Welcome, Guest |
You have to register before you can post on our site.
|
Online Users |
There are currently 259 online users. » 0 Member(s) | 258 Guest(s) Google
|
Latest Threads |
Dominica visa free countr...
Forum: Off Topic
Last Post: axied12
06-24-2025, 12:37 PM
» Replies: 0
» Views: 207
|
Advanced microneedling
Forum: Off Topic
Last Post: axied12
05-28-2025, 01:25 PM
» Replies: 0
» Views: 333
|
Caviar and cheese
Forum: Off Topic
Last Post: axied12
05-28-2025, 12:38 PM
» Replies: 0
» Views: 294
|
Top-rated countertop comp...
Forum: Off Topic
Last Post: axied12
05-04-2025, 06:42 AM
» Replies: 0
» Views: 445
|
Ryanair letenky levně do ...
Forum: Off Topic
Last Post: axied12
02-11-2025, 01:37 PM
» Replies: 0
» Views: 838
|
Trusted essay writing ser...
Forum: Off Topic
Last Post: axied12
01-30-2025, 08:16 AM
» Replies: 0
» Views: 754
|
Bootverkopers - actieve j...
Forum: Off Topic
Last Post: axied12
12-07-2024, 11:07 AM
» Replies: 0
» Views: 881
|
Services for individuals ...
Forum: Off Topic
Last Post: axied12
12-02-2024, 03:31 PM
» Replies: 0
» Views: 855
|
Used excavators
Forum: Off Topic
Last Post: axied12
11-13-2024, 09:22 AM
» Replies: 0
» Views: 802
|
Buy Higo Rocket in Dubai
Forum: Off Topic
Last Post: axied12
10-25-2024, 01:09 PM
» Replies: 0
» Views: 911
|
|
|
De reden waarom de Led Linear Light niet oplicht |
Posted by: bfiwi256 - 08-17-2021, 08:28 AM - Forum: Welcomes and Introductions
- No Replies
|
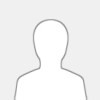 |
De reden waarom het led lineaire licht niet oplicht
Het led lineaire licht moet antistatisch zijn: omdat leds elektrostatisch gevoelige componenten zijn, als u geen antistatische maatregelen neemt bij het repareren van led lineaire lichten, zal de LED Linear Lamp worden doorgebrand, waardoor afval ontstaat. Men zou hier moeten opmerken dat de soldeerbout een antistatische soldeerbout moet gebruiken, en het onderhoudspersoneel moet ook antistatische maatregelen nemen (zoals het dragen van statische ringen en antistatische handschoenen, enz.)
Het aangepaste LEIDENE Lineaire Licht kan geen op hoge temperatuur ondersteunen: de twee belangrijke componenten van geleide lineaire lichten en FPC, geleide lineaire lichten zijn producten die geen op hoge temperatuur kunnen ondersteunen. Als FPC aan op hoge temperatuur verdergaat of zijn weerstaat temperatuur overschrijdt, zal het de dekkingsfilm van FPC veroorzaken te bellen, die direct zal veroorzaken de LEIDENE lineaire lamp om worden afgedankt. Tegelijkertijd is de LED Tri-Proof Lamp niet continu bestand tegen hoge temperaturen. Na een lange tijd bij hoge temperatuur, zal de LED chip doorbranden door de hoge temperatuur.
Daarom moet de soldeerbout die wordt gebruikt bij het repareren van de led-lichtstrip een temperatuurgeregelde soldeerbout zijn, en de temperatuur is beperkt tot een bereik, en het is verboden om naar believen te veranderen en in te stellen. Bovendien, zelfs zo, is het noodzakelijk om aandacht te besteden aan de soldeerbout niet te blijven op de pinnen van de LED Linear System lijn lamp voor meer dan 10 seconden tijdens het onderhoud. Als deze tijd wordt overschreden, kan de chip van de led-lijnlamp worden verbrand.
Als het led-lampje niet brandt, controleer dan of het circuit is aangesloten, of de verbinding slecht is en of de positieve en negatieve polen van de lichtbalk omgekeerd zijn aangesloten. De helderheid van de lichtbalk is duidelijk laag. Controleer of het nominale vermogen van de voeding lager is dan het vermogen van de lichtbalk, of dat de aansluitdraad te dun is, waardoor de aansluitdraad te veel stroom verbruikt. De voorkant van de lichtbalk is duidelijk helderder dan de achterkant. Controleer of de serielengte groter is dan de norm van de fabrikant.
Volgens de analyse van het materiaal van de printplaat, heeft de printplaat ook vele kwaliteitsniveaus. De meeste goedkope lijnlampen op de markt gebruiken het secundaire materiaal printplaat, die gemakkelijk delamineert na verhitting en de koperfolie is te dun. Gemakkelijk af te vallen, slechte hechting, koperfolie laag, en PCB laag zijn gemakkelijk te scheiden, niet om de stabiliteit van de schakeling te noemen, verwacht u dat de schakeling stabiel is, zelfs als de printplaat is als deze?
Met de voortdurende verbetering van de levensstandaard van de mensen, zijn LED-lampen overal te zien in het leven van mensen. Meer en meer klanten kiezen het voor verlichting, en het wordt begunstigd door iedereen voor zijn hoge helderheid, laag energieverbruik, en lange levensduur.
1. Wat moet ik doen als de LED High Bay Lamp-lamp niet brandt? De nieuw geïnstalleerde lamp moet worden gemeten met een elektrische pen om te zien of er spanning in het circuit zit. Als de lamp niet brandt, kan er een probleem zijn met de driver.
2.Wat moet ik doen als de helderheid van de LED-lamp afneemt? De lampkralen op elke string in de lamp zijn in serie geschakeld, en de strings zijn parallel geschakeld. Daarom zal, als er één lamp doorbrandt, de string met lampkralen niet oplichten. Als er niet veel lampkralen doorgebrand zijn, kunt u de twee soldeerpennen achter de doorgebrande lampkralen met een elektrische soldeerbout doorsolderen; als de lampkralen te veel doorbranden, moet u een nieuw lampkralenbord kopen.
3.Wat moet ik doen als het LED-lampje knippert? Controleer of de neutrale draad en de stroomdraad zijn omgewisseld. U moet controleren of de leiding bij de schakelaar rood is. Zo niet, overweeg dan dat de schakelaar mogelijk de neutrale lijn controleert. Vergeet niet deze op tijd te vervangen.
Veel huiseigenaren upgraden hun huizen van traditionele of klassieke stijlen naar ruimtes met een modern gevoel.
LED Tubular Light lineaire verlichting is een veelgebruikte verlichtingsarmatuur in de commerciële binnenhuisarchitectuur. Ze zijn echter niet exclusief voor deze sector. Met verschillende technologische ontwikkelingen is de esthetiek van lineaire verlichting geëvolueerd naar woonhuizen.
Maar voordat u de stap waagt, is het belangrijk om de verschillende soorten en toepassingen van lineaire verlichting te kennen. Lees verder om te ontdekken hoe u ze kunt gebruiken.
Wat is LED Panel Lamp lineaire verlichting?
Dit type plafondverlichting maakt gebruik van heel veel lichtgevende diodes (LED). Fabrikanten verpakken ze samen in een lange, smalle behuizing. Dit resulteert in een strook licht.
Het is een eenvoudig maar revolutionair concept voor de verlichting van woonruimtes. Voorheen bestond er wel LED lineaire verlichting, maar het verlichten van grote ruimtes was lastig. Je kon twee of meer fluorescentielampen gebruiken, maar het was moeilijk om een doorlopende lichtlijn te creëren.
Nu produceert LED Tube Light lineaire verlichting ononderbroken licht zonder zwarte of donkere vlekken achter te laten. Naarmate de technologie zich verder ontwikkelt, worden de esthetiek en de prestaties steeds beter.
Wat zijn de types van LED Wall Light lineaire verlichting?
Er zijn verschillende lineaire verlichtingsopties beschikbaar voor uw ruimte. Of het nu gaat om een kantoor of een grote woonruimte, het juiste type zal een tastbaar verschil maken. Bekijk deze twee soorten lineaire verlichting:
Hangende lineaire verlichting
Hangende lineaire verlichting is een van de populairste verlichtingstrends ter wereld. Creëer een onverwachte look door verschillende dramatische vormen en ophangniveaus te gebruiken.
Door de hoogte van de armaturen te verhogen of te verlagen, wordt de intensiteit van het licht aangepast. Dit kan een dramatisch verschil creëren voor de sfeer in een ruimte. U kunt kiezen tussen directe en indirecte opties om de nadruk te leggen op verschillende designelementen.
De eerste optie is ideaal voor sterke verlichting. Het verbetert de zichtbaarheid bij het uitvoeren van taken. De indirecte optie is uitstekend voor het creëren van de juiste sfeer of het uitbalanceren van harde elementen in een ruimte.
Ingebouwde lineaire verlichting
LED-inbouwstripverlichting neemt minder visuele ruimte in beslag. Het helpt om uw kamer groter te laten lijken omdat de verlichting terug in het oppervlak van het plafond is geplaatst.
Het doel van deze verlichting gaat verder dan het verschaffen van licht, het helpt de belangstelling voor de architectuur van de ruimte te bevorderen en creëert een eigentijdse sfeer. Google Promotional Products
Het is ook een geweldige optie om licht te werpen op specifieke objecten, zonder storende elementen toe te voegen aan het oppervlak van het plafond, zoals plafondlampen, tracklights of spots. Het resultaat is een strakke, eigentijdse en moderne look.
|
|
|
Qu'est-ce que l'éclairage linéaire à LED ? |
Posted by: bfiwi256 - 08-17-2021, 08:26 AM - Forum: Welcomes and Introductions
- No Replies
|
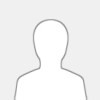 |
De nombreux fabricants et distributeurs de tubes LED prétendent réaliser des économies d'énergie de 50 % et plus lors du remplacement des tubes fluorescents T8 par des lampes de remplacement linéaires LED. Plusieurs distributeurs prétendent même que le même confort visuel sera maintenu après un tel remplacement. Les paramètres optiques et électriques de douze tubes LED linéaires disponibles dans le commerce ont été déterminés et l'évolution dans le temps de ces paramètres a été suivie. En outre, une étude de cas est présentée dans laquelle les lampes fluorescentes d'une petite salle de bureau ont été remplacées par des lampes linéaires LED de remplacement afin de comparer la distribution de l'éclairement sur le plan de travail, la perception de l'éblouissement et l'appréciation visuelle globale. Selon cette étude, il est clair que le remplacement d'un tube fluorescent classique par une lampe LED linéaire actuellement disponible peut avoir des conséquences graves sur la qualité de l'éclairage.
LED Linear est une expression que nous entendons souvent dans le domaine de la décoration intérieure commerciale, mais qu'est-ce que cela signifie exactement et comment l'utiliser ? Cet article vise à "démystifier" l'éclairage linéaire à LED et à vous donner un aperçu de comment et où l'utiliser, pour transformer sans effort des bureaux froids en bureaux exceptionnels !
Tout d'abord, parlons des LED. Une LED est l'abréviation de "Light Emitting Diode" (diode électroluminescente), une source de lumière très efficace et durable qui utilise un semi-conducteur pour convertir l'électricité en lumière. Lorsqu'une tension appropriée est appliquée aux fils, les électrons peuvent se recombiner avec les "trous d'électrons" à l'intérieur du dispositif, libérant ainsi de l'énergie sous forme de photons (lumière). La couleur de la lumière est déterminée par la bande d'énergie du semi-conducteur. Bon, assez de détails techniques, voyons comment la LED a vu le jour. Les LED sont apparues dès 1962, et ont été utilisées comme composants pratiques dans des articles électriques, tels que des feux d'avertissement. Les premières LED High Bay Lamp se limitaient à une lumière infrarouge de faible intensité, comme celles qui sont encore utilisées dans les télécommandes. Vous souvenez-vous de ces premières montres à LED avec un écran noir et des chiffres rouges qui apparaissaient lorsque vous appuyiez sur un bouton ? Les premières LED à lumière visible étaient également de faible intensité et limitées au rouge, mais les LED modernes sont désormais disponibles dans les longueurs d'onde visibles, ultraviolettes et infrarouges et peuvent être extrêmement lumineuses.
Qu'est-ce que l'éclairage linéaire à LED ? L'éclairage linéaire à LED consiste simplement à utiliser de nombreuses diodes électroluminescentes regroupées dans un boîtier long et étroit pour créer une bande de lumière. Ce concept simple a révolutionné la façon dont nous éclairons les espaces. Avant la conception de l'éclairage linéaire à LED, il était notoirement difficile d'éclairer de longs espaces tels que des bureaux, des entrepôts et des magasins. Ces espaces étaient éclairés par de grandes ampoules industrielles à incandescence. L'éclairage linéaire a commencé à évoluer dans les années 1950 avec les tubes fluorescents, principalement utilisés dans les espaces industriels. Dans les années 1970, cette technologie a été utilisée dans les maisons, les garages et les ateliers, ainsi que dans les espaces commerciaux. Cette évolution a créé un besoin de luminaires plus économiques et plus esthétiques. La création d'une ligne de lumière continue et ininterrompue n'était pas possible avant les LED Linear Lamp, car les tubes fluorescents devaient s'arrêter et repartir en laissant un point noir ou sombre. L'amélioration de l'apparence n'a pas eu lieu avant le début des années 2000, lorsque la première version de LED Linear telle que nous la connaissons a été créée. La demande pour les LED linéaires est maintenant énorme et continue de croître. La différence aujourd'hui est que l'éclairage architectural linéaire et la technologie LED ont élargi les applications des luminaires linéaires. Le secteur continue d'évoluer en améliorant l'esthétique et les performances, en s'éloignant des anciens boîtiers traditionnels, en utilisant mieux les matériaux et en intégrant des technologies plus avancées.
Les clients de Synergy aiment savoir quelques choses sur les normes et les réglementations relatives à l'éclairage, en particulier pour les espaces publics et de travail ; il suffit de demander et nous pouvons vous conseiller ! L'une des principales réglementations concerne l'éblouissement dû à l'éclairage. Il est donc important de réduire l'éblouissement direct et l'éblouissement réfléchi dans un environnement de bureau. L'indice d'éblouissement unifié (UGR) est utilisé comme mesure de l'éblouissement et est calculé en divisant l'éblouissement de toutes les lampes visibles par le laminage de fond de la pièce. Dans un environnement de bureau, un UGR inférieur à 19 est considéré comme acceptable pour une meilleure concentration. Vous voulez en savoir plus sur l'UGR19 ? Lisez notre guide UGR19 ici>> Les niveaux de lux sont également importants. Il s'agit essentiellement du niveau de lumière dans un espace, généralement mesuré à partir d'une hauteur spécifique (comme la hauteur du bureau dans un bureau). La CIBSE (Chartered Institution of Building Services Engineers) spécifie les niveaux de lux recommandés pour différentes zones dans le secteur des bâtiments commerciaux.
Nos clients apprécient une foule d'avantages offerts par l'éclairage linéaire à LED, notamment : Esthétique - si l'apparence est importante pour vous, alors l'éclairage linéaire à LED a une offre assez forte. Il offre une très grande polyvalence pour créer des designs uniques et accrocheurs. Les angles sur mesure, les courbes et le revêtement en poudre de couleur RAL personnalisé ne sont que quelques-unes des options disponibles qui font de LED Linear un choix facile. Lumière directionnelle - Les LED Tri-Proof Lamp sont directionnelles, ce qui réduit le besoin de réflecteurs et de diffuseurs qui peuvent piéger la lumière. Température de couleur - Les luminaires LED Linear offrent une large gamme de températures de couleur, qui influent sur la façon dont l'œil interprète la lumière. Du blanc froid au blanc chaud, les différentes températures peuvent être utilisées pour créer une ambiance et une atmosphère dans un espace. Le blanc neutre, ou 4000 kelvin pour utiliser son nom technique, est recommandé pour les bureaux et les zones de vente au détail, car il offre l'environnement le plus confortable. Rentabilité - un avantage évident, la LED Linear est extrêmement efficace en raison de sa faible consommation d'énergie, et aussi de sa longévité inhérente ; une LED durera généralement plusieurs fois plus longtemps qu'un tube fluorescent. Une fois que vous avez pris la décision d'utiliser un éclairage linéaire à LED pour votre espace, il y a une gamme déconcertante d'options, nous avons donc décomposé certains des facteurs clés à prendre en compte :
Les trois principaux types de luminaires linéaires à LED sont les luminaires suspendus, en surface ou encastrés. Les luminaires LED Linear System linéaires suspendus utilisent des fils de suspension pour être accrochés au plafond, et sont plus adaptés aux pièces ayant une hauteur de plafond généreuse. Ils sont également idéaux pour créer un éclairage d'accentuation étonnant - pensez à les suspendre au-dessus des bureaux de réception, des escaliers ou des atriums. Les luminaires linéaires à LED montés en surface sont montés sur la surface de la pièce et sont adaptés aux situations où les luminaires suspendus pourraient être trop bas en raison de la hauteur du plafond. Les luminaires linéaires à LED encastrés sont encastrés dans une surface, qu'il s'agisse d'un plafond, d'un mur ou... Cela offre des lignes nettes et ininterrompues.
Les luminaires linéaires à LED Tube Light peuvent être droits ou façonnés pour créer des sculptures spectaculaires pour un effet ultime. Les profils droits créent généralement un effet plus subtil, mais peuvent également être utilisés pour créer des designs géométriques accrocheurs. Les profils courbes contribuent généralement à créer un flux dans un espace et à donner une impression de mouvement. Les profils ronds sont souvent utilisés pour diviser l'espace en zones, en particulier dans les espaces ouverts. Par exemple, les anneaux de LED suspendus plus bas que l'éclairage environnant au-dessus des zones de collaboration créent un sentiment de concentration.
Les LED Fluorescent Lamp linéaires sont très polyvalentes et peuvent être utilisées pour un certain nombre d'applications d'éclairage. Éclairage général - il s'agit de l'éclairage de haut niveau qui fournit la lumière de fond dans un espace. Il faut veiller à ce que la lumière soit distribuée uniformément et à éviter les éblouissements. Éclairage de travail - il s'agit d'un éclairage ciblé pour des tâches spécifiques, comme un anneau de LED suspendu bas au-dessus d'une zone de collaboration. Accentuation - lumière utilisée pour un effet esthétique, par exemple pour mettre en valeur ou refléter la forme d'un élément architectural distinctif ou donner une impression de hauteur à une pièce. Nos luminaires encastrés LED Panel Lamp Linear sont parfaits pour cela. Laissez libre cours à votre imagination et les résultats peuvent être étonnants ! L'éclairage linéaire LED peut être un champ de mines déconcertant avec toutes les options disponibles. Cependant, les résultats que vous pouvez créer sont stupéfiants et rendent sans aucun doute un bureau cool exceptionnel, alors pour plus d'informations de notre sympathique équipe d'experts à Synergy, contactez-nous et nous vous aiderons à décider ce dont vous avez besoin !
LED LinearL'humble diode électroluminescente a également commencé comme une invention assez standard, mais grâce à sa propre personnalité électroluminescente, elle a fait irruption sur la scène au début des années 1960 comme un produit réalisé.
Le premier modèle achevé de la LED n'émettant que de la lumière rouge, elle était principalement utilisée pour l'éclairage d'urgence. Un modèle bleu a suivi, mais ces produits sont restés dans une gamme de prix très inaccessible au grand public. Une véritable perte pour les gens du monde entier !
Cependant, à l'approche des années 90, le prix des éclairages à LED a baissé, les matériaux sont devenus plus accessibles et des visionnaires innovants ont expérimenté les capacités et l'esthétique des LED.
L'une de ces conceptions inspirées a été la solution d'éclairage linéaire à LED Wall Light. Dans cette forme d'éclairage simple, mais révolutionnaire, les lampes à DEL sont alignées comme une unité étendue.
Mais pourquoi était-ce révolutionnaire ? Avant l'arrivée de l'éclairage linéaire à LED, les espaces de bureau étaient soumis à des difficultés lorsqu'il s'agissait d'éclairer de longs espaces avec une seule unité. L'éclairage linéaire existait sous la forme de tubes fluorescents, mais ces produits vacillants, bourdonnants et contenant du mercure ne permettaient pas d'éclairer complètement les pièces ou de fournir une solution esthétique pour obtenir un effet WOW.
L'éclairage LED était la solution dont les bureaux et les grands espaces intérieurs avaient besoin et, à ce jour, c'est l'une des options d'éclairage de bureau les plus populaires sur le marché. Si vous utilisez encore un éclairage fluorescent et que vous avez besoin d'une motivation supplémentaire pour changer, découvrez les avantages de l'éclairage LED par rapport à l'éclairage fluorescent Google Promotional Products.
|
|
|
لماذا يجب عليك استخدام الإضاءة الخطية؟ |
Posted by: bfiwi256 - 08-17-2021, 08:25 AM - Forum: Welcomes and Introductions
- No Replies
|
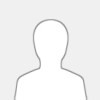 |
بالنسبة لمشروعك القادم ، ضع في اعتبارك تضمين الإضاءة الخطية LED. إنه يوفر إضاءة كافية لإضاءة أي مساحة معيشة كما أنه رائع أيضًا لتحسين التصميم الداخلي ، مما يجعل غرفتك أكثر جاذبية.
المصابيح الخطية LED هي مستقبل الإضاءة التجارية والسكنية. إن النمو الهائل في صناعة مصابيح LED العالمية هو دليل على ذلك. فيما يلي بعض الأسباب الأخرى للتبديل إلى الإضاءة الخطية Linear LED bulbs :
استخدامات عمذا كنت تعمل من المنزل ، فستستفيد من الإضاءة الخطية بتقنية 3 LED bulbs. يجعل إعداد عملك أكثر راحة ، مع الحفاظ على جمالية حديثة.
إنه يضيء الزوايا المظلمة في منزلك ويجعلها أكثر بهجة للعيش فيها.
تخصيص المشروع
توفر المصابيح الخطية LED Tri-Proof Lamp مجموعة متنوعة من درجات حرارة الألوان. يمكنك استخدامها لإبراز العناصر المختلفة لتصميمك الداخلي وخلق حالة مزاجية.
ستحصل على رؤية أفضل مع هذه الأضواء. يقدم السوق حلولًا متنوعة ، لذلك ليس من الصعب العثور على الحل المناسب. الإضاءة الخطية Linear LED System ممتازة أيضًا للتركيبات الأكثر تخصيصًا.
باستخدام أشرطة LED أو مقاطع الألمنيوم ، يمكنك عمل أنماط وتصميمات فريدة. هذا ما يجعل المساحة بأكملها تبدو فريدة من نوعها. جرب بعض تصميمات الإضاءة الخطية التي تصرخ 2021 لتحسين مظهر غرفتك هذا العام.
كفاءة
تتمثل إحدى الفوائد الرئيسية لإضاءة LED Bulbs on High Ceilings الخطية في المستوى العالي لكفاءة الطاقة. ستحصل على نفس القدر من ناتج الضوء الذي تحصل عليه من إضاءة الفلورسنت مع الإضاءة الخطية ، ومع ذلك ، ستستخدم طاقة أقل بكثير وتنفق أقل.
يمكنك الاعتماد على مصابيح LED لتدوم لفترة أطول من مصابيح الفلورسنت أو المصابيح المتوهجة. يمنحك الاستثمار فيها قيمة أكبر مقابل المال. اشترِ من الشركات المصنعة ذات الخبرة والموثوقية لتحقيق أقصى استفادة من مصابيح LED الخطية.
LED الخطي مقابل الفلورسنت الخطي: إيجابيات وسلبيات
يستخدم معظم مصنعي صناعة الإضاءة ذات السمعة الطيبة مصابيح LED tubes الخطية. النطاق متعدد الاستخدامات ، من خط القيمة إلى الإنتاج العالي. ولكن هناك مزايا للإضاءة الفلورية الخطية أيضًا. إليك التفاصيل بين إيجابيات وسلبيات كل نوع من أنواع الإضاءة:
إيجابيات LED الخطية
كما ذكرنا سابقًا ، تعد إضاءة LED أكثر كفاءة في استخدام الطاقة من الإضاءة الأخرى. يدوم المصباح حوالي 50000 ساعة ، ويفقد 30٪ من إنتاجه بعد عقد من الزمان. بعضها لديه عمر افتراضي أقل ، ولكن بشكل عام تدوم جميعها لفترة أطول من نظيراتها الفلورية.
لا تستخدم الإضاءة الخطية LED Panel Bulbs أي الزئبق ، مما يجعلها خيارًا صديقًا للبيئة.
تقدم معظم الشركات المصنعة لمصابيح LED ضمانات قوية للمنتجات ، مما يمنحك راحة البال.
سلبيات LED Wall Mounted Bulbs الخطية
العيب الأساسي لاستخدام مصابيح LED الخطية هو السعر. ومع ذلك ، فإن التكلفة معقولة الآن أكثر مما كانت عليه في الماضي.
تتمتع مصابيح LED الخطية بإطلالة لا حصر لها من الخيارات بأسعار مختلفة ، لذا قم ببعض الأبحاث لتجنب الشعور بالإرهاق.
إيجابيات الفلورسنت الخطية
إذا كنت تبحث عن منتج أقل تكلفة ، فإن الفلورسنت الخطي هو الأفضل. تكلفتها الأولية أقل من نظيرتها بتقنية LED tubes. كما أنه سهل التثبيت ويمكن أن يستمر لأكثر من 20000 ساعة. Google Offers
يمكن لبعض الفلورات الخطية (مجتمعة مع الصابورة اليمنى) أن تدوم لفترة أطول من ذلك. في بعض الحالات ، يمكن أن تستمر أكثر من 90.000 ساعة.
سلبيات الفلورسنت الخطية
الزئبق هو العيب الأساسي لاستخدام هذه المنتجات. إنها ليست صديقة للبيئة كما أنها توفر كفاءة أقل في استخدام الطاقة.
تعني التحسينات التكنولوجية استخدام معدن أقل سمية ، ومع ذلك ، فإنه لن يعمل بدون وجود كمية معينة.
استخدم الأضواء الخطية في مشروعك
إذا كنت تفكر في استخدام الأضواء الخطية ، ولكن لا تعرف من أين تبدأ ، يمكننا مساعدتك في التواصل مع محترفي الإضاءة للمساعدة في وضعك على المسار الصحيح لإنشاء تصميم إضاءة عالي التأثير.
بدلاً من ذلك ، قم بالتسجيل للحصول على حساب Archipro والانضمام إلى أكبر مجتمع للتصميم في نيوزيلندا والحصول على الإلهام من خيارات الإضاءة التي لا نهاية لها. تصفح المشاريع ، والوصول إلى الخبراء ، ومقارنة المنتجات.
|
|
|
Hvad er lineær LED-belysning (lineær kanalbelysning)? |
Posted by: bfiwi256 - 08-17-2021, 08:24 AM - Forum: Welcomes and Introductions
- No Replies
|
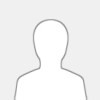 |
LED Trunk Linear System (lineært kanal-system) er en sætning, vi ofte hører inden for kommerciel indretning, men hvad betyder det, hvordan bruger vi det? Denne artikel giver et dybdegående kig på LED lineær belysning og giver dig indsigt i, hvordan og hvor du kan bruge den, så du nemt kan forvandle dit kontor til et cool, high-end kontor i moderne stil!
Lad os først tale om LED Linear Light. LED er en forkortelse for "lysemitterende dioder", en effektiv og langtidsholdbar kilde, der bruger halvledere til at omdanne elektrisk energi til lys. Når der påføres en passende spænding på ledningerne, kan elektronerne rekombineres med "elektronhuller" i enheden og frigive energi i form af fotoner (lys). Lysets farve bestemmes af halvlederens energi.
Ja, det er en teknisk ting, lad os se på, hvordan LED'er dannes.
LED'er dukkede op i begyndelsen af 1962 og blev brugt som brugsdele i elektroniske produkter, f.eks. advarselslamper. Tidlige LED'er var begrænset til infrarødt lys med lav intensitet, som f.eks. dem, der stadig anvendes i fjernbetjeninger. Kan du huske de LED-ure med sorte skærme, vil røde tal vises, når du trykker på knappen? Den første synlige LED er også meget lavintensiv og begrænset til rødt, men nu anvendes moderne LED'er i det synlige, ultraviolette og infrarøde bølgelængdeområde, og de kan opnå høj effekt i belysning.
LED-linjelys er ganske enkelt pakket i en lang, smal kuvert, hvor der anvendes en række "lysdioder" til at danne en lysstrimmel. Dette enkle koncept har revolutioneret den måde, vi belyser rum på.
Lange rum såsom belysning af kontorer, lagerbygninger og butikslokaler er vanskelige at belyse, før LED-lineærkonceptet opstod. Disse rum belyses med store industrielle glødepærer. Lineær belysning begyndte at udvikle sig i 1950'erne, primært til lysstofrør i industrielle rum. I 1970'erne blev denne teknologi anvendt i hjem, garager og værksteder samt i butikslokaler. Dette skaber yderligere et behov for billigere og mere æstetisk tiltalende armaturer. Det er ikke muligt at producere kontinuerligt uafbrudt lys før LED, fordi lysstofrøret skal stoppe og begynde at efterlade sorte eller mørke pletter.
Det forbedrede udseende dukkede først op i begyndelsen af 2000, og vi kender de tidlige versioner af LED-linjelamperne. Efterspørgslen efter tri-proof LED-light er enorm og fortsætter med at vokse. Forskellen nu er, at lineær arkitektonisk belysning og LED-teknologien udvider anvendelsesområdet for lineære armaturer. Efterhånden som æstetikken og ydeevnen forbedres, skiller den sig ud fra det gamle traditionelle kabinet, idet den anvender materialer på en bedre måde og vedtager mere avanceret teknologi, fortsætter industrien med at udvikle sig.
LED-linjelamper (lineært kanalanlæg) regler og standarder
Caihao Optoelectronics kunder vil gerne vide noget om belysningsstandarder og -regler, især på offentlige steder og arbejdspladser. Med mange års erfaring med fremstilling af LED-belysning kan vi give råd!
En af de vigtigste regler handler om blænding af belysning. Overdreven blænding fra belysning kan forårsage øjenbelastning og hovedpine, så det er vigtigt at reducere direkte blænding og reflekteret blænding i kontormiljøet. Unified Glare Scale (UGR) anvendes som et mål for blænding og beregnes ved at dividere blændingen fra alle synlige lys med rummets baggrundslaminat. I et kontormiljø anses en UGR på under 19 for at være den bedste koncentration, der er acceptabel.
LED-belysningsniveauet (lumen) er også vigtigt. Dette er grundlæggende niveauet af lysstyrke i rummet, som normalt måles fra en bestemt højde, f.eks. højden på et skrivebord i et kontor. De arkitektoniske standarder for belysningsdesign fastsætter det anbefalede niveau af lumen i forskellige områder af kommercielt byggeri.
Hvorfor bruge LED High Bay Light (lineært kanalanlæg)?
Vores kunder sætter pris på de mange fordele ved LED-lineær belysning(lineært kanalanlæg) , herunder:
Æstetik - Hvis udseendet er vigtigt for dig, er LED-linjelysene meget kraftige. Det giver en stor alsidighed til at skabe unikke og overbevisende designs. Tilpassede vinkler, kurver og farver med brugerdefineret udseende er blot nogle få af de muligheder, der er til rådighed, hvilket gør anvendelsen af LED-linjelys let.
Retningsbestemt lys - LED'er er retningsbestemt, hvilket reducerer behovet for reflektorer og diffusorer, der kan fange lyset.
Farvetemperatur - LED-linjelys (lineært kanalanlæg)giver et bredt udvalg af farvetemperaturer, der påvirker, hvordan øjet opfatter lys. Fra kold hvid til varm hvid kan forskellige temperaturer bruges til at skabe en atmosfære og stemning i rummet. Neutralhvid eller 4000 Kelvin bruger sit tekniske navn og anbefales til kontor- og butiksområder, der giver det mest behagelige miljø.
Omkostningseffektiv - En klar fordel, LED tube light fungerer meget effektivt på grund af dens lave strømforbrug og iboende levetid; LED er mange gange længere end lysstofrør og har typisk en levetid på mere end 50.000 timer.
|
|
|
Everything You Need To Know About High Bay Lighting |
Posted by: bfiwi256 - 08-17-2021, 08:23 AM - Forum: Welcomes and Introductions
- No Replies
|
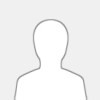 |
What is high bay lighting?
High bay lighting is the go-to solution in many workplaces for achieving bright and uniform illumination across large, high-ceilinged indoor spaces. It’s most often found in warehouses, department stores, manufacturing areas and sports halls.
But what is LED high bay light exactly, and how does it differ from other high-intensity lighting solutions?
Rather than any single fixture style, the term ‘high bay lighting’ refers to the positioning of the luminaires, and as such it covers a broad and flexible range of lamp types and fittings. As a rule of thumb, MatePro UFO highbay light is usually the best option for any indoor setting where the floor-to-ceiling height measures 8m (roughly 25’) or taller.
For less lofty spaces, low bays (or even a series of appropriately arranged floodlights) may be enough to get the job done. But, where indoor work areas span a great deal of vertical and horizontal space, the lighting solution needs to be both powerful and flexible.
In this guide, we’ll tell you everything you need to know about the various types of high bay lighting configurations available, and the sorts of environments they’re best suited to.
What’s the difference between high bay and low bay lighting?
Low bay lighting setups, as the name suggests, are more commonly used where there’s less vertical distance for the light to cover. In these situations, lower mounting positions will often allow for a shallower lighting angle, making it easier to illuminate vertical surfaces or to create specific lighting effects in smaller zones.
High bays are most often found in warehouses, gantries, above a large shop or conference floors, at sports facilities, in expansive factory or workshop environments...anywhere that needs uniform, brilliant illumination to maximise visibility and light quality over a wide area.
Apart from the different mounting altitudes, another key contrast between high bay and low bay light setups is that high bays tend to rely on more careful consideration of layout, fittings and components.
T-line linear highbay light must be chosen and positioned to ensure the light they cast is strong, uniform, and equally effective at hitting both vertical and horizontal surfaces from a wider angle.
To achieve this, high bay lighting tends to demand the more exacting placement of lamps and reflectors. When configured properly, high bay setups can achieve superb quality and intensity of light across the entirety of a wide, tall space.
LED stands for light-emitting diode which is a light conductor that emits white light when a current flows through it. LED panels are commonly used in video and photography as a directional light source. LED’s are known for their powerful white light, low energy consumption, and durability.
LED panel lights have become a popular option for creators in all different industries. Due to their practical and versatile design, there has been a surge in market demand for light panels. However, not all lights are created equal.
The LED Bulkheads' cool white light is an attractive alternative to the harsh orange output of SOX lamps. With efficiency comparable to that of fluorescent lighting, the LED Bulkhead is smaller than other lamps of the same output. Its instant start, with no warming-up period is a significant advantage for event triggered security lighting. The LED Bulkhead, rated at up to 60W, is the most powerful of a range that starts from 20W. With supply inputs ranging from 23.5W to 70.6W, this range has an electrical efficiency of 90%. The LEDs typically yield 100 lumens per watt and the light has a colour temperature of 5000 to 7500 K.
LED Tri-proof Lights are durable and eco-friendly alternative lighting systems to traditional fluorescent LED tube lights. LED Tri-proof Lights are designed to withstand severe environments and will help you reduce your energy consumption by up to 80%.
LED Tri-proof Lights are specifically built to withstand conditions susceptible to water, dust and corrosion impacts. Our Lighting tri-proof Lights are Incredibly durable and long lasting, they are highly resistant to heavy impacts.
|
|
|
Three Benefits of LED High Bay Lighting |
Posted by: bfiwi256 - 08-17-2021, 08:21 AM - Forum: Welcomes and Introductions
- No Replies
|
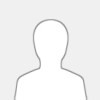 |
In the world of lighting, the high bay is a fixture that you would find in a warehouse, a factory, a gymnasium, or any large open area with relatively high ceilings. Many existing high bay lighting and low bay lighting applications utilize high intensity discharge (HID) lamps such as metal halide or high pressure sodium lamps.
Despite their widespread use, HID lamps utilize antiquated technology that costs building managers both directly and indirectly. Specifically, using HID lamps will result in: higher than necessary energy costs, frequent maintenance costs, and poor lighting performance. These issues can all be addressed by converting your existing lighting to LED.
Energy Savings
Energy savings is a primary driver behind why you should evaluate LED lighting for your building or facility. Common wattages for LED high bay lights can range from 95 watts to 495 watts. If we compare this wattage to a typical HID high bay fixture that same range is 175 watts to 1000 watts.
Consequently, by switching to LED lighting you are immediately reducing your energy consumption by 40%-60%. To put this in dollars, you would be saving $300 per fixture per year in electricity costs if you made the switch to LED lighting. Depending on the size of your facility this can really affect the operational balance sheet.
Maintenance Cost Reduction
By converting to LEDs you will also see a dramatic reduction in the maintenance of your T-Line linear highbay light fixtures. This is due to the way LEDs generate light, and the way they progress through their functional life. Instead of ceasing to function properly once a fuel source is significantly reduced, LED generated light output degrades very slowly over time. As a result, the functional life of an LED product can be significantly longer than that of a HID Lamp, therefore drastically reducing the maintenance load required.
For example, by converting conventional 400w HID T-Line modular linear highbay lighting to LED, a typical building with industrial light fixtures can save up to $5,341 over the course of three years in maintenance costs alone.
Lighting Performance
Finally, lighting performance is a critical factor in evaluating the move to a different type of lighting. From a performance standpoint, matepro ufo highbay lights are a head-and-shoulders above their HID counterparts.
LEDs utilize a multi-point design, meaning they distribute light on the intended surface evenly. Therefore, light levels across a given surface will vary less between fixture mounting locations. In addition to the even distribution of light, LEDs are available in a range of CCTs (correlated color temperatures) and as a result provide a range of options to increase the visual perception of “brightness."
In contrast, HID fixtures produce a “bright spot” directly underneath the fixture with light levels decreasing drastically as the distance between fixtures increases.
Conclusion
In conclusion, we can see that there are three primary drivers to consider installing an LED retrofit in your facility. By converting you will see immediate energy savings, decreased frequency of lighting maintenance, and an uptick in overall lighting performance.
LED Tri-proof light is a special light made of special protective materials, waterproof, dust-proof and anti-corrosion . Tri proof means "Waterproof" "Dust-proof" "Anti-corrosion".
Special anti-oxidation and anti-corrosion material and Silica Gel sealing ring are used to realize the protection requirements of lights. According to the actual working environment of the Tri-proof light, the surface of the lamp protection box is treated with nano-spraying plastic damp-proof and anticorrosive treatment, which prevents the entry of dust and moisture.
Because fluorescent fixtures are often mounted into ceilings and connected directly to mains electricity, they are relatively expensive and difficult to replace completely. As a result, it oftentimes makes the most economical sense to simply use the same fluorescent fixture, but replace the fluorescent tube with an LED tubar light. Therefore, it is important to understand the types of fluorescent tubes that were developed, so that the correct LED tube light can be retrofitted in place.
If you want LED panel lights for home or office, there will be different shapes and sizes available for you. Most commonly, you will have to choose between a square or round LED panel light. Although some people can make a decision easily, others will probably be pickier.
In general, you should choose a shape that looks beautiful in the context of use. However, when looking at the squares and circles of LED panel lights, you will encounter some technical differences. These differences may affect the functionality of the panel under certain settings.
|
|
|
Drei Vorteile der LED-Hochregalbeleuchtung |
Posted by: bfiwi256 - 08-17-2021, 08:20 AM - Forum: Welcomes and Introductions
- No Replies
|
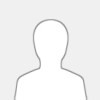 |
In der Welt der Beleuchtung ist das Hochregal eine Vorrichtung, die man in einem Lagerhaus, einer Fabrik, einer Sporthalle oder einem anderen großen offenen Bereich mit relativ hohen Decken findet. In vielen bestehenden Beleuchtungsanlagen für Hochregale und Tiefregale werden HID-Lampen (High Intensity Discharge) wie Halogen-Metalldampflampen oder Natriumdampf-Hochdrucklampen verwendet.
Trotz ihrer weiten Verbreitung verwenden HID-Lampen eine veraltete Technologie, die Gebäudeverwalter sowohl direkt als auch indirekt Kosten verursacht. Insbesondere die Verwendung von HID-Lampen führt zu höheren Energiekosten als nötig, zu häufigen Wartungskosten und zu einer schlechten Beleuchtungsleistung. All diese Probleme können durch die Umrüstung Ihrer vorhandenen Beleuchtung auf LED linear light gelöst werden.
Energieeinsparung
Energieeinsparungen sind einer der Hauptgründe, warum Sie LED tri-proof light für Ihr Gebäude oder Ihre Anlage in Betracht ziehen sollten. Gängige Wattzahlen für LED-Hochregalbeleuchtungen reichen von 95 bis 495 Watt. Vergleicht man diese Wattzahl mit einer typischen HID-Hochregalbeleuchtung, so liegt der gleiche Bereich zwischen 175 und 1000 Watt.
Wenn Sie also auf LED trunk linear umsteigen, reduzieren Sie Ihren Energieverbrauch sofort um 40-60 %. In Dollar ausgedrückt bedeutet dies, dass Sie durch die Umstellung auf LED-Beleuchtung 300 Dollar pro Leuchte und Jahr an Stromkosten einsparen würden. Je nach Größe Ihrer Einrichtung kann sich dies erheblich auf die Betriebsbilanz auswirken.
Senkung der Wartungskosten
Durch die Umstellung auf LED down light werden Sie auch eine drastische Verringerung der Wartungskosten für Ihre Hochregalbeleuchtung feststellen. Dies liegt an der Art und Weise, wie LEDs Licht erzeugen, und an der Art und Weise, wie sie ihre Funktionsdauer verlängern. Die von LEDs erzeugte Lichtleistung nimmt im Laufe der Zeit nur sehr langsam ab, so dass sie nicht mehr ordnungsgemäß funktioniert, sobald eine Brennstoffquelle deutlich reduziert wird. Infolgedessen kann die Lebensdauer eines LED-Produkts wesentlich länger sein als die einer HID-Lampe, wodurch sich der Wartungsaufwand drastisch verringert.
Durch die Umrüstung einer herkömmlichen 400-W-HID-Hochregalbeleuchtung auf LED kann ein typisches Gebäude mit industriellen Beleuchtungskörpern über einen Zeitraum von drei Jahren allein bei den Wartungskosten bis zu 5.341 $ einsparen.
Beleuchtungsleistung
Schließlich ist die Beleuchtungsleistung ein entscheidender Faktor bei der Bewertung der Umstellung auf eine andere Art von Beleuchtung. Vom Standpunkt der Leistung aus gesehen sind LEDs ihren HID-Gegenstücken haushoch überlegen.
LED panel lights verwenden ein Mehrpunktdesign, d. h. sie verteilen das Licht gleichmäßig auf der vorgesehenen Oberfläche. Daher variieren die Lichtstärken auf einer bestimmten Fläche weniger zwischen den verschiedenen Montageorten der Beleuchtungskörper. Zusätzlich zur gleichmäßigen Verteilung des Lichts sind LED high bay lights in einer Reihe von CCTs (korrelierte Farbtemperaturen) erhältlich und bieten daher eine Reihe von Optionen, um die visuelle Wahrnehmung der "Helligkeit" zu erhöhen.
Im Gegensatz dazu erzeugen HID-Scheinwerfer einen hellen Fleck" direkt unter dem Scheinwerfer, wobei die Lichtstärke mit zunehmendem Abstand zwischen den Scheinwerfern drastisch abnimmt.
Fazit
Abschließend können wir feststellen, dass es drei Hauptgründe gibt, die für eine LED-Umrüstung in Ihrer Einrichtung sprechen. Durch die Umrüstung werden Sie sofortige Energieeinsparungen, eine geringere Häufigkeit der Beleuchtungswartung und eine Verbesserung der Gesamtbeleuchtungsleistung feststellen. Erfahren Sie, wie eine LED-Retrofit-Anlage für Sie geeignet sein könnte - kontaktieren Sie Stouch Lighting noch heute und wir würden uns freuen, Ihnen eine kostenlose Einschätzung Ihrer Anlage zu geben.
|
|
|
What is the LED Batten light? |
Posted by: bfiwi256 - 08-17-2021, 08:19 AM - Forum: Welcomes and Introductions
- No Replies
|
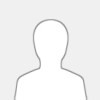 |
LED batten lights have come along way in the last few years with the technology of LED, now batten lights have loads of different options as oppose to every batten being 2 x 36 fluorescent battens. LED battens now are much more streamlined with a slim and minimalist look but yet still put out the same brightness, this is great because 4 foot fluorescent battens are a real eye saw but now with LED battens they can manipulate the fittings to give a much cleaner and less commercial look. The best thing about battens is they are super practical with a real bright light and wide beam angles. When buying your LED upton batten lights there are a few considerations to make so in this blog I will run through what questions to ask before buying and our favourite best selling LED general batten lights.
IP Rating - The IP rated refers to the light being suitable for indoor or outdoor. If your application is outdoors then go with IP66, this is a high rating which will protect from water and dust. If you are buying for indoor you can still go with a IP66 as it will still protect from dust and physical impacts, otherwise an IP20 is fine as well with most batten still sealed.
LED - There are still loads of fluorescent batten and tubes out there with people still replacing the tubes and ballasts, this is a bad idea as you can now buy for T8 LED direct replacement tubes. LED Battens use 70% less power and last 10 times longer than fluorescent tubes, LED tubes also now perform better in brightness and imitate a fluorescent tube without you knowing the difference. So always go with LED for all these reasons. LED tube lights are also much safer and better for the environment with fluorescent tubes containing mercury.
Integrated LED or LED Tubes - Most LED battens sold today are integrated which means once the light batten dies basically throw it out which isn't ideal as you will need to replace and get an electrician to come back and replace, this can cost around $200 with the call out fee. When a manufacturer makes something integrated they can make it better with heat sinks and pushing up the performance as there is only so much technology you can fit into a tube. So if you are buying a LED integrated batten, only buy from quality brands, buying from LiteHome these brands means you are buying from a manufacturer with strict quality control. Avoid cheap brands as you will only get headaches and they maybe not even comply. When buying anything, I think practical and purchasing a batten with LED T8 tubes means you can always replace the tubes yourself so literally can't go wrong, however with T8 battens, they look much more bulky and commercial, with LED integrated battens they much more slimline.
Colour Temperature - This is crucial to get right if you are installing LED battens in work environments such as garages, car parks, warehouses, workshops, kitchens etc, you should always look to use a temperature of a minimum 5000k as this colour spectrum reacts with the brain most in keeping alert and active. If your application needs to suit a heritage or traditional set up then you could look to use a 3000k or 4000k per perfuably and this will soften the light to create more ambience and warmth.
LED Linear light is a phrase we often hear in the realms of commercial interior design, but what exactly does it mean and how do we use it? This article aims to ‘de-mystify’ commercial LED Linear lighting and give you an insight into how and where to use it, to effortlessly turn cool offices into exceptional ones!
Firstly let’s talk about LEDs. An LED is short for ‘Light Emitting Diode’, which is a highly efficient long-lasting source of light that uses a semiconductor to convert electricity into light. When a suitable voltage is applied to the leads, electrons are able to recombine with ‘electron holes’ within the device, releasing energy in the form of photons (light). The colour of the LED trunk linear is determined by the energy band of the semiconductor.
|
|
|
FIBC Jumbo Bags |
Posted by: bfiwi256 - 08-17-2021, 08:17 AM - Forum: Welcomes and Introductions
- No Replies
|
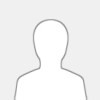 |
PP woven bags or jumbo bags are known as Flexible Intermediate Bulk Container Bags (FIBC bags). It is an economical and ideal packing used for the storage & transportation of powdered, granulated and bulk products like sand, fertilizers or plastic granules. FIBCs are most often made of thick woven polyethylene or polypropylene, either coated or uncoated. We are masters in making polypropylene texture/fabric in a type of cubic bags.
Rectangular jumbo Bags are easy for storing and carrying solid material. Also, these are resistant to any sort of physical damage. They don't cause any harm to the material while carrying in the bag. With a large storage capacity, these jumbo bags are ideal for carrying huge material in a convenient and simple manner.
U-Panel jumbo bags are constructed with three main body components – one that runs the full length of the bag forming the bottom and two sides (the “U”) and two additional pieces of fabric sewn between the U on two sides (the “Panel”). Generally, U-panel bags will maintain a square shape when filled, especially with the addition of internal baffles. U-panel bags are an industry standard and the most popular type of construction.
Baffles are pieces of fabric that are sewn to the inside corners of a bag to maintain its cube shape after filling. The baffles have holes that allow the product to flow freely through them. The baffles also prevent the bag from bulging, which makes the baffle jumbo bag stand up straight and in turn allows the bags to be more efficient in their use of space. Net and tie baffles are another type of baffle option, but not as common.
Type C jumbo Bags are known within the industry as conductive or groundable Bulk Bags or conductive jumbo bags. Constructed from non-conductive polypropylene material interwoven with conductive yarns that form a grid pattern, these are designed to control electrostatic charges by grounding. The inner or outer surfaces of the FIBC may have a thin coating. In this case, the breakdown voltage to the conductive threads must not exceed 6 kV to avoid propagating brush discharges The bag must be electrically grounded during filling and emptying - this is essential to the safe use and performance of a Type C bag.
Also called a tubular jumbo bag, the Circular Bag is made from fabric woven on a circular loom, which is then cut to the proper length for a specified bag height, thereby eliminating the vertical seams on each of the bag’s sides. The tubular body design is ideal as a linerless option for fine and hygroscopic materials. It is also an excellent alternative to the original four-panel bag construction.
What are anti-static FIBCs, or anti-statics jumbo bags? They are large transport and storage bags that resist electrostatic charge. Their typical diameter when filled is 45 to 48 inches, which allows the bags to fit two across in a typical shipping container or truck. They are standardized containers and meet ISO standards.
FIBCs, or flexible indeterminate bulk containers, have the following characteristics:
1. They cannot be handled manually when they are filled.
2. They are intended for the transport of solid material, whether flakes, powder or grains.
3. They require no further packaging.
4. They are designed for lifting from above by their lift loops or straps.
|
|
|
What Is Polyester Fabric? |
Posted by: fowjw558 - 08-17-2021, 02:46 AM - Forum: Welcomes and Introductions
- No Replies
|
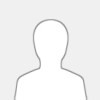 |
Polyester is a synthetic fabric that’s usually derived from petroleum. This fabric is one of the world’s most popular textiles, and it is used in thousands of different consumer and industrial applications.
Chemically, polyester is a polymer primarily composed of compounds within the ester functional group. Most synthetic and some plant-based polyester fibers are made from ethylene, which is a constituent of petroleum that can also be derived from other sources. While some forms of polyester are biodegradable, most of them are not, and polyester production and use contribute to pollution around the world.
In some applications, polyester may be the sole constituent of apparel products, but it’s more common for polyester to be blended with cotton or another natural fiber. Use of polyester in apparel reduces production costs, but it also decreases the comfortability of apparel.
When blended with cotton, polyester improves the shrinkage, durability, and wrinkling profile of this widely-produced natural fiber. Polyester fabric is highly resistant to environmental conditions, which makes it ideal for long-term use in outdoor applications.
The fabric we now know as polyester began its climb toward its current critical role in the contemporary economy in 1926 as Terylene, which was first synthesized by W.H. Carothers in the UK. Throughout the 1930s and 1940s, British scientists continued to develop better forms of ethylene fabric, and these efforts eventually garnered the interest of American investors and innovators.
Polyester fiber was originally developed for mass consumption by the DuPont Corporation, which also developed other popular synthetic fibers like nylon. During World War II, the Allied powers found themselves in increased need of fibers for parachutes and other war materiel, and after the war, DuPont and other American corporations found a new consumer market for their synthetic materials in the context of the postwar economic boom.
Initially, consumers were enthusiastic about the improved durability profile of polyester compared to natural fibers, and these benefits are still valid today. In recent decades, however, the harmful environmental impact of this synthetic fiber has come to light in great detail, and the consumer stance on polyester has changed significantly.
Nonetheless, polyester remains one of the most widely-produced fabrics in the world, and it’s hard to find consumer apparel that doesn’t contain at least some percentage of polyester fiber. Apparel that contains polyester, however, will melt in extreme heat, while most natural fibers char. Molten fibers can cause irreversible bodily damage.
Ethylene Polyester
Ethylene polyester (PET) is the most commonly-produced form of polyester fiber. The primary component of PET is petroleum-derived ethylene, and in the process of creating polyester fiber, ethylene serves as the polymer that interacts with other chemicals to create a stable fibrous compound.
There are four ways to make PET fiber, and the polyester production process varies slightly depending on which method is used:
1.Filament: Polyester filaments are continuous fibers, and these fibers produce smooth and soft fabrics.
2.Staple: Polyester staples resemble the staples used to make cotton yarn, and like cotton staples, polyester staples are usually spun into a yarn-like material.
3.Tow: Polyester tow is like polyester filament, but in polyester tow, the filaments are loosely arranged together.
4.Fiberfill: Fiberfill consists of continuous polyester filaments, but these filaments are produced specifically to have the most possible volume to make bulky products like pillows, outerwear, and stuffing for stuffed animals.
The process of creating polyester fiber begins with reacting ethylene glycol with dimethyl terephthalate at high heat. This reaction results in a monomer, which is then reacted with dimethyl terephthalate again to create a polymer.
This molten polyester polymer is extruded from the reaction chamber in long strips, and these strips are allowed to cool and dry, and then they are broken apart in to small pieces. The resulting chips are then melted again to create a honey-like substance, which is extruded through a spinneret to create fibers.
Depending on whether filaments, staple, tow, or fiberfill fibers are desired, the resulting polyester filaments may be cut or reacted with various chemicals to achieve the correct end result. In most applications, polyester fibers are spun into yarn before they are dyed or subjected to other post-production processes.
PCDT Polyester
The process of creating PCDT polyester is similar to the process of creating PET polyester, but this polyester variant has a different chemical structure. While PCDT also consists of ethylene glycol reacted with dimethyl terephthalate, different production processes are used to make these two common polyester variations.
Plant-Based Polyester
Most types of plant-based polyester are also made from ethylene glycol reacted with dimethyl terephthalate. While the source of the ethylene used in PET and PCDT polyester is petroleum, however, producers of plant-based polyester use ethylene sources like cane sugar instead.
[color=rgba(0, 0, 0, 0.8)]Chiffon fabric [/color]
Chiffon fabric was first made in France, but the production of this substance expanded worldwide as the Industrial Age picked up steam. By the first few decades of the 1900s, silk chiffon was in relatively wide production in the United States, and producers of this fabric in America were starting to show interest in replacing silk with another material for chiffon production.
Crepe fabric
Crepe fabric has no clear origin point in the history of human civilization. Since the concept behind crepe is so simple, many cultures have adopted forms of this fabric at one stage of development or another. For instance, Crepe is still used by Orthodox Greek women for mourning, and various cultures of the Indian subcontinent incorporate crepe into their traditional garments.
Satin Fabric
Satin Fabric refers to the weave of the fabric rather than the material. Satin is one of the three major textile weaves, along with plain weave and twill. The satin weave creates a fabric that is shiny, soft, and elastic with a beautiful drape. Satin fabric is characterized by a soft, lustrous surface on one side, with a duller surface on the other side. This is a result of the satin weaving technique, and there are many variations on what defines a satin weave.
Polyester is not biodegradable
The majority of polyesters are not biodegradable, meaning that the polyester fabric shirt you bought last season will not decompose for 20 years at best and 200 years at worst.
What’s more, polyester is partially derived from petroleum, and the oil manufacturing industry is the world’s largest pollutant.
Polyester dyes are not sustainable
Ever notice how polyester fabrics are stain-resistant? That’s because it takes a special kind of dye to colour polyester successfully. These dyes, known as disperse dyes, are insoluble in water. Like polyester, they are made up of a complex molecular structure that does not readily decompose.
Wastewater from textile factories containing leftover dye is difficult to treat. When it enters the environment, its toxicity causes serious problems to local plant and animal life.
In addition to causing environmental problems, polyester dyes are toxic to humans. Dye workers worldwide report higher incidences of cancers and lung disease than the general population.
Polyester manufacturing is water-thirsty
Acetate imitation fabric is created through an energy-intensive heating process and requires large quantities of water for cooling. If not managed properly, this can result in groundwater levels dropping and reduced access to clean drinking water, particularly in vulnerable communities where polyester is often manufactured.
More on those microfibres
Multiple studies have shown that synthetic fibres make up a good share of microplastics found in waters and are widely implicated as the source of pollution. It’s been suggested that more than 4,500 fibres can be released per gram of clothing per wash, according to the Plastic Soup Foundation.
Microfibres are so tiny they can easily move through sewage treatment plants. They do not biodegrade and bind with molecules from harmful chemicals found in wastewater. They are then eaten by small fishes and plankton, concentrating toxins and going up the food chain until they reach us. The consequences of microfibres on the human body have yet to be researched and revealed. Until then, here are our top tips on dealing with microfibres in clothing.
What Is Polyester Used For
Georgette printed fabric, as we all know, is often used for clothing, nowadays its more common to find blended cotton and polyester than full polyester. The main reason for this is the lack of breathability in pure polyester, and frankly few people like the look now. Blended fabrics also retain many of the benefits of polyester; being more resistant to wrinkling, having more stretch, and sometimes more resistant to wear.
Outside of fashion, polyester is used for a great variety of products; the most common being plastic bottles and containers. Some others include sailcloth, canoes, tarpaulin, LCDs, insulating tapes, various items for film, ropes, cord, and more. Polyester is also commonly used as a finish to high-quality wood products like pianos, guitars, and vehicle interiors (which is then polished to a glossy, durable finish).
|
|
|
|