deifies the architecture while ignoring the domesticity of Schröder and her children for which it was built. (Rietveld, though married, would become his client’s lover and live there too, returning to his family only at night.)
Luxurious floor-to-ceiling curtains outfitted the Czech Republic’s Villa Tugendhat, one of modernism’s most celebrated residences, a glass-walled villa designed by architect Ludwig Mies van der Rohe and decorated with designer Lilly Reich in the 1920s. Some of them were made of silver-gray shantung silk, while others were fashioned of black or white velvet, the uncomplicated lengths and plain colors framing a green landscape. The Frenchman Jean-Michel Frank may have been a pioneering reductivist, but even he understood the power of a pretty window. After all, he was the man who put dramatically ruffled curtains into Elsa Schiaparelli’s Place Vendôme fashion salon.
Concurrently, while the tastemakers of the 1920s and 1930s were paring back but not abandoning window treatments entirely, their traditionalist peers held faithful to layered looks that began in the 17th century, grew more complicated in the 18th century, and became suffocatingly elaborate in the 19th century. Sumptuous window dressings reached their 20th-century apotheosis in the work of the British tastemaker John Fowler, a cofounder of London’s Sibyl Colefax & John Fowler, as well as such disciples as America’s Mario Buatta.
Fowler’s curtains for aristocratic country houses and the apartments of international grandees remain a standard in the craft—lined, interlined, fringed, looped, swagged, tasseled, pinked, and otherwise elaborated in a manner that brings to mind the intricacies of haute couture as well as 18th-century France, one of the decorator’s passions. Among my favorites of the genre, though far simpler than Fowler’s swoony extravagances—such as the madly romantic cascades of silk taffeta in Evangeline and David Bruce’s famous London drawing room—are the ones that his colleague Tom Parr created in the 1980s for the Manhattan multipurpose living room of Grace, Countess of Dudley, and her longtime companion, Robert Silvers, editor in chief of the New York Review of Books. Great lengths of rose-splashed white chintz sluiced from ceiling to floor in the vast primary space—the 50-odd-foot sweep was divided into several areas for living and dining—emphasizing the height of the ceiling and parted to reveal views of Park Avenue.
Take note of the word parted. Beyond the myriad practical aspects, window treatments, from simple to elaborate, offer us moments of communion, as human hands—whether your own or those of Lady Dudley’s housekeeper—adjust them at will. There are aural pleasures too, from the clicking of curtain rings to the swish of fabric to the creak of shutters to the whir of roller blinds. Literally, the beauty of geometric blackout curtain is an open-and-shut case.
|
|
|
The Jacquard Loom: A Driver of the Industrial |
Posted by: nsj5521sw - 08-24-2021, 03:11 AM - Forum: Welcomes and Introductions
- No Replies
|
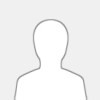 |
THE INSTITUTEThis month The Institute is focusing on how technology is transforming the garment industry. The electronic Jacquard loom was the first loom that automatically created complex textile patterns. This led to the mass production of cloth with intricate designs.
Joseph Marie Charles Jacquard of France was born into a family of weavers in 1752. He received no formal schooling but tinkered with ways to improve the mechanical textile looms of the day.
At that time, two people were needed on each loom. A skilled weaver and an assistant, or draw boy, chose by hand which warps (the lengthwise threads held under tension on the loom) to pull up so the weft (the thread inserted at right angles) could be pulled through the warps to create a pattern.
At an industrial exhibition in Paris in 1801, Jacquard demonstrated something truly remarkable: a loom in which a series of cards with punched holes (one card for each row of the design) automatically created complex textile patterns. The draw boy was no longer needed. Patterns that had been painstaking to produce and prone to error could now be mass-produced quickly and flawlessly, once programmed and punched on the cards.
The government of France soon nationalized the loom (or considered it government property) and compensated Jacquard with a pension to support him while he continued to innovate. He also was paid a royalty for each machine sold. It took Jacquard several more years to perfect the device and make it commercially successful.
The social and psychological impact of a machine that could replace human labor was immense.
HOW IT WORKED
Jacquard did not invent a whole new loom but a head that attaches to the loom and allows the weaving machine to create intricate patterns. Thus, any loom that uses the attachment is called a Jacquard loom.
The state-of the art loom at that time was one in which the harnesses holding the threads were raised or lowered by foot pedals on a treadle, leaving the weaver free to operate the machine with his hands. The Jacquard loom, in contrast, was controlled by a chain of punch cards laced together in a sequence. Multiple rows of holes were punched on each card, with one complete card corresponding to one row of the design. Chains of cards allowed sequences of any length to be constructed, not limited by the cards’ size.
Each hole position in the card corresponded to a hook, which could either be raised or lowered depending on whether the hole was punched. The hook raised or lowered the harness that carried and guided the thread. The sequence of raised and lowered threads created the pattern. A hook could be attached to a number of threads to create a continuous, intricate design.Already in the late 18th century, workers throughout Europe were upset with the increasing mechanization of their trades. Jacquard’s loom was fiercely opposed by silk-weavers in Paris who rightly saw it would put many of them out of work. In England, where an anti-industry workers movement was already well developed, news of the Jacquard loom fostered momentum for the Luddite movement, whose textile workers protested the new technology. Although the French looms did not arrive in England until the early 1820s, news of their existence helped intensify violent protests. People smashed the machines and killed textile mill owners; the authorities violently suppressed the protests. To this day, people who resist new technology are called Luddites.
But the high speed electronic Jacquard loom was too good to be ignored. Ultimately, it became standard throughout the industrializing world for weaving luxury fabrics, replaced by the dobby loom in the 1840s. In a dobby, a chain of bars with pegs, rather than foot pedals, is used to select and move the harness. Even then, parts of Jacquard’s control system could be adapted to the dobby loom.Perhaps what is most interesting about the Jacquard loom was its afterlife. When computer pioneer Charles Babbage, a British mathematician, envisioned an “analytical engine” in 1837 that would essentially become the first general-purpose computer, he decided that the computer’s input would be stored on punch cards, modeled after Jacquard’s system. Although Babbage never built his engine, he and his work were well known to the mathematics community and eventually influenced the field that came to be computer science.THE INSTITUTEThis month The Institute is focusing on how technology is transforming the garment industry. The Jacquard Loom was the first loom that automatically created complex textile patterns. This led to the mass production of cloth with intricate designs.
Joseph Marie Charles Jacquard of France was born into a family of weavers in 1752. He received no formal schooling but tinkered with ways to improve the mechanical textile looms of the day.
At that time, two people were needed on each loom. A skilled weaver and an assistant, or draw boy, chose by hand which warps (the lengthwise threads held under tension on the loom) to pull up so the weft (the thread inserted at right angles) could be pulled through the warps to create a pattern.
At an industrial exhibition in Paris in 1801, Jacquard demonstrated something truly remarkable: a loom in which a series of cards with punched holes (one card for each row of the design) automatically created complex textile patterns. The draw boy was no longer needed. Patterns that had been painstaking to produce and prone to error could now be mass-produced quickly and flawlessly, once programmed and punched on the cards.
The government of France soon nationalized the loom (or considered it government property) and compensated Jacquard with a pension to support him while he continued to innovate. He also was paid a royalty for each machine sold. It took Jacquard several more years to perfect the device and make it commercially successful.
The social and psychological impact of a machine that could replace human labor was immense.
HOW IT WORKED
Jacquard did not invent a whole new loom but a head that attaches to the loom and allows the weaving machine to create intricate patterns. Thus, any loom that uses the attachment is called a Jacquard loom.
The state-of the art loom at that time was one in which the harnesses holding the threads were raised or lowered by foot pedals on a treadle, leaving the weaver free to operate the machine with his hands. The Jacquard loom, in contrast, was controlled by a chain of punch cards laced together in a sequence. Multiple rows of holes were punched on each card, with one complete card corresponding to one row of the design. Chains of cards allowed sequences of any length to be constructed, not limited by the cards’ size.
Each hole position in the card corresponded to a hook, which could either be raised or lowered depending on whether the hole was punched. The hook raised or lowered the harness that carried and guided the thread. The sequence of raised and lowered threads created the pattern. A hook could be attached to a number of threads to create a continuous, intricate design.
Herman Hollerith\u2019s punched-card computer, invented in the early 1880s, was inspired by the Jacquard loomHerman Hollerith’s punched-card computer, invented in the early 1880s, was inspired by the Jacquard loom PHOTO: HULTON ARCHIVE/GETTY IMAGES
FIERCE OPPOSITION
Already in the late 18th century, workers throughout Europe were upset with the increasing mechanization of their trades. Jacquard’s loom was fiercely opposed by silk-weavers in Paris who rightly saw it would put many of them out of work. In England, where an anti-industry workers movement was already well developed, news of the high speed electronic Jacquard loom for weaving machine fostered momentum for the Luddite movement, whose textile workers protested the new technology. Although the French looms did not arrive in England until the early 1820s, news of their existence helped intensify violent protests. People smashed the machines and killed textile mill owners; the authorities violently suppressed the protests. To this day, people who resist new technology are called Luddites.
But the Jacquard loom was too good to be ignored. Ultimately, it became standard throughout the industrializing world for weaving luxury fabrics, replaced by the dobby loom in the 1840s. In a dobby, a chain of bars with pegs, rather than foot pedals, is used to select and move the harness. Even then, parts of Jacquard’s control system could be adapted to the dobby loom.
A LONG LEGACY
Perhaps what is most interesting about the Jacquard loom was its afterlife. When computer pioneer Charles Babbage, a British mathematician, envisioned an “analytical engine” in 1837 that would essentially become the first general-purpose computer, he decided that the computer’s input would be stored on punch cards, modeled after Jacquard’s system. Although Babbage never built his engine, he and his work were well known to the mathematics community and eventually influenced the field that came to be computer science.
In the mid-1880s, the U.S. Census Bureau began to experiment with ways to automate the way it was assessing the population of the United States and processing the answers to the questions survey takers asked each household. The data from the 1880 census was overwhelming; it took eight years to compile and process. Engineer Herman Hollerith, who was on the bureau’s technical staff, felt he could improve the process. He got busy and, in 1884, filed a patent for an electromechanical device that rapidly read information encoded by punching holes on a paper tape or a set of cards. In 1889 Hollerith’s newly formed Tabulating Machine Co. was chosen to process the 1890 census. The company was decidedly successful; data from the 1890 census was compiled in only one year. The 1890 population of the United States was put at 62,947,714 people.
Apparently, Hollerith based his concept on the electronic Jacquard loom machine. Historians disagree, however, as to whether he also was influenced by Babbage’s work.
The Tabulating Machine Co. eventually became IBM. (Some IEEE members undoubtedly remember using IBM punch cards into the 1970s.)
Thus, the computer industry—which became a field of cutting-edge innovation—was affected by at least two streams of influence from the Jacquard loom. It is only fitting and fair that computing is now generating innovation in the textile industry with such creations as wearables, 3-D printed clothing, and digital industrial knitting machines. Before even the telegraph, innovation in textile technology was one of the “engines” (along with steam power and iron production) that drove the Industrial Revolution.
When Joseph-Marie Jacquard, a French weaver and merchant, patented his invention in 1804, he revolutionised how patterned cloth could be woven. His Jacquard machine, which built on earlier developments by inventor Jacques de Vaucanson, made it possible for complex and detailed patterns to be manufactured by unskilled workers in a fraction of the time it took a master weaver and his assistant working manually.
The spread of Jacquard's invention caused the cost of fashionable, highly sought-after patterned cloth to plummet. It could now be mass produced, becoming affordable to a wide market of consumers, not only the wealthiest in society.
To weave fabric on a loom, a thread (called the weft) is passed over and under a set of threads (called the warp). It is this interlacing of threads at right angles to each other that forms cloth. The particular order in which the weft passes over and under the warp threads determines the pattern that is woven into the fabric.
Before the Jacquard system, a weaver's assistant (known as a draw boy) had to sit atop a loom and manually raise and lower its warp threads to create patterned cloth. This was a slow and laborious process.
The key to the success of Jacquard's invention was its use of interchangeable cards, upon which small holes were punched, which held instructions for weaving a pattern. This innovation effectively took over the time-consuming job of the draw boy.
When fed into the Jacquard mechanism (fitted to the top of the loom), the cards controlled which warp threads should be raised to allow the weft thread to pass under them. With these punch cards, Jacquard looms could quickly reproduce any pattern a designer could think up, and replicate it again and again.
First, a designer paints their pattern onto squared paper. A card maker then translates the pattern row by row onto punch cards. For each square on the paper that has not been painted in, the card maker punches a hole in the card. For each painted square, no hole is punched.
The cards, each with their own combination of punched holes corresponding to the part of the pattern they represent, are then laced together, ready to be fed one by one through the Jacquard mechanism fitted at the top of the loom. When a card is pushed towards a matrix of pins in the Jacquard mechanism, the pins pass through the punched holes, and hooks are activated to raise their warp threads. Where there are no holes the pins press against the card, stopping the corresponding hooks from raising their threads.
A shuttle then travels across the loom, carrying the weft thread under the warp threads that have been raised and over those that have not. This repeating process causes the loom to produce the patterned cloth that the punch cards have instructed it to create.Manchester engineering companies also began manufacturing Jacquard machinery to supply to the region's textile mills. Devoge and Co. was established in 1834 and continued producing Jacquard mechanisms until the 1980s.
Jacquard's invention transformed patterned cloth production, but it also represented a revolution in human-machine interaction in its use of binary code—either punched hole or no punched hole—to instruct a machine (the loom) to carry out an automated process (weaving).
The Jacquard needle loom machine is often considered a predecessor to modern computing because its interchangeable punch cards inspired the design of early computers.
With his Analytical Engine, Babbage envisaged a machine that could receive instructions from punch cards to carry out mathematical calculations. His idea was that the punch cards would feed numbers, and instructions about what to do with those numbers, into the machine.Ada Lovelace took Babbage's idea a step further, proposing that the numbers the engine manipulated could represent not just quantities, but any data. She saw the potential for computers to be used beyond mathematical calculation and proposed the idea of what we now know as computer programming.
Unfortunately, the Analytical Engine was never completed, and it was 100 years before Babbage's and Lovelace's predictions were realised.
However, their work, and the inspiration provided by Jacquard's revolutionary weaving machine, came to underpin the technological development of the modern computer.
|
|
|
How Toner Cartridges Work? |
Posted by: nsj5521sw - 08-24-2021, 03:08 AM - Forum: Welcomes and Introductions
- No Replies
|
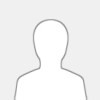 |
What do printers do? Well, they make paper copies of what's on your screen. But contrary to what you may think, modern LaserJet toner cartridges don't print using ink. So then how do LaserJet toner cartridges work?
Here's everything you need to know about LaserJet printers, toner cartridges, and which ones are the best to buy.
One of the interesting aspects of laser printers and copiers is the toner.
Rather than the printer applying ink, the paper actually “grabs” the toner.
The toner itself is not ink, but rather an electrically-charged powder made of plastic and pigment.
A LaserJet printer consists of several components. Let's start with the photoreceptor drum assembly, a revolving cylinder made of photoconductive material.
Printers beam a laser beam across the surface of this revolving drum. The drum has a positive charge, but the laser discharges the points it comes in contact with, leaving the resulting image with a negative charge (or vice versa). In this way, the laser draws the document or image you wish to print.The printer then coats the drum not with ink, but with powder. This powder sticks to the electrostatic image the laser has drawn. The powder consists of two ingredients: pigment and plastic. Pigment provides the color, while the plastic is there to adhere the pigment to paper. This mixture, known as toner, is spun in a component called the hopper.
The printer then feeds paper under the drum, first giving the paper a stronger negative charge than that of the electrostatic image. This enables the paper to pull the powder away from the drum.
The paper then passes through a pair of heated rollers referred to as the fuser. As it does, the plastic particles melt and blend with the paper. This process allows the powder to adhere to more types of paper than conventional ink, as long as they can handle the fuser's heat.
This is also why paper is hot when it first comes out of a laser printer.
Toner cartridges may largely do the same task, but they're not all the same. When planned obsolescence kicks in and the time comes to invest in a new one, you want to make sure you're buying a quality product.
To save money and walk away with the kind of experience you want, here are some questions to keep in mind while shopping:
Does the cartridge work in your printer? If you're buying a new cartridge, this is as simple as matching brand and model numbers. But if you're looking at third-party options, you may have to do more research. Even if a cartridge theoretically works with your printer, differences in toner powder or other components can result in damage. Triple-check reviews and whatever other information you can get your hands on.
How much does it cost to print a page? Toner cartridges can be expensive, sometimes more expensive than the cost of the printer itself. When comparing price, look at the cost per page, rather than the total cost of the cartridge. This gives you a more accurate read on whether one cartridge is truly more affordable than another.
How many pages can you print? Toner cartridges may be expensive, but you're getting a lot of pages for your buck. The average compatible toner cartridge for kyocera lasts over 1,500 pages. Some print more, and some print less. How many pages is an acceptable number to you?
Can you recycle this cartridge? Some LaserJet toner cartridge manufacturers provide their own recycling programs. Various department stores also perform this service. See which options are available in your area, and which brands are supported.
Manufacturers test and design new cartridges specifically for your machine. Refilling a cartridge adds variability to the process. Is it guaranteed to break your printer? Not at all. But you are exposing yourself to that risk. Though if you're used to buying used products, you may already be comfortable with such a gamble.
Unfortunately, you may not even have the option. Like inkjet printers, some LaserJet toner cartridges now contain chips that communicate when a cartridge is empty. You can refill the product, but without the ability to reset the chip, the printer will still think there's nothing there.
You may also notice a difference in print quality. A refilled cartridge might not give you the kind of crisp prints you expect. You may also find that you're not getting as many prints as you were before.
How does toner work?
The two ingredients of toner, plastic and pigment, each have a simple role in the printing process.
The pigment provides the color, while the plastic allows the pigment to stick to the paper when the plastic is heated and melts.
The melting process gives laser toner an advantage over ink, in that it binds firmly to the paper fibers, resisting smudges and bleeding.
This also provides an even, vivid tone that helps text appear sharp on paper.
Another advantage of toner is the cost. Offices usually choose laser printers because the cost of replacing the toner cartridges is less than inkjet printer cartridges, and laser printers tend to cost only slightly more than inkjet printers.
Anatomy of a toner cartridge
The design of a compatible toner cartridge for ricoh varies with different models and manufacturers, but the following components are commonly found in most toner cartridges.
Toner hopper:The small container which houses the toner
Seal:A removable strip that prevents toner from spilling before installation
Doctor blade: Helps control the precise amount of toner that is distributed to the developer
Developer:Transfers toner to the OPC drum
Waste bin:Collects residual toner wiped from the OPC drum
Wiper blade:Wipes away residual toner applied to the page
Primary charge roller (PCR):Applies a uniform negative to the OPC drum prior to laser-writing. It also erases the laser image
Organic photo-conductor (OPC) drum:holds an electrostatic image and transfers toner onto the paper
Drum shutter:protects the drum from light when outside the machine and retracts the drum into the printer
How does the cartridge work?
In most cartridges, the toner hopper, developer and drum assembly are all part of the replaceable cartridge unit.
When an image or text is being printed on paper, the printer gathers toner from the hopper with the developer.
The developer, composed of negatively-charged magnetic beads attached to a metal roller, moves through the hopper gathering toner.
The developer collects positively-charged toner particles and brushes them past the drum assembly.
The electrostatic image on the drum has a stronger negative charge than the beads on the developer, so the toner is pulled from the developer onto the drum.
Next, the drum moves over the paper. The paper has an even stronger negative charge than the drum, and pulls the toner particles off of the drum in the shape of the electrostatic image.
Next, the paper is discharged by the detac corona wire.
At this point, gravity is the only thing keeping the toner in place. In order to affix the toner, the paper needs to pass through the fuser rollers, which are heated by internal quartz tube lamps.
The heat melts the plastic in the toner particles, causing the toner to be absorbed into the paper fibers.
Although the melted plastic sticks to the paper, it does not adhere to the heated fuser rollers.
This is possible because the rollers are coated with Teflon, the same material that helps food slide out of non-stick frying pans.
Color vs. Monochrome Printing
Color toner works essentially the same way as monochrome toner, except the process is repeated for each of the toner colors.
The standard toner colors are cyan (blue), magenta (red), yellow and black. The black is needed because the three primary colors (red, yellow and blue) can be combined to form any color except black.
The reason for this is black is not technically a color, but the complete absence of color.
These four toner colors, when combined at varying levels of saturation and lightness, can produce millions of different shades and hues.
This quick guided tour of toner cartridges should help provide a basic understanding of how they work.
The current technology of compatible toner cartridge for canon has allowed laser printers to dominate the office printing market.
In the years to come, new designs of toner cartridges promise to provide more efficient and cost-effective solutions for office and home printing.
Eco-Friendly Toner Cartridges are range of remanufactured compatible toner cartridge for konica minolta selectively tested and produces locally. Majority of the used empties are collected locally to reduces local landfill. Singapore is a small city every inch counts, therefore every single cartridge we recycled helps.
"Check out OUR RANGE OF ECO-FRIENLDY CARTRIDGE"
More than just a business that wants to profit and make money, Green Cartridges Pte Ltd takes it corporate social responsibility seriously. We choose to actively take part in foresting environmental awareness by making printer owners realize the need to reuse and recycle cartridges to minimize waste pollution.
|
|
|
How Music and Instruments Began? |
Posted by: nsj5521sw - 08-24-2021, 03:05 AM - Forum: Welcomes and Introductions
- No Replies
|
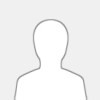 |
Music must first be defined and distinguished from speech, and from animal and bird cries. We discuss the stages of hominid anatomy that permit music to be perceived and created, with the likelihood of both Homo neanderthalensis and Homo sapiens both being capable. The earlier hominid ability to emit sounds of variable pitch with some meaning shows that music at its simplest level must have predated speech. The possibilities of anthropoid motor impulse suggest that rhythm may have preceded melody, though full control of rhythm may well not have come any earlier than the perception of music above. There are four evident purposes for music: dance, ritual, entertainment personal, and communal, and above all social cohesion, again on both personal and communal levels. We then proceed to how outdoor musical instrument began, with a brief survey of the surviving examples from the Mousterian period onward, including the possible Neanderthal evidence and the extent to which they showed “artistic” potential in other fields. We warn that our performance on replicas of surviving instruments may bear little or no resemblance to that of the original players. We continue with how later instruments, strings, and skin-drums began and developed into instruments we know in worldwide cultures today. The sound of music is then discussed, scales and intervals, and the lack of any consistency of consonant tonality around the world. This is followed by iconographic evidence of the instruments of later antiquity into the European Middle Ages, and finally, the history of public performance, again from the possibilities of early humanity into more modern times. This paper draws the ethnomusicological perspective on the entire development of music, instruments, and performance, from the times of H. neanderthalensis and H. sapiens into those of modern musical history, and it is written with the deliberate intention of informing readers who are without special education in music, and providing necessary information for inquiries into the origin of music by cognitive scientists.
But even those elementary questions are a step too far, because first we have to ask “What is music?” and this is a question that is almost impossible to answer. Your idea of music may be very different from mine, and our next-door neighbor’s will almost certainly be different again. Each of us can only answer for ourselves.
Mine is that it is “Sound that conveys emotion.”
We can probably most of us agree that it is sound; yes, silence is a part of that sound, but can there be any music without sound of some sort? For me, that sound has to do something—it cannot just be random noises meaning nothing. There must be some purpose to it, so I use the phrase “that conveys emotion.” What that emotion may be is largely irrelevant to the definition; there is an infinite range of possibilities. An obvious one is pleasure. But equally another could be fear or revulsion.
How do we distinguish that sound from speech, for speech can also convey emotion? It would seem that musical sound must have some sort of controlled variation of pitch, controlled because speech can also vary in pitch, especially when under overt emotion. So music should also have some element of rhythm, at least of pattern. But so has the recital of a sonnet, and this is why I said above that the question of “What is music?” is impossible to answer. Perhaps the answer is that each of us in our own way can say “Yes, this is music,” and “No, that is speech.”
Must the sound be organized? I have thought that it must be, and yet an unorganized series of sounds can create a sense of fear or of warning. Here, again, I must insert a personal explanation: I am what is called an ethno-organologist; my work is the study of musical tubular musical instrument (organology) and worldwide (hence the ethno-, as in ethnomusicology, the study of music worldwide). So to take just one example of an instrument, the ratchet or rattle, a blade, usually of wood, striking against the teeth of a cogwheel as the blade rotates round the handle that holds the cogwheel. This instrument is used by crowds at sporting matches of all sorts; it is used by farmers to scare the birds from the crops; it was and still is used by the Roman Catholic church in Holy Week when the bells “go to Rome to be blessed” (they do not of course actually go but they are silenced for that week); it was scored by Beethoven to represent musketry in his so-called Battle Symphony, a work more formally called Wellingtons Sieg oder die Schlacht bei Vittoria, Op.91, that was written originally for Maelzel’s giant musical box, the Panharmonicon. Beethoven also scored it out for live performance by orchestras and it is now often heard in our concert halls “with cannon and mortar effects” to attract people to popular concerts. And it was also, during the Second World War, used in Britain by Air-Raid Precaution wardens to warn of a gas attack, thus producing an emotion of fear. If it was scored by Beethoven, it must be regarded as a musical instrument, and there are many other noise-makers that, like it, which must be regarded as musical instruments.
And so, to return to our definition of music, organization may be regarded as desirable for musical sound, but that it cannot be deemed essential, and thus my definition remains “Sound that conveys emotion.”
But then another question arises: is music only ours? We can, I think, now agree that two elements of music are melody, i.e., variation of pitch, plus rhythmic impulse. But almost all animals can produce sounds that vary in pitch, and every animal has a heart beat. Can we regard bird song as music? It certainly conveys musical pleasure for us, it is copied musically (Beethoven again, in his Pastoral Symphony, no.6, op. 68, and in many works by other composers), and it conveys distinct signals for that bird and for other birds and, as a warning, for other animals also. Animal cries also convey signals, and both birds and animals have been observed moving apparently rhythmically. But here, we, as musicologists and ethnomusicologists alike, are generally agreed to ignore bird song, animal cries, and rhythmic movement as music even if, later, we may regard it as important when we are discussing origins below. We ignore these sounds, partly because they seem only to be signals, for example alarms etc, or “this is my territory,” and partly, although they are frequently parts of a mating display, this does not seem to impinge on society as a whole, a feature that, as we shall see, can be of prime importance in human music. Perhaps, too, we should admit to a prejudice: that we are human and animals are not…
So now, we can turn to the questions of vocalization versus motor impulse: which came first, singing or percussive rhythms? At least we can have no doubt whatsoever that for melody, singing must long have preceded instrumental performance, but did physical movement have the accompaniment of hand- or body-clapping and perhaps its amplification with clappers of sticks or stones, and which of them came first?
Here, we turn first to the study of the potentials of the human body. There is a large literature on this, but it has recently been summarized by Iain Morley in his The Prehistory of Music (Morley, 2013). So far as vocalization is concerned, at what point in our evolution was the vocal tract able to control the production of a range of musical pitch? For although my initial definition of music did not include the question of pitch, nor of rhythm, once we begin to discuss and amplify our ideas of music, one or other of these, does seem to be an essential—a single sound with no variation of pitch nor with any variation in time can hardly be described as musical.
All animals have the ability to produce sounds, and most of these sounds have meanings, at least to their ears. Surely, this is true also of the earliest hominims. If a mother emits sounds to soothe a baby, and if such sound inflects somewhat in pitch, however vaguely, is this song? An ethnomusicologist, those who study the music of exotic peoples, would probably say “yes,” while trying to analyze and record the pitches concerned. A biologist would also regard mother–infant vocalizations as prototypical of music (Fitch, 2006). There are peoples (or have been before the ever-contaminating influence of the electronic profusion of musical reproduction) whose music has consisted only of two or three pitches, and those pitches not always consistent, and these have always been accepted as music by ethnomusicologists. So we have to admit that vocal music of some sort may have existed from the earliest traces of humanity, long before the proper anatomical and physiological developments enabled the use of both speech and what we might call “music proper,” with control and appreciation of pitch.
In this context, it is clear also that “music” in this earliest form must surely have preceded speech. The ability to produce something melodic, a murmuration of sound, something between humming and crooning to a baby, must have long preceded the ability to form the consonants and vowels that are the essential constituents of speech. A meaning, yes: “Mama looks after you, darling,” “Oy, look out!” and other non-verbal signals convey meaning, but they are not speech.
The possibilities of motor impulse are also complex. Here, again, we need to look at the animal kingdom. Both animals and birds have been observed making movements that, if they were humans, would certainly be described as dance, especially for courtship, but also, with the higher apes in groups. Accompaniment for the latter can include foot-slapping, making more sound than is necessary just for locomotion, and also body-slapping (Williams, 1967). Can we regard such sounds as music? If they were humans, yes without doubt. So how far back in the evolutionary tree can we suggest that motor impulse and its sonorous accompaniment might go? I have already postulated in my Origins and Development of xylophone musical instrument (Montagu, 2007, p. 1) that this could go back as far as the earliest flint tools, that striking two stones together as a rhythmic accompaniment to movement might have produced the first flakes that were used as tools, or alternatively that interaction between two or more flint-knappers may have led to rhythms and counter-rhythms, such as we still hear between smiths and mortar-and-pestle millers of grains and coffee beans. This, of course, was kite-flying rather than a wholly serious suggestion, but the possibilities remain. At what stage did a hominim realize that it could make more sound, or could alleviate painful palms, by striking two sticks or stones together, rather than by simple clapping? Again we turn to Morley and to the capability of the physiological and neurological expression of rhythm.
The physiological must be presumed from the above animal observations. The neurological would again, at its simplest, seem to be pre-human. There is plenty of evidence for gorillas drumming their chests and for chimpanzees to move rhythmically in groups. However, apes’ capacity for keeping steady rhythm is very limited (Geissmann, 2000), suggesting that it constitutes a later evolutionary development in hominins. Perceptions of more detailed appreciation of rhythm, particularly of rhythmic variation, can only be hypothesized by studies of modern humans, especially of course of infantile behavior and perception.
From all this, it would seem that motor impulse, leading to rhythmic music and to dance could be at least as early as the simplest vocal inflection of sounds. Indeed, it could be earlier. We said above that animals have hearts, and certainly, all anthropoids have a heartbeat slow enough, and perceptible enough, to form some basis for rhythmic movement at a reasonable speed. Could this have been a basis for rhythmic movement such as we have just mentioned? This can only be a hypothesis, for there is no way to check it, but it does seem to me that almost all creatures seem to have an innate tendency to move together in the same rhythm when moving in groups, and this without any audible signal, so that some form of rhythmic movement may have preceded vocalization.
But Why Does Music Develop from Such Beginnings? What is the Purpose of Music?
There are four obvious purposes: dance, personal or communal entertainment, communication, and ritual.
Seemingly more important than these fairly obvious reasons for why music developed is one for why music began in the first place. This is something that Steven Mithen mentions again and again in his book, The Singing Neanderthals (Mithen, 2005): that music is not only cohesive on society but almost adhesive. Music leads to bonding, bonding between mother and child, bonding between groups who are working together or who are together for any other purpose. Work songs are a cohesive element in most pre-industrial societies, for they mean that everyone of the group moves together and thus increases the force of their work. Even today “Music while you Work” has a strong element of keeping workers happy when doing repetitive and otherwise boring work. Dancing or singing together before a hunt or warfare binds the participants into a cohesive group, and we all know how walking or marching in step helps to keep one going. It is even suggested that it was music, in causing such bonding, that created not only the family but society itself, bringing individuals together who might otherwise have led solitary lives, scattered at random over the landscape.
Thus, it may be that the whole purpose of music was cohesion, cohesion between parent and child, cohesion between father and mother, cohesion between one family and the next, and thus the creation of the whole organization of society.
Much of this above can only be theoretical—we know of much of its existence in our own time but we have no way of estimating its antiquity other than by the often-derided “evidence” of the anthropological records of isolated, pre-literate peoples. So let us now turn to the hard evidence of early musical practice, that of the surviving musical instruments.1
This can only be comparatively late in time, for it would seem to be obvious that sound makers of soft vegetal origin should have preceded those of harder materials that are more difficult to work, whereas it is only the hard materials that can survive through the millennia. Surely natural materials such as grasses, reeds, and wood preceded bone? That this is so is strongly supported by the advanced state of many early bone pipes—the makers clearly knew exactly what they were doing in making musical instruments, with years or generations of experiment behind them on the softer materials. For example, some end-blown and notch-blown flutes, the earliest undoubted ones that we have, from Geissenklösterle and Hohle Fels in Swabia, Germany, made from swan, vulture wing (radius) bones, and ivory in the earliest Aurignacian period (between 43,000 and 39,000 years BP), have their fingerholes recessed by thinning an area around the hole to ensure an airtight seal when the finger closes them. This can only be the result of long experience of flute making.
So how did tembos musical instrument begin? First a warning: with archeological material, we have what has been found; we do not have what has not been found. A site can be found and excavated, but if another site has not been found, then it will not have been excavated. Thus, absence of material does not mean that it did not exist, only that it has not been found yet. Geography is relevant too. Archeology has been a much older science in Europe than elsewhere, so that most of our evidence is European, whereas in Africa, where all species of Homo seem to have originated, site archeology is in its infancy. Also, we have much evidence of bone pipes simply because a piece of bone with a number of holes along its length is fairly obviously a probable musical instrument, whereas how can we tell whether some bone tubes without fingerholes might have been held together as panpipes? Or whether a number of pieces of bone found together might or might not have been struck together as idiophones? We shall find one complex of these later on here which certainly were instruments. And what about bullroarers, those blades of bone, with a hole or a constriction at one end for a cord, which were whirled around the player’s head to create a noise-like thunder or the bellowing of a bull, or if small and whirled faster sounded like the scream of a devil? We have many such bones, but how many were bullroarers, how many were used for some other purpose?
So how did pipes begin? Did someone hear the wind whistle over the top of a broken reed and then try to emulate that sound with his own breath? Did he or his successors eventually realize that a shorter piece of reed produced a higher pitch and a longer segment a lower one? Did he ever combine these into a group of tubes, either disjunctly, each played by a separate player, as among the Venda of South Africa and in Lithuania, or conjointly lashed together to form a panpipe for a single player? Did, over the generations, someone find that these grouped pipes could be replaced with a single tube by boring holes in it, with each hole representing the length of one of that group? All this is speculation, of course, but something like it must have happened.
Or were instruments first made to imitate cries? The idea of the hunting lure, the device to imitate an animal’s cry and so lure it within reach, is of unknown age. Or were they first made to imitate the animal in a ritual to call for the success of tomorrow’s hunt? Some cries can be imitated by the mouth; others need a tool, a short piece of cane, bits of reed or grass or bone blown across the end like a key or a pen-top. Others are made from a piece of bark held between the tongue and the lip (I have heard a credit card used in this way!). The piece of cane or bone would only produce a single sound, but the bark, or in Romania a carp scale, can produce the most beautiful music as well as being used as a hunting call. The softer materials will not have survived and with the many small segments of bone that we have, there is no way to tell whether they might have been used in this way or whether they are merely the detritus from the dining table.
This bone does raise the whole question of whether H. neanderthalensis knew of or practised music in any form. For rhythm, we can only say surely, as above—if earlier hominids could have, so could H. neanderthalensis. Could they have sung? A critical anatomical feature is the position of the larynx (Morley, 2013, 135ff); the lower the larynx in the throat the longer the vocal cords and thus the greater flexibility of pitch variation and of vowel sounds (to put it at its simplest). It would seem to have been that with H. heidelbergensis and its successors that the larynx was lower and thus that singing, as distinct from humming, could have been possible, but “seems to have been” is necessary because, as is so often, this is still the subject of controversy. However, it does seem fairly clear that H. neanderthalensis could indeed have sung. It follows, too, that while the Divje Babe “pipe” may or may not have been an instrument, others may yet be found that were ensemble musical instrument. There is evidence that the Neanderthals had at least artistic sensibilities, for there are bones with scratch marks on them that may have been some form of art, and certainly there is a number of small pierced objects, pieces of shell, animal teeth, and so forth, found in various excavations that can only have served as beads for a necklace or other ornamentation – or just possibly as rattles. There have also been found pieces of pigments of various colors, some of them showing wear marks and thus that they had been used to color something, and at least one that had been shaped into the form of a crayon, indicating that some reasonably delicate pigmentation had been desired. Burials have been found, with some small deposits of grave goods, though whether these reveal sensibilities or forms of ritual or belief, we cannot know (D’Errico et al., 2003, 19ff). There have also been found many bone awls, including some very delicate ones which, we may presume, had been used to pierce skins so that they could be sewn together. All this leads us to the conclusion that the Neanderthals had at least some artistic and other feelings, were capable of some musical practices, even if only vocal, and were clothed, rather than being the grunting, naked savages that have been assumed in the past.
|
|
|
What is velvet fabric? |
Posted by: nsj5521sw - 08-24-2021, 03:03 AM - Forum: Welcomes and Introductions
- No Replies
|
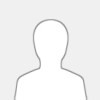 |
Velvet is a sleek, soft fabric that is commonly used in intimate garments, upholstery and other textile applications. Due to how expensive it was to produce velvet textiles in the past, this fabric is often associated with the aristocracy. Even though most types of modern velvet are adulterated with cheap synthetic materials, this unique fabric remains one of the sleekest, softest man-made materials ever engineered.
The first recorded mention of velvet fabric is from the 14th century, and scholars of the past mostly believed that this textile was originally produced in East Asia before making its way down the Silk Road into Europe. Traditional forms of velvet were made with pure silk, which made them incredibly popular. Asian silk was already very soft, but the unique production processes used to make velvet result in a material that’s even more sumptuous and luxurious than other silk products.
Until velvet gained popularity in Europe during the Renaissance, this fabric was commonly used in the Middle East. The records of many civilizations located within the borders of in modern Iraq and Iran, for instance, indicate that velvet was a favorite fabric among the royalty the region.
When machine looms were invented, velvet production became much less expensive, and the development of synthetic fabrics that somewhat approximate the properties of silk finally brought the wonders of velvet to even the lowest rungs of society. While today’s velvet may not be as pure or exotic as the velvet of the past, it remains prized as a material for curtains, blankets, stuffed animals, and all manner of other products that are supposed to be as soft and cuddly as possible.
While various materials can be used to make velvet, the process used to produce this burnout velvet fabric is the same regardless of which base textile is used. Velvet can only be woven on a unique type of loom that spins two layers of fabric simultaneously. These fabric layers are then separated, and they are wound up on rolls.
Velvet is made with vertical yarn, and velveteen is made with horizontal yarn, but otherwise, these two textiles are made with largely the same processes. Velveteen, however, is often mixed with normal cotton yarn, which reduces its quality and changes its texture.
Silk, one of the most popular velvet materials, is made by unraveling the cocoons of silkworms and spinning these threads into yarn. Synthetic textiles such as rayon are made by rendering petrochemicals into filaments. Once one of these yarn types is woven into velvet cloth, it can be dyed or treated depending on the intended application.
The main desirable attribute of velvet is its softness, so this textile is primarily used in applications in which fabric is placed close to the skin. At the same time, velvet also has a distinctive visual allure, so it’s commonly used in home decor in applications such as curtains and throw pillows. Unlike some other interior decor items, velvet feels as good as it looks, which makes this fabric a multi-sensory home design experience.
Due to its softness, velvet is sometimes used in bedding. In particular, this fabric is commonly used in the insulative blankets that are placed between sheets and duvets. Velvet is much more prevalent in womenswear than it is in clothing for men, and it is often used to accentuate womanly curves and create stunning eveningwear. Some stiff forms of velvet are used to make hats, and this material is popular in glove linings.
China leads the world as the most prolific producer of synthetic textiles. These and other reckless industrial practices have rapidly made this communist nation the world’s largest polluter as well, and China is lagging far behind the rest of the world’s gradual switch to sustainable fabrics and non-polluting production processes.
Since “velvet” refers to a fabric weave instead of a material, it can’t technically be said that velvet as a concept has any impact on the environment. The different materials used to make velvet, however, have varying degrees of environmental impact that should be carefully considered.
Environmental impact of silk
Silk is the closest thing we have to an ideal fabric from an environmental standpoint. This embossed velvet fabric is still, in most cases, produced the same way it has been produced for thousands of years, and since the production of silk is not aided by any pesticides, fertilizers, or other toxic substances, making this fabric does not have any significant negative environmental impact.
Environmental impact of rayon and other synthetic textiles
Rayon is the most commonly used substitute for silk in velvet and velvet-inspired fabrics, and the production of this synthetic substance is significantly harmful to the environment. The rayon production process involves multiple chemical washes, and the base material of this substance is petroleum.
Essentially, rayon is non-biodegradable fossil fuel product that introduces tons of harmful chemicals into the water supply as it is created. With these detractors in full view, the only reason that rayon is still produced is that it is inexpensive.
The term “velvety” means soft, and it takes its meaning from its namesake fabric: velvet. The soft, smooth fabric epitomizes luxury, with its smooth nap and shiny appearance. Velvet has been a fixture of fashion design and home decor for years, and its high-end feel and appearance make it an ideal textile for elevated design.
Velvet is a soft, luxurious fabric that is characterized by a dense pile of evenly cut fibers that have a smooth nap. Velvet has a beautiful drape and a unique soft and shiny appearance due to the characteristics of the short pile fibers.
Velvet fabric is popular for evening wear and dresses for special occasions, as the jaguar velvet fabric was initially made from silk. Cotton, linen, wool, mohair, and synthetic fibers can also be used to make velvet, making velvet less expensive and incorporated into daily-wear clothes. Velvet is also a fixture of home decor, where it’s used as upholstery fabric, curtains, pillows, and more.
The first velvets were made from silk and, as such, were incredibly expensive and only accessible by the royal and noble classes. The material was first introduced in Baghdad, around 750 A.D., but production eventually spread to the Mediterranean and the fabric was distributed throughout Europe.
New loom technology lowered the cost of production during the Renaissance. During this period, Florence, Italy became the dominant velvet production center.
Velvet is made on a special loom known as a double cloth, which produces two pieces of velvet simultaneously. Velvet is characterized by its even pile height, which is usually less than half a centimeter.
Velvet today is usually made from synthetic and natural fibers, but it was originally made from silk. Pure silk velvet is rare today, as it’s extremely expensive. Most velvet that is marketed as silk velvet combines both silk and rayon. Synthetic velvet can be made from polyester, nylon, viscose, or rayon.
There are several different Holland velvet fabric types, as the fabric can be woven from a variety of different materials using a variety of methods.
Crushed velvet. As the name suggests, crushed velvet has a “crushed” look that is achieved by twisting the fabric while wet or by pressing the pile in different directions. The appearance is patterned and shiny, and the material has a unique texture.
Panne velvet. Panne velvet is a type of crushed velvet for which heavy pressure is applied to the material to push the pile in one direction. The same pattern can appear in knit fabrics like velour, which is usually made from polyester and is not true velvet.
Embossed velvet. Embossed velvet is a printed fabric created via a heat stamp, which is used to apply pressure to velvet, pushing down the piles to create a pattern. Embossed velvet is popular in upholstery velvet materials, which are used in home decor and design.
Ciselé. This type of patterned velvet is created by cutting some looped threads and leaving others uncut.
Plain velvet. Plain velvet is usually a cotton velvet. It is heavy with very little stretch and doesn’t have the shine that velvet made from silk or synthetic fibers has.
Stretch velvet. Stretch velvet has spandex incorporated in the weave which makes the material more flexible and stretchy.
Pile-on-pile velvet. This type of velvet has piles of varying lengths that create a pattern. Velvet upholstery fabric usually contains this type of velvet.
Velvet, velveteen, and velour are all soft, drapey fabrics, but they differ in terms of weave and composition.
Velour is a knitted fabric made from cotton and polyester that resembles velvet. It has more stretch than velvet and is great for dance and sports clothes, particularly leotards and tracksuits.
Velveteen pile is much shorter pile than velvet pile, and instead of creating the pile from the vertical warp threads, velveteens pile comes from the horizontal weft threads. Velveteen is heavier and has less shine and drape than velvet, which is softer and smoother.
For budding fashion designers, understanding the characteristics and feel of different fabrics is key. In her 20s, Diane von Furstenberg convinced a textile factory owner in Italy to let her produce her first designs. With those samples, she flew to New York City to build one of the world’s most iconic and enduring fashion brands. In her fashion design MasterClass, Diane explains how to create a visual identity, stay true to your vision, and launch your product.
Become a better fashion designer with the MasterClass Annual Membership. Gain access to exclusive video lessons taught by fashion design masters including Marc Jacobs, Diane von Furstenberg, and more.
|
|
|
|